胶合板制造工艺学
胶合板的生产工艺

胶合板的生产工艺
胶合板是一种由多层木材经过交叉粘合而成的板材,具有均匀、稳定的结构和优良的物理力学性能。
下面是胶合板的生产工艺。
1. 原料准备:选择优质木材作为胶合板的原料,一般选择松木、桦木等木材。
将木材进行削皮、切割、修整等处理,使其符合制板要求。
2. 预处理:将原材料木片放入浸泡槽中,进行浸泡处理,以去除木材中的杂质和树皮,使木片更易于切割和粘合。
3. 切割:将经过预处理的木片进行切割,得到需要的尺寸和厚度,常见的有单板、马口铁等不同规格的切割方式。
4. 干燥处理:将切割好的木片进行干燥处理,以去除木材中的水分,常见的干燥方式有自然晾干和烘干两种,烘干一般采用干燥室进行。
5. 粘合:将干燥好的木片进行粘合处理,采用的粘合剂有间苯醌、酚醛胶等。
在粘合过程中,要控制好温度、压力和粘合剂的用量,以确保粘合质量。
6. 热压:将粘合好的木片放入热压机中进行热压处理,使粘合剂充分固化并增强木材的稳定性。
热压温度和时间根据木材种类和板材的用途有所不同。
7. 整理修整:将热压好的胶合板进行修整和整理,修剪边缘、
去除瑕疵,并使板材的尺寸和平整度达到要求。
8. 修饰处理:根据需要,对胶合板进行涂饰处理,增加其外观质感和防腐性能。
9. 质量检验:对生产好的胶合板进行质量检验,包括测量尺寸、检查含水率、强度等指标,确保产品符合标准要求。
10. 包装入仓:将合格的胶合板进行包装,常见的包装方式有
托盘包装、塑料薄膜包装等,然后将包装好的胶合板入库,待发货。
以上是胶合板的生产工艺,通过精细化的工艺流程,可以生产出优质的胶合板产品。
胶合板生产工艺流程
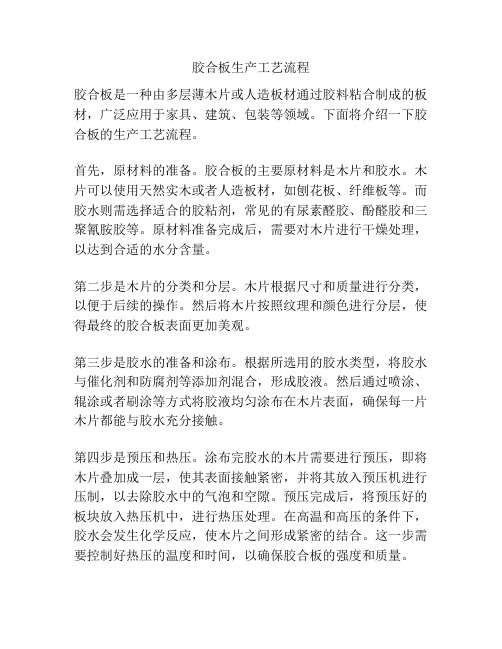
胶合板生产工艺流程胶合板是一种由多层薄木片或人造板材通过胶料粘合制成的板材,广泛应用于家具、建筑、包装等领域。
下面将介绍一下胶合板的生产工艺流程。
首先,原材料的准备。
胶合板的主要原材料是木片和胶水。
木片可以使用天然实木或者人造板材,如刨花板、纤维板等。
而胶水则需选择适合的胶粘剂,常见的有尿素醛胶、酚醛胶和三聚氰胺胶等。
原材料准备完成后,需要对木片进行干燥处理,以达到合适的水分含量。
第二步是木片的分类和分层。
木片根据尺寸和质量进行分类,以便于后续的操作。
然后将木片按照纹理和颜色进行分层,使得最终的胶合板表面更加美观。
第三步是胶水的准备和涂布。
根据所选用的胶水类型,将胶水与催化剂和防腐剂等添加剂混合,形成胶液。
然后通过喷涂、辊涂或者刷涂等方式将胶液均匀涂布在木片表面,确保每一片木片都能与胶水充分接触。
第四步是预压和热压。
涂布完胶水的木片需要进行预压,即将木片叠加成一层,使其表面接触紧密,并将其放入预压机进行压制,以去除胶水中的气泡和空隙。
预压完成后,将预压好的板块放入热压机中,进行热压处理。
在高温和高压的条件下,胶水会发生化学反应,使木片之间形成紧密的结合。
这一步需要控制好热压的温度和时间,以确保胶合板的强度和质量。
最后一步是修边和修整。
