电炉炉温控制系统设计开题报告[1]
基于模糊PID的电热炉温度智能控制系统的开题报告
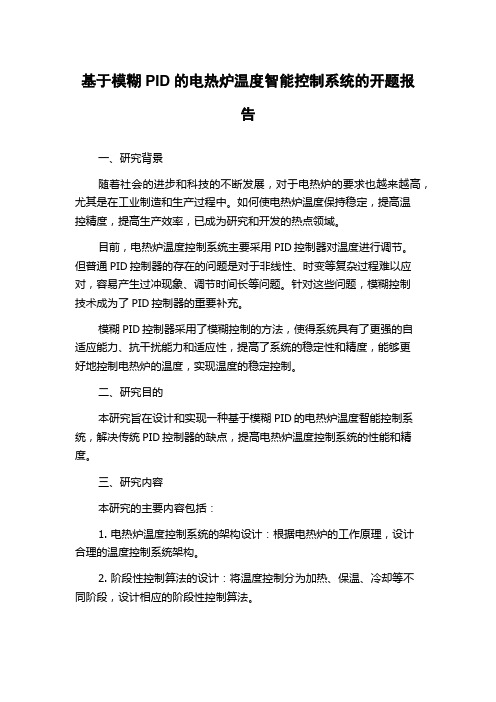
基于模糊PID的电热炉温度智能控制系统的开题报告一、研究背景随着社会的进步和科技的不断发展,对于电热炉的要求也越来越高,尤其是在工业制造和生产过程中。
如何使电热炉温度保持稳定,提高温控精度,提高生产效率,已成为研究和开发的热点领域。
目前,电热炉温度控制系统主要采用PID控制器对温度进行调节。
但普通PID控制器的存在的问题是对于非线性、时变等复杂过程难以应对,容易产生过冲现象、调节时间长等问题。
针对这些问题,模糊控制技术成为了PID控制器的重要补充。
模糊PID控制器采用了模糊控制的方法,使得系统具有了更强的自适应能力、抗干扰能力和适应性,提高了系统的稳定性和精度,能够更好地控制电热炉的温度,实现温度的稳定控制。
二、研究目的本研究旨在设计和实现一种基于模糊PID的电热炉温度智能控制系统,解决传统PID控制器的缺点,提高电热炉温度控制系统的性能和精度。
三、研究内容本研究的主要内容包括:1. 电热炉温度控制系统的架构设计:根据电热炉的工作原理,设计合理的温度控制系统架构。
2. 阶段性控制算法的设计:将温度控制分为加热、保温、冷却等不同阶段,设计相应的阶段性控制算法。
3. 模糊控制器设计:采用模糊控制理论设计模糊PID控制器,使控制器具有更好的自适应能力和鲁棒性。
4. 系统实现和测试:根据设计中的系统实现框架,进行系统实现和测试,并针对测试结果进行分析和总结,不断改进和优化系统。
四、研究方法本研究主要采用以下研究方法:1. 系统分析方法:对电热炉温度控制系统的物理特性、动态响应以及传递函数进行分析,为研究提供基础。
2. 模糊控制方法:采用模糊控制理论和模糊PID算法设计智能控制器。
3. 实验方法:对所设计的电热炉温度智能控制系统进行实验,测试系统的性能和精度。
五、研究意义本研究的意义在于:1. 提高电热炉温度控制系统的性能和精度,促进工业生产效率的提升。
2. 探究模糊控制技术在电热炉温度控制中的应用,为模糊控制技术的进一步发展提供实践基础。
温度控制系统开题报告

[1] 赖寿宏.微型计算机控制技术[M].北京:机械工业出版社,1994. [2] 陈伟人.MCS-51/96 系列单片机实用子程序集锦[M].清华大学出版社,1993. [3] 逢玉台,王团部.集成温度传感器AD590及其应用[J].国外电子元器件.2002,7(5): 3-4. [4] 康华光.电子技术基础[M].北京:高等教育出版社,2001. [5] 高培先.提高实时系统数据采集质量的研究[J].电子应用技术, 2002, 3(2):111-113. [6] 马西秦.自动检测技术[M],北京:机械工业出版社,2004. [7] 胡大可,李培弘,方路平.基于单片机8051的嵌入式开发指南[M].电子工业出版 社,2003. [8] 王宜怀.12 位 A/D 转换器 TLC2543 与 51 系列单片机接口技术[M],苏州:丝绸工学院 学报,1999. [9] 高鹏,安涛,寇怀成等.Protel99 入门与提高[M],北京:人民邮电出版社,2001. [10] 欧阳斌林,刘立山,蒋文科等.单片机原理及应用[M].中国水利水电出版社,2001. [11] 赵丽娟,邵欣.基于单片机的温度监控系统的设计与实现[M].机械制造,2006. [12] 张开生,郭国法.MCS-51 单片机温度控制系统的设计[M]. 微计算机信息,2005. [13] 马忠梅,张凯,马岩.单片机的C语言应用程序设计[M].北京:航空航天大学出版 社,2005. [14] M. Abramowitz, I. A. Stegun. Handbook of mathematical functions [M]. Dover, New York, 1965. [15] Yang Y, Yi. J, Woo, Y Y, Kim. B. Optimum design for linearity and efficiency of microwave Doherty amplifier using a new loadmatching technique [J]. Microw J, 2001, 44. [16] Vizimuller, P. RF design guide-systems, circuits and equations [M]. Artech House, Boston, MA, 1995. [17] Ferraro, Richard F. Programmer's Guide to the EGA, VGA, and Super VGA Cards [M]. 3rd ed. Reading, Mass. Addison-Wesley, 1995. ISBN 0-201-62490-7. [18] A. Papoulis. Probability random variables and stochastic process[M]. Mc-Graw Hill, New York, 1984. [19] R. Dye. Visual Object-Orientated Programming [J]. Dr. Dobbs Macintosh Journal, Sept.
