现有主要炼铁工艺的优缺点和研发方向
高炉炼铁的发展现状与展望

5、还原技术
还原技术是一种通过热还原反应将金属氧化物转化为金属单质的技术。该技 术具有能源消耗低、环境污染小等优势,是非高炉炼铁中的重要技术之一。其中, 碳热还原法是最常用的还原方法之一。
四、非高炉炼铁的生产实例
1、氧气转炉炼铁的生产实例
济钢170氧气转炉在经过改造后,成功实现了直接还原与熔融还原两种工艺 在同一个设备上交替进行。通过优化工艺参数和完善操作规程,该设备不仅显著 提高了生产效率,同时还降低了能源消耗和环境污染。
(2)智能化:通过应用互联网、大数据、人工智能等信息技术,实现高炉 炼铁的智能化生产和管理,提高生产效率和降低成本。
(3)绿色化:随着环保政策的加强,高炉炼铁的环保性能将得到进一步提 升,通过采用清洁能源、废弃物再利用等措施,实现生产过程的低碳和清洁化。
2、面临的挑战与机遇高炉炼铁行业未来面临的挑战包括环保政策的压力、 能源价格的波动以及国际市场竞争的激烈等。然而,随着技术的不断进步和市场 需求的发展,高炉炼铁行业也面临着巨大的机遇。例如,新兴市场国家的工业化 进程将带动钢铁需求的增长;清洁能源技术的发展也为高炉炼铁行业提供了新的 发展机遇。
参考内容
随着环境保护和能源消耗问题的日益突出,非高炉炼铁技术作为绿色、节能 的炼铁方式,正逐渐受到中国钢铁行业的和重视。本次演示将阐述中国非高炉炼 铁的现状、展望、关键技术及生产实例,以期为相关领域的发展提供参考。
一、中国非高炉炼铁的现状
非高炉炼铁主要通过直接还原、熔融还原、气化还原等方式将铁矿石或金属 铁还原成海绵铁或液态生铁。相较于传统的高炉炼铁,非高炉炼铁具有节能、环 保等优势。
3、政策环境在全球范围内,各国政府普遍环境保护和能源消耗问题,因此, 钢铁行业的政策环境也发生了变化。许多国家政府对高炉炼铁的环保性能提出更 高要求,鼓励发展清洁能源和循环经济。在中国,政府提出了《中国制造2025》 和《钢铁行业转型升级计划》,以推动高炉炼铁的节能减排和转型升级。
炼钢工艺发展的趋势
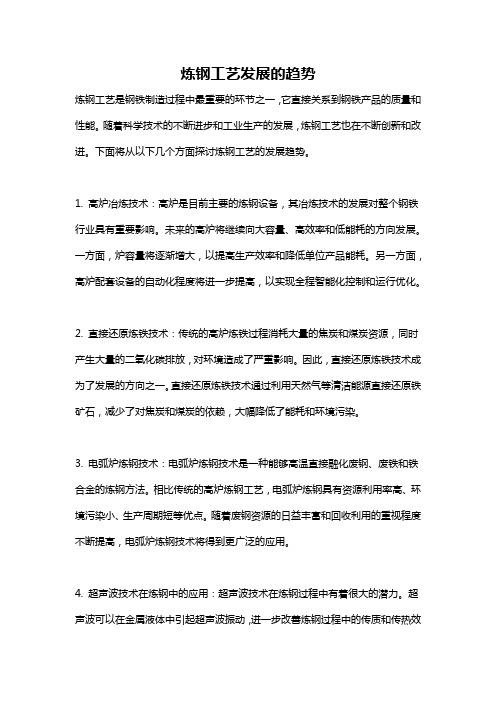
炼钢工艺发展的趋势炼钢工艺是钢铁制造过程中最重要的环节之一,它直接关系到钢铁产品的质量和性能。
随着科学技术的不断进步和工业生产的发展,炼钢工艺也在不断创新和改进。
下面将从以下几个方面探讨炼钢工艺的发展趋势。
1. 高炉冶炼技术:高炉是目前主要的炼钢设备,其冶炼技术的发展对整个钢铁行业具有重要影响。
未来的高炉将继续向大容量、高效率和低能耗的方向发展。
一方面,炉容量将逐渐增大,以提高生产效率和降低单位产品能耗。
另一方面,高炉配套设备的自动化程度将进一步提高,以实现全程智能化控制和运行优化。
2. 直接还原炼铁技术:传统的高炉炼铁过程消耗大量的焦炭和煤炭资源,同时产生大量的二氧化碳排放,对环境造成了严重影响。
因此,直接还原炼铁技术成为了发展的方向之一。
直接还原炼铁技术通过利用天然气等清洁能源直接还原铁矿石,减少了对焦炭和煤炭的依赖,大幅降低了能耗和环境污染。
3. 电弧炉炼钢技术:电弧炉炼钢技术是一种能够高温直接融化废钢、废铁和铁合金的炼钢方法。
相比传统的高炉炼钢工艺,电弧炉炼钢具有资源利用率高、环境污染小、生产周期短等优点。
随着废钢资源的日益丰富和回收利用的重视程度不断提高,电弧炉炼钢技术将得到更广泛的应用。
4. 超声波技术在炼钢中的应用:超声波技术在炼钢过程中有着很大的潜力。
