基于LabVIEW的虚拟仪器外文翻译
虚拟函数波形发生器中英文对照外文翻译文献
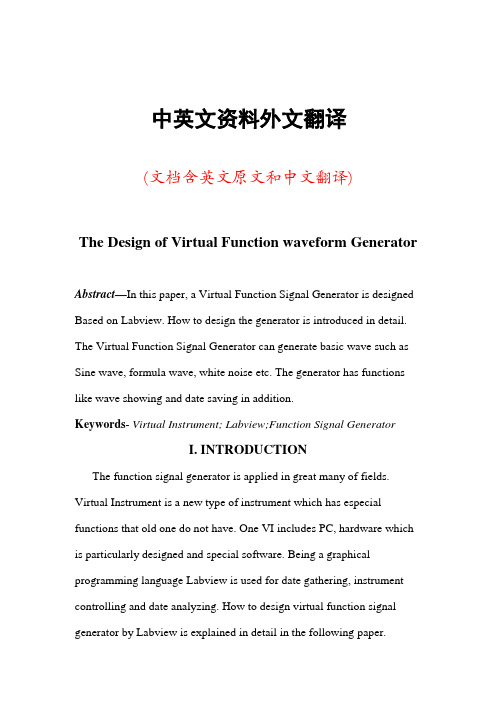
中英文资料外文翻译(文档含英文原文和中文翻译)The Design of Virtual Function waveform GeneratorAbstract—In this paper, a Virtual Function Signal Generator is designed Based on Labview. How to design the generator is introduced in detail. The Virtual Function Signal Generator can generate basic wave such as Sine wave, formula wave, white noise etc. The generator has functions like wave showing and date saving in addition.Keywords- Virtual Instrument; Labview;Function Signal GeneratorI. INTRODUCTIONThe function signal generator is applied in great many of fields. Virtual Instrument is a new type of instrument which has especial functions that old one do not have. One VI includes PC, hardware which is particularly designed and special software. Being a graphical programming language Labview is used for date gathering, instrument controlling and date analyzing. How to design virtual function signal generator by Labview is explained in detail in the following paper.II. TOTAL DESIGNAccording to the principle of function signal generator,four parts were designed to compose virtual function signal generator. These four parts are property setting, signal generating, wave showing and date saving.A. Panel of GeneratorIn this system the panel are divided to property setting panel(fig.1) and total structure panel(fig.2) . Main options in the first one are frequency, amplitude, duty cycle and samples etc. about signal. These properties can be set in this panel. Total structure panel just includes four parts that were presented above and some additional parts.Figure 1.Property Set Panel Figure2.Total Structure PanelB. Function about InstrumentsThe Virtual Function Signal Generator can generate basic waves such as Sine wave , special waves like formula wave and some kinds of noise. Signal’s frequency can be regulated delicately or roughly. Property can be reset quickly and be used as subprogram sometimes. Moreover has the generator functions like wave showing and date saving etc.III. SOFTWARE ABOUT VIRTUAL FUNCTION SIGNALGENERATORThe Virtual Function Signal Generator was designed base on Labview 7.0. There are three modules which compose this system: module of property setting, wave generating, wave showing and saving.A. Module of Property SettingFrequency setting and property resetting are two important parts of this module. How to change frequency value multiply is explained in fig.3. Node Selectting isapplied repeatedly and skillfully so that data can be input in manychannels. Then select data by switchbutton. So frequency controlling canbe designed as real instrument. Howto reset property quickly is explainedin fig.4.Figure4. Property ResetFigure3. Frequency ControlB. Module of Wave GeneratingThis module is the core of the Virtual Function Signal Generator. Structure CASE is used in this work. By special node many types of waves can be generated. For example, how to generate sine wave is explained in fig.5. The other ones can be generated in similar way.Figure5.Graphical Progranm About Sine Wave GenerateC. Module of Wave Showing and SavingIn fact this module is a composite one which include many functions as operating, applying, debugging, showing etc. Because of lots of acts would be operated though this interface, this interface must be not only practical but also nice. Fig.6 just explained how to solve these problems.Figure6.Graphical Program About TotalIV. CONCLUSIONBeing graphical language, Labview is very strong and easy tool to make system of measure and test. Virtual Function Signal Generator based on Labview has advantages such as having friendly interface, operating easily etc. It can generate many types of function signals which have big range of value of frequency and its output datas can be saved. So it can be applied widely.虚拟函数波形发生器的设计摘要在本次设计中,虚函数信号发生器是基于相位差来设计的。
Labview外文翻译(带中文对照)

LabVIEWLabVIEW is a highly productive graphical programming language for building data acquisition an instrumentation systems.With LabVIEW, you quickly create user interfaces that give you interactive control of your software system. To specify your system functionality,you simply assemble block diagrams - a natural design notation for scientists and engineers. Tis tight integration with measurement hardware facilitates rapid development of data acquisition ,analysis,and presentation bVIEW contains powerful built -in measurement analysis and a graphical compiler for optimum performance. LabVIEW is available for Windows 2000/NT/Me/9x, Mac OS, Linux, Sun Solaris, and HP-UX, and comes in three different development system options.Faster DevelopmentLabVIEW accelerates development over traditional programming by 4 to 10 times! With the modularity and hierarchical structure of LabVIEW, you can prototype ,design, and modify systems in a short amount of time. You can also reuse LabVIEW code easily and quickly in other applications.Better InvestmentUsing a Lab VIEW system, each user has access to a complete instrumentation laboratory at less than the cost of a single commercial instrument. In addition, user configurable LabVIEW systems are flexible enough to adapt to technology changes, resulting in a better bong-term investment.Optimal PerformanceAll LabVIEW applications execute at compiled speed for optimal performance. With the LabVIEW Professional Development System or Application Builder, you can build stand-alone executables or DLLs for secure distribution of your code. You can even create shared libraries or DLLs to call LabVIEW code from other programming languages.Open Development EnvironmentWith the open development environment of LabVIEW, you can connect to other applications through ActiveX, the Web, DLLs, shared libraries, SQL(for databases), DataSocket, TCP/IP,and numerous other e LabVIEW to quickly create networked measurement and automation systems that integrate the latest technologies in Web publishing and remote data sharing. LabVIEW also has driver libraries available for plug-in data acquisition, signal conditioning , GPIB,VXI,PXI, computer-based instruments,serial protocols, image acquisition, and motion control. In addition to the LabVIEW development systems, National Instruments offers a variety of add-on modules and tool sets that extend the functionality of LabVIEW .This enables you to quickly build customizable, robust measurement and automation systems.LabVIEW Datalogging and Supervisory Control ModuleFor high channel count and distributed applications, the LabVIEW Datelogging and Supervisory Control Module provides a complete solution. This module delivers I/O management, event logging and alarm management, distributed logging, historical and real-time trending, built-in security, configurable networking features, OPC device connectivity, and over 3,300 built-in graphics.LabVIEW Real-TimeFor applications that require real-time performance, National Instruments offers LabVIEWReal-Time. LabVIEW Real-Time downloads standard LabVIEW code to a dedicated hardware target running a real-time operating system independent from Windows.LabVIEW Vision Development ModuleThe LabVIEW Vision Development Module is for scientists, automation engineers,and technicians who are developing LabVIEW machine vision and scientific imaging applications. The LabVIEW Vision Development Module includes IMAQ Vision, a library of vision functions, and IMAQ Vision Builder, an interactive environment for vision applications. Unlike any other vision products, IMAQ Vision Builder and IMAQ Vision work together to simplify vision software development so that you can apply vision to your measurement and automation applications.Countless ApplicationsLabVIEW applications are implemented in many industries worldwide including automotive, telecommunications, aerospace, semiconductor, electronic design and production, process control, biomedical, and many others, Applications cover all phases of product development from research to design to production and to service. By leveraging LabVIEW throughout your organization you can save time and money by sharing information and software.Test and MeasurementLabVIEW has become an industry-standard development tool for test and measurement applications. With Test Stand, LabVIEW-based test programs, and the industry's largest instrument driver