机械运动和动力学中英文对照外文翻译文献
机械外文翻译外文文献英文文献机械臂动力学与控制的研究

外文出处:Ellekilde, L. -., & Christensen, H. I. (2009). Control of mobile manipulator using the dynamical systems approach. Robotics and Automation, Icra 09, IEEE International Conference on (pp.1370 - 1376). IEEE.机械臂动力学与控制的研究拉斯彼得Ellekilde摘要操作器和移动平台的组合提供了一种可用于广泛应用程序高效灵活的操作系统,特别是在服务性机器人领域。
在机械臂众多挑战中其中之一是确保机器人在潜在的动态环境中安全工作控制系统的设计。
在本文中,我们将介绍移动机械臂用动力学系统方法被控制的使用方法。
该方法是一种二级方法, 是使用竞争动力学对于统筹协调优化移动平台以及较低层次的融合避障和目标捕获行为的方法。
I介绍在过去的几十年里大多数机器人的研究主要关注在移动平台或操作系统,并且在这两个领域取得了许多可喜的成绩。
今天的新挑战之一是将这两个领域组合在一起形成具有高效移动和有能力操作环境的系统。
特别是服务性机器人将会在这一方面系统需求的增加。
大多数西方国家的人口统计数量显示需要照顾的老人在不断增加,尽管将有很少的工作实际的支持他们。
这就需要增强服务业的自动化程度,因此机器人能够在室内动态环境中安全的工作是最基本的。
图、1 一台由赛格威RMP200和轻重量型库卡机器人组成的平台这项工作平台用于如图1所示,是由一个Segway与一家机器人制造商制造的RMP200轻机器人。
其有一个相对较小的轨迹和高机动性能的平台使它适应在室内环境移动。
库卡工业机器人具有较长的长臂和高有效载荷比自身的重量,从而使其适合移动操作。
当控制移动机械臂系统时,有一个选择是是否考虑一个或两个系统的实体。
在参考文献[1]和[2]中是根据雅可比理论将机械手末端和移动平台结合在一起形成一个单一的控制系统。
文献翻译-机械运动和动力学

附录附录一英文资料Kinematics and dynamics of machineryOne princple aim of kinemarics is to creat the designed motions of the subject mechanical parts and then mathematically compute the positions, velocities ,and accelerations ,which those motions will creat on the parts. Since ,for most earthbound mechanical systems ,the mass remains essentially constant with time,defining the accelerations as a function of time then also defines the dynamic forces as a function of time. Stress,in turn, will be a function of both applied and inerials forces . since engineering design is charged with creating systems which will not fail during their expected service life,the goal is to keep stresses within acceptable limits for the materials chosen and the environmental conditions encountered. This obvisely requies that all system forces be defined and kept within desired limits. In mechinery , the largest forces encountered are often those due to the dynamics of the machine itself. These dynamic forces are proportional to acceletation, which brings us back to kinematics ,the foundation of mechanical design. Very basic and early decisions in the design process invovling kinematics wii prove troublesome and perform badly.Any mechanical system can be classified according to the number of degree of freedom which it possesses.the systems DOF is equal to the number of independent parameters which are needed to uniquely define its posion in space at any instant of time.A rigid body free to move within a reference frame will ,in the general case, have complex motoin, which is simultaneous combination of rotation and translation. In three-dimensional space , there may be rotation about any axis and also simultaneous translation which can be resoled into componention along three axes, in a plane ,or two-dimentional space ,complex motion becomes a combination of simultaneous along two axes in the plane. For simplicity ,we will limit our present discusstions to the case of planar motion:Pure rotation the body pessesses one point (center of rotation)which has no motion with respect to the stationary frame of reference. All other points on the body describe arcs about that center. A reference line drawn on the body through the center changes only its angulai orientation.Pure translation all points on the body describe parallel paths. A reference line drawn on the body changes its linear posion but does not change its angular oriention.Complex motion a simulaneous combination of rotion and translationm . anyreference line drawn on the body will change both its linear pisition and its angular orientation. Points on the body will travel non-parallel paths ,and there will be , at every instant , a center of rotation , which will continuously change location.Linkages are the bacis building blocks of all mechanisms. All common forms of mechanisms (cams , gears ,belts , chains ) are in fact variations of linkages. Linkages are made up of links and kinematic pairs.A link is an (assumed)rigid body which possesses at least two or more links (at their nodes), which connection allows some motion, or potential motion,between the connected links.The term lower pair is used to describe jionts with surface contact , as with a pin surrounded by a hole. The term higher pair is used to describe jionts with point or line contact ,but if there is any clerance between pin and hole (as there must be for motion ),so-called surface contact in the pin jiont actually becomes line contact , as the pin contacts actually has contact only at discrete points , which are the tops of the surfaces’asperities. The main practical advantage of lower pairs over higher pairs is their better ability to trap lubricant between their envloping surface. This ie especially true for the rotating pin joint. The lubricant is more easily squeezed out of a higher pair .as s result , the pin joint is preferred for low wear and long life .When designing machinery, we must first do a complete kinematic analysis of our design , in order to obtain information about the acceleration of the moving parts .we next want te use newton’s second law to caculate the dynamic forces, but to do so we need to know the masses of all the moving parts which have these known acceletations. These parts do not exit yet ! as with any design in order to make a first pass at the caculation . we will then have to itnerate to better an better solutions as we generate more information.A first estimate of your parts’masses can be obtained by assuming some reasonable shapes and size for all the parts and choosing approriate materials. Then caculate the volume of each part and multipy its volume by material’s mass density (not weight density ) to obtain a first approximation of its mass . these mass values can then be used in Newton’s equation.How will we know whether our chosen sizes and shapes of links are even acceptable, let alone optimal ? unfortunately , we will not know untill we have carried the computations all the way through a complete stress and deflection analysis of the parts. It it often the case ,especially with long , thin elements such as shafts or slender links , that the deflections of the parts, redesign them ,and repeat the force ,stress ,and deflection analysis . design is , unavoidably ,an iterative process .It is also worth nothing that ,unlike a static force situation in which a failed design might be fixed by adding more mass to the part to strenthen it ,to do so in a dynamic force situation can have a deleterious effect . more mass with the same acceleration will generate even higher forcesand thus higher stresses ! the machine desiger often need to remove mass (in the right places) form parts in order to reduce the stesses and deflections due to F=ma, thus the designer needs to have a good understanding of both material properties and stess and deflection analysis to properlyshape and size parts for minimum mass while maximzing the strength and stiffness needed to withstand the dynamic forces.One of the primary considerations in designing any machine or strucre is that the strength must be sufficiently greater than the stress to assure both safety and reliability. To assure that mechanical parts do not fail in service ,it is necessary to learn why they sometimes do fail. Then we shall be able to relate the stresses with the strenths to achieve safety .Ideally, in designing any machine element,the engineer should have at his disposal should have been made on speciments having the same heat treatment ,surface roughness ,and size as the element he prosses to design ;and the tests should be made under exactly the same loading conditions as the part will experience in service . this means that ,if the part is to experience a bending and torsion,it should be tested under combined bending and torsion. Such tests will provide very useful and precise information . they tell the engineer what factor of safety to use and what the reliability is for a given service life .whenever such data are available for design purposes,the engineer can be assure that he is doing the best justified if failure of the part may endanger human life ,or if the part is manufactured in sufficiently large quantities. Automobiles and refrigrerators, for example, have very good reliabilities because the parts are made in such large quantities that they can be thoroughly tested in advance of manufacture , the cost of making these is very low when it is divided by the total number of parts manufactrued.You can now appreciate the following four design categories :(1)failure of the part would endanger human life ,or the part ismade in extremely large quantities ;consequently, an elaborate testingprogram is justified during design .(2)the part is made in large enough quantities so that a moderate serues of tests is feasible.(3)The part is made in such small quantities that testing is not justified at all ; or the design must be completed so rapidlly that there is not enough time for testing.(4) The part has already been designed, manufactured, and tested and found to be unsatisfactory. Analysis is required to understand why the part is unsatisfactory and what to do to improve it .It is with the last three categories that we shall be mostly concerned.this means that the designer will usually have only published values of yield strenth , ultimate strength,and percentage elongation . with this meager information the engieer is expected to design against static and dynamic loads, biaxial and triaxial stress states , high and low temperatures,and large and small parts! The data usually available for design have been obtained from the simpletension test , where the load was applied gradually and the strain given time to develop. Yet these same data must be used in designing parts with complicated dynamic loads applied thousands of times per minute . no wonder machine parts sometimes fail.To sum up, the fundamental problem of the designer is to use the simple tension test data and relate them to the strength of the part , regardless of the stress or the loading situation.It is possible for two metal to have exactly the same strength and hardness, yet one of these metals may have a supeior ability to aborb overloads, because of the property called ductility. Dutility is measured by the percentage elongation which occurs in the material at frature. The usual divding line between ductility and brittleness is 5 percent elongation. Amaterial having less than 5 percent elongation at fracture is said to bebrittle, while one having more is said to be ductile.The elongation of a material is usuallu measured over 50mm gauge length.siece this did not a measure of the actual strain, another method of determining ductility is sometimes used . after the speciman has been fractured, measurements are made of the area of the cross section at the fracture. Ductility can then be expressed as the percentage reduction in cross sectional area.The characteristic of a ductile material which permits it to aborb largeoverloads is an additional safety factot in design. Ductility is also important because it is a measure of that property of a material which permits it to be cold-worked .such operations as bending and drawing are metal-processing operations which require ductile materials.When a materals is to be selected to resist wear , erosion ,or plastic deformaton, hardness is generally the most important property. Several methods of hardness testing are available, depending upon which particular property is most desired. The four hardness numbers in greatest usse are the Brinell, Rockwell,Vickers, and Knoop.Most hardness-testing systems employ a standard load which is applied to a ball or pyramid in contact with the material to be tested. The hardness is an easy property to measure , because the test is nondestructive and test specimens are not required . usually the test can be conducted directly on actual machine element .Virtually all machines contain shafts. The most common shape for shafts is circular and the cross section can be either solid or hollow (hollow shafts can result in weight savings). Rectangular shafts are sometimes used ,as in screw driver bladers ,socket wrenches and control knob stem.A shaft must have adequate torsional strength to transmit torque and not be over stressed. If must also be torsionally stiff enough so that one mounted component does not deviate excessively from its original angular position relative to a second component mounted on the same shaft. Generally speaking,the angle of twist should not exceed one degree in a shaft lengthequal to 20 diameters.Shafts are mounted in bearing and transmit power through such device as gears, pulleys,cams and clutches. These devices introduce forces which attempt to bend the shaft;hence, tha shaft must be rigid enough to prevent overloading of the supporting bearings ,in general, the bending deflection of a shaft should not exceed 0.01 in per ft of length between bearing supports.In addition .the shaft must be able to sustain a combination of bending and torsional loads. Thus an equivalent load must be considered which takes into account both torsion and bending . also ,the allowable stress must contain a factor of safety which includes fatigue, since torsional and bending stress reversals occur.For fiameters less than 3 in ,the usual shaft material is cold-rolled steel containing about 0.4 percent carbon. Shafts ate either cold-rolled or forged in sizes from 3in. to 5 in. for sizes above 5 in. shafts are forged and machined to size . plastic shafts are widely used for light load applications . one advantage of using plastic is safty in electrical applications, since plastic is a poor confuctor of electricity.Components such as gears and pulleys are mounted on shafts by means of key. The design of the key and the corresponding keyway in the shaft must be properly evaluated. For example, stress concentrations occur in shafts due to keyways , and the material removed to form the keyway further weakens the shaft.If shafts are run at critical speeds , severe vibrations can occur which can seriously damage a machine .it is important to know the magnitude of these critical speeds so that they can be avoided. As a general rule of thumb , the difference betweem the operating speed and the critical speed should be at least 20 percent.Many shafts are supported by three or more bearings, which means that the problem is statically indeterminate .text on strenth of materials give methods of soving such problems. The design effort should be in keeping with the economics of a given situation , for example , if one line shaft supported by three or more bearings id needed , it probably would be cheaper to make conservative assumptions as to moments and design it as though it were determinate . the extra cost of an oversize shaft may be less than the extra cost of an elaborate design analysis.Another important aspect of shaft design is the method of directly connecting one shaft to another , this is accomplished by devices such as rigid and flexiable couplings.A coupling is a device for connecting the ends of adjacent shafts. In machine construction , couplings are used to effect a semipermanent connection between adjacent rotating shafts , the connection is permanent in the sense that it is not meant to be broken during the useful life of the machinem , but it can be broken and restored in an emergency or when worn parts are replaced.There are several types of shaft couplings, their characteristics depend on the purpose for which they are used , if an exceptionally long shaft is required in a manufacturing plant or a propeller shaft on a ship , it is made in sections that are coupled together with rigid couplings. A common type of rigid coupling consists of two mating radial flanges that are attached by key driven hubs to the ends of adjacent shaft sections and bolted together through the flanges to form a rigid connection. Alignment of the connected shafts in usually effected by means of a rabbet joint on the face of the flanges.In connecting shafts belonging to separate device ( such as an electric motor and a gearbox),precise aligning of the shafts is difficult and a fkexible coupling is used . this coupling connects the shafts in such a way as to minimize the harmful effects of shafts misalignment of loads and to move freely(float) in the axial diection without interfering with one another . flexiable couplings can also serve to reduce the intensity of shock loads and vibrations transmitted from one shaft to another .中文翻译机械运动和动力学运动学的基本目的是去设计一个机械零件的理想运动,然后再用数学的方法去描绘该零件的位置,速度和加速度,再运用这些参数来设计零件。
机电专业论文英文文献及其中文译文

