湿法电解锌工艺设计设计流程选择概述
年产7万吨锌锭的湿法炼锌浸出车间的设计讲解

第三章锌电积工艺过程及设备计算3.1概述工业上从硫酸锌水溶液中电解沉积锌有三种工艺:即低酸低电流密度法(标准法);中酸中电流密度法(中间法)和高酸高电流密度法。
目前我国多采用中酸中电流密度法的下限,低酸低电流密度法上限的电解法。
表3-1为三种方法的比较。
表3-1 锌电积三种工艺的比较工艺方法电解液含H2SO4(克/升)电流密度(安/米2)优缺点酸低电流密度法(标准法)110--130 300--500 耗电少,生产能力小,基建投资大中酸中电流密度法(中间法) 130--160 500--300生产操作比前者简单,生产能力比前者大但比后者小基建投资小高酸高电流密度法220--300 800~1000 甚至大于1000生产能力大;耗电多;电解槽结构复杂。
3.2 设计任务设计生产能力为7万吨锌锭的电解设备3.3 原始资料3.3.1 设进入电解槽的电解液成份如表3-2所示:表3-2 进入电解槽的电解液成份(克/升)组成 Zn Fe Cd Cu CO Mn (克/升) 120 0.045 0.005 0.0004 0.005 4.7203.3.2 电解后电解废液成份如表3-3所示表3-3 电解废液成份(克/升)组成 Zn Fe Cd Cu CO Mn (克/升) 46 0.028 0.003 0.0002 0.005 3.2173.3.3 一些技术条件及技术经济指标用于制造锌粉之锌锭占年产锌锭量的百分比,β=0.028;年工作日为330日。
阴极锌熔铸直收率 η 1 = 97% 阴极电流密度 D 阴 = 520安培 槽电压 V 槽 = 3.20伏 电流效率 ηi = 98%阴极规格 长×宽×厚= 1000×666×4(毫米)3.4 工艺过程及设备计算3.4.1物料平衡及电解槽计算 阴极锌成份的计算在电积过程中,一部分铜、铁、镉与锌一齐在阴极上沉积,一升电解液得到的阴极锌含金属量如表3-4所示。
湿法冶锌工艺流程

湿法冶锌工艺流程
1.浸出:将含锌矿石(多为氧化锌矿石)研磨成一定粒度的粉末,然后与硫酸等溶液混合,通过浸出反应将锌溶解出来。
浸出反应一般可以分为两个步骤:首先是矿石的颗粒与溶液之间的扩散过程,然后是锌离子在溶液中的化学反应。
2.过滤:将浸出溶液中的固体杂质物通过过滤器进行过滤,得到含锌的滤液。
过滤是一个重要的步骤,它可以有效地去除溶液中的固体杂质,防止后续工艺发生堵塞和设备磨损。
3.净化:通过净化工艺,将滤液中的铁、铜、镉等杂质去除,以获得纯度更高的锌溶液。
常用的净化方法有镉精萃取法、铜脱除法、硫酸铁脱除法等。
4.电积:将经过净化的锌溶液通过电解槽进行电积操作,使锌离子在阳极上还原成金属锌,在阴极上沉积。
电积是将溶液中的锌还原成金属锌的最主要方法,通常使用铅和钢板作为阴极,将锌电积出来。
5.脱水:将电积出来的锌板通过烘干设备进行脱水处理,去除残留的水分,使锌板干燥。
6.熔炼:将脱水后的锌板送入熔炼炉中进行熔炼操作,将锌板熔化成液态锌。
通常采用间歇式熔炼,将锌板在炉中加热至熔点以上,使锌融化成液态,然后通过出铅孔排出熔化后的锌液。
7.精炼:通过精炼设备,对锌液进行精炼操作,以提高锌的纯度。
精炼一般采用电解精炼法,通过电解槽将锌液中的杂质去除,得到高纯度的锌。
8.出锌:将精炼后的锌液通过真空蒸馏或其他方法,将铅和其他低沸点杂质从锌液中蒸馏除去,最终得到纯度达到要求的锌。
总的来说,湿法冶锌工艺流程是一个包括浸出、过滤、净化、电积、脱水、熔炼、精炼和出锌等多个步骤的过程。
