胶合板的生产工艺
胶合板生产工艺

b.特种胶合板
1.细木工板 2.空芯板 3.装饰胶合板 4.塑化胶合板 5.木材层积塑料 6.异形胶合板
普通胶合板生产工艺流程
干燥——剪切 原木——截断——热处理——剥皮——定中心——旋切 剪切——干燥
修补——涂胶——组坯——预压——热压——冷却 ——裁边——砂光—分等——检验——入库
一、原木截断 按照胶合板的规格和质量要求,将原木 截断成所需要的长度。要根据原木缺陷, 确定合板的锯断位臵,以保证单板质量, 获得木材最大利用率。
D湿
木材径向干缩率(单板厚度方向R):3~6% 木材弦向干缩率(单板宽度方向T):6~12% 木材纵向干缩率(单板长度方向L):很小
R
L T
单板干缩不等时性 由于单板表面温度首先升高,水分很快蒸发,而首先导 致宽度方向的干缩,在含水率梯度作用下,内部水分向外扩散 并蒸发,才在厚度方向产生干缩。
单板干缩不均匀性和不等时性产生的现象 厚单板比薄单板宽度方向干缩量小(因为厚单板表层 干缩受内层干缩的制约作用大) 厚单板比薄单板厚度方向干缩量大(因为厚单板表层 过渡干缩) 单板干缩对工艺的影响 对于“先剪后干”工艺,剪切单板时需考虑干缩余量(包 括宽度和厚度):
(3)单板终含水率分布 含水率分布不均原因: 初含水率不均:边材高,心材低 干燥设备内不同位置风速、温度和湿度分布不均 控制措施 分类干燥 含水率在线检测技术:在干燥机后部安装连续式含水率测 定仪,尽早知道并调整干燥机的速度 干燥后堆放再使用:把干燥后的单板应堆放一段时间, 使其含水率均匀,可达到减少含水率偏差的效果.一般堆放24 小时
(2)升温阶段 介质温度:硬阔叶材高于软阔叶材 陆贮材高于水贮材 旋切厚单板的木段温度要高些 温度过高,单板容易起毛;太低,木材塑性不 足,易产生裂缝,甚至不能正常旋切。 介质升温速度:一般阔叶材低于针叶材,特别是易开裂的 木材其升温速度应偏慢。 柠檬桉、桦叶楠为2℃/h,枫香3~4℃/h。不易开裂的木 材可为5~6℃/h,如落叶松;但一般不宜超过10℃/h。
3.第三章 人造板制造——胶合板
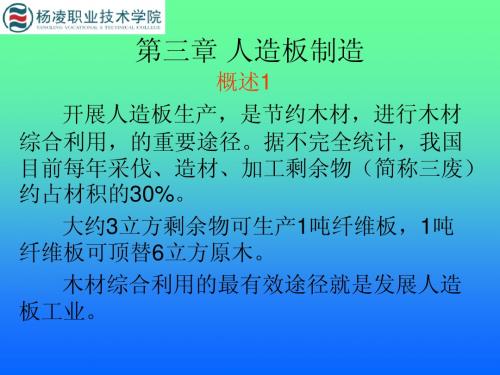
胶合板生产工艺(4)
干热法胶合板生产工艺: 2.单板制造:方法有旋制、刨制、 锯制三种,旋制最常用。 旋制——旋切机,定轴等速。单板 厚度等于木段旋转一周刀架的进给量。 旋切的单板板面花纹接近于旋切板
胶合板生产工艺(5)
干热法胶合板生产工艺: 3.单板干燥:方法有自热干燥和人 工干燥(机械)两种 人工干燥机——纵向或横向通风辊 式干燥机、网带式干燥机、喷气式网 袋连续干燥机、红外线对流混合式干 燥机等。
胶合板的组成与分类(2)
二、胶合板分类 按用途可以将胶合板分为:特种胶合板和一 般胶合板。一般胶合板可分为四类: Ⅰ类(NQF)——耐气候、耐沸水胶合板。 酚醛树脂胶粘合室外使用 Ⅱ类(NS)——耐水胶合板。脲醛树脂胶 粘合,短期冷水浸泡 Ⅲ类(NC)——耐潮胶合板。血胶粘合, 短期冷水浸泡 Ⅳ类(BNC)——不耐潮胶合板。豆胶粘 合,室内使用
胶合板
定义: 胶合板是原木经过旋切(或刨切)成 单板,再经过纵横交错排列胶压而成的三 层或多层板材。 特点: 胶合板以其幅面宽,厚度小,表面平 整、容重轻、纵横向强度大而均匀等优点 而广泛使用。
胶合板的组成与分类(1)