毕业论文外文文献翻译译文题目:INTEGRATION OF MACHINERY外文资料翻译资料来源:文章名:INTEGRATION OF MACHINERY 《Digital Image Processing》书刊名:作者:Y. Torres J. J. Pavón I. Nieto and J. A.Rodríguez章节:2.4 INTEGRATION OF MACHINERYINTEGRATION OF MACHINERY (From ELECTRICAL AND MACHINERY INDUSTRY)ABSTRACT Machinery was the modern science and technology development inevitable resultthis article has summarized the integration of machinery technology basic outlineand the development background .Summarized the domestic and foreign integration ofmachinery technology present situation has analyzed the integration of machinerytechnology trend of development. Key word:integration of machinery ,technology,present situation ,productt,echnique of manufacture ,trend of development 0. Introduction modern science and technology unceasing development impelleddifferent discipline intersecting enormously with the seepage has caused the projectdomain technological revolution and the transformation .In mechanical engineeringdomain because the microelectronic technology and the computer technology rapiddevelopment and forms to the mechanical industry seepage the integration of machinerycaused the mechanical industry the technical structure the product organizationthe function and the constitution the production method and the management systemhas had the huge change caused the industrial production to enter into quottheintegration of machineryquot by quotthe machinery electrificationquot for the characteristicdevelopment phase. 1. Integration of machinery outline integration of machinery is refers in theorganization new owner function the power function in the information processingfunction and the control function introduces the electronic technology unifies thesystem the mechanism and the computerization design and the software whichconstitutes always to call. The integration of machinery development also has becomeone to have until now own system new discipline not only develops along with thescience and technology but also entrusts with the new content .But its basiccharacteristic may summarize is: The integration of machinery is embarks from thesystem viewpoint synthesis community technologies and so on utilization mechanicaltechnology microelectronic technology automatic control technology computertechnology information technology sensing observation and control technologyelectric power electronic technology connection technology information conversiontechnology as well as software programming technology according to the systemfunction goal and the optimized organization goal reasonable disposition and thelayout various functions unit in multi-purpose high grade redundant reliable inthe low energy consumption significance realize the specific function value andcauses the overall system optimization the systems engineering technology .From thisproduces functional system then becomes an integration of machinery systematic orthe integration of machinery product. Therefore quotintegration of machineryquot coveringquottechnologyquot and quotproductquot two aspects .Only is the integration of machinerytechnology is based on the above community technology organic fusion one kind ofcomprehensivetechnology but is not mechanical technical the microelectronictechnology as well as other new technical simple combination pieces together .Thisis the integration of machinery and the machinery adds the machinery electrificationwhich the electricity forms in the concept basic difference .The mechanicalengineering technology has the merely technical to develop the machineryelectrification still was the traditional machinery its main function still wasreplaces with the enlargement physical strength .But after develops the integrationof machinery micro electron installment besides may substitute for certainmechanical parts the original function but also can entrust with many new functionslike the automatic detection the automatic reduction information demonstrate therecord the automatic control and the control automatic diagnosis and the protectionautomatically and so on .Not only namely the integration of machinery product ishumans hand and body extending humans sense organ and the brains look has theintellectualized characteristic is the integration of machinery and the machineryelectrification distinguishes in the function essence. 2. Integration of machinery development condition integration of machinerydevelopment may divide into 3 stages roughly.20th century 60s before for the firststage this stage is called the initial stage .In this time the people determinationnot on own initiative uses the electronic technology the preliminary achievement toconsummate the mechanical product the performance .Specially in Second World Warperiod the war has stimulated the mechanical product and the electronic technologyunion these mechanical and electrical union military technology postwar transferscivilly to postwar economical restoration positive function .Developed and thedevelopment at that time generally speaking also is at the spontaneouscondition .Because at that time the electronic technology development not yetachieved certain level mechanical technical and electronic technology union alsonot impossible widespread and thorough development already developed the productwas also unable to promote massively. The 20th century 7080 ages for the second stagemay be called the vigorous development stage .This time the computer technologythe control technology the communication development has laid the technology basefor the integration of machinery development . Large-scale ultra large scaleintegrated circuit and microcomputer swift and violent development has provided thefull material base for the integration of machinery development .This timecharacteristic is :①A mechatronics word first generally is accepted in Japanprobably obtains the quite widespread acknowledgment to 1980s last stages in theworldwide scale ②The integration of machinery technology and the product obtainedthe enormous development ③The various countries start to the integration ofmachinery technology and the product give the very big attention and the support.1990s later periods started the integration of machinery technology the new stagewhich makes great strides forward to the intellectualized direction the integrationof machinery enters the thorough development time .At the same time optics thecommunication and so on entered the integration of machinery processes thetechnology also zhan to appear tiny in the integration of machinery the footappeared the light integration of machinery and the micro integration of machineryand so on the new branch On the other hand to the integration ofmachinery systemmodeling design the analysis and the integrated method the integration ofmachinery discipline system and the trend of development has all conducted thethorough research .At the same time because the hugeprogress which domains and so on artificial intelligence technology neural networktechnology and optical fiber technology obtain opened the development vast worldfor the integration of machinery technology .These research will urge theintegration of machinery further to establish the integrity the foundation and formsthe integrity gradually the scientific system. Our country is only then starts fromthe beginning of 1980s in this aspect to study with the application .The State Councilhad been established the integration of machinery leading group and lists as quot863plansquot this technology .When formulated quot95quot the plan and in 2010 developed thesummary had considered fully on international the influence which and possiblybrought from this about the integration of machinery technology developmenttrend .Many universities colleges and institutes the development facility and somelarge and middle scale enterprises have done the massive work to this technicaldevelopment and the application does not yield certain result but and so on theadvanced countries compared with Japan still has the suitable disparity. 3. Integration of machinery trend of development integrations of machinery arethe collection machinery the electron optics the control the computer theinformation and so on the multi-disciplinary overlapping syntheses its developmentand the progress rely on and promote the correlation technology development and theprogress .Therefore the integration of machinery main development direction is asfollows: 3.1 Intellectualized intellectualizations are 21st century integration ofmachinery technological development important development directions .Theartificial intelligence obtains day by day in the integration of machineryconstructors research takes the robot and the numerical control engine bedintellectualization is the important application .Here said quottheintellectualizationquot is to the machine behavior description is in the control theoryfoundation the absorption artificial intelligence the operations research thecomputer science the fuzzy mathematics the psychology the physiology and the chaosdynamics and so on the new thought the new method simulate the human intelligenceenable it to have abilities and so on judgment inference logical thinkingindependent decision-making obtains the higher control goal in order to .Indeedenable the integration of machinery product to have with the human identicalintelligence is not impossible also is nonessential .But the high performancethe high speed microprocessor enable the integration of machinery product to havepreliminary intelligent or humans partial intelligences then is completelypossible and essential. In the modern manufacture process the information has become the controlmanufacture industry the determining factor moreover is the most active actuationfactor .Enhances the manufacture system information-handling capacity to become themodern manufacture science development a key point .As a result of the manufacturesystem information organization and structure multi-level makes the information thegain the integration and the fusion presents draws up the character informationmeasuremulti-dimensional as well as information organizations multi-level .In themanufacture information structural model manufacture information uniform restraintdissemination processing and magnanimous data aspects and so on manufacture knowledgelibrary management all also wait for further break through. Each kind of artificial intelligence tool and the computation intelligence methodpromoted the manufacture intelligence development in the manufacture widespreadapplication .A kind based on the biological evolution algorithm computationintelligent agent in includes thescheduling problem in the combination optimization solution area of technologyreceives the more and more universal attention hopefully completes the combinationoptimization question when the manufacture the solution speed and the solutionprecision aspect breaks through the question scale in pairs the restriction .Themanufacture intelligence also displays in: The intelligent dispatch the intelligentdesign the intelligent processing the robot study the intelligent control theintelligent craft plan the intelligent diagnosis and so on are various These question key breakthrough may form the product innovation the basicresearch system. Between 2 modern mechanical engineering front science differentscience overlapping fusion will have the new science accumulation the economicaldevelopment and societys progress has had the new request and the expectation tothe science and technology thus will form the front science .The front science alsohas solved and between the solution scientific question border area .The front sciencehas the obvious time domain the domain and the dynamic characteristic .The projectfront science distinguished in the general basic science important characteristicis it has covered the key science and technology question which the project actualappeared. Manufacture system is a complex large-scale system for satisfies the manufacturesystem agility the fast response and fast reorganization ability must profit fromthe information science the life sciences and the social sciences and so on themulti-disciplinary research results the exploration manufacture system newarchitecture the manufacture pattern and the manufacture system effectiveoperational mechanism .Makes the system optimization the organizational structureand the good movement condition is makes the system modeling the simulation andthe optimized essential target .Not only the manufacture system new architecture tomakes the enterprise the agility and may reorganize ability to the demand responseability to have the vital significance moreover to made the enterprise first floorproduction equipment the flexibility and may dynamic reorganization ability set ahigher request .The biological manufacture view more and more many is introduced themanufacture system satisfies the manufacture system new request. The study organizes and circulates method and technique of complicated systemfrom the biological phenomenon is a valid exit which will solve many hard nut tocracks that manufacturing industry face from now on currently .Imitating to livingwhat manufacturing point is mimicry living creature organ of from the organizationfrom match more from growth with from evolution etc. function structure and circulatemode of a kind of manufacturing system and manufacturing process. The manufacturing drives in the mechanism under continuously by ones ownperfect raise on organizing structure and circulating modeand thus to adapt theprocess ofwith ability for the environment .For from descend but the last productproceed together a design and make a craft rules the auto of the distance born producesystem of dynamic state reorganization and product and manufacturing the system tendautomatically excellent provided theories foundation and carry out acondition .Imitate to living a manufacturing to belong to manufacturing science andlife science ofquotthe far good luck is miscellaneous to hand overquot it will produceto the manufacturing industry for 21 centuries huge of influence .机电一体化摘要机电一体化是现代科学技术发展的必然结果本文简述了机电一体化技术的基本概要和发展背景。
Kinematics of Machinery

英汉对照:Kinematics of Machinery机械运动学10.1 Introduction .Because motion is inherent in machinery; kinematic quantities such as velocity and acceleration are of engineering importance in the analysis and design of machine components. Kinematic values in machines have reached extraordinary magnitudes. Rotative speeds, once considered high at 10,000r/min, are approaching 100,000r/min; large rotors of jet engines operate at 10,00010.1介绍。
因为运动是机械所固有的,运动学参数例如速度和加速度等工程参数在分析与设计中的机械零件中起到了很重要的作用。
运动的数值在机械中已经起到了特别的重要性。
转动速度,一度被视为高于10000转/分钟,接近100000转/分钟,大转子喷气发动机运转速度在10000to 15,000r/min, and small turbine wheels rotate at 30,000到15000转/分钟,和小汽轮机的轮子转动速度为30000to 60,000r/min.到60000转/分钟。
Size and rotative speed in rotors are related such that such that the smaller the size the greater the allowable rotative speed. A more basic quantity in rotors is peripheral speeds, which depends on rotative speed and size .Peripheral speeds in turbo machinery are reaching 大小和转子旋转速度是相关的,这样,较小的规模能够允许有更大的转动速度。
机械类外文文献及翻译
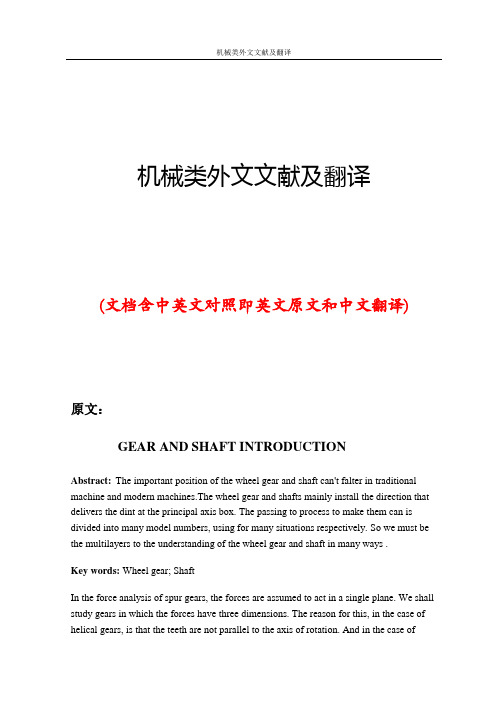
机械类外文文献及翻译(文档含中英文对照即英文原文和中文翻译)原文:GEAR AND SHAFT INTRODUCTIONAbstract:The important position of the wheel gear and shaft can't falter in traditional machine and modern machines.The wheel gear and shafts mainly install the direction that delivers the dint at the principal axis box. The passing to process to make them can is divided into many model numbers, using for many situations respectively. So we must be the multilayers to the understanding of the wheel gear and shaft in many ways .Key words: Wheel gear; ShaftIn the force analysis of spur gears, the forces are assumed to act in a single plane. We shall study gears in which the forces have three dimensions. The reason for this, in the case of helical gears, is that the teeth are not parallel to the axis of rotation. And in the case ofbevel gears, the rotational axes are not parallel to each other. There are also other reasons, as we shall learn.Helical gears are used to transmit motion between parallel shafts. The helix angle is the same on each gear, but one gear must have a right-hand helix and the other a left-hand helix. The shape of the tooth is an involute helicoid. If a piece of paper cut in the shape of a parallelogram is wrapped around a cylinder, the angular edge of the paper becomes a helix. If we unwind this paper, each point on the angular edge generates an involute curve. The surface obtained when every point on the edge generates an involute is called an involute helicoid.The initial contact of spur-gear teeth is a line extending all the way across the face of the tooth. The initial contact of helical gear teeth is a point, which changes into a line as the teeth come into more engagement. In spur gears the line of contact is parallel to the axis of the rotation; in helical gears, the line is diagonal across the face of the tooth. It is this gradual of the teeth and the smooth transfer of load from one tooth to another, which give helical gears the ability to transmit heavy loads at high speeds. Helical gears subject the shaft bearings to both radial and thrust loads. When the thrust loads become high or are objectionable for other reasons, it may be desirable to use double helical gears. A double helical gear (herringbone) is equivalent to two helical gears of opposite hand, mounted side by side on the same shaft. They develop opposite thrust reactions and thus cancel out the thrust load. When two or more single helical gears are mounted on the same shaft, the hand of the gears should be selected so as to produce the minimum thrust load.Crossed-helical, or spiral, gears are those in which the shaft centerlines are neither parallel nor intersecting. The teeth of crossed-helical fears have point contact with each other, which changes to line contact as the gears wear in. For this reason they will carry out very small loads and are mainly for instrumental applications, and are definitely not recommended for use in the transmission of power. There is on difference between a crossed heli : cal gear and a helical gear until they are mounted in mesh with each other. They are manufactured in the same way. A pair of meshed crossed helical gears usually have the same hand; that is ,a right-hand driver goes with a right-hand driven. In the design of crossed-helical gears, the minimum sliding velocity is obtained when the helix angle areequal. However, when