锌合金前处理
锌合金压铸件表面处理

锌合金压铸件表面处理1. 简介锌合金压铸件是一种常见的金属零件,具有很高的强度和耐腐蚀性。
然而,其表面通常需要进行处理以提高外观和性能。
本文将详细介绍锌合金压铸件表面处理的方法和技术。
2. 表面处理方法2.1 机械处理机械处理是锌合金压铸件表面处理的基本方法之一。
它包括去毛刺、抛光和打磨等步骤。
去毛刺可以通过机械切削或研磨来完成,以去除零件表面的毛刺和尖锐边缘。
抛光和打磨则可以提高零件表面的光洁度和平整度。
2.2 化学处理化学处理是锌合金压铸件表面处理的另一种常用方法。
它主要包括酸洗、电镀和化学转化膜等过程。
酸洗可以去除锌合金表面的氧化物和污垢,提供一个干净的表面用于后续处理。
电镀可以在锌合金表面形成一层金属镀层,提高其外观和耐腐蚀性。
化学转化膜则可以在锌合金表面形成一层化学转化膜,提高其耐磨性和耐腐蚀性。
2.3 热处理热处理是一种常用的锌合金压铸件表面处理方法。
它包括热处理和热喷涂两种方式。
热处理可以改变锌合金的组织结构和性能,提高其硬度和强度。
热喷涂则可以在锌合金表面形成一层涂层,提高其耐磨性和耐腐蚀性。
3. 表面处理技术3.1 硅溶胶处理硅溶胶处理是一种常用的锌合金压铸件表面处理技术。
它通过在锌合金表面形成一层硅溶胶膜来提高其耐腐蚀性和耐磨性。
硅溶胶处理可以在常温下进行,具有成本低、工艺简单和效果显著的优点。
3.2 电化学抛光电化学抛光是一种通过电化学方法去除锌合金表面的氧化物和污垢的技术。
它可以提高锌合金表面的光洁度和平整度,使其具有更好的外观和耐腐蚀性。
3.3 电镀技术电镀技术是一种常用的锌合金压铸件表面处理技术。
它可以在锌合金表面形成一层金属镀层,如镍、铬或锌等,以提高其外观和耐腐蚀性。
电镀技术可以根据需要选择不同的金属镀层,以满足不同的要求。
3.4 化学转化膜技术化学转化膜技术是一种通过化学反应在锌合金表面形成一层转化膜的技术。
转化膜可以提高锌合金表面的耐磨性和耐腐蚀性,同时保持其原有的外观。
锌合金发黑处理

锌合金发黑处理
锌合金的发黑处理是指为了使其颜色更加美观,更加坚固、防锈而进行的化学处理。
具体步骤如下:
1.清洗:清洗应用强有力的清洗溶液,常用清洗剂如浓氨水或热碱溶液。
清洗后,用水冲洗彻底,干燥。
2.化学表面处理:将锌合金件浸泡在氯化铵、硝酸铵等卤化物和氧化剂的溶液中,在一定时间内进行化学间接清洗、除锌和表面氧化等处理。
3.转化膜处理:让锌合金浸泡在化学转化液中,例如硫酸钠、氯化钠等,反应约10分钟,形成一层稳定的转化膜。
这样,就可以在锌合金表面形成一层防锈和保护层。
4.冷、热水冲洗:可以去除转化液残留物并稀释转化液的余部。
5.干燥:将锌合金进行烘干处理,完成后就可以达到防锈和美化锌合金表面的效果。
为防止镀层起泡,锌合金铸件应如何电镀前处理?

为防止镀层起泡,锌合金铸件应如何电镀前处理?
