汽轮机快冷系统总结综述
6号机1月20日干抽真空快冷操作总结丙值
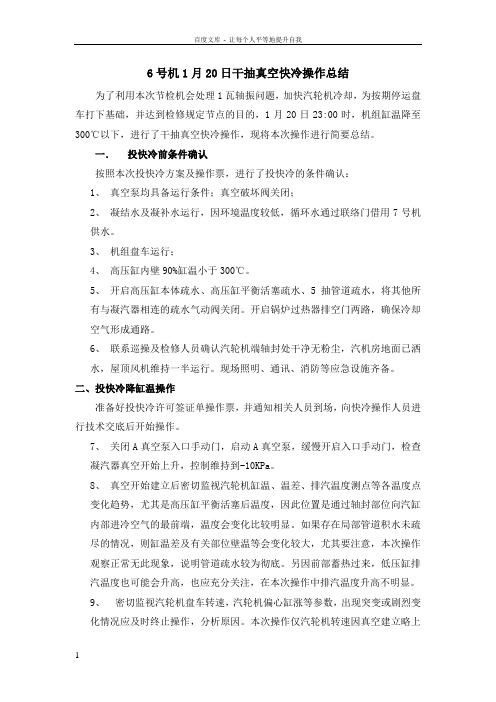
6号机1月20日干抽真空快冷操作总结为了利用本次节检机会处理1瓦轴振问题,加快汽轮机冷却,为按期停运盘车打下基础,并达到检修规定节点的目的,1月20日23:00时,机组缸温降至300℃以下,进行了干抽真空快冷操作,现将本次操作进行简要总结。
一.投快冷前条件确认按照本次投快冷方案及操作票,进行了投快冷的条件确认:1、真空泵均具备运行条件;真空破坏阀关闭;2、凝结水及凝补水运行,因环境温度较低,循环水通过联络门借用7号机供水。
3、机组盘车运行;4、高压缸内壁90%缸温小于300℃。
5、开启高压缸本体疏水、高压缸平衡活塞疏水、5抽管道疏水,将其他所有与凝汽器相连的疏水气动阀关闭。
开启锅炉过热器排空门两路,确保冷却空气形成通路。
6、联系巡操及检修人员确认汽轮机端轴封处干净无粉尘,汽机房地面已洒水,屋顶风机维持一半运行。
现场照明、通讯、消防等应急设施齐备。
二、投快冷降缸温操作准备好投快冷许可签证单操作票,并通知相关人员到场,向快冷操作人员进行技术交底后开始操作。
7、关闭A真空泵入口手动门,启动A真空泵,缓慢开启入口手动门,检查凝汽器真空开始上升,控制维持到-10KPa。
8、真空开始建立后密切监视汽轮机缸温、温差、排汽温度测点等各温度点变化趋势,尤其是高压缸平衡活塞后温度,因此位置是通过轴封部位向汽缸内部进冷空气的最前端,温度会变化比较明显。
如果存在局部管道积水未疏尽的情况,则缸温差及有关部位壁温等会变化较大,尤其要注意,本次操作观察正常无此现象,说明管道疏水较为彻底。
另因前部蓄热过来,低压缸排汽温度也可能会升高,也应充分关注,在本次操作中排汽温度升高不明显。
9、密切监视汽轮机盘车转速,汽轮机偏心缸涨等参数,出现突变或剧烈变化情况应及时终止操作,分析原因。
本次操作仅汽轮机转速因真空建立略上升,其他正常,同时就地汇报汽轮机本体无异常。
10、确认真空建立后缸温下降速度仍偏低,进行开汽门操作。
联系热控人员将汽轮机跳闸信号强制,在DEH阀门管理画面复归汽轮机跳闸,将汽轮机挂闸,开启主汽门,开启主调门方向阀,通过调门操作块设定调门开度逐渐开启调门。
浅谈大型汽轮机快速冷却技术的应用

浅谈大型汽轮机快速冷却技术的应用摘要:简述了大型汽轮机的快速冷却方式,并就快速冷却过程中的问题提出相应的措施。
关键词:大型汽轮机快速冷却方式问题措施1、大型汽轮机的快速冷却方式1.1按冷却介质分按冷却介质分,汽轮机的快速冷却方式可分为蒸汽冷却和空气冷却。
从传热性能来说,采用低参数蒸汽具有较大的放热系数。
例如取温度为20℃的空气及150℃的饱和蒸汽作比较,它们若以相同的流速流过相同管径的流道,蒸汽的放热系数约为空气的 3 倍。
除此之外采用蒸汽的最大好处就是系统不用作较大的改动,而且不必增添其他设备。
大功率机组通常为单元机组,可适当地增加一些管道从邻机的除氧器抽汽管路获得适当数量的蒸汽。
然而采用蒸汽作为冷却介质时,也有不利的因素:(1)对于单元机组,有时是利用锅炉的余热及炉底加热装置(冷源由邻炉来)产生的蒸汽作为汽源,有时直接将邻机的蒸汽(例如邻机除氧器、抽汽汽源)作为冷却介质。
由于蒸汽具有较大的热焓值,而这些蒸汽的温度和流量通常不便于调节,对在金属温度下降过程中的冷却速度控制不利,在采用顷流冷却时,甚至会造成汽轮机转速升高。
(2)低温蒸汽在流动过程中,可能携带水分,不但容易造成上、下缸冷却的不均匀,而且对停机后的金属保养不利。
采用空气冷却具有如下优点:(1)它独立于锅炉系统,特别适合于单元机组,可以随时启动供汽系统。
如果原有供检修用的压缩空气汽源合适的话,不必另添设备。
