钴钼系催化剂的硫化
钴钼系耐硫变换催化剂装填及使用过程注意事项
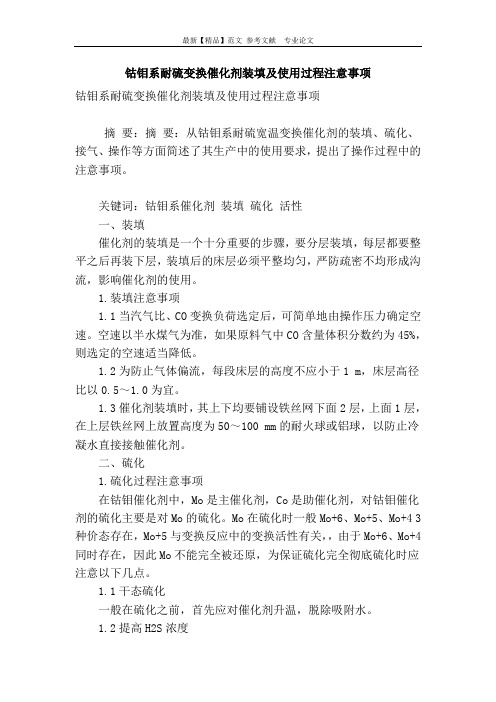
钴钼系耐硫变换催化剂装填及使用过程注意事项钴钼系耐硫变换催化剂装填及使用过程注意事项摘要:摘要:从钴钼系耐硫宽温变换催化剂的装填、硫化、接气、操作等方面简述了其生产中的使用要求,提出了操作过程中的注意事项。
关键词:钴钼系催化剂装填硫化活性一、装填催化剂的装填是一个十分重要的步骤,要分层装填,每层都要整平之后再装下层,装填后的床层必须平整均匀,严防疏密不均形成沟流,影响催化剂的使用。
1.装填注意事项1.1当汽气比、CO变换负荷选定后,可简单地由操作压力确定空速。
空速以半水煤气为准,如果原料气中CO含量体积分数约为45%,则选定的空速适当降低。
1.2为防止气体偏流,每段床层的高度不应小于1 m,床层高径比以0.5~1.0为宜。
1.3催化剂装填时,其上下均要铺设铁丝网下面2层,上面1层,在上层铁丝网上放置高度为50~100 mm的耐火球或铝球,以防止冷凝水直接接触催化剂。
二、硫化1.硫化过程注意事项在钴钼催化剂中,Mo是主催化剂,Co是助催化剂,对钴钼催化剂的硫化主要是对Mo的硫化。
Mo在硫化时一般Mo+6、Mo+5、Mo+4 3种价态存在,Mo+5与变换反应中的变换活性有关,,由于Mo+6、Mo+4 同时存在,因此Mo不能完全被还原,为保证硫化完全彻底硫化时应注意以下几点。
1.1干态硫化一般在硫化之前,首先应对催化剂升温,脱除吸附水。
1.2提高H2S浓度高硫浓度可保证硫化反应的需要,并缩短反应时间,不过在硫化初期不要将H2S含量提得太高,应采取逐渐渗透的方式,避免反应过急,使催化剂温度波动过大。
1.3低温硫化当床层温度达到180℃时,将气体入口温度降到170~180℃,然后加入CS2,使催化剂在H2S吸收区反应,可避免硫化初期温度超过200℃而引起的异常激烈反应。
主要硫化阶段为180~300℃为保证温度,应将炉温控制在250℃左右,并逐步加大CS2的量。
当分析显示变换炉出口H2S达到1 g/m3或进出口H2S含量相等时,保持运行2 h 即为合格。
硫化过程中注意要点

硫化过程中注意要点钴钼系耐硫低变催化剂硫化过程的控制要注意以下几点:①控制好升温硫化温度。
既要控制升温速度,又要保证床层能达到硫化最终温度。
②CS2加入量和加入时间的控制。
初期加入量小,逐步增加。
升温至20 0℃左右加入CS2。
③稳定操作。
空速、电加热功率、CS2加入量是硫化操作的三个主要调节手段。
在实际操作中应稳定CS2的加入量,以调气量为主、调电加热器的功率为辅。
④硫化要完全。
从硫化时间、床层温度、炉出口H2S浓度判断硫化终点,保证催化剂达到最佳活性。
在硫化操作中,应注意:1. 用半水煤气硫化,应控制半水煤气中氧含量≤0.5%,严防氧含量超标,并作预见性调节。
用变换气硫化时应防止床层带水。
2. CS2的加入时间不能过早,也不能过晚,一般在催化剂升温至200℃左右加入。
3. 严防油污带入床层。
油污易在高温下炭化,沉积于催化剂颗粒之中,影响催化剂的活性。
