派克压力传感器使用说明2
Lesker HPT 100 高压差压传感器操作指南说明书

Operating InstructionsHPT 100High Vacuum TransmitterPG0004KJL/G (0509)21.Safety Instructions...............................................................................................32.Understanding The HPT 100 (4)2.1.For Your Orientation ........................................................................................................................42.2.Product Identification (4)Package Contents ...........................................................................................................................42.3.Product Description (5)Connection Options .........................................................................................................................5Proper Use ........................................................................................................................................5Improper Use .. (5)3.Installation (6)3.1.Preparation For Installation ...........................................................................................................63.2.Vacuum Connection ........................................................................................................................63.3.Electrical Connection .....................................................................................................................73.4.Connections Plan.............................................................................................................................83.5.Disassembly (9)4.Operation (10)munication...............................................................................................................................114.3.Transmitter Equalization (13)5.Degas...................................................................................................................146.Error Signals ......................................................................................................147.Maintenance, Service .......................................................................................158.Technical Data (16)8.1.Data List ..................................................................................................................................168.2.Dimensions .............................................................................................................................178.3.Gas Correction Factor .. (17)9.Accessories .......................................................................................................1810.Supplementary Information (19)ContentsPagePlease note:Current operating instructions are also available at 31. Safety Instructions2.3. Product DescriptionThe digital Transmitter HPT 100 enables total pressure measurements in the range of7.5 x 10-10... 750 Torr (1x10-9... 1000 mbar).The transmitter can be operated in conjunction with the Lesker Digital Measuring and Control Units, with the Digital Power Pack and the Windows Measuring Software DokuStar (please see "Accessories") on a PC or with customer related, digital signal evaluation.The transmitter communicates optionally via a Serial Interface RS 232 or RS 485.The individual functions are described in more detail in the section "Communication" .The Transmitter HPT 100 has been tested and accepted in compliance with EN 61010/VDE 0411 ”Safety Equipment For Electrical Components” .Connection OptionsThe HPT 100 provides connection options for:–RS 232/485 (for communication with the display unit) or–Voltage supplyProper UseThe Digital Transmitter HPT 100 serves exclusively to provide total pressure measurements in the range (7.5 x 10-10... 750 Torr (1 x 10-9... 