而空气的流量和温度的控制也较为方便,对控制汽轮机的冷却速度和避免过大的热应力有利。
(2)空气流过金属表面的换热系数小,当两者温差出现瞬时过大时,也不至于引起被换热的金属表面产生急剧冷却(热冲击),即不至于使金属产生过大的热应力,允许的传热温差大,在适当的流动条件下便能满足加热冷却的要求。
(3)空气的温度变化不存在汽水两相互变(凝结)的特性,在快速冷却过程的同时也干燥了汽轮机的内部,对设备保养有良好作用。
以空气为冷却介质的快速冷却方式又可分为抽真空冷却和压缩空气冷却。
新型汽轮机快速冷却方法的原理及应用

自 冷却将会贻误检修 时间。快冷的实现 ,可以为机组 然 本体提前进 入检修或机组轴 系故障处理节省时 间和带来
方便 。
阳城 电厂2机 组 汽轮 机 采用 东 方汽 轮机 厂 生 产的
G M 通 用 瓤 艇 W V.j.e 21年 第1期 W ̄y n t 00 tx O
取主 厂房 内室温2  ̄ 0C,汽缸 壁温取 值 2 0 4 0C,汽轮 机 高 中压 缸假 设 为 0 ̄0  ̄ 直径25 .m、长度3 m的圆柱 。 定性温度t为平均温度 , t= / +  ̄l 2( f) () 4
2工艺流程 .
锅 炉产 生 的一 定压 力 、温 度 的蒸 汽通 过低 温过 热 器 、屏 式过 热 器 、高温过 热器进入 到高压 主汽门前 ,通过热工 强制信号 ,打开 高压 主汽门 、高压调门 ,余汽进入 高压缸 冷却 ,冷却 后的余汽 经过高排 逆 止 门后进入 到低温再热 器 、屏 式再热 器 ,利用屏 式再热 器两侧 的对 空 排 汽 ,把 蒸汽 排入 大 气 ,形成 蒸汽 通 路 。在此 过 程 中要严 格控 制 余
运动黏 度,m ; / s
—
—
温差;
1原 理 .
— —
热导率 ,W ( K ; / ) m-
对流换热 系数 ,W/ .) ( K。 m2
利 用与汽轮机缸 温始终 保持合理 温差 ( 0 ≤5 ℃)的蒸汽快速 冷却
汽轮机 ,在此过 程 中,温降速 度 <5 ℃/ ,以便 不致使 汽轮机 产生 ~8 h 有害热 应 力、热变形 ,发生 动静部 分碰撞 和磨 损 。余汽 温度 、压力 通过锅炉控制 ,并保 持5  ̄ 0C以上的过热 度。
理 、工 艺及理论 计算 过程。实测数据 的对 比分析表 明:
汽轮机总结

汽轮机总结汽轮机是一种将热能转化为机械能的装置,广泛应用于发电厂、石油化工等工业领域。
它以其高效、可靠的特点,在现代工业中扮演着重要的角色。
本文将从汽轮机的工作原理、组成部分以及未来发展趋势等方面进行总结。
首先,我们来了解汽轮机的工作原理。
汽轮机运用了热力学中的热力循环原理,利用燃烧产生的高温高压气体驱动叶片旋转,实现了能量转换。
其基本原理是:燃料在燃烧室中燃烧产生高温高压气体,然后通过喷嘴喷入叶轮,气体的高速旋转使叶轮转动,从而驱动发电机或其他设备工作。
同时,冷却系统会对叶轮进行冷却,以确保发电机的正常运行。
汽轮机的组成部分包括燃烧室、叶轮和发电机。
燃烧室是汽轮机内燃烧燃料的地方,通常采用高温高压的燃气。
叶轮是汽轮机中最关键的部分,它们通过高速旋转将燃烧产生的气体转化为机械能。
发电机则将机械能转化为电能,使其可以被工业和家庭使用。
随着科技的不断进步,汽轮机在结构和效率上也有了许多改进。
例如,新型的叶轮设计使得汽轮机能够更高效地工作。
此外,改进的材料和制造工艺也使汽轮机的性能得到提升。
随着对节能环保要求的提高,发展可再生能源已成为汽轮机领域的发展方向之一。
例如,有些发电厂将废弃物利用为燃料,通过汽轮机来发电,实现了能源的再利用。
未来汽轮机的发展趋势也值得关注。
随着新能源技术的发展,如风力、太阳能等,对汽轮机的需求可能会逐渐减少。
