橡胶挤出工艺
橡胶挤出设备工艺问题分析及解决措施

第 10 期顾 建.橡胶挤出设备工艺问题分析及解决措施621橡胶挤出设备工艺问题分析及解决措施顾 建(杭州朝阳橡胶有限公司,浙江杭州 310018)摘要:根据橡胶挤出机的作用及特点,针对生产过程中遇到的超温、熟粒、死胶、脱层和鼓包及气泡五大设备工艺问题进行分析并提出相应的解决措施。
研究表明,温度变化是导致挤出半制品出现异常的主要原因,而温度受季节、销钉排布、温控系统和螺杆间隙等多方面因素的影响,需要结合实际综合考虑,制定合理的解决方案。
关键词:橡胶;挤出机;设备工艺问题;解决措施中图分类号:TQ330.6+4;TQ330.4+4 文献标志码:B 文章编号:1006-8171(2018)10-0621-03橡胶螺杆挤出机是轮胎生产的关键设备之一,主要用于轮胎半制品如胎面、胎侧、三角胶、垫胶、内衬层等的挤出[1]。
在实际生产过程中,不同制品或同一种制品不同规格对挤出机的工艺参数设置要求不同,因此挤出机对生产制品的工艺符合性是评判设备是否异常的重要依据,由此产生的设备工艺问题也是技术人员面临的难题[2-4]。
本工作结合实际案例,对橡胶螺杆挤出机最常见的五大设备工艺问题进行深入分析,并提出相应的解决措施。
1 橡胶螺杆挤出机简介橡胶螺杆挤出机一般由电动机、联轴器、减速箱、喂料座、机筒、螺杆、销钉、机头和温控系统等组成。
胶料从喂料口进入挤出机,并在挤出机中受螺杆旋转作用被搅拌、混合、塑化和压紧,同时,伴随一定的温度和压力向机头方向移动,最后从机头口型挤出。
在挤出过程中,胶料的粘度和塑性会发生一定的变化,成为粘性流体状态。
2 挤出机设备工艺问题及解决措施橡胶螺杆挤出机容易出现的设备工艺问题有挤出制品破边、拉伸、断面尺寸不符等,其中以超温、熟粒、死胶、脱层和鼓包及气泡五大问题尤为突出。
2.1 超温超温(又名焦烧)是指在挤出机出口处,半制品的温度超出了工艺标准(120 ℃),导致表面凹凸不平,如图1所示。
(a)正常 (b)超温图1 超温与正常半制品对比根据橡胶螺杆挤出机结构和工作原理,分析造成制品超温的原因如下。
汽车橡胶密封条的挤出工艺

骨架类密封条加工思维导图1生胶1.1生三元乙丙胶耐老化性能极佳,在阳光下曝晒3年不见裂纹,弹性,而且还防滑,耐磨,寿命长,具备低密度和高填充性耐晒耐腐蚀,耐磨。
2配合剂2.1补强剂补强剂可以改善胶料的物理机械性能和耐老化性能等。
增加强度分子间结合强度,耐磨性,硬度提高,拉伸性能,抗撕裂性能橡胶制品行业最常见的补强剂是炭黑,炭黑可以显著提高橡胶制品的耐磨性、回弹性和补强性,是橡胶行业中用量最大的补强剂;2.1.1炭黑2.2填充剂填充剂的作用: 增加片剂的重量或体积,有利于成型和分剂量填充剂只能提高橡胶体积、降低原料成本轻质碳酸钙也就是我们常说的轻钙,它与陶土都是橡胶工业中常用的填充剂,可以增加胶料体积、减少胶料用量、降低生产成本。
