多电机同步控制
简析多电机同步控制技术

简析多电机同步控制技术我国现代工业的不断发展与机械自动化技术的不断提高,很多生产场合都无法满足现代工业的发展要求,其电机控制系统要求多台电机共同驱动一台设备运作。
在整个生产过程中,应尽量满足现代工业的发展需求,确保这些电机能够协调运行,所以多电机同步控制技术的应用越来越广泛,这种技术在机械传动系统中,尤其是卷接机组中,可以通过多个电机向多个主要机组,传递其生产需要的动力,这种传动方式是控制方式上的一大创新。
一、多电机同步控制技术为了保证多电机能够实现同步控制,可以通过两种方式:机械方式和电方式。
在同步控制技术应用初期,机械同步控制技术在工业自动化生产中广泛应用。
因为机械控制方式与传动连接十分可靠,这种连接在应用初期得到了广泛应用,但是这种机械控制方式有一些常见的缺点,整个系统智能运用一台电机作为动力输出,所以动力分配到各个单元的动力功率都比较小,很难进行系统同的维修工作,且系统只能获得有效的传动范围[1]。
机械同步控制系统通过齿轮、皮带、链条这些零件进行传动,造成整个系统出现劣迹误差,所以在整个控制过程中,系统的控制精度很容易受到影响。
工作人员在一些精度要求较高的环境,电方式的多电机协调控制更加灵活,拥有更高的精度和稳定性,并能在生产实践中,逐渐被完善。
二、卷接机中同步控制技术的应用流程多电机同步控制技术一般选用YJ27卷接机组,其机械设备结构复杂,且各个鼓轮的转速间应保持精准的比例关系。
现阶段,相关单位采用的是传统的机械式齿轮传动方式对各个鼓轮进行同步控制,从而保证系统精度,对于高速环境下的齿轮,工作人员应为其设置润滑系统,确保整个系统的传动链不会太长,机构系统导致传动造成过大,在连续工作时,造成设备损坏,润滑齿轮箱容易出现漏油,以及传动误差较大等现象,设备的维修量会大幅增加,传动系统速度的波动会影响卷接机的运用功能[2]。
(一)偏差耦合结构控制工作人员以YJ27卷接机组的几个主要的工作鼓轮作为研究对象,并总结这些设备的机械传动关系,得出他们之间的速度比例,然后算出每个鼓轮的负载特点,将与之相对的永磁同步电动机作为这种设备的驱动电机,在一定环境中建立起一个鼓轮的同步控制系统的仿真模型,然后通过这种仿真模型的相关原理,运用改进型屏偏差耦合对结构进行控制,制定模糊滑模控制策略,这也是一种比较理想的控制方法[3]。
如何用一个PLC控制两个或多个伺服电机同步运行

如何用一个PLC控制两个或多个伺服电机同步运行
主电机速度改变时,其它伺服电机也跟着同步运行.