温度控制系统开题报告
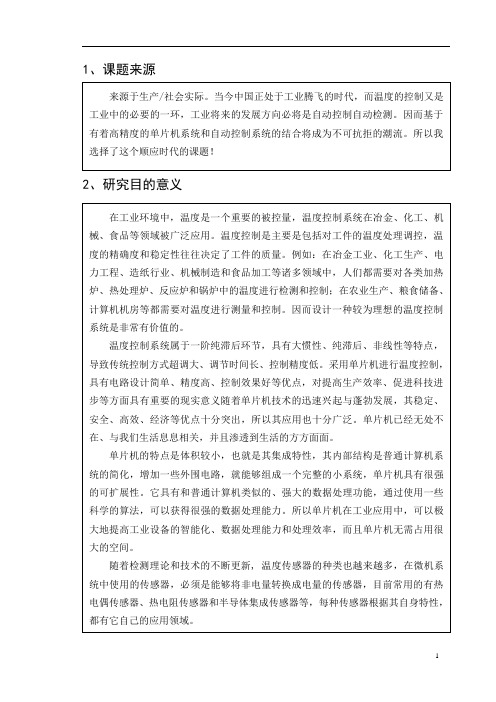
1
3、国内外研究现状和发展趋势综述
近年来,在温度检测技术领域中,多种新的检测原理与技术的开发应用己取得 了具有实用性的重大进展。新一代温度检测元件正在不断出现和完善化,主要包括 以下几种。(1)晶体管温度检测元件(2)集成电路温度检测元件(3)核磁共振温度检 测器(4)热噪声温度检测器(5)石英晶体温度检测器(6)光纤温度检测器(7)激光温 度检测器。目前国内外的温度控制方式越来越趋向于智能化,温度测量首先是由温 度传感器来实现的。测温仪器由温度传感器和信号处理两部分组成。温度测量的过 程就是通过温度传感器将被测对象的温度值转换成电的或其它形式的信号传递给 信号处理电路进行信号处理转换成温度值显示出来。温度传感器随着温度变化而引 起变化的物理参数有膨胀、电阻、电容、热电动势磁性能、频率、光学特性及热噪 声等等。随着生产的发展新型温度传感器还会不断出现,目前,国内外通用的温度传 感器及测温仪大致有以下几种热膨胀式温度计、电阻温度计、热电偶、辐射式测温 仪表、石英温度传感器测温仪。
在系统中,利用热电偶测得电阻炉实际温度并转换成毫伏级电压信号。该电压 信号经过温度检测电路转换成与炉温相对应的数字信号进入单片机,单片机进行数 据处理后,通过液晶显示器显示温度并判断是否报警,同时将温度与设定温度比较, 根据设定的算法计算出控制量,根据控制量通过控制固态继电器的导通和关闭从而 控制电阻丝的导通时间,以实现对炉温的控制。该系统中的时钟电路可以根据要求 进行准确计时。
of Contr01.1992 [11] 李士勇.模糊控制.神经控制和智能控制论[M].哈尔滨:哈尔滨工业大学出版社, 19961)在该领域已取得的研究成果 本人对该课题有了整体的认识和计划。
温度控制系统设计开题报告
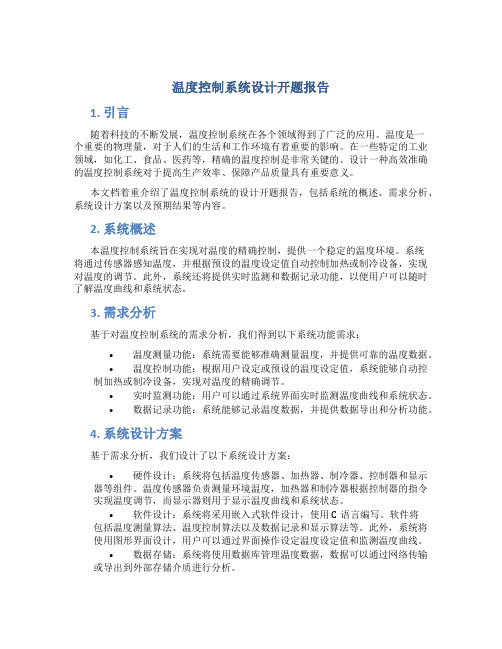
温度控制系统设计开题报告1. 引言随着科技的不断发展,温度控制系统在各个领域得到了广泛的应用。
温度是一个重要的物理量,对于人们的生活和工作环境有着重要的影响。
在一些特定的工业领域,如化工、食品、医药等,精确的温度控制是非常关键的。
设计一种高效准确的温度控制系统对于提高生产效率、保障产品质量具有重要意义。
本文档着重介绍了温度控制系统的设计开题报告,包括系统的概述、需求分析、系统设计方案以及预期结果等内容。
2. 系统概述本温度控制系统旨在实现对温度的精确控制,提供一个稳定的温度环境。
系统将通过传感器感知温度,并根据预设的温度设定值自动控制加热或制冷设备,实现对温度的调节。
此外,系统还将提供实时监测和数据记录功能,以便用户可以随时了解温度曲线和系统状态。
3. 需求分析基于对温度控制系统的需求分析,我们得到以下系统功能需求:•温度测量功能:系统需要能够准确测量温度,并提供可靠的温度数据。
•温度控制功能:根据用户设定或预设的温度设定值,系统能够自动控制加热或制冷设备,实现对温度的精确调节。
•实时监测功能:用户可以通过系统界面实时监测温度曲线和系统状态。
•数据记录功能:系统能够记录温度数据,并提供数据导出和分析功能。
4. 系统设计方案基于需求分析,我们设计了以下系统设计方案:•硬件设计:系统将包括温度传感器、加热器、制冷器、控制器和显示器等组件。
温度传感器负责测量环境温度,加热器和制冷器根据控制器的指令实现温度调节,而显示器则用于显示温度曲线和系统状态。
•软件设计:系统将采用嵌入式软件设计,使用C语言编写。
软件将包括温度测量算法、温度控制算法以及数据记录和显示算法等。
此外,系统将使用图形界面设计,用户可以通过界面操作设定温度设定值和监测温度曲线。
•数据存储:系统将使用数据库管理温度数据,数据可以通过网络传输或导出到外部存储介质进行分析。
