塑性工程系实验指导书
塑性成形原理实验指导书
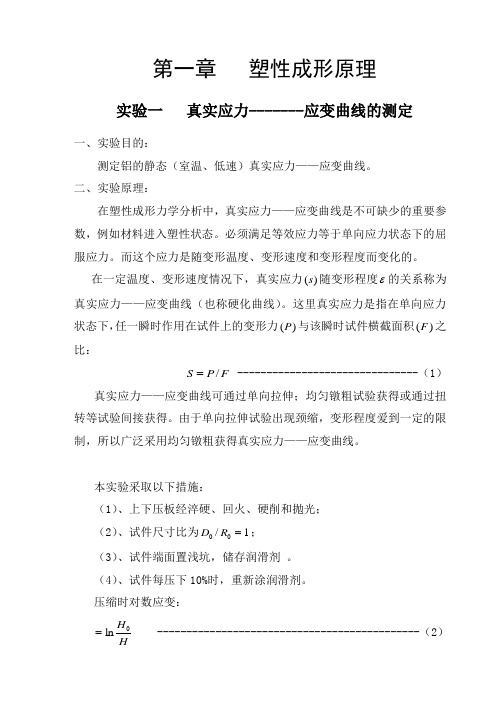
第一章 塑性成形原理实验一 真实应力-------应变曲线的测定一、实验目的:测定铝的静态(室温、低速)真实应力——应变曲线。
二、实验原理:在塑性成形力学分析中,真实应力——应变曲线是不可缺少的重要参数,例如材料进入塑性状态。
必须满足等效应力等于单向应力状态下的屈服应力。
而这个应力是随变形温度、变形速度和变形程度而变化的。
在一定温度、变形速度情况下,真实应力)(s 随变形程度ε的关系称为真实应力——应变曲线(也称硬化曲线)。
这里真实应力是指在单向应力状态下,任一瞬时作用在试件上的变形力)(P 与该瞬时试件横截面积)(F 之比:F P S /= -------------------------------(1)真实应力——应变曲线可通过单向拉伸;均匀镦粗试验获得或通过扭转等试验间接获得。
由于单向拉伸试验出现颈缩,变形程度爱到一定的限制,所以广泛采用均匀镦粗获得真实应力——应变曲线。
本实验采取以下措施:(1)、上下压板经淬硬、回火、硬削和抛光; (2)、试件尺寸比为1/00=R D ;(3)、试件端面置浅坑,储存润滑剂 。
(4)、试件每压下10%时,重新涂润滑剂。
压缩时对数应变:HH 0ln= ---------------------------------------------(2)0H ——压缩前试件高度H ——压缩瞬时试件高度压缩时的真实力按平均压力计算: 0F PF P S ==-----------------------------(3) F ——试件变形某一瞬时面积 ; 0F ——试件变形前面积; P ——轴向载荷。
三、实验设备和仪器:实验是在材力试验机上进行(也可在锤上或曲柄压力机上进行)。
力和变形的测量采用传感器、应变仪。
由X —Y 记录仪记录变形和位移的变化。
二个传感器及X —Y 记录仪简要说明见附录。
四、实验步骤:(1)、精确测量试件原始尺寸0D ,0H ;(2)、安装测力、测位移传感器并将其接入动态应变仪,再将应变仪输出端接入X —Y 记录仪;(3)、标定传达传感器(可直接用标定曲线);(4)、将试件上下端涂润滑剂(石腊),放在试件压板之间;(5)、加压变形,每变形△H= mm卸载,重涂润滑剂;(6)、再加压直至所需变形程度;(7)、X—Y记录仪记录变形过程。
金属塑性成型试验指导书

轧制不均匀变形分析一、实验目的通过不均匀变形的实验过程,了解和观察轧制过程中轧件出现的不均匀变性现象,分析产生不均匀变形结果的原因,从而掌握减少不均匀的措施和实验方法。
二、实验内容1.沿宽度方向压下不均2.沿高度方向压下均匀 三、实验说明因为压下量:H h h -=∆,L l l -=∆,B b b -=∆ 应变:H h h ∆=ε,L l l ∆=ε,Bb b ∆=ε 体积不变定律:0=++b l h εεε 如果:0=b ε,0=+l h εε 四、实验仪器、设备与材料1.Φ130mm 二辊实验轧机2.游标卡尺、锉刀、钢板尺3.铅试样、铝试样(见实验步骤) 五、实验操作过程1.沿轧件宽度方向高度上压下不均(1)用1.5mm 厚的铅试样卷成如图1尺寸与形状的试样三种,经一道轧成1mm 厚,观察结果并记录下来,比较三种不同情况,并分析其原因。
图1(2)将厚1.5mm 的铅试样折迭成如图2所示,经一道轧成1mm 厚,观察结果并记录下来。
(3)取铅试样3×40×60mm 中心有凹槽(如图3)的一块经一道轧成1.5mm 厚,观察结果并作出记录。
