钴钼系耐硫变换催化剂使用注意事项
钴钼系催化剂的硫化

硫化成功的必备条件有三个:1)要有足够高的硫化温度,一般不大于500 ℃;2)要有足够的强制硫化时间,并且最好有数小时的闷炉;3)强制硫化时,原料气中的硫化氢越高越好,一般不低于15 g/Nm3 。
硫化时要防止催化剂超温,超过550 ℃对催化剂造成危害,但短时间超温对催化剂活性影响不大。
一、硫化条件1、温度对硫化反应深度的影响很大,一般入口温度控制在230~260℃,床层温度控制在250~280℃。
硫化反应后期应尽量提温,适当的高温(~425℃)既可以保证催化剂的活性,又可缩短硫化时间。
2、硫化压力对硫化深度的影响不是很大,可根据装置的实际情况来确定压力,一般不低于1.0MPa(表压)。
3、H2S的浓度过低(体积分数≤0.2%)时,还原后的催化剂活性较差;H2S的较高时,对催化剂的影响不大。
出于安全考虑,H2S的浓度不宜提的太高。
4、系统中H2的体积分数尽量控制在10%~20%,过低会影响CS2的氢解,过高则有可能发生还原反应。
CS2在200℃以上时才发生氢解反应,所以添加CS2要等到温度达230℃左右开始添加。
过早添加容易使CS2氢解不完全,在系统内冷凝和吸附。
当达到温度时,就会突然发生氢解反应,放出大量的反应热导致床层温度暴涨。
但超过250℃再加CS2,就可能发生CoO和MoO3的还原反应,使催化剂失活。
运行过程中要保持H2的体积分数在10%~35%之间,因为当H2的浓度过低时,亦有可能造成CS2氢解不完全,在系统内冷凝和吸附。
当H2含量提高时,CS2大量氢解,释放过多的反应热,从而导致催化剂床层温度暴涨。
串联硫化时要防止“提温提硫”的同时发生,因为当上段硫穿透时,较高的热点温度和上段穿透的硫进入下一段,造成下段“提温提硫”,很容易造成超温。
钴钼系耐硫变换催化剂装填及使用过程注意事项
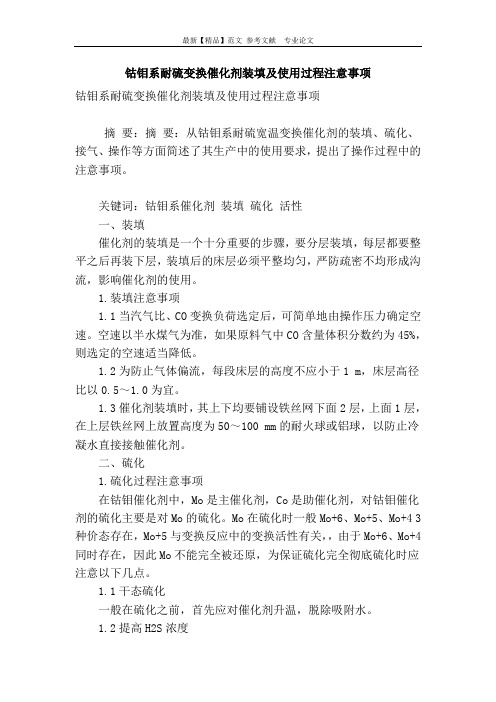
钴钼系耐硫变换催化剂装填及使用过程注意事项钴钼系耐硫变换催化剂装填及使用过程注意事项摘要:摘要:从钴钼系耐硫宽温变换催化剂的装填、硫化、接气、操作等方面简述了其生产中的使用要求,提出了操作过程中的注意事项。
关键词:钴钼系催化剂装填硫化活性一、装填催化剂的装填是一个十分重要的步骤,要分层装填,每层都要整平之后再装下层,装填后的床层必须平整均匀,严防疏密不均形成沟流,影响催化剂的使用。
1.装填注意事项1.1当汽气比、CO变换负荷选定后,可简单地由操作压力确定空速。
空速以半水煤气为准,如果原料气中CO含量体积分数约为45%,则选定的空速适当降低。
1.2为防止气体偏流,每段床层的高度不应小于1 m,床层高径比以0.5~1.0为宜。
1.3催化剂装填时,其上下均要铺设铁丝网下面2层,上面1层,在上层铁丝网上放置高度为50~100 mm的耐火球或铝球,以防止冷凝水直接接触催化剂。
二、硫化1.硫化过程注意事项在钴钼催化剂中,Mo是主催化剂,Co是助催化剂,对钴钼催化剂的硫化主要是对Mo的硫化。
Mo在硫化时一般Mo+6、Mo+5、Mo+4 3种价态存在,Mo+5与变换反应中的变换活性有关,,由于Mo+6、Mo+4 同时存在,因此Mo不能完全被还原,为保证硫化完全彻底硫化时应注意以下几点。