5. 预期结果通过本温度控制系统的设计和实现,我们预期可以达到以下目标:•温度测量误差小于0.5摄氏度,满足精确测量需求。
基于模糊神经网络电炉温度控制系统设计的开题报告

基于模糊神经网络电炉温度控制系统设计的开题报告一、选题背景电炉是一种常用的工业生产工具,温度控制是电炉控制系统中最重要的一环。
现有的电炉温度控制系统大多采用PID控制算法,但是该算法只适用于线性系统,对于非线性系统控制效果较差。
模糊控制算法由于其能够处理非线性、时变、模糊等问题而被广泛应用于工业控制领域。
本课题拟基于模糊神经网络设计电炉温度控制系统,以实现控制效果优于传统PID控制算法。
二、研究目的本项目旨在基于模糊神经网络设计一种电炉温度控制系统,以提高电炉控制性能,实现控制精度更高、稳定性更好的控制效果。
三、研究内容1. 分析目前电炉温度控制系统所采用的PID控制算法的优缺点;2. 研究模糊神经网络控制原理及其在非线性系统控制中的应用;3. 基于模糊神经网络设计电炉温度控制系统;4. 编写控制程序并进行仿真实验;5. 分析实验结果,比较模糊神经网络控制算法和PID控制算法的控制效果。
四、研究方法1. 文献调研法:对目前电炉温度控制系统控制算法的研究现状进行调研,了解目前电炉控制系统中常用的控制算法及其优缺点;2. 理论分析法:对模糊神经网络控制原理进行深入研究,掌握其原理及其在实际控制系统中的应用;3. 系统设计法:根据所掌握的理论知识,设计电炉温度控制系统,包括硬件系统设计和算法设计;4. 实验分析法:编写控制程序并进行仿真实验,分析实验结果,比较模糊神经网络控制算法和PID控制算法的控制效果。
五、预期成果本项目预期实现基于模糊神经网络的电炉温度控制系统设计。
经过实验验证,该系统可实现控制精度更高、稳定性更好的控制效果。
本项目的成果将填补电炉温度控制系统中模糊神经网络控制算法的研究空白,为电炉温度控制系统的进一步提升提供一定的理论和实践基础。
六、研究计划本项目计划在2021年9月至2022年6月期间完成。
具体任务安排如下:1. 第一阶段(2021年9月至2021年10月):文献调研及模糊神经网络控制原理的深入研究;2. 第二阶段(2021年11月至2022年2月):电炉温度控制系统设计及仿真实验;3. 第三阶段(2022年3月至2022年6月):系统实现及实验分析。
基于单片机的电加热炉温度控制系统的设计【开题报告】

开题报告电气工程及其自动化基于单片机的电加热炉温度控制系统的设计一、课题研究意义及现状在冶金、化工、建材、机械、食品、石油等各类工业中,广泛使用着加热炉、热处理炉、反应炉等,炉子温度控制是工业对象中一个主要的被控参数。
过去曾使用常规PID控制或继电-接触器控制,自动化程度低,动态控制精度差,满足不了日益发展的工艺技术要求。
由于电热锅炉控制存在较大难度,经研究和实验提出了电加热锅炉的循环投切和分段模糊控制的控制模式,较好地解决了电加热锅炉控制的理论和实际问题。
国内电加热炉控制有四个发展阶段:第一阶段:手动控制、温度仪表显示第二阶段:顺序控制器或PLC程控器,温度仪表参与控制第三阶段:全PLC控制第四阶段:专用电脑控制用电加热锅炉专用电脑取代通用的PLC,更取代温控表。
它具有全PLC控制的全部优点,并克服了全PLC控制的全部缺点,可产品化,成本低,易与各种电热锅炉配套,配备最先进和成熟的控制程序,现场参数可由一般操作人员在现场进行设置和解决。
因此电加热锅炉专用电脑控制器已被广泛采用。
电功率输出的元件分为有机械触点和无机械触点两大类。
前者是交流接触器,后者是可控硅,交流接触器只能用作有级功率调节,优点是主回路完全电气隔离,耐过流和过压能力较强、自身耗电小、发热量也小、价格较低,缺点是有机械动作噪声,触点寿命较短。
可控硅可以用作无级功率调节,也可用于有级功率调节,优点是无机械动作噪声,触点寿命较长,缺点是主回路不能完全关断,过电流和过电压能力差,自身耗电较大,需要强制散热,价格较高。
