锅炉脱硫方法总结
锅炉烟气脱硫技术方案及案例分析

锅炉烟气脱硫技术方案及案例分析随着环保意识的不断提高,锅炉烟气脱硫技术成为了重点关注的领域。
本文将介绍基于不同生产需求的锅炉烟气脱硫技术方案及其案例分析,以期帮助企业在选择和使用脱硫技术方案时有所依据。
一、海藻酸锌膜法生产需求:对流量小、效果好、成本低的脱硫技术有需求。
海藻酸锌膜法是一种通过将锌离子与海藻酸分子结合形成膜,在烟气中吸收二氧化硫的技术。
该技术具有处理流量小、效果好、成本低的优点。
案例分析:某热电厂以该技术制定了脱硫技术方案,采用了海藻酸锌膜法,将海藻酸、锌离子、钙离子等添加到烟气中,形成对二氧化硫具有吸收能力的膜。
该技术不仅处理效果好,还大大降低了脱硫成本。
二、喷射吸收脱硫技术生产需求:对处理高浓度二氧化硫的需求。
喷射吸收脱硫技术是一种通过将喷嘴喷出的乳化液喷入烟气中,将其中的二氧化硫与乳化液中的氧化剂反应而被吸收的技术。
案例分析:某钢铁生产企业在使用锅炉时发现,烟气中二氧化硫浓度较高,无法满足环保要求。
经过对多种脱硫技术的比较,企业选择了喷射吸收脱硫技术,并设计了相应的脱硫方案。
采用该技术后,企业二氧化硫排放浓度降低了90%以上,达到了严格的环保要求。
三、氨水脱硫技术生产需求:对处理大气浓度二氧化硫浓度较低的需求。
氨水脱硫技术是一种通过将氨水与烟气中的二氧化硫反应而使其减少的技术。
该技术相对比较成熟,处理二氧化硫效果显著,也相对容易实现。
案例分析:某燃煤发电企业选择了氨水脱硫技术,并制定了脱硫方案。
在实施过程中,企业对脱硫反应的控制和稳定性进行了优化,确保了脱硫效果的稳定、可靠,并满足了国家环保要求。
结语:本文介绍了针对不同生产需求的三种锅炉烟气脱硫技术方案及其案例分析。
对于企业在选择和使用锅炉烟气脱硫技术方案时,应根据企业自身生产情况和环保要求进行选择和合理规划,以达到最佳效果。
锅炉脱硫方案

锅炉脱硫方案锅炉脱硫方案引言燃煤锅炉是我国主要的能源供应来源之一,但燃煤带来了严重的环境污染问题,其中包括大量的二氧化硫(SO2)排放。
二氧化硫是导致酸雨形成的主要原因之一,对环境和人体健康带来严重的危害。
为了减少锅炉排放的二氧化硫,采取脱硫技术是必要的。
本文将介绍常见的锅炉脱硫方案,包括石灰石石膏法脱硫、石灰石浆液喷射法脱硫以及干法脱硫等。
石灰石石膏法脱硫原理石灰石石膏法脱硫是一种常见的湿法脱硫技术,其基本原理是利用石灰石和石膏来吸收和固定燃煤烟气中的二氧化硫。
具体过程如下:1. 烟气经过烟囱进入石灰石石膏法脱硫设备;2. 在脱硫设备中,喷射适量的石灰石浆液到烟气中;3. 石灰石浆液与烟气中的二氧化硫发生反应,生成硫化钙(CaSO3);4. 硫化钙进一步氧化生成石膏(CaSO4·2H2O)并固定在脱硫设备中。
