七大浪费(高级版)
管理中的七大浪费,比生产七大浪费更重要
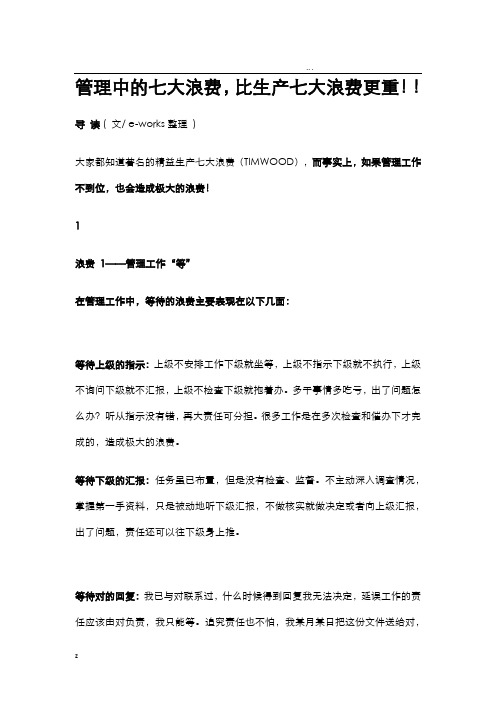
管理中的七大浪费,比生产七大浪费更重!!导读( 文/ e-works整理)大家都知道著名的精益生产七大浪费(TIMWOOD),而事实上,如果管理工作不到位,也会造成极大的浪费!1浪费1——管理工作“等”在管理工作中,等待的浪费主要表现在以下几面:等待上级的指示:上级不安排工作下级就坐等,上级不指示下级就不执行,上级不询问下级就不汇报,上级不检查下级就拖着办。
多干事情多吃亏,出了问题怎么办?听从指示没有错,再大责任可分担。
很多工作是在多次检查和催办下才完成的,造成极大的浪费。
等待下级的汇报:任务虽已布置,但是没有检查、监督。
不主动深入调查情况,掌握第一手资料,只是被动地听下级汇报,不做核实就做决定或者向上级汇报,出了问题,责任还可以往下级身上推。
等待对的回复:我已与对联系过,什么时候得到回复我无法决定,延误工作的责任应该由对负责,我只能等。
追究责任也不怕,我某月某日把这份文件送给对,这里记录得很清楚,对不回复我能怎么办?你还是和对联系一下吧,以免耽误工作。
等待生产现场的联系:职能部门不主动去为现场提供服务,而是坐等现场的联系,有时还很不耐烦,认为多等一会有什么了不起,却没有设身处地去为现场着想,重地影响了生产现场问题的及时解决。
这些“等待”在工作中是大量存在的,主要是中层管理人员缺乏责任心和主动精神,不愿意承担责任。
对于这种浪费,我们认为,根据不同企业的文化氛围,如果不能用Y理论激励员工去消除等待的浪费,就需要用X理论去加强管理,例如对于较重要的工作,可以用5W1H来进行计划分解,然后进行控制、检查和考核。
实际上,X和Y理论都不能从根本上解决问题,X+Y相辅相成也更好一些。
2浪费2——管理工作无序“没有规矩,不成圆”,这句古语说明了秩序的重要性。
缺乏明确的规章、制度、流程,工作中容易产生混乱,这是众所知的。
但如果有令不行、有章不循,按个人意愿行事造成的无序浪费,更是非常糟糕的事。
职责不清造成的无序:由于制度、管理等面的原因,造成某项工作好像两个部门都管,却纠缠不休,整天扯皮,使原来的有序反而变成无序,造成极大浪费。
生产现场的七大浪费

产生多余 的搬运, 造成布局、 作业顺序 的不合理
3、库存出现的地方和危害
案例5:
造成设备能力及 人员需求的误判
3、库存出现的地方和危害
案例6:
大量库存造 成制造周期 加长、工序 间距离大及
物料停滞
3、库存出现的地方和危害
库存会造成深层次浪费: 1)多余的仓库 2)多余的搬运 3)多余的管理、质量维护人员 4)使用多余的计算机 5)设备折旧、劳务费增加、成本增加
3、库存出现的地方和危害
案例1:
过多库存造成库房扩建与多 余资金占用,损失利息及管 理费用,物品的价值也会减
低,变成呆滞品
3、库存出现的地方和危害
案例2:
大量的变速箱壳 体造成防护(塑 料袋、黄油、托 板)与搬运费用
增加
3、库存出现的地方和危害
案例3:
大量的驱动轮 毂无法做到先
进先出
3、库存出现的地方和危害
第一步:取行车(行走3米)
第二步:将行车开到油缸存放
1
区(行走4米) 第三步:将油缸吊至分装区
转向缸暂 (行走6米)
