不锈钢对数控刀具设计要求
加工不锈钢对刀具、磨具材料及几何参数的选择

奥 氏体 不 锈 钢 是 以 铬 、 为 主 要 合 金 元 镍 素 , 量 加 入 钼 、 、 或 铌 而 成 的 高 耐 蚀 合 适 钨 钛 金 ,CrNiTi I 8 9 及Cr 8 1 l Ni0等 属 此 类 。 氏体 奥 不锈钢加热时 , 其组 织 不 变 , 火 不 能 使 其 强 淬 化, 韧性 和 塑 性 约 为 4 5钢 的 1 5倍 , 通 过 冷 . 但 加 工 硬 化 可 大 幅度 提高 强 度 。
维普资讯
总第 8 6期 20 0 2年 第 2期
山 西 冶 金
SH A N X I M E T A L L U R G Y
T ot 86 al
N o・ 2002
加 工 不 锈 钢 对 刀 具 、 具 材 料 及 几 何 参 数 的 选 择 磨
ma u a t r n r n n h s ma e i l ti e y i o t n o o t h o e t em a e ilo n f n f c u e a d g i di g t i t ra ,i sv r mp r a t f r h w O c o s h t ra fk i e
Abs r c T hi r il nt duc s t a nl ss e land is e ele ec nialpr ta t s a tc e i r e hest i es t e t xc l ntm ha c ope t be a e of r y c us is s cal r t pe i p ope t r y. I aus e t o ffculis t m anuf c ur he s a nl s t e , t tc e a gr a fdifi te O a t e t t i es s e l hus,w he n
【推荐下载】浅谈不锈钢切削加工中刀具切削参数
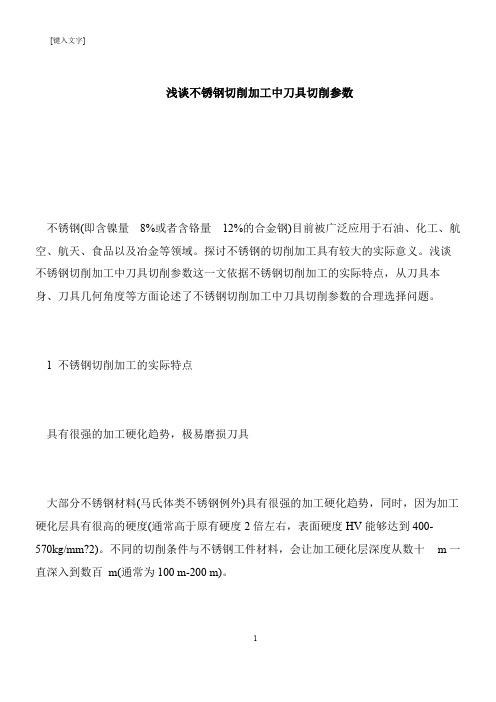
浅谈不锈钢切削加工中刀具切削参数 不锈钢(即含镍量8%或者含铬量12%的合金钢)目前被广泛应用于石油、化工、航空、航天、食品以及冶金等领域。
探讨不锈钢的切削加工具有较大的实际意义。
浅谈不锈钢切削加工中刀具切削参数这一文依据不锈钢切削加工的实际特点,从刀具本身、刀具几何角度等方面论述了不锈钢切削加工中刀具切削参数的合理选择问题。
1 不锈钢切削加工的实际特点 具有很强的加工硬化趋势,极易磨损刀具 大部分不锈钢材料(马氏体类不锈钢例外)具有很强的加工硬化趋势,同时,因为加工硬化层具有很高的硬度(通常高于原有硬度2倍左右,表面硬度HV能够达到400-570kg/mm?2)。
不同的切削条件与不锈钢工件材料,会让加工硬化层深度从数十m一直深入到数百m(通常为100 m-200 m)。
切屑不易折断或者卷曲 切削过程中切屑不易卷曲和折断。
特别是镗孔、钻孔、切断等工序的切削过程中,排屑困难,切屑易划伤已加工表面。
在数控机床上切削不锈钢时,断屑与排屑是重点考虑的问题。
切屑具有很强的粘附性,极易造成刀瘤 不锈钢材料具有很高的韧性,尤其是对其它金属材料具有较强的亲和力,加工过程非常容易造成刀瘤。
三高(高温度、高硬度、高强度)不易分离切屑 不锈钢的特性之一就是高温度、高硬度、高强度。
