结构胶和结构泡沫改善碰撞性能的可行技术
结构胶和结构泡沫——改善碰撞性能的可行技术

结构胶和结构泡沫——改善碰撞性能的可行技术Kyle Royston;Martin Hornung;Micheal Hajj;Jingfen ZHANG【摘要】为了新能源车的整车轻量化并保证其安全性,Henkel公司完成了两项新技术--结构泡沫和结构胶.该文测量了该组材料的物理、化学特性,以便实际应用和提高整车性能.结果表明:一种结构泡沫具有质量轻、强度和刚度高的优点,应用该种泡沫可减轻车辆自重,节省成本.在碰撞情况下提高车辆骨架对能量的吸收;另一种结构胶可提供有效连接方式,优化连接处应力分布,提高结构整体的强度和刚度,防止不同金属材料之间的电腐蚀,从而也降低生产成本.许多汽车生产商已经将该两项技术用于整车生产线上.【期刊名称】《汽车安全与节能学报》【年(卷),期】2010(001)004【总页数】7页(P313-319)【关键词】汽车安全性;轻量化结构;结构泡沫;结构胶;吸能【作者】Kyle Royston;Martin Hornung;Micheal Hajj;Jingfen ZHANG【作者单位】Henkel Japan,27-7 Shin Isogo-cho,Isogo-ku,Yokohama,235-0017,日本国;Henkel Japan,27-7 Shin Isogo-cho,Isogo-ku,Yokohama,235-0017,日本国;Henkel Japan,27-7 Shin Isogo-cho,Isogo-ku,Yokohama,235-0017,日本国;Henkel Japan,27-7 Shin Isogo-cho,Isogo-ku,Yokohama,235-0017,日本国【正文语种】中文【中图分类】U491.6A second consequence of added mass arises from consumers demand for continued or improved driving dynamics, a more powerful or larger engine must be used. A common side effect of increased engine power is increased fuel consumption. Remarkably, engine designers have been largely up to the task of creating ever more fuel ef ficient engines, techniques employed have included electronic fuel injection, variable valve timing, improved turbo charger designs, direct injection and hybrid propulsion systems. The overriding goal though is to have the best of both, a low mass vehicle structure meeting all safety expectations and a fuel ef ficient powertrain.Manufactures have explored new processing techniques and materials to increase vehicle safety while at the same time minimizing the mass of the vehicle. Taylor welded blanks allow utilizing two or more different thicknesses of steel in the same structural stamping, with the goal of placing additional steel only where it is needed. The hydroforming process, forming tubes by harnessing the force of internal fluid pressure, allows manufacturers to utilize complex variable sections and take advantage of stain hardening. Meanwhile alternative material utilization is also increasing, Ultra high strength steel (UHSS) and Advanced high strength steel (AHSS) combined are the most common of these materials. However alternative metals such have aluminum and magnesium are also becoming more prevalent. Utilizing these materials presents their own unique challenges however. AHSS is still somewhat dif ficult to acquire in Chinaand comes with a high cost of processing and initial capital investment. The use of aluminum and magnesium is problematic due to material cost as well as joining and galvanic corrosion dif ficulties.Figure 1: Data from Frost & Sullivan shows an ongoing trend in the automotive industry toward advanced steels and alternative materials as a means to reduced vehicle weight. Henkel chemical based products, structural adhesive and structural foam offer new tools to the automotive body engineer. These products help improve the ef ficiency of the metal structure and at the same time promote the use of multimetal assemblies. Structural adhesive and structural foam are both generally applied in the body shop. Structural adhesive is applied along the flange lines as a liquid prior to welding the sections together. Structural foam on the other hand is a solid part either a pressure sensitive tacky sheet cut to shape or a designed three dimensional part that can be welded, pinned or clipped into the assembly. Both materials then react in the elevated temperatures of the paint shop ovens, the adhesive cross links and forms a tough bond between the two