铝材表面热处理
铝合金热处理状态定义
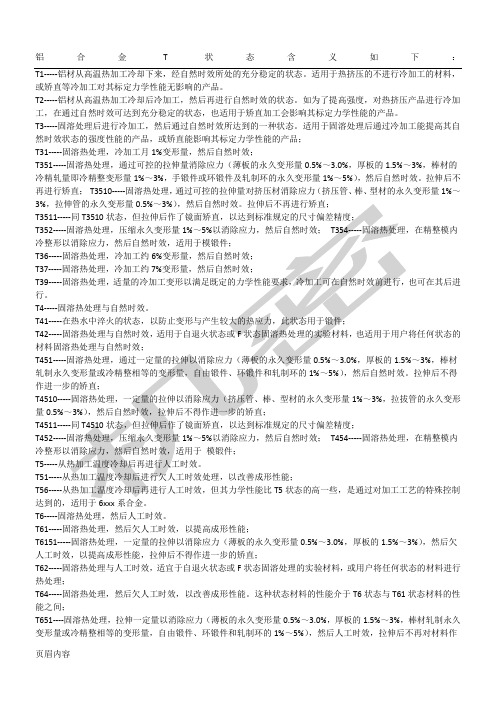
铝合金T状态含义如下:T1-----铝材从高温热加工冷却下来,经自然时效所处的充分稳定的状态。
适用于热挤压的不进行冷加工的材料,或矫直等冷加工对其标定力学性能无影响的产品。
T2-----铝材从高温热加工冷却后冷加工,然后再进行自然时效的状态。
如为了提高强度,对热挤压产品进行冷加工,在通过自然时效可达到充分稳定的状态,也适用于矫直加工会影响其标定力学性能的产品。
T3-----固溶处理后进行冷加工,然后通过自然时效所达到的一种状态。
适用于固溶处理后通过冷加工能提高其自然时效状态的强度性能的产品,或矫直能影响其标定力学性能的产品;T31-----固溶热处理,冷加工月1%变形量,然后自然时效;T351-----固溶热处理,通过可控的拉伸量消除应力(薄板的永久变形量0.5%~3.0%,厚板的1.5%~3%,棒材的冷精轧量即冷精整变形量1%~3%,手锻件或环锻件及轧制环的永久变形量1%~5%),然后自然时效。
拉伸后不再进行矫直;T3510-----固溶热处理,通过可控的拉伸量对挤压材消除应力(挤压管、棒、型材的永久变形量1%~3%T352-----T36-----T37-----T39-----进行。
T4-----T41-----T42-----T451-----~3%,棒材形量T452-----T5-----T51-----T56-----T6-----固溶热处理,然后人工时效。
T61-----固溶热处理,然后欠人工时效,以提高成形性能;T6151-----固溶热处理,一定量的拉伸以消除应力(薄板的永久变形量0.5%~3.0%,厚板的1.5%~3%),然后欠人工时效,以提高成形性能,拉伸后不得作进一步的矫直;T62-----固溶热处理与人工时效,适宜于自退火状态或F状态固溶处理的实验材料,或用户将任何状态的材料进行热处理;T64-----固溶热处理,然后欠人工时效,以改善成形性能。
这种状态材料的性能介于T6状态与T61状态材料的性能之间;T651----固溶热处理,拉伸一定量以消除应力(薄板的永久变形量0.5%~3.0%,厚板的1.5%~3%,棒材轧制永久变形量或冷精整相等的变形量,自由锻件、环锻件和轧制环的1%~5%),然后人工时效,拉伸后不再对材料拉拔管的永久变形量0.5%~3%),然后人工时效,拉伸后不再对材料作进一步的矫直;T6511-----同T6510状态,但拉伸后作了镜面矫直,以满足标准规定的尺寸偏差精度;T652-----固溶热处理,通过施压产生1%~5%永久变形以消除应力,然后人工时效;T654-----固溶热处理,在精整模内冷整形以消除应力,然后人工时效,适用于模锻件;T66-----固溶热处理,然后人工时效,通过对工艺过程进行特殊控制以使此状态材料的力学性能比T6状态的高一些(适用于6xxx系合金),其量由供需双方商定。
铝材的热加工原理及应用

铝材的热加工原理及应用1. 引言铝材作为一种广泛应用于工程领域的材料,其热加工技术在铝材加工中具有重要的地位。
本文将介绍铝材热加工的基本原理以及在工程应用中的具体应用。
2. 铝材的热加工基本原理铝材的热加工是通过控制材料的温度和应力,使其发生塑性变形,以达到材料形状调整或表面性质改善的目的。