2.2.1轻质碳酸钙2.3促进剂凡能加快硫化反应速度缩短硫化时间降低硫化反应温度减少硫化剂用量并能够提高或改善硫化胶的物理机械性能的配合剂称为硫化促进剂。
常用促进剂有促D、促M、促DM、促TT、促CBS、促BZ、促PZ、促DTDM、促Na-22等等。
它们用量虽少但对硫化速度具有重要作用。
2.4软化剂凡能增加胶料的塑性有利于配合剂在胶料中的分散便于加工并能适当改善橡胶制品耐寒性能的物质叫做软化剂。
常用软化剂有松焦油、二丁脂(DBP)、二辛脂(DOP)、石蜡、凡土林机油古马隆等。
第二章半成品胶料的生产2.5防老剂增防老剂是指具有延缓或抑制老化过程从而延长橡胶及其制品的贮存期和使用寿命的物质。
常用防老剂有防RD、防4010NA、防MB、防BLE-W等。
2.6硫化剂2.6.1硫化剂有2.6.2硫磺(S)、过氧化二异丙苯(DCP)、二硫化四甲基秋兰姆(TMTD)、3#硫化剂、TCY2.7促进剂活性剂硫化活性剂又称助促进剂提高促进剂的活性使促进剂进一步充分发挥其最大的促进作用。
常用活性剂有氧化锌(ZnO)、硬脂酸(SA)等。
2.8防焦剂防焦剂也叫硫化迟缓剂。
使胶料在加工过程中不发生早期硫化现象但又不妨碍在硫化温度下充分发挥促进剂的作用从而提高了胶料加工操作的安全性。
epdm橡胶挤出工艺常见问题

epdm橡胶挤出工艺常见问题EPDM橡胶挤出工艺是一种常用的加工方法,但在实际操作过程中,会遇到一些常见问题。
以下是几个常见问题及其解决方法:1. 塑性变形问题:在挤出过程中,EPDM橡胶可能会出现塑性变形问题,导致产品尺寸超出规定范围或形状变形。
这可能是由于挤出温度过高、挤出机速度过快或挤出头设计不合理等原因造成的。
解决方法是调整挤出温度、适当降低挤出机速度,并根据产品需求进行挤出头的优化设计。
2. 表面质量问题:EPDM橡胶挤出后的产品表面可能出现气泡、纹路或凹痕等质量问题。
这可能是因为挤出过程中橡胶材料内含有气体、挤出机过热或挤出模具存在缺陷造成的。
解决方法是确保橡胶材料充分干燥,调整挤出机温度并修复模具缺陷。
3. 温度控制问题:EPDM橡胶挤出过程需要严格控制温度,以保证材料的流动性和变形性能。
若温度不正确,会导致产品品质下降。
解决方法是使用专业的温度控制设备,并根据实际情况调整挤出机各个区域的温度。
4. 切断问题:在EPDM橡胶挤出后,可能需要对产品进行切断,但切断不当会导致产品损坏或产生不平整的切面。
解决方法是选择适当的切断工具,并确保切断过程平稳且垂直于挤出方向。
5. 成本控制问题:EPDM橡胶挤出加工的成本通常较高,主要是由于原材料成本和设备运行成本等多个因素所致。
解决方法是优化生产工艺,提高生产效率,降低废品率,并合理选择材料和设备以控制成本。
通过了解EPDM橡胶挤出工艺的常见问题及其解决方法,我们可以更好地应对这些问题,确保产品质量和生产效率。
在实际操作中,应根据具体情况进行调整和优化,以获得最佳结果。
三元乙丙橡胶挤出工艺

三元乙丙橡胶挤出工艺
三元乙丙橡胶是一种广泛应用于汽车、电气、建筑等领域的高性能橡胶材料。
