cnc加工中心刀具大全及如何选择【全解】
CNC加工中心刀具选用

加工中心上用的立铣刀一般有三种形式:球头刀(R=r)、端铣刀(r=0)和R刀(r图1 立铣刀结构示意图
加工空间曲面和变斜角轮廓外形时,由于球头刀具的球面端部切削速度为零,而且在走刀时,每两行刀位之间,加工表面不可能重叠,总存在没有被加工去除的部分,每两行刀位之间的距离越大,没有被加工去除的部分就越多,其高度(通常称为“残留高度”) 就越高,加工出来的表面与理论表面的误差就越大,表面质量也就越差。加工精度要求越高,走刀步长和切削行距越小,编程效率越低。因此,应在满足加工精度要求的前提下,尽量加大走刀步长和行距,以提高编程和加工效率。而在两轴及两轴半加工中,为提高效率,应尽量采用端铣刀,由于相同的加工参数,利用球头刀加工会留下较大的残留高度。因此,在保证不发生干涉和工件不被过切的前提下,无论是曲面的粗加工还是精加工,都应优先选择平头刀或R刀(带圆角的立铣刀)。不过,由于平头立铣刀和球头刀的加工效果是明显不同的,当曲面形状复杂时,为了避免干涉,建议使用球头刀,调整好加工参数也可以达到较好的加工效果。在选择刀刃长度和刀杆长度时,应考虑机床的情况及零件的尺寸是否会干涉。在可能的情况下,应尽量选短一些,以提高刀具的刚度。
(7)刀杆长度 刀尖到刀柄之间的距离。刀杆长度应大于刀刃有效长度。并且一般刀杆长度要大于工件总切深。如果不大于总切深,一定要检查刀柄是否会与工件相接触。
加工中心机床刀具是一个较复杂的系统,如何根据实际情况进行正确选用,是编程人员必须掌握的。只有对加工中心刀具结构和选用有充分的了解和认识,在实际工作中才能灵活运用,提高工作效率和安全生产。
铣削盘类零件的周边轮廓一般采用立铣刀。所用的立铣刀的刀具半径一定要小于零件内轮廓的最小曲率半径。一般取最小曲率半径的0.8到0.9倍即可。零件的加工高度(Z方向的吃刀深度)最好不要超过刀具的半径。若是铣毛坯面时,最好选用硬质合金波纹立铣刀,它在机床、刀具、工件系统允许的情况下,可以进行强力切削。
CNC机床加工中的刀具选型与切削参数优化

CNC机床加工中的刀具选型与切削参数优化CNC(Computer Numerical Control)机床是一种能够按照预先输入的程序指令进行自动化加工的机床。
在CNC机床加工中,刀具选型与切削参数的选择对于加工质量和效率起着至关重要的作用。
本文将就CNC机床加工中的刀具选型与切削参数优化进行探讨。
一、刀具选型在CNC机床加工中,刀具的选型要根据加工材料、加工要求以及加工方式来选择,常用的刀具选型有以下几种:1.硬质合金刀具硬质合金刀具具有优异的耐磨性和高硬度,适用于加工硬度较高的材料,如铸铁、合金钢等。
同时,硬质合金刀具还能够提供较好的切削性能和切削稳定性,因此在高速切削中得到广泛应用。
2.高速钢刀具高速钢刀具是热处理过的优质合金钢,具有较高的硬度和耐磨性。
高速钢刀具适用于一般加工材料的加工,价格相对较低,是较为经济实用的刀具选型。
3.立铣刀具立铣刀具适用于铣削工艺,能够完成平面铣削、开槽、镗孔等加工操作。
立铣刀具具有较高的刚性和切削性能,能够提高加工效率和加工精度。
4.钻孔刀具钻孔刀具用于钻孔加工,分为普通钻头和中心钻头两类。
普通钻头适用于常规钻孔操作,而中心钻头则适用于加工前的定位孔。
二、切削参数优化在CNC机床加工中,刀具的切削参数选取直接关系到加工效率和加工质量,合理的切削参数优化能够提高加工效率和延长刀具寿命。