以下是一些常用的铝材热加工方法:2.1 热轧热轧是指将高温下铝材进行连续的加工,通常在500℃以上进行。
这样可以大大降低铝材的强度和硬度,使其更容易进行变形。
热轧可用于生产铝板、铝带等产品。
2.2 热挤压热挤压是指将铝坯加热到较高温度,然后在模具中施加压力,使其通过钢模孔进行挤压成型。
这种方法常用于生产铝管、铝型材等产品。
2.3 铝材的热处理铝材的热处理是指将铝材加热到一定温度,然后进行退火、淬火等处理,以改变其内部结构和性能。
这样可以提高铝材的强度、硬度和耐腐蚀性。
3. 铝材热加工的工程应用铝材热加工在工程应用中有广泛的应用场景,以下是一些典型的应用场景:3.1 航空航天工业铝材热加工在航空航天工业中的应用非常广泛。
通过热加工可以生产各种形状复杂的铝合金零件,如发动机外壳、机翼等。
3.2 汽车制造业铝材热加工在汽车制造业中的应用越来越广泛。
通过热加工可以生产轻量化的汽车零部件,提高车辆的燃油效率和性能。
3.3 建筑与装饰工业铝材热加工在建筑与装饰工业中也有重要应用。
通过热加工可以生产各种铝合金型材,用于建筑结构和室内装饰。
3.4 电子工业铝材热加工在电子工业中的应用日益增多。
通过热加工可以生产铝基板、散热器等用于电子器件的关键部件。
4. 结论铝材的热加工是一种重要的材料加工技术,通过控制材料的温度和应力,在工程应用中能够实现铝材的形状调整和性能改善。
在航空航天、汽车制造、建筑装饰和电子工业等领域,铝材热加工都有着广泛的应用。
随着科技的进步,铝材热加工技术将会越来越重要,为各个行业的发展做出贡献。
以上是铝材的热加工原理及应用的简要介绍,由于篇幅限制,本文只涉及了一些基础知识和典型应用场景,希望可以对读者了解铝材热加工提供一些帮助。
铝型材热处理工艺

铝型材热处理工艺
铝型材热处理工艺是一种重要的加工技术,通过该工艺可以改变或优化铝型材的物理和机械性能,以满足各种不同的应用需求。
以下是铝型材热处理工艺的一般步骤:
1. 预热处理:将铝型材加热到一定的温度,以消除其内部的应力,提高材料的稳定性。
2. 固溶处理:将铝型材加热到高温,并保持一段时间,使铝型材内部的合金元素充分溶解,形成过饱和固溶体。
3. 淬火处理:将铝型材迅速冷却至室温,以固定其组织结构。
淬火处理可以提高铝型材的硬度、强度和耐磨性。
4. 时效处理:将铝型材加热到一定温度,并保持一段时间,使过饱和固溶体中的合金元素逐渐析出,形成强化相。
时效处理可以提高铝型材的强度和硬度,使其具有良好的机械性能。
5. 表面处理:对铝型材表面进行涂层、喷涂、电镀等处理,以提高其耐腐蚀性和美观度。
通过以上步骤,可以实现对铝型材热处理工艺的控制,以获得具有优良性能的铝型材。
铝材加硬的方法

铝材加硬的方法铝材是一种常见的金属材料,具有轻量、强度高、抗腐蚀等优点,在工业制造、建筑、航空等领域广泛应用。
但在某些特定的领域,铝材的硬度可能无法满足要求,此时需要采取加硬的方法来提升其硬度。
一、冷加工硬化冷加工硬化是一种常见的加硬方法,其原理是通过机械加工将铝材表面的晶粒细化,增加晶界数量,使得材料内部的晶体错位增多,从而提高其硬度。
常见的冷加工方式有轧制、拉伸、冷拔等。
轧制是将铝材通过辊道机械压制,使得晶粒细化,表面硬度提高。
拉伸是将铝材加热后拉伸,使得晶粒细化,内部应力增加,从而提高硬度。
冷拔是将铝材在室温下拉伸,使得晶粒细化,内部应力增加,从而提高硬度。