优点石灰石石膏法脱硫具有以下优点:- 技术成熟,应用广泛;- 脱硫效率高,可以将燃煤烟气中的二氧化硫去除率达到90%以上;- 石灰石和石膏是常见的资源,易于获取。
缺点石灰石石膏法脱硫也存在一些缺点:- 流程复杂,设备占地面积大;- 需要消耗大量的石灰石和石膏,增加运营成本;- 产生大量的废水和废渣,对环境造成一定影响。
石灰石浆液喷射法脱硫原理石灰石浆液喷射法脱硫是一种湿法脱硫技术的改进版,相比石灰石石膏法脱硫,其优化了吸收剂的使用方式,减少了浪费。
具体过程如下:1. 烟气进入脱硫设备,经过初级脱硫器和吸收塔;2. 在吸收塔中,通过喷射石灰石浆液,与烟气中的二氧化硫发生反应,生成硫酸钙(CaSO4);3. 吸收塔内的石灰石浆液与烟气充分接触,并与二氧化硫反应,最终生成硫酸钙;4. 石灰石浆液中的硫酸钙可定期取出,经过干燥处理后可用作建材等其他领域。
优点石灰石浆液喷射法脱硫相较于石灰石石膏法脱硫具有以下优点:- 优化了吸收剂的使用方式,减少了资源浪费;- 减少了废水和废渣的产生,对环境影响较小;- 硫酸钙可用作其他领域的原料,提高了资源综合利用。
脱硫的常见方式
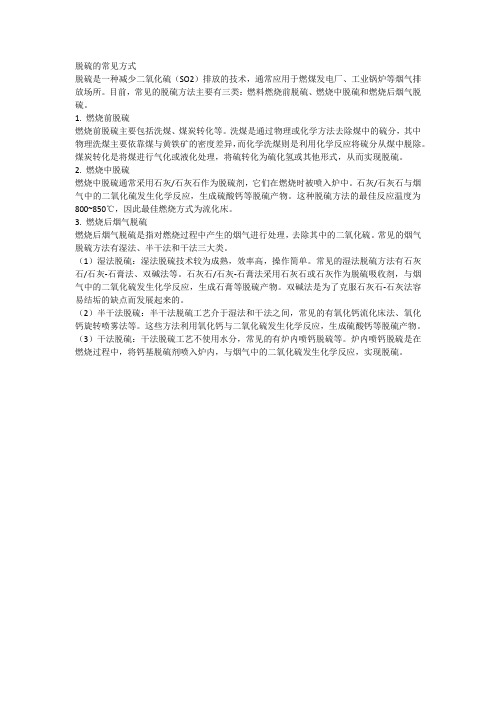
脱硫的常见方式脱硫是一种减少二氧化硫(SO2)排放的技术,通常应用于燃煤发电厂、工业锅炉等烟气排放场所。
目前,常见的脱硫方法主要有三类:燃料燃烧前脱硫、燃烧中脱硫和燃烧后烟气脱硫。
1. 燃烧前脱硫燃烧前脱硫主要包括洗煤、煤炭转化等。
洗煤是通过物理或化学方法去除煤中的硫分,其中物理洗煤主要依靠煤与黄铁矿的密度差异,而化学洗煤则是利用化学反应将硫分从煤中脱除。
煤炭转化是将煤进行气化或液化处理,将硫转化为硫化氢或其他形式,从而实现脱硫。
2. 燃烧中脱硫燃烧中脱硫通常采用石灰/石灰石作为脱硫剂,它们在燃烧时被喷入炉中。
石灰/石灰石与烟气中的二氧化硫发生化学反应,生成硫酸钙等脱硫产物。
这种脱硫方法的最佳反应温度为800~850℃,因此最佳燃烧方式为流化床。
3. 燃烧后烟气脱硫燃烧后烟气脱硫是指对燃烧过程中产生的烟气进行处理,去除其中的二氧化硫。
常见的烟气脱硫方法有湿法、半干法和干法三大类。
(1)湿法脱硫:湿法脱硫技术较为成熟,效率高,操作简单。
常见的湿法脱硫方法有石灰石/石灰-石膏法、双碱法等。
石灰石/石灰-石膏法采用石灰石或石灰作为脱硫吸收剂,与烟气中的二氧化硫发生化学反应,生成石膏等脱硫产物。
双碱法是为了克服石灰石-石灰法容易结垢的缺点而发展起来的。
(2)半干法脱硫:半干法脱硫工艺介于湿法和干法之间,常见的有氧化钙流化床法、氧化钙旋转喷雾法等。
