(工艺技术)2020年检试验工艺规程
(工艺技术)2020年无损检测通用工艺规程

无损检测通用工艺规程编制:审核:批准:日期:目录第1章编制说明 (3)第2章射线检测通用工艺规程 (5)第3章超声波检测通用工艺规程 (21)第1节承压设备对接焊接接头超声检测及质量分级 (24)第2节承压设备钢板超声检测及质量分级 (29)第3节承压设备用钢锻件超声检测及质量分级 (32)第4章磁粉检测通用工艺规程 (35)第5章渗透检测通用工艺规程 (39)第6章工艺卡附表 (44)第1节射线检测工艺卡 (44)第2节超声检测工艺卡 (45)第3节磁粉检测工艺卡 (46)第4节渗透检测工艺卡 (47)第一章编制说明1.1 范围本规程规定了对金属原材料、零部件和焊接接头进行射线检测、超声检测、磁粉检测、渗透检测的基本要求。
本规程适用于本公司钢制压力容器产品的无损检测工作。
1.2 引用标准和编制依据下列标准包含的条文,通过在本规程中引用而构成本规程的条文,在规程出版时,所有版本均为有效。
所有标准都会被修订,使用本规程的各方应探讨使用下列标准最新版本的可能性。
压力容器安全技术监察规程(1999年版)GB150-1998 《钢制压力容器》GB151-1999 《管壳式换热器》JB/T4730.1~4730.6-2005 《承压设备无损检测》《特种设备无损检测人员资格考核实施细则》《放射卫生防护基本标准》Q/JS.YLRQ--2008《质量保证手册》1.3 人员资格及职责1.3.1从事无损检测的人员必须持有国家质量监察机构颁发的并与其工作相适应的资格等级证书。
1.3.2从事无损检测的人员校正视力不得低于5.0,从事磁粉、渗透检测工作人员,不得有色盲、色弱。
1.3.3检测人员严格执行有关条例、规程、标准和技术规范,保证工作质量。
1.3.4评片人员的视力应每年检查一次,要求距离400mm能读出0.5mm的一组印刷体字母。
1.3.5检测操作人员必须按委托单要求并同时根据检测工艺规程进行操作,做好检测记录及签发检测报告。
检验技术操作规程
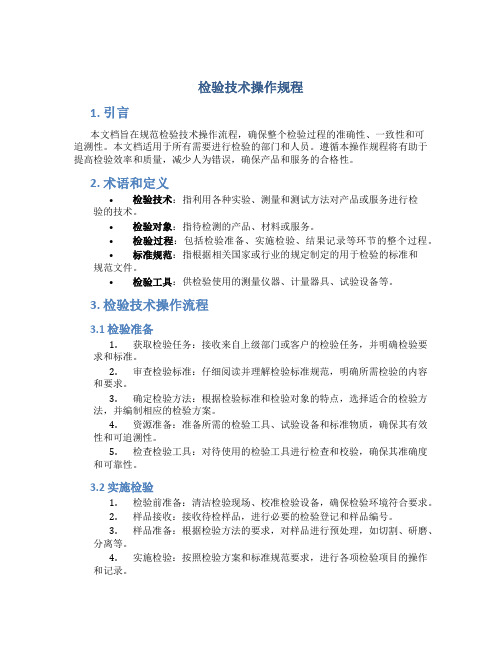
检验技术操作规程1. 引言本文档旨在规范检验技术操作流程,确保整个检验过程的准确性、一致性和可追溯性。
本文档适用于所有需要进行检验的部门和人员。
遵循本操作规程将有助于提高检验效率和质量,减少人为错误,确保产品和服务的合格性。
2. 术语和定义•检验技术:指利用各种实验、测量和测试方法对产品或服务进行检验的技术。
•检验对象:指待检测的产品、材料或服务。
•检验过程:包括检验准备、实施检验、结果记录等环节的整个过程。
•标准规范:指根据相关国家或行业的规定制定的用于检验的标准和规范文件。
•检验工具:供检验使用的测量仪器、计量器具、试验设备等。
3. 检验技术操作流程3.1 检验准备1.获取检验任务:接收来自上级部门或客户的检验任务,并明确检验要求和标准。
2.审查检验标准:仔细阅读并理解检验标准规范,明确所需检验的内容和要求。
3.确定检验方法:根据检验标准和检验对象的特点,选择适合的检验方法,并编制相应的检验方案。
4.资源准备:准备所需的检验工具、试验设备和标准物质,确保其有效性和可追溯性。
5.检查检验工具:对待使用的检验工具进行检查和校验,确保其准确度和可靠性。
3.2 实施检验1.检验前准备:清洁检验现场、校准检验设备,确保检验环境符合要求。
2.样品接收:接收待检样品,进行必要的检验登记和样品编号。
3.样品准备:根据检验方法的要求,对样品进行预处理,如切割、研磨、分离等。
4.实施检验:按照检验方案和标准规范要求,进行各项检验项目的操作和记录。
5.数据处理:对检测数据进行计算、统计和分析,得出检验结果。
6.结果评定:根据检验标准和规范,对检验结果进行评定,判断样品是否合格。
7.结果报告:编制检验报告,详细描述检验过程和结果,并提交相关人员或部门。