图2 图32.沿高度上均匀变形(1)将1×50×140mm 的铅试样绕于0.2×20×75mm 的铝板上,共绕三圈如下图4,用最大可能压下轧制,后将铅试样拆开,仔细观察铝片的情况。
(2)将1×50×70mm 的铅板迭放在同样尺寸的铝板上以△h=1mm 的压下量轧制,观察发生的现象。
图4六、实验思考与分析1.画出各实验前、后的示意图,并分析产生的各实验结果的原因及各部分所产生的应力情况。
2.简述不均匀变形的后果。
3.如何联系生产实际,采取措施来防止或减轻不均匀变形的不良影响。
实验二:滑动区和粘着区的测定一、实验目的在摩擦系数及变形区几何参数变化的条件下,测定滑动区和粘着区的大小。
二、实验原理在塑性变形过程中,接触表面金属质点相对于工具表面有径向滑动的区域,称为滑动区,没有径向滑动的区域叫粘着区。
材料塑性加工原理实验指导书

实验一 金属塑性变形力学特点(综合性实验)一、实验目的1、测定材料的真应力—真应变曲线,并与名义应力—应变曲线进行比较。
2、采用一元线性回归的方法,求出材料的形变强化指数 。
3、进一步掌握有关设备、仪器的使用、操作方法。
二、实验基本原理断裂力学中裂纹前方的应力应变场、裂纹尖端的钝化特性及扩展规律、在大变形条件下工作的构件与材料的变形与断裂行为、材料的塑性成型加工工艺都离不开对材料的塑性变形规律以及强化特性的了解和认识。
材料的塑性变形规律以及强化特性参数主要是通过单轴拉伸试验及其数据处理得到的,即本实验要进行的材料的真应力—真应变曲线及形变强化指数的测定。
材料性能的测试是通过试样进行的,试样制备是试验的重要环节,国家标准GB6397-86对此有详细的规定。
本试验采用圆棒试样,如图1所示。
试样的工作部分应保持均匀光滑以确保材料的单向应力状态。
均匀部分的有效工作长度称为标距,在本试验中由引伸计刀口的距离确定,参见图1,初始标距=50 mm ,和分别为工作部分的初始直径和初始面积。
试样的过渡部分应有适当的圆角以降低应力集中,两端的夹持部分用以传递载荷,其形状与尺寸应与试验机的钳口相匹配。
图1 圆棒拉伸试样简图1.真应力—真应变曲线在拉伸过程中由于试样任一瞬时的面积和标距(l l l ∆+=0)随时都在变化,而名义应力和名义应变是按初始面积和标距计算的,因此任一瞬时的真实应力和真实应变与相应的和之间都存在着差异,进入塑性以后这种差异逐渐增大。
在均匀变形阶段,真实应力的定义为A P s /=根据塑性变形体积不变的假设(Al l A V ==00),有)1(/00εσ+==l A Pl s真实应变(也叫对数应变)的定义为)1ln(ln 00ε+===⎰l l l dl e l l将上式展开: (323)2-+-=εεεe这说明在均匀变形的范围内,真应力恒大于名义应力,而真应变恒小于名义应变。
在弹性阶段由于应变值极小,二者的差异极小,没有必要加以区分。
塑性成型原理实验指导书

《塑性成型原理》课程实验指导书上海工程技术大学材料工程学院材料加工工程系2010~2011年实验须知1.上试验课前,必须预习课程试验指导书及相关的讲课内容,明确试验目的及步骤,并做好进行试验数据记录的准备(试验指导教师有检查预习情况的责任,对未预习者,不得进行试验)。
2.进入试验室后,必须听从试验指导老师及相关人员的指导,遵守试验室有关制度。
3.进入试验室后,必须听从试验指导教师或相关人员介绍设备使用情况,待熟悉设备后,经指导教师同意方能开动设备。
4.使用试验设备前,必须按照试验指导书中所规定的试验步骤进行相关试验。
进行试验时,思想必须集中,要安全操作试验设备,避免实事故发生。
