离子镀技术及应用讲解
离子镀

2.偏压对TiN薄膜的影响
与无偏压时的形貌相比,加偏压后,薄膜表面的大颗 粒尺寸减小且变得较为均匀
偏压对TiN薄膜的影响
与直流偏压的情况相比,在脉冲偏压下镀制的TiN薄膜表 面大颗粒无论是尺寸还是数量都明显减小,表面质量得到 大大改善。
3.改变氮气流量的条件下镀覆TiN 薄膜
可见氮气流量对TiN 薄膜的硬度有较大的 影响,随着氮气流量 的增加,薄膜的硬度 增加,当氮气流量为 0.18slm 时薄膜具有 最高的硬度;再继续 增加氮气流量时薄膜 的硬度反而减小。
膜/基材结合力等级随 温度变化情况 ,160℃ 与180℃时结合力最佳; 温度太低,膜层的厚度 减小且致密性差 ; 沉积温度过高将导致冷 却后膜层与基材之间产 生较大的应力,从而降 低了薄膜的结合力 。
温度对TiN薄膜的影响
沉积温度与TiN涂层表面 硬度的关系 涂层的硬度与薄膜生 长的组织形态有密切关系。 原子排列更加规则、孔隙 减小和晶界强化等原因都 可以提高涂层的表面硬度; 沉积温度过低,轰击 能量较低,TiN涂层形核 不充分,温度过高则晶粒 粗大。 对于多数PVD方法而 言,获得致密柱状晶的 TiN涂层基体温度大致在 400~550℃范围。
4.TiN薄膜厚度对耐磨性影响
由图可见,随着膜厚的的增加,硬度增加,比磨损率降低。
TiN薄膜厚度对耐磨性影响
TiN薄膜厚度为1.0μm 在磨损试验机上磨损 15 min后的形貌,可 见薄膜表面被全部破 坏; 当薄膜厚度超过2.0时, TiN薄膜耐磨性明显 提高 。
5.温度对TiN薄膜的影响
入射粒子能量高,与基体的结合强度高,膜层致密,耐久性好, 膜层硬度高(氮化钛膜显微硬度达HV2000以上),耐磨性好 (用于刀具表面强化,寿命可提高3~10倍),耐蚀性好; 与其他表面处理工艺结合使用效果更佳,如在A3钢基体上先镀 制过渡层后再镀制氮钛膜,耐磨性和耐蚀性均大幅度提高; 可镀基材广泛,可同时在不同金属材料的表面成膜,膜层的颜 色均匀一致; 成膜温度低(几乎可在常温下成薄膜),而膜层的热稳定性好 (600℃时膜层不脱落,不起皮); 用多弧离子镀膜工艺镀制的氮钛膜对光的吸收率达90%以上, 隐蔽性好,镀膜过程无环境污染,因此应用十分广泛。
阴极电弧离子镀原理
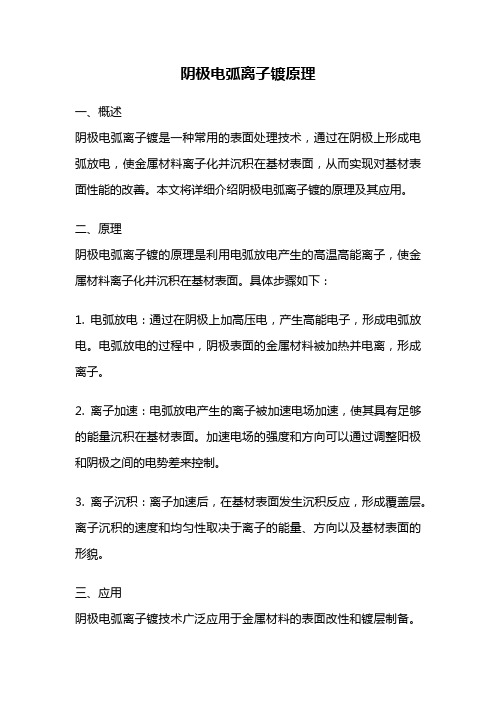
阴极电弧离子镀原理一、概述阴极电弧离子镀是一种常用的表面处理技术,通过在阴极上形成电弧放电,使金属材料离子化并沉积在基材表面,从而实现对基材表面性能的改善。
本文将详细介绍阴极电弧离子镀的原理及其应用。
二、原理阴极电弧离子镀的原理是利用电弧放电产生的高温高能离子,使金属材料离子化并沉积在基材表面。
具体步骤如下:1. 电弧放电:通过在阴极上加高压电,产生高能电子,形成电弧放电。
电弧放电的过程中,阴极表面的金属材料被加热并电离,形成离子。
2. 离子加速:电弧放电产生的离子被加速电场加速,使其具有足够的能量沉积在基材表面。
加速电场的强度和方向可以通过调整阳极和阴极之间的电势差来控制。
