10-应力腐蚀开裂-氢致开裂
10-应力腐蚀开裂-氢致开裂

四、氢致开裂的机理——氢鼓泡(生成氢分子)
氢鼓泡机理示意图
➢ H2S是弱酸,在酸性溶 液中主要以分子形式存在;
➢ 在金属表面阴极反应生 成大量的氢原子;
➢ 氢原子渗入金属内部, 通过扩散达到缺陷处,析出 氢气产生高压;
➢ 非金属夹杂物(如Ⅱ型 MnS)为裂纹的主要形核位 置。
34
抑制氢鼓泡的措施
机械原因:材料受力变形时造成钝化 膜破坏。
17
2、溶解(裂纹扩展)
➢ 裂纹扩展的可能途径:预先存在活性通道和应变产生的 活性通道。 ➢ 活性通道理论(拉伸应力较小时)
大的应力作用在裂缝尖端应力集中,使表面膜破裂。 合金中预先存在一条对腐蚀敏感的通道,在特定介质条 件下成为活性阳极。 形成活性通道可能性有:合金成分结构差异;晶界或亚 晶界;局部应力集中及应变引起阳极晶界区;应变引起表面 膜局部破裂;塑性变形引起的阳极区等。
氢原子
d
氢分子
a
c b
表面铁原子
e
h
+
++
++ h’
f
渗碳体或
g
固溶体碳原子
g’
内部铁原子
钢的氢腐蚀机理模型示意图
31
铁素体晶体结构和显微组织 含碳少
奥氏体晶体结构和显微组织 含碳多
抑制氢腐蚀的措施
➢ 温度:各种钢发生氢腐蚀的起始温度为200oC以上。 ➢ 氢分压:氢分压低时,发生表面脱碳难以鼓泡或开裂。 ➢ 介质气体:含氧或水蒸气时,降低氢进入钢中的速度; 含H2S时,孕育期变短。 ➢ 合金元素:碳含量增加,孕育期变短;加入形成碳化物 金属(Ti、Nb、Mo、W、Cr),减少甲烷生成;MnS为裂 纹源的引发处,应去除。 ➢ 热处理和冷加工。
腐蚀及开裂机理

腐蚀减薄1 盐酸(HCl)腐蚀盐酸(HCl)腐蚀在大多数普通精炼工艺中都受到关注。
不同浓度的盐酸对许多普通制造材料都产生侵蚀作用,而且常常存在于自然条件中。
特别是当它与会更容易发生腐蚀。
奥氏体不锈钢常常发生点蚀,而且会形成隙间腐蚀及/或氯致应力腐蚀裂纹。
如果含有氧化剂,或不经过退火处理(主要是指将材料曝露于高温一段很长时间后,然后再慢慢冷却的热处理制程。
主要目的是:(1)释放应力,(2)增加材料延展性和韧性,(3)产生特殊显微结构。
),则会加快镍合金的腐蚀。
人们关注的是主要精炼设备上的盐酸腐蚀,它包括原油蒸馏,氢处理,和催化重整。
在原油蒸馏中水解镁和钙氯盐后形成了HCl盐酸。
在氢处理设备中,进料口处有机氯化物加氢作用时会产生HCl,或者HCl 随着碳氢化合物或氢进入设备,然后在流体管道中与水浓缩在一起。
在催化重整设备中,氯化物会被催化剂和碳氢化合物带走,导致流体管道或再生系统发生盐酸腐蚀。
2 高温硫/环烷酸腐蚀高温硫腐蚀是一种常见的均匀腐蚀,当温度超过400ºF就会发生。
这种腐蚀在加工油的过程中,常与环烷酸腐蚀同时发生。
而环烷酸腐蚀通常为局部腐蚀。
这些自然存在的物质可能本身就具有腐蚀性,当热分解转化成硫化氢后也会产生腐蚀。
在加氢设备中存在氢元素和催化剂,使硫化物转变为H2S。
由于含有硫物质,许多原油会产生环烷酸。
在蒸馏过程中,这些酸易浓缩成高沸点的成分,例如常压下的重柴油,常压残油和真空柴油。
这些酸也可能存在于真空残油中,酸性较低的多产生点蚀,而酸性较高的产生槽状或沟状腐蚀,而且腐蚀速度更快。
环烷酸可以改变或破坏材料的保护层(硫化物或氧化物),从而持续加快硫化腐蚀速率,甚至会直接破坏原材料。
3高温H2S/H2腐蚀高温H2S/H2腐蚀是一种常见的均匀腐蚀,当温度超过400ºF时就会发生。
这种硫化物腐蚀不同于高温硫/环烷酸腐蚀。
H2S/H2腐蚀发生在氢加工设备中,例如氢除硫工艺和氢裂化装置中,当硫化物通过催化剂与氢气反应可转化为硫化氢。
应力腐蚀
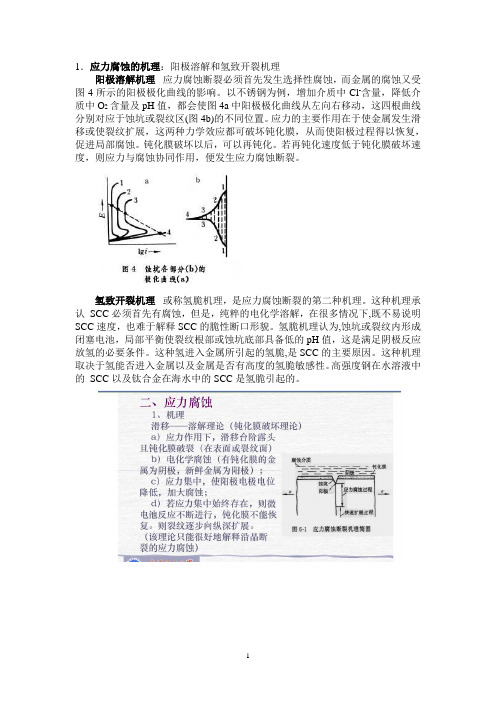
1.应力腐蚀的机理:阳极溶解和氢致开裂机理阳极溶解机理应力腐蚀断裂必须首先发生选择性腐蚀,而金属的腐蚀又受图4所示的阳极极化曲线的影响。
以不锈钢为例,增加介质中Cl-含量,降低介质中O2含量及pH值,都会使图4a中阳极极化曲线从左向右移动,这四根曲线分别对应于蚀坑或裂纹区(图4b)的不同位置。
应力的主要作用在于使金属发生滑移或使裂纹扩展,这两种力学效应都可破坏钝化膜,从而使阳极过程得以恢复,促进局部腐蚀。
钝化膜破坏以后,可以再钝化。
若再钝化速度低于钝化膜破坏速度,则应力与腐蚀协同作用,便发生应力腐蚀断裂。
氢致开裂机理或称氢脆机理,是应力腐蚀断裂的第二种机理。
这种机理承认SCC必须首先有腐蚀,但是,纯粹的电化学溶解,在很多情况下,既不易说明SCC速度,也难于解释SCC的脆性断口形貌。
氢脆机理认为,蚀坑或裂纹内形成闭塞电池,局部平衡使裂纹根部或蚀坑底部具备低的pH值,这是满足阴极反应放氢的必要条件。
这种氢进入金属所引起的氢脆,是SCC的主要原因。
这种机理取决于氢能否进入金属以及金属是否有高度的氢脆敏感性。
高强度钢在水溶液中的SCC以及钛合金在海水中的SCC是氢脆引起的。