用第一个伺服驱动的输出控制第二个伺服驱动器,就可以实现同步运动了,只要要求不是太高这种方法完全可行;
同步分控制精度来确定控制方案的;
1:简单的多个伺服电机转速的同步,完全可以PLC不同输出口发同一个速度出去,这个不是跟随;
2:伺服驱动有脉冲输出功能,可以用这个控制下一台伺服的速度,这个是简单跟随;
3:相应速度和跟随精度要求很高,建议使用多轴运动控制器,以前见过派克的一款,假设有A/B/C三台伺服,使用PLC控制A伺服,然后A伺服有AB反馈,通过AB反馈到B伺服达到对B伺服的控制,再通过B伺服的反馈,接到C伺服,这样就可以达到伺服的联动及同步性,以上的联动可能有毫秒级的偏差.但是使用在一般的机床上是没有什么问题的;
方法一:在一台电机上安装编码器,通过编码器的反馈去控制进另一台电机,来达到同步;
方法二:利用运动型控制PLC,里面带有电子凸轮机构,可以进行同步跟踪控制;。
c 多电机同步算法
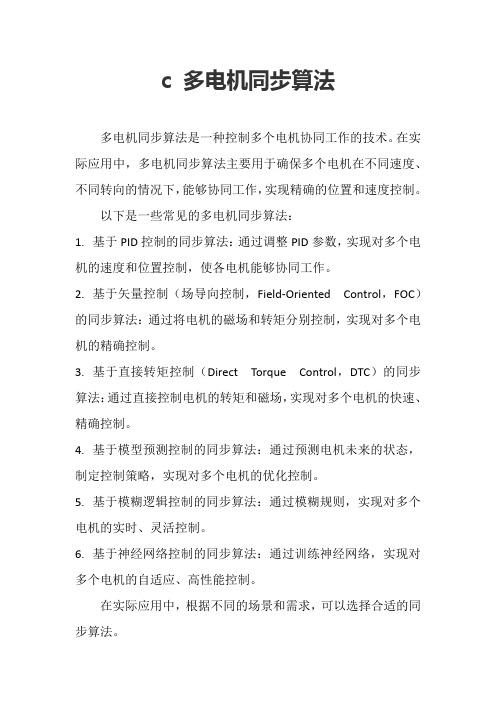
c 多电机同步算法
多电机同步算法是一种控制多个电机协同工作的技术。
在实际应用中,多电机同步算法主要用于确保多个电机在不同速度、不同转向的情况下,能够协同工作,实现精确的位置和速度控制。
以下是一些常见的多电机同步算法:
1.基于PID控制的同步算法:通过调整PID参数,实现对多个电机的速度和位置控制,使各电机能够协同工作。
2.基于矢量控制(场导向控制,Field-Oriented Control,FOC)的同步算法:通过将电机的磁场和转矩分别控制,实现对多个电机的精确控制。
3.基于直接转矩控制(Direct Torque Control,DTC)的同步算法:通过直接控制电机的转矩和磁场,实现对多个电机的快速、精确控制。
4.基于模型预测控制的同步算法:通过预测电机未来的状态,制定控制策略,实现对多个电机的优化控制。
5.基于模糊逻辑控制的同步算法:通过模糊规则,实现对多个电机的实时、灵活控制。
6.基于神经网络控制的同步算法:通过训练神经网络,实现对多个电机的自适应、高性能控制。
在实际应用中,根据不同的场景和需求,可以选择合适的同步算法。
需要注意的是,多电机同步算法的设计和实现需要考虑电机的特性、控制器的性能以及系统的稳定性等因素。
多电机同步操作的常识

多电机同步操作的常识多电机同步操作是指多个电机在同一工作环境下相互配合、协调工作,以实现其中一特定任务。
在很多工业生产场景中,例如自动化生产线、机械加工、食品加工等,常常需要多个电机同时工作,以提高生产效率和产品质量。
下面是关于多电机同步操作的一些常识。
1.同步操作的原理:多电机同步操作的关键在于准确控制每个电机的速度、位置和转矩。
通过给每个电机安装编码器或位置传感器,可以实时获取电机的实际运行状态,再根据需求在控制器中进行运算和调整,使得每个电机在时间上保持一致的运动方式。
2.控制方式:多电机同步操作可以通过两种控制方式实现,分别是集中式控制和分布式控制。
集中式控制是将所有电机连接到一个中央控制器,由中央控制器发送指令给每个电机,控制电机的运行。
而分布式控制则是将控制器安装在每个电机上,它们之间通过通信网络进行数据交换和指令传递。
3.控制算法:多电机同步操作的控制算法可以分为两类,即开环控制和闭环控制。
开环控制是指根据预先设定的运动规律和时间序列,通过发送相应的电机指令来控制电机的运行。
闭环控制则是通过不断地反馈电机的实际运行状态,并与预期的运行状态进行比较,对电机的运行进行动态调整和纠正。
4.传动系统的设计:多电机同步操作的设计中,传动系统的选择和设计非常重要。
传动系统包括了电机、减速器、传动带、链条和连杆等组成部分。
它们的选用和调整应能够适应电机的运行要求,以确保电机在运行中具有足够的扭矩和精确的位置转动。
5.同步误差的控制:在多电机同步操作中,由于工艺差异和系统扰动等原因,不同电机之间的运行状态很难完全一致。
此时需要通过控制器不断检测和调整电机的运行状态,以及时纠正同步误差。
常用的同步误差控制方法有前馈控制、自适应控制和模糊控制等。
6.安全保护措施:由于多电机同步操作通常涉及高功率和高速运动,因此在设计和使用中需要采取一些安全保护措施。
例如,为每个电机配备过载保护装置,当电机承受过大的载荷时能及时停止电机的运行。
舞台机械控制系统多电机同步控制分析

舞台机械控制系统多电机同步控制分析艺术表演离不开剧场的支撑,然而,在剧场中也不可缺少舞台机械。
它空间位置变化丰富、速度快慢不一,形式变化多端,所以,如何的控制舞台效果,就需要从舞台机械控制系统入手,多电机同步控制系统能够很好的满足以上多样的舞台需求,所以,必须要引起重视。
标签:舞台机械;控制系统;多电机;同步控制在控制舞台的时候,不但要依靠电机驱动装置,在舞台控制中,电机同步控制技术也是其中的核心技术之一,旋转台、防火幕、升降台等舞台设施都要由多台电机一同完成控制。
一旦没有协调控制多台电机,对演出效果必将带来很大的影响。
