刀库、机械手部分故障分析实例与诊断
立加刀库故障分析及解决方案
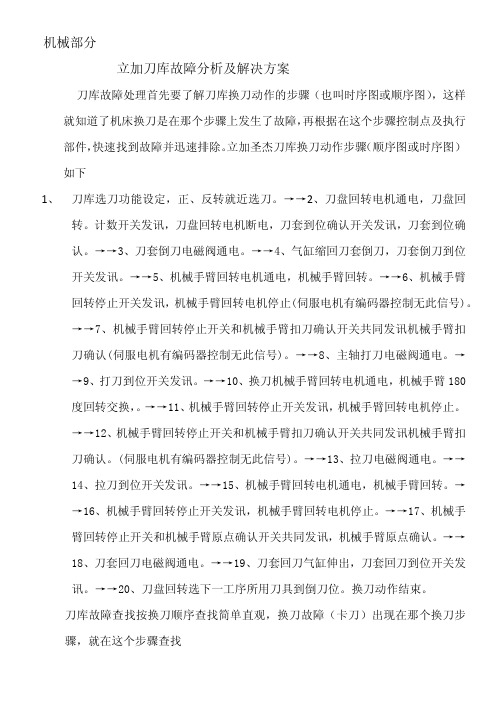
机械部分立加刀库故障分析及解决方案刀库故障处理首先要了解刀库换刀动作的步骤(也叫时序图或顺序图),这样就知道了机床换刀是在那个步骤上发生了故障,再根据在这个步骤控制点及执行部件,快速找到故障并迅速排除。
立加圣杰刀库换刀动作步骤(顺序图或时序图)如下1、刀库选刀功能设定,正、反转就近选刀。
→→2、刀盘回转电机通电,刀盘回转。
计数开关发讯,刀盘回转电机断电,刀套到位确认开关发讯,刀套到位确认。
→→3、刀套倒刀电磁阀通电。
→→4、气缸缩回刀套倒刀,刀套倒刀到位开关发讯。
→→5、机械手臂回转电机通电,机械手臂回转。
→→6、机械手臂回转停止开关发讯,机械手臂回转电机停止(伺服电机有编码器控制无此信号)。
→→7、机械手臂回转停止开关和机械手臂扣刀确认开关共同发讯机械手臂扣刀确认(伺服电机有编码器控制无此信号)。
→→8、主轴打刀电磁阀通电。
→→9、打刀到位开关发讯。
→→10、换刀机械手臂回转电机通电,机械手臂180度回转交换,。
→→11、机械手臂回转停止开关发讯,机械手臂回转电机停止。
→→12、机械手臂回转停止开关和机械手臂扣刀确认开关共同发讯机械手臂扣刀确认。
(伺服电机有编码器控制无此信号)。
→→13、拉刀电磁阀通电。
→→14、拉刀到位开关发讯。
→→15、机械手臂回转电机通电,机械手臂回转。
→→16、机械手臂回转停止开关发讯,机械手臂回转电机停止。
→→17、机械手臂回转停止开关和机械手臂原点确认开关共同发讯,机械手臂原点确认。
→→18、刀套回刀电磁阀通电。
→→19、刀套回刀气缸伸出,刀套回刀到位开关发讯。
→→20、刀盘回转选下一工序所用刀具到倒刀位。
换刀动作结束。
刀库故障查找按换刀顺序查找简单直观,换刀故障(卡刀)出现在那个换刀步骤,就在这个步骤查找一、 刀盘回转选刀过程可能产生故障有如下几种1、刀盘回转电机不转产生原因:(1)刀盘回转电机供应电流不当。
解决方法:检查电路及电源是否符合技术要求。
(2)刀盘回转电机刹车过紧。
刀库和换刀装置的故障诊断方法和维修分析

刀库和换刀装置的故障诊断方法和维修分析摘要:本文首先数控机床刀库与换刀装置为研究对象,首先简要分析了自动换刀装置的基本形式,指出了刀库及换刀机械手在日常运作时的常见故障,并给出了具体的维修方法,望能为此领域研究有所借鉴与帮助。
关键词:刀库;换刀装置;故障诊断;维修刀库与换刀装置是为大、中型加工中心提供配套支持,且实现自动换刀与刀具储备的两部分,乃是重型加工中心、高档加工中心的重要构成。
针对刀库来讲,其主要作用就是提供储刀位置,并且能够依程式控制,合理选刀具,并准确定位,以此完成刀具交换;而换刀装置则执行交换刀具的动作。
在实际运行当中,刀库和换刀装置经常会出现各种故障,因而会影响整个生产的正常开展。
本文结合实际情况,就其故障诊断方法及维修策略作一探讨。
1.自动换刀装置的基本形式(1)带刀库所对应的自动换刀系统。
针对此系统而言,其主要由两部分构成,其一为交换机,其二是刀库与刀具。
首先将加工时所需所有刀具均安装于刀柄上,于机外预先调整其尺寸,并按照特定方式,放到刀库当中。
在进行换刀时,首先会从刀库中选刀,并借助刀具交换装置,将刀具从刀库与主轴上取出,而在刀具交换后,把新刀具装到主轴上,然后把旧刀具放回到刀库当中。
需要指出的是,用于存放刀具的刀库容量很大,其除了能够安装于主轴箱的上方,还可根据现实需要,当作单独部件,安装于机床外,借助搬运装置而完成刀具的运送。