然而,汽轮机仍然是一种可靠、高效的能源转换装置,在许多工业和领域仍然有着广泛的应用前景。
未来,我们可以期待汽轮机技术的不断创新,以提高其效率和可靠性,并适应未来能源市场的需求。
除了在能源领域的应用外,汽轮机还有其他一些潜在的应用。
例如,在航空工业中,涡喷发动机就是一种应用了汽轮机原理的设备,将燃油燃烧产生的气体喷出从而提供推力。
汽轮机的应用还延伸到了船舶、石油化工等领域,使得这些工业的生产更加高效和可持续。
综上所述,汽轮机作为一种将热能转化为机械能的装置,在现代工业中发挥着重要的作用。
大型汽轮机快速冷却技术研究综述
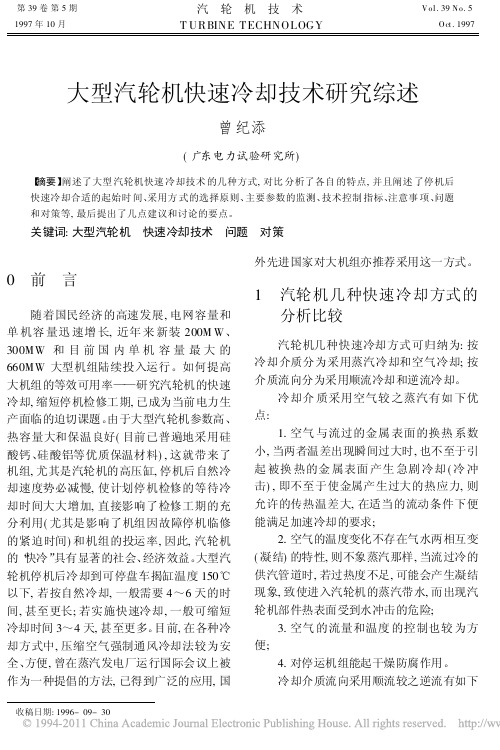
大型汽轮机快速冷却技术研究综述曾纪添(广东电力试验研究所)【摘要】阐述了大型汽轮机快速冷却技术的几种方式,对比分析了各自的特点,并且阐述了停机后快速冷却合适的起始时间、采用方式的选择原则、主要参数的监测、技术控制指标、注意事项、问题和对策等,最后提出了几点建议和讨论的要点。
关键词:大型汽轮机 快速冷却技术 问题 对策0 前 言随着国民经济的高速发展,电网容量和单机容量迅速增长,近年来新装200M W、300MW和目前国内单机容量最大的660MW大型机组陆续投入运行。
如何提高大机组的等效可用率——研究汽轮机的快速冷却,缩短停机检修工期,已成为当前电力生产面临的迫切课题。
由于大型汽轮机参数高、热容量大和保温良好(目前已普遍地采用硅酸钙、硅酸铝等优质保温材料),这就带来了机组,尤其是汽轮机的高压缸,停机后自然冷却速度势必减慢,使计划停机检修的等待冷却时间大大增加,直接影响了检修工期的充分利用(尤其是影响了机组因故障停机临修的紧迫时间)和机组的投运率,因此,汽轮机的“快冷”具有显著的社会、经济效益。
大型汽轮机停机后冷却到可停盘车揭缸温度150℃以下,若按自然冷却,一般需要4~6天的时间,甚至更长;若实施快速冷却,一般可缩短冷却时间3~4天,甚至更多。
目前,在各种冷却方式中,压缩空气强制通风冷却法较为安全、方便,曾在蒸汽发电厂运行国际会议上被作为一种提倡的方法,已得到广泛的应用,国外先进国家对大机组亦推荐采用这一方式。
1 汽轮机几种快速冷却方式的分析比较汽轮机几种快速冷却方式可归纳为:按冷却介质分为采用蒸汽冷却和空气冷却;按介质流向分为采用顺流冷却和逆流冷却。
冷却介质采用空气较之蒸汽有如下优点:1.空气与流过的金属表面的换热系数小,当两者温差出现瞬间过大时,也不至于引起被换热的金属表面产生急剧冷却(冷冲击),即不至于使金属产生过大的热应力,则允许的传热温差大,在适当的流动条件下便能满足加速冷却的要求;2.空气的温度变化不存在气水两相互变(凝结)的特性,则不象蒸汽那样,当流过冷的供汽管道时,若过热度不足,可能会产生凝结现象,致使进入汽轮机的蒸汽带水,而出现汽轮机部件热表面受到水冲击的危险;3.空气的流量和温度的控制也较为方便;4.对停运机组能起干燥防腐作用。
汽轮机快冷系统总结
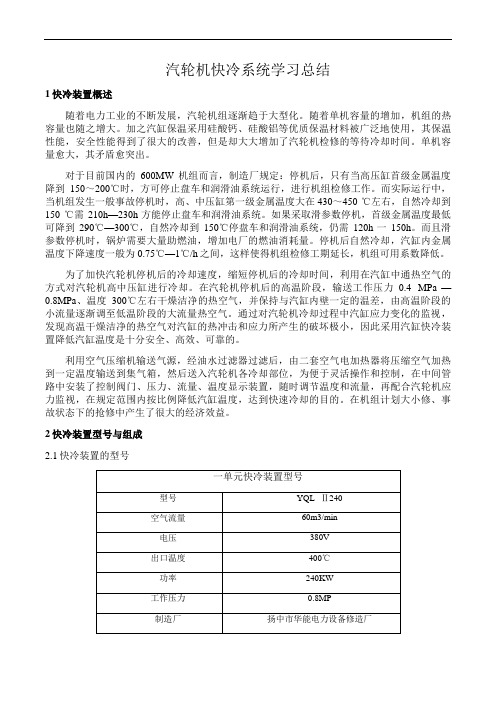
汽轮机快冷系统学习总结1快冷装置概述随着电力工业的不断发展,汽轮机组逐渐趋于大型化。
随着单机容量的增加,机组的热容量也随之增大。
加之汽缸保温采用硅酸钙、硅酸铝等优质保温材料被广泛地使用,其保温性能,安全性能得到了很大的改善,但是却大大增加了汽轮机检修的等待冷却时间。
单机容量愈大,其矛盾愈突出。
对于目前国内的600MW机组而言,制造厂规定:停机后,只有当高压缸首级金属温度降到150~200℃时,方可停止盘车和润滑油系统运行,进行机组检修工作。
而实际运行中,当机组发生一般事故停机时,高、中压缸第一级金属温度大在430~450 ℃左右,自然冷却到150 ℃需210h—230h方能停止盘车和润滑油系统。
