烧结配料对选矿的影响
烧结配料
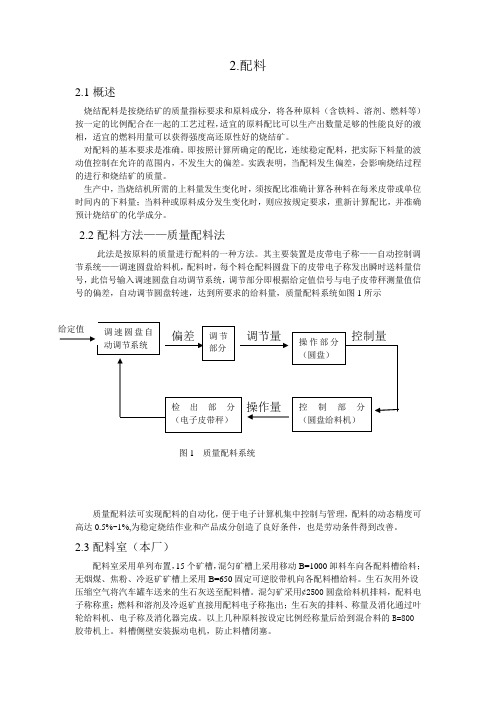
2.配料2.1概述烧结配料是按烧结矿的质量指标要求和原料成分,将各种原料(含铁料、溶剂、燃料等)按一定的比例配合在一起的工艺过程,适宜的原料配比可以生产出数量足够的性能良好的液相,适宜的燃料用量可以获得强度高还原性好的烧结矿。
对配料的基本要求是准确。
即按照计算所确定的配比,连续稳定配料,把实际下料量的波动值控制在允许的范围内,不发生大的偏差。
实践表明,当配料发生偏差,会影响烧结过程的进行和烧结矿的质量。
生产中,当烧结机所需的上料量发生变化时,须按配比准确计算各种料在每米皮带或单位时间内的下料量;当料种或原料成分发生变化时,则应按规定要求,重新计算配比,并准确预计烧结矿的化学成分。
2.2配料方法——质量配料法此法是按原料的质量进行配料的一种方法。
其主要装置是皮带电子称——自动控制调节系统——调速圆盘给料机,配料时,每个料仓配料圆盘下的皮带电子称发出瞬时送料量信号,此信号输入调速圆盘自动调节系统,调节部分即根据给定值信号与电子皮带秤测量值信号的偏差,自动调节圆盘转速,达到所要求的给料量,质量配料系统如图1所示质量配料法可实现配料的自动化,便于电子计算机集中控制与管理,配料的动态精度可高达0.5%-1%,为稳定烧结作业和产品成分创造了良好条件,也是劳动条件得到改善。
2.3配料室(本厂)配料室采用单列布置,15个矿槽,混匀矿槽上采用移动B=1000卸料车向各配料槽给料;无烟煤、焦粉、冷返矿矿槽上采用B=650固定可逆胶带机向各配料槽给料。
生石灰用外设压缩空气将汽车罐车送来的生石灰送至配料槽。
混匀矿采用¢2500圆盘给料机排料,配料电子称称重;燃料和溶剂及冷返矿直接用配料电子称拖出;生石灰的排料、称量及消化通过叶轮给料机、电子称及消化器完成。
以上几种原料按设定比例经称量后给到混合料的B=800胶带机上。
料槽侧壁安装振动电机,防止料槽闭塞。
调速圆盘自动调节系统 给定值 控制量偏差 调节部分 调节量 操作部分(圆盘) 操作量控制部分 (圆盘给料机)检出部分 (电子皮带秤) 图1 质量配料系统2.3.1配料主要设备A圆盘给料机a特点:给料粒度范围大(0-50mm),给料均匀准确,调整容易、运转平稳可靠,管理方便。
烧结原料水分对烧结生产有何影响
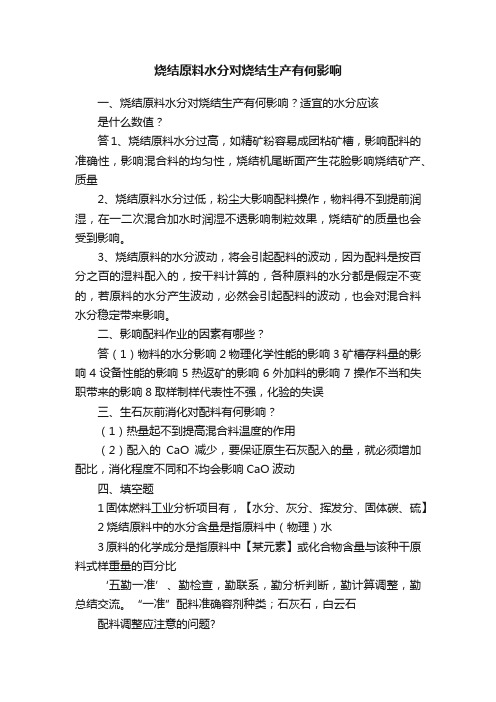
烧结原料水分对烧结生产有何影响一、烧结原料水分对烧结生产有何影响?适宜的水分应该是什么数值?答1、烧结原料水分过高,如精矿粉容易成团粘矿槽,影响配料的准确性,影响混合料的均匀性,烧结机尾断面产生花脸影响烧结矿产、质量2、烧结原料水分过低,粉尘大影响配料操作,物料得不到提前润湿,在一二次混合加水时润湿不透影响制粒效果,烧结矿的质量也会受到影响。
3、烧结原料的水分波动,将会引起配料的波动,因为配料是按百分之百的湿料配入的,按干料计算的,各种原料的水分都是假定不变的,若原料的水分产生波动,必然会引起配料的波动,也会对混合料水分稳定带来影响。
