螺纹紧固件失效分析案例(第1部分)
螺纹紧固件常见的失效模式分析

能 满 足设 计 要 求 。
2 . 5 延时 断裂
延时断裂常见原因为氢脆 , 氢脆是 在生产过程 ( 如电镀 、 焊 接) 中进入钢材 内部 的微量氢 , 在内部残余 的或外 加的应力作 用下导致材料脆化甚 至开裂 。常见易发生氢脆的紧 固件 有 : 自 攻钉/ 弹性垫圈, 8 级以上的经过电镀表 面处理 的螺栓 。
螺 纹 连 接 常 常 出现 螺 纹 滑 牙 , 造 成 螺 纹 滑 牙 的 主 要原 因有
情况 ; 螺栓拧进 的断面被顶住 , 如螺母为盲孔 的有效螺纹深 度
不够 。
2 . 3 应 力集 中部位 使 用后 断 裂
应力 集中部位使用后 断裂常见表现在螺 栓头部及头部 与 螺纹杆过度 的直角部位 , 造成应力集 中部位断裂的常见原因为 头部 与螺纹杆过度 的直角部位圆角过小 ; 螺栓冷镦成型时在头 部的塑性 流线存在缺陷 。 被联接 面与螺栓垂直度超差。
机 械类 产品装配 中 ,零 件与零件之 间主要依靠紧 固件联 接。 其 中螺纹 紧固件应用最 为广泛 , 紧固件的性 能及联接效 果 直接影响到产品的性能和安全以及使用寿命 。 紧固件 的失效是 常见机械类产 品质量问题产生的原因 , 因此螺纹 紧固件失效模 式 的潜在原 因分析 , 对 产品的质量提升有重要 的意义 。
螺纹脱碳 : 常见现象为装 配时感觉扭矩加不上 , 螺栓拆下后 , 发 现螺纹全部 或部分被磨平 , 以及螺栓螺纹或者螺母孔表面硬度
低; 内外螺纹尺寸配合 : 相配合 的联接付接触面积小 , 有两种情
况: 一是接 齿合的螺纹扣数 少 , 二是 螺纹与螺纹不在 中径 以内 接触( 即精度配合不好 , 螺栓螺纹和螺母 的螺纹接触不够 ) 。 同时 , 在装配方法 上如果装配不对孔 , 强拧也会 造成螺纹 滑牙 ; 螺纹摩擦系数过小 : 表面涂层 、 表 面粗糙 度 、 表 面润滑剂 不合理和螺栓螺纹或者螺纹孔有异物 , 损坏螺纹 以及螺栓跟螺 母的螺距 、 角度变异都会导致螺纹滑牙。
螺纹连接件表面涂层失效分析一例

图2 正常批次连接件拧紧—松开试验曲线图 (拧紧力矩=14 N·m)
2.2 连接件表面涂层厚度的检测
采用金相截面检测的方法对两组试验件螺纹连
接部位的表面涂层厚度进行测量。结果显示,正常件
的最大涂层厚度为42.6 μm(图4),符合局部最大
涂层厚度≯50μm的要求;而缺陷件的最大涂层厚度 为100.7μm(图5),是最大涂层厚度要求的2倍。
生 产现场
SHOP
SOLUTION
螺纹连接件表面涂层失效分析一例
摘要:通过实例介绍了一种分析汽车制动管路连接件失效原因的方法,即使用扭矩测试仪分析
汽车管路联接的拧紧和松开过程,并结合失效件螺纹表面涂层厚度的金相检测,可以准确、快速地
判定由螺纹连接件表面涂层造成的连接失效,为螺纹连接件表面涂层不良的检测分析提供了直观和
完整的级进模冲压工艺实例见图22。
图22 某级进模冲压工艺简图
AT &M
(上接第58页)
表1 试验结果汇总表
检测项目
正常件
轴向预紧力(拧紧力矩14 N·m)/kN
5.80~6.66
旋转角度(拧紧力矩14 N·m)/(°)
133~168
最大松开扭矩/N·m
7.71~10.21
螺纹摩擦系数
0.22~0.25
图1 正常件(左)与失效件(右)密封面变形情况的对比
纹连接件各5件,在汽车管路联接扭矩测试仪上连接 汽车制动管路和对手件,模拟实际装车过程的连接拧 紧情况。