通过这些步骤的处理,可以从含锌矿石中提取出纯度较高的锌,用于各种工业应用。
湿法炼锌净化工艺的选择

湿法炼锌净化工艺的选择广西来宾冶炼厂锌冶炼系统年产电锌3万t,为传统的湿法工艺流程,即:锌精矿-沸腾焙烧-焙砂硫酸浸出*浸出液净化—净化液电积—电锌。
2002 年3月开始技术改造扩建工程,使得电锌产量达到了年产6万t,在技术改造过程中,最关键的净化工艺拟采用三段连续净化取代改造前的两段间断净化。
因此,该工艺在生产中无论在设备上装置上还是在工艺操作中都引入了许多先进高效和适用的技术,有利于降低劳动强度、提高产率并实现生产过程的自动化控制。
1净化过程基本原理1.1净化方法净化过程是根据硫酸锌浸出液中不同的杂质及其含量,大多采用锌粉置换和加特殊试剂化学沉淀的方法将溶液中杂质除去。
工厂根据锌焙砂中性浸出上清液的特点,选择釆用加锌粉置换的逆歸净化方法。
1.2置换原理置换是一种氧化还原反应,置换的热力学过程可用金属活泼性的大小或电子得失的难易等来定性描述,中性浸出上清液锌粉置换反应为:MeSO4 + Zn = Z11SO4 + Me I置换过程中金属的平衡电位如表1所示。
表1置换过程中金属的平衡电位(298 K) V电极反应E°E平衡Zn2* +2e=Zn■0.763-0.752(150 g/L)Cd2* +2e=Cd-0.403-0.752(2xl0-7mg/L)Cu2+ +2e= Cu+ 0.337-0.752(3.18x 10-35 mg/L)Co2+ +2e=Co-0.227-0.752(5 x IQ-12 mg/L)Ni2+ +2e=Ni-0.250-0.752( 1.5x 10-17 mg/L)SbH3 = Sb+3H+ +3e+ 0.510+ 0.752(pH = 4, Pgb% = 202.65 Pa)A S H3 = As+ 3H*+3e+ 0.600+0.752(P H=4,P A1H3 = 202.65 Pa)置换的动力学过程的反应机理:加入的锌粉作为微电池的阳极溶入液相,在那里发生水化作用,继而向溶液深处扩散并参与溶液的对流运动。
锌的湿法冶金方法概述

锌的湿法冶金
锌的湿法冶金是指使用水溶液作为冶炼锌的介质,其主要包括电解法、酸浸法和氨浸法等几种方法。
1.电解法:将锌精矿放入电解槽中,加入电解液(主要成分为硫酸和氯化铵),在外加
电流的作用下,锌离子被还原成金属锌沉积在阴极上。
这种方法具有效率高、能耗低等优点,是目前最主要的生产方式。
2.酸浸法:将锌精矿浸入硫酸水溶液中,利用硫酸的氧化作用将锌离子溶解出来。
这
种方法适用于高品位的锌矿石,但浸出过程中会产生大量的酸性废水,对环境造成污染。
3.氨浸法:将锌精矿浸入氨水溶液中,通过氨水的配位作用将锌离子溶解出来。
这种
方法对锌矿石的品位要求较低,同时产生的废水为碱性废水,对环境污染较小。
但该方法的操作成本较高。
以上三种方法各有优缺点,应根据不同情况选择合适的冶炼方式。
除了上述的电解法、酸浸法和氨浸法外,还有其他一些较为次要的湿法冶金方法。
4.氯化法:将锌精矿与氯气反应,生成氯化锌,再通过还原反应得到金属锌。
这种方
法主要应用于高品位的锌矿石,但因为氯气对环境的危害性较大,所以逐渐被淘汰。
5.氧化焙烧法:将锌精矿加入到反应炉中,通过高温氧化反应,将锌矿石中的锌转化
为氧化锌,再通过还原反应得到金属锌。
这种方法主要适用于低品位的锌矿石,但因为会产生大量的氧化废气,对环境造成了污染。
