电子产品散热设计
电子产品热传设计-散热片的选择与设计
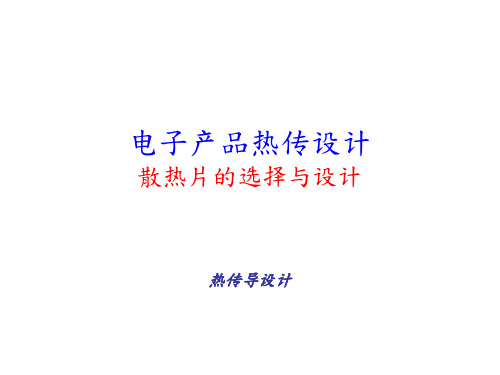
2. 挤型(Extrusion)散热片: 挤型的制造方式是由将材料在高压下强制流入 模孔中成形而使得固体转换为等截面的连续长 条。挤形是散热片制造中最广泛使用的方式, 设备投资的经额中等。可经由横切的方式产生 矩形的针状散热片,可产生锯齿状的鳍片以增 加10~20%的效能,但会降低挤型的速度。挤型 的高宽比限制可高到6,使用特殊模具设计时 则可到10的高宽比。
4. 散热片表面处理: 散热片表面做耐酸铝(Alumite) 或阳极处理可以增加辐射性能而增加
散热片的散热效能,一般而言,和颜色是白色或黑色关系不大。表面突起的 处理可增加散热面积,但是在自然对流的场合,反而可能造成空气层的阻碍, 降低效率。
上述之设计方式仅供散热片设计之参考,实际散热片设计时还需考虑与 组件以及环境的配合,尤其是高效能散热片的设计需配合实验量测验证以及 CFD 的分析模拟。
因此为了满足未来电子散热的需求,在散热片的形状、材料及制程上都必须 有更新的技术,此外整合其他散热组件的设计方式的也可以增加应用时的效率。 本次将介绍散热片的种类及制程,散热片的应用以及未来的设计需求。
&散热片的种类&
许多的散热片设计由于忽略了制造的概念,使得研发产品的可靠度及成本成 为最后量产的障碍。由制造方式来看,气冷的散热片可分为下面几种,如图一所 示,表一则为制程性能参数的整理。
表二各种不同散热片的材料比较
#散热片设计的一般原则#
接着我们进一步讨论散热片的详细的设计细节,首先介绍一般的方式, 这些点单的方法可以对一些应用简单的散热片设计提供设计标准: 1.包络体积以散热片的设计而言这里介绍一个简易的方法也就是包络体积的观 念所谓包络体积是指散热片所占的体积如果发热功率大,所需的散热片体积 就比较大。散热片的设计可就包络体积做初步的设计然后再就散热片的细部 如鳍片及底部尺寸做详细设计。发热瓦数和包络体基的关系如下式所示。
电子电路PCB的散热分析与设计

电子电路PCB的散热分析与设计随着科技的不断发展,电子设备已经成为了我们生活中不可或缺的一部分。
然而,在电子设备运行过程中,由于电路板上的元器件会产生大量的热能,如果散热不良,会导致设备性能下降、可靠性降低甚至出现安全问题。
因此,针对电子电路PCB的散热分析与设计至关重要。
本文将结合实际案例,对电子电路PCB的散热问题进行分析和讨论。
电路板的热阻:热阻是表示热量传递难易程度的物理量,值越小表示热量传递越容易。
电路板的热阻主要包括元器件的热阻和电路板本身的热阻,其中元器件的热阻受到其功耗、结点温度等因素的影响。
自然对流:自然对流是指空气在温度差的作用下产生的流动现象。
在电子设备中,自然对流可将热量从电路板表面传递到周围环境中,从而降低电路板温度。
然而,自然对流的散热效果受到空气流动速度、环境温度等因素的影响。
强迫通风:强迫通风是通过风扇等装置强制空气流动,以增强电子设备的散热能力。
强迫通风的散热效果主要取决于风扇的功率、风量等因素。
选择合适的导热材料:导热材料具有将热量从高温区域传导到低温区域的能力,常用的导热材料包括金属、陶瓷、石墨烯等。
在电路板设计中,应根据元器件的功耗和结点温度等因素,选择合适的导热材料。
提高电路板表面的散热能力:提高电路板表面的散热能力可以有效降低电路板的温度。
