铸件外观检查一般标准
铸件质量检查标准

一、目的:为了确保外协标准铸件、成品铸件质量符合工艺、技术要求,为了满足产品特性,结合相关文件特制定本标准。
二、适用范围:本办法适用于我公司产品外协、采购、装配过程中、全部铸件质量检查标准。
三、检查标准:3.1、铸件结构要符合设计要求或加工工艺要求。
无特殊要求时按铸件通用标准执行。
通用标准等级分为:交货验收技术条件标准;铸件质量分等通则(合格品、一等品、优等品)材质、检验方法;工艺和材料规格等一般性规则。
3.2、铸件成品检验。
铸件成品检验包括:相关技术条件的检验、表面质量检验、几何尺寸检验等项内容。
①相关技术条件的检验。
包括铸件化学成分、机械性能等检验内容。
机械性能检验和金相及化学成分检验等技术条件的检验,均必须按相关国家标准执行检验(此处略)。
②表面质量检验。
机械加工生产一线人员在工艺过程中对铸造毛坯的检查主要是对其外观铸造缺陷(如有无沙眼、沙孔、疏松、有无浇不足、铸造裂纹等)的检验;以及毛坯加工余量是否满足加工要求的检验。
表3-1铸件外观质量检验项目(GB6060.1—1985)表3-2 铸件表面粗糙度(R a 值μm)(GB6414—1986)③铸件成品几何尺寸检验。
主要一种是采用划线法检查毛坯的加工余量是否足够。
另一种方法是:用毛坯的参考基准面(也称工艺基准面)作为毛坯的检验基准面的相对测量法(需要测量相对基准面的尺寸及进行简单换算)。
表3-3 铸件尺寸公差数值(mm)(GB6414—1986)注:铸件基本尺寸≤10mm 时,其公差等级提高3 级;大于10mm 至等于15mm 时,其公差等级提高2级;大于16mm 至25mm 时,其公差等级提高1 级。
附表:铸件质量检验与缺陷处理实用技术。
压铸件外观检验标准
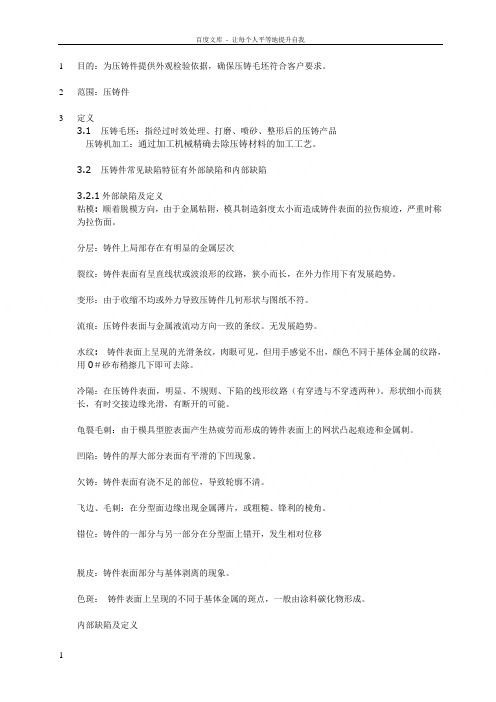
1目的:为压铸件提供外观检验依据,确保压铸毛坯符合客户要求。
2范围:压铸件3定义3.1压铸毛坯:指经过时效处理、打磨、喷砂、整形后的压铸产品压铸机加工:通过加工机械精确去除压铸材料的加工工艺。
3.2压铸件常见缺陷特征有外部缺陷和内部缺陷3.2.1外部缺陷及定义粘模: 顺着脱模方向,由于金属粘附,模具制造斜度太小而造成铸件表面的拉伤痕迹,严重时称为拉伤面。
分层:铸件上局部存在有明显的金属层次裂纹:铸件表面有呈直线状或波浪形的纹路,狭小而长,在外力作用下有发展趋势。
变形:由于收缩不均或外力导致压铸件几何形状与图纸不符。
