钴钼系变换催化剂的硫化步骤和方法
CO变换操作知识问答
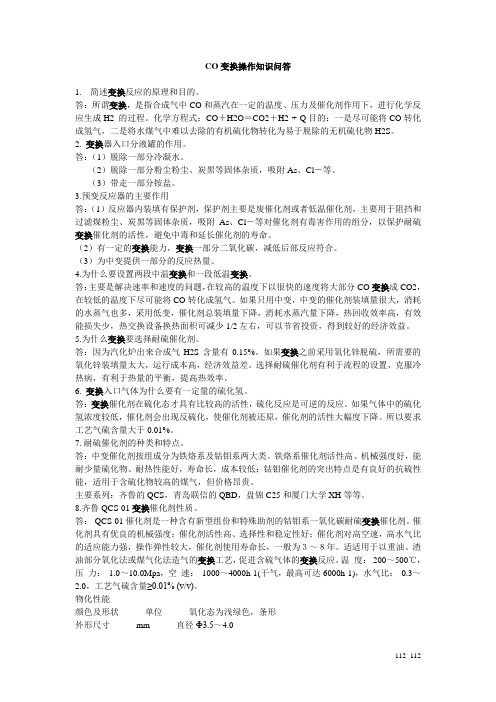
CO变换操作知识问答1. 简述变换反应的原理和目的。
答:所谓变换,是指合成气中CO和蒸汽在一定的温度、压力及催化剂作用下,进行化学反应生成H2 的过程。
化学方程式:CO+H2O=CO2+H2 + Q目的:一是尽可能将CO转化成氢气,二是将水煤气中难以去除的有机硫化物转化为易于脱除的无机硫化物H2S。
2. 变换器入口分液罐的作用。
答:(1)脱除一部分冷凝水。
(2)脱除一部分粉尘粉尘、炭黑等固体杂质,吸附As、Cl-等。
(3)带走一部分铵盐。
3.预变反应器的主要作用答:(1)反应器内装填有保护剂,保护剂主要是废催化剂或者低温催化剂,主要用于阻挡和过滤煤粉尘、炭黑等固体杂质,吸附As、Cl-等对催化剂有毒害作用的组分,以保护耐硫变换催化剂的活性,避免中毒和延长催化剂的寿命。
(2)有一定的变换能力,变换一部分二氧化碳,减低后部反应符合。
(3)为中变提供一部分的反应热量。
4.为什么要设置两段中温变换和一段低温变换。
答:主要是解决速率和速度的问题,在较高的温度下以很快的速度将大部分CO变换成CO2,在较低的温度下尽可能将CO转化成氢气。
如果只用中变,中变的催化剂装填量很大,消耗的水蒸气也多,采用低变,催化剂总装填量下降,消耗水蒸汽量下降,热回收效率高,有效能损失少,热交换设备换热面积可减少1/2左右,可以节省投资,得到较好的经济效益。
5.为什么变换要选择耐硫催化剂。
答:因为汽化炉出来合成气H2S含量有0.15%。
如果变换之前采用氧化锌脱硫,所需要的氧化锌装填量太大,运行成本高,经济效益差。
选择耐硫催化剂有利于流程的设置,克服冷热病,有利于热量的平衡,提高热效率。
6. 变换入口气体为什么要有一定量的硫化氢。
答:变换催化剂在硫化态才具有比较高的活性,硫化反应是可逆的反应。
如果气体中的硫化氢浓度较低,催化剂会出现反硫化,使催化剂被还原,催化剂的活性大幅度下降。
所以要求工艺气硫含量大于0.01%。
7. 耐硫催化剂的种类和特点。
合成氨复习题(1)

合成氨复习题(1)复习题第1章烃类蒸汽转化第⼆章重油部分氧化从化学热⼒学分析析炭发⽣:只有在转化管进⼝的⼀段位置可能析炭实际⽣产中温度的提⾼受到限制:①催化剂耐热温度②反应管材质耐⾼温③烃类分解发⽣热裂解导致析碳实际⽣产中温度的控制指标:①⼀段转化炉出⼝:800 ℃,甲烷含量10%;②⼆段炉出⼝:1000 ℃,甲烷含量<0.5% ⼯业⽣产对转化催化剂的要求:①活性⾼:催化剂活性愈⾼,转化速度越快,可增加空速,从⽽提⾼设备的⽣产效率;同时,⾼活性催化剂可从动⼒学上减少析碳的发⽣;②抗析碳:烃类,特别是⽯脑油蒸汽转化,最容易在床层⼊⼝1-3⽶处析碳;采取的措施是在催化剂研制上想办法,如英国ICI46-1催化剂,向催化剂中加⼊钾碱,在转化反应过程中,钾碱可缓慢释放,分布在催化剂表⾯上中和酸性中⼼,抑制⾮均相积碳。
③稳定性蒸汽转化操作条件苛刻,催化剂长期处在⽔蒸汽和⾼的氢分压、⾼的⽓体流速下,活性不随时间⽽衰退。
⽬前,转化催化剂的使⽤寿命⼀般为5年,使⽤终期和初期相⽐,活性衰退⼀般左右。
