稀土生产过程
稀土是怎么形成的

稀土是怎么形成的稀土是一种具有战略意义的金属,《美国新闻与世界报道》称,50年前,世界经济建立在钢、铝和铁之上,而今天,稀土金属正在重塑世界经济。
美国《连线》杂志称,稀土金属是21世纪科技的关键,如果没有它们,人们将不会有智能电话、混合动力车或者精确制导武器。
路透社的报道则举例说,丰田混合动力车普锐斯因节能而大受欢迎,但它所采用的电动马达和电池大量使用稀土金属。
独立商品咨询师、金属行业战略专家利夫特对路透社说,普锐斯是“世界上耗费稀土金属最多的产品”。
他称每部普锐斯发动机需要1公斤钕,每块电池需要10公斤到15公斤镧。
按经济学原理,商品的价格由商品的价值决定,同时受供求关系的影响,当某一势力对一种产品的供应量占有一定的比例时,就会形成某种程度的垄断,从而可以影响这种产品的价格。
铁矿石三巨头之所以敢年年提出令国际钢企发疯的涨价要求,正因他们垄断了世界铁矿石贸易量的70%,从而获得了铁矿石的定价权。
稀土是现代工业、国防及高新技术应用中极为重要的功能性材料,是一种极其珍贵的战略性资源,而中国又几乎是世界稀土唯一的供应商,在国际稀土贸易中所占份额远超铁矿石三巨头在国际铁矿石贸易中所占份额,为什么稀土的国际价格却连年走低呢?我们的稀土,到底比铁矿石差在哪儿呢?稀土一词是历史遗留下来的名称。
稀土元素是从18世纪末叶开始陆续发现,当时人们常把不溶于水的固体氧化物称为土。
稀土一般是以氧化物状态分离出来的,又很稀少,因而得名为稀土。
通常把镧、铈、镨、钕、钷、钐、铕称为轻稀土或铈组稀土;把钆、铽、镝、钬、铒、铥、镱、镥钇称为重稀土或钇组稀土。
也有的根据稀土元素物理化学性质的相似性和差异性,除钪之外(有的将钪划归稀散元素),划分成三组,即轻稀土组为镧、铈、镨、钕、钷;中稀土组为钐、铕、钆、铽、镝;重稀土组为钬、铒、铥、镱、镥、钇。
目前生产稀土金属常用的原料是它们的氯化物和氟化物。
(1)熔盐电解法工业上大批量生产混合稀土金属一般使用熔盐电解法。
稀土生产工艺流程图 +矿的开采技术要点
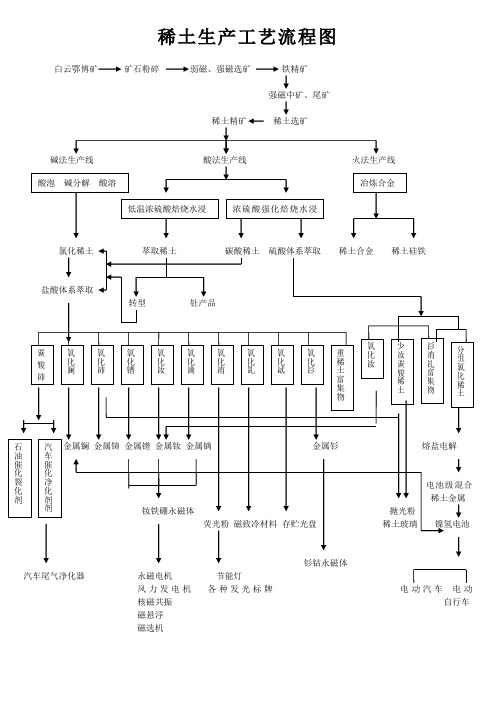
稀土生产工艺流程图白云鄂博矿 矿石粉碎 弱磁、强磁选矿 铁精矿强磁中矿、尾矿火法生产线汽车尾气净化器 永磁电机 节能灯风力发电机 各种发光标牌 电动汽车 电动核磁共振 自行车 磁悬浮磁选机稀土矿的开采技术和稀土矿开采方法介绍时间:2012-2-20 15:24:22 作者:稀土信息部点击:1606次网站电话:************稀土矿在地壳中主要以矿物形式存在,其赋存状态主要有三种:作为矿物的基本组成元素,稀土以离子化合物形式赋存于矿物晶格中,构成矿物的必不可少的成分。
这类矿物通常称为稀土矿物,如独居石、氟碳铈矿等。
作为矿物的杂质元素,以类质同象置换的形式,分散于造岩矿物和稀有金属矿物中,这类矿物可称为含有稀土元素的矿物,如磷灰石、萤石等。
呈离子状态被吸附于某些矿物的表面或颗粒间。
这类矿物主要是各种粘土矿物、云母类矿物。
这类状态的稀土元素很容易提取。
常用的稀土矿开采技术离子型稀土的技术是我国完全拥有的自主知识产权。
赣州有色冶金研究所是我国离子吸附型稀土矿的发现、命名和二代稀土提取工艺科技成果的主要享有单位。
时任赣州有色冶金研究所分管科研副所长、后任所长的丁嘉榆同志,作为离子型稀土矿第二代提取工艺的发明及应用的主要参与者、领导者,对这一事件的历史发展进程有着刻骨铭心的记忆。
应记者之约,丁嘉榆同志对这一历史事件进行了全面地、系统地回顾和总结。
时至1970年,在过去长达175年的稀土矿产资源开发利用史中,人们发现自然界中含稀土元素及其化合物的矿物多达200 种。
但真正实际有工业利用价值的稀土矿物原料却为数不多,数量约十种左右。
主要有独居石、铈硅石、氟碳铈矿、硅铍钇矿、磷钇矿、褐帘石、铌钇矿、黑稀金矿。
但这些矿物中却大部份含有一定数量的铀或钍,而且稀土矿物均以固态、矿物相矿物性态存在,它们往往是与放射性元素共生或伴生。