流痕:压铸件表面与金属液流动方向一致的条纹。
无发展趋势。
水纹: 铸件表面上呈现的光滑条纹,肉眼可见,但用手感觉不出,颜色不同于基体金属的纹路,用0#砂布稍擦几下即可去除。
冷隔:在压铸件表面,明显、不规则、下陷的线形纹路(有穿透与不穿透两种)。
形状细小而狭长,有时交接边缘光滑,有断开的可能。
龟裂毛刺:由于模具型腔表面产生热疲劳而形成的铸件表面上的网状凸起痕迹和金属刺。
凹陷:铸件的厚大部分表面有平滑的下凹现象。
欠铸:铸件表面有浇不足的部位,导致轮廓不清。
飞边、毛刺:在分型面边缘出现金属薄片,或粗糙、锋利的棱角。
错位:铸件的一部分与另一部分在分型面上错开,发生相对位移脱皮:铸件表面部分与基体剥离的现象。
色斑:铸件表面上呈现的不同于基体金属的斑点,一般由涂料碳化物形成。
内部缺陷及定义砂孔:在压铸件中,由于压铸的特殊性,铝合金是在高温、高速、高压的状态下成型的,所以压铸件内部是不可避免的存在孔洞,我们统称这些孔洞为砂孔。
缩孔:铸件凝固过程中,金属补偿不足所形成的呈现暗色、形状不规则的孔洞,即为缩孔气孔:因卷入气体而导致的压铸件内部的孔状缺陷,解剖后外观检查或探伤检查,气孔具有光滑的表面、形状为圆形。
脆性:铸件基体金属晶粒过于粗大或极小,使铸件易断裂或破碎渗漏:压铸件经耐压试验,产生漏气、渗水硬点:机械加工过程或加工后外观检查或金相检查:铸件上有硬度高于金属基体的细小质点或块状物使刀具磨损严重,加工后常常显示出不同的亮度。
压铸件外观通用检验标准(带图实例)
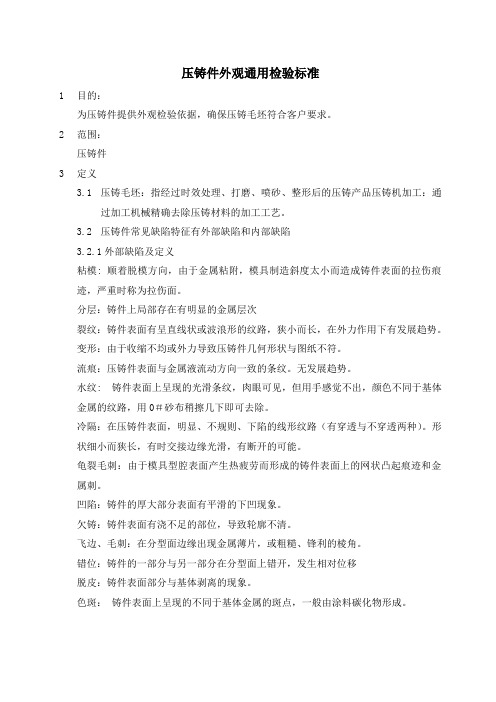
压铸件外观通用检验标准
1目的:
为压铸件提供外观检验依据,确保压铸毛坯符合客户要求。
2范围:
压铸件
3定义
3.1压铸毛坯:指经过时效处理、打磨、喷砂、整形后的压铸产品压铸机加工:通
过加工机械精确去除压铸材料的加工工艺。
3.2压铸件常见缺陷特征有外部缺陷和内部缺陷
3.2.1外部缺陷及定义
粘模: 顺着脱模方向,由于金属粘附,模具制造斜度太小而造成铸件表面的拉伤痕迹,严重时称为拉伤面。
分层:铸件上局部存在有明显的金属层次
裂纹:铸件表面有呈直线状或波浪形的纹路,狭小而长,在外力作用下有发展趋势。
变形:由于收缩不均或外力导致压铸件几何形状与图纸不符。
流痕:压铸件表面与金属液流动方向一致的条纹。
无发展趋势。
水纹: 铸件表面上呈现的光滑条纹,肉眼可见,但用手感觉不出,颜色不同于基体金属的纹路,用0#砂布稍擦几下即可去除。