(2)更换主轴头换刀。
如果数控机床当中安装有旋转刀具,那么对主轴头进行更换,便是一种比较简单的方式。
针对主轴头来讲,一般情况下,其有两种方式,即立式与卧式,且经常用转塔的转位对主轴头进行更换,以此来达到自动换刀的目的。
而在转塔所对应的各主轴头上,事先便安装有能够满足各工序操作需要的旋转刀具。
当换刀指令发出之后,各主轴头会按照指定顺序,旋转至加工位置,且与主轴运动相连接,主轴将刀具带动,并进行旋转,而对于其他处在非加工位置的主轴,均和主运动之间呈脱开状态。
刀库部分常见故障1[1]
![刀库部分常见故障1[1]](https://img.taocdn.com/s3/m/598fa330eefdc8d376ee32b5.png)
刀库部分常见故障1.故障现象:刀库摆进摆出撞击严重。
原因分析:①单向节流阀调整的不合适或有可能坏掉;②缓冲调整的不合适;③阻尼调整不合适;④可能对中调整的不合适。
解决办法:①重新调整调速节流阀位置使其运动速度合适。
②调整缓冲使刀库到位时的缓冲合适。
③调整阻尼,使刀库到位时的速度合适。
④重新调节对中。
2.故障现象:刀库摆进摆出有时不能摆到位,到位灯不亮。
原因分析:①可能原位信号X1000.6和到位信号X1000.7在原位和主轴位状态不正常,磁开关可能由于刀库震动导致位置松动;②可能刀库对中有问题;解决办法:①在机械上进行调整,如果机械确实到位了,请调整或紧固磁开关的位置,使刀库原位和主轴位信号状态正常;②重新调整对中。
3.故障现象:摆动刀库没有动作,有时只能单方向摆动。
原因分析:①检查摆出和摆进的电磁阀线圈电压是否正常(得电时为110V),可能电磁阀不正常,可能漏气;②可能固态继电器板上的保险不正常;③可能机械上有卡住的地方。
解决办法:①更换电磁阀;②如保险损坏请更换;③机械如有卡住的地方重新进行调整。
4.故障现象:刀库摆到主轴位时发现刀柄中心与主轴锥孔不同心。
原因分析:可能机械位置有变化,需要重新调整。
解决办法:把刀库摆到换刀位,松开摆动汽缸活塞杆上的背母,旋转活塞杆,就可以改变刀库对主轴的左右方向的位置;在刀库上部靠前位置,有两个调整螺钉,松开背母,旋转两个调整螺钉,就可以改变刀库对主轴的前后方向的位置。
5.故障现象:刀库在转动过程中有报警1009,刀库计数错误。
原因分析:①可能刀库电机上是有铁屑,导致被卡住;②刀库电机及计数开关线路是否正常;③可能计数开关状态不正常,刀库停止时X1000.5应该为1,在刀库转动过程中,X1000.5变为0,再次停止时又变为1;④可能开关松动,处于临界状态。
解决办法:①把刀库电机重新装配,把铁屑进行清理;②如果开关或线损坏请更换,刀库电机损坏请更换;③重新调整计数开关的位置。
刀库、机械手常见故障及排除方法表4—11
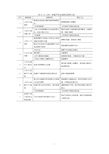
调节锁刀弹簧上的螺钉,使其最大载荷不超过额定值
6
刀具从机械手中脱落
机械手卡紧销损坏或没有弹出来
更换卡紧销或弹簧
6
刀具从机械手中脱落
换刀时主轴箱没有回到换刀点或换刀点发生漂移
重新操作主轴箱运动,使其回到换刀点位置,并重新设定换刀点
机械手抓刀时没有到位,就开始拔刀
调整机械手手臂,使手臂爪抓紧刀柄后再拔刀
表4—11刀库、机械手常见故障及排除方法
序号
故障现象
故障原因
排除方法
1
刀库不能旋转
联接电动机轴与蜗杆轴的联轴器松动
紧固联轴器上的螺钉
刀具重量超重
刀具重量不得超过规定值
2