下面分别从切削速度、进给量、切削深度等几个方面进行优化探讨。
1.切削速度切削速度是指刀具在加工过程中的旋转速度,需要根据材料硬度和刀具类型来选择合适的转速。
过高的切削速度会导致切削过程中的高温和过量磨损,而过低的切削速度则会影响加工效率。
因此,在确定切削速度时,需要考虑加工要求和刀具特性,以达到切削效果和刀具寿命的平衡。
2.进给量进给量是指刀具在加工过程中沿工件表面前进的距离,选择合适的进给量可以控制加工负荷,保证加工质量。
过小的进给量会导致切削效率低下,过大的进给量则容易引起振动和过度磨损。
CNC刀具的选择和选购

CNC刀具的选择和选购CNC常用刀具有哪些?如何选择刀具?1.CNC刀具种类常用的数控铣刀具按形状分为平底刀、圆鼻刀和球刀3种。
(1)平底刀平底刀也叫平刀或端铣刀,周围有主切削刃,底部为副切削刃。
可以用于开粗及清角、精加工侧平面及水平面。
一般情况下,开粗时尽量选较大直径的刀,装刀时尽可能短,以保证有足够的刚度,避免弹刀。
在选择小刀时,要结合被加工区域,确定最短的刀锋长及直身部分长,选择本公司现有的最合适的刀。
如果侧面带斜度叫斜度刀,可以精加工斜面。
(2)圆鼻刀圆鼻刀也叫平底R刀,可用于开粗、平面光刀和曲面外形光刀。
一般角半径为R0.1~R8。
一般有整体式和镶刀粒式的刀把刀。
镶刀粒的圆鼻刀也叫“飞刀”,主要用于大面积的开粗及水平面光刀。
飞刀开粗加工尽量选大刀,加工较深区域时,装刀长度先装短加工较浅区域,再装长加工较深区域,以提高效率且不过切。
(3)球刀球刀也叫R刀,主要用于曲面中光刀及光刀。
(常用于加工流道)一般情况下,要通过测量被加工图形的内圆半径来确定精加工所用的刀具,尽量选大刀光刀、小刀补刀加工。
2.刀具材料在金属切削加工中,刀具材料也就是切削部分,要承受很大的切削力和冲击,并受到工件及切屑的剧烈摩擦,产生很高的切削温度。
其切削性能必须要有以下方面。
(1)高的硬度:HRC62以上,至少要高于被加工材料的硬度。
(2)高的耐磨性:通常情况下,材料越硬、组织中碳物越多、颗粒越细、分布越均匀,其耐磨性就越高。
(3)足够的强度与韧性。
(4)高的耐热性。
(5)良好的导热性。
(6)良好的工艺性和经济性。
为了满足以上要求,现在的数控刀具一般由以下材料制成:(1)高速钢,如WMoAl系列。
(2)硬质合金,如YG3等。
(3)新型硬质合金,如YG6A。
(4)涂层刀具,如TiC、TiN、Al2O3。
(5)陶瓷刀具。
在高温下仍能承受较高的切削速度。
(6)超硬刀具材料。
cnc刀具工艺知识点总结
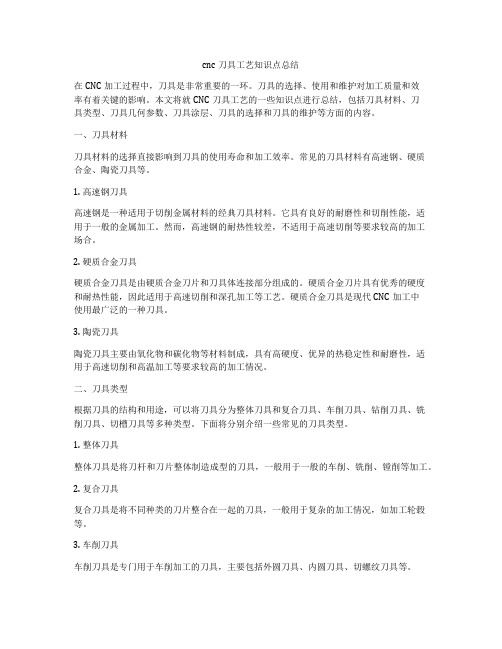
cnc刀具工艺知识点总结在CNC加工过程中,刀具是非常重要的一环。
刀具的选择、使用和维护对加工质量和效率有着关键的影响。
本文将就CNC刀具工艺的一些知识点进行总结,包括刀具材料、刀具类型、刀具几何参数、刀具涂层、刀具的选择和刀具的维护等方面的内容。
一、刀具材料刀具材料的选择直接影响到刀具的使用寿命和加工效率。
常见的刀具材料有高速钢、硬质合金、陶瓷刀具等。
1. 高速钢刀具高速钢是一种适用于切削金属材料的经典刀具材料。
它具有良好的耐磨性和切削性能,适用于一般的金属加工。
然而,高速钢的耐热性较差,不适用于高速切削等要求较高的加工场合。