本系统使用可控硅为输出的元件。
二、课题研究的主要内容和预期目标采用自动控制原理和单片机技术,对PID算法和单片机控制功能进行研究和设计,由可控硅元件来实现温度控制电路。
了解当前国内外电加热炉的研究与其产品市场;熟悉单片机技术,PID算法,可控硅元件等,为将来从事电子产品控制研发、制造及经营等方面工作打下基础。
毕业设计的具体内容:(1)研究和设计使用MCS-51单片机控制功能。
(完整word版)基于PLC的锅炉温度控制系统的设计-开题报告1
以锅炉为被控对象,以锅炉出口水温为主被控参数,以炉膛内水温为副被控参数,以加热炉电阻丝电压为控制参数,以PLC为控制器,构成锅炉温度串级控制系统;采用PID算法,运用PLC梯形图编程语言进行编程,实现锅炉温度的自
动控制。
可编程逻辑控制器(PLC)是集计算机技术、自动控制技术和通信技术为一体的新型自动控制装置。其性能优越,已被广泛的应用于工业控制的各个领域,并已经成为工业自动化的三大支柱(PLC、工业机器人、CAD/CAM)之一。
PLC技术在温度监控系统上的应用从整体上分析和研究了控制系统的硬件配置、电路图的设计、程序设计,控制对象数学模型的建立、控制算法的选择和参数的整定、人机界面的设计等。论文通过对德国西门子公司的S7-200系列PLC控制器,温度传感器将检测到的实际炉温转化为电压信号,经过模拟量输入模块转换成数字信号送到PLC中进行PID调节,PID控制器输出转化为0-10mA的电流信号输入控制可控硅电压调整器或触发板改变可控硅管导通角的大小来调节输出功率。对于监控画面,利用亚控公司的组态软件“组态王“
2011年03月24日
教研室审查意见:
教研室主任(签字):
2011年03月25日
2
华北科技学院
2011届本科毕业设热锅炉的应用领域相当广泛,电热锅炉的性能优劣决定了产品的质量好坏。目前电热锅炉的控制系统大都采用以微处理器为核心的计算机控制技术,既提高设备的自动化程度又提高设备的控制精度。
PLC的快速发展发生在上世纪80年代至90年代中期。在这时期,PLC在处理模拟量能力、数字运算能力、人机接口能力和网络能力得到了很大的提高和发展。PLC逐渐进入过程控制领域,在某些应用上取代了在过程控制领域处于统治地位的DCS系统。PLC具有通用性强、使用方便、适应面广、可靠性高、抗干扰能力强、编程简单等特点。[4]
箱式电热炉温度控制系统的研究的开题报告
箱式电热炉温度控制系统的研究的开题报告1. 研究背景箱式电热炉广泛应用于工业生产中的热处理、烧结、热解、烘干等领域,其重要的工作参数之一是控制温度。
传统的温度控制方法主要是利用炉膛内置的温度计进行控制,但是该方法存在精度较低、响应时间长、控制范围不够广等弊端。
因此,研究新型的温度控制系统已成为当前热处理设备研发中的重要方向。
2. 研究目的本研究的目的是设计一种基于单片机和智能控制技术的箱式电热炉温度控制系统,以提高温度控制精度和控制范围,实现自动化控制。
具体目标如下:(1)分析箱式电热炉的温度控制特点和需求,确定控制模式和控制算法。
(2)设计箱式电热炉的温度传感器、控制器和执行器,并搭建可靠的硬件平台。
(3)开发温度控制系统的软件,实现自动化控制、远程监控和数据采集等功能。
(4)进行实验验证,评价温度控制系统的性能指标和应用价值。
3. 研究内容(1)箱式电热炉的温度控制原理和控制算法:通过对箱式电热炉温度的变化规律进行分析和建模,确定适合的控制算法和控制方式。
(2)温度传感器、控制器和执行器的设计:根据控制算法和控制范围的要求,设计合适的温度传感器、控制器和执行器,并制作成可靠的电路电子设备。
(3)温度控制系统的软件开发:采用单片机和智能控制技术,设计相应的软件程序,实现系统的自动化控制、远程监控和数据采集等功能。