1.1干态硫化一般在硫化之前,首先应对催化剂升温,脱除吸附水。
1.2提高H2S浓度高硫浓度可保证硫化反应的需要,并缩短反应时间,不过在硫化初期不要将H2S含量提得太高,应采取逐渐渗透的方式,避免反应过急,使催化剂温度波动过大。
1.3低温硫化当床层温度达到180℃时,将气体入口温度降到170~180℃,然后加入CS2,使催化剂在H2S吸收区反应,可避免硫化初期温度超过200℃而引起的异常激烈反应。
主要硫化阶段为180~300℃为保证温度,应将炉温控制在250℃左右,并逐步加大CS2的量。
当分析显示变换炉出口H2S达到1 g/m3或进出口H2S含量相等时,保持运行2 h 即为合格。
钴钼系耐硫宽温变换催化剂使用过程注意事项
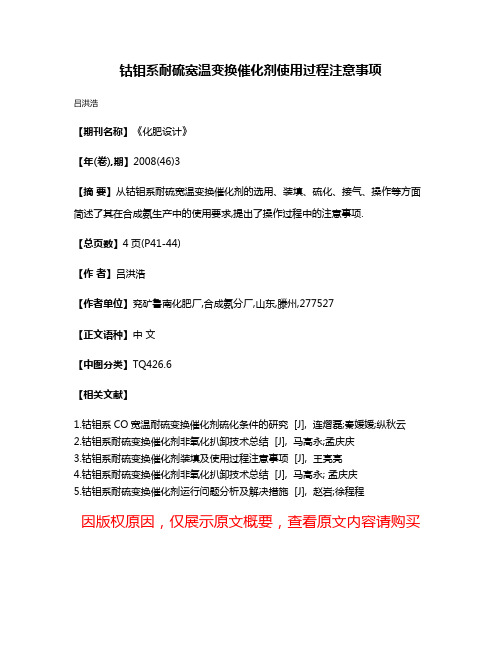
钴钼系耐硫宽温变换催化剂使用过程注意事项
吕洪浩
【期刊名称】《化肥设计》
【年(卷),期】2008(46)3
【摘要】从钴钼系耐硫宽温变换催化剂的选用、装填、硫化、接气、操作等方面简述了其在合成氨生产中的使用要求,提出了操作过程中的注意事项.
【总页数】4页(P41-44)
【作者】吕洪浩
【作者单位】兖矿鲁南化肥厂,合成氨分厂,山东,滕州,277527
【正文语种】中文
【中图分类】TQ426.6
【相关文献】
1.钴钼系CO宽温耐硫变换催化剂硫化条件的研究 [J], 连熠磊;秦媛媛;纵秋云
2.钴钼系耐硫变换催化剂非氧化扒卸技术总结 [J], 马高永;孟庆庆
3.钴钼系耐硫变换催化剂装填及使用过程注意事项 [J], 王亮亮
4.钴钼系耐硫变换催化剂非氧化扒卸技术总结 [J], 马高永; 孟庆庆
5.钴钼系耐硫变换催化剂运行问题分析及解决措施 [J], 赵岩;徐程程
因版权原因,仅展示原文概要,查看原文内容请购买。
耐硫变换催化剂循环硫化方案
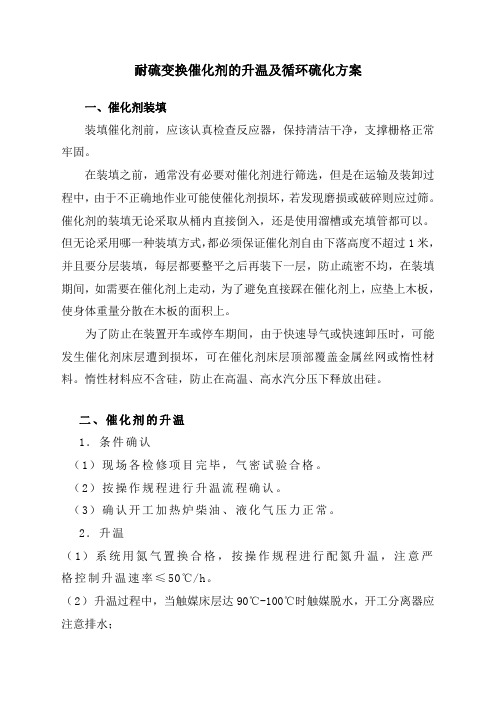
升 0.5 常温~120
30
3
0.5
120
6
温
0.5
120~220
30
3
0.5
220
6
备注 氮气量 20000Nm3/h 恒温释放吸附水
恒温拉平床层温差
三、催化剂的硫化 1、当催化剂床层温度达到 200℃~220℃时,把氢气加到氮气中,控
制反应器入口温度在 200℃~220℃,分析变换炉入口氢气含量 10%(干基) 左右。
耐硫变换催化剂的升温及循环硫化方案
一、催化剂装填 装填催化剂前,应该认真检查反应器,保持清洁干净,支撑栅格正常 牢固。 在装填之前,通常没有必要对催化剂进行筛选,但是在运输及装卸过 程中,由于不正确地作业可能使催化剂损坏,若发现磨损或破碎则应过筛。 催化剂的装填无论采取从桶内直接倒入,还是使用溜槽或充填管都可以。 但无论采用哪一种装填方式,都必须保证催化剂自由下落高度不超过 1 米, 并且要分层装填,每层都要整平之后再装下一层,防止疏密不均,在装填 期间,如需要在催化剂上走动,为了避免直接踩在催化剂上,应垫上木板, 使身体重量分散在木板的面积上。 为了防止在装置开车或停车期间,由于快速导气或快速卸压时,可能 发生催化剂床层遭到损坏,可在催化剂床层顶部覆盖金属丝网或惰性材 料。惰性材料应不含硅,防止在高温、高水汽分压下释放出硅。