稀土矿开采方法介绍1、辐射选矿法主要利用矿石中稀土矿物与脉石矿物中钍含量的不同,采用γ-射线选矿机,使稀土矿物与脉石矿物分开。
稀土生产过程中常用的废气处理方法

稀土生产中废气的产生过程及组成稀土生产由于原、辅材料的不同,所采用的生产工艺也不尽一致。
但在生产流程的许多工序都会产生废气,如氟碳铈矿浓硫酸焙烧法产生的含氟废气、稀土氯化物熔盐电解产生的含氯废气、稀土硅铁合金火法冶炼废气等。
这些工序的共同特点是产生的废气量大、危害性大,对废气的处理工艺具有代表性。
①硫酸焙烧法处理氟碳铈镧矿所产生的工业废气中含有害物质较多,主要有氟化氢、三氧化硫、二氧化硫、氟化硅和硫酸雾等。
其产生过程如下:浓硫酸分解稀土精矿的化学反应是比较复杂的,在低温段(窑尾)的反应更为剧烈,因此,有部分挥发后的硫酸雾也随尾气排出。
此外,在焙烧窑的尾气中还有二氧化碳和少量固体颗粒(烟尘)。
②稀土氯化物熔盐电解产生的含氯废气主要是阳极产生的氯气。
其反应过程为:2C1——2e—→Cl2↑在结晶氯化稀土电解时或氯化稀土脱水不完全电解时,还会产生氯化氢气体:2RECl3+3H2O→RE2O3+6HCl↑RECl3+H2O→REOCl+2HCl↑③用电弧炉生产稀土硅铁合金过程中会产生大量烟气,烟气由二氧化碳、一氧化碳、氟化硅、低价硅氧化物、二氧化硫等组成。
这些成分主要来源于碳素炉衬和石墨电极参与反应、氟化钙与二氧化硅作用、硫酸盐的分解等。
(MeO)+C→[Me]+CO↑2(CaF2)+2(SiO2)→(2CaO·SiO2)+SiF4↑(SiO2)+[Si]→2SiO↑MeSO4△MeO+SO3↑此外,烟气中还含有大量的固体尘粒,也是硅铁合金生产废气中的重要害物。
④除上述工序产生废气外,由于在湿法冶炼中所使用的化工材料也比较多,如:盐酸、氟氢酸、氢氧化钠、硝酸、氨等,它们与物料发生反应时,易挥发或排出氯化氢、氟化氢气体及硝酸雾、氨气等。
这些有害气体不但对生产净化设备有极强的腐蚀作用,而且对人体和动植物等危害较大,对环境的影响也非常突出。
稀土生产中产生的主要废气组成如下表,可见,稀土生产工艺决定了它所排出的废气中是固态、液态和气态物质混合的烟气。
稀土生产与分离工业工艺流程

稀土生产与分离工业工艺流程一、稀土选矿选矿是利用组成矿石的各种矿物之间的物理化学性质的差异,采用不同的选矿方法,借助不同的选矿工艺,不同的选矿设备,把矿石中的有用矿物富集起来,除去有害杂质,并使之与脉石矿物分离的机械加工过程。
当前我国和世界上其它国家开采出来的稀土矿石中,稀土氧化物含量只有百分之几,甚至有的更低,为了满足冶炼的生产要求,在冶炼前经选矿,将稀土矿物与脉石矿物和其它有用矿物分开,以提高稀土氧化物的含量,得到能满足稀土冶金要求的稀土精矿。
稀土矿的选矿一般采用浮选法,并常辅以重选、磁选组成多种组合的选矿工艺流程。
内蒙古白云鄂博矿山的稀土矿床,是铁白云石的碳酸岩型矿床,在主要成分铁矿中伴生稀土矿物(除氟碳铈矿、独居石外,还有数种含铌、稀土矿物)。
采出的矿石中含铁30%左右,稀土氧化物约5%。
在矿山先将大矿石破碎后,用火车运至包头钢铁集团公司的选矿厂。
选矿厂的任务是将Fe2O3从33%提高到55%以上,先在锥形球磨机上磨矿分级,再用圆筒磁选机选得62~65%Fe2O3的一次铁精矿。
其尾矿继续进行浮选与磁选,得到含45%Fe2O3以上的二次铁精矿。
稀土富集在浮选泡沫中,品位达到10~15%。
该富集物可用摇床选出REO 含量为30%的粗精矿,经选矿设备再处理后,可得到REO60%以上的稀土精矿。
二、稀土冶炼方法稀土冶炼方法有两种,即湿法冶金和火法冶金。
湿法冶金属化工冶金方式,全流程大多处于溶液、溶剂之中,如稀土精矿的分解、稀土氧化物、稀土化合物、单一稀土金属的分离和提取过程就是采用沉淀、结晶、氧化还原、溶剂萃取、离子交换等化学分离工艺过程。
