最新铸件孔隙率检验标准及方法(VW50093和PV6093介绍)PPT幻灯片课件
铸件孔隙率检测方法

铸件孔隙率检测方法
铸件孔隙率的检测方法有多种,其中一种简单直观、易于实施的方法是视觉检测法,通过直接观察铸件表面及断面的孔洞情况,判断其孔隙率大小。
这种方法适用于孔洞较大、表面可见的铸件,如灰铸铁等。
另一种检测方法是金相磨面法,该方法能够提供最准确的关于孔隙的来源和形成以及其它结构杂质的信息,因此它是一种对零件关键部位的情况具有最大说服力的检验方法。
但是,这种检验方法是一种非常耗时的破坏性检测方法,操作时要求特别地细心。
此外,还有专门的孔隙率检测仪可以用于检测铸件的孔隙率,该仪器通过在铸件中施加压力的方式,测量其孔隙率大小。
这种方法适用于各种类型的铸件,包括灰铸铁、球墨铸铁等。
综上所述,铸件孔隙率的检测方法有多种,具体选择哪种方法需要根据铸件的类型、孔隙大小和检测要求来决定。
《压铸件检验规范》课件
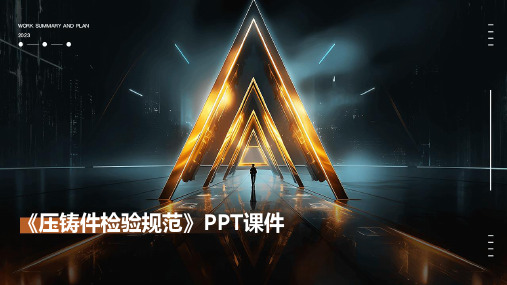
尺寸精度
内部缺陷
复杂度高、要求严格
汽车发动机缸体压铸件 是压铸件中较为复杂的 一种,其检验过程需严 格遵循相关标准,确保 产品质量。检验内容包 括外观质量、尺寸精度 、内部缺陷等方面。
检查表面是否光滑、无 气孔、无裂纹等缺陷。
测量各部位尺寸是否符 合图纸要求,确保装配 无误。
采用X光或超声波检测内 部是否存在气孔、缩孔 、裂纹等缺陷。
颜色和光泽
确保压铸件的颜色和光泽 符合要求,无明显色差。
铸造痕迹
检查压铸件上是否有铸造 痕迹,如浇口、溢流口等 。
尺寸检验
测量工具
使用卡尺、千分尺等测量工具,确保压铸件尺寸符合 图纸要求。
尺寸精度
检查压铸件的关键尺寸,如孔径、外径、厚度等,确 保在公差范围内。
形位公差
检查压铸件的形位公差,如平行度、垂直度、圆度等 。
夹渣
总结词
压铸件内部或表面存在与基体金属不 同的杂质或夹杂物。
详细描述
夹渣是由于在压铸过程中,金属液中 混入了非金属杂质或上一批金属残渣 而形成的。夹渣的位置和大小取决于 金属液的纯净度和浇注系统设计。
欠铸
总结词
压铸件因未完全填充模具型腔而出现的缺损或不足。
详细描述
欠铸是由于在压铸过程中,金属液流动受阻、浇口位置不当或模具设计不合理等原因造成的。欠铸通 常出现在铸件壁厚较薄或形状复杂的部位,导致铸件性能下降或无法满足使用要求。
缩孔
总结词
压铸件内部或表面出现不规则的孔洞或凹陷。
详细描述
缩孔是由于在压铸过程中,金属液冷却收缩时未能得到足够的补充而形成的。缩 孔的位置通常出现在铸件壁厚较大或热节处,与模具温度、金属液温度和浇注系 统设计等因素有关。
《铸件质量检测》课件

工业设备
铸造厂检测
对工业设备的铸件进行化学分析和 检测,确保设备的可靠性和耐用性。
对铸造过程中的铸件进行全面的质 量检测,提高铸件的一致性和产品 质量。
铸件质量检测的挑战与解决方案
挑战
复杂的铸件结构和形状增加了检测难度。
解决方案
采用先进的检测技术和设备,结合专业人员的经验和 知识。
总结和展望
铸件质量检测是保证工业制造质量的重要环节。 未来,随着技术的进步,铸件质量检测将更加智能化、精准化。
化学分析
通过化学分析仪器检测铸件的化学成分,确保铸件的材料质量达到要求。
铸件质量检测的关键环节
1
检测方法选择
根据铸件的特性和要求选择合适的检测方法。
2