2. 硬质合金刀具硬质合金刀具是由硬质合金刀片和刀具体连接部分组成的。
硬质合金刀片具有优秀的硬度和耐热性能,因此适用于高速切削和深孔加工等工艺。
硬质合金刀具是现代CNC加工中使用最广泛的一种刀具。
3. 陶瓷刀具陶瓷刀具主要由氧化物和碳化物等材料制成,具有高硬度、优异的热稳定性和耐磨性,适用于高速切削和高温加工等要求较高的加工情况。
二、刀具类型根据刀具的结构和用途,可以将刀具分为整体刀具和复合刀具、车削刀具、钻削刀具、铣削刀具、切槽刀具等多种类型。
下面将分别介绍一些常见的刀具类型。
1. 整体刀具整体刀具是将刀杆和刀片整体制造成型的刀具,一般用于一般的车削、铣削、镗削等加工。
2. 复合刀具复合刀具是将不同种类的刀片整合在一起的刀具,一般用于复杂的加工情况,如加工轮毂等。
3. 车削刀具车削刀具是专门用于车削加工的刀具,主要包括外圆刀具、内圆刀具、切螺纹刀具等。
钻削刀具是专门用于钻孔加工的刀具,主要包括中心钻、旋转钻、铰刀等。
5. 铣削刀具铣削刀具是专门用于铣削加工的刀具,主要包括立铣刀、面铣刀、滚齿刨刀等。
6. 切槽刀具切槽刀具是专门用于切槽加工的刀具,主要包括立式切槽刀、侧面切槽刀等。
三、刀具几何参数刀具的几何参数是刀具设计的关键要素,直接影响着刀具的切削性能和加工质量。
主要包括刀尖半径、刀身倾角、主偏角、切削刃倾角等。
CNC机床加工中的钻削刀具的选择与应用

CNC机床加工中的钻削刀具的选择与应用CNC机床是现代制造业中不可或缺的重要设备之一,其高精度和高效率的加工能力使其成为各行业中的首选。
而在CNC机床的加工过程中,钻削是其中一项常见而重要的操作。
本文将重点探讨CNC机床中钻削刀具的选择与应用,帮助读者更好地了解这一领域的知识。
一、钻削刀具的选择要点选择合适的钻削刀具对于机床加工来说至关重要。
以下是几个选择刀具的要点:1. 材料选择:钻削刀具的材料种类繁多,常见的有高速钢、硬质合金、陶瓷和涂层刀具等。
根据加工材料的硬度、耐热性和切削性能等不同要求,选择相应的材料。
2. 刀柄类型:刀柄的类型有直柄和螺旋槽柄两种。
直柄适用于简单的钻削操作,而螺旋槽柄则适用于深孔钻削,可提供更好的冷却和排屑效果。
3. 刀尖形状:根据加工需要选择合适的刀尖形状,如标准点角、圆头、镗刀等。
刀尖的选择会影响到加工后的孔形和表面质量。
4. 切削边角度:根据加工材料的硬度和切削要求选择合适的切削边角度。
通常情况下,较小的切削边角度适用于硬材料的加工,而较大的切削边角度适用于软材料的加工。
二、钻削刀具的应用场景在CNC机床的加工过程中,钻削刀具具有广泛的应用场景。
下面列举几种常见的应用场景:1. 钻削孔加工:钻削刀具用于加工各种孔径和深度的孔。
在进行孔加工时,应选择合适的钻削刀具和加工参数,确保孔的精度和表面质量。
2. 镗削孔加工:在需要加工大孔径和高精度的孔时,可以使用镗削刀具进行加工。
镗削刀具具有较高的刚度和稳定性,能够满足高精度孔加工的要求。
3. 深孔加工:对于需要进行深孔加工的工件,通常采用深孔钻削刀具。
这种刀具具有内部冷却系统,可以在加工过程中提高冷却效果和排屑能力,保证加工质量。
4. 钻削面加工:除了加工孔,钻削刀具还可以进行面加工。
例如,在加工平面等工件时,可以使用适当的钻头进行铣削和切削操作。
三、常见问题及解决方法在钻削刀具的选择与应用过程中,也会遇到一些常见问题。