刀套不能夹紧刀具
刀套上的调整螺钉松动或弹簧太松,造成卡紧力不足
顺时针旋转刀套两端的调节螺母,压紧弹簧,顶紧卡紧销
刀具超重
刀具重量不得超过规定值
3
刀套上不到位
装置调整不当或加工误差过大而造成拨叉位置不正确
调整好装置,提高加工精度
限位开关安装不正确或调整不当造成反馈信号错误
重新调整安装限位开关
4
刀具不能夹紧
气压不足
调整气压在额定范围内
增压漏气
关紧增压
刀具卡紧液压缸漏油
更换密封装置,卡紧液压缸不漏
刀具松卡弹簧上的螺母松动
旋紧螺母
5
刀具夹紧后不能松开
刀具重量超重
刀具重量不得超过规定值ห้องสมุดไป่ตู้
7
机械手换刀速度过快或过慢
气压太高或节流闪阀开口过大
保证气泵的压力和流量,旋转节流阀到换刀速度合适
加工中心、刀架、刀库和换刀机械手的故障诊断及排除

一、加工中心、刀架、刀库和换刀机械手的故障诊断及排除加工中心ATC 斗笠式刀库动作过程故障分析摘要:加工中心可将铣、镗、钻、铰、攻螺纹等多项功能集于一身,大大提高了生产效率。
换刀装置(ATC)是加工中心的重要组成部分,也是加工中心故障率最高的部分,约有50%的机床故障与换刀装置有关。
斗笠式刀库是加工中心比较常见的一种换刀装置,在本文中,我结合自己的工作经验,对斗笠式刀库的动作过程及换刀过程中容易出现的故障进行了简要的分析和说明。
关键词:加工中心ATC 斗笠式刀库动作过程故障分析0 引言加工中心的一个很大优势在于它有ATC装置,使加工变得更具有柔性化。
加工中心常用的刀库有斗笠式、凸轮式、链条式等,其中斗笠式刀库由于其形状像个大斗笠而得名,一般存储刀具数量不能太多,10~24把刀具为宜,具有体积小、安装方便等特点,在立式加工中心中应用较多。
1 斗笠式刀库的动作过程斗笠式刀库在换刀时整个刀库向主轴平行移动,首先,取下主轴上原有刀具,当主轴上的刀具进入刀库的卡槽时,主轴向上移动脱离刀具;其次主轴安装新刀具,这时刀库转动,当目标刀具对正主轴正下方时,主轴下移,使刀具进入主轴锥孔内,刀具夹紧后,刀库退回原来的位置,换刀结束。
刀库具体动作过程如下:1.1 刀库处于正常状态,此时刀库停留在远离主轴中心的位置。
此位置一般安装有信号传感器(为了方便理解,定义为A),传感器A发送信号输送到数控机床的PLC中,对刀库状态进行确认。
1.2 数控系统对指令的目标刀具号和当前主轴的刀具号进行分析。
如果目标刀具号和当前主轴刀具号一致,直接发出换刀完成信号。
如果目标刀具号和当前主轴刀具号不一致,启动换刀程序,进入下一步。
1.3 主轴沿Z方向移动到安全位置。
一般安全位置定义为Z轴的第一参考点位置,同时主轴完成定位动作,并保持定位状态;主轴定位常常通过检测主轴所带的位置编码器一转信号来完成。
1.4 刀库平行向主轴位置移动。
刀库刀具中心和主轴中心线在一条直线上时为换刀位置,位置到达通过信号传感器(B)反馈信号到数控系统PLC进行确认。
加工中心刀库(斗笠、圆盘)常见故障诊断及解决对策

一. 斗笠刀库故障
原因:
1.刀盘电机、进刀电机、退刀电机相序相反
2.进刀到位、退刀到位的信号检测线路有问题
3.主轴松到、紧刀到位信号检测线路有问题或推刀距离有偏差
4.主轴定位角度有偏差
5.主轴第二参考点有偏差
6.刀库乱刀号
7.刀盘计数开关损坏或刀盘旋转不停止
解决对策:
1.调整电机接线相序
2.调节进刀、退刀感应开关位置,如损坏更换
3.调节松、紧刀位置开关和打刀缸推刀距离
4.调节主轴参数3207(三菱)参数4077(发那科)至合适角度
