钣金件焊接质量检验规范--范文
钣金件检验标准5则范文

钣金件检验标准5则范文第一篇:钣金件检验标准3063钣金件检验标准一、适用范围: 公司产品306钣金件的尺寸、外观检验。
二、检验项目及验收标准: A.尺寸验收标准: 尺寸按图纸要求及钣金加工公差表执行,特殊情况以实际装配为准。
B.表面处理验收标准: 1.颜色、图案、光泽度与样板相符合,同批产品无色差(不得大于3度)。
2.附着检验:用百格刀划一面100方格到底材后,用3M胶布贴上,60度方向瞬间用力拉开,不得脱落40/100格。
3.溶剂检验:酒精擦拭后,不能有变色、掉色、无光泽等现象。
4.硬度检验:以H铅笔将笔芯前端切齐,铅笔与待测物成45度推出,表面无划伤。
C 外观判定标准, 1.表面不得有任何碰伤、开裂、刮伤等严重表面缺陷。
2.表面污点、颗粒、气泡检验: 2.1 A面: 整个表面内允许3点,每点直径1mm以下,点与点距离20mm以上。
2.2 B面: 整个表面内允许5点,每点直径1mm以下,点与点距离20mm以上。
2.3 C 面: 整个表面内允许7点,每点直径1mm以下,点与点距离20mm以上3.箱体内表面允许8点气泡或污点, 每点直径1mm以下,点与点距离20mm以上。
4.烤漆厚度30μm-60μm。
5、不得有纹印,粘有织物绒毛现象;6、不能有流挂:表面有液体流淌状的突起,顶端呈圆珠状;7、不能有颗粒:表面呈砂粒状,用手摸有阻滞感;8、不能有桔皮:外观呈现如桔皮般凹凸不平,不规则波纹; 5)不能有漏底:表面透青,露出底材颜色;6)不能有麻点:表面因收缩而呈现小孔(麻点),亦称针孔;7)不能有发花:表面颜色深浅不一,呈花纹状;8)不能起皱:局部堆积凸起,呈皱纹状(皱纹粉除外);9 不能有夹杂:涂层中夹有杂物;机械损伤:外力所致的划伤、刮花、磨损、碰伤。
备注:A面:使用时面对使用者的表面B面:与A面相邻的4个表面、C面:使用时背对使用者的表面第二篇:钣金件检验规范钣金件检验规范包装质量要求1、目的明确来料的包装要去,确保外包装能有效防护产品,避免在运输、搬运等过程造成损伤,同时确保来料产品易于识别和追溯。
钣金件设计规范范文

钣金件设计规范范文一、材料选择1.钣金件的材料选择应符合设计要求,根据使用环境和功能要求选择适当的材料。
2.材料的选择应考虑产品的强度、硬度、耐磨性、耐腐蚀性等性能指标。
二、结构设计1.钣金件的结构设计应满足产品的使用要求,确保合理分布载荷,提高产品的强度和刚度。
2.钣金件的结构设计应符合机械设计原理,避免应力集中、应力过高等问题的出现。
三、尺寸精度控制1.钣金件的尺寸精度应符合图纸和设计要求,尺寸偏差应控制在允许范围内,确保产品的互换性。
2.设计中应考虑到材料的收缩和变形等因素,合理设置公差,确保尺寸的精度和一致性。
四、工艺要求1.钣金件的工艺要求应明确,包括切割、弯曲、冲孔、焊接、打磨、抛光等工艺的要求和方法。
2.工艺要求应确保产品的加工精度、加工质量和外观要求,避免外表缺陷、毛刺和裂纹等问题的出现。
五、焊接要求1.钣金件的焊接应符合相关的焊接标准和规范,包括焊接工艺、焊接材料的选择和焊接质量的要求。
2.焊缝应均匀、牢固,焊接点应充分焊透,避免焊缝开裂、气孔和夹渣等问题。
六、表面处理1.钣金件的表面处理应符合使用要求,包括防腐处理、表面喷漆、镀铬、电镀等。
2.表面处理应提供一定的耐磨性、耐腐蚀性和美观性,确保产品的外观质量。