佚名
【期刊名称】《《表面工程资讯》》
【年(卷),期】2009(009)005
【摘要】答:锌合金铸件电镀的前处理是非常关键的,可从以下方面防止镀层起泡:(1)适于磨抛的锌合金铸件,在操作时用力要均匀,不宜用力过大,除去工件表面的厚度不应超过其致密层的厚度,因为下面是多孔、疏松结构。
如果抛光过度会破坏表面的致密层,一旦抛光膏和电镀液渗入基体的孔隙、裂纹中,镀层必然会出现起泡、脱皮现象;(2)锌合金铸件经抛光后,应及时用有机溶剂浸泡(约30min),将残留在工件表面上的抛光膏清除掉,然后进行化学除油或电解除油,其除油液应该是弱碱性的。
【总页数】1页(P47)
【正文语种】中文
【中图分类】TQ153.2
【相关文献】
1.锌合金压铸件表面处理后起泡原因及防止方法探讨 [J], 张嘉欣;路全增
2.锌合金压铸件起泡缺陷分析 [J], 吴春苗
3.锌合金压铸件电镀层起泡成因与消除对策 [J], 罗龚;黎德育;袁国辉;李宁
4.锌合金电镀易产生镀层起泡的原因是什么? [J],
5.锌合金压铸件起泡缺陷分析 [J], 吴春苗
因版权原因,仅展示原文概要,查看原文内容请购买。
锌合金的工艺流程
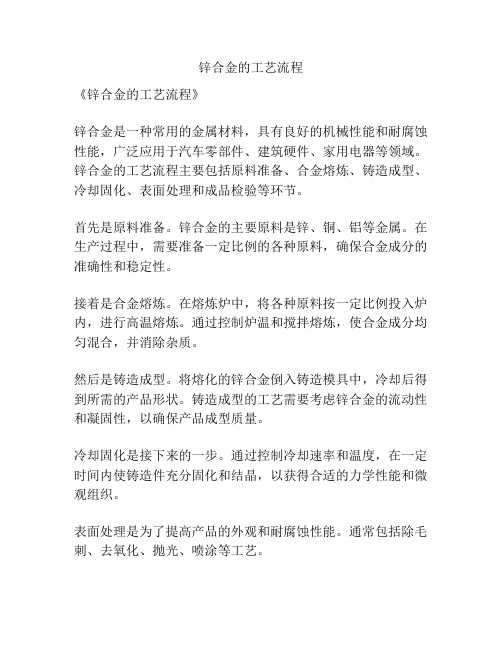
锌合金的工艺流程
《锌合金的工艺流程》
锌合金是一种常用的金属材料,具有良好的机械性能和耐腐蚀性能,广泛应用于汽车零部件、建筑硬件、家用电器等领域。
锌合金的工艺流程主要包括原料准备、合金熔炼、铸造成型、冷却固化、表面处理和成品检验等环节。
首先是原料准备。
锌合金的主要原料是锌、铜、铝等金属。
在生产过程中,需要准备一定比例的各种原料,确保合金成分的准确性和稳定性。
接着是合金熔炼。
在熔炼炉中,将各种原料按一定比例投入炉内,进行高温熔炼。
通过控制炉温和搅拌熔炼,使合金成分均匀混合,并消除杂质。
然后是铸造成型。
将熔化的锌合金倒入铸造模具中,冷却后得到所需的产品形状。
铸造成型的工艺需要考虑锌合金的流动性和凝固性,以确保产品成型质量。
冷却固化是接下来的一步。
通过控制冷却速率和温度,在一定时间内使铸造件充分固化和结晶,以获得合适的力学性能和微观组织。
表面处理是为了提高产品的外观和耐腐蚀性能。
通常包括除毛刺、去氧化、抛光、喷涂等工艺。
最后是成品检验。
对成品进行尺寸、外观、力学性能等方面的检测,以确保产品符合标准要求。
以上就是锌合金的工艺流程,通过严格控制每一个环节,可以生产出质量稳定、性能优良的锌合金产品。
锌合金压铸件电镀前处理

锌合金压铸件镀前处理由于锌合金压铸件是一次性压铸成型,生产效率高,加工成本低,尤其适用于公差要求不太严格而几何形状复杂的零部件,已被广泛用于代替铜、铜合金和钢铁材料制造的受力不太大而形状复杂的结构件和装饰件,其表面处理工艺也处于成熟阶段。
锌合金压铸件是以锌为主、铝为辅的合金,其化学稳定性差,因此需要用其它金属层予以保护,电镀层便是其中之一。
但在锌合金压铸件电镀前应了解其锌、铝含量之比。
铝含量过高,会加速表面层的氧化,造成镀层结合力下降:铝含量过低,则影响零件的韧性,在使用过程中易出现断裂。
从电镀及其使用角度来考虑,合金中的铝含量在3.5%~4%之间为佳。
锌合金压铸件镀前处理合理与否,是电镀成败的关键。
但在其镀前处理过程中,往往会将其前处理等同于其它金属材料的前处理,或者忽视了其中某个工序,而造成大量镀件返工或报废。
由于锌合金压铸件的特殊性,故返工很难,这就是锌合金压铸件在电镀过程中废品率高的原因。
一.锌合金压铸件镀前处理的注意事项1. 了解锌合金压铸件的结构特性:锌合金压铸件表面很像蒸馍表面,有一层0.02~0.10mln厚、光滑致密的金属层,在其下方则是疏松、多孔的结构。