在试验台上对两组试验件分别使用扭矩扳手平 稳、匀速地施加拧紧力矩至规定值,然后再反向松开 螺纹连接件,扭矩测试仪上的力值传感器、转角传感 器和扭矩传感器在拧紧和松开过程中会实时记录轴向 预紧力、拧紧力矩和扭矩扳手的转角等数据;通过专 用的数据采集软件可将实时记录的试验数据值绘制成 连续的连接件拧紧—松开试验曲线图(图2和图3), 对比两组试验曲线图就能够清楚、直观地看出这两
高强螺纹紧固件的失效模式、机理分析和设计原则
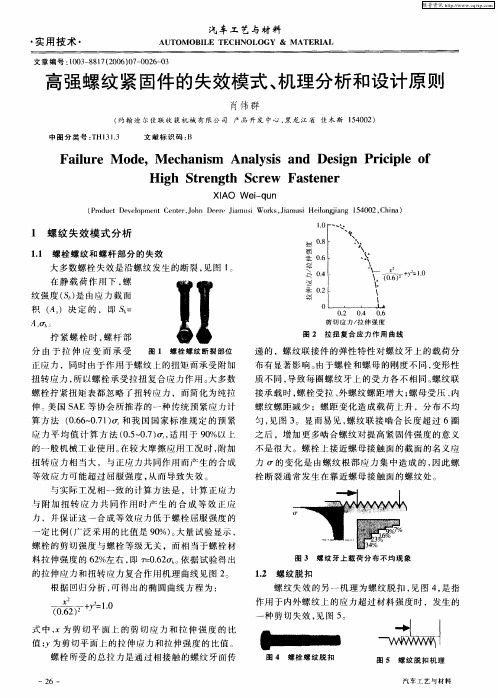
剪切 应 力/ 伸 强度 拉
拧 紧螺 栓 时 , 杆部 螺
分 由 于 拉 伸 应 变 而 承 受
图 2 拉扭 复合 应 力作 用 曲线
递 的 ,螺 纹联 接 件 的弹性 特性 对螺 纹牙 上 的载荷 分 布 有显 著影 响 。 由于 螺栓 和螺母 的刚度 不 同 , 变形性 质不同, 导致 每 圈螺纹 牙上 的受 力各 不相 同。 螺纹联 接 承载 时 , 栓受 拉 、 螺 外螺 纹螺距 增 大 ; 螺母受 压 、 内 螺 纹螺距 减 少 ;螺距 变化 造成 载荷 上升 ,分 布不 均 匀, 图 3 见 。显 而易 见 , 螺纹 联接 啮 合 长度 超过 6圈 之 后 ,增 加 更 多啮合 螺纹 对提 高 紧固件 强度 的意 义 不 是很 大 。螺栓 上接 近螺母 接 触 面的截 面 的名义 应 力 的 变化 是 由螺 纹根 部 应 力集 中造 成 的 , 因此 螺 栓 断裂 通 常发生 在靠 近螺母 接 触 面的 螺纹处 。
肖伟 群
( 翰 迪 尔佳联 收 获机 械 有 限公 司 产 品 开发 中心 , 龙 江 省 佳 木 斯 l4 0 ) 约 黑 5 0 2
中 图 分 类号 :Hl . T 313 文 献 标 识 码 : 1 3
Fa l r o e i e M d ,M e h n s An l ss a d De i n Pr cp e o u c a im a y i n sg ii l f
维普资讯
汽 车 工 艺与材 料
・
实 用技 术 ・
AUToM oBI LE TECHNoLoGY & M ATERI AL
文 章 编 号 :0 3 8 l (0 6 0 — 0 6 0 10 — 8 7 2 0 ) 7 0 2 — 3
案例一螺栓失效分析

案例一螺栓断裂失效分析某螺栓生产厂家生产的螺栓在用户使用过程中发生断裂,为分析螺栓断裂原因,进行了化学成分测试、金相组织观察、螺栓断口观察、能谱测试以及硬度测试等,并对螺栓断裂做出了结论。
1、化学成分分析螺栓成分分析采用成分分析仪,正常断裂、异常断裂螺栓成分见表1,从表中可以看出正常断裂螺栓与异常断裂螺栓成分都符合GB/T3077-1999《合金结构钢》中对45Mn2钢的要求。
表1材料化学成分分析结果(质量分数,% )2、金相组织分析取平行于断裂截面的试样,打磨、抛光并观察其组织形貌。
下图1(a)、1(b)所示为正常断裂螺栓与异常断裂螺栓的金相组织形貌,从图中可以看出螺栓金相组织均为回火马氏体。
(a.)正常断裂螺栓;(b)异常断裂螺栓图1螺栓金相组织形貌3、宏观断口形貌分析正常断裂螺栓、异常断裂螺栓宏观断口形貌如图2(a)、2(b)所示。
由图可知两个螺栓均从中心起裂,裂纹向四周扩展。
正常断裂螺栓与异常断裂螺 tiSf 裂纹源、扩展区、瞬断区三个部分,正常断裂螺栓扩展区面积 811^,瞬断区面积则比异常断裂螺栓小。