一、组成原则 组成分为:表板(面板、背板)和芯板 (又叫中板) 1.对称原则——对称平面两边层数相同; 对称层的单板在厚度、树种、含水率、纤维方 向制造方法(旋制、刨制、锯制)等均相同 2.奇数层原则——对称原则决定其必须是 奇数层。 3.厚度原则——相同厚度的胶合板,层数 越多,质量越好。
胶合板生产工艺(12) 干热法胶合板生产工艺: 组坯——将涂了胶的芯板、 面板与背板组成板坯的过程。芯 板不能整张化,需要手工拼接。 注意不能造成错位、歪斜、叠层。 离缝等
胶合板生产工艺(13)
干热法胶合板生产工艺: 热压胶合——把组成的板坯送到热压机中,在 一定温度和压力下处理,是胶层凝固,单板胶合的 过程。 三个作用:压力作用、热力作用、化学作用 工艺要求: 1.压力——10~18KG/cm2 2.温度——105~120度 3.时间——每毫米厚度45~50秒
胶合板的生产工艺

胶合板的生产工艺
胶合板是一种由多层木材经过交叉粘合而成的板材,具有均匀、稳定的结构和优良的物理力学性能。
下面是胶合板的生产工艺。
1. 原料准备:选择优质木材作为胶合板的原料,一般选择松木、桦木等木材。
将木材进行削皮、切割、修整等处理,使其符合制板要求。
2. 预处理:将原材料木片放入浸泡槽中,进行浸泡处理,以去除木材中的杂质和树皮,使木片更易于切割和粘合。
3. 切割:将经过预处理的木片进行切割,得到需要的尺寸和厚度,常见的有单板、马口铁等不同规格的切割方式。
4. 干燥处理:将切割好的木片进行干燥处理,以去除木材中的水分,常见的干燥方式有自然晾干和烘干两种,烘干一般采用干燥室进行。
5. 粘合:将干燥好的木片进行粘合处理,采用的粘合剂有间苯醌、酚醛胶等。
在粘合过程中,要控制好温度、压力和粘合剂的用量,以确保粘合质量。
6. 热压:将粘合好的木片放入热压机中进行热压处理,使粘合剂充分固化并增强木材的稳定性。
热压温度和时间根据木材种类和板材的用途有所不同。
7. 整理修整:将热压好的胶合板进行修整和整理,修剪边缘、
去除瑕疵,并使板材的尺寸和平整度达到要求。
8. 修饰处理:根据需要,对胶合板进行涂饰处理,增加其外观质感和防腐性能。
9. 质量检验:对生产好的胶合板进行质量检验,包括测量尺寸、检查含水率、强度等指标,确保产品符合标准要求。
10. 包装入仓:将合格的胶合板进行包装,常见的包装方式有
托盘包装、塑料薄膜包装等,然后将包装好的胶合板入库,待发货。
以上是胶合板的生产工艺,通过精细化的工艺流程,可以生产出优质的胶合板产品。
加工生产胶合板的工艺流程

加工生产胶合板的工艺流程集团文件版本号:(M928-T898-M248-WU2669-I2896-DQ586-M1988)加工生产胶合板的工艺流程原木加工生产胶合板的工艺流程:原木→原木锯断→木段蒸煮→木段剥皮→单板旋切→单板干燥→单板整理→涂胶组坯→预压→热压→裁边→砂光→检验分等→包装入库。
单板加工生产胶合板的工艺流程:单板整理→涂胶组坯→预压→热压→裁进→砂光→检验分等→包装入库。
加工工艺损耗:在胶合板整个生产过程中,原木锯断、单板旋切、单板干燥、单板整理、热压、裁边、砂光对木材损耗有影响,它分为有形损耗(有加工剩余物的)和无形损耗(干缩和压缩)。
木材损耗与原木材种、原木规格、设备状况、工艺技术以及成品板规格等因素有关。