例如温度维持在700 C的奥氏体类不锈钢的机械性能仍不会显着降低。
tips:感谢大家的阅读,本文由我司收集整编。
仅供参阅! 本文结合多年的材料管理经验,分析了当前施工企业在材料管理方面存在的问题,并针对性的提出了相应的对策,试论施工现场材料管理若干问题的思考的详细内容请看下文。
随时我国城市化进程的不断开展,施工企业抓住建设的历史性发展机遇,在各个方面都有长足的进步,但有一个最根本的问题一直困扰施工企业,那就是市场竞争日趋激烈,工程标价不断降低,企业由于利润水平逐年下滑,普遍感到企业发展的后劲不足,唯一的出路就是加强内部管理,控制成本。
不锈钢加工刀具切削参数

不锈钢加工刀具切削参数一、引言不锈钢是一种常用的材料,应用广泛于各个行业中。
在不锈钢加工中,刀具的选择和切削参数的确定对于加工质量和效率具有重要影响。
本文将从不锈钢加工刀具的选择和切削参数的确定两个方面展开论述。
二、不锈钢加工刀具的选择选择合适的刀具是确保不锈钢加工成功的首要条件。
不锈钢具有较高的硬度和良好的耐磨性,因此在选择刀具时需要考虑以下几个因素:2.1 刀具材料不锈钢加工通常选择硬质合金刀具,因为硬质合金具有较高的硬度和耐磨性,能够在不锈钢的高温和高切削力下保持较好的切削性能。
常见的硬质合金材料有WC-Co、WC-TiC-TaC等。
2.2 刀具形状根据不锈钢加工的具体需求,选择合适的刀具形状是十分重要的。
常见的刀具形状包括平面铣刀、立铣刀、球头铣刀等。
平面铣刀适用于对不锈钢表面进行平整加工,立铣刀适用于进行深度加工,球头铣刀适用于进行轮廓加工等。
2.3 刀具涂层通过刀具涂层可以提高刀具的耐磨性和切削性能,延长刀具的使用寿命。
在不锈钢加工中,常用的刀具涂层有TiN、TiCN、TiAlN等,这些涂层具有良好的耐磨性和热稳定性。
三、不锈钢加工切削参数的确定除了选择合适的刀具外,还需要确定合适的切削参数才能保证加工质量和效率。
切削参数的确定与不锈钢材料的性质、加工要求和刀具特点等因素密切相关。
3.1 切削速度切削速度是切削参数中最重要的一个参数,它决定着切削时刀具与工件之间的相对运动速度。
在不锈钢加工中,切削速度不宜过高,一般建议控制在60-100 m/min之间。
3.2 进给量进给量是指单位切削时间内切削刀具在切削方向上的移动距离。
对于不锈钢加工,进给量要适中,过小会导致加工效率低下,过大则容易导致切削刃磨损过快。
因此,根据具体情况选择合适的进给量十分重要。
3.3 主轴转速主轴转速是指切削时主轴单位时间内旋转的圈数。
选择合适的主轴转速可以保证切削进给率和表面质量。
在不锈钢加工中,一般建议选择较低的主轴转速,以提高刀具寿命和加工质量。
切削不锈钢时怎样选择刀具几何参数

切削不锈钢时怎样选择刀具几何参数?瓦尔特,株洲钻石,山特2009-8-13 8:59:551、前角g0:不锈钢的硬度、强度并不高,但其塑性、韧性都较好,热强性高,切削时切屑不易被切离。
在保证刀具有足够强度的前提下,应选用较大的前角,这样不仅能够减小被切削金属的塑性变形,而且可以降低切削力和切削温度,同时使硬化层深度减小。
车削各种不锈钢的前角大致为12°~30°。
对马氏体不锈钢(如2Cr13),前角可取较大值;对奥氏体和奥氏体+铁素体不锈钢,前角应取较小值;对未经调质处理或调质后硬度较低的不锈钢,可取较大前角;直径较小或薄壁工件,宜采用较大的前角。