因此在机械抛光时,严防抛穿其光滑致密层,避免疏松、多孔的内材暴露,致使镀层产生起泡、脱皮等不良现象。
2. 掌握锌合金压铸件的化学性能:在压铸过程中,工艺因素的影响会造成同一个锌合金压铸零件中产生富锌和富铝的部位。
强碱优先溶解富铝相,强酸则优先溶解富锌相。
若除油或浸蚀过程中使用强碱或强酸,在电镀时则会引起镀层起泡及脱皮,严重影响成品率。
为此,锌合金压铸件不宜在强酸或强碱中除油及浸蚀。
3. 加速锌合金压铸件镀前处理与入槽电镀的衔接速度:锌合金压铸件的镀前处理,是为了除去零件表面上的油污以及零件在空气中久留后被氧气氧化而生成的氧化膜,让镀液中的金属离子直接沉积在纯净的表面上。
镀前处理完成后的零件,应立即入槽电镀,不允许在大气中或水槽内久留,以免表面再被氧化或在表面上形成水化物,影响镀层的结合力。
锌合金喷涂前处理流程
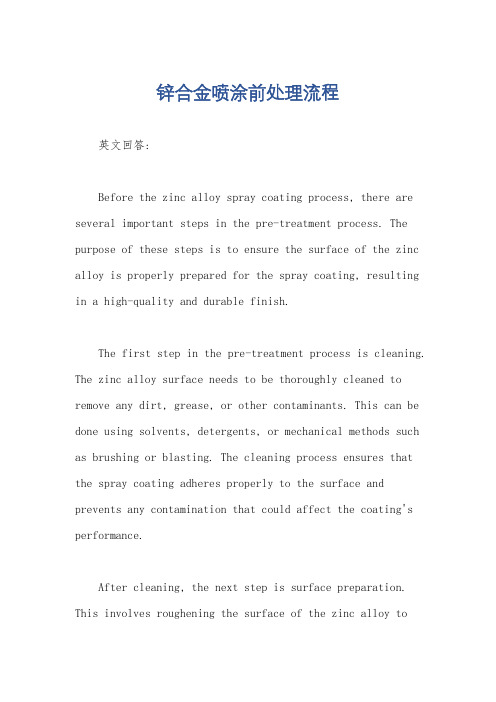
锌合金喷涂前处理流程英文回答:Before the zinc alloy spray coating process, there are several important steps in the pre-treatment process. The purpose of these steps is to ensure the surface of the zinc alloy is properly prepared for the spray coating, resulting in a high-quality and durable finish.The first step in the pre-treatment process is cleaning. The zinc alloy surface needs to be thoroughly cleaned to remove any dirt, grease, or other contaminants. This can be done using solvents, detergents, or mechanical methods such as brushing or blasting. The cleaning process ensures that the spray coating adheres properly to the surface and prevents any contamination that could affect the coating's performance.After cleaning, the next step is surface preparation. This involves roughening the surface of the zinc alloy tocreate a suitable texture for the spray coating to adhere to. Various methods can be used for surface preparation, such as sanding, grinding, or chemical etching. The choice of method depends on the specific requirements of the coating and the condition of the zinc alloy surface.Once the surface is prepared, the zinc alloy may need to undergo a pre-treatment