3.3 结果记录和追溯1.结果记录:将各项检验数据、结果和评定记录在相应的记录表格或数据库中。
2.结果保存:妥善保存检验记录,包括原始记录和报告,保证其完整和安全性。
2020年 终检作业指导书标准程序-工艺部 -三级文件-安全作业管理

4.2图解 拭未清 4.3、根据《
交与包 4.4图解
6.1、
条码1、组件
表面若2、按《
海润组等不符
合检验单背面
填写异八、
4.5图解无 20组/拖)叠放在托盘上,并放置于合格区域内,正常组件可及时七、异常处理 使用条码枪扫描条码入MES系统,将组件等级信息输入MES系统中。
五、注意事项
5.2、根据《生产计划通知单》领取相应的标签。
5.1、严格按照《海润组件外观检验标准》,对组件进行100%全检。
六、主要器具要求
5.3、贴标签时要使用模板,使得所有的标签都贴在组件的同一个位置。
方5cm处。
终 检 作 业 标 准 书
文件编号:HRM-PE-091 版本号:A/0 编制人; 审核人: 批准人: 页号:1/1
1.1、规范终检工序作业过程。
一、目的
四、作业流程3.3、组件工艺部和组件质量部负责文件实施中的有效性监督。
3.2、文件第一次培训由组件工艺组织。
二、范围
3.1、本规范内容由组件工艺部负责编制、归组件工艺部解释。
4.2、检查组件TPT,电池片,玻璃表面和边框是否有划伤,使用酒精擦2.1、适用与所有规格的组件的终检作业过程。
三、职责
4.1、开启电脑,打开MES系统,进入操作界面,设定班次。
4.5、在型材四角安放护角,把组件(35型材每30组/拖,45及50型材每
4.4、使用模板将标签贴在检验合格的组件背板上,铭牌距离他在条码下。
2020年(工艺技术)轧钢线材工艺操作规程

轧钢高线车间工艺操作规程目录1.上料工工艺规程12.一号台操作工工艺规程23.二号台操作工工艺规程44.加热工工艺规程55.三号台操作工工艺规程186.粗轧调整工工艺规程317.高线中轧调整工工艺规程348. 高线预精轧350轧机调整工工艺规程369. 高线预精轧2架轧机及精轧调整工工艺规程3810 A线双模块轧钢调整工工艺规程5311导卫工工艺规程5712装配工工艺规程6113风冷线管理工工艺规程6414集卷双芯棒操作工工艺规程6515头尾在线剪切工工艺规程6616打捆工工艺规程6717.盘卷称重工工艺规程6818标牌打印工工艺规程6819挂牌工工艺规程6920卸卷操作工工艺规程7021成品管理与码垛工工艺规程7022轧辊车工工艺规程7123铣工工艺规程7424样板工工艺规程7525辊环磨工工艺规程77工艺操作规程1.上料工工艺规程1.1岗位名称:上料工1.2岗位职责:负责配合质量站检查验收入厂钢坯,并据质保书将钢坯堆放在批定垛位。
对库存进行管理,对钢坯进行组坯入炉跑号,对不合格钢坯进行剔除。
1.3岗位工艺流程:1.框图2.工艺概述:炼钢厂连铸车间运送过来的钢坯,有冷坯和热坯经检查合格后,需要轧制的直接放在步进式上料台架上,经上料机构逐根向前移动移至挡钢钩,挡钢钩落下时单支落到钢槽。
再由拨钢机逐根转入进炉辊道向前运行,辊道间有测长辊,用于钢坯测量。
入炉辊道两侧有剔废装置如有弯曲、超差、超长、超短、脱方等不合格钢坯,经剔废装置剔出到剔废平台上,多根再一起吊走。
合格钢坯逐步在入炉辊道上运行至步进炉内的悬臂辊上,经液压推钢机推入步进炉的静梁上。
1.4工艺要求1.5正常操作1.根据生产指令和YB/T2011-2004标准,根据质保书认真核对到达钢坯的车号、支数,对外观质量进行检查,遇有疑问不清之处,立即找有关人员联系解决并作好记录。
2.依据交接班记录和质保书,认真核对坯料的规格钢种、钢号、垛位层数、数量和顺序,并收好质量站制作,按炉送钢卡要逐项填写,字迹清楚,不得漏项,并于使用前10分钟发送到1#台输入生产管理系统终端、轧钢厂后部岗位,遇换号时,必须明确将所换新号第一支及时通知冷床工,不得混号。
工艺验证和关键工艺参数工艺规程和主批生产记录关键物料供应