原木锯断:进口原木长度一般超过6米,要按工艺要求的长度和质量进行锯断,截取的木段应为胶合板成品尺寸外加加工余量的长度。
例如幅面1220mmX2440mm的成品胶合板,木段长度通常为2600mm或1300mm。
原木的长度和原木的弯曲度、缺陷等直接影响胶合板的出材率,产生的废料有小木段、截头和锯屑等,原木锯断损耗率一般在3~10%。
单板旋切:胶合板生产中应用最广的是旋切方法生产的单板,面背板的厚度一般为0.6mm左右,芯板、长中板的厚度一般为1.8mm左右。
该工序损耗最大,一是由于木段不圆度,相当一部分的碎单板不能使用;二是旋切机卡头对木段两端的夹牢而产生端部损耗;三是木芯损耗。
单板旋切产生的废料为碎单板和木芯,由此可见单板旋切损耗量与木段的材质、直径及设备性能有关,这部分损耗率在15%~25%。
单板干燥:旋切后的单板含水率很高,必须将单板干燥到符合胶合工艺的要求。
干燥后木材尺寸变小,称为干缩。
因含水率降低,单板的长度、宽度和厚度都会干缩。
干缩损耗与单板的树种、单板的含水率及单板厚度等因素有关。
干缩损耗率一般为4%~10%。
单板整理:单板整理包括剪切、拼板及修补。
将干燥后的带状单板、零片单板剪切成规格单板和可拼接单板,窄条单板经过拼接成整张单板,有缺陷的整张单板可通过修补达到工艺的质量要求。
胶合板生产工艺流程
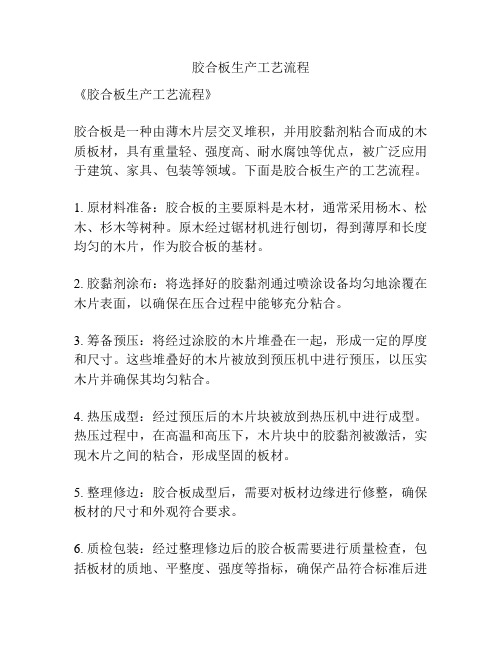
胶合板生产工艺流程
《胶合板生产工艺流程》
胶合板是一种由薄木片层交叉堆积,并用胶黏剂粘合而成的木质板材,具有重量轻、强度高、耐水腐蚀等优点,被广泛应用于建筑、家具、包装等领域。
下面是胶合板生产的工艺流程。
1. 原材料准备:胶合板的主要原料是木材,通常采用杨木、松木、杉木等树种。
原木经过锯材机进行刨切,得到薄厚和长度均匀的木片,作为胶合板的基材。
2. 胶黏剂涂布:将选择好的胶黏剂通过喷涂设备均匀地涂覆在木片表面,以确保在压合过程中能够充分粘合。
3. 筹备预压:将经过涂胶的木片堆叠在一起,形成一定的厚度和尺寸。
这些堆叠好的木片被放到预压机中进行预压,以压实木片并确保其均匀粘合。
4. 热压成型:经过预压后的木片块被放到热压机中进行成型。
热压过程中,在高温和高压下,木片块中的胶黏剂被激活,实现木片之间的粘合,形成坚固的板材。
5. 整理修边:胶合板成型后,需要对板材边缘进行修整,确保板材的尺寸和外观符合要求。
6. 质检包装:经过整理修边后的胶合板需要进行质量检查,包括板材的质地、平整度、强度等指标,确保产品符合标准后进
行包装出厂。
以上就是胶合板生产的工艺流程,通过严格的生产工艺和质量控制,生产出符合需求的胶合板产品,满足不同领域的应用需求。
胶合板生产工艺

临沂市林海木业有限公司胶合板生产工艺规程版本编号:A受控状态:文件编号:L H G Y-01文件发放号:编制:审核:批准:发布日期:2010-8-1 实施日期:2010-8-1芯板涂胶1胶粘剂的配制(1)脲醛胶质量指标:固体含量%46—55ph值7—9外观无色、白色或淡黄色无杂质均匀液体(2)树脂胶配制(重量比):脲醛胶100面粉40~502芯板涂胶芯板双面涂胶量:1100—1200克/3张(上胶量计算方法:上胶后重量-上胶前重量)1涂胶芯板质量必须符合要求,含水率为8—14%,温度40度以下。
对厚薄不均、长度不足、两横边带弧形、含水率大于15%的芯板要挑出放到指定地点。
