深孔加工的编程及技巧
加工中心钻深孔的编程方法

加工中心钻深孔的编程方法加工中心是一种能够进行多种加工操作的机床,它能够进行钻孔、铣削、切割等各种加工操作。
在加工中心钻深孔时,需要进行编程来控制加工过程。
下面将介绍一下加工中心钻深孔的编程方法。
手工编程是指操作员根据工艺要求和深孔钻的尺寸要求,手动输入程序进行编程。
手工编程需要操作员具备一定的加工经验和编程技术,在加工过程中需要根据具体要求进行调整和修正。
CAD/CAM编程是指通过计算机辅助设计(CAD)和计算机辅助制造(CAM)软件来进行深孔钻的编程。
操作人员首先使用CAD软件进行3D模型的设计,然后通过CAM软件进行加工路径的生成和刀具路径的优化,最后生成机床的加工程序。
CAD/CAM编程可以提高编程的精度和效率,减少操作员的工作量。
在编写加工中心钻深孔的程序时,需要注意以下几点:1.首先,确定深孔钻的参数,包括钻孔的直径、深度、切削速度、进给速度等。
这些参数需要根据具体的工件材料和加工要求来进行选择。
2.确定刀具的选择和安装方式。
深孔钻一般使用长钻杆和内冷却器,可以有效降低切削温度,提高加工质量。
3.编写切削路径。
切削路径应该保证刀具在钻削过程中的稳定性和最优切削条件。
一般来说,采用螺旋切削路径可以提高切削效率和加工质量。
4.设置冷却液的供给。
加工深孔钻时,需要通过内冷却液来降低钻头的温度,从而提高加工质量。
在编程过程中需要设置冷却液的供给时间和流量。
5.考虑加工中心的刀库和刀具切换。
在进行复杂零件的加工时,可能需要多次换刀。
在编写程序时要考虑到刀具的切换和切换点的选择,以避免刀具碰撞或者加工误差。
总结来说,编写加工中心钻深孔的程序需要根据具体的工艺要求和机床的特点来进行选择。
手工编程和CAD/CAM编程是两种常用的方法,都需要考虑到刀具选择、切削路径、冷却液的供给等因素。
通过合理的编程,可以提高加工效率和产品质量。
加工中心钻深孔的编程方法

加工中心钻深孔的编程方法首先,加工中心钻深孔的编程需要采用G代码进行控制,因此需要编写相应的G代码程序。
编程主要分为几个步骤。
第一步是确定钻孔顺序。
在编程的过程中,需要确定钻孔的顺序,即先钻哪些孔,后钻哪些孔。
这取决于工件的几何形状和孔的位置。
通常,可以按照从外到内、从上到下的方式确定钻孔顺序,以便保证加工的稳定性和高效性。
第二步是确定切削参数。
在编程之前,需要事先确定切削参数,包括切削速度、进给速度和切削深度等。
这些参数的选择需要根据工件材料和加工要求来确定。
切削参数的选择直接影响着钻孔的质量和加工效率。
第三步是确定坐标系。
在编程之前,需要确定加工中心的坐标系,以便编写相应的G代码程序。
加工中心的坐标系通常是以工件的一些参考面或参考点为基准建立的。
编程时,需要将钻孔的坐标位置进行转换,使其与加工中心的坐标系一致。
第四步是编写G代码程序。
编写G代码程序是将加工过程指令转换为机床能够理解和执行的代码。
编写G代码程序时,需要按照加工顺序和切削参数依次编写相应的G代码指令。
一般情况下,每一个钻孔都对应着一段G代码程序,包括进给指令、刀具选取指令等。
在编程过程中1.确保钻孔参数正确。
切勿将错误的参数输入到程序中,否则会影响钻孔的质量和加工效果。
2.合理选择进给方式。
对于较深的孔,进给方式选用螺纹进给能够提高加工效率和孔的质量。
3.考虑切削液的使用。
在加工过程中,可以适当使用切削液,以降低切削温度、延长工具寿命和提高加工质量。
总之,加工中心钻深孔的编程方法主要包括确定钻孔顺序、确定切削参数、确定坐标系和编写G代码程序。