2.应力腐蚀开裂的断口形貌:穿晶断口开裂图3.氢鼓泡产生机理,文字图通过实验和理论分析研究了氢鼓泡形核、长大和开裂的过程. 在充氢试样中发现直径小于100 nm未开裂的孔洞, 它们是正在长大的氢鼓泡, 也发现已开裂的鼓泡以及裂纹多次扩展导致破裂的鼓泡.分析表明, 氢和空位复合能降低空位形成能, 从而使空位浓度大幅度升高, 这些带氢的过饱和空位很容易聚集成空位团.H在空位团形成的空腔中复合成H2就使空位团稳定, 成为氢鼓泡核.随着H 和过饱和空位的不断进入, 鼓泡核不断长大, 内部氢压也不断升高.当氢压产生的应力等于被氢降低了的原子键合力时, 原子键断开, 裂纹从鼓泡壁上形核.图5 氢鼓泡形核、长大示意图(a) 空位V和原子氢H聚集成为空位-原子氢集团; (b) 原子氢在空位团中复合成分子氢H2, 使其稳定, 鼓泡核形成; (c) 空位和氢不断进入鼓泡核使其长大; (d) 当鼓泡核内氢压产生的应力等于原子键合力时, 在鼓泡壁形成裂纹首先, 氢(H)进入金属和空位(V)复合, 使空位形成能大大降低, 从而大幅度升高空位浓度, 这些过饱和空位容易聚集成空位团. 当4个或以上的空位或空位-氢复合体(V-H)聚集成空位四面体或空位团时, 内部形成空腔, 如图5(a). 空位所带的氢在空腔中就会复合成H2, 形成氢压. 由于室温时H2不能分解成H, 故含H2的空位团在室温是稳定的, 它就是鼓泡核, 如图5(b). 随着H和空位不断进入鼓泡核, 就导致鼓泡在充氢过程中不断长大, 同时氢压不断升高, 如图5(c). 当鼓泡中的氢压在内壁上产生的应力等于被氢降低了的原子键合力时, 原子键断裂, 裂纹沿鼓泡壁形核, 如图5(d). 随着氢的不断进入, 裂纹扩展, 直至鼓泡破裂4.氢进入金属材料的途径P1295.氢致脆断类型:可逆和不可逆,第一类和第二类6.第一类氢脆里的三种形式:氢腐蚀,氢鼓泡、白点,氢化物型氢脆7.第二类氢脆两种形式:应力诱发氢化物型氢脆,可逆氢脆8.氢脆的特征:氢蚀,白点宏观断口形貌9.氢的延迟断裂,氢致开裂过程10.氢致脆断的断口形貌特征P13111.减少氢脆倾向的途径:降低内氢的措施,降低环境氢的活性12.氢脆的特点(1)实验室中识别氢脆与应力腐蚀的一种办法是,当施加一小的阳极电流,如使开裂加速,则为应力腐蚀,而当施加一小阴极电流,使开裂加速者则为氢脆。
关于抗氢致开裂开裂及抗硫化物应力腐蚀开裂试验R-HIC钢板的问答

通常抗氢致开裂HIC(Hydrogen Induced Crack)主要是针对低碳高强度结构钢制压力管线讲的( 现代管线钢属于低碳或超低碳的微合金化钢)。
目前国内生产的此类专用钢(抗HIC专用钢)主要材料牌号有:16MnR(HIC),20R(HIC),SA516(HIC)。
该类钢的碳当量可用Ce=C+Mn6+(Cr+Mo+V)5+(Ni+Cu)15计算。
质保书中C:0.022,Mn:1.05,Cr:18.20,Ni:8.32材料成分大致符合不锈钢00Cr19Ni10(GBT1220—1992)主要元素成分要求。
提供的是00Cr19Ni10或类似材质,应该没有太大问题。
参考资料:关于提高提高管线钢抗HIC能力的措施提高管线钢抗HIC能力的措施有成份设计、冶炼控制、连铸工艺、控轧控冷等四个方面。
展开来说,主要有三点:提高钢的线纯净度。
采用精料及高效铁水预处理(三脱)及复合炉外精炼,达到S≤0.001%,P≤0.010%,[O]≤20ppm,[H]≤1.3ppm。
同时采用Ca处理。
②晶粒细化。
主要通过微合金化和控轧工艺使晶粒充分细化,提高成分和组织的均匀性。
为此,钢水和连铸过程要电磁搅拌;连铸过程采用轻压下技术;多阶段控制轧制及强制加速冷却工艺;Tio处理,使得钢获得优良的显微组织和超细晶粒,最终组织状态是没有带状珠光体的针状铁素体或贝氏体。
③昼降低含C量(C ≤0.06%),控制Mn含量,并添加Cu和Ni。
从炼钢来看,宝钢、武钢、鞍钢、攀钢、太钢等企业能生产不同等级的管线钢种,目前国内能生产X42、X52、X60、X65、X70等,X70目前在试用。
管线钢国产化程度大幅度提高,产品质量有了显著的改进,产品的成份控制、强度、韧性、晶粒度、焊接性能等均已接近或达到国外同类产品的水平。
高S原油加工过程中硫腐蚀及防护选材准则 thread-4029-1-1.html(作者前言):2001年1月,中国石化科技开发部邀请英国壳牌石油公司材料专家霍普金申(音译)在南京就“高S原油加工过程中硫腐蚀及防护选材准则”做了讲座。
应力腐蚀断裂
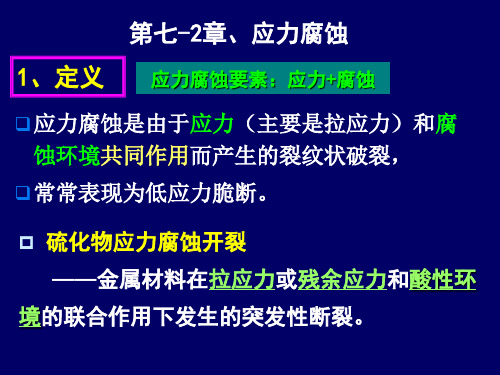
裂纹扩展速率(da/dt)与K1的关系——三阶段:
lg da dt
Ⅰ
Ⅱ
Ⅲ
K1SCC
K1C K1
图2 裂纹扩展速率(da/dt)与K1的关系
试验原理
疲劳裂纹扩展速率da/dN表达式
② 当整体金属仍是弹性 变形状态时,裂纹尖 端的前沿为塑性区。
③ 裂纹尖端前具有三向 拉伸应力区,氢可在 此处富集。
裂纹尖端易于继续阳 极溶解,裂纹壁上阴 极反应析出的氢易于 进入金属。
位错与氢结合;运动 的位错快速输送氢。
指出富集部位,三向 拉伸区较疏松,富集 氢可降低应变能。
硫化物应力(SSC)腐蚀
K1
=
P
C3
(a W
B a
)
3)硫化氢环境门限应力强度因子KISCC的测定