常用的方法包括增加电路板表面积、加装散热片、使用热管等。
合理安排元器件的布局:元器件的布局对电路板的散热效果有着重要影响。
在布局时,应尽量将高功耗元器件放置在电路板的边缘或中心位置,以方便热量迅速散出。
同时,应避免将高功耗元器件过于集中,以防止局部温度过高。
增强自然对流:自然对流是电路板散热的重要途径之一。
在电路板设计中,应尽量减少对自然对流的阻碍,如避免使用过高的结构、保持电路板表面的平整度等。
可在电路板下方或周围增加通风口或风扇等装置,以增强自然对流的散热效果。
采用强迫通风:强迫通风可以显著提高电子设备的散热能力。
10种PCB散热方法

10种PCB散热方法PCB(Printed Circuit Board)散热是电子产品设计中的一个重要环节,合理的散热方法可以保证电子产品的稳定运行和寿命。
下面将介绍10种常用的PCB散热方法。
1.散热片:在PCB板上加装散热片可以增加散热面积,提高散热效果。
散热片通常由铝、铜等金属材料制成,有助于将热量快速传导到周围的空气中。
2.散热孔:在PCB板上设计散热孔可以增加空气对板块的流动性,加强热量的带走。
合理的散热孔设计可以提高散热效果。
3.散热器:在PCB板的散热元件上安装散热器,可以通过散热器的扩散面积和散热风扇的风力来增加散热效果。
散热器通常由铝合金或铜制成。
4.散热膏:在高功耗元件和散热器之间使用散热膏可以提高导热效果。
散热膏的主要成分是硅油或聚合物,具有良好的导热性能。
5.PCB板设计优化:通过合理的电路布局和优化导线走向,可以减少电路板内部的热量堆积,提高散热效果。
6.板材选择:选择导热性能好的PCB板材料,如金属基板(如铝基板、铜基板等),可以提高热传导效果。
7.强制散热:利用风扇或气流,将空气强制引导到PCB板的散热元件上,增强散热效果。
这种方法适用于功耗较高的电子器件。
8.采用热管:热管是一种利用液体的蒸发冷凝过程来传导热量的器件,可以将热量从高温区域传递到低温区域,进一步提高散热效果。
9.线路板厚度增加:增加PCB板的厚度可以增加板层之间的热容量,降低热量堆积的风险,提高散热效果。
10.外部散热元件:在PCB板附近增加散热元件,如散热风扇或散热片等,可以进一步增加散热面积和风力,提高散热效果。
综上所述,PCB散热是一门综合性的技术,需要从多个角度综合考虑。
通过合理的散热方法和设计优化,可以有效降低电子产品的工作温度,提高其性能和可靠性。
PCB电路板散热设计技巧

PCB电路板散热设计技巧一、热设计的重要性电子设备在工作期间所消耗的电能,比如射频功放,FPGA芯片,电源类产品,除了有用功外,大部分转化成热量散发。
电子设备产生的热量,使内部温度迅速上升,如果不及时将该热量散发,设备会继续升温,器件就会因过热失效,电子设备的可靠性将下降。
SMT使电子设备的安装密度增大,有效散热面积减小,设备温升严重地影响可靠性,因此,对热设计的研究显得十分重要。
对于PCB电路板的散热是一个非常重要的环节,那么PCB电路板散热技巧是怎样的,下面我们一起来讨论下。
对于电子设备来说,工作时都会产生一定的热量,从而使设备内部温度迅速上升,如果不及时将该热量散发出去,设备就会持续的升温,器件就会因过热而失效,电子设备的可靠性能就会下降。
因此,对电路板进行很好的散热处理是非常重要的。