编程的准确性和合理性直接影响着钻孔的质量和加工效率。
因此,对于加工中心钻深孔的编程,需要严谨认真地进行,确保编程参数和程序的准确性和合理性。
深孔加工的编程及切削用量选择

深孔加工的编程及切削用量选择深孔加工的编程及切削用量选择-经济深孔加工的编程及切削用量选择周成东摘要:深孔加工技术是机械加工发展的一种产物,它是集麻花钻、绞刀等多种加工刀具于一身的新型切削工具,适用范围很广,真正运用到大型管板类群孔加工,是随着发电设备制造规模和能力不断提升,才逐渐进入人们的视线,特别是核能发电的出现,已经成为现阶段电能产出的主导形式,作为加工核电设备关键部件蒸发器管板的深孔加工,就更加受到我们的关注。
成为核电设备制造过程中必不可少的关键加工工序。
关键词:切削用量深孔加工编程引言在数控加工中会经常遇到深孔的加工,例如:螺纹底孔、定位销孔等。
在加工孔时我们一般都是用立式加工中心和数控铳床进行加工。
但在这些孔中深孔加工是较困难的,在孔加工中除了切削用量外,排削、冷却钻头也是需要解决的。
Y图为5个直径为&深度为200的深孔,该深孔加工存在孔深,容易断刀,难以保证同轴度,精度难以保证等问题。
下面我将从编程和切削用量两方面来来讨论和解决该深孔加工中遇到的问题。
一、深孔加工的编程指令1、深孔加工的指令格式很多的数控系统中都提供了深孔加工指令,这里以SIEMENS和FANUC为来进行叙述深孔加工。
(1)首先我们来谈一下SIEMENS系统,SIEMENS系统提供了 CYCLE83指令:CYCLE83为深孔往复排屑钻孔指令。
CYXLE83指令格式为:CYCLE83 (RTP, RFP, SDIS, DP, DPR, FDEP, FDPR, DAM, DTB, DTS, FRF, VA-RL)。
⑵我们下面来谈一下FANUC系统,FANUC系统提供了两种指令,分别为:G73和G83o G73为高速深孔往复排屑钻指令;G83为深孔往复排屑钻指令。
指令格式为:G73 X, Y, Z, R, Q, F,;G83 X, Y, Z, R, Q, F,;指令中:X、Y—指定孔在XY平面能的定位Z—孔底平面的位置(若是通孔,则钻尖应超出工件底面)R—R点平面所在的位置,R点高出工件顶面2至5毫米,Q—当有间隙进给时,刀具每次加I:深度F—孔加工切削进给时的进给速度2、深孔加工的动作(DCYCLE83孔加工该指令通过Z轴方向的间歇进给实现断屑和排屑的目的。
加工中心钻深孔的编程方法

加工中心钻深孔的编程方法加工中心是一种多功能的数控机床,能够进行多种加工操作,包括钻孔。
钻深孔是指钻孔深度较大的孔径。
进行钻深孔加工的编程方法需要考虑到以下几个方面。
首先,需要确定孔径和孔深。
在进行编程之前,需要明确要加工的钻孔的孔径和孔深。
这是编程的基础,也是后续计算加工参数和路径的依据。
其次,需要计算切削参数。
切削参数包括主轴转速、进给速度和切削进给量等。
主轴转速的选择需要考虑材料的硬度和刀具的耐用性。
进给速度的选择需要考虑加工的效率和表面质量。
切削进给量的选择需要考虑刀具和工件的强度和刚性等因素。
然后,需要选择合适的刀具。
钻深孔加工需要选择合适的直柄钻头或深孔钻头。
钻头的选择需要考虑到孔径和孔深,以及材料的硬度和加工精度等因素。
较大的孔径和较深的孔深通常需要较长的钻头和更大的冷却液流量。
接着,需要编写加工程序。
钻深孔加工的编程方法通常有两种:点位编程和插补编程。
点位编程是指根据孔径和孔深,计算每个点的坐标并依次钻孔。