5.实验完毕后,必须整理试验场地(须将试验设备擦拭干净,上油,打扫试验场地等)。
6.学生必须爱护国家财产,如有损坏仪器、设备、工具、量具等物,应立即报告实验指导教师及相关人员。
属自然损坏,酌情处理;属故意损坏,除责令其检查外,应呈报学校进行处理。
7.试验试样原则上不准拿出实验室,如确实因测量未完成或其他情况,须得到实验指导老师同意,方能办理借出手续。
8.实验报告内容包括实验目地,步骤,使用仪器设备、工、模具以及测量数据及其结果分析等各方面。
实验数据需用曲线表示出来时,一律用方格纸描绘。
9.实验报告一律用学校所规定的统一的实验报告纸撰写,在实验结束后一周内交给课程指导教师。
实验一真实应力-应变曲线的测定与绘制一、实验目的1、学会真实应力-应变曲线的实验测定和绘制2、加强对真实应力-应变曲线物理意义及用途的认识二、实验用材料、使用工具及仪器设备1、试样:20#钢,其尺寸如图1 所示图1 试样尺寸2、工具:游标卡尺、钢皮尺、冲子、光滑垫板3、仪器设备:600KN万能材料试验机三、实验内容真实应力-应变曲线反映了试样随着塑性变形程度增加,流动应力也相应不断上升,因此真实应力-应变曲线又称为硬化曲线。
真实应力-应变曲线的变化主要与实验材料的化学成分、组织结构、变形温度、应变速度等因素的影响有关。
金属塑性成形原理实验指导书

金属塑性成形原理实验指导书河南科技大学材料加工实验中心2008年3月实验一真实应力-应变曲线的绘制一、实验目的1、区别不同材料、不同热处理状态的金属试样形变特性。
2、掌握真实应力——应变(δ-ε)曲线建立过程以及用微机处理数据和绘制曲线的方法。
二、内容简介在金属塑性变形的研究中,用对数应变表示的真实应力-应变关系曲线具有普遍的意义,它是正确分析金属材料形变强化特性,计算变形力的依据。
该曲线是在对金属试样单向拉伸(或压缩)得到的拉伸(或压缩)曲线的基础上经数学转换绘制而成。
用电测方法记录拉伸曲线比材料实验机通常采用的方法精确,观察与测量也比较方便,能提高δ-ε曲线的绘制质量。
微机处理数据和绘制曲线能避免繁琐的人工计算,省时省力,因而在本实验中加以采用。
三、实验仪器、设备、工具与试样仪器:动态应变仪、位移、拉力传感器、X-Y函数记录仪、IBM-PC微机。
设备:60吨万能材料试验机。
工具:卡尺、半径规、冲子。
试样:正火处理A3钢和调质处理的45钢标准试样。
四、实验步骤1、接通各仪器电源,预热几分钟。
2、打试样标距LQ =100,并测量直径d。
3、将仪器有关旋纽搬到适当位置,预调平衡应变仪,装卡试样,调整到合适位置。
4、开试验机缓慢加载,观察记录曲线的变化。
当试样拉到塑性失稳点b时,记录最大拉应力值Pb(单位牛顿)。
5、在试样明显发生颈缩到断裂期间,适当停机2-3次。
每次都要测量细颈处直径dt,曲率半径Rt,并记在数据表内,在拉伸曲线的相应位置做标记以便查找该瞬时的拉力值,操作时要快捷,准确,配合得当。
6、每次记录完毕继续加载,直到最后断裂为止。
7、测量断裂后的标距L ,颈缩断裂处最小直径d min 和曲率半径R 。
8、在拉伸曲线上数出表示最大拉力的坐标格数Y b 和表示最大变形量的坐标格数X d (Y b和X d 均取成正整数)。
将实验过程中所有数据填入表1。
表1 实验数据记录表材 料原 始 尺 寸 载荷上升时 载 荷 下 降 时 断后尺寸 L 0D 0 P b D t R t d t R t d t R t L R d min五、数据处理1、拉伸曲线P-δ坐标值的标定由试验机读到的最大拉力P b 作为拉伸曲线上最高幅度Y b 的实际示值,并以P b /Y b 为纵坐标的比例尺可确定其它各点的实际拉力;把试样变化前后标距长度之差L-L 0/X d 为比例,确定其它各点的伸长变形值。