其挤出工艺是指将原料加热、混合后塑化,然后通过挤出机将其挤出成型。
三元乙丙橡胶挤出工艺的主要步骤包括原料预处理、混炼、挤出、冷却、切断和成品包装等环节。
其中,原料预处理是指将橡胶、填料、助剂等原材料进行筛选、称量等处理,以确保挤出工艺的稳定性和产品品质的稳定性。
混炼是将预处理后的原料加入到混炼机中进行混合,以使各种原材料充分混合,并达到理想的流动性和可加工性。
挤出是将混合好的原材料加入到挤出机中,通过压力和温度控制,将其挤出成型,形成所需的产品形状。
冷却是将挤出成型的产品在冷却机中进行冷却,以使其达到所需硬度和强度。
切断是将冷却后的产品按照所需长度进行切割,成品包装是将切断好的产品进行包装,以便存储和运输。
三元乙丙橡胶的挤出工艺需要严格控制原料配比、温度和压力等因素,以确保产品的稳定性和品质。
此外,挤出机的选择和调试也是影响挤出工艺效果的关键因素。
- 1 -。
橡胶管生产工艺流程
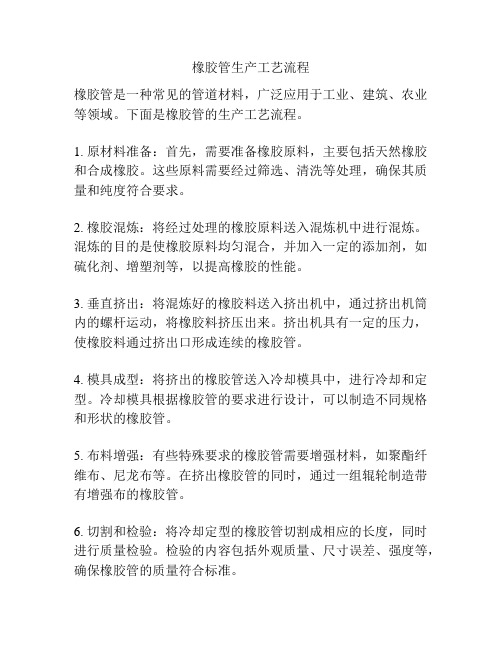
橡胶管生产工艺流程
橡胶管是一种常见的管道材料,广泛应用于工业、建筑、农业等领域。
下面是橡胶管的生产工艺流程。
1. 原材料准备:首先,需要准备橡胶原料,主要包括天然橡胶和合成橡胶。
这些原料需要经过筛选、清洗等处理,确保其质量和纯度符合要求。
2. 橡胶混炼:将经过处理的橡胶原料送入混炼机中进行混炼。
混炼的目的是使橡胶原料均匀混合,并加入一定的添加剂,如硫化剂、增塑剂等,以提高橡胶的性能。
3. 垂直挤出:将混炼好的橡胶料送入挤出机中,通过挤出机筒内的螺杆运动,将橡胶料挤压出来。
挤出机具有一定的压力,使橡胶料通过挤出口形成连续的橡胶管。
4. 模具成型:将挤出的橡胶管送入冷却模具中,进行冷却和定型。
冷却模具根据橡胶管的要求进行设计,可以制造不同规格和形状的橡胶管。
5. 布料增强:有些特殊要求的橡胶管需要增强材料,如聚酯纤维布、尼龙布等。
在挤出橡胶管的同时,通过一组辊轮制造带有增强布的橡胶管。
6. 切割和检验:将冷却定型的橡胶管切割成相应的长度,同时进行质量检验。
检验的内容包括外观质量、尺寸误差、强度等,确保橡胶管的质量符合标准。
7. 包装和贮存:将检验合格的橡胶管进行包装,通常使用塑料袋或纸箱进行包装。
然后进行贴标签,并存放在干燥、通风的仓库中,以保持橡胶管的质量和使用寿命。
以上是橡胶管的生产工艺流程。
通过这些步骤,原材料可以经过一系列的加工和处理,最终变成适用于不同需求的橡胶管产品。
橡胶生产工艺及技术经济分析论文

橡胶生产工艺及技术经济分析论文橡胶是一种重要的工业原材料,广泛应用于汽车、建筑、医疗、机械等领域。
橡胶生产工艺及技术经济分析是橡胶生产过程中非常重要的环节。
本文将从橡胶生产工艺、工艺优化和技术经济分析等方面进行分析和探讨。
一、橡胶生产工艺橡胶生产工艺主要分为自然橡胶和合成橡胶两种。
自然橡胶主要通过切割橡胶树皮得到。