这与异常断裂螺栓应力(比正常断裂螺栓断裂应力(215KN)小相吻合。
同时正常断裂螺栓断以蜃船)4、微观断口形貌分析图3所示为正常断裂螺栓与异常断裂螺栓断裂截面裂纹源附近的微 从图邵皆辍看岀正常断裂螺栓组织较为平整,而异常断裂螺栓中心附近可 昊簾爵的微孔。
图4所示为夹杂物所在位置,图5为夹杂物能谱分析图, 壽舅对应的元素分析表,从表中可以看出夹杂物中主要元素为0、Si,并存、Al 、Ca 元素,其中0元素的含量很大,故较杂物主要为Si02,常断裂螺栓在裂纹源附近呈凹陷(a)正图2螺栓(b)异常断裂 螺栓Mg 0>(a)、(b)为正常断裂螺栓;(c)、(d)为异常断裂螺栓;(d)图中三角形标记为 能谱点图3螺栓断&显微形貌图4夹杂物能谱分析表2夹杂物能谱测试化学成分元素 C0 Mg Al Si Ca Fe 重量百分比2. 95 39. 482. 36 5. 84 22. 10 2. 10 25. 18 原子百分比5. 6857. 172. 255. 0218. 231.2110.445、显微硬度分析取平行于断裂界面的试样,磨样、抛光并从表层到中心每隔1mm 测量其显 微硬度。
典型钢材失效分析案例详解
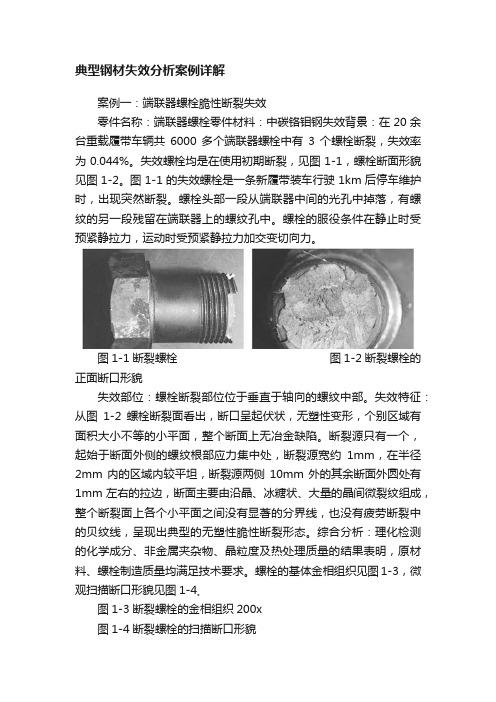
典型钢材失效分析案例详解案例一:端联器螺栓脆性断裂失效零件名称:端联器螺栓零件材料:中碳铬钼钢失效背景:在20余台重载履带车辆共6000多个端联器螺栓中有3个螺栓断裂,失效率为0.044%。
失效螺栓均是在使用初期断裂,见图1-1,螺栓断面形貌见图1-2。
图1-1的失效螺栓是一条新履带装车行驶1km后停车维护时,出现突然断裂。
螺栓头部一段从端联器中间的光孔中掉落,有螺纹的另一段残留在端联器上的螺纹孔中。
螺栓的服役条件在静止时受预紧静拉力,运动时受预紧静拉力加交变切向力。
图1-1断裂螺栓图1-2断裂螺栓的正面断口形貌失效部位:螺栓断裂部位位于垂直于轴向的螺纹中部。
失效特征:从图1-2螺栓断裂面看出,断口呈起伏状,无塑性变形,个别区域有面积大小不等的小平面,整个断面上无冶金缺陷。
断裂源只有一个,起始于断面外侧的螺纹根部应力集中处,断裂源宽约1mm,在半径2mm内的区域内较平坦,断裂源两侧10mm外的其余断面外圆处有1mm左右的拉边,断面主要由沿晶、冰糖状、大量的晶间微裂纹组成,整个断裂面上各个小平面之间没有显著的分界线,也没有疲劳断裂中的贝纹线,呈现出典型的无塑性脆性断裂形态。
综合分析:理化检测的化学成分、非金属夹杂物、晶粒度及热处理质量的结果表明,原材料、螺栓制造质量均满足技术要求。
螺栓的基体金相组织见图1-3,微观扫描断口形貌见图1-4。
图1-3断裂螺栓的金相组织200x图1-4断裂螺栓的扫描断口形貌查找生产作业,发现当初螺栓拧紧装配时,实际拧紧力矩远大于设计规定的力矩。
为对比分析,取9枚螺栓实物(8枚已使用无问题的螺栓,1枚未使用螺栓),进行强断拉伸试验。
螺栓拉伸试验断口的断裂源也同样位于一侧螺纹根部应力集中处,属于线断裂源,断口形貌平齐,见图1-5。
断口微观形貌见图1-6。
两种断口形貌对比见表1-1。
图1-5合格螺栓断口形貌(一) 图1-6合格螺栓断口形貌(二)表1-1两种断口形貌对比断口 失效件断口 无问题实物断口断口典型 形貌 断裂源附近的断面主要为沿晶断裂,呈冰糖 状,无明显塑性变形,还有少量韧窝。
紧固件典型失效形式及案例解析过载断裂