现应用较普遍的是有机溶剂萃取法,它是工业分离高纯单一稀土元素的通用工艺。
湿法冶金流程复杂,产品纯度高,该法生产成品应用面广阔。
火法冶金工艺过程简单,生产率较高。
稀土火法冶炼主要包括硅热还原法制取稀土合金,熔盐电解法制取稀土金属或合金,金属热还原法制取稀土合金等。
稀土提取工艺
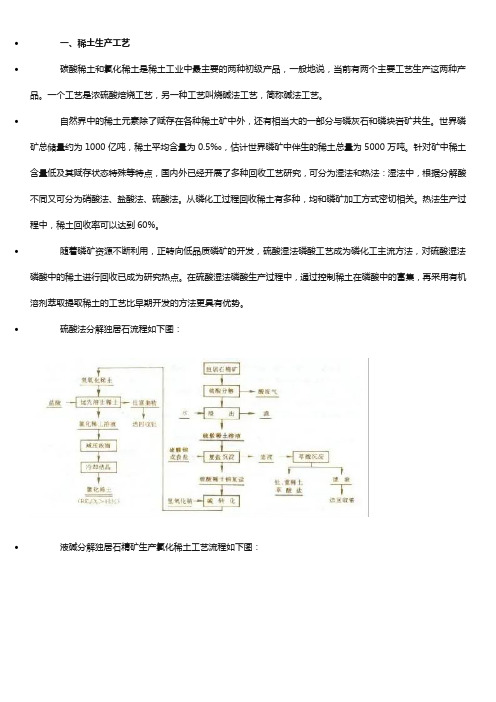
•一、稀土生产工艺•碳酸稀土和氯化稀土是稀土工业中最主要的两种初级产品,一般地说,当前有两个主要工艺生产这两种产品。
一个工艺是浓硫酸焙烧工艺,另一种工艺叫烧碱法工艺,简称碱法工艺。
•自然界中的稀土元素除了赋存在各种稀土矿中外,还有相当大的一部分与磷灰石和磷块岩矿共生。
世界磷矿总储量约为1000亿吨,稀土平均含量为0.5‰,估计世界磷矿中伴生的稀土总量为5000万吨。
针对矿中稀土含量低及其赋存状态特殊等特点,国内外已经开展了多种回收工艺研究,可分为湿法和热法:湿法中,根据分解酸不同又可分为硝酸法、盐酸法、硫酸法。
从磷化工过程回收稀土有多种,均和磷矿加工方式密切相关。
热法生产过程中,稀土回收率可以达到60%。
•随着磷矿资源不断利用,正转向低品质磷矿的开发,硫酸湿法磷酸工艺成为磷化工主流方法,对硫酸湿法磷酸中的稀土进行回收已成为研究热点。
在硫酸湿法磷酸生产过程中,通过控制稀土在磷酸中的富集,再采用有机溶剂萃取提取稀土的工艺比早期开发的方法更具有优势。
•硫酸法分解独居石流程如下图:•液碱分解独居石精矿生产氯化稀土工艺流程如下图:•二、稀土萃取工艺• 1.硫酸溶解度•铈组(硫酸复盐难溶)—镧、铈、镨、钕和钷;•铽组(硫酸复盐微溶)—钐、铕、钆、铽、镝和钬;•钇组(硫酸复盐易溶)—钇、铒、铥、镱、镥和钪。
• 2.萃取分离•轻稀土(P204弱酸度萃取)—镧、铈、镨、钕和钷;•中稀土(P204低酸度萃取)—钐、铕、钆、铽和镝;•重稀土(P204中酸度萃取)—钬、钇、铒、铥、镱、镥和钪。
• 3.萃取工艺简介在分离稀土元素的工艺流程中,由于17种元素的物理性质和化学性质极其相近,且稀土元素同伴生杂质元素较多,因此,其萃取流程是较为复杂的,常用的萃取工艺有三种:分步法、离子交换和溶剂萃取。
• 4.分步法•利用化合物在溶剂中溶解度的差别进行分离提纯的方式称为分步法。
从钇(Y)到镥(Lu),所有天然存在的稀土元素间的单一分离,包括居里夫妇发现的镭,都是用这种方法分离的。
稀土分离冶炼工艺流程图

白云鄂博矿床的物质成分白云鄂博矿床物质成分极为复杂,已查明有73种元素,170多种矿物。
其中,铌、稀土、钛、锆、钍及铁的矿物共近60种,约占总数的35%。
主要矿石类型有块状铌稀土铁矿石、条带状铌稀土铁矿石、霓石型铌稀土铁矿石、钠闪石型铌稀土铁矿石、白云石型铌稀土铁矿石、黑云母型铌稀土铁矿石、霓石型铌稀土矿石、白云石型铌稀土矿石和透辉石型铌矿石。
稀土生产工艺流程图白云鄂博矿矿石粉碎弱磁、强磁选矿铁精矿强磁中矿、尾矿稀土精矿稀土选矿风力发电机各种发光标牌电动汽车电动核磁共振自行车磁悬浮磁选机稀土精矿硫酸法分解(decomposition of rare earth concentrate by suIphuric acid method)稀土精矿用硫酸处理、生产氯化稀土或其他稀土化合物的稀土精矿分解方法。
本法具有对原料适应性强、生产成本低等优点,是稀土精矿工业上常用的分解方法,广泛用于氟碳铈矿精矿、独居石精矿和白云鄂博混合型稀土矿精矿的分解。
主要有硫酸化焙烧一溶剂萃取法、硫酸分解一复盐沉淀法、氧化焙烧一硫酸浸出法三种工艺。
硫酸化焙烧-溶剂萃取?? 主要用于分解白云鄂博混合型稀土矿精矿生产氯化稀土。
白云鄂博混合型稀土矿精矿成分复杂,属于难处理矿,其典型的主要成分(%)为:RE2O350~55,P2.5~3.5,F7~9,Ca7~8,Ba1~4,Fe3~4,ThO2约0.2。
精矿中放射性元素钍和铀含量低,冶炼的防护要求不高,适于用硫酸化焙烧法分解。