(4)系统性能评价和实验验证:通过对温度控制系统进行实验验证,测试系统的控制精度、温度响应速度、稳定性等性能指标,评价其应用价值和技术优劣。
4. 研究意义本研究的主要意义在于:(1)开发基于单片机和智能控制技术的箱式电热炉温度控制系统,提高温度控制精度和控制范围,实现自动化控制和远程监控。
(2)为箱式电热炉的现代化、智能化发展提供了关键技术支持和理论指导。
(3)为热处理工业的节能降耗、提高产品质量和生产效率做出了贡献。
5. 研究方法本研究采用如下研究方法:(1)分析箱式电热炉温度控制的特点和需求,确定控制算法和控制范围。
温度控制系统开题报告
温度控制系统开题报告温度控制系统开题报告一、引言温度控制系统是一种常见的自动化控制系统,广泛应用于工业、农业、医疗等领域。
随着科技的发展和人们对生活质量的要求不断提高,对温度控制系统的需求也日益增加。
本开题报告旨在探讨温度控制系统的设计、原理和应用,以期为相关领域的研究和实践提供参考。
二、温度控制系统的设计原理温度控制系统的设计原理主要包括传感器、执行器、控制算法和人机界面四个方面。
传感器用于感知环境温度,并将其转化为电信号;执行器根据控制算法的指令,调节加热或制冷设备的工作状态,以达到设定的温度;控制算法根据传感器反馈的温度信号,计算出执行器的控制指令;人机界面则提供了用户与温度控制系统进行交互的接口,方便用户设置温度设定值和监控系统运行状态。
三、温度控制系统的应用领域1. 工业领域在工业生产过程中,许多生产设备需要在特定的温度范围内运行,以确保产品的质量和生产效率。
温度控制系统可以实时监测和调节设备的温度,提高生产过程的稳定性和可控性。
2. 农业领域温度对于农作物的生长和发育有着重要的影响。
温度控制系统可以在温室、大棚等农业环境中,调节温度,为农作物提供适宜的生长条件,提高产量和品质。
3. 医疗领域医疗设备和药品的存储、运输和使用都需要在特定的温度条件下进行。
温度控制系统可以确保医疗设备和药品的质量和安全性,提高医疗服务的可靠性和效果。
四、温度控制系统的设计考虑因素在设计温度控制系统时,需要考虑以下因素:1. 精度要求:不同应用领域对温度控制的精度要求不同,需要根据实际需求选择合适的传感器和控制算法。
2. 响应速度:某些应用场景对温度变化的响应速度要求较高,需要选择响应速度较快的传感器和执行器。
3. 稳定性:温度控制系统需要具备较好的稳定性,能够在外界环境变化的情况下保持温度的稳定性。
4. 能耗和成本:温度控制系统的能耗和成本也是设计考虑的重要因素,需要在满足性能要求的前提下,尽可能降低能耗和成本。
电加热炉温度单片机控制系统设计【开题报告】
毕业设计开题报告电子信息工程电加热炉温度单片机控制系统设计1选题的背景、意义传统电加热炉以污染小、便于操作、集成性高、调幅范围广、成本低廉等各种好处慢慢受到使用者的青睐。
但是其对温度的控制上不甚理想,温度差别大、温度难以控制。
为了针对这种情况,应用单片机对电热加热炉进行智能控制的温度系统出现了。
电加热炉温控系统是以数字化控制为基础,以单片机为核心,采用温度变送器桥路和固态继电器控温电路,实现对电炉温度的自动控制。
并采用零点迁移技术和固态继电器控温电路,降低硬件成本,提高温控系统的性能价格比。
炉温信号通过温度检测及变送,变成电信号,与温度设定值进行比较,计算温度偏差和温度的变化率,再由智能控制算法进行推理,并得控制量,可控硅输出部分根据调节电加热炉的输出功率,即改变可控硅管的接通时间,使电加热炉输出温度达到理想的设定值。
电加热炉使用单片机控制炉温有以下几样优点:(1)可以有效地降低控制器硬件成本。
拥有更快的速度、更新功能的新一代微处理机不断上市,硬件价格会变得更便宜。
体积更小、重量更轻、耗能更少是它们的共同优点。
(2)可拥有更高的稳定性,内部集成电路的故障率更低。
(3)数字电路温度漂移更小,受其他参数影响更小,更加稳定。
(4)硬件设计趋于标准化。