④⾼强度:转化条件苛刻,⽣产中⼯况波动,转化管震动,管内⽓体流速很⾼,从⽽导致对催化剂冲刷、腐蚀。
这都要求催化剂具有较⾼的强度,耐压碎、耐膨胀、耐磨蚀,否则催化剂粉化,造成床层阻⼒增加。
⑤合理的⼏何形状:从提⾼催化剂内表⾯利⽤率、减少床层阻⼒等⽅⾯考虑,都要求催化剂有合理的⼏何形状;⽬前,转化催化剂多做j成环状。
催化剂的成分:活性组分载体助催化剂此外,还常加⼊润滑剂、扩孔剂等。
催化剂的制备:①共沉淀法②浸渍法活性组分:在元素周期表中,第Ⅷ族过度元素对烃类蒸汽转化反应都有催化作⽤;贵⾦属钌Ru、铑Rh、钯Pd、铱Ir、铂Pt的活都⾼于镍Ni,但从性能和经济⽅⾯考虑,活性组分,镍为最佳,所以镍是⽬前⼯业上唯⼀的活性组分。
NiO为制备催化剂最主要活性成份,含量以4-30%为宜。
助催化剂:为了提⾼镍的活性及稳定性,可添加助催化剂来达到抑制镍晶粒熔融过程,防⽌镍晶粒长⼤,从⽽使其有较⾼的稳定活性,延长使⽤寿命,并增加抗析碳能⼒。
脱氧工艺讲课内容

脱氧工艺一、岗位任务主要任务是脱除来自经过洗涤的气化粗煤气和焦炉气的混合煤气中微量的氧气,为后工序提供氧气含量要求脱至30ppm以下的合格原料气以满足后工段的工艺要求。
防止氧气组分的存在对后工序甲烷分离的冷箱设备操作带来有害影响。
正确使用和维护催化剂,延长其使用寿命。
二、工艺原理利用适合于本项目原料气含硫、含油等杂质工况的专用脱氧剂,在适宜温度条件和催化剂作用下O2 与 CO、H2进行反应使氧气得以脱除,其反应为:2CO+O2→2CO2O2+2H2→2H2O三、脱氧剂硫化原理脱氧剂为钴钼系耐硫低变催化剂,主要活性组分为氧化钼,以氧化钴为促进剂,以氧化铝为载体。
脱氧催化剂中的Co与Mo是以氧化态形式存在,这种形态的催化剂不具有活性,只有将Co、Mo转化为硫化态,才具有活性。
将催化剂中Co、Mo由氧化态转化为硫化态的过程称为催化剂的硫化,硫化分为强制硫化与自然硫化两种形式。
我厂采用CS2强制硫化的方法。
为使气体中有足够的H2S含量,以保证硫化过程顺利进行,通常采取向系统连续添加CS2的方法,并在一定温度下(200℃)发生氢解作用生成H2S。
其主要反应为:CS2+4H2 2H2S+CH4 ΔH=240KJ/molCoO+H2S CoS+H2O ΔH=13.6KJ/mol'MoO3+2H2S+ H2 MoS2+3H2O ΔH=48.1KJ/mol 上述CoO与MoO生成MoS2与CoS的反应是一个可逆的放热反应。
硫化氢穿透前,床层温度低于230℃。
催化剂上的金属氧化态在温度大于230℃后很容易被氢气还原,成为低价位的金属氧化物甚至成为单质金属,因此在硫化氢穿透催化剂床层前,应严格执行该指标(低价位的金属或单质金属难于硫化,同时被还原的金属对油有强的吸附作用,会加速裂解反应,造成催化剂大量积炭,使活性降低)四、工艺流程因催化剂为耐硫催化剂,开车前需先加入CS2气体,用以激活催化剂反应活性。
来自气化工段的粗煤气在界外与焦炉气混合后首先进入净化器(F61201A/B)中除去混合煤气中的油、粉尘等杂质,进入气气换热器(E61201)加热至160℃,然后进入脱氧器(D61201),在脱氧剂作用下将气体中的氧气脱除。