二、热处理热处理是通过改变铝材的晶体结构来提高其硬度的方法,常见的热处理方式有退火、淬火、时效等。
退火是将铝材加热到一定温度,保温一段时间,然后缓慢冷却,使得晶体结构重新排列,从而提高硬度。
淬火是将铝材加热到一定温度,然后快速冷却,使得晶体结构变得均匀,硬度提高。
时效是将铝材先进行固溶处理,然后在一定温度下保温一段时间,使得溶质元素在晶粒内部析出,从而提高硬度。
三、表面处理表面处理是将铝材表面进行化学处理或物理处理,从而形成一层硬度较高的保护层,提高其耐磨性和耐腐蚀性。
常见的表面处理方式有阳极氧化、电镀、喷涂等。
阳极氧化是将铝材表面通过电解氧化处理,形成一层氧化膜,从而提高其硬度和耐腐蚀性。
电镀是将铝材表面镀上一层金属,如镍、铬、铜等,形成一层保护层,提高其耐磨性和耐腐蚀性。
喷涂是将铝材表面喷上一层特殊的涂料,形成一层保护层,提高其耐磨性和耐腐蚀性。
铝材加硬的方法有很多种,可以根据具体需求选择合适的方法进行加工处理。
在实际应用中,需要根据材料的性能特点、工艺条件和经济成本等因素进行综合考虑,选用最适合的加硬方法,以获得最佳的加硬效果。
铝型材热处理的四把火:退火、正火、淬火及回火
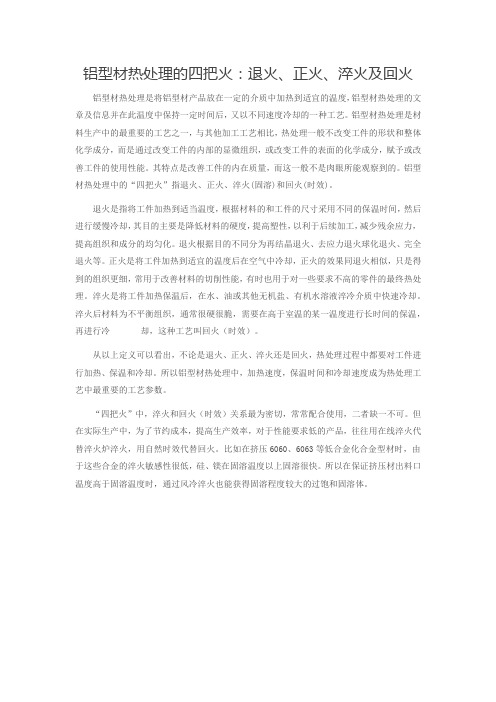
铝型材热处理的四把火:退火、正火、淬火及回火铝型材热处理是将铝型材产品放在一定的介质中加热到适宜的温度,铝型材热处理的文章及信息并在此温度中保持一定时间后,又以不同速度冷却的一种工艺。
铝型材热处理是材料生产中的最重要的工艺之一,与其他加工工艺相比,热处理一般不改变工件的形状和整体化学成分,而是通过改变工件的内部的显微组织,或改变工件的表面的化学成分,赋予或改善工件的使用性能。
其特点是改善工件的内在质量,而这一般不是肉眼所能观察到的。
铝型材热处理中的“四把火”指退火、正火、淬火(固溶)和回火(时效)。
退火是指将工件加热到适当温度,根据材料的和工件的尺寸采用不同的保温时间,然后进行缓慢冷却,其目的主要是降低材料的硬度,提高塑性,以利于后续加工,减少残余应力,提高组织和成分的均匀化。
退火根据目的不同分为再结晶退火、去应力退火球化退火、完全退火等。
正火是将工件加热到适宜的温度后在空气中冷却,正火的效果同退火相似,只是得到的组织更细,常用于改善材料的切削性能,有时也用于对一些要求不高的零件的最终热处理。
淬火是将工件加热保温后,在水、油或其他无机盐、有机水溶液淬冷介质中快速冷却。
淬火后材料为不平衡组织,通常很硬很脆,需要在高于室温的某一温度进行长时间的保温,再进行冷却,这种工艺叫回火(时效)。
从以上定义可以看出,不论是退火、正火、淬火还是回火,热处理过程中都要对工件进行加热、保温和冷却。
所以铝型材热处理中,加热速度,保温时间和冷却速度成为热处理工艺中最重要的工艺参数。
“四把火”中,淬火和回火(时效)关系最为密切,常常配合使用,二者缺一不可。
但在实际生产中,为了节约成本,提高生产效率,对于性能要求低的产品,往往用在线淬火代替淬火炉淬火,用自然时效代替回火。
比如在挤压6060、6063等低合金化合金型材时,由于这些合金的淬火敏感性很低,硅、镁在固溶温度以上固溶很快。
所以在保证挤压材出料口温度高于固溶温度时,通过风冷淬火也能获得固溶程度较大的过饱和固溶体。
金属表面热处理

浓硫酸 30
重铬酸钠 7.5 水 62.5
在室温下浸渍 1min ,水洗,干燥。