插补编程是指根据加工路径和切削参数,通过插补运动产生连续的切削轨迹。
点位编程适用于简单的孔径和孔深,而插补编程适用于复杂的孔形和大批量的钻深孔加工。
最后,需要进行程序验证和优化。
在进行实际加工之前,需要通过模拟和仿真等方法对加工程序进行验证。
在验证过程中,需要检查加工轨迹、切削参数和表面质量等方面是否满足要求。
如果存在问题,需要及时进行调整和优化。
总之,钻深孔的编程方法需要综合考虑孔径和孔深、切削参数、刀具选择、加工程序编写和程序验证等因素。
只有在充分理解和合理运用这些方法的基础上,才能有效地进行钻深孔加工。
G74深孔加工循环指令课件
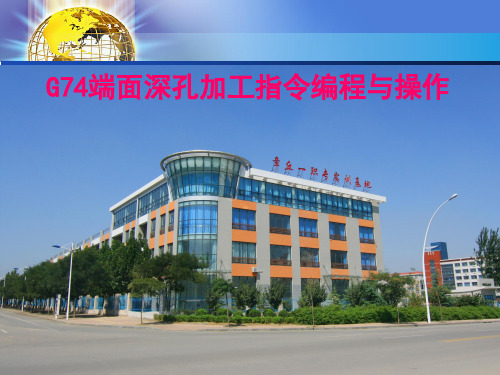
深孔加工循环指令

深孔加工循环指令深孔加工是一种非常常用的金属加工方法,它主要用于加工深孔、大孔径、高精度的工件。
深孔加工循环指令则是在加工过程中,按照一定的步骤和程序进行操作,以确保加工质量和效率的提高。
下面就来详细介绍一下深孔加工循环指令的相关内容。
首先,深孔加工循环指令需要根据具体的工件情况进行编写。
在编写指令时,需要考虑到工件的材料、形状、尺寸等因素,以及加工所需的孔径、深度、精度等要求。
只有根据具体情况编写指令,才能更好地保证加工质量和效率。
其次,深孔加工循环指令需要包含以下几个方面的内容:进刀、定位、主轴控制以及进给控制。
进刀是指工具沿着工件表面进行切削的过程,需要控制进给速度、进给量以及切削深度等参数。
定位是指将工具放到正确的位置,以便进行下一步的加工操作。
主轴控制是指控制主轴的转速和进给速度,以满足不同材料和工件的加工需求。
进给控制是指在切削过程中对进给量和速度进行调整,以获得最佳的加工效果。
再次,深孔加工循环指令需要确保加工的安全性和稳定性。
在编写指令时,应考虑到合理的切削力和切削温度分布,以避免加工过程中产生过大的热量和应力,从而导致工件变形或者损坏的情况发生。
同时,要合理选择加工液并掌握其使用方法,以提高刀具的寿命和加工质量。
最后,深孔加工循环指令需要根据实际情况进行优化。
通过对加工过程中的各个参数进行调整和优化,可以提高加工效率和质量。
同时,还可以采用一些先进的加工技术和设备,如高速切削、切削液加工等,以进一步改进加工效果。
总之,深孔加工循环指令是深孔加工过程中不可或缺的一部分。
通过合理编写和优化指令,可以提高加工效率和质量,实现更好的加工效果。
对于从事深孔加工的操作者来说,熟练掌握深孔加工循环指令的编写和运用,对于提高工作效率和质量具有非常重要的指导意义。
深孔加工编程及技巧
在数控加工中常遇到孔的加工,如定位销孔、螺纹底孔、挖槽加工预钻孔等。
采用立式加工中心和数控铣床进行孔加工是最普通的加工方法。
但深孔加工,则较为困难,在深孔加工中除合理选择切削用量外,还需解决三个主要问题:排屑、冷却钻头和使加工周期最小化。
本文将从编程方面讨论解决有关深孔加工的主要问题。
一、深孔加工的编程指令及自动编程1. 深孔加工指令格式大多数的数控系统都提供了深孔加工指令,这里以FANUC系统为例来进行叙述。
FANUC 系统提供了G73和G83两个指令:G73为高速深孔往复排屑钻指令,G83为深孔往复排屑钻指令。
其指令格式为:式中 X、Y——待加工孔的位置;Z——孔底坐标值(若是通孔,则钻尖应超出工件底面);R——参考点的坐标值(R点高出工件顶面2~5mm);Q——每一次的加工深度;F——进给速度(mm / min);G98——钻孔完毕返回初始平面;G99——钻孔完时返回参考平面(即R点所在平面)。