1000 mbar). It may only be connected to components specifically provided for this purpose.Improper UseThe following is regarded as improper:–The use for purposes not covered above and, in particular,–The connection to components not allowed for in their operating instructions;–The connection to components containing touchable, voltage carrying parts.No liability will be accepted for claims arising from improper use.The user bears the responsibility with respect to the process media.53.4. Connection Plan894. Operation4.1. GeneralOnce voltage has been supplied the transmitter is ready to operate. A stabilization time of 5-10 minutes must be considered of. It is usually better to ensure that the transmitter remains in operation all the time.Use Of The Filament Protective PanelDuring normal UHV applications, the transmitter can be operated without the filament protection.When applications are involved where greater levels of contamination are anticipated, the protective panel, which is included, must be used. It is important to observe the necessity for cleanliness when fitting the panel. The conductance value of the transmitter is reduced when the panel is used. In this case, operations should be restricted to 7.5 x 10-6 Torr (1 x 10-5mbar).The measured pressure depends on the type of gas. For matching to various types of gas a respective gas correction factor for the Pirani or Bayard-Alpert unit can be set; this generates the correct measurement value in the pressure range below 7.5 x 10-3 Torr (1x 10-2mbar). The gas type correction factor for air and N2has been set in the works to 1.00 (please also refer to Section 8.3.”Gas Correction Factor”).The transmitter has been factory adjusted. Re-adjustment may be necessary in the event of extreme temperatures or ageing etc. and is carried out with a connected vacuum controller via the PC-Software "DokuStar" or customer specific in accordance with the communication instructions.Please note that before equalization the transmitter must have been in operation for approximately 5 minutes (warm-up time) at the respective pressure. For correct zero point equalization, the pressure in the vacuum chamber must be below 3.75 x 10-5 Torr (5 x 10-5mbar). Baking outIf the bakeout temperature is higher than 60°C (140°F) the electronic unit must be removed. To avoid some mistakes the serial number of the complete unit is fixed up to the transmitter print.1011Answer of transmittera1, a2, a3:Unit address (“001” ... “015”, also see chapter 3.3 )p1, p2, p3:number (see table)I1, I2:data length (see table)data:see table or “NO_DEF”: wrong parameter number, “_LOGIC”: Access fault, “_RANGE”: Out of rangec1, c2, c3:checksum, sum of all ASCII up to checksum modulo (remainder) 256,for example “0120074002=?” => 48+49+50+ ... +61+63=620, 620 modulo 256 = 108 => “108”c R :Carriage return (ASCII code 13)Read request to transmitterFor example the character string and the ASCII code corresponds as follows:4.2. CommunicationThe transmitter communicates via the serial interface with the respective display units (plea-se see "Accessories"), but alternatively can also be controlled directly via the RS 232 or RS 485 by means of the interface protocol.The Interface protocol is in ASCII format which means that all data bytes are representable symbols with an ASCII code ≥32 with the exception of the telegram final symbol carriage return (C R , 13).4.3. Transmitter EqualizationAutomatic alignment in the "ur" range (under range)Starting with instrument version 010500, the alignment is run automatically while simultaneously the following conditions apply:–the pressure of the Bayard-Alpert component is < 5.0 • 10-5mbar.