检测设备准备
确保检测设备的完好与准备充分,以保证检测结果的准确性。
3
检测过程执行
按照规定的检测方法和步骤进行铸件的质量检测。
常见的铸件质量问题及其原因
《铸件质量检测》PPT课 件
铸件质量检测的背景和重要性
铸件的质量检测在工业制造中起着至关重要的作用。它确保铸件的质量符合 标准,提高产品的可靠性和耐用性。
铸件质量检测的常用方法和技术
无损检测
包括超声波检测、射线检测和磁粉检测等高效、无损的方法。
尺寸测量
利用传感器和测量工具进行精确的尺寸测量,以确保铸件的几何尺寸符合规定。
1 气孔缺陷
原因:熔融金属中存在气体,不完全排出或包裹在固化过程中形成气孔。
2 缩孔缺陷
原因:熔融金属在固化过程中由于收缩而形成孔。
3 夹杂物
原因:杂质、砂粒等进入熔融金属中,形成夹杂物。
铸件质量检测的案例分析
汽车零部件
通过无损检测和尺寸测量,确保汽 车零部件的质量符合标准,提高汽 车的安全性和可靠性。
PV_6097草案(孔隙率)

分类号:A6000 草案 2007年5月VOLKSW AGEN AG (大众汽车股份公司)气孔率测定按照VW 50097的规定PV6097公司标准主题词:气孔率、气孔率测定、气孔率试验、铸件的气孔率试验使用注意事项征求意见截止日期:2007-06-04 因为即将发布的正式标准可能与本草案有偏差,原则上不能按照本草案的规定执行。
如果特殊情况下仍然需要使用本标准的草案,使用者之间应进行协商。
目录1 适用范围 (1)2 目的 (2)3 标记 (2)4 定义和术语 (2)5 试验的实施 (2)5.1 有关参考面的规定 (2)5.1.1 允许的参考面的几何形状 (2)5.1.2 参考面的选择及其尺寸 (3)5.1.3 参考面的位置 (3)5.2 切割面(断面)或者投影面的选择 (4)5.3 待评定参考面的质量 (4)5.3.1 评定气孔级别S的参考面 (4)5.3.2 评定气孔级别D的参考面 (4)5.3.3 评定气孔级别F的参考面 (5)5.3.4 评定气孔级别G的参考面 (5)5.4 参考面的评定 (5)5.5 气孔率试验结果 (6)5.6 气孔率试验实例 (6)6 同时有效的文件 (6)附录(资料性附录) (7)A.1 气孔级别D——试样制备和评定时的问题和缺陷 (7)A.2 在一个金相抛光磨片上测定气孔率 (10)A.3 气孔率不同的磨片的图示 (15)1 适用范围本标准适用于图纸或同时有效的标准中含有VW 50097规定的气孔率要求的金属铸件。
以前的VDG-Merkblatt P 201规定的气孔率要求,应参照VW 50097中相应的规定执行。
后继2~19页专业负责人:K-GQL-2/1 Hannes W endt电话:+49-5361-9-38956 K-GQL-2 Stefan Eisenberg博士标准(EKTC,1733):EKTC/4 Gabriela Bochynek电话:+49 5361-9-21698 Manfred Terlinden机密。
《铸件锻件的检验》课件

总结
铸件和锻件检验的重要性
铸件和锻件检验是确保产品质量的重要步骤,可以有效避免事故的发生。
检验流程与方法总结
合理的检验流程和方法有助于提高检验效率和精度。
未来发展趋势
未来随着技术的发展,无损检测和数字化检验将成为主流趋势。
锻件检验
锻件检验的目的
验证锻件是否通过正确的铸造和加工过程,符 合设计要求和标准。
