工厂出货检验流程图及工作细则
公司工厂流程成品检验工作流程
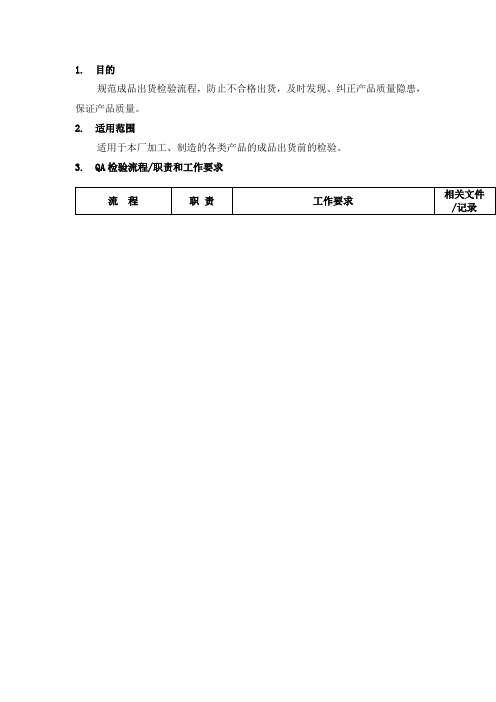
1. 目的
规范成品出货检验流程,防止不合格出货,及时发现、纠正产品质量隐患,保证产品质量。
2. 适用范围
适用于本厂加工、制造的各类产品的成品出货前的检验。
3. QA检验流程/职责和工作要求
本文档可编辑,内容仅供参考,需要结合您的实际情况进行修改调整。
编辑技巧:
ctrl+z是office软件撤回的操作,但是一般计算机默认只可以撤几步就不能撤了,这时我们可以通过设置word选项-高级,来设置可取消操作数即可
编辑文档时如果想要快速插入时间可以按shift+alt+d,时间显示的方式以天为单位,比如2018/3/22,按着shift+alt+t,时间显示以当天分钟为单位:08:31。
出货全检操作规程(3篇)

第1篇一、目的为确保产品质量,防止不合格产品流出,本规程规定了出货全检的操作流程和注意事项,旨在规范全检作业,提高产品质量和客户满意度。
二、适用范围本规程适用于公司所有出货产品的全检工作。
三、职责1. 品质管理部门:负责制定全检标准、监督全检过程、确保全检质量。
2. 生产部门:负责提供符合全检标准的产品,协助品质管理部门进行全检。
3. 检验员:负责具体执行全检操作,确保全检结果的准确性。
四、全检流程1. 准备阶段- 检验员根据产品规格、检验标准及检验计划,准备好检验工具、设备、记录表格等。
- 生产部门提供符合全检标准的产品,并确保产品标识清晰。
2. 检验阶段- 检验员按照检验标准,对产品进行全面检查,包括外观、尺寸、性能等方面。
- 检验过程中,发现不合格产品,立即记录不合格原因,并通知生产部门进行处理。
- 检验员对每项检验项目进行详细记录,包括检验结果、检验时间、检验员等信息。
3. 判定阶段- 检验员根据检验结果,判定产品是否合格。
- 合格产品放行,不合格产品进行返工或返修。
4. 复检阶段- 对于返工或返修后的产品,进行复检,确保产品质量。
- 复检合格的产品方可放行。
5. 记录阶段- 检验员将检验结果记录在检验记录表上,并签名确认。
- 品质管理部门定期对检验记录进行汇总和分析,为质量改进提供依据。
五、注意事项1. 检验员应熟悉检验标准和操作流程,确保检验结果的准确性。
2. 检验过程中,应严格遵守操作规程,确保安全。
3. 对于不合格产品,应及时通知相关部门进行处理,防止不合格产品流出。
4. 定期对检验工具、设备进行校准和维护,确保其精度和可靠性。
六、附则1. 本规程由品质管理部门负责解释和修订。
2. 本规程自发布之日起实施。
通过以上规程的实施,我们将确保产品质量,为客户提供满意的产品,提升公司品牌形象。
第2篇一、目的为确保产品出厂质量,满足客户需求,降低客户投诉率,特制定本规程。
本规程适用于所有出货产品的全检工作。
成品出货检验流程图
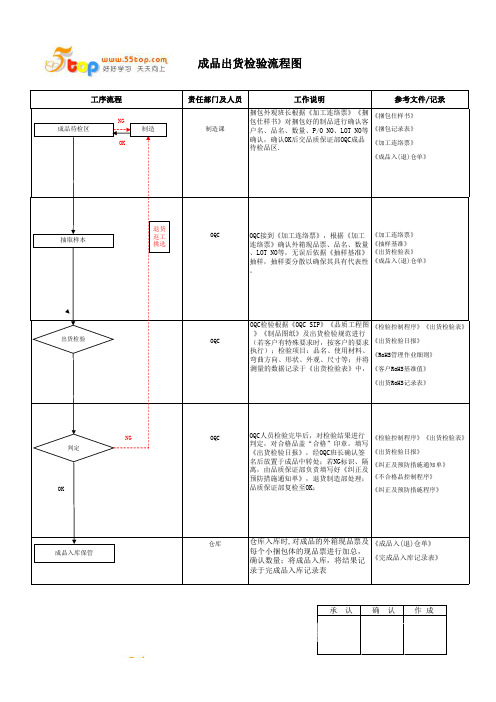