原理?? 经瘩细的稀土精矿与浓硫酸混合后加热焙烧到423~673K温度时,稀土和钍均生成水溶性的硫酸盐。
氟碳铈矿与硫酸的主要反应为:2REFCO3+3H2SO4=RE2(SO4)3+3HF↑+2CO2+2H2O独居石与硫酸的主要反应是:2REPO4+3H2SO4=RE2(SO4)3+2H3PO4Th3(PO4)4+6H2SO4=3Th(SO4)2+4H3PO4铁、钙等杂质也生成相应的硫酸盐。
稀土提取及分离
稀土提取及分离稀土是指一组具有特殊化学性质的17种元素,包括镧系、铈系、钕系、钐系、铽系、镝系、钬系、铒系、铥系和镱系元素。
这些元素在工业生产中具有广泛的应用,尤其是在高科技领域,如电子、光电、医疗器械等。
稀土的提取及分离是稀土产业链的重要环节,本文将对其进行详细介绍。
稀土的提取主要有矿石浸取法和离子交换法两种方法。
矿石浸取法是将稀土矿石经过破碎、磨矿等工艺处理后,通过酸浸法或碱浸法提取稀土。
其中,酸浸法适用于含磷的稀土矿石,而碱浸法适用于含碳酸盐的稀土矿石。
离子交换法则是利用离子交换树脂将稀土离子从溶液中吸附,并通过洗脱和再生等步骤获得稀土产品。
稀土的分离主要是通过溶剂萃取法和离子交换法实现的。
溶剂萃取法是利用有机相和水相之间的分配系数差异,通过萃取剂将稀土离子从溶液中提取到有机相中,然后通过洗脱和分离等步骤获得纯度较高的稀土产品。
离子交换法则是利用离子交换树脂的选择性吸附作用,根据稀土离子的不同特性,通过洗脱和再生等步骤实现稀土的分离。
稀土的提取及分离过程中需要注意的是,稀土元素之间在物理和化学性质上的相似性较高,因此在分离过程中往往会产生难以分离的混合物。
为了克服这一问题,可以通过改变萃取条件、选择适当的分离剂和控制溶液pH值等方法来实现稀土的有效分离。
稀土的提取及分离过程还需要考虑环境保护的因素。
稀土矿石的开采和提取过程中会产生大量废水和废弃物,其中含有重金属和放射性物质等有害物质。
因此,在稀土提取及分离过程中需要采取相应的环境保护措施,如废水处理和废弃物的合理处置,以减少对环境的污染。
稀土的提取及分离是稀土产业链的重要环节,通过矿石浸取法、离子交换法、溶剂萃取法等多种方法可以实现稀土的提取及分离。
在实际操作中,需要充分考虑稀土元素之间的相似性,选择合适的分离剂和控制条件来实现有效的分离。
同时,还需要关注环境保护的问题,通过合理的废水处理和废弃物处置等措施,减少对环境的影响。
稀土产业的发展离不开稀土的提取及分离技术的进步和创新,将为我国高科技产业的发展提供重要支撑。
稀土萃取工艺流程原理
稀土萃取工艺流程原理 稀土元素在现代工业中扮演着重要角色,广泛应用于电子产业、石油化工、冶金工业等领域。
为了获得高纯度的稀土元素,人们开发出了各种稀土萃取工艺流程。
本文将详细介绍稀土萃取工艺流程的原理,并通过实例帮助读者更好地理解。
一、稀土萃取工艺流程概述 稀土萃取工艺流程是通过萃取剂与含稀土溶液之间的反应来实现稀土元素的提取。
一般情况下,稀土元素与其他杂质离子混合在含稀土溶液中,通过萃取工艺可以将其分离出来。
萃取工艺主要包括三个步骤:萃取、洗涤和回收。
萃取是稀土萃取工艺流程的第一步,也是最主要的步骤之一。
在这一步骤中,萃取剂与含稀土溶液发生化学反应,稀土元素被转移至萃取剂中形成络合物,而杂质离子则留在残余液中。
选择合适的萃取剂是关键,一般常用的有二烷基脲类、有机酸类、腈类等。
此外,温度、pH值以及浓度等因素也会影响稀土元素的萃取效果。
举个例子,以稀土钕为例,当含钕溶液与二烷基脲类萃取剂进行接触时,二烷基脲类萃取剂中的有机锆,可以与钕形成络合物,而杂质离子无法被提取,从而实现了钕的分离。
洗涤是稀土萃取工艺流程的第二步。
在这一步骤中,目的是去除附着在萃取剂上的杂质离子,使得稀土元素得以纯化。
通常采用不同浓度的酸性溶液进行洗涤,酸性环境有助于去除杂质。