二、镁及镁合金表面处理方法 [方法 1] 脱脂处理。常用溶剂为:三氯乙烯、丙酮、醋酸乙酯和丁酮等。
[方法 2]
脱脂后在下述溶液中于 70-75°C 下浸渍 5min :
氢氧化钠 12
水 100
用冷水冲洗,再于下述溶液中在 20°C 浸渍 5min :
常用的表面处理方法主要有脱脂处理法、机械处理法和化学处理法三大类。选择表面处 理法应考虑多种因素,其中主要包括:
(1)表面污染物的种类。如动物油、植物油、矿物油、润滑油、脏土、流体、无机盐、 水份、指纹等。
(2)污染物的物理特性。如污染物的厚度、紧密或疏松程度等。、 (3)胶接材料的种类。如钢材料可用碱溶液,而处理黄铜、铝材料时应考虑选用腐蚀 性较小的温和溶液。 (4)需要清洁的程度。 (5)清洗液的清洁能力和设备情况。 (6)危险性和价格成本等。 金属表面处理方法 金属表面在各种热处理、机械加工、运输及保管过程中,不可避免地会被氧化,产生 一层厚薄不均的氧化层。同时,也容易受到各种油类污染和吸附一些其他的杂质。 油污及某些吸附物,较薄的氧化层可先后用溶剂清洗、化学处理和机械处理,或直接用化学 处理。对于严重氧化的金属表面,氧化层较厚,就不能直接用溶剂清洗和化学处理,而最好 先进行机械处理。 通常经过处理后的金属表面具有高度活性,更容易再度受到灰尘、湿气等的污染。为此,处 理后的金属表面应尽可能快地进行胶接。 塑料表面处理方法 塑料可分为热塑性塑料和热固性塑料两大类。在通常情况下,热固性塑料要比热塑性 塑料容易胶接。但它们的表面能量均低于玻璃、陶瓷、金属等亲水性材料,而且它们表面常 会粘附脱模剂或逸出增塑剂,因此不易为胶粘剂所浸润,从而影响胶接强度。因此,一般均 需对塑料进行表面处理。由于塑料的品种众多,各种性能差别很大,因此表面处理的方法也 就很不相同。以下介绍几种常见的塑料表面处理方法。 橡胶表面处理方法 一般的橡胶材料表面都比较光滑,需要经机械处理或化学处理增加其粗糙度,才能达
铝合金牌号及热处理状态
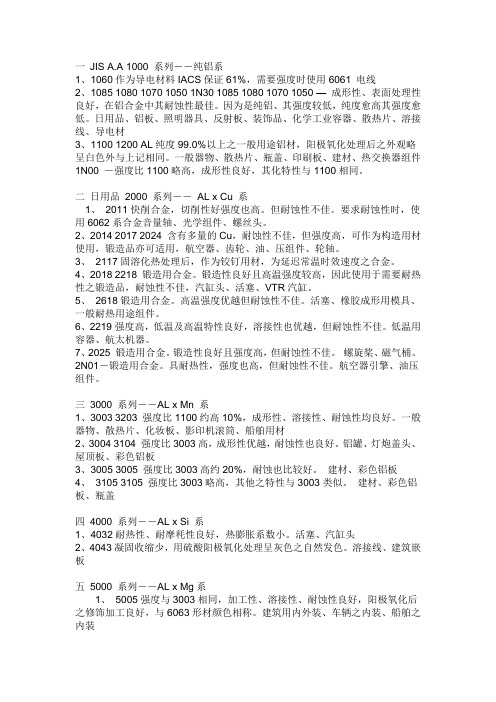
一JIS A.A 1000 系列--纯铝系1、1060作为导电材料IACS保证61%,需要强度时使用6061 电线2、1085 1080 1070 1050 1N30 1085 1080 1070 1050 —成形性、表面处理性良好,在铝合金中其耐蚀性最佳。
因为是纯铝、其强度较低,纯度愈高其强度愈低。
日用品、铝板、照明器具、反射板、装饰品、化学工业容器、散热片、溶接线、导电材3、1100 1200 AL纯度99.0%以上之一般用途铝材,阳极氧化处理后之外观略呈白色外与上记相同。
一般器物、散热片、瓶盖、印刷板、建材、热交换器组件1N00 -强度比1100略高,成形性良好,其化特性与1100相同。
二日用品2000 系列--AL x Cu 系1、2011快削合金,切削性好强度也高。
但耐蚀性不佳。
要求耐蚀性时,使用6062系合金音量轴、光学组件、螺丝头。
2、2014 2017 2024 含有多量的Cu,耐蚀性不佳,但强度高,可作为构造用材使用,锻造品亦可适用,航空器、齿轮、油、压组件、轮轴。
3、2117固溶化热处理后,作为铰钉用材,为延迟常温时效速度之合金。
4、2018 2218 锻造用合金。
锻造性良好且高温强度较高,因此使用于需要耐热性之锻造品,耐蚀性不佳,汽缸头、活塞、VTR汽缸。