library, you have a single, consistent development and execution environment for your entire system.Process Control and Factory AutomationLabVIEW is used in numerous process control and factory automation applications.Many scientists and engineers look to LabVIEW for the high speed, high channel count measurement and control that graphical programming offers.For large, complex industrial automation and control applications, the LabVIEW Data logging and Supervisory Control Module provides the same graphical programming as LabVIEW, but is designed specifically for monitoring large numbers of I/O points, communicating with industrial controllers and networks, and providing PC-based control.Machine Monitoring and ControlLabVIEW is ideal for machine monitoring and predictive maintenance applications that need deterministic control, vibration analysis, vision and image processing, and motion control. With the LabVIEW platform of products including LabVIEW Real-Time for real-time deterministic control and the LabVIEW Data logging and Supervisory Control Module, scientists and engineers can create powerful machine monitoring and control applications quickly and accurately.Research and AnalysisThe integrated LabVIEW measurement analysis library provides everything you need in an analysis package. Scientists and researchers have used LabVIEW to analyse and compute real results for biomedical, aerospace, and energy research applications, and in numerous other industries. The available signal generation and processing, digital filtering, windowing, curve-fitting, For specialized analysis, such as joint time-frequency analysis, wavelet,and model-based spectral analysis, LabVIEW offers the specially designed Signal Processing Toolset.The Sound and Vibration Toolset offers octave analysis, averaged and nonaveraged frequency analysis, transient analysis, weighted filtering, and sound-level measurement, and more.Draw Your Own SolutionWith LabVIEW, you build graphical programs called virtual instruments (VIs) instead of writing text-based programs. You quickly create front panel user interfaces that give you the interactive control of your system. To add functionality to the user interface, you intuitively assemble block diagrams- a natural design notation for engineers and scientists.Create the Front PanelOn the front panel of your VI, you place the controls and data displays for your system by selecting ob jects from the Controls palette, such as numeric displays, meters, gauges, thermometers, LEDs, charts,and graphs.When you complete and run your VI,you use the front panel to control your system whether you move a slide, zoom in on a graph, or enter a value with the keyboard.Construct the Graphical Block DiagramTo program the VI, you construct the block diagram without worrying about the syntactical details of text-based programming languages. You do this by selecting objects (icons) from the Functions palette and connecting them together with wires to transfer data among block diagram objects. These objects include simple arithmetic functions, advanced acquisition and analysis routines, network and file I/O operations, and more.Dataflow ProgrammingLabVIEW uses a patented dataflow programming model that frees you from the linear architecture of text-based programming languages. Because the execution order in LabVIEW is determined by the flow of data between nodes,and not by sequential lines of text,you can create block diagrams that execute multiple operations in parallel. Consequently, LabVIEW is a multitasking system capable of running multiple execution threads and multiple VIs in parallel.Modularity and HierarchyLabVIEW VIs are modular in design, so any VI can run by itself or as part of another VI. You can even create icons for your own VIs, so you can design a hierarchy of VIs that serve as application building blocks. You can modify, interchange, and combine them with other VIs to meet your changing application needs.Graphical CompilerIn many applications, execution speed is critical. LabVIEW is the only graphical programming system with a compiler that generates optimized code with execution speeds comparable to compiled C programs. You can even use the LabVIEW profiler to analyse and optimize time-critical operations. Consequently, you increase your productivity with graphical programming without sacrificing execution speed.Measurements and MathematicsLabVIEW includes a variety of other measurement analysis tools. Examples include curve fitting, signal generation, peak detection, and probability and statistics. Measurement analysis functions can determine signal characteristics such as DC/RMS levels, total harmonic distortion (THD),impulse response, frequency response, and cross-power spectrum. LabVIEW users can also deploy numerical tools for solving differential equations, optimization, root finding, and other mathematical problems.In addition, you can extend these built-in capabilities by entering MATLAB or HIQ scripts directly in your LabVIEW programs. For charting and graphing, you can rely on the built-in LabVIEW 2D and 3D visualization tools. 2D tools include features such as autoscaling X and Y ranges, reconfigurable attributes (point/line styles, colors, and more)andcursors, Microsoft Windows users can employ OpenGL-based 3D graphs and then dynamically rotate, zoom, and pan these graphs with the mouse.Development SystemThe LabVIEW Professional Development System facilitates the development of high-end, sophisticated instrumentation systems for developers working in teams, users developing large suites of VIs, or programmers needing to adhere to stringent quality standards.Built on the Full Development System, the Professional Development System also includes the LabVIEW Application Builder for building stand-alone executables and shared libraries (DLLs)and creating distribution kits. In addition, the development system furnishes source code control tools and offers utilities for quantitatively measuring the complexity of your applications. With graphical differencing, you can quickly identify both cosmetic and functional differences between two LabVIEW applications.We include programming standards and style guides that provide direction for consistent LabVIEW programming methodology. The system also contains quality standards documents that discuss the steps LabVIEW users must follow to meet internal regulations or FDA approval. The Professional Development System operates on Windows 2000/NT/Me/9x,Mac OS, HP-UX, and Linux.LabVIEW Full Development SystemThe LabVIEW Full Development System equips you with all of the tools you need to develop instrumentation systems. It includes GPIB, VISA, VXI, RS-232, DAQ, and instrument driver libraries for data acquisition and instrument control. The measurement analysis add DC/RMS measurements, single tone analysis, harmonic distortion analysis, SINAD analysis, limit testing, signal generation capabilities, signal processing, digital filtering, windowing, curve fitting, statistics, and a myriad of linear algebra and mathematical functions. The development system also provides functions for direct access to DLLs, ActiveX, and other external code. Other features of the system include Web publishing tools, advanced report generation tools, the ability to call MATLAB and HiQ scripts, 3D surface, line, and contour graphs, and custom graphics and animation. The Full Development System operates on Windows 2000/NT/Me/9x, Mac OS, HP-UX, and Linux.LabVIEW Base PackageUse the LabVIEW Base Package, the minimum LabVIEW configuration, for developing data acquisition and analysis, instrument control, and basic data presentation. The Base Package operates on Windows 2000/NT/Me/9x.Debug License for LabVIEWIf you deploy LabVIEW applications, including LabVIEW tests for use with Test Stand, the debug license allows you to install the LabVIEW development system on the target machines so you can step into your test code for complete test debugging. This license is not intended for program development.虚拟仪器(LabVIEW)虚拟仪器是一种高效用于构建数据采集与监测系统图形化编程语言。
外文翻译---基于LabVIEW的电流互感器校验仪
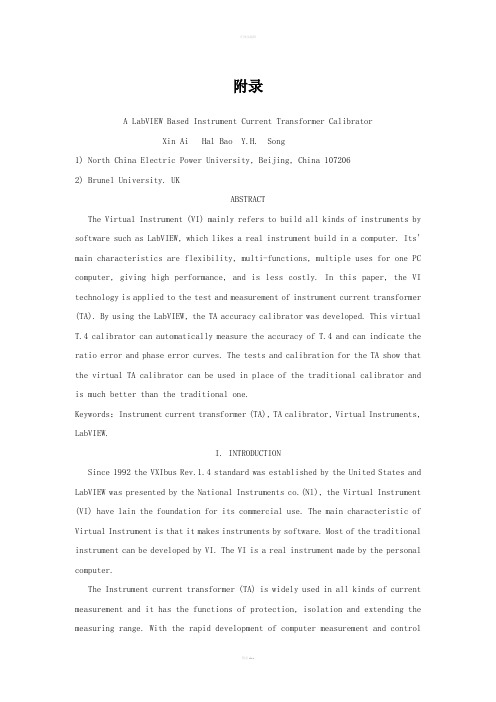
