Noise and vibration DC-motor(直流电机噪音及振动)
永磁同步电机高频振动与噪声研究
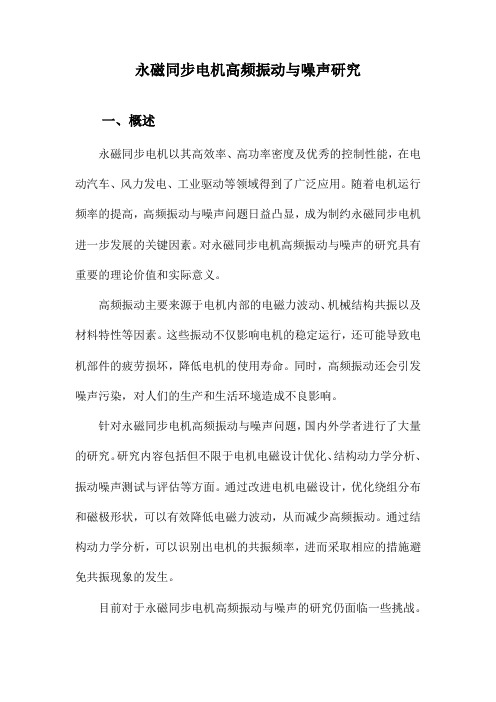
永磁同步电机高频振动与噪声研究一、概述永磁同步电机以其高效率、高功率密度及优秀的控制性能,在电动汽车、风力发电、工业驱动等领域得到了广泛应用。
随着电机运行频率的提高,高频振动与噪声问题日益凸显,成为制约永磁同步电机进一步发展的关键因素。
对永磁同步电机高频振动与噪声的研究具有重要的理论价值和实际意义。
高频振动主要来源于电机内部的电磁力波动、机械结构共振以及材料特性等因素。
这些振动不仅影响电机的稳定运行,还可能导致电机部件的疲劳损坏,降低电机的使用寿命。
同时,高频振动还会引发噪声污染,对人们的生产和生活环境造成不良影响。
针对永磁同步电机高频振动与噪声问题,国内外学者进行了大量的研究。
研究内容包括但不限于电机电磁设计优化、结构动力学分析、振动噪声测试与评估等方面。
通过改进电机电磁设计,优化绕组分布和磁极形状,可以有效降低电磁力波动,从而减少高频振动。
通过结构动力学分析,可以识别出电机的共振频率,进而采取相应的措施避免共振现象的发生。
目前对于永磁同步电机高频振动与噪声的研究仍面临一些挑战。
一方面,电机内部的电磁场和机械结构相互耦合,使得振动与噪声的产生机制复杂多样,难以准确描述和预测。
另一方面,随着电机技术的不断发展,新型材料和先进制造工艺的应用使得电机的振动噪声特性也发生了变化,需要不断更新和完善研究方法和手段。
本文旨在深入研究永磁同步电机高频振动与噪声的产生机理和影响因素,提出有效的抑制措施和优化方案,为永磁同步电机的设计、制造和运行提供理论支持和实践指导。
1. 永磁同步电机概述永磁同步电机,作为电动机和发电机的一种重要类型,以其独特的优势在现代工业中占据着举足轻重的地位。
其核心特点在于利用永磁体来建立励磁磁场,从而实现能量的高效转换。
定子产生旋转磁场,而转子则采用永磁材料制成,这种结构使得永磁同步电机在运行时能够保持稳定的磁场分布,进而实现平稳且高效的能量转换。
永磁同步电机可以分为他励电机和自励电机两种类型,前者从其他电源获得励磁电流,后者则从电机本身获取。
无刷电机电磁噪音振动的最主要原因分析和有效解决途径
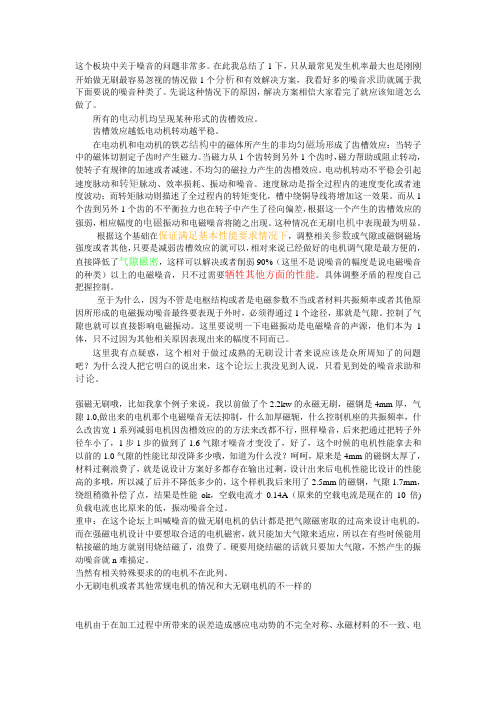
这个板块中关于噪音的问题非常多。
在此我总结了1下,只从最常见发生机率最大也是刚刚开始做无刷最容易忽视的情况做1个分析和有效解决方案,我看好多的噪音求助就属于我下面要说的噪音种类了。
先说这种情况下的原因,解决方案相信大家看完了就应该知道怎么做了。
所有的电动机均呈现某种形式的齿槽效应。
齿槽效应越低电动机转动越平稳。
在电动机和电动机的铁芯结构中的磁体所产生的非均匀磁场形成了齿槽效应:当转子中的磁体切割定子齿时产生磁力。
当磁力从1个齿转到另外1个齿时,磁力帮助或阻止转动,使转子有规律的加速或者减速。
不均匀的磁拉力产生的齿槽效应。
电动机转动不平稳会引起速度脉动和转矩脉动、效率损耗、振动和噪音。
速度脉动是指全过程内的速度变化或者速度波动;而转矩脉动则描述了全过程内的转矩变化,槽中绕铜导线将增加这一效果。
而从1个齿到另外1个齿的不平衡拉力也在转子中产生了径向偏差,根据这一个产生的齿槽效应的强弱,相应幅度的电磁振动和电磁噪音将随之出现。
这种情况在无刷电机中表现最为明显。
根据这个基础在保证满足基本性能要求情况下,调整相关参数或气隙或磁钢磁场强度或者其他,只要是减弱齿槽效应的就可以,相对来说已经做好的电机调气隙是最方便的,直接降低了气隙磁密,这样可以解决或者削弱90%(这里不是说噪音的幅度是说电磁噪音的种类)以上的电磁噪音,只不过需要牺牲其他方面的性能。
具体调整矛盾的程度自己把握控制。
至于为什么,因为不管是电枢结构或者是电磁参数不当或者材料共振频率或者其他原因所形成的电磁振动噪音最终要表现于外时,必须得通过1个途径,那就是气隙。
控制了气隙也就可以直接影响电磁振动。
这里要说明一下电磁振动是电磁噪音的声源,他们本为1体,只不过因为其他相关原因表现出来的幅度不同而已。
这里我有点疑惑,这个相对于做过成熟的无刷设计者来说应该是众所周知了的问题吧?为什么没人把它明白的说出来,这个论坛上我没见到人说,只看见到处的噪音求助和讨论。
某纯电动汽车驱动系统24阶振动噪声的分析与优化
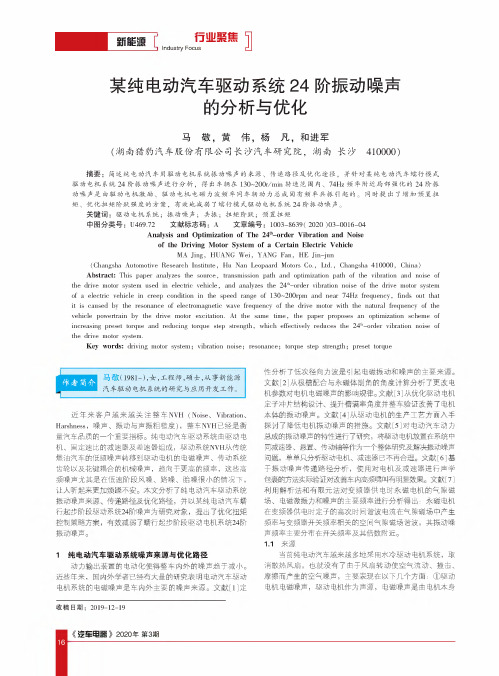
6 52
8-
7 60
8
-8
8 68
'-8 0 '
9 76
h 0 8.
10 84 11 92 12 100
8
-8
"-8
亠
040
1 12 8
16
2 20
"16 24 '1
3 28
”24 32( J
4 36 5 44
32
40
卩40 48 '
6 52
>48 56.
7 60 8 68 9 76
56
64
*64 72”
在变频器供电时定子的高时间谐电流在气隙磁场
频率与变频器开关频率相关的空间气隙磁场谐波-其振动噪
声频率主要分布在开关频率及其倍数附近。
1.1来源 当前纯电动汽车越来越多地米用水冷驱动电机系统,取
消散热风扇,也就没 由于风扇转动 空气流动、撞击、
摩擦而 的空气噪声,主要现在以下几个 :①驱动
电机电磁噪声,驱动电机作为声源,电磁噪声是由电机本身
驱动电机电 力 频率 车辆动力总成 频率共振引起
的。驱动电机和减速器连在
成的模态(74Hz),
驱动电机电力的频率着转速变,在蠕行步加速的
过程 着驱动电机转速、扭的上,新的模态 频率
电力波频率 ,
振。
综上所述,结合整车振动噪声测试数据和整车动力总成 频响、模态测试结果,车辆在130〜200r/min转速范围内,在 74Hz频率附近局部强 的24振动噪声是由驱动电机激励、
矩、优化扭矩阶跃强度的 ,有效地减弱了蠕行模式驱动电机系统24阶振动噪? %
关键词:驱动电机系统;振动噪?;共振;扭矩阶跃;预置扭矩
无刷直流电机噪音标准
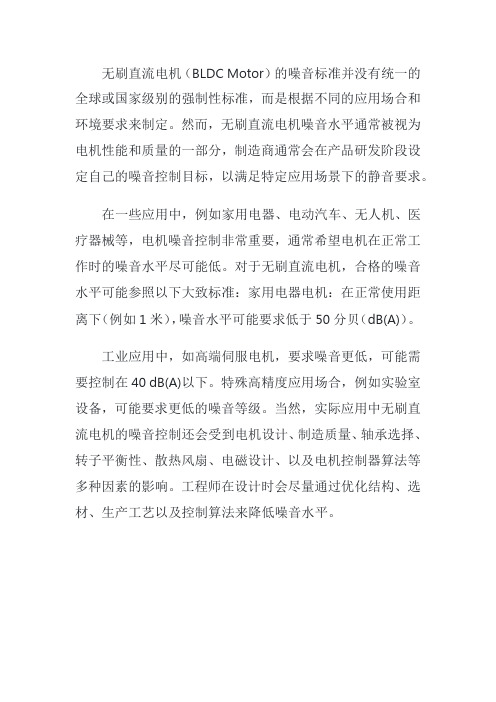
无刷直流电机(BLDC Motor)的噪音标准并没有统一的全球或国家级别的强制性标准,而是根据不同的应用场合和环境要求来制定。
然而,无刷直流电机噪音水平通常被视为电机性能和质量的一部分,制造商通常会在产品研发阶段设定自己的噪音控制目标,以满足特定应用场景下的静音要求。
在一些应用中,例如家用电器、电动汽车、无人机、医疗器械等,电机噪音控制非常重要,通常希望电机在正常工作时的噪音水平尽可能低。
对于无刷直流电机,合格的噪音水平可能参照以下大致标准:家用电器电机:在正常使用距离下(例如1米),噪音水平可能要求低于50分贝(dB(A))。
工业应用中,如高端伺服电机,要求噪音更低,可能需要控制在40 dB(A)以下。
特殊高精度应用场合,例如实验室设备,可能要求更低的噪音等级。
当然,实际应用中无刷直流电机的噪音控制还会受到电机设计、制造质量、轴承选择、转子平衡性、散热风扇、电磁设计、以及电机控制器算法等多种因素的影响。
工程师在设计时会尽量通过优化结构、选材、生产工艺以及控制算法来降低噪音水平。
永磁直流电动机振动和噪声分析
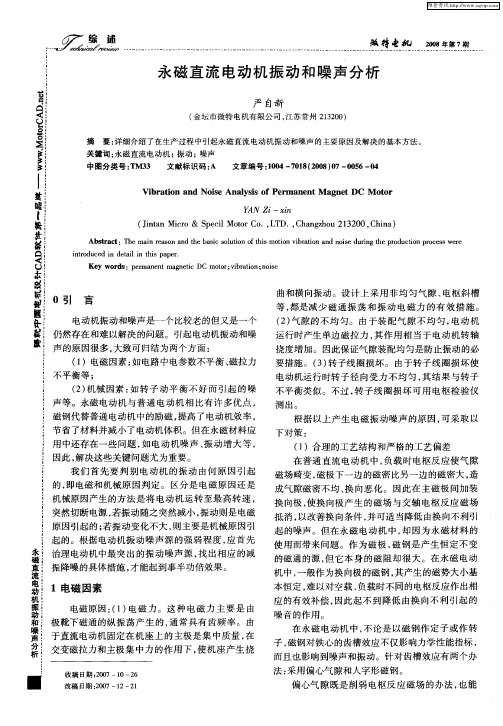
曲和横 向振 动 。设 计 上 采用 非 均 匀 气 隙 、 电枢斜 槽 等 , 是 减少 磁 通 振 荡 和 振 动 电磁 力 的有 效措 施 。 都
() 2 气隙 的不 均 匀 。由 于装 配气 隙不 均 匀 , 电动 机 运 行 时产生 单边 磁拉 力 , 作 用 相 当 于 电动 机 转轴 其
! 节 省 了材 料并 减小 了 电动机体 积 。但在永 磁材 料应 用 中还存 在一 些 问题 , 电动 机 噪 声 、 动增 大 等 , 如 振
因此 , 决这些关 键 问题尤 为 重要 。 解 我 们 首 先 要 判 别 电动 机 的振 动 由何 原 因引 起 的, 即电磁 和机 械 原 因判 定 。 区分 是 电磁 原 因还 是 机械 原 因产 生 的方 法 是将 电动 机 运 转 至最 高 转 速 ,
苗uⅡv o .
.. . ~ … …
薹
… … …
,
… …
钼『 ● 妊 聿 铎 盆 嘘 吐
… … … … … … … … … … … … … … … … … … 一
.
苎
… 28蔓. . …O !…. O. 塑 …主
永磁 直 流 电动机 振 动 和 噪声 分 析
严 自新
( 坛 市 微 特 电 机 有 限 公 司 , 苏 常州 2 30 ) 金 江 120
Ab t a t T eman r a o n eb s o ui n o i mo in v b ain a d n i u ig t ep o u t n p o e sw r sr c : h i e s n a d t a i s l t ft s t i r t n os d r r d ci r c s e e h c o h o o e n h o
永磁同步电机的振动与噪音解析
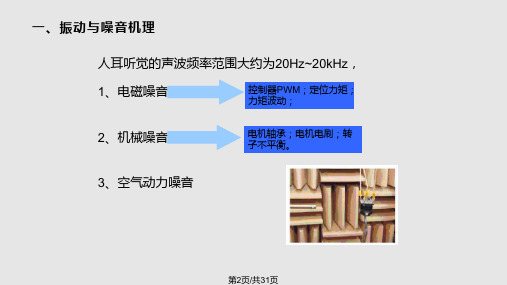
理想次数
二、定位力矩
啸叫
大电机噪音与电流波形 噪音频率为电流频率的18倍 机械转速的180次
第16页/共31页
理想次数
三、方波无刷直流电机力矩波动与噪音
波动力矩 波动力矩—指令一定下不同转角对应的电磁力矩波动分量 引起的原因:电动势e和电流 i 的波形偏离了理想波形
Tr
1
ei
T
第17页/共31页
❖存在幅值偏差Δi
Tr
2 i sin 2
3
--υ=2P
❖ 存在相位偏差Δθ
Tr
2 i cos 2
3
--υ=2P
❖ 存在恒定成分ΔI
Tr I sin --υ=P
存在 次谐波成分i
Tr icos( 1)
第23页/共31页
五、抑制措施
