H型钢生产工艺流程图
H形钢制作流程
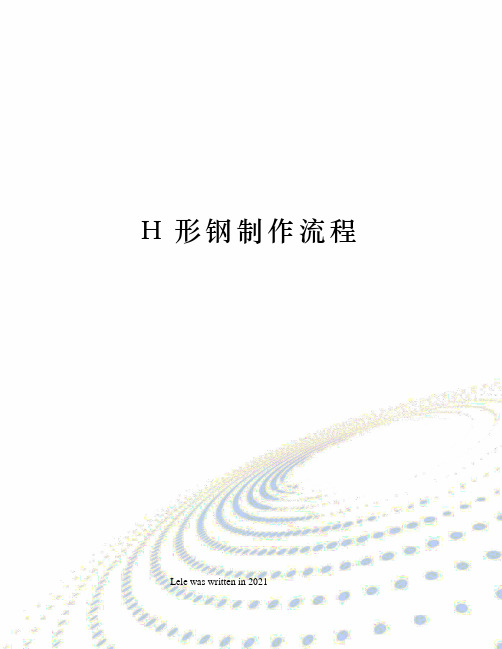
H形钢制作流程 Lele was written in 202101、H型钢机械组立工序作业示意图0101、检查板料是否符合要求后(平整度、直线度、拼缝余高、及错边量、毛刺是否清除干净等),将翼板放置在组立机辊轮架上,用横向压紧轮定位翼板的位置;0102、再放置腹板,用腹板横向压紧轮和上压紧轮,固定腹板位置,且保证腹板拼缝和翼板拼缝间距不小于200mm,翼缘板拼接长度不得小于2倍板宽;腹板拼接宽度不得小于300mm,长度不得小于600mm;0103、检验腹板是否处于正中位置,腹板与翼板是否处于垂直状态,并进行相应调整后将端部先进行点固焊。
腹板中心偏移的允许偏差小于2mm,翼缘垂直度小于3mm;0104、启动组立机送进装置,随着工件移动在腹板两侧采用CO2气体保护焊或手工电弧焊进行点固焊接。
点固焊接长度宜采用40~50mm,点固焊接的间隔宜采用300~500mm。
点固焊焊点表面应平坦、均匀、无缺陷。
组立缝应严密,翼腹板间隙≤1mm,当间隙过大时应进行补焊;0105、点焊牢固之后将T型板吊离滚轮架;0106、将另一翼板放置在组立机辊轮架上,用横行压紧轮,定位翼板的位置;0107、放置T型板,用腹板横向压紧轮和上压紧轮,固定T型板位置,之后进行H型组立;0108、检验腹板是否处于正中位置,腹板与翼板是否处于垂直状态,进行调整,截面高度是否符合要求;确认合格后将端部先进行点固焊。
腹板中心偏移的允许偏差小于2mm,翼缘垂直度小于3mm,截面高度允许偏差±2mm;0109、启动组立机,随着工件移动,在腹板两侧采用CO2气体保护焊或手工电弧焊进行点固焊接。
点固焊接长度宜采用40~50mm,点固焊接的间隔宜采用300~500mm。
点固焊焊点表面应平坦、均匀、无缺陷。
组立缝应严密,翼腹板间隙≤1mm,当间隙过大时应进行补焊;0110、对H型钢截面尺寸、点焊质量进行全面检查。
自检合格后做好记录,将组立好的H型钢吊离滚轮架,并报检验员抽检。
H型钢制作工艺

序工程概况一、焊接H制作执行标准及工艺流程图:1.1 《钢结构工程施工质量验收规范》GB50205-2001。
1. 2 《高层民用建筑钢结构技术规程》JGJ99-1998。
1. 3 《建筑钢结构焊接技术规程》JGJ 81-2002。
1. 4 《钢结构高强螺栓连接的设计、施工及验收规范》JGJ82-91。
1. 5 《焊缝符号表示方法》GB324—88。
二、施工工艺1.1下料2.1.1根据供料宽度,合理进行配料,充分利用板的宽度方向,大料优先配料,出现板边(宽度余料)时,应将小料同时排版,作到本批次供料尽量用完,余下长度方向的料头,转入小料(或回收)。
长度方向预留30〜40mm荒料。
