PCB微切片
PCB微切片制作与分析报告

微切片制作与分析报告经过一段时间对微对片的制作与分析观察,从中收获很多.微切片是我们用于分析问题﹑认证问题和解决问题的一个重要手段和工具.尤其对我们制程工程师来说,对于问题的分析确认和以及条件变更,起着相当重要的作用.因此,对于我们制程工程师来说,学会制作分析微切片是我们的一项基本技能。
微切片的制作标准是﹔抛光完美﹑织纹清晰可见﹐无明显刮痕。
按照一般的流程﹐要想制作一个好的微切片﹐主要分为以下几个步骤﹒1﹒取样把样品从板内或测试coupon上取下﹒公司化验室有两种用于提取样品的机台一种是切割机﹐主要用于切割较薄的板子﹐或是板边取样另一种是捞床﹐主要用于捞取较厚的板子﹐或离板边较远处取样﹒2﹒烘烤(1).热应力切片必须经过121℃-149℃烘烤至少6小时.(2).烘烤后将样品放入干燥器内的陶瓷板上冷却至室温.3﹒热应力试验(1).样品从干燥器中取出后涂上助焊剂.(2).热应力条件依客户规格4. 灌胶灌胶的目的是为了固定试片﹐方便研磨.(1)将样品用适当溶剂清洗干净.(2)将切下的样本放置压克力中﹒然后将固化剂和树脂粉混合均匀后倒入模子中﹐烘烤加速硬化或在常温下使溶剂挥发硬化起到固定样品的作用﹒在该步骤中﹐注意在灌胶前需要将试样放正﹐胶要调得黏稠适度﹐太稀会影响胶凝固的时间﹐太浓胶不易灌到孔内﹐且容易产生气泡另外要注意的是要尽量减少灌胶时产生的气泡胶﹒5﹒研磨研磨是在高速转盘上利用砂纸的切削力﹐将样本磨至我们所需要观察的地方﹒这是制作一个好的微切片的关键步骤﹐是制作微切片技术的精华所在﹐往往一个微切片制作的好坏在很大程度上就取决于研磨过程质量的好坏﹒(1).用180#,1200#,2400#砂纸磨到孔中心.(2).用4000#砂纸去除切片表面刮痕,使之光滑平整.研磨的要点是:对孔壁而言其截面必须落在孔心平面之附近,必须要两壁平行﹐必须要消除大多数砂痕﹒6﹒抛光为了便于观察﹐我们将微切片研磨后还要经过几个动作﹐来加以保证微切片的制作质量﹒(1)抛光时应加0.3um氧化铝膏作抛光助剂.(2)抛光时要不断改变方向,使之产生均匀的抛光效果直至刮痕完全消除,切片表面光亮如镜.一般抛光1~3min.7﹒微蚀(1)用微蚀液在切片表面擦约2~3秒,使电镀界面显现,必要时重新微蚀2~3秒.(2)用清水或纯水将微蚀液冲掉后吹干.备注:两种典型微蚀液NH4.H2O,H2O2微蚀液K2Cr2O7微蚀液8﹒判读(1)在放大100X明视下观察并判读所有要求之内容.