《捆包仕样书》制造课《捆包记录表》《加工连络票》《成品入(退)仓单》OQC《加工连络票》《抽样基准》《出货检验表》《成品入(退)仓单》《检验控制程序》《出货检验表》OQC《出货检验日报》《RoHS管理作业细则》《客户RoHS基准值》《出货RoHS记录表》OQC《检验控制程序》《出货检验表》《出货检验日报》《纠正及预防措施通知单》《不合格品控制程序》《纠正及预防措施程序》仓库《成品入(退)仓单》《完成品入库记录表》工作说明捆包外观班长根据《加工连络票》《捆包仕样书》对捆包好的制品进行确认客户名、品名、数量、P/O NO、LOT NO等确认,确认OK后交品质保证部OQC成品待检品区.OQC接到《加工连络票》,根据《加工连络票》确认外箱现品票、品名、数量、LOT NO等,无误后依据《抽样基准》抽样,抽样要分散以确保其具有代表性。
OQC检验根据《OQC SIP》《品质工程图》《制品图纸》及出货检验规范进行(若客户有特殊要求时,按客户的要求执行);检验项目:品名、使用材料、弯曲方向、形状、外观、尺寸等;并将测量的数据记录于《出货检验表》中,OQC人员检验完毕后,对检验结果进行判定,对合格品盖“合格”印章。
填写《出货检验日报》,经OQC班长确认签名后放置于成品中转处;若NG标识、隔离,由品质保证部负责填写好《纠正及预防措施通知单》,退货制造部处理;品质保证部复检至OK;仓库入库时,对成品的外箱现品票及每个小捆包体的现品票进行加总,确认数量;将成品入库,将结果记录于完成品入库记录表参考文件/记录成品出货检验流程图工序流程责任部门及人员NG退货返工挑选成品待检区成品入库保管NGOK承认确认作成出货检验抽取样本判定OK制造。
工厂出货检验流程图及工作细则

流程责任部门工作内容
相关文件/表单商务部
商务部、仓库仓库OQC 检验员OQC 检验员
OQC 检验员仓库保安
1、商务部根据出货计划安排,在OA 上
公布具体出货明细。
2、商务制定《发货单》,并督促销售和财务审核,由仓库打印、仓管员签名确认。
仓管员确认单据明细无误后,由仓库账务员做销售出库单,将帐调出仓库,打印《销售出库单》并由仓管员和OQC 共同签名确认。
3、仓库依据发货通知单上的产品型号、规格、数量进行备货。
4、OQC 根据《发货单》,按《组件出货检查表》进行检验检查。
5、OQC 检验完毕,填写《组件出货检查表》进行检验检查。
6、OQC 检验合格,在发货单上签名(须签全名,不允许只签姓名或者一个字、或字迹潦草—详见范本一);如发现不符合项,处理流程参见《不合格品控制
程序》。
7、仓管员在得到OQC 检验员确认货物
合格之后,尽快装箱发货,不得以各种
理由推迟发货。
8、该批产品在厂门检查,保安人员须
确认《发货单》上具备可识别的OQC 人员的签名,否则不得放行出货。
《发货单》《销售出库单》《组件出货检查表》、《唛头打印规范》、《组件成品检验标准》《不合格品控制程序》、《HOLD
单》、
《重工作业程序》、《重工单》各种表单需经相关部门领导审批后方可生效。
结束
保安确认
仓库出货
仓库备货
OQC 检验
检验结果
出货通知
开始
填写检验表
订单审核。
出货检验规范