电机本体
定位力矩 优化电机系统固有频率
控制器
力矩波动
方波驱动器 正弦波驱动器
第6页/共31页
一、振动与噪音机理
合成磁动势:
F (,t) Fs cos[p(1 ) 1t] Frk cos[kp(0 t)]
k
气隙磁密: B (,t) F / S
单位面积力: B2 (,t) 20
N, cos( t) ,
第7页/共31页
一、振动与噪音机理
一、不随时间变化的恒定力波,即零次力波。恒定力波只是对定 子铁心产生静压力时铁心产生静变形,不产生振动和噪音; 二、定子磁动势同次谐波,力波角频率为2ηω1; 三、转子磁动势同次谐波,力波角频率为2kω1; 四、定子磁动势不同次谐波,力波角频率为(ηi±ηj)ω1 ; 五、转子磁动势不同次谐波力波,角频率为(ki±kj)ω1 ; 六、定、转子磁动势不同次谐波力波,角频率为(ηi±kj)ω1; 七、定、转子磁动势同次谐波力波,角频率为2ηiω1;
燃料电池系统集成技术中的噪声与振动控制研究
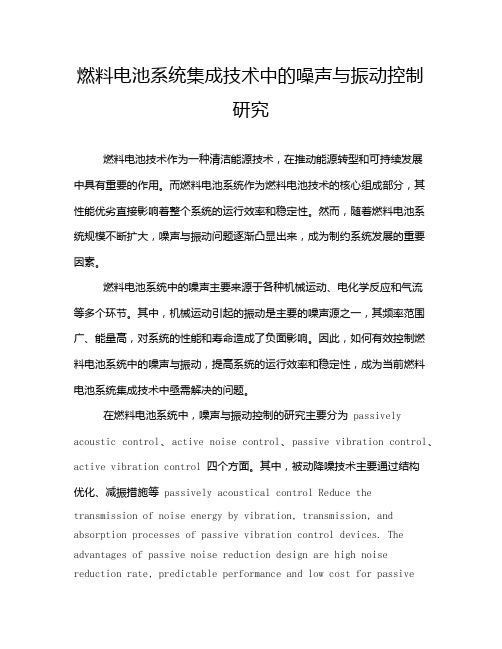
燃料电池系统集成技术中的噪声与振动控制研究燃料电池技术作为一种清洁能源技术,在推动能源转型和可持续发展中具有重要的作用。
而燃料电池系统作为燃料电池技术的核心组成部分,其性能优劣直接影响着整个系统的运行效率和稳定性。
然而,随着燃料电池系统规模不断扩大,噪声与振动问题逐渐凸显出来,成为制约系统发展的重要因素。
燃料电池系统中的噪声主要来源于各种机械运动、电化学反应和气流等多个环节。
其中,机械运动引起的振动是主要的噪声源之一,其频率范围广、能量高,对系统的性能和寿命造成了负面影响。
因此,如何有效控制燃料电池系统中的噪声与振动,提高系统的运行效率和稳定性,成为当前燃料电池系统集成技术中亟需解决的问题。
在燃料电池系统中,噪声与振动控制的研究主要分为 passively acoustic control、active noise control、passive vibration control、active vibration control 四个方面。
其中,被动降噪技术主要通过结构优化、减振措施等 passively acoustical control Reduce the transmission of noise energy by vibration, transmission, and absorption processes of passive vibration control devices. The advantages of passive noise reduction design are high noise reduction rate, predictable performance and low cost for passivenoise reduction. The main example of a passive noise reduction device is a silencer. 另外利用橡胶垫(rubber pad)、密封件(sealing),以及结构材料,使振动降低来减小振动对人体的刺激【Vlad Curmei;Niculescu M]][F];而在主动降噪技术方面,通过传感器采集系统内部噪声与振动信息,并通过控制器对抗声波进行相位和幅值调节,以消除或抵消噪声与振动,使系统运行在更加安静和平稳的状态,提高系统的整体性能。
直流电机噪音大的原因
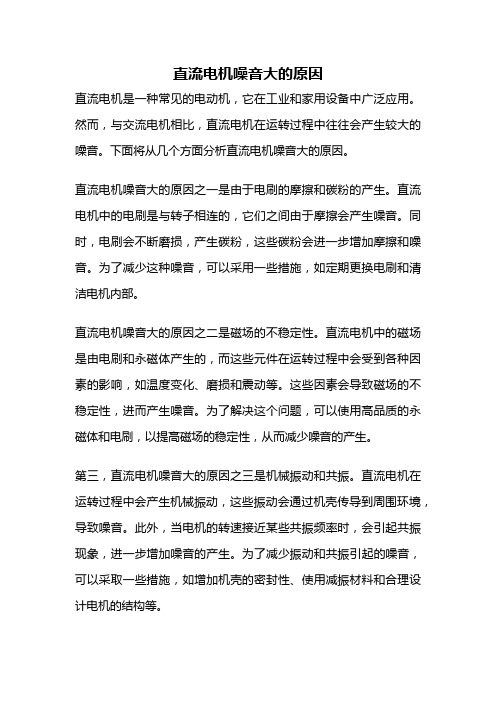
直流电机噪音大的原因直流电机是一种常见的电动机,它在工业和家用设备中广泛应用。
然而,与交流电机相比,直流电机在运转过程中往往会产生较大的噪音。
下面将从几个方面分析直流电机噪音大的原因。
直流电机噪音大的原因之一是由于电刷的摩擦和碳粉的产生。
直流电机中的电刷是与转子相连的,它们之间由于摩擦会产生噪音。
同时,电刷会不断磨损,产生碳粉,这些碳粉会进一步增加摩擦和噪音。
为了减少这种噪音,可以采用一些措施,如定期更换电刷和清洁电机内部。
直流电机噪音大的原因之二是磁场的不稳定性。
直流电机中的磁场是由电刷和永磁体产生的,而这些元件在运转过程中会受到各种因素的影响,如温度变化、磨损和震动等。
这些因素会导致磁场的不稳定性,进而产生噪音。
为了解决这个问题,可以使用高品质的永磁体和电刷,以提高磁场的稳定性,从而减少噪音的产生。
第三,直流电机噪音大的原因之三是机械振动和共振。
直流电机在运转过程中会产生机械振动,这些振动会通过机壳传导到周围环境,导致噪音。
此外,当电机的转速接近某些共振频率时,会引起共振现象,进一步增加噪音的产生。
为了减少振动和共振引起的噪音,可以采取一些措施,如增加机壳的密封性、使用减振材料和合理设计电机的结构等。
第四,直流电机噪音大的原因之四是电机内部的电磁干扰。
直流电机在运转过程中会产生电磁场,这个电磁场会干扰周围的电子设备,从而产生噪音。
为了减少这种干扰,可以采用屏蔽材料和滤波器等电磁兼容措施,以减少电机对周围设备的干扰,从而降低噪音的产生。
直流电机噪音大的原因主要包括电刷的摩擦和碳粉产生、磁场的不稳定性、机械振动和共振以及电机内部的电磁干扰等。
为了减少直流电机噪音,可以采取一系列措施,如定期更换电刷、使用高品质的永磁体和电刷、增加机壳的密封性、使用减振材料和合理设计电机的结构、采用屏蔽材料和滤波器等。
通过这些措施的综合应用,可以有效降低直流电机的噪音水平,提高设备的运行质量和环境舒适度。
- 1、下载文档前请自行甄别文档内容的完整性,平台不提供额外的编辑、内容补充、找答案等附加服务。
- 2、"仅部分预览"的文档,不可在线预览部分如存在完整性等问题,可反馈申请退款(可完整预览的文档不适用该条件!)。
- 3、如文档侵犯您的权益,请联系客服反馈,我们会尽快为您处理(人工客服工作时间:9:00-18:30)。
3482IEEE TRANSACTIONS ON MAGNETICS, VOL. 40, NO. 6, NOVEMBER 2004Characterization of Noise and Vibration Sources in Interior Permanent-Magnet Brushless DC MotorsHong-Seok Ko and Kwang-Joon KimAbstract—This paper characterizes electromagnetic excitation forces in interior permanent-magnet (IPM) brushless direct current (BLDC) motors and investigates their effects on noise and vibration. First, the electromagnetic excitations are classified into three sources: 1) so-called cogging torque, for which we propose an efficient technique of computation that takes into account saturation effects as a function of rotor position; 2) ripples of mutual and reluctance torque, for which we develop an equation to characterize the combination of space harmonics of inductances and flux linkages related to permanent magnets and time harmonics of current; and 3) fluctuation of attractive forces in the radial direction between the stator and rotor, for which we analyze contributions of electric currents as well as permanent magnets by the finite-element method. Then, the paper reports on an experimental investigation of influences of structural dynamic characteristics such as natural frequencies and mode shapes, as well as electromagnetic excitation forces, on noise and vibration in an IPM motor used in washing machines. Index Terms—Brushless machines, electromagnetic forces, noise, permanent magnet, vibrations.Fig. 1.Cross sections of BLDC motors.I. INTRODUCTIONCONVENTIONAL direct current commutator motors with permanent magnets are easy to control and require few semiconductor devices. Yet, they have serious operational problems in association with brushes. For