记录关键物料供应
2020/11/12
工艺验证和关键工艺参数工艺规程和 主批生产记录关键物料供应
北京市药品质量受权人培训内容
质量管理决定权的行使-工艺验证和 1 关键工艺参数的批准
质量管理决定权的行使-工艺规程 2 和主批生产记录的批准
质量管理否决权的行使-关键物料 3 供应商的审计
• 药品生产过程的验证内容必须包括: –空气净化系统 –工艺用水系统 –生产工艺及其变更 –设备清洗 –主要原辅材料变更 –无菌药品生产过程的验证内容还应增加: 灭菌设备 药液滤过及灌封(分装)系统
工艺验证和关键工艺参数工艺规程和 主批生产记录关键物料供应
1.法规要求-GMP(200909征求意见稿)
工艺验证和关键工艺参数工艺规程和 主批生产记录关键物料供应
1. 法规要求-GMP(200909征求意见稿)
第七章 确认与验证
152条 采用新的生产处方或生产工艺前,应 验证其对常规生产的适用性。生产工艺 在使用规定的原辅料和设备条件下,应 能始终生产出符合预定的用途、符合药 品注册批准或规定的要求和质量标准的 产品。
• 第五十七条
药品生产验证应包括厂房、设施及设备安
装确认、运行确认、性能确认和产品验证。
• 第五十八条
产品的生产工艺及关键设施、设备应按验
证方案进行验证。当影响产品质量的主要因素,如工艺、质
量控制方法、主要原辅料、主要生产设备等发生改变时,以
及生产一定周期后,应进行再验证。
• 第五十九条
应根据验证对象提出验证项目、制定验证
工艺验证和关键工艺参数工艺规程和 主批生产记录关键物料供应
1. 法规要求-GMP(200909征求意见稿)
工艺部检验检测安全操作规程
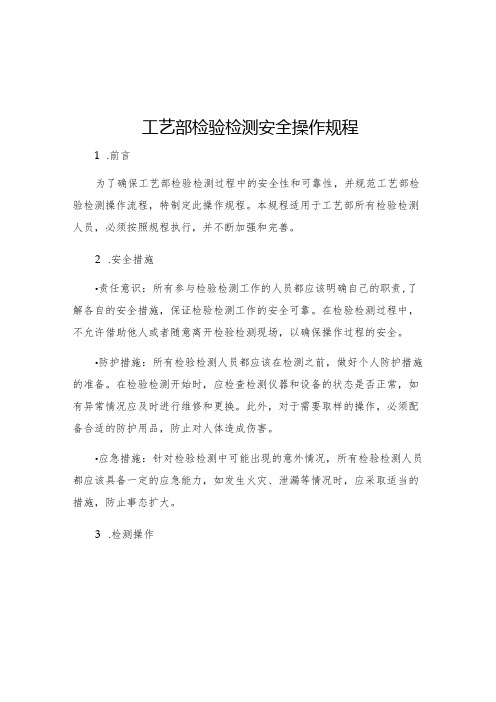
工艺部检验检测安全操作规程1.前言为了确保工艺部检验检测过程中的安全性和可靠性,并规范工艺部检验检测操作流程,特制定此操作规程。
本规程适用于工艺部所有检验检测人员,必须按照规程执行,并不断加强和完善。
2.安全措施•责任意识:所有参与检验检测工作的人员都应该明确自己的职责,了解各自的安全措施,保证检验检测工作的安全可靠。
在检验检测过程中,不允许借助他人或者随意离开检验检测现场,以确保操作过程的安全。
•防护措施:所有检验检测人员都应该在检测之前,做好个人防护措施的准备。
在检验检测开始时,应检查检测仪器和设备的状态是否正常,如有异常情况应及时进行维修和更换。
此外,对于需要取样的操作,必须配备合适的防护用品,防止对人体造成伤害。
•应急措施:针对检验检测中可能出现的意外情况,所有检验检测人员都应该具备一定的应急能力,如发生火灾、泄漏等情况时,应采取适当的措施,防止事态扩大。
3.检测操作•检验计划制定:在检验检测之前,应根据检验任务和产品特性,制定详细的检验计划,包括检验目的、检验依据、检验方法、检验标准等,明确检验流程和操作规范,并进行审批和备案。
•检验记录和保存:在检验检测过程中,检验人员应详细记录每个样品的检验结果和过程,记录表格中应包括样品编号、检验日期、检验项目、检验结果、检验依据等信息,确保检验数据的可追溯性。
同时,检验记录必须妥善保存,保证时间长久并保密。
•不良品处理:在检验检测过程中,如果发现存在不合格或不良现象,应立即停止检验检测并及时记录,详细记载不合格、不良信息和发现的原因,并按照相应的不良品处理流程进行处理。
4.运行规范•设备操作规范:检验人员在进行检验检测之前,应先了解该设备的操作规范并进行操作维护。
操作设备前应进行全面的检查,确保设备完好无损,以保证检验检测过程的准确性和可信度。
•设备维护和保养:检验人员必须根据操作规范对设备进行定期检查和保养,维护好设备正常运行。
对于出现异常的情况应及时进行维修和更换,以确保设备的安全性和可靠性。
工艺验证标准操作规程
