齿轮加工工艺
齿轮轴的加工工艺步骤

齿轮轴的加工工艺步骤一、引言在机械制造领域中,齿轮轴是一种重要的零部件,它通常用于传动系统中的齿轮装置。
在齿轮轴的加工过程中,需要进行多个步骤,包括铣削、车削、磨削等工艺。
本文将对齿轮轴的加工工艺步骤进行详细的探讨。
二、铣削加工铣削是齿轮轴加工的第一步,主要用于将齿轮轴的表面进行平整和平行处理。
具体的步骤如下:1. 准备工作•确定齿轮轴的加工尺寸和精度要求•选择适当的铣刀和切削参数•检查铣床的刀具和夹具是否安装正确2. 夹紧齿轮轴•将齿轮轴夹紧在铣床的工作台上•确保齿轮轴夹紧稳固,不会出现松动的情况3. 调整刀具位置•将铣刀移动到离工件表面一定距离的位置•通过刀具的上下调整,确定适当的铣削深度4. 开始铣削•打开铣床的电源,启动铣床•调整进给速度和切削速度,开始进行铣削•按照预定的路径沿着齿轮轴的轴向进行铣削三、车削加工车削是齿轮轴加工的第二步,主要用于将齿轮轴的外径和内孔进行加工。
具体的步骤如下:1. 准备工作•确定齿轮轴的轴向和径向尺寸•选择适当的车刀和车削参数•检查车床的刀具和夹具是否安装正确2. 夹紧齿轮轴•将齿轮轴夹紧在车床的工作台上•使用合适的夹具保证齿轮轴的夹紧稳固3. 调整刀具位置•将车刀移动到离工件表面一定距离的位置•调整刀具的高度和偏置,确保刀具与齿轮轴的表面接触4. 开始车削•打开车床的电源,启动车床•调整进给速度和切削速度,开始进行车削•沿着齿轮轴的轴向和径向进行车削,实现所需的外径和内孔尺寸四、磨削加工磨削是齿轮轴加工的最后一步,主要用于提高齿轮轴的表面质量和精度。
具体的步骤如下:1. 准备工作•确定齿轮轴的磨削要求和精度要求•选择适当的砂轮和砂轮参数•检查磨床的砂轮和夹具是否安装正确2. 夹紧齿轮轴•将齿轮轴夹紧在磨床的工作台上•确保齿轮轴夹紧稳固,不会出现松动的情况3. 调整磨削参数•调整磨床的进给速度和切削速度•通过调整砂轮的位置和偏置,确定适当的磨削深度和砂轮与齿轮轴的接触位置4. 开始磨削•打开磨床的电源,启动磨床•沿着齿轮轴的轴向和径向进行磨削,实现所需的表面质量和精度要求五、总结通过铣削、车削和磨削等工艺步骤,齿轮轴可以得到满足要求的加工结果。
齿轮的加工工艺过程

齿轮的加工工艺过程
嘿,朋友们!今天咱们来聊聊齿轮的加工工艺过程,这可有意思啦!
你知道吗,齿轮这小家伙,别看它个头不大,作用可大着呢!要把它制造出来,那可得经过一系列精细又有趣的步骤。
选好材料后,就得给它“整形”啦。
通过锻造或者铸造,让它大致有个齿轮的样子。
这就好比给小朋友捏橡皮泥,先捏个大概的形状出来。
然后呢,就是滚齿或者插齿啦。
这就像是给齿轮“雕刻”出牙齿,让它能够准确地转动和咬合。
这可是个精细活,稍微有点偏差都不行。
再之后,还有热处理。
这就像是给齿轮“锻炼身体”,让它变得更结实、更耐用。
经过热处理的齿轮,就像是经过锻炼的运动员,更有力量啦!