2.1.2根据施工图纸,合理拼接材料,下列部位严禁设置拼接接口:a牛腿处的上下200mm范围内。
b加劲板100mm范围内。
c孔群100mm范围内。
d吊车梁长度方向,跨中1/3范围内。
2.1.3焊接H型钢的翼缘板与腹板应相互错开200mm以上,且翼缘板尽量避免设置在一个平面。
2.1.4材料的平面度超出允许偏差时,应进行较平,较平后的材料应符合表2.1.3-1。
2.2 制孔2.2.1零件的制孔,首选数控钻床,在钻制前,应将零件表面的氧化铁打磨干净,钢板必须进行平直。
2.2.2零件上的孔在数控钻床无法钻制时,可用80摇臂钻钻孔,零件必须垫平、固定牢靠。
2.1.3-1 钢材矫正后的允许偏差2.3 拼接2. 3.1材料的拼接,优先考虑整体拼接,焊接完毕后,经无损探伤 检验合格后,再进行切割板条。
2. 3. 2 当材料需要接净料时,应用粉线测、拉直线度,接口处不得 出现急剧弯曲现象,宽度允许错口 1mm ,直线度允许L/1000,且不 大于5mm 。
2. 3. 3 拼接材料的允许错边,见表2.3.3-1,拼接接口形式见图2.3.3-1.2. 3.4 拼接材料焊缝的一端或(或无接口)翼缘有缩进尺寸的一端,必须将材料标明方向(下或左)端;画出组立草图,转到组立工序。
H型钢组立、十字柱装焊顺序(图文流程)
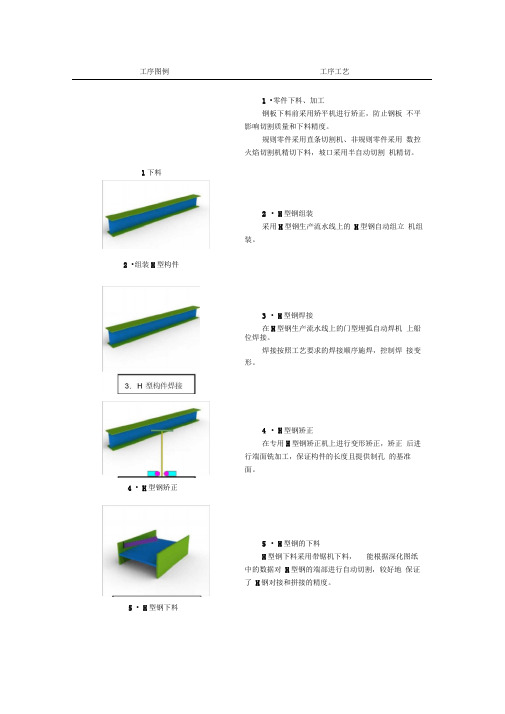
1•零件下料、加工钢板下料前采用矫平机进行矫正,防止钢板不平影响切割质量和下料精度。
规则零件采用直条切割机、非规则零件采用数控火焰切割机精切下料,坡口采用半自动切割机精切。
1下料2• H型钢组装采用H型钢生产流水线上的H型钢自动组立机组装。
2 •组装H型构件3• H型钢焊接在H型钢生产流水线上的门型埋弧自动焊机上船位焊接。
焊接按照工艺要求的焊接顺序施焊,控制焊接变形。
4• H型钢矫正在专用H型钢矫正机上进行变形矫正,矫正后进行端面铣加工,保证构件的长度且提供制孔的基准面。
4 • H型钢矫正5• H型钢的下料H型钢下料采用带锯机下料,能根据深化图纸中的数据对H型钢的端部进行自动切割,较好地保证了H钢对接和拼接的精度。
5 • H型钢下料6• H型钢的钻孔H钢的钻孔采用本公司先进的数控三维钻床,拥有精密度测量系统及软件和H钢标记系统,重复定位精度达0.01m m;其能对翼板和腹板进行高速高效地自动钻孔,可满足工程的工期需要和质量要求。
6 •三维钻孔7• H型钢的锁口H型钢锁口加工采用日本引入的先进设备进行加工,其能对H型钢全自动送料、定位、夹紧、锁口及端部坡口自动加工,加工精度高,加工表面质量优。