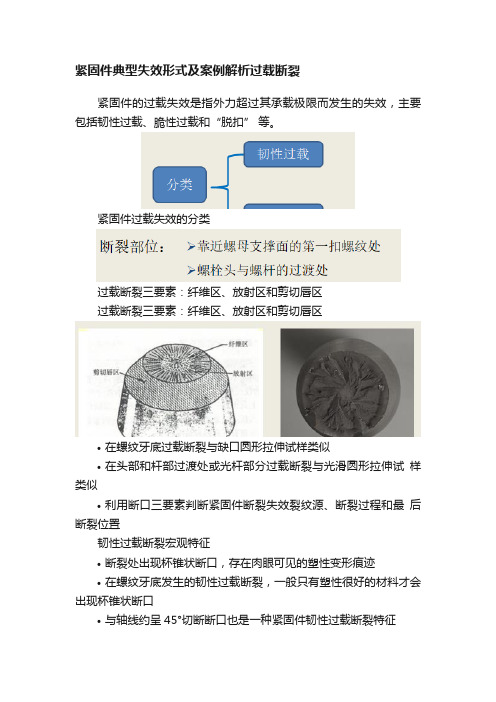
紧固件典型失效形式及案例解析过载断裂紧固件的过载失效是指外力超过其承载极限而发生的失效,主要包括韧性过载、脆性过载和“脱扣” 等。
紧固件过载失效的分类过载断裂三要素:纤维区、放射区和剪切唇区过载断裂三要素:纤维区、放射区和剪切唇区•在螺纹牙底过载断裂与缺口圆形拉伸试样类似•在头部和杆部过渡处或光杆部分过载断裂与光滑圆形拉伸试样类似•利用断口三要素判断紧固件断裂失效裂纹源、断裂过程和最后断裂位置韧性过载断裂宏观特征•断裂处出现杯锥状断口,存在肉眼可见的塑性变形痕迹•在螺纹牙底发生的韧性过载断裂,一般只有塑性很好的材料才会出现杯锥状断口•与轴线约呈45°切断断口也是一种紧固件韧性过载断裂特征•断口表面较粗糙、色泽灰暗、呈纤维状或鹅毛绒状•从紧固件表面一侧起源向另一侧扩展的过载断裂断口上,源区存在由表面起始的扩展棱线,最后断裂区一般有剪切唇•由表面周向起源,最终断裂区位于紧固件心部的过载断裂断口上,可见由周向边缘起始的扩展棱线,断口心部为纤维区韧性过载断裂宏观特征的应用•影响紧固件韧性过载断裂宏观特征的主要因素:受力状态和材料的塑性•通过断裂外观形态、宏观塑性变形方式、纤维的形态等对紧固件受力状态进行初步的判断例:拉伸应力导致的断裂:断口往往呈杯锥状或呈与应力轴45°的斜断口韧性过载断裂宏观特征的应用例:冲击应力或弯矩作用时:断口宏观特征上也可见放射棱线和剪切唇,但剪切唇在紧固件圆周上不完整例:扭转拉伸应力作用下断口呈现明显的“漩涡状”扭转痕迹韧性过载断裂微观特征•韧窝是紧固件韧性断裂的主要微观特征,但并非充要判据•判断紧固件是韧性断裂还是脆性断裂更为关键的在于紧固件断裂前是否发生可察觉的塑性变形紧固件韧性过载原因案例解析案例解析某螺栓在安装过程发生异常断裂失效存在“月牙形”高温氧化色原始断面根据扭矩、轴力、扭矩系数之间的关系抗拉强度扭矩系数K编号断裂扭矩NmMPa1-1 431.9 1222 0.0722-1 510 1240 0.084从图表中数据可以看出,螺纹和垫片未润滑和润滑后吹干扭矩系数和摩擦系数变化较小,而润滑后对扭矩系数和摩擦系数有显著的影响,从1#模拟安装情况可以看出,扭矩未达到530Nm前,就出现屈服现象。
紧固件断裂失效类型及原因分析

紧固件断裂失效类型及原因分析前言机器或钢结构件是由许多个零件和部件组成,这些零件和部件绝大部分是通过螺纹紧固件连接在一起的。
一旦紧固失效将造成机器失灵,严重者甚至出现人员伤亡事故。
由于紧固失效的常见性和潜在的严重性,所以我们应认真仔细地分析并找出紧固失效的原因,采取纠正措施,以杜绝紧固失效的发生。
紧固失效有两种,一种是螺栓断裂,被紧固零件瞬间分离,这种失效往往会造成严重的后果;还有一种是螺纹副松动和螺栓或螺母滑牙,被紧固零件出现一定范围的相互位移,造成机器部分功能失常。
人们发现,及时采取措施可以避免事故的发生。
如因未发现任其继续发展,螺栓和螺母终将分离,同样会引发重大安全事故。
紧固失效后直观现象是螺栓断裂或螺母与螺栓分离,因此人们一般认为螺栓断裂是螺栓质量有问题,螺母松动是螺母质量不好。
大家往往忽略了设计和安装中的问题。
一、剪切断裂剪切断裂出现在螺栓只受预紧力的连接中(见图1)。
剪切断口出现在螺栓杆部,位于两个被紧固零件的结合面处(见图1),断口有小面积的平整光亮剪切面。