cnc选刀技巧
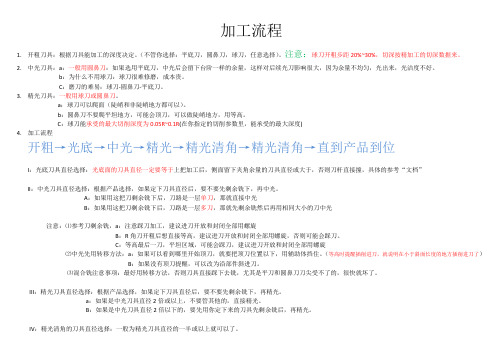
加工流程1.开粗刀具:根据刀具能加工的深度决定。
(不管你选择:平底刀,圆鼻刀,球刀,任意选择)。
注意:球刀开粗步距20%~30%,切深按精加工的切深数据来。
2.中光刀具:a:一般用圆鼻刀:如果选用平底刀,中光后会留下台阶一样的余量,这样对后续光刀影响很大,因为余量不均匀,光出来,光洁度不好。
b:为什么不用球刀:球刀很难修磨,成本贵。
C:磨刀的难易:球刀-圆鼻刀-平底刀。
3.精光刀具:一般用球刀或圆鼻刀。
a:球刀可以爬面(陡峭和非陡峭地方都可以)。
b:圆鼻刀不要爬平坦地方,可能会顶刀,可以做陡峭地方,用等高。
C:球刀能承受的最大切削深度为0.05R~0.1R(在你指定的切削参数里,能承受的最大深度)4.加工流程开粗→光底→中光→精光→精光清角→精光清角→直到产品到位I:光底刀具直径选择:光底面的刀具直径一定要等于上把加工后,侧面留下夹角余量的刀具直径或大于,否则刀杆直接撞,具体的参考“文档”II:中光刀具直径选择:根据产品选择,如果定下刀具直径后,要不要先剩余铣下,再中光。
A:如果用这把刀剩余铣下后,刀路是一层单刀,那就直接中光B:如果用这把刀剩余铣下后,刀路是一层多刀,那就先剩余铣然后再用相同大小的刀中光注意:⑴参考刀剩余铣,a:注意踩刀加工,建议进刀开放和封闭全部用螺旋B:R角刀开粗后想直接等高,建议进刀开放和封闭全部用螺旋,否则可能会踩刀。
C:等高最后一刀,平坦区域,可能会踩刀,建议进刀开放和封闭全部用螺旋⑵中光先用转移方法:a:如果可以看到哪里开始顶刀,就要把顶刀位置以下,用辅助体挡住。
(等高时提醒插削进刀,就说明在小于斜面长度的地方插削进刀了)B:如果没有顶刀提醒,可以改为沿部件斜进刀。
⑶混合铣注意事项:最好用转移方法,否则刀具直接踩下去铣,尤其是平刀和圆鼻刀刀尖受不了的,很快就坏了。
III:精光刀具直径选择:根据产品选择,如果定下刀具直径后,要不要先剩余铣下,再精光。
a:如果是中光刀具直径2倍或以上,不要管其他的,直接精光。
数控铣(加工中心)的刀具选用
数控铣(加工中心)的刀具选用数控铣床上所采用的刀具要根据被加工零件的材料、几何形状、表面质量要求、热处理状态、切削性能及加工余量等,选择刚性好、耐用度高的刀具。
常见刀具见图1。
1. 铣刀类型选择被加工零件的几何形状是选择刀具类型的主要依据。
(1)加工曲面类零件时,为了保证刀具切削刃与加工轮廓在切削点相切,而避免刀刃与工件轮廓发生干涉,一般采用球头刀,粗加工用两刃铣刀,半精加工和精加工用四刃铣刀,如图2所示。
图1 常见刀具图2 加工曲面类铣刀(2)铣削较大平面时,为了提高生产效率和提高加工表面粗糙度,一般采用刀片镶嵌式盘形铣刀,如图3所示。
图3 加工大平面铣刀(3)铣削小平面或台阶面时一般采用通用铣刀,如图4所示。
图4 加工台阶面铣刀(4)铣键槽时,为了保证槽的尺寸精度、一般用两刃键槽铣刀,如图5所示。
(5)孔加工时,可采用钻头、镗刀等孔加工类刀具,如图6所示。
2. 铣刀结构选择铣刀一般由刀片、定位元件、夹紧元件和刀体组成。
由于刀片在刀体上有多种定位与夹紧方式,刀片定位元件的结构又有不同类型,因此铣刀的结构形式有多种,分类方法也较多。
选用时,主要可根据刀片排列方式。
刀片排列方式可分为平装结构和立装结构两大类。