七、装配要求1.钣金件的装配应符合设计要求,确保装配的精度、装配的牢固性和安全性。
2.装配过程中应注意避免零件的变形、划伤和损坏等情况的发生。
八、质量检验1.钣金件的质量检验应按照相关的标准和规范进行,包括尺寸测量、外观质量、强度检验等方面。
2.质量检验应覆盖产品的各个环节,从材料采购、加工制造到成品出厂,确保产品的合格率和合格质量。
以上就是钣金件设计规范的主要内容,设计人员在设计过程中应严格按照规范进行,确保产品的质量和安全性。
同时,也需要与相关的生产工艺人员和质量检验人员密切配合,共同保证产品的设计、制造和使用的一致性和有效性。
钣金件检验标准
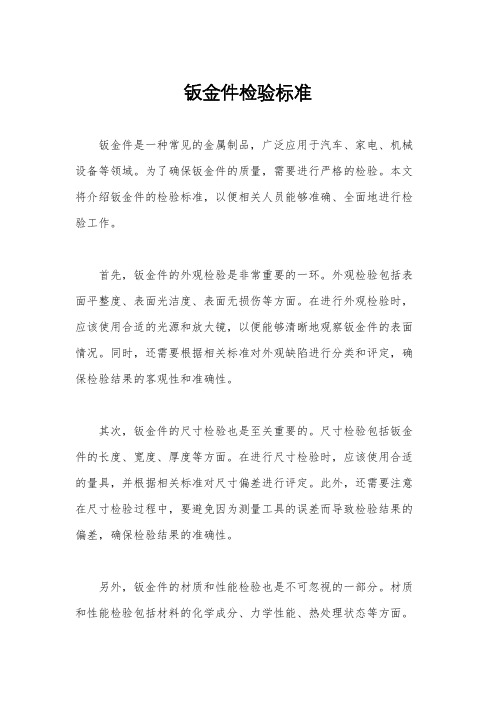
钣金件检验标准钣金件是一种常见的金属制品,广泛应用于汽车、家电、机械设备等领域。
为了确保钣金件的质量,需要进行严格的检验。
本文将介绍钣金件的检验标准,以便相关人员能够准确、全面地进行检验工作。
首先,钣金件的外观检验是非常重要的一环。
外观检验包括表面平整度、表面光洁度、表面无损伤等方面。
在进行外观检验时,应该使用合适的光源和放大镜,以便能够清晰地观察钣金件的表面情况。
同时,还需要根据相关标准对外观缺陷进行分类和评定,确保检验结果的客观性和准确性。
其次,钣金件的尺寸检验也是至关重要的。
尺寸检验包括钣金件的长度、宽度、厚度等方面。
在进行尺寸检验时,应该使用合适的量具,并根据相关标准对尺寸偏差进行评定。
此外,还需要注意在尺寸检验过程中,要避免因为测量工具的误差而导致检验结果的偏差,确保检验结果的准确性。
另外,钣金件的材质和性能检验也是不可忽视的一部分。
材质和性能检验包括材料的化学成分、力学性能、热处理状态等方面。
在进行材质和性能检验时,需要使用相应的实验设备和试验方法,确保检验结果的可靠性和准确性。
同时,还需要对检验结果进行合理的解读,并根据相关标准对材质和性能的合格与否进行评定。
最后,钣金件的包装和标识也需要进行检验。
包装和标识检验包括包装的完整性、标识的清晰度、标识的准确性等方面。
在进行包装和标识检验时,需要根据相关标准对包装和标识的要求进行检查,确保产品能够符合相关的法规和标准要求。
总之,钣金件的检验工作是非常重要的,它直接关系到产品的质量和安全。
只有严格按照相关标准进行检验,才能够保证钣金件的质量达到要求。
希望本文所介绍的钣金件检验标准能够对相关人员有所帮助,确保产品质量和用户利益。
钣金产品检验规范

文件编号:QA-002
版本version: 版次Edition Number :01
页码:第 页 ,共 12 页
文件名称
钣金产品通用检验规范
File Name Sheet Metal Inspection Standards
制订部门Develop Department: 品质部Quality Department
3.1.16剥离:噴涂表面局部脫落。 Peeling:Some spraying areas peel.
3.2.3刮伤:喷涂表面划伤,且已伤至底层,露出金属底材颜色。 Scuffing: There are scratches on the spraying surface,even scratch into base material so that the color of base metal material exposes.