3. 离子沉积:离子加速后,在基材表面发生沉积反应,形成覆盖层。
离子沉积的速度和均匀性取决于离子的能量、方向以及基材表面的形貌。
三、应用阴极电弧离子镀技术广泛应用于金属材料的表面改性和镀层制备。
具体应用包括:1. 表面硬化:通过在金属基材表面沉积硬质合金或陶瓷材料,提高基材的硬度和耐磨性,延长使用寿命。
2. 防腐蚀:通过在金属基材表面镀上抗腐蚀性材料,提高基材的耐腐蚀性能,增加使用寿命。
3. 表面修复:对磨损或腐蚀的金属表面进行修复,使其恢复原有的功能和外观。
4. 金属涂层:在金属基材表面沉积金属涂层,如镍、铬、锌等,以改善金属表面的光泽度和装饰性能。
5. 功能涂层:在金属基材表面沉积具有特殊功能的涂层,如导电涂层、隔热涂层、抗反射涂层等,以满足不同的应用需求。
四、优势阴极电弧离子镀具有以下优势:1. 高效节能:离子镀过程中,离子的能量高、速度快,能够实现较高的沉积速率,提高生产效率。
2. 沉积均匀:通过调整加速电场的强度和方向,可以实现对离子沉积的控制,使得镀层均匀、致密。
3. 可控性强:通过控制电弧放电参数、加速电场参数和基材表面的预处理,可以实现对镀层性能的调控。
4. 适应性广:阴极电弧离子镀可用于多种金属材料和非金属材料的镀层制备,对于复杂形状的基材也具有良好的适应性。
离子镀的原理与作用过程
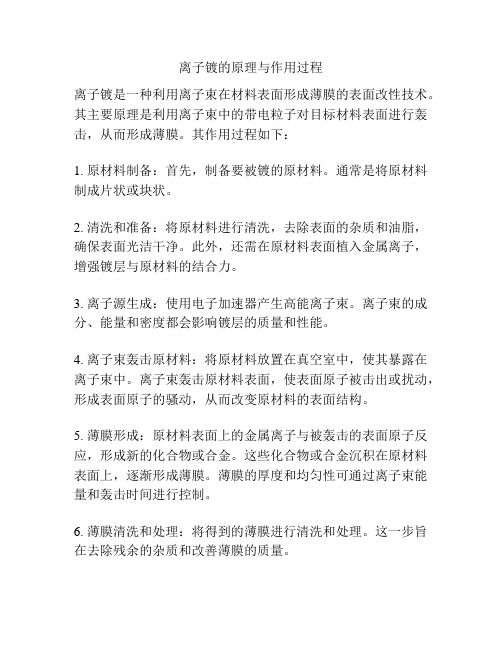
离子镀的原理与作用过程
离子镀是一种利用离子束在材料表面形成薄膜的表面改性技术。
其主要原理是利用离子束中的带电粒子对目标材料表面进行轰击,从而形成薄膜。
其作用过程如下:
1. 原材料制备:首先,制备要被镀的原材料。
通常是将原材料制成片状或块状。
2. 清洗和准备:将原材料进行清洗,去除表面的杂质和油脂,确保表面光洁干净。
此外,还需在原材料表面植入金属离子,增强镀层与原材料的结合力。
3. 离子源生成:使用电子加速器产生高能离子束。
离子束的成分、能量和密度都会影响镀层的质量和性能。
4. 离子束轰击原材料:将原材料放置在真空室中,使其暴露在离子束中。
离子束轰击原材料表面,使表面原子被击出或扰动,形成表面原子的骚动,从而改变原材料的表面结构。
5. 薄膜形成:原材料表面上的金属离子与被轰击的表面原子反应,形成新的化合物或合金。
这些化合物或合金沉积在原材料表面上,逐渐形成薄膜。
薄膜的厚度和均匀性可通过离子束能量和轰击时间进行控制。
6. 薄膜清洗和处理:将得到的薄膜进行清洗和处理。
这一步旨在去除残余的杂质和改善薄膜的质量。
离子镀技术可以用于制备具有不同性质和功能的薄膜,如防腐蚀涂层、耐磨涂层、陶瓷涂层等。
离子镀薄膜具有良好的附着力、致密度高、硬度高、抗腐蚀性好等特点,可以改善材料表面的性能。
磁控溅射离子镀

磁控溅射离子镀磁控溅射离子镀随着科技的不断发展,材料表面处理技术也越来越受到人们的关注。
其中,磁控溅射离子镀技术是一种非常先进的表面处理方法。
本文将从原理、工艺、应用等方面详细介绍磁控溅射离子镀技术。
一、磁控溅射离子镀技术的原理磁控溅射离子镀技术是一种利用磁场控制离子运动的表面处理技术。