5.调节轴参数2038(三菱)参数1241(发那科)到合适坐标值及调节栅格量 6.做刀库刀号归零操作PLC开关16号(三菱),PMC开关K2.0(发那科) 7. 调节计数开关位置,如损坏则需更换
二. 圆盘刀库故障
原因:
1.刀盘电机、手臂电机相序相反
2.刀盘电机、手臂电机刹车松紧不当
3.刀套上及下位置有偏差或刀套气缸到位感应开关位置不合适 4.手臂扣刀位置有偏差,扣不紧,有异响
5.手臂未归零位,换刀动作不能继续
6.刀套号错乱。
OKUMA OSP700自动换刀刀库故障诊断与维修

例5~例6.刀库门报警的故障维修
例3.换刀错误的故障维修
故障现象:一台配套OKUMA OSP700系统,型号为XHAD765的数控机床,换刀中1号大刀未插回大刀刀位,大刀刀位插着其他刀,实际刀号刀位与机床控制系统中刀号刀位不符,即换刀错误,机床无报警,幸亏操纵工细心,及时发现停机。
分析及处理过程:换刀错误是一种危险的故障,由于无报警,机床将继续工作,直到发生设备事故报警。由于换刀与众多位置开关和PLC控制程序及CNC处理过程有关,应重点检查这几部分。手工将实际刀具刀位调整到与控制系统中的一致,再执行换刀,发现除换1号刀外,其他换刀过程均正常。手动方式下,打开刀库侧门,按刀库上行或下行键,旋转刀库刀链,观察刀位表中当前刀位变化,发现在1号与30号刀位过渡时,刀位显示与实际刀位相差一个刀位,原来是刀库在过零点时出现刀位错误。关机后检查零点开关插头、刀库旋转计数开关插头与FUB-P4M4相关插头,发现进油。将插头清理后再重新插好,过20min再开机,换得手动方式,打开刀库门。手动上行、下行移动刀库,观察刀库在过零点时刀位显示正常,再切换到MDI方式,输进T1M6执行换刀,再输进T30 M6执行换刀。经查实际刀位刀号与刀位刀具表中一致,进行正常加工,未出现错误。
多次维修证实,各位置开关均采用插头联接是该机床电气一大缺陷,轻易接触不良引起故障。由于刀库零点开关与刀库旋转计数开关共用一个插头供电,当插头接触不良而刀库又过零点时,易引起刀库旋转计数开关闪烁,导致错误计数。
圆盘式刀库(机械手)常见问题及解决方法

圆盘式刀库(机械手)常见问题及解决方法
加工中心常用的刀库类型有圆盘式刀库,斗笠式刀库,链式刀库,其中销售量最大的是圆盘式刀库,因为其换刀速度快,稳定性高,对刀具的保护好而深受客户喜爱。
下面我说一下在售后过程中客户反映最多的问题。
在换刀过程中,由于报警导致刀库机械手不在位问题
这种问题大多数是由于气压不够报警造成,当然也有些换刀过程中停电这种小概率事件
这种情况下需要手动将机械手归位
方法如下,40#刀库使用12mm扳手在刀库上方有个带有半圆拉环的电机
将拉环向上拉到顶
然后使用扳手转动电机轴的6角螺丝,具体方向看情况,直到把机械手摇回原位,可以在刀库开窗后看感应灯,然后将电机的拉环放下,完成机械手的复位
最后将垂直的刀套水平即可,方法如下,:找到如图所示的双向电磁阀
在电磁阀下面有俩小按钮,此阀为红色,其他阀颜色可能有不同,不过位置一样功能一样
按下按钮,(俩按钮一个控制水平一个控制垂直,不反应就按另一个),刀套水平,完成刀库归位。
来源:滕州市大恒机床有限公司。
- 1、下载文档前请自行甄别文档内容的完整性,平台不提供额外的编辑、内容补充、找答案等附加服务。
- 2、"仅部分预览"的文档,不可在线预览部分如存在完整性等问题,可反馈申请退款(可完整预览的文档不适用该条件!)。
- 3、如文档侵犯您的权益,请联系客服反馈,我们会尽快为您处理(人工客服工作时间:9:00-18:30)。