然后呀,还有磨削加工。
这就像是给齿轮“化妆”,让它的表面更加光滑,转动起来更顺畅。
还有一系列的检验和测试。
这就像是给齿轮“考试”,看看它是不是合格,能不能胜任工作。
你看,制造一个小小的齿轮,居然有这么多步骤,是不是很神奇?每一个步骤都需要师傅们的精心操作和严格把关,这样才能做出高质量的齿轮。
所以呀,别小看这小小的齿轮,它背后可是凝聚了好多人的心血和智慧呢!怎么样,朋友们,现在是不是对齿轮的加工工艺过程有了更清楚的了解啦?。
第8章 齿轮加工技术
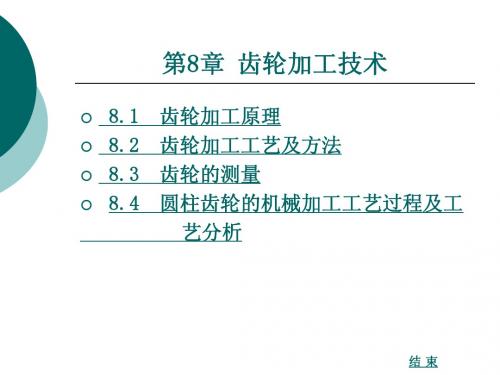
8.1 8.2 8.3 8.4
齿轮加工原理 齿轮加工工艺及方法 齿轮的测量 圆柱齿轮的机械加工工艺过程及工 艺分析
结束
8.1 齿轮加工原理
8.1.1 常见齿轮的种类
齿轮在切削加工时,工件和刀具按一定规律运动,利用
刀具切削刃对工件毛坯的切削作用,切除毛坯上多余的金属, 而得到所要求的表面形状。常用的齿轮有圆柱齿轮,圆锥齿 轮及蜗杆蜗轮等,而以圆柱齿轮应用最广。齿轮齿面的表面 形状有渐开线表面,摆线表面,圆弧表面等,渐开线表面齿 轮是最常用的齿轮,它能方便地在机床上加工出来,图8-1为 常见齿轮种类。
上一页 下一页 返回
补充:热轧
热轧就是在高于合金再结晶温度的温度中使其软 化后用压轮把材料压成薄片或钢坯的横截面,使 材料形变,但材料物理性质并无变化。
补充:冷轧
冷轧是对已经过热轧、除麻点除氧化工序的材料在 低于合金再结晶温度的温度中用压轮进一步碾压材 料以让材料有再结晶的过程。经过反覆的冷压-- 再结晶--退火--冷压(反覆2~3次)过程, 材料里的金属发生分子级别的改变(再结晶),形 成的合金物理性质发生改变。
上一页 下一页 返回
图8-8 直齿圆柱齿轮的铣削
返回
8.2 齿轮加工工艺及方法
3)铣刀的选择。根据齿轮模数、压力角、齿轮齿数选择正确 铣刀。 4)分度计算与调整。据齿轮齿数选择合适的分度方法,计算 后进行有关调整。 5)确定合理铣削用量及切削液。按照切削用量选择原则,考 虑齿轮铣刀是铲齿成型铣刀,所选铣削速度应比普通铣刀略 低。为了保证齿轮加工质量和铣刀耐用度,可采用乳化液、 轻柴油等切削液。 6)对中心 对刀是使铣刀廓形的对称平面通过齿坯轴线。如偏 离标准中心,铣出的齿形将向一边倾斜,严重影响齿轮质量, 常用的方法有试切法,划线法。 7)铣削。
齿轮磨削加工工艺
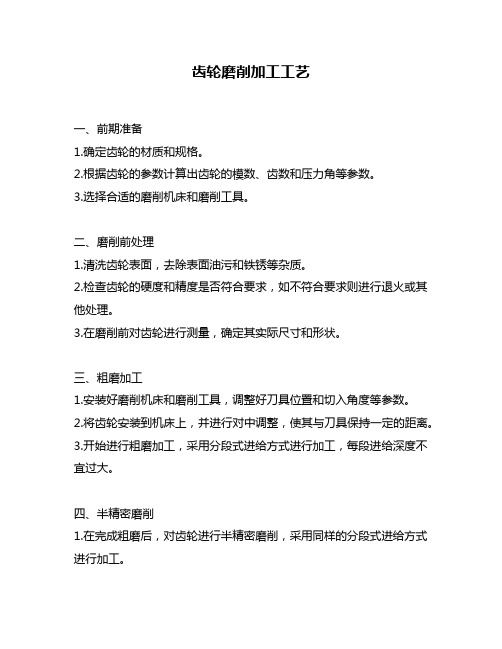
齿轮磨削加工工艺
一、前期准备
1.确定齿轮的材质和规格。
2.根据齿轮的参数计算出齿轮的模数、齿数和压力角等参数。
3.选择合适的磨削机床和磨削工具。
二、磨削前处理
1.清洗齿轮表面,去除表面油污和铁锈等杂质。
2.检查齿轮的硬度和精度是否符合要求,如不符合要求则进行退火或其他处理。
3.在磨削前对齿轮进行测量,确定其实际尺寸和形状。
三、粗磨加工
1.安装好磨削机床和磨削工具,调整好刀具位置和切入角度等参数。