其主要原理是:在真空环境下,将制品作为阴极,利用高速电子轰击产生的离子在磁场作用下被聚集和加速,从而沉积在制品表面形成薄膜。
这种薄膜具有高硬度、高耐磨、耐腐蚀性好、不易脱落等优点。
二、磁控溅射离子镀技术的工艺流程1. 处理前的准备工作要先将制品表面进行清洗,去除表面的油污、灰尘等。
2. 真空排气将加工件、目标和溅射室等装置放置在真空室内,打开真空系统进行排气,直至达到所需真空度。
3. 溅射物的加热将制品和目标加热至一定温度,使其表面温度达到一定的范围,有助于提高溅射效率和薄膜质量。
4. 溅射室充气将惰性气体注入溅射室中作为离子的载体,从而形成离子束。
5. 磁场建立通过磁铁制成的磁场使得离子束向阴极开展自动运动,溅射出的物质在阴极表面沉积形成一层薄膜。
6. 增加反应气体通过向溅射过程通入反应气体,使沉积物质形成化学反应并调控膜层成分。
7. 薄膜形成及整体清洗经过多次溅射后,薄膜形成,清洗处理后即可使用。
三、磁控溅射离子镀技术的应用磁控溅射离子镀技术在工业界有着广泛应用,主要应用于以下领域:1. 电子工业用于制造电子元器件、半导体器件和显示器件中的各种金属及合金薄膜。
2. 光学工业制造反射膜、半反射膜、介质膜和滤光片等。
3. 机械工业制造模具、刀具、轴承、涡轮叶片等。
4. 生物医学制造医疗器械、人工关节、高品质耗材。
总之,磁控溅射离子镀技术具有高效、高质、低污染的特点,在工业生产中的应用越来越广泛。
pvd离子镀

pvd离子镀PVD离子镀引言:PVD离子镀(Physical Vapor Deposition)是一种常用的表面处理技术,通过在材料表面沉积薄膜来改善其性能。
本文将介绍PVD 离子镀的原理、应用领域以及一些相关的发展趋势。
一、PVD离子镀的原理PVD离子镀是利用物理方法将金属、合金或陶瓷等材料的原子或分子沉积在基材表面,形成一层薄膜。
其主要原理包括蒸发、溅射和离子镀三个过程。
1. 蒸发:通过加热源将材料加热至蒸发温度,使其原子或分子脱离表面并进入气相状态。
2. 溅射:通过离子轰击的方式,使材料离子从材料表面剥离,并在真空中扩散,最终沉积在基材表面。
3. 离子镀:通过施加电场,将离子加速并定向沉积在基材表面,形成一层致密、均匀的薄膜。
二、PVD离子镀的应用领域PVD离子镀技术广泛应用于各个领域,主要包括以下几个方面:1. 电子行业:PVD离子镀可以制备金属、氧化物或硅等材料的导电薄膜,用于电子元器件、集成电路和显示屏等的制造。
2. 光学领域:通过PVD离子镀,可以制备具有特定光学性质的薄膜,如反射镜、透镜、滤光片等,广泛应用于光学仪器和光电子设备中。
3. 机械工业:利用PVD离子镀技术可以在刀具、模具等工具表面形成耐磨、耐蚀的涂层,提高其使用寿命和耐用性。
4. 汽车工业:PVD离子镀被广泛应用于汽车外观件的镀膜,如车身镀铬、车灯镀膜等,提高汽车的装饰性和耐候性。
5. 医疗领域:PVD离子镀可以制备生物相容性材料的表面涂层,用于人工关节、牙科种植等医疗器械,提高其生物相容性和耐腐蚀性。
三、PVD离子镀的发展趋势随着科学技术的不断进步,PVD离子镀技术也在不断发展和创新。