5、2618锻造用合金。
高温强度优越但耐蚀性不佳。
活塞、橡胶成形用模具、一般耐热用途组件。
6、2219强度高,低温及高温特性良好,溶接性也优越,但耐蚀性不佳。
低温用容器、航太机器。
7、2025 锻造用合金。
锻造性良好且强度高,但耐蚀性不佳。
螺旋桨、磁气桶。
2N01-锻造用合金。
具耐热性,强度也高,但耐蚀性不佳。
航空器引擎、油压组件。
三3000 系列--AL x Mn 系1、3003 3203 强度比1100约高10%,成形性、溶接性、耐蚀性均良好。
一般器物、散热片、化妆板、影印机滚筒、船舶用材2、3004 3104 强度比3003高,成形性优越,耐蚀性也良好。
铝及铝合金热处理工艺
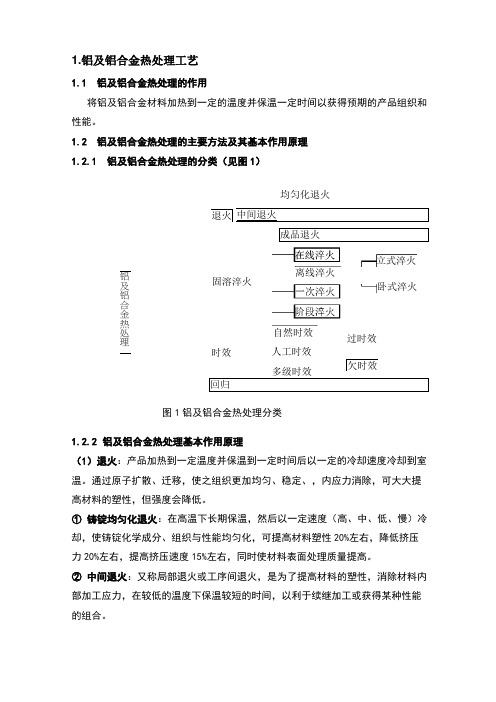
1.铝及铝合金热处理工艺1.1 铝及铝合金热处理的作用将铝及铝合金材料加热到一定的温度并保温一定时间以获得预期的产品组织和性能。
1.2 铝及铝合金热处理的主要方法及其基本作用原理 1.2.1 铝及铝合金热处理的分类(见图1)均匀化退火中间退火成品退火回归图1铝及铝合金热处理分类1.2.2 铝及铝合金热处理基本作用原理(1)退火:产品加热到一定温度并保温到一定时间后以一定的冷却速度冷却到室温。
通过原子扩散、迁移,使之组织更加均匀、稳定、,内应力消除,可大大提高材料的塑性,但强度会降低。
① 铸锭均匀化退火:在高温下长期保温,然后以一定速度(高、中、低、慢)冷却,使铸锭化学成分、组织与性能均匀化,可提高材料塑性20%左右,降低挤压力20%左右,提高挤压速度15%左右,同时使材料表面处理质量提高。
② 中间退火:又称局部退火或工序间退火,是为了提高材料的塑性,消除材料内部加工应力,在较低的温度下保温较短的时间,以利于续继加工或获得某种性能的组合。
退火 铝及铝合金热处理固溶淬火时效 人工时效 多级时效欠时效离线淬火卧式淬火立式淬火自然时效过时效③完全退火:又称成品退火,是在较高温度下,保温一定时间,以获得完全再结晶状态下的软化组织,具有最好的塑性和较低的强度。
(2)固溶淬火处理:将可热处理强化的铝合金材料加热到较高的温度并保持一定的时间,使材料中的第二相或其它可溶成分充分溶解到铝基体中,形成过饱和固溶体,然后以快冷的方法将这种过饱和固溶体保持到室温,它是一种不稳定的状态,因处于高能位状态,溶质原子随时有析出的可能。
但此时材料塑性较高,可进行冷加工或矫直工序。
①在线淬火:对于一些淬火敏感性不高的合金材料,可利用挤压时高温进行固溶,然后用空冷(T5)或用水雾冷却(T6)进行淬火以获得一定的组织和性能。
②离线淬火:对于一些淬火敏感性高的合金材料必须在专门的热处理炉中重新加热到较高的温度并保温一定时间,然后以不大于15秒的转移时间淬入水中或油中,以获得一定的组织和性能,根据设备不同可分为盐浴淬火、空气淬火、立式淬火、卧式淬火。
- 1、下载文档前请自行甄别文档内容的完整性,平台不提供额外的编辑、内容补充、找答案等附加服务。
- 2、"仅部分预览"的文档,不可在线预览部分如存在完整性等问题,可反馈申请退款(可完整预览的文档不适用该条件!)。
- 3、如文档侵犯您的权益,请联系客服反馈,我们会尽快为您处理(人工客服工作时间:9:00-18:30)。