二、影响配料作业的因素有哪些?答(1)物料的水分影响2物理化学性能的影响3矿槽存料量的影响4设备性能的影响5热返矿的影响6外加料的影响7操作不当和失职带来的影响8取样制样代表性不强,化验的失误三、生石灰前消化对配料有何影响?(1)热量起不到提高混合料温度的作用(2)配入的CaO减少,要保证原生石灰配入的量,就必须增加配比,消化程度不同和不均会影响CaO波动四、填空题1固体燃料工业分析项目有,【水分、灰分、挥发分、固体碳、硫】2烧结原料中的水分含量是指原料中(物理)水3原料的化学成分是指原料中【某元素】或化合物含量与该种干原料式样重量的百分比‘五勤一准’、勤检查,勤联系,勤分析判断,勤计算调整,勤总结交流。
“一准”配料准确容剂种类;石灰石,白云石配料调整应注意的问题?滞后性,返矿循环影响,除尘放灰影响烧结矿主要质量指标,TFe,SiO2,CaO,MgO,FeO,Al2O3,碱度R,转鼓。
烧结原料分;含铁原料,溶剂,燃料配料作业的定义根据对烧结矿的质量指标要求和原料成分将各种烧结料(含铁原料,溶剂,燃料)按一定的比例组成配合料的工序过程作用和意义1提高烧结成分的稳定性对高炉顺产增铁节焦具有重大意义。
搞好配料是高炉优质高产,低耗的先决条件2精心配料是获得优质烧结矿的前提。
烧结原料总结汇报

烧结原料总结汇报烧结原料总结汇报烧结原料是指用于制备烧结矿的各种原材料,包括铁矿石、焦炭、石灰石和配料等。
烧结过程是指将这些烧结原料经过炉内高温煅烧、氧化还原和结晶等反应,形成烧结矿的过程。
烧结原料在烧结过程中起着至关重要的作用,对烧结矿的质量和性能具有直接影响。
下面将对常见的烧结原料进行总结汇报。
1. 铁矿石:铁矿石是制备烧结矿的主要原料,它是由铁矿石矿石和氧化铁矿石组成的。
常见的铁矿石有赤铁矿、磁铁矿和褐铁矿等。
铁矿石的物理性质和化学成分直接影响烧结矿的组成和性能。
2. 焦炭:焦炭是烧结过程中重要的还原剂,它具有高固定碳含量、低灰、低硫和良好的机械强度等特点。
焦炭在高温条件下能够和铁矿石反应产生一系列还原反应,从而促进烧结矿中的铁矿石氧化还原反应的进行。
3. 石灰石:石灰石是烧结矿的主要熔剂,它在高温条件下能够与铁矿石中的硅酸盐和氧化铁石进行反应,生成易熔的矽酸钙和液相。
石灰石的质量和石灰石与铁矿石的配比对烧结矿的熔融性、融化温度和液相组成等有很大影响。
4. 配料:配料是指将各种烧结原料按一定的比例混合制备成的烧结原料混合料。
配料的质量和配比直接影响烧结矿的成分和物理性能。
通过合理的配料,可以在一定程度上改善烧结矿的熔融性、弹性、抗返矿性能等。
综上所述,烧结原料对烧结矿的质量和性能具有重要的影响。
铁矿石是烧结矿的主要原料,其物理性质和化学成分对烧结矿的组成和性能起着决定性作用。
焦炭作为还原剂能够促进烧结矿中的氧化还原反应。
石灰石作为熔剂能够改善烧结矿的熔融性和融化温度。
通过合理的配料,可以改善烧结矿的物理性能和抗返矿性能。
合理选择和使用烧结原料,优化烧结矿的质量和性能,对冶金行业的发展和节能减排具有重要意义。
通过对烧结原料的总结汇报,我们可以更好地理解烧结过程和烧结矿的形成机制,为冶金行业的研究和生产提供技术支持。
同时,我们也要强调烧结原料的合理使用和资源综合利用,提高烧结矿质量,减少能源消耗和环境污染,助力可持续发展的目标实现。
烧结矿中FeO对烧结矿质量的影响
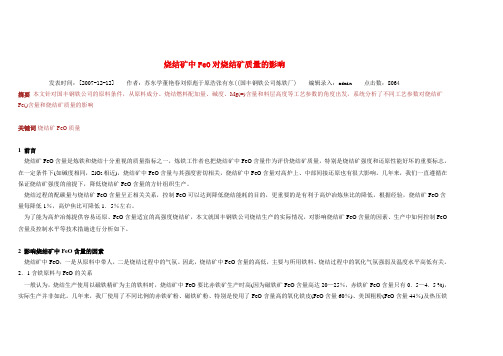
摘要本文针对国丰钢铁公司的原料条件,从原料成分、烧结燃料配加量、碱度、Mg(=)含量和料层高度等工艺参数的角度出发,系统分析了不同工艺参数对烧结矿Fe()含量和烧结矿质量的影响关键词烧结矿 FeO 质量1 前言烧结矿FeO含量是炼铁和烧结十分重视的质量指标之一,炼铁工作者也把烧结矿中FeO含量作为评价烧结矿质量,特别是烧结矿强度和还原性能好坏的重要标志,在一定条件下(如碱度相同,SiO2相近),烧结矿中FeO含量与其强度密切相关,烧结矿中FeO含量对高炉上、中部间接还原也有很大影响。
