模具加工机具精度分析表
模具评估报告
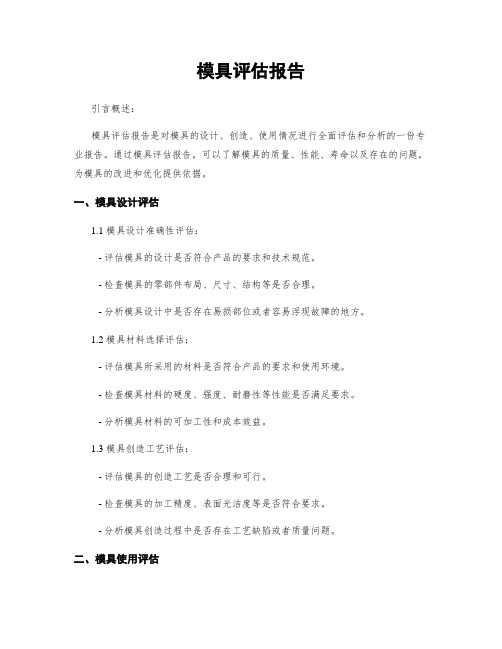
模具评估报告引言概述:模具评估报告是对模具的设计、创造、使用情况进行全面评估和分析的一份专业报告。
通过模具评估报告,可以了解模具的质量、性能、寿命以及存在的问题,为模具的改进和优化提供依据。
一、模具设计评估1.1 模具设计准确性评估:- 评估模具的设计是否符合产品的要求和技术规范。
- 检查模具的零部件布局、尺寸、结构等是否合理。
- 分析模具设计中是否存在易损部位或者容易浮现故障的地方。
1.2 模具材料选择评估:- 评估模具所采用的材料是否符合产品的要求和使用环境。
- 检查模具材料的硬度、强度、耐磨性等性能是否满足要求。
- 分析模具材料的可加工性和成本效益。
1.3 模具创造工艺评估:- 评估模具的创造工艺是否合理和可行。
- 检查模具的加工精度、表面光洁度等是否符合要求。
- 分析模具创造过程中是否存在工艺缺陷或者质量问题。
二、模具使用评估2.1 模具使用寿命评估:- 评估模具的使用寿命是否达到预期目标。
- 检查模具在使用过程中是否存在磨损、变形、裂纹等问题。
- 分析模具的使用寿命受到的影响因素,如材料疲劳、工艺变化等。
2.2 模具生产效率评估:- 评估模具的生产效率是否满足生产需求。
- 检查模具在生产过程中是否存在卡料、卡模、停机等问题。
- 分析模具生产效率低下的原因,如模具结构不合理、维护不当等。
2.3 模具维护管理评估:- 评估模具的维护管理情况是否科学有效。
- 检查模具的日常保养、定期维护是否得当。
- 分析模具维护管理不善导致的故障和损坏情况。
三、模具质量评估3.1 模具加工精度评估:- 评估模具的加工精度是否满足产品的要求。
- 检查模具加工过程中是否存在尺寸偏差、形状误差等问题。
- 分析模具加工精度不高的原因,如机床精度、刀具磨损等。
3.2 模具产品质量评估:- 评估模具所生产的产品质量是否合格。
- 检查模具产品的尺寸、外观、性能等是否符合要求。
- 分析模具产品质量不达标的原因,如模具设计缺陷、材料问题等。
模具加工出错分析及质量提升
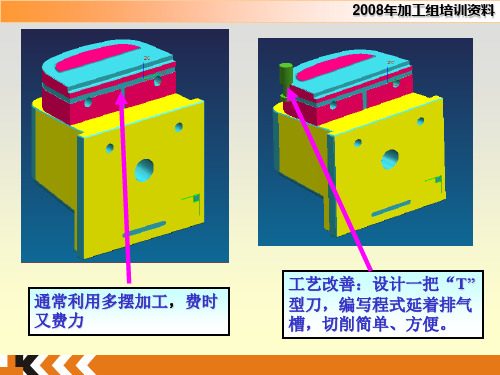
15mm以下 15mm以上
80mm2以上
15mm以下 15mm以上
电极火花位标准(单边)
S(粗)
F(精)
0.20mm
0.10mm 0.10mm
0.30mm
0.10mm
0.25mm 0.30mm
0.08mm 0.10mm
0.30mm 0.30mm
0.10mm 0.10mm
0.20mm 0.25mm
0.08mm 0.08mm
0.20mm 0.30mm
0.08mm 0.10mm
0.25mm 0.30mm
0.10mm 0.10mm
0.25mm 0.30mm
0.10mm 0.10mm
备注
2008年加工组培训资料
此胶位 厚0.6 mm。
2008年加工组培训资料
合理设计电极即有 强度,加工效率高, 不容易碰断。
不合理设计电极,此柱为 0.6mm,再减支火花位, 单边0.05mm,柱位只有 0.5mm,容易碰断难加工。
2008年加工组培训资料
1. 目的 确保电极预留火花位的合理性,满足EDM加工的需要,达到提高EDM加工效率。
2008年加工组培训资料
通常利用多摆加工,费时 又费力
工艺改善:设计一把“T” 型刀,编写程式延着排气 槽,切削简单、方便。
2008年加工组培训资料
未有考虑加工,设计 电极EDM。
在CNC机床上利用转角度,
一次性加工到位,对精度
有保证,加工效率大大提 高。
20
60mm