3
存区
第四步:分装转向油缸
第五步:将转向油缸装到车架
2
行
上(行走3米) 第六步:返回原位(行走3米)
车
前车架存放区
前桥存放区
4、改善搬运浪费的着眼点
1)注意操作环节
改善后
二工序
改善后:
3、生产过剩的浪费案例
案例1:
危害:掩盖问题,不能及时发现不合格品。
3、生产过剩的浪费案例
案例2:
危害:难以判断员 工作业是否饱满、 物料转运是否及时 等问题。
3、生产过剩的浪费案例
精益生产之七大浪费

精益生产之七大浪费精益生产是一种以最小化浪费为目标,通过优化流程和提高效率来提高产品质量和客户满意度的管理方法。
在精益生产中,有七大浪费被认为是造成资源浪费和低效率的主要原因,它们是:过产、等待、运输、不合格、运动、库存和过程错误。
1. 过产(Overproduction):过产是指在没有实际需求的情况下进行生产活动,导致产品过度积压和资源浪费。
这不仅会给企业带来高成本,还会增加库存量和缩短产品寿命。
2. 等待(Waiting):等待是指生产过程中出现的不必要的停顿和延迟。
这可能是由于设备故障、物料不足、工人缺席等原因导致的。
等待会降低生产效率,增加生产周期,延迟产品交付。
3. 运输(Transportation):运输是指不必要的材料和产品的长距离运输。
这使得运输成为了一个独立的过程,需要额外的时间和资源。
这些额外的步骤可能会导致物料的损坏、遗失和延迟,进一步增加了生产成本。
4. 不合格(Defects):不合格是指生产中出现的错误、缺陷和质量问题。
不合格的产品需要进行修正、重新制造或报废,这增加了不必要的时间和资源。
这不仅会导致生产延误,还会降低产品质量和客户满意度。
5. 运动(Motion):运动是指工人在生产过程中进行不必要的移动和动作。
这可能是由于生产线布局不合理、工具和设备摆放不当等原因导致的。
这增加了工人的体力消耗,降低了生产效率,也增加了人为错误的可能性。
6. 库存(Inventory):库存是指未经加工的原材料和半成品的储存量。
过多的库存可能会导致资金占用、过期损失、储存空间浪费等问题。
此外,库存过多也会隐藏潜在的问题,如质量问题和需求变化的风险。
7. 过程错误(Processing):过程错误是指生产过程中出现的不必要的重复、增补和调整。
这可能是由于不合理的工艺流程、工具和设备的不良设计等原因导致的。
这会增加生产成本和时间,降低生产效率和产品质量。
有效管理和消除以上七大浪费是精益生产的关键。
生产过程中的七大浪费

生产过程中的七大浪费一、七种浪费之一:等候的浪费等候就是闲着没事,等着下一个动作的到临,这类浪费是无庸置疑的。
造成等候的原由往常有:作业不均衡、安排作业不妥、歇工待料、质量不良等。
以制造部性能试验课等候电控盘为例,因为电控盘不可以按要求实时入厂,有可能没法如期交货,而当电控盘入厂后,又需要抢进度,可能会出现加班、质量问题等。
还有一种就是“监督机器”的浪费,有些工厂买了一些速度快、价钱高的自动化机器,为了使其能正常运行或其余原由,比如:清除小故障、增补资料等等,往常还会此外安排人员站在旁边监督。
所以,固然是自动设施,但仍需人员在旁照料,特称之为“闲视”的浪费。