几年来,我们一直遵循在保证烧结矿强度的前提下,降低烧结矿FeO含量的方针组织生产。
烧结过程的配碳量与烧结矿FeO含量呈正相关关系,控制FeO可以达到降低烧结能耗的目的,更重要的是有利于高炉冶炼焦比的降低,根据经验,烧结矿FeO含量每降低1%,高炉焦比可降低1.5%左右。
为了能为高炉冶炼提供容易还原、FeO含量适宜的高强度烧结矿,本文就国丰钢铁公司烧结生产的实际情况,对影响烧结矿FeO含量的因素、生产中如何控制FeO 含量及控制水平等技术措施进行分析如下。
2 影响烧结矿中FeO含量的因素烧结矿中FeO,一是从原料中带人,二是烧结过程中的气氛。
因此,烧结矿中FeO含量的高低,主要与所用铁料、烧结过程中的氧化气氛强弱及温度水平高低有关。
2.1含铁原料与FeO的关系一般认为,烧结生产使用以磁铁精矿为主的铁料时,烧结矿中FeO要比赤铁矿生产时高(因为磁铁矿FeO含量高达20—25%,赤铁矿FeO含量只有0.5—4.5 %),实际生产并非如此。
几年来,我厂使用了不同比例的赤铁矿粉、磁铁矿粉、特别是使用了FeO含量高的氧化铁皮(FeO含量60%)、美国粗粉(FeO含量44%)及热压铁粉(FeO含量95%),使用了高FeO含量的矿粉,燃料消耗明显降低,烧结矿FeO含量无上升,烧结矿强度也没有影响(见表1、表2)。
由表2可以看出,使用FeO含量高的磁铁矿粉、热压铁粉,与FeO含量低的赤铁矿粉,在R2相近的情况下,生产出的烧结矿FeO与强度并无明显变化,FeO含量高的含铁料燃料消耗反而低,原因如下:磁铁精粉细:—200目占60%左右,比表面积大,矿物单体分离较完全,在燃料配比低,氧化气氛强的条件下,容易与通过料层的氧发生反应:2Fe3O4+1/2O2=3Fe2O3采用不同FeO含量的铁矿物烧结,最后FeO含量基本接近,原因是烧结熔融带中大量的Fe2O3转变成FeO,原始赤铁矿中FeO含量只有0.4—4.5%,经过熔融带,FeO升高,在冷凝与冷却过程中,与吸入的氧气进行再氧化,放出部分热量,所以,烧结矿中FeO含量很接近。
项目三 烧结配料
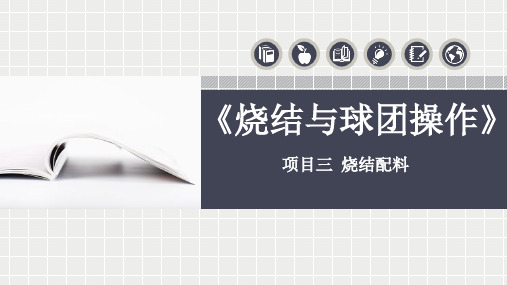
用熔剂、返矿粉等配料,但不适用水分含量较大的精矿粉;
1— 电 动 机 ;2— 减
直筒式套筒采用刮刀排料,堵料现象较蜗牛式套筒轻,但
速器;3—圆盘;4—
下料量波动大。故当精矿或粉矿用量较大时,宜用带活动
套筒;5—闸门
刮刀的套筒;当熔剂或燃料用量少,而且要求精确性高时,
宜用闸门式套筒。
相关知识
一、配料设备
设混合矿减重ax =0.084%×0.9+1.06%=1.14%;
石灰石减重a =42.25%;
炉尘减重a尘
=10.87%+0.102%×0.9=10.96%;
焦粉减重a焦 =80.9%+0.8%×0.9+2.17%=83.7%;
总减重a=Xax +Ya +8a尘 +8a焦 =0.0114X+0.4225Y+0.88+6.7=0.0114X+0.4225Y+7.58
偏大,因此,应根据干料量的变化来进行必要的调整。
4.同一品种原料下料量过大时,最好用两台给料机给料,可减少下料量的波动。