工艺验证标准操作规程 The manuscript was revised on the evening of 2021XXXX有限公司现行文件1.目的:建立工艺验证的标准操作规程,并规范其操作。
2.范围:适用于公司所有生产产品工艺的验证。
3.责任:生产部门负责验证方案与报告的编写;化验室负责验证过程中的检测工作;质量部负责验证方案与报告的批准与其中的偏差调查。
4.规程:验证的类型:工艺验证通常可以按照以下三种方式进行:前验证、同步验证、回顾性验证。
4.1.1前验证:针对新的生产工艺或当工艺发生重大变化时所进行的工艺验证应采用前验证的方式,在验证成功结束之后才可以以放行产品。
工艺验证中所生产的产品批量应与最终上市的产品批量相同。
通常,工艺验证要求进行连续三个成功批次的生产。
4.1.2同步验证:在某些非常特殊的情况下也可以接受通过同步验证的方式进行工艺验证,即在常规生产过程中进行验证。
同步验证中生产的产品如果符合所有验证方案中规定的要求,可以在最终验证报告完成之前放行。
进行同步验证的决定必须合理、有文件记录并且经过质量部门批准。
同步性验证方法适用于以下情况:4.1.2.1由于需求很小而不常生产的产品;4.1.2.2生产量很小的产品,如放射性药品;4.1.2.3从前未经验证的遗留工艺过程,没有重大改变的情况下;4.1.2.4已有的、已经验证的工艺过程发生较小的改变时;4.1.2.5已验证的工艺进行周期性再验证时。
4.1.3回顾性验证:有些历史遗留的产品未进行工艺验证。
4.1.3.1这些工艺过程在满足以下条件可以通过对历史数据回顾的方式进行回顾性验证:4.1.3.一直按照市售产品批量规模进行生产,能够很好的理解生产中的工艺过程并都记录下来;4.1.3.有通过药典规定或经过验证实验方法进行检测所得到的充足可靠的验证数据;4.1.3.对关键程序参数和关键质量特性做了规定并进行了控制;4.1.3.建立了工艺过程的中间控制和可接受标准;4.1.3.没有由于操作失误和设备故障之外而引起的任何工艺过程或产品失败;4.1.3.在产品生产中应用的药物活性成分的杂质谱已经建立;4.1.3.同时还应具备:工艺过程没有重大的历史改变:所有关键工艺参数和关键质量特征都可以作为有代表性的历史数据;执行回顾性验证的决定应得到质量部门批准。
工艺部检验检测安全操作规程
工艺部检验检测安全操作规程工艺部检验检测安全操作规程一、前言本工艺部检验检测安全操作规程制定的目的,旨在制定安全操作规范,规范人员在检验检测时的工作流程,提高工作效率;同时确保操作人员的人身安全和设备完好,保证测试结果的准确性。
本规程适用于工艺部检验检测人员在日常检验检测工作中的操作。
二、一般原则1. 严格遵守生产文件、相应的安全操作规程和管理制度,按工艺要求进行操作。
2. 严格执行各项质量标准规定,严禁有意或无意的偷工减料。
3. 操作前必须检查设备和环境的安全情况,必要时加强安全防护措施。
4. 尊重工艺设备和工具的知识产权,保护设备和工具的完整性和安全性。
5. 操作时必须佩戴相应的劳动防护用品,如安全帽、安全鞋、防护眼镜等。
6. 工作中不得喧哗,要遵守环保、卫生等有关规定,严禁吸烟、乱扔垃圾等行为。
三、设备与环境安全规范1. 操作前要进行设备检查,必须确保设备是否正常工作,并仔细检查设备周围环境是否安全。
2. 要缩小设备和物品之间的距离,将无关物品放置到外面,避免压缩物品。
3. 在取样、处理、检验中,必须维持设备的完整性,防止设备损坏或接触电源。
4. 经过测试的设备在进入清洗或维修前必须先停用,严禁旁观,以免发生事故。
5. 设备、工具和机器损坏时,应及时更换或维修,以保持良好状态。
6. 在操作过程中,若发现任何设备、工具或机器损坏,应及时汇报处理。
四、操作规范1. 在操作前,将试剂分配在试管中,并仔细检查试管是否清洁干燥,排除残留物的可能性。
2. 在进行实验前,必须仔细认真阅读试剂放置的相关有关文件,确定采取的方法是正确并且稳定的。
3. 在操作中应遵循规定的程序,不得改变或缩短任何步骤。