油污主要来源,一是半水煤气中带油,特别是回收压缩二段余热后,半水煤气带油更多,因此要经常排放油水分离器、焦炭过滤器倒淋。
二是通过CS2带入。
CS2是有机溶剂,CS2贮罐阀门等所带油污会溶于CS2而带入床层,因此要预先把硫化系统的油清洗干净。
4. 硫化过程中要加强H2S的分析,开始每小时一次,后期半小时一次,分析结果力求准确。
5. CS2是易燃危险品,硫化时要注意安全,加强管理,谨慎操作。
用固体硫化剂代替CS2硫化比较完全。
6. 用高硫煤制得,半水煤气中H2S含量大于2g/m3(标),硫化时可以不加CS2,利用未脱硫的半水煤气自然硫化。
但硫化时间长,催化剂的活性一般不如采用CS2硫化效果好。
因此,自然硫化较少采用。
耐硫变换催化剂及其使用技术
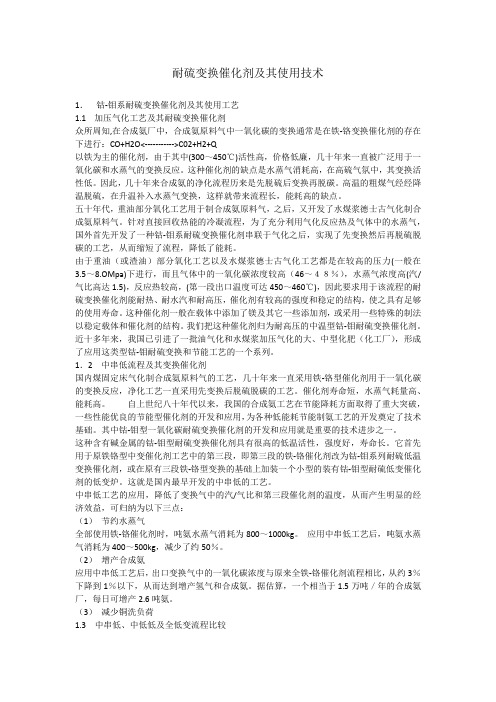
耐硫变换催化剂及其使用技术1.钴-钼系耐硫变换催化剂及其使用工艺1.1加压气化工艺及其耐硫变换催化剂众所周知,在合成氨厂中,合成氨原料气中一氧化碳的变换通常是在铁-铬变换催化剂的存在下进行:CO+H2O<----------->C02+H2+Q以铁为主的催化剂,由于其中(300~450℃)活性高,价格低廉,几十年来一直被广泛用于一氧化碳和水蒸气的变换反应。
这种催化剂的缺点是水蒸气消耗高,在高硫气氛中,其变换活性低。
因此,几十年来合成氨的净化流程历来是先脱硫后变换再脱碳。
高温的粗煤气经经降温脱硫,在升温补入水蒸气变换,这样就带来流程长,能耗高的缺点。
五十年代,重油部分氧化工艺用于制合成氨原料气,之后,又开发了水煤浆德士古气化制合成氨原料气。
针对直接回收热能的冷凝流程,为了充分利用气化反应热及气体中的水蒸气,国外首先开发了一种钴-钼系耐硫变换催化剂串联于气化之后,实现了先变换然后再脱硫脱碳的工艺,从而缩短了流程,降低了能耗。
由于重油(或渣油)部分氧化工艺以及水煤浆德士古气化工艺都是在较高的压力(一般在3.5~8.OMpa)下进行,而且气体中的一氧化碳浓度较高(46~48%),水蒸气浓度高(汽/气比高达1.5),反应热较高,(第一段出口温度可达450~460℃),因此要求用于该流程的耐硫变换催化剂能耐热、耐水汽和耐高压,催化剂有较高的强度和稳定的结构,使之具有足够的使用寿命。
这种催化剂一般在载体中添加了镁及其它一些添加剂,或采用一些特殊的制法以稳定载体和催化剂的结构。
我们把这种催化剂归为耐高压的中温型钴-钼耐硫变换催化剂。
近十多年来,我国已引进了一批油气化和水煤浆加压气化的大、中型化肥(化工厂),形成了应用这类型钴-钼耐硫变换和节能工艺的一个系列。
1.2中串低流程及其变换催化剂国内煤固定床气化制合成氨原料气的工艺,几十年来一直采用铁-铬型催化剂用于一氧化碳的变换反应,净化工艺一直采用先变换后脱硫脱碳的工艺。
耐硫变换催化剂硫化过程

31一、硫化剂的种类合理选用硫化剂是预硫化技术应用的关键,目前常见的硫化机主要划分为以下几种:1.有机硫化剂。
有机硫化剂主要包括有机过氧化物、含硫促进剂和多硫聚合物等,与元素硫一样,有机硫化剂在硫化反应时同样存在反应剧烈、放热集中等问题,而且有机硫化剂预硫化催化剂存在释放硫现象,不利于运输和装填。
2.无机硫化剂。