adjacent panels. Whereas the Terocore expands bridging a necessary gap in assembly before cross linking and bonding to mating surfaces of the vehicle structure.The primary purpose of both structural adhesive and structural foam is to improve the ef ficiency of the vehicle structure. A typical automotive section or assembly is composed of several components, usually steel stampings joined by the use of spot welding. As the structure is loaded the spot welded joint is responsible for holding these componentstogether and transferring energy from one component to the next. The stress however is concentrated around the point of contact the spot weld, creating an uneven stress distribution along the flange. Structural adhesive aims to improve the ef ficiency of this joint, as illustrated in Figure 2A, by utilizing the entire flange surface area to distribute stress, thereby prolonging joint failure. In very similar fashion point loading or geometrical changes in the section necessitated by vehicle design, including holes, bends and joints create stress concentrations in the section components. Structural foam can be deployed locally in these locations, shown in Figure 2B, to transfer energy between the components to improve the ef ficiency of the larger open section.Figure 2: a) Increased energy absorption of lap shear test specimen by combination of spot welding and adhesive bonding [5] and b) elimination of local buckling due to broadening of the deformation area [6]Using structural adhesive to improve the joint ef ficency, can be further illustrated by observing the effects of a box beam three point bend test. Figure 3, shows a section representative of an automotive b-pillar that was impacted at a 45° angle, representative of a side impact in which both vehicles are in motion. Inspection of the test sample prepared using traditional spot welding showed a large distortion and separation of the spot weld flange. Whereas the test sample prepared with impact optimized adhesive showed no such separation. Maintaining integrity of the flange results in increased energy absorption capacity, after 160 mm of displacement the spot welded beam absorbed 1.962 kJ whereas the beamwith impact optimized adhesive showed 2.630 kJ, a signi ficant improvement. The source of this large difference was not merely the energy required to bend the adhesive, but it was primarily the result of the improved ef ficiency of the joint, which allowed the assembly to work more effectively.Figure 3: Weld flange separation and energy absorption at 130 mm de flection for box beam joined by spot welding only and joined by bonding using an impact resistant adhesive (no spot welding applied)A crash event involves one or more vehicles in motion, the kinetic energyof this motion must be absorbed by the vehicle structure in order to bring the vehicles to rest. Generally speaking it is preferable for the structural members comprising the passenger compartment to absorb this energy with little deformation. Increased deformation of this structure increases the risk of occupant injuries resulting from impacting the interior surface as it intrudes upon the passenger space. The most signi ficant result of the improved ef ficiency resulting from structural adhesive use becomes evident when comparing beam deformation at a given level of energy absorption. The energy absorption chart in Figure 4, for instance has a line drawn at 2.0 kJ of energy, the spot welded beam deforms 139 mm while beam assembled with