表面粗糙度误差的测量与检验
第5章表面粗糙度及检测

对附加评定参数Rsm和Rmr(c),一般不能作为独立参数选用,只 有少数零件的重要表面且有特殊功能要求时才附加选用。Rsm主要在对 涂漆性能有要求时,以及冲压成形时对抗裂纹、抗振、抗腐蚀、减小流 体流动摩擦阻力等有要求时选用。支承长度率Rmr(c)主要在对耐磨性、 接触刚度选用
i 1
(2)轮廓算术平均中线:
表面粗糙度的评定参数及标注
在取样长度L内,由中线至轮廓上、下两边的面积等。这条 中线就叫轮廓算术平均中线,应用很广。
F1 F2 F2n1 F2 F4 F2n
表面粗糙度的评定参数及标注
二 . 评定参数及数值
国家标准GB/T 3505-2009规定的评定表面粗糙度的参数有幅度参数、间距 参数、混合参数以及曲线和相关参数等四类。 。
表面粗糙度的标注
表面粗糙度的标注
在零件图上,表面粗糙度代号周围一般只标注幅度参数Ra或Rz的符 号和允许值。 当要求在表面粗糙度参数的所有实测值中超过规定值的个数少于总 数的16%时,应在图样上标注表面粗糙度的上限值或下限值;当要求在 表面粗糙度的所有实测值中不得超过规定值时,应在图样上标注表面粗 糙度的最大值或最小值。
(5)在确定表面粗糙度参数值时,应注意它与尺寸公差和几何公差的协调。尺 寸公差值和几何公差值越小,表面粗糙度的Ra或Rz值应越小,同一公差等级时, 轴的表面粗糙度Ra或Rz值应比孔小。 (6)要求防腐蚀、密封性能好或外表美观表面的表面粗糙度要求应较高。 (7)凡有关标准已对表面粗糙度要求作出规定(如与滚动轴承配合的轴颈和外 壳孔的表面粗糙度)时,则应按相关规定确定表面粗糙度参数值。
表面粗糙度的评定参数及标注
4.曲线和相关参数
Rmr(c)的大小反映了轮廓表面峰谷的形状,同样水平位置下 Rmr(c)值越大,表面实体材料越长,接触刚度和耐磨性越好。如图 5-8所示,图5-8a比图5-8b的接触刚度和耐磨性好。
粗糙度检测方法及评定【干货技巧】
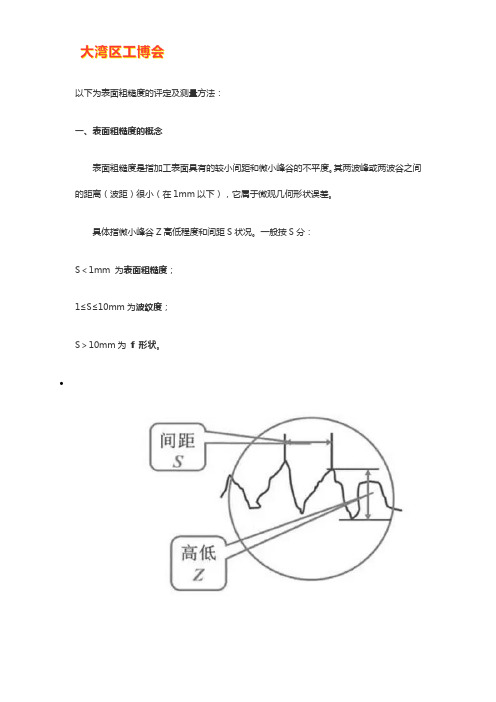
以下为表面粗糙度的评定及测量方法:一、表面粗糙度的概念表面粗糙度是指加工表面具有的较小间距和微小峰谷的不平度。
其两波峰或两波谷之间的距离(波距)很小(在1mm以下),它属于微观几何形状误差。
具体指微小峰谷Z高低程度和间距S状况。
一般按S分:S<1mm 为表面粗糙度;1≤S≤10mm为波纹度;S>10mm为f 形状。
•二、VDI3400、Ra、Rmax对照表国家标准规定常用三个指标来评定表面粗糙度(单位为μm):轮廓的平均算术偏差Ra、不平度平均高度Rz和最大高度Ry。
在实际生产中多用Ra指标。
轮廓的最大微观高度偏差Ry在日本等国常用Rmax符号来表示,欧美常用VDI指标。
下面为VDI3400、Ra、Rmax 对照表。
三、表面粗糙度形成因素表面粗糙度一般是由所采用的加工方法和其他因素所形成的,例如加工过程中刀具与零件表面间的摩擦、切屑分离时表面层金属的塑性变形以及工艺系统中的高频振动、电加工的放电凹坑等。
由于加工方法和工件材料的不同,被加工表面留下痕迹的深浅、疏密、形状和纹理都有差别。
四、表面粗糙度对零件的影响主要表现影响耐磨性。
表面越粗糙,配合表面间的有效接触面积越小,压强越大,摩擦阻力越大,磨损就越快。
影响配合的稳定性。
对间隙配合来说,表面越粗糙,就越易磨损,使工作过程中间隙逐渐增大;对过盈配合来说,由于装配时将微观凸峰挤平,减小了实际有效过盈,降低了连接强度。