the helix angle are not equal, the gear with the larger helix angle should be used as the driver if both gears have the same hand.Worm gears are similar to crossed helical gears. The pinion or worm has a small number of teeth, usually one to four, and since they completely wrap around the pitch cylinder they are called threads. Its mating gear is called a worm gear, which is not a true helical gear. A worm and worm gear are used to provide a high angular-velocity reduction between nonintersecting shafts which are usually at right angle. The worm gear is not a helical gear because its face is made concave to fit the curvature of the worm in order to provide line contact instead of point contact. However, a disadvantage of worm gearing is the high sliding velocities across the teeth, the same as with crossed helical gears.Worm gearing are either single or double enveloping. A single-enveloping gearing is onein which the gear wraps around or partially encloses the worm.. A gearing in which each element partially encloses the other is, of course, a double-enveloping worm gearing. The important difference between the two is that area contact exists between the teeth of double-enveloping gears while only line contact between those of single-enveloping gears. The worm and worm gear of a set have the same hand of helix as for crossed helical gears, but the helix angles are usually quite different. The helix angle on the worm is generally quite large, and that on the gear very small. Because of this, it is usual to specify the lead angle on the worm, which is the complement of the worm helix angle, and the helix angle on the gear; the two angles are equal for a 0-deg. Shaft angle.When gears are to be used to transmit motion between intersecting shaft, some of bevel gear is required. Although bevel gear are usually made for a shaft angle of 0 deg. They may be produced for almost any shaft angle. The teeth may be cast, milled, or generated. Only the generated teeth may be classed as accurate. In a typical bevel gear mounting, one of the gear is often mounted outboard of the bearing. This means that shaft deflection can be more pronounced and have a greater effect on the contact of teeth. Another difficulty, which occurs in predicting the stress in bevel-gear teeth, is the fact the teeth are tapered.Straight bevel gears are easy to design and simple to manufacture and give very good results in service if they are mounted accurately and positively. As in the case of squr gears, however, they become noisy at higher values of the pitch-line velocity. In these cases it is often go : od design practice to go to the spiral bevel gear, which is the bevel counterpart of thehelical gear. As in the case of helical gears, spiral bevel gears give a much smoother tooth action than straight bevel gears, and hence are useful where high speed are encountered.It is frequently desirable, as in the case of automotive differential applications, to have gearing similar to bevel gears but with the shaft offset. Such gears are called hypoid gears because their pitch surfaces are hyperboloids of revolution. The tooth action between such gears is a combination of rolling and sliding along a straight line and has much in common with that of worm gears.A shaft is a rotating or stationary member, usually of circular cross section, having mounted upon it such elementsas gears, pulleys, flywheels, cranks, sprockets, and other power-transmission elements. Shaft may be subjected to bending, tension, compression, or torsional loads, acting singly or in combination with one another. When they are combined, one may expect to find both static and fatigue strength to be important design considerations, since a single shaft may be subjected to static stresses, completely reversed, and repeated stresses, all acting at the same time.The word “shaft” covers numerous v ariations, such as axles and spindles. Anaxle is a shaft, wither stationary or rotating, nor subjected to torsion load. A shirt rotating shaft is often called a spindle.When either the lateral or the torsional deflection of a shaft must be held to close limits, the shaft must be sized on the basis of deflection before analyzing the stresses. The reason for this is that, if the shaft is made stiff enough so that the deflection is not too large, it is probable that the resulting stresses will be safe. But by no means should the designer assume that they are safe; it is almost always necessary to calculate them so that he knows they are within acceptable limits. Whenever possible, the power-transmission elements, such as gears or pullets, should be located close to the supporting bearings, This reduces the bending moment, and hence the deflection and bending stress.Although the von Mises-Hencky-Goodman method is difficult to use in design of shaft, it probably comes closest to predicting actual failure. Thus it is a good way of checking a shaft that has already been designed or of discovering why a particular shaft has failed in service. Furthermore, there are a considerable number of shaft-design problems in which the dimension are pretty well limited by other considerations, such as rigidity, and it is only necessary for the designer to discover something about the fillet sizes, heat-treatment,and surface finish and whether or not shot peening is necessary in order to achieve the required life and reliability.Because of the similarity of their functions, clutches and brakes are treated together. In a simplified dynamic representation of a friction clutch, or brake, two in : ertias I and I traveling at the respective angular velocities W and W, one of which may be zero in the case of brake, are to be brought to the same speed by engaging the clutch or brake. Slippage occurs because the two elements are running at different speeds and energy is dissipated during actuation, resulting in a temperature rise. In analyzing the performance of these devices we shall be interested in the actuating force, the torque transmitted, the energy loss and the temperature rise. The torque transmitted is related to the actuating force, the coefficient of friction, and the geometry of the clutch or brake. This is problem in static, which will have to be studied separately for eath geometric configuration. However, temperature rise is related to energy loss and can be studied without regard to the type of brake or clutch because the geometry of interest is the heat-dissipating surfaces. The various types of clutches and brakes may be classified as fllows:. Rim type with internally expanding shoes. Rim type with externally contracting shoes. Band type. Disk or axial type. Cone type. Miscellaneous typeThe analysis of all type of friction clutches and brakes use the same general procedure. The following step are necessary:. Assume or determine the distribution of pressure on the frictional surfaces.. Find a relation between the maximum pressure and the pressure at any point. Apply the condition of statical equilibrium to find (a) the actuating force, (b) the torque, and (c) the support reactions.Miscellaneous clutches include several types, such as the positive-contact clutches, overload-release clutches, overrunning clutches, magnetic fluid clutches, and others.A positive-contact clutch consists of a shift lever and two jaws. The greatest differences between the various types of positive clutches are concerned with the design of the jaws. To provide a longer period of time for shift action during engagement, the jaws may be ratchet-shaped, or gear-tooth-shaped. Sometimes a great many teeth or jaws are used, and they may be cut either circumferentially, so that they engage by cylindrical mating, or on the faces of the mating elements.Although positive clutches are not used to the extent of the frictional-contact type, they do have important applications where synchronous operation is required.Devices such as linear drives or motor-operated screw drivers must run to definite limit and then come to a stop. An overload-release type of clutch is required for these applications. These clutches are usually spring-loaded so as to release at a predetermined toque. The clicking sound which is heard when the overload point is reached is considered to be a desirable signal.An overrunning clutch or coupling permits the driven member of a machine to “freewheel” or “overrun” bec ause the driver is stopped or because another source of power increase the speed of the driven. This : type of clutch usually uses rollers or balls mounted between an outer sleeve and an inner member having flats machined around the periphery. Driving action is obtained by wedging the rollers between the sleeve and the flats. The clutch is therefore equivalent to a pawl and ratchet with an infinite number of teeth.Magnetic fluid clutch or brake is a relatively new development which has two parallel magnetic plates. Between these plates is a lubricated magnetic powder mixture. An electromagnetic coil is inserted somewhere in the magnetic circuit. By varying the excitation to this coil, the shearing strength of the magnetic fluid mixture may be accurately controlled. Thus any condition from a full slip to a frozen lockup may be obtained.齿轮和轴的介绍摘要:在传统机械和现代机械中齿轮和轴的重要地位是不可动摇的。
机械工程专业外文文献及翻译
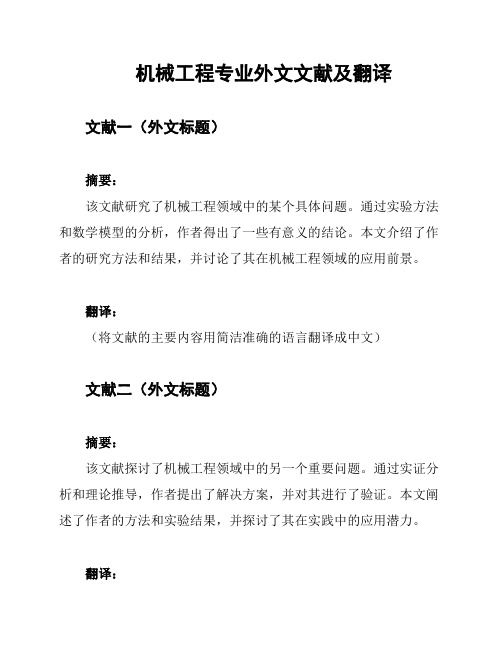
机械工程专业外文文献及翻译文献一(外文标题)
摘要:
该文献研究了机械工程领域中的某个具体问题。
通过实验方法和数学模型的分析,作者得出了一些有意义的结论。
本文介绍了作者的研究方法和结果,并讨论了其在机械工程领域的应用前景。
翻译:
(将文献的主要内容用简洁准确的语言翻译成中文)
文献二(外文标题)
摘要:
该文献探讨了机械工程领域中的另一个重要问题。
通过实证分析和理论推导,作者提出了解决方案,并对其进行了验证。
本文阐述了作者的方法和实验结果,并探讨了其在实践中的应用潜力。
翻译:
(将文献的主要内容用简洁准确的语言翻译成中文)
文献三(外文标题)
摘要:
该文献研究了机械工程领域中的另一个新颖课题。
作者通过数
值模拟和实验验证,得出了一些有趣的发现。
本文介绍了作者的研
究过程和结果,并讨论了其对机械工程领域的影响。
翻译:
(将文献的主要内容用简洁准确的语言翻译成中文)
总结
本文档介绍了三篇机械工程专业的外文文献,包括摘要和翻译。
这些文献都对机械工程领域中的不同问题进行了研究,并提出了相
关的解决方案和发现。
希望这些文献能为机械工程专业的学生和研
究人员提供有价值的参考和启发。
机械外文文献及翻译
与机械相关的外文及翻译Multidisciplinary Design Optimization of Modular Industrial Robots by Utilizing High Level CAD Templates1、IntroductionIn the design of complex and tightly integrated engineering products, it is essential to be able to handle interactions between different subsystems of multidisciplinary nature [1]. To achieve an optimal design, a product must be treated as a complete system instead of developing subsystems independently [2]. MDO has been established as a convincing concurrent design optimization technique in development of such complex products [3,4].Furthermore, it has been pointed out that, regardless of discipline, basically all analyses require information that has to be extracted from a geometry model [5]. Hence, according to Bow-cutt [1], in order to enable integrated design analysis and optimization it is of vital importance to be able to integrate an automated parametric geometry generation system into the design framework. The automated geometry generation is a key enabler for so-called geometry-in-the-loop[6] multidisciplinary design frameworks, where the CAD geometries can serve as framework integrators for other engineering tools.To eliminate noncreative work, methods for creation and automatic generation of HLCt have been suggested by Tarkian [7].The principle of high HLCts is similar to high level primitives(HLP) suggested by La Rocca and van Tooren [8], with the exception that HLCts are created and utilized in a CAD environment.Otherwise, the basics of both HLP and HLCt can, as suggested byLa Rocca, be compared to parametric LEGOV Rblocks containing a set of design and analysis parameters. These are produced and stored in libraries, giving engineers or a computer agent the possibility to first topologically select the templates and then modify the morphology, meaning theshape,of each template parametrically.2、Multidisciplinary Design FrameworkMDO is a “systematic approach to design space exploration”[17], the implementation of which allows the designer to map the interdisciplinary relations that exist in a system. In this work, the MDO framework consists of a geometry model, a finite element(FE) model, a dynamic model and a basic cost model. The geometry model provides the analysis tools with geometric input. The dynamic model requires mass properties such as mass, center of gravity, and inertia. The FE model needs the meshed geometry of the robot as well as the force and torque interactions based on results of dynamic simulations.High fidelity models require an extensive evaluation time which has be taken into account. This shortcoming is addressed by applying surrogate models for the FE and the CAD models. The models are briefly presented below. 2.1 High Level CAD Template—Geometry ModelTraditionally, parametric CAD is mainly focused on morphological modifications of the geometry. However, there is a limit to morphological parameterization as follows:•The geometries cannot be radically modified.•Increased geometric complexity greatly increases parameterization complexity.The geometry model of the robot is generated with presaved HLCts, created in CATIA V5. These are topologically instantiated with unique internal design variables. Topological parameterization allows deletion, modification, and addition of geometricelements which leads to a much greater design space captured.Three types of HLCts are used to define the industrial robot topologically; Datum HLCt which includes wireframe references required for placement for the Actuator HLCTs and Structure HLCts, as seen Fig.2.Fig. 2 An industrial robot (left) and a modular industrial robot(right) The names of the references that must be provided for each HLCt instantiation are stored in the knowledge base (see Appen-dix A.4), which is searched through by the inference engine. In Appendix A, pseudocode examples describes how the references are retrieved and how they are stored in the knowledge base.The process starts by the user defining the number of degrees of freedom (DOF) of the robot (see Fig. 3) and is repeated until the number of axis (i) is equal to the user defined DOF.In order to instantiate the first Structure HLCt, two Datum and two actuator instances are needed. References from the two Datum instances help orienting the structure in space, while the geometries of the actuator instances, at both ends of the link, are used to construct the actuator attachments, as seen in Figs. 2 and 3. For the remaining links, only one new instance of both datum and actuator HLCts are required, since the datum and actuator instances from adjacent links are already available.Appendix A.2 shows a pseudocode example of an instantiation function. The first instantiated datum HLCt is defined with reference to the absolute coordinate system. The remaining datum HLCt instances are placed in a sequential order, where the coordinate system of previous instances is used as reference for defining the position in space according to user inputs (see also AppendixA.3). Furthermore, the type of each actuator and structure instance is user defined.Fig. 3 The high level CAD template instantiation process Since it is possible to create new HLCts in the utilized CAD tool, the users are not forced to merely choose from the templates available. New HLCts can be created, placed in the database and parametrically inserted into the models.2.2 Dynamic ModelThe objective of performing dynamic simulation of a robot is to evaluate system performance, such as predicting acceleration and time performance, but it also yields loads on each actuated axis, needed for actuator lifetime calculations and subsequent stress analysis based on FE calculations. Thedynamic model in the outlined framework is developed in Modelica using Dymola, and it constitutes a seven-axis robot arm based on the Modelica Standard library [18].The dynamic model receives input from the geometry model,as well as providing output to the FE model, which is further described in Sec. 2.3. However, to better understand the couplings between the models, the Newton –Euler formulation will be briefly discussed. In this formulation, the link velocities and acceleration are iteratively computed, forward recursivelyWhen the kinematic properties are computed, the force and torque interactions between the links are computed backward recursively from the last to the first link2.3 FE Surrogate ModelTo compute the structural strength of the robot, FE models for each robot link is created utilizing CATIA V5, see Fig. 4. For each HLCt, mesh and boundary conditions are manually preprocessed in order to allow for subsequent automation for FE-model creation. The time spent on preprocessing each FE-model is thus extensive. Nonetheless, the obtained parametric FE-model paves way for automated evaluation of a wide span of concepts. Each robot link is evaluated separately with the load conditions extracted from the dynamicmodel. The force (fi-11and fi) and torque (ţi-1and ti) are applied on the surfaceswhere the actuators are attached.2.4 Geometric Surrogate Models.Surrogate models are numerically efficient models to determine the relation between inputs and o utputs of a model [19]. The input variables for the proposed application are the morphological variables thickness and link height as well as a topological variable actuator type. The outputs of the surrogate models are mass m, Inertia I, and center of gravity ri,ci.To identify the most suitable type of surrogate model for the outlined problem, a range of surrogate models types are created and evaluated using 50 samples. The precision of each surrogate model is compared with the values of the original model with 20 new samples. The comparison is made using the relative average absolute error (RAAE) and relative maximum absolute error (RMAE) as specified by Shan et al. [20], as well as the normalized root mean square error (NRMSE), calculated as seen in Eq. (3). All precision metrics are desired to be as low as possible, since low values mean that the surrogate model is accurateThe resulting precision metrics can be seen in Appendix B and the general conclusion is that anisotropic kriging [21], neural networks [22], and radialbasis functions [23] are the most promising surrogate models. To investigate the impact of increasing number of samples, additional surrogate models of those three are fitted using 100 samples, and the results compiled in Appendix B. The resulting NRMSEs for 50 and 100 samples for anistotropic kriging, neural networks, and radial basis functions can be seen in Fig.5. The figures inside the parentheses indicate the number of samples used to fit the surrogate models.Fig. 5 Graph of the NRMSEs for different surrogate models,fitted using 50 and 100 samplesAccording to Fig. 5, anisotropic kriging outperforms the other surrogate models and the doubling of the number of samples usedfor fitting the surrogate model increases the precision dramatically.2.5 FE Surrogate ModelsFor generating FE surrogate models, the anisotropic kriging was also proven to be the most accurate compared to the methods evaluated in Sec. 2.4. Here, one surrogate model is created for each link. Inputs are thickness,actuators, force (fi-11and fi) and torque (ţi-1and ti). The output for eachsurrogate model is maximum stress (MS).A mean error of approximately 9% is reached when running 1400 samples for each link. The reason for the vast number of samples, compared to geometry surrogate models, has to do with a much larger design space.利用高水平CAD模板进行模块化工业机器人的多学科设计优化1 介绍指出,除了规则,基本上所有的分析都需要信息,而这些信息需要从一个几何模型中提取。