3.1.4变色:底色或预期的颜色发生改变,或零件表面不同区域的颜色、光泽程度不一致。 Color-changing:Bottom color or prospective color changes; or the color and glossinee of different areas on the surface of spare part are different, not the same.
3.1.7镀痕/流痕:由于镀层厚度不均匀造成零件表面上波纹状或条状异常的区域。 Plating mark/flow mark: Because of the unevenly thick plating layer, there are corrugated or strip-like lines on some areas.
焊接检验标准:规范钣金结构件的检验标准
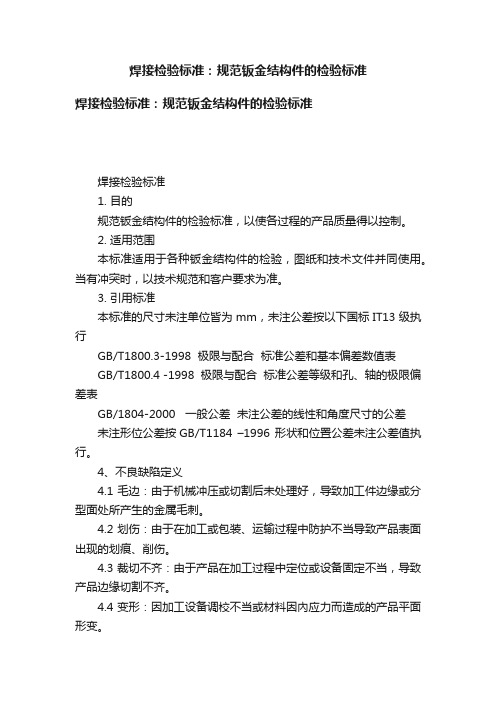
焊接检验标准:规范钣金结构件的检验标准焊接检验标准:规范钣金结构件的检验标准焊接检验标准1. 目的规范钣金结构件的检验标准,以使各过程的产品质量得以控制。
2. 适用范围本标准适用于各种钣金结构件的检验,图纸和技术文件并同使用。
当有冲突时,以技术规范和客户要求为准。
3. 引用标准本标准的尺寸未注单位皆为mm,未注公差按以下国标IT13级执行GB/T1800.3-1998 极限与配合标准公差和基本偏差数值表GB/T1800.4 -1998 极限与配合标准公差等级和孔、轴的极限偏差表GB/1804-2000 一般公差未注公差的线性和角度尺寸的公差未注形位公差按GB/T1184 –1996 形状和位置公差未注公差值执行。
4、不良缺陷定义4.1 毛边:由于机械冲压或切割后未处理好,导致加工件边缘或分型面处所产生的金属毛刺。
4.2 划伤:由于在加工或包装、运输过程中防护不当导致产品表面出现的划痕、削伤。
4.3 裁切不齐:由于产品在加工过程中定位或设备固定不当,导致产品边缘切割不齐。
4.4 变形:因加工设备调校不当或材料因內应力而造成的产品平面形变。
4.5 氧化生锈:因产品加工后未进行相应防锈处理或处理措施不当,而导致产品表面出现锈斑。
4.6 尺寸偏差:因加工设备的精度不够,导致产品尺寸偏差超过设计允许水平。
4.7“R角”过大/小:产品因折弯或冲压设备精度不够,导致折弯处弧度过大/小。
4.8 表面凹痕:由于材料热处理不好或材料生锈,其内部杂质导致金属表面形成的凹痕。
4.9 倒圆角不够:产品裁切边缘因切割或冲压原因产生的锐边未处理成圆弧状,易导致割手。
4.10 硬划痕:由于硬物磨擦而造成产品表面有明显深度的划痕(用指甲刮有明显感觉)。
4.11虚焊:因焊接操作不当造成的焊接不牢固。
4.12裂纹:焊后焊口处出现的裂痕。
5、焊接检验标准5.1焊缝应牢固、均匀,不得有虚焊、裂纹、未焊透、焊穿、豁口、咬边等缺陷。
焊缝长度、高度不均不允许超过长度、高度要求的10%。
钣金设计规范

钣金设计规范钣金设计规范是指钣金加工和设计中需要遵循的一系列标准和要求。
下面是一份钣金设计规范的范例,仅供参考。
一、材料选择和规范1. 钣金材料应符合国家相关标准,如GB/T、ASTM等。
2. 板材厚度的选择应根据设计要求和力学分析进行合理计算。