材料在硫化氢环境下的 抗断裂特性
实验方法 用螺栓对试样加载P0 ,
用引伸计测量加载过程 中试样裂纹开口位移, 记录中止时位移量V0
试件放入H2S溶液中,经过一定 时间,试件裂纹扩展 ,螺栓力
松弛,载荷下降, 则KI下降,
三向受拉处,物质最稀松,有空穴产生,氢集中 在空穴中。
焊接时,氢离子结合呈氢原子或氢分子,形 成107的大气压。高的压力使钢材表面出现 氢鼓包,内部产生裂纹。
要求焊接时焊条要烘干,不得受潮。
3.硫化物应力腐蚀性能试验方法
美国腐蚀工程协会NACE TM0177—2005规定了四种标准 方法:
W - a 2.5( Ke )2 0.2
K1SCC/s>0.3,视为合格
应力腐蚀和氢脆

分子态
化合态
▪ 在一般情况下,氢以间隙原子状态固溶在金属中, 对于大多数工业合金,氢的溶解度随温度降低而 降低。
▪ 氢在金属中也可通过扩散聚集在较大的缺陷(如空 洞、气泡、裂纹等)处以氢分子状态存在。
▪ 氢还可能和一些过渡族、稀土或碱土金属元素作 用生成氢化物,或与金属中的第二相作用生成气 体产物,如钢中的氢可以和渗碳体中的碳原子作 用形成甲烷等。
▪ 解放初期黄铜子弹壳开裂现象:原因是润滑用肥皂水中 含微量铵离子。
二、应力腐蚀产生的条件
▪ (1)只有在拉伸应力作用下才能引起应力腐蚀开 裂(近年来,也发现在不锈钢中可以有压应力引起)。 这种拉应力可以是外加载荷造成的应力,但 主要是各种残余应力,如焊接残余应力、热处理 残余应力和装配应力等。 据统计,在应力腐蚀开裂事故中,由残余应 力所引起的占80%以上,而由工作应力引起的则 不足20%。
▪ 当KⅠ值降低到某一临界值(图中为38MPa.m1/2) 时,应力腐蚀开裂实际上就不发生了。这一KⅠ 值称之为应力腐蚀临界场强度因子,也称应力
腐蚀门槛值,以 KⅠSCC表示(SCC表示应力腐蚀 断裂)。
应力腐蚀临界应力场强度因子KISCC
✓试样在特定化学介质中不发生应力腐蚀断裂的 最大应力场强度因子,也称为应力腐蚀门槛值。 ✓表示含有宏观裂纹的材料在应力腐蚀条件下的 断裂韧度。 ✓一定的材料与介质,KISCC值恒定。是金属材料 的一个力学性能指标。
▪ 钛合金(Ti-8Al-1Mo-1V)的预制裂纹试祥在恒载荷作用下,于 3.5%Nacl水溶液中进行应力腐蚀试验的结果。
Ti-8Al-1Mo-1V预制裂纹试祥的KⅠ-tf曲线
▪ 该合金的KⅠc=100MPa.m1/2,在3.5%盐水中, 当初始KⅠ值仅为40 MPa.m1/2时,仅几分钟试样 就破坏了。如果将KⅠ值稍微降低,则破坏时间 可大大推迟。
金属在h2s环境中抗硫化应力开裂和应力开裂及应力腐蚀开裂的试验方法
金属在h2s环境中抗硫化应力开裂和应力开裂及应力腐蚀开裂的试验方法全文共四篇示例,供读者参考第一篇示例:金属在H2S环境中的抗硫化应力开裂和应力开裂以及应力腐蚀开裂是工程材料研究中一个重要的课题。
随着工业发展的进步,金属在硫化氢环境下遇到的腐蚀问题越来越严重,因此对金属的抗硫化能力进行有效评估和研究显得尤为重要。
本文将重点介绍金属在H2S环境中抗硫化应力开裂和应力开裂以及应力腐蚀开裂的试验方法。
一、抗硫化应力开裂试验方法1.慢应变速率拉伸试验(SSRT)慢应变速率拉伸试验是一种常用的用于评估金属抗硫化应力开裂能力的试验方法。
在试验中,将金属样品置于硫化氢环境中,通过施加不同应变速率的拉伸载荷来评估金属的应力开裂敏感性。
通过观察试验样品的断口形貌,可以判断金属在H2S环境中的抗硫化应力开裂能力。
2.冲击试验(Charpy V-notch Impact Test)Charpy V-notch冲击试验是一种常用的测试金属在低温下的韧性能力的方法,也可以用于评估金属在H2S环境中的抗硫化应力开裂能力。
通过在冲击试验中引入硫化氢气体,可以模拟实际工作环境下的应力开裂情况,进一步评估金属的性能。
2.环境应力开裂试验(Environmental Stress Cracking Test)2.断裂力学分析(Fracture Mechanics Analysis)断裂力学分析是一种常用的方法,用于评估金属在应力腐蚀开裂条件下的裂纹扩展行为。
通过对金属样品的裂纹形貌和裂纹扩展速率等参数进行分析,可以评估金属在应力腐蚀开裂条件下的裂纹扩展机制和发展规律。
第二篇示例:金属在H2S环境中抗硫化应力开裂和应力开裂及应力腐蚀开裂是材料科学和工程领域一个重要而复杂的问题。
H2S是一种常见的硫化氢气体,常常存在于石油、天然气等工业生产中。
金属材料在H2S环境中受到应力作用时容易发生各种腐蚀和开裂现象,这对于工程结构的安全性和可靠性都提出了严峻的挑战。
应力腐蚀和氢脆
在纵向断面上,裂纹呈现近似圆形或椭圆形的银白色斑点, 故称白点;在横断面宏观磨片上,腐蚀后则呈现为毛细裂 纹,故又称发裂。
10CrNiMoV钢锻材调质后纵断面上的白点形貌
如炼油过程中的一些加氢反应装置;石油化工生产
过程中的甲醇合成塔等。
二、氢的来源
按照氢的来源可将氢脆分为内部氢脆和环境氢脆。
⑴内部氢脆:材料在使用前内部已含有足够的氢