这些方法利用氧化钙与二氧化硫发生化学反应,生成硫酸钙等脱硫产物。
(3)干法脱硫:干法脱硫工艺不使用水分,常见的有炉内喷钙脱硫等。
炉内喷钙脱硫是在燃烧过程中,将钙基脱硫剂喷入炉内,与烟气中的二氧化硫发生化学反应,实现脱硫。
锅炉脱硫脱销方案
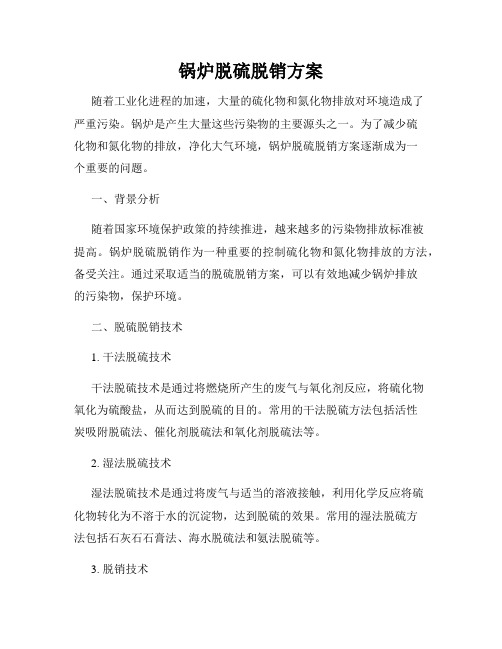
锅炉脱硫脱销方案随着工业化进程的加速,大量的硫化物和氮化物排放对环境造成了严重污染。
锅炉是产生大量这些污染物的主要源头之一。
为了减少硫化物和氮化物的排放,净化大气环境,锅炉脱硫脱销方案逐渐成为一个重要的问题。
一、背景分析随着国家环境保护政策的持续推进,越来越多的污染物排放标准被提高。
锅炉脱硫脱销作为一种重要的控制硫化物和氮化物排放的方法,备受关注。
通过采取适当的脱硫脱销方案,可以有效地减少锅炉排放的污染物,保护环境。
二、脱硫脱销技术1. 干法脱硫技术干法脱硫技术是通过将燃烧所产生的废气与氧化剂反应,将硫化物氧化为硫酸盐,从而达到脱硫的目的。
常用的干法脱硫方法包括活性炭吸附脱硫法、催化剂脱硫法和氧化剂脱硫法等。
2. 湿法脱硫技术湿法脱硫技术是通过将废气与适当的溶液接触,利用化学反应将硫化物转化为不溶于水的沉淀物,达到脱硫的效果。
常用的湿法脱硫方法包括石灰石石膏法、海水脱硫法和氨法脱硫等。
3. 脱销技术脱销是将烟气中的氮氧化物转化为氮和水,从而实现氮化物的净化过程。
常用的脱销技术包括选择性催化还原法、吸附法和非选择性催化还原法等。
三、应用方案根据具体情况,针对锅炉脱硫脱销,制定了以下方案:1. 采用干法脱硫技术由于实施湿法脱硫技术需要大量的水资源和处理设备,成本较高,可选择干法脱硫技术。
根据燃料的种类和硫化物的浓度,选择适当的干法脱硫方法,如活性炭吸附或氧化剂脱硫。
在设计脱硫系统时,应充分考虑投资、运维成本和设备的可靠性。
2. 结合湿法脱硫技术湿法脱硫技术能够更彻底地减少硫化物的排放,但也面临着水资源的限制和设备的高成本。
可以结合湿法脱硫技术的优势,将它应用于硫化物浓度较高的区域,以获得更好的脱硫效果。
3. 采用脱销技术对于氮化物的净化,可以考虑使用脱销技术。
选择合适的脱销催化剂和操作条件,能够有效地将氮氧化物转化为无害的氮和水。
四、实施步骤1. 调研分析在制定脱硫脱销方案前,应充分了解锅炉的情况,包括燃料种类、硫化物和氮化物排放浓度等。
锅炉脱硫原理
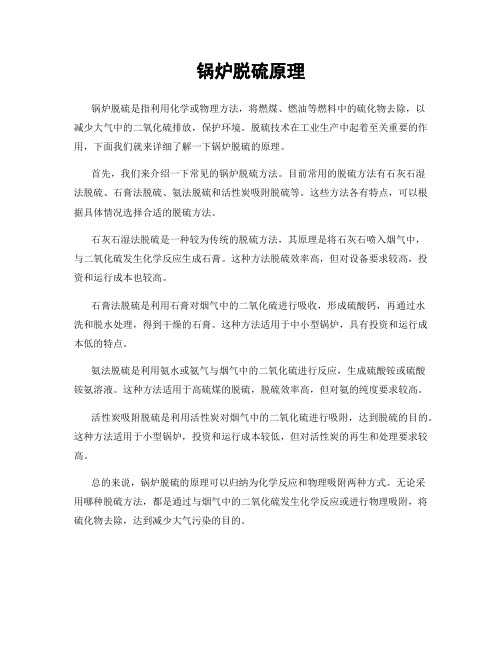
锅炉脱硫原理锅炉脱硫是指利用化学或物理方法,将燃煤、燃油等燃料中的硫化物去除,以减少大气中的二氧化硫排放,保护环境。