继续以上面的例子,通过将稀土钕络合物所在的萃取剂接触酸性溶液,可以使杂质离子与溶液中的酸发生反应,从而实现了杂质的去除,使得钕元素得到纯化。
回收是稀土萃取工艺流程的最后一步,目的是将萃取剂中的稀土元素从络合物中分离出来。
此步骤通常采用水解、还原或蒸馏等方法来进行。
接着以上面的例子,可以通过加热水解或还原反应,将稀土钕所形成的络合物分解,并得到纯化的稀土钕元素。
稀土萃取工艺流程是通过萃取剂与含稀土溶液之间的反应实现稀土元素的提取的一种方法。
其主要包括萃取、洗涤和回收三个步骤。
在萃取过程中,合适的萃取剂和适宜的条件对于稀土元素的提取至关重要。
稀土矿石的开采和加工方法
,
汇报人:
单击此处添加目录项标题
稀土矿石的开采
稀土矿石的加工方法
稀土矿石的分离与提纯
稀土矿石的回收与再利用
稀土矿石的环保与安全问题
目录
添加章节标题
01
稀土矿石的开采
02
露天开采
概述:露天开采是一种常见的稀土矿石开采方式,适用于地表浅层、矿体分布较广的稀土矿床。
开采步骤:首先进行矿区规划,然后进行矿体剥离,接着进行矿石破碎和运输,最后进行矿石加工和销售。
加强环保宣传教育,提高员工环保意识
安全防护措施
应急预案:制定应急预案,对可能出现的安全事故进行及时处理,以减少人员伤亡和财产损失。
穿戴防护服:工作人员必须穿戴符合规定的防护服,包括但不限于防尘口罩、手套、眼镜等。
定期检查:对开采和加工设备进行定期检查,确保设备正常运行,防止因设备故障导致的安全事故。
破碎:将矿石破碎成小块,便于后续处理
研磨:将破碎后的矿石研磨成粉末,提高后续处理的效率
磁选:利用磁性差异,将稀土元素与其他元素分离
混合法
稀土矿石的分离与提纯
04
离子交换法
原理:利用离子交换树脂选择性地吸附和交换稀土离子
过程:将稀土矿石粉碎、浸出、过滤、洗涤、烘干、煅烧、研磨、混合、压片、装柱、洗脱、浓缩、结晶、分离、烘干、包装
优点:操作简单、成本低、效率高、环保
应用:广泛应用于稀土矿石的分离与提纯
溶剂萃取法
添加标题
添加标题
添加标题
添加标题
优点:操作简单,成本低,适用于大规模生产
原理:利用有机溶剂对稀土离子的溶解度差异进行分离
缺点:有机溶剂对环境有影响,需要处理
稀土生产工艺流程图
稀土生产工艺流程图白云鄂博矿 矿石粉碎 弱磁、强磁选矿 铁精矿强磁中矿、尾矿火法生产线汽车尾气净化器 永磁电机 节能灯风力发电机 各种发光标牌 电动汽车 电动核磁共振 自行车磁悬浮磁选机看稀土原矿生产新闻中有离子型稀土矿原矿“堆浸工艺”这个词,是怎样的工艺?怎么翻译成英文或日文?堆浸提金是指将低品位金矿石或浮选尾矿在底垫材料上筑堆,通过氰化钠溶液循环喷淋,使矿石中的金、银溶解出来。
含金贵液用活性炭吸附、锌置换沉淀或直接电解沉积等方法回收金,提金后的尾渣经消毒后排放。
堆浸法提金具有工艺简单、操作容易、设备少、动力消耗少、投资省、见效快、生产成本低等特点。
堆浸用于处理0.5-3g/t的低品位矿石,金的回收率50-80%,甚至能达到90%。
因此,堆浸法使原来认为无经济价值的许多小型金矿、低品位矿石、尾矿或废石现在都能得以经济回收。
我国在二十世纪八十年代将堆浸法广泛用于工业生产。
堆浸法适合处理以下几种矿产资源:1、规模较大,以前认为不能利用的低品位金银矿;2、矿山开采过程中剥离的低品位含金“废石”;3、地质坑探和矿山掘进中采掘出的中低品位含金矿石;4、含金品位稍高,但规模较小,不宜建机械化选厂的金银矿;5、采用常规氰化法处理经济上不利的金矿;6、含金的冶炼烧渣、高品位尾矿和含有金的大型废石场。
堆浸提金生产工艺主要由堆浸场地的修筑、矿石的预处理(破碎或制粒)、筑堆、喷淋浸出、含金贵液中金的回收以及废矿堆的消毒、卸堆等几部分组成。
堆浸的生产成本:尾矿堆浸成本度大约在30-40元/吨,原矿堆浸成本大约在40-50元/吨.我想问一下现在离子型稀土矿的开采方法是什么方法成本怎样计算需要什么试剂?????????????离子型稀土第一代提取工艺,可简述为"异地提取工艺",或归结为"池浸工艺"。