锻件检验方法
目测检验、无损检验、化学成分分析、机械性 能测试等。
目测检验
检测锻件的表面缺陷、气泡及其他不良痕迹。
无损检验
通过射线和超声波等无损检查技术检测锻件质量。
检验标准和要求
铸件检验标准和要求
• 《GB/T 6414-2008 铸钢品质控制标准通则》 • 《GB/T 2828.1-2012接收抽样检验 一般检
铸件检验设备和工具
超声波探伤、化学分析仪、温度计、砂型材料成分 分析设备等。
锻件检验设备和工具
拉力试验机、硬度仪、X光机等。
检验流程与注意事项
1
铸件检验流程与注意事项
包括熔炼前、熔炼中、浇注、冷却砂型、取样、理化试验、铸件外观检查、铸件 缺陷分析等流程。
2
锻件检验流程与注意事项
包括钢锭选料、锻造工艺、锻件热处理、机械加工、成品定尺、产品质量检验等 流程。
验程序》 • 《GB/T2665-2008压力管道及其配件铸钢件
理化试验方法》
锻件检验标准和要求
• 《GB/T 9074.2-2009 钢锻件的理化检验方 法第2部分:组成分析》
• 《GB/T 30632金压差达标检验
规程》
检验设备和工具
确保产品质量,减少不必要 的浪费,防止产品出现安全 隐患。
最新铸件孔隙率检验标准及方法(VW50093和PV6093介绍)

10
如果图纸或标准里有这个标准、在技术条件和其他标准里出现或被提及, 那么以下的通用要求对整个零件都适用。 铸铁或铸钢零件:VW50093-%1 锌合金零件 其他零件 :VW50093-%10 :VW50093-5%
如果有例外的要求,必须写入图纸
11
VW50093和VW50097的区别
VW50097(Old) D10/2 VW50093(New) %10/Ф2 or Rz0/%10/Ф2
D10/R
D5/2/P1 D5/2/M S10/4 S5 但试样粗糙度Rz小于15μm
%10 %4
(中间三分之一区域) (外面三分之一区域)
%5/Ф2(中间三分之一区域) %5/Ф1(外面三分之一区域) %5/Ф2/Nk1 Rz25/%10/Ф4 Rz15/%5
F4
F2/2/A2/P0.5
Z4
Z2/Ф2/A2/U0.5
8
VW50093- %10/Ф2/A3/H1 整个评判面都允许疏松出现 孔隙之间的最低距离 3X Фmin 最大单个孔隙直径小于 2mm 孔隙率小于10%
9
VW50093-Z4/Ф2/A2/Hk1/U0.5 Ф0.5以下的孔隙可以忽略不计 疏松在评判面中间三分之一区域是允许的 孔隙之间的最低距离 2X Фmin 最大单个孔隙直径小于 2mm 评判面上最多可以有4个孔隙
1.2.6 Z : 最多允许的单独孔隙的数量,仅用于加工面。 疏松被认为是一个单独的孔隙而计入。
5
1.2.7 H、HR、Hk : 材料堆积(疏松) 材料堆积是指当两个孔隙之间的距离小于较小那个孔隙 的直径时的那些孔隙堆积。
H : 指整个评判面上的疏松 HR :指整个评判面外面三分之一壁厚的区域 HK :指整个评判面中间三分之一的区域 H、HR、Hk 后面有两个选项 选项 0 :表示疏松是不允许的 选项 1 :表示疏松是允许的 如果图纸在允许疏松的同时也定义了单个孔隙的最大尺寸(Ф), 此时的疏松被当成一个单独的孔隙来对待,也就是说疏松的最大 尺寸不能大于Ф。
铸件的质量检验方法及标准PPT课件
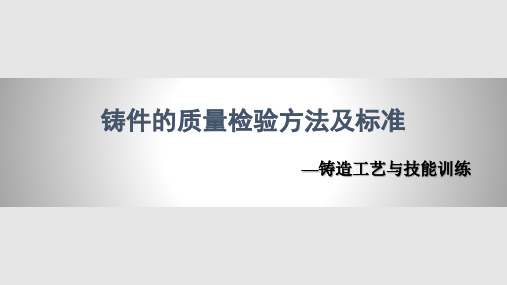