总的来说,湿法冶金方法相对于干法冶金方法来说,工艺流程更为复杂,但其适用范围更广,能够处理更多种不同品位的锌矿石,且可以生产出较为高纯度的金属锌。
但湿法冶金方法中会产生大量的废水和废气,需要进行处理和净化,以减少对环境的影响。
湿法冶锌中性浸出电解沉积

湿法冶锌中性浸出电解沉积
引言:
一、原理:
二、工艺流程:
1.锌原料浸出:将锌原料浸入稀硫酸溶液中,通过加热和搅拌等方式将锌溶解成溶液中的锌离子。
2.电解沉积:用浸出溶液作为电解液,将阴极和阳极分别放入电解槽中,施加电流使锌离子在阴极上沉积成金属锌。
3.锌的回收:将电解沉积得到的金属锌进行收集和处理,以得到高纯度的锌产品。
三、设备:
1.浸出槽:用于将锌原料和浸出溶液进行反应和搅拌。
2.电解槽:用于进行电解沉积反应,其中放置有阴极和阳极。
3.电源:用于提供所需的电流,使锌离子在阴极上沉积成金属锌。
4.收集系统:用于收集和处理电解沉积得到的金属锌。
四、应用:
1.锌冶炼:通过湿法冶锌中性浸出电解沉积方法可以提取和生产金属锌,用于制备锌合金和锌制品。
2.锌回收:湿法冶锌中性浸出电解沉积可以将废弃物和废旧锌制品中的锌回收利用,减少资源浪费和环境污染。
结论:
湿法冶锌中性浸出电解沉积是一种有效的锌冶炼方法,通过该方法可以实现锌的提取和回收。
该方法的原理基于电解的原理,工艺流程包括锌原料浸出、电解沉积和锌的回收等步骤,并需要相应的设备支持。
该方法在锌冶炼和锌回收领域有广泛的应用。
电解锌工艺流程
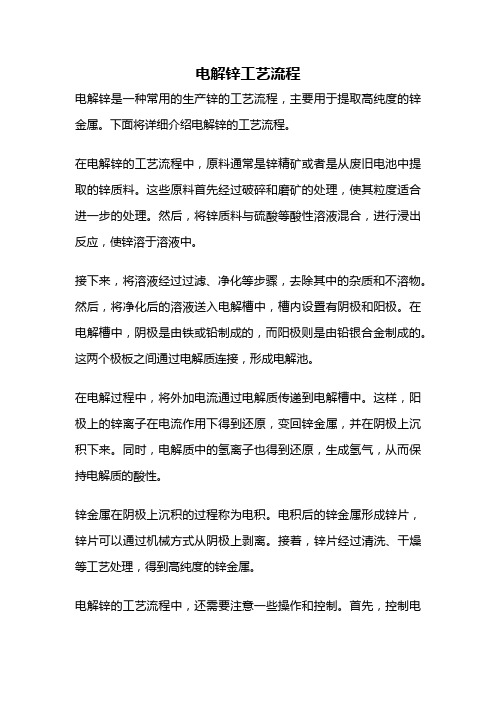
电解锌工艺流程电解锌是一种常用的生产锌的工艺流程,主要用于提取高纯度的锌金属。
下面将详细介绍电解锌的工艺流程。
在电解锌的工艺流程中,原料通常是锌精矿或者是从废旧电池中提取的锌质料。
这些原料首先经过破碎和磨矿的处理,使其粒度适合进一步的处理。
然后,将锌质料与硫酸等酸性溶液混合,进行浸出反应,使锌溶于溶液中。
接下来,将溶液经过过滤、净化等步骤,去除其中的杂质和不溶物。
然后,将净化后的溶液送入电解槽中,槽内设置有阴极和阳极。
在电解槽中,阴极是由铁或铅制成的,而阳极则是由铅银合金制成的。
这两个极板之间通过电解质连接,形成电解池。
在电解过程中,将外加电流通过电解质传递到电解槽中。
这样,阳极上的锌离子在电流作用下得到还原,变回锌金属,并在阴极上沉积下来。
同时,电解质中的氢离子也得到还原,生成氢气,从而保持电解质的酸性。
锌金属在阴极上沉积的过程称为电积。
电积后的锌金属形成锌片,锌片可以通过机械方式从阴极上剥离。
接着,锌片经过清洗、干燥等工艺处理,得到高纯度的锌金属。
电解锌的工艺流程中,还需要注意一些操作和控制。
首先,控制电流密度和温度是非常重要的,这会影响电积速率和锌金属的质量。
此外,还需要定期检查电解槽的电解质浓度和纯度,以及阴极和阳极的状况,及时进行维护和更换。
总结一下,电解锌是一种常用的生产锌金属的工艺流程。
通过将锌质料溶解在酸性溶液中,然后经过净化和电解的过程,得到高纯度的锌金属。
在整个工艺流程中,需要注意操作和控制,以确保产品质量和生产效率。
电解锌工艺流程的应用,为锌金属的生产提供了一种有效的方法。
小型炼锌厂采用湿法炼锌工艺流程的选择和优化
121 仪 器设 备 __
锌技术不仅难度大而且还会造成严重的环境污染。 所以我国的炼锌厂多采用湿法炼锌技术 , 但湿法炼 锌 的前 期 投入 量 大 , 不适 于小 型 炼 锌 厂 , 以本 文 所 对其工 艺进行 了如 下摸索 性试 验 。
1 试 验
122 电极过程 所控 电积 参数 ..