脱硫技术在工业生产中起着至关重要的作用,下面我们就来详细了解一下锅炉脱硫的原理。
首先,我们来介绍一下常见的锅炉脱硫方法。
目前常用的脱硫方法有石灰石湿法脱硫、石膏法脱硫、氨法脱硫和活性炭吸附脱硫等。
这些方法各有特点,可以根据具体情况选择合适的脱硫方法。
石灰石湿法脱硫是一种较为传统的脱硫方法,其原理是将石灰石喷入烟气中,与二氧化硫发生化学反应生成石膏。
这种方法脱硫效率高,但对设备要求较高,投资和运行成本也较高。
石膏法脱硫是利用石膏对烟气中的二氧化硫进行吸收,形成硫酸钙,再通过水洗和脱水处理,得到干燥的石膏。
这种方法适用于中小型锅炉,具有投资和运行成本低的特点。
氨法脱硫是利用氨水或氨气与烟气中的二氧化硫进行反应,生成硫酸铵或硫酸铵氨溶液。
这种方法适用于高硫煤的脱硫,脱硫效率高,但对氨的纯度要求较高。
活性炭吸附脱硫是利用活性炭对烟气中的二氧化硫进行吸附,达到脱硫的目的。
这种方法适用于小型锅炉,投资和运行成本较低,但对活性炭的再生和处理要求较高。
总的来说,锅炉脱硫的原理可以归纳为化学反应和物理吸附两种方式。
无论采用哪种脱硫方法,都是通过与烟气中的二氧化硫发生化学反应或进行物理吸附,将硫化物去除,达到减少大气污染的目的。
除了选择合适的脱硫方法外,还需要注意脱硫设备的运行参数和操作控制。
脱硫设备的运行参数包括烟气温度、湿度、氧含量等,需要根据不同的脱硫方法进行调节。
操作控制方面,需要对脱硫设备进行定期检查和维护,确保设备的正常运行。
在实际应用中,锅炉脱硫技术需要根据工业生产的具体情况进行选择和优化,以达到经济、环保和可持续发展的目标。
随着环保意识的提高和技术的进步,相信锅炉脱硫技术会在未来得到更广泛的应用和发展。
综上所述,锅炉脱硫是通过化学反应和物理吸附的方式,将燃料中的硫化物去除,以减少大气中的二氧化硫排放。
燃煤锅炉烟气脱硫工程总结

结晶池 , 经过塔底分布系统将亚硫酸铵氧化为硫
酸铵 。
( ) 收剂 ( 4吸 氨水 ) 给 系统 。本 装置 可使 用 供
质量分 数 5 ~2 % 氨 水 , 水 由氨 水 泵 定 量 加 % 0 氨 入到脱 硫塔 底循 环 浆 液 中 , 补充 脱 硫 系统 所 消 以 耗 的吸收剂 。氨 水 加 入量 根 据 循 环脱 硫 液 的 p H 和净烟 气 中的 S 量控 制 。 O含 () 5 工艺 水系 统 。工 艺 水 主要 用 于 冲 洗脱 硫 塔除雾 器 、 管道及 机泵 的机 封 。 ( ) 酸铵后 处理 系统 。将 脱 硫 系 统 的硫 酸 6硫
塔 内顶 端 的除沫器 , 除去夹 带 的液 体 , 烟气 通过 净 吸收塔 塔顶 直 排 大气 。烟气 中 9 % ( 积 分数 ) 9 体
