氮化铝陶瓷粉体制备方法研究进展
氮化铝粉体制备的研究及展望

研究的重点。本文综合阐述了国内外有关氮化铝粉 体的制备方法 , 并对氮化铝粉体制备的发展方向进行
了展望 。
收稿 日期 :0 0 0 — 2 2 1— 7 1
基金项目: 教育部新世纪优秀人才支持计划(c T 0 一 76 ; 省重点科技仓 新团队(O 9 5 0 N E 一 7 O 8)浙江 2O R o l ) o 通讯联系人 : 徐时清, — 矧: uj @h c a . r E m s cu o i o x l m l n c
过 2×1 时 ,陶瓷的绝 缘 性 能 就 出 现 明 显 下 降[ 0 6 1 。
此外, 细小的粉体颗粒和窄的粒度分布均能有效提高 氮化铝陶瓷的烧结性能m 从而有效提高氮化铝陶瓷 , 的热传导与电绝缘性能 , 并降低其介 电损耗。因此 ,
如何获得氧等杂质含量低、 粉体粒径小以及粒度分布 窄的高质量氮化铝粉体已成为 目前广大科研工作者
究可以追溯到一百多年前, 但当时仅将其作为一种固 氮剂用作化肥。由于氮化铝是共价化合物 , 自扩散系
的热导率产生负面影响, 氮化铝的导热机制是声子传
导, 晶格的缺陷 、 气孔和杂质都会对声子产生散射 , 从
而降低氮化铝陶瓷的热导率。特别是 O原子固溶入
数小 , 熔点高, 导致其难以烧结 ; 直到 2 o世纪 5 年 o
第 3 卷第 4期 1 21年 1 0 0 2月
《 陶瓷学报 》
J OIRN AI 7 0F CERAM I CS
Vo . . 1 31 No. 4 D e 2 0 c. 01
文章 编 号 :00 27 ( 00 O - 6 1 o 10 — 28 2 1 )4 0 5- 7
《 陶瓷学报》 0 0年 第 4期 21
氮化铝陶瓷基板制备工艺的研究
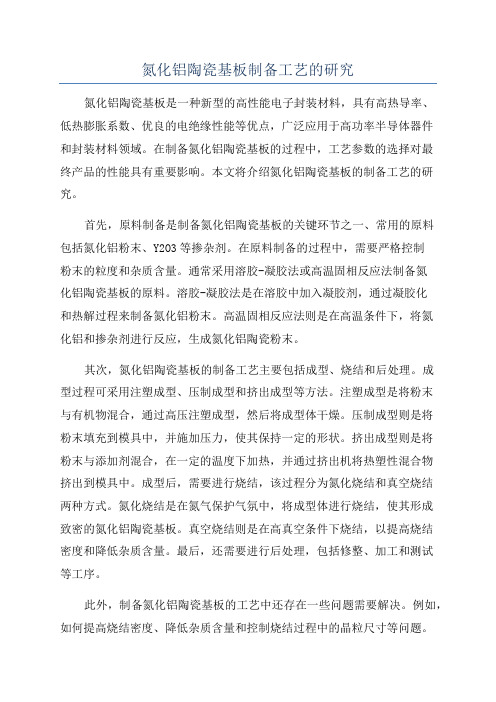
氮化铝陶瓷基板制备工艺的研究氮化铝陶瓷基板是一种新型的高性能电子封装材料,具有高热导率、低热膨胀系数、优良的电绝缘性能等优点,广泛应用于高功率半导体器件和封装材料领域。
在制备氮化铝陶瓷基板的过程中,工艺参数的选择对最终产品的性能具有重要影响。
本文将介绍氮化铝陶瓷基板的制备工艺的研究。
首先,原料制备是制备氮化铝陶瓷基板的关键环节之一、常用的原料包括氮化铝粉末、Y2O3等掺杂剂。
在原料制备的过程中,需要严格控制粉末的粒度和杂质含量。
通常采用溶胶-凝胶法或高温固相反应法制备氮化铝陶瓷基板的原料。
溶胶-凝胶法是在溶胶中加入凝胶剂,通过凝胶化和热解过程来制备氮化铝粉末。
高温固相反应法则是在高温条件下,将氮化铝和掺杂剂进行反应,生成氮化铝陶瓷粉末。
其次,氮化铝陶瓷基板的制备工艺主要包括成型、烧结和后处理。