热压完成后的胶合板需要经过修边机的加工,将边缘修整成规整的形状。
同时还需要进行打磨和砂光处理,以使胶合板表面更加光滑平整。
以上就是胶合板的生产工艺流程。
胶合板具有强度高、质量稳定等优点,广泛应用于建筑材料、家具制造、车辆制造等领域。
胶合板的生产工艺流程需要经过多个环节,每一步都非常重要,影响着胶合板的质量和性能。
随着技术的发展和创新,胶合板的生产工艺也在不断进步,使得胶合板的质量得到了进一步提高。
胶合板的生产工艺流程

胶合板的生产工艺流程胶合板是一种由薄木片经胶合加压而成的板材,具有结构均匀、强度高、耐久性好等优点,被广泛用于建筑、家具、包装等领域。
胶合板的生产工艺流程主要包括原材料准备、预处理、修整、切割、拼花、拼装、脱水、热压、修边和包装等环节。
首先是原材料准备,胶合板的基材通常采用针叶木(如松木、云杉木)或阔叶木(如桦木、白桦木)的木片,这些木片要经过去皮、去杂质、去油渍等处理,以保证板材的质量。
然后是预处理,将经过处理后的木片进行干燥处理,通常采用干燥室或干燥窑进行高温干燥,使木材中的水分含量降低至10%左右,以提高胶合板的稳定性。
接下来是修整,将预处理后的木片进行修整,去除边缘不齐、不平整的部分,并剪去边角,使其形状规整。
然后是切割,将经过修整的木片进行切割,通常采用旋切或刨切的方法将木片切割成一定的厚度,然后根据需要,采取不同的尺寸和厚度进行分组。
然后进行拼花,拼花是指将不同的木片按照一定的规则和方式进行组合拼接,以形成不同的木纹效果和颜色层次感。
这一环节需要工人根据经验和艺术审美进行操作,以达到理想的外观效果。
接下来是拼装,将拼花后的木片进行拼装,使用胶水将木片粘合在一起,并进行适当的压实,以增强胶合板的结合力。
然后是脱水,将拼装好的胶合板放置在脱水机中进行脱水处理,将木材中多余的水分脱去,并使板材表面变得更加平坦。
然后是热压,将脱水后的胶合板放入热压机中,进行高温高压处理,使胶水快速固化,将胶合板的每一层木片牢固地粘合在一起。
接下来是修边,将经过热压后的胶合板进行修边处理,去除残留的边角和不平整的部分,使板材的边缘变得平直整齐。
最后是包装,将修边后的胶合板进行包装,常用的包装方式有塑料包装和纸箱包装,以保护胶合板的出厂品质,并方便运输和存储。
以上就是胶合板的生产工艺流程,通过以上环节的处理,可以制造出质量稳定、强度优良的胶合板产品。
胶合板的生产工艺流程
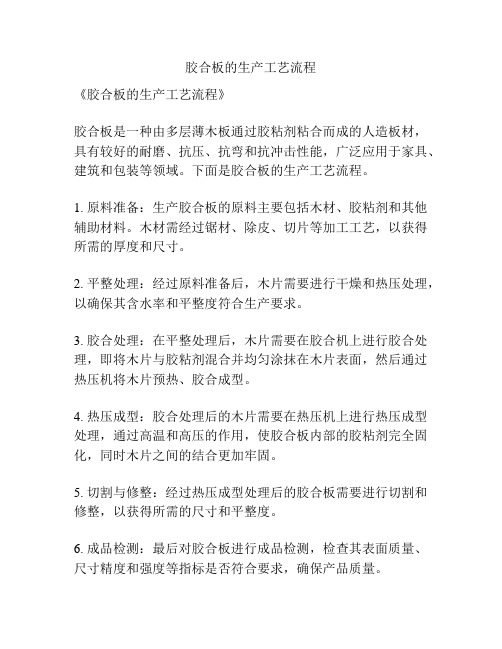
胶合板的生产工艺流程
《胶合板的生产工艺流程》
胶合板是一种由多层薄木板通过胶粘剂粘合而成的人造板材,具有较好的耐磨、抗压、抗弯和抗冲击性能,广泛应用于家具、建筑和包装等领域。
下面是胶合板的生产工艺流程。
1. 原料准备:生产胶合板的原料主要包括木材、胶粘剂和其他辅助材料。
木材需经过锯材、除皮、切片等加工工艺,以获得所需的厚度和尺寸。
2. 平整处理:经过原料准备后,木片需要进行干燥和热压处理,以确保其含水率和平整度符合生产要求。