氧化锌脱硫剂

• COS + H2 =H2S + CO • CS2 + 4 H2=2H2S +CH4 注:氧化锌脱硫剂对噻吩的转化能力很低,不能直接吸收,
因此单用氧化锌不能将有机硫化物除尽
(二)氧化锌脱硫剂
ZnO为主体(约80%),还加入CuO、MgO、MnO2等作为 助剂。
脱硫剂常用型号: T 302、T 304、T 305 。
机硫在350 ~400℃左右。
压力: 氧化锌脱硫属于内扩散控制过程,提高压力有利于加快反应 速度,其大小取决于原料气的压力和脱硫工序在合成氨生产 中的部位,一般为0.7~7Mp 硫容量: 评价脱硫剂的一个重要指标。指的是单位质量新的氧化锌脱 硫剂吸收硫的量。氧化锌脱硫剂使用过程如下图所示
• 靠近气体入口的氧化锌先被硫饱和, 随着使用时间的增长,饱和层逐渐 扩大。
•CO+H2 =CH4+ H2O+Q •CO2+4H2 = CH4+ 2H2O+Q •O2+H2 =H2O+Q
(三)工艺条件
1.温度:350~430℃之间 2.压力:0.7~7Mp 3.空速:入口气空间速度500~1500L/h 4.氢气加入量:维持反应后含量5~10% 5.CO+ CO 2:小于0.5%
一、钴钼加氢转化法
• 钴钼加氢转化法是一种脱除含氢原料气中有机硫的 预处理措施。
• 有机硫化物脱除一般比较困难,但将其在钴钼催化 剂存在下加氢转化成硫化氢就容易脱除了。
• 采用钴钼加氢可使天然气、石脑油原料中的有机硫 几乎全部转化成硫化氢,再以氧化锌法便可将硫化
氢脱除到0.02 L / L。
(一)钴钼加氢催化剂
(二)钴钼加氢转化法原理 1.转化反应
一氧化碳的变换技术6.2
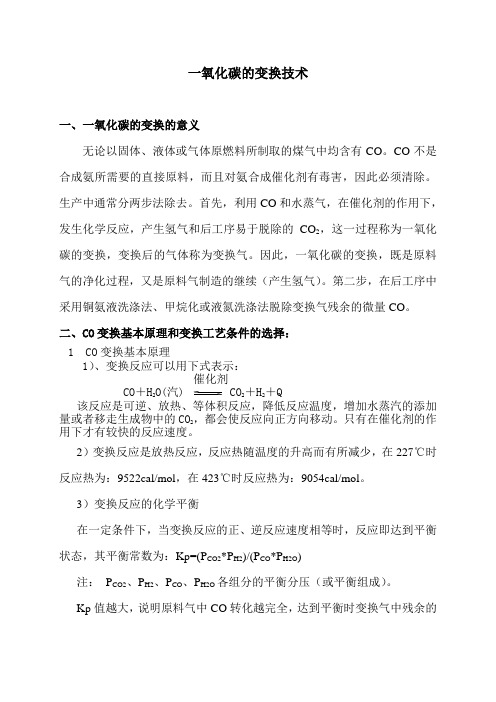
一氧化碳的变换技术一、一氧化碳的变换的意义无论以固体、液体或气体原燃料所制取的煤气中均含有CO 。
CO 不是合成氨所需要的直接原料,而且对氨合成催化剂有毒害,因此必须清除。
生产中通常分两步法除去。
首先,利用CO 和水蒸气,在催化剂的作用下,发生化学反应,产生氢气和后工序易于脱除的CO 2,这一过程称为一氧化碳的变换,变换后的气体称为变换气。
因此,一氧化碳的变换,既是原料气的净化过程,又是原料气制造的继续(产生氢气)。
第二步,在后工序中采用铜氨液洗涤法、甲烷化或液氮洗涤法脱除变换气残余的微量CO 。
二、CO 变换基本原理和变换工艺条件的选择:1 CO 变换基本原理1)、变换反应可以用下式表示:催化剂CO +H2O(汽2+H 2+Q该反应是可逆、放热、等体积反应,降低反应温度,增加水蒸汽的添加量或者移走生成物中的CO 2,都会使反应向正方向移动。
只有在催化剂的作用下才有较快的反应速度。
2)变换反应是放热反应,反应热随温度的升高而有所减少,在227℃时反应热为:9522cal/mol ,在423℃时反应热为:9054cal/mol 。
3)变换反应的化学平衡在一定条件下,当变换反应的正、逆反应速度相等时,反应即达到平衡状态,其平衡常数为:Kp=(P CO2*P H2)/(P CO *P H2O )注: P CO2、P H2、P CO 、P H2O 各组分的平衡分压(或平衡组成)。