成型过程可采用注塑成型、压制成型和挤出成型等方法。
注塑成型是将粉末与有机物混合,通过高压注塑成型,然后将成型体干燥。
压制成型则是将粉末填充到模具中,并施加压力,使其保持一定的形状。
挤出成型则是将粉末与添加剂混合,在一定的温度下加热,并通过挤出机将热塑性混合物挤出到模具中。
成型后,需要进行烧结,该过程分为氮化烧结和真空烧结两种方式。
氮化烧结是在氮气保护气氛中,将成型体进行烧结,使其形成致密的氮化铝陶瓷基板。
真空烧结则是在高真空条件下烧结,以提高烧结密度和降低杂质含量。
最后,还需要进行后处理,包括修整、加工和测试等工序。
此外,制备氮化铝陶瓷基板的工艺中还存在一些问题需要解决。
例如,如何提高烧结密度、降低杂质含量和控制烧结过程中的晶粒尺寸等问题。
目前,一种较为有效的方法是添加适量的助烧结剂,如铝酸盐、硼酸盐和硅酸盐等,以促进烧结反应的进行。
此外,还可以通过控制烧结温度和时间等参数来调节烧结过程,进一步优化制备工艺。
综上所述,氮化铝陶瓷基板的制备工艺是一个复杂的工程,需要控制好原料制备、成型、烧结和后处理等工艺参数。
氮化铝陶瓷粉体制备方法研究进展

氮化铝陶瓷粉体制备方法研究进展作者:江楠来源:《科技资讯》2019年第18期摘 ;要:氮化铝陶瓷属优质陶瓷材料,自身热导率高、电绝缘性良好、介电常数及损耗低,受到高功率电子生产行业广泛欢迎。
氮化铝陶瓷主要应用在高导热基板材料和高功率电子器件封装上,其自身优势性能对促进机械电子行业发展有重要作用。
该文就高质量氮化铝陶瓷粉体制备进行详细分析,分析其技术进展,旨在为深入了解氮化铝陶瓷粉体制备方式,为相关部门深入氮化铝陶瓷研究提供有力参考。
关键词:氮化铝陶瓷 ;粉体 ;制备方法 ;研究进展中图分类号:O614 ; 文献标识码:A ; ; ; ; ; ;文章编号:1672-3791(2019)06(c)-0073-02氮化铝(Aluminum nitride,AlN)属六方纤锌矿共价键化合物,呈灰白色,导热率高,高温下材料稳定,可和硅材料热膨胀系数相匹配,为理想的电子封装散热材料,对一些对散热要求较高的设备而言,以氮化铝为支持,可以增加设备自身散热性能,实现设备稳定工作在电子机械中应用广泛,可以减小传统电子散热器体积,降低成本[1]。
1 ;氮化铝陶瓷性能氮化铝陶瓷性能和其粉体纯度有直接联系,粉体杂质将降低陶瓷热导率,进而导致气孔及杂质对声子散射。
其中,O原子固溶进氮化铝晶格,占据N原子位置,导致Al空缺,形成声子,降低热导率。
若氮化铝陶瓷含氧量为0.12wt%,热导率对应为185W/(m.K),氮化铝陶瓷含氧量增加到0.31wt%,热导率对应降低为130W/(m.K)。
此外,杂质存在还影响陶瓷绝缘性,若氮化铝粉体中Si、Fe等元素含量在2x10-4以上,则氮化铝绝缘性明显下降。