—铸造工艺与技Байду номын сангаас训练
一、铸件质量检验概述
根据用户要求和图样技术条件等有关协议的规定,用目测、量具、仪 表或其他手段检验铸件是否合格的操作过程称为铸件检验。
铸件质量检验的依据是:铸件图、铸造工艺文件、有关标准及铸件交 货验收技术条件。
二、铸件的质量等级
检验后,根据铸件的质量情况可分为下列三类:
(3)铸件质量偏差的检测 1)铸件质量偏差检测术语见表11-4。 2)铸件公称质量的确定 3)铸件质量公差等级和公差数值的确定 4)铸件质量偏差的检验和评定程序
(4)铸件浇冒口残余量的检验 (5)铸件表面和近表面缺陷的目测检验 用肉眼或借助于低倍放大镜,检查暴露在铸件表面的 宏观缺陷,同时检查铸件的生产标记是否正确齐全。检 查时应判定铸件对于检查项目是否合格,区分合格品、 返修品和废品。 (6) 铸件内腔质量的检验
2. 铸件内在质量的检验 铸件内在质量是指一般不能用肉眼直观检查出来的铸 件内部状况和达到用户要求的程度。检验内容包括铸件 的化学成分、物理和机械性能、金相组织以及存在于铸 件内部的孔洞、裂纹、夹杂物等缺陷。 铸件内在质量的检验方法和检验内容见表11-5。
3. 质量检验报告 检验人员在接受检验任务之后,将按照有关的检验项 目和试验规范对有关产品进行检验。检验结束后必须开具 质量检验报告,提供相关数据。 质量检验报告一般包括以下内容: 被测试样的产品名 称、试样名称、测试项目、委托单位或部门、委托日期、 测试日期、测试环境、测试人员、校核、审核、批准人员、 测试仪器、设备、测试标准、测试方法、测试数据、测试 结果。
三、铸造生产检验过程
检验工作不应以检验为目的,而应作为改善铸件质量的有效方法。铸造生产 的检验可分为彼此密切相关的三个阶段,见表11-2。
铸件质量检测PPT课件
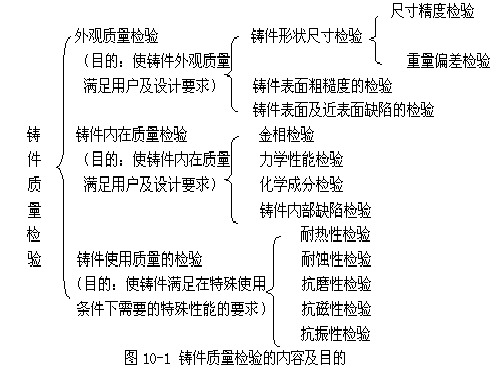
a) b) c) 图10-12 变形示意图 a) 模样变形 b)铸形变形 c)铸件变形
三、检验方法及结果 1. 铸件外形及几何尺寸的检测 2. 铸件重量偏差检验 3. 铸件化学成分检验 4. 铸件本体的金相检验 5. 球墨铸铁及活塞环的力学性能 6. 铸件的无损检测 7. 铸件缺陷分析
图10-25 灰铸铁B型抗拉试样 a) B1型 b) B2型
三、化学成分检验 四、铸件内部缺陷检验 第四节 铸件质量检验的工程应用实例 一、铸件简介 二、铸件质量检验项目 1.铸件外形及几何尺寸的检测,并由此测定铸造收缩率; 2.铸件重量偏差检验; 3.球墨铸铁化学成分分析; 4.铸件本体的合金检验; 5.球墨铸铁活塞环的力学性能; 6.无损检测(抽查); 7.铸件缺陷分析。
a) b) 图10-14 错芯示意图 图10-15 偏芯(漂芯)示意图 a)水平砂芯上浮 b) 凸出砂台断裂上浮 图10-16金属夹杂物示意图(下图)
a) b) 图10-20灰铸铁单试样铸坯示意图 图10-21 灰铸铁单附铸试块铸坯图
a) b) 图10-22 U形单铸试块和Y形单铸试块图 a)U形试块图 b)Y形试块图
第三节 铸件内在质量检验
铸件内在质量是通常是指其室温状态时的力学性能,金相组织及化学成分,内部缺陷等,对于特殊用途的铸件,还应包括如下一些特殊性能,如高(低)温力学性能、耐磨性、耐蚀性、减振性、承压密封性、电学、磁学性能等等。 一、金相检验 二、力学性能检验 1、拉伸试验及试样毛胚 2、冲击试验 3、硬度试验