所以,文章通过对舞台机械控制系统多电机同步控制相关内容进行了分析。
1 多电机同步控制的相关阐述这种控制指的是在确保系统快速性与高精度的基础上,令多个电机一同工作。
电控制与机械控制是两种主要的控制方式。
初期的控制系统,经常对机械同步控制方式进行应用,对机械的传动装置进行应用,将各个运动部分连接到一块,进而完成多轴同步的目的,能够非常简单的完成这种同步操作,难度在电气系统设计中较少,所以,在设备相对固定且对控制精度要求低的场合得到了有效的应用。
机械同步控制方法在上个设计所搭建的舞台机械控制系统中得到了大量的应用。
然而,在科技不断发展的推动下,极大的提升了人们的生活质量,也将越来越高的精度要求抛向了同步控制,此外,随着电机控制技术的不断发展,从而能够同步完成多台电机的驱动,从而将同步控制精度和质量提升,这就是我们所讲的电控方式。
应用一台电机驱动电控方式的各个轴,利用主控制器,确保每个轴的电机能够协调工作,进而同步运行。
同机械控制方式进行比较,电控方式控制精度会更高,较大的同搭建灵活性,能够非常容易的改动设备,能够低成本的完成设备的维护。
2 具体的控制对策分析2.1 主从式控制在跟随原理的串联运行方式的基础上发展起来了主从控制,简单而言,就是将下一台电机的速度输入用上一台电机的速度输出,就是主动电机的速度变化由从动单机进行跟踪,进而完成同步的目的。
浅析多电机的同步控制策略析

浅析多电机的同步控制策略析摘要:本文分析了多电机同步控制技术,并讨论了控制策略和控制策略比较,同时展望了多电机的同步控制特性,如何控制多电机的同步精度已成为工业控制中的关键技术。
基于同步控制技术的理论,设计了同步控制系统的硬件平台。
在硬件平台的基础上,设计了软件部分。
通过改进同步控制算法,提高了同步精度。
关键词:多电机;同步控制;策略一、引言随着现代科学技术的发展和机电一体化水平的提高,电机已成为现代工业自动化系统中的重要执行机构。
电机由于其结构紧凑、控制方便、运行稳定、响应快等优良特性,应用于自动化程度高的场合,需要对印刷机械、制造等速度、位置、力矩等进行精确控制。
造纸机械、纺织机械、工业机器人、高速电梯、数控机床等重要行业得到广泛应用。
在许多工业自动化系统中,常常需要同时使用多个电机。
当电机之间存在速度和位置约束时,需要采用适当的控制策略来协调各电机的运行。
为了满足实际需要。
二、多电机同步控制技术多电机同步控制技术有着广泛的应用,如科学、自然科学、工程和社会。
同步控制技术是影响产品质量和生产效率的关键因素。
所谓的电机同步是指系统中的每个电机必须根据要求在自身运行和其他电机运行之间保持一定的关系。
通常有三种类型的不变关系:(1)在系统中的所有电机的速度或位移被保持相同,它是一个同步控制系统里最简单的系统。
(2)同步控制的多台电机的速度或角位移,维持一个不变的比例系数。
例如,在许多情况下,系统中的各个电机速度或位移并不要求保持同一个数据,但要求各台电机之问维持一定的比值。
(3)此外,除了上述两种情况外,还有第三种情况,在某些生产情况下,要求电机之间的速度或位移保持一个固定的差值,而不是要求它们之间保持一种比例系数。
同步控制系统的判断基于两个不同:同步差值和跟踪差值。
同步差异是电机之间的速度或位移的差异。
它反映了不同电机之间的同步。
跟踪差值是单台电机的输出值和给定值的比较,他反应的是电机本身对设定值的响应情况。
多永磁电机传动系统的同步控制策略研究
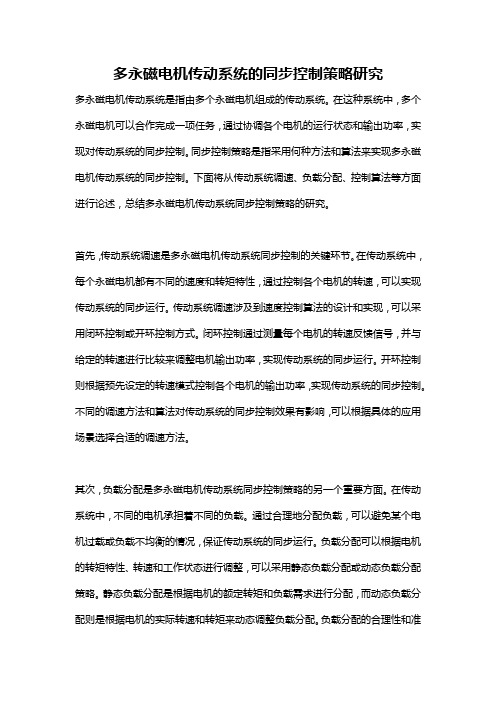
多永磁电机传动系统的同步控制策略研究多永磁电机传动系统是指由多个永磁电机组成的传动系统。
在这种系统中,多个永磁电机可以合作完成一项任务,通过协调各个电机的运行状态和输出功率,实现对传动系统的同步控制。
同步控制策略是指采用何种方法和算法来实现多永磁电机传动系统的同步控制。
下面将从传动系统调速、负载分配、控制算法等方面进行论述,总结多永磁电机传动系统同步控制策略的研究。
首先,传动系统调速是多永磁电机传动系统同步控制的关键环节。
在传动系统中,每个永磁电机都有不同的速度和转矩特性,通过控制各个电机的转速,可以实现传动系统的同步运行。
传动系统调速涉及到速度控制算法的设计和实现,可以采用闭环控制或开环控制方式。
闭环控制通过测量每个电机的转速反馈信号,并与给定的转速进行比较来调整电机输出功率,实现传动系统的同步运行。
开环控制则根据预先设定的转速模式控制各个电机的输出功率,实现传动系统的同步控制。
不同的调速方法和算法对传动系统的同步控制效果有影响,可以根据具体的应用场景选择合适的调速方法。
其次,负载分配是多永磁电机传动系统同步控制策略的另一个重要方面。
在传动系统中,不同的电机承担着不同的负载。
通过合理地分配负载,可以避免某个电机过载或负载不均衡的情况,保证传动系统的同步运行。
负载分配可以根据电机的转矩特性、转速和工作状态进行调整,可以采用静态负载分配或动态负载分配策略。