examples, the brushes require regular maintenance and induce noise by friction with the commutators. A solution for these problems is brushless direct current (BLDC) motors. BLDC motors can be classified into two types, as shown in Fig. 1 according to the geometric shape and location of permanent magnets. Compared with surface mounted permanent-magnet (SPM) motors, interior permanent-magnet (IPM) motors have several advantages. One advantage comes from the position of magnets. Because permanent magnets are embedded in the rotor, the IPM motors can be used at higher speeds without debonding of the permanent magnets from the rotor due to the centrifugal forces. Another obvious advantage of the IPM motors is higher efficiency. That is, in addition to the mutual torque from the permanent magnets, the IPM motors utilize the reluctance torque generated by the rotor saliency [1].Manuscript received June 28, 2002; revised June 7, 2004. H.-S. Ko was with the Mechanical Engineering Department, Korea Advanced Institute of Science and Technology (KAIST), Daejon 305-701, Korea. He is now with Samsung Electronics Company Ltd., Suwon 443-742, Korea (e-mail: hskatom@yahoo.co.kr). K.-J. Kim is with the Mechanical Engineering Department, KAIST, Daejon 305-701, Korea (e-mail: kjkim@mail.kaist.ac.kr). Digital Object Identifier 10.1109/TMAG.2004.832991Regarding the noise and vibration, the IPM motors have more sources than the SPM motors. Furthermore, analysis of magnetic field in the IPM motors is more difficult due to the magnetic saturations, especially in the rotors. In an IPM motor, the electromagnetic excitation sources can be classified into three parts: cogging torque, ripples of mutual and reluctance torque, and fluctuations of radial attractive force between the rotor and stator. In an SPM motor, only the mutual torque is generally considered and an analytical method can be used [2], [3]. For the IPM motors, however, the finite-element method (FEM) is used to account for the magnetic saturation at the rotor core and, besides the mutual torque, the reluctance torque needs to be considered. In addition, although only the permanent magnet may be considered to calculate the radial attractive forces between the rotor and stator in the IPM motors [4], the electromagnetic field due to the currents may become significant depending on the loading and generate serious excitation forces. In this paper, a technique that can efficiently calculate the cogging torque as a function of rotor position by including saturation effects is proposed. Then, a torque equation for characterizing the space and time harmonics with respect to the mutual and reluctance torque ripples is used to extract their fluctuating components. The radial attractive forces due to the electric currents in the stator as well as the permanent magnets in the rotor are calculated by the FEM and its effects on noise and vibration are investigated. The noise and vibration in the motors are mostly generated by the electromagnetic sources and subsequently can be amplified by the dynamic characteristics of the motor structure. Therefore, influences of natural frequencies and mode shapes of the structures are experimentally investigated for the noise and vibration of an IPM motor under study. II. ELECTROMAGNETIC EXCITATION SOURCES Electromagnetic excitations in electric motors are caused by variation of both circumferential and radial forces acting between the stator and the rotor with respect to the time and space.0018-9464/04$20.00 © 2004 IEEEKO AND KIM: CHARACTERIZATION OF NOISE AND VIBRATION SOURCES IN IPM BLDC MOTORS3483Torque ripples in an IPM motor, the result of dynamic circumferential forces multiplied by an appropriate radius, are composed of two sources; cogging torque and ripples of mutual and reluctance torque. The cogging torque is due to physical geometry of the stator teeth and the rotor magnets. The ripples of mutual and reluctance torque are produced by harmonics of the flux linkages related to magnets, inductances, and currents. In addition, fluctuation of attractive forces in the radial direction between the rotor and stator works as excitation