影响疲劳强度。
粗糙零件的表面存在较大的波谷,它们像尖角缺口和裂纹一样,对应力集中很敏感,从而影响零件的疲劳强度。
影响耐腐蚀性。
粗糙的零件表面,易使腐蚀性气体或液体通过表面的微观凹谷渗入到金属内层,造成表面腐蚀。
影响密封性。
粗糙的表面之间无法严密地贴合,气体或液体通过接触面间的缝隙渗漏。
影响接触刚度。
接触刚度是零件结合面在外力作用下,抵抗接触变形的能力。
机器的刚度在很大程度上取决于各零件之间的接触刚度。
影响测量精度。
零件被测表面和测量工具测量面的表面粗糙度都会直接影响测量的精度,尤其是在精密测量时。
表面粗糙度与测量
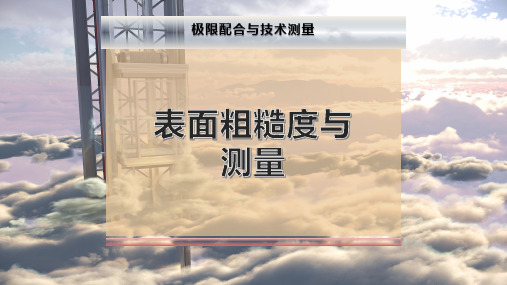
Page 10
1.2.2表面粗糙度的主要评定参数 (GB/T 1031—95)
▪ 2.微观不平度十点高度Rz
• 微观不平度十点高度Rz是指在取样长度l内,选取 5个最大的轮廓峰高的平均值与5个最大的轮廓谷 深的平均值之和,如图所示。Rz值越大时,表面 越粗糙。因测点少,Rz值不能充分反映表面微观 几何形状的特性,但轮廓峰高和轮廓谷深易用光 学显微镜测量,再加上计算方便,所以应用较多 。
• 3.轮廓中线
• 轮廓中线是指评定表面粗糙度参数值大小的一条基准线 。轮廓中线有以下两种。
▪ (1)轮廓的最小二乘中线
• 轮廓的最小二乘中线是指根据实际轮廓用最小二乘法来 确定的基准线,即在取样长度内,使轮廓上各点至一条 假想线的距离hi的平方和为最。
▪ (2)轮廓的算术平均中线
• 轮廓的算术平均中线是指在取样长度内,由一条假想线 将实际轮廓分成上下两部分,并使上下部分的面积相等 ,这条假想线就是算术平均中线,如图6.4所示。
▪ (2)表面粗糙度样块的使用方法
• 1)要求表面粗糙度样块的形状、材料、加工方法、加工纹理与被测工 件相同。
• 2)注意将表面粗糙度样块与被测工件放在同一自然条件下(光线、温 度、湿度等)进行比较。
• 3)通过观察、手触摸的感觉来判断是否合格,触摸时手的移动方向应 与加工纹理相垂直。
• 4)Ra值在1.6μm以上时,应借助5倍以上的放大镜进行观察。
▪ 1.对配合性能的影响 ▪ 2.对耐磨性的影响 ▪ 3.对工作精度的影响 ▪ 4.对抗疲劳强度的影响 ▪ 5.对抗腐蚀性的影响 ▪ 6.对零件其他性能的影响
表面粗糙度的测量
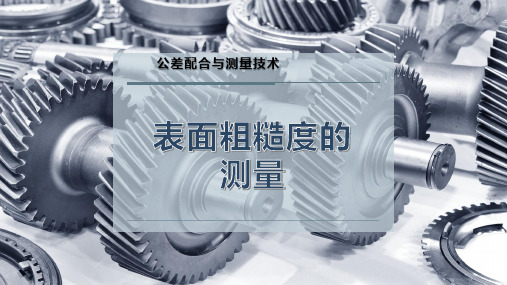
光切法测量原理为从光源发出的光线经聚光镜和狭缝形成一束扁 平光带,通过物镜组以45°方向投射在被测表面上。由于被测表面上 存在微观不平的峰谷,被具有平直边缘的狭缝像的亮带照亮后,表面 的波峰在S点产生反射,波谷在S′点产生反射,在与被测表面成另一 个45°方向经物镜放大后反射到目镜分划板上。从目镜中可以看到被 测表面实际轮廓的影像各自成像在分划板的a和a′处,若两点之间的 距离为N,用目镜上的测微百分表测出轮廓影像的高度N,根据物镜组 的放大倍数K,即可算出被测轮廓的实际高度h。
公差配合与要进行尺寸和形位误差的 测量,还要进行表面粗糙度的测量。其测量方法很多,下面 仅介绍几种常见的测量方法。 一、比较法
比较法是将被测表面与表面粗糙度样块相比较来判断工 件表面粗糙度是否合格的检验方法。
表面粗糙度样块的材料、加工方法和加工纹理方向最好 与被测工件相同,这样有利于比较,提高判断的准确性。另 外,也可以从生产的零件中选择样品,经精密仪器检定后, 作为标准样板使用。
公差配合与测量技术