机械设计外文文献翻译、中英文翻译、外文翻译
外文原文:Mechanical designAccording to user requirements of special mechanical working principle, structure, movement, power and energy transmission, various parts of the material and shape size, lubrication methods for design, analysis and calculation and mechanical designTranslate them into a specific description to be made based on the workingprocess. Mechanical design is an important part of mechanical engineering, machinery is produced in the first step, is to determine the mechanical properties of the main factors. Mechanical design goal is: in various limited conditions (such as materials, processing ability, theory and calculation method of design of the best machinery ), i.e. to make optimization design. Optimization design to consider the many requirements, generally : the best performance, the minimum cost, the minimum size and weight, use the reliability, minimum consumption and the minimum environmental pollution. These requirements are often contradictory, but their relative importance for the mechanical type and use vary. The designer's task is to weigh up one thing against another according to the specific circumstance, take all factors into consideration, make the design of the mechanical optimal comprehensive technical and economic effect. In the past, optimization design depends on the designer's knowledge, experience and vision. As the base of mechanical engineering theory and the value engineering, systems analysis and other new disciplines in the development, manufacture and use of technical economy the accumulation of data, as well as computer application, optimize gradually abandon the subjective judgment and rely on scientific computing. In the service of different industry different machinery, application of different working principle, requires a different function and characteristic. Industrial machinery design, especially the whole and the entire system of mechanical design, must be attached to the relevant industrial technology to form an independent discipline. So the design of agricultural machinery, mining machinery, textile machinery, automobile design design design, ship design, design of pump, compressor, turbine design, engine design, machine design, professional mechanical design branch. However, many of these professional design and many common technologies, such as the analysis and synthesis of mechanisms, and can analysis and calculation, engineering materials, strength of materials, transmission, lubrication, sealing, and standardization, reliability, process optimization. In addition, there are research design work of the inherent law and the rationality of the design methods and steps of the new design methodology. The mechanical design of the general technology and rational design methodology brings together into an independent, comprehensive mechanical design is mechanical engineering practice and education workers are working hard.A machine quality basically depends on the quality of design. Manufacturing process on the quality of the machine the role, essence is to realize the design requiredquality. Therefore, the machine's design phase is the key decision machine. Mechanical designThe discussion of the design process refers only to the narrow sense of technical design process. It is a creative process, but also a try best to use the successful experience of the job. Be well to the inheritance and innovation to combine, in order to design a high quality machine. As a complete machine, it is a complex system. To improve the design quality, must have a scientific design program. Although it is not possible for a list of valid in all cases only program, but, according to the long term experience, a machine design process basically can be as shown in Table 2- 1. 1for each stage are respectively brief description. ( a ) the planning stage in accordance with the production or life presents the need to design new machines, the planning stage is a stage of preparation. At this time, to design the machines only a vague notion. In the planning stages, to deal with the design of the machine needs to do the full investigation and analysis. Through the analysis, to further clarify the machine the function that should have, and for the subsequent decision proposed by the environmental, economic, and processing time and other aspects of the identified constraints. Based on this, clearly written assignments on the overall requirements and design details, finally forms the design task book, as the stage summary. The design task book generally should include : the machine function, economy and environmental protection estimates, manufacturing requirements with respect to roughly estimate, basic requirements, and completed the task of design is expected duration. At this point, the requirements and conditions in general can only give a reasonable range, but not the exact number. For example can be used must meet the requirements, minimum requirements, hoping to reach the requirements shall be identified.( two) scheme design stage the stage of design play a key role. In this one phase is also fully demonstrated the design work have multiple solutions ( solution ) features. The function of the machine analysis, is to design of the proposed machine function must meet the requirements of the minimum requirements, and hope to achieve the requirements of comprehensive analysis, namely, these functions can be realized, a number of features with no contradiction, can substitute each other. Finally determines the functional parameters, as the basis for further design. In this step, want appropriate processing need and possibility, the ideal and the reality, development goals and the goals may arise between the contradictory problem. To determine the functional parameters, then propose possible solutions, which is made possible by the plan. Seek solution, according to the driving part, a transmission part and execution part are respectively discussed. , more commonly used method is to first from the operative portion began to discuss. Discuss machine execution part, the first is about the working principle of selection. For example, the design and manufacture of screw machine, its working principle can be used in the cylindrical blank by turning thread approach, can also be used in the cylindrical blanks with thread rolling die rolling thread approach. It puts forward two kinds of different working principles. Its working principle is different, of course, the design of the machine will fundamentally different. Special is to be stressed, must continue to research and development of newworking principle. It is an important way of the development of design technology. According to the different working principle, can develop a variety of different execution mechanism scheme. For example, only the thread cutting, can use the workpiece can only rotate and tool for linear motion to the cutting thread ( such as in lathe cutting thread ), also can make the workpiece is fixed and the cutter to rotate and move to the cutting thread ( such as die processing thread ). That is to say, even for the same kind of work principle, also may have several different structural schemes. The original motivation scheme also can have multiple choice. Because of the power supply of the universality and the electric drive technology development, it can be said that the vast majority of the fixed mechanical is preferred choice as prime mover part of motor. The original motivation for transport, the main thermal engineering machinery and agricultural machinery. Even with the motor as the motive, there are both AC and DC selection, high speed and low speed selection. The transmission part of the scheme is more complicated and diverse. For the same transmission task, by a variety of institutions and different body combination to complete. Therefore, if the prime mover Part IV, said the number of possible schemes, N2and N3respectively representing the transmission part and the execution part number of possible schemes, then the machine the overall number of possible schemes of Ni x N2x N3. The above is only on the machine is composed of three main parts to discuss the. Sometimes, also considering the configuration assistant system, in this regard, books no longer discuss. In so many programmes, technically feasible only a few. On the several feasible solutions, from technology and economy and environmental protection and other aspects of a comprehensive evaluation. Evaluation of the method are many, now with economic evaluation for example omitted description. According to the economic evaluation, it is necessary to take into account the design and manufacture of economy, should cost taken into account when using economy. If the machine structure is more complex, its design and manufacture cost is relatively increased, but its function will be more complete, productivity is higher, so the use of economy is also good. In turn, the structure is relatively simple, the function is not complete machinery, design and manufacturing cost is less, but the use of cost will increase. Evaluation of structural scheme design and manufacturing economy, can also be used to represent the cost of unit efficiency. For example, the unit output power cost, unit cost. Machine evaluation, but also on the machine reliability analysis, the reliability as an evaluation index. From the point of view of reliability, the blind pursuit of complex structure is often not wise. Generally speaking, the system is more complex, then the system reliability is lower. In order to improve the reliability of complex systems, it is necessary to increase the parallel system, which will inevitably increase the cost of the machine. The environmental protection is also design must be carefully considered important aspects. Have a bad effect on the environment of the technical scheme, must detailed analysis, and puts forward the technical maturity of the solution. Through the evaluation, the final decision, according to determine a next step technology design of the schematic diagram or kinematic diagram of mechanism. In the program design phase, to correctly handle the relationship between reference and innovation. Similar machines ought to draw lessons from the successful precedent,originally weak and inconsistent with the current task demands of the part should be improved or changed. We should not only actively innovation, against conservative and copy the original design, but also against a novelty and reasonable original experience abandoned the two wrong tendencies.( three) the technical design stage design goal was to generate assembly sketches and assembly sketches. The sketch design identified the components and parts of the form and basic size, including connections between components, spare, parts of the form and basic size. The final drawing parts drawing, parts and assembly drawings and assembly drawings. In order to determine the main parts of the basic size, must do the following:1) the kinematic design of machines. According to determine the structure scheme, determine the driver parameters ( power, speed, linear speed etc. ). Then do the kinematics calculation, thereby determining the motion components of movement parameters ( speed, velocity, acceleration ). 2) the machine dynamics calculation. Combined with the structure and motion parameters, calculation of the main part of the load size and characteristics. The calculated load, the part is designed, which is applied to parts of the nominal ( or nominal ) load. 3) parts of the working capability design. The known major parts by the nominal load size and characteristics, can be zero, parts of the preliminary design. The designs are based on the ability to work standards, should be zero, parts of the general failure situation, job characteristics, environmental conditions and reasonably develop, generally have the strength, stiffness, vibration, life criterion. Through calculation and comparison, then decided to spare, parts of the basic size. 4) assembly sketches and general assembly sketch design. According to the main components, the basic size, design a component assembly sketches and assembly sketches. The sketch of all parts of the shape and size of the structured design. In this step, need good coordination among the various parts of the structure and size, to consider a comprehensive design of zero, parts of the process of the structure, so that all the parts have the most reasonable configuration. 5) the main parts of the check. There are some parts, in the above third ) step due to the specific structure of undetermined, difficult to conduct detailed work capacity calculation, we can only do a preliminary calculation and design. In the draw assembly design and assembly sketches, all parts of the structure and size are known, the mutually abutting the relations between components also known as. Only then, can be more accurately determined action on the part of load, decisions affecting parts working ability detail factor. Only on this condition, it can and must be for something important or shape and stress condition of complex parts for accurate calculation of. According to the check results, repeatedly modify parts of the structure and size, until satisfied. In the technical design of the various steps in, nearly thirty or forty years with the development of the optimization design technology, more and more shows it can make the selection of structural parameters to achieve the best capacity. Some new numerical method, such as finite element method, can make previously difficult to quantitative calculation problems in obtaining excellent approximation calculation results. For a few very important, the structure is complex and expensive parts, where necessary, must use the model test method to the design, namely according to the preliminary design drawings to create a model, through the experiment, to find out theweak parts of the structure or the redundant section size, thus enhance or reduce the modification to the original design, finally achieving the perfect degree. Mechanical reliability theory for the technical design stage, according to the viewpoint of reliability design of zero, parts of structure and its parameters to make it meet the requirement of reliability evaluation, put forward the improvement design is proposed, which can further improve the quality of machine design. These new design methods and concepts, shall, should be applied in the design and promotion, make get corresponding development. Sketch design completed, according to the sketch has identified parts of basic size, design parts drawing. At this time, there are still a large number of parts structure details to be examined and determined. Design work plan, full consideration should be given to the processing of parts and assembly process, parts during machining process and processing after completion of the inspection requirements and implementation methods. Some details of the arrangement if the parts work ability was worth considering influence, must go back to check the work ability. Finally draw out in addition to the standard outside of all parts of the map. According to the final shape of the parts of the structure and size, to draw the part and assembly drawings and assembly drawings. Through this work, can check out the detail drawings may be hidden in the size and structural errors. People regard this work popularly called paper assembly.