(2)除非另有说明,一般以放大200X为最终判定倍数经过上面几个步骤﹐一个切片的制作就基本完成了﹐下面我就KS组常用到的一些微切片作一个基本介绍﹒1﹒孔未堵满孔未堵满也是KE站内常见的不良之一﹒对于内层的堵孔﹐如果孔未堵满﹐在后续制程中易残留药水﹐从而产生重大的报废等不良后果﹒而对于外层堵孔﹐如果未堵满容易产生孔发黄﹐出现假性露铜的不良﹐客户也是不能接受的当然﹐不同的客户对孔未堵满各有不同的管控标准﹐如果在客户标准范围内的孔未堵满﹐还是可以接受的﹒究其原因﹐常见的有﹔(1)网版未对准(2)印刷时油墨有气泡(3)刮刀压力不足﹒(4)油墨粘度不够(5)研磨过度(6)底座粘板﹒2.油墨起泡油墨起泡是KE站主要不良之一,其主要原因及对策有如下几点油墨厚度是KE印刷时经常提到的一个控制参数﹒如果控制不好﹐会对产品质量产生较大的影响﹒按照IPC规范﹐拒焊油墨厚度的规格为﹔(1)原板厚度﹔>=0﹒4mil;(2)拐角厚度﹔>=0﹒2mil (3)线路和铜面厚度﹔>=0﹒2mil﹒导电油墨的规格是﹔基材厚度﹔0﹒6~2﹒0mil拐角厚度﹔0﹒2~2﹒0mil铜面厚度﹔0﹒4~2﹒0mil﹒油墨太薄﹐则影响线路的阻抗﹐外观等﹒而且易引起油墨起泡等不良﹐进而造成板子报废等后果﹒油墨太厚﹐同样会影响线路的阻抗﹐而且对生产成本也会有较大的影响﹒就本站来说﹐影响油墨厚度的原因﹐常见的有﹔(1)网版目数(2)网版间距(3)刮刀压力(4)刮刀角度(5)刮刀厚度(6)印刷速度(7)印刷次数(8)油墨粘度等﹒。
PCB切片制作方法课件

標準做法:將沖切或鋸切的方形切片垂直放入壓克 力模具中,將灌模膠依比例(牙托粉:牙托水=1.5: 1)輕輕攪拌均勻後,從切片樣品的一側慢慢灌入切 片灌模中,使膠流經孔壁,再注滿整個罐模,靜置 約15~20分鐘直至完全硬化。
切片室異常匯總
1.空板通孔切片可見現象:
板材結構,孔銅厚度,孔銅品質,孔壁破洞,流錫情形, 鑽孔對準,層間對準,孔環變異,蝕刻情形,膠渣情形, 鑽孔情形(如挖破,釘頭),燈芯滲銅,孔銅拉離,反蝕回, 環壁互連品質(ICD),粉紅圈,點狀孔破等.
切片室異常匯總
2.熱應力填錫的通孔切片:(一般為288℃,10秒的熱應 力試驗)
a.斷角(Corner Cracking), b.樹脂縮陷(Resin Recession), c.壓合空洞(Laminalion Void), d.焊環浮起(Lifted Land), e.內環銅箔微裂, f.通孔焊錫好壞, g.吹孔(blow hole),
切片室異常匯總,允收標準詳解
電路板之微切片
主要內容
切片製作方法 切片製作允收標準
微切片的製作
1.取樣(Sample Cutting): 2.封膠(Resin Encapsulation): 3.磨片(Grinding): 4.拋光(Polish): 5.微蝕(Microetch): 6.攝影(Photography):
要點: 對孔壁而言其介面必須落在孔心平面之附近, 必須要兩壁平行,不可出現喇叭孔,必須要消除大多 數沙痕.