用样板比较时,可以用肉眼判断,也可以用手触摸感觉, 为了提高比较的准确性,还可以借助放大镜和比较显微镜。 这种测量方法简便易行,适于在车间现场使用,常用于评定 中等或较粗糙的表面。 二、光切法
光切法就是利用“光切原理”来测量零件表面的粗糙度; 工厂中常用的光切显微镜(又称为双管显微镜),就是根 据光切原理制成的测量粗糙度仪器。
光切显微镜
三、针描法 针描法的工作原理是利用金刚石触针在被测表面上等速
缓慢移动,由于实际轮廓的微观起伏,迫使触针上下移动, 该微量移动通过传感器转换成电信号,并经过放大和处理得 到被测参数的相关数值。按照针描法原理测量表面粗糙度的 常用量仪有电动轮廓仪。
实验三表面粗糙度测量

实验三 表面粗糙度测量实验 3— 1用双管显微镜测量表面粗糙度一、实验目的1. 了解用双管显微镜测量表面粗糙度的原理和方法。
2. 加深对粗糙度评定参数轮廓最大高度Rz 的理解。
二、实验内容用双管显微镜测量表面粗糙度的Rz 值。
三、测量原理及计量器具说明参看图 1,轮廓最大高度 Rz 是指在取样长度 lr 内,在一个取样长度范围内,最大轮廓峰高 Rp 与最大轮廓谷深 Rv 之和称之为轮廓最大高度 。
即Rz = Rp + Rvp 12p 34p5p 6ZZpZpZZZzv 45R3Zvv 6v 1 v 2ZvZZ ZZ中线lr图 1图 2双管显微镜能测量 80~1μ m 的粗糙度,用参数 Rz 来评定。
双管显微镜的外形如图 2 所示。
它由底座 1、工作台 2、观察光管 3、投射光管 11、支臂 7 和立柱 8 等几部分组成。
双管显微镜是利用光切原理来测量表面粗糙度的,如图3 所示。
被测表面为 P 1、 P 2 阶 梯表面,当一平行光束从 450方向投射到阶梯表面上时,就被折成 S 1 2和 S 两段。
从垂直于 光束的方向上就可在显微镜内看到S 1 2 和 S 2 1 2和 S 两段光带的放大象 S 1 。
同样, S 和S 之间 距离 h 也被放大为 S 1 和 S 2 之间的距离 h 1 。
通过测量和计算, 可求得被测表面的不平度高度 h 。
图 4 为双管显微镜的光学系统图。
由光源 1 发出的光,经聚光镜 2、狭缝 3、物镜 4 以450 方向投射到被测工件表面上。
调整仪器使反射光束进入与投射光管垂直的观察光管内,经物镜 5 成象在目镜分划板上, 通过目镜可观察到凹凸不平的光带 (图 5 b )。
光带边缘即工件表面上被照亮了的 h 1 的放大轮廓象为 h 1′,测量亮带边缘的宽度 h 1′,可求出被测表面的不平度高度 h 1:h 1 = h 1 cos450=h 1cos450N式中N —物镜放大倍数。
表面粗糙度计算的误差分析与改进方法研究

表面粗糙度计算的误差分析与改进方法研究表面粗糙度是表面几何形态的一个重要指标,它在制造领域以及质量控制等方面有着广泛的应用。
表面粗糙度的计算是基于表面上小范围内的形态变化量,并且通过不同的计算方法来描述不同尺度下的表面粗糙度。
这篇文章将对表面粗糙度计算的误差分析和改进方法进行探讨。
1. 误差源分析1.1 仪器误差表面粗糙度计算的误差源包括仪器误差和环境噪声干扰。
仪器误差是指表面粗糙度测试设备在测量时所带来的误差。
由于实验仪器精度不同,从而导致表面粗糙度数据的误差大小也不同。
因此,在表面粗糙度测试中,应根据需要选择适当的测量精度和测量设备。
同时,根据实际应用的粗糙度要求,适当控制精度不必要的提高,这样可以有效降低测试成本。