的 S 被脱 除 , 它 酸 性 气 体 ( H I H ) O 其 如 C 和 F 和
部分 N 脱硫塔 内同 时被 脱 除 , O在 净烟 气 温度 降 至5 0℃左 右 。锅 炉 的烟气设 置旁 路挡板 门 , 硫 脱
() 3 氧化 空气 系统 。采 用 空 气压 缩 机 将 满足 压力 和温度 要求 的压缩 空气 送 至脱硫 塔下部 氧化
硫 中间产 品亚硫 酸 铵 或亚 硫 酸 氢 铵 的水 溶 液 ; 在 脱 硫塔 的氧化 段鼓 人压 缩空 气进行 亚硫 酸铵 的氧 化 反应 , 将亚 硫酸 铵直接 氧化 成硫 酸铵溶 液 。
化 风机送 人 的空 气进 行 强 制 氧 化 , 亚 硫 酸 盐 氧 将 化成 硫 酸盐 ; 氧化 后 的 吸 收液 经 泵送 入 脱 硫 塔浓 缩段 进行 浓 缩 结 晶 , 成 质 量 分 数 为 5 一1% 形 % 0
10t锅炉脱硫脱硝方案
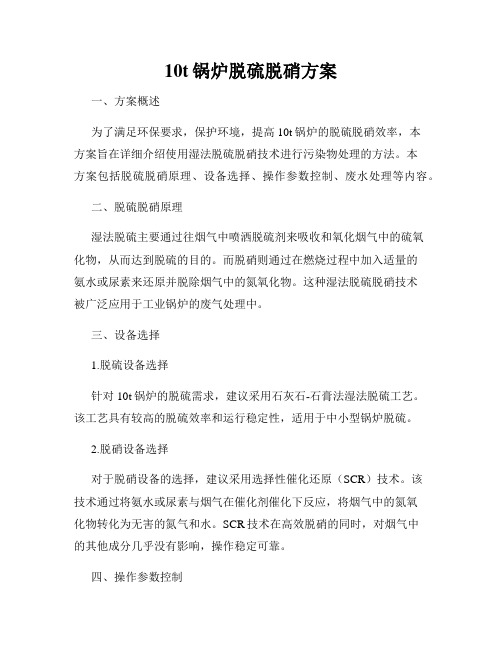
10t锅炉脱硫脱硝方案一、方案概述为了满足环保要求,保护环境,提高10t锅炉的脱硫脱硝效率,本方案旨在详细介绍使用湿法脱硫脱硝技术进行污染物处理的方法。
本方案包括脱硫脱硝原理、设备选择、操作参数控制、废水处理等内容。
二、脱硫脱硝原理湿法脱硫主要通过往烟气中喷洒脱硫剂来吸收和氧化烟气中的硫氧化物,从而达到脱硫的目的。
而脱硝则通过在燃烧过程中加入适量的氨水或尿素来还原并脱除烟气中的氮氧化物。
这种湿法脱硫脱硝技术被广泛应用于工业锅炉的废气处理中。
三、设备选择1.脱硫设备选择针对10t锅炉的脱硫需求,建议采用石灰石-石膏法湿法脱硫工艺。
该工艺具有较高的脱硫效率和运行稳定性,适用于中小型锅炉脱硫。
2.脱硝设备选择对于脱硝设备的选择,建议采用选择性催化还原(SCR)技术。
该技术通过将氨水或尿素与烟气在催化剂催化下反应,将烟气中的氮氧化物转化为无害的氮气和水。
SCR技术在高效脱硝的同时,对烟气中的其他成分几乎没有影响,操作稳定可靠。
四、操作参数控制1.脱硫操作参数控制(1)石灰石浆液浓度:控制在10%~20%之间,过高的浓度会增加脱硫剂的消耗,过低的浓度则会降低脱硫效率。
(2)石灰石进料量:根据锅炉负荷和石灰石的硫含量,合理调节进料量,以保证脱硫效果。
2.脱硝操作参数控制(1)氨水或尿素投加量:根据烟气中氮氧化物的浓度和反应催化剂的性能,确定适当的投加量,以达到高效脱硝效果。
(2)催化剂活性:定期检测催化剂的活性,确保其在反应过程中的稳定性和催化效果。
五、废水处理在脱硫脱硝过程中产生的废水需要进行处理,以减少对环境的影响。