Kp 值越大,说明原料气中CO 转化越完全,达到平衡时变换气中残余的CO含量越少。
由于变换反应是放热反应,降低温度有利于平衡向右移动,因此平衡常数随温度的降低而增大。
250℃时为86.51,450℃时为:7.311。
在工业生产中,受催化剂装填量、设备投资的经济效益等因素影响,反应不可能也没必要达到平衡,只能尽可能接近平衡。
实际的流程组合中,一般利用高温段之后再进行低温变换,就是为了提高反应平衡常数,从而提高变换率,降低变换气CO含量。
浅谈变换催化剂和变换炉的选择

浅谈变换催化剂和变换炉的选择摘要:变换工艺根据所选用的催化剂是否耐硫,将变换工艺分为耐硫变换和非耐硫变换工艺。
变换反应的顺利进行主要取决于两方面的因素,催化剂和变换炉。
本文通过介绍不同类型变换催化剂和变换炉的发展、应用及优缺点,为广大化工同行在变换催化剂和变换炉的选择上提供帮助。
关键词:变换工艺;变换催化剂;变换炉1变换催化剂的选择通常使用的催化剂有高温变换催化剂、低温变换催化剂和宽温耐硫变换催化剂。
1.1高温变换催化剂高温变换催化剂其活性相是由Fe2O3部分还原得到的Fe3O4。
在实际应用过程中,高温烧结导致Fe3O4表面积下降,引起活性的急剧下降,造成纯Fe3O4的活性温区很窄,耐热性很差。
因此常加入结构助剂提高其耐热性,防止烧结引起的活性下降。
由于铁铬系高温变换催化剂中铬是剧毒物质,造成在生产、使用和处理过程中对人员和环境的污染及毒害,但工业化与应用业绩较少。
高温变换催化剂的粉化是它的一个主要问题。
催化剂的更换往往不是由于活性丧失,而是由于粉化造成过大的压差。
部分催化剂的粉化,引起气流不均匀,也将导致转化率下降。
蒸汽消耗较高,有最低水气比要求,要求变换入口水气比在1.4以上,变换后的水气比应大于0.8,导致过剩蒸汽冷凝量过多、能耗增加,不宜选用。
1.2低温变换催化剂低变催化剂的最大特点就是活性温度低,在200~260℃的范围内,变换反应就能迅速进行。
低变催化剂对硫化物极为敏感,由于生成铜盐而永久性中毒。
氯或氯离子也引起永久性中毒,这是由于催化剂发生结晶而引起的。
另外,原料气中的不饱和烃可能在催化剂表面析炭或结焦。
1.3宽温耐硫变换催化剂钴钼系耐硫宽温变换催化剂具有很高的低温活性,它比铁系高温变换催化剂起活温度低100~150℃,甚至在160℃就显示出优异的活性,与铜系低温变换催化剂相当,且其耐热性能与铁铬系高温变换催化剂相当,因此具有很宽的活性温区,几乎覆盖了铁系高温变换催化剂和铜系低温变换催化剂整个活性温区。
宽温变换催化剂的装填及活化方案

宽温变换催化剂的装填及活化方案1、催化剂的装填:1.1、催化剂的装填非常重要,催化剂装填的好坏将直接影响系统阻力降及气体分布,进而影响催化剂性能的发挥;1.2、催化剂装填前应将变换炉清扫干净,并清理检查;1.3、催化剂、保护剂及脱氧剂的装填层的下部需填充耐火球或氧化铝球,每层之间均铺设两层8~10目的不锈钢丝网。
催化剂的上表面最好再铺设一层钢丝网,其上放置50mm高的耐火球或氧化铝球,以免冷凝水接触催化剂;1.4、催化剂必须装填均匀、密实,防止气体偏流;1.5、催化剂装填时,颗粒自由落体的高度不得大于0.5米;1.6、为防止催化剂进水或发生意外,故催化剂应在硫化前1~2天装填,不宜过早装填;1.7、催化剂装填的重量、容积、高度及热偶位置应作详细记录并存档以备查。