2.深孔加工的动作深孔加工动作是通过Z轴方向的间断进给,即采用啄钻的方式,实现断屑与排屑的。
虽然G73和G83指令均能实现深孔加工,而且指令格式也相同,但二者在Z向的进给动作是有区别的,图1和图2分别是G73和G83指令的动作过程。
图1 G73指令动作过程图2 G83指令动作过程从图1和图2可以看出,执行G73指令时,每次进给后令刀具退回一个d值(用参数设定);而G83指令则每次进给后均退回至R点,即从孔内完全退出,然后再钻入孔中。
深孔加工与退刀相结合可以破碎钻屑,令其小得足以从钻槽顺利排出,并且不会造成表面的损伤,可避免钻头的过早磨损。
G73指令虽然能保证断屑,但排屑主要是依靠钻屑在钻头螺旋槽中的流动来保证的。
因此深孔加工,特别是长径比较大的深孔,为保证顺利打断并排出切屑,应优先采用G83指令。
3. 常规自动编程方法这里以MasterCAM V9为例,其钻孔参数设置对话框如图3所示。
图3 钻孔参数设置对话框(1)高度参数高度参数包括Clearance(安全高度)、Retract(参考高度)、Feedplane(下刀位置)、Top of stock(工件顶面)和Depth(切削深度)等。
powermill编程,深孔加工技巧和注意点
powermill编程,深孔加工技巧和注意点PowerMill编程,深孔加工技巧和注意点随着制造业的发展,加工技术也在不断地发展。
深孔加工是一种常见的加工方式,它可以用于加工各种形状的孔,比如圆孔、方孔、六角孔等。
在深孔加工中,PowerMill是一种常用的编程软件,它可以帮助我们进行高效准确的加工。
一、PowerMill编程PowerMill是一种CAM软件,它可以实现从CAD模型到CNC程序的快速转换。
PowerMill具有强大的自动化功能,可以自动生成加工路径,同时还可以进行仿真和优化,以确保最终的加工质量。
在PowerMill中进行编程需要考虑以下几个方面:1.选择正确的加工参数在编程之前,需要根据具体的工件和材料选择正确的加工参数,比如刀具直径、切削速度、进给速度等。
这些参数的选择对于加工效率和加工质量都有着至关重要的影响。
2.生成合适的加工路径在PowerMill中,可以使用自动化工具来生成加工路径。
但是,在某些情况下,自动生成的路径可能不够理想,需要手动修改。
在修改路径时,需要考虑刀具的尺寸和形状,以及材料的硬度和韧性等因素。
3.进行仿真和优化在编写完程序之后,需要进行仿真和优化,以确保最终的加工质量。
在仿真过程中,可以检查加工路径是否正确,是否存在碰撞等问题。
而在优化过程中,可以根据加工效率和加工质量等因素对加工参数和加工路径进行调整。
二、深孔加工技巧深孔加工是一种复杂的加工方式,需要注意以下几个技巧:1.选择合适的刀具深孔加工需要使用特殊的深孔钻头。
在选择刀具时,需要考虑孔径、孔深、材料等因素。
同时,需要选择高质量、高精度的刀具,以确保加工质量。
2.优化进给方式深孔加工需要使用适当的进给方式,以避免刀具断裂、孔壁损坏等问题。
在选择进给方式时,需要考虑材料的硬度和韧性等因素,同时还需要考虑刀具的尺寸和形状。
3.控制切削速度深孔加工需要控制切削速度,以确保加工质量。
在加工过程中,需要根据材料的硬度和韧性等因素来选择合适的切削速度,并且还需要根据刀具的尺寸和形状进行调整。
数控铣孔加工编程及技巧
数控铣孔加工编程及技巧一、数控铣孔加工编程的基本原则1.程序要简洁明了,避免加工路径重叠和多余的切削。
2.合理选择切削刀具,考虑材料的硬度、孔径和深度等因素。