超声波可以在金属液体中引起超声波振动,进一步改善炼钢过程中的传质和传热效果,提高钢的纯净度和均匀性。
此外,超声波还可以用于检测和监测钢铁产品中的缺陷和杂质,提高质量控制的准确性和效率。
5. 粉煤气化技术:粉煤气化技术是一种利用煤炭资源进行炼钢的新技术。
通过对煤炭进行气化,产生合成气,再利用合成气进行炼钢,既能够提高煤炭资源的利用率,又能够减少对传统能源的依赖和环境污染。
粉煤气化技术属于绿色环保型炼钢工艺,对于改善钢铁行业的能源结构和减少碳排放具有重要意义。
总体来说,炼钢工艺的发展趋势是朝着高效、环保、智能化和资源综合利用的方向发展。
国内外高炉炼铁技术的发展现状和趋势

国内外高炉炼铁技术的发展现状和趋势高炉炼铁技术是金属冶炼工业发展的基础,是保证金属铁质量和产量的关键技术,也是社会经济发展的重要依托。
近年来,随着金属冶炼工业的快速发展,国内外高炉炼铁技术的发展也取得了显著的成就,为保证金属铁质量、提高产量、提高经济效益发挥了重要作用。
首先,国内外高炉炼铁技术取得了重大突破,进一步提高了金属铁质量。
随着科学技术的进步,添加剂和冶炼工艺的改进,使高炉炼铁工艺取得重大进展,不仅能够有效提高铁素体组成,同时也能够改善铁水的流动性,有利于铁块的全面成型。
此外,利用新型炉料和改进的热处理技术,可以有效降低铁水的含氧量,提高铁液的液相容量,从而获得更高品质的铁。
其次,国内外高炉炼铁技术的发展,还大大提高了铁的产量。
传统的高炉炼铁工艺存在着大量的炉料损失,限制了铁的产量。
随着国内外高炉炼铁技术的发展,炉料损失大大减少,产量得到提高。
通过对炼铁工艺及其参数进行优化调整,获得合理的炉料计算和分配,进而有效提高铁的产量。
此外,结合智能技术、自动化技术和智能控制技术,还可以实现远程监控和智能化管理,可以使高炉炼铁效率更高,产量更大。
最后,国内外高炉炼铁技术的发展,对提高经济效益具有重要意义。
国内外高炉炼铁技术的发展,不仅缩短了铁的生产周期,提高了产量,而且可以减少能耗消耗和废气排放,降低了生产成本,有利于提高企业的竞争力,实现更高的经济效益。
此外,国内外高炉炼铁技术的发展还可以改善炼铁终端的工作环境,为炼铁行业的发展创造更加良好的条件。
以上是国内外高炉炼铁技术的发展现状和趋势的概述,未来的发展趋势可以简单地总结为以下几点:继续提高高炉炼铁质量和产量,推广智能技术,进一步优化炼铁工艺,合理设计炉料配比,提高炼铁效率,减少能耗和污染,改善炼铁环境,提高经济效益,实现绿色经济发展。
未来,相信国内外高炉炼铁技术将取得更好的发展,为我们社会的经济发展提供更多的依托。
钢铁行业智能冶炼

钢铁行业智能冶炼智能技术的快速发展正在逐渐渗透到各行各业,钢铁行业也不例外。
智能冶炼作为一个创新的生产方式,正逐渐成为钢铁行业的主要发展方向。
本文将探讨钢铁行业智能冶炼的现状、优势以及未来的发展趋势。
一、智能冶炼简介随着科技的迅猛发展,钢铁企业日益意识到传统冶炼方式存在的一些问题。
传统冶炼方法通常需要大量人工操作,无法充分利用资源,且存在一定的安全风险。
智能冶炼通过引入人工智能、大数据、物联网等技术手段,实现冶炼过程的自动化、智能化和精细化,从而提高生产效率和产品质量。
二、智能冶炼的优势1.提高生产效率:智能冶炼能够实现冶炼过程的自动化控制,减少人工干预,从而提高生产效率。
智能冶炼设备能够实时监测和调整冶炼参数,确保冶炼过程的稳定性和效率。
2.降低能耗和排放:智能冶炼通过优化能源利用和减少废气废水的产生,实现了能耗和环境排放的降低。