5.应十分注意下料量少的物料品种的下料量。由于影响下料量的因素较多,在人工操作
时要严格配料操作,班与班统一操作,要勤称量勤校正。铁料每15min校正一次,根据
具体情况规定各种下料量的波动范围。
掌握影响配料准确的因素,熟悉实际烧结矿成分与配料计算值发生偏差
的原因及调整措施。
任务
描述
配料操作是根据配料单准确配料,使用圆盘给料机给料,电子皮带秤称
量依次按配比加入混匀矿、返矿、熔剂、燃料等原料,通过皮带运输到烧结
混匀系统。配料必须按配料单准确配料,使配合料的化学成分合乎规定;配碳
烧结配矿优化及高炉生产应对实践

M etallurgical smelting冶金冶炼烧结配矿优化及高炉生产应对实践张利波摘要:近些年,高炉炼铁一直是冶炼生铁过程中应用的最重要的技术,居于主导地位。
最近几年,全球的学者即使研究出许多高炉炼铁技术,不过在制作成本的经济性方面,依旧不能和以往的高炉制造技术进行比较。
国内,因为历史条件与制造成本的干预,非高炉炼铁技术的发展速度较慢,超过百分之九十五的生铁依旧借助高炉进行制作。
高炉生产期间,入炉原料重点是烧结矿、球团矿和块矿,而且烧结矿的比例高于百分之八十。
所以,烧结矿的品质高低在高炉生产过程中占据着主导作用,提升烧结矿品质对于缩减制作成本、保证高炉良好的运行具备着较高的作用。
关键词:烧结配矿优化;高炉生产;应对实践对策现如今使用的矿粉、矿石以及含铁工业物料等,使得烧结原料逐渐繁杂,如何通过原料的优化搭配实现品质最优、成本最优是钢铁生产重点关注的问题。
烧结矿是高炉的主要“口粮”,其质量的好坏直接影响高炉生产稳定和各项经济技术指标的完成。
为了确保烧结矿质量稳定,工作人员运用智能化手段,提升烧结配料精度,改善烧结矿质量,为高炉高效生产筑牢保障。
1 研究背景1.1 铁矿粉市场行情在我国环保政策高效实施的环境下,钢铁公司开始限制产量,铁矿石的需求数目逐渐下降。
不过在2017年~2018年鉴因为钢铁利润空间的变化,个别产能被释放,导致铁矿石的需求数目逐渐提升。
身为铁矿石的出产地澳大利亚与巴西境内铁矿石的出产量也随之增加,不过市场依然处于供需不平衡的状态,导致铁矿石的流通价格较高。
并且,因为持续的挖掘与应用优质资源,导致地球上的优质铁矿石数量逐步的减少,铁矿石供需框架的调节会是后期国际上需要一起面临与开展的工作。
我国铁矿石的存储数量位于世界前列,大约为整体存储量的百分之十二,整体的应用潜力较高。
由于铁矿的开采、加工工艺的提升,铁矿资源的整体应用会呈现出良好的经济性。
1.2 烧结配矿结构优化的理论基础低品矿粉为减少烧结资金投入最为重要的方式,不过品味下降可能导致非铁元素的高效提升,造成烧结矿品质降低,为后续高炉生产留下隐藏的危害,科学的应用铁矿粉高温特性展开烧结配矿,能够提升烧结配矿的效果。
高炉炼铁对烧结矿的要求
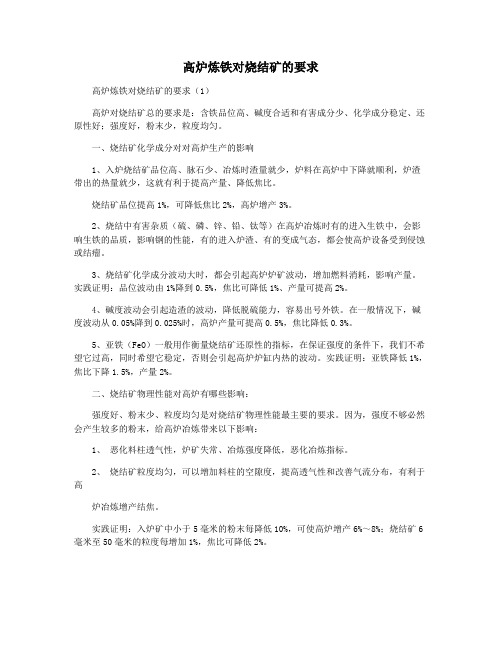
高炉炼铁对烧结矿的要求高炉炼铁对烧结矿的要求(1)高炉对烧结矿总的要求是:含铁品位高、碱度合适和有害成分少、化学成分稳定、还原性好;强度好,粉末少,粒度均匀。
一、烧结矿化学成分对对高炉生产的影响1、入炉烧结矿品位高、脉石少、冶炼时渣量就少,炉料在高炉中下降就顺利,炉渣带出的热量就少,这就有利于提高产量、降低焦比。
烧结矿品位提高1%,可降低焦比2%,高炉增产3%。