sources. The cogging torque, ripples of mutual and reluctance torque, and fluctuation of the radial attractive forces will be discussed next in more detail.Fig. 2. Geometric configuration of IPM motor.A. Cogging Torque The cogging torque is defined as a torque produced by magnetic forces in the circumferential direction between the stator teeth and the magnets of rotor. Because it is superposed on the mean output torque as a fluctuating component, it can be an important performance index of noise and vibration as well as smoothness in rotations of the rotor. In order to calculate the resultant torque for a given position of the rotor relative to the stator by taking the magnetic saturation in the rotor core and the complex geometric shapes of the stator teeth and rotor magnets into account, it is inevitable to employ numerical methods such as the FEM. Since this torque is rotor-position dependent, the numerical calculation must be repeated for every position of the rotor, which should be very time consuming and, hence, may not be a good tool at the phase of parametric study [5]. In this section, an efficient technique that can be useful in the initial design and modification stages is suggested. The technique is composed of the following steps. The first step is to calculate the flux density through the magnet, rotor core, air gap, slotless stator, rotor core, and the magnet by employing the FEM, just once to deal with the saturation problems in the rotor core. The second step is to obtain the boundary conditions in the slotted air gap by employing the concept of relative permeance [6]. The third is to compute the flux density in the slotted air gap as a series solution of the magnetic potential equation with the boundary conditions obtained from the second step. Finally, the cogging torque is derived from the Maxwell stress formula with movement of the rotor with respect to the stator. The flux density and field intensity in the air gap can be related as given in the following equation by assuming magnetic saturation does not occur in the air-gap region: (1) where is the permeability of air. Since the field intensity can be represented in terms of a magnetic scalar potential defined as (2) governing equation of the magnetic potential in the air-gap region is given by (3) where is the number of slots. Therefore, the second boundary condition is written as The circumferential coordinate denotes the angular displacement of the stator-fixed coordinate and the circumferential coordinate denotes the angular displacement of the rotor-fixed coordinate as shown in Fig. 2. The coordinate is related to the , where the coordinate by the rotor movement is the rotational displacement of the rotor with coordinate respect to the stator and given by the rotation frequency multiplied by the time, i.e., is equal to . Therefore, the flux density on the inner surface of the stator in the radial direction and the one on the outer surface of the rotor in the circumferential direction in the slotless air gap can be respectively represented by Fourier series as (4) (5) where is the number of pole pairs. The flux density in the slotted air gap can be obtained by solving the governing equation (3) with two boundary conditions. One comes from the fact that the slotting effect on the circumferential flux distribution on the outer surface of rotor can be neglected. Therefore, the circumferential flux density along the outer surface of the rotor can be represented by (5). The other comes from the fact that the radial flux density on the inner surface of the stator in slotted air gap can be calculated by the product of the radial flux density in the slotless air gap and the relative permeance in (6) (6)(7)3484IEEE TRANSACTIONS ON MAGNETICS, VOL. 40, NO. 6, NOVEMBER 2004The general solution of (5) in the slotted air gap may be proposed as follows:(8) Hence, the flux density in the slotted air gap can be written asFig. 