附录A LabVIEW Based Instrument Current Transformer CalibratorXin Ai Hal Bao Y.H. Song1) North China Electric Power University, Beijing, China 1072062) Brunel University. UKABSTRACTThe Virtual Instrument (VI) mainly refers to build all kinds of instruments by software such as LabVIEW, which likes a real instrument build in a computer. Its' main characteristics are flexibility, multi-functions, multiple uses for one PC computer, giving high performance, and is less costly. In this paper, the VI technology is applied to the test and measurement of instrument current transformer (TA). By using the LabVIEW, the TA accuracy calibrator was developed. This virtual T.4 calibrator can automatically measure the accuracy of T.4 and can indicate the ratio error and phase error curves. The tests and calibration for the TA show that the virtual TA calibrator can be used in place of the traditional calibrator and is much better than the traditional one.Keywords:Instrument current transformer (TA), TA calibrator, Virtual Instruments, LabVIEW.I. INTRODUCTIONSince 1992 the VXIbus Rev.1.4 standard was established by the United States and LabVIEW was presented by the National Instruments co.(Nl), the Virtual Instrument (VI) have lain the foundation for its commercial use. The main characteristic of Virtual Instrument is that it makes instruments by software. Most of the traditional instrument can be developed by VI. The VI is a real instrument made by the personal computer.The Instrument current transformer (TA) is widely used in all kinds of current measurement and it has the functions of protection, isolation and extending the measuring range. With the rapid development of computer measurement and controltechnology, and with the sequent emergence of current transformer and transducer, there is an increasing number of current transformers with high accuracy and low secondary current. The standard TA secondary current is usually1A or 5A: some non-standard TA secondary current may be 0 1A or lower. Although we have the technique to make this kind of calibrator by means of hardware such as single chip computer and electronic circuit, DSP and so on, it will cost too much money for these no-standard calibrator and will take too much time and the calibrator made by these hardware mill not be satisfactory in both function and practicality for designing all kinds of new TA.The calibrator that adopts VI technology not only can meet the requirements of the traditional one but also can satisfy customers with such advantages as multi-functions, convenience, and high ratio between performance and cost. The experiment results indicate that the virtual calibrator can provide excellent condition for TA measurement and design. The VI technology and personal computer must be widely used in the area of calibration on instrument transformer.Ⅱ. THE WORKING PRINCIPLE OF TA CALIBRATOR The error of TA includes ratio error and phase error. The measuring of the error of TA or the calibration of the accuracy of TA usually applies differential measuring method. The method needs a standard TA except the measured TA and a TA calibrator. There is the same turn ratio between the standard and measured T4 and the standard TA's accuracy should be 2 levels higher than the measured one. The calibrator function lies in forming comparison circuits, measuring, and showing the error at all range. The comparison circuit, also referred to the difference measuring principle circuit, is showed in Fig. 1. By measuring the voltage on I, and Rd, calculate the corresponding current. Then the calibrator can indicate the error.When a TA has the same turn ratio between the primary and secondary winding, the self-comparison circuit could be used and is shown in Fig.2. In the figures, TA0 and TAX are standard and TA being measured respectively. Np and Ns are primary and secondary winding turns. ip and io, id, i, are primary current secondary standard current, secondary error current, secondary current of TA being measured respectively. Ro and R,R, are secondary winding's resistance of standard TA, error current detecting resistance, burden resistance of TA being measured respectively. To and K, Tb. T, are voltage sampling points which can calculate the current In this paper, only voltage between K and T, voltage between Tb and T, are being measured and they represent the voltage on R, and R, respectively.In general, the TA calibrator's principle of the sample resistance should be: 1) it can not affect the accuracy of the comparison circuit. In the ideal condition R, and Rd should be 0, but it can not be sampled. So there must be sample resistance, in this paper, R, as shown in Fig, is used;1)the magnitude of the sample resistance should make the sampled standard current and error current in pro rata and should not have too much difference. The sampled resistance is set by experiment: R, is the secondary standard current sampling resistance and can be 0.1-0.50, R, is the error current sampling resistance and can be, R, is the burden resistance and it depends on the TA being measured. E$ sampling the voltage uo and U, on R, and R, respectively, the ratio error and phase error are showed on the LED through some process and calculations.According to the TA error's phase diagram, when io is maximum, the value of id is the ratio error; when io changes from negative to positive and equals to 0, the value of id is the phase error. For the same principle, the relationship is equal to the voltage signal U, and ud. showed in Fig.3. a and b is represent the ratio error and phase error separately. the TA's real ratio error C and phase error 6 can be found out through proper calculation,Where U, is the amplitude of uo The T.4 calibrator doesn't need very high accuracy. 1% to 3% error for the calibrator is enough. Because of the difference measuring principle, the error is the read error of calibrator, that is, the TA's error's error being measured. But the calibrator needs to have a suitable enlargement factor. The calibrator maximum enlargement factor through all channels should be 1000 times.III. THE PRINCIPLE OF VIRTUAL CA LIBRATORThe Virtual Instrument consists of three parts: the external comparison circuit (showed in Fig.1 or Fig.2), data acquisition card (PCI-6023) installed in the PC and the VI program by LabVIEW Then, after the two channels' signal U, and ud come into the PC through the ADC, the rest of the work is done by the software. In this paper we use voltage U, on R, substitute for U, approximatively. The virtual calibrator's work flow chart is shown as follow:1) Set the essential initial values of the virtual calibrator;2) Press the start button to start to work, adjusting the voltage regulator andchanging the primary current, let the ratio between primary current and the rated current change from10% to 120%;3) The VI program will group the voltage signal U, and ud , then use the digitalfilter to eliminate the harmonic:4) Calculate the root-mean-square (RMS) value of tlx and 14, find out the amplitude of 21;5) Calculate the RMS valve of io (substitute for f, ), i, and the ratio between io and it's rated current and show the results.6) Find out the a and b showed in Fig. 3, calculate the ratio error and phase error and show the results.7) Set the L times loop, record and show the errors acquired by every time,8) Show and print all the results of calibration.9)Stop.The front panel of the virtual calibrator has the Controls, indictor and Switch.The function of Controls is to set the initial value before it works, The function of the Indictor is to show at1 kinds of needed values, including digital, curve and diagram etc.. 