二、印制电路板温升因素分析引起印制板温升的直接原因是由于电路功耗器件的存在,电子器件均不同程度地存在功耗,发热强度随功耗的大小变化。
印制板中温升的2种现象:(1)局部温升或大面积温升;(2)短时温升或长时间温升。
在分析PCB热功耗时,一般从以下几个方面来分析。
2.1电气功耗(1)分析单位面积上的功耗;(2)分析PCB板上功耗的分布。
2.2印制板的结构(1)印制板的尺寸;(2)印制板的材料。
2.3印制板的安装方式(1)安装方式(如垂直安装,水平安装);(2)密封情况和离机壳的距离。
2.4热辐射(1)印制板表面的辐射系数;(2)印制板与相邻表面之间的温差和他们的绝对温度2.5热传导(1)安装散热器;(2)其他安装结构件的传导。
2.6热对流(1)自然对流;(2)强迫冷却对流。
从PCB上述各因素的分析是解决印制板的温升的有效途径,往往在一个产品和系统中这些因素是互相关联和依赖的,大多数因素应根据实际情况来分析,只有针对某一具体实际情况才能比较正确地计算或估算出温升和功耗等参数。
三、PCB热设计的一些方法1通过PCB板本身散热目前广泛应用的PCB板材是覆铜/环氧玻璃布基材或酚醛树脂玻璃布基材,还有少量使用的纸基覆铜板材。
电子产品防水散热结构设计

电子产品防水散热结构设计
随着工业产品的不断升级,现在很多工业产品都需要防水及散热,目前国内有很多产品适应于工业产品防水及散热结构设计。
比如:GOEL防水透气膜、GOEL防水透气阀等!
对于机箱需要解决防尘、防潮、防水与散热问题,可以采用GOEL防水透气阀!在国内,各种户外机箱、电信机箱、高铁机箱等都利用GOEL防水透气阀解决防尘、防潮、防水与散热问题。
GOEL防水透气阀具有防水、防尘、防油污,防护等级达到IP68。
耐化学剂、耐高低温、抗老化等,提高产品苛刻环境中的可靠性。
防止结露、结雾,提高产品使用寿命。
微散热及平衡压差。
提高产品的完整性等特性!
同时解决防尘、防潮、防水与散热.
GOEL防水透气膜及防水透气阀产品可以解决工业产品防水及散热结构设计,目前大多数工业产品都有应用哦,如:LED灯具、汽车电机、电池、ECU、传感器、通讯设备、手机、电动理发器、电动剃须刀、电动牙刷、美容电动仪等。
电子设备自然对流散热的优化策略
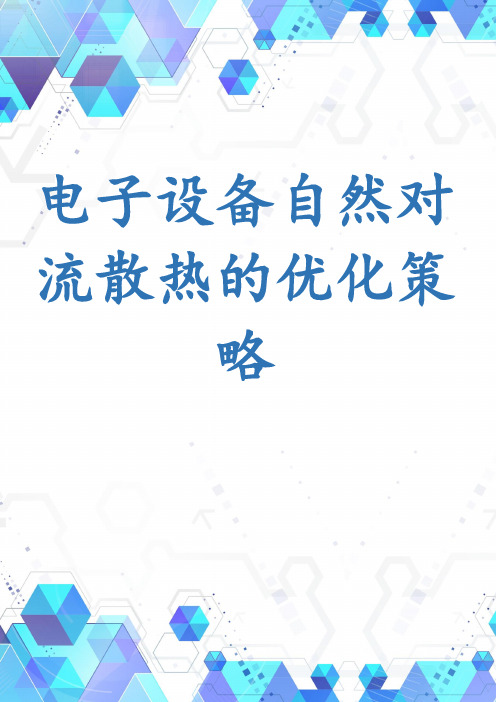
电子设备自然对流散热的优化策略电子设备自然对流散热的优化策略电子设备散热是一个重要的问题,特别是在高负荷运行时。
如果设备无法有效散热,会导致过热,降低性能甚至引发损坏。
因此,优化设备的自然对流散热至关重要。
下面将逐步介绍一些优化策略。
第一步,设计散热结构。
要优化自然对流散热,首先需要设计出合适的散热结构。
这包括选择合适的散热片、散热管等散热元件,并合理布局它们。
散热片的形状、材料和表面积都会影响散热效果。
同时,散热结构的布局也要考虑到设备内部的空间限制以及空气流动的方向。
第二步,合理布局电子元件。
电子元件的布局也会影响散热效果。
将产生较多热量的元件集中排列,避免堆叠,可以减少热量积聚的可能性,提高散热效果。
此外,对于散热要求较高的元件,可以考虑使用散热片或散热模块进行加装,以增加散热面积。
第三步,合理安排通风口和风扇。
通风口和风扇是促进自然对流散热的重要组成部分。
通风口的设计要考虑到空气流动的方向,避免死角。
通风口的尺寸和数量也要根据设备的散热需求进行合理安排。