a) b) 图10-5 冷裂示意图 图 10-4缩孔、缩松、疏松示意图 a)缩孔 b)缩松、疏松
第二节 铸件外观质量检验方法
一、常见铸造缺陷的特征及识别 图10-2 飞翅、毛刺示意图 a)飞翅 b)毛刺 c)脉纹
- 1、下载文档前请自行甄别文档内容的完整性,平台不提供额外的编辑、内容补充、找答案等附加服务。
- 2、"仅部分预览"的文档,不可在线预览部分如存在完整性等问题,可反馈申请退款(可完整预览的文档不适用该条件!)。
- 3、如文档侵犯您的权益,请联系客服反馈,我们会尽快为您处理(人工客服工作时间:9:00-18:30)。
铸铁或铸钢零件:VW50093-%1
锌合金零件 :VW50093-%10
其他零件
:VW50093-5%
如果有例外的要求,必须写入图纸
11
11
VW50093和VW50097的区别
D10/2 D10/R
VW50097(Old)
D5/2/P1
D5/2/M S10/4 S5 但试样粗糙度Rz小于15μm F4 F2/2/A2/P0.5
1.2.6 Z : 最多允许的单独孔隙的数量,仅用于加工面。 疏松被认为是一个单独的孔隙而计入。
5
5
1.2.7 H、HR、Hk : 材料堆积(疏松) 材料堆积是指当两个孔隙之间的距离小于较小那个孔隙 的直径时的那些孔隙堆积。
H : 指整个评判面上的疏松 HR :指整个评判面外面三分之一壁厚的区域 HK :指整个评判面中间三分之一的区域
14
14
2 .试样的制备要求 2.1 Rz=0
(替代2007版PV6097)
2.1 基准面的选择 PV6097(Old)
PV6093(New)
一般只可以用正方形(螺纹和不起 密封作用的含孔面除外,此时应 选整个截面),如果要用其他形 式的基准面,那么必须经开发实 验室允许并在图纸或相关标准中 加以注明(且只有圆形、三角形 和矩形可以选择)。
13
举例: VW50093- Rz0/%5/Ф3/N0
不允许粗大气孔群出现
标准号一定要写
最大单个孔隙直径小于 3mm
孔隙率小于5%
金相抛光态试样
8
8
VW50093- %10/Ф2/A3/H1
整个评判面都允许疏松出现 孔隙之间的最低距离 3X Фmin 最大单个孔隙直径小于 2mm 孔隙率小于10%
9
9
最新铸件孔隙率检验标准及方法介绍 (VW50093和PV6093)
1
1
1.金属零件孔隙率要求(VW50093)
1.1 应用范围: 适用于所有金属铸件(黑色金属及有色金属)及各种 铸造方法。如果得到相关实验室的许可,也可以应用 于非金属的注塑类零件,但此时在图纸上要添加相关 的注明。(替代2007版VW50097)
4
4
1.2.3 Ф :孔的直径, 单位mm,以0.5mm为级数进行修约,小于0.5mm不存在。
1.2.4 A : 孔隙之间的距离 (VW50097中的An) 这是一个系数,实际允许两个孔隙之间的最小距离=两个孔隙 之中较小的那个孔隙的直径 X 系数 A
1.2.5 U : 孔隙直经小于U的孔隙可以忽略不计(对应VW50097中的Pn), 仅用于加工面(如密封面),以0.1mm为级数进行修约。
H、HR、Hk 后面有两个选项 选项 0 :表示疏松是不允许的 选项 1 :表示疏松是允许的 如果图纸在允许疏松的同时也定义了单个孔隙的最大尺寸(Ф), 此时的疏松被当成一个单独的孔隙来对待,也就是说疏松的最大 尺寸不能大于Ф。