1 外部信号故障加工中心的外围信号主要用在如轴、刀库、机械手、交换工作台、辅助设备、模块外部接口及控制电器的辅助触点等部位。
主要功能包括:液位检测、温度检测、压力检测、到位检测、行程检测、状态检测、按钮触点以及各种使能等。
这类外围信号通常都设置了相应的报警代码和提示信息,维护人员通过提示便能快捷地定位故障点。
同时,也可通过:A= 梯形图、信号状态查阅界面以及:B= 装置指示灯来综合诊断。
找到故障点后结合实际情况进行调整、维修或更换。
偶尔也遇到库存备件缺乏的情况,在确定不影响机床正常运行的情况下,可暂时将故障点短接,以缓解生产压力,备件一到及时更换。
对一些动作频率相对较高的部位,应特别注意观察和记录,如:主轴刀具状态、回参考点挡块、交换工作台位置检测、刀库和机械手位置状态等。
外部信号范围广,故障多,以下简要举几例说明之。
(1)一台THM6350卧式加工中心出现“"1008液压压力不足”报警,且该报警有规律地出现,经观察发现实际压力完全满足。
这是典型的辅助设备外部报警。
报警提示,该压力继电器已损坏。
因备件库中暂时无该型压力继电器,万用表测量该点两端阻值满足短接要求。
同时,交待操作工在备件未到期间,必须注意实际液压压力情况,并随时报告。
经处理,缓解了生产压力。
(2)一台VMC1000C立式加工中心,采用FANUC 0i-MA数控系统,Z、A 两轴为一双轴模块驱动。
在拆走旋转台后,出现“401 Z AXIS READY OFF”报警信息。
因任务需要,决定暂时使用X、Y、Z三轴进行其它工件加工。
应将A 轴屏蔽,其屏蔽步骤是:首先修改NC参数?NO 1023的A为“—4”;然后将PMC中的保持继电器K8.2设为“1”;最后将原驱动模块的接口封锁处理。
到现场初步检查后认为已做到,但报警仍然未清除。
分析认为原因出在封锁未生效,拆开所使用连接器发现里面未短接,而且型号有误。
最后使用型号为HRIOS F140-2015的PCR-EV20MDT的连接器,并将其9 和10(即*DRDYn 和*MCONn)短接封锁后,机床报警清除,满足了工作需求。
原因出在工作人员把连接器使用错。
(3)一进口五坐标加工中心,采用AB10数控系统。
自动刀库不能正常换刀,刀盘转到正确刀位后来回旋转,未正常判别刀位。
该刀库记数方式采用8421 代码,使用5个感应器判别,即感应头对应金属刀盘上有孔为“0”,反之为“1”。
调查情况时得知,近期机修人员拆卸过刀库,但拆卸时是整体移出,排除上、下刀盘位置异位,手动方式单步旋转正常。
据控制原理分析认为是数刀不正确,应检查5个感应信号状态正常与否(感应器淡绿色指示灯亮表示电源送到,黄色指示灯亮表示感应状态为1)。
手动方式下旋转刀盘一周,仔细观察发现3号感应器一直保持同一状态。
到此,判断要么是感应头上有脏物或铁屑,要么感应器已损坏。
将手指伸进孔中触摸发现上面有铁屑,清除后,信号状态恢复,执行自动换刀正常。
2 连接器件故障连接器件主要指导线和连接器。
这类故障主要表现在" 个方面:一是导线破损、断裂;二是线间出现短路或干扰;三是接头处或接口连接不良;四是错接或误插。
连接器件作为设备的信息通道,在支持设备的运行中具有举足轻重的作用。
据我们维护中不完全统计,机床故障的近三成是该方面所致。
加工环境及条件是该方面的直接原因,也有一部分归属于使用时间过长而老化、腐蚀的缘故。
如:一台宁江THM6350卧式加工中心,配置FANUC 0i-M数控系统。
在交换工作台时,按下“手动/自动启动”按钮后,托板(内工作台)升起,而托板架未上升,始终保持此状态,无法实现工作台的交换。