impact resistant adhesive only deforms 102 mm. This reduction of deformation would translate to a reduction of intrusion and corresponding increase in survival space of 37 mm.Figure 4: Energy absorption and d isplacement of steel box beams under 45° impact depending on joining method: Spot welding versus bonding withstiffening adhesive (no spot welding applied) versus bonding with impact resistant adhesive (no spot welding applied)A similar study was conducted on beams utilizing Terocore structural foam. The box beam sections were prepared with a layer of Terocore structural foam applied between the outer panel and the reinforcement. Evident in Figure 5 is that the Terocore beam absorbed much more energy throughout the deformation than the standard construction beam. The increase energy absorption rate allows the Terocore beam to absorb 2.0 kJ in 60 mm less de flection than the standard construction beam a signi ficant increase in survival space.Figure 5: E nergy absorption and displacement of steel box beams under 45° impact: spot welding only versus reinforcement with structural foam plus spot weldingFigure 6: Weld flange separation and energy absorption at 130 mm de flection for box beam joined by spot welding only and joined by bonding using an impact resistant adhesive (no spot welding applied) Analagous to the adhesively bonded beams the beams using Terocore absorb more energy at a given de flection than does the traditional beam. The Terocore beam absorbed 4.03 kJ at 130 mm of de flection compared to only 1963for the standard construction beam, an increase of over two times.The improvement with Terocore demonstrated here is in line with prior experiments conducted by Mazda. In a paper entitled ‘Devel opment of a technique to strengthen body frame with structural foam’ it was shown that structural foam when applied between the inner and reinforcement ofa b-pillar increased the bending moment by more than 50%. The authors explain that the structural foam reinforcement prevents the onset of local deformation in the steel panels, allowing the assembly to maintain its shape stability and function throughout the impact event as it was designed. This concept of using Terocore as an enabling technology to improve the ef ficiency of the existing structure is further enhanced by examination of the energy absorption contribution of each component of the assembly. Figure 7 shows the energy absorbed by the components both before and after the application of Terocore. Notice that the top red sliver on the columns with Terocore, is the contribution of the Terocore itself. The Terocore absorbs less than 5% of the total energy of the bending event. If we look at the contribution of the reinforcement however, we see that it nearly doubles from the standard beam to the Terocore beam. The Terocore enables this steel reinforcement to work much more ef ficiently.Figure 7: Increase of energy absorption of reinforcement panel and eliminated local buckling by reinforcement using structural foam due to energy transfer between outer skin and reinforcement panel [6]Let’s go back now and reexamine the first set of Terocore reinforced box beams shown in Figure 6. You will notice that like the spot welded only beams, it still shows separation of the flange line. The Terocore applied between the outer and the reinforcement has increased the ef ficiency of the large open section of the beams, but has done nothing to improve the joint ef ficiency. Even with the improved section