'The switch decides the start and stop of the virtual calibrator.Of course, to change the measuring range, the operator needs to adjust the voltage regulator and change the primary current. This operation is necessary like that of the traditional calibration, but the recording for the error in any range is done by the virtual calibration. This confirms the accuracy of recording and relieves the operator's work. The use of virtual calibrator is most interesting.The controls of virtual calibrator include:1) Setting the two sampling (analogue input) channels;2) Setting the magnitude of sampling resistance in the comparison circuit;3) Setting the secondary rated current of measured TA;4) Setting the number of sampling of error curve;The Indictor of virtual calibrator has:1) Showing ratio and phase error, ratio between the primary current and the rated ones in digital;2) Showing ratio and phase error, ratio between the primary) current and the ratedones In curves and diagram, where the curve include the active sampling points and function fitting curves;3) Showing the error for the ratio between the primary current and the rated current from 10% to 1 20°%;4) Showing the waveform of standard and error current, digital value of amplitude;5) Showing of digita1 RMS value the standard and error current;6) Showing the pole of TA in the comparison circuit;The above shows that the function of virtual calibrator is greatly expended that of the traditional ones. 7111s kind of calibrator is not only convenient to use, but also makes the performance of the calibrator much better. From the function that shows the waveform, we can find out if there are some harmonics in the current, and confirm the accuracy for the calibrator.IV. EXPERIMENTThe virtual calibrator is mainly characterized by the flexibility compared with the traditional ones. Although the front panel has many functions, they can be easily extended by the user. So the virtual calibrator is of important value for the non-standard TA calibration.In the experiment, the primary current produce by a step-up current transformer and its' current controlled by a voltage regulator. Through fitting the comparison circuit, the measuring range of the virtual calibrator can be set in any value. This paper gives SA and 0.1A two kinds of TA’s calibration experiment. The pa rameter and method, results are presented below.A. 5A TA experimentThe parameter of TA being measured is:Because of the 1:1 ratio of turn, the calibration for it doesn't need standard TA. The calibration circuit show in Fig2 We can apply self calibration method to measure it’s accuracy. The results are presented in the Ftg.4 and Fig5 and show that this TA's accuracy can be defined as 0.5 degree.B. 0.1A TA experimentThe parameter of standard TA:From the Fig4 and 5, the accuracy of the TA being measured can be defined as 0.5 degree. In the experiment, the input signal of virtual calibrator should be properly grounded to avoid the disturbance. The sampling resistance in the comparison circuit should use precise ones and with no induction.V. CONCLUSIONSThe VI technique is one of the new scientific and technique productions. Theappearance of VI is called“Revolution of Measuring and Control Technology”. According to the development of the software and hardware for computers, the VI t~hn01Ogy will have more developing space. The VIS will replace most of the traditional ones in the 21th century. With its flexibility, the virtual calibrator can measure any kind of T.4 including standard and non-standard ones. But the traditional calibrator can not measure most of the non-standard TA. It can record and save, display the data automatically. The method presented in this paper gives a new way to make he TA calibration. The main characteristics of the virtual calibrator are:1) Flexibility, virtual calibrator is mainly made of LabVIEW software and can beeasily modified by rewrite some software;2.) Multi function, VI is designed on PC. It has waveform indictor, parametercontrols and so on. At the time we calibrating a TKs accuracy, these functions can indicate many information such as waveform quality and so on;3) Convenience to carry and use;4) High efficiency and accuracy.;5) High ratio between performance and cost;6) For multiple use in one PC.7) It can record and save, display the calibration data automatically.基于LabVIEW的电流互感器校验仪Xin Ai Hai Bao T. H. Song---布鲁塞尔大学摘要虚拟仪器(VI),指的是利用软件在计算机上建立各种各样的仪器,比如说LabVIEW,就象是真的建立在计算机上的仪器一样。
如何利用LabVIEW进行虚拟仪器设计和仿真

如何利用LabVIEW进行虚拟仪器设计和仿真利用LabVIEW进行虚拟仪器设计和仿真LabVIEW(Laboratory Virtual Instrument Engineering Workbench)是一种集数据采集、信号处理、仪器控制和虚拟仪器设计于一身的集成开发环境,广泛应用于各个领域的工程实验和测试中。
本文将介绍如何利用LabVIEW进行虚拟仪器设计和仿真,并提供一些实际案例来说明其应用价值。
一、LabVIEW介绍LabVIEW是由美国国家仪器公司(National Instruments, NI)于1986年推出的一种图形化编程语言。
与传统的文本编程语言相比,LabVIEW通过将函数块拖拽到界面上并进行连接来组成程序,使得程序的开发更加直观、易于理解。
LabVIEW提供了丰富的工具箱和函数库,可用于数据采集、信号处理、仪器控制和用户界面设计等方面。
二、虚拟仪器设计虚拟仪器是指利用计算机软件和硬件模拟真实仪器的功能。
利用LabVIEW可以轻松地设计各种虚拟仪器,如示波器、信号发生器、频谱分析仪等,用于实现数据采集和信号处理等功能。
LabVIEW提供了众多的仪器模拟器和控件,用户只需简单地拖拽和配置这些组件,即可实现一个功能完备的虚拟仪器。
三、虚拟仪器仿真利用LabVIEW进行虚拟仪器仿真可以帮助用户在设计阶段快速验证算法和性能,并且可以方便地进行多种参数的调整和测试。
LabVIEW提供了灵活且强大的仿真工具,用户可以根据需要配置仿真场景、定义仿真信号和操作流程,并通过动态调整参数和监测仿真结果来完成虚拟仪器的性能评估。
四、LabVIEW在工程实践中的应用1. 数据采集和处理利用LabVIEW可以方便地搭建数据采集系统,并通过各种传感器和硬件设备获取实时数据。
同时,LabVIEW提供了丰富的信号处理函数和算法,可以对采集的数据进行滤波、降噪、频谱分析等处理,从而提取出有效信息。
2. 仪器控制和自动化LabVIEW支持与各类仪器设备的通讯和控制,可以通过GPIB、USB、Ethernet等接口与仪器进行连接,并通过LabVIEW编写程序来实现仪器的自动化控制。
外文翻译(中文)-- 基于LabVIEW的直流电机及温度控制PID控制器
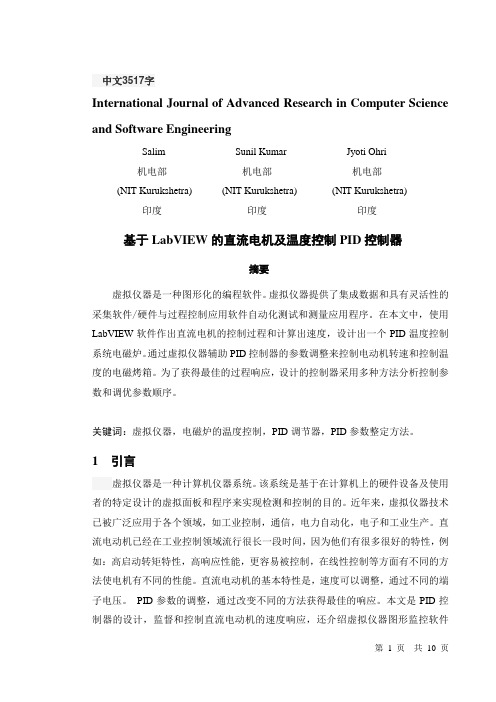
中文3517字International Journal of Advanced Research in Computer Science and Software EngineeringSalim Sunil Kumar Jyoti Ohri机电部机电部机电部(NIT Kurukshetra) (NIT Kurukshetra) (NIT Kurukshetra)印度印度印度基于LabVIEW的直流电机及温度控制PID控制器摘要虚拟仪器是一种图形化的编程软件。
虚拟仪器提供了集成数据和具有灵活性的采集软件/硬件与过程控制应用软件自动化测试和测量应用程序。
在本文中,使用LabVIEW软件作出直流电机的控制过程和计算出速度,设计出一个PID温度控制系统电磁炉。
通过虚拟仪器辅助PID控制器的参数调整来控制电动机转速和控制温度的电磁烤箱。
为了获得最佳的过程响应,设计的控制器采用多种方法分析控制参数和调优参数顺序。
关键词:虚拟仪器,电磁炉的温度控制,PID调节器,PID参数整定方法。
1 引言虚拟仪器是一种计算机仪器系统。
该系统是基于在计算机上的硬件设备及使用者的特定设计的虚拟面板和程序来实现检测和控制的目的。
近年来,虚拟仪器技术已被广泛应用于各个领域,如工业控制,通信,电力自动化,电子和工业生产。
直流电动机已经在工业控制领域流行很长一段时间,因为他们有很多很好的特性,例如:高启动转矩特性,高响应性能,更容易被控制,在线性控制等方面有不同的方法使电机有不同的性能。
直流电动机的基本特性是,速度可以调整,通过不同的端子电压。
PID参数的调整,通过改变不同的方法获得最佳的响应。
本文是PID控制器的设计,监督和控制直流电动机的速度响应,还介绍虚拟仪器图形监控软件LabVIEW 仿真,涉及监管控制系统的设计,建造和展示。
有很多算法/文学调谐的PID 控制器,如反应曲线,齐格勒尼科尔斯的方法,Tyreus Luyben 提出的方法。
基于LabVIEW的虚拟仪器设计实验
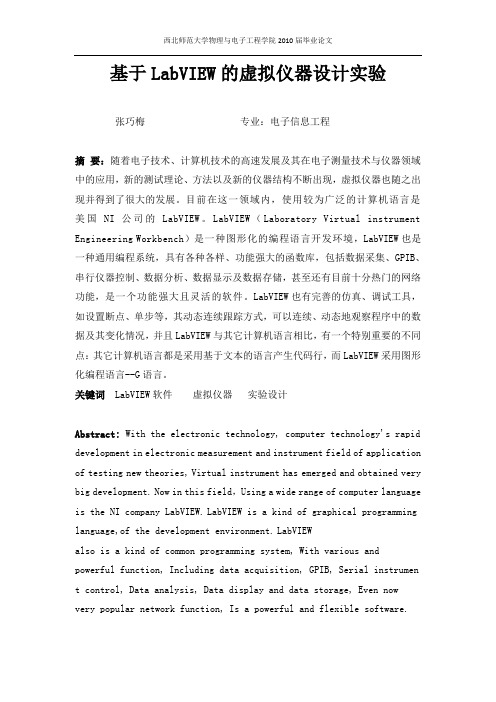
基于LabVIEW的虚拟仪器设计实验张巧梅专业:电子信息工程摘要:随着电子技术、计算机技术的高速发展及其在电子测量技术与仪器领域中的应用,新的测试理论、方法以及新的仪器结构不断出现,虚拟仪器也随之出现并得到了很大的发展。
目前在这一领域内,使用较为广泛的计算机语言是美国NI公司的LabVIEW。
LabVIEW(Laboratory Virtual instrument Engineering Workbench)是一种图形化的编程语言开发环境,LabVIEW也是一种通用编程系统,具有各种各样、功能强大的函数库,包括数据采集、GPIB、串行仪器控制、数据分析、数据显示及数据存储,甚至还有目前十分热门的网络功能,是一个功能强大且灵活的软件。
LabVIEW也有完善的仿真、调试工具,如设置断点、单步等,其动态连续跟踪方式,可以连续、动态地观察程序中的数据及其变化情况,并且LabVIEW与其它计算机语言相比,有一个特别重要的不同点:其它计算机语言都是采用基于文本的语言产生代码行,而LabVIEW采用图形化编程语言--G语言。
关键词 LabVIEW软件虚拟仪器实验设计Abstract: With the electronic technology, computer technology's rapid development in electronic measurement and instrument field of application of testing new theories,Virtual instrument has emerged and obtained very big development.Now in this field,Using a wide range of computer language is the NI company bVIEW is a kind of graphical programming language,of the development bVIEWalso is a kind of common programming system,With various and powerful function,Including data acquisition, GPIB,Serial instrumen t control,Data analysis,Data display and data storage,Even now very popular network function,Is a powerful and flexible software.LabVIEW also have simulation and Debugging tools.If set breakpoint and Single-step etc.The dynamic continuosly,Can continuously and dynamic observations of the data and programs.And with other computer language LabVIEW have a particularly important difference: Other computer language is based on the text of the language code, but LabVIEW using graphical programming language - G language. Keywords: LabVIEW Software Virtual instrument Experiment目录引言 (4)1.虚拟仪器系统概述 (4)1.1.虚拟仪器概念 (4)1.2.虚拟仪器的特点 (4)1.3.虚拟仪器的分类 (5)1.4.虚拟仪器的软件开发环境 (5)2.图形化编程语言LabVIEW (5)2.1.LabVIEW概述 (5)2.2.LabVIEW的使用 (6)3.LabVIEW虚拟仪器实验 (7)3.1.一个虚拟温度报警器 (7)3.1.1.此实验的前面板设置 (7)3.1.2.此实验的程序框设置 (7)3.1.3.结果演示 (13)3.2.一个虚拟示波器 (14)3.2.1.前面板设置 (14)3.2.2.函数程序框图 (19)3.2.3.演示结果 (21)3.3.一个虚拟滤波器 (23)3.3.1.前面板设置 (23)3.3.2程序框设计 (23)3.3.3.运行结果: (25)结束语 (26)参考文献 (27)引言虚拟仪器是基于计算机的软硬件测试平台,它可代替传统的测量仪器,如示波器,逻辑分析仪,信号发生器,频谱分析仪等;可集成于自动控制,工业控制系统;可自由构建成专有仪器系统。
LABVIEW虚拟仪器设计与应用
LABVIEW虚拟仪器设计与应用LabVIEW(Laboratory Virtual Instrument Engineering Workbench)是一款由美国国家仪器公司(National Instruments)开发的虚拟仪器设计与应用软件。
LabVIEW通过图形化的方式实现了虚拟仪器的设计与控制,简化了仪器的编程和控制过程,广泛应用于科研、工业自动化、教育等领域。
LabVIEW的主要特点是使用图形化的编程语言G(Graphical)语言来编写程序。
G语言以图形化的方式表示程序的流程,通过连接各种函数模块实现数据处理、传输、显示等功能。
相较于传统的文本化编程语言,G语言更加直观、易理解,使得用户可以更快地完成程序的编写。
LabVIEW具有丰富的虚拟仪器库,用户可以根据自己的需要选择不同类型的仪器模块,进行自定义的仪器设计。
LabVIEW支持常见的硬件设备,如数字采集卡、信号发生器、示波器等,通过与硬件设备的连接,实现对仪器的控制和数据的采集。
虚拟仪器设计是LabVIEW的重要应用之一、通过LabVIEW,用户可以设计出具有完整功能的虚拟仪器界面,实时采集和处理数据,并进行结果的显示和分析。
虚拟仪器设计不仅提高了实验的可重复性和准确性,还大大降低了实验设备的成本,简化了实验的操作流程。
另外,LabVIEW也可以用于工业自动化领域,为工业过程提供可视化的控制界面。
用户可以根据实际需求,使用LabVIEW设计出各种控制算法和界面,实现对工业设备的自动控制和监测。
LabVIEW支持与PLC、传感器和执行器等硬件设备的连接,使得系统的控制更加便捷和灵活。
在教育领域,LabVIEW可以用于教学实验的设计和实施。