H2S 分析 1 次/ 半小时
四、硫化过程中不正常情况的处理 1、床层温升缓慢 配氢量或氮气量过高,入口温度控制较低,可通过增加开工加热器的
蒸汽量,提高变换炉入口温度来控制。 2、床层温度急剧上升 二硫化碳加入过快或入口温度调节过高都可能导致温度急剧上升。可
采取的措施为:降低变换炉入口温度;减少直到停止加入二硫化碳。
变换催化剂升温硫化注意事项
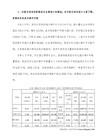
置 换 4~6 200-300 180-200 直 至出 口 硫 化 氢 含 量
≤1g/m3 ,并入系统。
以防电加热器超压。
(3) 在煤气升温结束前,硫化罐应按要求装填好CS2,检查制氮机所送管线是否通畅,升压至
0.1~0.2MPa备用。
3.3. 硫化期
(1) 待低变炉进口温度达210℃,即可用N2将CS2压入系统,用硫化罐出口流量计控制CS2加入量,保证入炉CS2浓度为5~10g/m3,开始硫化。
3.4. 强化期
催化剂层各点为400~450℃,保持~4小时出口H2S含量≥10g/NM3,强化硫化结束。
3.5. 降温置换阶段
(1) 硫化至各段均进入降温置换阶段,控制电炉出口温度200℃,待床层温度降至≤300℃,然后
停止加 CS2置换。
(2) 联系检修拆、加盲板后,即可导气制合格变换气开车。
(3) 变换常压放空运行两小时后至变换气成分合格后方可向后工序送气。
(4) 注意事项:
(1) 升温硫化严格按要求进行,升温期间,单点温度不得超过500℃,升温速率严格按30∽50℃/h
进行。
(2) 硫化过程中,严格控制进口煤气中O2%,严防O2含量跑高造成炉温急骤上升,烧毁触媒, CS
(2) 控制电炉出口温度200~250℃。催化剂床层温度200~300℃,时间约为8~10小时,待于出
口硫化氢≥ 3g/NM3,可认为硫化初期结束。
(3) 硫化时密切注意床层温度,用电加热器组数、CS2加入量及煤气量等调节床层温度。
(4) 硫化时炉进口H2含量应保证≥25%,便于CS2氢解。
反应生成H2S,与CoO、MoO3反应生成CoS、MoS2。
浅析变换工艺催化剂的使用及常见问题的处理

浅析变换工艺催化剂的使用及常见问题的处理作者:永学健张涛来源:《中国化工贸易·下旬刊》2019年第07期摘要:本篇文章中所讲的变换催化剂主要指的是钴、钼系催化剂,这种催化剂使用时间较长,使用面积覆盖也较为广泛,为钴、钼系催化剂的积累了丰富的使用经验。
但是在钴、钼系催化剂这么多年的使用过程之中,也出现了诸多的问题影响了催化剂的正常使用。
因此,笔者针对现如今关于钴、钼系催化剂在使用当中的问题提出自己的论述观点,并且总结出原因分析以及提出此昂对应的解决办法,希望可以对钴、钼系催化剂的使用有一定的借鉴意义。
关键词:变换工艺催化剂;钴、钼系催化剂;催化剂的使用钴、钼系催化剂主要适用于以煤或者是重油为主要原料的合成氨厂,这种催化剂有着超高的耐硫功能,但是在没有或者有很少的硫化氢的环境之中,钴、钼系催化剂的活性就会比较弱。
由于最近几年,人们越发的关注环境保护问题,化肥行业也随之开展了节约能源,降低能源消耗的工作,因此,钴、钼系催化剂由于它的耐硫功能就得到了诸多厂家的青睐,但是在使用的过程之中由于存在着问题没有得到解决,也就造成了催化剂在工作之中出现结焦、失活等现象的发生。