1.2 环境噪声干扰环境噪声干扰是指在表面粗糙度测试过程中,由环境噪声污染信号引起的测量误差。
由于现实环境中存在各种各样的干扰源,例如电磁辐射、机械振动等,从而导致表面粗糙度测试结果的误差。
解决这个问题需要采取一系列措施,如在测试过程中有效隔离干扰源、防止干扰源的信号波形入侵等。
2. 计算方法的误差分析2.1 平均高度Ra的误差分析平均高度Ra是表面粗糙度计算中最常用的指标之一。
计算公式为:Ra=1/n∑|yi-y|其中,yi是预先选择的一条长度为l的参考线,n是样本点数。
平均高度Ra的误差来源于采样点不足或过多。
当采样点过少时,计算得到的结果可能与真实值相差较大,因为样本点不能充分反映表面的实际形态。
相反,当采样点过多时,计算出来的平均值会趋近于真实值,但是计算时间会变长,且样本误差还是存在的。
因此,正确选择采样点数极为重要。
2.2 峰值Rp和谷值Rv的误差分析峰值Rp和谷值Rv是表面粗糙度描述不规则凸凹形态的重要指标。
计算公式为:Rp=max(yi)-yiRv=yi-min(yi)其中,yi是预先选择的一条长度为l的参考线。
峰值Rp和谷值Rv的误差来源于设置计算区域的不同,以及区域内样本点的选择。
表面粗糙度与检测(新国标)

在给定的水平位置C上,轮廓的实体材料长度Ml(C)与评定长度ln的比率。
n
bi
Rm(rc) i1 ln
Ml(C)/ln
C = Rz %
图5.8 轮廓的支承长度率
表面粗糙度评定参数共 4个:
基本参数 2个
附加参数 (辅助参数)
2个
Ra —轮廓算术平均偏差 Rz —轮廓最大高度 RSm — 轮廓单元平均宽度 Rmr(c) —轮廓支承长度率
见表5-1。 2.评定长度
评定长度是指评定轮廓表面粗糙度所必须的一段长度,它可以 包括一个或几个取样长度,如图5-2所示。由于被测表面上各处的 表面粗糙度不一定很均匀,在一个取样上往往不能合理反映被测量 表面的粗糙度,所以需要在几个取样长度上分别测量,取其平均值 作为测量结果。
3. 中线—指具有几何轮廓形状并划分轮廓的基准线 轮廓算术平均中线:在取样长度内,划分实际轮廓为上、 下两部分面积相等的线
Z(x)
Z P1
Z Pmax
中线
Rz
Z v1
Z v2
Z vmax
x
lr
最大高度Rz
2. 间距参数
轮廓单元: 一个轮廓峰和相邻轮廓谷的组合。
轮廓单元宽度Xsi: 中线与一个轮廓单元相交线段的长度。
轮廓单元的平均宽度 RSm:
在取样长度lr
内,轮廓单元宽度Xsi的平均值:
RSm
1 m
m i1
Xsi
3. 混合参数(形状参数) 轮廓的支承长度率Rmr(C) —
摩擦面比非摩擦面值小;
参数值的选用 (标准化)
考虑(类比法)、密封性好等值小;
注意与尺寸公差和几何公差的协调
特殊应按标准规定确定粗糙度值
表面粗糙度及检测

第六章表面粗糙度及检测第一节概述用任何方法获得的零件表面,都不会绝对的光滑平整,总会存在着由较小间距的峰和谷组成的微观高低不平。
这种加工表面上具有的微观几何形状误差称为表面粗糙度。
它主要是在加工过程中,由于刀具切削后留下的刀痕、切屑分离时的塑性变形、工艺系统中存在高频振动及刀具和零件表面之间的磨擦等原因所形成的。
表面粗糙度对零件的功能要求、使用寿命、可靠性及美观程度均有直接的影响。