( four) the preparation of technical documents phase technology file types, commonly used in the machine design brochures, manuals, and other standard parts list. Design calculation specification, should include the scheme selection and technical design all the conclusions of the content. Preparation for users of machine instructions, should introduce the users machine performance parameters, operation methods, daily maintenance and simple repair method, spare parts catalog. Other technical documents, such as inspection single, purchased parts list, acceptance, as needed and not be compiled. ( five) the computer application in mechanical design with the development of computer technology, the computer in the mechanical design has been increasingly widely used, and there have been many efficient design, analysis software. It can be used in the design phase of projects, can be of different includes large and complex project structural strength, stiffness and dynamic characteristics of precision analysis. At the same time, also in the computer to build virtual prototype, using virtual prototype simulation to verify the design, which realizes the design phase fully assess the feasibility of the design. Can say, the computer technology in machinery design promotion has already changed mechanical design process, it enhances the design quality and efficiency advantages is difficult to estimate. The above briefly introduced the machine design program. Broadly speaking, in the machine manufacture process, appear likely at any time due to technical reasons for modifying the design condition. If you want to modify, should follow certain procedures. Machine factory, should have planned to carry out investigation; in addition, users in the use of the process will also give the design or manufacture sector feedback problems. Design department according to these information, through the analysis, it is also possible for the original design was modified, even remodel. These work, although generalized also belong to design program components, butbelongs to another level of problems, this book will not discuss its specific content. But as design worker, should have a strong sense of social responsibility, to my vision extends into the manufacture, use and waste utilization of total process, repeated constantly improve the design, in order to make the quality of the machine to continue to improve, to better meet the needs of production and lifeAt the beginning of the design before, must make the design task. When the design task is more complex, using three general stages of design, the preliminary design, technical design and working drawing design; when the task is relatively simple, such as the simple mechanical model design, general machinery inherited design or variant design, it will start a design to achieve technical design depth, after review, modification and approval to do working drawing design, and become two stage design. In the three stage design in the preliminary design stage, design of the main steps of : determining the working principle and basic structure, motion design, main spare parts, drawing design, preliminary master plan, the preliminary design review. In the design phase, the main steps are: according to the review comments to modify the design, design of all parts, drawing the new general plan, technical design review. In working drawing design stage, according to the review comments to modify the design, draw all the working drawings and make all technical documents. For the mass or mass production of products, but also shape design. In the design of each step, may be found in the previous step some decided not reasonable, it need to fold back in front of that step, modify the irrational decisions, redo the subsequent design work. 1, making design task it is the preparatory work of the design. Design task is based on the user orders, the market needs and the new research results. Design departments application technology and market information, to be listed options, comparing its advantages and disadvantages, and business departments and users together, formulates the reasonable design target. The new design is particularly important. The goal of the task error will be caused serious damage to the economy, even with the overall failure. 2, determine the working principle and basic structure types such as design task did not make specific provision, designed the first step is to determine the overall program, that is determined by the application of the working principle and the structure types. Such as the design of high power marine diesel engine, the first to determine the two stroke, double action, crosshead, low-speed diesel engine, or by four stroke, single function, medium speed diesel engine. Another example is designed for crushing rock crushing machinery, we must first determine the using extrusion and bending as the main role of the jaw crusher or gyratory crusher, or used to shock as the main role of the single rotor or double rotor impact crusher. 3, exercise design scheme is determined, then the need to apply the mechanism knowledge, choose appropriate institutions in order to obtain the desired motion scheme. The above mentioned jaw crusher on the movable jaw plate to swing into the crushing chamber rock by extrusion, bending and splitting the role and broken, and the swing jaw plate can adopt a double elbow board mechanism of simple swinging, or using a single elbow board mechanism of complex oscillation. In the new design, may need to be integrated with a new mechanism to obtain the required movement, this is often a difficult job. Therefore, designers commonly applied as faras possible the existing and mature mechanism is proposed for sports program. 4, structure design and draw the preliminary general motion design, designers began to carry on the structural design, calculation of the main part of the force, strength, shape, size and weight, and the mapping of the main components, sketch. Then if found out that selection of structure is not feasible, we must adjust or modify structure. At the same time also should be considered a possible cause overheating, excessive wear or vibration part. In this step, the designer through sketching will find each part of the shape, size, such as the proportion of contradiction. In order to enhance or improve certain aspects, may weaken or deterioration on the other hand. Then we must weigh up one thing against another, coordination, in order to achieve the best effect. Sketch by repeatedly revise that initial satisfaction, will be able to draw the preliminary master plan and estimated cost. A preliminary layout strictly according to scale, selection of sufficient view and section. 5, preliminary review of the initial layout drawing, the need to please the type of machinery has experience in the design, manufacture and use of personnel as well as the user or commissioned to design the delegate of the unit to conduct a preliminary examination. A review of results such as that is not designed ( such as weight, volume big, cost is too high, the reliability of structure is the doubt ), shall be to exercise design, and even to other working principle and basic structure. In most cases, to take certain measures to improve design. 6, technology design according to the preliminary examination opinions, to modify the design, and the mapping of all parts and components. On the main parts and components for accurate stress analysis, according to the analysis results of modified parts of the shape, size and other details, and the provisions of material and heat treatment. Determine the machining accuracy of the parts and components and assembly of the assembly conditions. Complete lubrication design, electrical design ( drive and control ). Redraw the map, some important and production machinery can sometimes produce model. Will complete the technical design submitted second review 7, draw working drawings according to second review comments made last modified, can draw formal part drawing, assembly drawing and assembly drawing, writing a parts list, wearing parts list, use the guide and other technical documents. Design responsible person should pay attention to coordinate the parts between the size, check the coupling between tolerance, review some parts of the strength and stiffness. Complete the parts after the start to check the drawings, it is very important work. After careful proofreading to ensure smooth processing assembly drawings. The most reliable method of proofreading is based on drawing good parts drawing heavy draw a general assembly drawing, all contradictions will be shown. In the detail drawing but also the need for two tasks: one is the process of audit, the convenient processing of the parts and the manufacturing cost is reduced the two is the standard audit, so that parts of structure, size, tolerance, heat treatment technology and standard and general parts conform to the standard. 8, trial production and designed for single or small batch production machinery, through the steps to complete the design drawings can be put into production. For batch or lot production machinery, before formal production prototype system to test, function test and identification of, by, then by batch process batch production. In batch production in the problems may also needto design corresponding modification, become available for formal production by using modular design.The design of mechanical parts with many constraints, design criteria design should meet the constraint condition. 1, technical performance standards technical performance includes the function of products, manufacturing and operation status of all property, refers to the static performance, dynamic performance is also used to refer to. For example, the product can transfer power, efficiency, service life, strength, stiffness, friction resistance, wear resistance, thermal stability, vibration characteristics. Technical performance criterion refers to the relevant technical performance to meet the stipulated requirements. For example, the vibration will generate additional dynamic load and stress, especially when the frequency is close to the mechanical systems or parts of the natural frequency, resonance phenomenon will occur, then the amplitude will increase sharply, may lead to the parts and even whole system rapidly damage. Vibration stability criterion is limiting the mechanical systems or parts of the vibration parameters, such as frequency, amplitude, noise in the provisions of the scope of the permit. And as the machine when the fever may cause thermal stress, thermal strain, even will cause thermal damage. Thermal characteristics of guidelines is to restrict the various related thermal parameters ( such as the thermal stress, thermal strain, temperature rise ) in the specified range. 2, standardization and design of mechanical products related to the main standard generally are: the concept of Standardization: involved in the design process of the terminology, symbols, units of measurement shall be in accordance with the standard; objective form standardization: parts, raw materials, equipment and energy structure, size, performance, should be uniform choice. Methods: standardized operation method, measurement method, test method etc should be according to the relevant provisions. Standardization in the entire design process all behavior, must meet the requirements for standardization. Has been released and the design of mechanical parts related standard, from the scope of application of speaking, can be divided into national standards, industry standards and enterprise standards for three grade. From the use of mandatory, can be divided into must be performed and recommended the use of the two kind. 3: reliability, reliability standards for products or components within the prescribed conditions, the expected life to finish regulation function of theprobability of Reliability criterion refers to design products, components or parts should be able to meet the requirements of the reliability requirements in 4, the safety criterion for safety of machinery parts including: Security: defined in terms of external load and within a specified period of time, such as fracture parts not excessive deformation, excessive wear and without loss of stability and so on. Machine safety: a machine to ensure that the required conditions of trouble, can normally achieve functional requirements. Work safety: refers to the operation personnel protection guarantee the safety of humanand health of body and mind. Environmental security: refers to the machines to the surrounding environment and people do not cause the pollution and harmDesign methodology to design thinking to rational process, so that the design can follow certain logic, so that more designers can make good design. It generally。
机械专业外文翻译中英文翻译外文文献翻译
英文资料High-speed millingHigh-speed machining is an advanced manufacturing technology, different from the traditional processing methods. The spindle speed, cutting feed rate, cutting a small amount of units within the time of removal of material has increased three to six times. With high efficiency, high precision and high quality surface as the basic characteristics of the automobile industry, aerospace, mold manufacturing and instrumentation industry, such as access to a wide range of applications, has made significant economic benefits, is the contemporary importance of advanced manufacturing technology. For a long time, people die on the processing has been using a grinding or milling EDM (EDM) processing, grinding, polishing methods. Although the high hardness of the EDM machine parts, but the lower the productivity of its application is limited. With the development of high-speed processing technology, used to replace high-speed cutting, grinding and polishing process to die processing has become possible. To shorten the processing cycle, processing and reliable quality assurance, lower processing costs.1 One of the advantages of high-speed machiningHigh-speed machining as a die-efficient manufacturing, high-quality, low power consumption in an advanced manufacturing technology. In conventional machining in a series of problems has plagued by high-speed machining of the application have been resolved.1.1 Increase productivityHigh-speed cutting of the spindle speed, feed rate compared withtraditional machining, in the nature of the leap, the metal removal rate increased 30 percent to 40 percent, cutting force reduced by 30 percent, the cutting tool life increased by 70% . Hardened parts can be processed, a fixture in many parts to be completed rough, semi-finishing and fine, and all other processes, the complex can reach parts of the surface quality requirements, thus increasing the processing productivity and competitiveness of products in the market.1.2 Improve processing accuracy and surface qualityHigh-speed machines generally have high rigidity and precision, and other characteristics, processing, cutting the depth of small, fast and feed, cutting force low, the workpiece to reduce heat distortion, and high precision machining, surface roughness small. Milling will be no high-speed processing and milling marks the surface so that the parts greatly enhance the quality of the surface. Processing Aluminum when up Ra0.40.6um, pieces of steel processing at up to Ra0.2 ~ 0.4um.1.3 Cutting reduce the heatBecause the main axis milling machine high-speed rotation, cutting a shallow cutting, and feed very quickly, and the blade length of the workpiece contacts and contact time is very short, a decrease of blades and parts of the heat conduction. High-speed cutting by dry milling or oil cooked up absolute (mist) lubrication system, to avoid the traditional processing tool in contact with the workpiece and a lot of shortcomings to ensure that the tool is not high temperature under the conditions of work, extended tool life.1.4 This is conducive to processing thin-walled partsHigh-speed cutting of small cutting force, a higher degree of stability, Machinable with high-quality employees compared to the company may be very good, but other than the company's employees may Suanbu Le outstanding work performance. For our China practice, we use the models to determine the method of staff training needs are simple and effective. This study models can be an external object, it can also be a combination of internal and external. We must first clear strategy for the development of enterprises. Through the internal and external business environment and organizational resources, such as analysis, the future development of a clear business goals and operational priorities. According to the business development strategy can be compared to find the business models, through a comparative analysis of the finalization of business models. In determining business models, a, is the understanding of its development strategy, or its market share and market growth rate, or the staff of the situation, and so on, according to the companies to determine the actual situation. As enterprises in different period of development, its focus is different, which means that enterprises need to invest the manpower and financial resources the focus is different. So in a certain period of time, enterprises should accurately selected their business models compared with the departments and posts, so more practical significance, because the business models are not always good, but to compare some aspects did not have much practical significance, Furthermore This can more fully concentrate on the business use of limited resources. Identify business models, and then take the enterprise of the corresponding departments and staff with the business