日志电镀热度 3已有 497 次阅读2011-2-25 09:43|个人分类:表处理|需电镀零件预留电镀余量一般规定编号共10页第1页第版1 范围本标准规定了我公司需电镀零件除螺纹外的预留电镀余量的一般要求,作为零件工艺编制、零件生产制造、零件镀前检验验收的标准。
本标准适用于我公司所有电镀零件,包括铝及铝合金零件、铜及铜合金零件、锌合金零件、钢铁基体零件、复合材料零件等。
(如有特殊情况,在机加工艺规程或相关技术文件中注明)。
2规范性引用文件下列文件中的条款通过本规范的引用而成为本规范的条款,凡是注日期的引用文件,其随后的所有修改单(不包括勘误的内容)或修订版不适用于本规范,然而鼓励根据本规范达成协议的各方研究是否可以使用这些文件的最新版本。
凡是不注日期的引用文件,其最新版本适用于本规范。
GJB/Z594A 金属镀覆层和化学覆层选择原则与厚度系列3 预留余量原则3.1 一般原则:一般情况下,需表面处理零件加工时各尺寸预留余量=2×镀层厚度中限。
例:图纸规定零件表面处理Ap·Ni20,表示化学镀镍20~30μm,则预留余量为2×25μm=0.05mm。
3.2 公差圆整原则:考虑到量具制作及尺寸测量的便利性,按照四舍五入的原则预留实际余量。
除特殊要求外,公差精度一般控制到0.01mm。
但是如果图纸尺寸精度等级为0.001mm,则不对其镀层余量进行圆整。
例:钢基零件表面处理为Ep·Cu5Ni5b,表示含义为需电镀铜5~8μm,电镀亮镍5-8μm,则镀层厚度中限以13μm计算,预留镀层余量为2×13μm=26μm,一般情况下,按照四舍五入的原则,实际余量按照30μm即0.03mm预留。
编制审核标检校队审定批准需电镀零件预留电镀余量一般规定编号共10页第2页第版3.3 公差压缩原则(对于图纸标注公差△>0.06的尺寸有效)对于镀层厚度为8~30μm的零件,孔、槽尺寸的下限按预留原则所得余量上浮0.05mm,孔、槽尺寸的上限上浮0.025mm;轴、键尺寸的上限按照预留余量原则所得余量下浮0.05mm,轴、键尺寸的下限下浮0.025mm。
例:铝基零件,表面处理为Ap·Ni20或Ap·Ni8,某孔图纸尺寸Φ,则机加时按照Φ控制;某键宽图纸尺寸,则机加时按照控制。
3.4 不留余量原则下列情况可不留余量:3.4.1 实际镀层厚度低于8μm的壳体零件尺寸;3.4.2 公差大于0.05mm的插针、插孔及前、内、后套等接触类铝基尺寸。
3.5 预留余量优先原则零件生产时,一般按照3.3→3.2→3.1→3.4的顺序考虑加工尺寸的电镀余量。
4. 预留余量及检验控制方法4.1 电连接器壳体类零件根据公司实际情况,综合考虑生产管理、工艺协调、量具使用等因素,对采用Ep·Zn8、Ep·Ni8、Ap·Ni8、Ap·Ni10、Ep·Cu8·Ap·Ni8(铁基零件)、SB·Ap·Ni10·Ep·Ni1b、Ap·Ni20、Ap·Ni8·Ep·Cd12c2D(OL)、Ap·Ni10·Ep·CrBK、Et·A(S)·C1(BK)后喷漆等镀锌、镀镍、化学镀镍、镀镉、镀黑铬、硫酸阳极化后喷漆等的表面处理方式的电连接器壳体零件。
预留余量一般按照:图纸标注公差△>0.06mm的尺寸,预留预留按照3.2条和3.3条执行。
图纸标注公差0.03mm<△≤0.06mm的尺寸镀层厚度8~30μm时,孔、槽尺寸公差按预留余量原则所得余量平均上移;轴、键尺寸公差按预留余量原则所得余量平均下移。