电积 温 度 控 制 在 4  ̄ 0C,电 积过 程 中加 入 牛胶
2 m / 加 人碳 酸锶 01/ 0 gL, . L以及 少 :称 取含 锌 矿 粉 3g放在 0
2 0 l 杯 中 ,加 入 2 o L硫 酸 1 0 10 5m 烧 ml \ 5 ~ 8 mL在不
于稀 硫酸 , 故要 用 稀硫 酸 除去 硫酸 铅 ) 同时用 该 矿 , 粉 调 节 p 4 趁 热 减 压 过 滤 , 液 至 于 2 0 L烧 H= , 滤 5m
杯中。
2 )氧 化除 F 、 n 杂 质 :将上 面滤 液加 热至 e M 8 ~ 0C ,滴加 0 m l Mn 0 9  ̄后 . o LK O 至微 红 时 停止 加 5 \ 入 , 续加 热 至无 色 , 制溶 液 p 4 趁 热减 压 过 继 控 H ,
深 :.m 4 3  ̄ m。 5
仪器 : 杯 , 氏漏 斗 , 滤瓶 , 烧 布 抽 滤纸 。
试剂 : 含锌 矿 粉 ( 主要 成分 为 氧化 锌 )纯 锌 粉 , , 0 mo L K o 溶液 ,mo L硫 酸 3 o\。 . l Mn4 5 / 2 l \ ml L
11 .. 制备 方法 2
11 硫酸锌 的 制备 .
11 1 仪 器 和 试 剂 ..
可控 硅 整 流 器 : G F44 0 输 出 电压 2 V, K C 2/00 f 4 输 出 电 流 4 0A ,电解 槽 长× × = .m 08mx 00 1 宽 深 1 x .8 1 1 6 厚度 5 . m, 0 mm, 四槽 ( 际用 一 槽 )阳极 铅 板 共 实 , 尺 寸 :0 m 60 m,厚 度 5 m 阴极 为纯 铝 板 尺 90 mx 8 m m 寸 :0 m x 0 m 80 m 70 m厚 度 4 m,废 电解液储 槽 直径X m
湿法冶锌工艺设计流程
湿法冶锌工艺设计流程1.原料准备:首先需要准备好锌原料。
常用的锌原料有锌精矿、湿法炼锌渣等。
这些原料需要进行粉碎和磨细处理,以便提高后续工艺步骤的操作性能。
2.浸出处理:将经过处理的锌原料与硫酸等酸性溶液进行反应,使锌离子溶于溶液中。
该步骤需要注意配料比例、温度、搅拌速度等参数的控制,以提高浸出效果。
3.溶液净化:将浸出得到的含锌溶液进行净化处理,以去除杂质和次产物。
常用的净化方法有沉淀法、溶解法、离子交换法等。
这些方法可以去除掉溶液中的铁、铅、铜、镉等杂质,使溶液达到一定的纯度。
4.浓缩处理:经过净化的含锌溶液常常需要进行浓缩处理。
这一步骤可以利用蒸发、结晶、吹膜等方法,将溶液中的水分去除,使得溶液的锌含量提高。
5.电解精炼:经过浓缩处理后的含锌溶液需要进行电解精炼,以进一步提高锌的纯度。
该步骤通常采用电解槽,将含锌溶液作为电解液,通过外加电流的方式,使锌离子在阴极上得到析出,形成高纯度的金属锌。
6.锌产品处理:在电解精炼后,得到的金属锌通常需要进一步加工成为使用价值更高的锌产品。
常见的处理方法有冶炼成锌锭、制备锌合金、生产锌粉等。
这些产品可以根据市场需求,进一步加工利用或销售。
7.尾矿处理:工艺过程中会产生一些含有有害物质的尾矿。
这些尾矿需要经过环境友好的处理方式,以减少对环境的影响。
常见的尾矿处理方法有浸出、固化、中和、填埋等。
需要注意的是,湿法冶锌工艺设计流程中的每个步骤都需要进行实验和试验,以确定适合具体工艺要求的操作条件和参数。
同时,在设计过程中需要充分考虑工艺效率、能源消耗、环境保护等方面的综合因素,以确保设计出安全、高效、环保的湿法冶锌工艺流程。
湿法炼锌原理和工业流程
湿法炼锌原理和工业流程好的呀,那咱们就开始聊聊湿法炼锌的原理和工业流程吧。