–the measured value of the Pirani component does not change for one minute and does deviate too much from the most recent calibration value.Manually operated alignment when operations via display unit DPG 101 or DPG 109:➡Equalization of the transmitter as described in section 4.4. or 4.5. of the DPG instructions.Manually operated alignment communication via RS 232 or RS 485:➡Evacuate the vacuum system to the pressure of p<1 x 10-5mbar.➡Set the adjusting pressure point [P:741] to «000» for low pressure and transmit.➡Transmit the actual pressure value ([P:740] with «000000» ) for low pressure (represents p < 1.0 • 10-5); ==> ‘’ur’’ (under Range).➡Vent to atmospheric pressure with air or N2; afterwards wait about 10 minutes.➡Set the adjusting pressure point [P:741] to «001» for high pressure and transmit.➡Set the actual pressure value to the atmospheric pressure (e.g. «100023» for 1000 mbar).13146. Error SignalsDeposits on the electrode of the hot cathode tubes can cause instability in themeasurement signals and lead also to increased desorption in the ultra high vacuum range which, in turn, can lead to a too high measured pressure.In such cases it is desirable, at pressures of below 1.5 x 10-6Torr (2 x 10-6mbar), to clean the anode of the transmitter by baking out the adsorbed gas particles. This is carried out (via the connected measuring unit) by starting the Windows Software DokuStar in accordance with thecommunication instructions relating to the degassing procedure. In this way the anode is warmed up by ohmic heat up to 800 °C (1500°F). Although baking out lasts approximately 3minutes, the process can be discontinued at any time beforehand.No transmission of measurement values is possible during the time the transmitter is in degassification mode.5. DegasKurt J.Lesker Company 1925 Worthington Ave Clairton, PA 15025 。
Parker Hannifin Econo-Ram II TM系列线性位置传感器选项说明说明书
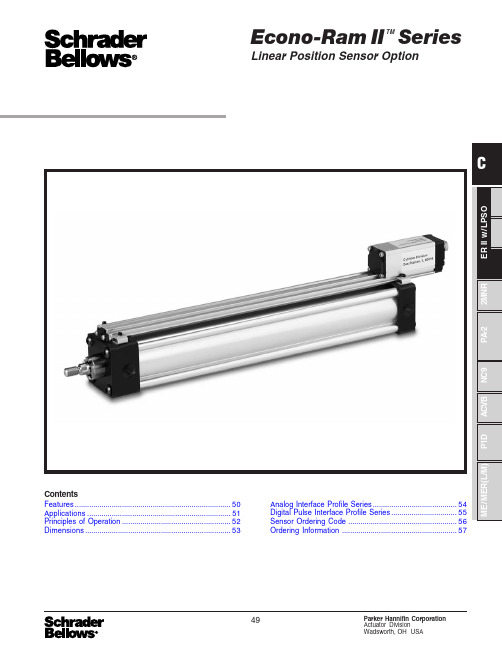
Contents Features (50)Applications (51)Principles of Operation (52)Dimensions.......................................................................53Econo-Ram II TM Series Linear Position Sensor OptionAnalog Interface Profile Series (54)Digital Pulse Interface Profile Series (55)Sensor Ordering Code (56)Ordering Information (57)Econo-Ram II TMSeriesC089Precise Position Feedback Non-Contact Sensing Analog or Digital Outputs Bore Sizes 2" - 8"Available in Eleven Mounting StylesLinear Position Sensor Option forEcono-Ram II TMCylinderFeaturesEcono-Ram II TMSeriesC089–pneumatic cylinders –tooling and tool handling –presses –casting and rolling mills –foundries –injection molding –leveling machines –transport systems –lift controls –level monitoring –tunnel boring equipment–die casting–portal robots–woodworkingmachinery –flight simulators –cutting/slitting machinery –conveying –packaging machines –windmills –elevators–X-Y tables –anywhere linear motion must be monitored!Linear transducers offer features which assure reliable operation in many areas of automation and process technology, even under extreme ambient conditions.Injection Molding MachineWind PowerGeneratorMetal Form PressPaper Cutting MachineBottling MachinePneumatic CylinderInjection Molding MachineStamping ApplicationsApplicationsEcono-Ram II TM SeriesC089Principles of OperationThe measuring element (“waveguide”), consists of a special nickel-alloy tube.A copper conductor is introduced through the length of this tube. The start of measurement is initiated by a short current pulse.This current generates a circular magnetic field which rotates around the waveguide. A permanent magnet at the point