在电路集成过程中采取了一些更好的屏蔽设备,能有效避免电路中比较大的瞬态电流、电压引起的电磁干扰麻烦,所以可靠性更高。
(5)采用微处理机的数字控制,使信息的双向传输能力得到很大提高,可随时改变控制参数。
(6)提高了信息存贮、监控、诊断以及分级控制的能力,使伺服系统更趋于智能化。
[1-7]2相关研究的最新成果及动态电加热炉随着科学技术的发展和工业生产水平的提高,已经在冶金、化工、机械等各类工业控制中得到了广泛应用,并且在国民经济中占有举足轻重的地位。
对于这样一个具有非线性、大滞后、大惯性、时变性、升温单向性等特点的控制对象,很难用数学方法建立精确的数学模型,因此用传统的控制理论和方法很难达到好的控制效果。
- 1、下载文档前请自行甄别文档内容的完整性,平台不提供额外的编辑、内容补充、找答案等附加服务。
- 2、"仅部分预览"的文档,不可在线预览部分如存在完整性等问题,可反馈申请退款(可完整预览的文档不适用该条件!)。
- 3、如文档侵犯您的权益,请联系客服反馈,我们会尽快为您处理(人工客服工作时间:9:00-18:30)。
电炉炉温控制系统设计开题报告一、课题的开发背景与需求分析随着现代科学技术的迅猛发展,各个领域对温度控制系统的精度、稳定性等的要求越来越高,控制系统也千变万化。
例如:在冶金工业、化工生产、电力工程、造纸行业、机械制造和食品加工等诸多领域中,人们都需要对各类加热炉、热处理炉、反应炉和锅炉中的温度进行检测和控制等等。
随着电炉广泛应用于各行各业,其温度控制通常采用模拟或数字调节仪表进行调节,但存在着某些固有的缺点。
而采用单片机进行炉温控制,不仅可以大大地提高控制质量和自动化水平,而且具有良好的经济效益和推广价值。
本设计以AT89C51单片机为核心控制器件,以MAX6675作为A/D转换器件,采用闭环直接数字控制算法,通过控制可控硅来控制热电阻,进而控制电炉温度,最终设计了一个满足要求的电炉微型计算机温度控制系统。
二、调研分析经过开题期间的文献查阅和实际情况调研,了解到在电炉炉温控制过程中主要应用AT89C51、MAX6675、LED显示器、LM324比较器等等,而主要是通过K型(镍铬-镍硅)热电偶温度传感器采集环境温度,以单片机为核心控制部件,并通过四位数码管显示实时温度的一种数字温度计。
软件方面采用汇编语言来进行程序设计,使指令的执行速度快,节省存储空间。
为了便于扩展和更改,软件的设计采用模块化结构,使程序设计的逻辑关系更加简洁明了,使硬件在软件的控制下协调运作。
而系统的过程则是:首先,通过设置按键,设定恒温运行时的温度值,并且用数码管显示这个温度值.然后,在运行过程中将采样的温度模拟量送入A/D转换器中进行模拟-数字转换,再将转换后的数字量用数码管进行显示,最后用单片机来控制加热器,进行加热或停止加热,直到能在规定的温度下恒温加热。
三、关键技术与解决方案1、温度传感器的选取目前市场上温度传感器较多,主要有以下几种方案:方案一:选用铂电阻温度传感器。
此类温度传感器线性度、稳定性等方面性能都很好,但其成本较高。
方案二:采用热敏电阻。
选用此类元器件有价格便宜的优点,但由于热敏电阻的非线性特性会影响系统的精度。
方案三:采用K型(镍铬-镍硅)热电偶。
其可测量1312℃以内的温度,其线性度较好,而且价格便宜。
K型热电偶的输出是毫伏级电压信号,最终要将其转换成数字信号与CPU通信。
传统的温度检测电路采用“传感器-滤波器-放大器-冷端补偿-线性化处理-A/D转换”模式,转换环节多、电路复杂、精度低。
在本系统中,采用的是高精度的集成芯片MAX6675来完成“热电偶电势-温度”的转换,不需外围电路、I/O接线简单、精度高、成本低。
MAX6675是MAXIM公司开发的K型热电偶转换器,集成了滤波器、放大器等,并带有热电偶断线检测电路,自带冷端补偿,能将K型热电偶输出的电势直接转换成12位数字量,分辨率0.25℃,工作电压为3.0~5.5V。