3. 不同材料的选择应考虑其物理、化学性能的适应性,确保材料的强度、耐蚀性和可焊性等性能满足要求。
二、加工工艺和规范1. 钣金加工过程中应确保对操作人员和设备的安全,并采取相应的防护措施。
2. 加工过程中应避免产生过多的热变形和应力集中,使用合适的冷却介质和工艺控制,如冷却水等。
3. 加工精度要求高的钣金件应采取适当的夹持装置和定位方式,确保其形状和尺寸的准确性。
三、表面处理和喷涂规范1. 钣金件表面处理应根据设计要求和使用环境选择合适的方式,如除锈、抛光、喷砂等。
2. 喷涂涂料应符合相关的标准和规范,确保涂层的附着力、耐腐蚀性和美观度。
3. 各工序之间应有合理的缓冲时间,防止过早的重叠喷涂或处理,造成质量问题。
四、焊接和连接规范1. 焊接工艺应符合相关的标准和规范,如焊接材料的选择、焊接接头的形式、焊接电流和电压的控制等。
2. 焊接前应进行合适的预热处理,控制焊接过程中的温度和速度,使接头处得到良好的焊接质量。
五、设计尺寸和公差规范1. 钣金件的设计尺寸应符合相关的标准和规范,如图样加工尺寸、公差限制等。
2. 钣金件的公差应根据其用途和重要程度进行合理设定,精度要求高的部件应采用较小的公差限制。
六、安全和环保规范1. 钣金加工过程中应符合相关的安全规定,如操作人员的防护用具、紧急停机设备等。
2. 钣金加工过程中应减少废料和废弃物的产生,合理利用资源,符合环保要求。
七、质量检验和测试规范1. 钣金件的质量检验应根据相关标准和规范进行,如外观质量、尺寸偏差、表面粗糙度等。
2. 钣金件的力学性能和耐腐蚀性能等也应进行合适的测试和检验,确保其质量和使用寿命。
八、设计文件和记录规范1. 钣金件的设计图纸应准确、清晰,包含必要的尺寸、公差、材料信息、表面处理要求等。
焊接检验规范
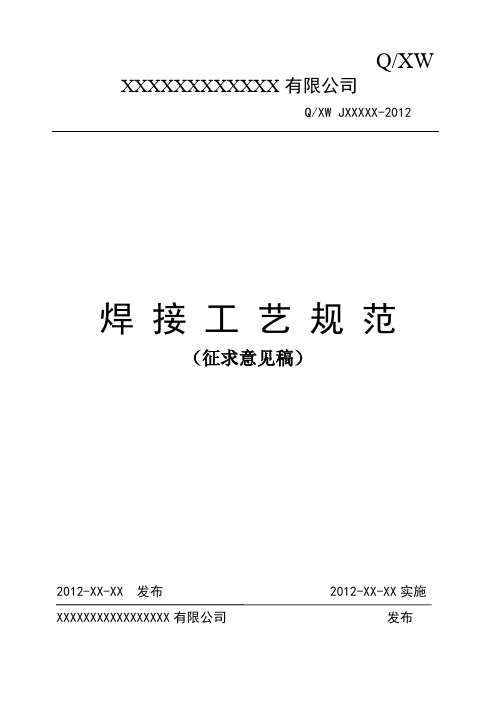
Q/XW XXXXXXXXXXXX有限公司Q/XW JXXXXX-2012焊接工艺规范(征求意见稿)2012-XX-XX 发布 2012-XX-XX实施XXXXXXXXXXXXXXXXX有限公司发布Q/XW JXXXXX-2012 1.目的确定钣金件焊接时的工艺守则,确定检验作业条件,明确检验方法,建立判定标准,以确保产品品质。
2.适用范围本规范本规程适用于公司通用产品的焊接指导与检验;当本规范与工艺文件和图纸冲突时,以工艺文件和图纸为准。
3.引用标准GB/T706-2008 《热轧型钢》GB/T1800.3 《标准公差数值》GB10854-89 《钢结构焊缝外形尺寸》GB/T 2828 《逐批检查计效抽样程序及抽样表》GB/T19804-2005 《焊接结构的一般尺寸公差和行为公差》GB/T12469-90 《焊接质量保证钢熔化焊接头的要求和缺陷分级》GB/T709-2006 《热轧钢板和钢带的尺寸、外形、重量及允许偏差》4.工艺要求4.1焊接方法选用原则表1 焊接方法选用原则Q/XW JXXXXX-2012 4.2 焊接用辅料援用原则表2 焊接用辅料援用原则4.3 点焊接头的最小搭边宽度和焊点的最小点距点焊接头的最小搭边宽度最小搭边宽度b=4δ+8 (δ取最大值)b —搭边宽度 mmδ—材料厚度 mm表3 点焊接头的最小搭边宽度和焊点的最小点距单位:mmQ/XW JXXXXX-2012 4.4 点焊焊接工艺规范表4 点焊焊接工艺规范Q/XW JXXXXX-2012 4.5 螺母凸焊焊接工艺规范表5 螺母凸焊焊接工艺规范4.6 CO2 焊焊接工艺规范表6 CO2 焊焊接工艺规范Q/XW JXXXXX-2012 4.7 CO2 定位焊缝的长度和间距5. CO2保护焊作业指导二氧化碳气体保护焊用的CO2气体,大部分为工业副产品,经过压缩成液态装瓶供应。