2.将齿轮安装到机床上,并进行对中调整,使其与刀具保持一定的距离。
3.开始进行粗磨加工,采用分段式进给方式进行加工,每段进给深度不宜过大。
四、半精密磨削
1.在完成粗磨后,对齿轮进行半精密磨削,采用同样的分段式进给方式进行加工。
2.为了保证加工质量,需要对磨削机床和磨削工具进行定期检查和维护。
3.在半精密磨削过程中,需要注意控制切削速度、进给速度和切削深度等参数,以确保加工精度。
五、精密磨削
1.在完成半精密磨削后,进行最后的精密磨削。
此时需要采用更加细致的进给方式和切入角度等参数。
2.为了保证加工质量,需要对磨削机床和磨削工具进行更加细致的检查和维护。
3.在精密磨削过程中,需要采用更加严格的控制方法来控制切割参数,以确保齿轮的最终形态、尺寸和表面质量。
六、后处理
1.完成齿轮的精密磨削后,需要对其表面进行清洗,并去除可能存在的毛刺和其他杂质。
2.对齿轮进行测量,并与原始设计要求进行比较,以确保其符合要求。
3.最后将齿轮包装好,并妥善保存。
齿轮加工工艺过程
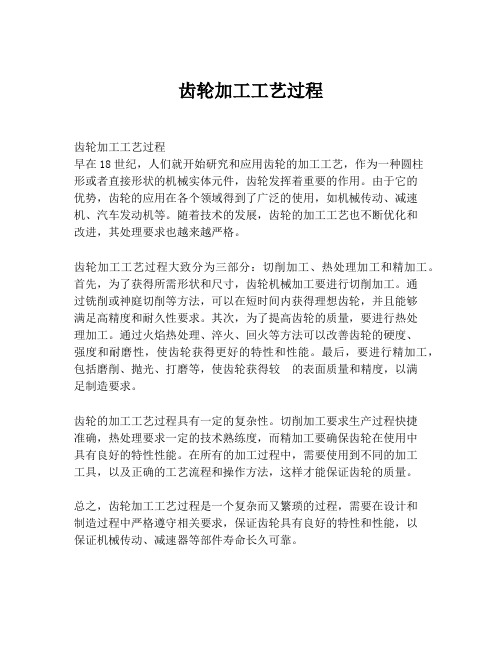
齿轮加工工艺过程
齿轮加工工艺过程
早在18世纪,人们就开始研究和应用齿轮的加工工艺,作为一种圆柱
形或者直接形状的机械实体元件,齿轮发挥着重要的作用。
由于它的
优势,齿轮的应用在各个领域得到了广泛的使用,如机械传动、减速机、汽车发动机等。
随着技术的发展,齿轮的加工工艺也不断优化和
改进,其处理要求也越来越严格。
齿轮加工工艺过程大致分为三部分:切削加工、热处理加工和精加工。
首先,为了获得所需形状和尺寸,齿轮机械加工要进行切削加工。
通
过铣削或神庭切削等方法,可以在短时间内获得理想齿轮,并且能够
满足高精度和耐久性要求。
其次,为了提高齿轮的质量,要进行热处
理加工。
通过火焰热处理、淬火、回火等方法可以改善齿轮的硬度、
强度和耐磨性,使齿轮获得更好的特性和性能。
最后,要进行精加工,包括磨削、抛光、打磨等,使齿轮获得较 的表面质量和精度,以满
足制造要求。
齿轮的加工工艺过程具有一定的复杂性。
切削加工要求生产过程快捷
准确,热处理要求一定的技术熟练度,而精加工要确保齿轮在使用中
具有良好的特性性能。
在所有的加工过程中,需要使用到不同的加工
工具,以及正确的工艺流程和操作方法,这样才能保证齿轮的质量。
总之,齿轮加工工艺过程是一个复杂而又繁琐的过程,需要在设计和
制造过程中严格遵守相关要求,保证齿轮具有良好的特性和性能,以
保证机械传动、减速器等部件寿命长久可靠。
齿轮 轴 壳体 加工工艺流程

检验
检验各部位尺寸和表面加工情况
50
入库
涂油入库
工种
工序内容
5
下料
根据设计要求,合理下料
10
车
用三爪卡盘夹持工件,车端面见平,钻中心孔,用尾架顶端顶住,粗车各个台阶,直径、长度均留余量2mm。
15
热
调制处理
20
钳
修研两端中心孔
25
车
双顶尖装夹,半精车各台阶。切相关退刀槽,倒角。
30
插
用插齿机,插出花键。
35
钳
修研两端中心孔
40