风扇的选择要考虑到风量和噪音等因素,以确保散热效果和使用舒适性的平衡。
第四步,减少热量积聚。
除了提高散热效果外,还应该尽量减少热量的产生和积聚。
这可以通过优化电路设计、增加散热材料的导热性等方式来实现。
例如,采用高效的电源供应器、使用低功耗的元件等都可以减少设备内部的热量产生。
第五步,合理使用设备。
在使用设备时,要注意避免堵塞通风口,保持通风畅通。
同时,避免将设备放置在高温环境下使用,这会增加设备散热的负担。
另外,定期清洁设备,清除堆积的灰尘和杂质,也是保持散热效果的关键。
通过以上优化策略,可以有效提高电子设备的自然对流散热效果,保证设备在高负荷运行时的稳定性和可靠性。
当然,不同设备的散热需求也会有所不同,因此在具体实施优化策略时,还需要考虑到设备的特点和使用环境的要求。
电子封装的散热设计原理

电子封装的散热设计原理电子封装的散热设计原理在现代电子产品中,散热是一个非常重要的设计考虑因素。
随着电子元件和集成电路的不断发展,电子封装的散热设计原理也变得越来越关键。
本文将介绍一些常见的电子封装散热设计原理。
首先,散热设计的目标是将电子元器件产生的热量迅速有效地传导、辐射和对流到周围环境中。
通过合理的散热设计,可以保持电子元器件的工作温度在安全范围内,提高其工作效率和寿命。
一种常见的散热设计原理是利用导热材料。
导热材料,如硅胶脂、硅胶垫等,具有良好的导热性能,可以将电子元器件的热量迅速传导到散热器或散热片上。
通过选择合适的导热材料,可以提高热量的传导效率,从而减少电子元器件的温度升高。
另一种散热设计原理是利用散热器或散热片。
散热器通常由铝或铜等材料制成,具有良好的热传导性能。
散热器通过增大表面积,提高空气的对流效果,加速热量的辐射。
同时,散热片的设计也非常重要。
通过增加散热片的数量和密度,可以增强散热器的散热能力,有效降低电子元器件的温度。
此外,风扇也是一种常用的散热设计原理。
风扇能够通过强制对流,将散热器表面的热量带走。
通过选择合适的风扇尺寸和转速,可以提供足够的风量,保持电子元器件的工作温度稳定。
最后,设计良好的散热路径也是散热设计的重要原则。
通过合理的散热路径设计,可以确保热量能够顺利地从电子元器件传导到散热器或散热片上,并最终通过对流、辐射等方式散发到周围环境中。
综上所述,电子封装的散热设计原理包括利用导热材料、散热器和散热片、风扇以及设计合理的散热路径等。
通过合理地应用这些原理,可以有效降低电子元器件的温度,提高其工作效率和寿命。
在未来的电子封装设计中,散热设计将继续发挥重要的作用,随着技术的不断发展,也会出现更多创新的散热设计原理。
电子设备的散热设计和温度控制
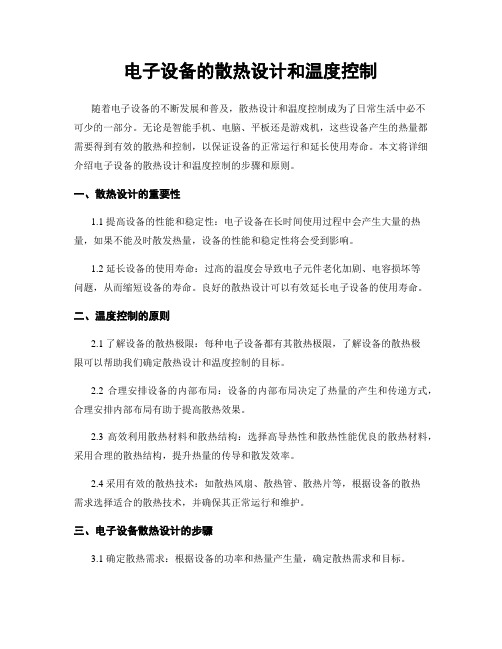
电子设备的散热设计和温度控制随着电子设备的不断发展和普及,散热设计和温度控制成为了日常生活中必不可少的一部分。
无论是智能手机、电脑、平板还是游戏机,这些设备产生的热量都需要得到有效的散热和控制,以保证设备的正常运行和延长使用寿命。
本文将详细介绍电子设备的散热设计和温度控制的步骤和原则。
一、散热设计的重要性1.1 提高设备的性能和稳定性:电子设备在长时间使用过程中会产生大量的热量,如果不能及时散发热量,设备的性能和稳定性将会受到影响。
1.2 延长设备的使用寿命:过高的温度会导致电子元件老化加剧、电容损坏等问题,从而缩短设备的寿命。