7•锁口加工工序图例 工序工艺多-"-解"零件下料腹板上划T 型 H 型组立 H 型钢船形焊构件分割线拆分后的T 型构件 H 型构件沿长度方向H 型钢矫正切割拆分成T 型构件H 型钢部件 T 型钢部件十字型构件2. H 螫诅立灵二次施工3、制蛰均糕、® ①工序图例制作工序说明l r板轲下料(1) 板材加工钢板下料前采用矫平机进行矫正,防止钢板不平影响切割质量和下料精度。
规则零件采用直条切割机、非规则零件采用数控火焰切割机精切下料,坡口采用半自动切割机。
(2)H型钢组装焊接H型钢的翼缘板拼接缝和腹板拼接缝的间距不宜小于翼缘板拼接长度不应小于600mm腹板拼接宽度不应小于不应小于600mm200mm300mm长度(4)H 型钢矫正在专用H 型钢矫正机上进行变形矫正,矫正后进行端面铳加工,保 证构件的长度且提供制孔的基准面。
H型钢生产工艺流程
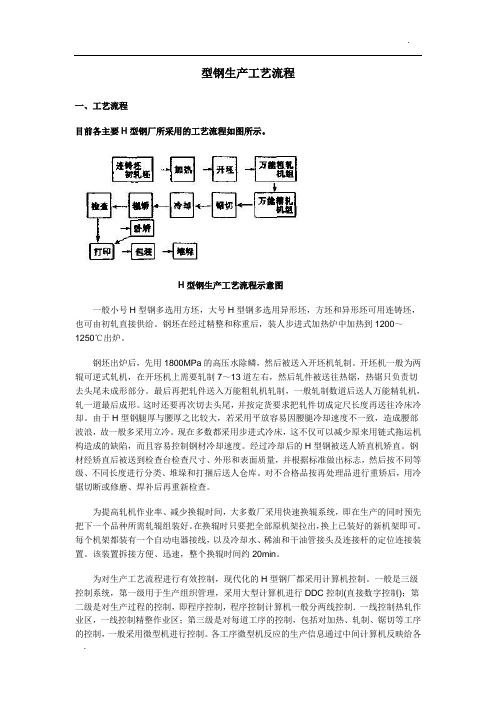
型钢生产工艺流程一、工艺流程目前各主要H型钢厂所采用的工艺流程如图所示。
H型钢生产工艺流程示意图一般小号H型钢多选用方坯,大号H型钢多选用异形坯,方坯和异形坯可用连铸坯,也可由初轧直接供给。
钢坯在经过精整和称重后,装人步进式加热炉中加热到1200~1250℃出炉。
钢坯出炉后,先用1800MPa的高压水除鳞,然后被送入开坯机轧制。
开坯机一般为两辊可逆式轧机,在开坯机上需要轧制7~13道左右,然后轧件被送往热锯,热锯只负责切去头尾未成形部分。
最后再把轧件送入万能粗轧机轧制,一般轧制数道后送人万能精轧机,轧一道最后成形。
这时还要再次切去头尾,并按定货要求把轧件切成定尺长度再送往冷床冷却。
由于H型钢腿厚与腰厚之比较大,若采用平放容易因腰腿冷却速度不一致,造成腰部波浪,故一般多采用立冷。
现在多数都采用步进式冷床,这不仅可以减少原来用链式拖运机构造成的缺陷,而且容易控制钢材冷却速度。
经过冷却后的H型钢被送人矫直机矫直。
钢材经矫直后被送到检查台检查尺寸、外形和表面质量,并根据标准做出标志,然后按不同等级、不同长度进行分类、堆垛和打捆后送人仓库。
对不合格品按再处理品进行重矫后,用冷锯切断或修磨、焊补后再重新检查。
为提高轧机作业率、减少换辊时间,大多数厂采用快速换辊系统,即在生产的同时预先把下一个品种所需轧辊组装好。
在换辊时只要把全部原机架拉出,换上已装好的新机架即可。
每个机架都装有一个自动电器接线,以及冷却水、稀油和干油管接头及连接杆的定位连接装置。
该装置拆接方便、迅速,整个换辊时间约20min。
为对生产工艺流程进行有效控制,现代化的H型钢厂都采用计算机控制。
一般是三级控制系统,第一级用于生产组织管理,采用大型计算机进行DDC控制(直接数字控制);第二级是对生产过程的控制,即程序控制,程序控制计算机一般分两线控制.一线控制热轧作业区,一线控制精整作业区;第三级是对每道工序的控制,包括对加热、轧制、锯切等工序的控制,一般采用微型机进行控制。
H型钢加工制作工艺流程