并导致了脆性,它可以是材料在冶炼、热加工、 热处理、焊接、电镀、酸洗等制造过程中产生。
严格控制电镀工艺,镀后还要通过 对电镀件长时间的烘烤,使游离状 的氢得以释放,减轻对镀件产品的 影响。
M——裂纹截面上的弯矩, M=F·。 L B——试样厚度。 W—— 试样宽度。 a—— 裂纹长度。
1/ 2
4.12M KI 3/ 2 BW
1 3 a a3
能力知识点3 提高应力腐蚀抗力的措施
降低和消除应力
在加工(如热处理、焊接、电镀等)和装配过程中, 应尽量避免产生残余拉应力,或者在加工中采取 必要的消除应力措施。 制备和装配时尽量使结构具有最小的应力集中系 数,并使其与介质接触部分具有最小的残余拉应 力。
三、氢脆的类型和特点
氢可通过不同的机制使金属脆化,因氢脆的种类 很多,现将常见的几种氢脆现象从其特征简介如 下。
1.氢蚀
这是由于氢与金属中的第二相作用生成高压气体,使基体 金属晶界结合力减弱而导致金属脆化。 如在石油高压加氢及液化石油气的设备中,在300~ 500℃时,由于氢与钢中的碳化物作用生成高压的CH4气 泡,当气泡在晶界上达到一定密度后,金属的塑性将大幅 度降低。 这种氢脆现象的断裂源产生在工件与高温、高压氢气相接 触的部位。 宏观断口形貌:呈氧化色,颗粒状;微观:晶界明显加宽, 呈沿晶断裂。
10-应力腐蚀开裂-氢致开裂
应力腐蚀开裂很普遍,化工
行业约占四分之一。危害性极大,
如飞机失事,桥梁断裂,油气管
爆炸。
6
304不锈钢在沸腾45%MgCl 溶液中的穿晶裂纹
敏化304不锈钢在室温连多硫 酸溶液中的晶间裂纹
应力腐蚀的裂纹有晶间型、穿晶型和混合型三种类型。
二、SCC发生的条件和特征
1、力学特征
应力腐蚀是应力和环境腐蚀的联合作用造成的破坏。
1、贫铬理论—晶界碳化物析出(过渡期,固溶处理可消除)
晶界碳化物析出示意图
敏化热处理 不锈钢在弱氧化性介质中发生的 晶间腐蚀,可以用贫铬理论解释。
奥氏体不锈钢(含碳相对高) 铁素体不锈钢(含碳、氮低) 晶间腐蚀最易发生在活化—钝化 过渡区。
3
2、阳极相理论—晶界σ相析出并溶解 (过钝化区,固溶处理不能消除)
可逆氢脆:含氢金属在高速变形时并不显示脆性,而在缓慢
变形时由于氢逐渐向应力集中处富集,在应力与氢交互作用下形成 裂纹形核、扩展,最终导致脆性断裂。
28
2、第一类氢脆:氢脆的敏感性随应变速率增加而增加,即材 料在加载前存在某种裂纹源,加载后在应力作用下加快了裂 纹的形成与扩展。 氢腐蚀:氢在高温高压下与金属中第二相发生化学反应,生成
如锅炉钢在碱性溶液中的碱脆 低碳钢在硝酸溶液中的硝脆 奥氏体不锈钢在含氯离子溶液中的氯脆 黄铜在氨气氛中的氨脆 高强度钢在酸性或中性NaCl中的氢脆
特定的电位范围:应力腐蚀、点蚀和缝隙腐蚀的发展有 一个共同点—均以“闭塞电池”机制为推动力。
10
合金的应力腐蚀断裂电位区(阴影)
铁的裂纹pH值及其电位分布
电位(V)
γ相
1.5
1.0
σ相
0.5
应力腐蚀断裂
应力腐蚀断裂一.概述应力腐蚀是材料、或在静主要是拉应力和腐蚀的共同作用下产生的失效现象..它常出现于用钢、黄铜、高强度铝合金和中;凝汽器管、矿山用钢索、飞机紧急刹车用高压气瓶内壁等所产生的应力腐蚀也很显着..常见应力腐蚀的机理是:零件或构件在应力和腐蚀介质作用下;表面的氧化膜被腐蚀而受到破坏;破坏的表面和未破坏的表面分别形成阳极和阴极;阳极处的金属成为离子而被溶解;产生电流流向阴极..由于阳极面积比阴极的小得多;阳极的电流密度很大;进一步腐蚀已破坏的表面..加上拉应力的作用;破坏处逐渐形成裂纹;裂纹随时间逐渐扩展直到断裂..这种裂纹不仅可以沿着金属晶粒边界发展;而且还能穿过晶粒发展..应力腐蚀过程试验研究表明:当金属加上阳极电流时可以加剧应力腐蚀;而加上阴极电流时则能停止应力腐蚀..一般认为压应力对应力腐蚀的影响不大..应力腐蚀的机理仍处于进一步研究中..为防止零件的应力腐蚀;首先应合理选材;避免使用对应力腐蚀敏感的材料;可以采用抗应力腐蚀开裂的不锈钢系列;如高镍奥氏体钢、高纯奥氏体钢、超纯高铬铁素体钢等..其次应合理设计零件和构件;减少..改善腐蚀环境;如在腐蚀介质中添加缓蚀剂;也是防止应力腐蚀的措施..采用金属或非金属保护层;可以隔绝腐蚀介质的作用..此外;采用阴极保护法见也可减小或停止应力腐蚀..本篇文章将重点介绍应力腐蚀断裂失效机理与案例研究;并分析比较应力腐蚀断裂其他环境作用条件下发生失效的特征..;由于应力腐蚀的测试方法与本文中重点分析之处结合联系不大;故不再本文中加以介绍..二.应力腐蚀开裂特征1引起应力腐蚀开裂的往往是拉应力..这种拉应力的来源可以是:1. 工作状态下构件所承受的外加载荷形成的抗应力..2. 加工;制造;热处理引起的内应力..3. 装配;安装形成的内应力..4. 温差引起的热应力..5. 裂纹内因腐蚀产物的体积效应造成的楔入作用也能产生裂纹扩展所需要的应力..2每种合金的应力腐蚀开裂只对某些特殊介质敏感..一般认为纯金属不易发生应力腐蚀开裂;合金比纯金属更易发生应力腐蚀开裂..下表列出了各种合金风应力腐蚀开裂的环境介质体系;介质有特点:即金属或合金可形成纯化膜;弹介质中有有破坏纯化膜完整性的离子存在..