首先要做的是选定棵树,然后用划痕方法将树皮割开,让乳液流出来收集,我们收集好的乳液会进入橡胶场进行加工。
经析出器分离,得到结块橡胶,进一步经过洗涤等工艺,得到极细小的颗粒状物料,即乳胶干胶,最终经加工加工成各种形状。
合成橡胶生产工艺主要过程为合成、混炼、压制,并可进行最终处理。
合成是指各种单体经过聚合反应形成高分子链的过程,主要原材料是苯乙烯、丁二烯和苯乙烯丁二烯共聚物。
混炼则是将各种原材料加入到橡胶机进行机械切割,使各种单体分散均匀,加入助剂形成橡胶混炼胶。
压制则是将橡胶混炼胶放到模具中进行挤出或压制,最终得到不同形状的橡胶制品。
二、工艺优化工艺优化是为了提高生产效率、工艺稳定性和产品质量,主要包括以下方面:1、原材料优化。
选择优质原材料可以降低生产成本,提高工艺稳定性。
2、工艺参数优化。
优化橡胶混炼机的转速和加热温度,可以降低能耗,提高混炼质量。
3、工艺流程优化。
通过优化工艺流程可以缩短生产周期、降低能量消耗和提高产品质量。
4、检测优化。
通过建立完整的检测流程和标准,可以保证产品的可靠性和质量。
三、技术经济分析技术经济分析是橡胶生产中非常重要的环节,可以通过技术经济比较,选择最优的橡胶生产工艺和流程。
以合成橡胶为例,技术经济分析主要从以下五个方面入手:1、生产能力。
生产能力必须符合市场需求和公司规模。
2、原材料成本。
原材料成本直接影响到最终产品价格和市场竞争力。
3、设备技术水平。
先进设备可以降低能源消耗、生产效率提高,但也需要更高的设备投入。
4、企业管理模式。
优秀的管理模式和员工素质可以提高生产效率和产品质量。
橡胶压延与压出—压出(橡胶加工课件)

3. 挤出机的规格和型号如何表示?
❖ 规格表示
▪ 挤出机的规格是以螺杆外直径来表示,其单位是mm。
▪ 国产挤出机的规格有Φ30、Φ45(实验用);Φ60、Φ65、Φ85、Φ90 (挤出胶管);Φ115、Φ120、Φ150、Φ200(挤出胎面);Φ250、 Φ300(滤胶用)等。
❖ 型号表示
▪ 螺杆挤出机型号是以螺杆外直径前冠以符号来表示。
2. 挤出机有哪些分类方法?
❖ 按物料分橡胶挤出机和塑料挤出机; ❖ 按螺杆数目的多少可分为单螺杆、双螺杆和多螺杆挤出机; ❖ 按可否排气可分为排气和非排气挤出机; ❖ 按螺杆在空间的位置可分为卧式和立式挤出机; ❖ 按工艺条件(喂料方式)可分为热喂料和冷喂料挤出机; ❖ 按用途可分为塑炼、混炼、滤胶和压型挤出机等多种类型。
⑥ ③ 胶螺度料纹相可槽匹的塑配压性,缩否大比则,会流大造动,成性半半好成成,品品挤致断出密面速性尺度提寸快高不,,准挤但确出胶,变料甚形生
小热至,高表半,面易成出焦品现表烧裂面;纹光等滑弊,病挤。出一生般热接小,取但速可度塑要性比太大挤,
则挤出半成品缺乏挺性,易产生变形。
出速度稍快为宜。
8、什么是冷喂料挤出?有何特点?
挤出
挤出
• 预热机筒,机头,口型和芯型,一般采用蒸汽介质
加热至规定温度范围(需10~15min)。
6、热喂料挤出工艺操作流程方法?