其主要工艺过程为:表土剥离→开挖含矿山体、搬运矿石→浸矿池→将按一定比例(浓度要求)配置的电解质溶液作为"洗提剂"或"浸矿剂",加入浸矿池,溶液对池中含"离子相"稀土矿石进行"渗滤洗提"或"淋洗" →溶液中活泼离子与稀土离子交换,"离子相"稀土从含矿载体矿物中交换出来,成为新状态稀土;加入"顶水",获含稀土母液;母液经管道或输液沟流入集液池或母液池,然后进入沉淀池;浸矿后废渣从浸矿池中清出,异地排放→在沉淀池中加入沉淀剂、除杂剂,使稀土母液中稀土除杂、沉淀,获混合稀土;池中上清液经处理后,返回浸矿池,作"洗提剂"循环使用→混合稀土经灼烧,获纯度≥92%的混合稀土氧化物。
- 1、下载文档前请自行甄别文档内容的完整性,平台不提供额外的编辑、内容补充、找答案等附加服务。
- 2、"仅部分预览"的文档,不可在线预览部分如存在完整性等问题,可反馈申请退款(可完整预览的文档不适用该条件!)。
- 3、如文档侵犯您的权益,请联系客服反馈,我们会尽快为您处理(人工客服工作时间:9:00-18:30)。
中国稀土火法冶金技术发展评述稀土火法冶金专业委员会一、稀土火法冶金技术发展概要1.稀土火法冶金发展历程稀土金属冶炼工艺研究是由瑞典化学家G.Mosander于1862年首次用于金属钠、钾还原无水氯化铈制备金属铈开始的,以后在1875年W.Hitekrand和T.Norton又首次用氯化物熔盐电解法制得了金属铈、镧和少量镨钕混合金属,到20世纪30年代末逐步发展了稀土氯化物和氟化物金属热还原和熔盐电解两大工艺技术开始工业生产混合稀土金属,当时主要是生产打火石(发火合金)。
稀土金属和合金冶炼工艺技术的进步、生产规模的扩大无不同市场新的需求和时代的科技进步相联系。
第二次世界大战后至20世纪60年代末美国等先进发达国家大力发展核技术,其中包括核技术需要的材料科学和技术,极大地促进了单一稀土元素分离工艺的发展,使离子交换法和溶剂萃取法分离单一稀土元素得到了发展,成为工业生产的方法,同时获得原子俘获截面小的金属钇和俘获截面大的金属钐、铕,发展了稀土氟化物钙热还原法和氧化钐、氧化铕直接用镧还原-蒸馏法分别制备金属钇和金属钐、铕的工艺技术,这些成果基本上奠定了这两种工艺方法产业化的基础。
20世纪70年代,混合稀土金属在钢中应用,尤其在低合金钢管线钢上应用有了突破,使稀土在钢铁中应用的消耗量占到总消耗量的50%以上,从而推动了稀土氯化物熔盐电解法生产混合稀土金属产业化技术的发展,相继有德国Goldschmidt公司开发了5万安培的大型电解槽和我国上海跃龙化工厂10000安培电解工艺设备投入生产,世界和我国混合稀土金属的产量在20世纪70年代末分别达到8400吨和1200吨。
在稀土钢中应用突破进展的同时,稀土硅-镁球化剂得到了工业规模的应用。
我国利用包钢高炉渣为原材料以硅铁合金为还原剂在电炉中冶炼稀土硅铁合金的工艺技术得到很大发展,建立了专业生产厂,在20世纪70年代末产量达到了4000多吨。
20世纪70年代初钐钴永磁材料开发成功并很快达到了工业规模的应用,这一重要的市场动力,迅猛地促进了金属钐的工艺技术成果转为工业生产,从而使稀土氧化物还原-蒸馏工艺、设备达到产业化规模,单炉量由100克级到公斤级,到2000年已达到100公斤级,钐的回收率也由试验室的90%,提高到95%,金属钐的纯度由99%提高到99.95%。
20世纪80年代初日本住友金属公司开发成功NdFeB高性能永磁材料,由于其性能价格比的极大优势,市场需求异常强劲,年产量在最初的数年间成倍增长,市场动力推动了我国稀土氟化物体系氧化钕电解工艺、设备产业化的进程,电解槽规模由试验室100余安培提到了3000安培,到2000年末达到6000安培,2002年万安级电解槽已投入工业生产,且稀土技术经济指标和金属质量都大幅度提高,同时NdFeB永磁材料需要金属镝的市场扩大,使金属热还原法制备金属镝的工艺技术和设备也达到了产业化的规模,单炉产量达到百公斤级,直收率达到96%,金属镝纯度达99.5%。