良好的散热设计可以有效延长电子设备的使用寿命。
二、温度控制的原则2.1 了解设备的散热极限:每种电子设备都有其散热极限,了解设备的散热极限可以帮助我们确定散热设计和温度控制的目标。
2.2 合理安排设备的内部布局:设备的内部布局决定了热量的产生和传递方式,合理安排内部布局有助于提高散热效果。
2.3 高效利用散热材料和散热结构:选择高导热性和散热性能优良的散热材料,采用合理的散热结构,提升热量的传导和散发效率。
2.4 采用有效的散热技术:如散热风扇、散热管、散热片等,根据设备的散热需求选择适合的散热技术,并确保其正常运行和维护。
三、电子设备散热设计的步骤3.1 确定散热需求:根据设备的功率和热量产生量,确定散热需求和目标。
3.2 分析设备的内部布局:了解设备的内部结构和布局,确定热源的位置和热量的传导路径。
3.3 选择合适的散热材料:根据散热需求,选择高导热性和散热性能优良的散热材料,如铜、铝、陶瓷等。
3.4 优化散热结构:根据设备的散热需求,设计合理的散热结构,包括散热风道、散热孔、散热片等。
3.5 确定散热技术:根据设备的散热需求和可行性,选择合适的散热技术,如散热风扇、散热管、液冷等。
3.6 进行温度模拟和测试:利用计算机仿真和实际测试,对散热设计进行验证和调整,确保散热效果符合预期。
- 1、下载文档前请自行甄别文档内容的完整性,平台不提供额外的编辑、内容补充、找答案等附加服务。
- 2、"仅部分预览"的文档,不可在线预览部分如存在完整性等问题,可反馈申请退款(可完整预览的文档不适用该条件!)。
- 3、如文档侵犯您的权益,请联系客服反馈,我们会尽快为您处理(人工客服工作时间:9:00-18:30)。
YEALINK产品热设计VCS项目散热预研欧国彦2012-12-4电子产品的散热设计一、为什么要进行散热设计在调试或维修电路的时候,我们常提到一个词“**烧了”,这个**有时是电阻、有时是保险丝、有时是芯片,可能很少有人会追究这个词的用法,为什么不是用“坏”而是用“烧”其原因就是在机电产品中,热失效是最常见的一种失效模式,电流过载,局部空间内短时间内通过较大的电流,会转化成热,热**不易散掉,导致局部温度快速升高,过高的温度会烧毁导电铜皮、导线和器件本身。
所以电失效的很大一部分是热失效。
高温对电子产品的影响:绝缘性能退化;元器件损坏;材料的热老化;低熔点焊缝开裂、焊点脱落。
温度对元器件的影响:一般而言,温度升高电阻阻值降低;高温会降低电容器的使用寿命;高温会使变压器、扼流圈绝缘材料的性能下降,一般变压器、扼流圈的允许温度要低于95C;温度过高还会造成焊点合金结构的变化—IMC增厚,焊点变脆,机械强度降低;结温的升高会使晶体管的电流放大倍数迅速增加,导致集电极电流增加,又使结温进一步升高,最终导致元件失效。
那么问一个问题,如果假设电流过载严重,但该部位散热极好,能把温升控制在很低的范围内,是不是器件就不会失效了呢答案为“是”。
由此可见,如果想把产品的可靠性做高,一方面使设备和零部件的耐高温特性提高,能承受较大的热应力(因为环境温度或过载等引起均可);另一方面是加强散热,使环境温度和过载引起的热量全部散掉,产品可靠性一样可以提高。
二、散热设计的目的控制产品内部所有电子元器件的温度,使其在所处的工作环境条件下不超过标准及规范所规定的最高温度。