出货检验规范建立出货检查控制程序 ,为确保产品出厂前进行最终检验和测试,判定产品品质符合顾客要求,防止不合格品流出。
一、职责1)品质部负责产品出货前检验的执行与结果记录,负责所有技术要求的相关检验记录。
2)研发工程部负责检验项目及参数值的确定。
3)营销部负责产品出货前的检验通知。
4)仓库负责产品出货检验工作的配合。
5)生产部负责对不合格产品进行返工返修及按需要执行纠正措施。
二、检验控制流程1)产品入库前/出货检验实施:①生产部装配车间完成装配后首先进行内部自检、互检、复检,确认合格后填写《内部报检单》向品质部报检。
(报检单内容应清楚反映:机型、名称、报检数量、装配员工自检签名、复检人员签名、具体报检时间)②品质部接到生产部装配车间《内部报检单》后,首先确认报检的机型、数量与销售部出货通知单相符。
③品质部确定了生产部报检信息与出货信息一致后对出货产品进行检验。
④品质部应重点对机器的结构、功能、系统等按照标准文件设定参数进行测试。
⑤在检验过程中发现不良问题较多而且超过 3个低级问题时,检验员无须再检验可以直接向生产部车间主管提出拒检,同时做好不良标识待处理。
⑥品质部拒绝检验已作好不良标识后要及时向生产主管反馈不良信息,由生产部装配主管或生产工艺人员找到异常问题机器的装配者要求立即返工并对机器重新检验,直到自检合检后再次向品质报检。
⑦品质部接到生产部装配车间二次报检后,应重点对返工的部位进行检验,同时按照系统出厂参数设定值进行调试确保合格,最后将检验结果记录于《产品检验报告》中。
⑧二次检验合格下架后,品质部还要根据客户远近评估包装方式并对包装要求进行监控,一定要满足在运输过程中对机器造成损坏因素的预防效果。
⑨最后检查包装所使用的包装是否符合规格要求,是否有破损,出货标贴或警示标识是否醒目等,所有工作完成后方可出货。
⑩最后品质部还得跟装车过程,监督在装车过程中防止造成损坏。
2)库存品出货检验实施:①仓库接到销售部出货通知后通知生产部,要求安排员工将要出货的产品重新提交待检验区,挂上“待检”牌待检,同时并向品质部报检。
品质部出货检验流程图
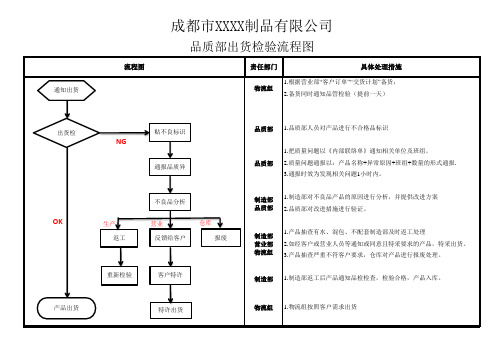
品质部制造部 1.物流组按照客户需求出货物流组制造部
营业部
物流组 3.通报时效为发现相关问题1小时内。
1.制造部对不良品产品的原因进行分析,并提供改进方案
2.品质部对改进措施进行验证。
1.产品抽查有水、混包、不配套制造部及时返工处理品质部制造部
品质部品质部出货检验流程图
成都市XXXX制品有限公司
3.产品抽查严重不符客户要求,仓库对产品进行报废处理。
2.如经客户或营业人员等通知或同意且特采要求的产品,特采出货。
1.制造部返工后产品通知品检检查,检验合格,产品入库。
具体处理措施1.根据营业部“客户订单”“交货计划”备货;
2.备货同时通知品管检验(提前一天)1.品质部人员对产品进行不合格品标识
1.把质量问题以《内部联络单》通知相关单位及班组。
2.质量问题通报以:产品名称+异常原因+班组+数量的形式通报.