pcb微切片制作与不良分析

微切片制作(一)一、概述电路板品质的好坏、问题的发生与解决、制程改进的评估,在都需要微切片做为客观检查、研究与判断的根据(Microsectioning此字才是名词,一般人常说的Microsection是动词,当成名词并不正确)。
微切片做的好不好真不真,与研判的正确与否大有关系焉。
一般生产线为监视(Monitoring)制程的变异,或出货时之品质保证,常需制作多量的切片。
次等常规作品多半是在匆忙几经验不足情况下所赶出来的,故顶多只能看到真相的七、八成而已。
甚至更多缺乏正确指导与客观比较不足下,连一半的实情都看不到。
其等含糊不清的影像中,到底能看出什么来?这样的切片又有什么意义?若只是为了应付公事当然不在话下。
然而若确想改善品质彻底找出症结解决问题者,则必须仔细做好切取、研磨、抛光及微蚀,甚至摄影等功夫,才会有清晰可看的微切片画面,也才不致误导误判。
二、分类电路板解剖式的破坏性微切法,大体上可分为三类:1、微切片系指通孔区或其他板材区,经截取切样灌满封胶后,封垂直于板面方向所做的纵断面切片(Vertical Section),或对通孔做横断面之水平切片(Horizontal section),都是一般常见的微切片。
图1.左为200X之通孔直立纵断面切片,右为100X通孔横断面水平切片。
若以孔与环之对准度而言,纵断面上只能看到一点,但横断面却只可看到全貌的破环。
2、微切孔是小心用钻石锯片将一排待件通孔自正中央直立剖成两半,或用砂纸将一排通孔垂直纵向磨去一般,将此等不封胶直接切到的半壁的通孔,置于20X~40X的立体显微镜下(或称实体显微镜),在全视野下观察剩余半壁的整体情况。
此时若另将通孔的背后板材也磨到很薄时,则其半透明底材的半孔,还可进行背光法(Back Light)检查其最初孔铜层的敷盖情形。
图 2.为求检验与改善行动之效率与迅速全盘了解起见,最方便的方法就是强光之下以性能良好的立体显微镜(40X~60X)直接观察孔壁。
PCB微切片制作及缺点判读简介

3. 切片判断
3.13 回蚀(Etc back) 针对孔璧内层铜环上下对其介电层加以移除而退回之部分,铜孔壁与突 出内层孔环形成三面包夹结合, 但如过度回蚀造成孔壁粗糙也会导致应 力断裂可能
20 of 26
3. 切片判断
3.11 金属层与通孔孔壁的介电层间距
IPC:金属层自孔壁退后形成导体 间距>0.1mm或优于采购文件
21 of 26
3. 切片判断
3.12 灯芯效应(Wicking)
通常是结合力不好或者是钻孔等导致玻纤之间结合不 好,电镀时,药水渗入,形成灯芯状。
IPC:渗铜未超过0.1mm
15 of 26
3. 切片判断
3.6 孔铜完整性 有否镀瘤(Nodule), 夹杂物(Inclusion)孔口铜层结晶情形
IPC:不影响孔径
16 of 26
3. 切片判断
3.7 破洞(孔破)
一个切片只允许有三个破洞出现,破洞是焊锡时吹孔(Blow Hole) 最大原因,另外,会导致产品导致严重的失效。
IPC:1. 不可超过3个破洞 2. 大小未超过总板厚5% 3. 内层孔环与孔璧互连 接口不可出现镀层破洞 4. 破洞</=1/4圆周
NG
OK
17 of 26
3. 切片判断
3.8 钻孔品质 孔壁是否有孔壁粗糙及挖破情形
厂规:<1.4mil IPC:粗糙未降低孔铜 且孔径符合规格
18 of 26
3. 切片判断
9 of 26
2. 切片制作技巧