一、湿法炼锌原理。
1. 锌的存在形式。
咱得知道,在自然界中呢,锌大多是以硫化物的形式存在的,像闪锌矿(ZnS)就很常见。
那要把锌从这些矿石里弄出来,就得利用一些化学的魔法啦。
2. 主要化学反应。
这里面有个很关键的反应呢,就是把硫化锌先变成氧化锌。
怎么变呢?一般是通过焙烧这个过程。
硫化锌和氧气一反应,就变成了氧化锌和二氧化硫啦,方程式是2ZnS + 3O₂ = 2ZnO+ 2SO₂。
这个二氧化硫可不能浪费呀,它还能用来制硫酸呢。
然后呢,氧化锌就开始和硫酸反应,这就是湿法炼锌里特别重要的一步。
反应式是ZnO + H₂SO₄ = ZnSO₄ + H₂O。
这样就把锌变成了硫酸锌溶液啦,这个溶液里就包含了我们想要的锌元素哦。
接下来,就要把锌从硫酸锌溶液里提取出来。
这时候就轮到电积上场啦。
在电积槽里,硫酸锌溶液做电解液,用铅板做阳极,铝板做阴极。
通电之后呢,溶液里的锌离子就会跑到阴极上去,在阴极上得到电子变成锌单质。
反应式就是Zn²⁺ + 2e⁻= Zn。
这就像是锌离子排着队,一个一个地到阴极这个“新家”去变成锌金属啦。
二、湿法炼锌工业流程。
1. 矿石预处理。
在开始炼锌之前,矿石得先处理一下。
这就像我们做菜之前要洗菜切菜一样。
首先得把矿石破碎和磨细,这样能让后面的反应更充分。
要是矿石都是大块大块的,里面的锌怎么能好好地和其他物质反应呢?把矿石磨得细细的,就像是给锌打开了一扇大门,让它能更好地参与到后面的化学过程中去。
2. 焙烧。
磨细后的矿石就进入焙烧环节啦。
这个过程就像是给矿石来一场热烘烘的派对。
在焙烧炉里,矿石和空气热烈地接触,发生前面说的硫化锌变成氧化锌的反应。
这个过程可得控制好温度哦,温度不合适的话,反应就可能不彻底,或者会产生一些我们不想要的杂质。
就像烤蛋糕一样,温度和时间都得恰到好处,不然蛋糕就不好吃啦。
3. 浸出。
湿法锌工艺流程
湿法锌工艺流程
湿法锌工艺流程
湿法锌工艺是一种将锌从锌矿石中分离出来的方法,主要通过化学反应来实现。
下面是湿法锌工艺的一般流程:
1. 破碎与磨矿:先将锌矿石进行破碎,使其颗粒大小合适,然后进行磨矿,即用磨矿设备对矿石进行细磨。
这一步的目的是将矿石颗粒破碎并提高浸出效果。
2. 酸溶浸出:将磨矿后的锌矿与稀硫酸进行混合,然后加热反应。
这个步骤的主要目的是将锌矿石中的锌溶解出来,形成硫酸锌溶液。
3. 澄清过滤:将溶液经过澄清处理,去除其中的杂质和固体颗粒。
这一步的目的是提高后续步骤的反应效果。
4. 电积杂质去除:通过将硫酸锌溶液进行电解,使溶液中的其他金属离子在阳极处析出,从而去除杂质。
这一步的目的是提高锌的纯度。
5. 电积锌:将经过除杂的硫酸锌溶液电解,使锌在阴极处析出。
这样就可以将锌从溶液中沉积出来,得到纯净的锌产品。
6. 锌收集与干燥:将电积出来的锌收集起来,并加以干燥处理。
这一步的目的是得到锌的成品。
7. 浸出液处理:将溶液中的杂质进行处理,使其变为无害物质。
这样可以减少环境污染。
总的来说,湿法锌工艺是一种通过溶解、电解和沉积等步骤将锌从锌矿石中分离的方法。
经过多个步骤的反应、过滤和处理,最终可以得到纯净的锌产品。
这种工艺具有高效、环保的优点,被广泛应用于各种锌矿石的处理中。
但是,由于涉及到一系列的化学反应和设备操作,工艺过程中还需要严格控制各参数和操作条件,以确保工艺的稳定性和产品质量。
- 1、下载文档前请自行甄别文档内容的完整性,平台不提供额外的编辑、内容补充、找答案等附加服务。
- 2、"仅部分预览"的文档,不可在线预览部分如存在完整性等问题,可反馈申请退款(可完整预览的文档不适用该条件!)。