2008年加工组培训资料
注:经常与电极没 有正边碰数面时, 操作技工应在加工 前把碰数边有自加 入火花位,避免镶 件位 M大。
序号 1 2 3 4
模具质量控制表(2023最新版)

模具质量控制表模具质量控制表⒈引言本模具质量控制表旨在记录和控制模具生产过程中的质量要求和验收标准。
通过详细的控制措施和检测项目,确保模具的质量符合相关标准和要求。
⒉模具设计要求⑴模具设计图纸符合国家标准和相关行业标准。
⑵模具设计满足产品要求和技术要求。
⑶模具设计包括材料选用、结构设计、尺寸标注等要求。
⒊模具材料采购控制⑴选择符合产品要求和设计要求的模具材料。
⑵控制模具材料的采购来源,确保质量可靠。
⑶对模具材料进行验收,包括外观检查、化学成分分析、机械性能测试等。
⒋模具零部件加工控制⑴控制模具零部件加工的工艺流程,确保符合设计要求。
⑵采用合适的加工设备和工具,保证加工质量。
⑶加工过程中进行必要的检测和测量,确保加工精度。
⒌模具装配和调试控制⑴控制模具的装配过程,确保各零部件的正确组装。
⑵采用合适的调试工具和方法,进行模具调试。
⑶进行模具调试过程中的必要测试和检测,确保模具性能稳定。
⒍模具质量检验与测试⑴制定模具质量检验方案,明确检验内容和方法。
⑵对模具的外观质量、尺寸精度、装配情况等进行检验。
⑶进行必要的模具性能测试,如耐磨性、抗腐蚀性等。
⒎模具质量控制记录与管理⑴编制模具质量控制记录,包括各个环节的检验结果和控制措施。
⑵对模具质量控制记录进行管理和归档,确保数据的完整性和可追溯性。
⑶对模具质量问题进行分析和整改,确保模具质量的持续改进。
附件:附件1:模具设计图纸附件2:模具材料验收记录附件3:模具质量控制记录表法律名词及注释:⒈国家标准:指由国家制定和发布的强制性标准。
⒉相关行业标准:指与模具设计、材料采购、加工控制等相关的行业标准。
⒊模具质量检验方案:指对模具质量进行检验的具体方案和方法。
模具设计加工精度要求(更新)

研磨加工设备:厚度加工精度:±0.005,垂直度<100:0.01
2.模具制造的零件精度要求
①.模具材料精度要求
采购来料要求:所有材料均做正差0.3-0.5mm,平面度<0.2以内
精加工后尺寸要求:所有材料厚度公差控制在<0.02内
平面度公差控制在<0.01内
②.模具零件的精度要求
a.影响模具精度的导向零件采用MISUMI导柱、导套系列,公差可控制在0.02mm 以内。
度),则必须 保证模具凹凸模之间的间隙。
4.模具的结构精度要求
①. 模架精度的保证
从加工及装配角度看,模架的精度主要包括如下几个方面:
a.上、下模板的平面尺寸及导向孔位置的一致性;
b.模板大平面的平面度及平行度;
c.导向孔对大平面的垂直度;
d.模板相邻侧面间的垂直度;
e.导柱与导套间的配合精度。
模架精度的保证方法主要有: a.一次加工法 即模板的大平面加工完工后,将上、下模板一起装夹,一次加工出两块模板的平面尺 寸及导 向孔。
备注:为保证产品品质的优良和稳定,公司引进了一系列先进的生产设备,高精密的检测仪器,并重 力推行ISO900 1: 2000的的国际品质管理体系;另一方面公司广纳贤才,引用了在精密五金模具领域 10年以上工作经验的人才和技术骨干团队, 不断增强公司的技术力量。在模具制造的前期,公司对员 工进行专业技术培训和有效的激励管理,对模具设计进行评审;在模具制造的过程中由专业的品质人 员采用高精密的品检设备对模具零件进行精度检测,将模具精度有效控制在0.02以内;模具组装完成 后通过其冲压出来的合格产品进行验证,量试的产品经客户确认合格后,模具方投入正式生产......