2.5 微蚀(micro-etch) 空板通孔直切切片一般可看到现象有 to layer registration)、孔环(Annular板材结构、孔铜厚度、孔铜 完整情形、破洞(VOID)、流锡情形、钻孔对准及层间对准(layer ring)、蚀刻情形、胶渣(Smear)情形、叠构及钻孔情形等
PCB切片

至少在1 mil以上,微蚀良好时可看清楚一次铜二次铜甚至厚化铜的层次,要注意有些制程会出现孔铜厚度差别很大的情形,由切片上左右两条铜壁厚度可明显的看出。
4.1.2孔铜完整情形
有否镀瘤(Nodule)夹杂物(Inclusion)孔口之阶梯式镀层(Step plating)及铜层结晶情形。
早期用“铬酸(Cr03)加入少量硫酸及食盐的方法”已经落伍,而且会使锡铅层发黑,不宜再用,氨水法则锡铅面仍呈现洁白,其中常见之黑点分布那是铅量较多区现象。
要做研究判断的切片必须要做仔细的抛光及微蚀的工作,否则只有白费功夫而已,一般出货性大量的切片,只好集体抛光,检查前再做微蚀,如此至少也可看到真像8.9分。
3.6.1 目视焦距与摄影焦距不完全相同,不可以目视为准,需多牺牲几张找出真正摄影焦距来。
3.6.2曝Biblioteka 所需之光量=光强度x时间,好的像片要尽量使时间延长及减少光强度,加上各种滤光片后可得各种不同效果的像片。
3.6.3影像表面须平整,否则倍数大时,(100x以上)会出现局部清楚局部模糊现象,得像后,要阴干透彻后才得触摸,避免造成画面受损。
4.1.5对准情形
可由孔壁两侧的内层长短情形看出层间对准情形及钻孔与印刷之间的对准情形。
4.1.6蚀刻
可看到侧蚀(undercut)及算出蚀刻因子,也可看到印刷或干膜的侧壁情形。
4.1.7胶渣
可看到除胶渣或回蚀(Etch back)的情形,过度除胶造成玻璃突出孔壁粗糙以致孔铜不平整也可能造成吹孔,除胶渣不足时,内层与孔铜之间有黑线或分隔(Separation)出现。
可对多层板面区或通孔区做层次间45°的斜切,然后以实体显微镜观察45°切面上导体间的情形。
PCB板微切片制作钉头问题分析

PCB板微切片制作钉头问题分析PCB板微切片制作钉头问题分析"Nail Heading钉头"在早期规范与品质观念中,被认为是一项必须检查的重点。
例如MIL-P-55110E中即规定,多层板内环之钉头宽度不可超过该铜箔厚度的1.5倍。
钉头的起因是出于钻针的过度损耗,或钻孔作业管理不良,使得钻针在穿孔过程中,并未对铜箔做正常的切削,而是用不利的钻针在强迫切削穿过之际,同时也对铜箔产生侧向推挤的动作,致使所形成孔环的侧壁,于瞬间高温及强压下被挤扁变宽而成为钉头。
看到钉头时几可立刻判断是钻孔制程管理不善所致,并成为容易被客户所发现与挑剔的缺失,表示钻孔的其他品质也颇有问题。
但自从SMT与起后,大部份零件已改为板面贴装,只有少数仍采用通孔插焊。
因而排除引脚焊脚而只用于导通互连的通孔,其品质已不如早期那么关键与受到重视。
虽然大环境已发生上述的变化,但许多客户对"钉头"仍然进行检验,尤其是过度的钉头,仍然是钻孔不良的一种表徵,也一定是出自钻针切削前缘的不利,崩刃、刃角变圆等问题,而这些问题也一定会引发出孔壁其他品质的不良。
此等纰漏一旦被发现时自不免又要大伤脑筋,要面对应如何搪塞客户如何改善缺失的窘境了。
当钻针情况最好时,其所切削过的孔环侧缘并未受到不当的挤压,因而铜箔截面宽度应如上左画面一般,不应有任何增宽才对。
上右图即为受到高温推挤变形而造成的钉头。