在常温下标准瓶满瓶时,压力为5~7MPa(50~70kgf/cm2)。
钣金件外观质量验收规范

2.9待抛光的不锈钢钣金件、焊接件划痕深度<0.05mm。
2.10氩弧焊、二氧化碳气体保护焊、氧焊、压力电阻焊零件,按焊接及打磨修整实物标样进行外观质量验收检验。
2.6零件点焊或断续焊时,要求焊点分布均匀,在同一平面内焊点间距基本一致,间距公差±3mm,点焊焊点基本大小一致,焊点半径≤3mm,深度≤0.5mm。
2.7零件连续焊时,外观焊缝应光滑平整或呈均匀的西鳞波纹状,不允许有尖角、熔渣、氧化皮、烧穿、塌角、咬边。焊缝修整半径≤折弯半径,且基本一致。不形成零件外形尺寸轮廓的焊缝可不打磨(主要是焊接结构件)。
1范围
本标准规定了钣金件、焊接件外观质量验收准则。
本标准适用于钣金件、焊接件外观质量的检验和判定。
2.验收准则
2.1钣金件、焊接件表面应光滑、平整、无凹凸,不允许有锤痕、手感明显的压痕、喷溅、浮锈、划伤、打磨凹坑等缺陷。
2.2钣金件、焊接件(涂漆件除外)表面有划痕或焊接痕迹时,不能局部打磨,要做外表整体修整。修整时,应采取由粗至细多层次抛磨的修整方法,保证零件表面整体光滑、平整、抛磨纹路一致。
2.3允许钣金涂漆件表面局部有油漆层可遮盖的轻微划痕(划痕深度≤0.2mm),划痕两边不能有凸起。在钣金涂漆件表面可做局部打磨修整,修整时,除点焊自然形成的无法消除的圆形凹坑外,不允许形成打磨凹坑、抛光片打磨形成的深痕。
2.4钣金件表面处理前不允许有明显划痕,钣金件表面处理前外表面允许缺陷按表1。
表1钣金件表面处理前允许的缺陷
零件外表面尺寸
划痕长度L(mm)
划痕深度H(mm)
处数N
长度(mm)
宽度(mm)
<100
- 1、下载文档前请自行甄别文档内容的完整性,平台不提供额外的编辑、内容补充、找答案等附加服务。
- 2、"仅部分预览"的文档,不可在线预览部分如存在完整性等问题,可反馈申请退款(可完整预览的文档不适用该条件!)。
- 3、如文档侵犯您的权益,请联系客服反馈,我们会尽快为您处理(人工客服工作时间:9:00-18:30)。
钣金件焊接质量检验规范—范文1.目的确定钣金件焊接时的工艺守则,确定检验作业条件,明确检验方法,建立判定标准,以确保产品品质。
2.适用范围本规范本规程适用于公司通用产品的焊接指导与检验;当本规范与工艺文件和图纸冲突时,以工艺文件和图纸为准。