细小粉体及较窄力度分布,则可提高氮化铝陶瓷烧结性能,提高其的热传导及绝缘性。
2 ;氮化铝陶瓷粉体制备方法氮化铝陶瓷粉体制备方式较多,有铝粉直接氮化法、Al2O3碳热还原、自蔓延高温合成、溶剂热合成、等离子化学合成、化学气相沉积法等[2]。
氮化铝材料及其粉体制备的现状与展望
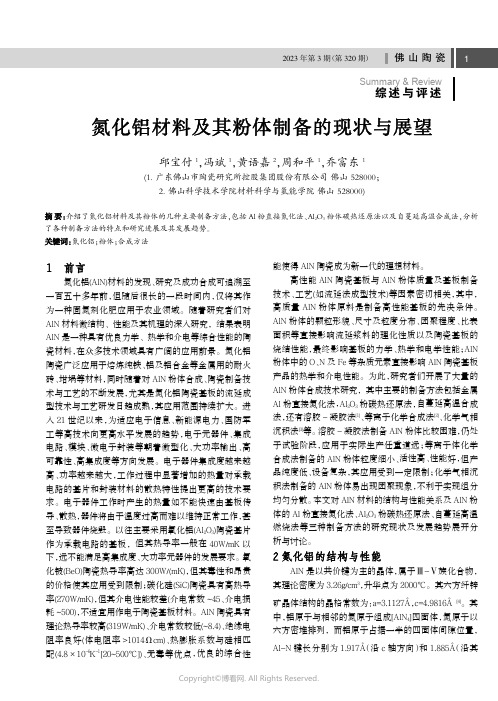
氮化铝(AlN)材料的发现、研究及成功合成可追溯至一百五十多年前,但随后很长的一段时间内,仅将其作为一种固氮剂化肥应用于农业领域。
随着研究者们对AlN 材料微结构、性能及其机理的深入研究,结果表明AlN 是一种具有优良力学、热学和介电等综合性能的陶瓷材料,在众多技术领域具有广阔的应用前景。
氮化铝陶瓷广泛应用于熔炼纯铁、铝及铝合金等金属用的耐火砖、坩埚等材料,同时随着对AlN 粉体合成、陶瓷制备技术与工艺的不断发展,尤其是氮化铝陶瓷基板的流延成型技术与工艺研发日趋成熟,其应用范围持续扩大。
进入21世纪以来,为适应电子信息、新能源电力、国防军工等高技术向更高水平发展的趋势,电子元器件、集成电路、模块、微电子封装等朝着微型化、大功率输出、高可靠性、高集成度等方向发展。
电子器件集成度越来越高、功率越来越大,工作过程中显著增加的热量对承载电路的基片和封装材料的散热特性提出更高的技术要求。
电子器件工作时产生的热量如不能快速由基板传导、散热,器件将由于温度过高而难以维持正常工作,甚至导致器件烧毁。
以往主要采用氧化铝(Al 2O 3)陶瓷基片作为承载电路的基板,但其热导率一般在40W/mK 以下,远不能满足高集成度、大功率元器件的发展要求。
氧化铍(BeO)陶瓷热导率高达300W/(mK),但其毒性和昂贵的价格使其应用受到限制;碳化硅(SiC)陶瓷具有高热导率(270W/mK),但其介电性能较差(介电常数~45、介电损耗~500),不适宜用作电子陶瓷基板材料。
AlN 陶瓷具有理论热导率较高(319W/mK)、介电常数较低(~8.4)、绝缘电阻率良好(体电阻率>1014Ωcm)、热膨胀系数与硅相匹配(4.8×10-6K -1[20~500℃])、无毒等优点,优良的综合性能使得AlN 陶瓷成为新一代的理想材料。
高性能AlN 陶瓷基板与AlN 粉体质量及基板制备技术、工艺(如流延法成型技术)等因素密切相关,其中,高质量AlN 粉体原料是制备高性能基板的先决条件。
氮化铝陶瓷的研究和应用进展

氮化铝陶瓷的研究和应用进展摘要从氮化铝陶瓷的实际应用领域进行了氮化铝陶瓷应用现状及前景的介绍;从其制备工艺介绍了氮化铝陶瓷的研究状况,并指出了低成本的粉末制备工艺和氮化铝陶瓷的复杂形状成形技术是目前很有价值的氮化铝陶瓷的研究方向。