出现剪切断裂有下列原因:图1 图21、设计原因⑴被紧固零件的结合面间摩擦系数太小或螺栓规格不够大造成预紧力F'不够,即:fF'<F ( f-结合面间的摩擦系数 )此时结合面间摩擦力小于横向工作载荷F,被紧固零件出现相对滑移,螺栓承受孔壁的挤压,当挤压力足够大时螺栓被剪切断。
在运动部件上因冲击力更大,所以出现的可能性也更大。
为了避免这种现象的发生,在设计上可以采用减载件和台阶来承受横向载荷,使螺栓仅起纯连接作用(见图2)。
⑵在振动工作环境下工作零件的紧固,未采用具有防松功能的紧固件。
在工作一段时间后,紧固件螺纹副出现松动,螺栓夹紧力(预紧力F')下降,此时也将发生上述同样的结果。
为了避免因松动而造成紧固失效,设计时应采用具有防松功能的紧固件,如美国施必牢防松螺母、有效力矩螺母。
2、装配原因装配时预紧扭矩过小,造成预紧力不够,即F'小,出现上述同样的结果。
螺栓失效分析

螺栓失效分析■ 史可庆,刘哲,刘永超2017年5月接到某公司邀请,分析解决该公司设备失效问题。
到厂后对于此失效设备进行了初步调查取证:此失效件为齿轮上的固定螺栓,螺栓头部与本体断开失效。
沟通得知本产品的相关信息,螺栓为购买的轧制半成品,材质为20MnTiB 。
自行热处理后使用,工艺为:860℃保温后淬火,然后420℃回火。
成品硬度为33~40HRC ,抗拉强度R m ≥1030MPa ,淬火后心部90%以上为马氏体。
调取热处理操作记录和监控,排除工艺执行问题引发失效的可能性。
1. 宏观分析失效螺栓为在齿轮上的固定螺栓,螺栓头部与本体断开失效,头部内端面有明显的撕裂失摘要:某公司齿轮上螺栓失效。
通过宏观分析、成分分析、硬度测试、金相分析等工作,对失效的原因进行了分析。
结果表明:该螺栓在近内表面54.25μm 处存在裂纹,此缺陷在淬火前已存在,淬火后使得缺陷加剧扩展,导致螺栓服役期间失效。
建议首先严格控制原材料的纯净度,降低夹杂物的影响,其次增加热处理前的无损检测工序,以保证淬火质量。
关键词:螺栓失效;裂纹;硫化物夹杂;疲劳断裂扫码了解更多效形貌,且有明显贝纹线。
该螺栓外表面是经过涂层处理的,有银色涂层存在,如图1所示。
2. 理化分析(1)光谱分析 将螺栓头部外端面用铣床铣掉表层涂层,进行光谱分析和硬度测试如图2所示,结果如表1、表2所示。
根据表1的结果分析,成分符合20MnTiB 的要求,且无明显的成分偏析状况。
(2)硬度检验 将螺栓头部沿着中心轴线锯切为两半,磨制试样,然后在内端面进行硬度检验如图3所示。
分析结果如表2所示。
根据表2的结果分析内外表面硬度(a ) (b )图1 失效螺栓宏观形貌表1 外表面化学成分分析(质量分数) (%)均符合32~39H R C要求,根据D I N50150标准推算强度也符合R m≥1040MPa的要求。
(3)金相检验将剖切面进行磨制抛光,进行金相分析,在剖切面一侧发现靠近内端面有一处裂纹,裂纹方向与内端面平行,裂纹距内端面最大距离305.35μm,距内端面最小距离54.25μm。
- 1、下载文档前请自行甄别文档内容的完整性,平台不提供额外的编辑、内容补充、找答案等附加服务。
- 2、"仅部分预览"的文档,不可在线预览部分如存在完整性等问题,可反馈申请退款(可完整预览的文档不适用该条件!)。
- 3、如文档侵犯您的权益,请联系客服反馈,我们会尽快为您处理(人工客服工作时间:9:00-18:30)。
螺纹紧固件失效分析案例全国紧固件标准化技术委员会机械工业通用零部件产品质量监督检测中心二〇〇八年6月序机械产品失效是一门关于研究机械产品质量的综合性技术学科,主要研究失效的规律与机理。