目前常用的无机硫化剂有元素硫、硫化氢、二硫化碳和硫代硫酸铵等,元素硫作为硫化剂的最明显优势是硫化效率高,与其他硫化剂相比,单位质量硫化剂中硫的含量最高,1mol元素硫可以生成8mol的硫化氢。
而且元素硫常温下化学稳定性较好,不易与空气发生作用,存储、运输和装填较为便利。
但元素硫与催化剂作用较弱,同时硫化反应剧烈,很容易使催化剂烧结。
3.混合硫化剂。
单一使用有机和无机硫化剂在实际应用中都存在一定缺陷,为此,诸多学者将研究重点放在混合硫化剂上。
像将元素硫与石蜡混合作为混合硫化剂或是溶于含有硫醇、脂肪酸的有机聚硫化合物溶液中。
目前常见集中硫化剂的物化性质如下表1所示: 表1 硫化剂物化性质二、预硫化反应机理1.硫化剂分解硫化剂分解是指硫化剂在催化剂作用下通过硫化工艺发生化学反应生成硫化氢的过程。
结合上文给出的几种常见硫化剂写出硫化剂分解过程中发生的化学反应表达式如下:(1)二硫化碳 4H 2+CS 2=CH 4+2H 2S(2)二甲基二硫化物 3H 2+CH 3SSCH 3=2CH 4+2H 2S (3)二甲基硫化物 2H 2+CH 3SCH 3+2H 2=CH 4+H 2S (4)乙硫醇 H 2+CH 3CH 2SH=CH 3CH 3+H 2S(5)正丁硫醇H 2+CH 3CH 2CH 2CH 2SH=CH 3CH 2CH 2CH 3+H 2S 2.催化剂活性组分的相态转化耐硫变换催化剂硫化过程的主要目的有两点,第一,使催化剂中的活性组分处于最佳活性价态。
第二,将催化剂中的金属活性组分转化为硫化物。
钴钼系变换催化剂的硫化步骤和方法

硫化步骤:触媒升温硫化曲线表:阶段执行时间(hr) 空速(h-1 ) 床层各点温度(℃) 入炉H2S含量(g/Nm3 ) 备注1.升温12~14 200~300 常温~210 用煤气将系统置换合格后推电炉升温2.硫化期20~24 100~200 210~300 10~15 待出口气的H2S含量≥3g/Nm3 ,床层穿透3.强化期109 100~200 300~350350~450 15~20 变换炉出口H2S含量≥10g/Nm34.降温置换~8 200~300 180~200 0.05 出口H2S含量≤0.5g/Nm3 ,并入系统生产1、煤气升温阶段(1) 常温~120℃(6~8h),120℃恒温2 h,120~200℃(4h)。
(2) 按升温硫化流程调节好有关阀门,压缩机1台三出送气压力<0.2MPa,最大循环气量15000Nm3/h。
(3) 待电加热器、变换炉各处煤气置换O2<0.5%,电加热器通气正常后,启3组电炉丝开始煤气升温。
(4) 打开循环气体出口阀,关低变炉出口DN150放空阀,将循环气体导入压机一入煤气总管,开始循环升温。
(5) 电加热器升温时,采取必要措施严格按升温曲线进行。
升温期间视各段温升情况及时增减电炉丝组数,调节各段进气阀开度、气量或煤气换热器进出口煤气副线阀等。
当两变换炉床层温差较大时,可用进两炉的升温煤气阀调节不同入炉点的气量。
(6) 升温期间,严格控制煤气中O2<0.5%,防止电加热器起火**,严格控制煤气系统压力不得超过0.3MPa。
(7) 恒温前应先降低热煤气温度。