静态负载分配是根据电机的额定转矩和负载需求进行分配,而动态负载分配则是根据电机的实际转速和转矩来动态调整负载分配。
负载分配的合理性和准确性对传动系统的同步控制效果有着重要的影响,需要根据实际情况进行研究和调整。
最后,控制算法是实现多永磁电机传动系统同步控制的核心。
传统的控制算法包括PID控制、模糊控制和神经网络控制等方法。
PID控制是一种经典的控制方法,通过调整比例、积分和微分系数来实现对传动系统的同步控制。
模糊控制则采用模糊集合和模糊推理来处理传动系统的非线性和不确定性,实现同步控制。
两台电机如何通过变频器实现同步控制呢
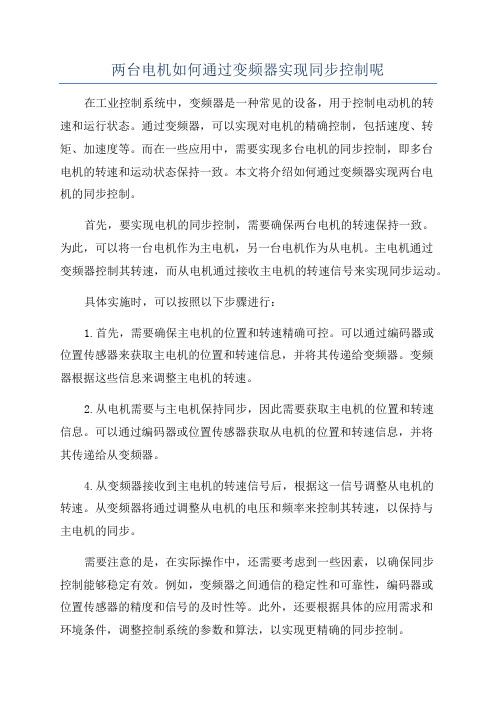
两台电机如何通过变频器实现同步控制呢在工业控制系统中,变频器是一种常见的设备,用于控制电动机的转速和运行状态。
通过变频器,可以实现对电机的精确控制,包括速度、转矩、加速度等。
而在一些应用中,需要实现多台电机的同步控制,即多台电机的转速和运动状态保持一致。
本文将介绍如何通过变频器实现两台电机的同步控制。
首先,要实现电机的同步控制,需要确保两台电机的转速保持一致。
为此,可以将一台电机作为主电机,另一台电机作为从电机。
主电机通过变频器控制其转速,而从电机通过接收主电机的转速信号来实现同步运动。
具体实施时,可以按照以下步骤进行:1.首先,需要确保主电机的位置和转速精确可控。
可以通过编码器或位置传感器来获取主电机的位置和转速信息,并将其传递给变频器。
变频器根据这些信息来调整主电机的转速。
2.从电机需要与主电机保持同步,因此需要获取主电机的位置和转速信息。
可以通过编码器或位置传感器获取从电机的位置和转速信息,并将其传递给从变频器。
4.从变频器接收到主电机的转速信号后,根据这一信号调整从电机的转速。
从变频器将通过调整从电机的电压和频率来控制其转速,以保持与主电机的同步。
需要注意的是,在实际操作中,还需要考虑到一些因素,以确保同步控制能够稳定有效。
例如,变频器之间通信的稳定性和可靠性,编码器或位置传感器的精度和信号的及时性等。
此外,还要根据具体的应用需求和环境条件,调整控制系统的参数和算法,以实现更精确的同步控制。
通过变频器实现两台电机的同步控制,可以应用在许多工业场景中。
例如,自动化生产线中的输送带、同步驱动机械臂等。
通过有效地实现同步控制,不仅可以提高生产线的工作效率和精度,还可以减少因电机运动不同步而引起的故障和损耗。
总结起来,通过变频器实现两台电机的同步控制需要确保主电机的位置和转速精确可控,从电机通过接收主电机的转速信号来实现同步运动。
同时,还需要考虑通信稳定性、传感器精度和环境因素等因素,以优化同步控制系统的性能。
- 1、下载文档前请自行甄别文档内容的完整性,平台不提供额外的编辑、内容补充、找答案等附加服务。
- 2、"仅部分预览"的文档,不可在线预览部分如存在完整性等问题,可反馈申请退款(可完整预览的文档不适用该条件!)。
- 3、如文档侵犯您的权益,请联系客服反馈,我们会尽快为您处理(人工客服工作时间:9:00-18:30)。
multiple axes to improve the synchronization accuracy. In 1980, a cross-coupled controller for dual-axis feed drive systems was introduced by Koren [2] for the synchronization motion of two independent motion axes. Based on the coupling between two different axes, other approaches [3-5] were also proposed to compensate the synchronization errors in different systems. To handle more general coordinated systems in motion control, Chiu and Tomizuka [6] formulated the coordination control of multiple motion axes in a geometrical framework for three dimensional curves. With this framework, different researchers started to porpoise various cross-coupled controllers that reduce the contour error of multiple motion axes in mechanical systems. Xiao et al. [7] proposed a generalized synchronization controller for multi-axis