3. 胶合处理:在平整处理后,木片需要在胶合机上进行胶合处理,即将木片与胶粘剂混合并均匀涂抹在木片表面,然后通过热压机将木片预热、胶合成型。
4. 热压成型:胶合处理后的木片需要在热压机上进行热压成型处理,通过高温和高压的作用,使胶合板内部的胶粘剂完全固化,同时木片之间的结合更加牢固。
5. 切割与修整:经过热压成型处理后的胶合板需要进行切割和修整,以获得所需的尺寸和平整度。
6. 成品检测:最后对胶合板进行成品检测,检查其表面质量、尺寸精度和强度等指标是否符合要求,确保产品质量。
通过上述工艺流程,胶合板的生产过程完成。
胶合板作为一种高性能的人造板材,具有较好的物理和机械性能,被广泛应用于建筑、家具和包装等行业。
胶合板生产工艺

胶合板生产工艺胶合板是一种由多层木片胶合而成的一种工程板材,广泛应用于建筑、家具、包装等各个领域。
胶合板的生产工艺主要分为原料处理、精细加工、热压胶合、修边切割和品质检验五个步骤。
首先,原料处理是胶合板生产的第一步。
首先,选用经过脱水烘干的高质量原木为原料,将原木进行刨花处理,刨下的木片具有较好的平整度和厚度一致性,作为胶合板的基材。
然后,将刨花木片按照一定的配比进行混合,使其具有一定的平均密度,使板材具有更好的强度和稳定性。
接下来是精细加工阶段。
将经过混合的刨花木片进行干燥处理,降低其含水率,提高板材的稳定性。
然后,对干燥后的木片进行筛分和分层分类,根据不同的要求为板材分层,使板材的物理性质更加均匀。
然后,将筛分好的木片进行修整,使其边缘光滑,并根据需要进行指榫连接等加工处理,以增加板材的强度和稳定性。
然后是热压胶合阶段。
将经过精细加工的木片按照一定的层数进行堆叠,然后将热固性胶涂布在每层木片的表面上。
然后,将胶涂布的木片堆叠进行热压,通过高压和高温的作用,使胶涂布的木片发生胶化反应,将木片紧密地结合在一起,形成整体的胶合板。
在热压过程中,通过一系列的工艺参数的控制,如温度、压力、厚度、时间等,使胶水完全渗透到木片的内部,提高板材的强度和稳定性。
完成热压胶合后,胶合板需要进行修边切割。
首先,对热压后的板材进行修边处理,去除板材的毛刺和不规则边缘,使板材的尺寸和外观更加规整。
然后,根据需要,对板材进行切割和修整,使其符合要求的尺寸和形状。
最后是品质检验。
对生产的胶合板进行质量检验,包括外观质量、尺寸精度、强度和稳定性等方面的检测。
合格的胶合板将进行包装并储存,不合格的胶合板将进行返工或淘汰处理。
以上是胶合板生产的主要工艺流程。
胶合板的生产工艺严格控制每个环节的质量,以确保生产出优质的胶合板产品。
胶合板的生产工艺不仅需要优质的原料和先进的设备,还需要有严格的生产管理和操作要求,以确保产品的质量和稳定性。
胶合板工序生产工艺

胶合板工序生产工艺胶合板是一种常用的人造板材,由多层木材经过胶合工艺制成。
胶合板的生产工序生产工艺非常重要,它直接关系到胶合板的质量和使用性能。
本文将详细介绍胶合板的生产工序生产工艺。
一、原材料准备胶合板的原材料主要是木材,包括采伐后的原木和木材切片。
在生产过程中,需要对原材料进行加工和处理,以保证其质量和适用性。