高速钢铣刀取gn=10°~20°,硬质合金铣刀取gn=5°~10°;铰刀一般取g0=8°~12°;丝锥一般取g0=15°~20°(机用)或g0=20°(手用)。
2、后角a0:加大后角能减小后刀面与加工表面的摩擦,但会使切削刃的强度和散热能力降低。
后角的合理值取决于切削厚度,切削厚度小时,宜选较大后角。
不锈钢车刀或镗刀通常取a0=10°~20°(精加工)或a0=6°~10°(粗加工);高速钢端铣刀取a0=10°~20°,立铣刀取a0=15°~20°;硬度合金端铣刀取a0=5°~10°,立铣刀取a0=12°~16°;铰刀和丝锥取a0=8°~12°。
3、主偏角kr、副偏角k′r,和re:减小主偏角可增加刀刃工作长度,有利于散热,但在切削过程中使径向力加大,容易产生振动,常取kr=45°~75°,若机床刚性不足,可适当加大。
副偏角常取k′r=8°~15°。
为了加强刀尖,一般应磨出e=0.5~1.0 mm 的刀尖圆弧。
数控刀具在耐蚀不锈钢材料零件中的应用

数控刀具在耐蚀不锈钢材料零件中的应用摘要:本文针对不锈钢 Z8CND17-04 材料,采用金相法对零件在最终进行疲劳试验发生断裂的质量问题进行了分析,定性地说明了加工的硬化层是导致零件表面产生裂纹的原因之一,结合公司现有的生产条件,制定了切削试验方案,避免了零件表面硬化层的产生,提高了零件的质量及生产效率。
关键词:不锈钢;金相;硬度;刀具寿命;硬化层1、现状与问题描述零件材料为法国标准牌号 Z8CND17-04 属于马氏体不锈钢,硬度HRC36-41,表面粗糙度 Ra0.4,一般车削加工实现比较困难。
实际加工选择肯纳刀具公司的刀片DNGP15402KC730。
切削速度111 m/min;进给 0.02 mm/s;切深 0.075 mm,零件加工完成后,要求做疲劳试验。
试验条件为在循环加载最小载荷 Fmin=-4859 KN,最大载荷Fmax=4083 KN 的作用下,寿命要达到 733 600 次以上。
但是公司加工的零件在试验进行到 110 000 次循环次数时靠近大端处发生断裂失效。
见图 1 所示。
图1 活塞断裂图2、原因分析2.1 金相分析从金相显示裂纹扩展是本次失效的主要原因,从切面可看到镀铬层和基体交界面,机加工纹路呈波浪状,镀铬层里的裂纹延伸至基体中并靠近断裂起始源,机加工表面粗糙度表现为铬层和基体交界处形成波峰和波谷,在波峰处存在残余拉应力,波谷处存在残余压应力。
大多数镀铬层的裂纹在交界面的波峰处产生,而且图2 中硬化层中存在扩展裂纹,初步断定镀铬层里的扩展裂纹是由加工硬化引起的。
图 2 断裂横截面2.2 对比试验分析对比其他供应商使用的刀片是DNMG110404MF1025。
我们对所用切削参数、加工后的金相图片、维氏硬度进行了对比,结果如下:从表 1 看出 DNMG11040404MF1025 的刀片几何圆角,切削速度,进给,切深均是DNGP150402KC730 的2 倍。
且在铬层和基体交界面显示平缓,刀片基体心部和表面差只有22 HV。
数控刀具材料金属切削加工的要求

数控刀具材料金属切削加工的要求数控刀具材料指与数控加工刀具匹配的切削部分的材料。
显然,数控刀具除满足属切削的基本要求外,还必须适应数控加工的特定要求。