如果采取滑参数停机,首级金属温度最低可降到290℃—300℃,自然冷却到150℃停盘车和润滑油系统,仍需120h一150h。
而且滑参数停机时,锅炉需要大量助燃油,增加电厂的燃油消耗量。
停机后自然冷却,汽缸内金属温度下降速度一般为0.75℃—1℃/h之间,这样使得机组检修工期延长,机组可用系数降低。
为了加快汽轮机停机后的冷却速度,缩短停机后的冷却时间,利用在汽缸中通热空气的方式对汽轮机高中压缸进行冷却。
在汽轮机停机后的高温阶段,输送工作压力0.4 MPa —0.8MPa、温度300℃左右干燥洁净的热空气,并保持与汽缸内壁一定的温差,由高温阶段的小流量逐渐调至低温阶段的大流量热空气。
通过对汽轮机冷却过程中汽缸应力变化的监视,发现高温干燥洁净的热空气对汽缸的热冲击和应力所产生的破坏极小,因此采用汽缸快冷装置降低汽缸温度是十分安全、高效、可靠的。
利用空气压缩机输送气源,经油水过滤器过滤后,由二套空气电加热器将压缩空气加热到一定温度输送到集气箱,然后送入汽轮机各冷却部位,为便于灵活操作和控制,在中间管路中安装了控制阀门、压力、流量、温度显示装置,随时调节温度和流量,再配合汽轮机应力监视,在规定范围内按比例降低汽缸温度,达到快速冷却的目的。
1000mw汽轮机快速冷却的应用与分析
运行与维护118丨电力系统装备 2019.20Operation And Maintenance2019年第20期2019 No.20电力系统装备Electric Power System Equipment在提高大型汽轮机组初参数同时,停机之后自然冷却时长提升,检修时长延长,使机组可用效率受到干扰,通过强制冷却,能使冷却速率提升,并有效缩短冷却时间,可以保证机组可用率的提高。
1 自然冷却自然冷却主要就是内部换热,其为热辐射与热传导,涵盖有内缸以及外缸存在的辐射换热,包括叶片和隔板间辐射换热,囊括有转子和汽缸间辐射换热,同时包含汽缸与隔板间热传导以及转子轴承间热传导,并包括汽缸外表面同空气间热对流[1]。
如图1所示,该图是一次机组滑参数停机之后自然冷却过程,并将打闸时刻设成时间零点。
在停机时,自满负荷滑参数开始降负荷,在自然冷却的过程中,高压转子温度一定大于中压转子70℃,意味着高压转子与汽缸冷却速率直接影响机组冷却时长。
一旦需要冷却为100℃,将会耗时半个月 之久。
2 冷却方案2.1 厂家方案介绍本次研究中的机组,于高压主汽阀以及调节阀间设计快冷接口,中压主汽阀以及调节阀间同样有相同设计,空气将通过快冷接口引入,并有序进至通流结构冷却。
快冷方案关键囊括三个步骤。
首先,滑参数降负荷阶段。
在保证高排、中排蒸汽具有 20℃ 过热度的前提下,使锅炉负荷降至尽可能低,通过速率(0.5~0.7℃/min)使主、再热汽温得到下降。
图1 机组自然冷却过程其次,自然冷却阶段。
汽轮机打闸并停机,锅炉MFT 。
使主、再热蒸汽管路压力下降,同时闭合旁路与轴封系统,开启快冷接口,盘车运行12 h 。
最后,为快速冷却阶段。
闭合管道疏水,保存缸体疏水。
开启真空泵,通过控制高、中压调节阀开度,于高、中压缸之中鼓入空气,通过小于7℃/h 的冷却速率快冷。
实际方案整个过程大致为82 h ,远远短于自然冷却。
2.2 方案分析自然冷却经历12 h 之后进行快冷,这种情况下高压缸之中温度大致为400℃,而中压缸中内温度大致是300℃。
国产600MW机组汽轮机快速冷却技术的应用
国产600MW机组汽轮机快速冷却技术的应用已难以满足用户不断增长的需求。
客户越来越多地希望管理层和现场级能够使用统一的、与办公自动化技术兼容的通信解决方案。
基于这种需求,以太网技术开始逐渐从工厂和企业信息管理层向底层渗透,广泛应用于工厂控制级通信。
从目前工业自动化控制领域情况来看,以太网技术取代现场总线是工业控制发展的必然趋势。