首先,需要对原木进行去皮、切割和修整等预处理工序,将其加工成符合要求的木材坯料。
然后,对木材坯料进行蒸煮处理,以去除木材中的树脂和其他杂质。
同时,还需要对木材进行干燥处理,以控制其含水率,以防止胶合板在使用过程中发生变形和开裂等问题。
二、切片和修整经过原材料准备后,需要对木材进行切片和修整。
切片是将木材坯料切割成一定厚度的木片,一般要求木片的厚度均匀、表面光滑。
修整是指对木片进行修整和修饰,以去除木片表面的瑕疵和不良部分。
切片和修整工序的质量对胶合板的最终质量有很大影响,因此需要严格控制工序参数,确保木片的质量和尺寸符合要求。
三、胶合处理胶合是胶合板生产的核心工序,也是胶合板得名的原因。
胶合处理是将切片好的木材片层叠在一起,并使用胶水进行粘合。
胶水是胶合板胶合的重要原材料,其选择和使用要符合相关标准。
胶合处理需要控制胶水的用量、粘合时间和压力等参数,以确保胶合板的质量和强度。
胶合处理后,需要对胶合板进行修整和修饰,以去除胶水溢出和不良部分。
四、热压处理胶合处理完成后,需要对胶合板进行热压处理。
热压处理是将胶合板放入热压机中,通过加热和压力作用,使胶水在木材片之间充分固化。
热压处理的温度、压力和时间等参数要根据胶水的特性和胶合板的要求进行合理选择。
热压处理后,胶合板的强度和稳定性将得到进一步提高。
五、修整和修饰热压处理完成后,需要对胶合板进行最后的修整和修饰。
修整是指对胶合板进行去毛刺、切割和修整,以使其尺寸和表面平整。
修饰是指对胶合板进行表面处理,如涂漆、磨光等,以改善其外观和使用性能。
胶合板生产工艺流程
胶合板生产工艺流程胶合板是一种由薄木板胶合而成的板材,具有轻质、强度高、不易变形等优点,因此在建筑、家具、包装等领域得到广泛应用。
胶合板的生产工艺流程主要包括原料准备、切削成型、干燥处理、胶合成型、热压加工等环节。
首先是原料准备。
生产胶合板的原料主要是木材,包括杨木、杉木、松木等。
这些木材需要经过去皮、切割、修整等加工,以确保木材表面光滑、尺寸一致。
同时,还需要对原料木材进行水分含量检测,以确保木材的含水率符合生产要求。
接下来是切削成型。
经过原料准备的木材进入切削机,被切削成一定厚度的木片。
这些木片经过旋刨机处理,使其表面光滑均匀,然后通过成型机进行成型,形成所需尺寸的薄木板。
然后是干燥处理。
薄木板经过成型后,需要进行干燥处理,以去除木材中的水分,提高木材的稳定性和强度。
通常采用热风干燥或者热压干燥的方式,确保木材的含水率符合生产要求。
接着是胶合成型。
经过干燥处理的薄木板,需要进行胶合处理。
在胶合过程中,通常采用酚醛胶、脲醛胶等胶水,将薄木板按照一定的顺序和方向进行胶合,形成多层结构。
在胶合过程中,需要控制好胶水的用量和均匀涂布,确保每一层木板之间都能够牢固粘合。
最后是热压加工。
经过胶合成型的多层薄木板,需要进行热压加工,以确保板材的密度和强度。
热压过程中,需要控制好温度、压力和时间,使胶合板在高温高压的环境下形成均匀的结构,提高板材的强度和稳定性。