provided by structuralfoam, remaining ef ficiency can still be realized by utilizing structural adhesive in the spot welded joints.The second area where Henkel structural adhesive and structural foam helps to expand the automotive engineer’s toolbox and of fer additional methods to improve crash performance while at the same time maintaining a low mass, is by enabling the use of multi-metal assemblies.A dif ficulty which arises when utilizing multiple metals in an assembly is galvanic corrosion. Galvanic corrosion occurs when two different metals such as aluminum and steel are in contact in the presence of a corrosive substance. Electrons from the less noble material flow to the more noble metal and instigate corrosion. In order to prevent the flow of electrons from one metal to the other, one must place an insulating material in between, structural adhesive and structural foam are two such materials that are suitable for this task.Utilizing multiple metals in an assembly is especially appealing to an automotive designer, as it allows the selection of the best suited material from a wide basket of materials. A door for instance could utilize a light weight smooth finish aluminum stamping, applied to a ultra light weight magnesium structure that is locally reinforced at the hinges with steel plates, such a closure assembly is shown in Figure 8. Dif ficulties however arise when attempting to join such an assembly. In addition to the problem of galvanic corrosion, welding of these dissimilar metals is not feasible. Mechanical fasteners meanwhile somewhat defeat the purpose as it adds considerable mass, and like spot welding still creates point loadsalong the joint, with the exception that now a hole is needed in the substrates elevating stress maxima even further. Adhesive bonding eliminates these concerns, the continuous film between these dissimilar substrates provides a barrier to electron flow while at the same time evenly distributing stress across the joint surface.Figure 8: An example of a multimetal closure assembly prepared for Shanghai VW to be used at the 2010 World Expo in Shanghai.Structural adhesive or Terocore can serve as a conductive barrier in the prevention of galvanic corrosion between dissimilar metals. This allows designers to utilize a reinforcement material that is different from the remainder of the section components. An aluminum extrusion or magnesium casting can thereby be bonded into a steel structure. The testing, whose results are shown in Figure 9, used the same box beams that have been discussed previously but rather than using an all steel construction these utilize different reinforcement materials. A designer can fine tune the system by means of material selection, balancing performance and mass. The beams illustrated here utilize a steel shell, but the same concept could be employed with an aluminum assembly, steel inserts could be added to reinforce local areas of concern by utilizing a Terocore composite solution.Figure 9: Weld flange separation and energy absorption at 130 mm de flection for box beam joined by spot welding only and joined by bonding using an impact resistant adhesive (no spot welding applied)The modern challenges placed upon vehicle design of improving vehiclecrash performance while at the same time improving fuel ef ficiency are often in con flict. In order to achieve both of these targets automotive designers much look to new processes, techniques and materials. Henkel Terokal structural adhesive and