钻孔动作中高速旋转的钻针最后与孔壁接触者为"刃角"(Corner),当其呈现900时切削效果最好,一旦变圆后即容易出现钉头。
出现钉头的孔壁其他品质也好不到那里去,上左100X之八层板孔环已出现钉头,孔壁同时也有被挖破的创伤。
左200X画面轻微的钉头也带来Wedge Void的明显趋势(幸亏被化学铜良好电度所罩住,若PTH是其他直接电镀施工时,八成逃不了成为楔形孔破的可能。
注意:凡有玻织渗铜者多半是出自化学铜制程)。
PCB微切片分析

1.13 孔壁怎粗糙这是业界非常流行的一种说法,笔者时常被问到国际规范对孔壁粗糙是如何检验及允收的。
甚至有很多人以话传话,认为规范中允收的上限是1mil,事实上这全是子虚乌有的传说。
著名的各国际规范中均从未提到过Hole Roughness一词,只有孔铜破洞(Voids)或孔铜厚度不足等。
当然某些供需双方所自行订定的规范则不在此限,且其优先程度也高过国际规范。
"孔壁粗糙"当然是来自钻孔的不良,其中又以钻针情况不佳为主因。
说的更仔细一点,那就是针尖上两个第一面(First Facet)的切削前缘(Cutting Lips)出现崩破(Chipping),无法顺利切削玻璃束所致。
或针尖外侧两刃角(Corner)崩损磨圆,失去原来直角修整孔壁的功能。
于是在破烂刀具的又劈又撞情形下,经常会把迎面而来的纵向玻织束撞成破裂陷落的坑洞,不过横向撞折断者则尚可维持平坦。
下附各图中读者可清楚的看到其孔壁放大的细部情形。
图1 迎面而来纵向纱束被劈散成坑的详情(注意:此切片在采样切板时,剪裁落点太靠近孔体,以致造成内层孔环铜箔被严重拉扯弯曲变形的画面,此样已完成PTH与一次铜,故起伏落差情形更为夸张明显)。
图2 此为六层板之全层通孔,各铜箔内环已明显出现钉头(Nail Heading),并有玻织束被挖破的画面,但这种孔壁钻破与钉头之间似乎并无必然的关系。
注意:切片制作时的灌胶一定要小心,不但一定要填满而且烘烤硬化时也不可太急,以防胶内产生空洞。
如此不但画面不美且还会影响到孔铜厚度的观察与细部真相。
图3 孔壁上虽已出现一个挖破之凹陷,不过铜箔内环并无明显的钉头。
图4 过度钉头几乎一定会出现较大的挖破,出自钻孔的纵向玻璃纱束之挖破,除与钻针尖部的"刃角"损耗有密切关系外,也与钻针的偏转(Run Out)或摇摆(Wobble)有关。
此图可清楚见到钉头已远超过允收规格(钉头宽度不可超过铜箔厚度的1.5倍)。
PCB微切片讲义
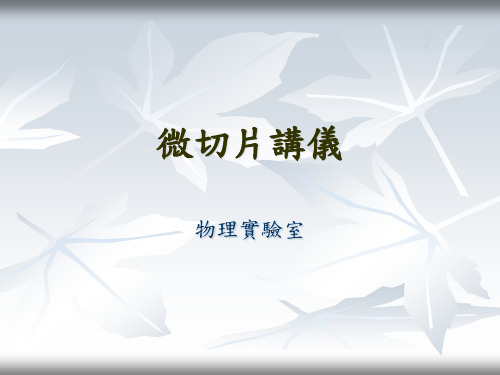
(4) 改用2500#沙紙打磨去除粗糙表面“孔的1/2位置”所预 设“指示线”的出现1/2位置,并伺机修平粗糙的表面。
4、 抛 光(Poish) 要看清切片的真相必须仔细抛光,以消除砂纸的刮痕。
因镀铜过程中有固体 粒子附著,再被铜层所加 厚造成的瘤粒,与钻孔并 无关系.
夹杂
如圖附著物是一铜开始不久就附上,再被后续包围而成的夹杂物。须知槽液 中各种浮游固体粒子常会著落而成镀瘤(注:垂直挂镀的板子,其孔内流速 很小,愈是深孔愈糟糕)
薄膜状外来物或未除尽之原来不良皮膜会在板面铜层上被后来镀层所包围
(1).拋光時首先將拋光粉和水對調,約4-5勺拋光粉裝入0.5升的拋光瓶 內加滿水用力搖1-2分鐘,將水與粉融合.故名拋光液.
(2).將拋光絨布打湿,將抛光液倒入適當在絨布上,進行拋光 (3).拋光時要保持與孔的方向一致,這樣可以避免受力方向不同造成 的拉傷.拋光1-2分鐘,拋亮即可.