1 钴、钼系催化剂的正确使用在上个世纪50年代的时候,钴、钼系催化剂就是在当时研发的最新型的催化剂,它对一氧化碳的变换工艺有着很好的变幻效果。
最有典型的主要是有K8-11等等。
钴、钼系催化剂主要是通过氧化铝为主要的載体,利用氧化铝改善低温活性性能,钴、钼系催化剂的助催化剂在一般情况之下都是选择碱金属钾。
在进行催化剂的选用的时候,一定要注意不仅是要关注它的活性性能,还要考虑它的强度。
通常情况下来说的话,催化剂的活性与强度是成反比例的,催化剂的活性性能越好,反之,催化剂的强度就会变得非常的差[1]。
催化剂生产商在进行制造催化剂的过程之中要充分的考虑到强度与活性性能二者之间的关系,并且还要找到一个可以达到这两者之间的平衡点。
钴、钼系催化剂的最大的特点就是很高的宽温耐硫性,这种催化剂通常情况之下都具有良好的活性性能、较高的机械强度以及选择性,尤其是在低温变换活性和低硫变换活性这两个方面,在世界上也是处于领先地位的,同时钴、钼系催化剂对高空速、高水气的环境适应能力很强,具有良好的稳定,还具有较大的操作弹性。
耐硫变换催化剂及其使用技术
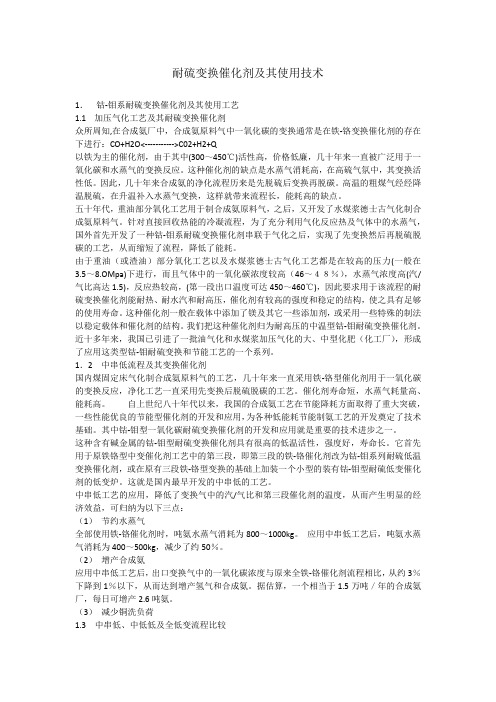
耐硫变换催化剂及其使用技术1.钴-钼系耐硫变换催化剂及其使用工艺1.1加压气化工艺及其耐硫变换催化剂众所周知,在合成氨厂中,合成氨原料气中一氧化碳的变换通常是在铁-铬变换催化剂的存在下进行:CO+H2O<----------->C02+H2+Q以铁为主的催化剂,由于其中(300~450℃)活性高,价格低廉,几十年来一直被广泛用于一氧化碳和水蒸气的变换反应。
这种催化剂的缺点是水蒸气消耗高,在高硫气氛中,其变换活性低。
因此,几十年来合成氨的净化流程历来是先脱硫后变换再脱碳。
高温的粗煤气经经降温脱硫,在升温补入水蒸气变换,这样就带来流程长,能耗高的缺点。
五十年代,重油部分氧化工艺用于制合成氨原料气,之后,又开发了水煤浆德士古气化制合成氨原料气。
针对直接回收热能的冷凝流程,为了充分利用气化反应热及气体中的水蒸气,国外首先开发了一种钴-钼系耐硫变换催化剂串联于气化之后,实现了先变换然后再脱硫脱碳的工艺,从而缩短了流程,降低了能耗。
由于重油(或渣油)部分氧化工艺以及水煤浆德士古气化工艺都是在较高的压力(一般在3.5~8.OMpa)下进行,而且气体中的一氧化碳浓度较高(46~48%),水蒸气浓度高(汽/气比高达1.5),反应热较高,(第一段出口温度可达450~460℃),因此要求用于该流程的耐硫变换催化剂能耐热、耐水汽和耐高压,催化剂有较高的强度和稳定的结构,使之具有足够的使用寿命。
这种催化剂一般在载体中添加了镁及其它一些添加剂,或采用一些特殊的制法以稳定载体和催化剂的结构。
我们把这种催化剂归为耐高压的中温型钴-钼耐硫变换催化剂。
近十多年来,我国已引进了一批油气化和水煤浆加压气化的大、中型化肥(化工厂),形成了应用这类型钴-钼耐硫变换和节能工艺的一个系列。
1.2中串低流程及其变换催化剂国内煤固定床气化制合成氨原料气的工艺,几十年来一直采用铁-铬型催化剂用于一氧化碳的变换反应,净化工艺一直采用先变换后脱硫脱碳的工艺。