- 3、如文档侵犯您的权益,请联系客服反馈,我们会尽快为您处理(人工客服工作时间:9:00-18:30)。
湿法电解锌工艺流程选择概述1.。
1 工艺流程选择根据原料成份采用常规的工艺流程,技术成熟可靠,劳动环境好,有较好的经济效益,同时综合回收铜、镉、钴等伴生有价金属。
工艺流程特点如下:(1)挥发窑产出的氧化锌烟尘一般含气氟、氯、砷、锑杂质,且含有较高的有机物,影响湿法炼锌工艺,所以通常氧化锌烟尘需先进多膛焙烧脱除以上杂质。
(2)氧化锌烟尘和焙砂需分别进行浸出,浸出渣采用回转窑挥发处理,所产氧化锌烟尘送多膛焙烧炉处理。
(3)氧化锌烟尘浸出液返焙砂系统,经中性浸出浓密后,上清液送净液车间处理,净液采用三段净化工艺流程。
(4)净化后液送往电解车间进行电解。
产出阴极锌片经熔铸后得锌锭成品。
(5)净液产出的铜镉渣和钴渣进行综合回收(或外卖)。
1.6.2 工艺流程简述焙砂经中浸、酸浸两段浸出、浓密、过滤,得到中浸上清液及酸浸渣。
酸浸渣视含银品位进行银的回收后送回转窑挥发处理得氧化锌,经脱氟、氯,然后进行单独浸出,浸液与焙砂系统的浸出液混合后送净液。
回转窑渣送渣场堆存。
产出的中浸上清液经三段净化,即第一段用锌粉除铜镉;第二段用锌粉和锑盐高温除钴;第三段再用锌粉除复溶的镉,以保证新液的质量,所得新液送电解。
电解采用传统的电解沉积工艺,用人工剥离锌片,剥下的锌片送熔铸,产出锌锭。
采用上述工艺流程的理由:主要是该工艺流程基建投资省,易于上马,建设周期短、见效快、效益高。
这在株冶后10万吨电锌扩建、广西、、等多家企业的实践中,已得到充分证实和肯定。
对净液工艺的选择,目前国外湿法炼锌净液流程的发展趋势,主要是溶液深度净化。
采用先冷后热的净液流程,为保证净液质量,设置三段净化,当第二段净化质量合格时,也可以不进行第三段净化,直接送电解。
该流程稳妥可靠,净化质量高,能满足生产0#锌和1#锌的新液质量要求。
作业制度,拟采用连续操作,国西北冶、株冶等都有生产经验。
与间断操作相比,可大减少设备的容积,减少设备数量,相应可减少厂房建筑面积,故可大幅度降低基建投资。
1..3 综合利用及环境保护浸出渣可根据含银品位高低进行银的回收后再送回转窑处理,所得氧化锌经脱氟、氯后进入氧化锌浸出系统,进一步回收锌、铟等有价金属。
净液所得铜镉渣经低酸浸出后,所得铜渣可作为炼铜原料出售。
浸出液经锌粉置换,所得贫镉液含锌很高,返回锌浸出车间,所得海绵镉进一步处理后,获得最终产品镉锭出售。
净液所得钴渣,经酸洗脱锌后根据含钴品位再考虑是否回收钴,暂时先堆存(或外卖)。
熔铸所得浮渣,其粗粒可返回熔化或作生产锌粉用。
处理所得氧化锌可作为生产硫酸锌或氯化锌的原料,根据需求而定。
各湿法炼锌车间的污酸、污水,经中和沉处理后,可达到国家工业排放标准。
为合理使用电能,本设计根据国外电解工厂的经验,电流密度采用白天低(400A/ m2)夜间高(500A/ m2)的操作制度;根据比利时老山锌公司、日本的彦岛、饭岛、小鸣浜和安中等国外诸多10万吨/年以上电锌厂电解车间采用自然通风、局部强制通风和两班制剥锌的生产经验,本设计采用车间自然通风,所有可能产生酸雾的溜槽和贮槽均加盖并予以强制抽风,剥锌厂房局部强制通风,将酸雾对车间造成的污染降至最低水平。
综上所述,本设计不仅充分考虑了"三废"的有效治理,改善了环保条件,而且使之得到综合利用,提高了有价金属的回收率;2冶炼工艺设计采用成熟的工艺流程,技术落实可靠,劳动环境好,又有较好的经济效益,同时可综合回收铜、镉、钴等伴生有价金属。