以上就是胶合板生产的工艺流程。
通过原料准备、切削成型、干燥处理、胶合成型、热压加工等环节,最终形成具有优良性能的胶合板产品。
胶合板的生产工艺流程虽然复杂,但通过科学的工艺控制和精细的操作,能够生产出高质量的胶合板产品,满足不同领域的需求。
胶合板生产工艺流程及介绍
胶合板生产工艺流程及介绍胶合板是一种常见的木质板材,广泛应用于家具制造、建筑工程和包装行业等领域。
它由多层木材经过特定的生产工艺加工而成,具有较高的强度和稳定性。
下面将介绍胶合板的生产工艺流程及相关信息。
胶合板的生产工艺流程主要包括原材料准备、胶粘剂制备、木材切割、层积、热压、修整和检验等环节。
首先是原材料准备。
胶合板的原材料主要是木材和胶粘剂。
木材应选择质量好、干燥充分的板材,以确保胶合板的质量和稳定性。
胶粘剂通常使用酚醛树脂、脲醛树脂或酚醛脲醛树脂等。
胶粘剂的选择应根据胶合板的用途和要求进行合理搭配。
接下来是胶粘剂制备。
根据不同的胶粘剂种类和生产工艺,将胶粘剂与水、硬化剂等按一定比例混合搅拌,使其达到一定的粘度和流动性。
胶粘剂的制备过程需要严格控制参数,确保胶粘剂的质量和性能。
然后是木材切割。
将经过处理的木材按一定规格和尺寸进行切割,通常使用锯木机或刨床等工具进行操作。
切割后的木材应保持平整和光滑,以确保后续层积和热压过程的顺利进行。
接下来是层积。
将切割好的木材按一定的顺序和方向进行层积,每层木材之间应涂抹胶粘剂,以确保胶合板的粘结强度。
层积时要注意木材之间的间隙和压紧力度,以保证胶合板的平整度和稳定性。
然后是热压。
将层积好的木材放入热压机中进行加热和压制。
热压过程中,胶粘剂会被激活,形成牢固的粘结。
热压的温度、时间和压力等参数需要根据胶粘剂的种类和厚度进行合理调控,以确保胶合板的质量和性能。
之后是修整。
经过热压后的胶合板需要进行修整和修边,以去除多余的杂质和不平整的部分。
修整过程通常使用锯木机或修边机等设备进行操作,使胶合板的尺寸和形状符合要求。
最后是检验。
对修整后的胶合板进行质量检验,包括外观质量、物理性能和环保指标等方面。
合格的胶合板可以进行包装和出厂销售,不符合要求的则需要进行再次处理或淘汰。
总结起来,胶合板的生产工艺流程包括原材料准备、胶粘剂制备、木材切割、层积、热压、修整和检验等环节。
简述胶合板的生产工艺
简述胶合板的生产工艺
胶合板是一种由多层薄木片通过胶水粘合而成的板材,其生产工艺可以概括为以下几个步骤:
1. 原材料准备:选择优质的木材作为原料,常用的包括杉木、松木、桦木等。
木材经过去皮、修整和切割,制成长度宽度合适的薄木片。
2. 制备胶水:选择合适的胶合剂,如酚醛胶、尿素醛胶、三聚氰胺胶等,并根据需要进行调配。
胶水要具有一定的粘接强度和耐水性。
3. 制备胶合板芯层:将薄木片按照一定的方向排列,形成芯层。
通常在芯层中交替排列纵向木片和横向木片,以增加胶合板的稳定性。
4. 涂胶:将事先配置好的胶水均匀涂布在芯层上,确保每一层都被胶水覆盖。
5. 层叠:将涂胶的芯层按照一定的顺序层叠起来,使木片的纹理方向相互垂直。