2、烧结中有害杂质(硫、磷、锌、铅、钛等)在高炉冶炼时有的进入生铁中,会影响生铁的品质,影响钢的性能,有的进入炉渣、有的变成气态,都会使高炉设备受到侵蚀或结瘤。
3、烧结矿化学成分波动大时,都会引起高炉炉矿波动,增加燃料消耗,影响产量。
实践证明:品位波动由1%降到0.5%,焦比可降低1%、产量可提高2%。
4、碱度波动会引起造渣的波动,降低脱硫能力,容易出号外铁。
在一般情况下,碱度波动从0.05%降到0.025%时,高炉产量可提高0.5%,焦比降低0.3%。
5、亚铁(FeO)一般用作衡量烧结矿还原性的指标,在保证强度的条件下,我们不希望它过高,同时希望它稳定,否则会引起高炉炉缸内热的波动。
实践证明:亚铁降低1%,焦比下降1.5%,产量2%。
二、烧结矿物理性能对高炉有哪些影响:强度好、粉末少、粒度均匀是对烧结矿物理性能最主要的要求。
因为,强度不够必然会产生较多的粉末,给高炉冶炼带来以下影响:1、恶化料柱透气性,炉矿失常、冶炼强度降低,恶化冶炼指标。
2、烧结矿粒度均匀,可以增加料柱的空隙度,提高透气性和改善气流分布,有利于高炉冶炼增产结焦。
实践证明:入炉矿中小于5毫米的粉末每降低10%,可使高炉增产6%~8%;烧结矿6毫米至50毫米的粒度每增加1%,焦比可降低2%。
烧结矿强度差,粉末就多,使高炉炉尘吹出量增加,增加了炼铁的原料消耗,浪费了资源。
一个1000万吨生铁的炼铁厂,若吨铁炉尘量增加50公斤,则一年多吹走的路尘量就达50万吨。
感谢您的阅读,祝您生活愉快。
烧结实业部质量指标影响因素

烧结内部控制要求:
成分 TFe FeO MgO R2 Pb Zn Na2O+k2O 转鼓 粒度 要求 ≥55% 9%-11.5% 2.2%-2.5%
1.8%±0.1%
备注
原料稳定后考虑1.8%±0.08%
≤0.02% ≤0.02% ≤0.1 ≥77.33% 5-10≤23%
烧 结 品 质
凝 聚 成 才
好,但是流动性差,不易排出炉外,从而影响高炉顺行。相反,如果酸性氧化
物含量高,炉渣的流动性好,凝固后的固态炉渣呈现玻璃状,一般称为玻璃渣 或者长渣,这样的炉渣脱硫效果很差,但是流动性好。所以高炉操作者要调整 炉渣的成分,也就是炉渣的碱度,既保持优良的流动性,也能有很好的脱硫效 果,使生铁达到一类要求。
的之接还原;
烧 结 品 质
凝 聚 成 才
烧结分厂
烧结矿对高炉冶炼的影响及质量的要求 一般烧结矿碱度在1.85±0.1条件下,软化的开始温度在1200-1220, 软化终了温度在1320-1330,软化温度区间在110-120,凡软化温度区 间(T2-T1)变小,对降低高炉软熔带的区间是有利的。反之,如果软 化开始温度降低,软化温度区间自然变大,不利于软熔带透气性改善, 一般影响烧结矿荷重软化性能的主要因素有: 一是烧结矿的还原性能:烧结矿还原性能的改善有利于烧结矿在升温过 程中形成液相,温度升高,导致烧结矿的软化开始温度升高。 二是烧结矿中脉石的熔点:在烧结矿碱度基本不变的条件下,烧结矿中 脉石的熔点不变,碱度低熔点低,碱度高熔点高;
因为磷化物是催性物质,冷凝时聚集于钢的晶界周围,减弱晶粒间的结 合力,使钢材在冷却时产生很大的脆性,从而造成钢的冷脆现象。由于
磷早烧结和选矿过程中不易脱除,在高炉冶炼过程中几乎全部还原进入
- 1、下载文档前请自行甄别文档内容的完整性,平台不提供额外的编辑、内容补充、找答案等附加服务。
- 2、"仅部分预览"的文档,不可在线预览部分如存在完整性等问题,可反馈申请退款(可完整预览的文档不适用该条件!)。