(8) 在煤气升温结束前3h,两硫化罐应按要求灌装好CS2,并连接好N2瓶,升压至0.45~0.5MPa、并排水后备用。
(9) 升温期间,要注意及时排放油分离器和活性炭滤油器导淋,严防油水带入系统。
(10) 循环升温时,不必开放空,待硫化开始后,可在系统出口处打开放空置换一部分气体,以补充氢气含量。
钴钼系耐硫变换催化剂硫化工艺的选择和应用

a pl ai n o h n f curr . p i t ft e ma u a t e s c o
Co - Mo 系耐硫变换催化剂的硫化处理

Co - Mo系耐硫变换催化剂的硫化处理1、硫化反应耐硫变换催化剂在使用前一般要将其活性组份的氧化态转化为硫化态,这一转化过程称之为硫化。
钴钼系耐硫催化剂的硫化反应在热力学上可用下列式子表示:CS2 + 4H2 = 2H2S + CH4 + 230. 45 kJMoO3 + H2 + 2H2S = MoS2 + 3H2O +48. 15 kJCoO + H2S = CoS + H2O + 13. 4 kJCO + 3H2 = CH4 + H2O + 214. 8 kJCO+H2O = CO2+H2 +41.19 KJ/mol2H2 +O2 =2 H2O + 241. 83 kJ上述反应均为放热反应。
常用的硫化剂有CS2和H2S两种。
其中H2S来自高硫煤气或固体硫化剂, CS2可直接加入原料气。
另外,硫氧化碳等有机硫也可作硫化剂。
2、硫化反应机理在催化剂的硫化过程中,不论采用何种硫化方法,最基本的硫化剂就是H2S。
因此只要在硫化条件下容易提供H2S的物质都可用作硫化剂。
工业上通常采用低分子量的有机硫化合物和无机的固体硫化剂。
硫化过程通常分为两个反应步骤,即硫化剂的分解和催化剂活性组分的相态转化。
(1)硫化剂的分解硫化剂的分解是指硫化剂在催化剂正常的硫化工艺条件下,硫化剂与氢气或水发生化学反应生成H2S的过程,下面是常见的几种硫化剂及其分解反应。
CS2(二硫化碳)十4H2=CH4十2H2SCOS(硫氧碳)十H2O=CO2十H2S(2)硫化对耐硫变换催化剂的作用:使催化剂中的金属组分即活性组分由氧化态变成硫化态,如MoO3变成活性物种MoS2;使催化剂中的活性组分处于最佳活性价态,以Mo为例,Mo由MoO3中Mo6+经过硫化变为活性物种MoS2。
MoO3和CoO在催化剂硫化过程中发生的化学变化表示如下:(3)硫化剂的选择从硫化剂的分解反应上看,其最终产物为H2S,理论上认为除本身的分解反应外,不会对催化剂的硫化过程造成影响。
钴钼系催化剂反硫化的处理

Tr a m e o — 0 Ca a y t I e s - u f r z t0 e t nt f r Co M t l s nv r e S l u i a i n
第3 7卷 第 2期
21 年 O 1 4 月
化 x 设 计 通 讯 -
Che ia m c lEng n e i sg i e rng De i n Com m u c ton nia i s ’ 55 ‘
钻 钼 系催 化 剂 反 硫 化 的 处 理
曹昭 军 , 吕洪 浩 , 汪 宇安