拋光良好無 刮傷的良跡
3、磨 片(Crinding) 在高速转盘上利用砂纸的切削力,将切样磨到通孔正中央
的剖面,亦即圆心所座落的平面上,以便正确观察孔壁之截 面情况。研磨時注意順著口子磨保持方向一致:
(1) 先用240#沙紙,粗磨到通孔的開口位置止.(注意研磨過程 中适量冲水,以方便减热与滑润。)
(2) 改用600#沙紙磨到“孔的1/3位置”并伺机修平改正已 磨歪磨斜的表面。
4.1、空板通孔切片(含喷过锡的板子)可看到各种现象有:
板材结构、孔铜厚度、孔铜品质、孔壁破洞、流锡情形、钻孔对准、层 间对准、孔环变异、蚀刻情形、胶渣情形、钻孔情形(如挖破、钉头)、 灯芯渗铜、孔铜拉离、反蚀回、环壁互连品质(ICD)、粉红圈、点状孔 破(Wedge Void)等,
- 1、下载文档前请自行甄别文档内容的完整性,平台不提供额外的编辑、内容补充、找答案等附加服务。
- 2、"仅部分预览"的文档,不可在线预览部分如存在完整性等问题,可反馈申请退款(可完整预览的文档不适用该条件!)。
- 3、如文档侵犯您的权益,请联系客服反馈,我们会尽快为您处理(人工客服工作时间:9:00-18:30)。
明视200X之斜 切片
暗视200X之斜 切片
三、制作技巧
微切片需填胶抛光与微蚀,才能看清各种真实品质.以下为 制作过程的重点:
1、取 样(Sample culling)
剥膜及蚀刻后尚未熔锡之画面,其二铜与锡铅之横 向扩镀
网印负片法熔锡后的切片
由圖可以看出二铜镀得特别厚,不但超越 油墨而且还侧爬颇远 ,孔环外缘截面呈现缺口
2、干 膜 阻 剂
此200X画面的油墨阻剂(如同墙壁)出现 异常,致使二次铜一开始往墙外恻向伸出, 有了镀铜层在非导体表面建立基地,锡铅镀 层当然就毫不客气顺理成章的成长,其结果 不免造成板子的报废。
各种直接电镀法),即全板镀铜直到完成孔壁铜厚之要求随即以 干膜进行盖孔式(Tenting)的影像转移,再直接蚀刻 .
4.1.2孔銅完整情形 1.銅瘤
是否有銅瘤(Nodule)夾雜物(Inclusion)孔口之階梯式鍍層 (Step plating)及銅層結晶情形.
一銅鍍銅不均形 成的铜瘤
鑽孔毛刺造成,鍍一銅時, 形成的瘤狀
膠渣會影響孔环与铜壁的互连 IPC-6012对此明文规定:过份除胶渣所造成的回蚀深度的不可超
过1mil。
内层孔环与孔壁之间有未除尽的残余胶渣
镀上的铜壁又被拉开的情形
一面镀一面不断被拉开的情形
重铬酸过镀除胶渣造成孔 壁表面的树脂全部溶出, 其缩陷造成断点整齐的玻 纤束突出
除膠渣良好圖片
未做除胶渣的双面板孔铜壁 经喷锡后退即出现了罕见的 严重拉离(Pull Away)
二、分类
电路板解剖式的破坏性微切法,大体上可分为三类: 1、 微 切 片
系指通孔区或其他板材区,经截取切样灌满封胶后,封垂直 于板面方向所做的纵断面切片(Vertical Section),或对通孔做横 断面之水平切片(Horizontal section),都是一般常见的微切片。
若以孔与环之对准度而言,纵断面上只能看到一 点,但横断面却可看到全貌的破环。
(3) 改用1200#沙紙細磨到“孔的1/2位置”所预设“指示线” 的出现,并伺机修平改正已磨歪磨斜的表面。
(4) 改用2500#沙紙打磨去除粗糙表面“孔的1/2位置”所预 设“指示线”的出现1/2位置,并伺机修平粗糙的表面。
4、 抛 光(Poish) 要看清切片的真相必须仔细抛光,以消除砂纸的刮痕。
而X定义是指“从阻剂边缘横量到最
细铜腰之宽距而言”
同一孔壁处被咬薄的放大特写镜头,其两端虽已塞有绿漆,但 可能仍留有细缝,造成蚀刻液的毛细渗入而局部咬薄的现象。
由于过度蚀铜而未将铜盐彻底去掉,以致造成化学镍层的浮 离,或进一步掏空现象
铜面前处理不良时,化学镍虽可镀上去,但当镍层之内应力太 大时,产生浮离现象
3、磨 片(Crinding) 在高速转盘上利用砂纸的切削力,将切样磨到通孔正中央
的剖面,亦即圆心所座落的平面上,以便正确观察孔壁之截 面情况。研磨時注意順著口子磨保持方向一致:
(1) 先用240#沙紙,粗磨到通孔的開口位置止.(注意研磨過程 中适量冲水,以方便减热与滑润。)
(2) 改用600#沙紙磨到“孔的1/3位置”并伺机修平改正已 磨歪磨斜的表面。
4.1.5对準情形
可由孔壁兩側的內層長短情形看出層間對準情形及鑽孔與印刷 之間的對準情形.