2、催化剂硫化前的准备:2.1、准备符合压力容器要求的一定容积的CO2储罐一个,CO2的使用量可按每立方米催化剂消耗150~180Kg/准备;2.2、准备足够量的N2,2.3、准备CS2转子流量计一只;2.4、消防器具及劳动防护用品准备充足;2.5、电器、仪表调试和格;2.6、升温硫化所需的分析仪器、药品及分析人员到位。
3、催化剂硫化的注意事项:3.1、气量(空速)、电加热器及CS2加入量是催化剂硫化操作的三个重要调节手段,操作过程中应尽量不采用多元手段调节;3.2、不宜采用未经冷凝的煤气进行硫化,防止水蒸气和冷凝水带入;3.3、全低变流程不能中、低变催化剂串联或同时硫化,并且中、低变得硫化及注意事项都要按此方案进行;3.4、CS2具有有毒、易燃的特性,使用时应避免外溢和直接接触。
CS2具有较高的挥发性,储罐周围要严禁烟火,应以醒目的方式明示,并有专人负责。
使用人员需进行学习培训;3.5、升温硫化的过程中,一定要保证煤气中的O2含量小于0.5%;3.6、进行循环硫化的H2含量必须大于25%;3.7、升温前用惰性气体对系统进行置换至O2含量小于0.5%以内。
催化剂硫化

催化剂硫化1.催化剂硫化的目的和原理1.1硫化目的:在一定的温度和硫化氢分压下,把催化剂的活性组分(氧化镍、氧化钼等)由活性低的氧化态变成活性稳定的硫化态,提高催化剂活性和稳定性,延长催化剂寿命。
虽然加氢催化剂在使用氧化态形式开工后,也会因较弱的加氢活性促使一部分原料中的硫化物发生加氢脱硫反应,生成硫化氢,继而使催化剂金属组分从氧化态转化为硫化态,但这种转化是在催化剂长时间与高温氢气接触、并且有大量结焦的情况下进行,催化剂的活性金属组分在转化为硫化态之前,有一部分可能被氢还原,这种氢还原或已经沉积有炭的金属组分很难再被硫化,从而使催化剂处于低的加氢活性,并带来短的寿命。
因此,加氢催化剂在接触原料油之前,必须先将催化剂活性金属组分的氧化态用硫化剂将其转化为硫化态,即进行催化剂预硫化。
本装置催化剂硫化方式采用湿法硫化。
1.2 预硫化原理:预硫化时,硫化反应极其复杂。
在反应器内会发生两个主要反应:(1)硫化剂(DMDS)和氢气反应,产生硫化氢和甲烷,反应会放出热量。
预硫化时该反应一般在反应器入口发生,反应速度较快。
反应方程式:CS2+4H2→CH4+2H2S(2)氧化态的催化剂活性组分(氧化镍、氧化钼等)和硫化氢反应变成硫化态的催化剂活性组分,反应会放出热量。
预硫化时该反应发生在各个床层。
反应方程式:M O O3+2H2S+H2→M O S2+3H2O3N i O3+2H2S+H2→NiS2+3H2O(3)副反应:在有氢气存在、无硫化氢的条件下,氧化态的催化剂活性组分(氧化镍、氧化钼等)被氢气还原,生成金属镍、钼和水,导致催化剂活性损失。
温度越高(大于230℃),反应越严重;在循环气中的硫化氢含量过高时,会生成金属的多硫化物,降低了催化剂活性,易造成产品腐蚀不合格。
2. 催化剂硫化应具备的条件(1)反应系统催化剂干燥、高压气密结束,紧急泄压和急冷氢试验问题整改完。