3.引用标准GB/T706-2008 《热轧型钢》GB/T1800.3 《标准公差数值》GB10854-89 《钢结构焊缝外形尺寸》GB/T 2828 《逐批检查计效抽样程序及抽样表》GB/T19804-2005 《焊接结构的一般尺寸公差和行为公差》GB/T12469-90 《焊接质量保证钢熔化焊接头的要求和缺陷分级》GB/T709-2006 《热轧钢板和钢带的尺寸、外形、重量及允许偏差》4. 工艺要求4.1焊接方法选用原则4.2 焊接用辅料援用原则4.3 点焊接头的最小搭边宽度和焊点的最小点距点焊接头的最小搭边宽度最小搭边宽度b=4δ+8 (δ取最大值)b —搭边宽度mm δ—材料厚度mm 4.4 点焊焊接工艺规范4.5 螺母凸焊焊接工艺规范4.6 CO2 焊焊接工艺规范4.7 CO2 定位焊缝的长度和间距5. CO2保护焊作业指导二氧化碳气体保护焊用的CO2气体,大部分为工业副产品,经过压缩成液态装瓶供应。
在常温下标准瓶满瓶时,压力为5~7MPa(50~70kgf/cm2)。
低于1MPa(10个表压力)时,不能继续使用。
焊接用的CO2气体,一般技术标准规定的纯度为99%以上,使用时如果发现纯度偏低,应作提纯处理。
二氧化碳气体保护焊的规范参数包括电源极性、焊丝直径、电弧电压、焊接电流、气体流量、焊接速度、焊丝伸出长度、直流回路电感等。
a. 电源极性二氧化碳气体保护焊焊接一般材料时,采用直流反接;在进行高速焊接、堆焊和铸铁补焊时,应采用直流正接。
b. 焊丝直径二氧化碳气体保护焊的焊丝直径一般可根据表选择。
c. 电弧电压和焊接电流对于一定直径的焊丝来说,在二氧化碳气体保护焊中,采用较低的电弧电压,较小的焊接电流焊接时,焊丝熔化所形成的熔滴把母材和焊丝连接起来,呈短路状态称为短路过渡。
大多数二氧化碳气体保护焊工艺都采用短路过渡焊接。
当电弧电压较高、焊接电流较大时,熔滴呈小颗粒飞落称为颗粒过渡。
φ1.6或φ2.0mm 的焊丝自动焊接中厚板时,常采用这种过渡。
φ3mm以上的焊丝应用较少。
ΦO.6~φ1.2mm的焊丝主要采用短路过渡,随着焊丝直径的增加,飞溅颗粒的数量就相应增加。
当采用φ1.6mm的焊丝,仍保持短路过渡时,飞溅就会非常严重。
焊接电流与电弧电压是关键的工艺参数。
为了使焊缝成形良好、飞溅减少、减少焊接缺陷,电弧电压和焊接电流要相互匹配,通过改变送丝速度来调节焊接电流。
在小电流焊接时,电弧电压过高,金属飞溅将增多;电弧电压太低,则焊丝容易伸人熔池,使电弧不稳。
在大电流焊接时,若电弧电压过大,则金属飞溅增多,容易产生气孔;电压太低,则电弧太短,使焊缝成形不良。
d. 气体流量二氧化碳气体流量与焊接电流、焊接速度、焊丝伸出长度及喷嘴直径等有关。
气体流量应随焊接电流的增大、焊接速度的增加和焊丝伸出长度的增加而加大。
一般二氧化碳气体流量的范围为8~25L/min。
如果二氧化碳气体流量太大,由于气体在高温下的氧化作用,会加剧合金元素的烧损,减弱硅、锰元素的脱氧还原作用,在焊缝表面出现较多的二氧化硅和氧化锰的渣层,使焊缝容易产生气孔等缺陷;如果二氧化碳气体流量太小,则气体流层挺度不强,对熔池和熔滴的保护效果不好,也容易使焊缝产生气孔等缺陷。
e. 焊接速度随着焊接速度的增大,则焊缝的宽度、余高和熔深都相应地减小。
如果焊接速度过快,气体的保护作用就会受到破坏,同时使焊缝的冷却速度加快,这样就会降低焊缝的塑性,而且使焊缝成形不良。
反之,如果焊接速度太慢,焊缝宽度就会明显增加,熔池热量集中,容易发生烧穿等缺陷。
f. 焊丝伸出长度指焊接时焊丝伸出导电嘴的长度。
焊丝伸出长度增加,则使焊丝的电阻值增加,造成焊丝熔化速度加快,当焊丝伸出长度过长时,因焊丝过热而成段熔化,结果使焊接过程不稳定、金属飞溅严重、焊缝成形不良和气体对熔池的保护作用减弱;反之,当焊丝伸出长度太短时,则焊接电流增加,并缩短了喷嘴与焊件之间的距离,使喷嘴过热,造成金属飞溅物粘住或堵塞喷嘴,从而影响气流的流通。