关键词氮化铝陶瓷;高热导率;应用领域;制备工艺中图分类号 o614文献标识码 a文章编号1674-6708(2010)14-0052-02氮化铝(aln)是一种综合性能优良新型陶瓷材料,具有优良的热传导性,可靠的电绝缘性,低的介电常数和介电损耗,无毒以及与硅相匹配的热膨胀系数等一系列优良特性,被认为是新一代高集程度半导体基片和电子器件封装的理想材料,受到了国内外研究者的广泛重视.在理论上,aln的热导率为320w/(m),工业上实际制备的多晶氮化铝的热导率也可达100~250 w/(m),该数值是传统基片材料氧化铝热导率的5倍~10倍,接近于氧化铍的热导率,但由于氧化铍有剧毒,在工业生产中逐渐被停止使用。
与其它几种陶瓷材料相比较,氮化铝陶瓷综合性能优良,非常适用于半导体基片和结构封装材料,在电子工业中的应用潜力非常巨大。
1 aln陶瓷的直接应用1.1 aln作为基板材料高电阻率、高热导率和低介电常数是集成电路对封装用基片的最基本要求。
封装用基片还应与硅片具有良好的热匹配、易成型、高表面平整度、易金属化、易加工、低成本等特点和一定的力学性能。
大多数陶瓷是离子键或共价键极强的材料,具有优异的综合性能,是电子封装中常用的基片材料,具有较高的绝缘性能和优异的高频特性,同时线膨胀系数与电子元器件非常相近,化学性能非常稳定且热导率高。
长期以来,绝大多数大功率混合集成电路的基板材料一直沿用a1203和beo陶瓷,但a1203基板的热导率低,热膨胀系数和si不太匹配;beo虽然具有优良的综合性能,但其较高的生产成本和剧毒的缺点限制了它的应用推广。
因此,从性能、成本和环保等因素考虑,二者已不能完全满足现代电子功率器件发展的需要。
自蔓延燃烧法制备AlN陶瓷粉体的研究进展
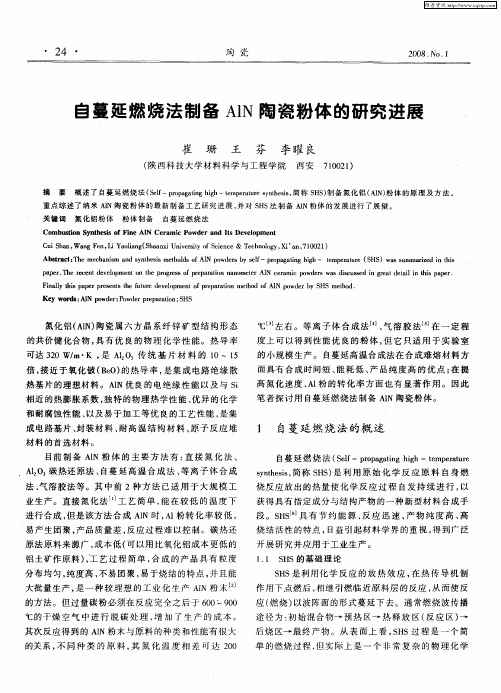
Ke r s: N o e ; o e rp r t n; HS y wo d AI p wd r P wd rpe a ai S o
氮化 铝( 1 ) 瓷属 六方 晶系 纤 锌矿 型 结 构形 态 AN 陶
的共价 键化合 物 , 有优 良的 物理 化 学 性 能。 热导 率 具
℃ 左 右 。等 离 子体 合 成 法¨ 、 溶胶 法 在 一 定 程 气 度 上可 以得 到性 能优 良的粉 体 , 它 只适 用 于 实验 室 但 的小规模 生 产 。 自蔓延 高温合成 法在 合成难 熔材 料方 面具有 合成 时间短 、 耗 低 、 品纯 度 高 的优 点 ; 提 能 产 在 高 氮化速 度 、 l 的转 化 率方 面也 有 显 著作 用 。 因此 A粉
维普资讯
・ Biblioteka 2 ・ 4 陶 瓷
2 o No. o8 1
.