Terocore structural foams are two very useful tools have available. Both technologies enable the vehicle structure to work more ef ficiently. Terokal structural adhesive improves the ef ficiency of the structural joints, by distributing stress across the entire surface area. Terocore on the other hand improves the ef ficiency of the section, distributing load from component to component and preventing local buckling. Furthermore, Terokal structural adhesive and Terocore structural foam enable the use of multimetal assemblies. These bonding agents provide a continuous insulating layer which prevents galvanic corrosion and reduces or eliminates the need for mechanical fasteners. Without these concerns designers are free to select their material of choice where appropriate based upon speci fic vehicle requirements.[1] Wallentowitz H, Wohlecker R, Johannaber M, et al. Determination of weight elasticity of fuel economy for conventional ICE vehicles, hybrid vehicles and fuel cell vehicles [R]. Forschungsgesellschaft Kraftfahrwesen mbH Aachen, Body Department, June 2007.[2] Wallentowitz H, Wohlecker R, Henn R. Communication module mass reduction [R]. Forschungsgesellschaft Kraftfahrwesen mbH Aachen, November 2006.[3] World Auto Steel. Advanced High Strength Steel (AHSS) Application Guidelines Version 4.0 [S]. World Auto Steel ORG, March 2009[4] Ishida K, Fukahori M, Hanakawa K, et al. Development of a technique to strengthen body frame with structural foam [C]// SAE 2001 World Congress,2001-01-0313.[5] Hornung M, Doba T, Agarwal R, et al. Structural Adhesives foe Energy Management and Reinforcement of Body Structures [J]. JAdhesion Society of Japan, 2008, 44: 258-263.[6] Hornung M, Hajj M. Structural Bonding for Lightweight Construction[C]// 4th Intl Light Metals Technology Conf,June 2009.[7] Frost & Sullivan. Global Analysis of Weight Reduction Strategies at Major OEMs [R]. M37A-18, July 2009.[8] Ishida K, Fukahori M, Hanakawa K, et al. Development of a technique to strengthen body frame with structural foam [C]// SAE 2001 World Congress, No. 2001-01-0313,As consumers and governments around the globe press for improved crash safety they are met with con flicting demands: improve crash safety while also improving fuel ef ficiency. Common techniques of improving crashworthiness include increasing the gauge of the existing steel structural components, or adding additional reinforcements in critical areas where the vehicle structure buckles during impact. In each of these scenarios however signi ficant mass is added to the vehicle, a consequence that is somewhat counterproductive. While the structure is getting stronger it also is getting heavierwhich also means that at speed the vehicle has more kinetic energy. In order to meet the same level of crashperformance the now heavier vehicle must absorb more energy before it settles to rest.。
铝侧围外板滚边连接技术浅析

铝侧围外板滚边连接技术浅析作者:***来源:《时代汽车》2024年第02期摘要:很多汽车厂在车身上已经应用钢制零件与铝制零件的混合连接工艺,由于钢、铝材料属性的差异,导致不能采用常规的电阻点焊进行连接操作;本文针对某项目车身铝侧围外板与钢侧围内板连接需求进行工艺分析,该项目采用滚边工艺增加结构胶接的方式去解决铝侧围外板与钢侧围内板总成连接需求,既要考虑密封条、顶饰条、玻璃安装面对车身功能需求又要保证连接后的车身属性需求。
关键词:滚边工艺摩擦单元焊预装挂钩结构胶 BOP SPR GEO点1 前言为了实现“炭达峰”、“炭中和”的双炭目标,各汽车企业已经把车身减重作为衡量产品设计优劣的重要指标,在保证车身安全强度和碰撞性能的前提下,尽量降低车身设计重量,从而降低汽车整备重量,降低能源消耗值;众所周知铝制零件与钢制零件比较有密度低、硬度弱、延展性強、抗腐蚀性高、导电性强等特性,由于两者特性差异在车身不同结构会存在一些钢制零件与铝制零件混合应用的情况,一般会使用SPR、FDS、摩擦单元焊(SRE)、胶粘等异种金属连接技术,但是此项目的铝侧围外板件与钢制内板采用这些连接工艺还存在一些车身结构技术上的难点,如采用标准FDS、SPR连接后侧门止口的厚度和长度无法有效配合卡接密封条,侧围内板为热成型材料屈服强度超过SPR钉子材料本身的强度,需要特殊材料与型号的钉子才可以完成连接增加了生产开发成本;因此考虑采用滚边工艺和结构胶粘接工艺去解决这些问题,为后续铝侧围外板和钢制内板混合应用的项目提供结构设计参考。