4. 操作过程中不得离开操作岗位,离开前需要注意让同事或其他负责人知道。
5. 操作过程中宣传、吃饭、谈话、烟、喝酒等行为是严禁的。
6. 处理实验废料时,应按照有关规定进行处理。
7. 当对环境造成污染或污染环境时,必须采取措施予以处理。
工艺验证标准操作规程
工艺验证原则操作规程The manuscript was revised on the evening ofXXXX有限公司现行文献1.目的:建立工艺验证的原则操作规程,并规范其操作。
2.范畴:合用于公司全部生产产品工艺的验证。
3.责任:生产部门负责验证方案与报告的编写;化验室负责验证过程中的检测工作;质量部负责验证方案与报告的同意与其中的偏差调查。
4.规程:验证的类型:工艺验证普通能够按照下列三种方式进行:前验证、同时验证、回想性验证。
4.1.1前验证:针对新的生产工艺或当工艺发生重大变化时所进行的工艺验证应采用前验证的方式,在验证成功结束之后才能够以放行产品。
工艺验证中所生产的产品批量应与最后上市的产品批量相似。
普通,工艺验证规定进行持续三个成功批次的生产。
4.1.2同时验证:在某些非常特殊的状况下也能够接受通过同时验证的方式进行工艺验证,即在常规生产过程中进行验证。
同时验证中生产的产品如果符合全部验证方案中规定的规定,能够在最后验证报告完毕之前放行。
进行同时验证的决定必须合理、有文献统计并且通过质量部门同意。
同时性验证办法合用于下列状况:4.1.2.1由于需求很小而不常生产的产品;4.1.2.2生产量很小的产品,如放射性药品;4.1.2.3从前未经验证的遗留工艺过程,没有重大变化的状况下;4.1.2.4已有的、已经验证的工艺过程发生较小的变化时;4.1.2.5已验证的工艺进行周期性再验证时。
4.1.3回想性验证:有些历史遗留的产品未进行工艺验证。
4.1.3.1这些工艺过程在满足下列条件能够通过对历史数据回想的方式进行回想性验证:4.1.3.始终按照市售产品批量规模进行生产,能够较好的理解生产中的工艺过程并都统计下来;4.1.3.有通过药典规定或通过验证明验办法进行检测所得到的充足可靠的验证数据;4.1.3.对核心程序参数和核心质量特性做了规定并进行了控制;4.1.3.建立了工艺过程的中间控制和可接受原则;4.1.3.没有由于操作失误和设备故障之外而引发的任何工艺过程或产品失败;4.1.3.在产品生产中应用的药品活性成分的杂质谱已经建立;4.1.3.同时还应含有:工艺过程没有重大的历史变化:全部核心工艺参数和核心质量特性都能够作为有代表性的历史数据;执行回想性验证的决定应得到质量部门同意。
工艺技术检试验工艺规程
工艺技术检试验工艺规程1 超声检测通用工艺规程2 承压设备用钢板超声检测专用工艺3 承压设备用锻件超声检测专用工艺4 承压设备用奥氏体钢超声检测专用工艺5 承压设备用无缝钢管超声检测专用工艺6 承压设备用复合钢板超声检测专用工艺7 承压设备对接焊接接头超声检测专用工艺8 承压设备T型焊接接头超声检测专用工艺9 钢制承压设备管子和管道环向对接焊接接头超声检测专用10 承压设备用钢螺栓坯件超声检测专用工艺11 在用承压设备超声检测专用工艺12 超声测厚检测通用工艺13 模拟式超声检测仪操作规程14 数字式超声检测仪操作规程15超声波探伤仪系统自校规程16 超声测厚仪操作规程1 超声检测通用工艺规程1.1 范围1.1.1 本工艺规定了承压设备采用A型脉冲反射式超声波探伤仪检测工件缺陷的超声检测方法。
1.1.2 本工艺适用于金属材料制承压设备用原材料、零部件和焊接接头的超声检测,也适用于金属材料制在用承压设备的超声检测。
1.2 引用标准1.2.1 GB150-98《钢制压力容器》。
1.2.2劳部发[1996]276号《蒸汽锅炉安全技术监察规程》。
1.2.3 JB/T4730-2005《承压设备无损检测》1.3 一般要求1.3.1 检测人员(1)凡从事超声波检测的人员,必须经过国家劳动部门考核,取得各级资格的人员是能从事与其资格相适应的工作。