而且介质中的有害物质浓度往往很低;如大气中微量的H 2S 和NH 3可分别引起钢和铜合金的应力腐蚀开裂..空气中少量NH 3是鼻子嗅不到的;却能引起黄铜的氨脆..再如奥氏体不锈钢在含有几个ppm 氯离子的高纯水中就会出现应力腐蚀开裂..再如低碳钢在硝酸盐溶液中的“硝脆”;碳钢在强碱溶液中的“碱脆”都是给定材料和特定环境介质结合后发生的破坏..氯离子能引起不锈钢的应力腐蚀开裂;而硝酸根离子对不锈钢不起作用;反之;硝酸根离子能引起低碳钢的应力腐蚀开裂;而氯离子对低碳钢不起作用..表1.常见材料应力腐蚀开裂发生的介质3应力腐蚀开裂是材料在应力和环境介质共同作用下经过一段时间后;萌达到生裂纹;裂纹扩展到临界尺寸;此时由于裂纹尖端的应力强度因子KI;发生失稳断裂..即应力腐蚀开裂过程分为三个阶段:材料的断裂韧性KIc裂纹萌生;裂纹扩展;失稳断裂..1.裂纹的萌生裂纹源多在保护膜破裂处;而膜的破裂可能与金属受力时应力集中与应变集中有关;此外;金属中存在孔蚀;缝隙腐蚀;晶间腐蚀也往往是SCC 裂纹萌生处..萌生期长短;少则几天;长达几年;几十年;主要取决于环境特征与应力大小..2.裂纹扩展应力腐蚀开裂的裂纹扩展过程有三种方式..应力腐蚀开裂裂纹的扩展速率da/dt与裂纹尖端的应力强度因子K1的关系具有图示的三个阶段特征..在第一阶段da/dt随K1降低而急剧减少..当KI降到Kiscc以下时应力腐蚀开裂裂纹不再扩展..在第二阶段;裂纹扩展与应力强度因子KI大小无关;主要受介质控制..在这阶段裂纹出现宏观和微观分枝..但在宏观上;裂纹走向与抗应力方向是垂直的..第三阶段为失稳断裂;纯粹由力学因素KI 控制;da/dt随KI增大迅速增加直至断裂..3应力腐蚀开裂属于脆性断裂..即使塑性很高的材料也是如此..其断口呈多种形貌..有沿晶断裂;准解理;韧性断裂等..图1.应力腐蚀开裂da/dt与KI关系三.应力腐蚀开裂机制应力腐蚀开裂现象很多;目前尚未有统一的见解;不同学派的观点可能从电化学;断裂力学;物理冶金进行研究而强调了它们的作用..1电化学理论1; 活性通道理论该理论认为;在金属或合金中有一条易于腐蚀的基本上是连续的通道;沿着这条活性通道优先发生阳极溶解..活性通道可以是晶界;亚晶界或由于塑性变形引起的阳极区等..电化学腐蚀就沿着这条通道进行;形成很窄的裂缝裂纹;而外加应力使裂纹尖端发生应力集中;引起表面膜破裂;裸露的金属成为新的阳极;而裂纹两侧仍有保护膜为阴极;电解质靠毛细管作用渗入到裂纹尖端;使其在高电流密度下加速裂尖阳极溶解..该理论强调了在拉应力作用下保护膜的破裂与电化学活化溶解的联合作用..2.快速溶解理论..该理论认为活性通道可能预先是不存在的;而是合金表面的点蚀坑;沟等缺陷;由于应力集中形成裂纹;裂纹一旦形成;其尖端的应力集中很大;足以使其尖端发生塑性变形到一个塑性;该塑性具有很大的溶解速度..这种理论适用于自纯化金属;由于裂纹两侧纯化膜存在;更显示裂纹尖端的快速溶解;随着裂纹向前发展;裂纹两侧的金属重新发生纯化再纯化;只有当裂纹中纯化膜的破裂和再纯化过程处于某种同步条件下才能使裂纹向前发展;如果纯化太快就不会产生裂纹进一步腐蚀;若再纯化太慢;裂纹尖端将变圆;形成活性较低的蚀孔..图2.快速溶解理论机理图3.膜破裂理论该理论认为金属表面有一层保护膜吸附膜;氧化膜;腐蚀产物膜;在应力作用下;被露头的滑移台阶撕破;使表面膜发生破裂图3b局部暴露出活性裸金属;发生阳极溶解;形成裂纹图3c..同时外部保护膜得到修补;对于自纯化金属裂纹两侧金属发生再纯化;这种再纯化一方面使裂纹扩展减慢;一方面阻止裂纹向横向发展;只有在应力作用下才能向前发展..4.闭塞电池理论该理论是在活性通道理论的基础上发展起来的..腐蚀就先沿着这些活性通道进行;应力的作用在于将裂纹拉开;以免被腐蚀产物堵塞;但是闭塞电池理论认为;由于裂纹内出现闭塞电池而使腐蚀加速这类似于缝隙腐蚀即在裂纹内由于裂纹内金属想要发生水解:FeCl2+2H2O→FeOH2+2HCl;使Ph值下降;甚至可能产生氢;外部氢扩散到金属内部引起脆化..闭塞电池作用是一个随催化腐蚀过程;在拉应力作用下使裂纹不断扩展直至断裂..2吸氢变脆理论..该理论是从一些塑性很好的合金在发生应力腐蚀开裂时具有脆性断裂的特征提出的变脆是否由氢脆引起该理论认为裂纹的形成与发展主要与裂纹尖端氢被引入晶格有关;如奥氏体不锈钢在裂纹尖端;Cr阳极氧化生成CrO3使其酸度增大..2Cr+3H2O→Cr2O3+6H++6e..当裂纹尖端的电位比氢的平衡电位负时;氢离子有可能在裂纹尖端被还原;变成吸附的氢原子;向金属内部扩展;从而形成氢脆..3应力吸附破裂理论..该理论认为由于环境中某些破坏性组分对金属表面内表面的吸附;削弱了金属原子间的结合力;在抗拉力作用下引起破裂..四.影响应力腐蚀开裂的因素影响应力腐蚀开裂的因素可以大致分为环境因素、应力因素以及冶金因素;现整理为图4框图所示..图4.影响应力腐蚀的因素五、应力腐蚀的防护措施从应力腐蚀的机理来看;从材料与环境介质、力学因素三方面因素考虑防护措施..从防护的方法来分防止应力腐蚀应从减少腐蚀和消除拉应力两方面来采取措施..1.要尽量避免使用对应力腐蚀敏感的材料;2.