3.Cogging torque profile with rotor positions. TABLE I PARAMETERS OF IPM MOTOR UNDER STUDY(9)Fig. 4.Harmonic components of cogging torque.The circumferential stress in air gap is calculated by the Maxwell stress tensor as (11) Therefore, the cogging torque can be calculated as (12) where is an arbitrary circle in the air gap with the radius from the center of the rotor , and is the axial length of the rotor. Fig. 3 shows estimations of the cogging torque by the proposed technique together with those by measurements and the conventional FEM, where the flux density is computed with parameters as shown in Table I. The results of the proposed technique show good agreement with those of FEM and measurement both in magnitude and waveform. Fig. 4 shows the components of the cogging torque harmonics. Therefore, the(10)KO AND KIM: CHARACTERIZATION OF NOISE AND VIBRATION SOURCES IN IPM BLDC MOTORS3485cogging torque can generate the noise and vibration at the frequency of the rotor rotation multiplied by 24 and its higher harmonics. B. Mutual and Reluctance Torque Ripples As explained in the introduction, the output torque of an IPM motor is given by sum of the mutual torque and the reluctance torque, each of which can be expressed by using the following energy method [7]: (13)By substituting (15) and (17) into (13), the mutual torque can be rewritten as follows:(18) harmonics, and where is the order of the flux linkage is the order of current harmonics. When is zero, the mutual torque is constant, i.e., completely static. When and are multiples of three, the mutual torque should have harmonics at the source frequency multiplied by such multiples of three. By substituting (16) and (17) into (14), the reluctance torque can be rewritten as follows:(14) In the above equations, the coordinate is the electrical angle and given by the mechanical angle multiplied by the number , , , and the currents of pole pairs , i.e., is equal to in the coils of phase , , and , respectively, the inductance between the phase and the phase , and the flux by the permanent magnets linking the phase . Ripples of the mutual and reluctance torque, defined as fluctuating components of the output torque, are governed by several factors such as the shape of currents with respect to time, variations of inductances, and with respect to rotor movement, which are flux linkages further discussed in the following. in (13) can be represented by Fourier The flux linkage series as (15) where , , and are 0, , and , respectively. The inductance matrix can be formulated as follows [8]:(19) where and stand for the order of current harmonics and the order of inductance harmonics. It can be seen from (19) that or the reluctance torque become static only when is zero and, when , or are multiples of three, it should have harmonics at the source frequency times multiples of three. Equation (18) and (19) are very useful for characterizing and, hence, reducing the mutual and reluctance torque ripples. For example, when the space harmonics ( and ) are beyond control or the ripples of the mutual and reluctance torque can be reduced by controlling the waveform of the current . The flux linkage of the IPM motor under study can be obtained by an integral of the flux density due to the permanent magnet in air gap as follows: (20) where is the number of coils per phase per pole pairs and a half of the slot pitch. The flux density in the middle of air(16) where is harmonic coefficients of the self inductance and those of mutual inductance. Variations of inductance with respect to the rotor position are caused by the magnetic saturation of the rotor core. Therefore, in IPM motors the inductance matrix should be obtained by the FEM or measurements. The currents supplied to the IPM motors are often not a pure harmonic function of time and, hence, can be represented by Fourier series as follows: (17) where the leading angle is an angle between the fundamental component of the flux fields by the magnets and that by the currents. The electrical angle is also given by the source frequency multiplied by the time, i.e., is equal to .3486IEEE TRANSACTIONS ON MAGNETICS, VOL. 40, NO. 6, NOVEMBER 2004Fig. 5. Harmonic coefficients of flux linkage .Fig. 6. Self inductance Lby measurements.Fig. 7. (a) Waveform and (b) harmonic coefficients of current at 500 r/min.gap due to the permanent magnets can be obtained