process called conversion coating. Conversion coating involves applying a chemical solution to the surface to create a thin layer that improves the adhesion of the spray coating. This layer also provides corrosion resistance and enhances the overall durability of the coating. Common conversion coating methods for zinc alloys include chromate conversion coating and phosphate conversion coating.After conversion coating, the zinc alloy is ready for the spray coating process. The spray coating is typically applied using a spray gun or other spraying equipment. The coating material, which can be a zinc alloy or another type of coating, is evenly sprayed onto the surface of the zinc alloy. The thickness of the coating can be controlled byadjusting the spraying parameters, such as the spray pressure and nozzle size.Once the spray coating is applied, it needs to be cured or dried. Curing can be done through various methods, such as air drying, oven drying, or using infrared lamps. The curing process ensures that the coating fully adheres to the surface and achieves its desired properties, such as hardness, corrosion resistance, and appearance.In conclusion, the pre-treatment process for zinc alloy spray coating involves cleaning, surface preparation, conversion coating, spray coating, and curing. Each step plays a crucial role in ensuring the quality and durability of the final coating. By following these pre-treatment steps, the zinc alloy can be properly prepared for the spray coating process, resulting in a high-performance and long-lasting finish.中文回答:在进行锌合金喷涂前处理流程时,有几个重要的步骤。