该托板架的升降由液压系统控制。
检查液压压力正常,查看控制托板架上升的电磁阀发现未执行。
该电磁阀由继电器KA13的常开触点控制,而继电器KA13的线圈由PMC输出点Y1004.1直接供给24V电源。
通过PMC状态显示功能检查Y1004.1的状态,执行前后始终为“0”,即未给出信号。
分析认为,某一输入条件未得到满足使机床处于等待状态。
决定从Y1004.1入手,利用PLC梯形图动态显示功能来诊断故障。
涉及的主要梯形图如图$ 所示。
在手动方式下,正常交换工作台导通路径如图中箭头方向,即要满足R68.3、R62.0 和Y1003.5导通。
从梯形图可以看出,R68.3导通条件是R68.2和R62.0导通,R62.0又由外部信号来控制。
动态观察发现X1004.5通,X1006.3未变化。
经查X1006.3为托板(工作台)上升到位信号。
用金属尺靠近感应头发现信号无变化,以为是感应器本身损坏。
更换后发现故障依旧。
校线时发现24V导线已断路。
拆开护板后发现因油质腐蚀该导线一接头已断路,重新接好后。
机床恢复正常。
连接器件作为控制元件之间的信息传递通道,和生活中的通道一样,必须经常进行疏通,以防止通道堵塞、断流、分支和交叉等异常情况发生。
因此,我们应高度重视机床连接器件的日常护理工作,保持机床各部位干净整洁,确保线路连接及走向的严谨合理,发现问题,及时处理,对不合理和有后患的地方应及时进行优化性改进,以提高使用的可靠性。
3 执行元件故障这里所说的执行元件包括:电动机、继电器、接触器、电磁阀等。
相对来说,这部分元器件是打开控制柜最能直观见到的。
出现此类故障后,应注重排除的先后顺序。
比如出现电动机过载,可能原因有电动机过热、有杂物堵塞、空开或接触器损坏、电动机损坏及加工条件过高等。
此时脱开电动机线就可以分清是电动机侧还是强电柜侧有问题。
有时,甚至通过目视、触摸、气味、声音等直观法就可以得出结论。
如:一台THK46100卧式加工中心,采用FANUC 0-mate数控系统。
在自动方式加工过程中,出现“1019 RELAY OVERLOAD”报警。
查阅外部报警信息表提示为空开跳闸。
打开电气柜发现QF2空开已跳闸,以为是电压瞬间波动过大所致。
重新合上空开后报警消除。
试加工后,再次跳闸。
经查,发现切削液电动机启动瞬间猛烈跳动,10S左右又跳闸。
检查电动机已损坏,更换后,机床恢复正常。
4 各种参数、数据和程序故障参数、数据和程序是数控设备运行必不可少的条件。
其中,主要包括NC 机床参数、PMC 参数、补偿参数、PLC程序、换刀程序、宏程序和加工程序等。
此类故障主要表现为以下几方面:(1)系统参数丢失,导致系统混乱或某项功能丧失;(2)系统参数部分或个别发生了变化;(3)操作不当,出现数据写入错误;(4)有关程序被丢失、改动及编制不妥;(5)对参数或数据修改过程中设置不当。
一旦参数破坏严重,常常需要重装系统才能够恢复。
一台宁江THM6350卧式加工中心,采用FANUC 0i-M数控系统。
在加工过程中,出现机床运动的实际尺寸与给定值不符,无报警信息。
该机床在此故障前曾发生过在操作" 轴运动时数显变化而实际位置不动,检查发现" 轴皮带轮被拉断所致。
更换皮带轮后对" 轴零点偏置(参数1850)进行了修正。
刚试运行便发现了实际值与给定值不符的现象。
此类故障通常有( 种可能原因:一是位置环问题,这其中包括如光栅尺、编码器及它们的连接电缆故障,也可能是伺服模块级的故障。