焙砂送球磨后,分别经中浸、酸浸两段浸出、浓密、过滤,得到中浸上清夜及酸浸渣。
酸浸渣送回转窑挥发处理的氧化锌,经多膛焙烧炉脱氟、氯后进行单独浸出处理,中浸液返至浸出系统的中性浸出,氧化锌酸浸液用锌粉置换产出铟渣,留待进一步处理。
酸浸渣送渣场堆存,待回收Pb、Zn等有价金属。
浸出系统产出的中浸上清夜经三段净化,即第一段用锌粉除铜、镉,第二段用锌粉、锑盐除钴、镍,第三段用锌粉除残镉,所得净化后液即新液送往电解。
电解采用传统的电解沉积工艺,采用人工剥离锌片,剥下的锌片送熔铸,采用低频感应电炉熔锌,最终产出1#锌和部分0#锌的锌锭。
本设计金属回收率:锌93.5% 其中:浸出95%;净液99.3%;电解99.5%;熔铸99.7%2.2 浸出2.2.1 工艺流程简述2.2.1.1 备料焙砂用刮板运输机送到浸出厂房的料仓,由料仓锥底排出经星形给料器、称量给料机再进入中性浸出槽上的螺旋给料机,将焙砂送入浸出槽。
从电解车间来的废电解液、阳极泥浆分别泵入废电解液贮槽和阳极泥搅拌槽。
净液工段来的各种含锌溶液和过滤干燥厂房来的过滤液及洗液均泵入混合液贮槽。
凝聚剂溶液的制备:在凝聚剂溶解槽中加入水并通蒸汽,控制温度40~60℃,逐渐加入凝聚剂,配制成1%的浓度,使用时用水稀释到0.1%浓度,存放在凝聚剂贮槽中,用泵送入各浓密机。
2.2.1.2 中性浸出中性浸出选用4台φ4500×5500机械搅拌槽,单槽反应间断作业。
将废电解液、阳极泥浆、混合液、MnO2矿粉分别给入中性浸出槽配液,控制始酸H2SO450~80g/l,Fe2+≤0.1g/l,然后加入焙砂,在加料时不断的用试纸测定槽的酸度,保证中性浸出终点PH=5~5.2。
中性浸出矿浆由槽下部排出流入溜槽后进到中间槽,经泵打入1台φ18m中性浸出浓密机,其浓密溢流即为中浸上清夜,直接经溜槽流入中上清贮槽。
浓密机底流经泵送至酸性浸出槽。
2.2.1.3 酸性浸出酸性浸出槽与中性浸出槽规格相同,选用3台间断作业。
中浸底流泵入酸浸槽后,加入废电解液和浓硫酸,并通入蒸汽加热至75~85℃,控制浸出终点PH=2~3。
酸性浸出矿浆由槽下部排出经溜槽和泵槽打入1台φ15m酸性浸出浓密机,其浓密底流经中间槽泵送到渣过滤干燥工段,选用3台F=100m2带隔膜的压滤机压滤,所得滤渣经皮带运输机送到火法的给料系统,给入干燥窑。
其浓密溢流返回中性浸出。
2.2.1.4 氧化锌中性浸出氧化锌中性浸出选用1台φ4500×5500机械搅拌槽,间断作业。
浸出渣在火法车间经干燥、挥发产出氧化锌,经多膛焙烧炉脱硫、氯后,通过圆盘给料机送入1台湿式溢流球磨机,该球磨机规格为φ1200×2400,磨矿液来自渣滤干燥工段的压滤液和洗液,与氧化锌一同进入球磨机,磨矿的氧化锌矿浆经中间贮槽泵送到浸出车间的氧化锌中性浸出槽,同时加入废电解液,控制浸出终点酸度PH=4.8~5.2。
浸出后矿浆泵送至1台φ15m氧化锌中浸浓密机进行液固分离,浓密溢流经槽泵送至混合液贮槽,浓密机底流泵送入氧化锌酸性浸出槽。
2.2.1.5 氧化锌酸性浸出氧化锌酸性浸出选用1台φ4500×5500机械搅拌槽,间断作业。
氧化锌中浸底流、废电解液和浓硫酸同时加入槽中,浸出始酸H2SO4150~200g/l,控制浸出终酸20g/l左右,然后泵入1台φ15m氧化锌酸浸浓密机进行液固分离,浓密溢流经中间槽泵送至铟富(置换)槽用锌粉置换后再经压滤机压滤,所得滤渣即铟渣,待进一步处理得精铟。
滤液返回氧化锌中浸槽。
浓密机底流泵至1台F=100m2压滤机压滤,所得滤液返回氧化锌中性浸出槽,所得的滤渣经浆化用1台F=100m带隔膜的压滤机压滤洗涤后由气动排渣料斗卸入渣车,运送渣场。