废水处理包括初期的固液分离和后续的中和、沉淀、过滤等处理过程。
处理后的废水达到排放标准后,可安全排放或进行再利用。
六、总结本方案详细介绍了10t锅炉脱硫脱硝方案,包括脱硫脱硝原理、设备选择、操作参数控制、废水处理等内容。
通过采用湿法脱硫脱硝技术,结合适当的设备选择和操作参数控制,可以实现高效、稳定的脱硫脱硝效果,满足环保要求,保护环境。
我公司锅炉烟气脱硫运行总结
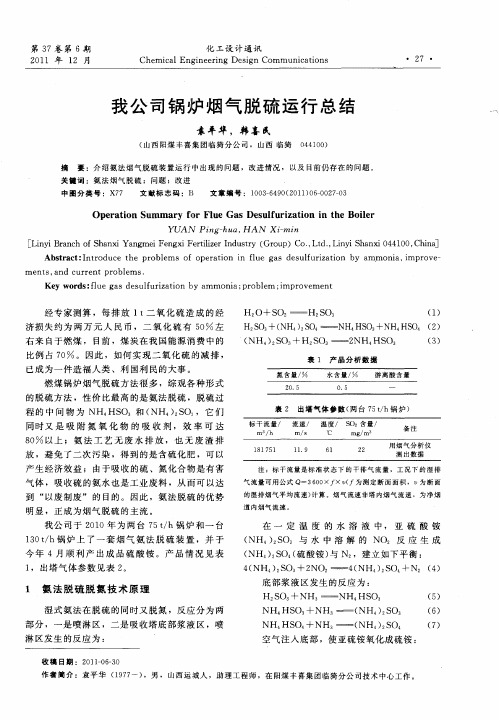
整套 装置布 置 紧凑 , 占地 面积小 ,主要 是 由 于采用 塔 内氧化 和结 晶 。和其他 工艺相 比,如塔 外氧 化和结 晶工 艺 ,不 仅 占地少 ,投 资也 少 ,还 节约 了大部 分能 源 。塔 外结 晶需 要用蒸 汽对 硫酸
铵溶 液进行 再热 ,否则 硫 酸铵结 晶会造 成管 道和 设备 堵塞 ,用蒸 汽提 温来 提高硫 酸铵溶 液 的溶解
其 中 ,式 ( ) 吸收 二氧化 硫最 有效 的途径 , 1是 它 跟喷 头 的 喷雾 效 果 有 很 大 的关 系 ,喷 头效 果
好 ,扇 面大 ,覆盖 区域宽 ,脱硫 效 果就好 。锅 炉 烟气 中氮 氧化 物 的产 生 主要是 因为燃 主要是
化 工设 计 通 讯
( 8)
第 3 7卷
有极少 量 的水被 污泥带 走 。硫酸 铵浆 液经离 心机 后 晶体 水 含量小 于 5 ,再经 干 燥 机干 燥 得合 格 的硫 酸 铵 成 品 ,最 后 用 自 动 包 装 机 包 装 ,按 4 g 袋 或 5 g 袋 装好后 送入 仓库 。 0 / k 0 / k 装 置原 设计 采用 p 显控 仪控 制脱 硫 塔集 液 H 池 中氨水 的加入 量 ,p 值 控制 在 5 , 以保 证 H ~6 二氧化 硫 的吸收 率和控 制 氨的逃 逸 。浆 液排 出采 用在 线密 度测量 ,浆 液密度 控制 在 1 2 g I左 . 8 / k 右 。通过 控制循 环量来 控制 烟气 出 口温度 和出 口 二氧 化硫浓 度 ,出 口烟气温 度控 制在 6 C左 右 , 0” 出 口 二 氧 化 硫 控 制 在 排 放 标 准 之 内 ( 超 过 小 40 / ) 0 m 。采 用 YQ3 0 一 型 烟 气 分 析 仪 , mg 0 0B
- 1、下载文档前请自行甄别文档内容的完整性,平台不提供额外的编辑、内容补充、找答案等附加服务。
- 2、"仅部分预览"的文档,不可在线预览部分如存在完整性等问题,可反馈申请退款(可完整预览的文档不适用该条件!)。
- 3、如文档侵犯您的权益,请联系客服反馈,我们会尽快为您处理(人工客服工作时间:9:00-18:30)。
锅炉脱硫方法