Co - Mo 系耐硫变换催化剂的硫化处理

Co - Mo系耐硫变换催化剂的硫化处理1、硫化反应耐硫变换催化剂在使用前一般要将其活性组份的氧化态转化为硫化态,这一转化过程称之为硫化。
钴钼系耐硫催化剂的硫化反应在热力学上可用下列式子表示:CS2 + 4H2 = 2H2S + CH4 + 230. 45 kJMoO3 + H2 + 2H2S = MoS2 + 3H2O +48. 15 kJCoO + H2S = CoS + H2O + 13. 4 kJCO + 3H2 = CH4 + H2O + 214. 8 kJCO+H2O = CO2+H2 +41.19 KJ/mol2H2 +O2 =2 H2O + 241. 83 kJ上述反应均为放热反应。
常用的硫化剂有CS2和H2S两种。
其中H2S来自高硫煤气或固体硫化剂, CS2可直接加入原料气。
另外,硫氧化碳等有机硫也可作硫化剂。
2、硫化反应机理在催化剂的硫化过程中,不论采用何种硫化方法,最基本的硫化剂就是H2S。
因此只要在硫化条件下容易提供H2S的物质都可用作硫化剂。
工业上通常采用低分子量的有机硫化合物和无机的固体硫化剂。
硫化过程通常分为两个反应步骤,即硫化剂的分解和催化剂活性组分的相态转化。
(1)硫化剂的分解硫化剂的分解是指硫化剂在催化剂正常的硫化工艺条件下,硫化剂与氢气或水发生化学反应生成H2S的过程,下面是常见的几种硫化剂及其分解反应。
CS2(二硫化碳)十4H2=CH4十2H2SCOS(硫氧碳)十H2O=CO2十H2S(2)硫化对耐硫变换催化剂的作用:使催化剂中的金属组分即活性组分由氧化态变成硫化态,如MoO3变成活性物种MoS2;使催化剂中的活性组分处于最佳活性价态,以Mo为例,Mo由MoO3中Mo6+经过硫化变为活性物种MoS2。
MoO3和CoO在催化剂硫化过程中发生的化学变化表示如下:(3)硫化剂的选择从硫化剂的分解反应上看,其最终产物为H2S,理论上认为除本身的分解反应外,不会对催化剂的硫化过程造成影响。
- 1、下载文档前请自行甄别文档内容的完整性,平台不提供额外的编辑、内容补充、找答案等附加服务。
- 2、"仅部分预览"的文档,不可在线预览部分如存在完整性等问题,可反馈申请退款(可完整预览的文档不适用该条件!)。
- 3、如文档侵犯您的权益,请联系客服反馈,我们会尽快为您处理(人工客服工作时间:9:00-18:30)。
K8-11系列催化剂使用注意事项一、催化剂的使用1.1 催化剂的装填装填催化剂之前,必须认真检查反应器,保持清洁干净,支撑栅格正常牢固。
为了避免在高的蒸汽分压和高温条件下损坏失去强度,催化剂床层底部支撑催化剂的金属部件应选用耐高温和耐腐蚀的惰性金属材料。
惰性材料应不含硅,防止高温、高水汽分压下释放出硅。
催化剂装填时,通常没有必要对催化剂进行过筛,如果在运输及装卸过程中,由于不正确地作业使催化剂损坏,发现有磨损或破碎现象必须过筛。
催化剂的装填无论采取从桶内直接倒入,还是使用溜槽或充填管都可以。
但无论采用哪一种装填方式,都必须避免催化剂自由下落高度超过1米,并且要分层装填,每层都要整平之后再装下一层,防止疏密不均,在装填期间,如需要在催化剂上走动,为了避免直接踩在催化剂上,应垫上木版,使身体重量分散在木版的面积上。