锌合金前处理

锌合金零件表面抛光膏及油污的去除(1)除抛光膏。
零件抛光后表面残留一定的抛光膏,应当尽早除去这些残留的抛光膏,因为时间久了,抛光膏易硬化而不易除去。
除抛光膏可将工件浸泡在60℃~70℃的浓硫酸中(尽可能不掺水),使零件表面的抛光膏被浓硫酸氧化去除。
因为抛光膏的主要成分除金属氧化物(Mg0、Ca0、Al2O3、Fe2O3等)之外,主要是硬脂酸、石蜡等成分,这些有机物会被浓硫酸氧化。
这种方法在规模不大的厂家应用颇广。
其中关键是浓硫酸中不可掺进水,掺进水的浓硫酸对锌合金零件产生严重腐蚀,所以工件抛光后须干燥入硫酸槽。
还有就是使用由有机溶剂、表面活性剂组成的”冷脱剂”、”除蜡水”等溶液除抛光膏,若在除蜡水中配以超声波,则效果更佳。
通过热或冷脱脂,使锌合金表面的蜡垢润湿溶胀而部分溶解,提高超声波除蜡效率。
热脱脂是介于化学除油与除蜡之间的一种特殊形式,说它特殊,是因为它在超声波除蜡之前,其作用是尽可能使蜡垢润湿、溶胀,这种作用是靠碱液、非离子型活性剂与阴离子型表面活性剂等在适当温度下协同完成。
超声波能否快捷干净地将工件表面的蜡垢除尽,取决于热或冷脱脂的效果。
配制热脱脂的水质电导率在50μs/cm以下即可。
采用有机物冷脱脂,对锌合金压铸件而言,应为首选。
因它不仅无需加温,而且熔蜡润湿效果明显,对工件无不良腐蚀。
其工艺配方为:二甲苯7.5mL/L,二氯甲烷47.5 mL/L,复合非离子型表面活性剂15mL/L~20mL/L,阴离子型表面活性剂5mL/L~7mL/L,酮或醚适量,在室温下处理5min左右。
(2)超声波除蜡。
超声波除蜡时,单位有效容积的功率一般设计在8 W/L较合理。
当<8w/ L时,除蜡速度较慢,影响生产的连续性;当>8 W/L时,锌合金压铸件在65℃~70℃下连续工作5min,会对零件表面产生较明显的失光失重现象,使得零件的富铝相中的铝优先溶解,造成麻点,甚至造成镀层起泡。
在配制超声波除蜡液时,若使用较差的水质,由于水中过量的金属阳离子不能被除蜡水中的络合剂完全络合,金属阳离子就有可能渗入到蜡垢之中或存在于工件表面,减弱了带负电荷的蜡垢与蜡垢之间、蜡垢与工件之间的电斥力,使得除蜡效果大大降低。
锌合金电镀工艺流程

锌合金电镀工艺流程
《锌合金电镀工艺流程》
锌合金电镀是一种将锌合金沉积在金属基材上的表面处理工艺,可以增加金属的硬度、耐磨性和抗腐蚀性,同时也具有美观的外观。
以下是锌合金电镀工艺流程的主要步骤:
1. 预处理
首先需要对金属基材进行预处理,这包括清洗、脱脂和除锈等步骤。
清洗可去除表面的杂质和油脂,脱脂可以去除基材表面的油脂和污垢,而除锈则是为了去除金属表面的锈斑和氧化物。
2. 化学镀底
接下来是进行化学镀底,将金属基材浸泡在特定的化学溶液中,通过化学反应形成一层均匀的镀底层,以提高电镀层与基材的附着力。
3. 电镀
在经过化学镀底后,金属基材就可以进行电镀了。
在电镀槽中,将含有锌离子的电镀液通电,使锌离子在金属基材表面沉积,形成一层锌合金电镀层。
4. 清洗与烘干
完成电镀后,金属基材需要经过清洗和烘干的步骤,以去除残留的电镀液和水分,同时使电镀层表面变得光滑。
5. 表面处理
最后需要进行表面处理,这包括抛光、喷漆或其他表面装饰工艺,以增加电镀层的外观和耐用性。
通过以上流程,金属基材就完成了锌合金电镀,得到了一层均匀、耐磨的锌合金电镀层,提高了基材的使用寿命和美观度。
- 1、下载文档前请自行甄别文档内容的完整性,平台不提供额外的编辑、内容补充、找答案等附加服务。
- 2、"仅部分预览"的文档,不可在线预览部分如存在完整性等问题,可反馈申请退款(可完整预览的文档不适用该条件!)。