这样的层叠结构能够增强胶合板的强度和稳定性。
6. 加热压制:将层叠好的胶合板送入热压机中,通过加热和压力作用下,使胶水充分固化。
通常情况下,压力会达到几十至上百吨,加热温度为120-150摄氏度,时间为数分钟至数小时。
7. 整理修边:经过热压后的胶合板表面可能不平整,需要经过修边处理,使其边缘平直、规格尺寸精确。
8. 干燥修整:胶合板在生产过程中会吸收一定的湿气,需要进行干燥处理,以达到所需的含水率。
9. 检验质量:对生产出来的胶合板进行质量检验,包括外观质量、强度测试、厚度测量等。
符合标准的胶合板才能被认可并投入市场使用。
以上是胶合板的基本生产工艺流程,根据实际需要和技术条件的不同,还可以进行其他辅助工艺,如防腐处理、覆膜处理等,以满足不同需求。
杨木胶合板生产工艺简述
杨木胶合板生产工艺简述杨木胶合板是一种常用的家具和建筑材料。
它由多层杨木薄片经胶合制成,具有较高的强度和抗湿性。
以下是杨木胶合板的生产工艺简述:1. 原材料准备:首先需要选择优质的杨木作为原材料。
这些杨木需要被锯成薄片,长宽尺寸根据需要进行调整。
2. 搅拌胶水:将胶水和水按一定比例混合,并经过搅拌使其均匀。
3. 薄片处理:将切好的杨木薄片放入大槽中,浸泡在水中一段时间以去除杨木中的杂质,并使其湿度适中。
4. 薄片烘干:经过浸泡后的杨木薄片需要进行烘干处理,使其水分含量适当。
通常会使用热风烘干机或烘箱来完成这一步骤。
5. 胶合:将烘干后的杨木薄片依次放置在胶水混合物中,确保每片薄片都被充分涂覆胶水。
6. 压制:将涂有胶水的杨木薄片依次放在压制机的工作台上,并施加一定的压力,使其胶合。
7. 热压:通过将胶合好的杨木薄片放入热压机中,施加高温和高压,使其胶水充分固化,增强胶合板的强度。
8. 整平修边:经过胶合和热压后的杨木胶合板可能会出现不平整的表面,需要进行修整和修边处理,使其达到平整和美观的要求。
9. 检验和包装:对生产好的杨木胶合板进行质量检验,确保其符合产品标准要求。
合格的胶合板经过包装,做好防潮、防尘等措施,以便于运输和使用。
以上是杨木胶合板的生产工艺简述。
整个过程包括杨木薄片的处理、胶水的制作和使用、胶合和热压等工艺,旨在制造出高质量的杨木胶合板产品。
杨木胶合板是一种多层木质板材,由杨木薄片经过胶合制作而成。
它是一种常用的家具和建筑材料,广泛应用于家庭装修、家具制作、建筑施工和包装等领域。
杨木胶合板具有较高的强度、稳定性和抗湿性,因此深受市场的青睐。
杨木胶合板的生产工艺经过了多个环节,通过科学的加工和优质的原材料,以确保产品的质量和性能。
首先,在杨木胶合板的生产过程中,原材料的选择非常重要。
优质的杨木被选中后,根据需要被锯成薄片,长宽尺寸可以根据产品的要求进行调整。
杨木的选择主要考虑木材的物理性能、材质的纤维方向以及外观质量等因素。
- 1、下载文档前请自行甄别文档内容的完整性,平台不提供额外的编辑、内容补充、找答案等附加服务。
- 2、"仅部分预览"的文档,不可在线预览部分如存在完整性等问题,可反馈申请退款(可完整预览的文档不适用该条件!)。