一般,细丝二氧化碳气体保护焊,焊丝伸出长度为8~14mm;粗丝二氧化碳气体保护焊,焊丝伸出长度为10~20mm。
g. 直流回路电感在焊接回路中,为使焊接电弧稳定和减少飞溅,一般需串联合适的电感。
当电感值太大时,短路电流增长速度太慢,就会引起大颗粒的金属飞溅和焊丝成段炸断,造成熄弧或使起弧变得困难;当电感值太小时,短路电流增长速度太快,会造成很细颗粒的金属飞溅,使焊缝边缘不齐,成形不良。
再者,盘绕的焊接电缆线就相当于一个附加电感,所以一旦焊接过程稳定下来以后,就不要随便改动。
6. 零部件的焊接6.1 焊接前对各零部件依照图样进行认真检查,如发现材料尺寸不符合或有严重缺陷的不得进行焊;机械加工件不得有磕碰划伤现象,影响外观质量的不得擅自使用;以上情况应及时上报质检员,并由质检员重新确认是否可以使用。
6.2 电焊条、焊丝等质量必须符合国家有关标准的规定。
6.3 凡标牌不清、品质不明、包装破损或储存期过长的焊条、焊丝,必须经检验鉴定符合标准规定后方可使用。
6.4 电焊条受潮及存放时间较长应进行烘干后方可使用。
6.5 焊接前应检查周围环境、焊接设备及工具是否符合工艺和安全要求。
6.6 电焊条、焊丝的选用应根据以下原则选择:a、当焊件母材为低碳或低合金钢时应按强度等级原则选择。
b、对于耐热钢、不锈钢等应选择与母材化学成分一致的焊条。
c、根据焊件的工作条件、使用性能及焊接设备、工艺条件、焊接效率和经济性选择。
d、图样及工艺有要求的按图样、工艺规定的执行。
6.7 焊接设备的选择应根据零部件的材料、结构、设备工作场地进行选择,图样及工艺有要求的按图样、工艺规定的执行。
6.8 零件的焊前清理:6.8.1 焊接前应清除锈蚀、氧化皮、油污、气割飞溅物等,焊件有明显弯曲和凹凸不平的应校直校平后再进行焊接。
6.8.2 机械加工件焊前必须清理锈蚀和油污,清理过程中注意保护加工件的外露边或面,尤其是焊后不加工的光面。
6.8.3 焊接后无法除锈、清除氧化皮等表面处理的应进行表面处理后再进行焊接。
6.9 焊接过程的工艺要求:6.9.1 为保证各焊接零件之间的相互位置应首先进行定位焊接,自检焊件位置尺寸无误后再进行连续焊接。
6.9.2 钢板之间、型材之间或者相互之间的对接,焊接接头对口的错边量不得超出下表的规定:6.9.3 焊接较大构件时为减小焊接变形,应根据焊缝的不同部位、变形的方向采用合理的焊接顺序和焊接方向,尽量采用对称焊接法进行焊接,对变形量较大的构件应先进行小部件组焊,组后将各组焊件拼焊成形。
6.9.4 板材拼接时应根据板厚预留0.5mm—3mm的间隙。
6.9.5 根据焊件的材质、厚度及焊接设备、焊接部位、焊条及焊丝规格等选择合适的电流、电压、焊接速度及运条方法。
a、多层多道的CO2气保焊尽量采用小焊脚,保证焊缝均匀平滑。
角焊单层焊脚一般不大于6mm最大不能超过10mm,如:12—15mm 焊脚需要采用两层四道焊缝。
大焊脚的长焊缝尽量根据位置采用埋弧焊。
b、“V”型坡口CO2气保焊,单层焊缝厚度不大于6mm,打底焊不大于4mm。
c、平焊缝单道焊缝宽度不大于8mm,焊缝高度不高于3mm,直线度和平面度≤2mm。