在设计设备结构时要力求合理;尽量减少应力集中和积存腐蚀介质;3. 是在加工制造设备时;要注意消除残余应力..六、应力腐蚀断裂的典型案例高压热交换器管的破裂案例1: CO2材质: 0Cr18Ni10尺寸及结构: 19× 1.6;共232根;每根长8.5米..管与管板采用胀焊连接..工作环境:..进口温度:180℃;管内:湿CO2出口温度40~50℃;压力:80~90kgf..管外:冷却水含氧6~10ppm;Cl-80~100ppm进口温度:32~34 ℃;出口温度:80 ℃;压力:4 kgf..损坏情况:运转2月后发现泄漏;运转3个月检修时发现70多根管子破裂..破裂多发生在高温侧管板缝隙附近..分析检验:裂纹从管外壁产生;向内壁扩展;属穿晶型应力腐蚀裂纹特征..断口扫描电镜发现;破裂是典型的脆性解理断裂;是由氯化物应力腐蚀造成的..图5. 67管与管板连接及管上应力腐蚀裂纹示意图ab c图6. 管板缝隙处破裂的管子案例二:化肥厂冷却器管的破损材质:00Cr18Ni10 尺寸: 19× 2;管外-冷却水工作环境:管内-高温CO2损坏情况:运转不到半年;发生多处破损事故..分析检验:裂纹以横裂为主..裂纹由外壁产生;向内壁扩展;属典型的穿晶型应力腐蚀裂纹..图7.冷却器管外部裂纹特征案例三:金属材料中氢致开裂断口案例材质:33CrNiMoA工艺情况:850℃保温2h后炉冷;超声波探伤发现内部有缺陷;图1:经淬火处理浸蚀方法:图8:未浸蚀;图9:50%盐酸水溶液浸蚀;图10:4%硝酸酒精溶液浸蚀组织说明:图8:20mm切片压开裂成纵向断口;其中有许多圆形、卵形白斑———即白点缺陷..白点表面呈粗晶状..图9:横向截面低倍组织形貌;有许多辐射状短裂纹;它们在纵向即为白点..图3:裂纹处横向金相试样形貌;白点为锯齿状裂纹;裂纹细小、刚挺、穿晶..白点产生的原因;一般认为与钢中氢含量较高有关..由于钢中氢原子脱溶、聚集结合成氢分子;产生极大压力;在热加工中与热应力、组织应力叠加造成裂纹..图8. 20mm切片压开裂成纵向断口图9. 横向截面低倍组织形貌图10. 4%硝酸酒精溶液浸蚀组织图材料: 20MnMo工艺情况:锻造后空冷;冲击试验组织说明:冲击断口试样;断口上有白点;透射电镜碳二次复型图像;白点区为准解理断裂;通常称之为氢致解理..图11. 冲击断口试样断口组织图材料:20钢螺钉工艺情况:冷镦成型合镀锌组织说明:螺钉断口..螺钉经酸洗后表面电镀锌;在安装时发生断裂..断口宏观形貌光滑平坦..扫描电镜观察具有准解理特征;并有发纹等;属氢脆断裂..低碳钢虽对氢脆不像高强度钢那样敏感;但如酸洗后未经除氢处理;也有可能会引起氢脆..图12.螺钉断口组织图材料:35钢螺钉工艺情况:热锻、调质后镀锌组织说明:螺钉断口..螺钉经酸洗后表面电镀锌;在安装时发生断裂..断口呈脆性特征;微观形貌为准解理断裂;并有发纹等特征;为氢脆断裂..图13.螺钉断口组织图材料:65Mn工艺情况:淬火、回火后酸洗、电镀组织说明:由65Mn钢制作的弹簧片;在安装时发生断裂..断口为典型的冰糖状沿晶断裂;在断裂的晶面上有细小的爪状纹及发纹等特征..此为高强度钢氢脆断口的特征..高强度钢在酸洗电镀后必须进行除氢处理;除氢不及时或除氢不彻底均会导致氢脆..图14.65Mn钢制作的弹簧片断口形貌材料:65Mn工艺情况:淬火、回火后酸洗、电镀组织说明:酸洗及电镀过程中的氢进入钢中后常沿晶界处聚集;导致晶界脆化;形成沿晶断裂..氢在扩散、聚集过程中留下发纹、爪状纹等特征..氢脆断裂时在微区局部晶界上因氢损伤较轻;故断裂时在局部区域能观察到韧窝;见图中上部区..图15. 65Mn钢断口形貌材料:1Cr18Ni9Ti工艺情况:冷变形后去应力退火组织说明:在奥氏体不锈钢的应力腐蚀断口上除河流花样外还有羽毛状及扇形状花样;这种花样通常在经变形而使晶粒拉长的材料中出现..图16.奥氏体不锈钢的应力腐蚀断口材料:1Cr18Ni9Ti工艺情况:固溶处理组织说明:应力腐蚀失效断口..奥氏体不锈钢在氯离子环境下使用造成的应力腐蚀的断口形貌;有河流花样特征..这是由于应力腐蚀裂纹沿一定的晶面扩展;通常发生开裂的主要晶面有{100}、{110}、{111}等..图中点状小颗粒为断口表面上的腐蚀产物;用能谱仪分析通常能检测到氯元素..图17. 奥氏体不锈钢在氯离子环境应力腐蚀的断口形貌材料:1Cr18Ni9Ti工艺情况:固溶处理组织说明:氯离子环境下的应力腐蚀断口上的泥状花样;其特征似干裂的泥块..通常在腐蚀产物堆积较厚的区域出现;是腐蚀产物开裂的特征..图18.氯离子环境下的应力腐蚀断口泥状花样材料:1Cr18Ni9Ti工艺情况:固溶处理组织说明:氯离子环境下的应力腐蚀断口..由于介质中氯离子对断口的浸蚀;在某些区域会出现腐蚀坑..这种腐蚀坑常呈现规则的形状;类似于金相位错腐蚀坑..图中所示腐蚀坑为正方形;可说明此腐蚀坑所在的开裂晶面为{100}晶面..图19. 氯离子应力腐蚀断口几何形状的腐蚀坑特征七.参考文献1.中国钢企百科;2.肖纪美;氢致材料开裂的分析方法;3.王吉会;郑俊萍;刘家臣;黄定海;材料力学性能 ..。