1、刀具材料金属切削加工的基本要求金属切削过程中,刀具切削部分承受着很大的切削力与冲击力,并伴随着强烈的金属塑性变形与剧烈的摩擦,产生大量的切削热,造成切削区域极高的切削温度与温度梯度。
因此,刀具材料应具备以下基本性能。
(1)高的硬度和耐磨性刀具材料的硬度必须高于被加工材料的硬度,其硬度在室温条件下也应在62HRC以上。
如高速工具钢的硬度为63~70HRC,硬质合金的硬度为89~93HRA。
刀具材料的耐磨性是刀具材料抵抗磨损的能力。
一般来说,刀具材料硬度越高,耐磨性也越好。
此外,刀具材料的耐磨性还与金相组织中化学成分(碳化物、氮化物等)、硬质点的性质和数量、颗粒大小和分布状况等有关。
金相组织中碳化物越多,颗粒越细,分布越均匀,其耐磨性也越好。
(2)足够的强度和韧性刀具切削部分的材料在切削时要承受很大的切削力和冲击力,因此,刀具材料必须要有足够的强度和韧性,以确保其加工过程中不出现破损、崩刃等。
(3)耐热性指刀具材料高温下保持上述性能的能力,又称热硬性。
高温硬度越高,表示耐热性越好,因此在高温时抗塑性变形的能力、抗磨损的能力也越强。
一般碳素工具钢的热硬性约300℃、高速工具钢约600℃、硬质合金约900℃。
(4)导热性导热性好,则切削时产生的热量容易传导出去,从而降低切削部分的温度,减轻刀具磨损。
此外,导热性好的刀具材料其耐热冲击和抗热龟裂的性能增强,这种性能对采用脆性刀具材料进行断续切削,特别在加工导热性能差的工件时尤为重要。
(5)良好的加工工艺性加工工艺性指刀具材料加工制造的难易程度,刀具材的工艺性包括:锻造、焊接、切削加工、磨削和热处理等性能。
(6)经济性与市场购买性经济性是正确选用刀具材料、降低产品成本的主要据之一,也是评价新型刀具材料的重要指标之一。
切削不锈钢时怎样选择刀具几何参数

切削不锈钢时怎样选择刀具几何参数切削不锈钢时选择刀具几何参数非常重要,它直接影响到加工效率、表面质量和刀具寿命等方面。
在选择刀具几何参数时,一般需要考虑刀具材质、切削速度、进给速度、切削深度和刀具直径等因素。
下面将从这几个方面详细介绍如何选择刀具几何参数。
首先,选择合适的刀具材质是重要的一步。
不锈钢是一种难以切削的材料,具有高硬度、高强度和良好的耐腐蚀性等特点。
因此,切削不锈钢时需要使用具有较高硬度和较高热稳定性的刀具材料,如刚玉、PVD涂层硬质合金、PCD等。
这些材料具有很高的切削速度和硬度,能够有效地切削不锈钢。
其次,选择合适的切削参数。
切削速度和进给速度是选择刀具几何参数的关键因素之一、切削速度是指刀具在单位时间内切削工件的长度,进给速度是指工件在单位时间内移动的距离。
对于不锈钢材料,由于其硬度较高,切削时容易产生较大的摩擦和热量,因此需要使用较低的切削速度和进给速度。
通常建议切削速度在60-120米/分钟,进给速度在0.1-0.2毫米/刀齿。
另外,切削深度也是选择刀具几何参数时需要考虑的因素之一、切削深度是指刀具切削时每次进给的深度,它决定了每次切削的材料厚度。
对于不锈钢材料,切削深度一般建议控制在0.10-0.25毫米,以避免产生过大的热量和切削力,从而影响刀具寿命和加工质量。
最后,选择合适的刀具直径也是非常重要的。
刀具直径决定了切削过程中切削力和切削振动的大小。
通常情况下,刀具直径越大,切削力越大,切削振动越小。
对于不锈钢材料,由于其硬性较高,刀具直径选择较大一点可以提高切削效率并减小切削振动,同时也会增加切削力和刀具的受力情况。