20世纪90年代初镍氢二次电池成果开始产业化,由于其比容量高于镍镉二次电池且不会造成环境污染,很快打开市场且增长迅速,Ni/MH电池的市场需求极大地推动了电池阴极合金生产技术和设备的发展完善,主要表现在利用稀土氯化物熔盐体系电解,成功地生产出低镁、低铁的富镧或富铈混合稀土金属。
一般铁镁含量较前约低了一倍,满足了电池阴极合金的要求。
2002年电池级混合稀土金属产量已达4000多吨。
在此时期大磁致伸缩材料(TbDyFe合金)的应用也已打开了市场,年生产量由数公斤增加到数百公斤,这一应用市场推动了高纯稀土金属镝、铽的工艺技术的产业化,不仅生产规模单炉产量由百克级提高到数十公斤级,而且纯度达到99.5%~99.99%,2002年全国高纯金属镝和铽的产量分别达到500公斤和250公斤。
随着高新技术的发展,对稀土金属及合金的需求还将进一步扩大,从而定会促进稀土金属及合金制备工艺技术和设备的进一步发展。
2.稀土火法冶金技术分类和发展目标稀土火法冶金技术分为三大类:熔盐电解、金属热还原和火法提纯技术。
这三类工艺技术的发展目标是短流程、低消耗、高效益和利于环保。
二、稀土金属熔盐电解工艺技术发展概况和评述采用稀土氯化物熔盐体系(RCl3-KCl)电解工艺技术,以1000A级规模生产混合稀土金属是由奥地利Treibacher厂从20世纪50年代初开始的,电解槽型为上插石墨阳极,以铁棒为阴极,槽体是由耐火砖砌筑,在以后50年的发展中,电解规模扩大到10000A、50000A,槽型改进为以耐腐蚀的钨或钼为上插阴极,上插石墨多阳极,耐火砖砌筑槽体;阳极气体(含氯气和氯化物挥发物)经水淋洗和碱中和后排放;稀土氯化物原料由轻稀土全混氯化物原料改进为钕钐分组后(即不含变价元素Sm、Eu)的轻稀土氯化物原料,电流效率约提高5个百分点以上,在此基础上,由于元素Nd价高,又进一步采用Pr-Nd分离后,少Nd的混合稀土氯化物为原料进行电解,使电流效率进一步提高到55%~60%。
氟化物熔盐体系(RF3-LiF)电解稀土氧化物工艺技术,早期在20世纪60年代进行了试验研究,对于氟化物熔盐体系、电解温度、电极过程及稀土氧化物在该体系中的溶解度进行了大量的工作,证明稀土在氟化物熔盐体系中溶解损失和二次反应较少,与氯化物熔盐体系电解过程相比较,电流效率高一倍,电耗低50%以上,同时阳极气体(CO2、CO及微量的氟化合物)污染较轻,因此有很好的工业前景。
20世纪80年代至90年代,由于NdFeB永磁材料市场需求金属钕旺盛,促进了采用氟化物熔盐体系电解氧化钕生产金属钕的产业化进程。
在近20年中我国采用3000安培电解槽生产金属钕,2001年的产量达到6000多吨。
如此大的市场推动了万安级大型化电解槽的开发,以提高单槽产量、电解过程的机械化和自动化程度以及便于采取综合治理污染和电解渣的回收利用。
2000年开始研发万安级大型电解槽的工艺、槽型、电解过程自动化控制及回收处理阳极气体的措施,现已投入使用。
稀土金属熔盐电解工艺技术进展概况见表1。
自20世纪80年代以来,氯化物熔盐体系电解技术发展缓慢,奥地利Treibacher厂及德国Goldschmidt厂都停止了用该技术生产混合稀土金属,主要原因是环境污染,成本高,我国上海跃龙化工厂也停止了10000安培电解槽运行,除生产过程产生的氯气及氯盐挥发物污染环境外,电流效率低、电耗高(约为18~20度/公斤金属)和稀土回收率较低(80%~85%)也是该技术发展的障碍。
氟化物熔盐体系电解稀土氧化物生产稀土金属的技术在解决了耐氟盐腐蚀的槽体材料后发展迅速,电解过程实现了自动化控温、加料和真空虹吸出金属,综合处理回收阳极气体,防止了大气污染。
技术经济指标如电流效率达到85%左右,稀土回收率90%以上,金属钕的质量满足了高性能NdFeB永磁材料的要求,且具有较好的均匀性和一致性。