motion system by incorporating cross-coupling technology into optimal control architecture. Jeong and You [8] applied a cascaded control structure to compensate both acceleration and position. Thus, the robustness of speed of each axis against disturbances and synchronization errors can be guaranteed. In 2003, Sun [9] applied the adaptive control method into the position synchronization of multi-robot for assembly tasks. In this paper, we investigated the synchronization of a three actuator system. The loading of the individual axis changes under different operating conditions. As the inertia and viscous damping of the multi-axis motion system become time varying, controller with a fixed structure might not be able to provide the same performance under different operating condition. Especially, some system parameters vary while the multi-axis system is under operation. Therefore, it is necessary to develop a controller that is capable to deal with the changing parameters and still maintain the accuracy. Two different type controllers were studied to evaluate the synchronization performance: a feedback controller with cross-coupling dynamics in the feedback loop and an adaptive controller that compensates the varying parameters. The proposed adaptive controller tries to reduce or eliminate possible uncertainties through a learning mechanism. By learning from the past information, uncertainties can be reduced and thus better performance can be expected. The organization of this paper is as following. The modeling process is introduced in the second section. The third
Adaptive Control of Sychronization for Multi-Axis Motion System
Marvin H.-M. Cheng Sirajus Salekeen
Dept of Mech. and Elec. Engr Tech Georgia Southern University Statesboro, GA, USA {hmcheng, ssalekeen} @
Ezzat G. Bakhoum
Dept of Electrical Engineering University of West Florida Pensacola, FL, USA ebakhoum@
Cheng-Yi Chen