(1)平装结构(刀片径向排列).图7 平装结构铣刀平装结构铣刀(如图7所示)的刀体结构工艺性好,容易加工,并可采用无孔刀片(刀片价格较低,可重磨)。
由于需要夹紧元件,刀片的一部分被覆盖,容屑空间较小,且在切削力方向上的硬质合金截面较小,故平装结构的铣刀一般用于轻型和中量型的铣削加工。
图5 加工槽类铣刀图6 孔加工刀具(2)立装结构(刀片切向排列) 立装结构铣刀(如图8所示)的刀片只用一个螺钉固定在刀槽上,结构简单,转位方便。
虽然刀具零件较少,但刀体的加工难度较大,一般需用五坐标加工中心进行加工。
由于刀片采用切削力夹紧,夹紧力随切削力的增大而增大,因此可省去夹紧元件,增大了容屑空间。
由于刀片切向安装,在切削力方向的硬质合金截面较大,因而可进行大切深、大走刀量切削,这种铣刀适用于重型和中量型的铣削加工。
CNC刀具类型与选择
CNC刀具类型与选择1、整体式铣刀a、平底刀b、圆鼻刀c、球头刀(材料分:硬质合金刀、高速钢刀)2、可转位机夹铣刀a、面铣刀b、三面刃铣刀c、立铣刀立铣刀是加工模具型腔和箱体最常用的工具,行切法铣平面的切削宽度是刀具直径的60%~80%。
面铣刀a.疏齿:不等齿距铣刀,容屑槽宽度大,适合铣削不锈钢和铝合金等长屑金属;又因铣刀同时铣削金属的齿数少,故切削力小,适合小功率主轴机床或工件夹持薄弱的工件。
b、密齿:属于齿数适中铣刀,通用性范围广,通常作为首选推荐铣刀,当要求铣削切削力较小时,通常采取减少刀片数目的方法,但要均匀的邻位拆除。
c、超密齿:用于主轴功率足够的机床,在工件夹持足够的情况下,可获得大切深大走刀的高效率金属去除率。
也适合灰铸铁等要求容屑率低的金属铣削。
面铣刀的主偏角(10°、45°、90°)刀片刃口和工件的加工表面之间的夹角。
在相同进给速度下,减小主偏角,则切削厚度变薄,切屑与切削刃的接触长度更长。
较小的主偏角也可使刀具更为平稳地进入切口,有助于减小径向压力和锥孔的压力。
90°:可以铣削具有台肩要求的工件,可以获得直角边,但是会产生绝大部分的径向压力,同时也意味着被切得表面承受的轴向压力较小,这对于低强度结构的工件、薄壁工件的加工很有积极意义。
45°:轴向和径向压力大小值接近,会产生更为平稳的压力,且对机床功率要求相对较小,为平面铣削首选刀具。
10°:主要用于插铣,并且也是小切深、大走刀量面铣刀。
常用于模具宽大型腔加工时,大量快速去除余量。
因为径向切削力很小,因而可以降低因刀杆悬伸过长而产生的震动趋势。
69°、75°铣刀,主要用于冷硬铸铁和铸钢的表面粗加工。
圆刀片:具有连续可变的主偏角(从0°~90°),其值取决于切入深度的情况。
具有非常坚固的切削刃,切削力均匀分布,适合高进给速率的加工,常用于模具型腔的快速去除余量,具有薄切削效应,适合加工耐热合金和钛合金。
数控铣(加工中心)的刀具选用
千里之行,始于足下。
数控铣(加工中心)的刀具选用
在数控铣床(加工中心)中,刀具的选择对加工效率和加工质量有着重要的
影响。
下面将就刀具材料、刀具形状、刀具涂层等几个方面来探讨数控铣床刀
具的选用。
1. 刀具材料:常见的刀具材料有高速钢、硬质合金和刚玉等。
高速钢刀具具有较好的塑性和切削性能,适用于切削材料比较软的工件;硬质合金刀具具
有较高的硬度和耐磨性能,适用于切削材料比较硬的工件;刚玉刀具则在超硬
材料加工中具有较好的切削性能。
2. 刀具形状:常见的刀具形状有平头刀、球头刀、角形刀和弧形刀等。