例:铝基体零件,表面处理为SB·Ap·Ni10·Ep·Ni1b,某孔图纸尺寸Φ,则机加时按照Φ控制;铝基体零件,表面处理为Ap·Ni20,某键宽图纸尺寸为,则机加时按照控制。
对于卡钉孔尺寸,JY系列及JY599系列铝基体机加时按照Φ控制,其余型产品铝基体壳体卡钉孔按照Φ控制。
超出以上规定的表面处理方式的预留余量原则按照第三章规定执行。
光连接器壳体零件4.2.1 铜基体壳体零件镀层厚度低于8μm的表面处理方式不留镀层余量。
例:对表面处理为Ep·Ni5、Ep·Ni3b或Ap·Ni3的铜基零件不留镀层余量。
4.2.2 超出4.2.1条规定的表面处理方式的预留余量原则按照第三章规定执行。
4.3 铜基插针,插孔类零件需电镀零件预留电镀余量一般规定编号共10页第3页第版镀银、镀锡零件前套、内套零件机加时前套、内套类零件配合孔尺寸上浮0.01mm,内套类零件外圆直径、凸台直径尺寸下调0.01mm。
其他零件机加时插针针头以及尺寸公差≤0.05mm的尺寸均预留0.015mm电镀余量。
即孔、槽类尺寸上浮0.015mm,轴、键类尺寸下调0.015mm;插针、后套强装台处尺寸下调0.01mm;后套类零件配合孔尺寸上浮0.015mm;针套类零件插针端下调0.015mm,配合孔上浮0.015mm;插针、后套、针套之外的其他零件的公差≤0.05mm的尺寸均预留0.015mm电镀余量,其余尺寸不预留电镀余量。
示例见图6.4.3.2 镀金零件机加时,镀金零件直接按图纸尺寸进行加工。
导销、导套、镶件等类零件导销、导套、镶件等类零件尺寸公差≤0.05mm的尺寸预留电镀余量见表1。
导销、导套、镶件等类零件尺寸公差>0.05mm的尺寸,镀层厚度为1~5μm 时,不留电镀余量;镀层厚度>5μm时,孔、槽尺寸的下限按预留余量原则所得余量上浮0.03mm,孔、槽尺寸的上限上浮0.01mm;轴、键尺寸的上限按预留余量原则所得余量下浮0.03mm,轴、键尺寸下限下浮0.01mm。
例:钢基导套,表面处理为Ep·Cu5Ni5b,图纸标注某孔尺寸Φ,则机加时按照Φ控制;某键宽图纸尺寸,则机加时按照控制。
表1 导销、导套、镶件类零件尺寸公差≤0.05mm的尺寸预留电镀余量基体种类镀层厚度(μm)1~5 5~8 8~12 16~24铜合金基体轴不留余量不留余量/孔不留余量不留余量/碳钢基体轴下浮0.01 下浮0.01 下浮0.02 下浮0.035 孔上浮0.01 上浮0.01 下浮0.02 下浮0.035不锈钢基体不留余量注1):铜合金导销、导套、镶件类零件实际镀层厚度按照附录A.2.3执行。
4.5 玻璃封接产品零件4.5.1 4J29壳体和碳钢壳体4J29壳体和碳钢壳体的镀前螺纹尺寸按照Q/21EJ145《需涂镀保护层螺纹涂镀前后控制规定》执行;封接部位尺寸不留电镀余量;其他尺寸中若公差<0.10mm,则孔槽尺寸上浮0.02mm,轴键尺寸下浮0.02mm;若公差≥0.10mm,则按照图纸尺寸进行加工。
不锈钢壳体和钛合金壳体封接后表面处理为ECP或CHP的不锈钢壳体以及表面处理为喷砂的钛合金壳体直接按需电镀零件预留电镀余量一般规定编号共10页第4页第版照图纸尺寸进行加工。
封接后表面处理为电镀的不锈钢壳体按照4.5.1预留电镀余量。
4.5.3 插针插针针头尺寸控制:镀前尺寸按照Φ加工,镀后尺寸按照图纸要求:Φ。