机械零件的失效是在特定的工作条件下,当其所具备的失效抗力指标不能满足工作条件的要求时发生的。
导致零件失效的本质原因可能是材料本身的失效抗力不足,也可能是零件存在与设计或制造等过程有关的缺陷。
产品的早期失效往往是产品质量低劣或质量管理不善及科学技术水平不高的直接反映。
失效发生后能否尽快作出正确的判断,确定失效原因,制定防止失效的措施,则是衡量有关科技人员技术水平的重要标志。
加入WTO后,我国的产品将参与国际市场的竞争,于是提高产品质量成为提高竞争力的关键因素。
失效分析则是定量评定产品质量的重要基础,也是保证产品可靠性的重要手段。
机械科学研究总院、机械工业通用零部件产品质量监督检测中心在进行大量失效分析的基础上(包括对断裂、腐蚀和磨损的深入研究,特别是断口、裂纹和痕迹分析),分析了可能出现失效的形式和类型,以供大家在生产中借鉴,在生产工艺中加以避免出现失效的可能;同时,在今后的质量纠纷中维护自己的正当权益。
机械工业通用零部件产品质量监督检测中心熊学端研究员从事了几十年失效分析研究工作,有很深的理论造诣,积累了丰富的失效分析经验,本文中列举了部分螺纹紧固件失效分析案例,希望能够为生产企业及用户提供良好的参考和借鉴;同时,中心愿为生产企业和用户在今后的失效分析中提供技术咨询和指导。
全国紧固件标准化技术委员会目 录第一部分 失效分析概述 (1)1. 失效定义 (1)2. 失效分析的意义、目的 (1)3. 失效的来源 (1)4. 失效分析的思路、方法 (1)5. 断口分析 (2)6. 断口分析部分名词术语 (3)第二部分 失效分析案例 (7)1. 汽车上臂螺栓断裂原因分析 (7)2. 溜冰鞋螺钉、螺母断裂原因分析 (12)3. 紧定螺钉断裂原因分析报告 (20)4. 连杆螺栓断裂原因分析 (25)5. 汽车轮毂螺栓断裂原因分析 (29)6. M8×55高强度螺栓断裂原因分析 (33)7. 高压开关螺栓断裂原因分析报告 (37)8. 沟槽刚性接头紧固螺栓断裂原因分析报告 (42)9. 定位螺钉断裂原因分析 (47)10. M36×280高强度螺栓断裂原因分析 (53)11. 高压线塔联结螺栓断裂原因分析 (59)12. 中压电器用螺栓断裂原因分析报告 (64)13. 网架螺栓断裂原因分析 (66)14. 螺钉断裂原因分析 (69)15. 吊环螺钉断裂失效分析 (73)16. 螺栓失效原因分析 (79)第一部分 失效分析概述在具体讲述螺纹紧固件失效分析案例以前,先对失效分析的定义、意义、目的;失效的来源;失效分析的思路与方法;断口分析和名词术语等做一简单叙述。
1.失效定义一个零件或部件不能履行设计赋予它规定的功能,称该零件或部件失效。
它包括以下三个内容:a.完全不能工作;b.可以工作,但不能令人满意地完成预期的功能;c.受到严重损伤不能可靠而安全的连续使用,必须拆下来进行修理或更换。
应注意把失效与废品区别开来,前者是在使用过程中出现的,后者是在生产制造过程中产生的。
另外,失效又分为正常失效和非正常失效,达到设计寿命的为正常失效,反之为非正常失效,后者才是通常失效分析工作的主要对象。
2.失效分析的意义、目的机械产品设计者的主要任务,是为社会提供质量好、寿命长、成本低的产品。
一种新产品的诞生,开始并不是完美的,多少会存在各种大小不同的问题,这在设计、制造中可能难以发现,往往只有在使用中才能充分暴露。