3.设置适当的进给速度和转速,确保切削效果和表面光洁度。
4.动态平衡切削力,避免过大或过小的切削力对加工精度的影响。
5.考虑孔壁的厚度和强度需求,在切削过程中要避免过度切削。
6.编写错误检测程序,确保数控铣床工作正常。
7.确保切削工具的几何精度和刃口质量,以保证加工孔的精度。
二、数控铣孔加工编程的步骤1.准备加工零件的图纸和机床资料。
2.分析零件的结构和加工要求,确定切削刀具和刀具路径。
3.选择合适的刀具,并计算切削参数,如进给量、转速和切削速度。
4.编写加工程序,包括初始点的设定、刀具半径补偿和进给速度设定。
6.检查程序的正确性和合理性,做好错误检测和修改。
7.将编写好的加工程序传输到数控铣床,并进行试切和调整。
三、数控铣孔加工编程的技巧1.合理选择切削刀具,根据孔径和深度选择合适的铣刀或钻头。
2.对于大孔径或深孔加工,可以采用铺铣切削法,即使用多个刀具进行切削,每个刀具只负责一部分切削,从而减小切削力和堆积效应。
3.采用切削参数的优化设计,如采用层进给法和变进给法,根据不同的切削情况选择最佳的进给速度和转速。
4.对于复杂结构的零件,可以考虑使用孔类刀具或特殊形状刀具,以减少切削次数和加工时间。
5.根据材料的硬度和切削性能选择合适的冷却液和润滑剂,以提高切削效果和延长刀具寿命。
6.注意切削路径的选择,尽量避免切削路径重叠和过多的插补,以提高加工效率和加工质量。
7.切削力平衡,避免过度切削导致切削力过大或过小,影响加工质量和工具寿命。
8.编写合适的检测程序,对加工过程进行实时监控和检测,避免加工失误和设备故障。
9.对于薄壁孔的加工,可以采用先铣后孔的方法,先用铣刀将孔外侧加工成合适的形状,再用钻头进行精确的孔加工。
10.定期检查和维护数控铣床,保持其正常工作状态,减少故障发生的可能性。
1.端面深孔加工循环(G74)
课题7.5端面深孔加工循环(G74)教学目的和要求:1、掌握端面深孔循环指令G74编程方法2、能够G74指令编写加工程序教学重点难点:1、掌握端面深孔循环指令G74编程方法2、能够G74指令编写加工程序教学方式: 课堂理论教学教学时数3学时教学内容深孔钻循环功能适用于深孔钻削加工,如图 7-6所示。
1、编程格式G74 R(e)G74 X(U) ____ Z(W) ____ I____ K____ D____ F____其中X表示B点X坐标;U表示A→B增量值;Z表示C点的z坐标;W表示A→C的增量值;I表示x方向的移动量(无符号指定);K表示z方向的切削量(无符号指定);D表示切削到终点时的退刀量;F表示进给速度。
如果程序段中X(U)、I 、D为0,则为深孔钻加工。
2、走刀路线走刀路线如图7-6所示:图 7-6深孔钻削循环3、编程实例例1:采用深孔钻削循环功能加工图 7-6所示深孔,试编写加工程序。
其中: e=1 ,△ k=20 , F=0.1 。
O0005N10 G50 X200 Z100 T0202;N20 M03 S600;N30 G00 X0 Z1;N40 G74 R1;N50 G74 Z-80 Q20 F0.1;N60 G00 X200 Z100;N70 M30;例2:如图7-7所示,要在车床上钻削直径为10mm,深为100mm的深孔,其程序为:N01 G50 X50.0 Z100.0:建立工件坐系N02 G00 X0 Z68.0;钻头快速趋近N03 G74 Z 8.0 K5.0 F0.1 S800;用G74指令钻削循环N04 G00 X50.0 Z 100.0;刀具快速退至参考点图7-7【小结】:本课题主要是介绍G74的格式及应用,要注意G74指令的使用方法及注意事项,能够用G74编制中等复杂轴类零件的深孔加工数控加工程序。