金属塑性原理实验指导书(金材)

金属塑性原理实验指导书(金材)《金属塑性成形原理》实验指导书编写:刘易凡广东工业大学材料与能源学院二零一三年九月印刷实验一金属板材成形力学性能测试 (3)实验二杯突实验 (19)实验项目名称:金属板材成形力学性能测试实验项目性质:综合性所属课程名称:金属塑性成形原理实验计划学时:4一、实验目的通过本试验,理解和掌握金属塑性理论的相关知识,理解和掌握金属板料力学性能对塑性成形工艺的影响。
二、实验内容1.理解和掌握金属弹性模量(E)的概念,弹性模量与变形的关系。
2.理解和掌握屈服应力(ζs)、抗拉强度(ζb)、屈强比(ζs/ζb)。
3.理解和掌握金属薄板的均匀延伸率(δu)、总延伸率(δk),及其对金属薄板塑性成形性能的影响。
4.理解和掌握金属材料的加工硬化概念及其在金属塑性成形加工中的一些应用,掌握确定金属薄板应变硬化指数(n)的方法。
5.理解和掌握金属薄板的塑性应变比(γ及-γ)、凸耳参数(△γ),塑性应变比γ值与冲压成形性能的关系。
6.掌握金属薄板拉伸时伸长ΔL 与载荷F 曲线的拟合绘制方法,7掌握金属薄板拉伸时标称应力—应变曲线的拟合绘制方法;掌握金属薄板实际应力—应变曲线(硬化曲线)的绘制方法。
三、相关知识概述1.标称应力—应变曲线金属板料单向静力拉伸实验中,标称应力ζ=0A F与相对线应变ε= 0L L的关系曲线称为标称应力—应变曲线,其中 F 为拉伸载荷,A 0为试样原始横截面积,ΔL 为试样标距伸长量,L 0为试样原始标距长度。
2.标称应力—应变曲线的变形三阶段它分为弹性变形、均匀塑性变形和局部塑性变形阶段。
3.屈服应力屈服点是弹性变形与塑性变形分界点,对于有明显屈服点的金属,标称应力—应变曲线上屈服平台的应力称为屈服应力ζs ;对于没有明显屈服点的金属,在曲线上无屈服平台,这时规定试件产生残余应变ε=0.2%的应力作为材料的屈服应力,称为屈服强度,一般用ζ0.2表示。
对于理想塑性材料,屈服应力为常数,但对于一般工程材料,进入塑性状态后,继续变形时,会产生强化,则屈服应力将不断变化,即为后继屈服应力。
塑性实验实验报告

姓名:学号:班级:材料1012013年4月18日塑性实验实验报告一、实验目的1)掌握利用DEFORM-3D对塑性成型力学问题进行有限元建模的基本步骤。
2)掌握CAD和CAE软件的配合使用,进行塑性成型力学问题的模拟分析。
二、实验原理DEFORM-3D是在一个集成环境内综合建模、成形、热传导和成形设备特性进行模拟仿真分析。
适用于热、冷、温成形,提供极有价值的工艺分析数据。
如:材料流动、模具填充、锻造负荷、模具应力、晶粒流动、金属微结构和缺陷产生发展情况等。
DEFORM- 3D功能与2D类似,但它处理的对象为复杂的三维零件、模具等。
不需要人工乾预,全自动网格再剖分。
前处理中自动生成边界条件,确保数据准备快速可靠。
DEFORM- 3D模型来自CAD系统的面或实体造型(STL/SLA)格式。
DEFORM -3D 是一套基于工艺模拟系统的有限元系统(FEM),专门设计用于分析各种金属成形过程中的三维 (3D) 流动,提供极有价值的工艺分析数据,有关成形过程中的材料和温度流动。
典型的DEFORM-3D应用包括锻造、挤压、镦头、轧制,自由锻、弯曲和其他成形加工手段。
三、实验步骤1.DEFORM前处理过程(Pre Processer)进入DEFORM前处理窗口。