为了正确地测量和评定零件表面粗糙度,自从1956年颁布了第一个表面光洁度标准JB 50-56以来,我国对表面粗糙度国家标准已进行了多次修订,现在实施的相关标准主要有GB/T3505-2000《产品几何技术规范(GPS)表面结构轮廓法表面结构的术语、定义及参数》(代替GB/T3505-2000)、GB/T1031-2009《产品几何技术规范(GPS)表面结构轮廓法表面粗糙度参数及其数值》(代替GB/T 1031-1995)、GB/T 10610-2009《产品几何技术规范(GPS)表面结构轮廓法评定表面结构的规则和方法》(代替GB/T 10610-1998)、GB/T131-2006《产品几何技术规范(GPS)技术产品文件中表面结构的表示法》(代替GB/T 131-1993《机械制图表面粗糙度符号、代号及其注法》)、GB/T 6062-2009《产品几何技术规范(GPS)表面结构轮廓法接触(触针)式仪器的标称特性》(代替GB/T 6062-2002)。
本章将对上述标准的主要内容进行介绍。
一、表面粗糙度轮廓的界定物体与周围介质分离的表面称为实际表面。
为了研究零件的表面结构,通常用垂直于零件实际表面的平面与该零件实际表面相交所得到的轮廓作为评估对象。
该轮廓称为表面轮廓,它是一条轮廓曲线,如图6.1所示。
图6.1零件的实际表面与表面轮廓加工以后形成的零件的实际表面一般处于非理想状态,其截面轮廓形状是复杂的,同时存在各种几何形状误差。
- 1、下载文档前请自行甄别文档内容的完整性,平台不提供额外的编辑、内容补充、找答案等附加服务。
- 2、"仅部分预览"的文档,不可在线预览部分如存在完整性等问题,可反馈申请退款(可完整预览的文档不适用该条件!)。
- 3、如文档侵犯您的权益,请联系客服反馈,我们会尽快为您处理(人工客服工作时间:9:00-18:30)。
《机械零件测量与检验》
表面粗糙度误差的测量与检验——电子教案
数控技术专业
名师课堂资源开发小组
2016年2月
项目四:零件表面粗糙度误差的测量与检验
请对矩形花键套零件的表面粗糙度进行检测。
如图13-1
图13-1 矩形花键套
一、零件表面粗糙度的分析
外图13-1为矩形花键套,从零件图样分析可得,该零件表面粗糙度要求较高的有7
70js
圆柱面Ra1.6,其次为Ra3.2,其余为Ra6.3.。
表面粗糙度的相关专业术语及知识点
零件的表面结构原于产品几何技术规范(GPS),其几何特征只能用微米(um)级的参数来描述,通常要用光学量仪才能确定其精度等级。
表面结构含粗糙度轮廓、波纹度轮廓和原始轮廓三个方面的内容,国家标准规定采用轮廓法确定相应的参数。
表面结构的粗糙度感觉零件的加工、检验中使用较普遍,是本章节重点介绍的内容。
1、表面结构国家标准
国家标准规定用轮廓法确定表面结构(粗糙度、波纹度和原始轮廓),对有关术语、定义、参数和表面结构的标注作出了明晰的规范。
现行使用的国家标准有:GB/T 3503-2009、GB/T 1031-2009和GB/T 131-2006。
GB/T 3503-2009 产品几何技术规范(GPS)表面结构轮廓法术语、定义及表面结构参数。
代替GB/T 3505-1983、GB/T 3505-2000。
GB/T 1031-2009 产品几何技术规范(GPS) 表面结构轮廓法表面粗糙度参数及其数值。
代替GB/T 1031-1995。
现行国家标准对原标准中的一些参数、代号作出修改,例如:将“轮廓最大高度”参数代号“Ry”改成为“Rz”;“轮廓微观不平度的平均间距”参数代号“Sm”改为“Rsm”;“取样长度”代号由“L”改为“Lr”。
GB/T 131-2006 产品几何技术规范(GPS) 技术产品文件中表面结构的表示法代替了GB/T 131-1993。