6
6
1.2.8
N、NR、NK :粗大气孔群 粗大气孔群是指当材料堆积(疏松)尺寸大于允许的 单个最大孔隙尺寸( Ф)时的那些孔隙。
N
:指整个评判面上的粗大气孔群
NR
:指整个评判面外面三分之一壁厚的区域
NK
:指整个评判面中间三分之一的区域
N、NR、Nk 后面有两个选项 选项 0 :表示粗大气孔群是不允许的 选项 1 :表示粗大气孔群是允许的 如果后面的选项没有标明,那么选项1自动适用,也 就是说粗大气孔群是允许的。
7
7
如果允许粗大气孔群出现,那么也就意味着疏松是可以接受的。反之, 如果不允许粗大气孔群出现,并不意味着不允许出现疏松,只要满足图纸 对疏松的那些要求( H、HR、Hk )即可。
13
要点: 基准面的选择应尽可能使其涵盖的面积最大
超出评判面的部分的面积最多占评判面面积的5%, 而且在二值化进行计算孔隙率时要将其剔除。
如果评判面可能含有两种不同大小的评判区域, 那么从较小区域中深入到较大区域的部分不能 超过较小区域总面积的一半。 图中A/B 要小于1。
评判面尽量选择那些承载较大应力且有断裂风险 的区域,如果测试者不能确定,需和产品设计人 员进行沟通。
旧标准VW50097孔隙率参数简介 - 孔隙度:孔隙在应力种类D、S、F、G中所占的百分比
(在应力种类F中每个基准面最大许可的气孔数) - 直径(选项):单一气孔的最大许可直径(mm)
2
2
- 附加项 An: 两个相邻孔的最小间距A=n*Ф(Ф为较小的那个气孔的直径)
M: 粗大气孔群只允许出现在零件的壁厚中心
C: 粗大气孔群只允许出现在材料的堆积(热节)部位
R: 孔隙率(D10-D30)只适用壁厚的中心三分之一区域,外部三 分之一区域的要求为D4
Pn: 最大允许气孔大小只适用壁厚的中心三分之一区域,外部三 分之一区域其气孔直径必须小于n(但在应力种类F时,表示小 于n以下的气孔可以忽略
3
3
1.2 新标准VW50093孔隙率参度,单位为μm。 如果图纸未定义具体数值,那么Rz=0μm自动适用, 也就是说要达到金相试样的表面要求(抛光态)。
1.2.2
%:
孔隙率百分比 评判面中孔隙所占的百分比。 如果要求是小于5%,那么还必须在3X4mm的子评判区域里同时 满足小于4%的要求(这和VW50097中D1-D4评判时的附加要求 是一致的),但当图纸要求铸铁和铸钢的孔隙率是小于5%时, 这个4%的附加要求可以在图纸里进行注明。 1%-4%时修约到整数,大于5%时以5%为级数进行修约,0%不 存在。
VW50093-Z4/Ф2/A2/Hk1/U0.5 Ф0.5以下的孔隙可以忽略不计
疏松在评判面中间三分之一区域是允许的 孔隙之间的最低距离 2X Фmin 最大单个孔隙直径小于 2mm 评判面上最多可以有4个孔隙
10
10
如果图纸或标准里有这个标准、在技术条件和其他标准里出现或被提及, 那么以下的通用要求对整个零件都适用。
VW50093(New) %10/Ф2 or Rz0/%10/Ф2 %10 (中间三分之一区域) %4 (外面三分之一区域) %5/Ф2(中间三分之一区域) %5/Ф1(外面三分之一区域) %5/Ф2/Nk1 Rz25/%10/Ф4 Rz15/%5 Z4 Z2/Ф2/A2/U0.5
12
12
2.气孔率的测定(PV6093)