冷隔:在压铸件表面,明显、不规则、下陷的线形纹路(有穿透与不穿透两种)。
形状细小而狭长,有时交接边缘光滑,有断开的可能。
龟裂毛刺:由于模具型腔表面产生热疲劳而形成的铸件表面上的网状凸起痕迹和金属刺。
凹陷:铸件的厚大部分表面有平滑的下凹现象。
欠铸:铸件表面有浇不足的部位,导致轮廓不清。
飞边、毛刺:在分型面边缘出现金属薄片,或粗糙、锋利的棱角。
错位:铸件的一部分与另一部分在分型面上错开,发生相对位移
脱皮:铸件表面部分与基体剥离的现象。
色斑:铸件表面上呈现的不同于基体金属的斑点,一般由涂料碳化物形成。
压铸件外观检验标准
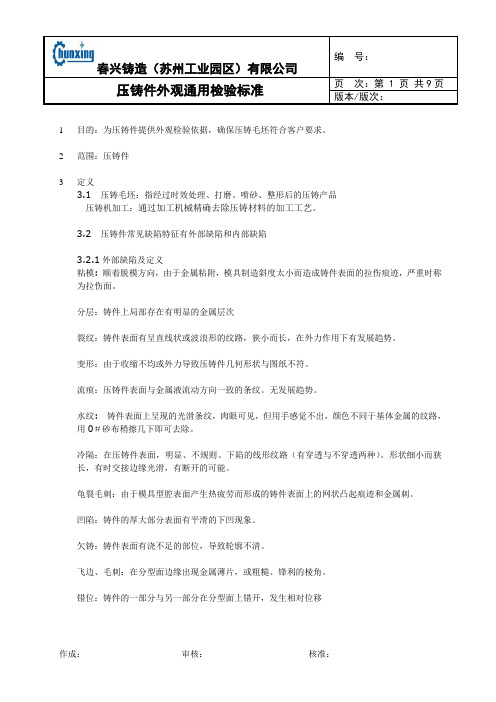
压铸件外观通用检验标准页次:第 1 页共9页版本/版次:1目的:为压铸件提供外观检验依据,确保压铸毛坯符合客户要求。
2范围:压铸件3定义3.1压铸毛坯:指经过时效处理、打磨、喷砂、整形后的压铸产品压铸机加工:通过加工机械精确去除压铸材料的加工工艺。
3.2压铸件常见缺陷特征有外部缺陷和内部缺陷3.2.1外部缺陷及定义粘模: 顺着脱模方向,由于金属粘附,模具制造斜度太小而造成铸件表面的拉伤痕迹,严重时称为拉伤面。
分层:铸件上局部存在有明显的金属层次裂纹:铸件表面有呈直线状或波浪形的纹路,狭小而长,在外力作用下有发展趋势。
变形:由于收缩不均或外力导致压铸件几何形状与图纸不符。
流痕:压铸件表面与金属液流动方向一致的条纹。
无发展趋势。
水纹: 铸件表面上呈现的光滑条纹,肉眼可见,但用手感觉不出,颜色不同于基体金属的纹路,用0#砂布稍擦几下即可去除。
冷隔:在压铸件表面,明显、不规则、下陷的线形纹路(有穿透与不穿透两种)。
形状细小而狭长,有时交接边缘光滑,有断开的可能。
龟裂毛刺:由于模具型腔表面产生热疲劳而形成的铸件表面上的网状凸起痕迹和金属刺。
凹陷:铸件的厚大部分表面有平滑的下凹现象。
欠铸:铸件表面有浇不足的部位,导致轮廓不清。
飞边、毛刺:在分型面边缘出现金属薄片,或粗糙、锋利的棱角。
错位:铸件的一部分与另一部分在分型面上错开,发生相对位移压铸件外观通用检验标准页次:第 2 页共9页版本/版次:脱皮:铸件表面部分与基体剥离的现象。
色斑:铸件表面上呈现的不同于基体金属的斑点,一般由涂料碳化物形成。
32.2内部缺陷及定义砂孔:在压铸件中,由于压铸的特殊性,铝合金是在高温、高速、高压的状态下成型的,所以压铸件内部是不可避免的存在孔洞,我们统称这些孔洞为砂孔。