智能冶炼设备可以精确控制燃烧过程,提高能源利用效率,减少二氧化碳等有害气体的排放。
3.提高产品质量:智能冶炼可以实现对冶炼过程的精细化控制,提高产品质量。
通过智能监测和分析数据,及时发现和纠正冶炼过程中的问题,确保产品的合格率和成品率。
4.安全性更高:智能冶炼设备可以实时监测冶炼过程中的温度、压力等参数,及时发现隐患,避免事故的发生。
自动化控制系统可以有效减少人为操作的风险,提高工作安全性。
三、智能冶炼的发展趋势1.人工智能在冶炼中的应用:随着人工智能技术的不断发展,将会出现更多智能化的冶炼设备。
通过人工智能技术,冶炼设备可以实现自主学习和决策,进一步提高冶炼过程的智能性和稳定性。
2.物联网技术的融入:物联网技术将为智能冶炼提供更广阔的发展空间。
通过将各个环节的冶炼设备实现互联互通,可以实现冶炼过程的全面监控和协调控制,提高生产效率。
3.大数据分析的应用:大数据分析可以帮助钢铁企业更好地了解生产过程,挖掘数据背后的规律,及时发现和解决问题。
通过大数据分析,钢铁企业可以实现冶炼过程的优化调整,进一步提高生产效率和产品质量。
金属冶炼开拓金属冶炼新技术为工业进步注入新动力
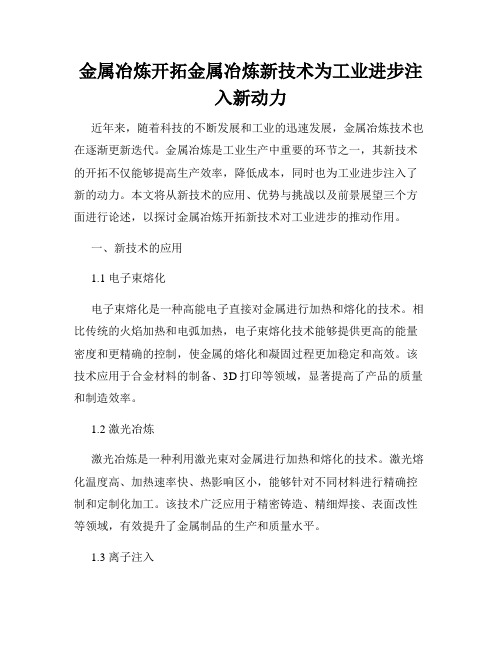
金属冶炼开拓金属冶炼新技术为工业进步注入新动力近年来,随着科技的不断发展和工业的迅速发展,金属冶炼技术也在逐渐更新迭代。
金属冶炼是工业生产中重要的环节之一,其新技术的开拓不仅能够提高生产效率,降低成本,同时也为工业进步注入了新的动力。
本文将从新技术的应用、优势与挑战以及前景展望三个方面进行论述,以探讨金属冶炼开拓新技术对工业进步的推动作用。
一、新技术的应用1.1 电子束熔化电子束熔化是一种高能电子直接对金属进行加热和熔化的技术。
相比传统的火焰加热和电弧加热,电子束熔化技术能够提供更高的能量密度和更精确的控制,使金属的熔化和凝固过程更加稳定和高效。
该技术应用于合金材料的制备、3D打印等领域,显著提高了产品的质量和制造效率。
1.2 激光冶炼激光冶炼是一种利用激光束对金属进行加热和熔化的技术。
激光熔化温度高、加热速率快、热影响区小,能够针对不同材料进行精确控制和定制化加工。
该技术广泛应用于精密铸造、精细焊接、表面改性等领域,有效提升了金属制品的生产和质量水平。
1.3 离子注入离子注入技术通过将能量高的离子束注入到金属表面,改变金属的物理性能,从而增强金属的硬度、耐磨性和耐腐蚀性。
该技术广泛应用于制备高性能材料、材料表面处理等领域,为材料的开发和应用提供了新的途径。
二、新技术的优势与挑战2.1 优势金属冶炼开拓的新技术相较于传统技术,具有以下优势:首先,新技术能够提高生产效率和降低生产成本。
例如,电子束熔化和激光冶炼技术的应用,可以实现快速加热和凝固,加速生产周期,同时减少材料的浪费和能源的消耗。
其次,新技术能够提高产品的质量和性能。
通过精确控制材料的熔化和凝固过程,可以优化金属的组织结构和力学性能,提高产品的强度、硬度和韧性等指标。
最后,新技术能够实现材料的定制化和个性化加工。
不同于传统冶炼技术的批量生产,新技术可以根据产品需求进行精细化加工和个性化定制,满足不同行业和用户的需求。
2.2 挑战金属冶炼开拓新技术面临一些挑战:首先,新技术的研发和应用需要投入大量的研究与开发资源。
钢铁行业中的炼钢工艺和钢材分类
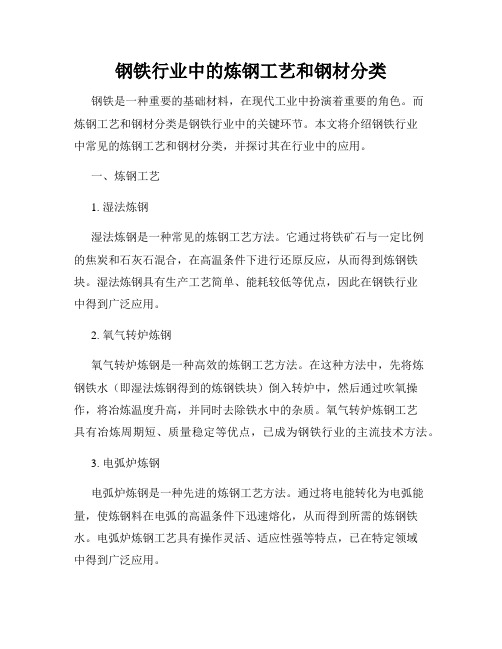