挤出
挤出
• 供胶调节口型,检查挤出半成品尺寸、表面状态,直
至符合要求后才能开始挤出半成品;
• 半成品公差范围:一般小规格的为±0.75mm,大规格的为 ± 1.0~1.5mm。
• 通常,胶料的热塑性越高, 流动性越好,挤出越容易, 但热塑性太高,胶料挺性差,
橡胶加工工艺—橡胶压出工艺(高分子成型课件)
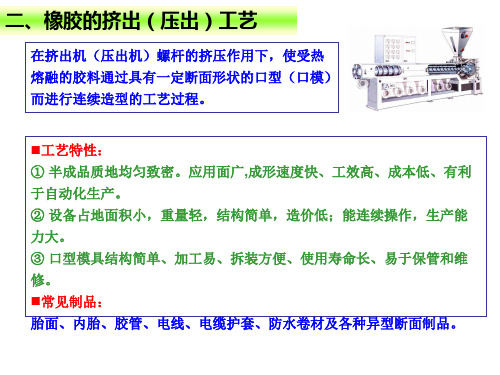
二、橡胶的挤出(压出)工艺
(一)压出机工作原理及胶料的运动状态 3 物料在口型中的流动状体和挤出变形 胶料经机头进入口型后,由于口型形状不同及内表 面对物料流动的阻碍,物料流动速度也存在有与机 头类似的速度分布。中间流速大,越接近口型壁流 速越小 。 一般粘弹性的物料,从口型挤出后就不可避免地存 在松弛现象,即:胶条的长度会沿挤出方向缩短, 厚度沿垂直挤出方向增加(离模膨胀现象或称作挤 出变形现象)。挤出后的变形(收缩和膨胀)可以控制 在一定范围,但不可能完全消除。要求收缩率为 2~5%。 物料可塑性小、含胶率大,填充剂用量小,物料挤 出快,机头和口型温度低,膨胀和收缩率就大。
二、橡胶的挤出(压出)工艺
在挤出机(压出机)螺杆的挤压作用下,使受热 熔融的胶料通过具有一定断面形状的口型(口模) 而进行连续造型的工艺过程。
工艺特性: ① 半成品质地均匀致密。应用面广,成形速度快、工效高、成本低、有利 于自动化生产。 ② 设备占地面积小,重量轻,结构简单,造价低;能连续操作,生产能 力大。 ③ 口型模具结构简单、加工易、拆装方便、使用寿命长、易于保管和维 修。 常见制品: 胎面、内胎、胶管、电线、电缆护套、防水卷材及各种异型断面制品。
二、橡胶的挤出(压出)工艺
(一)压出机工作原理及胶料的运动状态
1 胶料在挤出机中的运动状态
加料段:加入的条状胶料,受到旋转螺杆的推挤作用形成连续的胶 团,并沿着螺槽的空间一边旋转,一边不断前进。 压缩段:加料段输送过来的松散胶团在压缩段被逐渐压实、软化, 并把夹带的空气向加料段排出。同时胶团间间隙缩小,密度增高, 进而粘在一起,再加上受到剪切和搅拌作用,因而胶团逐渐被加热 塑化形成连续的粘流体。 挤出段:在挤出段,压缩段输送过来的物料进一步塑化均匀,并输 送到机头和口模处挤出成型。
- 1、下载文档前请自行甄别文档内容的完整性,平台不提供额外的编辑、内容补充、找答案等附加服务。
- 2、"仅部分预览"的文档,不可在线预览部分如存在完整性等问题,可反馈申请退款(可完整预览的文档不适用该条件!)。
- 3、如文档侵犯您的权益,请联系客服反馈,我们会尽快为您处理(人工客服工作时间:9:00-18:30)。
橡胶挤出机压出工艺第十四章压出工艺压出(挤出)是使高弹态的橡胶在挤出机机筒及转动的螺杆的相互作用下,连续地制成各种不同形状半成品的工艺过程。
应用:制造轮胎胎面、内胎胎筒、纯胶管、胶管内外层胶和电线电缆等半成品;也可用于胶料的过滤、造粒、生胶的塑炼、金属丝覆胶及上下工序的联动。
挤出成型的特点:(1)操作简单、工艺控制较容易,可连续化、自动化生产,生产效率高,产品质量稳定。
(2)应用范围广。
通过挤出机螺杆和机筒的结构变化,可突出塑化、混合、剪切等作用中的一种,与不同的辅机结合,可完成不同工艺过程的综合加工。