層間對 準良好
層間對準 不夠好
4.1.6蚀刻因子
可看到側蝕(undercut)及算出蝕刻因子,也可看到印刷或乾膜的 側壁情形.
X
所谓蚀刻因子(F)系指向下的蚀深V,
除以侧蚀X所得商值F之谓也(F=V/X)。
V
以特殊专用的钻石锯自板上任何位置取样,或用剪床剪掉 无用板材而得切样。注意后者不可太逼近孔边,以防造成通孔受 到拉扯变形。此时,最好先将大样剪下来,再用钻石锯片切出所 要的真样,以减少机械应力造成失真。(本廠是採用金相切片機 及沖片機取樣)
2、封 胶(Resin Encapsulation)
封胶之目的是为夹紧检体减少变形,系采用适宜的树脂类将通孔 灌满及将板样封牢。把要观察的孔壁与板材予以夹紧固定,使在 削磨过程中其铜层不致被拖拉延伸而失真 (封膠形式有很多種,本 廠是购买现成的压克力成型模塊,将待檢切片固定在模塊槽中灌 入冷凝胶封膠。)
微切片講儀
物理實驗室
一、概述
电路板品质的好坏、问题的发生与解决、制程改进的评估, 大都需要微切片做为客观检查、研究与判断的根据 (Microsectioning此字才是名词,一般人常说的Microsection 是动词,当成名词并不正确)。微切片做的好不好真不真,与 研判的正确与否大有关系焉。一般生产线为监视(Monitoring) 制程的变异,或出货时之品质保证,常需制作多量的切片。次 等常规作品多半是在匆忙及经验不足情况下所赶出来的,故顶 多只能看到真相的七、八成而已。甚至更多缺乏正确指导与客 观比较不足下,连一半的实情都看不到。其等含糊不清的影像 中,到底能看出什么来?这样的切片又有什么意义?若只是为 了应付公事当然不在话下。然而若确想改善品质彻底找出症结 解决问题者,则必须仔细做好切取、研磨、抛光及微蚀,甚至 摄影等功夫,才会有清晰可看的微切片画面,也才不致误导误 判。
微蚀过度以致铜面 出现氧化变暗
6、照像
原切片若為100分時,則由顯微鏡下看到的倒影,按顯微鏡的性能 只可看到85%-95%的程度,而用照相機照下來時,也只有85%-95%,照 像最難處在焦距的對準,此點困難很多.要做到對準很難,但為記錄溝 通起見,照相是最好的方法.
焦距適當
焦距不適當
四、判读
微切片可以檢驗到的項目有:
因镀铜过程中有固体 粒子附著,再被铜层所加 厚造成的瘤粒,与钻孔并 无关系.
夹杂
如圖附著物是一铜开始不久就附上,再被后续包围而成的夹杂物。须知槽液 中各种浮游固体粒子常会著落而成镀瘤(注:垂直挂镀的板子,其孔内流速 很小,愈是深孔愈糟糕)
薄膜状外来物或未除尽之原来不良皮膜会在板面铜层上被后来镀层所包围
通孔直立切片上看到的不管是原本就存在的胶渣(Smear)分离,或 是后续高温中才发生的分离,甚至互连处部份夹杂物或分离等, IPC-6012在表3-7中对Class2的板类也规定一律不能允收
过度钉头几乎一定会出现较大的挖破,出 自钻孔的纵向玻璃纱束之挖破,除与钻针 尖部的"刃角"损耗有密切关系外,也与钻针 的偏转(Run Out)或摇摆(Wobble)有关
(1).拋光時首先將拋光粉和水對調,約4-5勺拋光粉裝入0.5升的拋光瓶 內加滿水用力搖1-2分鐘,將水與粉融合.故名拋光液.