models for comparison, the two can be found in the performance gap, a comparative analysis to find reasons, in accordance with this business reality, the final identification of training needs. The cost of training is needed, if not through an effective way to determine whether companies need to train and the training of the way, but blind to training, such training is difficult to achieve the desired results. A comparison only difference between this model is simple and practical training.1.5 Can be part of some alternative technology, such as EDM, grinding high intensity and high hardness processingHigh-speed cutting a major feature of high-speed cutting machine has the hardness of HRC60 parts. With the use of coated carbide cutter mold processing, directly to the installation of ahardened tool steel processing forming, effectively avoid the installation of several parts of the fixture error and improve the parts of the geometric location accuracy. In the mold of traditional processing, heat treatment hardening of the workpiece required EDM, high-speed machining replace the traditional method of cutting the processing, manufacturing process possible to omit die in EDM, simplifying the processing technology and investment costs .High-speed milling in the precincts of CNC machine tools, or for processing centre, also in the installation of high-speed spindle on the general machine tools. The latter not only has the processing capacity of general machine tools, but also for high-speed milling, a decrease of investment in equipment, machine tools increased flexibility. Cutting high-speed processing can improve the efficiency, quality improvement, streamline processes, investment and machine tool investment and maintenance costs rise, but comprehensive, can significantly increase economic efficiency.2 High-speed millingHigh-speed milling the main technical high-speed cutting technology is cutting the development direction of one of it with CNC technology, microelectronic technology, new materials and new technology, such as technology development to a higher level. High-speed machine tools and high-speed tool to achieve high-speed cutting is the prerequisite and basic conditions, in high-speed machining in the performance of high-speed machine tool material of choice and there are strict requirements.2.1 High-speed milling machine in order to achieve high-speed machiningGeneral use of highly flexible high-speed CNC machine tools, machining centers, and some use a dedicated high-speed milling, drilling. At the same time a high-speed machine tool spindle system and high-speed feeding system, high stiffness of the main characteristics of high-precision targeting and high-precision interpolation functions, especially high-precision arc interpolation function. High-speed machining systems of the machine a higher demand, mainly in the following areas:General use of highly flexible high-speed CNC machine tools, machining centers, and some use a dedicated high-speed milling, drilling. At the same time a high-speed machine tool spindle system and high-speed feeding system, high stiffness of the main characteristics of high-precision targeting and high-precision interpolation functions, especially high-precision arc interpolation function. High-speed machining systems of the machine a higher demand, mainly in the following areas:High-speed milling machine must have a high-speed spindle, the spindle speed is generally 10000 ~ 100000 m / min, power greater than 15 kW. But also with rapid speed or in designated spots fast-stopping performance. The main axial space not more than 0 .0 0 0 2 m m. Often using high-speed spindle-hydrostatic bearings, air pressure-bearing, mixed ceramic bearings, magneticbearing structure of the form. Spindle cooling general use within the water or air cooled.High-speed processing machine-driven system should be able to provide 40 ~ 60 m / min of the feed rate, with good acceleration characteristics, can provide 0.4 m/s2 to 10 m/s2 acceleration and deceleration. In order to obtain good processing quality, high-speed cutting machines must have a high enough stiffness. Machine bed material used gray iron, can also add a high-damping base of concrete, to prevent cutting tool chatter affect the quality of processing. A high-speed data transfer rate, can automatically increase slowdown. Processing technology to improve the processing and cutting tool life. At present high-speed machine tool manufacturers, usually in the general machine tools on low speed, the feed of the rough and then proceed to heat treatment, the last in the high-speed machine on the half-finished and finished, in improving the accuracy and efficiency at the same time, as far as possible to reduce processing Cost.2.2 High-speed machining toolHigh-speed machining tool is the most active one of the important factors, it has a direct impact on the efficiency of processing, manufacturing costs and product processing and accuracy. Tool in high-speed processing to bear high temperature, high pressure, friction, shock and vibration, such as loading, its hardness and wear-resistance, strength and toughness, heat resistance, technology and economic performance of the basic high-speed processing performance is the key One of the factors. High-speed cutting tool technology development speed, the more applications such as diamond (PCD), cubic boron nitride (CBN), ceramic knives, carbide coating, (C) titanium nitride Carbide TIC (N) And so on. CBN has high hardness, abrasion resistance and the extremely good thermal conductivity, and iron group elements between the great inertia, in 1300 ℃ would not have happened significant role in the chemical, also has a good stability. The experiments show that with CBN cutting toolHRC35 ~ 67 hardness of hardened steel can achieve very high speed. Ceramics have good wear resistance and thermal chemical stability, its hardness, toughness below the CBN, can be used for processing hardness of HRC <5 0 parts. Carbide Tool good wear resistance, but the hardness than the low-CBN and ceramics. Coating technology used knives, cutting tools can improve hardness and cutting the rate, for cutting HRC40 ~ 50 in hardness between the workpiece. Can be used to heat-resistant alloys, titanium alloys, hightemperature alloy, cast iron, Chungang, aluminum and composite materials of high-speed cutting Cut, the most widely used. Precision machining non-ferrous metals or non-metallic materials, or the choice of polycrystalline diamond Gang-coated tool.2.3 High-speed processing technologyHigh-speed cutting technology for high-speed machining is the key. Cutting Methods misconduct, will increase wear tool to less than high-speed processing purposes. Only high-speed machine tool and not a good guide technology, high-speed machining equipment can not fullyplay its role. In high-speed machining, should be chosen with milling, when the milling cutter involvement with the workpiece chip thickness as the greatest, and then gradually decreased. High-speed machining suitable for shallow depth of cut, cutting depth of not more than 0.2 mm, to avoid the location of deviation tool to ensure that the geometric precision machining parts. Ensure that the workpiece on the cutting constant load, to get good processing quality. Cutting a single high-speed milling path-cutting mode, try not to interrupt the process and cutting tool path, reducing the involvement tool to cut the number to be relatively stable cutting process. Tool to reduce the rapid change to, in other words when the NC machine tools must cease immediately, or Jiangsu, and then implement the next step. As the machine tool acceleration restrictions, easy to cause a waste of time, and exigency stop or radical move would damage the surface accuracy. In the mold of high-speed finishing, in each Cut, cut to the workpiece, the feed should try to change the direction of a curve or arc adapter, avoid a straight line adapter to maintain the smooth process of cutting.3 Die in high-speed milling processing ofMilling as a highly efficient high-speed cutting of the new method,inMould Manufacturing has been widely used. Forging links in the regular production model, with EDM cavity to be 12 ~ 15 h, electrodes produced 2 h. Milling after the switch to high-speed, high-speed milling cutter on the hardness of HRC 6 0 hardened tool steel processing. The forging die processing only 3 h20min, improve work efficiency four to five times the processing surface roughness of Ra0.5 ~ 0.6m, fully in line with quality requirements.High-speed cutting technology is cutting technology one of the major developments, mainly used in automobile industry and die industry, particularly in the processing complex surface, the workpiece itself or knives rigid requirements of the higher processing areas, is a range of advanced processing technology The integration, high efficiency and high quality for the people respected. It not only involves high-speed processing technology, but also including high-speed processing machine tools, numerical control system, high-speed cutting tools and CAD / CAM technology. Die-processing technology has been developed in the mold of the manufacturing sector in general, and in my application and the application of the standards have yet to be improved, because of its traditional processing with unparalleled advantages, the future will continue to be an inevitable development of processing technology Direction.4 Numerical control technology and equipping development trend and countermeasureEquip the engineering level, level of determining the whole national economy of the modernized degree and modernized degree of industry, numerical control technology is it develop new developing new high-tech industry and most advanced industry to equip (such as information technology and his industry, biotechnology and his industry, aviation, spaceflight, etc. national defense industry) last technology and getting more basic most equipment. Marx has ever said "the differences of different economic times, do not lie in what is produced, and lie in how to produce,produce with some means of labor ". Manufacturing technology and equipping the most basic means of production that are that the mankind produced the activity, and numerical control technology is nowadays advanced manufacturing technology and equips the most central technology. Nowadays the manufacturing industry all around the world adopts numerical control technology extensively, in order to improve manufacturing capacity and level, improve the adaptive capacity and competitive power to the changeable market of the trends. In addition every industrially developed country in the world also classifies the technology and numerical control equipment of numerical control as the strategic materials of the country, not merely take the great measure to develop one's own numerical control technology and industry, and implement blockading and restrictive policy to our country in view of " high-grade, precision and advanced key technology of numerical control " and equipping. In a word, develop the advanced manufacturing technology taking numerical control technology as the core and already become every world developed country and accelerate economic development in a more cost-effective manner, important way to improve the overall national strength and national position. Numerical control technology is the technology controlled to mechanical movement and working course with digital information, integrated products of electromechanics that the numerical control equipment is the new technology represented by numerical control technology forms to the manufacture industry of the tradition and infiltration of the new developing manufacturing industry, namely the so-called digitization is equipped, its technological range covers a lot of fields: (1)Mechanical manufacturing technology; (2)Information processing, processing, transmission technology; (3)Automatic control technology; (4)Servo drive technology;(5)Technology of the sensor; (6)Software engineering ,etc..Development trend of a numerical control technologyThe application of numerical control technology has not only brought the revolutionary change to manufacturing industry of the tradition, make the manufacturing industry become the industrialized symbol , and with the constant development of numerical control technology and enlargement of the application, the development of some important trades (IT , automobile , light industry , medical treatment ,etc. ) to the national economy and the people's livelihood of his plays a more and more important role, because the digitization that these trades needed to equip has already been the main trend of modern development. Numerical control technology in the world at present and equipping the development trend to see, there is the following several respect [1- ] in its main research focus.5 A high-speed, high finish machining technology and new trend equippedThe efficiency, quality are subjavanufacturing technology. High-speed, high finish machining technology can raise the efficiency greatly , improve the quality and grade of the products, shorten production cycle and improve the market competitive power. Japan carries the technological research association first to classify it as one of the 5 great modern manufacturing technologies forthis, learn (CIRP) to confirm it as the centre in the 21st century and study one of the directions in international production engineering.In the field of car industry, produce one second when beat such as production of 300,000 / vehicle per year, and many variety process it is car that equip key problem that must be solved one of; In the fields of aviation and aerospace industry, spare parts of its processing are mostly the thin wall and thin muscle, rigidity is very bad, the material is aluminium or aluminium alloy, only in a situation that cut the speed and cut strength very small high, could process these muscles, walls. Adopt large-scale whole aluminium alloy method that blank " pay empty " make the wing recently, such large-scale parts as the fuselage ,etc. come to substitute a lot of parts to assemble through numerous rivet , screw and other connection way, make the intensity , rigidity and dependability of the component improved. All these, to processing and equipping the demand which has proposed high-speed, high precise and high flexibility.According to EMO2001 exhibition situation, high-speed machining center is it give speed can reach 80m/min is even high , air transport competent speed can up to 100m/min to be about to enter. A lot of automobile factories in the world at present, including Shanghai General Motors Corporation of our country, have already adopted and substituted and made the lathe up with the production line part that the high-speed machining center makes up. HyperMach lathe of U.S.A. CINCINNATI Company enters to nearly biggest 60m/min of speed, it is 100m/min to be fast, the acceleration reaches 2g, the rotational speed of the main shaft has already reached 60 000r/min. Processing a thin wall of plane parts, spend 30min only, and same part general at a high speed milling machine process and take 3h, the ordinary milling machine is being processed to need 8h; The speed and acceleration of main shaft of dual main shaft lathes of Germany DMG Company are up to 120000r/mm and 1g.In machining accuracy, the past 10 years, ordinary progression accuse of machining accuracy of lathe bring 5μm up to from 10μm already, accurate grades of machining center from 3~5μm, rise to 1~1.5μm, and ultraprecision machining accuracy is i t enter nanometer grade to begin already (0.01μm).In dependability, MTBF value of the foreign numerical control device has already reached above 6 000h, MTBF value of the servo system reaches above 30000h, demonstrate very high dependability .In order to realize high-speed, high finish machining, if the part of function related to it is electric main shaft, straight line electrical machinery get fast development, the application is expanded further .5.2 Link and process and compound to process the fast development of the lathe in 5 axesAdopt 5 axles to link the processing of the three-dimensional curved surface part, can cut with the best geometry form of the cutter , not only highly polished, but also efficiency improves by a large margin . It is generally acknowledged, the efficiency of an 5 axle gear beds can equal 2 3 axle gearbeds, is it wait for to use the cubic nitrogen boron the milling cutter of ultra hard material is milled and pared at a high speed while quenching the hard steel part, 5 axles link and process 3 constant axles to link and process and give play to higher benefit. Because such reasons as complicated that 5 axles link the numerical control system , host computer structure that but go over, it is several times higher that its price links the numerical control lathe than 3 axles , in addition the technological degree of difficulty of programming is relatively great, have restricted the development of 5 axle gear beds.At present because of electric appearance of main shaft, is it realize 5 axle complex main shaft hair structure processed to link greatly simplify to make, it makes degree of difficulty and reducing by a large margin of the cost, the price disparity of the numerical control system shrinks. So promoted 5 axle gear beds of head of complex main shaft and compound to process the development of the lathe (process the lathe including 5).At EMO2001 exhibition, new