了解DEFORM前处理中的常用图标设置模拟控制增加新对象网格生成材料的选择确立边界条件温度设定凸模运动参数的设置模拟控制设定设定对象间的位置关系对象间关系“Inter-Object”的设定生成数据库退出前处理窗口2.DEFORM求解(Simulator Processer)3.DEFORM后处理(Post Processer)了解DEFORM后处理中的常用图标。
步的选择真实应变金属流线载荷——行程曲线体积变化曲线四、实验过程五、实验结果组别1(10/0.08)组别3(30/0.08)组别五(10/0.15)组别六。
2013(10级)塑性模具生产实习报告撰写指导书

2013(10级)塑性模具生产实习报告撰写指导书第一篇:2013(10级)塑性模具生产实习报告撰写指导书报告内容:一、实习目的二、实习安排(指实习地点及进行方式,按企业分别列出即可)三、实习内容(围绕实习任务,按工艺方法如冲压、锻造、铸造、机械加工以及模具加工等集中归纳撰写)四、总结(感受与建议)实习报告要求用河南科技大学作业纸(题头为绿色)——由学校教务处监制印刷的。
模具、塑性专业生产实习报告撰写指导书一、实习目的与要求生产实习是专业教学计划中的重要组成部分,是学生获得专业基础知识的重要环节之一;也是毕业后参加实际工作的一次预演。
学生在实习前已学完所有基础理论课程,并进入《塑料工艺与模具》、《冲压工艺与模具》、《锻造工艺与模具》、《模具制造学》和《成形机械》等专业课程的学习;在实习中应深入生产加工现场,认真实习,获取直接知识,巩固所学理论,完成实习指导人(现场工程师或技术人员)所布置的各项工作任务,培养和锻炼独立分析问题和解决问题的能力。
其主要要求为:1、通过实习在现场直接观察,在了解零件的生产过程、模具结构、设备结构和特点基础上,查阅必要的工艺文件和图纸。
了解塑料模具、冲模结构;了解某些新材料、新工艺和现代化管理方法等。
丰富和扩大学生的专业知识领域。
2、通过生产实习,使学生对塑性成形工艺和典型模具制造工艺等内容进一步加深理解,巩固课堂所学内容。
3、通过现场实习了解企业的组织机构及企业经营管理方式;对工序的组成,加工成本的控制,生产要素的管理有所了解。
4、有条件时,可参加实际生产工作,灵活运用已学的理论知识解决实际问题,培养学生独立分析问题和解决问题的能力。
5、学习广大工人和现场技术人员的优秀品质,树立刻苦钻研科学技术,为祖国建设多作贡献的思想。
学习质量管理的基本方法;对工艺质量过程控制有所了解。
了解现行的国家有关模具质量检验和管理的标准。
二、实习内容要求:1、看懂工程设计图;了解制件的性质、规格、生产工艺过程等。
- 1、下载文档前请自行甄别文档内容的完整性,平台不提供额外的编辑、内容补充、找答案等附加服务。
- 2、"仅部分预览"的文档,不可在线预览部分如存在完整性等问题,可反馈申请退款(可完整预览的文档不适用该条件!)。
- 3、如文档侵犯您的权益,请联系客服反馈,我们会尽快为您处理(人工客服工作时间:9:00-18:30)。
实验一 利用拉伸试验绘制真实应力应变曲线一、实验目的1.掌握如何利用拉伸实验测定分析金属材料塑性变形抗力规律;2.掌握利用拉伸图()ΔL F -绘制真实应力曲线()∈-S 的方法;3.进一步理解真实应力-应变曲线的意义;4.熟悉WAW -1000C 微机控制电液伺服万能材料试验机的使用方法。
二、实验原理各种变形温度、速度等条件下的流动应力变化规律对研究金属塑性成形问题是必不可少的。
这些规律通常表达为条件应力-应变曲线()εσ-或真实应力-应变曲线()∈-S 。