缩孔:铸件凝固过程中,金属补偿不足所形成的呈现暗色、形状不规则的孔洞,即为缩孔气孔:因卷入气体而导致的压铸件内部的孔状缺陷,解剖后外观检查或探伤检查,气孔具有光滑的表面、形状为圆形。
铸件表面质量验收标准

铸铁件验收项目及标准铸件的表面质量主要包括铸件的表面缺陷、尺寸精度、形状偏差、表面粗糙度、表面清理质量等;1、铸件表面缺陷的检验1.1表面缺陷检验的一般要求1.1.1 铸件非加工表面上的浇冒口必须清理得与铸件表面同样平整,加工面上的浇冒口残留量应符合技术要求,若无要求,则按表8执行;1.1.2 在铸件上不允许有裂纹、通孔、穿透性的冷隔和穿透性的缩松、夹渣等机械加工不能去除的缺陷;1.1.3 铸件非加工表面的毛刺、披缝、型砂、砂芯等应清理干净;1.1.4 铸件一般待加工表面,允许有不超过加工余量范围内的任何缺陷存在;重要加工面允许有不超过加工余量2/3的缺陷存在,但裂纹缺陷应予清除;加工后的表面允许存在直径*长度*深度小于等于2*2*2的非连片孔洞的铸造缺陷;1.1.5 作为加工基准面(孔)和测量基准的铸件表面,平整度小于等于2.0毫米、粗糙度Ra50以内;1.1.6 铸件表面气孔、砂眼、夹渣面积不大,但比较分散或者有连片麻点的表面不予接收;1.1.7 除技术要求特别注明的铸件外,对于表面有气孔、缩孔、砂眼等缺陷的铸钢件允许补焊,但铸铁件未经允许不得焊补(铸铁件实行一案一判的原则)但补焊面积不允许超过铸件面积的10%,焊接质量应符合JB/T 5000.7-2007标准要求,补焊后必须退火、机械性能达到图纸要求,且不得有渗漏及影响外观的缺陷;1.2铸件外观质量等级表1 铸件外观质量等级2、铸件尺寸的检验2.1铸件毛坯尺寸公差铸件尺寸公差应按毛坯图或技术条件规定的尺寸公差等级执行,当技术文件未规定尺寸公差时,则应以GB6414-1999为依据,并按照表2选定公差值(粗线框内为推荐使用公差等级);(单位:mm)表2铸件尺寸公差2.2铸件分型面处最大错型值应不得超过表2所示公差值,当需进一步限制错型量时,应从表3中选取;表3 错型值(GB6414-1999)2.3铸件加工余量应符合表4的规定,有特殊要求的表面应在技术要求中单独标注加工余量;表4 加工余量(单位:mm)3、表面粗糙度检测表面粗糙度总体检测原则依据图纸要求,当图纸无要求是执行国标GB/T15056-1994;3.1一般情况下,表面粗糙度要求 Ra50,铸件难以清理的部位,局部允许Ra100,待加工表面允许降低1级;3.2.