最高允许温度的计算应以元器件的应力分析为基础,并且与产品的可热设计、冷却方式、散热器、热管技术靠性要求以及分配给每一个元器件的失效率相一致。
三、散热设计的方法1、冷却方式的选择我们机电设备常见的是散热方式是散热片和风扇两种散热方式,有时散热的程度不够,有时又过度散热了,那么何时应该散热,哪种方式散热最合适呢这可以依据热流密度来评估,热流密度=热量 / 热通道面积。
按照《GJB/Z27-92 电子设备可靠性热设计手册》的规定(如下图1),根据可接受的温升的要求和计算出的热流密度,得出可接受的散热方法。
如温升40℃(纵轴),热流密度cm2(横轴),按下图找到交叉点,落在自然冷却区内,得出自然对流和辐射即可满足设计要求。
大部分散热设计适用于上面这个图表,因为基本上散热都是通过面散热。
但对于密封设备,则应该用体积功率密度来估算,热功率密度=热量 / 体积。
下图(图2)是温升要求不超过40℃时,不同体积功率密度所对应的散热方式。
比如某电源调整芯片,热耗为,体积为,体积功率密度==cm3,查下图得出金属传导冷却可满足要求按照上图,可以得出冷却方法的选择顺序:自然冷却一导热一强迫风冷一液冷一蒸发冷却。
体积功率密度低于cm3传导、辐射、自然对流等方法冷却;强迫风冷;~cm3液冷;大于cm3蒸发冷却。
注意这是温升要求40℃时的推荐参考值,如果温升要求低于40℃,就需要对散热方式降额使用,时就需要选择强迫风冷,如果要求温升很低,甚至要选择液冷或蒸发冷却了。
2、散热器的选择这里面还应注意一个问题,是不是强迫风冷能满足散热要求,我们就可以随便选择风扇转速呢,当然不是,风扇的转速与气流流速有直接关系,这里又涉及一个新概念——热阻。
热阻=温度差 / 热耗(单位℃/W)热阻越小则导热性能越好,这个概念等同于电阻,两端的温度差类似于电压,传导的热量类似于电流。
风道的热阻涉及流体力学的一些计算,如果我们在热设计方面要求不是很苛刻,可通过估算或实验得出,如果要求很苛刻,可以查阅《GJB/Z27-92 电子设备可靠性热设计手册》,里面有很多系数、假设条件的组合,三言两语说不清楚,个别系数我也没搞明白如何与现实的风道设计结合,比如,风道中有一束电缆、风道的壁不是均匀的金属板,而是有高低不平带器件的电路板,对一些系数则只能估算了,最准确的方式反而是实验测量了。
热阻更多的是用于散热器的选择,一般厂家都能提供这个参数。
举例,芯片功耗20W,芯片表面不能超过85℃,最高环境温度55℃,计算所需散热器的热阻R。
计算:实际散热器与芯片之间的热阻近似为℃/W,则(R+=(85-55) ℃/20W,则R=℃/W。
依据这个数值选散热器就可以了。
这里面注意一个问题,我们在计算中默认为热耗≈芯片功率,对一般的芯片,我们都可以这样估算,因为芯片中没有驱动机构,没有其他的能量转换机会,大部分是通过热量转化掉了。
而对于电源转换类芯片或模块,则不可以这样算,比如电源,它是一个能源输出,它的输入电量一部分转化成了热,另外很大部分转化成电能输出了,这时候就不能认为热耗≈功率。
3、散热器的设计方法、散热器设计的步骤通常散热器的设计分为三步a:根据相关约束条件设计处轮廓图。
b:根据散热器的相关设计准则对散热器齿厚、齿的形状、齿间距、基板厚度进行优化。
c:进行校核计算。
3.2、自然冷却散热器的设计方法、考虑到自然冷却时温度边界层较厚,如果齿间距太小,两个齿的热边界层易交叉,影响齿表面的对流,所以一般情况下,建议自然冷却的散热器齿间距大于12mm,如果散热器齿高低于10mm,可按齿间距≥倍齿高来确定散热器的齿间距。