燃煤锅炉主要有三种脱硫方法:燃烧前脱硫、燃烧中脱硫、燃烧后脱硫
燃烧前脱硫:常用方法就是洗煤,经过物理处理,去除煤中的硫份,降低煤燃烧后排出的二氧化硫含量。
燃烧中脱硫:炉内脱硫,常用方法是在煤中参入固硫剂,在燃烧时产生的二氧化硫遇到固硫剂被劫持下来,并结合生成固体化合物,然后随炉渣排出。
这是目前最经济、实效、应用广泛的方法。
燃烧后脱硫:烟气脱硫主要是对硫的回收利用,此方法在旋流除尘脱硫塔内,加入吸收剂,烟气与其接触后发生反应,形成硫酸盐,随灰水排至尘灰池沉淀处理,达到脱硫的效果。
脱硫工艺:
1.石膏法
石灰石——石膏法脱硫工艺是世界上应用最广泛的一种脱硫技术。
它的工作原理是:将石灰石粉加水制成浆液作为吸收剂泵入吸收塔与烟气充分接触混合,烟气中的二氧化硫与浆液中的碳酸钙以及从塔下部鼓入的空气进行氧化反应生成硫酸钙,硫酸钙达到一定饱和度后,结晶形成二水石膏。
经吸收塔排出的石膏浆液经浓缩、脱水,使其含水量小于10%,然后用输送机送至石膏贮仓堆放,脱硫后的烟气经过除雾器除去雾滴,再经过换热器加热升温后,由烟囱排入大气。
由于吸收塔内吸收剂浆液通过循环泵反复循环与烟气接触,吸收剂利用率很高,钙硫比较低,脱硫效率可大于95%。
2.喷雾干燥法
喷雾干燥法脱硫工艺以石灰为脱硫吸收剂,石灰经消化并加水制成消石灰乳,消石灰乳由泵打入位于吸收塔内的雾化装置,在吸收塔内,被雾化成细小液滴的吸收剂与烟气混合接触,与烟气中的SO2发生化学反应生成CaSO3,烟气中的SO2被脱除。
与此同时,吸收剂带入的水分迅速被蒸发而干燥,烟气温度随之降低。
脱硫反应产物及未被利用的吸收剂以干燥的颗粒物形式随烟气带出吸收塔,进入除尘器被收集下来。
脱硫后的烟气经除尘器除尘后排放。
为了提高脱硫吸收剂的利用率,一般将部分除尘器收集物加入制浆系统进行循环利用。
该工艺有两种不同的雾化形式可供选择,一种为旋转喷雾轮雾化,另一种为气液两相流。
喷雾干燥法脱硫工艺具有技术成熟、工艺流程较为简单、系统可靠性高等特点,脱硫率可达到85%以上。
脱硫灰渣可用作制砖、筑路,但多为抛弃至灰场或回填废旧矿坑。
3.磷铵肥法
磷铵肥法烟气脱硫技术属于回收法,以其副产品为磷铵而命名。
该工艺过程主要由吸附(活性炭脱硫制酸)、萃取(稀硫酸分解磷矿萃取磷酸)、中和(磷铵中和液制备)、吸收(磷铵液脱硫制肥)、氧化(亚硫酸铵氧化)、浓缩干燥(固体肥料制备)等单元组成。
它分为两个系统:
烟气脱硫系统——烟气经高效除尘器后使含尘量小于200mg/Nm3,用风机将烟压升高到7000Pa,先经文氏管喷水降温调湿,然后进入四塔并列的活性炭脱硫塔组(其中一只塔周期性切换再生),控制一级脱硫率大于或等于70%,并制得30%左右浓度的硫酸,一级脱硫后的烟气进入二级脱硫塔用磷铵浆液洗涤脱硫,净化后的烟气经分离雾沫后排放。