温度数据通过SPI端口输出给单片机,其冷端补偿的范围是-20~80℃,测量范围是0~1023.75℃。
表1 MAX6675的引脚功能图当MAX6675的CS引脚从高电平变为低电平时, MAX6675 将停止任何信号的转换并在时钟SCK的作用下向外输出已转化的数据。
相反,当CS从低电平变回高电平时, MAX6675将进行新的转换。
在CS 引脚从高电平变为低电平时, 第一个字节D15 将出现在引脚SO。
一个完整的数据读过程需要16个时钟周期,数据的读取通常在SCK 的下降沿进行。
MAX6675的输出数据为16位,其中D15 始终无用, D14~D3对应于热电偶模拟输入电压的数字转换量, D2用于检测热电偶是否断线(D2为1表明热电偶断开) , D1 为MAX6675 的标识符, D0 为三态。
需要指出的是:在以往的热电偶电路设计中,往往需要专门的断线检测电路, 而MAX6675 已将断线检测电路集成于片内,从而简化了电路设计。
D14~D3 为12 位数据,其最小值为0 ,对应的温度值为0 ℃; 最大值为4095 , 对应的温度值为1023.75 ℃; 由于MAX6675 内部经过了激光修正, 因此, 其转换结果与对应温度值具有较好的线性关系。
温度值与数字量的对应关系为: 温度值= 1023.75 ×转换后的数字量/ 4095。
由于MAX6675 的数据输出为3 位串行接口, 因此只需占用微处理器的3 个I/ O 口。
图2 是以89C51系列单片机为例给出的系统连接图。
使用时, 可用软件模拟同步串行读取过程。
图中串行外界时钟由微处理器的P1.3 提供,片选信号由P1.2 提供,转换数据由P1. 1 读取。
热电偶的模拟信号由T+ 和T-端输入,其中T- 需接地。
MAX6675 的转换结果将在SCK的控制下连续输出,如图1所示。
图1 温度检测电路比较以上三种方案,方案三具有明显的优点,因此选用方案三。
2、键盘显示部分控制与显示电路是反映电路性能、外观的最直观部分,所以此部分电路设计的好坏直接影响到电路的好坏。
方案一:采用可编程控制器8279与数码管及地址译码器74LS138组成,可编程/显示器件8279实现对按键的扫描、消除抖动、提供LED的显示信号,并对LED显示控制。
用8279和键盘组成的人机控制平台,能够方便的进行控制单片机的输出。
方案二:采用单片机AT89C52与4X4矩阵组成控制和扫描系统,并用89C52的P1口对键盘进行扫描,并用总线的方式在P0口接1602液晶来显示炉温和设定值,这种方案既能很好的控制键盘及显示,又为主单片机大大的减少了程序的复杂性,而且具有体积小,价格便宜的特点。
对比两种方案可知,方案一虽然也能很好的实现电路的要求,但考虑到电路设计的成本和电路整体的性能,我们采用方案二。
3、控制电路部分方案一:采用8031芯片,其内部没有程序存储器,需要进行外部扩展,这给电路增加了复杂度。
方案二:采用2051芯片,其内部有2KB单元的程序存储器,不需外部扩展程序存储器。
但由于系统用到较多的I/O口,因此此芯片资源不够用。
方案三:采用AT89C52单片机,其内部有4KB单元的程序存储器,不需外部扩展程序存储器,而且它的I/O口也足够本次设计的要求。
比较这三种方案,综合考虑单片机的各部分资源,因此此次设计选用方案三。
4、报警部分当电炉温度高于上限温度时,报警系统报警。
显示部分可实时显示电炉的炉温值。
多功能控制按键,通过软件控制实现按键的多功能操作,可以完成设定温度基准值和报警取消等功能。
5、PID过程控制部分(1)过程控制的基本概念过程控制――对生产过程的某一或某些物理参数进行的自动控制。
1)模拟控制系统模拟调节器图2 基本模拟反馈控制回路被控量的值由传感器或变送器来检测,这个值与给定值进行比较,得到偏差,模拟调节器依一定控制规律使操作变量变化,以使偏差趋近于零,其输出通过执行器作用于过程。