磨
用砂轮靠端面,磨各轴肩。
45
检验
检验各部的加工工序
序号
工种
工序内容
5
铸造
按图纸要求铸造
10
清砂
清砂处理
15
热
人工时效处理
20
涂漆
表面涂防锈漆
25
铣
在数控铣床上,讲毛坯孔定位夹紧,粗精铣各基面及轴承座结合面,并加工其上所有螺孔及定位孔。
30
钳
装配轴承座
35
钻
按要求钻孔。
40
钳
去毛刺,清洗。
1.齿轮的加工工序
序号
工序内容
5
毛坯锻造
10
正火
15
粗车外圆及端面,留余量1.5-2mm,钻镗花键底孔
20
拉花键孔
25
钳工去毛刺
30
精车外圆,端面及槽至要求
35
检验
40
插齿,留剃余量0.04-0.06mm
45
倒角
50
钳工去毛刺
55
剃齿
60
齿部高频淬火
齿轮研磨工艺
齿轮研磨工艺
齿轮研磨工艺是一种对齿轮进行精密加工的方法,旨在提高齿轮的表面质量和精度。
下面是齿轮研磨工艺的一般步骤:
1. 准备工作:首先,需要对要研磨的齿轮进行清洗和检查,以确保表面没有污垢、油脂或其他杂质。
同时,检查齿轮的尺寸、形状和齿形,以确定研磨的目标和要求。
2. 选择研磨介质:根据齿轮的材料和要求,选择合适的研磨介质。
常用的研磨介质包括砂纸、砂轮、砂带等。
3. 固定齿轮:将齿轮固定在研磨设备上,确保其稳定并能够旋转。
4. 研磨操作:启动研磨设备,使齿轮与研磨介质接触,并按照预定的研磨参数进行研磨。
研磨参数包括研磨速度、压力、时间等,这些参数的选择将根据齿轮的材料、尺寸和要求来确定。
5. 检查和修整:在研磨过程中,定期检查齿轮的表面质量和精度。
如果发现表面有划痕、磨损或其他缺陷,可以进行修整操作,如更换研磨介质、调整研磨参数等。
6. 清洁和润滑:研磨完成后,对齿轮进行清洁,去除研磨介质和产生的碎屑。
然后,可以根据需要对齿轮进行润滑处理,以提高其使用寿命和性能。
齿轮研磨工艺是一种精细的加工方法,可以显著提高齿轮的表面质量和精度。
通过控制研磨参数和选择合适的研磨介质,可以获得高质量的齿轮,满足各种应用的要求。
盘类齿轮加工工艺流程学习心得
盘类齿轮加工工艺流程学习心得
1.一般整体齿轮的加工工艺过程:
锻造——正火——粗车——半精车——滚齿——渗碳——车碳层——淬火——磨平面——精车孔——磨孔——磨齿——检验——清洗——入库。
2.组合式齿轮的加工工艺过程。
如图一所示盘类零件在机床上的加工工艺。
首先,此图分为齿圈和齿体两部分。
齿圈材料为机械性能较好的40CrMoTi碳素合金钢,轮体材料为锻造C级钢。
它的加工工艺路线是:
粗车——热处理——半精车——热套——精车——钻油孔——滚齿——热处理——磨孔——磨齿——检验——清洗——入库。
零件加工工序是:
1.在立式车床上粗车齿圈和轮体。
2.在立式车床上半精车齿圈厚度和内孔、轮体厚度和外径(保证齿圈内孔和轮体外径的过盈配合量为0.85——0.95mm)
3.热套齿圈和轮体。
4.在立式车床上精车齿圈外径和下工序的找正基准(齿圈外径两侧0.2——0.3mm)。