以下是一些PVD离子镀技术的发展趋势:1. 高效率:研究人员不断改进蒸发源和离子源的设计,提高蒸发和离子镀的效率,减少能源消耗和材料浪费。
2. 多功能性:将不同材料的离子镀技术结合起来,可以实现多层复合薄膜的制备,拓展PVD离子镀的应用领域。
离子镀铝技术介绍
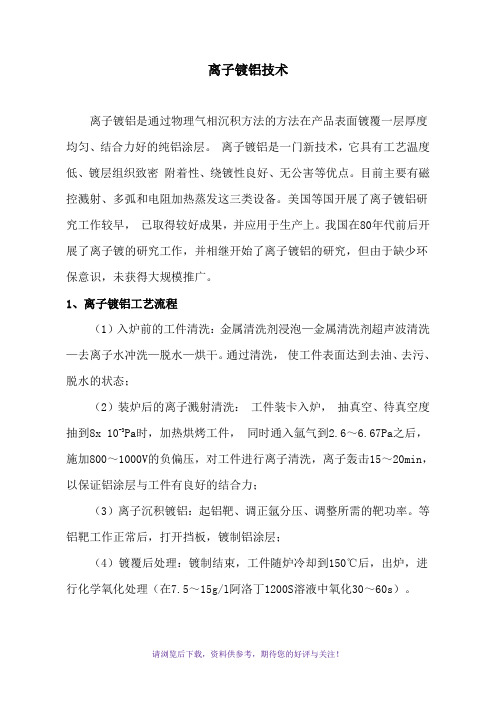
离子镀铝技术离子镀铝是通过物理气相沉积方法的方法在产品表面镀覆一层厚度均匀、结合力好的纯铝涂层。
离子镀铝是一门新技术,它具有工艺温度低、镀层组织致密附着性、绕镀性良好、无公害等优点。
目前主要有磁控溅射、多弧和电阻加热蒸发这三类设备。
美国等国开展了离子镀铝研究工作较早,已取得较好成果,并应用于生产上。
我国在80年代前后开展了离子镀的研究工作,并相继开始了离子镀铝的研究,但由于缺少环保意识,未获得大规模推广。
1、离子镀铝工艺流程(1)入炉前的工件清洗:金属清洗剂浸泡—金属清洗剂超声波清洗—去离子水冲洗—脱水—烘干。
通过清洗,使工件表面达到去油、去污、脱水的状态;(2)装炉后的离子溅射清洗:工件装卡入炉,抽真空、待真空度抽到8x 10-3Pa时,加热烘烤工件,同时通入氩气到2.6~6.67Pa之后,施加800~1000V的负偏压,对工件进行离子清洗,离子轰击15~20min,以保证铝涂层与工件有良好的结合力;(3)离子沉积镀铝:起铝靶、调正氩分压、调整所需的靶功率。
等铝靶工作正常后,打开挡板,镀制铝涂层;(4)镀覆后处理:镀制结束,工件随炉冷却到150℃后,出炉,进行化学氧化处理(在7.5~15g/l阿洛丁1200S溶液中氧化30~60s)。
2、离子镀铝涂层的特点离子镀铝是为了取代电镀镉涂层而发展起来的。
由于电镀镉的一些问题,现在欧美国家已禁止使用电镀镉涂层,这些问题主要有:普通的电镀镉工艺不但造成环境污染,而且要引起高强钢和钛合金氢脆;电镀镉涂层的耐蚀性能低于离子镀铝层;电镀镉涂层的使用温度低于232℃,而离子镀铝层可用于500℃。
离子镀铝有下列优点:(1)离子镀铝层的组织结构可以通过工艺参数控制,从而得到晶粒细小、厚度均匀、结台力优异的涂层;(2)采用离子镀铝工艺不会造成环境污染,也不损害基体的机械性能,甚至能明显提高某些基体材料的疲劳性能;(3)离子镀铝涂层比电镀镉和锌涂层具有更好的保护性能和更高的使用温度;(4)铝涂层除了保护作用之外,还具有其它许多优异的性能,例如优异的导电性和漂亮的外观等。
离子镀氮化钛薄膜刀具的镀膜工艺与镀膜刀具的实际应用
离子镀氮化钛薄膜刀具的镀膜工艺与镀膜刀具的实际应用离子镀氮化钛薄膜刀具是一种新型的刀具镀膜技术,它采用离子镀技术在刀具表面形成一层坚硬、耐磨、耐蚀的氮化钛薄膜,从而提高了刀具的切削性能和寿命。
本文将介绍离子镀氮化钛薄膜刀具的镀膜工艺和实际应用。
一、镀膜工艺离子镀氮化钛薄膜的镀膜工艺是一种利用离子束轰击刀具表面形成薄膜的技术。
具体可以分为以下几个步骤:1、预处理:将刀具加热至300℃左右,以去除刀具表面的油垢和氧化物。
2、清洗:用丙酮、乙醇等有机溶剂将刀具表面彻底清洗干净。