控制规律用对应的模拟硬件来实现,控制规律的修改需要更换模拟硬件。
2)、微机过程控制系统图3 微机过程控制系统基本框图以微型计算机作为控制器。
控制规律的实现,是通过软件来完成的。
改变控制规律,只要改变相应的程序即可。
3)数字控制系统DDC图4 DDC系统构成框图DDC(Direct Digital Congtrol)系统是计算机用于过程控制的最典型的一种系统。
微型计算机通过过程输入通道对一个或多个物理量进行检测,并根据确定的控制规律(算法)进行计算,通过输出通道直接去控制执行机构,使各被控量达到预定的要求。
由于计算机的决策直接作用于过程,故称为直接数字控制。
DDC系统也是计算机在工业应用中最普遍的一种形式。
4)模拟PID控制系统组成图5 模拟PID 控制系统原理框图PID 调节器是一种线性调节器,它将给定值r(t)与实际输出值c(t)的偏差的比例(P)、积分(I)、微分(D)通过线性组合构成控制量,对控制对象进行控制。
A 、PID 调节器的微分方程⎥⎦⎤⎢⎣⎡++=⎰tDI P dt t de T dt t e T t e K t u 0)()(1)()( 式中 )()()(t c t r t e -=B 、PID 调节器的传输函数 ⎥⎦⎤⎢⎣⎡++==S T S T K S E S U S D D I P 11)()()(5)PID 调节器各校正环节的作用A 、比例环节:即时成比例地反应控制系统的偏差信号e(t),偏差一旦产生,调节器立即产生控制作用以减小偏差。
B 、积分环节:主要用于消除静差,提高系统的无差度。
积分作用的强弱取决于积分时间常数TI ,TI 越大,积分作用越弱,反之则越强。
C 、微分环节:能反应偏差信号的变化趋势(变化速率),并能在偏差信号的值变得太大之前,在系统中引入一个有效的早期修正信号。
(1) 数字PID 控制器1)模拟PID 控制规律的离散化表2 模拟PID 控制规律2)数字PID 控制器的差分方程[]000)()()()1()()()()(u n u n u n u u n e n e T T i e T T n e K n u D I P ni D I P +++=+⎭⎬⎫⎩⎨⎧--++=∑=式中 )()(n e K n u P P = 称为比例项 ∑==ni IPI i e T T K n u 0)()( 称为积分项[])1()()(--=n e n e TT K n u DPD 称为微分项 四、系统完成的功能该系统的被控对象为电炉,采用热阻丝加热,利用大功率可控硅控制器控制热阻丝两端所加的电压大小,来改变流经热阻丝的电流,从而改变电炉炉内的温度。
可控硅控制器输入为0~5伏时对应电炉温度0~500℃,温度传感器测量值对应也为0~5伏,对象的特性为带有纯滞后环节的一阶惯性系统,这里惯性时间常数取T 1=30秒,滞后时间常数取τ=10秒。
该系统利用单片机可以方便地实现对PID 参数的选择与设定,实现工业过程中PID 控制。
它采用温度传感器热电偶将检测到的实际炉温进行A/D 转换,再送入计算机中,与设定值进行比较,得出偏差。
对此偏差按PID 规律进行调整,得出对应的控制量来控制驱动电路,调节电炉的加热功率,从而实现对炉温的控制。
利用单片机实现温度智能控制,能自动完成数据采集、处理、转换、并进行PID 控制和键盘终端处理(各参数数值的修正)及显示。
在设计中应该注意,采样周期不能太短,否则会使调节过程过于频繁,这样,不但执行机构不能反应,而且计算机的利用率也大为降低;采样周期不能太长, 否则会使干扰无法及时消除,使调节品质下降。
五、系统模块设计1、系统硬件设计框图与元器件选择电炉炉温控制系统的硬件选用MCS—51系列89C51作为主控中心。
为实现对系统的处理,将温度传感器采集得到的值,与通过键盘设置的上限及下限值进行比较,系统根据比较结果进行相应的控制操作。