比如在产品检测过程中,调试人员和氦检人员站在产品旁边等候,这类状况能否还有?除了在直接生产过程中有等候外,其余管理工作中就没有等候这类浪费发生吗?当制造部在生产新产品发生一些问题时,技术部和质量保证部能否能立刻解决而不需要现场人员长时间等候?如何减少这类等候?二、七种浪费之二:搬运的浪费大多半人皆会认可搬运是一种无效的动作,也有人会认为搬运是一定的动作,因为没有搬运,如何做下一个动作?好多人都有这类想法。
正因为这样,大多半人默认它的存在,而不想法除去它。
有些人想到用输送带的方式来战胜,这类方式仅能称之为花大钱减少体力的耗费,但搬运自己的浪费并无除去,反而被隐蔽了起来。
搬运的浪费若分解开来,又包括搁置、聚积、挪动、整理等动作的浪费。
今年以来,生产管理部和制造部每个月均对总生产工时进行汇总剖析,发此刻实质作业时间减少的同时,总工时却在增加,经认真剖析后发现,是两个工厂间的运输工时居高不下,特别是由二工厂向一工厂搬运原资料的工时占大多半。
怎么样战胜?日本三洋大型课为减少搬运,把四个车间归并成两个,一些零零件的加工由本来在别处加工变为在生产线旁进行加工,从而减少搬运。
在不行能完整除去搬运的状况下,应从头调整生产布局,尽量减少搬运的距离。
大家能够考虑一下本公司的生产布局应当如何更改?如何最大限度地减少搬运?三、七种浪费之三:不良品的浪费产品制造过程中,任何的不良品产生,皆造成资料、机器、人工等的浪费。
七大浪费
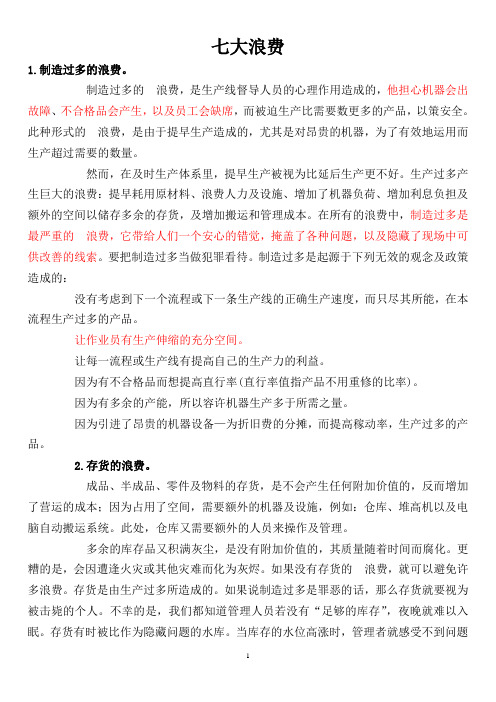
七大浪费1.制造过多的浪费。
制造过多的浪费,是生产线督导人员的心理作用造成的,他担心机器会出故障、不合格品会产生,以及员工会缺席,而被迫生产比需要数更多的产品,以策安全。
此种形式的浪费,是由于提早生产造成的,尤其是对昂贵的机器,为了有效地运用而生产超过需要的数量。
然而,在及时生产体系里,提早生产被视为比延后生产更不好。
生产过多产生巨大的浪费:提早耗用原材料、浪费人力及设施、增加了机器负荷、增加利息负担及额外的空间以储存多余的存货,及增加搬运和管理成本。
在所有的浪费中,制造过多是最严重的浪费,它带给人们一个安心的错觉,掩盖了各种问题,以及隐藏了现场中可供改善的线索。
要把制造过多当做犯罪看待。
制造过多是起源于下列无效的观念及政策造成的:没有考虑到下一个流程或下一条生产线的正确生产速度,而只尽其所能,在本流程生产过多的产品。
让作业员有生产伸缩的充分空间。
让每一流程或生产线有提高自己的生产力的利益。
因为有不合格品而想提高直行率(直行率值指产品不用重修的比率)。
因为有多余的产能,所以容许机器生产多于所需之量。
因为引进了昂贵的机器设备—为折旧费的分摊,而提高稼动率,生产过多的产品。
2.存货的浪费。
成品、半成品、零件及物料的存货,是不会产生任何附加价值的,反而增加了营运的成本;因为占用了空间,需要额外的机器及设施,例如:仓库、堆高机以及电脑自动搬运系统。
此处,仓库又需要额外的人员来操作及管理。
多余的库存品又积满灰尘,是没有附加价值的,其质量随着时间而腐化。
更糟的是,会因遭逢火灾或其他灾难而化为灰烬。
如果没有存货的浪费,就可以避免许多浪费。
存货是由生产过多所造成的。
如果说制造过多是罪恶的话,那么存货就要视为被击毙的个人。
不幸的是,我们都知道管理人员若没有“足够的库存”,夜晚就难以入眠。