肥料制备系统——在常规单槽多浆萃取槽中,同一级脱硫制得的稀硫酸分解磷矿粉(P2O5 含量大于26%),过滤后获得稀磷酸(其浓度大于10%),加氨中和后制得磷氨,作为二级脱硫剂,二级脱硫后的料浆经浓缩干燥制成磷铵复合肥料。
4. 炉内喷钙尾部增湿法
炉内喷钙加尾部烟气增湿活化脱硫工艺是在炉内喷钙脱硫工艺的基础上在锅炉尾部增设了增湿段,以提高脱硫效率。
该工艺多以石灰石粉为吸收剂,石灰石粉由气力喷入炉膛850—1150℃温度区,石灰石受热分解为氧化钙和二氧化碳,氧化钙与烟气中的二氧化硫反应生成亚硫酸钙。
由于反应在气固两相之间进行,受到传质过程的影响,反应速度较慢,吸收剂利用率较低。
在尾部增湿活化反应器内,增湿水以雾状喷入,与未反应的氧化钙接触生成氢氧化钙进而与烟气中的二氧化硫反应。
当钙硫比控制在2.0—2.5时,系统脱硫率可达到65—80%。
由于增湿水的加入使烟气温度下降,一般控制出口烟气温度高于露点温度10—15℃,增湿水由于烟温加热被迅速蒸发,未反应的吸收剂、反应产物呈干燥态随烟气排出,被除尘器收集下来。
5.烟气循环流化床法
烟气循环流化床脱硫工艺由吸收剂制备、吸收塔、脱硫灰再循环、除尘器及控制系统等部分组成。
该工艺一般采用干态的消石灰粉作为吸收剂,也可采用其它对二氧化硫有吸收反应能力的干粉或浆液作为吸收剂。
由锅炉排出的未经处理的烟气从吸收塔(即流化床)底部进入。
吸收塔底部为一个文丘里装置,烟气流经文丘里管后速度加快,并在此与很细的吸收剂粉末互相混合,颗粒之间、气体与颗粒之间剧烈摩擦,形成流化床,在喷入均匀水雾降低烟温的条件下,吸收剂与烟气中的二氧化硫反应生成CaSO3 和CaSO4。
脱硫后携带大量固体颗粒的烟气从吸收塔顶部排出,进入再循环除尘器,被分离出来的颗粒经中间灰仓返回吸收塔,由于固体颗粒反复循环达百次之多,故吸收剂利用率较高。
6.氨水洗涤法
该脱硫工艺以氨水为吸收剂,副产硫酸铵化肥。
锅炉排出的烟气经烟气换热器冷却至90-100℃,进入预洗涤器经洗涤后除去HCI和HF,洗涤后的烟气经过液滴分离器除去水滴进入前置洗涤器中。
在前置洗涤器中,氨水自塔顶喷淋洗涤烟气,烟气中的SO2被洗涤吸收除去,经洗涤的烟气排出后经液滴分离器除去携带的水滴,进入脱硫洗涤器。
在该洗涤器中烟气进一步被洗涤,经洗涤塔顶的除雾器除去雾滴,进入脱硫洗涤器。
再经烟气换热器加热后经烟囱排放。
洗涤工艺中产生的浓度约30%的硫酸铵溶液排出洗涤塔,可以送到化肥厂进一步处理或直接作为液体氮肥出售,也可以把这种溶液进一步浓缩蒸发干燥加工成颗粒、晶体或块状化肥出售。