2 钴 钼 系 催 化 剂 反 硫 化 的 原 因分 析
第 二 个 月 的 一 天 , 控 制 室 监 控 人 员 反 映 , 中 变 炉
热 点温 瞍突然 从 1 3C下降 到 3 7C.波动 幅 度 2 8
较 大 , 明 显 出 现 异 常 。 技 术 人 员 立 即 对 当 时 各 种
运行 数据 趋势 图进 行调 查 .具体 情况 如下 :系统
20 0 5年 根 据 我 厂 的 操 作 经 验 ,笔 者 对 钻 钼
系 催 化 剂 接 气 过 程 中 超 温 问 题 进 行 了 讨 论 , 并 在
似现 象 ,并且 一 次 比一 次情 况严 重 ,而且 ,中变 炉 的热点 温 度仍存 在不 断下 降 的趋势 ,每 次波 动 后 ,热点 温度很 难 再恢 复到 原来 的状 态 。我们 虽 然每 次都 做 了调整 ,但 只能 暂时稳 定 炉温 ,没 有
( 州 开 阳 化 1 有 限 公 ห้องสมุดไป่ตู้ .贵 州 丌 阳 5 0 0 ) 贵 : 5 3 0
- 1、下载文档前请自行甄别文档内容的完整性,平台不提供额外的编辑、内容补充、找答案等附加服务。
- 2、"仅部分预览"的文档,不可在线预览部分如存在完整性等问题,可反馈申请退款(可完整预览的文档不适用该条件!)。
- 3、如文档侵犯您的权益,请联系客服反馈,我们会尽快为您处理(人工客服工作时间:9:00-18:30)。
硫化成功的必备条件有三个:
1)要有足够高的硫化温度,一般不大于500 ℃;2)要有足够的强制硫化时间,并且最好有数小时的闷炉;3)强制硫化时,原料气中的硫化氢越高越好,一般不低于15 g/Nm3 。
硫化时要防止催化剂超温,超过550 ℃对催化剂造成危害,但短时间超温对催化剂活性影响不大。
一、硫化条件
1、温度对硫化反应深度的影响很大,一般入口温度控制在230~260℃,床层温度控制在250~280℃。
硫化反应后期应尽量提温,适当的高温(~425℃)既可以保证催化剂的活性,又可缩短硫化时间。
2、硫化压力对硫化深度的影响不是很大,可根据装置的实际情况来确定压力,一般不低于1.0MPa(表压)。
3、H2S的浓度过低(体积分数≤0.2%)时,还原后的催化剂活性较差;H2S的较高时,对催化剂的影响不大。
出于安全考虑,H2S的浓度不宜提的太高。
4、系统中H2的体积分数尽量控制在10%~20%,过低会影响CS2的氢解,过高则有可能发生还原反应。
CS2在200℃以上时才发生氢解反应,所以添加CS2要等到温度达230℃左右开始添加。
过早添加容易使CS2氢解不完全,在系统内冷凝和吸附。
当达到温度时,就会突然发生氢解反应,放出大量的反应热导致床层温度暴涨。
但超过250℃再加CS2,就可能发生CoO和MoO3的还原反应,使催化剂失活。
运行过程中要保持H2的体积分数在10%~35%之间,因为当H2的浓度过低时,亦有可能造成CS2氢解不完全,在系统内冷凝和吸附。
当H2含量提高时,CS2大量氢解,释放过多的反应热,从而导致催化剂床层温度暴涨。
串联硫化时要防止“提温提硫”的同时发生,因为当上段硫穿透时,较高的热点温度和上段穿透的硫进入下一段,造成下段“提温提硫”,很容易造成超温。