Japanese 5 of worker machine process lathe adopt complex main shaft hair, can realize the processing of 4 vertical planes and processing of the wanton angle, make 5 times process and 5 axles are processed and can be realized on the same lathe, can also realize the inclined plane and pour the processing of the hole of awls. Germany DMG Company exhibits the DMUVoution series machining center, but put and insert and put processing and 5 axles 5 times to link and process in once, can be controlled by CNC system or CAD/CAM is controlled directly or indirectly.5.3 Become the main trend of systematic development of contemporary numerical control intelligently, openly, networkedly.The numerical control equipment in the 21st century will be sure the intelligent system, the intelligent content includes all respects in the numerical control system: It is intelligent in order to pursue the efficiency of processing and process quality, control such as the self-adaptation of the processing course, the craft parameter is produced automatically; Join the convenient one in order to improve the performance of urging and use intelligently, if feedforward control , adaptive operation , electrical machinery of parameter , discern load select models , since exactly makes etc. automatically; The ones that simplified programming , simplified operating aspect are intelligent, for instance intelligent automatic programming , intelligent man-machine interface ,etc.; There are content of intelligence diagnose , intelligent monitoring , diagnosis convenient to be systematic and maintaining ,etc..Produce the existing problem for the industrialization of solving the traditional numerical control system sealing and numerical control application software. A lot of countries carry on research to the open numerical control system at present, such as NGC of U.S.A. (The Next Generation Work-Station/Machine Control), OSACA of European Community (Open System Architecture for Control within Automation Systems), OSEC (Open System Environment for Controller) of Japan, ONC (Open Numerical Control System) of China, etc.. The numerical control system melts tobecome the future way of the numerical control system open. The so-called open numerical control system is the development of the numerical control system can be on unified operation platform, face the lathe producer and end user, through changing, increasing or cutting out the structure target(numerical control function), form the serration, and can use users specially conveniently and the technical know-how is integrated in the control system, realize the open numerical control system of different variety , different grade fast, form leading brand products with distinct distinction. System structure norm of the open numerical control system at present, communication norm , disposing norm , operation platform , numerical control systematic function storehouse and numerical control systematic function software development ,etc. are the core of present research.The networked numerical control equipment is a new light spot of the fair of the internationally famous lathe in the past two years. Meeting production line , manufacture system , demand for the information integration of manufacturing company networkedly greatly of numerical control equipment, realize new manufacture mode such as quick make , fictitious enterprise , basic Entrance that the whole world make too. Some domestic and international famous numerical control lathes and systematic manufacturing companies of numerical control have all introduced relevant new concepts and protons of a machine in the past two years, if in EMO2001 exhibition, " Cyber Production Center " that the company exhibits of mountain rugged campstool gram in Japan (Mazak) (intellectual central production control unit, abbreviated as CPC); The lathe company of Japanese big Wei (Okuma ) exhibits " IT plaza " (the information technology square , is abbreviated as IT square ); Open Manufacturing Environment that the company exhibits of German Siemens (Siemens ) (open the manufacturing environment, abbreviated as OME),etc., have reflected numerical control machine tooling to the development trend of networked direction.5.4 Pay attention to the new technical standard, normal setting-up5.4.1 Design the norm of developing about the numerical control systemAs noted previously, there are better common ability, flexibility, adaptability, expanding in the open numerical control system, such countries as U.S.A. ,European Community and Japan ,etc. implement the strategic development plan one after another , carry on the research and formulation of the systematic norm (OMAC , OSACA , OSEC ) of numerical control of the open system structure, 3 biggest economies in the world have carried on the formulation that nearly the same science planned and standardized in a short time, have indicated a new arrival of period of change of numerical control technology. Our country started the research and formulation of standardizing the frame of ONC numerical control system of China too in 2000.5.4.2 About the numerical control standardThe numerical control standard is a kind of trend of information-based development of manufacturing industry. Information exchange among 50 years after numerical control technology was born was all because of ISO6983 standard, namely adopt G, M code describes how processes,。
机械英文参考文献及翻译
机械英文参考文献及翻译第一篇:机械英文参考文献及翻译Abstract: With a focus on the intake tower of the Yanshan Reservoir, this paper discusses the method of modeling in the 3D CAD software SolidWorks and the interface processing between SolidWorks and the ANSYS code, which decreases the difficulty in modeling complicated models in ANSYS.In view of the function of the birth-death element and secondary development with APDL(ANSYS parametric design language), a simulation analysis of the temperature field and thermal stress during the construction period of the intake tower was conveniently conducted.The results show that the temperature rise is about29.934 □ over 3 or 4 days.The temperature differences betweena ny two points are less than 24 □.The thermal stress increases with the temperature difference and reaches its maximum of 1.68 MPa at the interface between two concrete layers.Key words: SolidWorks;ANSYS;APDL;birth-death element;temperature field;thermal stress 1 Introduction Mass concrete is widely used in civil and hydraulic engineering nowadays, and its thermal stress increasingly attracts attention during design and construction.It is necessary to analyze the temperature field and thermal stress of important mass concrete structures with both routine methods and the finite element method(FEM).Some researchers have done a large amount of simulation analyses using FEM software(Tatro 1985;Barrett et al.1992;Kawaguchi and Nakane 1996;Zhu and Xu 2001;Zhu 2006), but difficulties in these methods remain.There are two main difficulties:(1)Most mass concrete structures are complex and difficult to model with FEM software.(2)Complete simulation is difficult with FEM softwarebecause of the complex construction processes and boundary conditions of concrete.The structure of the intake tower of the Yanshan Reservoir is complex.It is 34.5 m high and there is a square pressure tunnel at the bottom, the side length of which is 6 m.The intake tower was modeled in the 3D CAD software SolidWorks and imported into ANSYS with an interface tool.Then, using the APDL program, analysis of the temperature field and thermal stress during construction was conducted.2 Modeling in SolidWorks and interface processing between SolidWorks and ANSYS 2.1 Modeling in SolidWorks SolidWorks is a CAD/CAE/CAM/PDM desktop system, and the first 3D mechanical CAD software in Windows developed by the SolidWorks company.It provides product-level automated design tools(Liu and Ren 2005).The outside structure of the intake tower is simple but the internal structure is relatively complex.Therefore, the process of modeling is undertaken from the inside to the outside.The integrated and internal models of the intake tower are shown in Fig.1 and Fig.2.图片Fig.1 Integrated model Fig.2 Cross section 2.2 Interface processing between SolidWorks and ANSYS ANSYS is a type of large universal finite element software that has a powerful ability to calculate and analyze aspects of structure, thermal properties, fluid, electromagnetics, acoustics and so on.In addition, the interface of ANSYS can be used to import the CAD model conveniently(Zhang 2005), which greatly reduces the difficulties of dealing with complex models.The interface tools are given in Table 1.Table 1 CAD software packages and preferred interface tools 图表1After modeling in SolidWorks, it is necessary to save the model as a type of Parasolid(*.x_t)so as to import it into ANSYS correctly.Then, in ANSYS, the importing of the model iscompleted with the command “PARAIN, Name, Extension, Path, Entity, FMT, Scale” or the choice of “FileDImportDPARA...” in the GUI interface.There are two means of importing: selecting or not selecting “Allow Defeaturing”,the differences of which are shown in Fig.3 and Fig.4.图片Fig.3 Importing with defeaturing Fig.4 Importing without defeaturing 3 Analysis of temperature field of intake tower The temperature analysis of the intake tower during the construction period involves aspects of the temperature field and thermal stress.The calculation must deal with the problems of simulation of layered construction, dynamic boundary conditions, hydration heat, dynamic elasticity modulus, autogenous volume deformation of concrete and thermal creep stress, which are difficult to simulate directly in ANSYS.APDL is a scripting language based on the style of parametric variables.It is used to reduce a large amount of repetitive work in analysis(Gong and Xie 2004).This study carried out a simulation analysis of the temperature field considering nearly all conditions of construction, using the birth-death element and programming with APDL.3.1 Solving temperature field principle 3.1.1 Unsteady temperature field analysis The temperature of concrete changes during the construction period due to the effect of hydration heat of cement.This problem can be expressed as a heat conduction problem with internal heat sources in the area.The unsteady temperature field T(x, y, z,D)is written as(Zhu 1999): 公式1where □ is the thermal conductivity of concrete, c is the specific heat of concrete, □ is the density of concrete, □ is the adiabatic temperature rise of concrete, and □ is the age of concrete.In the 3D unsteady temperature field analysis, the functional form I e(T)is 公式2 where □R is a subfield of unit e;□0is the area on surface D , which is only in boundary units;c □ □ □□;□ is the exothermic coefficient;the thermal diffusivity c □ □ □ □;and isthe air temperature.a T3.1.2 Initial conditions and boundary conditions of concrete The initial conditions are the distribution laws of the initial transient temperature of internal concrete.The calculated initial temperature of concrete is 10 □.The index formula of hydration heat of cement is 公式 3 where t is the pouring time.The conversion between Q and □ is 公式4 The boundary conditions involve the laws of interaction between concrete and the surrounding medium.When concrete is exposed to the air, the boundary condition is 公式5 where n is the normal direction.Both and a T □ are constants or variables(Ashida and Tauchert 1998;Lin and Cheng 1997).During the maintenance period, the insulation materials of concrete are steel formworks and straws, and the exothermic coefficient of the outer surface is reduced as equivalent processing.The exothermic coefficients of the steel formwork and the straw are 45 kJ/(m2h+0)and 10 kJ/(m2h+0),respectively.Based on the local temperature during construction, the following formula can be fitted according to the temperature variation curve: 公式63.2 Analysis of temperature field in ANSYS The simulation scheme of layered construction, which is based on the real construction scheme, is shown in T able 2.The pouring days in Table 2 are all the total days of construction for each layer.A layer is not poured until the former layer is poured.图表2The feature points are selected in every layer above the base plate.The maximum temperatures and the temperature curvesare given in Table 3 and Fig.5, respectively.Table 3 Coordinates and maximum temperature of feature points 图表3 图片5 Fig.5 Maximum temperature curves Fig.5 shows that the maximum temperature of each layer occurs on the 3rd or 4th day after pouring, and then the temperature decreases with time, which is consistent with related literature(Lin and Cheng 1997;Luna and Wu 2000;Wu and Luna 2001).In Fig.5, the numbers of feature points from 2 to 8 are corresponding to their maximum temperature curves from Nodetemp 2 to Nodetemp 8, and the curve of Nodetemp 9 is the air temperature curve.Feature point 8, the maximum temperature of which is 29.934 □ , occurrin g on the 206th day of the total construction period, shows the maximum temperature rise during the construction period.Feature point 4, the coordinates of which are(16.4, 16.0, 5.0), shows the maximum temperature difference of 23.5340.4 Analysis of thermal stress of intake tower Expansion or contraction of the structure occurs during heating and cooling.If the expansion or contraction of different parts is inconsistent, then thermal stress occurs.The indirect method was adopted in this study: the temperature of nodes was first obtained in analysis of the temperature field, and then applied to the structure as a body load.4.1 Selection of calculating parameters The parameters of concrete are given in Table 4.The elasticity modulus is 公式7 T able 4 Parameters of concrete 图表4 The creep effect must be considered in analysis of temperature stress.The creep degree of concrete is influenced by the cement type, water-cement ratio and admixture.The formula of the creep degree is 公式8 Considering the creep degree, the formula of the elasticity modulus is adjusted to be 公式94.2 Analysis of thermal stress in ANSYS As in analysis of thetemperature field, feature points were selected in each layer above the base plate, and their coordinates were the same as those in the temperature field analysis.The maximum thermal stress of each point is shown in Table 5.Feature point 9, the coordinates of which are(17.4, 10.8, 8.0), is the point with the maximum thermal stress.Table 5 Maximum thermal stress of feature points 图表5The thermal stress curves of feature points are shown in Fig.6.图片6Fig.6 Maximum stress curves In Fig.6, the numbers of feature points from 2 to 9 are corresponding to their maximum stress curves from S1_2 to S1_9, and the S1_10 curve is the ultimate tensile stress o f concrete.The formula of concrete’s ultimate tensile stress is 公式10 The figures and table show that the maximum thermal stress of the intake tower is 1.68 MPa, occurring on the 90th day of the construction period, which is the end of the third layer maintenance period and the beginning of the pouring of the fourth layer.It is known that the thermal stress increases with the temperature difference.Feature point 9 is located at the interface between the third layer and the fourth layer.Thus, it is postulated that the maximum thermal stress is caused by the instantaneous temperature difference between two layers in the pouring period.In Fig.6, the S1_10 curve shows the ultimate tensile stress curve of concrete.It is known that the maximum thermal stress of each point in the intake tower during the construction period is less than the ultimate tensile stress of concrete.5 Conclusions ⑴ The problem of the interface between SolidWorks and ANSYS is resolved in this study, realizing an effective combination of the advantages of both SolidWorks and ANSYS and providing a basis for analysis in ANSYS.(2)Using abirth-death element and considering layered construction, dynamic boundary conditions, hydration heat, the dynamic elasticity modulus, autogenous volume deformation and creep of concrete, the temperature field and thermal stress during the construction period are conveniently obtained due to the virtues of secondary development with APDL.(3)The analysis of temperature shows that the temperature of concrete rises rapidly in the early stage of construction, reaches a maximum value of 29.934 □ on the 3rd or 4th day after pouring, drops thereafter, and is consistent with air temperature after about 30 days.The thermal stress increases with the temperature difference, and the occurrence time of the maximum thermal stress is consistent with that of the maximum temperature difference.The maximum thermal stress occurs at the interface of new and old layers and is caused by the instantaneous temperature difference, the value of which is 1.68 MPa.(4)The maximum thermal stress is less than the ultimate tensile stress of concrete, which illustrates that the curing measures in construction are effective.Meanwhile, in view of the fact that the maximum thermal stress occurs at the interface of new and old layers, more attention should be paid to it, especially when there is a long interval of time between the pouring of different layers.References Ashida, F., and Tauchert, T.R.1998.An inverse problem for determination of transient surface temperature from piezoelectric sensor measurement.Journal of Applied Mechanics, 65(2), 367-373.[doi:10.1115/1.2789064] Barrett, P.R., Foadian, H., James, R.J., and Rashid, Y.R.1992.Thermal-structural analysis methods for RCC dams.Proceedings of the Conference of Roller Concrete III, 407-422.San Diego: ASCE.Gong, S.G., and Xie, mands and Parametric Programming inANSYS.Beijing: China Machine Press.(in Chinese)Kawaguchi, T., and Nakane, S.1996.Investigations on determining thermal stress in massive concrete structures.ACI Materials Journal, 93(1), 96-101.Lin, J.Y., and Cheng, T.F.1997.Numerical estimation of thermal conductivity from boundary temperature measurements.Numerical Heat Transfer, 32(2), 187-203.[doi:10.1080/***87] Liu, L.J., and Ren, J.P.2005.Application of the secondary development in SolidWorks.Mechanical Management and Development,(1), 74-75.(in Chinese)Luna, R., and Wu, Y.2000.Simulation of temperature and stress fields during RCC dam construction.Journal of Construction Engineering and Management, ASCE, 126(5), 381-388.[doi: 10.1061/(ASCE)0733-9364(2000)126:5(381)] Tatro, S.B.and Schrader, E.K.1985.Thermal consideration for roller compacted concrete.ACI Structural Journal, 82(2), 119-128.Wu, Y., and Luna, R.2001.Numerical implementation of temperature and creep in mass concrete.Finite Elements in Analysis and Design, 37(2), 97-106.[doi:10.1016/S0168-874X(00)00022-6] Zhang, J.2005.Interface design between AutoCAD and ANSYS.Chinese Quarterly of Mechanics, 26(2), 257-262.(in Chinese)Zhu, B.F.1999.Thermal Stresses and Temperature Control of Mass Concrete.Beijing: China Electric Power Press.(in Chinese)Zhu, B.F., and Xu, P.2001.Methods for stress analysis simulating the construction process of high concrete dams.Dam Engineering, 6(4), 243-260.Zhu, B.F.2006.Current situation and prospect of temperature control and cracking prevention technology for concrete dam.Journal of Hydraulic Engineering, 37(12), 1424-1432.(in Chinese)第二篇:英文文献翻译(模版)在回顾D和H的文章时,我愿意第一个去单独地讨论每一篇,然后发表一些总体的观点。