使用面积法作为验收依据面积法常用的比较样块评定铸件表面粗糙度;方法如下:3.2.1 铸造表面粗糙度比较样块应符合GB6060.1-1997标准;3.2.2 按照国标BWZ001-88评定铸件表面粗糙度的等级;3.2.3 铸件的浇道、冒口、修补的残余表面及铸造表面缺陷(如粘砂、结疤等)不列为被检表面;3.2.4 以铸造表面粗糙度比较样块为对照标准,对被检铸件的铸造表面用视觉或触觉的方法进行对比;3.2.5 用样块对比时,应选用适于铸造合金材料和工艺方法的样块进行对比;3.2.6 被检的铸造表面必须清理干净,样块表面和被检表面均不得有锈蚀处;3.2.7 用样块对比时,砂型铸造表面被检点数应符合表7的规定;特种铸造表面被检点数应按表8的规定加倍;被检点应平均分布,每点的被检面积不得小于与之对比面的面积;表7 被检铸造表面最低检测数3.2.8 当被检铸造表面的粗糙度介于比较样块两级参数值之间者,所确定的被检铸造表面的粗糙度等级为粗的一级;3.2.9 对被检铸造表面,以其80%的表面所达到的最粗表面粗糙度等级,为该铸造表面粗糙度等级;3.3铸件表面清理检测3.3.1 铸件几何形状必须完整,非加工面上的清理损伤不应大于该处的尺寸偏差,加工面上的损伤不应大于该处加工余量的1/2;3.3.2允许铸件表面有少量的局部低凹或打磨痕迹,在直径不大于 8mm,并能保证铸件规定的最小的壁厚;3.3.3为去除铸造缺陷而打磨后的铸件表面粗糙度应与一般铸件表面粗糙度基本一致;3.3.4除特殊情况外,铸件表面允许残留的浇冒口、毛刺,多肉残余量应按表8的要求进行;表8 浇冒口、毛刺、多肉等允许残留量值3.3.5铸件表面须经过防锈处理,保证在铸件进入面加工时不得有任何的锈蚀;3.3.6铸件表面如有油漆要求的,必须按有关涂装规定执行;4、铸件重量检测对于没有特殊要求的铸件,重量偏差可以不作为验收依据;如果技术条件有要求,供需双方协商后,铸件的重量偏差也应作为验收依据,一般应符合表6的规定;表6 铸件重量偏差。
01-铸件外观质量检验标准
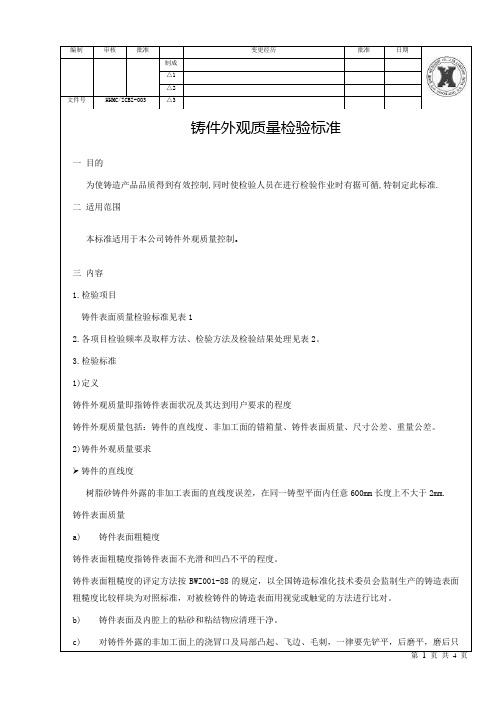
编制审核批准变更经历批准日期
制成
△1
△2
文件号HHMC/ZCBZ-003 △3
铸件外观质量检验标准
一目的
为使铸造产品品质得到有效控制,同时使检验人员在进行检验作业时有据可循,特制定此标准.
二适用范围
本标准适用于本公司铸件外观质量控制.