存货有时被比作为隐藏问题的水库。
当库存的水位高涨时,管理者就感受不到问题的严重性,像质量的问题、机器故障、及员工缺勤,也因此而失去了改善的机会。
七大浪费——精选推荐

七⼤浪费七⼤浪费1.1 浪费的认识——是只增加成本及⼯时未增加任何附加价值的活动;——尽管是增加价值的活动,所⽤的资源超过了“绝对最少”的界限,也是浪费;1.2等待的浪费——等待就是闲着没事,等着下⼀个动作的来临。
另⼀种“监视机器”的浪费。
结果:会造成⼈员、作业、时间、机器的浪费及库存、在制品的增加。
分析:⼯序间作业不平衡、计划不周全、⼤批量⽣产、停⼯待料、品质不良、机器配置不当等、排除⼩故障、补充材料。
对策:平准化⽣产⽅式、⾃働化、防错裝置、快速換模、产品別配置。
1.3搬运的浪费——⼤多数⼈都会认为搬运是必需的动作,因为没有搬运,如何做下⼀个动作。
正因为如此,便有很多⼈默许它的存在,⽽不去设法消除它。
更有甚者,做了很长的传送带来代替这种搬运。
这种⽅式只能称为花⼤钱减少体⼒的消耗,但搬运本⾝的浪费并没有消除,反⽽被隐藏起来。
其中搬运浪费若分解开来看,⼜包含放置、堆积、移动、整理等动作的浪费。
结果:空间使⽤的浪费、⽣产⼒降低、搬运⼯时增加、搬运设备增加、不良的发⽣。
分析:⼯程别集中的⽔平式布置、Layout不合理、⼤批量⽣产、单能⼯、坐式作业、低活性度。
对策: U形线配置、流程式⽣產、多能⼯化、站⽴式作業、活性系数的改善、混载搬运。
1.4不良品的浪费——产品制造过程中,任何不良品产⽣,都会造成材料、机器、⼈⼯等,任何返修都是额外的成本⽀出。
若不良品⼀量成为报废品,更造成材料、⼈⼯等各种浪费,甚⾄增加处理报废的善后费⽤。
因此公司在推⾏精益⽣产时要强调第⼀次就把事情做好,前⼯程绝不把不良品流到后⼯程,彻底避免不良品的浪费。
结果:材料费的增加、⽣产⼒降低、检查⼈员、制程增加、不良、顾客抱怨增加。
分析:重视下游的作业、检查⽅法、检查基准不全、品质过剩、标准作业的不全。
对策:⾃働化、标准作业、防错裝置、全数检查、品保制度的健全。
1.5动作的浪费——不必要的动作,不产⽣附加价值的动作,过快或过慢的动作。
是不是要拿上、拿下如此频繁?有没有步⾏的动作、弯腰的动作、对准的动作、直⾓转弯的动作等?若⼯位设计的好,有很多动作都可被省掉。
七大浪费都是什么

七大浪费都是什么
1、等待的浪费:作业不平衡,安排作业不当、待料、品质不良等。
2、搬运的浪费:车间布置采用批量生产,依工作站为区别的集中的水平式布置所致。
(分工艺流程批量生产),无流线生产的观念。
3、不良品的浪费:工序生产无标准确认或有标准确认未对照标准作业,管理不严密、松懈所导致。
4、动作的浪费:生产场地不规划,生产模式设计不周全,生产动作不规范统一。
5、加工的浪费:制造过程中作业加工程序动作不优化,可省略、替代、重组或合并的未及时检查。
6、库存的浪费:管理者为了自身的工作方便或本区域生产量化控制一次性批量下单生产,而不结合主生产计划需求流线生产所导致局部大批量库存。
7、制造过多(早)的浪费:管理者认为制造过多与过早能够提高效率或减少产能的损失和平衡车间生力。
七大浪费

五、库存浪费
库存量越大资金积压越大,利息负担越重,仓 库管理需求增加,产品变质、失效等……浪费.