2.2.2 主要技术操作条件2.2.2.1 中性浸出浸出液固比10:1浸出温度65~75℃浸出时间1~2h浸出终点酸度PH=5~5.22.2.2.2 酸性浸出浸出液固比10:1浸出温度75~85℃浸出时间2~4h浸出终点酸度PH=2~32.2.2.3 氧化锌中性浸出浸出液固比6~8.1浸出温度65~75℃浸出时间1~1.5h浸出终点酸度PH=4.8~5.22.2.2.4 氧化锌酸性浸出浸出液固比5~6.1浸出温度80~90℃浸出时间6~8h浸出始酸150~200g/lH2SO4浸出酸20g/lH2SO42.2.2.5 锌粉置换置换温度75~85℃置换时间3~4h始酸20g/lH2SO4终酸PH=4.8~5.02.2.3 主要技术经济指标2.2.3.1 焙砂锌浸出率85~90%2.2.3.2 浸出渣率~40%(以焙烧料计)2.2.3.3 上清夜产量33~34m3/h2.2.3.4 浸出渣量18240t/a(干量)2.2.3.5 氧化锌浸出渣量~2100t/a(干量)2.2.3.6 铟渣量112t/a(干量)主要成分In≥3%2.2.3.7 原材料单耗硫酸(98%H2SO4)120kg/t析出锌锰矿粉(MnO275%)15kg/t析出锌凝聚剂(3#)1kg/t析出锌蒸汽(0.2~0.3MPA)0.85t/t析出锌生产水 4.7m3/t析出锌2.3.1 工艺流程简述由浸出送来的中浸上涉清液泵入一段净化槽,一段净化槽共2台,规格为φ4500×5500,V=87m3/台,两台并联间断操作。
锌粉经振动给料机加入一段净化槽,反应完成后排料至中间槽,再用泵送至3台F=100m2 的厢式压滤机进行液固分离,所得滤渣即铜镉渣,经浆化后泵至镉工段回收镉。
所得滤液经2台F=30m2 的螺旋板加热器加温到85~90℃后经加热后液贮槽送往二段净化槽。
二段净化槽共4台,规格同一段净化槽,也是4台并联间断操作。
锌粉经振动给料机加入各净化槽,酒石酸锑钾溶液用人工加入槽,反应完成后排料至中间槽,再用泵送至3台F=100m2的厢式压滤机压滤,所得滤渣即钴渣,再经酸洗、压滤后,所得滤渣即钴精矿,暂堆存待回收钴。
滤液用锌粉、酒石酸锑钾沉钴后,再经压滤,滤渣与钴精矿卸在同一堆场,滤液送浸出车间。
二段净化压滤后液送往三段净化槽。
三段净化槽共2台,规格也同一段净化槽,两台并联间断操作。
锌粉经振动料机加入槽,以除去残余的镉。
反应完成后排料至中间槽,再用泵送至3台F=100m2的厢式压滤机压滤,所得滤渣含锌较高,用人工返回到一段净化槽再利用。
所得滤液即新液,用废电解液使新液含H2SO4l~3g/l ,减少新液在输送过程中的结晶,然后用泵送往电解车间。
净液工段产出的铜镉渣经浆化后,送往镉工段2台φ3000×3200,V=24m3机械搅拌槽进行铜镉渣的浸出,两台并联间断操作。
加入废电解液,控制始酸10g/l,终点PH=5.2~5.4。
矿浆经中间槽用泵送至1台F=40m2的厢式压滤机压滤,滤液送置换槽,产出滤渣即铜渣,可作为中间产品出售。
置换在1台φ3000×3200,V=24m3机械搅拌槽进行,置换前加入硫酸,控制溶液PH=2~3,以溶解锌粉表面的氧化锌膜,增加锌粉活性,加速置换速度。
置换后液用泵送至1台F=40m2的厢式压滤机压滤,产出滤液即贫镉液,用泵送回浸出车间。
所得滤渣即海绵镉,可作中间产品出售。
2.4 电解2.4.1 工艺流程简述净液工段送来的新液温度70~80,与经过空气冷却塔冷却后的废电解温度约34℃,在混液槽中混合,通过控制新液和废电解液的混合比(1:15~20)来保证电解槽操作温度在37~42℃之间。