钢铁行业中的炼钢工艺和钢材分类钢铁是一种重要的基础材料,在现代工业中扮演着重要的角色。
而炼钢工艺和钢材分类是钢铁行业中的关键环节。
本文将介绍钢铁行业中常见的炼钢工艺和钢材分类,并探讨其在行业中的应用。
一、炼钢工艺1. 湿法炼钢湿法炼钢是一种常见的炼钢工艺方法。
它通过将铁矿石与一定比例的焦炭和石灰石混合,在高温条件下进行还原反应,从而得到炼钢铁块。
湿法炼钢具有生产工艺简单、能耗较低等优点,因此在钢铁行业中得到广泛应用。
2. 氧气转炉炼钢氧气转炉炼钢是一种高效的炼钢工艺方法。
在这种方法中,先将炼钢铁水(即湿法炼钢得到的炼钢铁块)倒入转炉中,然后通过吹氧操作,将冶炼温度升高,并同时去除铁水中的杂质。
氧气转炉炼钢工艺具有冶炼周期短、质量稳定等优点,已成为钢铁行业的主流技术方法。
3. 电弧炉炼钢电弧炉炼钢是一种先进的炼钢工艺方法。
通过将电能转化为电弧能量,使炼钢料在电弧的高温条件下迅速熔化,从而得到所需的炼钢铁水。
电弧炉炼钢工艺具有操作灵活、适应性强等特点,已在特定领域中得到广泛应用。
二、钢材分类根据化学成分和用途,钢材可分为多个不同的分类。
以下是常见的钢材分类:1. 炭素钢炭素钢是最基础的钢材,其含碳量在0.02%~2.11%之间。
根据碳含量的不同,炭素钢可再细分为低碳钢、中碳钢和高碳钢等。
炭素钢在各个领域都有广泛应用,如建筑、汽车制造等。
2. 合金钢合金钢是在炭素钢中添加其他合金元素,以提高钢材的性能。
根据添加的不同合金元素,合金钢可再细分为铬钢、镍钢、钼钢等。
合金钢在航空、航天等高端领域有着重要地位。
3. 不锈钢不锈钢是一种表面具有耐腐蚀性能的钢材。
根据其化学成分和组织结构的不同,不锈钢可以分为奥氏体不锈钢、铁素体不锈钢等。
不锈钢在厨具、化工等行业中得到广泛应用。
4. 高速工具钢高速工具钢是一种硬度高、耐磨性能好的钢材。
它通常用于制造切削工具和模具等高强度工具。
高速工具钢在机械制造业中起到关键作用。
试析现有主要炼铁工艺的优缺点和研发方向
1当前主要炼铁方式的优势与缺陷
1.1高炉炼铁工艺
这是当前应用最广泛的炼铁工艺,在冶铁业有着重要的作用与地位。高炉炼铁工艺在我国的应用十分广泛,我国有近九成的钢铁是通过高炉炼铁的方式生产的。高炉炼铁工艺的优势是已经形成了比较完善的应用体系,配套设施也比较完善,可以通过协调配合发挥出更大的作用。此外,高炉炼铁工艺的热效率高,可以满足炼铁过程中的高温需求,也可以在最大程度上保证炼铁效率,它本身的炼铁技术十分先进,代表着当前最先进的技术水平。同时,高炉炼铁的生产成本较低,可以为企业提供较大的利润空间,得到了广泛的发展与应用。但是高炉炼铁工艺也存在着明显的缺陷,一是高炉炼铁所需要的动力能源是焦炭,而焦炭属于不可再生资源,这就使得高炉炼铁工艺的能源资源无法保证持续的供应,因为总有一天会耗尽;二是由于高炉炼铁需要燃烧大量的焦炭,会排放出大量的有害气体,造成环境污染,不利于环保工作的顺利开展;三是高炉炼铁工艺的流程与环节过长,无法及时的产出。虽然它的资金成本很低,可以提升利润空间,但是这种工艺的时间成本过高,会耗费企业极大的精力;四是这种工艺的资源利用率低,无法对资源进行二次利用,不能有效的提升生产效率,不利于提升高炉炼铁的质量与效率,会造成严重的资源浪费。如图一所示,图中所展示的是高炉炼铁工艺的具体操作流程,根据此图我们也可以看出高炉炼铁工艺在控制污染物排放等方面做的还不到位,无法减少污染物的排放,不利于环境保护工作的顺利开展。
试析现有主要炼铁工艺的优缺点和研发方向