by (9) and can be rewritten as (21) Therefore, the harmonic coefficients of the flux linkages around the phase , , and can be derived by substituting (21) into (20) as follows: (22) Fig. 5 shows harmonic coefficients of the flux linkage and Fig. 6 measured self inductance . The inductance is close to a sinusoidal wave and, hence, higher harmonics of the inductance except the fundamental can be neglected. The IPM motor under study is for washing machines and runs at 500 r/min in the slow washing mode and at 10 000 r/min in the fast dehydration mode. Fig. 7 shows the current at 500 r/min under the load of 9.6 kg cm and Fig. 8 harmonic with components of the mutual, reluctance, and total torque, where it can be seen that the reluctance torque which does not exist in the SPM motors, resulted in increase of the static torque by about component by 19.7% and, surprisingly, decrease of the about 47%. Here, the stands for the rotation frequency, which is twice the source frequency for a 4-pole IPM motor. Yet, the component, which does not show up in the SPM motors, showed up undesirably. Fig. 9 shows waveform in time domain and harmonic coefficients of currents for the motor running at under no-load. The output torque 10 000 r/min with and the ripples are shown in Fig. 10, where it can be seen that not only and component but also component hasFig. 8. Harmonic components of output torque at 500 r/min when lead angle is 30 .0shown up, and the reluctance torque has contributed to decrease of the static torque as well as the dynamic torque. C. Fluctuation of Attractive Forces Between the Rotor and Stator Excitation sources explained in Section II-A and B are variations with time of the output torques, which were classified into cogging torques independent of the electric current and ripples of the mutual and reluctance torque due to the currents. In this subsection, another type of excitation source is discussed, which is related to the spatial distribution of the radial attractive forces between the stator and the rotor. The radial attractive force or so called the Maxwell stress on the inner surface of the stator can be written as [4]: (23)KO AND KIM: CHARACTERIZATION OF NOISE AND VIBRATION SOURCES IN IPM BLDC MOTORS3487Fig. 11.Distributions of radial flux density on inner surface of stator.Fig. 9. Waveform and harmonic coefficients of current at 10 000 r/min (a) waveform (b) harmonic coefficients.Fig. 12. Radial attractive force at given stator’s slot with respect to rotor positions.Fig. 10. Harmonic components of output torque at 10 000 r/min when lead angle is 15 .Since permeability of the iron in the rotor and stator is extremely large compared with that of the air, the stress due to the flux , which is inversely proportional to the density in the iron, permeability of the iron, can be neglected. Therefore, the radial attractive force on the end surfaces of the stator’s teeth can be written as (24) The equivalent air gap of the SPM motor given by is rather large compared with the pure air gap since the relative recoil permeability of the magnets is approximately 1. Therefore, the magnetic flux in the air gap by the currents in the stator can be neglected. The air gap in theIPM motors, however, is just because the magnets are embedded into the rotor. As a consequence, it is essential to take the magnetic field by the currents into consideration to analyze the effects of the attractive forces on noise and vibration in the IPM motor. Fig. 11 shows distributions of the radial flux density on the inner surface of the stator when the magnitude of currents is 2.5 A. The maximum flux density by both magnets and currents is three times larger than that by the magnets alone. Fig. 12 shows variations of the radial attractive force on a given stator teeth with movement of the rotor with respect to the stator. Fig. 13 shows harmonic components of the corresponding attractive forces, where it can be seen that integer multiples of component show up and the radial attractive force at by both magnets and currents is about 14 times larger than that by the magnets alone. Therefore, it can be claimed in general that the radial