- 1、下载文档前请自行甄别文档内容的完整性,平台不提供额外的编辑、内容补充、找答案等附加服务。
- 2、"仅部分预览"的文档,不可在线预览部分如存在完整性等问题,可反馈申请退款(可完整预览的文档不适用该条件!)。
- 3、如文档侵犯您的权益,请联系客服反馈,我们会尽快为您处理(人工客服工作时间:9:00-18:30)。
(文档含英文原文和中文翻译)中英文对照翻译英文资料Kinematics and dynamics of machineryOne princple aim of kinemarics is to creat the designed motions of the subject mechanical parts and then mathematically compute the positions, velocities ,and accelerations ,which those motions will creat on the parts. Since ,for most earthbound mechanical systems ,the mass remains essentially constant with time,defining the accelerations as a function of time then also defines the dynamic forces as a function of time. Stress,in turn, will be a function of both appliedand inerials forces . since engineering design is charged with creating systems which will not fail during their expected service life,the goal is to keep stresses within acceptable limits for the materials chosen and the environmental conditions encountered. This obvisely requies that all system forces be defined and kept within desired limits. In mechinery , the largest forces encountered are often those due to the dynamics of the machine itself. These dynamic forces are proportional to acceletation, which brings us back to kinematics ,the foundation of mechanical design. Very basic and early decisions in the design process invovling kinematics wii prove troublesome and perform badly.Any mechanical system can be classified according to the number of degree of freedom which it possesses.the systems DOF is equal to the number of independent parameters which are needed to uniquely define its posion in space at any instant of time.A rigid body free to move within a reference frame will ,in the general case, have complex motoin, which is simultaneous combination of rotation and translation. In three-dimensional space , there may be rotation about any axis and also simultaneous translation which can be resoled into componention along three axes, in a plane ,or two-dimentional space ,complex motion becomes a combination of simultaneous along two axes in the plane. For simplicity ,we will limit our present discusstions to the case of planar motion:Pure rotation the body pessesses one point (center of rotation)which has no motion with respect to the stationary frame of reference. All other points on the body describe arcs about that center. A reference line drawn on the body through the center changes only its angulai orientation.Pure translation all points on the body describe parallel paths. A reference line drawn on the body changes its linear posion but does not change its angular oriention.Complex motion a simulaneous combination of rotion and translationm . any reference line drawn on the body will change both its linear pisition and its angular orientation. Points on the body will travel non-parallel paths ,and there will be , at every instant , a center of rotation , which will continuously change location.Linkages are the bacis building blocks of all mechanisms. All common forms of mechanisms (cams , gears ,belts , chains ) are in fact variations of linkages. Linkages are made up of links and kinematic pairs.A link is an (assumed)rigid body which possesses at least two or more links (at their nodes), which connection allows some motion, or potential motion,between the connected links.The term lower pair is used to describe jionts with surface contact , as with a pin surrounded by a hole. The term higher pair is used to describe jionts with point or line contact ,but if there is any clerance between pin and hole (as there must be for motion ),so-called surface contact in thepin jiont actually becomes line contact , as the pin contacts actually has contact only at discrete points , which are the tops of the surfaces’asperities. The main practical advantage of lower pairs over higher pairs is their better ability to trap lubricant between their envloping surface. This ie especially true for the rotating pin joint. The lubricant is more easily squeezed out of a higher pair .as s result , the pin joint is preferred for low wear and long life .When designing machinery, we must first do a complete kinematic analysis of our design , in order to obtain information about the acceleration of the moving parts .we next want te use newton’s second law to caculate the dynamic forces, but to do so we need to know the masses of all the moving parts which have these known acceletations. These parts do not exit yet ! as with any design in order to make a first pass at the caculation . we will then have to itnerate to better an better solutions as we generate more information.A first estimate of your parts’masses can be obtained by assuming some reasonable shapes and size for all the parts and choosing approriate materials. Then caculate the volume of each part and multipy its volume by material’s mass density (not weight density ) to obtain a first approximation of its mass . these mass values can then be used in Newton’s equation.How will we know whether our chosen sizes and shapes of links are even acceptable, let alone optimal ? unfortunately , we will not know untill we have carried the computations all the way through a complete stress and deflection analysis of the parts. It it often the case ,especially with long , thin elements such as shafts or slender links , that the deflections of the parts, redesign them ,and repeat the force ,stress ,and deflection analysis . design is , unavoidably ,an iterative process .It is also worth nothing that ,unlike a static force situation in which a failed design might be fixed by adding more mass to the part to strenthen it ,to do so in a dynamic force situation can have a deleterious effect . more mass with the same acceleration will generate even higher forces and thus higher stresses ! the machine desiger often need to remove mass (in the right places) form parts in order to reduce the stesses and deflections due to F=ma, thus the designer needs to have a good understanding of both material properties and stess and deflection analysis to properlyshape and size parts for minimum mass while maximzing the strength and stiffness needed to withstand the dynamic forces.One of the primary considerations in designing any machine or strucre is that the strength must be sufficiently greater than the stress to assure both safety and reliability. To assure that mechanical parts do not fail in service ,it is necessary to learn why they sometimes do fail. Then we shall be able to relate the stresses with the strenths to achieve safety .Ideally, in designing any machine element,the engineer should have at his disposal should have been made on speciments having the same heat treatment ,surface roughness ,and size asthe element he prosses to design ;and the tests should be made under exactly the same loading conditions as the part will experience in service . this means that ,if the part is to experience a bending and torsion,it should be tested under combined bending and torsion. Such tests will provide very useful and precise information . they tell the engineer what factor of safety to use and what the reliability is for a given service life .whenever such data are available for design purposes,the engineer can be assure that he is doing the best justified if failure of the part may endanger human life ,or if the part is manufactured in sufficiently large quantities. Automobiles and refrigrerators, for example, have very good reliabilities because the parts are made in such large quantities that they can be thoroughly tested in advance of manufacture , the cost of making these is very low when it is divided by the total number of parts manufactrued.You can now appreciate the following four design categories :(1)failure of the part would endanger human life ,or the part ismade in extremely large quantities ;consequently, an elaborate testingprogram is justified during design .(2)the part is made in large enough quantities so that a moderate serues of tests is feasible.(3)The part is made in such small quantities that testing is not justified at all ; or the design must be completed so rapidlly that there is not enough time for testing.(4) The part has already been designed, manufactured, and tested and found to be unsatisfactory. Analysis is required to understand why the part is unsatisfactory and what to do to improve it .It is with the last three categories that we shall be mostly concerned.this means that the designer will usually have only published values of yield strenth , ultimate strength,and percentage elongation . with this meager information the engieer is expected to design against static and dynamic loads, biaxial and triaxial stress states , high and low temperatures,and large and small parts! The data usually available for design have been obtained from the simple tension test , where the load was applied gradually and the strain given time to develop. Yet these same data must be used in designing parts with complicated dynamic loads applied thousands of times per minute . no wonder machine parts sometimes fail.To sum up, the fundamental problem of the designer is to use the simple tension test data and relate them to the strength of the part , regardless of the stress or the loading situation.It is possible for two metal to have exactly the same strength and hardness, yet one of these metals may have a supeior ability to aborb overloads, because of the property called ductility. Dutility is measured by the percentage elongation which occurs in the material at frature. The usual divding line between ductility and brittleness is 5 percent elongation. Amaterial having less than 5 percent elongation at fracture is said to bebrittle, while one having more is said to be ductile.The elongation of a material is usuallu measured over 50mm gauge length.siece this did not a measure of the actual strain, another method of determining ductility is sometimes used . after the speciman has been fractured, measurements are made of the area of the cross section at the fracture. Ductility can then be expressed as the percentage reduction in cross sectional area.The characteristic of a ductile material which permits it to aborb largeoverloads is an additional safety factot in design. Ductility is also important because it is a measure of that property of a material which permits it to be cold-worked .such operations as bending and drawing are metal-processing operations which require ductile materials.When a materals is to be selected to resist wear , erosion ,or plastic deformaton, hardness is generally the most important property. Several methods of hardness testing are available, depending upon which particular property is most desired. The four hardness numbers in greatest usse are the Brinell, Rockwell,Vickers, and Knoop.Most hardness-testing systems employ a standard load which is applied to a ball or pyramid in contact with the material to be tested. The hardness is an easy property to measure , because the test is nondestructive and test specimens are not required . usually the test can be conducted directly on actual machine element .Virtually all machines contain shafts. The most common shape for shafts is circular and the cross section can be either solid or hollow (hollow shafts can result in weight savings). Rectangular shafts are sometimes used ,as in screw driver bladers ,socket wrenches and control knob stem.A shaft must have adequate torsional strength to transmit torque and not be over stressed. If must also be torsionally stiff enough so that one mounted component does not deviate excessively from its original angular position relative to a second component mounted on the same shaft. Generally speaking,the angle of twist should not exceed one degree in a shaft length equal to 20 diameters.Shafts are mounted in bearing and transmit power through such device as gears, pulleys,cams and clutches. These devices introduce forces which attempt to bend the shaft;hence, tha shaft must be rigid enough to prevent overloading of the supporting bearings ,in general, the bending deflection of a shaft should not exceed 0.01 in per ft of length between bearing supports.In addition .the shaft must be able to sustain a combination of bending and torsional loads. Thus an equivalent load must be considered which takes into account both torsion and bending . also ,the allowable stress must contain a factor of safety which includes fatigue, since torsional and bending stress reversals occur.For fiameters less than 3 in ,the usual shaft material is cold-rolled steel containing about 0.4 percent carbon. Shafts ate either cold-rolled or forged in sizes from 3in. to 5 in. for sizes above 5in. shafts are forged and machined to size . plastic shafts are widely used for light load applications . one advantage of using plastic is safty in electrical applications, since plastic is a poor confuctor of electricity.Components such as gears and pulleys are mounted on shafts by means of key. The design of the key and the corresponding keyway in the shaft must be properly evaluated. For example, stress concentrations occur in shafts due to keyways , and the material removed to form the keyway further weakens the shaft.If shafts are run at critical speeds , severe vibrations can occur which can seriously damage a machine .it is important to know the magnitude of these critical speeds so that they can be avoided. As a general rule of thumb , the difference betweem the operating speed and the critical speed should be at least 20 percent.Many shafts are supported by three or more bearings, which means that the problem is statically indeterminate .text on strenth of materials give methods of soving such problems. The design effort should be in keeping with the economics of a given situation , for example , if one line shaft supported by three or more bearings id needed , it probably would be cheaper to make conservative assumptions as to moments and design it as though it were determinate . the extra cost of an oversize shaft may be less than the extra cost of an elaborate design analysis.Another important aspect of shaft design is the method of directly connecting one shaft to another , this is accomplished by devices such as rigid and flexiable couplings.A coupling is a device for connecting the ends of adjacent shafts. In machine construction , couplings are used to effect a semipermanent connection between adjacent rotating shafts , the connection is permanent in the sense that it is not meant to be broken during the useful life of the machinem , but it can be broken and restored in an emergency or when worn parts are replaced.There are several types of shaft couplings, their characteristics depend on the purpose for which they are used , if an exceptionally long shaft is required in a manufacturing plant or a propeller shaft on a ship , it is made in sections that are coupled together with rigid couplings. A common type of rigid coupling consists of two mating radial flanges that are attached by key driven hubs to the ends of adjacent shaft sections and bolted together through the flanges to form a rigid connection. Alignment of the connected shafts in usually effected by means of a rabbet joint on the face of the flanges.In connecting shafts belonging to separate device ( such as an electric motor and a gearbox),precise aligning of the shafts is difficult and a fkexible coupling is used . this coupling connects the shafts in such a way as to minimize the harmful effects of shafts misalignment of loads and to move freely(float) in the axial diection without interfering with one another .flexiable couplings can also serve to reduce the intensity of shock loads and vibrations transmitted from one shaft to another .中文翻译机械运动和动力学运动学的基本目的是去设计一个机械零件的理想运动,然后再用数学的方法去描绘该零件的位置,速度和加速度,再运用这些参数来设计零件。