(2).將拋光絨布打湿,將抛光液倒入適當在絨布上,進行拋光 (3).拋光時要保持與孔的方向一致,這樣可以避免受力方向不同造成 的拉傷.拋光1-2分鐘,拋亮即可.
拋光良好無 刮傷的良跡
5、 微蚀(Microetch)
微蝕液的配比: 5~10 cc氨水 + 45cc纯水 + 2~3滴双氧水
将抛光面洗净擦干后即可进行微蚀,以界分出金属之各层面与其 结晶状况。用棉花棒沾着微蚀液,在切片表面轻擦约2~3秒锺,2~3秒 后立即擦干,否則銅面會變色氧化,良好的微蚀将呈现鲜红铜色.
适當微蚀
微蚀不足
4.13孔壁镀铜层破洞 (孔破)
IPC-6012对“孔壁镀铜层破洞”称之为Plating Void并指出Class 2的板
类,在每个试样切片中“只允许出现一个破洞”,且还须符合规定,即:
一、不管镀层破洞的长度或大小,每个切样上只许出现一个。 二、所出现的破洞不可大于板厚的5%。 三、孔壁与各内环交接处不可出现镀层破洞。 四、不许出现环状孔破(Circumferantial Void,俗称Ring Void).一旦出现破 洞者,还需自同批板中另外加做切片,当后者完全不再出现孔破时,上述有 "孔破"的试样才能允收。IPC-6012在此种规格中似乎不够严格,当杯状的孔 铜壁有破洞时,可能会对插焊的填锡喷气,而推开液锡造成吹孔(Blow Hole)。但此等孔破对通孔另一种功能的"互连"导通影响并不大。
由铜箔延伸出 所造成的瘤.
一銅鍍銅不均 形成的瘤
毛头若出现在非插件 孔用途的孔口,只要不断 落, 可能造成短路的危机. 但對插件孔而言,會造成 困扰.
机械刷磨消除孔口之铜层 毛头时,然会经电镀铜的 额外增时常只将毛头压入 孔中并未真正剥除。当厚, 终至形成孔口的塞孔铜瘤.
因镀铜过程中 有固体粒子附 形成的瘤
过度除胶引起的孔壁粗 糙度
轻微的撞破引起的孔壁 粗糙度及釘頭
發生孔破的原因主要有: 一、钻孔粗糙挖破玻织布,以致深陷处不易完成金属化及电镀铜层。 二、PTH前处理不良,以致局部化学铜层或直接电镀层等,无法有效建立导 电的基地,电镀铜自然也不易进入。 三、直接电镀处理不良,或事后又出现脱落,此时通孔中间常出现环状孔 破。 四、楔形孔破(Wedge Void)或称“连续点状孔破”,将另阅专文讨论。 五、镀铜孔壁原本良好,但事后又被其他制程(如锡铅层不良)所弄破甚至 咬断者,
纯钯直接电镀与 镀铜后所发现的 粉红圈与楔形孔 破(Wedge Void)
4.1.1孔銅厚度
孔銅厚度至少在0.8mil以上,微蝕良好時可清楚的看出一次銅二 次銅甚至厚化銅的層次,要注意有些制程會出現孔銅厚度差別很大 的情形,由切片上左右兩條銅壁厚度可明顯的看出.
鍍層不均
鍍層均勻
化学铜
一铜
二铜
线路电镀负片法之孔铜是由化学铜、一铜与二铜所共组成 正片法全板电镀铜系在PTH孔壁金属化之后(如化学铜或其他
200X之通孔直 立纵断面切片
100X通孔横断 面水平切片
2.微切孔的制作方法: 小心用钻石锯片将一排待檢通孔自正中央直立剖成两半,