1.真实应力(S )是单向应力状态下作用于试样瞬时断面上的应力,也即瞬时的流动应力,它反映了材料的变形抗力,可表示为:AF S = (1-1) 式中: F —瞬时载荷;A —试样瞬时断面积。
而条件应力A F σ= (1-2) 由于式中0A 指的是试样的原始断面积,因此,真实应力更精确地反映了某一瞬时作用于试样断面上的流动应力。
2.真实应变按不同的应变表示方式可有三种形式:(1)相对伸长0010L L L L ΔL ε-==(1-3)式中:0L —试样原始标距长度;1L —拉伸后标距的长度。
(2)相对断面收缩率10A A A ψ-= (1-4) 式中:0A —试样原始断面积;1A —拉伸过程中试样瞬时断面积。
(3)对数应变(真实应变)LdL d ∈= (1-5) 式中:L —试样的瞬时长度;dL —瞬时的试样长度改变量。
显然,对数应变反映了瞬态的变形,比其它两种应变更真实地表示了试样的变形程度。
另外,对数应变还具备其所特有的优点:(a )对数应变具有可加性,即当连续分段变形时,总的应变等于各段应变之和;(b )试样在拉伸一倍再压缩至原长时的两种对数应变值互为相反数,即:l n 2L 2L 2L L =∈-=∈→→(c )用对数应变表示的拉伸真实应力-应变曲线和压缩真实应力-应变曲线完全重合, 仅应力有拉、压之分;(d )用对数应变表示的真实应力-应变曲线还与简单加载条件 下的等效应力-等效应变曲线完全相同。
以上说明,用真实应力和对数应变表示的真实应力-应变曲线更具有普遍意义。
由于塑性条件与应力状态无关,所以都以单向拉伸时的屈服应力作为真实应力。
3.真实应力-应变曲线的建立真实应力-应变曲线可以通过拉伸实验、压缩实验和扭转实验等方法来建立,而作真实应力-真实应变曲线()∈-S 比较方便,可以由拉伸图作出的条件应力-应变曲线()εσ-做相应的换算得出。
图1-1 条件应力-应变曲线与真实应力-应变曲线由图1-1看出,与条件应力-应变曲线相比,真实应力-应变曲线没有极值,在试样屈服后单调上升,表明材料抗塑性变形的能力随应变的增加而增加,即不断产生硬化(故真实应力-应变曲线又称为硬化曲线)。
在真实应力-应变曲线上与抗拉强度bσ相对应的点的切线与横轴交点到该点在横坐标距离为1,另外:应变关系:()ε1ln L L ln01+=∈= (1-6) 应力关系:在颈缩阶段以前,为均匀拉伸,故()ε1σA F S +== (1-7)在颈缩阶段以后,试样处于不均匀的三向应力状态,从出现颈缩一直到拉断是不均匀拉伸,存在“形状硬化”现象,要获得单向应力状态下的真实应力,须用齐别尔公式进行修正,以去除“硬化效应”的影响:8ρd 1S S'k += (1-8) 式中:'S —去除形状硬化后的真实应力;S —包含形状硬化的真实应力;ρ—细颈处试样外形的曲率半径。
图1-2 细颈处试样外形尺寸一般情况下,试件的最大应变可达1.0以上,但最大应变量受到出现颈缩的限制,另外,也只能测出试样在颈缩开始的瞬间(b 点)和断裂点(k 点)的载荷和截面积,因此颈缩开始后仅b 、k 两点是精确的,同时(1-8)式只是一个近似公式,这样使得绘制出的真实应力-应变曲线仅在颈缩阶段以前(3.0~2.0 )是精确的。
当变形量很大时,可用压缩试验来做,甚至可获得ε=3.9的变形程度。
三、实验条件1.WAW -1000C 微机控制电液伺服万能材料试验机;2.游标卡尺、冲子、铁锤等;3.45#标准试样(如图1-3)一个。