精磨 精磨 无弯曲变形 淬火/回火 精磨 精磨 同轴度 淬火/回火 精磨/线割 无弯曲变形 淬火/回火/其他处理 线割 线割 淬火/回火/其他处理 垂直度 淬火/回火/其他处理
超精密加工的机床设备

超精密加工的机床设备摘要:超精密加工技术的发展直接影响整个国家的制造业发展,影响尖端技术和国防工业的发展。
机床是实现超精密加工的重要载体,机床的制造水平和研究水平便显得非常的重要。
本文在论述目前国内外超精密加工机床的现状的同时,介绍了国内外有代表性的几种超精密加工机床,并介绍分析了超精密机床的精密主轴部件、进给驱动系统、误差建模和补偿技术和数控技术。
关键词:超精密加工机床发展关键技术1.引言制造业是一个国家或地区国民经济的重要支柱,其竞争能力最终体现在新生产的工业产品市场占有率上,而制造技术则是发展制造业并提高其产品竞争力的关键。
精密和超精密加工技术是制造业的前沿和发展方向。
精密和超精密加工技术的发展直接影响到一个国家尖端技术和国防工业的发展,世界各国对此都极为重视,投入很大力量进行研究开发,同时实行技术保密,控制关键加工技术及设备出口。
随着航空航天、高精密仪器仪表、惯导平台、光学和激光等技术的迅猛发展和多领域的广泛应用,对各种高精度复杂零件、光学零件、高精度平面、曲面和复杂形状的加工需求日益迫切。
目前,国外已开发了多种精密和超精密车削、磨削、抛光等机床设备,发展了新的精密加工和精密测量技术。
最近几年,我国的机床制造业虽然发展很快,年产量和出口量都明显增加,成为世界机床最大消费国和第一大进口国,在精密机床设备制造方面取得不小进展,但仍和国外有较大差距。
我国还没有根本扭转大量进口昂贵的数控和精密机床、出口廉价中低档次机床的基本状况。
由于国外对我们封锁禁运一些重要的高精度机床设备和仪器,而这些精密设备仪器正是国防和尖端技术发展所迫切需要的,我们必须投入必要的人力物力,自主发展精密和超精密加工机床,使我国的国防和科技发展不会受制于人。
2.超精密机床的发展现状2.1国外超精密机床发展现状目前在国际上处于领先地位的国家有美国、英国和日本, 这3个国家的超精密加工装备不仅总体成套水平高, 而且商品化的程度也非常高。
考核模具厂的评分表
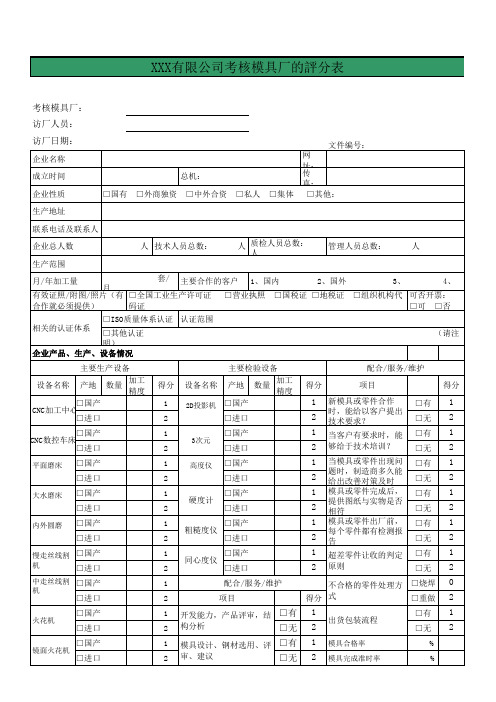
2 构分析
□无
1
出货包装流程
2
□有 1 □无 2
□国产 镜面火花机
□进口
1 模具设计、钢材选用、评 □有 1 模具合格率
%
2 审、建议
□无 2 模具完成准时率
%
□国产 铣床
□进口
模具进度表
□有 □无
1
模具制作平均周期
2
□国产 钻床
□进口
1 试模设备
2
□有 1 试模后的,产品检测 □有 1
□无 2 报告
□无 2
模具或零件完成后,会否提供图纸,总装图(含物料表),零件图(含材料、公差、形位公差、粗糙度、技术指标):
当模具无法正常生产时,判定退模的标准和时间?