通过LabVIEW,教师可以设计出具有交互性和实时性的教学实验界面,帮助学生更好地理解和掌握实验原理和方法。
同时,LabVIEW的图形化编程语言也降低了学习的门槛,对于初学者来说更易于上手。
综上所述,LabVIEW是一款功能强大、应用广泛的虚拟仪器设计与应用软件。
Labview虚拟仪器外文文献及翻译
Labview (虚拟仪器)Abstract:摘要Labview is a highly productive graphical programming language for building data acquisition and instrumentation systems. With Labview , you quickly create user interfaces that give you interactive control of your software system .To specify your system functionality , you simply assemble block diagrams---a natural design notation for scientists and engineers .Its tight integration with measurement hardware facilitates rapid development of data acquisition ,analysis ,and a graphical compiler for optimum performance .Labview is available for Windows 2000/NT/Me/9x,Mac OS,Linux ,Sun Solaries , and HP-UX , and comes in three different development system options.虚拟仪器是一种高性能的用于建立数据采集和仪器检测系统的图形编辑语言。
在虚拟仪器的使用中,你可以快速建立让你交互式控制你的软件系统的用户界面.在要指定你的系统功能时,你只需要装配框图——一种针对科学家和工程师的自然的设计表示法。
它的硬件测量的紧密集成促进了数据采集,分析和图形化编译最佳性能的发展。
Labview图形化编程语言中英文对照外文翻译文献
Labview图形化编程语⾔中英⽂对照外⽂翻译⽂献中英⽂资料外⽂翻译National Instruments LabVIEW: A Programming Environment for Laboratory Automation and Measurement .National Instruments LabVIEW is a graphical programming language that has its roots in automation control and data acquisition. Its graphical representation, similar to a process flow diagram, was created to provide an intuitive programming environment for scientists and engineers. The language has matured over the last 20 years to become a general purpose programming environment. LabVIEW has several key features which make it a good choice in an automation environment. These include simple network communication, turnkey implementation of common communication protocols (RS232, GPIB, etc.), powerful toolsets for process control and data fitting, fast and easy user interface construction, and an efficient code execution environment. We discuss the merits of the language and provide an example application suite written in-house which is used in integrating and controlling automation platforms.Keywords: NI LabVIEW; graphical programming; system integration; instrument control; component based architecture; robotics; automation; static scheduling; dynamic scheduling; databaseIntroductionCytokinetics is a biopharmaceutical company focused on the discovery of small molecule therapeutics that target the cytoskeleton. Since inception we have developed a robust technology infrastructure to support our drug discovery efforts. The infrastructure provides capacity to screen millions of compounds per year in tests ranging from multiprotein biochemical assays that mimic biological function to automated image-based cellular assays with phenotypic readouts. The requirements for processing these numbers and diversity of assays have mandated deployment of multiple integrated automation systems. For example, we have several platforms for biochemical screening, systems for live cell processing, automated microscopy systems, and an automated compound storage and retrieval system. Each in-house integrated system is designed around a robotic arm and contains an optimal set of plate-processing peripherals (such as pipetting devices, plate readers, and carousels) depending on its intended range of use. To create the most flexible, high performance, and cost-effective systems, we have taken the approach of building our own systems in-house. This has given us the ability to integrate the most appropriate hardware and software solutions regardless of whether they are purchased from a vendor or engineered de novo, and hence we can rapidly modify systems as assay requirements change.To maximize platform consistency and modularity, each of our 10 automated platforms is controlled by a common, distributed application suite that we developed using National Instruments (NI) LabVIEW. This application suite described in detail below, enables our end users to create and manage their own process models (assayscripts) in a common modeling environment, to use these process models on any automation system with the required devices, and allows easy and rapid device reconfiguration. The platform is supported by a central Oracle database and can run either statically or dynamically scheduled processes.NI LabVIEW BackgroundLabVIEW, which stands for Laboratory Virtual Instrumentation Engineering Workbench is a graphical programming language first released in 1986 by National Instruments (Austin, TX). LabVIEW implements a dataflow paradigm in which the code is not written, but rather drawn or represented graphically similar to a flowchart diagram Program execution follows connector wires linking processing nodes together. Each function or routine is stored as a virtual instrument (VI) having three main components: the front panel which is essentially a form containing inputs and controls and can be displayed at run time, a block diagram where the code is edited and represented graphically, and a connector pane which serves as an interface to the VI when it is imbedded as a sub-VI.The top panel (A) shows the front panel of the VI. Input data are passed through “Controls” which are shown to the left. Included here are number inputs, a file path box, and a general error propagation cluster. When the VI runs, the “Indicator”outputs on the right of the panel are populated with output data. In this example, data include numbers (both as scalar and array), a graph, and the output of the error cluster. In the bottom panel (B) the block diagram for the VI is shown. The outer case structure executes in the “No Error” case (VIs can make internal errors o r if called as a sub-VI the caller may propagate an error through the connector pane).Unlike most programming languages, LabVIEW compiles code as it is created thereby providing immediate syntactic and semantic feedback and reducing the time required for development and testing.2Writing code is as simple as dragging and droppingfunctions or VIs from a functions palette onto the block diagram within process structures (such as For Loops, or Case Structures) and wiring terminals (passing input values, or references). Unit testing is simplified because each function is separately encapsulated; input values can be set directly on the front panel without having to test the containing module or create a separate test harness. The functions that generate data take care of managing the storage for the data.NI LabVIEW supports multithreaded application design and executes code in an inherently parallel rather than sequential manner; as soon as a function or sub-VI receives all of its required inputs, it can begin execution. In Figure 1b, all the sub-VIs receive the array input simultaneously as soon as the For Loop is complete, and thus they execute in parallel. This is unique from a typical text-based environment where the control flows line by line within a function. When sequential execution is required, control flow can be enforced by use of structures such as Sequences, Events, or by chaining sub-VIs where output data from one VI is passed to the input of the next VI.Similar to most programming languages, LabVIEW supports all common data types such as integers, floats, strings, and clusters (structures) and can readily interface with external libraries, ActiveX components, and .NET framework. As shown in Figure 1b, each data type is graphically represented by wires of different colors and thickness. LabVIEW also supports common configuration management applications such as Visual SourceSafe making multideveloper projects reasonable to manage.Applications may be compiled as executables or as Dynamic Link Libraries (DLLs) that execute using a run-time engine similar to the Java Runtime Environment. The development environment provides a variety of debugging tools such as break-points, trace (trace), and single-step. Applications can be developed using a variety of design patterns such as Client-Server, Consumer-Producer, andState-Machine. There are also UML (Unified Modeling Language) modeling tools that allow automated generation of code from UML diagrams and state diagrams.Over the years, LabVIEW has matured into a general purpose programming language with a wider user base.NI LabVIEW as a Platform for Automation and InstrumentationOur experience creating benchtop instrumentation and