of measurement is used as the marker element, whose lines of field run at right angles to the electromagnetic field. In the area on the waveguide where the two fields intersect, a magneto-strictive effect causes an elastic deformation of the waveguide, which propagates along the wave guide in both directions in the form of a mechanical wave.The propagation velocity of this wave in the waveguide is 2830 m/s, and is nearly insensitive to environmental effects (e.g., temperature, shock, contamination).The component of the wave which reaches the far end of the waveguide is damped there, whereas the component which arrives at the signal converter is changed into an electrical signal by reversing the magnetostrictive effect. The wave travel time from its point of origin to the signal converter is directly proportional to the distance between the permanent magnet and the signal converter. A time measurement then allows the distance to be determined with extremely high accuracy.DesignThe transducers are made to the same safety and reliability standards for use in the harshest conditions:– The electronics unit is compactly designed using SMD technology. The boards are protected in a space-saving, rugged aluminum extruded housing.– The waveguide is protected in the extruded aluminum housing.QualityEach and every transducer undergoes a specially designed, computer-controlled testing procedure which includes 100% checking of all specified data.Generation of the ultrasonic torsion pulse in a metallic conductor based on theprinciple of magnetostriction.WaveguideMechanicalwave Initial pulseSignal converter coil (patented process) ReceiverDamping MechanicalwaveElectromagneticfieldPosition markerwith magnetsCopperconductorPrinciples of OperationEcono-Ram II TMSeriesC089Bore Rod DiameterA B Stop Tube LengthA 1B 25/8.95 1.3 1.00 1.312 1/25/8.90 1.25 1.00 1.2513 1/41.64 1.0.750 1.01 3/841.63.99.750.991 3/851.55.79.6250.791 3/86 1 3/8.47.46.500.451 3/481 3/8.28.44.375.441 3/4The drawings below show that the Linear Position Sensor is longer than the cylinder of the same stroke length. The sensor overhang on the head end of the cylinder, as indicated by dimension A, may be eliminated by adding stop tubing, which effectively increases the gross stroke of the cylinder. The recommended stop tube lengths areNO STOP TUBEprovided in the table below for each bore size. The examples show that the electrical stroke of the sensor will always match the net stroke of the cylinder.As a result of the limited sensing range of the sensor, it will overhang at the cap end of the cylinder by the amount of dimension B.Example B: To eliminate sensor overhang on the head end of a 2.0" bore cylinder, add 1.0" of recommended stop tube length.The cylinder gross stroke becomes 13" and the net stroke remains 12". Specify a sensor with an electrical stroke of 12". Note that the electrical stroke equals cylinder net stroke length.Example C: To eliminate sensor overhang on the head end of a 5.0" bore cylinder, add .625" of recommended stop tube length.The cylinder gross stroke becomes 12.625" and the net stroke remains 12". Specify a sensor with an electrical stroke of 12".Note that the electrical stroke equals cylinder net stroke length.No Stop Tube With Stop TubeDimensionsanalog E analogBTL5-E1_-M_ _ _ _-R-S324...20 mA500 Ohm 0.2 µABTL5-E1...BTL5-E1... 