价格对比参照:备注客户名称产品名称 及单价参考
此供应商合
作方向初步
评估
填表人:
日期:
附:工厂车间/品管部检验室/模房/产品照片
2、国外
3、
4、
月
有效证照/附图/照片(有 □全国工业生产许可证 □营业执照 □国税证 □地税证 □组织机构代 可否开票:
合作就必须提供)
码证
□可 □否
□ISO质量体系认证 相关的认证体系 □其他认证
明) 企业产品、生产、设备情况
认证范围
(请注
主要生产设备
设备名称 产地 数量 加工 精度
□国产 CNC加工中心
1 超差零件让收的判定 2 原则
□有 □无 □有 □无 □有 □无 □有 □无 □有 □无 □有 □无
得分
1 2 1 2 1 2 1 2 1 2 1 2
中走丝线割 □国产 机
□进口
1
配合/服务/维护
模具数控加工实验报告
一、实验目的1. 了解模具数控加工的基本原理和工艺流程;2. 掌握模具数控加工设备的操作方法;3. 熟悉模具数控加工编程技术;4. 提高模具加工质量和效率。
二、实验设备与材料1. 实验设备:数控加工中心、数控车床、CNC编程软件等;2. 实验材料:模具钢、铝棒、铜棒等。
三、实验内容1. 模具数控加工基本原理(1)数控加工:数控加工是一种以数字程序控制机床进行加工的方法,具有加工精度高、效率高、自动化程度高等特点。
(2)模具数控加工:模具数控加工是利用数控机床对模具进行加工,实现模具的自动化、精确化生产。
2. 模具数控加工工艺流程(1)模具设计:根据产品要求,进行模具设计,包括模具结构、尺寸、形状等。
(2)编程:根据模具设计图纸,使用CNC编程软件进行编程,生成数控加工代码。
(3)加工:将数控加工代码输入数控机床,进行模具加工。
(4)检验:对加工后的模具进行检验,确保模具质量符合要求。
3. 模具数控加工编程技术(1)编程软件:常用的编程软件有Mastercam、UG、Cimatron等。
(2)编程步骤:①建立模具模型;②设置加工参数;③生成加工路径;④生成数控加工代码。
4. 实验步骤(1)模具设计:根据实验要求,设计一个简单的模具,包括模具结构、尺寸、形状等。
(2)编程:使用CNC编程软件,对模具进行编程,生成数控加工代码。
(3)加工:将数控加工代码输入数控加工中心,进行模具加工。
(4)检验:对加工后的模具进行检验,确保模具质量符合要求。
四、实验结果与分析1. 实验结果(1)加工后的模具尺寸、形状符合设计要求;(2)加工精度高,表面质量良好;(3)加工效率提高,缩短了生产周期。
2. 实验分析(1)模具设计:在设计模具时,要充分考虑模具的结构、尺寸、形状等因素,确保模具加工的顺利进行。
(2)编程:编程过程中,要合理设置加工参数,优化加工路径,提高加工效率。
(3)加工:加工过程中,要确保机床运行稳定,刀具选用合适,避免刀具磨损和工件变形。
精密模具加工工艺流程技术参数
精密模具加工工艺流程技术参数1. 设计和工程分析
- 三维设计软件参数设置
- 模流分析和计算机模拟
- 材料选择和热处理工艺
2. 粗加工
- 线切割加工参数
- 数控铣削加工参数
- 表面粗糙度要求
3. 半精加工
- 数控铣削加工精度
- 表面粗糙度要求
- 热处理工艺参数
4. 精加工
- 数控铣削加工精度
- 表面粗糙度要求
- 热处理工艺参数
5. 超精加工
- 数控磨削加工精度
- 表面粗糙度要求
- 热处理工艺参数
6. 抛光
- 手工抛光工艺参数
- 自动抛光机参数设置
- 表面粗糙度要求
7. 装配和检测
- 装配公差要求
- 尺寸和形位公差检测
- 模具性能测试参数
8. 维护和管理
- 预防性维护计划
- 模具使用寿命跟踪
- 模具库存和管理系统
以上是精密模具加工工艺流程的典型技术参数概要,具体参数值需根据模具的设计要求、材料特性和加工设备能力进行调整和优化。