摘要:本文从当前主要炼铁工艺的现实情况与发展需要出发,针对其中存在的缺陷与问题进行了细致的分析与研究,并详细的阐述了不同炼铁工艺的优势与劣势,在今后炼铁技术的研发方向上提出了具有科学性与可行性的发展意见与实施策略,对于在控制生产成本的基础上不断提升炼铁工艺的效率与质量具有积极的意义。
金属冶炼技术的挑战与前景展望
金属冶炼技术的挑战与前景展望金属冶炼技术作为人类文明进步的重要标志之一,已经经历了数千年的演变。
从最初的火法炼铜到现代的真空熔炼技术,金属冶炼技术在不断地创新与发展。
然而,随着金属资源的逐渐枯竭和环境保护意识的提高,金属冶炼技术面临着前所未有的挑战。
本文将分析当前金属冶炼技术所面临的挑战,并对未来金属冶炼技术的发展前景进行展望。
资源枯竭金属资源的开采与冶炼是有限的。
目前,许多重要的金属资源已经进入枯竭阶段,如铜、锌、铅等。
金属资源的枯竭导致了金属价格的波动,给金属冶炼企业带来了巨大的经营风险。
因此,开发新的冶炼技术和提高现有技术的利用率成为当务之急。
环境保护传统的金属冶炼技术往往伴随着大量的环境污染问题。
例如,火法炼铜过程中产生的二氧化硫会严重污染空气,对人类健康和生态环境造成威胁。
因此,如何在冶炼过程中减少污染物的排放,实现绿色冶炼,是金属冶炼技术面临的重要挑战。
能源消耗金属冶炼过程需要大量的能源,尤其是高温炼制过程。
随着能源价格的上涨,降低能源消耗成为金属冶炼企业追求的目标。
因此,研究高效、节能的冶炼技术对于降低生产成本具有重要意义。
前景展望绿色冶炼绿色冶炼是未来金属冶炼技术发展的重要方向。
绿色冶炼技术目的是实现高效、低污染的冶炼过程。
例如,采用湿法炼铜技术可以大大减少二氧化硫的排放,实现环境友好型冶炼。
此外,利用可再生能源如太阳能、风能等替代传统的化石能源,也有助于降低金属冶炼过程中的能源消耗。
高效利用提高金属资源的利用效率是解决金属资源枯竭问题的关键。
未来金属冶炼技术将更加注重提高金属回收率,实现资源的循环利用。
例如,采用先进的选矿技术和冶炼工艺,可以有效地提高金属的提取效率。
同时,加强金属废弃物的回收利用,也有助于缓解金属资源短缺的压力。
技术创新随着科技的不断进步,金属冶炼技术也将迎来新的突破。
例如,纳米技术在金属冶炼中的应用可以提高金属的熔点,降低能耗。
此外,等离子体技术、生物技术等新兴技术在金属冶炼领域的应用,也有望实现高效、低污染的冶炼过程。
高炉炼铁技术创新实践及未来展望
千里之行,始于足下。
高炉炼铁技术创新实践及未来展望高炉炼铁技术是钢铁工业中非常重要的一个环节,对于钢铁产量和质量有着直接影响。
随着科技的不断发展和进步,高炉炼铁技术也在不断创新和实践。
本文将介绍高炉炼铁技术的创新实践及未来展望。
高炉炼铁技术主要包括焦炭冶炼、铁矿石还原和炉渣处理三个方面。
近年来,针对这几个环节进行了一系列的技术创新,以提高钢铁产量和质量,减少能源消耗和环境污染。
首先,在焦炭冶炼方面,高炉炼铁技术实践了煤炭气化技术,将煤炭转化为合成气或制备气,用来代替部分焦炭。
这样可以减少焦炭的消耗量,提高炉温和炉效,提高炼铁效果和节约能源。
其次,在铁矿石还原方面,高炉炼铁技术实践了混合还原技术,将不同种类的铁矿石混合使用,以提高还原效率和减少还原剂的消耗。
同时,还运用了制粒和球团矿技术,提高了炉料的密实度和还原性能,使得炼铁效果更好。
再次,在炉渣处理方面,高炉炼铁技术实践了炉渣处理技术,包括高炉渣套料、炉渣粉磨和炉渣稳定化等。