、自然冷却散热器表面的换热能力较弱,在散热齿表面增加波纹不会对自然对流效果产生太大的影响,所以建议散热齿表面不加波纹齿。
、自然对流的散热器表面一般采用发黑处理,以增大散热表面的辐射系数,强化辐射换热。
、由于自然对流达到热平衡的时间较长,所以自然对流散热器的基板及齿厚应足够,以抗击瞬时热负荷的冲击,建议大于5mm以上。
3.3、强迫冷却散热器的设计方法3.3.1、在散热器表面加波纹齿,波纹齿的深度一般应小于。
、增加散热器的齿片数。
目前国际上先进的挤压设备及工艺已能够达到23的高宽比,国内目前高宽比最大只能达到8。
对能够提供足够的集中风冷的场合,建议采用低温真空钎焊成型的冷板,其齿间距最小可到2mm。
3.3.3、采用针状齿的设计方式,增加流体的扰动,提高散热齿间的对流换热系数。
3.3.4、当风速大于1m/s(200CFM)时,可完全忽略浮升力对表面换热的影响。
3.4、在一定冷却条件下,所需散热器的体积热阻大小的选取方法3.5、在一定的冷却体积及流向长度下,确定散热器齿片最佳间距的大小的方法3.6、不同形状、不同的成型方法的散热器的热传递效率比较的大小的方法3.7、散热器的相似准则数及其应用方法、相似准则数的定义3.7.2、相似准则数的应用、散热器的基本的优化方法、不同风速下散热器齿间距选择方法、优化散热器齿间距的经验公式及评估风速变化对热阻的影响的经验公式、辐射换热的考虑原则①如果物体表面的温度低于50℃,可忽略颜色对辐射换热的影响。
因为此时辐射波长相当长,处于不可见的红外区。
而在红外区,一个良好的发射体也是一个良好的吸收体,发射率和吸收率与物体表面的颜色无关。
②对于强迫风冷,由于散热表面的平均温度较低,一般可忽略辐射换热的贡献。
③如果物体表面的温度低于50℃,可不考虑辐射换热的影响。
④辐射换热面积计算时,如表面积不规则,应采用投影面积。
即沿表面各部分绷紧绳子求得的就是这一投影面积,如下图所示。
辐射传热要求辐射表面必须彼此可见。
4、风路的设计方法、自然冷却的风路设计机柜的后门(面板)不须开通风口。
底部或侧面不能漏风。
应保证模块后端与机柜后面门之间有足够的空间。
机柜上部的监控及配电不能阻塞风道,应保证上下具有大致相等的空间。
对散热器采用直齿的结构,模块放在机柜机架上后,应保证散热器垂直放置,即齿槽应垂直于水平面。
对散热器采用斜齿的结构,除每个模块机箱前面板应开通风口外,在机柜的前面板也应开通风口。
、强迫冷却的风路设计、设计要点:如果发热分布均匀,元器件的间距应均匀,以使风均匀流过每一个发热源.如果发热分布不均匀,在发热量大的区域元器件应稀疏排列,而发热量小的区域元器件布局应稍密些,或加导流条,以使风能有效的流到关键发热器件。
如果风扇同时冷却散热器及模块内部的其它发热器件,应在模块内部采用阻流方法,使大部分的风量流入散热器。
进风口的结构设计原则:一方面尽量使其对气流的阻力最小,另一方面要考虑防尘,需综合考虑二者的影响。
风道的设计原则风道尽可能短,缩短管道长度可以降低风道阻力;尽可能采用直的锥形风道,直管加工容易,局部阻力小;风道的截面尺寸和出口形状,风道的截面尺寸最好和风扇的出口一致,以避免因变换截面而增加阻力损失,截面形状可为园形,也可以是正方形或长方形;、电源系统典型的风道结构-吹风方式、电源系统典型的风道结构-抽风方式5、热设计的思路以上部分是定量设计部分的内容,在有了一个定量的设计指导后,也有一些具体的工程技巧来帮助实现理论计算结果的要求。