图1-3 标准试样 四、试验方法与步骤1.拉伸试样取标距100 mm ,精确测量试样原始尺寸:标距0L ,直径0D ,在标距的两端和中间三处,分别按互相正交的位置各测量一次,取以三处中最小一处的平均直径0D ,计算原始截面面积;2.试验机准备,装好记录纸,调整试验机的测量系统;3.装夹试样,进行拉伸试验;缓慢加载,观察当试验机指针上下摆动时,说明试样开始发生屈服,此时指针摆到最小位置时的载荷值为屈服载荷Fs ,继续加载至试样断裂,从指针上读出最大载荷F b ;4.将试样从断口处紧连在一起,按图1-2测量断口处的k d ,D ,b 及此时的标距1L ;5.处理数据,绘制真实应力-应变曲线由(1-2)式,(1-3)式,选取适当比例,将拉伸曲线转化重合为条件应力-应变曲线()εσ-,如图1-4所示。
断裂时的载荷F k 可根据记录纸上该点与Fs ,F k 在图中相对位置量出,另外,由于试样存在弹性变形,拉断(即卸载)后,将沿平行于oc 的直线kd 回弹,所以,测量出01L L ΔL'-=必须折算成ΔL ,并按比例量出其值后才能代入公式计算。
然后再利用相应公式,将条件应力转化为真实应力,相对伸长转化对数应变,从而就绘制出真实应力-应变曲线()∈-S 。
图1-4 拉伸图与条件应力-应变图五、实验报告要求1.写明试验的目的、原理、设备以及试验步骤;2.正确处理数据,绘制真实应力-应变曲线()∈-S ;3.请说明真实应力-应变曲线的意义。
实验二 塑性成形中的摩擦问题设计性实验摩擦问题是塑性成形中的突出问题,对塑性成形工艺有重大影响。
以此知识点开展设计性实验内容,加强学生的设计能力,较深入地研究塑性成形中摩擦的特点、数学模型以及摩擦系数测定的方法。
项目一 圆环镦粗法测定金属材料在塑性变形时的摩擦系数一、实验目的1.熟悉利用圆环镦粗法测定金属材料在塑性变形时摩擦系数的方法;2.了解摩擦系数理论校准曲线的绘制方法和过程;3.观察圆环镦粗的内、外孔的变形规律;4.认识变形与摩擦及润滑的关系。
二、基本原理在塑性加工中,被加工金属与工、模具之间都有相对运动或相对运动的趋势,因而在接触表面便产生阻止切向运动的阻力,即摩擦力。
它是高压下产生的摩擦,而且多在高温下进行,情况复杂。
摩擦系数通常是指接触面上的平均摩擦系数。
为了正确计算金属材料在塑性变形时的变形力,必须测定摩擦系数,或者根据具体变形条件、润滑条件合理选用由实验测定出的摩擦系数值。
1.根据库仑定律,摩擦系数μ可表示为:N σμτ⋅= (2-1)式中:τ —接触表面上的摩擦切应力;N σ—接触表面上的法向(正)应力。
在金属塑性成形时,K τ=,N σS =,则分别由Tresca 屈服准则和Mises 屈服准则可得0.577~0.5μ max =。
当K τ<时,摩擦切应力的变化规律的两种假设—库仑摩擦条件和常摩擦力条件,可表示为:S μ'τ⋅= (2-2)式中: S —流动应力;μ'—(换算)摩擦系数,它与摩擦因子m 的关系是:2m μ'=(Tresca 屈服准则) 3m μ'= (Mises 屈服准则) 摩擦因子m 是随变形条件而变的常数。
2.摩擦系数的测定目前常用的摩擦系数的测定方法有;(1)直接测定法,即直接测出正应力和切应力,从而确定摩擦系数,如夹钳-轧制法等;(2)间接测定法,即根据摩擦系数对金属中性层位置的影响测定摩擦系数,如圆环镦粗法、楔块镦粗法等。
本实验项目采用圆环镦粗法测定金属材料在塑性变形时的摩擦系数。
图2-1 圆环镦粗的变形情况a) 镦粗前圆环试样 b) m <m c c) m >m c在平砧间镦粗圆环试件时,由于试件与砧面间摩擦状况不同,即摩擦系数不同,圆环试件的变形情况不同,其内径、外径在镦粗后也将有不同的变化。