这些技术可以减少炉渣的生成和排放,降低对环境的污染,同时还能回收利用一部分有价值的元素。
未来,高炉炼铁技术仍将继续创新和发展。
一方面,可以进一步拓宽原料的来源,包括使用青海盐湖等资源,以降低对传统铁矿石的依赖程度。
另一方面,可以进一步提高炉渣的利用率,实现钢铁工业的循环经济。
此外,还可以用高效节能的加热方式替代传统的冶炼方法,以进一步降低能源消耗和环境污染。
第1页/共2页锲而不舍,金石可镂。
综上所述,高炉炼铁技术的创新实践为钢铁工业的发展提供了重要支撑。
未来,随着技术的不断进步和创新,高炉炼铁技术将更加高效、环保和可持续,为钢铁产量和质量的提高做出更大贡献。
同时,需要在技术创新的同时,加强对环境保护的重视,实现钢铁工业的可持续发展。
金属冶炼技术的国内外比较分析
精炼
对提取出的金属进行提 纯和精制,以满足不同
用途的要求。
金属冶炼技术的发展历程
古代金属冶炼
古代人类主要采用简单的熔炼和 锻打方法,从矿石中提取金属。
近代金属冶炼
随着科技的发展,开始采用大规模 的熔炼和提取技术,同时出现了多 种新型的金属冶炼方法。
现代金属冶炼
采用先进的工艺和设备,实现高效 、环保、节能的金属冶炼,同时不 断探索新的金属冶炼技术和方法。
提高资源利用率和环保性能
01
推广循环经济理念,实现资源高效利用。
02
优化冶炼工艺,降低能耗和物耗,减少污染物排放 。
03
开发环保技术和产品,推动绿色发展。
加强国际合作与交流
01
积极参与国际技术交流与合作,拓宽视野。
02 学习借鉴国外先进经验,提高我国金属冶炼技术 的国际竞争力。
03 加强与国际标准对接,推动我国标准国际化进程 。
金属冶炼的重要性
金属冶炼是现代工业和经济发展的重 要基础,为机械制造、建筑、交通、 电子、航空航天等领域提供关键材料 ,支撑着人类社会的进步和发展。
金属冶炼的基本流程
矿石准备
将矿石破碎、磨细,以 便更好地进行冶金反应
。
熔炼
将矿石中的有用成分和 杂质一起熔化,形成熔
融态的锍。
提取
通过化学反应或电解等 方法,从熔融态的锍中
新材料研发
国内金属冶炼技术正积极 开展新材料研发,推动金 属产业升级和转型。
03 国际金属冶炼技术现状
国际金属冶炼的主要方法
电弧炉熔炼法
利用电弧产生的高温熔炼矿石 和金属,具有较高的熔炼效率
和较低的成本。
闪速熔炼法
- 1、下载文档前请自行甄别文档内容的完整性,平台不提供额外的编辑、内容补充、找答案等附加服务。
- 2、"仅部分预览"的文档,不可在线预览部分如存在完整性等问题,可反馈申请退款(可完整预览的文档不适用该条件!)。
- 3、如文档侵犯您的权益,请联系客服反馈,我们会尽快为您处理(人工客服工作时间:9:00-18:30)。
现有主要炼铁工艺的优缺点和研发方向
摘要:当前,钢铁企业炼铁工艺中,热效率已经很高,工艺技术设备也已完善,大型化、长寿化的高炉炼铁工艺作为我国主要炼铁设备,将继续在炼铁领域占统治地位。
在我国社会主义市场经济体制改革不断深入的背景下,钢铁企业要不断进行自主创新,提高炼铁工艺基础管理水平,积极引进或开发最新炼铁工艺,特别是节能减排技术,切实保证产品质量,促进企业经济效益和社会效益的提高。
关键词:炼铁工艺;优缺点;发展
一、钢铁企业炼铁工艺发展现状及问题
近几年随着我国市场经济的快速发展和科学技术的不断进步,钢铁企业高炉炼铁工艺不断优化,具有热效率高、技术完善、设备使用寿命长等优点,同时我国炼铁技术取得了一定的成就,比如提高转炉炉龄,提高转炉作业率,强化供氧技术等等;特别是“十二五”规划以来,我国钢铁企业重视炼铁工艺优化,重点进行节能减排技术的开发,比如滚筒法连续处理工艺等,大力引进先进设备,生铁产量逐年提高,说明我国节能减排工作取得了一定的进展。