平头刀适用于平面铣削和侧面铣削,常用于粗加工;球头刀适用于曲面加工和球
面加工,常用于精加工;角形刀适用于开槽和切割等操作;弧形刀适用于轮廓
加工和复杂曲线加工。
3. 刀具涂层:刀具涂层能够提高刀具的硬度、耐磨性和润滑性,从而延长刀具寿命和提高加工质量。
常见的刀具涂层有TiN、TiC、TiCN、AlTiN等。
TiN 涂层主要用于加工不锈钢、铸铁和铝合金等材料;TiC涂层适用于加工高硬度
材料;TiCN涂层具有较好的耐磨性和润滑性能;AlTiN涂层具有良好的耐热性
和耐磨性能,适用于高温和高硬度材料加工。
在选择刀具时,还需考虑工件材料、加工要求和加工稳定性等因素。
另外,刀具的刃数、刀具直径和切削参数等也需要根据具体情况进行选择。
在刀具的
使用过程中,还需注意及时更换磨损的刀具、合理设置刀具余量和刀具进给速
度等,以保证加工效率和加工质量。
第1页/共1页。
数控加工常用刀具及参数选择
数控加工常用刀具及加工参数刀具的选择和刀具参数的设置是数控加工工艺中的重要内容,合理地选用刀具和设置刀具参数不仅可以影响数控机床的加工效率,而且可以直接影响加工质量。
1.数控铣削加工常用刀具铣削用刀具通常称为铣刀,普通铣床上的刀具可以用于数控铣床和加工中心上。
一般立式数控加工用铣刀的种类可以有很多种划分方法,既可以从刀具的材料上划分,也可以从刀具的外形上划分,还可以从刀具的用途等方面来划分。
依刀具的外形,数控加工常用的刀具有平刀、圆鼻刀(飞刀)、球刀三种。
(1)平刀平刀底面是平面,平刀是一种以侧刃切削的刀具,所以使用平刀加工时应尽量避免切入底面的工件表面,一般平刀用作开粗和加工平面。
常用平刀大小有D1、D2、D4、D6、D8、D10、D12、D16、D20。
(2)圆鼻刀(飞刀)圆鼻刀底面是平面,每刃都带有圆角,因为底面是平面,所以加工时也应尽量避免切入底面的工件表面,一般圆鼻刀用作开粗,圆鼻刀开粗效果比平刀好。
常用圆鼻刀(飞刀)大小有D25R5、D3OR5。
(3)球刀球刀的切削刃有180°,所以球刀一般用作精加工,球刀切削时较稳定,但球刀不能用作开粗。
常用球刀大小有R1、R2、R3、R4、R5、R6、R8。
2.加工参数的选择随着模具制造技术的高速发展,刀具的加工参数的设置对加工的效率和加工质量的影响越来越大。
熟练掌握刀具加工参数的设置有利于提高加工的效率和加工质量。
刀具加工参数包括切削速度、进给量、背吃刀量(切削深度)和切削宽度。
(1)切削速度v切削速度是指铣刀刀齿切削处的线速度。
v=πDn/1000式中v—切削速度(m/min);D—铣刀直径(mm),周铣时为圆柱铣刀外圆直径;n—主轴转速(rmin)(2)进给量a,f铣削进给量有三种形式:铣刀每转过一个刀齿相对工件移动的距离称为每齿进给量a,其大小决定着一个刀齿的负载,a越大,切削力越大,刀齿的负载也越大。
铣刀每转相对工件移动的距离称为每转进给量f。
- 1、下载文档前请自行甄别文档内容的完整性,平台不提供额外的编辑、内容补充、找答案等附加服务。
- 2、"仅部分预览"的文档,不可在线预览部分如存在完整性等问题,可反馈申请退款(可完整预览的文档不适用该条件!)。
- 3、如文档侵犯您的权益,请联系客服反馈,我们会尽快为您处理(人工客服工作时间:9:00-18:30)。
cnc加工中心刀具大全及如何选择
内容来源网络,由深圳机械展收集整理!