- 3、如文档侵犯您的权益,请联系客服反馈,我们会尽快为您处理(人工客服工作时间:9:00-18:30)。
烧结配料对选矿的影响摘要:烧结成分的稳定性对高炉顺行、以及增铁节焦具有重大的意义,因此,搞好配料工作是高炉优质、高产、低耗的先决条件,是获得优质烧结矿的前提,烧结矿使用的原料种类繁多,物理化学性质各不相同。
为了合理综合利用国家资源,生产出符合高炉冶炼要求而且成分相对稳定的烧结矿,同时还要兼顾生产过程的要求,烧结厂必须根据本厂原料的供应情况及物理化学性质选择合适的原料,通过计算确定配料比,并严格按配比确定每条电子称皮下料量,经常进行重量检查(跑盘)及时调整。
正文:所谓烧结,就是把粉状物料转变为致密体,是一个传统的工艺过程。
人们很早就利用这个工艺来生产陶瓷、粉末冶金、耐火材料、超高温材料等。
一般来说,粉体经过成型后,通过烧结得到的致密体是一种多晶材料,其显微结构由晶体、玻璃体和气孔组成。
烧结过程直接影响显微结构中的晶粒尺寸、气孔尺寸及晶界形状和分布。
无机材料的性能不仅与材料组成(化学组成与矿物组成)有关,还与材料的显微结构有密切的关系。
现代工艺所用的烧结方法有鼓风烧结、抽风烧结、在烟气中烧结三种,其中最常用的是抽风烧结。
现代工艺的烧结流程一般包括原燃料的接受、贮存,溶剂、燃料的准备,配料,混合,制粒,布料,点火烧结,热矿破碎,热矿筛分,热矿冷却,冷矿筛分,铺底料、成品烧结矿及返矿的贮存、运输等工艺环节。
在烧结过程中最重要的环节要数配料了,搞好配料工作是高炉优质、高产、低耗的先决条件,是获得优质烧结矿的前提,烧结矿使用的原料种类繁多,物理化学性质各不相同。
为了合理综合利用国家资源,生产出符合高炉冶炼要求而且成分相对稳定的烧结矿,同时还要兼顾生产过程的要求,烧结厂必须根据本厂原料的供应情况及物理化学性质选择合适的原料,通过计算确定配料比,并严格按配比确定每条电子称皮下料量,经常进行重量检查(跑盘)及时调整.目前国内常用的配料方法有两种,即容积配料法和重量配料法。
容积配料法是利用物料的堆比重,通过给料设备对物料容积进行控制,达到配加料所要求的添加比例的一种方法。
此法优点是设备简单,操作方便。
其缺点是物料的堆比重受物料水分、成分、粒度等影响。
所以,尽管闸门开口大小不变,若上述性质改变时,其给料量往往不同,造成配料误差。
重量配料法是按照物料重量进行配料的一种方法,该法是借助于电子皮带称和定量给料自动调节系统实现自动配料的。
优点是:重量配料比容积配料更加精确,特别是对添加数量较少的原料,这一点更明显。
除这两种配料法外,化学成分配料是一种目前最为理想的配料方法,它采用先进的在线检测技术,随时测出原料混合料成分并输入微机进行分析、判断、调整,使烧结矿质量稳固在高水平。
国外对这种方法也处于开发阶段,我国的宝钢、首钢已具备开发这种水平的条件。
原燃料性质及其对烧结过程和质量的影响:1、含铁原料精矿粉是含铁贫矿经过细磨选矿处理,除去了一部分脉石和杂质使含铁量提高的极细的矿粉。
在烧结生产过程中,除了精矿粉外,往往还添加一些其它的含铁原料(如高炉返矿、铁皮和富矿粉等),这样做有两个目的,一是为了增加烧结混合料成球核心,改善混合料的透气性,提高烧结机利用系数,降低烧结矿成本。
二是为了提高烧结矿的品位,为高炉顺产、高产创造条件。
返矿具有多孔的结构,含低熔点化合物,有利于烧结过程液相的生成,提高烧结矿的强度,有利于烧结料粒度的组成,改善透气性,提高烧结矿质量。