2 串芯人员要清除芯板上的杂物,涂胶量要均匀,没涂到胶的部位要用手工刷胶,不允许有空白点;胶堆积的地方要清除多余的胶,串芯人员同时要负责挑出不合格的芯板,并应放到指定处。
3涂胶后的芯板要做到先串先用,涂胶芯板陈化时间不应超过30分钟。
4涂胶芯板的使用要合理,禁止不同树种的芯板同时涂胶、同时使用。
组坯1 组坯时要做到一边一头齐,每摊位板坯上下,左右要对齐。
排芯时涂胶芯板及中板上附有的垃圾等杂物要清理干净2 严格掌握板坯的陈化时间,一般情况不许超过30分钟。
3 禁止不同树种、厚度的芯板混排在同一层;板坯对称层树种、厚度要一致。
4 生产过程中挑出的不合格芯板、单板要放在指定地点,不得乱放。
5 认真填写移送单和交接记录,发现问题及时反馈。
板坯预压1 板坯要及时送入预压机,压力13~15MPa,预压时间根据板坯的预压效果而定,一般控制在120—180分钟。
2预压时板坯不允许有卷边、卷角现象,预压时板坯的各部位要均匀受压,预压效果要保证板坯粘接成一体。
3认真填写移送单,做好交接记录,发现问题及时反馈。
板坯修整1板坯上的孔洞要用与本板树种一致的补片补好。
2板坯上的重叠要用修补刀割除,但不能修成离缝。
1板坯上的宽大于2mm,长大于100mm的离缝要用补条补好。
胶合板生产工艺文件
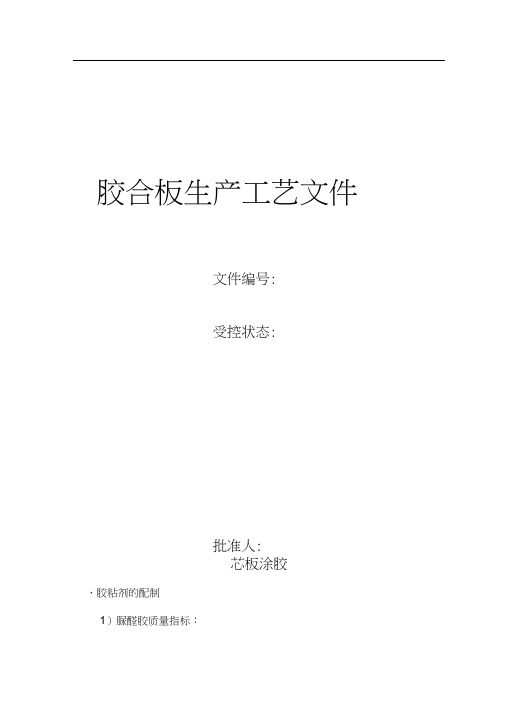
胶合板生产工艺文件文件编号:受控状态:批准人:芯板涂胶、胶粘剂的配制1)脲醛胶质量指标:固体含量%46〜55p H值7 〜9.5外观无色、白色或淡黄色无杂质均匀液体游离甲醛含量< 0.3%(2)脲醛胶配重量比):制(脲醛胶:面粉100:352、芯板涂胶1.0mm〜1.4mm芯板双面涂胶量:(250〜300)g/心1.5mm^2.0mm芯板双面涂胶量:(350〜400)g/ m2;(1 )涂胶芯板质量必须符合要求,含水率为(8〜12)%,温度40 度以下。
对厚薄不均、长度不足、两横边带弧形、含水率大于13%的芯板要挑出放到指定地点。
(2)串芯人员要清除芯板上的杂物,涂胶量要均匀,没涂到胶的部位要用手工刷胶,不允许有空白点;胶堆积的地方要清除多余的胶,串芯人员同时要负责挑出不合格的芯板,并应放到指定处。
(3)涂胶后的芯板要做到先串先用,涂胶芯板陈化时间不应超过30 分钟。
(4)涂胶芯板的使用要合理,禁止不同树种的芯板同时涂胶、同时使用。
组坯1、组坯时要做到一边一头齐,每摊位板坯上下,左右要对齐。
排芯时涂胶芯板及中板上附有的垃圾等杂物要清理干净2、严格掌握板坯的陈化时间,一般情况不许超过30 分钟。
3、禁止不同树种、厚度的芯板混排在同一层;板坯对称层树种、厚度要一致。
4、生产过程中挑出的不合格芯板、单板要放在指定地点,不得乱放。
5、认真填写移送单和交接记录,发现问题及时反馈。
板坯修整1、板坯上的孔洞要用与本板树种一致的补片补好。
2、板坯上的重叠要用修补刀割除,但不能修成离缝。
3、板坯上的宽大于2mn,长大于100mm勺离缝要用补条补好。
4、修补时挑出的不合格板坯要放到指定地点,并在缺陷处作上标记。
5、修整的板坯要按树种、规格整齐堆放,并作上标记。
热压1、热压工艺参数:温度:(100〜115)C,压力:(10~12)MPa2、热压前应逐张清理压板上的木屑、胶带等污物,每块压板四角温度均匀,达到所要求温度后方可入板生产。