H型钢加工制作工艺流程4.1.2焊接H型钢加工制作工艺和方法1、钢板的预处理、矫平、下料切割钢板下料切割前需要进行钢板预处理,出去钢板表面的氧化层,提高钢板表面的致密性,保证焊接质量。
钢板下料切割采用精密数控火焰钢板切割机。
2、钢板对接钢板对接坡口采用半自动精密切割,钢板对接焊接采取半自动埋弧焊焊接。
3、T型部件制作T型组立在H型钢生产线上全自动组立机上组立成型,确保T型组立腹板与翼缘板的垂直度达到设计要求,组立后进行临时固定,固定采用附加工艺板方法固定。
4、H型钢组立H型钢组立在进口H型钢生产线上组立,四个液压定位系统顶紧H型钢构件的上下翼缘板和腹板上进行定位;调节翼缘板的平行度和翼板和腹板的垂直度然后固定;固定焊接采用CO2气体保护焊。
5、H 型钢焊接H 型钢焊接在H 型钢自动生产线上进行全自动埋弧焊节,将合格的H 型钢构件吊上船形胎架上,调节其焊接位置后固定焊接,焊接采取对称焊接顺序施焊。
6、H 型钢矫正H 型钢四条主焊缝焊接后由于焊接产生的热量一时难以释放;然而产生焊接应力变形,所以构件焊接后为确保翼缘板的平行度要求。
需要进行H 型钢的矫正。
矫正在H 型钢自动生产线上的矫正机上矫正。
7、型钢测量H 型钢在成型后需要进行测量,测量主要是翼缘板平行度,翼缘板与腹板的垂直度是否符合设计要求。
8、H 型钢钻孔、端面加工H 型钢成型后进行钻孔加工,钻孔在进口全自动三维数控钻床上加工,确保孔间距符合设计要求;由于工程结构系高层钢结构,所以端面加工是保证钢结构对接的重要质量因素。
端面加工主要在端面铣床上进行铣削坡口。
确保两端面的平行度。
9、构件抛丸除绣构件制作完成合格后进入抛丸除绣加工,抛丸除绣主要采取进口八头全自动抛丸除绣机抛丸。
10、构件标识、存放将构件编号定位标记等按工艺规定标注在规定位置,杆件存放时应注意保护,下层垫枕木,多层构件堆放时注意构件变形。
3.2.4.2焊接H 型钢加工制作工艺细则1、钢板拼接采购的钢板若长度不够,应进行钢板对接。
H型钢生产工艺流程
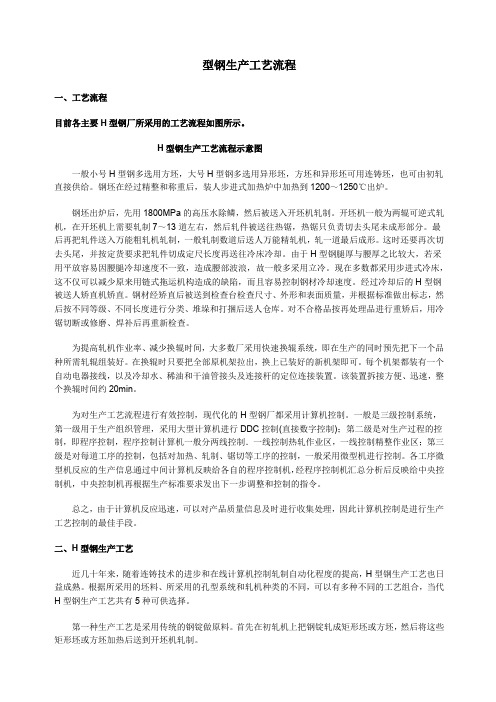
型钢生产工艺流程一、工艺流程目前各主要H型钢厂所采用的工艺流程如图所示。
H型钢生产工艺流程示意图一般小号H型钢多选用方坯,大号H型钢多选用异形坯,方坯和异形坯可用连铸坯,也可由初轧直接供给。
钢坯在经过精整和称重后,装人步进式加热炉中加热到1200~1250℃出炉。
钢坯出炉后,先用1800MPa的高压水除鳞,然后被送入开坯机轧制。
开坯机一般为两辊可逆式轧机,在开坯机上需要轧制7~13道左右,然后轧件被送往热锯,热锯只负责切去头尾未成形部分。
最后再把轧件送入万能粗轧机轧制,一般轧制数道后送人万能精轧机,轧一道最后成形。
这时还要再次切去头尾,并按定货要求把轧件切成定尺长度再送往冷床冷却。