attractive forces in the IPM motors are far larger than those in the SPM motors regarding the noise and vibration and that the motor structure will be excited at harmonics of the frequency of rotor rotation multiplied by the number of poles or twice the number of pair of poles. In summary of this section, it is claimed that the electric current in the stator in the IPM BLDC motors is far more strongly responsible for noise and vibration than in the SPM motors and that the frequency characteristics of the electromagnetic excitation sources in the IPM BLDC motors can be described as follows.3488IEEE TRANSACTIONS ON MAGNETICS, VOL. 40, NO. 6, NOVEMBER 2004Fig. 13.Harmonic components of radial attractive force.1) Cogging torque: the lowest common multiple of numbers of slots and poles times the rotating frequency and its higher harmonics. and its 2) Ripples of mutual and reluctance torque: higher harmonics. 3) Fluctuations of radial attractive force: number of poles times and its higher harmonics. III. NOISE AND VIBRATION OF MOTOR UNDER OPERATION In this section, the noise and vibration measured for an IPM motor running are presented and discussed for the purpose of supporting the claims in Section II. For the IPM motor, which had noticeable noise problems at 10 000 r/min, measurements were made with power on and immediately after disconnection of the power in order to investigate contribution of the electromagnetic excitation sources. The spectrum of an acceleration signal measured from a point on the outer surface of the stator is shown in Fig. 14. Since the axial length of the stator is short relative to the diameter, transverse modes were not observed in the frequency range shown in Fig. 14 but the acceleration signal was taken at one position on the center plane where the vibrations were largest. After the disconnection of the electric power, the rotating frequency decreased slightly from 188 Hz (11 200 r/min) to 168 Hz (10 000 r/min) and, as can be seen in the figure, most of the peaks with power on disappeared after power off, which are believed to be related to the electromagnetic excitations. Although the peak at was reduced in its magnitude by power off, it did not disappear completely because this peak was contributed by fluctuations of the radial attractive force due to the permanent magnets. A power spectrum of sound pressure level was measured at 10 000 r/min with power on and is shown in Fig. 15, where the first peak at 168 Hz, which was observed also in the acceleration shown in Fig. 14, is believed to be due to the rotor unbalance. Comparing the peak frequencies of the sound pressure level spectrum in Fig. 15 with those in Figs. 4, 10, and 13 allows the source of each peak to be understood. That is, the peaks at , , , and are due to variation of the radial attractive forces with rotation of rotors with four poles, the peak at due to the ripples of torque, and the peaks at and due to both fluctuation of the attractive force and ripples of the mutual and reluctance torque. The peaks at and seem to have been magnified by resonance because natural modes happened to exist at these frequencies, 1.34 and 2.67 kHz, respectively, which were found atFig. 14.Distributions of radial flux density on inner surface of stator.Fig. 15.Noise of IPM motor at 10 000 r/min.the stage of modal testing and operational deflection shape analysis for investigation of possible coincidence between excitation frequencies and modal properties of the structure. The natural frequencies and mode shapes were obtained from the measurements along the centerline on the surface of the stator and are shown in Fig. 16. The first mode at 865 Hz looks like a rigid body motion of the stator relative to the rotor and the modes at 1.34 and 2.64 kHz the first and the second elastic mode, respectively. Fig. 17 shows operational deflection shapes of the stator at major peak frequencies in Fig. 15. The deflection shape at 168 Hz, the rotating frequency of the rotor seems to be a rigid body motion where the stator itself whirls. The deflection shapes at both 1.34 and 2.67 kHz coincided with mode shapes at the corresponding natural frequencies, as