但是,目前我国钢铁企业炼铁工艺中还是存在一定的问题:
一是我国炼铁工艺的能耗、废弃物回收利用和环境治理等与国家炼铁水平还是有很大的差距。
二是炼铁工艺管理不够规范,比如说辅料、铁合金等的分类管理。
三是当下炼铁中的二氧化碳的排放量高于国际水平,产品质量没达到国际水平。
四是炼铁工艺设计缺乏创新,一定程度上影响了炼铁工艺的使用。
二、高炉炼铁工艺
在当前,主要的钢铁生产都是以高炉流程生产的.高炉流程是现代钢铁生产流程的龙头。
因此,就对高炉炼铁工艺的优缺点进行分析:
高炉反应器的优点是热效率高、技术完善,设备已大型化、长寿化,单座高炉年产铁最高可达400万吨左右,一代炉役的产铁量可达5000万吨以上,可以说,没有现代化的大型高炉就没有现代化的钢铁工业大生产。
在今后相当长时期内,高炉流程在我国将继续是主要产铁设备,继续占统治地位.我国已完全掌握现代先进高炉技术,单位建设投资和生产成本相对较低.
但目前人们对高炉工艺流程有种种不满:
一是高炉必须要用较多焦炭,而炼焦煤越来越少,焦炭越来越贵;
二是环境污染严重,特别是焦炉的水污染物粉尘排放、烧结的SO:粉尘排放;三是传统炼铁流程长,投资大;
四是从铁、烧、焦全系统看重复加热、降温,增碳、脱碳,资源、能源循环使用率低,热能利用不合理。
在炼铁工序的结构优化中重点应抓好高炉流程的优化,高炉流程优化的主要目标是降低能耗,节省资源、改善环保.
近年来炼铁工艺技术取得了重大技术进步,它主要体现在以下几个方面:
①高炉长寿技术,最近十年,炼铁工作者为延长高炉寿命,从注重高炉整体寿命优化设计、精心施工、操作和维护等方面开发了许多新技术和新工艺,取得了显著的效果,先进高炉一代炉役(无中修)寿命可达18年以上。
高炉长寿技术主要体现在全炉体装冷却器(壁)从炉底炉至炉喉全部采用冷却器,无冷却盲区;在风口以上,炉腹、炉腰和炉身下部,软熔带根部上下移动区域使用自我造衬、自我保护无过热的铜冷却壁,在此区域淡化耐材炉衬的作用,依靠在表面形成稳定的可再生的渣皮来保护铜冷却壁;高效冷却设备和优质耐材炉衬的有效匹配,如在高炉炉缸侧壁区域使用热压小块碳砖、优质微孔碳砖配合铸铁冷却壁结构。
②高炉炉型设计理论的新发展:增加炉缸死铁层设计深度(达到炉缸直径的20-30%),减少炉缸内铁水环流对炉缸侧壁的侵蚀。
逐步减小高利用系数(炉役平均有效容积利用系数大于2.0)、高煤比(炉役平均喷煤量达150kg/t以上)高炉炉腹角。
对富氧大量喷煤强化冶炼的高炉,高炉炉型设计中将炉腹冷却壁放置到风口前中心点向上4X4ft及5X12ft炉腹上两点的连线以外,即可避免冷却壁因高煤比富氧喷吹、高利用强化系数冶炼而过早损坏。
③高炉以煤代焦、降低入炉焦比达到新水平。
④对高炉强化冶炼炉内煤气通过能力限度有了明确的认识。
⑤提高炉顶压力是降低燃料比、焦比及增产的重要手段。
三、炼铁工艺优化的有效措施
1、钢铁企业要加强研究炼铁生产过程中的技术经济问题,特别注重经济效益的研究,应用全面系统的优化方法分析钢铁企业的炼铁工艺,杜绝主观片面的优化判断,加强优化过程中的调查研究,掌握钢铁市场的最新信息,并做出准确科学的优化判断。
2、钢铁企业要坚持精料方针政策,不断提高高炉炼铁原料的质量。
根据炼铁工艺中用料杂的特点,关于烧结用矿粉问题上,对于供用量较大的矿点以单烧品位堆料原则供用,对于供用量较小并且矿粉品位相对低的矿点,要专门设立精