二是涉及到数控参数问题,如进给单位(公制6 英制)、检测倍乘比参数的设置是否发生了变化。
三是机械上存在一定的阻力或联接松动所致。
以上述原因分析为依据,我们由易到难逐一进行了检查排除。
经查,该故障是由于进给单位的参数设置由原来的公制变成了英制,即参数1001#0由“0”变成了“1”。
将参数改回“0”后,机床恢复正常。
特别提到的是在加工中心的自动换刀过程中,执行到某一句突然中断,出现无资料提示的报警号且信息提示。
这时,应仔细在系统中找到换刀程序(大型刀库的换刀程序同样分主程序和子程序,可采用查找功能找到故障段),读懂停顿语句的含义,分析逻辑关系,有效利用程序来诊断故障。
同时,确保换刀程序没有发生变化。
5 伺服系统故障为了保证加工中心能达到较高的加工精度,必须具有性能优良、可靠性强、精度高的伺服系统来支持。
随着数控事业日新月异的发展,伺服系统也得到了前所未有的进步。
位置伺服的三环结构,充分利用了设备的潜力,高速及其准确的定位,使数控机床得到了广泛的应用。
伺服系统已全面进入了交流伺服时代,模块化、集成化、开放化是其发展的趋势。
同时,给维护工作也带来了极大的方便,一旦出现故障后,为了赢得生产时间,可采用备件替换法使机床及时得到恢复。
由于伺服系统的速度环和电流环的可靠性较高,通常,现场中伺服系统故障以位置环的故障率为最高,因为如编码器、光栅尺、伺服电动机等机构受外部影响较大。
现代数控设备已具有强大的故障自诊断能力。
伺服故障发生后,可以通过两种途径得到提示信息:一是驱动模块上的%89 或指示灯状态,二是根据":+ 上报警号和信息提示。
在不确定情况下,可以通过交叉换位法、备板置换法来诊断。
有条件的用户可以通过建立数控实验平台来诊断。
另一方面,在判断伺服驱动故障时应特别留意以下部位:!保险有无损坏;"模块或电动机的风扇(或散热器)的运转情况,查看有无积尘和接触不良;#可以单独更换部分#"; 板(如轴卡)进行尝试,此项应根据资料上说明进行;$检查存储器的电池电量是否充足;%整流器件或可直接判断已损坏电子管是否损坏。
发现上述故障完全可以自主修复。
当然,还可以在企业库存的坏模块中进行组合性试利用。
事实证明这样能为企业节省大量的维护成本。
目前,由于大部分企业现场维修人员没有完备的参考资料和修理条件,对集成度高或难于判断的故障应送到专门的板级维修部门修复。
同时,规模大、损坏频率高的企业还可以采用参保方式来节约成本开销。
如:一进口TM1800五坐标加工中心,采用SIEMENS 840D 数控系统。
在加工过程中车间突然断电,待重新启动机床后,机床出现以下报警:①300201轴A1驱动器访问时,错误2340;②300901轴A1驱动器停止信号B被触发;③21612通道1 轴(X、Y、Z、C)正在运动时VDI信号“调节使能”被复位;④600707 TURN-STOP C/S P2:SPINDLE DRIVE NOT READY。
从报警信息看出报警(1)和(2)与A轴有关,各轴模块同时损坏的可能性在实际故障中是相当小的。
初步认为,系统检测到# 轴驱动模块有故障后,导致通道1 轴VDU信号的“调节使能”被复位,以及主轴驱动未准备好。
查看300201报警解释原因有两点:“一是与一个或多个模块的电压掉电有关;二是硬件(包括ASICs总线和驱动模块)已经损坏。
”为了防止接触不良的可能,决定关断机床电源,将各接口取下检查并重新插接。
重新启动机床后发现起初四个报警已经消失,但出现新的报警内容为“300006 起码有一个模块(模块驱动号Y1)在驱动总线上没有发现。