一般情况下,催化剂床层顶部应覆盖金属网和/或惰性材料,主要是为了防止在装置开车或停车期间因高的气体流速可能发生催化剂被吹出或湍动,可能由于气体分布不均发生催化剂床层湍动,损坏催化剂。
由于高压,原料气密度较大,为了尽可能的减小床层阻力降,应严格控制催化剂床层高度和催化剂床层高径比。
通常催化剂床层高度应控制在3~5m;催化剂床层高径比控制在1.0~1.8。
1.2 开车1.2.1 升温为防止水蒸气在催化剂上冷凝,首次开车升温时,应使用惰性气体(N2、H2、空气或天然气)把催化剂加热到工艺气露点以上温度,最好使用N2。
采用≤50℃/h的升温速度加热催化剂,根据最大可获得流量来设定压力,从而确保气体在催化剂上能很好分布。
在通常情况下,气体的有效线速度不应小于设计值的50%,但也不应超过设计值。
当催化剂床层温度达到100℃~130℃时,恒温2~3小时排除吸附的物理水,然后继续升温至200℃~230℃时,进行下一步的硫化程度。
如果最初加热选用的是空气,在引入硫化气之前,必须用氮气或蒸汽吹扫系统,以置换残余氧气。
硫化气的切换基本上在常压或较高压力下进行,这取决于气流的方便。
1.2.2 硫化与铁铬系催化剂的还原相似,钴钼系耐硫变换催化剂使用前一般需要经过活化(硫化)方能使用,硫化的好坏对硫化后催化剂的活性有着重要作用。
如果工艺气中的硫含量较高,一般使用工艺气直接硫化时,硫化过程中可能发生下述反应:CoO+H2S ↔ CoS+H2O ∆H0298=-13.4KJ/mol (1)MoO3+2H2S+H2↔ MoS2+3H2O ∆H0298=-48.1KJ/mol (2)CO+H2O ↔ CO2+H2∆H0298=-41.4KJ/mol (3)CO+3H2↔ CH4+H2O ∆H0298=-206.2KJ/mol (4)硫化过程为了使产生的热量尽可能小,便于硫化温度控制,在硫化过程中应尽可能地抑制这后两个反应,特别是反应(4),通常催化剂转化成硫化态后,对反应(3)是有利的,但催化剂为氧化态时,并在较高的压力下,即开车的初期对反应(4)是有利的。
为了初期一般采用低压、小气量硫化,随着硫化,逐渐提高压力和气量。
如果工艺气中的硫含量较低,可采用补加硫化剂进行硫化,可利用的硫化剂有多种。
主要有H2S、硫醚、硫醇、CS2和COS等用CS2和COS作为硫化剂时,硫化过程除了发生上述反应外,还发生如下反应:CS2+4H2↔ 2H2S+CH4∆H0298=-240.6KJ/mol (5)COS+H2O ↔ CO2+H2S ∆H0298=-35.2KJ/mol (6)反应(5)产生热量最多,如果用CS2来硫化催化剂,应控制加料速度,防止超温。
温度达200℃时,CS2的氢解才具有较大的转化率。
硫化时,硫的加入量一般根据催化剂中的活性组份完全硫化来计算,K8-11G 催化剂每1000kg近似需56kg硫,加硫速度依催化剂床层温升情况而定。
由反应器出口H2S含量大大增加并与入口平衡来确定硫化结束。
温度大于200℃时,硫化反应就可以足够高的速度进行,以CS2作硫化剂单独循环时,要求气体和催化剂床层之间的∆T≤50℃,选用天然气或氮气加热催化剂时应加入5~10%氢气,以利于CS2氢解;而使用工艺气硫化时,∆T也应≤50℃。