因此,返矿的配加量、返矿质量的好坏,直接影响烧结生产过程的进行。
2、熔剂(1)熔剂的分类熔剂可分为碱性熔剂、酸性熔剂和中性熔剂三类。
多国铁矿的脉石多以SiO2为主,所以普遍使用碱性熔剂。
碱性熔剂即含CaO和MgO高的熔剂。
常用的熔剂有:石灰石(CaCO3)生石灰(CaO)、消石灰(CaOH2)和白云石(主要是CaCO3和MgCO3)。
(2)烧结对熔剂的要求碱性氧化物含量要高;S、P杂质要少;酸性氧化物含量SiO2+Al2O3 越低越好,;粒度和水分适宜。
(3)配加熔剂的目的烧结生产过程中配加熔剂的目的主要有三个;一是将高炉冶炼时高炉所配加的一部分或大部分熔剂和高炉中大部分化学反应转移到烧结过程中来进行,从而有利于高炉进一步提高冶炼强度和降低焦比;二是碱性熔剂中的CaO和MgO与烧结料中的氧化物及酸性脉石SiO2、Al2O3 等在高温作用下,生成低熔点的化合物,以改善烧结矿强度、冶金性和还原性;三是加入碱性熔剂,可提高烧结料的成球性和改善料层透气性,提高烧结矿质量和产量。
白灰也称生石灰,主要成分是CaO,其遇水即消化成消石灰(CaOH2)后,在烧结料中起粘结剂的作用,增加了料的成球性,并提高了混合料成球后的强度,改善了烧结料的粒度组成,得高了料层的透气性。
其次,由于消石灰粒度极细,比表面积比消化前增大100倍左右,因此与混合料中其它成分能更好的接触,加快固液相反应,不仅加速烧结过程,而且防止游离CaO存在,而且它还可以均匀分布在烧结料中,有利于烧结过程化学反应的进行。
再次,白灰消化放出的热量,可以提高混合料料温。
从另一个方面来看,生石灰用量也不宜过多;a、生石灰用量过多,烧结料会过分疏松,混合料堆密度下降,生球强度反而会变坏。
由于烧结速度过快,返矿率增加,产量降低。
另外,生石灰量过多,烧结料水分不易控制。
b、烧结前必须使生石灰全部消化,使用生石灰时必须相应增加混合前打水量,保证必要消化时间,使生石灰颗粒一般在一次混合机内松散开,绝大多数消化,生石灰粒度一般要小于3mm。
c、生石灰在配料前的运输和储运中,尽量避免受潮,以防止事先消化去CaO的作用。
d、生石灰不宜长途运输和皮带转运,极易产生粉尘,恶化劳动条件。
(4)、烧结料中加入石灰石对烧结矿质量的影响a、CaO成分增加,其软化区间缩小,燃烧层厚度减薄,改善料层透气性。
b、石灰石的细粉比精矿粘结性好,有利于混合料成球,而较粗的部分本身就具有良好的透气性,可以改善烧结料透气性。
c、烧结过程中石灰石分解,放出CO2,起疏松料层作用,大大改善料层透气性。
通过石灰石的加入,使垂直燃烧速度增加,产量提高。
d、石灰石的加入量也不宜过多,如石灰石量过多成球条件变坏,由于透气性变好,机速加快,矿物结晶不完全。
另外,CaO过多易形成正硅酸钙体系液相,导致冷却时风化碎裂,使烧结矿强度降低。
(5)、用消石灰来代替石灰石的好处a、消石灰粒度很细,亲水性强,而且有粘性,大大改善烧结料透气性,提高小球强度。
b、消石灰比表面积大,增加混合料最大湿容量,可使烧结料过湿层有较好的透气性。
c、粒度细微的消石灰颗粒比粒度较粗的石灰石颗粒更易产生低熔点化合物,液相流动好,凝结成块,从而降低燃料用量和燃烧带阻力。
但消石灰用量也不宜过多,过多的消石灰使烧结料过于松散,烧结矿脆性大,强度下降,成品率下降。