不过以太网技术在工厂控制系统中的应用并不是一个简单的移植过程,既要保持普通以太网技术的优势,又须解决工业现场应用中的一些问题,如实时性、运动控制、故障安全和网络安全等,同时还需兼容现有工业以太网和现场总线通信系统。
PROFInet很好地解决了以太网技术向底层扩展的问题,实现了工厂通信系统的纵向统一。
大理卷烟厂打叶复烤线电气控制系统除在设备控制层应用了Profibus DP/PA总线技术外,在ET200分布式I/O间使用了PROFInet I/O通信,在各生产段PLC之间使用了PROFInet CBA 进行通信。
而在车间主干网络(即光纤环网),除充分应用西门子SCALANCE工业交换设备的冗余功能外,还应用了VLAN、第三层交换等以太网技术,以满足复杂的车间网络环境及大量的客户端网络IP 和数据流量的管理需求。
以上PROFInet技术方案在打叶复烤生产线设计并调试成功,目前在大理卷烟厂打叶复烤车间运行良好并获得用户好评。
借助于实时通信技术,PROFInet可直接应用于底层的现场级通信(包括运动控制),由此也实现了全厂通信网络的纵向统一,管理层可方便地将现场生产数据集成到企业信息处理系统中,为MES和ERP系统的应用打下基础;基于组件的自动化(CBA)将自动化系统的构建简化为不同功能工艺模块间的连接,大大降低了系统构建成本;IT标准和网络安全使用户在现场通信网络中放心享受IT技术带来的便利;集成的故障安全功能保证了系统可靠性,为PROFInet在过程自动化领域中的应用奠定了良好基础。
汽轮机快冷系统的运行
3.17 汽轮机快冷系统的运行3.17.1概述汽轮机强制冷却装置是一种适合各汽轮机停机时强行加快冷却设备,它借助于常用压缩空气经本装置的滤清除水、加热至一定温度(即干燥空气)后,经管道输入汽缸体中,对汽缸及通流部份包括高中压转子进行强制冷却,以缩短汽轮机停机冷却时间,如果采用自然冷却,一般需要五至七天,采用汽轮机强制冷却装置只需二天左右,对于停机检修(特别是事故停机)争取了时间,为停机后早日恢复发电创造条件。
压缩空气通过过滤器进入气、油、水分离器,净化后进入加热器,根据罐壁温度要求,净化空气加热成干燥热空气—俗称冷却空气,然后进入分气箱,分气箱作为储存、混温、配气之用再经加热空气出口,(此出口的个数根据汽轮机冷却需要确定)分别导入高压缸及中压缸中,连通阀做调配流量用。
3.17.2汽轮机快冷系统投入条件3.17.2.1机组润滑油系统、顶轴油系统、盘车运行正常。
3.17.2.2汽机调节级缸温降至320℃以下时。
3.17.2.3压缩空气压力0.6~0.8MPa。
3.17.2.4汽缸冷却速度8~10℃/h。
3.17.3装置主要不见的质量标准及参数3.17.3.1油、气、水分分离器,电加热器壳体及分气管按钢制压力容器GB150—89、GB151—89设计。
工作压力:0.8MPa。
工作温度:<350℃(工作温度可根据用户要求另行设计)。
容积:20mm3/min×2。
3.17.3.2电加热器按JB-2379电热元件使用时间在7000h以上。
3.17.3.3出口空气质量等级根据GB/T1327791及ISO/DP8573/1-88为243。
3.17.3.4控制柜由温控系统与电动阀门控制系统所组成,温控系统采用最新线路设计,其特点简单、可靠、柜内工作温度低,从而保证了可控硅及加热器的正常使用。
环境温度:<70℃。
相对湿度:<85%。
电源电压:380V±10% 50Hz(三相四线制)。
3.17.4 汽轮机快冷系统投入前的检查准备工作3.17.4.1 检查确认该系统检修/安装工作已结束,工作票已终结,无关人员撤离现场,按系统阀门检查卡进行全面检查,确认各阀门状态正确。
汽轮机快冷系统讲解概述.