(3)可根据产品的不同要求,通过改变机头口型成型出各种断面形状的半成品。
也可通过两机(或三机)复合压出不同成分胶料或多色的复合胎面胶。
(4)设备占地面积小、质量轻、机器结构简单、造价低、灵活机动性大。
挤出机的分类:根据加工物料的不同可分为:橡胶挤出机和塑料挤出机;根据结构特征可分为:热喂料挤出机、冷喂料挤出机和排气冷喂料挤出机;根据螺杆数量可分为:单螺杆挤出机、双螺杆挤出机和多螺杆挤出机;根据工艺用途不同分为:压出挤出机、滤胶挤出机、塑炼挤出机、混炼挤出机、压片挤出机及脱硫挤出机等。
§14.1 橡胶挤出机挤出机的规格用螺杆的外径表示,并在前面冠以“SJ”或“XJ”,S表示塑料;X表示橡胶;J表示挤出机。
如SJ-90表示螺杆外径为90mm的塑料挤出机;而XJ-200表示螺杆外径为200mm的橡胶挤出机。
一.挤出机结构挤出机结构通常由机筒、螺杆、加料装置、机头(口型)、加热冷却装置、传动系统等部分组成。
挤出机的主要技术参数有:螺杆直径、长径比、压缩比、转速范围、螺杆结构、生产能力、功率等。
1.机筒机筒在工作中与螺杆相配合,使胶料受到机筒内壁和转动螺杆的相互作用,以保证胶料在压力下移动和混合,通常它还起热交换的作用。
为了使胶料沿螺槽推进,必须使胶料与螺杆和胶料与机筒间的摩擦系数尽可能悬殊,机筒壁表面应尽可能粗糙,以增大摩擦力,而螺杆表面则力求光滑,以减小摩擦系数和摩擦力。
否则,胶料将紧包螺杆,而无法推向前进。
(1)机筒的结构形式按结构可分为整体式和组合式两种。
(2)喂料口与旁压辊喂料口的结构与尺寸对喂料影响很大,而喂料情况往往影响挤出产量。
在喂料口侧壁螺杆的一旁加一压辊构成旁压辊喂料,此种结构供胶均匀,无堆料现象,半成品质地致密,能提高生产能力,但功率消耗增加。
2.螺杆螺杆是挤出机的主要工作部件。
它在工作中产生足够的压力使胶料克服流动阻力而被挤出,同时使胶料塑化、混合、压缩,从而获得致密均匀的半成品。
螺杆的分类:按螺纹头数分:单头、双头、三头和复合螺纹螺杆。
双头螺纹螺杆用于压型挤出;单头螺纹螺杆多用于滤胶;复合螺纹螺杆多用于塑炼等。
按螺纹方向分:有左旋和右旋两种,橡胶挤出机多用右旋螺纹螺杆。
按螺杆外型分:有圆柱形、圆锥形、圆柱圆锥复合形螺杆。
圆柱形螺杆多用于压型和滤胶;圆锥形螺杆多用于压片和造粒;复合形螺杆多用于塑炼。
按螺纹的结构形式分:普通型(如等深变距型或等距变深型),分流型(如销钉型),分离型(如副螺纹型)和复合型螺杆等。
螺杆的结构:螺杆的结构分工作部分(指螺纹部和头部)和连接部分(指尾部),工作部分直接完成挤出作业,尾部起支持和传动作用。
螺杆工作部分的主要参数有:螺纹头数、压缩比、导程、槽深及螺纹升角等。
(1)长径比螺杆螺纹部分长度L与外直径D之比为长径比(L/D),是挤出机的重要参数之一。
长径比大,胶料在挤出机内走的路程长,受到的剪切、挤压和混合作用就大。
热喂料挤出机的长径比一般在3~8之间,而冷喂料挤出机的长径比一般为8~17,甚至达到20。
(2)压缩比螺杆加料端的螺槽容积与出料端的螺槽容积之比为压缩比,它表示胶料在挤出机中可能受到的压缩程度。
比值越大,半成品致密性越好。
压缩比的大小视挤出机的用途而异。
压缩比过大,虽然可保证半成品质地致密,但挤出过程的阻力增大,胶料升温高易产生焦烧,且影响产量;压缩比过小影响半成品致密程度。