当库存的水位高涨时,管理者就感受不到 问题的严重性,像质量的问题、机器故障、 及员工缺勤,也因此而失去了改善的机会.
六、等待浪费
由于生产原料供应中断、作业不平衡和生产计 划安排不当等原因造成的无事可做的等待.
消除等待浪费
1.CELL生产方式;
3.人机工作分离; 5.切换的改善;
2.生产线平衡法;
4.全员生产性维护;
七、动作浪费
生产操作动作上的不合理导致的时间浪费,如: 生产作业时调整位置﹑翻转产品﹑取放工具物 料等不必要的动作浪费
动作经济原则的四条基本原则: 减少动作的数量 双手同时进行动作 缩短动作的距离 轻松动作
7
大浪费Байду номын сангаас
一、不良浪费
由于工厂内出现不良品,需进行处置的时间、 人力和物力的浪费,以及由此造成的相关损失。 对待不良三不政策:
Don’t accept 不接受 Don’t make 不制造 Don’t deliver 不传递
二、过量生产浪费
是由突发事件预防﹑自动化应用不当﹑制程设 定过长﹑生产计划未平准化﹑工作负荷不平 衡﹑多余检验等造成的制造过多于下一制程需 求的浪费.
劳模
三、加工浪费
也叫过分加工的浪费, 多余的加工和过分精确的 加工,造成资源的浪费. 四大类型:
品质过剩 检查过剩 加工过剩 设计过剩
四、搬运浪费
是一项无生产附加价值的工作,包含移动、堆 积、整列、放置等……浪费. 改善方法:
合理化布局 合理化搬运工具 合理化搬运方法
- 1、下载文档前请自行甄别文档内容的完整性,平台不提供额外的编辑、内容补充、找答案等附加服务。
- 2、"仅部分预览"的文档,不可在线预览部分如存在完整性等问题,可反馈申请退款(可完整预览的文档不适用该条件!)。
- 3、如文档侵犯您的权益,请联系客服反馈,我们会尽快为您处理(人工客服工作时间:9:00-18:30)。
D:不良品浪费
生产过程中,因来料或制程不良,造成的各种损失,需进行处置的时间﹑人力和物 力的浪费。 不良品浪费的影响: 一方面是内部损失,任何的不良品产生,都会造成原材料、辅助材料、机器、 人工等的浪费,额外的修复、挑选、追加检查人员等都是额外的成本支出 ;
另一方面是外部损失,由于产品不良导致降 价处理、订单取消和市场信誉损失等。
寻找工具/材料 过度的伸展/弯腰
左右120度
W:等待浪费
指等待人、材料、设备、信息等,即非满负荷的浪费。
等待分为两部分: 一、来自管理的等待 等待上级的指示 等待下级的汇报 等待对方的回复 等待生产现场的联系
二、来自生产现场的等待 生产线转线要等待 缺料要等待 生产线不平衡要等待 生产通知单或设计图纸未送
过量生产浪费指的是先于下一个工序或客户实际需求而生产的产品。
过量生产危害:
设备及用电、气、油等能源的增加; 放置地、仓库空间增加; 多余的作业时间、管理工时; 搬运的增加; 增加不良品的风险。
O:过量生产的浪费
过量生产浪费产生消除方法:
准确掌握不良率; 制订宽放标准和计划校正机制; 缩短制造周期; 生产线平衡分析; 制定单次传送量标准; 一个流作业; 严格按客户需求生产; 使生产设计流速=客户需求节拍时间;
D:不良品浪费