由于H型钢腿厚与腰厚之比较大,若采用平放容易因腰腿冷却速度不一致,造成腰部波浪,故一般多采用立冷。
现在多数都采用步进式冷床,这不仅可以减少原来用链式拖运机构造成的缺陷,而且容易控制钢材冷却速度。
经过冷却后的H型钢被送人矫直机矫直。
钢材经矫直后被送到检查台检查尺寸、外形和表面质量,并根据标准做出标志,然后按不同等级、不同长度进行分类、堆垛和打捆后送人仓库。
对不合格品按再处理品进行重矫后,用冷锯切断或修磨、焊补后再重新检查。
为提高轧机作业率、减少换辊时间,大多数厂采用快速换辊系统,即在生产的同时预先把下一个品种所需轧辊组装好。
在换辊时只要把全部原机架拉出,换上已装好的新机架即可。
每个机架都装有一个自动电器接线,以及冷却水、稀油和干油管接头及连接杆的定位连接装置。
该装置拆接方便、迅速,整个换辊时间约20min。
为对生产工艺流程进行有效控制,现代化的H型钢厂都采用计算机控制。
一般是三级控制系统,第一级用于生产组织管理,采用大型计算机进行DDC控制(直接数字控制);第二级是对生产过程的控制,即程序控制,程序控制计算机一般分两线控制.一线控制热轧作业区,一线控制精整作业区;第三级是对每道工序的控制,包括对加热、轧制、锯切等工序的控制,一般采用微型机进行控制。
【技术】H型钢生产工艺流程
【技术】H型钢生产工艺流程导读:为生产出质量好、成本低的H型钢,首先需要确定一个合理的生产工艺流程。
目前各主要H型钢厂所采用的主流工艺流程如下图所示。
一般中小规格(H400×200及以下规格)H型钢多选用方坯、矩形坯,较大规格(H400×200以上规格)H型钢多选用异形坯,矩形坯和异形坯都可用连铸坯。
从连铸过来的钢坯在经过称重后,装入步进式(或推钢式,现在用于生产型钢的推钢炉已经比较少)加热炉中加热到1200~1250℃出炉。
步进式加热炉大多数采用上、下布置的双预热式烧嘴,可对不同规格钢坯提供最佳的温度控制,并节约燃料。
钢坯出炉后,先用10-25MPa的高压水除鳞,然后送入开坯机轧制。
开坯机一般为两辊可逆式轧机(在小型钢上也有采用三辊轧机的,但工艺局限性强不利于生产组织),在开坯机上需要轧制5~13道次左右,然后轧件被送往切头飞剪或热锯,热锯只负责切去头部未成形部分,但飞剪可切头、分段及切尾。
切头后的轧件送入精轧机组进行轧制,国内主要厂家小规格型钢精轧都采用全连轧形式,大规格型钢精轧都为可逆轧制。
经精轧轧制后一般都直接送上冷床进行冷却,但也有采用上冷床前进行分段或上冷床后切头的。
大规格型钢由于腿厚与腰厚差比较大,若采用平放容易因腰腿冷却速度不一致,造成腰部波浪,故一般多采用立冷。
但小规格H型钢主流厂家都采用步进齿式冷床都在齿条上斜放,采用步进式齿式冷床不仅可以减少原来用链式拖运机构造成的缺陷,而且容易控制钢材冷却速度。
经过冷却后的H 型钢被送人矫直机矫直。