硫化结束时,将温度慢慢提升到规定的变换入口温度。
K8-11G催化剂的硫化程序(1)用工艺气硫化用工艺气硫化催化剂,尤其在较高压力下,应该注意存在甲烷化反应的可能性。
为了防止此反应发生,或者如果已经发生了这种反应,应通过控制温度来限制此反应。
硫化前,应该用氮气吹净反应器,催化剂在近似于0.5MPa压力下,按上述升温程序用氮气升温到200~230℃,然后,把湿工艺气加到到氮气中(比例:湿工艺气:氮气=1:3)同氮气一起进入反应器,并保持温度,压力不变。
采用渣油部分氧化气作原料,由于气体混合物中,氢气分压、CO分压低,甲烷化反应的可能性很小,万一发生此反应导致超温,则可通过减少或切断工艺气,用氮气将催化剂床层冷却到250℃左右,再慢慢地加入湿工艺气继续硫化。
当硫化剂床层温度稳定时,将湿工艺气流量增加一倍。
同时相应减少氮气,为的是使气体的线速度不超过允许值,此时气体的比率为:工艺气:氮气=2:3。
为了达到所规定的硫含量,缩短硫化时间,可以通过添加硫成分。
增加硫分的办法有两种,一种是增加工艺气流量并相应地减少氮气流量直到停用氮气,但是要严格防止硫化过快引起超温,在催化剂被硫化20%之前,不宜增加流量,另一种办法是增加工艺气的硫含量,例如当工艺气体中硫含量较低时,可添加CS2等硫化剂或向原料渣油中添加硫化剂、煤中添加硫磺,后者安全,易于控制。
但是,不管采用何种办法增加硫分,缩短硫化时间,都必须保证由硫化反应造成的温升∆T不能超过50℃当有明显的硫穿透时,为了深度硫化,应逐步增加压力至0.8Mpa、1.2Mpa、1.5Mpa进行硫化。
当在1.5Mpa压力下有明显的硫穿透时,表明硫化接近完全,等出口硫含量与入口硫含量平衡时,表明硫化结束。
如有几个反应器时,当第一反应器的催化剂基本硫化完成后,必须将温度增加到280~300℃以上,目的是使第二或第三反应器达到足够高的温度,保证硫化完成,但不应超过350℃。
硫化结束后,以10~15℃/h的速度将入口温度提高到设计温度,将工艺气流量及压力也相应地提高到设计值,同时切除N和停止补充硫分。
此时,催化2剂床层温度要保持足够高,避免水蒸气在催化剂上冷凝。
(2)用循环气硫化当催化剂床层入口温度达到200℃~230℃时,开始进行硫化程序。
首先按设计用硫量的50%(m/m)进行硫化,硫化开始,可以通过分析反应器出口硫含量变化来观察硫化进行情况,同时注意温度变化。
在硫化剂的含量增加到所规定的设计值之前,应该保持温度稳定,并且温升 T不应超过50℃。
当床层出口有显著的硫穿透时,表明催化剂硫化接近完全。
硫化末期催化剂床层几乎没有硫化反应,然后以近似于10~15℃/h的速度,把入口温度提高到规定温度(280~300℃)。
如有几个反应器时,当第一反应器的催化剂基本硫化完成后,必须将温度增加到280~300℃以上,目的是使第二或第三反应器达到足够高的温度,保证硫化完成,但不应超过350℃。
硫化结束后,停止送入硫分,如果可能,变换反应器的压力应通过天然气、氮气、氢气或这三种气体的混合气提压到约 3.0MPa。
然后将原料气送入催化剂床层,慢慢的把压力和温度调整到设计值。
在这个阶段,应该一直小心保持流速,并且根据实际压力调节气体流量,注意催化剂上的气体有效线速度不超过设计值。