更多相关内容,就在深圳机械展刀具展区!
首先我们来认识一下常用的cnc加工中心刀具:
平底刀:也称平刀或端铣刀。
周围有主切削刃,底部为副切削刃。
可以作为开粗及清角,精加工侧平面及水平面。
有D16,D12,D1O,D8,D6,D4,D3,D2 ,D1.5,D1等。
D表示切削刀刃直径。
一般情况下,开粗时尽量选较大直径的刀,装刀时尽可能短,以保足够的刚度,避免弹刀。
在选择小刀时,要结合被加工区域,确定刀锋长及直身部分长,选择现有的合适的刀。
圆鼻刀:也称平底R刀。
可用于开粗、平面光刀和曲面外形光刀。
一般角半径为R0.8和R5。
一般有整体式和镶刀粒式的刀把刀。
带刀粒的圆鼻刀也称飞刀,主要用于大面积的开粗,水平面光刀。
有D50R5,D30R5, D25R5, D25R0.8, D21R0.8,D17RO.8等。
飞刀开粗加工尽量选大刀,加工较深区域时,先装短加工较浅区域,再装长加工较深区域,以提高效率且不过切。
球刀:也称R刀。
主要用于曲面中光刀(即半精加工)及光刀(即精加工)。
常用的球刀有D16R8, D12R6, D10R5, D8R4, D6R3, D5R2.5(常用于加工流道),D4R2, D3R1.5, D2R1, D1R0.5。
一般情况下,要通过测量被加工图形的内圆半径来确定精加工所用的刀具,选大刀光刀,小刀补刀加工。
如何选择cnc加工中心刀具:
刀具的选择是在数控编程的人机交互状态下进行的。
应根据机床的加工能力、工件材料的性能、加工工序、切削用量以及其它相关因素选用刀具及刀柄。
刀具选择总的原则:安装调整方便刚性好,耐用度和精度高。
在加工要求的前提下,选择较短的刀柄以提高刀具加工的刚性。
选取刀具时,要使刀具的尺寸与被加工工件的表面尺寸相适应。
1.平面零件周边轮廓的加工,常采用立铣刀。
2.铣削平面时,应选硬质合金刀片铣刀。
3.加工凸台、凹槽时,选高速钢立铣刀。
4.加工毛坯表面或粗加工孔时,可选取镶硬质合金刀片的玉米铣刀。
5.对一些立体型面和变斜角轮廓外形的加工,采用球头铣刀、环形铣刀、锥形铣刀和盘形铣刀。
6.在进行自由曲面加工时,由于球头刀具的端部切削速度为零,因此,为保加工精度,切削行距一般取得很能密,故球头常用于曲面的精加工。
7.平头刀具在表面加工质量和切削效率方面都优于球头刀,因此,只要在保证不过切的前提下,无论是曲面的粗加工还是精加工,都应优选择平头刀。
8.在加工中心上,各种刀具分别装在刀库上,按程序规定随时进行选刀和换刀动作。
因此必须采用标zhun刀柄以便使钻、镗、扩、铣削等工序用的标zhun 刀具,迅速准确地装到机床主轴或刀库上去。
应尽量减少刀具数量;一把刀具装夹后应完成其所能进行的所有加工部位;粗精加工的刀具应分开使用即使是相同尺寸规格的刀具;先铣后钻;先进行曲面精加工再进行二维轮廓精加工;在可能的情况下,应尽可能利用数控机床的自动换刀功能,以提高生产效率等。
内容来源网络,由深圳机械展收集整理!
更多相关内容,就在深圳机械展!。