- 1、下载文档前请自行甄别文档内容的完整性,平台不提供额外的编辑、内容补充、找答案等附加服务。
- 2、"仅部分预览"的文档,不可在线预览部分如存在完整性等问题,可反馈申请退款(可完整预览的文档不适用该条件!)。
- 3、如文档侵犯您的权益,请联系客服反馈,我们会尽快为您处理(人工客服工作时间:9:00-18:30)。
高压气体而引起材料脱碳、内裂纹和鼓泡现象。 形成高压,导致表面鼓泡或内部裂纹。
裂纹源而引发氢脆。
巴氏合金表面的氢鼓泡
巴氏合金表面呈阶梯状的裂纹
30
四、氢致开裂的机理——氢腐蚀(生成甲烷、硅烷)
氢分子
a d
氢原子
c
b
表面铁原子
e
h
+
g’
g
渗碳体或 固溶体碳原子
+ + ++
f
h’
内部铁原子
31
钢的氢腐蚀机理模型示意图
调整热处理和控制轧制状态。
35
第三节 腐蚀疲劳
一、腐蚀疲劳的定义
位错再次开动、 膜破裂
说明:4~7图为放 大倍数为200000 倍的结果。
金属再次快速溶解 产生穿晶型SCC开裂 (放大100倍)
3、断裂
应力腐蚀裂纹扩展到临界尺寸,便会在机械力作用下发
生失稳快速断裂。
氢致开裂型应力腐蚀: 特殊的应力腐蚀,阳极金属溶解
腐蚀所对应的阴极过程为析氢反应,且氢原子能扩散进入金
属并控制裂纹的形核和扩展。
24
合理选材
改变合金成分(低C, Cr, N, Mo) 改变合金组织 (热处理)
改变应力
避免应力集中
减少外应力 消除内应力
改变应力方向
合理结构
SCC控制
改变环境
调整环境温度、浓度、pH
加缓蚀剂
环境处理 电化学保护 阴极保护 阳极保护 牺牲阳极 表面处理 表面处理 表面电镀
5
第四章 应力作用下的腐蚀
第一节 应力腐蚀开裂
一、应力腐蚀开裂的定义(Stress Craking Corrosion)
冶金因素
应力腐蚀开裂(SCC)— 受 拉伸应力作用的金属材料在特定 介质中,特定介质和应力协同作 用发生脆性断裂现象。 应力腐蚀开裂很普遍,化工 行业约占四分之一。危害性极大, 如飞机失事,桥梁断裂,油气管 爆炸。 6
发生SCC的合金表面往往存在钝化膜或其他保护膜,在
大多数情况下合金发生SCC时均匀腐蚀速度很小,因此金属 失重甚微。
二元和多元合金对应力腐蚀开裂敏感性较高。 适当增加Cr、Al元素可提高奥氏体不锈钢抵抗应力腐蚀 开裂的能力;而C、N、S、P等易于在晶界上析出,促进SCC 的发生。
13
三、SCC裂纹扩展过程
快速溶解理论—活性通道不必预先存在, 也可能发生SCC,
表面某种因素(如点蚀源等)使应力集中, 前沿区迅速形变
屈服, 溶解速度很大( 0.5A/ cm2), 而两侧仅为10-5A/cm2 , 可促 使SCC发生。(拉伸应力较大时)
静态金属阳极区 (稳定阳极)
阴极
1/2O2+H2O+2e- 2OH-
1、裂纹扩展的三个阶段
裂纹孕育期:应力集中,微裂纹成 核,时间为几分钟~几十年; 裂纹扩散期:由裂纹源发展到极限 应力值对应的裂纹深度。扩散速度约为
10-6-10-3 mm/min,比均匀腐蚀快近106倍, 但仅为纯机械断裂速度的10-10倍;
破裂期:机械因素控制,随应力强 度增大,材料断裂。
26
2、氢在金属中的存在形式 固溶体:氢以H+、H- 、H的形态固溶于金属中。氢原子是所
有元素中几何尺寸最小的,其半径仅为0.053 nm,因而易于扩散进 入金属并占据金属晶格的间隙位置。
氢化物:氢与稀土金属、钛、钴等金属元素可生成一定的氢 氢分子:氢含量达到一定浓度时,能从过饱和固溶体中析出 气团:氢与位错结合形成气团,可看成一种相。
A
迅速屈服
A*
屈服金属阳极区 (动力阳极)
溶液
A
阴极
1/2O2+H2O+2e- 2OH-
A区(裂纹两侧): 电流密度 ~ 10-5A/cm2 A*区(裂纹尖端): 电流密度 ~ 0.5A/cm2
奥氏体不锈钢应力腐蚀破裂模型图
304不锈钢在沸腾45%MgCl 溶液中的穿晶裂纹
敏化304不锈钢在室温连多硫 酸溶液中的晶间裂纹
活性通道理论(拉伸应力较小时) 大的应力作用在裂缝尖端应力集中,使表面膜破裂。 合金中预先存在一条对腐蚀敏感的通道,在特定介质条
活性通道。
件下成为活性阳极。
形成活性通道可能性有:合金成分结构差异;晶界或亚 晶界;局部应力集中及应变引起阳极晶界区;应变引起表面
膜局部破裂;塑性变形引起的阳极区等。
18
1.5
γ相
σ相
在弱氧化性介质中,析出σ
电位(V)
1.0 0.5 0 -0.5 -0.05 0 0.1
相的不锈钢处于较低的电位区
间,此时σ相较γ相还稍耐腐蚀, 不易产生晶间腐蚀。
0.2 0.3
强氧化性介质中,在过钝
化电位下σ相发生严重腐蚀,其 阳极活性电流急剧增加。
电流密度(A/cm2)
不锈钢γ相和σ相的阳极极化曲线 (H2SO4-CuSO4介质)
课程回顾
电偶腐蚀
金属M、N偶接前
M+ H+ H2
金属M、N偶接后
M+ H+ H2
M N
e-
ee-
M
N
eH2
H2
H+
N+
H+
当金属N得到完全保护时,金属N的腐蚀停止,其阴极 反应叠加到对金属M的腐蚀上;金属M的阳极反应相匹配的
阴极电流由金属M、N的阴极反应共同提供。
1
可以利用作为防护措施!