不良品浪费改善方法: 1、从稳定的人员追求稳定的质量,然后再逐步加以改善 2、对人员进行良好的企业训练; 3、注重工作绩效,透过统计技术来管制; 4、将作业规范和程序文件化、标准化; 5、消除环境(工作场所)的脏乱现象,开展6S 活动; 6、对机器设备开展预防性维修保养; 7、与供货商建立良好的稳定的合作,保证来料的质量; 8、对发现的不良品及时处置并预防再次发生,持续进行质量改进; 9、有改善活动,真正消除不良品。
O:过度加工浪费
指内、外部客户需求以外的多余操作、处理,包括品质过剩、检查过剩、加工过剩等;
• 没完没了的修饰 • 外加设备 • 较长的制造周期 • 生产效力降低 • 频繁的分类,测试,检验 • 额外的复印件/过多的信息 • 能源过度消耗 • 额外的加工工序
O:过度加工浪费
消除过度加工的思考 • 能否去除次零件的全部或部分 • 能否把公差放宽; • 能否改用通用件或标准件; • 能否改善材料的回收率; • 能否改变生产方法; • 能否把检验省略掉; • 供应商是否适当; • 是否确实了解客户的需求。
到要等待 机器发生故障要等待 作业不平衡要等待
W:等待浪费
过多的等待会产生以下不良后果:
各项工作不能正常开展,管理难度加大; 生产任务不能按时完成; 不能保证产品的发货需求; 设备利用率低; 劳动生产率降低; 制造成本增加; 生产现场管理混乱,容易导致质量事故的发生
O:过量生产的浪费
THANKS
*********
认识七大浪费分类
数
量
动作
过度加工
库存
的Hale Waihona Puke 等待七种人
类型
缺陷
员
的
生产过剩
搬运
质
量
的
T:搬运浪费
- 找到、拿起、移动、用手放 - 从手推车移到货板 - 从货仓到工厂 - 从工厂到生产线 - 从生产线到车间 - 从车间到操作工位
搬运浪费指流程中因两点距离远而造成的搬运、走动等浪费,包括人的浪费和机器的 浪费。搬运本身是一种无附加价值的动作,若分解开来又分为:放置、堆积、移动、整列 等动作浪费。
Seven waste training courses
*****
在竞争激烈的环境中,我们要比别人获得更多的效益,才能够顺利地 生存下去。我们不能有丝毫的浪费。上面简单地介绍了七种浪费的概念并 结合本公司的实际情况进行了进一步的说明,但所提出的问题仅是冰山露 出海面的部分,大量的问题隐藏在水面之下,而且生产现场中的问题由于 目视可见,解决起来相对容易一些,而管理部门存在的问题则隐藏较深, 解决起来较困难,但如果解决了,则见效大。希望避免重复出现生产一线 轰轰烈烈,而管理部门春风拂面的局面,真正从思想上认清“浪费”带来 的危害,从而真正在行动上去消除“浪费”,降低成本,提高效率,增加 效益。
磕碰,变形 难以实现先进先出
变更成本
产品换型、 市场价格变化
M:动作浪费
生产操作动作上的不合理导致的时间浪费,任何对生产(服务)不增值的人员/机器 的动作。
单手、两手空闲的浪费 步行的浪费
转身角度太大的浪费 伸背、弯腰动作的浪费
不了解作业技巧,动作配合不好
上下60度
作业动作停顿的浪费
T:搬运浪费
搬运浪费的表现
过度搬运
仓储质量降低
过多的搬运设备 过度能源消耗
大面积储存区 损坏或丢失物品
过量配送人员
I:过度库存的浪费
库存指除单件流动产品以外所有的物料、半成品、成品。 过度库存给企业带来的成本:
资金成本
资金积压 设备投入 场地占用
管理成本
搬运量、场地、 防护、管理
质量成本