热喂料挤出机常用压缩比为1.3~1.4,有时可达1.6~1.7;冷喂料挤出机常用压缩比为1.7~1.8,有时可达1.9~2.0。
(3)螺纹导程S与升角α同一螺纹连续转一圈相应点间的距离称螺纹导程。
当螺纹直径确定后,螺纹导程不但决定了升角,而且影响螺纹槽的容积,它们的关系为:(3-1)(3-2)式中 F—螺纹槽纵截面积;i—螺纹头数。
当S增大时,α也增大,此时吃料方便,产量高,但过大可能造成塑化不均,影响半成品质量,且螺杆加工也困难;当S减小时,α也减小,此时轴向压力大,胶料在机筒内停留时间延长,塑化均匀,半成品质量好,但螺纹容积小,产量下降。
螺纹升角α一般为12~35o,螺纹导程S为(0.5~1)D。
(4)螺纹槽深度h螺纹槽深度减小时,胶料速度梯度增大,有利于胶料的剪切塑化,但胶料升温高、产量小,增大h可提高产量,但过大时产量增加并不显著,且影响螺杆的强度。
一般h=(0.18~0.25)D,螺杆直径大时系数取大值。
(5)螺杆头部形状螺杆头部形状选择应有利于胶料流动,防止产生死角而引起胶料焦烧。
螺杆头部形状有四种:平头螺杆头、弹头型螺杆头、锥型螺杆头和球型螺杆头。
平头螺杆头其顶端有死角,多用于滤胶机上;锥型螺杆头无死角,有利于胶料流动,且不易焦烧。
3.机头机头对不同的挤出工艺(如压型、滤胶、混炼、造粒等),其作用与结构也不相同。
对压型挤出机的机头来说,其主要作用是:使胶料由螺旋运动变为直线运动;使机筒内的胶料在挤出前产生必要的挤出压力,以保证挤出半成品密实;使胶料进一步塑化均匀;使挤出半成品成型。
(1)机头的类型按机头的结构分:有芯型机头和无芯型机头。
按与螺杆的相对位置分:直向机头、直角机头和斜角机头。
按机头用途不同分:内胎机头、胎面机头、电缆机头等。
按机头内胶料压力大小分:低压机头、中压机头、高压机头。
(2)机头的结构橡胶挤出机的机头结构主要分为圆筒形、扁平形、T型和Y型。
a.内胎挤出机头(圆筒形)用以制造各种空心制品,如胶管、内胎、密封条等等。
这种结构的机头又分为可调整口型和可调节芯型。
b.胎面挤出机头(扁平形)用以制造轮胎胎面。
这种机头又分为整体式和复合式两种。
c.电线、电缆挤出机头(T型和Y型)用以制造电线电缆绝缘层,轮胎钢丝圈及胶管包胶等。
其结构一般有两种形式:直角机头和斜角机头。
二.挤出机的选用橡胶挤出机的选用,由所需半成品的断面大小和厚薄来决定。
对于压出实心或圆形中空半成品,一般口型尺寸约为螺杆直径的0.3~0.75左右。
口型过大,螺杆推力小,机头内压力不足,排胶不均匀,半成品形状不规整;口型过小,压力太大,速度虽快些,但剪切作用增加,引起胶料生热,增加胶料焦烧的危险。
§14.2 挤出过程原理一.工作原理挤出成型是在一定条件下将具有一定塑性的胶料通过一个口型连续压送出来,使它成为具有一定断面形状的产品的工艺过程。
胶料沿螺杆前移过程中,由于机械作用及热作用的结果,胶料的粘度和塑性等均发生了一定的变化,成为一种粘性流体。
根据胶料在挤出过程中的变化,一般将螺杆工作部分按其作用不同大体上分为喂料段、压缩段和挤出段三部分。
各段工作特点如下:1.喂料段:又称为固体输送段,此段从喂料口起至胶料熔融开始。
胶料进入加料口后,在旋转螺杆的推挤作用下,在螺纹槽和机筒内壁之间作相对运动,并形成一定大小的胶团。