4...20 mA 20...4 mA0 V output 10...0 V 0...10 V GND +24 V DC (GND)Specifications subject to change.analog A analog BTL5-A11-M_ _ _ _-R-S320...10 Vmax. 10 mA 5 mV0.1 mVBTL5-ALL ...not used signal GND 10...0 V 0...10 V GND +24 V DC (GND)Output signalTransducer interface Input interface Ordering code Output voltage Output current Load current max. ripple.Load resistance System resolution Hysteresis RepeatabilityOutput update rate max. non-linearityTemperature coefficient Voltage outputCurrent outputShock loading VibrationTraverse velocity of magnet Operating voltage Current drawPolarity reversal protected Overvoltage protection Dielectric constant Operating temperature Storage temperature S32 Pin assignments Pin Color Output signals1 YE2 GY3 PK 5 GN Supply voltage6 BU7 BN8 WHConnect shield to housing.Please enter code for output signal andnominal stroke in ordering code.≥≥≥BTL transducers with analog outputs are available in the ranges of 0...10V, 4...20mA with rising or falling signal.≥Ordering Sample:BTL5-A11-M_ _ _ _-R-SU 022-S32Standard stroke lengths (mm)Output signal 1increasing and decreasing (for A)0increasing7decreasing (for E)4 µm6 µm (hysteresis + resolution)STANDARD = 1 ms 1400 mm±100 µm to 500 mm stroke ±0.02 % 501...3606 mm stroke [150 µV/°C + (5 ppm/°CxPxU/L)]xDT [0.6 µA/°C + (10 ppm/°CxPxI/L)]x DT100 g/11 ms per IEC 68-2-2712 g, 10...2000 Hz per IEC 68-2-6any24 V DC ± 20%150 mAyesTranszorb protection diodes 500 V (Ground to housing)-40...185 °F (-40...85°C)-40...212 °F (-40...100°C)≥≥≥≥M Interface Differential START/STOP control-specific interface.SeriesTransducer interfaceUser interfaceOrdering codeSystem resolutionRepeatabilityResolutionHysteresisStandard sampling ratemax. non-linearityTemperature coefficient of overall system Traverse velocity of magnetOperating voltageCurrent drawOperating temperatureStorage temperatureS32 Pin assignments Pin Color Input/output signals Input1 YEOutput2 GYInput3 PKOutput5 GN Supply voltage6 BU7BN8WH Shield connected to housingBTL5 Low Profilepulse Mpulse MBTL5-M1-M_ _ _ _-R-S 32BTL5-M1-M...INITSTART/STOPINITSTART/STOPGND+24 V DC(GND)BTL5 Low Profilepulse Ppulse PBTL5-P1-M_ _ _ _-R-S 32BTL5-P1-M...INITSTART/STOPINITSTART/STOPGND+24 V DC(GND)Specifications subject to change.Process-dependent/control dependentHysteresis + Resolution2 µm4 µmfSTANDARD = 1 kHz 1400 mm±100 µm to 500 mm nominal stroke±0.02 % 501...3750 mm nominal stroke(6 µm + 5 ppm x L)/°Cany24 V DC ±20 % or ±15V DC ±2% (optional)100 mA-40...185 °F (-40...85°C)-40...212 °F (-40...100°C)≥≥≥≥P Interface Compatible with BTA processors and various OEM controls. Reliable signal transmission, even over cable lengthsup to 500 m (1640ft.) between BTA and BTL, is assured by the especially noise-immune RS485Please enter code for nominal stroke in ordering code.Ordering Sample:BTL5-P1-M_ _ _ _-R-SU 022-S32Standard strokelengths (mm)Output signaldifferential drivers andreceivers. Noise signals areeffectively suppressed.Econo-Ram II TM SeriesC089Output SignalA=E=M=P=Generation 5= 8 pin quick disconnect metal connector= integral axial cable (with 5 m cable; specify length)If A in positionIf E in positionStandard Lengths2005130077401025012760152701788020390230100254110280120305130330150381160407180457200508220560240610260661280711300762320813360914401016421067481220501270601524701778802032902286100254011027941203048Note: Electrical stroke = Net Cylinder StrokeS 3 2K A 0 5Sensor Ordering CodeEcono-Ram II TMSeriesC089How to Order by Model NumberHow to Order by Model Number...Econo-Ram II Series Pneumatic CylindersEcono-Ram II Series air and hydraulic cylinders can be specified by modelnumber by using the tables shown at right.1.TYPESelect the Model Number Code which identifies the single or double rod end air or hydraulic cylinder.2.BORE & ROD DIAMETERSelect the Model Number Code which identifies the desired bore size and rod diameter combination.3.MOUNTING & CUSHIONINGSelect the