3、离子清洗:用氢气、氮气等离子束对刀具表面进行清洗,去除表面杂质和氧化物。
4、离子镀膜:用含氮物质的离子束轰击刀具表面,使其形成一层氮化钛薄膜。
5、后处理:对镀膜刀具进行退火等处理,使其薄膜结构更加致密,提高切削性能和寿命。
二、实际应用离子镀氮化钛薄膜刀具具有优良的性能和广阔的应用前景,在机械加工、航空航天、汽车制造、模具制造、医疗器械等领域都有着重要的应用。
离子镀氮化钛薄膜刀具可以提高刀具的硬度和抗磨性能,使其具有更好的耐磨性和耐蚀性,延长使用寿命,降低工业生产成本。
在数控加工中,离子镀氮化钛薄膜刀具可以提高切削速度、加工精度和表面质量,提高加工效率和生产效益。
总之,离子镀氮化钛薄膜刀具的镀膜工艺和实际应用,不仅推动了制造业的技术进步和产业升级,而且对于推进可持续发展具有重要意义。
离子镀氮化钛薄膜刀具的应用不仅能提高生产效率和降低成本,还能大幅度提高加工质量、精度和稳定性。
该技术广泛应用于高速切削、重切削和大批量生产等领域,极大地促进了工业生产的发展和不断提高。
离子镀氮化钛薄膜刀具不仅可以用于金属材料的加工,也逐渐应用于陶瓷、塑料等材料的加工。
离子镀技术可以改善镀膜的组织结构,提高膜层的密实性和均匀性,从而使刀具在复杂的切削环境中具有更加出色的性能表现。
随着离子镀技术的不断发展和改进,新型离子镀氮化钛薄膜刀具的研制和应用也将不断拓展。
真空离子镀技术
真空离子镀技术1、技术简介该技术原理如下:在真空室内采用真空弧光放电技术,在阴极材料表面产生弧光,使阴极材料蒸发,形成原子和离子。
在电场作用下,原子和离子束高速轰击作为阳极的工件表面。
与此同时向真空室内通入反应气体,即可在工件表面形成具有优良性能的镀层。
阴极材料(也称靶材)一般采用钛、铬、锆等金属,常用反应气体为氮气和碳氢化合物气体。
获得的镀层有TiN、CrN、TiC、ZrN等。
真空离子镀技术具有下列优点:(1)可获得高硬度的镀层,镀层摩擦系数小,耐磨性高。
(2)镀层化学稳定性好,抗高温氧化,耐蚀性好。
(3)镀层美观。
可获得如18K金的金黄色色泽及其它彩色膜。
(4)镀层与基材结合力高。
其结合力要高于传统的磁控溅射、真空蒸镀等涂层,镀层不易剥落。
(5)生产过程对环境无污染。
镀层形成速度快,节电、节水。
2、技术指标镀层厚度:3~5μm。
镀层硬度:1300~1800HV3、应用说明(1)刃具、模具等工具的表面强化。
在高速钢、硬质合金制造的刃具(如钻头、铣刀、车刀)及模具表面获得超高硬度的TiN、TiC、ZrN等镀层,提高刃具、模具的耐磨性和外观质量。
(2)机械零件的表面强化。
如凸轮、叶片、气门、轧辊表面获得耐磨镀层,延长零件使用寿命。
(3)彩色膜钢板生产应用。
可在尺寸为1m×2m、厚度为0.2mm~0.6mm 的不锈钢板和低碳钢板上获得金黄色TiN或其它彩色膜, 耐磨耐蚀性好,彩色膜钢板用于高档饭店、宾馆、办公大楼等装饰用。
(4)日用品的装饰镀。
如手表壳、表带、眼镜架、餐具、高档卫生洁具、吊灯、门把等的装饰。
电弧离子镀
电弧离子镀
电弧离子镀是一种高效的表面处理技术,它可以在金属表面形成一层坚硬、耐磨、耐腐蚀的涂层,提高金属的使用寿命和性能。