(2)检测人员必须掌握仪器的综合性能,并能独立进行检测。
(3)检测人员必须熟悉超声波检测有关标准,能按标准要求选择适当方法校正仪器,并能进行熟练的检测操作。
(4)检测人员应能根据被检工件的材质、规格、加工工艺过程、材料曲率等,预计缺陷可能产生的部位和类型,并能进行正确的定位和定量。
1.3.2 检测设备(1)超声检测设备均应具有产品质量合格证或合格的证明文件。
(2)探伤仪、探头和系统性能(a)探伤仪采用A型脉冲反射式超声波探伤仪,其工作频率范围为1-5MHz,仪器至少在荧光屏满幅度的80%范围内呈线形显示,探伤仪应具有80dB以上的连续可调衰减器,步进级每档不大于2dB,其精度为任意相邻12dB误差在±1dB以内,最大累计误差不超过1dB。
- 1、下载文档前请自行甄别文档内容的完整性,平台不提供额外的编辑、内容补充、找答案等附加服务。
- 2、"仅部分预览"的文档,不可在线预览部分如存在完整性等问题,可反馈申请退款(可完整预览的文档不适用该条件!)。
- 3、如文档侵犯您的权益,请联系客服反馈,我们会尽快为您处理(人工客服工作时间:9:00-18:30)。
超声波检测工艺规程1 超声检测通用工艺规程2 承压设备用钢板超声检测专用工艺3 承压设备用锻件超声检测专用工艺4 承压设备用奥氏体钢超声检测专用工艺5 承压设备用无缝钢管超声检测专用工艺6 承压设备用复合钢板超声检测专用工艺7 承压设备对接焊接接头超声检测专用工艺8 承压设备T型焊接接头超声检测专用工艺9 钢制承压设备管子和管道环向对接焊接接头超声检测专用10 承压设备用钢螺栓坯件超声检测专用工艺11 在用承压设备超声检测专用工艺12 超声测厚检测通用工艺13 模拟式超声检测仪操作规程14 数字式超声检测仪操作规程15超声波探伤仪系统自校规程16 超声测厚仪操作规程1 超声检测通用工艺规程1.1 范围1.1.1 本工艺规定了承压设备采用A型脉冲反射式超声波探伤仪检测工件缺陷的超声检测方法。
1.1.2 本工艺适用于金属材料制承压设备用原材料、零部件和焊接接头的超声检测,也适用于金属材料制在用承压设备的超声检测。
1.2 引用标准1.2.1 GB150-98《钢制压力容器》。
1.2.2劳部发[1996]276号《蒸汽锅炉安全技术监察规程》。
1.2.3 JB/T4730-2005《承压设备无损检测》1.3 一般要求1.3.1 检测人员(1)凡从事超声波检测的人员,必须经过国家劳动部门考核,取得各级资格的人员是能从事与其资格相适应的工作。
(2)检测人员必须掌握仪器的综合性能,并能独立进行检测。
(3)检测人员必须熟悉超声波检测有关标准,能按标准要求选择适当方法校正仪器,并能进行熟练的检测操作。
(4)检测人员应能根据被检工件的材质、规格、加工工艺过程、材料曲率等,预计缺陷可能产生的部位和类型,并能进行正确的定位和定量。
1.3.2 检测设备(1)超声检测设备均应具有产品质量合格证或合格的证明文件。
(2)探伤仪、探头和系统性能(a)探伤仪采用A型脉冲反射式超声波探伤仪,其工作频率范围为1-5MHz,仪器至少在荧光屏满幅度的80%范围内呈线形显示,探伤仪应具有80dB以上的连续可调衰减器,步进级每档不大于2dB,其精度为任意相邻12dB误差在±1dB以内,最大累计误差不超过1dB。
水平线性误差不大于1%,垂直线性误差不大于5%。
其余指标应符合JB/T9214的规定。
(b)探头a. 检测常用探头有单直探头,单斜探头等。
b. 晶片有效面积一般不应超过500mm2,且任一边长不应大于25mm。
c. 单斜探头声束轴线水平偏离角不应大于2°,主声束垂直方向不应有明显的双峰。
(c)超声探伤仪和探头的系统性能a. 在达到所探工件的最大检测声程时,其有效灵敏度余量应大于或等于10dB。
b. 仪器和探头的组合频率与公称频率误差不得大于±10%。