Model Number Code which identifies the desired mounting style and cushioning option. Cushions available only for air cylinders model FW2 &FX2. Note: Mounting styles with asterisk (*) can be ordered assembled to the cylinder or as a basic (MX0) no-mount cylinder with a bolt on mounting kit as a separate item (1-1/4 - 4" Bores).4.ROD END STYLESelect the Model Number Code which identifies the desired rod end thread style.5.SEAL TYPEComplete the model number by selecting the type of seals desired. Note: Reed or solid state sensors available with standard seals only.6.STROKE LENGTHIt is necessary to specify the stroke length desired following the ModelNumber. For example: FW2B108121 with 6" stroke. Note: Minimum stroke length applies to cylinders ordered with unassembled mounting kits. Seemounting style dimensional tables for appropriate minimum stroke length.THE FW2B108121 EXAMPLE WOULD IDENTIFY:A single rod end air cylinder with 2" bore size, 5/8" diameter piston rod, cap fixed clevis mounting, with a small male rod end thread, Nitrile seals and a 6" stroke.SPECIFYING THE DESIRED TRUNNION LOCATION: (Style MT4 Mounting)For cylinders with intermediate trunnion mounting, specify the distance between the piston rod reference point and the center-line of the trunnion pin (Dimension “XI”).OPTIONAL MOUNTING ACCESSORIES Specify separately by part number the desired optional mounting or rod end accessories.SPECIAL MODIFICATIONSFor special modifications other than piston rod end, use “S” in the 11th position of the model number and describe the special feature required.Example: FW2B108121S with 6" strokeS = Ports to be in position #21Model Number CodeTypeAirHydraulic ▲Single Rod End FW2 FW4Double Rod End FX2FX42Bore Rod Model Size Dia. Number Code 1 1/4"1/2"N501 1/2"5/8"A101"A112"5/8"B101"B112 1/2"5/8"C101"C113 1/4"1"D111 3/8"D124"1"E111 3/8"E125"1"F111 3/8"F126" 1 3/8"G121 3/4"G138"1 3/8"J121 3/4"J133Model Code NumberNFPA Non- Cush.Cush.Cush.Mounting StyleStyle Cush. Head Cap.Both Side End Angles (1-1/4" - 8") MS1*01020304Side Lug (1-1/2" - 8") ▲ MS205060708Side Tapped (1-1/4" - 8") MS413141516Eng Lug Mount (1-1/4" - 4")MS717181920Head Rectangular Flange (1-1/4" - 6") MF1*21222324Cap Rectangular Flange (1-1/4" - 6") MF2*25262728Head Square (8") ME337383940Cap Square (8")ME441424344Tie Rod Extended Both Ends (1-1/4"-8") MX153545556Tie Rod Extended Cap End (1-1/4" - 8") MX257585960Tie Rod Extended Head End (1-1/4" - 8") MX361626364Detachable Pivot Eye (1-1/4" - 4") MP4*65666768Head Trunnion (1-1/2" - 8") ▲ MT169707172Cap Trunnion (1-1/2" - 8") ▲MT273747576Intermediate Fixed Trunnion (1-1/4" - 8") MT477787980Cap Fixed Clevis (1-1/2" - 8") ▲MP1*81828384Cap Detachable Clevis (1-1/4" - 8") MP2*85868788No Mount (BASIC) (1-1/4" - 8") MX093949596Sleeve Nut Mount (1-1/4" - 8") MX597989900Side Tapped withN/AT1T2T3T4Sleeve Nuts (1-1/4" - 8")4Rod End Style Model Code NumberSmall Male 2Short Female 3Intermediate Male 4Special – Specify5Model Seal Type †Code NumberNo Bumpers 1Magnetic Piston 3Bumper-Piston Seal4Nitrile Seals Magnetic Piston6w/Bumper-Piston Seal Bumper Both Ends B Bumper Head End H Bumper Cap EndC Viton Seals26Specify Stroke Length6"NOTE: For cylinders ordered with unassembled mounting kits see minimum stroke length of the dimensional table of the corresponding mounting style.Note: Addition of Bumper (B, H, or C) results in a 1/4"stroke loss per Bumper. For example, a 6" stroke cylinder with Bumpers both ends has an effective stroke of 5-1/2"†Bumpers not available in 1-1/4" Bore.