物流组流程图责任部门
通知出货
出货检产品出货贴不良标识返工
重新检验通报品质异不良品分析反馈给客户客户特许特许出货报废生产营业
仓库OK NG。
成品出货检验工作标准流程
已投产机返工,生产再重送首件
首件检验合格,OQC通知生产线组长在《首件确认表》上签字确认后,生产部批量生产
首件检验合格,OQC批量抽检
根据产品检验标准、规范,《产品检验抽样规定》,设计文件,批量抽检
记录抽检的每台机流水号
首批检验合格机抽一箱做整箱落地试验
首批检验合格机(配有电源的产品)抽一箱做24小时煲机试验
OQC组长
检验员
作业员
OQC组长/领班
QE/PIE
OQC
PIE
批量抽检合格,组长在《OQC检验报告》签字确认
合格话机在生产部产成品送检单上盖蓝色QA PASS章,外箱贴绿色QA合格证贴纸,客户产品盖蓝色QA PASS章,
记录每一订单箱号范围、流水号范围、物流码范围
生产线封箱,OQC监督,外箱底部贴白色封箱签
客户产品批量合格后,OQC填写送检单通知客户验货
客户、QE、PIE对机,
OQC转发客户验货报告
工程发出《坏机分析报告》和《返工报告》
计划安排返工,返工后再重新送检
客户验货合格,OQC检验员核对卡板数量在生产部产成品送检单上注明客户检验合格
生产线将合格产品入成品仓
送检单
客户验货报告
《坏机分析报1.目的规范成品出货检验流程,防止不合格出货,及时发现、纠正产品质量隐患,保证产品质量。
2.适用范围适用于本厂加工、制造的各类产品的成品出货前的检验。
3.QA检验流程/职责和工作要求
流程
职责
工作要求
相关文件
/记录
首件检验
生产
生产
检验员
OQC组长
QE
PIE/OQC组长/PQC组长
成品出货检验流程
在成品出货的过程中进行检验,保证送到客户手中的产品没有不合格品。
出货检验的流程如下:
一、提前通知
1、仓管员根据成品的库存情况,提前三天以上填单通知品管部(化验室)
对本批成品进行检验。
2、库存若超过三个月以上的产品应立即填单通知品管部(化验室)对本
批产品进行检验。
二、检验准备
检验人员针对检验产品,准备好相应的资料、样品,提前半小时通知仓管员进行检验准备。
三、产品品质检验的内容
检验人员根据产品的规格及数量,确定抽样计划,对出货产品品质进行检验,检验内容包括:
1、外观检查、净含量检测
2、物理特性及化学特性
3、产品抗冲击能力
4、检查产品包装和标识
5、微生物的检测
四、结果判定
检验人员根据产品品质标准判定抽检情况填写“品质抽检报告”,合格的直接盖章有效。
反之抽检中出现不合格品的数量,则直接交品管确定不合格品处理意见。
仓管员不得擅自移动此类产品。
五、产品的补救和返工、返修、报废
品管部根据检验结果,确定送检产品的情况,并书面通知制造单位进行补救、返工、返修、报废。
六进行验货记录
检验人员在完成所有检验后,及时填写“成品出货检验报告”交主管签批后存档。
工厂出货验货流程以及标准
工厂出货验货流程以及标准下载温馨提示:该文档是我店铺精心编制而成,希望大家下载以后,能够帮助大家解决实际的问题。
文档下载后可定制随意修改,请根据实际需要进行相应的调整和使用,谢谢!并且,本店铺为大家提供各种各样类型的实用资料,如教育随笔、日记赏析、句子摘抄、古诗大全、经典美文、话题作文、工作总结、词语解析、文案摘录、其他资料等等,如想了解不同资料格式和写法,敬请关注!Download tips: This document is carefully compiled by theeditor. I hope that after you download them,they can help yousolve practical problems. The document can be customized andmodified after