为此,设计、制造者必须针对产品使用中出现的失效进行仔细分析,找出问题的症结,重新改进设计、制造。
再投入使用,发现问题,再改进,这个循环过程也许要反复进行多次。
因此,失效分析是机械差品的质量由不完善走向完善的必经之路,是机械产品可靠性设计重要的一环。
最近一些年来,委托我们进行失效分析的任务越来越多,这是好事,这并不反应产品质量越来越差,而恰恰反应了生产者、客户对产品高质量的追求。
3.失效的来源造成失效的来源主要有以下方面:——设计——选材——材料缺陷——制造工艺(冷加工、热加工、表面处理等等)——贮存、运输(碰撞、锈蚀…)——装配(如螺栓拧紧力矩…)——服役条件(环境温度、受力状态、腐蚀环境、相关件的影响等)因此,失效来源不能单归咎于生产制造者,还包括流通环节和使用者的一些问题。
4.失效分析的思路、方法失效分析也有繁、简之分。
一些零部件的失效在现场很快能确定失效原因,这是简单的。
但是对一些大型零部件(如飞机、电站转子…),一些复杂且影响因素很多的零部件的失效分析,则必须组织多专业的科技人员,动用一些专用的检测仪器设备。
进行失效分析时,要做的工作包括(根据分析工作的难易来取舍):(1) 收集背景资料:失效件的设计图纸、要求;失效件的制造历史;失效件的服役情况、环境、受力情况…。
(2) 失效件的现场状态:运行记录、询问现场人员、拍照。
(3) 化学成分分析:鉴别材料的选择是否正确。
(4) 无损探伤:磁粉、超声波、着色、涡流、X射线、γ射线、工业CT…。
(5) 断口分析:保存好失效件的断口,不要受到损伤,不要将两个断口去吻对,断口上的附着物不要忙于清除。
断口的清洗要小心谨慎。
(6) 金相检验:包括低倍与高倍。
(7) 断口电镜分析:扫描电镜,透射电镜,俄歇谱仪,能谱分析等。
(8) 相结构分析:X射线衍射。
(9) 受力分析:光弹,应变片,涂漆,X射线应力测定。
(10) 力学性能测试:硬度,σb ,σs,δ,ψ,Ak,Klc,da/dN…。
(11) 断裂模拟试验:对一些吃不准的破坏形式,根据受力条件、环境进行模拟重现。
(12) 分析、结论。
5.断口分析断裂是机器零件失效最严重的表现形式之一。
对断裂的研究已发展成一门独立的边缘学科,涉及到断裂力学,断裂物理,断裂化学和断口学等多个分支。
其中断口存储记录了大量失效特征及失效原因的信息,因此,断口分析是失效分析最基本,也是最重要的方法之一。
尽管如此,在断口上记录的信息毕竟有限,加之对断口的基本研究仍在深入,以及在复杂工况条件下断口形貌的变异,增加了断口分析的难度和结论的可靠性。
因此绝不能把断口分析和失效分析等同起来,把断口分析所得出的结论充当零件失效原因的结论。
(1) 断口保存断口不要磕碰,不要把两个匹配断口用力去吻对,以免断口形貌失真。
断口上的一些残留物、污迹往往是失效的证据,不要轻易去除。
比如断口上的油污、锈迹等往往是裂纹产生在热处理前或后的判据。
待分析的断口要用干净的纸、布包好,防潮,以免锈蚀。
(2) 存在多个断口时,对每个断口的位置要标明,编号,照相留存。
(3) 断口清洗当对断口要进行清洗时,可用酒精、丙酮等清洗;不干胶带反复粘贴;电镜薄膜粘贴;超声波清洗。
当断口污染、锈迹严重时,可用化学方法清洗;呈弱酸性的溶液,碱液清洗(如醋酸,磷酸,稀氢氧化钠溶液,10%~20%的草酸等)。
清洗完后,用酒精淋洗,吹干后便于观察或置于干燥箱中保存。