2、表面粗糙度
1)实际轮廓
实际轮廓是指一个平面与表面相交所得的轮廓线,称为表面轮廓。
如图13-2所示。
图13-2 实际轮廓
评定表面结构时,通常按轮廓上波长的大小将表面轮廓误差分成三类:波长λ<1mm 属于表面粗糙度;波距λ在1~10mm属于表面波纹度;波距λ>10mm属于形状误差。
零件实
际轮廓的几何误差如图13-3所示。
(a)
(b)
(c)
(d)
图13-3 实际轮廓的几何误差
(a)表面粗糙度轮廓(b)波纹度轮廓(c)形状误差轮廓(d)截面轮廓
2)评定表面粗糙度的基本术语
(1)取样长度Lr
在X轴方向判别被评定轮廓不规则特征的长度。
即用于评定具有表面粗糙度时所取的一段基准长度。
Ra参数值与取样长度Lr值的对应关系。
见表13-1所示。
表13-1 Ra参数值与取样长度Lr值的对应关系
(2)评定长度Ln
评定长度是评定轮廓表面粗糙度所必需的一段长度。
一般包含一个或几个取样长度在内,如取标准评定长度ln=5lr。
若被测表面比较均匀,可选ln<5lr;若均匀性差,可选ln >5lr。
(3)轮廓中线
用以评定表面粗糙度参数值大小的一条参考线称为轮廓中线(在一个取样长度Lr之内)。
轮廓中线可以是最小二乘中线(如图13-4所示)或算术平均中线(如图13-5所示),视具体的评定参数而定。
图13-4 轮廓最小二乘中线
图13-5 轮廓算术平均中线
3)表面粗糙度评定参数
(1)轮廓算术平均偏差Ra(如图13-6所示)
在一个取样长度lr范围内,被评定轮廓上各点至轮廓中线的纵坐标值的绝对值的算术平均值,即
图13-6 轮廓算术平均偏差Ra
(2)轮廓最大高度Rz (图13-7)
轮廓最大高度Rz 是指取样长度Lr范围内,轮廓峰顶线Zpmax与轮廓谷底线Zpmax间的最大距离,即 Rz = Zpmax + Zvmax
图13-7 轮廓最大高度Rz
(3)轮廓单元的平均宽度RSm
一个轮廓峰与相邻的轮廓谷的组合叫做轮廓单元,在一个取样长度lr 范围内,轮廓单元相交线段的宽度(轮廓的宽度Xs )的平均值RSm ,即为
4)表面粗糙度的选用(见表13-2所示)
表13-2 表面粗糙度的表面特征、加工方法及应用
∑==m
i si
X m RSm 1
1
轴和孔的表面粗糙度参数推荐值见表13-3
表13-3 轴和孔的表面粗糙度参数推荐值5)表面粗糙度的标注
(1)表面粗糙度的符号表面粗糙度符号、代号及意义见表13-4
表13-4 表面粗糙度符号、代号及意义
表13-5 表面粗糙度画法与标注示例
3)不同表面粗糙度的外观情况
表13-6 不同表面粗糙度的外观情况
4)各种加工方法所能达到的表面粗糙度
表13-7 各种加工方法所能达到的表面粗糙度
二、选用计量器具
根据零件表面粗糙度要求,可选择以下计量器具进行测量检验:
零件名称序号检测项目量具类别量具名称数量备注
矩形花键套1Ra1.6,3.2,6.3 量仪+样板
表面粗糙度仪(表面
粗糙度样板)
1套
相关技术测量知识1、计量器具选用
表13-8 表面粗糙度的检测方法、适用范围及说明
如图13-6所示相应计量器具
图13-6(a)表面粗糙度样板
图13-3
图13-6b 便携式表面光洁度仪
图13-6c 粗糙度仪
三、零件表面粗糙度的测量与检验
1、矩形花键套位置误差检测表(单件):
注:1、评定结果:合格为OK,不合格为NG,重修为CG,特采为TG ; 零件
图号 检测项目
实测值 评定结果 检测者 备注
0.03 OK 刘四 0.02 OK。