downloading,please adjust and use it according toactual needs, thank you!In addition, our shop provides you with various types ofpractical materials,such as educational essays, diaryappreciation,sentence excerpts,ancient poems,classic articles,topic composition,work summary,word parsing,copy excerpts,other materials and so on,want to know different data formats andwriting methods,please pay attention!一、工厂出货验货流程1. 验货准备(1)查阅订单、生产计划、生产进度表等,确认出货产品名称、型号、规格、数量等信息。
工厂出货检验流程
工厂出货检验流程
一、审核工厂信息
1.检查准备出货的厂家产品是否符合合同要求;
2.检查厂家生产能力是否可以满足订单的安排;
3.检查厂家有无专业技术设备及质量保证体系;
4.工厂的管理程序是否有质量保证体系,其质量体系的贯彻程度是否符合要求;
5.厂家是否具有合法的营业执照、税务登记证件和专业证件;
6.工厂有无良好的质量控制和质量体系;
7.厂家是否在业内具有良好的信誉,是否有近期正规的合同;
二、工厂出货检验
1.进行质量检验抽查,确认产品外观完好、尺寸正确;
2.检查搭配配件是否符合要求,数量是否正确;
3.对外观细节如颜色、烙字、标识等进行检查;
4.进行随机拆卸检查,检查内件及件的接触性;
5.进行功能测试,确定产品的质量指标;
6.对产品的包装进行检查,保证产品的完整性;
7.检查出货的产品是否符合客户的要求;
三、产品出厂
1.进行最终检验,确保产品完全符合质量规定;
2.将合格的产品按照订单要求进行打包和标识;
3.按照出厂条件,将产品组装到箱子中;
4.按照要求,将包装好的产品进行发货;
5.将出厂记录的信息更新到财务凭证中;。
- 1、下载文档前请自行甄别文档内容的完整性,平台不提供额外的编辑、内容补充、找答案等附加服务。
- 2、"仅部分预览"的文档,不可在线预览部分如存在完整性等问题,可反馈申请退款(可完整预览的文档不适用该条件!)。
- 3、如文档侵犯您的权益,请联系客服反馈,我们会尽快为您处理(人工客服工作时间:9:00-18:30)。
4、OQC根据《发货单》,按《组件出货检查表》进行检验检查。
5、OQC检验完毕,填写《组件出货检查表》进行检验检查。
6、OQC检验合格,在发货单上签名(须签全名,不允许只签姓名或者一个字、或字迹潦草—详见范本一);如发现不符合项,处理流程参见《不合格品控制程序》。
各种表单需经相关部门领导审批后方可生效。
7、仓管员在得到OQC检验员确认货物合格之后,尽快装箱发货,不得以各种理由推迟发货。
8、该批产品在厂门检查,保安人员须确认《发货单》上具备可识别的OQC人员的签名,否则不得放行出货。
《发货单》
《销售出库单》
《组件出货检查表》、《唛头打印规范》、《组件成品检验标准》
《不合格品控制程序》、《HOLD单》、《重工作业程序》、《重工单》
流程
责任部门
工作内容
相关文件/表单
商务部
商务部、仓库
仓库
OQC检பைடு நூலகம்员
OQC检验员
OQC检验员
仓库
保安
1、商务部根据出货计划安排,在OA上公布具体出货明细。
2、商务制定《发货单》,并督促销售和财务审核,由仓库打印、仓管员签名确认。仓管员确认单据明细无误后,由仓库账务员做销售出库单,将帐调出仓库,打印《销售出库单》并由仓管员和OQC共同签名确认。