4.5.4 其它零件对于复合封接结构(基壳体——玻璃饼——管式零件——玻璃饼或玻璃管——插针的结构)的封接产品,加工时管式零件外圆尺寸一般按照Φ控制,管式零件内孔尺寸一般按照Φ控制(封接部位不留余量)同轴产品零件预留余量方法4.6.1 中心接触件铜基零件:按照4.3.1条2以及4.3.2执行(包括QBe2铍青铜零件);4J29基体类零件:参照4.5条插针针头尺寸预留余量。
4.6.2 外壳体类接触件非气密封产品壳体按照4.1执行;气密封壳体按照4.5执行。
4.7 复合材料壳体预留余量方法参照4.1条执行。
定位弹簧零件定位弹簧轴向尺寸控制规定根据试验结果,定位弹簧轴向尺寸在热处理时效后收缩0.005~0.015mm,表面处理酸洗钝化后亦有一定缩短,因此对定位弹簧轴向尺寸规定如下:下料时,铍青铜带断面应平齐、光滑,不能有须毛刺影响尺寸测量;图纸规定定位弹簧轴向尺寸在下料成型时按照,控制;四车间热表面处理后定位弹簧轴向尺寸符合。
5. 零件检验控制方法镀前检验需留余量镀前尺寸检验控制按照3、4章规定执行。
镀后检验对零件镀后检验控制按照图纸执行。
对于尺寸公差大于0.03mm的金属壳体零件以及公差大于0.05mm的其他金属零件,因为镀前镀层厚度范围的原因,允许镀后超差±0.01mm。
以前生产产品控制方法鉴于我公司产品种类复杂,很多产品已经长期生产,为了不至于影响生产,对已生产的具体产品零件的镀层余量预留原则作如下规定:1)XC及其派生系列零件预留尺寸为五键槽高度和宽度、卡钉孔、卡簧和槽间距、花需电镀零件预留电镀余量一般规定编号共10页第5页第版键圆盘的尺寸,示例如图1.2)JY598系列产品零件预留尺寸为壳体径向尺寸、五键及五键槽高度和宽度、卡钉孔、卡簧槽和槽间距的尺寸,其中卡钉孔、卡簧槽和槽间距尺寸示例见图2。
3)JY599系列产品零件预留尺寸为壳体径向尺寸、五键及五键槽高度和宽度、卡钉孔的尺寸,示例见图3.4)JY599Ⅲ-25(拉火绳)产品零件预留尺寸为壳体径向尺寸、五键及五键槽高度和宽度、卡簧槽和槽间距的尺寸,其余卡簧槽和槽间距尺寸示例见图4,另外21E8.164.585套筒的尺寸全部预留电镀余量。
5)XC及其派生系列附件FJJP、FJJPG、FJGP、FJGWP的套筒和中间螺帽的预留尺寸示例见图5.对于新开发的产品以及异型壳体类零件,应对其径向尺寸、孔类及槽类尺寸按以上原则预留电镀余量。
镀层标识及镀层厚度说明见附录A.零件图号后缀汇总见附录B.需电镀零件预留电镀余量一般规定编号共10页第6页第版附录A(规范性附录)镀层标识及镀层厚度说明A.1 镀层标注符号的识别按照GJB594A《金属镀覆层和化学覆盖层选择原则与厚度系列》的规定,镀层厚度范围系列一般为:1~3μm(中限2μm),3~5μm(中限4μm),5~8μm (中限6.5μm),8~12μm(中限10μm),10~17μm(中限13.5μm),12~18μm(中限15μm),18~24μm(中限21μm)等,且标注镀层厚度时一般写镀层厚度的下限。
A.2 不同基体零件镀镍层(电镀亮镍、电镀暗镍)厚度规定为了统一以前设计产品图纸中不同零件镀镍层厚度差异大的问题,规范零件生产、保证镀镍层质量,特作如下规定。
A.2.1 钢基体零件镀镍层厚度规定a. 图纸标注为Ep·Cu8Ni5b、DCu5/L2Ni5、DCu/L2Ni5、DL2Ni8、Ep·Cu3Ni5b、Ep·Cu5Ni5b等铁基体镀亮镍零件,生产时均按Ep·Cu5Ni5b进行机加(预留电镀余量)、电镀和检验控制。