自蔓 延燃 烧 法 制备 AN陶 瓷粉 体 的研究 进 展 1
崔 珊 王 芬 李 曜 良
( 陕西科 技大学 材料 科学 与工程 学 院
摘 要
西安
70 2 ) 10 1
概 述 了 自蔓 延燃 烧 法 (e —poaa n i Sl rpgtgh h—tnea r sn ei, f i g e prte yt s 简称 S S 制 备 氮 化 铝 ( 1 ) 体 的 原理 及方 法 。 t u h s H) AN 粉
氮化铝陶瓷粉体制备方法研究进展

氮化铝陶瓷粉体制备方法研究进展氮化铝陶瓷具有高硬度、高耐磨、高耐腐蚀等优异性能,近年来已经成为研究的热点之一。
氮化铝陶瓷粉体的制备方法对其性能和应用领域有着重要的影响。
本文将对氮化铝陶瓷粉体制备方法的研究进展进行综述。
机械法是一种常用的氮化铝陶瓷粉体制备方法。
这种方法的关键在于选取合适的原料、研磨介质、工艺参数等。
常用的研磨介质有氧化铝、氧化钇和氧化镁等,其目的是防止研磨过程中产生的杂质与粒子混合。
在机械法制备氮化铝陶瓷粉体时,其平均粒径、分布性及物理性质等性能往往与研磨时间、研磨介质、研磨比例等因素密切相关。
溶胶-凝胶法是一种利用水解的前驱体制备氮化铝陶瓷粉体的方法。
其制备过程一般分为胶溶液的制备、胶体的制备、氮化铝陶瓷粉体的制备以及热处理等步骤。
此法可以制备出纯度高、粒度均匀、致密度好的氮化铝陶瓷粉体。
但是,由于其操作条件比较苛刻,如制备过程在高温下进行等,因此工艺较为复杂。
3. 气相反应制备氮化铝陶瓷粉体气相反应法是目前制备氮化硅陶瓷粉体的主要方法之一。
在此方法中,可使用硝酸铝、氨气等为前驱体,在高温高压的条件下通过氮化反应得到氮化铝陶瓷粉体。
此法可以制备纯度高、晶粒细小的氮化铝陶瓷粉体。
但是,其反应条件比较苛刻,容易造成能量浪费。
4. 其他制备方法除了以上三种氮化铝陶瓷粉体制备方法外,近年来还出现了一些新的制备方法。
例如化学汽相沉积法、等离子体增强化学气相沉积法等。
这些方法在制备过程中有着独特的优势,而且能够制备出各具特色的氮化铝陶瓷粉体,为氮化铝陶瓷的应用提供了新的选择。
综上所述,氮化铝陶瓷粉体制备方法多种多样,各具特点。
在实际应用中,需要根据具体情况选取合适的制备方法,使其性能达到最佳状态。
随着制备工艺的不断改进以及新技术的出现,氮化铝陶瓷的应用前景将不断拓展。
氮化铝陶瓷粉体制备方法研究进展
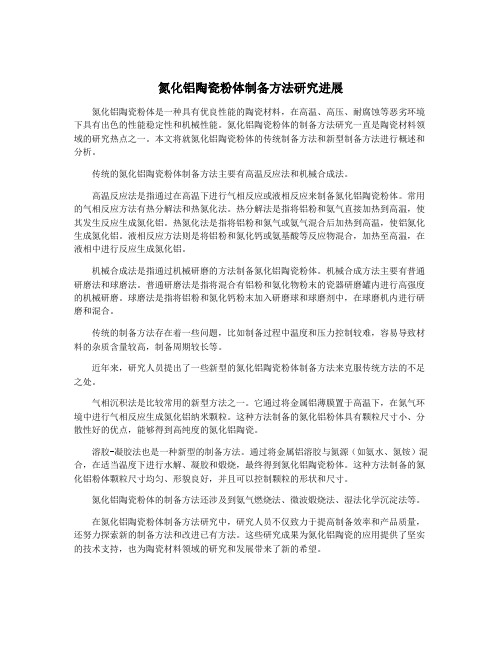
氮化铝陶瓷粉体制备方法研究进展氮化铝陶瓷粉体是一种具有优良性能的陶瓷材料,在高温、高压、耐腐蚀等恶劣环境下具有出色的性能稳定性和机械性能。
氮化铝陶瓷粉体的制备方法研究一直是陶瓷材料领域的研究热点之一。
本文将就氮化铝陶瓷粉体的传统制备方法和新型制备方法进行概述和分析。
传统的氮化铝陶瓷粉体制备方法主要有高温反应法和机械合成法。
高温反应法是指通过在高温下进行气相反应或液相反应来制备氮化铝陶瓷粉体。
常用的气相反应方法有热分解法和热氮化法。
热分解法是指将铝粉和氨气直接加热到高温,使其发生反应生成氮化铝。
热氮化法是指将铝粉和氮气或氨气混合后加热到高温,使铝氮化生成氮化铝。