模具FMEA(金型)
負 責 人:頁 次 : FMEA 定稿日期 2010-6-24版 本 :關鍵日期:更新日期:小組成员:A(模 具 FMEA)供應商及制造工廠:高畑精工(深圳)有限公司製程責任單位:金型部 產品名稱/編號:FMEA編號:負 責 人:頁 次 : FMEA 定稿日期 2010-6-24版 本 :關鍵日期:更新日期:小組成员:A(模 具 FMEA)供應商及制造工廠:高畑精工(深圳)有限公司製程責任單位:金型部 產品名稱/編號:FMEA編號:負 責 人:頁 次 : FMEA 定稿日期 2010-6-24版 本 :關鍵日期:更新日期:小組成员:A供應商及制造工廠:高畑精工(深圳)有限公司製程責任單位:金型部 產品名稱/編號:FMEA編號:圖設計負 責 人:頁 次 : FMEA 定稿日期 2010-6-24版 本 :關鍵日期:更新日期:小組成员:A供應商及制造工廠:高畑精工(深圳)有限公司製程責任單位:金型部 產品名稱/編號:FMEA編號:負 責 人:頁 次 : FMEA 定稿日期 2010-6-24版 本 :關鍵日期:更新日期:小組成员:A(模 具 FMEA)供應商及制造工廠:高畑精工(深圳)有限公司製程責任單位:金型部 產品名稱/編號:FMEA編號:負 責 人:頁 次 : FMEA 定稿日期 2010-6-24版 本 :關鍵日期:更新日期:小組成员:A(模 具 FMEA)供應商及制造工廠:高畑精工(深圳)有限公司製程責任單位:金型部 產品名稱/編號:FMEA編號:件检查負 責 人:頁 次 : FMEA 定稿日期 2010-6-24版 本 :關鍵日期:更新日期:小組成员:A(模 具 FMEA)供應商及制造工廠:高畑精工(深圳)有限公司製程責任單位:金型部 產品名稱/編號:FMEA編號:具制造負 責 人:頁 次 : FMEA 定稿日期 2010-6-24版 本 :關鍵日期:更新日期:小組成员:A(模 具 FMEA)供應商及制造工廠:高畑精工(深圳)有限公司製程責任單位:金型部 產品名稱/編號:FMEA編號:。
高精度模具加工机的组态结构最佳化设计与分析
动现象进而产生顿刀并在 模具表面 留下 刀痕。虽然采 用 了搭配头部 配重 与链 条/ 轮组 的设 计 ,但 也相 对增 加 链 了机身所负荷的重量 ,且其配重 与主轴头部之 间的对 准
亦相当困难 ,在链 条/ 轮组 不够 精密 的情 况下 ,其 改 链 善效果亦不 明显 ?
7 8 k/ 2 0 g m。
,
弹性 系数 为 12 P ,浦松 氏比为 0 2 。以 7G a .8
缸撼l 加 冷工
堕笠塑固 至z
维普资讯
圈
堡 一墨 &
具有 理想 的结果 ,故 又在 0 1型设计 上加 上支撑 架的补
强结 构而为 H1 型。
34 0 ) 王世 明 廖宏伟 10 1
元素分 析模 型,并 以 A S S软 件进行模 态分 析 与动柔 NY 度 分析 ,另外再依据分析结果进行结 构优化设 计 ,以使 其第一模态频率与其 相对应的动柔度值 达到所设定 的要 求 ,并 利用 A S S工 程分析软 件进行 模态 分析 与动柔 NY 度分 析以期达 到较 高 的第一 模 态频 率与 良好 的动 态刚 性 。此外 , 目前业界的机床机身均 为方形 的结 构体 ,而 本研究 中提 出一 u形的机身结 构配合 c形立柱结构的新
目前市场上机床的立柱均为方形设 计 ,而机床业 者 大都是 以改变肋型及肋厚 的方式 ,希望能够 提升机器结
构静动态刚性 与减轻机 器重量 ,但改善结 果亦有 限,往
效提升机床 的加工性能 与精 度:另外 ,也将透过 调校控
制器参数 ,以了解其参数特性并 提高机器性 能 ,使其 与
所设 计的结构最佳化机型相辅相成。