摩擦系数很小时,镦粗后圆环的内径、外径都要增大(图2-1b ),随着摩擦系数的增加,镦粗试件的变形特征逐渐发生变化,当摩擦系数超过某一临界值(m c =0.05~0.06),在圆环中出现一个半径为n R 的中性层:该层以外的金属向外流动,以内的金属向中心流动,使得圆环的外径增大,内径减小(图2-1c )。
实验和研究表明,中性层半径n R 与摩擦因子m 有关,因此根据中性层半径n R 和圆环尺寸可以确定摩擦因子m 值。
虽然中性层半径无法直接测量,由于镦粗后的圆环内径变化与中性层半径n R 有关,所以也可以由测量内径确定摩擦系数。
通常是利用塑性理论对圆环变形进行分析,在理论上推导出中性层半径n R 、摩擦因子m 与圆环尺寸的理论关系,求出给定一个m 时在连续的较小的压缩量下与圆环内径变化的对应关系,进而由此可作出下同摩擦系数条件下,内径随压缩量而变化的一系列曲线 — 摩擦系数理论校准曲线。
直接根据每次镦粗后圆环的内径、高度查出试件在这种变形条件下的摩擦因子m 并求得摩擦系数μ值。
三、摩擦系数标定曲线的绘制根据功平衡法(即能量法),并作如下假设:金属材料服从Mises 屈服准则,接触面上的摩擦切应力符合常摩擦力条件【参见式(2-2)】,均匀变形,变形前后体积不变,而且不考虑形状硬化等情况。
由于摩擦系数和中性层半径n R 在镦粗过程中都在变化,因此采用等小变形法绘制理论曲线。
1.根据圆环原始尺寸求摩擦因子的临界值m c : (此时0r R n =)⎪⎪⎪⎪⎪⎪⎭⎫ ⎝⎛⎪⎪⎭⎫ ⎝⎛++⎪⎪⎭⎫ ⎝⎛⎪⎪⎭⎫ ⎝⎛-=400200000c 3113ln 12m r R r R R r R H (2-3) 式中:H —镦租前圆环高度;0r —镦粗前圆环内径;0R —镦粗前圆环外径。
2.预先给定一系列m 值,由圆环原始尺寸求n R(如可以分别令m =0,0.05,0.1,0.2,0.3,0.4,0.5,0.6,0.7,0.8,0.9,1.0,各求出一组镦粗后的圆环尺寸)1)当0r R n ≤,即c m m ≤时()⎥⎥⎦⎤⎢⎢⎣⎡⋅⎪⎪⎭⎫ ⎝⎛--⎥⎥⎦⎤⎢⎢⎣⎡⋅⎪⎪⎭⎫ ⎝⎛-=x R r x x x R r R R n 4002400011123 (2-4) 式中,2000001 R m exp ⎪⎭⎪⎬⎫⎪⎩⎪⎨⎧⎥⎦⎤⎢⎣⎡⎪⎪⎭⎫ ⎝⎛-⎪⎭⎫ ⎝⎛-=R r H r R x 注意:若在c m m <时,求出的n R 满足0r R n >和式(2-5),则改用式(2-6)计算n R 。
⎪⎪⎪⎪⎪⎪⎭⎫ ⎝⎛⎪⎪⎭⎫ ⎝⎛++⎪⎪⎭⎫ ⎝⎛⎪⎪⎭⎫ ⎝⎛-≥4002000003113ln 121m r R r R R r H R (2-5) 2)当00R R r n <<,即c m m >时⎪⎪⎪⎭⎪⎪⎪⎬⎫⎪⎪⎪⎩⎪⎪⎪⎨⎧-⋅⎥⎥⎦⎤⎢⎢⎣⎡-⎪⎪⎭⎫ ⎝⎛⎪⎪⎭⎫ ⎝⎛++⎪⎪⎭⎫ ⎝⎛-≈1m 321111m 32020000202020R H r R R r r R H R R n (2-6)3.设圆环在小变形(1=∆h mm )下n R 保持不变,利用体积不变条件求变形后圆环的内径1r 、外径1R :()h H r R h R r n n 20221--= (2-7) ()2120201r r R h H R +-= (2-8) 式中,h —圆环镦粗后的高度,h H h ∆-=4.将第一次小变形后的1r ,1R 和h 作为第二次等小变形前的原始尺寸0r ,0R 和H ,重复步骤1、2、3计算出第二次等小变形后的圆环尺寸,如此反复连续计算,直到压缩量为原始高度的50%为止,就得出一组m 、h 、0r 对应关系。