2
晶间腐蚀(合金材料在高温使用时发生)
环境因素
力学因素
S C C 三要素
304不锈钢在沸腾45%MgCl 溶液中的穿晶裂纹
敏化304不锈钢在室温连多硫 酸溶液中的晶间裂纹
应力腐蚀的裂纹有晶间型、穿晶型和混合型三种类型。
二、SCC发生的条件和特征
1、力学特征 应力腐蚀是应力和环境腐蚀的联合作用造成的破坏。
在固定(静止)应力情况,称为应力腐蚀 开裂(SCC)
蚀结构,为局部应力腐蚀裂纹萌生提供了必要条件。
E
E 过钝化区
E
晶间腐蚀 Eb tp
钝化区
Eb p Ep
SCC
Etp
点蚀发生、发展
D
点蚀发展 缝隙腐蚀发生、发展
点蚀不发生 晶间腐蚀 与钝化有关! SCC
Ep
C A
B
过渡区 活化区(失电子) 阴极区(得电子)
O lg io lg ip’
lg ip
lgi
1、贫铬理论—晶界碳化物析出(过渡期,固溶处理可消除)
敏化热处理
不锈钢在弱氧化性介质奥氏体不锈钢(含碳相对高) 铁素体不锈钢(含碳、氮低) 晶间腐蚀最易发生在活化—钝化
3
晶界碳化物析出示意图
过渡区。
2、阳极相理论—晶界σ相析出并溶解 (过钝化区,固溶处理不能消除)
氢鼓泡机理示意图
置。
34
抑制氢鼓泡的措施 温度:氢鼓泡在室温下出现,升高或降低温度可减少开 裂现象。 硫含量:降低钢中硫含量可减少硫化物夹杂数量,降低 合金化:钢中加入铜(0.2~0.3%)能抑制表面反应,减 钢对氢鼓泡的敏感性。
少氢的渗入;加入铬、钼、钒、铌、钛能提高基体对裂纹扩 散的阻力。
应力腐蚀的裂纹有晶间型、穿晶型和混合型三种类型。
氢脆理论 — 裂缝内pH 下降, 电位负移。发生H+还原
H渗入金属 H2 析出, 导致SCC前沿变脆而开裂。
裂纹的比较
阳极溶解型
氢脆型
22
无应力时氧化膜稳定
应力导致位错 在滑移面塞积
应力增加、位错开动、 膜破裂
金属溶解、隧洞形成
溶解区重新进入钝态
钝化膜的局部破坏可能由化学或机械 原因造成。 化学原因:如在应力作用下点蚀坑根 部引发应力腐蚀开裂;钝化膜处于不稳定 状态(腐蚀电位在过渡区),应力腐蚀开 裂在钝化膜薄弱部位形核。 机械原因:材料受力变形时造成钝化 膜破坏。
17
2、溶解(裂纹扩展)
裂纹扩展的可能途径:预先存在活性通道和应变产生的
金属(Ti、Nb、Mo、W、Cr),减少甲烷生成;MnS为裂 纹源的引发处,应去除。
热处理和冷加工。
33
四、氢致开裂的机理——氢鼓泡(生成氢分子)
H2S是弱酸,在酸性溶 在金属表面阴极反应生 氢原子渗入金属内部,
液中主要以分子形式存在; 成大量的氢原子; 通过扩散达到缺陷处,析出 氢气产生高压; 非金属夹杂物(如Ⅱ型 MnS)为裂纹的主要形核位
27
化物;与硅、碳等非金属元素生成SiH4或CH4。 氢气。
三、氢致开裂的类型
1、第二类氢脆:氢脆的敏感性随应变速率增加而降低,即材 料在加载前不存在裂纹源,加载后在应力和氢作用下逐渐形 成裂纹源,最终导致脆性断裂。 应力诱发氢化物型氢脆:氢在应力作用下在应力集中区富 可逆氢脆:含氢金属在高速变形时并不显示脆性,而在缓慢
O
lgi
电位Etp称作“点蚀电位”或“破裂电位” 、“过钝电位” :金 电位Eb称为“再钝化电位”或“保护电位” :再次达到钝化电流
属表面局部地区的电极电位达到并高于临界电位值时,才能形成小孔腐蚀。
对应的电位。
12
3、材料学特征
发生均匀腐蚀的体系则一般不会发生SCC,且主要是合 金发生SCC,纯金属极少发生。
表面有机涂覆
第二节 氢致开裂
一、氢致开裂的定义
氢致开裂:又称氢脆或氢损伤,原子氢在合金晶体结构 内的渗入和扩散所导致的脆性断裂的现象。
二、金属中的氢
1、金属中氢的来源
内氢来源:如冶炼、 焊接、酸洗、阴极充氢等。 外氢来源:如工业环境中吸收氢(如油井H2S)、水溶液中微电池