c. 仪器和直探头组合的始脉冲宽度:对于频率为5MHz的探头,其占宽不得大于10mm;对于频率为2.5MHz的探头,其占宽不得大于15mm。
d. 直探头的远场分辩力应大于或等于30dB,斜探头的远场分辨力应大于或等于6dB。
e.仪器和探头的系统性能应按JB/T9214和JB/T10062的规定进行测试。
1.3.3 超声检测一般方法(1)检测准备(a)承压设备的制造、安装和在用检验中,超声检测的检测时机及抽检率的选择等应按相关法规、标准及有关技术文件的规定。
(b)所确定检测面应保证工件被检部分均能得到充分检查。
(c)焊缝的表面质量应经外观检测合格。
所有影响超声检测的锈蚀、飞溅和污物等都应予以清除,其表面粗糙度应符合检测要求。
表面的不规则状态不得影响检测结果的正确性和完整性,否则应做适当的处理。
(2)扫查覆盖率为确保检测时超声声束能扫查到整个被检区域,探头的每次扫查覆盖率应大于探头直径(斜探头的宽)的15%。
(3)探头的移动速度探头的移动速度不应超过150㎜/s。
(4)扫查灵敏度扫查灵敏度不应低于基准灵敏度。
(5)耦合剂应采用透声性好,且不损伤检测表面的耦合剂,如机油、浆糊、甘油和水等。
(6)耦合补偿(a)表面粗糙度补偿在检测和缺陷定量时,应对由表面粗糙度引起的能量损耗进行补偿。
(b)衰减补偿在检测和缺陷定量时,应对材质衰减引起的检测灵敏度下降和缺陷定量误差进行补偿。
(c)曲面补偿对于探测面是曲面的工作,应采用曲率半径与工件相同或相近的参考试块,对比进行曲率补偿。
1.3.4 系统校准和复核(1)一般要求系统校准应在标准试块上进行,校准中应使探头主声束垂直对准反射体的反射面,以获得稳定和最高的反射信号。
(2)仪器校准每隔3个月至少应对仪器的水平线性和垂直线性进行一次测定,测定方法按JB/T10061的规定。
(3)新购探头测定新购探头应有探头性能说明书,新探头使用前应进行前沿距离、K值、主声束偏离、灵敏度余量和分辨力等主要参数的测定。
测定应按JB/T10062的有关规定进行,并满足要求。
(4)检测前仪器和探头系统的测定(a)使用仪器—斜探头系统,检测前应测定前沿距离、K值、主声束偏离,调节或复核扫描量程和扫查灵敏度。
(b)使用仪器—直探头系统,检测前应测定是脉冲宽度、灵敏度余量和分辨力,调节或复核扫描量程和扫查灵敏度。
(5)检测过程中仪器和探头系统的复核遇到下述情况应对系统进行复核:(a)校准后的探头、耦合剂和仪器调节旋钮发生改变时。
(b)检测人员怀疑检测量程或扫查灵敏度有变化时。
(c)连续工作4h以上时。
(d)工作结束时。
(6)检测结束前仪器和探头系统的复核(a)每次检测结束前,应对扫描量程进行复核。
如果任意一点在扫描线上的偏移超过扫描线读数的10%,则扫描量程应重新调整,并对上一次复核以来所有的检测部位进行复检。
(b)每次检测结束前,扫查灵敏度进行复核。
一般对距离—波幅曲线的校核不少于3点。
如曲线上任何一点幅度下降2dB,则应对上一次复核以来所有的检测部位进行复检;如幅度上升2dB,则应对所有的记录信号进行重新评定。
(7)校准、复核的有关注意事项校准、复核和对仪器进行线性检测时,任何影响仪器线性的控制器(如抑制或滤波开关等)都应放在“关”的位置或处于最低水平上。
1.3.5 试块(1)标准试块(a)标准试块a. 标准试块是指本部分规定的用于仪器探头系统性能校准和检测校准的试块,本部分采用的标准试块有:a) 钢板用标准试块:CBⅠ、CBⅡ。
b) 锻件用标准试块:CSⅠ、CSⅡ、CS Ⅲ。
c) 焊接接头用标准试块:CSK-ⅠA、CSK-ⅡA、CSK-ⅢA、CSK-ⅣA。
b.标准试块应采用与被检工件相同或近似声学性能的材料制成,该材料用直探头探测时,不得有大于或等于φ2㎜平底孔当量直径的缺陷。
c.标准试块尺寸精度应符合相关标准要求。
d.标准试块的其他制造要求应符合JB/T10063和JB/T7913的规定。
(b)对比试块a. 对比试块是指用于检测校准的试块。