(2)分馏系统热油运运转正常,具备接收生成油条件。
- 1、下载文档前请自行甄别文档内容的完整性,平台不提供额外的编辑、内容补充、找答案等附加服务。
- 2、"仅部分预览"的文档,不可在线预览部分如存在完整性等问题,可反馈申请退款(可完整预览的文档不适用该条件!)。
- 3、如文档侵犯您的权益,请联系客服反馈,我们会尽快为您处理(人工客服工作时间:9:00-18:30)。
硫化步骤:
触媒升温硫化曲线表:
阶段 执行时间
(hr) 空速
(h-1 ) 床层各点
温度(℃) 入炉H2S含 量(g/Nm3 ) 备 注
1.升温 12~14 200~300 常温~210 用煤气将系统置换合格
后推电炉升温
2.硫化期 20~24 100~200 210~300 10~15 待出口气的
H2S含量≥3g/Nm3 ,床层穿透
3.强化期 10
9 100~200 300~350
350~450 15~20 变换炉出口H2S含量≥10g/Nm3
4.降温置换 ~8 200~300 180~200 0.05 出口H2S含量
≤0.5g/Nm3 ,并入系统生产
1、煤气升温阶段
(1) 常温~120℃(6~8h),120℃恒温2 h,120~200℃(4h)。
(2) 按升温硫化流程调节好有关阀门,压缩机1台三出送气压力<0.2MPa,最大循环
气量15000Nm3/h。
(3) 待电加热器、变换炉各处煤气置换O2<0.5%,电加热器通气正常后,启3组电炉
丝开始煤气升温。
(4) 打开循环气体出口阀,关低变炉出口DN150放空阀,将循环气体导入压机一入煤
气总管,开始循环升温。
(5) 电加热器升温时,采取必要措施严格按升温曲线进行。升温期间视各段温升情况
及时增减电炉丝组数,调节各段进气阀开度、气量或煤气换热器进出口煤气副线阀等。当两
变换炉床层温差较大时,可用进两炉的升温煤气阀调节不同入炉点的气量。
(6) 升温期间,严格控制煤气中O2<0.5%,防止电加热器起火**,严格控制煤气系统
压力不得超过0.3MPa。
(7) 恒温前应先降低热煤气温度。
(8) 在煤气升温结束前3h,两硫化罐应按要求灌装好CS2,并连接好N2瓶,升压至
0.45~0.5MPa、并排水后备用。
(9) 升温期间,要注意及时排放油分离器和活性炭滤油器导淋,严防油水带入系统。
(10) 循环升温时,不必开放空,待硫化开始后,可在系统出口处打开放空置换一部分
气体,以补充氢气含量。
2、催化剂硫化阶段
(1) 12-16h,210-300℃,入炉煤气中H2S 10-15g/Nm3,300℃恒温8h。
(2) 升温至床层进口温度达210℃,硫化罐排水后,即可用N2将CS2压人系统,用硫
化罐出口阀,控制CS2加入量,保证入炉H2S浓度为10-15 g/m3,开始硫化并稍开系统
出口放空阀。
(3) 硫化时,密切注意硫化罐液位,当快加完时,应立即切断,倒换另一台继续加入
CS2,退出的一台要立即灌装CS2并加压、排水后备用,两CS2罐交替使用,专人负责。
(4) 密切注意床层温度,用电加热器组数、煤气量、煤气换热器进出口煤气副线阀、
CS2加入量或进两炉的升温煤气阀等调节,维持床层温度在210-300℃。