5.在CW61100车床上精车轮体内孔、端面、切槽、齿圈两端面,车出油槽达到工艺文件的要求。
三、齿坯车削加工采用的切削参数
在上述加工工艺过程中,精车工序要达到工艺文件规定的表面。
45钢齿轮加工工序
45钢齿轮加工工序一、引言45钢是一种常用的金属材料,具有较好的强度、塑性和韧性,因此在齿轮加工中得到了广泛应用。
本文将详细介绍45钢齿轮的加工工序,包括毛坯准备、粗车削、精车削、齿轮磨削、齿面热处理、齿形修正、表面处理和质量检测等方面。
二、毛坯准备在齿轮加工前,需要进行毛坯准备。
首先,根据齿轮的设计要求,选择合适的45钢材料,并进行锻造和轧制等工艺,制成具有一定形状和尺寸的毛坯。
毛坯的尺寸和形状应符合齿轮的设计要求,以确保后续加工的顺利进行。
三、粗车削粗车削是齿轮加工的第一道工序,其主要目的是去除毛坯的余量,使齿轮的外形初步成型。
在粗车削过程中,应根据齿轮的设计要求,选择合适的刀具和切削参数,对毛坯进行切削加工。
粗车削后,齿轮的外形应基本符合设计要求,为后续的精车削和磨削加工打下基础。
四、精车削精车削是齿轮加工的重要工序之一,其主要目的是进一步细化齿轮的外形和尺寸,提高齿轮的精度和表面质量。
在精车削过程中,应根据齿轮的设计要求,选择合适的刀具和切削参数,对粗车削后的齿轮进行切削加工。
精车削后,齿轮的外形和尺寸应符合设计要求,表面质量也应达到一定的标准。
五、齿轮磨削齿轮磨削是提高齿轮精度和表面质量的重要工序。
在磨削过程中,应选择合适的砂轮和磨削参数,对精车削后的齿轮进行磨削加工。
通过磨削加工,可以进一步细化齿轮的外形和尺寸,提高齿轮的精度和表面质量。
同时,磨削还能够去除齿轮表面的划痕、毛刺等缺陷,提高齿轮的外观质量。
六、齿面热处理齿面热处理是提高齿轮硬度和耐磨性的重要工序。
在热处理过程中,应选择合适的加热方式和加热温度,对齿轮进行加热处理。
通过热处理,可以改变齿轮表面的组织结构,提高其硬度和耐磨性。
同时,热处理还能够消除齿轮内部的应力,提高其稳定性和可靠性。
七、齿形修正齿形修正是在齿轮加工过程中对齿形进行微调的重要工序。
在修正过程中,应选择合适的修正工具和方法,对齿形进行微调。
通过修正处理,可以进一步改善齿轮的啮合性能和提高其使用寿命。
齿轮加工工艺过程和分析
齿轮的生产过程一.齿轮的主要加工面1.齿轮的主要加工表面有齿面和齿轮基准表面,后者包括带孔齿轮的基准孔、切齿加工时的安装端面,以及用以找正齿坯位置或测量齿厚时用作测量基准的齿顶圆柱面。
2.齿轮的材料和毛坯常用的齿轮材料有15 钢、 45 钢等碳素结构钢;速度高、受力大、精度高的齿轮常用合金结构钢,如20Cr, 40Cr, 38CrMoAl,20CrMnTiA等。
齿轮的毛坯决定于齿轮的材料、结构形状、尺寸规格、使用条件及生产批量等因素,常用的有棒料、锻造毛坯、铸钢或铸铁毛坯等。
二、直齿圆柱齿轮的主要技术要求,1.齿轮精度和齿侧间隙GBl0095 《渐开线圆柱齿轮精度》对齿轮及齿轮副规定了12 个精度等级。