2.压缩段:又称为塑化段,此段从胶料开始熔融起至全部胶料产生流动止。
压缩段接受由喂料段送来的胶团,将其压实、进一步软化,并将胶料中夹带的空气向喂料段排出。
3.压出段:又称为计量段,把压缩段输送来的胶料进一步加压搅拌,此时螺纹槽中已形成完全流动状态的胶料。
由于螺杆的转动促使胶料流动,并以一定的容量和压力从机头流道均匀挤出。
二.胶料在挤出段中的流动状态一般把胶料在挤出段中的流动看成是顺流、倒流、漏流和环流的综合流动。
顺流:由于螺杆转动促使胶料沿着螺纹槽向机头方向的流动,它促使胶料挤出,又称为挤流。
它的速度分布近似直线,在螺杆表面速度最大,在机筒内壁速度近似为零。
顺流对挤出产量有利。
倒流:由于机头对胶料的阻力引起的,也称压力倒流或逆流。
胶料顺着压力梯度沿螺杆通道而产生倒流。
倒流引起挤出产量减少。
漏流:在螺杆螺峰与机筒内壁间缝隙,由于机头阻力而引起的,它与顺流方向相反,它引起挤出产量减少,见图3-1。
环流:又称为横流,由于螺杆旋转时产生的推挤作用引起的流动,它与顺流成垂直方向,促使胶料混合,对产量无影响,见图3-2。
环流对胶料起着搅拌混炼、热交换和塑化的作用。
图3-1 漏流流动示意图1—机筒;2—螺杆图3-2 环流流动示意图1—机筒;2—螺杆图3-3 顺流和逆流的综合速度分布(a)顺流;(b)逆流;(c)顺流和逆流的综合速度分布;1—机筒内壁;2—螺杆;h—螺槽深度三.胶料在机头内的流动状态胶料在机头内的流动,是指胶料在离开螺纹槽后,到达口型板之前的流动。
胶料在螺杆螺纹槽中的流动是呈螺旋状前进的,但从螺杆头端出来进入机头流道时,料流形状发生了急骤的变化,即由旋转运动变为直线运动,而且由于胶料具有一定的粘性,其流动速度在流道中心要比靠近机头内壁处快得多,其速度分布呈抛物线状。
机头压力:在机头流道所形成的对物料的压力,该压力在通过机头时,逐渐下降。
当物料挤出口模时,下降为零。
机头压力的成因:(1)由过滤网和过滤板的阻力形成;(2)由机头口模流道内壁摩擦及流道收缩而形成。
机头的结构要使胶料在由螺杆到口型的整个流动方向上受到的推力和流动速度尽可能保持一致。
为此,机头内的饿流道应呈流线型,无死角或停滞区,不存在任何湍流。
四.胶料在口型中的流动和压出膨胀1.胶料在口型中的流动胶料经机头流道进入口型后,通过口型时受到更强烈的剪切塑化后挤出口型外。
因此,口型内的流动状态及口型结构尺寸决定了制品的最终形状和质量。
胶料是在机头所形成的流体静压力作用下流过口型的,因此,胶料在口型中的流动只表现为轴向运动。
由于口型厚度一般很薄,胶料在口型中形成的压力梯度很大。
2.压出膨胀胶料是粘弹性体,当它流过口型时,同时经历粘性流动和弹性变形。
胶料由机头进入口型时,一般是流道变窄,流速增大,在流动方向上形成速度梯度。
这种速度使胶料产生拉伸弹性变形。
当口型流道较短时胶料拉伸变形来不及恢复,压出后产生膨胀现象。
(即压出物的直径大于口型直径,而轴向出现回缩)。
压出膨胀量主要取决于胶料流动时可恢复变形量和松弛时间的长短。
影响压出膨胀的因素:(1)工艺因素口型形状、口型(板厚度)壁长度、机头口型温度、压出速度等。
(2)配方因素生胶和配合剂的种类、用量、胶料可塑性等。
一般来说,胶料可塑性小、含胶率高、压出速度快,胶料、机头和口型温度低时,压出物的膨胀率(或收缩率)就大。