2 铝侧围外板滚边方案描述汽车企业的侧围外板零件和侧围内板大多采用常规的电阻点焊进行连接,成本低、效率高、质量稳定;对于铝侧围外板与钢侧围内板连接则需要采用钢、铝异种金属的冷连接技术,还需要在连接位置增加结构胶,能够防电化学腐蚀作用,但是由于侧围内板是热成型零件屈服强度达到1300Mpa以上,无法用普通的SPR钉进行有效连接,普通钉模组合要求下板(侧围内板)的强度不能超出SPR钉材料本身的强度,否则无法形成有效的互锁连接点,达不到SPR要求的连接强度;所以铝侧围外板与钢侧围内板主要采用结构胶固化加滚边工艺进行连接;本项目在焊装合拼工位将车身零件(侧围外板、车身分总成、前顶横梁外板、后顶横梁外板)涂胶并由主拼夹具进行二次合拼形成车身外总拼框架,采用4mm尺寸特殊SPR钉进行预点定操作,在下一工序机器人对外板滚边操作与侧围内板进行连接。
结构胶的作用和用途

结构胶的作用和用途结构胶是一种广泛应用于建筑、汽车、航空、电子等领域的粘合材料,其作用和用途非常广泛。
本文将从结构胶的定义、种类、特点、应用领域等方面详细介绍结构胶的作用和用途。
一、结构胶的定义和种类结构胶是一种粘合材料,它能够将两种或两种以上的材料牢固粘合在一起,形成一个整体。
结构胶的种类很多,常见的有环氧树脂胶、聚氨酯胶、丙烯酸酯胶、硅酮胶等。
二、结构胶的特点1. 强度高:结构胶的粘合强度非常高,能够承受大的拉伸、剪切和剥离力,可以在不同的环境下保持一定的强度。
2. 耐久性好:结构胶的耐久性非常好,可以在不同的温度、湿度和化学介质下长时间使用。
3. 填充性好:结构胶具有很好的填充性,可以填充不同形状和大小的缝隙,提高粘合的牢固度。
4. 施工方便:结构胶使用方便,可以用手工或机械设备施工,可以在不同的温度和湿度下使用。
三、结构胶的应用领域1. 建筑领域:在建筑领域,结构胶主要用于粘合钢筋、混凝土、玻璃、陶瓷、石材等材料,增强建筑结构的强度和稳定性。
2. 汽车领域:在汽车领域,结构胶主要用于粘合车身、车窗、车灯、轮毂、座椅等部件,提高汽车的安全性和舒适性。
3. 航空领域:在航空领域,结构胶主要用于粘合飞机机翼、机身、起落架等部件,提高飞机的强度和稳定性。
4. 电子领域:在电子领域,结构胶主要用于粘合电路板、芯片、显示屏等部件,提高电子设备的性能和可靠性。
四、结构胶的优缺点1. 优点:结构胶具有强度高、耐久性好、填充性好、施工方便等优点,能够满足不同领域的需求。
2. 缺点:结构胶的缺点是粘结时间较长,需要等待一定时间才能达到最大的粘合强度,一些结构胶对环境的要求比较高,需要在特定的温度和湿度下使用。
五、结论结构胶是一种非常重要的粘合材料,具有广泛的应用领域和优良的性能。
在未来,随着科技的不断发展和创新,结构胶的应用范围将会越来越广泛,成为推动各个领域发展的重要推动力。
发泡剂和结构胶

发泡剂和结构胶是两种不同的材料,分别具有不同的用途。
发泡剂是一种化学品,主要用于制作泡沫材料,如泡沫塑料、泡沫玻璃等。
发泡剂可以在材料中产生气泡,使材料具有轻质、隔热、吸音等特性。
常见的发泡剂有聚氨酯、聚苯乙烯等。
结构胶是一种强力胶水,可以用于粘接建筑材料,如木材、金属、石材等。
结构胶的特点是具有极强的粘接力和耐水、耐气候、耐高温等性能。
常见的结构胶有环氧树脂胶、聚氨酯胶、丙烯酸胶等。
需要注意的是,发泡剂和结构胶属于不同类型的材料,不能混淆使用。
同时,在使用发泡剂和结构胶时,需要注意材料的性质和用途,以免出现不必要的损坏或安全隐患。
结构胶、耐厚胶试验工作规定

江苏省建伟幕墙装饰工程有限公司结构胶、耐候胶试验工作管理规定QB/JW-GJ·1011.1 总则1.2 为在建筑幕墙工程中贯彻《玻璃幕墙工程技术规范》JGJ102标准,确保幕墙工程的安全可靠。
制定本规定。
1.2 建筑幕墙工程上使用的结构硅酮密封胶(简称结构胶)和耐候硅酮密封胶(简称耐候胶),均应进行粘接力和相容性试验。
1.3 结构胶和耐候胶粘接力和相容性试验应在使用前由供应厂商进行并提交检测报告。
2. 试验工作程序及内容结构胶、耐候胶粘接力和相容性试验应按以下程序及内容进行:2.1 试验工作程序流程图28 32.2 填写试验申请表设计人员在幕墙工程设计图样会签后,主要材料确定后应及时填写试验申请表。
试验申请表见附件。
2.3 提供设计图样和资料设计人员在填写试验申请表时,应同时提供幕墙粘结节点图样和粘结节点设计所需要的全部技术数据:2.3.1 玻璃板块或金属板块的最大尺寸;2.3.2 结构胶或耐候胶粘接宽度和厚度尺寸;2.3.3 物理性能参数:风荷载设计值、节点位移、最大温差、防震烈度和其它引起位移的因素等。
2.4 审批、存档和送验,试验申请表、图样和资料经校对和审核后,复制一份。
一份设计员自存,一份送供应科。
2.5 制备试验样品供应科在收到试验申请资料后的一周内,应按试验要求和设计人员提供的资料完成试验样品的制备。
并负责送交试验单位进行试验。
2.6 试验周期一般试验周期需5~6星期完成。
试验的全部资料应在工程施工前6~7周发出。
如要求缩短试验周期应在试验申请表内提出。
试验时间最少需4~5 星期完成。
2.7 试验报告供应科应及时索回试验报告。
2.7.1 供应科在收到试验合格报告后,原件送交质安科保存,复印件的一份转交设计员,另一份供应科留作备案。
2.7.2 试验不合格情况的处理供应科在收到试验不合格报告后,应及时将信息和试验不合格报告直接反馈给设计人员。
设计人员可重新选择胶料或与其相接触的材料,并重新填写试验申请报告,再进行试验。
建筑结构胶在加固补强与改造工程中的应用:进展与未来
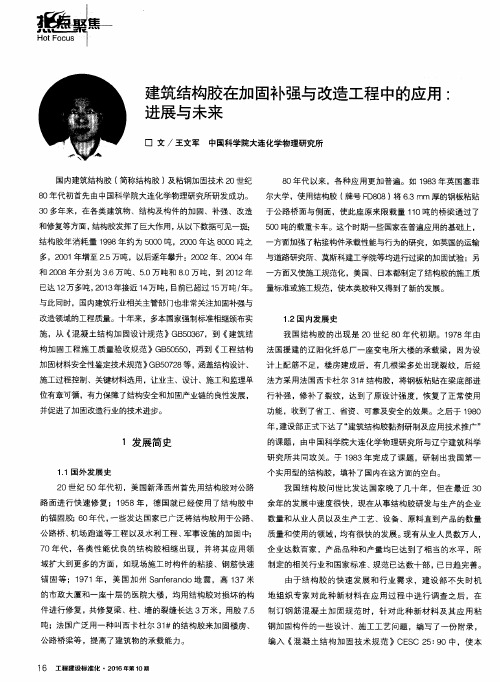
2 O世纪 5 0年代初 ,美国新泽西州首先用结构胶 对公路
路面进 行快速修 复 ;1 9 5 8年 ,德 国就已经使用 了结构胶 中 余年的发展 中速度很快 ,现在从事结构胶研发 与生产 的企业 的锚 固胶; 6 0年代 , 一 些发达 国家已广泛将结构胶 用于公路 、 数量和从业人员 以及生产工艺 、设备 、原料直 到产 品的数量
2 0世 纪 8 0年代 中期 ,我 国建 筑 行 业 迅 猛 发 展 , 与此 同
此规 范于 1 9 9 0年制订并公布 实施 ,它的制订 与实施又促进 时仍有大量 的老 旧建筑物 需要 进行 加固与改造 。此 时期 的市 结构胶的研究与开发。特别在近十年来 ,住房城 乡主管部 门 场 需求 大大促进 了结构胶 的推广 与应用 。9 O年代 以来 ,结
由于结 构胶 的快速 发展 和行业 需求 ,建 设部 不失 时机
的市政大厦 和一 座十层 的医院大楼 ,均 用结构胶对损坏的构 地组 织专 家对此 种新 材料在 应用过 程 中进行调 查之后 ,在
件进行修 复 , 共修复梁 、柱、墙 的裂缝长达 3万米 ,用胶 7 . 5 制订 钢筋 混凝土 加 固规范 时,针对此 种新 材料及 其应 用粘 吨;法国广 泛用一种 叫西卡杜 尔 3 1 #的结构胶来加 固楼房 、
公路桥 梁等 ,提 高了建筑物的承载 能力。
钢加 固构件 的一些设计 、施工工艺问题 ,编写 了一份附录 , 编入 《 混 凝土 结构 加 固技术 规范 》CE S C 2 5: 9 0中,使 本
1 6 工程 建设标准化 ・ 2 0 1 6年第1 0期
类胶种在 使用时得 以走 向规范化 ,确保其使用质量与安全。
公路桥 、 机场跑道 等工程 以及水 利工程 、 军 事设施 的加固中;
汽车车身设计与制造工艺新技术
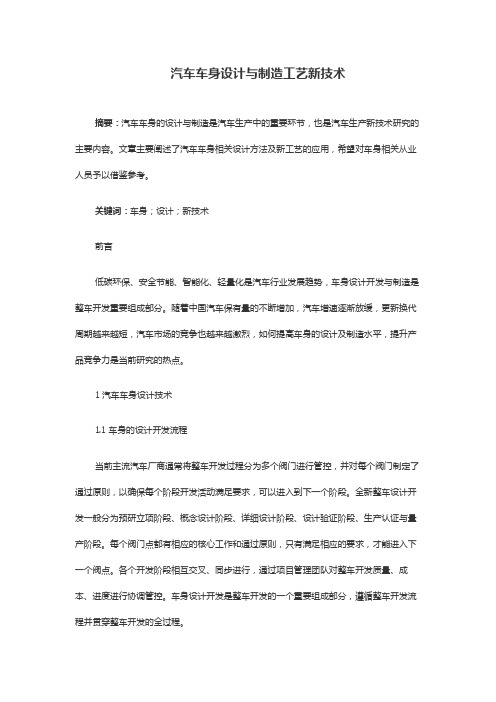
汽车车身设计与制造工艺新技术摘要:汽车车身的设计与制造是汽车生产中的重要环节,也是汽车生产新技术研究的主要内容。
文章主要阐述了汽车车身相关设计方法及新工艺的应用,希望对车身相关从业人员予以借鉴参考。
关键词:车身;设计;新技术前言低碳环保、安全节能、智能化、轻量化是汽车行业发展趋势,车身设计开发与制造是整车开发重要组成部分。
随着中国汽车保有量的不断增加,汽车增速逐渐放缓,更新换代周期越来越短,汽车市场的竞争也越来越激烈,如何提高车身的设计及制造水平,提升产品竞争力是当前研究的热点。