一般的热设计思路有三个措施:降耗、导热、布局。
、降耗降耗是不让热量产生;导热是把热量导走不产生影响;布局是热也没散掉但通过措施隔离热敏感器件;有点类似于电磁兼容方面针对发射源、传播路径、敏感设备的三个措施。
降耗是最原始最根本的解决方式,降额和低功耗的设计方案是两个主要途径,低功耗的方案需要结合具体的设计进行分析,不予赘述。
器件选型时尽量选用发热小的元器件,如片状电阻、线绕电阻(少用碳膜电阻);独石电容、钽电容(少用纸介电容);MOS、CMOS电路(少用锗管);指示灯采用发光二极管或液晶屏(少用白炽灯),表面安装器件等。
除了选择低功耗器件外,对一些温度敏感的特型元件进行温度补偿与控制也是解决问题的办法之一,尤其是放大电路的电容电阻等定量测量关键器件。
降额是最需要考虑的降耗方式,假设一根细导线,标称能通过10A的电流,电流在其上产生的热量就较多,把导线加粗,增大余量,标称通过20A的电流,则同样都是通过10A电流时,因为内阻产生的热损耗就会减小,热量就小。
而且因为降额,在环境温度升高时,器件性能下降情况下,但因为有余量,即使性能下降,也能满足要求,这是降额对于增强可靠性的另一个作用。
、导热导热的设计规范比较多,挑一些比较常见的罗列具体如下:A、进风口和出风口之间的通风路径须经过整个散热通道,一般进风口在机箱下侧方角上,出风口在机箱上方与其最远离的对称角上;B、避免将通风孔及排风孔开在机箱顶部朝上或面板上;C、为防止气流回流,进口风道的横截面积应大于各分支风道截面积之和;D、对靠近热源的热敏元件,采用物理隔离法或绝热法进行热屏蔽。
热屏蔽材料有:石棉板、硅橡胶、泡沫塑料、环氧玻璃纤维板,也可用金属板和浇渗金属膜的陶瓷;E、将散热>1w的零件安装在机座上,利用底板做为该器件的散热器,前提是机座为金属导热材料;F、热管安装在热源上方且管与水平面夹角须>30度;G、PCB用多层板结构(对EMC也有非常非常大的好处),使电源线或地线在电路板的最上层或最下层…H、热源器件专门设计在一个印制板上,并密封、隔离、接地和进行散热处理;I、散热装置(热槽、散热片、风扇)用措施减少热阻:a、扩大辐射面积,提高发热体黑度;b、提高接触表面的加工精度,加大接触压力或垫入软的可展性导热材料;c、散热器叶片要垂直印制板;d、大热源器件散热装置直接装在机壳上;J、密封电子设备内外均涂黑漆可辅助散热;为避免辐射热影响热敏器件、热源屏蔽罩内面的辐射能力要强(涂黑),外面光滑(不影响热敏器件),通过热传导散热;K、密封电子设备机壳内外有肋片,以增大对流和辐射面积;L、不重复使用冷却空气;M、为了提高主要发热元件的换热效率、可将元件装入与其外形相似的风道内;N、抽鼓风冷却方式的选择…O、风机的选择…P、被散热器件与散热器之间充填导热膏(脂),以减小接触热阻;Q、被散热器件与散热器之间要有良好的接触,接触表面光滑、平整,接触面粗糙度Ra≤μm;R、辐射是真空中传热的唯一方法a、确保热源具有高的辐射系数,如果处于嵌埋状态,利用金属传热器传至冷却装置上;b、增加辐射黑度ε;c、增加辐射面积s;d、辐射体对于吸收体要有良好的视角,即角系数φ要大;e、不希望吸收热量的零部件,壁光滑易于反射热。