d、CO2气体保护焊电流须在260A以上才能获得较大熔深。
在开坡口(钝边≤2且留间隙)条件下,使用Ф1.2的焊丝打底焊推荐电流90—120A。
填充焊和盖面焊可适当加大电流,确保层间融合并避免冷裂纹。
6.9.6 焊接铸铁件等较重要件时应先坡口、预热后再焊接,并采取保温措施。
6.9.7 焊缝多层施焊时,应将前道焊缝的焊渣清理干净,并打磨焊瘤将不良焊缝修磨至合格。
6.9.8 焊缝的补焊应先清除油污、重新坡口、打磨后再进行焊接。
7. 焊接件的检验7.1 检验工具检验用焊缝尺寸测量尺、卷尺、钢直尺、游标卡尺等量具应经计量室检定或校准,量具上应有检定或校准合格标志并在合格有效期内。
7.2 焊前检验7.2.1 焊前检验的定义:当天生产开始、更换产品、更换设备、维修设备生产中断、换操作人员等情况均应首检。
7.2.2 焊接操作前焊工应做好相关准备工作由焊工对下列项目自检后报焊接检验员检验进行焊前检验,焊前检验合格后在零件醒目位置上做合格标识,焊前检验不合格焊工不得继续操作。
7.3 焊前检验项目:—图样、工艺文件的适用性;—焊工操作证书的适用性、有效性;—仪表、量具的有效性;—母材及制备的检验(如坡口形状、尺寸等);—焊接材料的检验;—工装、夹具及定位;焊接工作条件的适宜性—工艺文件、操作规程的特殊要求,如防止变形;7.4 过程巡检7.4.1在焊接过程中检验员应不断的对各工位按下列项目进行巡检,一般时间间隔不超过一小时,巡检过程如中发现影响后续焊接质量的因素操作人员应立即停工整改。
7.4.2 巡检项目:—主要焊接参数(如电流、电弧电压、焊接速度)—预热温度(如工艺文件有要求);—焊接顺序(如工艺文件有要求);—焊接材料和正确使用及保管;—变形的控制;—中间检查,如尺寸检验。
7.5 最终检验7.5.1 按照图纸检查焊缝是否焊接完毕。
7.5.2 焊缝的外形尺寸a. 焊缝最大宽度和最小宽度的差值,在任意50mm焊缝长度范围内不得大于4mm,整个焊缝长度范围内不得大于5mm。
b. 除图样或工艺规范有特殊要求,埋弧焊焊缝余高为0~3mm,手工电弧焊、气体保护焊焊缝余高平焊为0~3mm,手工电弧焊、气体保护焊焊缝余高其余焊法为0~4mm 。
焊缝表面凹凸,在焊缝任意25mm长度范围内,焊缝余高的差值不得大于2mm。
c. 焊缝边缘直线度,在任意300mm连续焊缝长度内,焊缝边缘沿焊缝轴向的直线度,埋弧焊不得大于4mm,手工电弧焊、气体保护焊不得大于3mm。
7.6 抽样原则在对焊接件进行计数抽检时,一般按GB2828一般检查水平Ⅱ级,正常检查一次抽样方案AQL=2.57.7 焊缝缺陷7.7.1各单位应在技术文件中规定焊接缺陷检验标准,如图样或相关技术文件无特殊要求,焊接缺陷不得超过下表Ⅲ级。
注:a)表内δ为连接处较薄的板厚;h 为设计焊缝有效厚度b)除注明角焊缝缺陷外其余均为对接、角接焊缝通用。
C)咬边如经磨削修整并平滑过渡则只按焊缝最小允许厚度值评定。
D)特定条件下要求平缓过渡时不受本规定限制7.7.2当要求检测焊缝内部缺陷时,应制订相应检测规程,规定内部缺陷级别。
7.8 焊接结构的尺寸公差和形位公差7.8.1 焊接结构的尺寸公差和形位公差应符合图样、工艺文件或各单位规定的技术标准要求,如无特殊要求则按7.8.2、7.8.3、7.8.4中Ⅰ级公差。