- 3、如文档侵犯您的权益,请联系客服反馈,我们会尽快为您处理(人工客服工作时间:9:00-18:30)。
当容器(如锅炉)内的气体温度为100℃ (随海拔高度增加,温度相应的升高),而湿 度为100%时,容器内的空气全部排出而被水 蒸气所代替,此时的水蒸气叫做饱和水蒸气, 此时容器内的压力是一个绝对压力(1kg/cm3, 即约为0.1MPa),压力表的读数是零。
(2)单板在旋切过程中有些纤维被切断,材质比较疏松,水 分向外传导阻力小,单板表面蒸发作用和内部扩散作用彼 此相适应,采用高温也不会产生开裂、变形等缺陷。
2. 可采用高速气流垂直单板表面喷射,高速气流可达
15-20m/s,大大提高干燥速度。
采用高速气流为什么能提高干燥速度?
当高速热气流平行于单板表面流过时,相互之间产生了摩
擦,而使气流速度减小,与单板表面接触的薄层,速度接近
于零,呈现凝滞的空气薄膜,把热空气与单板表面隔开,这
层薄膜称为临界层。 2
临界层的厚度随着离板端距离增加
而增加,由于单板中的水分只能通过缓
慢的扩散作用,穿过临界层而进入空气
流,同时空气流中的热量缓慢的通过临
a
界层向单板内部传导,因而临界层影响
了热交换的效率,降低了单板中的水分 逸出速率。
单板含水率的测定方法有重量法、电阻测湿 法、介质常数测湿、微波测湿法。
§4-2 单板干燥的基本原理
一、单板干燥的特点(与板、方材比较)
1.可采用高温快速干燥工艺,t=170℃—180℃,最高 300℃, 由于温度高,干燥速度可大大加快。
为什么单板干燥可采用高温快速干燥?
(1)旋切后的单板由于幅面大,厚度小,主要依靠横跨纤维 方向的横向通道传导水分,水分移动的路径短(因为木 材里的水分可以以细胞腔作为纵向通道,顺着纤维长度 方向运动,从木材的两端面排出(长度方向),也可以 以细胞壁的纹孔作为贯通的横向通道,细胞壁内还有许多 孔隙使水分从木材侧面排出(宽度或厚度方向)。
低于干燥机内热空气的蒸汽压,因此单板表面水分
基本不蒸发。
单单
板板 含温
Ⅰ
Ⅱ
热空气所供给的热
水度 率(
℃ %
量全部用来提高单板的
( )
温度,使单板温度很快 )
上升到湿球温度。
Ⅲ
温度
含水率
干燥时间(min)
II 恒速干燥期
是以蒸发自由水为主,单板表面水分的蒸发速度和 单板里面水分向外传导的速度大致是相等的,因此称为 恒速干燥期。热空气所供给的热量全部用于水分蒸发, 单板的温度仍然维持在湿球温度。
要排除更多水分,在胶合板热压胶合过程中,各层单板 收缩变形很大,因此胶合板内应力较大,易变形。 ⑷ 如果含水率过高,胶固化不充分,胶合强度不好。 (5) 湿单板在贮存中易产生边缘开裂、中间发霉变色等 缺陷。
对于酚醛、脲醛树脂胶合板,要求单板 的终含水率为8%-12%最适宜;血胶、豆胶 等蛋白质胶的胶合板,要求单板的终含水率 为8%-15%。
热空气所供给的 热量一小部分用于水
单单 板板 含温 水度
Ⅰ
Ⅱ
Ⅲ
℃ %
分蒸发,大部分用于
率( (
பைடு நூலகம்
提高单板温度,使单