- 3、如文档侵犯您的权益,请联系客服反馈,我们会尽快为您处理(人工客服工作时间:9:00-18:30)。
锌合金零件表面抛光膏及油污的去除
(1)除抛光膏。
零件抛光后表面残留一定的抛光膏,应当尽早除去这些残留的抛光膏,因为时间久了,抛光膏易硬化而不易除去。
除抛光膏可将工件浸泡在60℃~70℃的浓硫酸中(尽可能不掺水),使零件表面的抛光膏被浓硫酸氧化去除。
因为抛光膏的主要成分除金属氧化物(Mg0、Ca0、Al2O3、Fe2O3等)之外,主要是硬脂酸、石蜡等成分,这些有机物会被浓硫酸氧化。
这种方法在规模不大的厂家应用颇广。
其中关键是浓硫酸中不可掺进水,掺进水的浓硫酸对锌合金零件产生严重腐蚀,所以工件抛光后须干燥入硫酸槽。
还有就是使用由有机溶剂、表面活性剂组成的”冷脱剂”、”除蜡水”等溶液除抛光膏,若在除蜡水中配以超声波,则效果更佳。
通过热或冷脱脂,使锌合金表面的蜡垢润湿溶胀而部分溶解,提高超声波除蜡效率。
热脱脂是介于化学除油与除蜡之间的一种特殊形式,说它特殊,是因为它在超声波除蜡之前,其作用是尽可能使蜡垢润湿、溶胀,这种作用是靠碱液、非离子型活性剂与阴离子型表面活性剂等在适当温度下协同完成。
超声波能否快捷干净地将工件表面的蜡垢除尽,取决于热或冷脱脂的效果。
配制热脱脂的水质电导率在50μs/cm以下即可。
采用有机物冷脱脂,对锌合金压铸件而言,应为首选。
因它不仅无需加温,而且熔蜡润湿效果明显,对工件无不良腐蚀。
其工艺配方为:二甲苯7.5mL/L,二氯甲烷47.5 mL/L,复合非离子型表面活性剂15mL/L~20mL/L,阴离子型表面活性剂5mL/L~7mL/L,酮或醚适量,在室温下处理5min左右。
(2)超声波除蜡。
超声波除蜡时,单位有效容积的功率一般设计在8 W/L较合理。
当<8w/ L时,除蜡速度较慢,影响生产的连续性;当>8 W/L时,锌合金压铸件在65℃~70℃下连续工作5min,会对零件表面产生较明显的失光失重现象,使得零件的富铝相中的铝优先溶解,造成麻点,甚至造成镀层起泡。
在配制超声波除蜡液时,若使用较差的水质,由于水中过量的金属阳离子不能被除蜡水中的络合剂完全络合,金属阳离子就有可能渗入到蜡垢之中或存在于工件表面,减弱了带负电荷的蜡垢与蜡垢之间、蜡垢与工件之间的电斥力,使得除蜡效果大大降低。
这就是为什么一种好的除蜡水在某些厂使用效果良好,而在另一些厂效果则不见得好,或者一段时间好而另一段时间不好的重要原因。
许多供应商并没有给客户予以提醒:当水质中含有过多的如Cu+2,在工件表面会因置换铜而使得镀层局部起泡。
实践证明,选用电导率在50uS/cm以下的水质均可。
对锌合金压铸件而言,选择除蜡水的第一条原则就是pH值。
一般情况下,锌合金的临界使用pH值为l0。
也就是说,当任何一种除蜡水按其说明书配制完毕后,其溶液的pH≤10,否则,在特定的除蜡条件下易使零件产生失光失重,甚至发暗发黑现象,这样的除蜡水不能使用。
第二条原则就是除蜡效果,在说明书要求的前提下,除蜡速度快、易清洗的除蜡水宜选用。
第三条原则就是除蜡水的使用量和使用寿命。
(3)除油。
对于锌合金零件表面的油污来说,通常是使用有机溶剂除油,然后再用碱性溶液除油。
这是因为有机溶剂除油后可能会滞留在工件表面上,从而给后面的电镀带来不利影响。
另外,由于锌合金材料的主要成分是锌和铝,它们是两性金属,因此,碱性化学除油液的碱度也不能太强。
通常是磷酸三钠、碳酸钠、表面活性剂等成分,在50℃~60℃,3min~6min即可。
一般浸渍除油后的零件还应进行电解除油,电解除油最好是先用阴极电解除油,再用阳极电解除油。
但不要在同一槽中进行阴极或者阳极电解除油。