b. 对比试块的外形尺寸应能代表被检工件的特征,试块厚度与被检工件厚度相对应。
如果涉及到两种或两种以上不同厚度部件焊接接头的检测,试块的厚度由其最大厚度来决定。
c. 对比试块反射体的形状、尺寸和数量应符合相关标准的要求。
1.3.6 检测报告及底片资料存档(1)检测报告至少应包括:(a)委托单位。
(b)被检工件:名称、编号、规格、材质、坡口型式、焊接方法和热处理状况。
(c)检测设备:探伤仪、探头、试块。
(d)检测规范:技术等级、探头K值、探头频率、检测面和检测灵敏度。
(e)检测部位及缺陷类型:尺寸、位置和分布应在草图上予以标明,如有因几何形状限制而检测不到的部位,也应加以说明。
(f)检测结果及质量分级、检测标准名称和验收等级。
(g)检测人员和责任人员签字及其技术资格。
(h)检测日期。
(2) 超声检测的有关资料(检测位置示意图、检测原始记录、检测报告等过程结果质量记录资料)必须妥善保管7年以上。
2 承压设备用钢板超声检测专用工艺2.1 适用范围2.1.1 本工艺适用于板厚为6-250mm的碳素钢、低合金钢制承压设备用板材的超声检测和质量分级。
2.1.2 奥氏体钢板材、镍及镍合金板材以及双相不锈钢板材的超声检测也可参照本章执行。
2.2 引用标准2.2.1 GB150《钢制压力容器》2.2.2 JB/T4730-2005《承压设备无损检测》2.2.3 检测人员2.3.1 凡从事超声波检测的人员,必须经过国家技监部门考核,取得不同等级资格的人员只能从事与其资格相适应的工作。
2.3.2 检测人员必须掌握仪器的综合性能,并能独立进行检测。
2.3.3检测人员必须熟悉超声波检测有关标准,能按标准要求选择适当方法校正仪器,并能进行熟练的检测操作。
2.3.4检测人员应能根据被检工件的材质、规格、加工工艺过程、材料曲率等,预计缺陷可能产生的部位和类型,并能进行正确的定位和定量。
2.2.4 探头选用2.4.1 探头选用应按表1的规定进行。
2.4.2 双晶探头的性能应符合JB/T4730-2005《承压设备无损检测》标准附录A(规范性附录)的要求。
2.2.5 标准试块2.5.1 T≤20mm的钢板,采用JB/T4730-2005标准要求的CBⅠ标准试块。
图1 CBI标准试块2.5.2 T>20mm的钢板,采用JB/T4730-2005标准要求的CBⅡ标准试块。
2.6 基准灵敏度2.6.1 T ≤20mm 的钢板,用CB Ⅰ试块将工件等厚部分的第一次底波高度调整到满幅度的50%。
再提高10dB 作为基准灵敏度。
2.6.2 T >20mm 时,将CB Ⅱ试块φ5平底孔第一次反射波调整到满幅度的50%,作为基准灵敏度。
2.6.3 板厚不小于探头的3倍近场区时,可取钢板无缺陷的完好部位的第一次底波满幅度50%来校准灵敏度,符合2.6.2100100条的规定。
2.7 检测方法2.7.1检测面可选钢板任一扎制平面进行检测,如需要也可两面进行检测。
2.7.2 耦合方式可采用直接接触法或液浸法。
2.7.3扫查方式(1)探头沿垂直于钢板压延方向,间距为100mm的平行线进行扫查。
在钢板剖口预定线两侧各50mm(当钢板厚度超过100mm时,以钢板厚度的一半为准)内应作100%扫查,如图所示:图3 探头扫查示意图(2)根据合同、技术协议书或图样的要求,也可采用其他形式的扫查。
2.8 缺陷记录2.8.1在检测过程中发现下列情况之一者,作为缺陷:(1)缺陷第一次反射波高≥50%,F1≥50%者。
(2)B1<100%,而F1/B1≥50%者。
(3) B1<50%者。
2.2.8.2缺陷的测定(1)检出缺陷后,在其周围继续进行检测,以确定其延伸。
(2)单直、双直探头在检测面使F1=25%满刻度或F1/B1=50%,此时探头移动的距离指示长度,但双直探头移动方向应与声波分割面相垂直。
(3)当采用F2与B2来评定缺陷时,检测灵敏度以相应的第二次反射波来校准。