胶合板生产工艺

胶合板生产工艺胶合板是一种由多层木片胶合而成的一种工程板材,广泛应用于建筑、家具、包装等各个领域。
胶合板的生产工艺主要分为原料处理、精细加工、热压胶合、修边切割和品质检验五个步骤。
首先,原料处理是胶合板生产的第一步。
首先,选用经过脱水烘干的高质量原木为原料,将原木进行刨花处理,刨下的木片具有较好的平整度和厚度一致性,作为胶合板的基材。
然后,将刨花木片按照一定的配比进行混合,使其具有一定的平均密度,使板材具有更好的强度和稳定性。
接下来是精细加工阶段。
将经过混合的刨花木片进行干燥处理,降低其含水率,提高板材的稳定性。
然后,对干燥后的木片进行筛分和分层分类,根据不同的要求为板材分层,使板材的物理性质更加均匀。
然后,将筛分好的木片进行修整,使其边缘光滑,并根据需要进行指榫连接等加工处理,以增加板材的强度和稳定性。
然后是热压胶合阶段。
将经过精细加工的木片按照一定的层数进行堆叠,然后将热固性胶涂布在每层木片的表面上。
然后,将胶涂布的木片堆叠进行热压,通过高压和高温的作用,使胶涂布的木片发生胶化反应,将木片紧密地结合在一起,形成整体的胶合板。
在热压过程中,通过一系列的工艺参数的控制,如温度、压力、厚度、时间等,使胶水完全渗透到木片的内部,提高板材的强度和稳定性。
完成热压胶合后,胶合板需要进行修边切割。
首先,对热压后的板材进行修边处理,去除板材的毛刺和不规则边缘,使板材的尺寸和外观更加规整。
然后,根据需要,对板材进行切割和修整,使其符合要求的尺寸和形状。
最后是品质检验。
对生产的胶合板进行质量检验,包括外观质量、尺寸精度、强度和稳定性等方面的检测。
合格的胶合板将进行包装并储存,不合格的胶合板将进行返工或淘汰处理。
以上是胶合板生产的主要工艺流程。
胶合板的生产工艺严格控制每个环节的质量,以确保生产出优质的胶合板产品。
胶合板的生产工艺不仅需要优质的原料和先进的设备,还需要有严格的生产管理和操作要求,以确保产品的质量和稳定性。
- 1、下载文档前请自行甄别文档内容的完整性,平台不提供额外的编辑、内容补充、找答案等附加服务。
- 2、"仅部分预览"的文档,不可在线预览部分如存在完整性等问题,可反馈申请退款(可完整预览的文档不适用该条件!)。
- 3、如文档侵犯您的权益,请联系客服反馈,我们会尽快为您处理(人工客服工作时间:9:00-18:30)。
胶合板的生产工艺
(2012/08/03 10:22)
目录:公司动态
浏览字体:大中小
3 胶合板的生产
(1).常用的方法是干热法
旋切和刨切单板经干燥后,单板含水率在8%--12%,涂胶组坯在热压机中胶合,几乎各种胶粘剂都可以用此种方法生产胶合板,而且胶合时间短,胶合强度高,板面平整光洁,不易变形。
胶合板的生产工艺
①木段准备阶段:原木截断、蒸煮、剥皮等工序
②单板制造阶段:单板旋切、干燥、修补、胶拼和剪切
③胶合板制造阶段:单板涂胶、组坯、预压、热压及冷却
④胶合板加工阶段:裁边、修整和表面加工
剪切好的单板用淋胶或涂胶的方法涂胶、组坯、预压、热压、最后经过裁边、砂光、出成品。
4、常用胶合板分类
目前家装主要应用3、5、9、12厘胶合板,材质有以下几种:
柳桉芯胶合板:采用进口柳桉材质做芯板,强度高,不易变形,
价格较贵。
杂木芯胶合板:采用硬杂木做芯板,强度较高,价格中等。
杨木芯胶合板:采用杨木做芯板,强度较低,价格低。