【课外作业】:用G74指令完成P226页图(45)、(46)的深孔加工。
- 1、下载文档前请自行甄别文档内容的完整性,平台不提供额外的编辑、内容补充、找答案等附加服务。
- 2、"仅部分预览"的文档,不可在线预览部分如存在完整性等问题,可反馈申请退款(可完整预览的文档不适用该条件!)。
- 3、如文档侵犯您的权益,请联系客服反馈,我们会尽快为您处理(人工客服工作时间:9:00-18:30)。
深孔加工的编程及技巧
本文通过对深孔加工指令G73和G83动作过程的分析,提出设置合理参数的方法,总结了特殊深孔加工的编程技巧,并给出了应用技巧方法处理的实例。
在数控加工中常遇到孔的加工,如定位销孔、螺纹底孔、挖槽加工预钻孔等。
采用立式加工中心和数控铣床进行孔加工是最普通的加工方法。
但深孔加工,则较为困难,在深孔加工中除合理选择切削用量外,还需解决三个主要问题:排屑、冷却钻头和使加工周期最小化。
本文将从编程方面讨论解决有关深孔加工的主要问题。
一、深孔加工的编程指令及自动编程
1. 深孔加工指令格式
大多数的数控系统都提供了深孔加工指令,这里以FANUC系统为例来进行叙述。
FANUC系统提供了G73和G83两个指令:G73为高速深孔往复排屑钻指令,G83为深孔往复排屑钻指令。
其指令格式为:
式中X、Y——待加工孔的位置;
Z——孔底坐标值(若是通孔,则钻尖应超出工件底面);
R——参考点的坐标值(R点高出工件顶面2~5mm);
Q——每一次的加工深度;
F——进给速度(mm / min);
G98——钻孔完毕返回初始平面;
G99——钻孔完时返回参考平面(即R点所在平面)。
2.深孔加工的动作
深孔加工动作是通过Z轴方向的间断进给,即采用啄钻的方式,实现断屑与排屑的。
虽然G73和G83指令均能实现深孔加工,而且指令格式也相同,但二者在Z向的进给动作是有区别的,图1和图2分别是G73和G83指令的动作过程。
图1 G73指令动作过程
图2 G83指令动作过程
从图1和图2可以看出,执行G73指令时,每次进给后令刀具退回一个d值(用参数设定);而G83指令则每次进给后均退回至R点,即从孔内完全退出,然后再钻入孔中。
深孔加工与退刀相结合可以破碎钻屑,令其小得足以从钻槽顺利排出,并且不会造成表面的损伤,可避免钻头的过早磨损。
G73指令虽然能保证断屑,但排屑主要是依靠钻屑在钻头螺旋槽中的流动来保证的。
因此深孔加工,特别是长径比较大的深孔,为保证顺利打断并排出切屑,应优先采用G83指令。
3. 常规自动编程方法
这里以MasterCAM V9为例,其钻孔参数设置对话框如图3所示。
图3 钻孔参数设置对话框
(1)高度参数
高度参数包括Clearance(安全高度)、Retract(参考高度)、Feedplane(下刀位置)、Top of stock(工件顶面)和Depth(切削深度)等。
安全高度是指在此高度上刀具可以在任何位置平移而不会与工件或夹具发生碰撞;参考高度为开始一个刀具路径前刀具回缩的位置,参考高度应高于下刀位置;下刀位置是指当刀具在下刀位置之上先快速下降,当下降到该位置后再以慢速接近工件;工件顶面是指工件上表面的高度值;切削深度是指最后的加工深度。
(2)钻孔参数
根据孔加工方式的不同,可设置的参数个数也不同,各参数的含义如下:
Lst Peck——第一次啄钻深度;
Subsequent Peck——以后每次的啄钻深度;