integrated automation systems has validated our choice of LabVIEW as an appropriate tool. LabVIEW enables rapid development of functionally rich applications appropriate for both benchtop applications and larger integrated systems. On many occasions we have found that project requirements are initially ill defined or change as new measurements or new assays are developed.. There are several key features of the language that make it particularly useful in an automation environment for creating applications to control and integrate instrumentation, manage process flow, and enable data acquisition.Turnkey Measurement and Control FunctionLabVIEW was originally developed for scientists and engineers .The language includes a rich set of process control and data analysis functions as well as COM, .NET, and shared DLL support. Out of the box, it provides turnkey solutions to a variety of communication protocols including RS232, GPIB, and TCP/IP. Control structures such as timed While Loops allow synchronized and timed data acquisition from a variety of hardware interfaces such as PCI, USB, and PXI. DataSocket and VI ServerDeployment of an integrated system with multiple control computers requires the automation control application to communicate remotely with instrument drivers existing on remote computers. LabVIEW supports a distributed architecture by virtue of enabling seamless network communication through technologies such as VI Server and DSTP (data sockets transfer protocol). DSTP is an application layer protocol similar to http based on Transmission Control Protocol/Internet Protocol (TCP/IP). Data sockets allow easy transfer of data between remote computers with basic read and write functions. Through VI server technology, function calls can be made to VIs residing on remote computers as though they are residing on the local computer. Both Datasockets and VI server can be configured to control accesses privileges.Simple User Interface (UI) ImplementationIn addition to common interface controls such as text boxes, menu rings, and check-boxes, LabVIEW provides a rich set of UI controls (switches, LEDs, gauges, array controls, etc.) that are pertinent to laboratory equipment. These have their origins in LabVIEWs laboratory roots and help in development of interfaces which give scientists a clear understanding of a system's state. LabVIEW supports UI concepts including subpanels (similar to the Multiple Document Interface), splitter bars, and XControls (analogous to OCX controls).Multithreaded Programming EnvironmentThe inherent parallel environment of LabVIEW is extremely useful in the control of laboratory equipment. Functions can have multiple continuous While Loops where one loop is acquiring data rapidly and the other loop processes the data at a much slower rate. Implementing such a paradigm in other languages requires triggering an independent function thread for each process and developing logic to manage synchronization. Through timed While Loops, multiple independent While Loops can be easily synchronized to process at a desired period and phase relative to one another. LabVIEW allows invoking multiple instances of the same function witheach maintaining its own data space. For instance, we could drag many instances of the Mean sub-VI onto the block diagramin Figure 1b and they would all run in parallel, independent of one another. To synchronize or enforce control flow within the dataflow environment, LabVIEW also provides functions such as queues, semaphores, and notification functions.NI LabVIEW Application Example: The Open System Control Architecture (OSCAR)OSCAR is a LabVIEW-based (v7.1) automation integration framework and task execution engine designed and implemented at Cytokinetics to support application development for systems requiring robotic task management. OSCAR is organized around a centralized Oracle database which stores all instrumentation configuration information used to logically group devices together to create integrated systems (Fig. 2). The database also maintains Process Model information from which tasks and parameters required to run a particular process on a system can be generated and stored to the database. When a job is started, task order and parameter data are polled by the Execution Engine which marshals tasks to each device and updates task status in the database in real time. Maintaining and persisting task information for each system has two clear benefits. It allows easy job recovery in the event of a system error, and it also provides a process audit trail that can be useful for quality management and for troubleshooting process errors or problems.Each OSCAR component is distributed across the company intranet and communicates with a central database. Collections of physical devices controlled through OSCAR Instrument packages (OIP) make up systems. Users interact with systems through one of the several applications built on OSCAR. Each application calls the RTM which marshals tasks from the database to each OIP. OSCAR has sets of tools for managing system configurations, creating Process Models, monitoring running processes, recovering error-state systems, and managing plate inventory in storage devices.OSCAR uses a loosely coupled distributed component architecture, enabled in large part by LabVIEWs DSTP and remote VI technologies that allow system control to be extended beyond the confines of the traditional central control CPU model. Any networked computer or device can be integrated and controlled in an OSCAR system regardless of its physical location. This removes the proximity constraints of traditional integrated systems and allows for the utilization of remote data crunchers, devices, or even systems. The messaging paradigm used shares many similarities with current Service Oriented Architectures or Enterprise Service Bus implementations without a lot of required programming overhead or middleware; a centralized server is not required to direct the XML packets across the network. An additional benefit to this loosely coupled architecture is the flexibility in front-end application design. OSCAR encapsulates and manages all functionality related to task execution and device control, which frees the developer to focus on the unique requirements of a given application. For example, an application being created for the purpose of compound storage and retrieval can be limited in scope to requirements such as inventory management and LIMS integration rather than device control, resource allocation, and task synchronization.The OSCAR integration framework consists of multiple components that enable device and system configuration, process modeling, process execution, and process monitoring. Below are descriptions of key components of the framework. Integration PlatformThe Oscar Instrument Package (OIP) is the low level control component responsible for communicating with individual devices. It can support any number of devices on a system (including multiple independent instances of the same type of device) and communicates to the Runtime Manager (RTM) via serialized XMLstrings over DSTP. This allows the device controller and RTM components to exist on separate networked computers if necessary. Additionally, the OIP controller communicates with a device instance via LabVIEW remote VI calls which provide a lower level of distribution and allow the device drivers to exist on a separate networked computer from the controller. At Cytokinetics, we currently support approximately 100 device instances of 30 device types which are distributed across 10 integrated systems.System ManagementAn OSCAR system is a named collection of device instances which is logically represented in the database. The interface for each device (commands and parameters) is stored in the database along with the configuration settings for each device instance (i.e., COM port, capacity). The System Manager component provides the functionality to easily manipulate this information (given appropriate permissions). When a physical device is moved from one system to another, or a processing bottleneck alleviated by addition of another similar device, system configuration information is changed without affecting the processes that may be run on the system.Process ModelingA process model is