矿杂配,进行矿粉的二次混配,这样大大提高了烧结矿的碱度以及品位稳定性;在炼铁工序中焦炭供用上,根据焦炭上料系统特点以及焦炭供应量及质量的情况,推行“堆新用旧、供户至炉”的原则,从而保证各高炉焦炭供用的稳定性;炼铁过程中用的酸性料,应用电子称配料实现精确混配的目标,保证了配料粒度组成。
对炼铁焦炭入炉上,实行切分后分级入炉工艺,并对二区的烧结矿系统进行优化,实行烧结矿分级入炉,在强度上下功夫,同时要在净料入炉上下功夫。
建成球团矿、块矿筛分系统,同时增加烧结矿的冷返矿筛工序,从而入炉粉末率大大下降。
3、提高炼铁工艺基础管理水平。
建立、完善炼铁过程中五大体系的管理标准,五大体系包括:标准体系、指标体系、参数体系、成本体系、信息体系。
确保随时监控炼铁系统的原料投入、控制参数、指标变化、生产成本以及事件发生,能够及时扼制系统波动。
4、加强焦炭炼焦工艺技术的优化。
为降低炼焦的成本,缓解主焦煤短缺的现状,我国焦化界要重视优化配煤的推广。
我国钢铁企业炼铁要推广干熄焦炭和捣固焦炭的使用,小的高炉不可片面追求炼铁中焦炭的热性能,而要通过科学有效的方法来降低焦炭用量,如提高喷煤比和降低燃料比的方法就相当有效。
四、现有高炉炼铁流程工艺改进的方向
(一)炼焦工艺的努力方向
拓宽炼焦煤资源,炼焦生产工艺和技术上多元化。
如利用捣固炼焦大幅度提高装炉煤的堆密度,从而提高弱粘煤和非炼焦煤炼焦的比例降低焦炭成本、风选破碎配煤工艺、煤调湿等。
为了以煤代焦、降低入炉焦比,应强化不提高主焦煤比例条件下进一步提高焦炭的热强度的技术手段研究,进一步降低炼焦工序能耗、控制炼焦污染,建设国内一流清洁生产焦炉。
(二)烧结工艺的努力方向
烧结机是高炉利用铁粉矿低成本炼铁的核心手段,进一步提高烧结利用系数增加烧结矿产能,通过技术创新最大限度地回收烧结环冷机的烟气余热能;通过热烟气循环新技术降低燃料比和烧结烟气及粉尘的排放量;针对烧结生产过程中多种污染排放的严重环境污染问题,通过开发高效、低成本的适合中国特点的持久性有机污染物二恶英、SO2减排的技术措施,通过调整烧结原料有选择地严格限制使用含氯、含油原料等技术措施,采用烟气脱硫等新技术大幅度减少烧结机SO2、二恶英污染物排放量,争取改变烧结机是钢铁厂二恶英、SO2和烟粉尘污染主要源头的丑陋形象,建成世界最清洁生产的烧结厂,提高烧结工艺的生存力。
同时要持续研发低成本配矿技术、低SiO2的烧结技术、开发烧结人工智能控制系统。
目前烧结机SO2、烟粉尘排放占钢铁企业排放总量的50%~80%。
结语
钢铁企业炼铁工艺优化过程中要重视高炉炼铁工序的优化,使高炉炼铁面向低能化,并要节省炼铁资源、改善炼铁环境。
其次,国家要大力提高煤炭界的洗煤技术,将焦煤灰份降到最低,此措施即能减少煤炭的运输量,还能降低运输费用,最重要的是使我国炼铁工艺达到节能减排的目的。
最后,要鼓励创新研究,开展非高炉炼铁技术,发展有中国特色的炼铁工艺,促进我国钢铁企业炼铁技术的进步,创造领先世界的新炼铁流程。
参考文献
[1]杨海舟.高炉炼铁工艺中气体流程的建模研究[D].浙江大学,2010.
[2]邓虹峰.炼铁工艺创新对钢铁工业发展的影响[J].冶金经济与管理,2008,01:35-38.
[3]张俊杰.钢铁企业炼铁工艺优化问题研究[J].科技传播,2013,04:43-45.
[4]张寿荣.关于高炉炼铁工艺和熔融还原炼铁工艺的评述[J].炼铁,1995,01:45-48.。