本文将从电弧离子镀的原理、应用和优缺点三个方面进行介绍。
电弧离子镀的原理是利用高温电弧将金属材料蒸发成离子,然后通过电场加速离子,使其沉积在工件表面形成涂层。
电弧离子镀的工艺流程包括清洗、预处理、电弧离子镀和后处理等步骤。
其中,清洗和预处理是非常重要的步骤,它们可以去除工件表面的污垢和氧化物,提高涂层的附着力和质量。
电弧离子镀的应用非常广泛,它可以用于金属表面的硬化、防腐、耐磨、导电和美化等方面。
例如,电弧离子镀可以在汽车发动机的气门、曲轴等部件表面形成硬质涂层,提高其耐磨性和耐腐蚀性;电弧离子镀还可以在手机、电脑等电子产品的金属外壳表面形成金属质感的涂层,提高产品的美观度和质感。
电弧离子镀的优点是涂层质量高、附着力强、硬度高、耐磨性好、耐腐蚀性强、导电性好等。
但是,电弧离子镀也存在一些缺点,例如设备成本高、工艺复杂、涂层厚度不易控制、涂层成分不易调节等。
此外,电弧离子镀还存在一些环境和安全问题,例如电弧放电会产生大量的氮氧化物和臭氧等有害气体,需要进行排放和处理。
电弧离子镀是一种高效的表面处理技术,它可以在金属表面形成坚
硬、耐磨、耐腐蚀的涂层,提高金属的使用寿命和性能。
电弧离子镀的应用非常广泛,但是也存在一些缺点和环境安全问题,需要在实际应用中加以注意和解决。
真空离子镀和微弧氧化
真空离子镀与微弧氧化真空离子镀和微弧氧化是两种先进的表面处理技术,它们在材料科学、电子工程、机械工程等领域具有广泛的应用前景。
下面将详细介绍这两种技术的原理、应用、优缺点等方面。
一、真空离子镀1.原理真空离子镀是一种在真空环境中,利用离子束对材料表面进行沉积和改性的技术。
其基本原理是利用高能离子束撞击材料表面,将离子能量传递给材料表面原子,使其激活并离开表面进入真空中,然后在真空中沉积形成一层薄膜。
在真空离子镀过程中,首先需要将待处理的材料放入真空室中,然后通过加热或电子束蒸发等方法将材料表面的原子激活。
激活后的原子在真空中形成气态原子或分子,这些原子或分子通过吸附或反应等过程形成一层薄膜。
在沉积过程中,还可以通过添加不同的反应剂和材料,控制薄膜的成分和结构。
2.应用真空离子镀在许多领域都有广泛的应用,如航空航天、电子、汽车等。
在航空航天领域,真空离子镀可以提高飞行器表面的耐腐蚀性和抗氧化性;在电子领域,真空离子镀可以用于制造薄膜电子器件,提高器件的性能和稳定性;在汽车领域,真空离子镀可以用于制造高性能的汽车零部件,提高零部件的耐磨性和耐腐蚀性。
此外,真空离子镀还可以用于制造高性能的涂层和复合材料。
例如,通过控制薄膜的成分和结构,可以制造出具有高硬度、高耐磨性、高耐腐蚀性的涂层;通过将不同的材料进行复合处理,可以制造出具有优异性能的复合材料。
3.优缺点优点:(1) 能够在真空中进行操作,避免了大气环境对材料表面的污染;(2) 可以实现精确的薄膜厚度控制,提高薄膜的质量和稳定性;(3) 可以实现多种元素的沉积和掺杂,提高薄膜的性能和多样性;(4) 可以在较低的温度下进行操作,降低了能耗和成本。