表1 稀土熔盐电解工艺技术进展概况三、金属热还原法制备稀土金属的技术发展概况和评述根据稀土金属的熔点、沸点不同,金属热还原制备稀土金属的技术大致分为三种:一是针对轻稀土金属如Pr、Nd熔点较低,但沸点很高(即在标准状态下,饱和蒸气压很低)的性质,适合用它们的氯化物如NdCl3用金属钙在1150℃还原(2NdCl3(液)+3Ca(液) = 2Nd (液)+3CaCl2(液))获得金属钕。
该项技术在20世纪70年代进行过实验室研究工作,到20世纪80年代由于氧化物电解技术成功地用于工业生产,而没有进一步完善;稀土氯化物热还原的另一实例是氯化钇在1000℃锂热气相还原(YCl3(气)+3Li(气)=Y(固)+3LiCl(气))得固态粉末状金属钇,该项技术也只进行了实验室工作,并没有得到工业应用;二是针对沸点很低(即标准状态下,饱和蒸气压很高)的稀土金属如Sm、Eu、Yb、Tm,可用其氧化物为原料用金属镧或混合轻稀土金属作还原剂,进行还原-蒸馏(如在1450℃,Sm2O3(固)+2La(液)=2Sm(气)+La2O3(固)),在炉子的冷凝区得到固状金属。
这种技术由于金属钐的市场需求,已工业化;三是针对沸点低、熔点很高的稀土金属如Dy、Er、Y、Lu的性质,适合用它们的氟化物以金属钙为还原剂进行钙热直接还原(如在1500℃,2YF3(液)+3Ca(液)=2Y(液)+3CaF2(液)),或者用中间合金法即钙热还原过程中加入熔点较低的合金组元如镁使其与高熔点的稀土金属形成熔点较低的合金,同时加入氯化钙助熔剂,以降低渣的熔点,这样还原温度可在约980℃~1000℃下进行,还原后得到的稀土金属镁合金再进行真空蒸馏除去镁而得到海绵态的稀土金属。
整个反应为:YF3(固)+Ca(液)+Mg(液)+CaCl2(液)=YMg(液)+CaF3oCaCl2(液)Ymg→Y(海绵体)+Mg(气.固)中间合金法生产高熔点的重稀土金属已工业化,2002年北京有色金属研究总院稀土材料国家工程研究中心用此法生产用于NdFeB永磁材料的金属镝还原得到的镝镁中间合金单炉产量达100公斤,合金单炉装料量达1000公斤,金属镝的回收率达96%以上,金属镝的纯度Dy/TREM>99.5%,非稀土杂质分析见表2。
表2 中间合金法生产的金属镝中非稀土杂质分析(%,质量分数)四、稀土氧化物的直接还原-蒸馏技术进展和评述金属钐、铕、镱、铥在真空度小于10-3乇时,其蒸气压为1mmHg时的温度都比金属镧、铈的熔点低2~3倍,因此可用还原-蒸馏反应:RE2O3(固)+2La(液)→2R(气)+La2O3(固)获得相应的稀土金属。
该反应平衡时的产率是由它的平衡常数决定的,即lgP=A-B/T,因此对于不同蒸气压值的还原-蒸馏炉料,采用不同的还原-蒸馏温度,以期提高产率。
近年来由于钐钴永磁合金工业的发展,该工艺技术发展很快。
为了降低成本,还原剂采用镧铈混合稀土金属,普遍使用大功率中频感应炉,单炉产量由最初100克级、公斤级到100公斤,且金属回收率提高到95%以上,该工艺技术进展见表3。
表3 稀土氧化物的直接还原-蒸馏技术进展表3说明该工艺技术对于蒸气压较高的稀土金属如Sm、Eu、Yb、Tm是成功的,但对于制备金属镝、钬和铒,由于它的蒸气压值远低于上述金属蒸气压值,还原-蒸馏的反应平衡常数小,需要更高的温度(1650~1750℃)、更长的蒸馏时间,稀土金属的直收率低,产率也低,因此该技术对于制备金属Dy、Ho、Er没有获得工业上的应用。
五、稀土金属合金冶炼工艺技术的进展和评述稀土合金基本上可分为两类:一是中间合金,其特点是稀土含量较高、质脆,不是最终应用的产品,而是一种冶金和机械工业用的添加剂如RE-Si-Fe合金,它是用作钢铁的调质剂,另如RE-Mg、RE-Al中间合金,它是用作镁基和铝基合金的添加剂,它们一般是采用电解法或对掺法制得的;二是稀土与其它金属元素冶炼成的精密合金,如钕铁硼永磁合金、铽镝铁磁致伸缩合金,它们都具有一定的功能性,属功能材料。