快冷控制柜操作手册
在停机后准备投入快冷前,要把快冷装置接通电源,接好气路,匆冲管。在能够向快 冷控制柜送电后,先检查一下电源线,热电偶输出连线是否正确,控制柜元器件、螺 丝是否松动损坏,如有异常及时更换或拧紧,确认无误后可以通电试车。 1 、先合上快冷控制柜内电源空气开关,电源指示灯亮,电压表、数显调节仪均有指示,可 控硅触发仪的“POW”指示灯亮; 2 、将“就地/远程”转换开关切至就地位置; 3 、按住数显调节仪上的“PID按钮”,旋转“PID调节旋钮”进行温度设定(向右旋转增大 、向左旋转减小),数值的大小在数显调节仪有显示,这个设定值是实际需要的温度 值; 4 、按住数显调节仪上的“上限按钮”,旋转“上限调节旋钮”,设定上限温度值(向右旋 转增大、向左旋转减小),数值的大小在数显调节仪有显示,如果温度超过这个数值 会报警,超高温指示灯亮; 5 、按住数显调节仪上的“下限按钮”,旋转“下限调节旋钮”,设定下限温度值(向右旋 转增大、向左旋转减小),数值的大小在数显调节仪有显示,如果温度低于这个数值 会报警,超低温指示灯亮; 6 、将可控硅触发仪上的“手动/自动”切换开关切至“MAN”位置;可控硅触发仪上的 “MAN”指示灯亮;
系统流程
有关说明
最新快冷操作说明-电气部分(修改) ZQK-1型汽轮机快冷装置控温柜操作说明 快冷控制柜操作手册
CL系列汽轮机快速冷却装置
最新快冷操作说明-电气部分(修改)
一、投运快冷前的调试准备工作及步骤: 1.确认快冷装置已安装正常。 2.将调压器调至最小值。(使用ZK-3X调压器,将旋钮逆时针调至最小。) 3.快冷装置电源、气源送上。 4.关闭高中压缸所有快冷进气门,打开快冷排空暖管阀门。 5.打开快冷装置控制柜,合上空气开关,按下控制柜面板上“电源开”按钮(绿 色) 。 6.检查确认电路接触及绝缘状况正常。在控制柜面板上按下电磁阀或电动门的“ 阀门开”按钮(绿色)。 7.打开油水分离器下面的排污阀,打开集气联箱底部疏水门。顺时针打开快冷加 热器进气蝶阀至全开。 8.微开压缩空气进气闸阀,并缓缓打开该阀。
- 1、下载文档前请自行甄别文档内容的完整性,平台不提供额外的编辑、内容补充、找答案等附加服务。
- 2、"仅部分预览"的文档,不可在线预览部分如存在完整性等问题,可反馈申请退款(可完整预览的文档不适用该条件!)。
- 3、如文档侵犯您的权益,请联系客服反馈,我们会尽快为您处理(人工客服工作时间:9:00-18:30)。
汽轮机快冷系统学习总结1快冷装置概述随着电力工业的不断发展,汽轮机组逐渐趋于大型化。
随着单机容量的增加,机组的热容量也随之增大。
加之汽缸保温采用硅酸钙、硅酸铝等优质保温材料被广泛地使用,其保温性能,安全性能得到了很大的改善,但是却大大增加了汽轮机检修的等待冷却时间。
单机容量愈大,其矛盾愈突出。
对于目前国内的600MW机组而言,制造厂规定:停机后,只有当高压缸首级金属温度降到150~200℃时,方可停止盘车和润滑油系统运行,进行机组检修工作。
而实际运行中,当机组发生一般事故停机时,高、中压缸第一级金属温度大在430~450 ℃左右,自然冷却到150 ℃需210h—230h方能停止盘车和润滑油系统。
如果采取滑参数停机,首级金属温度最低可降到290℃—300℃,自然冷却到150℃停盘车和润滑油系统,仍需120h一150h。
而且滑参数停机时,锅炉需要大量助燃油,增加电厂的燃油消耗量。
停机后自然冷却,汽缸内金属温度下降速度一般为0.75℃—1℃/h之间,这样使得机组检修工期延长,机组可用系数降低。
为了加快汽轮机停机后的冷却速度,缩短停机后的冷却时间,利用在汽缸中通热空气的方式对汽轮机高中压缸进行冷却。
在汽轮机停机后的高温阶段,输送工作压力0.4 MPa —0.8MPa、温度300℃左右干燥洁净的热空气,并保持与汽缸内壁一定的温差,由高温阶段的小流量逐渐调至低温阶段的大流量热空气。
通过对汽轮机冷却过程中汽缸应力变化的监视,发现高温干燥洁净的热空气对汽缸的热冲击和应力所产生的破坏极小,因此采用汽缸快冷装置降低汽缸温度是十分安全、高效、可靠的。
利用空气压缩机输送气源,经油水过滤器过滤后,由二套空气电加热器将压缩空气加热到一定温度输送到集气箱,然后送入汽轮机各冷却部位,为便于灵活操作和控制,在中间管路中安装了控制阀门、压力、流量、温度显示装置,随时调节温度和流量,再配合汽轮机应力监视,在规定范围内按比例降低汽缸温度,达到快速冷却的目的。