(4) 二次断口的打开有时断口受到严重损坏,断裂细节观察不到,此时可将次生裂纹处打开进行观察,往往可以更加真实地反映断裂的细节。
此时,应将断裂处反响折断,以防断口受到挤擦损伤,有时可将试样深冷处理(如液氮),使材料脆化,便于折断。
(5) 配对断口的提供。
有时单个断口不能反映断裂的力学特征,对配对断口进行观察比比对便可得出结论,如张开型断裂,扭转剪切型断裂,从韧窝的相对变形方向便可判断受力性质(图1)。
图1 在三种应力状态下形成的显微空洞及微坑形状的示意图(a)正应力 (b)剪切应力 (c)撕裂应力为了对断裂性质作初步定性分析,在肉眼观察零件的实际断口时,主要从以下几个方面入手:(1) 观察断口是否存在放射花样或人字纹,人字纹的顶点就是裂纹源的位置。
根据放射区和纤维区面积的相对大小,可以大致定性估计断裂性质。
放射区大,所受外力就大,脆性也就越大。
(2) 断口上是否存在弧形线,如有海滩状弧线,说明是疲劳破断。
(3) 断口的粗糙程度,断口越糙,表明韧性纤维断裂所占比重越大。
反之,断口细平,多光泽,则解理脆性断裂所占比重大。
(4) 断口颜色,断口灰暗,塑性大。
(5) 断口与最大正应力方向的交角。
脆断时,断口与最大正应力方向垂直,而纯剪断时断口与最大切应力方向平行。
6.断口分析部分名词术语(1) 沿晶断裂实际金属材料为多晶粒结构,晶粒之间的边界称之为晶界,沿晶界扩展的裂纹,叫沿晶断裂。
图2就是它的断口形貌,宛如冰糖状,所以又叫冰糖状断口。
图2 沿晶断裂断口形貌 2000×(2) 穿晶断裂与沿晶断裂相反,裂纹在晶粒内部扩展。
(3) 解理断裂一种在正应力作用下产生的穿晶断裂,通常沿一定的严格的晶面——解理面分离,如体心立方金属中,(001)面就是解理面。
解理断裂的形貌特征为河流花样,河流的上游(支流)就是裂纹发源处。
肉眼观察断口时,旋转断口,可以看到许多闪闪发光的亮点(常称小刻面)就是解理面。
解理断裂形貌如图3所示。
图3 解理断裂的河流花样(4) 准解理断裂在断口微观形貌上,可看到解理断裂的特征,同时又伴随着一定的塑性变形痕迹,称之为准解理(如图4)。
图4 准解理形貌 2400×(5) 韧窝它的断裂特征是发生了明显的塑性变形。
断裂过程由显微空洞的形成、长大连接组成。
这些显微空洞称之为韧窝(图5)。
这种断裂方式属于韧性断裂。
图5 韧窝断裂 5500×(6) 剪切唇断裂过程的最后阶段,表面光滑,与拉应力方向呈45度,通常称之为拉边,此时裂纹是在平面应力状态下发生失稳扩展,材料塑性变形很大。
(7) 放射花样裂纹快速扩展在断口上留下的撕裂痕迹,它的放射方向就是裂纹扩展的方向(图6)。
图6 放射花样(8) 疲劳断裂在全部结构零件的破坏中,疲劳断裂占绝大多数,因此引起人们的特别关注。
疲劳是在周期交变应力作用下产生的一种突发破坏形式,在静载荷条件下不。
通常低于材料的屈服极限。
存在疲劳。
疲劳的抗力指标是疲劳极限σr疲劳断裂,在宏观上没有显著的塑性变形,从这个意义上说,疲劳破断属于脆性断裂。
疲劳断口大体上可分成三个区:裂纹源区;裂纹扩展区;裂纹快速扩展区(瞬断区)和剪切唇(图7)。
图7 疲劳断口形貌疲劳源区:一个光滑、细腻的细小区域,由于受交变应力的作用,裂纹两侧因反复挤压而变得平坦、光滑。
裂纹扩展区:该区的最大特点是有疲劳弧线(又称贝壳花样或海滩花样),这是裂纹扩展中的停顿或应力大小变化时,裂纹前沿线所留下的痕迹。
该区的微观形貌是存在疲劳辉纹(图8),这是一些相互平行的条带,每一个条带对应一次应力循环。