电解除油的溶液成分有氢氧化钠、磷酸三钠、碳酸钠、表面活性剂等成分,在50℃~60℃下,电流密度为2A/dm2~4A/dm2,30s~60s即可。
使用阳极电解除油,时间10s~15s(工件上有均匀气泡时即可),氢氧化钠可以增加溶液电导,防止电压过高腐蚀工件。
除油溶液温度不宜过低,否则电压会升高;温度也不能过高,否则碱会同零件基体的反应加剧,从而发生腐蚀溶解,以50℃~60℃为宜。
使用阴极电解除油时,由于在零件上析出较多氢,氢有很好的还原作用(活化其表面),原子氢结合成氢气冲击工件表面,达到很好的除油效果。
但仅用阴极电解除油,由于使用时间一长,溶液的污染就可能造成金属离子沉积在工件表面、电镀层发花、结合力不良等弊病。
这时若再用阳极电解除油,工件表面有一剥离(溶解)过程,工件表面表现出很好的活性,为后面电镀层结合力的提高打下了好的基础。
如果只使用阴极电解除油,则应该经常更新溶液,尽可能维护好除油溶液,要防止铜杂质污染溶液。
如仅使用阳极电解除油也是可以的。
只要保证在阳极电解除油前零件表面油污已大部分除净即可。
需要注意的是:除油过程中水洗一定要彻底,除油后工件经活化、水洗后,应不憎水,与水亲合,不应因除油不彻底零件存在残留的抛光蜡,经酸性镀铜加厚后而产生腐蚀点。
除油溶液还应保持一定的浓度和纯度,要定期更换,以防异金属离子浓度达到一定值时而产生置换层,影响镀层的结合力,特别是除油液应与铁基零件、铜基零件分开进行,这一点千万不要被忽略。
4.活化
除油后的锌合金工件经过清洗,而且必须进行活化后才能进行电镀。
通常的活化溶液分别有:HF(40%)59/L~209/L、H2S04(98%)159/L~759/L或者 HCl(37%)l09/L~209/L,在室温下浸3s~6s即可,经验是以零件表面析出氢气后再延长ls~2s为宜。
活化溶液的选择,视锌合金的牌号或回料使用的比例而定。
回料较多的锌合金零件,需使用氢氟酸活化,因为回料中时常会带人硅杂质,氢氟酸属于弱酸,对基体的腐蚀速率较小。
对锌合金压铸件而言,也可以不使用盐酸、硫酸或氢氟酸进行活化,因为这些酸为无机强酸,对工件的腐蚀性强,富锌相析氢严重,其表面致密层会遭到严重破坏。
因此,也可以选用固体酸进行活化处理,可以保证零件表面的密着性变化小,无起泡、麻点等缺陷。
固体酸活化溶液为:①草酸109/L,酒石酸59/L,硫酸3mL/L~5mL/L,缓蚀剂适量,室温,3s~10s。
②C6H807 409/L~509/L,H3B03适量,NH4HF适量,缓蚀剂0.29/L~O.39/L,室温下活化处理5s~10s.
5.预镀
为提高锌合金零件电镀层的结合力,通常要采取预镀措施,通常有氰化物词镀铜,后续通过焦磷酸盐镀铜,增加零件表面铜层厚度,而且铜层致密,深镀能蔓好,镀液本身近中性,工件电镀时间长些也不致于被溶液腐蚀。
同时多一道焦磷酸盐预镀铜工艺,还可以防止氰化物镀铜液清洗不良而对后道酸铜、亮镍带来篚污染。
随着氰化物电镀工艺的限制,直接使用焦磷酸盐预镀铜工序,或者使用预镪中性镍工艺。
预镀中性镍的电流密度较小,要镀到一定厚度的时间较长。
预镪中性镍的溶液主要成分有:NiS04·6H20 1009/L~1209/L,NaCl l29/L~169/L, H3B03 309/L~35 9/L,Nas C6H507·2H20 1209/L~1509/L。
pH 7.O~7.5,镀液温度40℃~50℃,电流密度0.8A/dm2~1.2A/dm2。
采用阴极移动。
锌合金零件电镀中性镍的优点是,pH值近中性,对工件腐蚀少,即使有少量Zn2+溶解,因柠檬酸钠会隐蔽Zn2+,不影响镀层的结合力;另外镀层体系中不含预镀铜层,有利于零件做CASS腐蚀试验测试。
缺点是镍比较贵、成本高,该工艺的电流密度小,镀到一定厚度的生产用时较长等。