1汽车车身设计技术1.1车身的设计开发流程当前主流汽车厂商通常将整车开发过程分为多个阀门进行管控,并对每个阀门制定了通过原则,以确保每个阶段开发活动满足要求,可以进入到下一个阶段。
全新整车设计开发一般分为预研立项阶段、概念设计阶段、详细设计阶段、设计验证阶段、生产认证与量产阶段。
每个阀门点都有相应的核心工作和通过原则,只有满足相应的要求,才能进入下一个阀点。
各个开发阶段相互交叉、同步进行,通过项目管理团队对整车开发质量、成本、进度进行协调管控。
车身设计开发是整车开发的一个重要组成部分,遵循整车开发流程并贯穿整车开发的全过程。
1.2车身平台化模块化随着汽车行业竞争加剧以及消费者对汽车品质要求的不断提高,各大汽车厂商推出新车型的速度不断加快。
车身平台化、模块化开发的运用,不但可以大幅缩短研发的周期、降低开发成本,提升规模效益,而且可以有效降低技术风险、提高产品可靠性。
基于新的平台发展规划策略,丰田、大众、通用、日产等主流汽车企业越来越多的新车型逐步上市,增强了市场竞争力并取得了良好的经济效益。
国内自主品牌也从早期的完全逆向开发逐渐进入到正向开发阶段,并开始重视并加大平台化研究。
1.3车身新结构新材料的运用(1)车身新结构车身概念设计阶段通常会根据总布置和造型进行主体架构的设计构想,再进行详细结构设计。
概念设计阶段运用先进的仿真分析方法,不需要详细的3D几何模型就可构建前期概念有限元模型,进行大量有较大差异的方案分析并逐渐优化,按照先整体后局部的设计思路,在概念设计阶段确定车身整体框架结构。
结构胶和结构泡沫——改善碰撞性能的可行技术

Spot WeldingAdhesive BondingWeldbondingElongation S h e a rS t r e s sS h e a rS t r e s s S h e a rS t r e s sL o a d L o a dL o a dCollapseFixFix Without foam (0.10 rad)With foam (0.10 rad)Energy AbsorptionSpot welding only Flange separates, can improve with adhesive back flangeback flange Flange separates,can improve with adhesive Spot welding +Structural foamMean energy absorption: 1.962 kJ@ 130 mm deflection Mean energy absorption: 4.03 kJ @ 130 mm deflection糍Impact hammerreinforcementpanel结构胶和结构泡沫——改善碰撞性能的可行技术作者:Kyle Royston, Martin Hornung, Micheal Hajj, Jingfen ZHANG作者单位:Henkel Japan,27-7 Shin Isogo-cho,Isogo-ku,Yokohama,235-0017,日本国刊名:汽车安全与节能学报英文刊名:JOURNAL OF AUTOMOTIVE SAFETY AND ENGERGY年,卷(期):2010,01(4)被引用次数:1次参考文献(8条)1.Wallentowitz H;Wohlecker R;Johannaber M Determination of weight elasticity of fuel economy for conventional ICE vehicles,hybrid vehicles and fuel cell vehicles 20072.Wallentowitz H;Wohlecker R;Henn R Communication module mass reduction 20063.World Auto Steel Advanced High Strength Steel (AHSS)Application Guidelines Version4.0 20094.Ishida K;Fukahori M;Hanakawa K Development of a technique to strengthen body frame with structural foam[外文会议] 20015.Hornung M;Doba T;Agarwal R Structural Adhesives foe Energy Management and Reinforcement of Body Structures 20086.Hornung M;Hajj M Structural Bonding for Lightweight Construction 20097.Frost &;Sullivan Global Analysis of Weight Reduction Strategies at Major OEMs[M37A-18]8.Ishida K;Fukahori M;Hanakawa K Development of a technique to strengthen body frame with structural foam[外文会议] 2001本文读者也读过(3条)1.杨洋从白车身材料技术看汽车安全[期刊论文]-汽车与配件2008(1)2.燕来荣铝合金车轮轻装上路——现代汽车安全、环保、节能的最佳选择[期刊论文]-汽车运用2007(9)3.顾春祺基于虚拟试验的车用结构胶合技术研究[学位论文]2008引证文献(1条)1.吕晓江.刘卫国.颜先华.张海洋.同大永.赵福全高密度结构泡沫对汽车前纵梁耐撞性的影响及应用[期刊论文]-汽车安全与节能学报 2013(2)引用本文格式:Kyle Royston.Martin Hornung.Micheal Hajj.Jingfen ZHANG结构胶和结构泡沫——改善碰撞性能的可行技术[期刊论文]-汽车安全与节能学报 2010(4)。
- 1、下载文档前请自行甄别文档内容的完整性,平台不提供额外的编辑、内容补充、找答案等附加服务。
- 2、"仅部分预览"的文档,不可在线预览部分如存在完整性等问题,可反馈申请退款(可完整预览的文档不适用该条件!)。
- 3、如文档侵犯您的权益,请联系客服反馈,我们会尽快为您处理(人工客服工作时间:9:00-18:30)。
Kyle Royston, Martin Hornung, Micheal Hajj, Jingfen ZHANG
(Henkel Japan, 27-7 Shin Isogo-cho, Isogo-ku, Yokohama, 235-0017, Japan)
Abstract: A structural foam and a structural adhesive produced by Henkel Co. were introduced contributing to light weight construction and automotive safety for new energy automotive industry. Of these two new solutions, the chemical aspects, mechanical properties were measured for automotive application cases and the improvement contributions to vehicle performance. The results show that the structural foam has the excellent properties of being lightweight, providing both high strength and stiffness, therefore, offering many weight saving and cost reduction solutions, thus, increases the energy absorption capacity of the vehicle structure during collision situations; the structural adhesive provides an effective joint line, optimizing stress distribution, increasing structural strength and stiffness, preventing galvanic corrosion, and hence can also provide alternative cost reduction opportunities. These technologies were used by many OEMs (Original Equipment Manufacturer) on automotive production lines.