因此,在选择刀具直径时需要综合考虑加工效率和刀具寿命等因素。
综上所述,选择刀具几何参数时需要考虑刀具材料、切削速度、进给速度、切削深度和刀具直径等因素。
合理选择刀具几何参数有助于提高切削效率、加工质量和刀具寿命。
不锈钢材料具有高硬度和高强度的特点,因此切削不锈钢时需要使用具有高硬度和高热稳定性的刀具材料,并选择适当的切削参数和刀具尺寸,以实现高效、稳定和优质的切削加工。
不锈钢nc加工参数
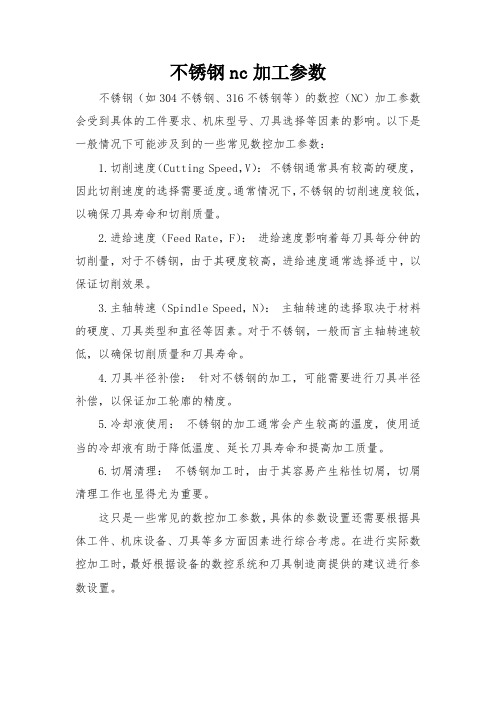
不锈钢nc加工参数
不锈钢(如304不锈钢、316不锈钢等)的数控(NC)加工参数会受到具体的工件要求、机床型号、刀具选择等因素的影响。
以下是一般情况下可能涉及到的一些常见数控加工参数:
1.切削速度(Cutting Speed,V):不锈钢通常具有较高的硬度,因此切削速度的选择需要适度。
通常情况下,不锈钢的切削速度较低,以确保刀具寿命和切削质量。
2.进给速度(Feed Rate,F):进给速度影响着每刀具每分钟的切削量,对于不锈钢,由于其硬度较高,进给速度通常选择适中,以保证切削效果。
3.主轴转速(Spindle Speed,N):主轴转速的选择取决于材料的硬度、刀具类型和直径等因素。
对于不锈钢,一般而言主轴转速较低,以确保切削质量和刀具寿命。
4.刀具半径补偿:针对不锈钢的加工,可能需要进行刀具半径补偿,以保证加工轮廓的精度。
5.冷却液使用:不锈钢的加工通常会产生较高的温度,使用适当的冷却液有助于降低温度、延长刀具寿命和提高加工质量。
6.切屑清理:不锈钢加工时,由于其容易产生粘性切屑,切屑清理工作也显得尤为重要。
这只是一些常见的数控加工参数,具体的参数设置还需要根据具体工件、机床设备、刀具等多方面因素进行综合考虑。
在进行实际数控加工时,最好根据设备的数控系统和刀具制造商提供的建议进行参数设置。
- 1、下载文档前请自行甄别文档内容的完整性,平台不提供额外的编辑、内容补充、找答案等附加服务。
- 2、"仅部分预览"的文档,不可在线预览部分如存在完整性等问题,可反馈申请退款(可完整预览的文档不适用该条件!)。
- 3、如文档侵犯您的权益,请联系客服反馈,我们会尽快为您处理(人工客服工作时间:9:00-18:30)。
加工不锈钢数控刀具设计及选材
1.数控刀具的设计
加工不锈钢时,刀具切削部分的几何形状,一般应从前角、后角方面的选择来考虑。
在选择前角时,要考虑卷屑槽型、有无倒棱和刃倾角的正负角度大小等因素。
不论何种数控刀具,加工不锈钢时都必须采用较大的前角。
增大刀具的前角可减小切屑切离和清出过程中所遇到的阻力。
对后角选择要求不十分严格,但不宜过小,后角过小容易和工件表面产生严重摩擦,使加工表面粗糙度恶化,加速数控刀具磨损。
并且由于强烈摩擦,增强了不锈钢表面加工硬化的效应;数控刀具后角也不宜过大,后角过大,使刀具的楔角减小,降低了切削刃的强度,加速了刀具的磨损。
通常后角应比加工普通碳钢时适当大些。
前角的选择从切削热的产生和散热方面说,增大前角可减小切削热的产生,切削温度不致于太高,但前角过大则因刀头散热体积减小,切削温度反而升高。
减小前角可改善刀头散热条件,切削温度有可能降低,但前角过小,则切削变形严重,切削产生的热量不易散掉。
实践表明,取前角go=15°——20°最为合适。