三内容
1.检验项目
铸件表面质量检验标准见表1
2.各项目检验频率及取样方法、检验方法及检验结果处理见表2。
3.检验标准
1)定义
铸件外观质量即指铸件表面状况及其达到用户要求的程度
铸件外观质量包括:铸件的直线度、非加工面的错箱量、铸件表面质量、尺寸公差、重量公差。
2)铸件外观质量要求
➢铸件的直线度
树脂砂铸件外露的非加工表面的直线度误差,在同一铸型平面内任意600mm长度上不大于2mm. 铸件表面质量
a)铸件表面粗糙度
铸件表面粗糙度指铸件表面不光滑和凹凸不平的程度。
铸件表面粗糙度的评定方法按BWZ001-88的规定,以全国铸造标准化技术委员会监制生产的铸造表面粗糙度比较样块为对照标准,对被检铸件的铸造表面用视觉或触觉的方法进行比对。
b)铸件表面及内腔上的粘砂和粘结物应清理干净。
c)对铸件外露的非加工面上的浇冒口及局部凸起、飞边、毛刺,一律要先铲平,后磨平,磨后只。
铸件外观标准附示意图
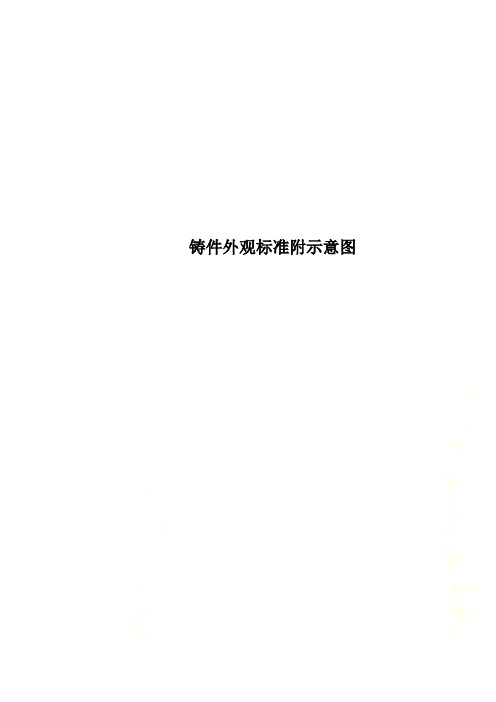
铸件外观标准附示意图铝、锌合金铸件外观检查标准1.范围及基本责任1.1 应用于对铸件产品外观检查。
1.2 质量部负责人和生产部负责人负责推行及维持。
2.外观表面质量的定级2.1 质量的定级按使用范围分为三级,见下表:表面质量使用范围备注相应使用之AQL水平1 级喷涂工艺要求高的表面;需镀铬.抛光.研磨的表面;相对运动的配合面;危险应力区的表面一般相当于(▽6)⊕Ⅱ1.0% (个别0.65%)2 级喷涂要求一般或要求密一般相当于(▽5)ΘⅡ2.5%封的表面;需镀锌.阳极氧化的表面;喷涂前不补涂的表面;装配接触面;3 级具保护性(例如防锈)的喷涂表面;紧固接触面;喷涂前可允许补涂的表面;其它要求低的表面;一般相当于(▽4)ΟⅡ4.0%3.压铸件外观检查项目3.1 成型不良a)项目代号:A1b)定义:成型过程中填充不完整的部位这是因为以下原因所造成的:-----料不足-----料温低-----模温低-----压力不足,压入速度太慢c)检查:目视d)要求:1级和2级:不允许3级:如不影响装配及使用则允许3.2 冷格a)项目代号:A2b)定义:温度较低的金属流互相对接但未熔合而出现的缝隙,呈不规则的线形,有穿透.不穿透的两种,在外力作用下有发展的趋势。
c)检查:目视d)要求:1级:不允许2级:在每一个表面允许2处,其长度不大于铸件最大轮廓尺寸的1/10,深度不大于壁厚的1/5,离铸件边缘距离不小于4mm,并且两冷格间距不小于10mm。
3级:在每一个表面允许2处,其长度不大于铸件最大轮廓尺寸的1/5,深度不大于壁厚的1/4,离铸件边缘距离不小于4mm,并且两冷格间距不小于10mm。
3.3 流纹a)项目代号:A3b)定义:表面上用手感觉得出的局部下陷的纹路。
此缺陷无发展的可能,用抛光法能去除。
c)检查:目视d)要求:1级:允许流纹面积不超过总面积的5%,其深度不大于0.05mm。
2级:允许流纹面积不超过总面积的15%,其深度不大于0.07mm。
铸件表面质量验收标准