其中, 1~2 级为超精密等级; 3— 5 级为高精度等级; 6~8 级为中等精度等级; 9~12 级为低精度等级。
用切齿工艺方法加工、机械中普遍应用的等级为7 级。
按照齿轮各项误差的特性及它们对传动性能的主要影响,齿轮的各项公差和极限偏差分为三个公差组 ( 表 13—4) 。
根据齿轮使用要求不同,各公差组可以选用不同的精度等级。
齿轮副的侧隙是指齿轮副啮合时,两非工作齿面沿法线方向的距离 ( 即法向侧隙 ) ,侧隙用以保证齿轮副的正常工作。
加工齿轮时,用齿厚的极限偏差来控制和保证齿轮副侧隙的大小。
2.齿轮基准表面的精度齿轮基准表面的尺寸误差和形状位置误差直接影响齿轮与齿轮副的精度。
因此GBl0095 附录中对齿坯公差作了相应规定。
对于精度等级为 6~8 级的齿轮,带孔齿轮基准孔的尺寸公差和形状公差为IT6-IT7 ,用作测量基准的齿顶圆直径公差为IT8 ;基准面的径向和端面圆跳动公差,在 11-22 μm之间 ( 分度圆直径不大于 400mm的中小齿轮 ) 。
3.表面粗糙度齿轮齿面及齿坯基准面的表面粗糙度,对齿轮的寿命、传动中的噪声有一定的影响。
6~8 级精度的齿轮,齿面表面粗糙度 Ra 值一般为 0.8—3.2μ m,基准孔为 0.8—1.6 μm,基准轴颈为 0.4—1.6μm,基准端面为 1.6~ 3. 2μ m,齿顶圆柱面为 3.2μm。
- 1、下载文档前请自行甄别文档内容的完整性,平台不提供额外的编辑、内容补充、找答案等附加服务。
- 2、"仅部分预览"的文档,不可在线预览部分如存在完整性等问题,可反馈申请退款(可完整预览的文档不适用该条件!)。
- 3、如文档侵犯您的权益,请联系客服反馈,我们会尽快为您处理(人工客服工作时间:9:00-18:30)。
车床主轴箱齿轮
机械加工工艺过程设计
(机电09级)
1.问题提出
零件的几何精度直接影响零件的使用性能,而机械加工工艺过程制定的是否合理将直接影响零件的加工精度。
针对车床主轴箱齿轮,应用所学的机械制造基础知识进行一次加机械工工艺过程设计的综合性工程应用训练。
2.专题研究的目的
(1)掌握零件主要部分技术要求的分析方法;
(2)掌握零件材料的选择方法和确定毛坯的制备方法及工艺;
(3)掌握工艺分析方法;
(4)掌握定位基准的选择方法;
(5)掌握制定出合理的零件加工顺序的原则和方法;
(6)掌握制定出合理的零件加工路线的方法。
3.研究内容
图1所示为车床的一根传动轴车床主轴箱齿轮,完成该齿轮零件的机械加工工艺过程设计。
工艺设计的具体内容包括:
1、进行零件主要部分的技术要求分析研究;
2、确定齿轮的材料、毛坯的制备方法及工艺、热处理工艺;
3、进行加工工艺分析;
4、确定定位基准;
5、制定齿轮的加工顺序;
6、制定齿轮的加工路线;
4.设计过程
4.1零件主要部分的技术要求分析研究
(1)齿轮的工作面为齿面,在传动过程中接触的两齿面会产生一定相互滑动,导致齿面磨损。
严重时,会加大齿侧间隙而引起传动不平稳和冲击。
为保证传动的平稳性,并且减小摩擦,应采用较高的表面粗糙度,此处选择2.5um.