后角的选择粗加工时,对强力切削的数控刀具则要求切削刃口强度高,则应取较小的后角;精加工时,数控刀具磨损主要发生在切削刃区和后刀面上,对于不锈钢这种易出现加工硬化的材料,其后刀面摩擦对加工表面质量及刀具磨损影响较大,合理的后角应为:加工奥氏体不锈钢(185HB以下),其后角可取6°——8°;加工马氏体不锈钢(250HB以上),其后角取6°——8°;加工马氏体不锈钢(250HB以下),其后角为6°——10°为宜。
刃倾角的选择刃倾角的大小和方向,确定了流屑的方向,合理选择刃倾角ls,通常取-10°——20°为宜。
在微量精车外圆、精车孔、精刨平面时,应采用大刃倾角数控刀具:应取ls45°——75°。
2.数控刀具材料的选择
对刀杆材料的要求加工不锈钢时,由于切削力较大,故刀杆必须具备足够的强度和刚性,以免在切削过程中发生颤振和变形。
这就要求选用适当大的刀杆截面积,同时还应采用强度较高的材料来制造刀杆,如采用调质处理的45号钢或50号钢。
对数控刀具切削部分材料的要求加工不锈钢时,要求数控刀具切削部分的材料具有较高的耐磨性,并能在较高的温度下保持其切削性能。
目前常用有高速钢数控刀具和硬质合金数控刀具。
由于高速钢只能在600°C以下保持其切削性能,因此不宜用于高速切削,而只适
用于在低速情况下加工不锈钢。
由于硬质合金刀具比高速钢刀具具有更好的耐热性和耐磨性,因此用硬质合金材料制成的数控刀具更适合不锈钢的切削加工。
硬质合金材质分钨钴合金(YG)和钨钴钛合金(YT)两大类。
钨钴类合金具有良好的韧性,制成的数控刀具可以采用较大的前角与刃磨出较为锋利的刃口,在切削过程中切屑易变形,切削轻快,切屑不容易粘刀,所以在一般情况下,用钨钴合金加工不锈钢比较合适。
特别是在振动较大的粗加工和断续切削加工情况下更应采用钨钴合金刀片,它不象钨钴钛合金那样硬脆,不易刃磨,易崩刃。
钨钴钛合金的红硬性较好,在高温条件下比钨钴合金耐磨,但它的脆性较大,不耐冲击、振动,一般作不锈钢精车加工刀具。
数控刀具材料的切削性能关系着数控刀具的耐用度和生产率,数控刀具材料的工艺性影响着刀具本身的制造与刃磨质量。
宜选择硬度高、抗粘结性和韧性好的刀具材料,如YG类硬质合金,最好不要选用YT类硬质合金,尤其是在加工1Gr18Ni9Ti奥氏体不锈钢应绝对避免选用YT类硬质合金,因为不锈钢中的钛(Ti)和YT类硬质合金中的Ti产生亲合作用,切屑容易把合金中的Ti带走,促使刀具磨损加剧。
生产实践表明,选用YG532、YG813
及YW2三种牌号材料加工不锈钢具有较好的加工效果
3.切削用量的选择
为了抑制积屑瘤和鳞刺的产生,提高表面质量,用硬质合金刀具进行加工时,切削用量要比车削一般碳钢类工件稍低些,特别是切削速度不宜过高,一般推荐切削速度
Vc=60——80m/min,切削深度为ap=4——7mm,进给量f=0.15——0.6mm/r为宜。
4.对数控刀具切削部分表面粗糙度的要求
提高数控刀具切削部分的表面光洁度可减少切屑形成卷曲时的阻力,提高数控刀具的耐用度。
与加工普通碳钢相比较,加工不锈钢时应适当降低切削用量以减缓刀具磨损;同时还要选择适当的冷却润滑液,以便降低切削过程中的切削热和切削力,延长数控刀具的使用寿命。
苏州硕朔五金工具有限公司专业生产制造各种数控钨钢铣刀、钨钢钻头、钨钢铰刀、非标T型铣刀、焊接刀具、钨钢成型刀具及其他非标刀具,并提供相关刀具的修磨业务。