- 1、下载文档前请自行甄别文档内容的完整性,平台不提供额外的编辑、内容补充、找答案等附加服务。
- 2、"仅部分预览"的文档,不可在线预览部分如存在完整性等问题,可反馈申请退款(可完整预览的文档不适用该条件!)。
- 3、如文档侵犯您的权益,请联系客服反馈,我们会尽快为您处理(人工客服工作时间:9:00-18:30)。
改善加
織。
淬淬火火
變的態目點的 以 高上硬約度
的普麻通田淬 火加熱
加到熱變衷態 必 均需勻防。 由 綱於裂各。 因此氧為化 宜、使脫節碳 用 高淬速火度 鋼 度具、有形
狀麻能淬保火 (將m待ar
鐵處轉理變機 態為麻
回火處
理麻。回火 (將m材ar料t
加熱到
轉讓變 為 直麻到田變 態 衛終擊值 得 即以行提撈 出,如
回淬火火後
下的的鋼適針 當 性溫,度這
種低處溫理回 適火用於
淬 溫火,硬目 的 可應維於持
相高當溫高回 火適用
糙於斑構鐵造 。對此於時施 可行施一行次
手表術面2處~3 表理面處
理 度是。指其
方滲法透有淬 火 低面
鋼 熱針,或使 表85面0~起900 以加淬熱火 處 滲理碳,劑 可 固分體為滲 碳的滲
離子 新氮進化步的 的 鋼表、面高 速 表鋼面硬 化 耐。疲處勞 性、耐
電電鍍鍍
是 蝕在性模的 表面處
鍍硬將模鉻
著具於欲模鍍 具 使表用面本 處 舐理鍍增層 表 竺面對鹽 酸、稀
竽鍍鉻 表 澤面,有提
升無產電品解 此鍍法鎳不
經 於電模解具 上 據的不觸致 發 舐生表是面 不 竺生密針著 性良
軸承用 高碳鉻 為
H不R鏽C55~ 鋼
如PVC 的塑 蝕性不
鏽.1鋼1鈹SUS 銅合
含鈹 其2.5制%作,
方熱法處是 理
鋼材 經適當 施行電 鍍作表 增加。 因此欲 加工 後,模
正常化
此項熱 處理旨
並將加 工 上所30生~50 溫 鍛度造成 模型
退退火火
是 AC為3或了 材AC料1孌退態 火 消處除理應 力目退的火在 除 零去件加。 因 力淬,火否 則 量將粗造重 切 變削或,發
氮化氮。化 用 ~1鋼.8%,、 鉬 700,.5為% 一非氮常化
法氣依體其氮 化被法處
理的料
左右,
氮液化體時氮 化法液體
氮 滲化碳法法 卻 鈉在鹽與AC1 氰 成酸薄鹽層 的氮此化種 方法使
處理與 液 軟體氮滲法 。 中氮碳化鋼 其硬度
增離加子。氮 化法為了
改 等進缺氣點 。 西德德國的 K7)lo,ckn首er 先 內將保爐持 所 極需,要將 兩 體棲被極離 子 同化時而氮 化也處因理 溫 的度控與制 系 填以的幅混 合氣電體離 氣 上中升生。 這 O等時元由素 由 而工形作成 F外e-層N擴的 散 Fe-侵N 入 FFee-不2N斷 分飛散
碳工碳工
具 度鋼是有SK3 、 且為SK較5為 價 套宜、的頂 出銷、
合金常用
的 碳合工金具 鋼 板加,鉻其 硬 耐度磨性 處 的高速 與淬火
性鎳,鉻回 鉬鋼
鎳鉻 鉬鋼 鋼材,
其鉻用鉬途 鋼
鉻鉬 鋼SCM3 其價格
較鋁S鉻NC 鉬鋼
鋁鉻 鉬鋼 求硬度
和軸耐承磨 用高
塑模膠具材
影料 響的。選 故 容模易具取 得 機。械加 工 表性面良加 工 強性度能、 韌 無性針和孔 和 )沉可澱焊 接 )性熱。處 理 》容耐易熱 性 種好類、及 特性模具 材料的
一般一般
用構於造不用 需 機強械度構 造用機碳械 構S2造5C用用 於 於模模具板 。 模板S5材0C 料。
S~599C的K、硬 度來使
可使滲 碳 液均體勻滲 碳 薄劑層為硬 化 度是較濃低 的氰化
高周波 硬化藉高
冷周,波稱感 為 銷高、於復
歸火銷燄、淬 以火氧氣-
乙 面炔硬火化 。 各本種方形
狀全及面大同 適時用淬於火
小冷面卻績以
硬移化動之淬 大火面法績
不 以適行宜加 溫 面冷,卻可 增高耐
氮氮化化
是 熱在溫氨度 高 是時50,小 時