) )
板温度很快上升到干
球温度,这样就完成
了单板干燥过程。
干燥时间(min)
三、影响单板干燥速度的主要因素
单板干燥速度直接影响干燥机生产能力, 提高干燥速度是提高干燥机产量的最有效方法。 干燥速度实际就是单板水分排出的速度,影响 因素总的来看可分为两大方面:
在此阶段热空气供给
单单 板板
的热量大部分用于水分的
含温 水度
蒸发,一小部分用于提高 率 (
单板温度,使单板的温度
( )
基本维持在湿球温度而略 )
有升高,这是单板干燥的
重要阶段。
℃ %
ⅠⅡ
Ⅲ
干燥时间(min)
(2)减速干燥第二阶段:
在此阶段单板含水率低于纤维饱和点很多,水分 向外传导更加困难,水分蒸发速度也大大下降;
§4-1 单板干燥的终含水率
一、最适宜的单板终含水率
旋切后的单板含水率很高,不符合胶合工艺的要求 (湿热法除外),必须进行干燥,太高太低都不行。 如果干燥含水率过低,会出现以下问题:
⑴ 当木材含水率低于纤维饱和点时,就易出现干缩, 干缩损失大。
⑵ 含水率越低,干燥时间越长,容易浪费能源,降低 干燥机生产能力。
⑶ 含水率低,在加工运输过程中易破损。 ⑷ 含水率过低,涂胶后胶粘剂易渗透到单板上去,同
时由于含水率过低的单板羟基活性减小和单板表面 纤维的物理性能受损伤,这些都会影响胶接强度。
如果含水率过高也不行,会出现以下问题:
⑴ 如果含水率过高,涂胶组坯后,胶易渗透到表板表 面上,形成透胶。
⑵ 如果含水率过高,在热压过程中易产生分层鼓泡。 ⑶ 如果含水率过高,热压胶合后胶合板含水率很低,
在这一阶段也蒸发掉 单 单
一少部分吸着水,这表现 板 板
在含水率远在纤维饱和点
含温 水度
℃ %
以上时,单板就开始干缩。
率 (
(
吸着水存在于细胞壁内, )
失去吸着水,木材就会发 )
生干缩。这一阶段时间很
短。
ⅠⅡ
Ⅲ
干燥时间(min)
III 减速干燥期
(1)减速干燥第一阶段:
蒸发掉全部自由水和大部分吸着水,在此阶段单 板表面水分的蒸发速度和单板里面水分向外传导的速 度已经不相适应了,单板干燥速度开始下降。
1
1—单板 2--气流速度 a—临界层
近年来,国内外对单板干燥的特性作了较 深的研究,从提高温度和气流速度两个方面 来加速干燥过程。目前,广泛采用的喷气式 干燥机就是采用垂直单板表面喷射高速热气 流来冲破或扰乱临界层来提高传热效率,加 速内部水分的扩散,缩短干燥时间。
二、单板干燥过程
I 加热期
单板刚接触热空气,单板表面的自由水蒸汽压
干燥介质的影响:包括介质温度、热空气相 对湿度、热空气速度。
单 板 本 身 条 件:包括单板树种、单板初含 水率、单板厚度等。
㈠ 干燥介质的影响
⑴ 干燥介质温度(热空气温度)
干燥介质温度是影响单板干燥速度的重要因素。 温度越高,供单板内部水分汽化的能量就越大,使得 干燥单板内的水分很快汽化,则单板内外蒸汽压力梯 度增大。同时,由于单板表面水分蒸发快,使单板内 外含水率梯度也增大,水蒸气扩散速度和水分传导系 数相应增大,单板水分排出速度加快,干燥速度加快。 即温度升高,干燥速度快。