the logical progression of a sequence of tasks. For example, a biochemical assay might include the following steps (1) remove plate from incubator, (2) move plate to pipettor, (3) add reagent, (4) move plate to fluorescent reader, (5) read plate, and (6) move plate to waste. The Process Modeler component allows the end user to choose functions associated with devices and organize them into a sequence of logical tasks. The resulting process model is then scheduled via a static schedule optimization algorithm or saved for dynamic execution (Fig. 3). Aprocess model is not associated with a physical system, but rather a required collection of devices. This has two importantbenefits: (1) the scientist is free to experiment with virtual system configurations to optimize the design of a future system or the reconfiguration of an existing system, and (2) any existing process model can be executed on any system equipped with the appropriate resources.The top panel (A) shows the Process Schedule Modeler, an application that graphically displays statically scheduled processes. Each horizontal band represents a task group which is the collection of required tasks used by a process; tasks are color coded by device. The bottom panel (B) shows the UI from the Automated Imaging System application. The tree structure depicts the job hierarchy for an imaging run. Jobs (here AIS_Retrieval and AIS_Imaging) are composed of task groups. As the systems runs, the tasks in the task group are executed and their status is updated in the database.Process ExecutionProcess execution occurs by invoking the OSCAR RTM. The RTM is capable of running multiple differing processes on a system at the same time allowing multiple job types to be run in parallel. The RTM has an application programming interface (API) which allows external applications to invoke its functionality and consists of two main components, the Task Generator Module (TGM) and the Execution Engine. External applications invoke an instance of a Process Model through the TGM at which point a set of tasks and task parameters are populated in the OSCAR database. The Execution Engine continually monitors the database for valid tasks and if a valid task is found it is sent to the appropriate device via the OIP. The OSCAR system supports running these jobs in either a static or dynamic mode. For processes which must meet strict time constraints (often due to assay requirements), or require the availability of a given resource, a static schedule is calculated and stored for reuse.The system is capable of optimizing the schedule based on actual task operation times (stored in the database).Other types of unconstrained processes benefit more from a dynamic mode of operation where events trigger the progress of task execution as resources become available in real-time. When operating dynamically, intelligent queuing of tasks among multiple jobs allows optimal use of resources minimizing execution time while allowing for robust error handling.Process MonitoringAll systems and jobs can be monitored remotely by a distributed application known as the Process Monitor. This application allows multiple users to monitor active jobs across all systems for status and faults and provides email notification for fault situations.ConclusionCytokinetics has built and maintains an automation software infrastructure using NI LabVIEW. The language has proven to be a powerful tool to create both rapid prototype applications as well as an entire framework for system integration and process execution. LabVIEW's roots in measurement instrumentation and seamless network communication protocols have allowed systems to be deployed containing multiple control computers linked only via the network. The language continues to evolve and improve as a general purpose programming language and develop a broad user base.。
LabVIEW中的虚拟仪器设计和开发
LabVIEW中的虚拟仪器设计和开发LabVIEW(Laboratory Virtual Instrument Engineering Workbench)是一款由国家仪器公司(National Instruments)开发的图形化编程平台,用于虚拟仪器设计和开发。
本文将介绍LabVIEW中的虚拟仪器设计和开发的基本原理、应用场景以及开发流程。
一、LabVIEW虚拟仪器设计的基本原理在LabVIEW中,虚拟仪器是由各种测量和控制模块组成的图形化程序,它们模拟了真实世界中的各种仪器和设备。
LabVIEW通过将这些模块连接起来形成数据流图(Dataflow Diagram),实现了虚拟仪器的设计和开发。
虚拟仪器的设计和开发过程中,首先需要选择和配置合适的模块,例如传感器、数据采集卡、执行器等。
然后利用LabVIEW提供的各种模块库,通过简单的拖拽、连接和配置,实现虚拟仪器中各个模块之间的功能关联。
LabVIEW的编程语言是一种图形化语言,称为G语言(G-language)。
用户可以使用G语言来编写虚拟仪器的程序,利用各个模块的输入和输出来实现数据采集、信号处理、控制执行等功能。
G语言的编程方法与传统的文本编程语言有所不同,它更加直观、易于理解,即使是对于没有编程经验的用户也能够很快上手。
二、LabVIEW虚拟仪器设计的应用场景LabVIEW的虚拟仪器设计和开发广泛应用于各个领域的科学研究、工程实验和生产制造等环节。
以下是几个典型的应用场景:1. 科学实验室:LabVIEW可以用于设计和开发各种科学实验的虚拟仪器,例如物理实验、化学实验、生物实验等。
通过LabVIEW可以实现实时数据采集、信号处理、曲线绘制、数据分析等功能,帮助科学家和研究人员更好地进行实验和研究工作。
2. 工程测试:LabVIEW可以作为工程测试的核心工具,用于开发各种测试仪器的虚拟化解决方案。
它支持多种通信协议和接口,可以与各种传感器、仪器和设备进行数据交互。
- 1、下载文档前请自行甄别文档内容的完整性,平台不提供额外的编辑、内容补充、找答案等附加服务。
- 2、"仅部分预览"的文档,不可在线预览部分如存在完整性等问题,可反馈申请退款(可完整预览的文档不适用该条件!)。
- 3、如文档侵犯您的权益,请联系客服反馈,我们会尽快为您处理(人工客服工作时间:9:00-18:30)。
基于LabVIEW的虚拟仪器模拟风力太阳能系统混合动力站(节选)介绍在最简单的层面上,数据采集可以手动完成如使用纸笔记录读数或任何其他工具。
对于某些应用这种形式的数据采集是足够的。
然而,数据记录中的应用这需要大量的数据读数,非常频繁的录音是有必要的,它包括了仪器或微控制器获取和记录数据准确(1995里格比和多尔比,)。
急诊化验室虚拟仪器工程平台(LabVIEW)是一个功能强大的灵活的仪器仪表和分析应用软件工具,(美国国家仪器仪表,2002)在今天这新兴技术并被广泛采用的学术界,工业LabVIEW已成为一个重要的工具,已代替了政府实验室数据的标准采集,仪器控制和分析软件。
现有的1.5千瓦的额定风力太阳能混合动力站显示(图1)。
设计与施工的可再生能源发电系统报告(磐诚,等铝,2000)。
在大学校园的平台上,有良好的教育机会本科生和研究生以现有的风力太阳能知识,学生们在协同研究基于风力太阳能发电站的传统的电网火力发电厂。
特别是在一些组件可再生能源如蓄电池和直流电源逆变器,可导致供电质量和电网出现一些问题,当太阳风稳定性出现问题时,根据汽轮机和发电机(帕特尔,1999)的电力系统与化石燃料这些相互作用都是由于大量的不同动力学参与的风力涡轮机和蒸汽涡轮机。
图1显示了photovol TAIC(PV)与太阳能电池板120个W评级,mastmounted1千瓦的风力涡轮机,和风速计,包括风方向和速度传感器的风能太阳能发电站并行运作,并收取12 V电池组包括六个深循环铅酸电池。
太阳面板安装在机架上的轨道,白天太阳光从320个0度的初始位置度。
该系统还包括基于固态器件的一个1.5kVA额定直流到交流电源逆变器,保护设备如交流和直流电路断路器,熔断器,避雷器,一套线性和非线性负载,连接电缆,和接线盒。
在国家的电压和电流系统学生们介绍了稳定的研究,说明了电能质量由于小的线性和非线性负荷的影响(磐诚和蒂默曼,1999)。
太阳风混合发电站已被用来作为大学本科电气部分电力和机械实验室内容以及示范单位高中和社区访问大学生(磐诚,等,2003)。
虽然电力系统和项目的可再生能源的内容有助于可再生能源的教学现实世界的应用,计算机辅助测量和数据采集模块的缺乏阻碍我们发展状态的艺术监控数据处理系统1999。
本文将主要集中在最近完成的LabVIEW监测和处理后系统的状态变量为基础的数据采集模块:直流电压,直流电流,交流电压,交流电流,风速,风向,直流电源,从现有的风力太阳能发电站的交流电源。
该仪器系统提供了一个机会,获得美国国家仪器实践经验的学生(Ni)的数据采集硬件,和LabVIEW软件版本6i的直流电压,直流电流的实时监测,风速,风向,DC和AC电源波形。
该项目的其他最有用的好处包括学生接口设备如电压和电流传感器在交流和直流侧,并使用隔离放大器之间的传感器输出和输入电脑。
该系统不仅被用于数据采集和仪器控制应用,而且对于一般用途的应用如数据库开发,数据分析程序,网络通信。
例如,计算机执行的风光互补发电系统的实时虚拟仪器网络化对高校的服务器,并可以访问任何校园远程计算机通过网络进行实时监控的目的。
校友调查的毕业生近15年覆盖完成2001夏季大学工业技术部。
调查工具被送往120校友参与其各自公司的机电/电子系统。
完成的调查数据从70(的目标组58.33%)和58(占82.86%的受访者)的人表示,雇主宁愿雇用与模拟或数字数据采集工作知识的毕业生,分析和解释。
他们还表明,一个有能力制定一系列其他问题的解决方案,以及机电和电子系统的特定的计算机素养是一个加号。
测量仪器是不包括在本文。
工业咨询委员会成员的工业技术部在2003学年也显示数据采集技能的员工的必要性。
因此,在LabVIEW仪表系统将帮助学生发展中的数据采集技术,分析。
计算机辅助测量和风接口—太阳能发电系统目的是将六个实验变量:直流电压,直流电流,交流电压,交流电流,风速,风向成计算机可读的存储和显示,实时的结果。
直流电源和交流电源需要计算和通过其他预定的变量使用LabVIEW的编程能力监测。
信号调理硬件条件和隔离电压和风信息信号之前被连接到数据采集板将在整体系统的虚拟仪器发挥重要作用。
风的太阳能发电站的仪器相包括下列硬件:cr4110-10真有效值交流电流传感器和一个cr5210 50直流霍尔效应电流传感器从CR磁,电压和电流分配器和缩放电路,一个风监测装置称为风速仪,LabVIEW 6i专业开发系统为Windows NT/98,pci-6071e I / O板,一个DAQ驱动软件,一个SH 100100屏蔽电缆,SCSI - II的连接器,一个scb-100屏蔽连接器块,一个隔离放大器电路,和一个PC。
用示波器检查模拟信号也将是非常有用的。
图2说明了整个仪表系统的框图。
四太阳能电池板和风力发电机产生的直流电压被施加到电池组。
一个年轻的05103v风速计提供两个电压信号对应的风向和风速值。
这些风的信号被馈送到ad21oan隔离放大器和输出应用到国家仪器的scb-100数据采集(DAQ)。
两个电压信号,一个从电池输出和一个来自逆变器的输出也适用于隔离放大器通过其相应的电压缩放电路。
两个电流信号,一个来自电池的输出通过一个直流霍尔效应电流传感器,和其他从逆变器的输出通过一个真有效值交流电流传感器直接输入到数据采集板。
CR 5210-50直流霍尔电流传感器可以提供0 - 5 V直流输入0-50直流电流。
同样,Cr 4110-10交流电流传感器可以提供一个信号输入为一个AC。
图3电流0~5伏直流描绘的逆变器和交流负载银行,包括奔腾III计算机,各种高效节能荧光灯,白炽灯等,一个电加热器,和一个风扇。
的交流负载的总功率约1400 W的仪器系统主要利用电脑的电源是由风能和太阳能混合动力系统提供的。
在实际的范围视图显示波形的预处理信号,需要适当的校准使用算术或逻辑功能期货可在LabVIEW?图6描述了为下午5:15到32 PM时间段的数据采集VI前面板。
如图7所示,直流电源具有值241.97当交流电源具有值238.65W的差对应的损失通过逆变器。
发电和相应的监测值增加至1500 W在充分的阳光和/或风力条件。
风向为逆时针从北。
5.2英里每小时的平均风速记录在6:25 PM时间6:26 PM。