Dept of Electrical Engineering Cheng-Shu University Kaohsiung, Tpaper investigate on motion synchronization of multiple axes systems. Two different control strategies, a crosscoupling controller in feedback loop and an adaptive controller, were used to synthesize the synchronization compensator with the cross-coupling dynamics among the axes. By using these strategies, the asymptotic convergence of both tracking and synchronization errors are achieved. The comparison of the two controllers of the nominal plant is discussed. Experimental results of a three-axis motion system that include system uncertainties are also illustrated to verify the effectiveness of the proposed approach. Index Terms—position synchronization, linear quadratic control, cross-coupling dynamics.
I. INTRODUCTION In industrial manufacturing systems, such as machine tools and plotters, one often encounters situations in which two or more axes need to be coordinated. With the increasing demand of manufacturing platforms with multiple robotic arms or conveyers, motion synchronization of multi-axis movement has drawn much more attention recently. The synchronization may be linear or rotary motion. When two or more axes of motion are involved in a single movement, the system is employing multi-axis motion. The need for multi-axis synchronization arises whenever the axes must move together. In such kind of control applications, the system performance depends more on the coordination of multiple motion actuators rather than individual motion actuator. For instance, the position coordination during motion may be required to avoid collision if some interlocking parts exist in the system. These kinds of demands for improvements in system performance lead to the research activities in this area. Since 1980s, it has been known that the coordination performance can be improved by compensating the differences in dynamics of individual actuators [1]. Nevertheless, the early researches did not take the coupling among different axes into consideration and the controllers were still synthesized independently. The diminished dimensional accuracy in those systems due to the poor synchronization of relevant axes was recognized. Therefore, different research groups have proposed various coordinating schemes and cross-coupled controllers for