(5) 硫化时炉进口H2含量应保证≥25%,便于CS2氢解。
(6) 待分析炉出口H2S≥3g/Nm3,即H2S穿透床层,维持稳定,应减少或关闭 CS2
加入量,床层≤300℃恒温8h。
3、强化硫化阶段
(1) 300一350℃4h,入炉H2S15-20 g/Nm3 ,350℃恒温6 h
(2) 350一450℃5h,入炉H2S15-20 g/Nm3 ,450℃恒温4 h
(3) 待H2S穿透底层,300℃恒温结束,增加CS2系统加入量,逐步提高床层温度至
350℃,入炉H2S维持在15-20 g/m3,强化硫化4h左右,变换炉出口H2S增至 10 g/
m3,减少CS2加入量,床层350℃恒温6h。
(4) 床层 350℃恒温结束后,增加CS2系统加入量,炉温提至 450℃,入炉H2S控制
在15-20 g/m3以上,强化硫化5h,低变炉进出口H2S基本一致后,再恒温4 h,强化硫
化结束。
(5) 强化硫化过程中,利用恒温期间,安排一到二次系统螺栓热把紧。
4、降温置换
(1) 强化硫化结束,开大变换炉出口放空阀和变换系统出口放空阀放空,逐步退出电
加热器,用煤气降温置换,将床层温度降至300℃,停止加CS2,继续用煤气降温置换至 180~
200℃,且第二变换炉出口H2S<0.5g/Nm3。
(2) 硫化结束,联系调度停压缩机、关闭送气阀,同时关循环硫化气体去压机一入阀
门、 进出变换系统阀门、硫化煤气管道各阀门。用第二变换炉出口或系统出口放空阀,将
系统压力卸到0.05MPa后关闭放空,系统保压。
(3) 硫化升温管线、设备置换和加盲板:拆开电加热器进口煤气管线阀后法兰和出口
管线去两变换炉的阀前法兰,从电加热器倒淋倒入低压蒸汽,控制压力<0.3MPa,置换电
加热器及其进出口管道、硫化煤气管线,由各盲板处敞口放空和硫化罐处放空。置换合格后,
插上述盲板。
(4) 出变换系统回压机一入的管线置换:关闭管线两端的阀门,打开一入端阀前放空,
管内卸压,从变换端阀后倒淋通低压蒸汽置换,控制压力<0.3MPa,置换合格后,关闭倒
淋、放空阀,两端阀内法兰加盲板。
(5) 检查确认其他阀门开关位置符合开车要求后即可联系调度,导气开车。
(6) 全面检查系统内各阀门的开关情况、仪表情况和盲板抽加情况,并调节正常。
(7) 联系调度将中压蒸汽送至总阀前,开蒸汽导淋阀进行外管暖管,把脱盐水加入冷
凝液贮槽。将变换气冷却系统用脱盐水、循环水导入系统并调节正常。
(8) 联系压缩机一台送气,送气后,开煤气DN300进口阀及导淋阀,打开中压蒸汽自
调阀加蒸汽。用变换气出口DN350总阀前DN150放空阀控制系统压力并适当放空。
(9) 系统升压到1.0Mpa以上(视后工序需求),变换气合格后,开变换气出口DN350
总阀,关DN150放空阀向变脱工序送气。
(10) 床层温度正常后,半水煤气气量增大,应逐步增加蒸汽用量和提高变换压力,并
视催化剂床层温度开用淬冷过滤器及调节煤气入炉温度,将床层温度控制在指标范围内。视
合成甲醇生产需要,适时调节变换气中CO含量以满足后工序生产要求。至此开车结束转入
正常生产。
(11) 每小时巡回检查一次,各处导淋排放一次。