铸铁件验收项目及标准铸件的表面质量主要包括铸件的表面缺陷、尺寸精度、形状偏差、表面粗糙度、表面清理质量等;1、铸件表面缺陷的检验1.1表面缺陷检验的一般要求1.1.1铸件非加工表面上的浇冒口必须清理得与铸件表面同样平整,加工面上的浇冒口残留量应符合技术要求,若无要求,则按表8执行;1.1.2在铸件上不允许有裂纹、通孔、穿透性的冷隔和穿透性的缩松、夹渣等机械加工不能去除的缺陷;1.1.3铸件非加工表面的毛刺、披缝、型砂、砂芯等应清理干净;1.1.4铸件一般待加工表面,允许有不超过加工余量范围内的任何缺陷存在;重要加工面允许有不超过加工余量2/3的缺陷存在,但裂纹缺陷应予清除;加工后的表面允许存在直径*长度*深度小于等于2*2*2的非连片孔洞的铸造缺陷;1.1.5作为加工基准面(孔)和测量基准的铸件表面,平整度小于等于2.0 毫米、粗糙度Ra50以内;1.1.6铸件表面气孔、砂眼、夹渣面积不大,但比较分散或者有连片麻点的表面不予接收;1.1.7除技术要求特别注明的铸件外,对于表面有气孔、缩孔、砂眼等缺陷的铸钢件允许补焊,但铸铁件未经允许不得焊补(铸铁件实行一案一判的原则)但补焊面积不允许超过铸件面积的10%,焊接质量应符合JB/T 5000.7-2007标准要求,补焊后必须退火、机械性能达到图纸要求,且不得有渗漏及影响外观的缺陷;1.2铸件外观质量等级表1 铸件外观质量等级1、一般零部件采用B级精度,在检查过程中,如有一个或多个项目超出B级精度要求的零部件均判定为不合格;2、影响到零部件安全、性能的部位,外观质量采用A级精度,如果有一个或多个项目超出规定级精度要求的零部件均判定为不合格;2、铸件尺寸的检验2.1铸件毛坯尺寸公差铸件尺寸公差应按毛坯图或技术条件规定的尺寸公差等级执行,当技术文件未规定尺寸公差时,则应以GB6414-1999为依据,并按照表2选定公差值(粗线框内为推荐使用公差等级);表2铸件尺寸公差(单位:mm)2.2铸件分型面处最大错型值应不得超过表2所示公差值,当需进一步限制错型量时,应从表3中选取;表 3 错型值(GB6414-1999)2.3铸件加工余量应符合表4的规定,有特殊要求的表面应在技术要求中单独标注加工余量;表4加工余量(单位:mm)3、表面粗糙度检测表面粗糙度总体检测原则依据图纸要求,当图纸无要求是执行国标GB/T15056-1994;3.1一般情况下,表面粗糙度要求Ra50,铸件难以清理的部位,局部允许 Ra100,待加工表面允许降低1级;3.2.使用面积法作为验收依据面积法常用的比较样块评定铸件表面粗糙度;方法如下:3.2.1铸造表面粗糙度比较样块应符合GB6060.1-1997标准;3.2.2按照国标BWZ001-88评定铸件表面粗糙度的等级;3.2.3铸件的浇道、冒口、修补的残余表面及铸造表面缺陷(如粘砂、结疤等)不列为被检表面;3.2.4以铸造表面粗糙度比较样块为对照标准,对被检铸件的铸造表面用视觉或触觉的方法进行对比;3.2.5用样块对比时,应选用适于铸造合金材料和工艺方法的样块进行对比;3.2.6被检的铸造表面必须清理干净,样块表面和被检表面均不得有锈蚀处;3.2.7用样块对比时,砂型铸造表面被检点数应符合表7的规定;特种铸造表面被检点数应按表8的规定加倍;被检点应平均分布,每点的被检面积不得小于与之对比面的面积;表7 被检铸造表面最低检测数3.2.8当被检铸造表面的粗糙度介于比较样块两级参数值之间者,所确定的被检铸造表面的粗糙度等级为粗的一级;3.2.9对被检铸造表面,以其80%的表面所达到的最粗表面粗糙度等级,为该铸造表面粗糙度等级;3.3铸件表面清理检测3.3.1铸件几何形状必须完整,非加工面上的清理损伤不应大于该处的尺寸偏差,加工面上的损伤不应大于该处加工余量的1/2;3.3.2允许铸件表面有少量的局部低凹或打磨痕迹,在直径不大于8mm,并能保证铸件规定的最小的壁厚;3.3.3为去除铸造缺陷而打磨后的铸件表面粗糙度应与一般铸件表面粗糙度基本一致;3.3.4除特殊情况外,铸件表面允许残留的浇冒口、毛刺,多肉残余量应按表 