阅读每分钟数可以通过调色板在前面板上显示IntroductionAt the simplest level, data acquisition can be accomplished manually using paper and pencil, recording readings from a multimeter or any other instrument. For some applications this form of data acquisition may be adequate. However , data recording applications that require large number of data readings where very frequent recordings are necessary must include instruments or microcontrollers to acquire and record data precisely (Rigby and Dalby, 1995). Lab oratory V irtual I nstrument Engineering W orkbench (LabView™) is a powerful and flexible instrumentation and analysis software application tool which was developed in 1986 by the National Instruments (National Instruments, 2002). LabView™ has become a vital tool in today’s emerging technologies and widely adopted throughout academia, industry, and government laboratories as the standard for data acquisition, instrument control and analysis software.An existing 1.5 kW rated wind-solar hybrid power station is shown in Figure 1. The design and construction of the renewable energy based power system was reported earlier (Pecen, et al., 2000). The existing wind-solar testbed at UNI campus has been an excellent educational opportunity for undergraduate and graduate students to study complex interactions in the electrical power grid between conventional coal-fired power plants and wind-solar based power stations.Particularly some components in the renewable energy plants such as batteries and dc-to-ac power inverters can lead to power quality and grid stability problems when wind-solar power systems are tied to fossil-fuel based turbine and generators (Patel, 1999). These interactions are mostlydue to the vast dynamics differences involved in wind turbines and steam turbines. Figure 1 shows four Photovoltaic (PV) solar panels with a power rating of 120 W for each, one mastmountedwind turbine with 1 kW, and an anemometer that includes a wind direction and a speed sensor. The hybrid wind-solar power station operates in parallel, and charges a 12 V battery bank which includes six deep cycle lead acid batteries. The solar panels are installed on a frame whichtracks the sun light during the day from an initial position of 0 degree to 320 degree. The system also includes a 1.5kVA rated dc-to-ac power inverter based on solid-state devices, protectionequipment such as ac and dc circuit breakers, fuses, surge arrester, a set of linear and non-linear loads, connecting cables, and junction boxes. Students are introduced to the studies of steady state voltage and currents in the system, illustrating power quality problems due to small linear and nonlinear load effects (Pecen and Timmerman, 1999). The wind-solar hybrid power station has been used as part of the undergraduate electrical power and machinery laboratory content as well as a demonstration unit for visiting high school and community college students (Pecen, et al., 2003).Although the power system and renewable energy content of the project have helped in teaching real-world applications of the renewable energy, the lack of computer aided instrumentation and data acquisition modules prevented us from developing a stateof-the-art data monitoring and processing system in 1999. This paper will focus mainly on recently completed LabView™ based data acquisition module for monitoring and processing the following system state variables: dcvoltage, dc current, ac voltage, ac current, wind speed, wind direction, dc power, and ac power from the existing wind-solar power station.The instrumentation system provides students with an opportunity to gain practical experience on National Instruments (NI) data acquisition hardware, and the LabView™ Version 6i software for the real-time monitoring of dc voltage, dc current, wind speed, wind direction, dc and ac power waveforms. Other most useful benefits of the project include the students’ ability to interface devices such as voltage and current sensors on both ac and dc sides, and the use of isolation amplifiers between sensor outputs and computer inputs. The developed system has not only been used for data acquisition and instrument control applications, but also for general purpose applications such as database development, data analysis programs, and network communications. For example, the computer executing the real-time virtual instrumentation of the windsolar power system is networked to the university server, and can be accessed by any remote computer on campus through the network for real-time monitoring purposes.An alumni survey covering last 15 year of graduates was completed in summer 2001 in the Department of Industrial Technology at UNI. The survey instrument was sent to 120 alumni who are involved in electromechanical/electronic systems of their respective companies. The completed survey data was obtained from 70 (58.33% of the targeted group) and 58 (82.86% of total respondents) of them indicated that employers prefer hiring of graduates with a working knowledge of analog or digital data acquisition, analysis and interpretation. They have also indicated that an ability to formulate a range of alternative problem solutions, and computer literacy specific to electromechanical and electronic systems is a plus. Survey instrument is not included in this paper. Industrial advisory board members of the Industrial Technology Department during the academic year of 2002-2003 have also indicated the necessity of data acquisition skills for their prospective employees. Thus, this LabView™instrumentation system will help the students to develop skills in data acquisition, and analysis.Computer Aided Instrumentation and Interface of the Wind-Solar Power SystemThe objective is to transform the six experimental variables: DC voltage, DC current, AC voltage, AC current, wind speed, and wind direction into a form readable by the computer, display and store the results in real time . The DC power and AC power need to be calculated and monitored through the other predetermined variables using LabView’s programming capabilities. The signal conditioning hardware to condition and isolate the voltage and wind information signals before being connected to the DAQ board will play a significant role in the virtual instrumentation of the overall system. The instrumentation phase of the wind-solar power station includes the following hardware: One CR4110-10 True RMS AC Current Transducer and one CR5210- 50 DC Hall-Effect Current Transducer from CR Magnetics, voltage and current divider and scaling circuits, one wind monitoring device called anemometer, a LabView 6i Professional Development System for Windows NT/98, one PCI-6071E I/O Board, one NI-DAQ Driver Software, one SH 100100 Shielded Cable, SCSI-II Connectors, one SCB-100 Shielded Connector Block, one isolation amplifier circuit, and a PC. A DMM and an oscilloscope to check the analog signals would also be very useful. Figure 2 illustrates a block diagram of the overall instrumentation system. DC voltage generated by four solar panels and one wind generator is applied to the battery bank.A Young 05103V Anemometer provides two voltage signals corresponding to wind speed and wind direction values. These wind signals are fed to AD21OAN Isolation Amplifiers and the output is applied to National Instrument’s SCB-100 Data Acquisition Board (DAQ). Two voltage signals, one from battery output and one from inverter output are also applied to isolation amplifiers through their corresponding voltage divider-scaling circuits. Two current signals, one from battery output through a DC Hall-Effect current transducer, and the other from inverter output through one true rms AC current transducer are fed directly to the DAQ board. The CR 5210-50 DC Halleffect current transducer may provide 0- 5.0 V DC for an input current of 0-50 A DC. Similarly, the CR 4110-10 AC current transducer may provide a signal of 0-5 V DC for an input current of 0-10 A AC. Figure 3 depicts the inverter and AC load bank which includes a Pentium III computer, a variety of energy efficient fluorescent lights, several incandescent lights, one electrical heater, and a fan. The total power rating of the AC loads is about 1400 W. The instrumentation system basically uses a computer whose power is supplied by wind and solar hybrid system.To view the displayed waveforms in actual ranges, the preconditioned signals require appropriate calibration using the arithmetic and/or logic function futures available in LabView™ Figure 6 depicts the front panel of the data acquisition VI for the time period of 5:15 pm to 5:32 pm. As seen in Figure 7, the DC power has a value of 241.97 W while the AC power has a value of 238.65 W. The difference corresponds to losses through the inverter. The power generation and corresponding monitoring values increase up to 1500 W during full sun and/or wind conditions. The wind direction is shown as counter clock wise from north. An average wind speed of 5.2 mph was recorded during the time period of 6:25 pm to 6:26 pm. The number of readings per minute can be adjusted through the palette as shown in the front panel.。