在机组计划大小修、事故状态下的抢修中产生了很大的经济效益。
2快冷装置型号与组成2.1快冷装置的型号图1快冷装置系统图快速冷却装置有进汽电磁阀、气液分离器、电加热器、截止阀、压力表、流量计、控制柜、测温元件、集气箱等组成。
其中快冷装置控制柜是整个装置的核心部分,用来控制压缩空气加热的温度和速度。
整个系统利用检修空压机输送气源,经油水过滤器过滤后,由两套空气电加热器将压缩空气加热到一定温度输送到集气箱,然后送入汽轮机高、中压缸进行冷却。
为了便于灵活操作和控制,在中间管路中安装了控制阀门,压力、流量、温度显示装置,可随时调节温度和流量,及汽轮机的应力监视,在规定范围内按比例降低汽缸温度,达到快速冷却的目的。
3快冷装置的原理定电公司快冷控温柜的工作原理是采用XMT数字温度调节仪、集成电路触发器、大功率可控硅和热电偶组成测量、调节、控制回路。
利用测量热电偶将加热器出口温度转换成毫安信号,送给XMT数字温度调节仪进行放大、比较后,显示相应温度值,同时输出0~10 mA电流,送给ZK—3可控硅电压调节器。
当显示值高于设定值时,XMT输出为0 mA 电流。
当显示值低于设定值时,XMT输出为10 mA电流,当显示值与设定值相接近时(即输入设定值附近),XMT输出电流按P、I、D规律变化,使控温柜具有良好的控制精度和调节性能。
ZK—3可控硅电压调节器根据XMT温度调节器送来的0~10 mA电流信号,自动改变可控硅的触发脉冲数量,即控制可控硅在单位时间内的导通角度,调节电压控制加热元件的加热功率,达到均匀控制温度的目的。
4.1投入条件•尽量采用滑参数停机方式,一般待高压缸第一级金属温度和中压持环温度降至350℃-380℃以下时,方可投入快冷装置。
•机组打闸停机后,盘车装置投入连续运行,大轴偏心度小于0.076mm。
•高、中、低压缸金属温度、胀差、汽缸膨胀、轴向位移表指示准确。
•停运真空泵、停运主机轴封供汽系统,开启真空破坏门。
•保留一台循环水泵运行,一台凝结水泵运行,低压缸喷水减温投入。
•关闭所有高低压本体疏水一、二次门。
•确认高排逆止阀关闭,高排逆止阀前疏水开启,开启高排通风阀。
•低压缸人孔门开启。
•隔绝小机与主机的系统联系。
•检查供快冷气源的空压机工作正常。
4.2快冷装置的投入•检查机组滑参数停运,高压缸调节级金属温度和中压持环金属温度降至350℃以下•检查汽轮发电机组盘车连续运行,盘车电流正常•检查汽轮机大轴偏心度小于0.076mm•检查高、中、低压缸金属温度、胀差、汽缸膨胀、轴向位移指示准确,参数正常•检查保留一台循环泵运行•检查凝结泵运行•检查低压缸喷水减温投入•检查1、2、3号真空泵全部停运•检查主机轴封系统已停运•检查1、2号真空破坏门开启,凝汽器真空到0•检查关闭所有高低压本体疏水一、二次门•确认高排逆止门关闭,开启高排逆止门前疏水门•检查小机与主机的系统联系已隔绝•联系检修开启高排通风阀•联系检修开启低压缸人孔门•检查检修用空压机运行正常,检修压缩空气压力正常•检查检修压缩空气系统与仪用压缩空气系统可靠隔离•可以将脱硫空压机储气罐与检修空压机储气罐并列,注意系统不超压•快冷装置电加热器测绝缘合格,快冷装置电缆测绝缘合格送电•检查汽轮机快冷联箱至高中压缸快冷供气手动门关闭严密•开启汽轮机快冷联箱疏水手动门•检查快冷装置并联阀门关闭•检查快冷装置串联阀门开启•关闭快冷装置集气箱出口至汽轮机阀门•开启快冷装置集气箱排空门•开启快冷装置进汽管路及集气箱疏水门•开启快冷装置进汽手动门,注意检修压缩空气系统压力下降幅度•开启快冷装置钥匙开关•将快冷装置手动、自动调节器调至最低•启动快冷装置控制按钮•根据缸温情况逐渐调整快冷装置的设定温度、报警温度•投入快冷装置温度自动调节•关闭快冷装置进气管路疏水门•检查汽轮机快冷进气联箱疏水门开启•开启快冷集气联箱供气手动总门•开启快冷集气联箱至高压缸供气手动总门•开启快冷集气联箱至中压缸供气手动总门•开启快冷装置至机组供气手动门•适当关小快冷装置排空门进行暖管•测量汽轮机快冷进气联箱疏水门判断暖管效果•快冷装置集汽箱疏水门保持微开,其余各点疏水门关闭•检查压缩空气温度与高压缸调节级金属温度差小于50℃•根据需要投入高压缸快冷时开启快冷进气联箱至高压缸供气门•检查压缩空气温度与中压持环