▲Not available in 1-1/4" Bore.How to Order Schrader Bellows Econo-Ram II Cylinders with Sensors:Sensors are not mounted to the cylinder prior to shipment. When ordering a cylinder to accommodate a sensor:1.Derive a proper model number as shown in the table above.e 3 or 6 for Seal Type (step 5).3.If using B, H, or C for Seal Type, then place an “S” in the Special Modification column of the model number and request a Magnetic Piston.4.Order sensors as separate line items.Example:For cylinder prepared for sensor only –FW2B108123 with 6" strokeModel Number Example FW2B108121W/6"Econo-Ram II TMSeriesC089Mounting Mounting Style Mounting DescriptionStyle Mounting Description Code Code MT1Head Trunnion MX0No Mount (Basic)MT2Cap Trunnion MP4†Detachable Pivot Eye MS2Side Lug MP1†Cap Fixed Clevis MS1Single End Angle MP2†Cap Detachable ClevisMS4Side Tapped MS7End Lug MountMF2Cap Rectangular Flange (6"-8" only)Table A – Cylinder Mounting Styles without Stop Tube OptionMounting Mounting Style Mounting DescriptionStyle Mounting Description Code Code MX0No Mount (Basic)MF1Head Rectangular Flange (2"-6")MF2Cap Rectangular Flange (6"-8" only)MX3Tie Rods Extended Head EndMT1Head Trunnion MT2Cap Trunnion MX5Sleeve Nut MountMP4†Detachable Pivot Eye MS2Side Lug MP1†Cap Fixed Clevis MS1Side End Angle MP2†Cap Detachable Clevis MS4Side Tapped ME3Head Square (8")MS7End Lug MountTable B – Cylinder Mounting Styles with Stop Tube Option† For rear clevis mounts MP4, MP1 and MP2, rotation is limited due to sensor interference.† For rear clevis mounts MP1, MP2 and MP4, rotation is limited due to sensor interference.Example Model Number FW2B108123S with 6" stroke S = Install Linear Position Transducer BTL-5-A11-MO127-RSU022S32at Position #1, Ports at Position #2,1" Stop Tube, 5" Net Effective StrokeSensor Ordering CodeStep 1.Create Model Number of Econo-Ram II cylinderutilizing the “How to Order” code on previous page. Make sure of the following:a)2" bore or largerb)Mounting style per tables A or B below c)Seal Type Style 3 or 6d)Add “S” after Seal Type Code Step 2.Create sensor part number from previous pages Step 3.List Cylinder Model Number with commonmodifications below it as follows:a)Sensor part number from previous pages b)Sensor positionc)Port position (if other than position 1)d)Length of stop tubing, gross stroke and net stroke (if required)Air CylindersEcono-Ram II TMSeriesParker Hannifin Corporation Actuator D ivisionWadsworth, OH USA48C089SPLIT WELD ROD BOLT COUPLER PLATE DIA.A B C D E F BOLT SIZE CIRCLE PART NO.PART NO..625 1.50 2.00 .50 .56.2504#10-24 x .94 LG 1.125147234 0062148174 00621.00 2.00 2.50 .50 .88.2506.250-20 x 1.25 LG 1.500147234 010******* 01001.375 2.50 3.00 .63 1.00.2506.312-18 x 1.50 LG 2.000147234 0138148174 01381.753.004.00.631.25.2508.312-18 x 1.75 LG2.375147234 0175148174 0175Table 1 — Part Numbers and DimensionsNote: Screws are not included with safety coupler or weld plate.Flange Style Piston Rod EndSplit Couplers and Weld PlatesWARNING: Piston rod separation from the machine membercan result in severe personal injury or even death to nearby per-sonnel. The cylinder user must make sure the weld holding the weld plate to the machine is of sufficient quality and size to hold the intended load. The cylinder user must also make sure the bolts holding split coupler to the weld plate are of sufficient strength to hold the intended load and installed in such a way that they will not become loose during the machine’s operation.!Catalog AU03-SB0900P-2/NAFlange Style Piston Rod End。
微型压力传感器的使用方法

微型压力传感器的使用方法微型压力传感器是一种可以测量物体表面压力的精密仪器。
它通常由传感器和读数仪两部分组成。
首先,将微型压力传感器放置在需要测量压力的物体表面上。
确保传感器完全接触物体表面,然后将读数仪连接到传感器上。
接下来,打开读数仪并选择所需的测量单位和范围。
对于大多数微型压力传感器,可以选择psi、kPa、bar等测量单位。
开始进行测量前,请确保物体表面没有任何杂质,以免影响测量结果。
然后,轻轻地施加压力在传感器上,使其读数仪显示压力值。