液相反应方法则是将铝粉和氮化钙或氨基酸等反应物混合,加热至高温,在液相中进行反应生成氮化铝。
机械合成法是指通过机械研磨的方法制备氮化铝陶瓷粉体。
机械合成方法主要有普通研磨法和球磨法。
普通研磨法是指将混合有铝粉和氨化物粉末的瓷器研磨罐内进行高强度的机械研磨。
球磨法是指将铝粉和氮化钙粉末加入研磨球和球磨剂中,在球磨机内进行研磨和混合。
传统的制备方法存在着一些问题,比如制备过程中温度和压力控制较难,容易导致材料的杂质含量较高,制备周期较长等。
近年来,研究人员提出了一些新型的氮化铝陶瓷粉体制备方法来克服传统方法的不足之处。
气相沉积法是比较常用的新型方法之一。
它通过将金属铝薄膜置于高温下,在氮气环境中进行气相反应生成氮化铝纳米颗粒。
这种方法制备的氮化铝粉体具有颗粒尺寸小、分散性好的优点,能够得到高纯度的氮化铝陶瓷。
溶胶-凝胶法也是一种新型的制备方法。
通过将金属铝溶胶与氮源(如氨水、氮铵)混合,在适当温度下进行水解、凝胶和煅烧,最终得到氮化铝陶瓷粉体。
这种方法制备的氮化铝粉体颗粒尺寸均匀、形貌良好,并且可以控制颗粒的形状和尺寸。
氮化铝陶瓷粉体的制备方法还涉及到氨气燃烧法、微波煅烧法、湿法化学沉淀法等。
在氮化铝陶瓷粉体制备方法研究中,研究人员不仅致力于提高制备效率和产品质量,还努力探索新的制备方法和改进已有方法。
- 1、下载文档前请自行甄别文档内容的完整性,平台不提供额外的编辑、内容补充、找答案等附加服务。
- 2、"仅部分预览"的文档,不可在线预览部分如存在完整性等问题,可反馈申请退款(可完整预览的文档不适用该条件!)。
- 3、如文档侵犯您的权益,请联系客服反馈,我们会尽快为您处理(人工客服工作时间:9:00-18:30)。
氮化铝陶瓷粉体制备方法研究进展
随着科学技术的不断发展,高性能氮化铝陶瓷材料的研究备受关注。
而氮化铝陶瓷粉体的制备方法则是氮化铝陶瓷材料研究的重要基础。
本文主要介绍了氮化铝陶瓷粉体制备方法的研究进展。
一、热反应法
热反应法是最早用于制备氮化铝粉体的方法,其原理是利用反应热将铝和氮化物转化为氮化铝。
热反应法具有制备工艺简单、反应速度较快等优点,但也存在着反应条件难以控制、产物结晶度低等缺点。
氮气反应法是利用氮气和铝在高温下进行反应,得到氮化铝粉末的一种方法。
该方法主要优点为可获得高纯度且晶粒细小的氮化铝粉末,但需要高温高压条件,能耗较高。
三、溶胶凝胶法
溶胶凝胶法是采用溶胶化学原理,将金属的氧化物转化为高分子物质,并通过热处理方法转化为金属氧化物、金属化合物、金属、无机和有机骨架,从而获得氮化铝粉末。
溶胶凝胶法具有借助化学反应实现制备、反应速度高、制备出的产品具有较高精度控制等优点。
四、氧化还原法
氧化还原法是指先将铝与氮化物加入反应器中,再加热至高温,经氮气氛围下还原,得到氮化铝粉末。
氧化还原法制备氮化铝粉末优点是制备出的粉末具有较高的晶粒度以及良好的流动性,但需要高温高压条件,对反应器的材料要求较高,同时还存在着反应难度较大且产物中存在少量杂质的问题。
综上所述,氮化铝陶瓷粉体的制备方法具有各自的优缺点,应根据不同的应用需求选择合适的制备方法。
未来应进一步探索制备高性能氮化铝陶瓷粉体的新方法,并提高制备粉体的纯度、成分均匀性和产品性能。