金属温度差小于50℃•根据需要投入中压缸快冷时开启快冷进气联箱至中压缸供气门•暖管结束后关闭汽轮机快冷进气联箱疏水门•全关快冷装置排空门•注意监视检查高、中压缸进汽区金属温度,并根据此温度调整快冷速度•高压缸第一级金属温度300-350℃,温降率应小于5℃/h,进汽与金属温度温差小于50℃•高压缸第一级金属温度200-300℃,温降率应小于8℃/h,进汽与金属温度温差小于80℃•高压缸第一级金属温度150-200℃,温降率应小于10℃/h,进汽与金属温度温差小于100℃•高压缸调节级金属温度和中压持环金属温度降至200℃以下时,可增大通风量,加热器改为并联运行图2快冷装置外观图3快冷装置进线刀闸4.3快冷装置投运后的控制1 开始送气时小温差,小流量,然后逐步增大流量。
汽轮机快冷装置实现了温降过程中的变流量冷却。
汽缸高温阶段流量温度选择应为高温小流量(400℃/5-10m3/min),汽缸低温阶段流量温度选择应为低温大流量(100-200℃/15-60m3/min)。
2 进入汽缸的空气温度与金属温度之差不许超过100℃.3 快速冷却空气温降小于6℃/h。
4 在整个冷却过程中严格控制各指标在规定范围内,高压缸第一级金属温度300-400℃,温降率应小于5℃/h,进汽与金属温度温差小于50℃;高压缸第一级金属温度200-300℃,温降率应小于8℃/h,进汽与金属温度温差小于80℃;高压缸第一级金属温度150-200℃,温降率应小于10℃/h,进汽与金属温度温差小于100℃。
5 如高低胀差达到报警值,上下缸温差大于42℃或蒸汽室内外壁金属温差大于83℃时,应减少快速冷却空气量,控制汽缸的温降速度或停止快速冷却。
6 严格控制汽缸进气温度和通风量,空气加热器出口温度应平稳降低,无突跳现象,否则停止快速冷却。
7 一旦压缩空气中断,立即停止加热器运行,关闭高中压缸供气门。
8 如空气加热器失电,不能控制空气温度时,立即关闭集气箱出口门,停止快速冷却,防止向汽缸内送冷空气。
图4快冷装置温度控制柜图5冷却气源通向高中压缸手门4.4快冷装置的退出1 检查高压缸第一级金属温度小于120℃,检查中压持环金属温度小于 120℃。
2 关闭至高压缸快冷各供气分门(4个)。
3 开启快冷装置排空门。
4 关闭至中压缸快冷各供气分门(4个)。
5 关闭至高、中压缸供气总门。
6 将控制柜上ZK—3可控硅电压调节器自动调节切至手动调节,然后调至最小。
7 按下控制柜上停止按钮,停止快冷装置加热器运行。
8 关闭压缩空气进气门,注意检修压缩空气系统压力不超压。
9 关闭快冷装置排空门。
10检查关闭快冷装置所有疏水门。
11拉开快冷控制柜进线刀闸,将快冷装置停电。
12联系检修关闭高排通风阀,恢复低压缸人孔门。
5快冷装置操作的注意事项1.当汽轮机停机后需进行强制冷却时,首先应对强冷系统进行充分吹扫,排尽系统管道内的积水,吹去其污垢。
2.投入电加热器,调节出口气温,对系统进行暖管。
3.汽轮机停机后10~12小时,汽缸内疏水充分排尽后,短接热工信号强制关闭高中压缸本体及导汽管和1、3级抽汽管道抽汽截阀前气动疏水阀,其目的是防止压缩空气短路。
4.待系统暖管充分,分气箱内压缩空气温度和汽缸内首级金属温度之差小于150℃时,可分别打开各分路隔离阀,关闭气暖管排气阀,开始通气冷却。
5.在冷却过程中,确保有关辅助系统运行正常(主要包括润滑油系统、顶轴油系统、盘车装置、低缸喷水系统、循环水系统等)。
以上任一系统退出运行,应马上停止汽轮机快速冷却,直到系统恢复运行后继续进行。
6.在快速冷却过程中,同时加强对厂用压缩空气系统工况监视,定期对汽水分离器,分气箱,空压机储气罐进行放水,清理过滤器。
一旦发现压缩空气中断,立即切断电加热装置电源。
7.当汽轮机首级金属温度下降到130℃左右时,可停止快速冷却,打开前面所强制关闭的所有疏水阀,此时缸温将有10~20℃的反弹。
8.再盘车12小时左右,确认气缸内金属温度停止反弹,开始平稳下降,各项参数均正常,可停止盘车机润滑油系统运行,许可检修工作。
9.快速冷却投入前,汽轮机高、中压缸应充分排尽疏水,并全面隔离。
防止因疏水排放不尽或系统隔离不严,而使冷气、冷水进入汽缸,出现局部温差过大,温降率过大的现象。
10.只有压缩空气压力正常、流量正常,方可投入空气加热装置,在空气加热装置温度符合要求后才能向汽轮机送汽。