Peck Clearance——啄孔间隙;
Chip Break——退刀量;
Dwell——刀具暂停在孔底部的时间;
Shift——设置退刀时离开孔表面的距离。
(3)自动编程产生的程序段
由图3对话框中设定参数值所产生的程序段为:
N110G98G83Z-150.R2.Q5.F90
比较对话框设定参数与所产生的程序段,可以看出:
1)程序段中产生了第一次啄钻深度值Q5,“以后每次啄钻深度值”和“啄钻间隙值”两参数不起任何作用;
2)G73和G83指令在钻孔时孔底动作均为快速返回,不会产生暂停的动作,即Dwell设定值在此程序段中没有得到体现。
而在实际加工中,当钻头退出时,钻屑在冷却液冲刷下会落入孔中。
这种情况尤其会发生在对钢料的加工中。
当钻头再次进入后,它将撞击位于孔底部钻屑。
钻屑在刀具的作用下开始旋转,将钻屑切断或熔化。
因此,在必要时应暂停加工来清理吹净钻屑。
3)若加工台阶深孔,如图4所示,其加工工艺一般是先加工直径为20的孔,然后再钻底部直径为10的孔。
然而用G83指令加工底部直径为10mm的深孔时,将在直径20mm的长度上造成较大的时间浪费。
图4 台阶孔
二、编程技巧
鉴于存在上述几个缺陷,我们将钻孔参数设置对话框中的Lst Peck参数设置成65,而Subsequent Peck的参数设置成5,Dwell设置成0(即不延时)。
同时打开后置处理文件,将Usecanpeck项的Yes,改成NO,则产生如下程序:
%O0000(文件名)
(PROGRAM NAME - T1)(程序名)
(DATE, Day-Month-Year - 26-04-04TIME, Hr:Min - 14:00)(编程时间)
N100G21(公制单位)
N102G0G17G40G49G80G90(XY平面,半径补偿取消,长度补偿取消,固定循环取消,绝对编程)
( 10. CENTER DRILL TOOL - 1 DIA. OFF. - 1 LEN. - 1 DIA. - 10.)(刀具说明)
N104T1M6(换刀)
N106G0G90G54X0.Y0.S1145M03M08(调用工件坐标系,刀具移至X0Y0,启动主轴,开冷却泵)
N108G43H1Z50.(长度正补偿,刀具运动至安全高度)
N110Z2.(刀具运动至下刀位置)
N112G1Z-63.F90(第一次啄钻,深度至为Z-63。
这段可以删除)
N114G0Z2.(快速退回至R点。
此程序段可删除)
N116Z-61.(快速运动至Z-61的位置,留有2mm的啄孔间隙)
N118G1Z-68F90(钻至Z-68的深度,从Z-63钻至Z-68,每次啄钻5mm)
N120G0Z2.(快速退回至下刀位置)
N122Z-66.(快速运动至Z-66的位置,留有2mm的啄孔间隙)
N124G1Z-73.(钻至Z-73的深度,从Z-68钻至Z-73,每次啄钻5mm)
N126G0Z2.
N121G04P2000(延时2秒。
此程序段为手工插入)
N128Z-71.
N130G1Z-78.
……
从上面程序中可以看出,第一次啄钻深度即达Z-68的位置,使整个加工过程的时间缩短。
但因没有延时,故需用手工对程序进行修改。
一般只需要在钻至较深的位置时插入G04 P2000程序段(延时2秒),使钻头在R点延时足够的时间,以充分冷却钻头,保证钻头有足够的耐用度。
三、结论
通过合理地设置钻孔加工参数和适当地修改后置处理文件,使自动编程产生的程序能满足深孔加工的断屑、保证刀具充分冷却等实际情况。