缺点:(1) 需要高真空环境,增加了设备和操作的成本;(2) 操作过程中需要严格控制温度、压力等参数,否则会影响薄膜的质量和稳定性;(3) 对于某些特殊材料和复杂结构,难以实现均匀的薄膜沉积。
二、微弧氧化1.原理微弧氧化是一种在常压或高压环境下,利用电化学方法对材料表面进行氧化处理的技术。
- 1、下载文档前请自行甄别文档内容的完整性,平台不提供额外的编辑、内容补充、找答案等附加服务。
- 2、"仅部分预览"的文档,不可在线预览部分如存在完整性等问题,可反馈申请退款(可完整预览的文档不适用该条件!)。
- 3、如文档侵犯您的权益,请联系客服反馈,我们会尽快为您处理(人工客服工作时间:9:00-18:30)。
离子镀设备
离子镀原理图
多弧离子镀
离子镀特点
附着性能好:高速离子能量为3000-5000电子伏特,当其高 速轰击工件时,不但沉积速度快,而且能够穿透工件表面,形 成一种注入基体很深的扩散层,离子镀的界面扩散深度可达四 至五微米,也就是说比普通真空镀膜的扩散深度要深几十倍, 甚至上百倍,因而彼此粘附得特别牢。
清洗过程简易:离子镀工艺自身就有一种离子轰击清洗作用, 并且这一作用还一直延续于整个镀膜过程。清洗效果极好,能 使镀层直接贴近基体,有效地增强了附着力,简化了大量的镀 前清洗工作。
可镀材料广泛:离子镀由于是利用高能离子轰击工件表面,使 大量的电能在工件表面转换成热能,从而促进了表层组织的扩 散作用和化学反应。然而,整个工件,特别是工件心部并未受 到高温的影响。因此这种镀膜工艺的应用范围较广,受到的局 限性则较小。通常,各种金属、合金以及某些合成材料、绝缘 材料、热敏材料和高熔点材料等均可镀复。即可在金属工件上 镀非金属或金属,也可在非金属上镀金属或非金属,甚至可镀 塑料、橡胶、石英、陶瓷等。
蒸发源接阳极,工件接阴极,当通以三至五千伏高压直流电以 后,蒸发源与工件之间产生弧光放电。由于真空罩内充有惰性 氩气,在放电电场作用下部分氩气被电离,从而在阴极工件周 围形成一等离子暗区。
带正电荷的氩离子受阴极负高压的吸引,猛烈地轰击工件表面, 致使工件表层粒子和脏物被轰溅抛出,从而使工件待镀表面得 到了充分的离子轰击清洗。
绕镀能力强:离子镀时,蒸发料粒子是以带电离子的形式在电 场中沿着电力线方向运动,因而凡是有电场存在的部位,均能 获得良好镀层,这比普通真空镀膜只能在直射方向上获得镀层 优越得多。因此,这种方法非常适合于镀复零件上的内孔、凹 槽和窄缝。等其他方法难镀的部位。
镀层质量好:离子镀的镀层组织致密、无针孔、无气泡、厚度 均匀。甚至棱面和凹槽都可均匀镀复,不致形成金属瘤。像螺 纹一类的零件也能镀复,由于这种工艺方法还能修补工件表面 的微小裂纹和麻点等缺陷,故可有效地改善被镀零件的表面质 量和物理机械性能。
离子镀应用
离子镀技术及应用
什么是离子镀
离子镀在真空条件下,利用气体放电使气体或被蒸发物质部分 电离,并在气体离子或被蒸发物质离子的轰击下,将蒸发物质 或其反应物沉积在基片上的方法。
其中包括磁控溅射离子镀、反应离子镀、空心阴极放电离子镀 (空心阴极蒸源自法)、多弧离子镀(阴极电弧离子镀)等。
离子镀的历史
离子镀的工作过程