每个反应器都必须保持足够高的温度,以保证高于露点温度25℃以上。
1.3正常运转为了延长催化剂使用寿命,在正常运转期间应尽可能保持较低的入口温度(露点以上25℃),并保持温度、压力、水/气、硫化氢浓度等各项操作参数的平稳,减少开停车次数,避免无硫操作或含量过低。
运行中,不允许瞬间大幅度降压或升压。
注意各反应器的压差变化,工况改变或操作异常时,应注意测定出口CO含量,必要时标定各项参数。
当长时间运转后催化剂活性衰退,出口CO的含量增加时,可小幅度逐渐提高入口温度使出口CO含量保持在设计值以下。
1.4停车装置短时间停车时,在不发生蒸汽冷凝的情况下,切断原料气保持压力即可。
如果是较长时间停车,则应该降低反应器压力,引纯氮吹扫保护催化剂,防止蒸汽冷凝,保持反应器压力稍大于常压。
如果要从反应器中卸出催化剂,应用氮气将催化剂冷却到50~70℃,打开反应器顶部的人孔和反应器出口卸料阀,卸出催化剂。
1.5使用过的催化剂开车操作中已经用过的催化剂呈硫化状态,因此必须绝对避免这些催化剂与空气接触。
加热这些催化剂的最好方法是使用天然气或纯氮。
若氮气中含有少量氧气,,应该加入适量氢气。
也可用纯氢升为了防止形成可能造成下游装置腐蚀的SO2温,但必须考虑到氢气会使催化剂脱硫,最好使用纯氮来加热催化剂。
1.6催化剂的氧化和再生催化剂再生的目的在于尽可能使催化剂恢复到原来的活性。
但是,这种再生只有由于外来化合物而引起的活性降低,并且这类化合物可用氧脱除时才有可能,通常这类化合物是指在变换炉上游形成的碳,或者在操作期间,沉积在催化剂上,向焦碳一样的聚合物。
催化剂床层阻力降的上升常常是由于原料气中夹带的杂质和焦碳在上层催化剂沉积造成的。
当焦碳含量达到5%~10%(m/m)时,应进行除碳再生。
再生方法通常采用添加少量空气(如开始2%然后逐渐增加到10%)的水蒸气或N2,在一定温度下与焦碳反应生成CO2、CO。
脱除碳的同时,催化剂中的硫化物也会与氧反应生成SO2。
氧化过程放出大量的热量,因此要缓慢进行,严防超温烧毁催化剂。
根据床层温度变化和出口CO2含量的变化判断氧化反应进行情况,逐渐增加空气量直至出口检测不到CO2,表明再生过程结束。
为了达到满意的再生效果,蒸汽的入口温度可选择在350~400℃,达到预定入口温度之后,开始通入空气,密切注意催化剂床层温度变化,防止超温。
依除碳情况,可将入口温度降到300℃,床层热点温度最好接近450~500℃。
为了利于气体分布,烧碳时应降低压力,但也不能过低,以避免气速太高。
碳和硫不仅与氧反应,也能与水蒸气反应,因此出口气体除CO2和SO2之外,还有氢和硫化氢。
若再生后床层阻力降仍然较大,则应卸出催化剂筛除杂质和破碎催化剂,然后重新装填,最好按原来的床层位置回装催化剂,补充的新催化剂装在最上层。
由于上述再生和重新装填催化剂操作复杂,不易掌握,最好不采用再生的办法。
由于杂质和焦碳沉积主要集中在催化剂的入口部分,因此推荐采用更换上层催化剂的办法来达到降低阻力降和恢复上层催化剂活性的目的。
也可用在流程上增加预变换段,装少量催化剂起到滤除粉尘、杂质和毒物的作用,保护主床催化剂。
2、反硫化形成的条件(1)在一定的温度、水汽比的条件下,有相对应的最低H2S含量。