由于H型钢断面模数较大,一般都采用8辊、9辊或10辊式矫直机矫直,矫直辊间距最大可达2200mm。
钢材经矫直后被送入编组台架进行分组等候锯切,经冷锯按定尺长度锯切后被送到检查台检查尺寸、外形和表面质量,然后进行分类、堆垛和打捆后送入仓库。
对不合格品按按缺陷种类进行对应的重矫、修磨、焊补及其它处理,然后进入对应质检程序检查合格后再分类入库。
H型钢构件打底焊工序作业示意图
H型钢构件打底焊工序作业示意图
0201、将构件摆放在平台上,并检查组立工序中点焊质量和组立间隙是否符合焊接要求,当有坡口时,检查坡口是否符合要求;
0202、按要求装配引弧板和熄弧板,引熄弧板的宽度应大于80mm,长度大于150mm,厚度大于10mm;引熄弧板的坡口形式应与母材一致;
0203、必要时,根据材质和板厚进行焊前预热,若母材为Q345按下列要求进行预热:a.40
0204、焊接,a.工艺没有特殊要求时,按下列参数进行施焊:I=240~310A,U=29~33V,V=24~35cm/min,b.为了减少焊接变形,焊接时采用分段退焊法进行焊接;如下图5所示:打底焊高度原则上不宜大干10mm;c.对设计要求全熔透区域背面清根;
0205、分段退焊示意图,数字顺序为焊接顺序(也可采用分段跳焊法焊接,焊接时尽可能采取对称焊接);
0206、焊接后检查焊缝外观质量,合格后清除毛刺飞溅。
H型钢制作工艺流程
焊接H型钢的制作工艺学校:新疆职业大学院系:机电学院班级:焊接09—1姓名:***学号:**************目录1. 制作工艺方案确定2. 原材料矫正3.下料4. 切割后的矫正5. 组装6. 焊接7. 焊后矫正8. 连接板和加劲板的焊接9. 焊后矫正10. 涂装11. 防火涂料施工12. 结论焊接H型钢的制作工艺:本工程设计采用轧制H型钢,型号为HE600A、HE700B、HE700A、HE500A。
但因市场上采购不到设计要求的轧制H型钢,通过设计变更认可,采用焊接H 型钢。
1.制作工艺方案确定焊接H型钢制作采用H型钢生产自动流水线,焊接方式采用埋弧焊。
焊接工程师根据施工图中所有焊接接头型式,母材材质、厚度、焊接位置,结合所采用焊接方法,进行综合考虑,按相关焊接工艺评定标准规定,在焊接前进行严格周密的焊接工艺评定试验,将评定报告中的焊接参数作为施焊的指导性文件。
焊工须参加相应资格的焊工考试,合格后方可进行相应资格的焊接作业。
所有参加焊接的焊工必须按照相应的焊接工艺规程的规定进行操作。
在焊接H型钢制作中,关键工序有:下料、组装、焊接、矫正。
特殊工序为焊接。
其制作工艺流程详见下图:焊接H型钢制作工艺流程图。
file:///C:/Users/ADMINI~1/AppData/Local/Temp/ksohtml/wps_clip_image-3 1271.png焊接H型钢制作工艺流程图2、原材料矫正钢材在存放、运输、吊装等过程中不当会引起变形,影响到号料的准确性,所以号料前应将变形材料进行矫正。