3、烧结矿碱度(1)碱度的分类碱度是烧结矿的碱性氧化物与酸性氧化物百分比含量比值。
二元碱度R=Cao/SiO2;三元碱度R=CaO+MgO/SiO2;四元碱度R=CaO+MgO/SiO2+Al2O3烧结矿按R分为三种;普通烧结矿、自熔性烧结矿,高碱性烧结矿。
普通烧结矿又叫酸性烧结矿。
即烧结矿的碱度低于高炉炉渣的碱度,一般都有小于1.0,这种烧结矿在入炉冶炼时需加入一定数量的熔剂。
自熔性烧结的碱度等于或稍高于高炉炉渣的碱度,一般为1.2-1.5左右,其烧结矿在入炉冶炼时不需另加熔剂。
高碱度烧结矿又叫熔剂性烧结矿,其碱度高于高炉炉渣的碱度,一般都大于1.5。
其烧结矿在入炉冶炼时,可以代替部分或全部熔剂,可常与富矿或酸性烧结矿、酸性球团矿配合使用。
(2)高碱度烧结矿的特点因现在普遍生产的是高碱度烧结矿,就其特点做一概述;a、高碱度烧结矿强度高,稳定性好,粒度均匀,粉末少。
b、高碱度烧结矿具有良好的还原性,这是因为高碱度烧结矿是以易还原的铁酸钙为主要液相;随碱度提高,烧结矿中FeO降低,还原性得到改善;高碱度烧结矿处于还原性最好的结构状态。
其中的磁铁矿晶粒细小且密集,并被铁酸钙包裹或溶蚀。
c、高碱度的烧结矿软化开始温度和软化终了温度均有所下降。
d、高碱度烧结矿含硫量有所提高,这是因为烧结料中的CaO有吸硫作用,形成CaS留于烧结矿中。
(3)烧结中配加白云石的目的烧结料中加入白云石主要是为了提高烧结矿MgO含量从而提高烧结矿的质量(强度),并改善高炉炉渣的流动性。
以上文字和烧结生产实践证明,配料发生偏差是影响烧结过程正常进行和烧结矿产质量的重要因素。
固体燃料配入量波动±0.2%,会使烧结矿的强度和还原性受到影响,烧结矿的含铁量和碱度波动就会影响高炉炉温和造渣制度,严重时,会引发高炉悬料、蹦料现象。
因此各国都非常重视烧结矿化学成分的稳定性。
参考文献:(1)《烧结配料知识》;(2)牛秦洲,叶恒舟,吴一峰. 烧结厂烧结配料专家系统设计[J]桂林工学院学报, 2002,(04)(3)李小斌,梁英,杨重愚. 碱石灰烧结法生料浆配料算法[J]轻金属, 1992,(02)(4)袁晓丽. 烧结优化配矿综合技术系统的研究[D]中南大学, 2007(5)王喜玲. 基于预估校正法的大规模优化算法在烧结配料优化中的应用研究[D]中南大学, 2009(6)宋万军,王俊峰,颜军. 烧结现场适用配料计算[J]. 河南冶金, 1999, (06) .(7)张艳允. 邯钢烧结配料优化的探讨[J]. 烧结球团, 2002, (02) .(8)梁中渝,胡林,邓能运,袁勇. 优化烧结配料[J]. 重庆工业高等专科学校学报, 2002,(01) .(9)刘代飞,范晓慧,孙文东,蒋文笛. 烧结通用配料计算软件系统的开发[J]. 烧结球团, 2003, (01) .(10)潘金华. 集散控制系统在烧结配料中的应用[J]. 烧结球团, 2002, (06) .(11)高丙寅. 用Excel作烧结配料计算[J]. 烧结球团, 2001, (01) .(12)杨东进,陈继国,于忠念,向天德. 烧结配料优化分析[J]. 烧结球团, 2000, (01) .(13)那树人. 多种矿石的烧结配料计算[J]. 烧结球团, 1985, (02) .(14)周永铁. 烧结配料工序中的精矿总量控制[J]. 企业技术开发, 2005, (08) . (15)黄明芳. 浅谈烧结配料[J]. 南京广播电视大学学报, 2001, (02) .。