8的要求进行;表8 浇冒口、毛刺、多肉等允许残留量值3.3.5铸件表面须经过防锈处理,保证在铸件进入面加工时不得有任何的锈蚀;3.3.6铸件表面如有油漆要求的,必须按有关涂装规定执行;4、铸件重量检测对于没有特殊要求的铸件,重量偏差可以不作为验收依据;如果技术条件有要求,供需双方协商后,铸件的重量偏差也应作为验收依据,一般应符合表6的规定;表6铸件重量偏差。
- 1、下载文档前请自行甄别文档内容的完整性,平台不提供额外的编辑、内容补充、找答案等附加服务。
- 2、"仅部分预览"的文档,不可在线预览部分如存在完整性等问题,可反馈申请退款(可完整预览的文档不适用该条件!)。
- 3、如文档侵犯您的权益,请联系客服反馈,我们会尽快为您处理(人工客服工作时间:9:00-18:30)。
一.适用范围:
1.灰铸铁和球墨铸铁件;
2.客户有专门要求的以客户要求为准。
二.细 则:
1.表面粗糙度:
(1)表面粗糙度的凸凹高度差:壁厚10mm 以下要小于0.3mm;
壁厚10mm以上要小于0.5mm。
局部超标可以打磨,打磨后再抛丸。
(2)表面粗糙度越细越好,但里面和外面,平面和垂直面要均匀。
可选用典型产品作为比照样板。
2.错箱和涨箱:
(1)铸件分型面最大尺寸100mm以内,错箱要小于1mm;100至
600mm错箱要小于2mm;600mm以上错箱要小于3.5mm。
(2)如果产品在本厂加工,而且错箱超差能够通过加工修正的,可以通过加工重新修正,但这些产品要分开管理。
(3)非加工面的涨箱,如果能够通过打磨或简单加工去除的,可以修理,但修理后要再抛丸。
(4)加工面出现的涨箱(指在本厂加工的加工面),只要能够去除并不影响其它尺寸,可以算合格毛坯。
3.飞边毛刺:
飞边毛刺打磨残留量在0.5mm以下即可。
4.变形、翘曲:
底座、盖板类的变形挠度允许量:自由状态放置在平台上,其最大变形量要保证在总长度的0.5%以下,比如600mm长可以3mm以下。
作成第 1 页/共 2 页
批准
5.气孔、渣眼、砂眼类:
(1)加工面不允许有此类缺陷。
在本厂加工的产品,加工面孔眼不超过加工量,可以通过加工去除。
(2)非加工面的孔眼可以修补(铁基修补胶)、焊补,但必须符合以下范围:深度小于该部壁厚的三分之一、长或宽小于该部壁厚;
数量5处以下。
需要电镀、热镀、粉体涂漆、电泳涂漆的不在此列。
6.表面皱纹:
皱纹深度小于0.5mm,长度小于四倍壁厚,可以通过打磨方法处理。
7.冷隔、浇不足:
冷隔(汤境)浇不足为废品,不能修补。
8.多肉:
掉砂多肉通过铲磨不能恢复原形状的为废品。
9.缺肉:
掉砂碰伤浇口根部缺肉,参考孔眼类的修补范围。
10.打磨修补:
(1)打磨后残留量保证在0.5mm以下,不允许过度打磨。
(2)局部打磨过度的限度:深1mm长度不超过该部壁厚。
(3)修补剂颜色要与铸件接近,不能形成成片的修补面。
(4)修补剂未硬化产品不可涂漆和包装。
三.说 明:
本标准为通用标准,具体产品如按上述标准不能保证尺寸、加工和涂装要求的,则以图纸或客户要求为准。
修订说明:
2017.8.20制订。
2018.2.19第一次修订。
作成第 1 页/共 2 页
批准。