主要采用机械矫正的方法,如型钢调直机、压力机等设备进行矫正,矫正后的允许偏差见下表:钢材矫正后的允许偏差。
钢材矫正后的允许偏差见下表项目允许偏差局部平面度钢板厚度t≤14 1.5 任意1m内钢板厚度t>14 1.03、下料根据图纸尺寸进行钢板排版,排版时预留焊接收缩余量和加工余量,余量为25~30mm;采用数控多头直条切割机进行切割,切割前,检查气源是否充足,割嘴是否畅通;切割过程中,观察火焰是否正常;切割完毕,清除构件表面的毛刺、飞溅、熔渣,并打磨光滑,构件按编码整齐摆放。
H型钢工艺流程.ppt
切割
切割前,对下料工确定的号料尺寸进行复核,核对无误 后,方可进行切割。切割前应将钢材切割区域表面的铁锈 、污物等清除干净,切割后应清除熔渣和飞溅物。切割的 允许偏差应符合下表的规定。
注:t为切割面厚度。
气割操作应注意的工艺要点:
A、气割前必须检查确认整个气割系统的设备和工具全部运转 正常,并确保安全。在气割过程中应注意:
④ H型钢翼板与腹板之间的组装间隙△≤1mm。
焊接
焊接顺序:打底焊一道,填充焊一道,翻身,碳弧气刨清根,反面打底 填充,盖面,翻身,正面填充,盖面焊。
焊前准备 为防止焊缝缺陷产生,焊接应在组装质量检查合格后进行。在每
个焊口施焊前,对坡口及周边的范围内进行清理。清除水份、脏物、 铁锈、油漆、油污等杂物。施焊前确认可施焊条件,检查坡口尺寸、 角度、钝边、间隙等是否符合设计要求,并作好记录,作为超声波检 查的依据。正式施焊前,对钢板焊缝区(100mm)进行预热,以减少 钢材收缩应力。 焊条、焊剂应进行烘干,根据焊接条件、坡口形式、 施焊位置、板材厚度选择合理的焊接电流及焊条,焊接时,严禁在焊 缝区域外母材上打火引弧。重要结构在施焊前,应进行模拟实物的确 认性试验。确定工艺参数等,经无损探伤合格后,作抗拉、抗弯、冲 击试验。全部合格后,方可准予施工。
a、气压稳定,不漏气 b、压力表、速度计等正常无损。 c、机体行走平稳,使用轨道时奥保持平直和无振动。 d、 割嘴气流畅通,无污损。 e、割炬的角度和位置准确。
B、气割时应选择正确的工艺参数,工艺参数的选择主要是根据气 割机械的类型和可切割的钢板厚度进行确定。
C、切割时应调节好氧气射流(风线)的形状,使其达到并保持 轮廓清晰、风线长和射力高。
拼装
H型组对前应对钢材表面曲度、高度、平整度进行检查。对钢板 接触面的毛刺、污物和杂物等应清理干净,以保证构件的组装紧密 结合。组立前应备齐检测工具,如直角钢尺、钢板尺等,以保证组 立后有足够的精度。点焊焊材材质应与主焊缝材质相同,长度50m左 右,间距300mm,焊缝高度不得大于6mm,且不超过设计高度的2/3。 由于构件较长,故腹板和翼缘板都有对接焊缝。