Key words: automotive safety; lightweight construction; structural foam; structural adhesive; energy absorption
结构胶和结构泡沫——改善碰撞性能的可行技术
Kyle Royston, Martin Hornung, Micheal Hajj, Jingfen ZHANG
收稿日期 / Received :2010-10-22
作者信息 / First author : Kyle ROYSTON,Profesore。 E-mail :Kyle.Royston@
Second author :Martin HORNUNG。
E-mail :Martin.Hornung@
2010, Vol. 1 No. 4
which also means that at speed the vehicle has more kinetic energy. In order to meet the same level of crash performance the now heavier vehicle must absorb more energy before it settles to rest.
Figure 1: Data from Frost & Sullivan shows an ongoing trend in the automotive industry toward advanced steels and alternative materials as a means to reduced vehicle weight.
ISSN 1674-8484 汽车安全与节能学报, 2010 年, 第 1 卷 第 4 期 CN 11-5904/U J Automotive Safety and Energy, 2010, Vol. 1 No. 4
10/12 313 — 319
Crash Performance Enabling Technologies, Structural Adheise and Structrural Foam
Henkel chemical based products, structural adhesive and structural foam offer new tools to the automotive body engineer. These products help improve the efficiency of the metal structure and at the same time promote the use of multimetal assemblies.
include increasing the gauge of the existing steel structural components, or adding additional reinforcements in critical areas where the vehicle structure buckles during impact. In each of these scenarios however significant mass is added to the vehicle, a consequence that is somewhat counterproductive. While the structure is getting stronger it also is getting heavier
Introduction
As consumers and governments around the globe press for improved crash safety they are met with conflicting demands: improve crash safety while also improving fuel efficiency. Common techniques of improving crashworthiness
Thire author : Micheal HAJJ。
E-mail :Michael.Hajj@
Fourth author : Jingfen ZHANG。
E-mail :Jingfen.zhang@
314
J AБайду номын сангаасtomotive Safety and Energy
Manufactures have explored new processing techniques and materials to increase vehicle safety while at the same time minimizing the mass of the vehicle. Taylor welded blanks allow utilizing two or more different thicknesses of steel in the same structural stamping, with the goal of placing additional steel only where it is needed. The hydroforming process, forming tubes by harnessing the force of internal fluid pressure, allows manufacturers to utilize complex variable sections and take advantage of stain hardening. Meanwhile alternative material utilization is also increasing, Ultra high strength steel (UHSS) and Advanced high strength steel (AHSS) combined are the most common of these materials. However alternative metals such have aluminum and magnesium are also becoming more prevalent. Utilizing these materials presents their own unique challenges however. AHSS is still somewhat difficult to acquire in China and comes with a high cost of processing and initial capital investment. The use of aluminum and magnesium is problematic due to material cost as well as joining and galvanic corrosion difficulties.
(Henkel Japan, 27-7 Shin Isogo-cho, Isogo-ku, Yokohama, 235-0017, 日本国 )