could be expected.KO AND KIM: CHARACTERIZATION OF NOISE AND VIBRATION SOURCES IN IPM BLDC MOTORS3489Fig. 16.Mode shapes of IPM motor under study.attractive forces due to the magnetic flux by the permanent magnets in the rotor and electric currents in the stator was computed by the FEM to include nonlinear effects, where significance of the magnetic flux due to the electric current that is often neglected in the SPM motors was pointed out. In an illustrative investigation into an IPM motor, peak frequencies in the spectrum of the sound pressure level could be linked with such excitation sources and modal characteristics of the motor structure as well. REFERENCES[1] T. J. E. Miller, Brushless Permanent-Magnet and Reluctance Motor Drives. New York: Oxford Univ. Press, 1989. [2] Z. Q. Zhu and D. Howe, “Analytical prediction of the cogging torque in radial-field permanent magnet brushless motors,” IEEE Trans. Magn., vol. 28, pp. 1371–1374, Mar. 1992. [3] A. B. Proca, A. Keyhani, and A. EL-Antably, “Analytical model for permanent magnet motors with surface mounted magnets,” in Proc. IEMD ’99, pp. 767–769. [4] K. T. Kim, K. S. Kim, S. M. Hwang, T. J. Kim, and Y. H. Jung, “Comparison of magnetic forces for IPM and SPM motor with rotor eccentricity,” IEEE Trans. Magn., vol. 37, pp. 3448–3451, Sept. 2001. [5] D. Howe and Z. Q. Zhu, “The influence of finite element discretization on the prediction of cogging torque in permanent magnet excited motors,” IEEE Trans. Magn., vol. 28, pp. 1080–1083, Mar. 1992. [6] Z. Q. Zhu and D. Howe, “Instantaneous magnetic field distribution in brushless permanent magnet dc motor, part III: Effect of stator slotting,” IEEE Trans. Magn., vol. 29, pp. 143–151, Jan. 1993. [7] T. S. Low, K. J. Tseng, T. H. Lee, K. W. Lim, and K. S. Lock, “Strategy for the instantaneous torque control of permanent-magnet brushless DC drives,” Proc. Inst. Elect. Eng. , vol. 137, pp. 355–363, Nov. 1990. [8] P. C. Kraus, Analysis of Electric Machines. New York: McGraw-Hill, 1987.Fig. 17.Operational deflection shapes at 10 000 r/min.IV. CONCLUSION Analysis of electromagnetic excitation sources in the IPM motors is far more difficult than in the SPM motors because magnetic saturations in the rotor core are more likely to occur in the former. In this paper, such sources were classified into three types and efficient methods were presented to characterize each source, and then contribution of the sources to the noise and vibration was investigated for an IPM motor. An efficient technique was presented for computation of the cogging torque, where magnetic saturations in the rotor can be taken into account by employing the FEM just once for the slotless stator and effects of the stator slot are reflected by the concept of relative permeance. A formula was derived for representation of ripples of the torque based on the output torque formula. It was shown that the space and time harmonics are responsible for the torque ripples at three times the source frequency and their integer multiples. Then distribution of radialHong-Seok Ko received the B.S. degree in mechanical engineering from Korea University, Seoul, Korea, in 1991, and the M.S. and Ph.D. degrees in mechanical engineering from Korea Advanced Institute of Science and Technology (KAIST), Daejon, in 1993 and 2003, respectively. From 1993 to 1998, he was with LG Innotec Corporation. He is currently with Samsung Electronics Company Ltd., Suwon, Korea. His academic interests involve the noise and vibration induced by the electromagnetic excitation sources.Kwang-Joon Kim received the B.S. and M.S. degrees in mechanical engineering from Seoul National University, Seoul, Korea, in 1976 and 1978, respectively, and the Ph.D. degree from the University of Wisconsin, Madison, in 1982. He is a Professor in the Department of Mechanical Engineering at the Korea Advanced Institute of Science and Technology (KAIST), Daejon. His current interests include the application of viscoelastic materials for vibration control, vibration isolation based on power transmission approach, modal testing and operational deflection shape analysis, and noise and vibration of electric motors.。