(2)齿轮Φ40H7内孔表面与传动轴为过盈配合,内孔表面为摩擦表面,应采取较高的表面粗糙度要求,此处选择2.5um.
(3)齿轮端面和齿顶面为非工作表面,表面粗糙度要求较低,此处为5um.
(4)齿轮端面采用端面圆跳动,既保证了端面与基准轴的垂直度要求又保证
了齿轮轴向的圆柱度要求。
(5)Φ40H7内孔选用直线度、垂直度、圆柱度等形位公差,保证了内孔对基准轴的高精度要求。
4.2确定齿轮的材料、毛坯的制备方法及工艺、热处理工艺
1、选择齿轮的材料时,需考虑到机床齿轮工作平稳,无强烈冲击,负荷不大,转速中等,对齿轮强度和韧性的要求不高,但材料要有高的硬度和好的耐磨性。
另外综合选用材料的经济因素,选用45#钢。
2、毛坯的制备方法
锻造:下料—自由锻—正火处理
3、热处理工艺:正火或调质处理后再经高频感应加热表面淬火,齿面硬度可达52HRC,齿心硬度为220~250HBS,能够满足性能要求。
○1正火:将齿轮放入炉中加热到840-8800C,保温约3小时。
出炉后在空气中冷却。
目的:充分消除锻造内应力,细化晶粒,适当提高齿轮的硬度,为以后的机加工做性能准备,同时为后序的热处理做组织准备。
○2表面淬火+回火
表面淬火:利用感应加热淬火装置,只对轮齿部位进行局部感应加热表面淬火。
工艺:将齿轮置于感应器内,通入交流电,轮齿温度达到860-9000C后,随即用水快速冷却,淬火后表面不得有裂纹。
目的:提高轮齿表面硬度和耐磨性,淬火后表面硬度可达到48-53HRC,淬硬层可达3-4mm。
回火:将齿轮放入炉中加热到200-2400C,保温约1h,出炉后在空气中冷却。
目的:消除淬火内应力,防止变形和开裂;获得稳定的组织,保证尺寸稳定性;
提高齿轮韧性,调整齿轮的强度和硬度,获得较好的综合力学性能。
4.3加工工艺分析
1、作为定位的基准内孔40H7表面粗糙度精度比基准端面的要求高,基准端面的粗糙度较粗,为5um。
但它对基准孔的端面圆跳动0.018um,比一般精度的齿轮要求高,因此在齿坯加工中,尚需留一定的余量进行精加工。
2、精加工孔和端面采用磨削的加工方法。
先以齿轮分度圆和端面作为定位基准磨孔,再以孔定位基准磨削面,控制端面圆跳动的要求,以确保齿形精加工用的精基准的精确度。
3、该齿轮精度要求较高,工序安排滚齿后应留有一定的磨齿的加工余量。
4.4定位基准
粗基准:毛坯外圆及端面
精基准:内孔及端面
4.5齿轮的加工顺序
下料后,锻造,然后去除锻造内应力,然后粗车成合适的形状,再精车,滚齿,做出齿轮的形状后在进行热处理,提高齿轮表面强度、硬度。
此后,再消除在淬火时产生的内应力,最后磨齿,精磨。
4.6齿轮的加工路线
齿轮的加工工艺路线:
下料——锻造——正火——粗加工——调质——半精加工——高频感应表面淬火+低温回火——精磨——成品
5、齿轮工艺过程
齿轮加工工艺过程具体如下表所示:。