测量完成后,注意将传感器从物体表面上取下。
最后,将读数仪归零并储存数据,以备未来参考。
总的来说,微型压力传感器是一种广泛应用于工业控制、科学研究、医学等领域的重要工具,正确的使用方法可以保证测量结果的准确性和可靠性。
Parker Hannifin 快速连接部门的 SensoControl 诊断仪说明书
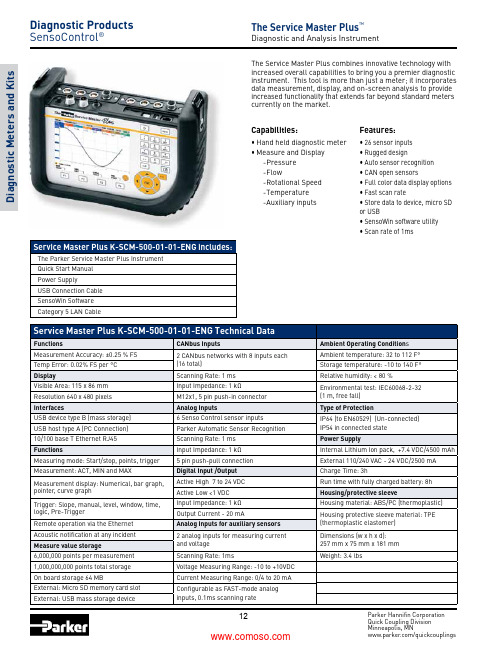
Service Master Plus K-SCM-500-01-01-ENG includes:
The Parker Service Master Plus Instrument Quick Start Manual Power Supply USB Connection Cable SensoWin Software Category 5 LAN Cable
Diagnostic Meters and Kits
Diagnostic Products SensoControl®
The Service Master Plus™
Diagnostic Instrument Kits
Kit Contents:
Case The Parker Service Master Plus Instrument 2 Transducers 2 Transducer Cables (5m CAN or Analog) Power Supply USB Connection Cable SensoWin Software Quick Start Manual Category 5 LAN Cable
Capabilities:
• Hand held diagnostic meter • Measure and Display
-Pressure -Flow -Rotational Speed -Temperature -Auxiliary inputs
Features:
• 26 sensor inputs • Rugged design • Auto sensor recognition • CAN open sensors • Full color data display options • Fast scan rate • Store data to device, micro SD or USB • SensoWin software utility • Scan rate of 1ms
Parker Hannifin Veriflo SQ2Micro高压微型压力调节器产品说明说明书
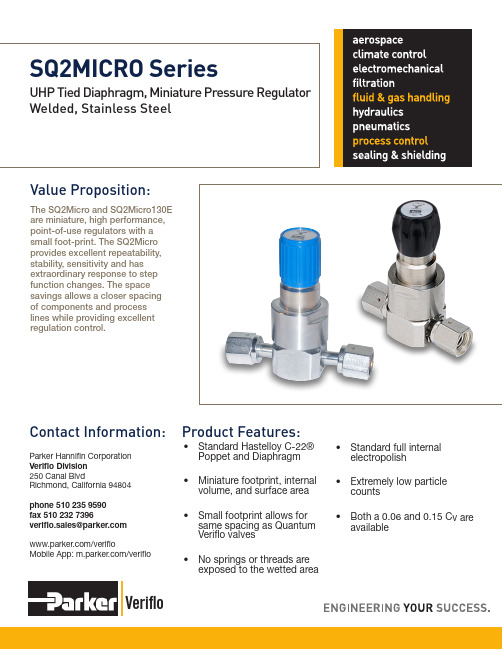
VerifloContact Information:Parker Hannifin Corporation Veriflo Division 250 Canal BlvdRichmond, California 94804phone 510 235 9590fax 510 232 7396************************/verifloMobile App: /verifloValue Proposition:The SQ2Micro and SQ2Micro130E are miniature, high performance,point-of-use regulators with a small foot-print. The SQ2Micro provides excellent repeatability, stability, sensitivity and has extraordinary response to step function changes. The space savings allows a closer spacing of components and process lines while providing excellent regulation control.UHP Tied Diaphragm, Miniature Pressure Regulator Welded, Stainless SteelSQ2MICRO SeriesProduct Features:• Standard full internal electropolish • Extremely low particle counts • Both a 0.06 and 0.15 C v are available• Standard Hastelloy C-22® Poppet and Diaphragm • Miniature footprint, internal volume, and surface area • Small footprint allows for same spacing as Quantum Veriflo valves • No springs or threads are exposed to the wetted areaSQ2MICRO SeriesFlow CurveDimensional DrawingSQ2Micro Flow Curve0.05.010.015.020.025.030.035.040.045.050.00.05.010.015.020.025.030.035.0P S I G O u t l e t P r e s s u r eN 2Flow LPMBOTTOM VIEWø 1.44(36.6 mm)3.54(90 mm)1/4 FSLP1/4 FSHP0.44(11.2 mm)1.25 SQ(31.8 mm)2.78(70.6 mm)0.707 SQ(18 mm)1.00(25.4 mm)4X 10-32UNF-2B“A” Style BodyAdditional flow curves available upon requestBasic Series MICROMICRO130ERange30 = 30 psig60 = 60 psigBody Material= 316L Stainless SteelPorting2P = 2 Ports3P = 3 PortsSee Regulator Porting Guide for additionaloptions and port layoutsPort StyleFS = 1/4” Face SealTS = 1/4” Tube Stub Not availablewith “A” Style bodyConnectionsM = MaleF = FemaleI = Internal Face Seal Availablewith “A” style body onlyOptional FeaturesThis section can have multiple optionsSS = Stainless Steel InternalsIncludes 316L Stainless Steeldiaphragm, compresson memberand poppet. Recommended forCarbonyl Ni(CO)4 ServiceA = “A” Style Body FS Port StyleOnlyTH = Hastelloy C-22® TrimIncludes Hastelloy C-22®diaphragm, compresson memberand poppetVESP = Vespel® Seat Recommendedfor Nitrous Oxide N2O Service1 2 3457134567 SQ2 MICRO 30 2P FS MF TH SQ2M ICRO130E303P FS MIM ASQ2MICRO302PFSMFTHSQ2MICRO130E303PFSMIMASamples:Finished Orders:62Build a SQ2MICRO Series regulator by replacing the numbered symbols with an option from the corresponding tables below.Contact factory for most up to date lead time information.Blue = Configurations that have selections in blue may have an extended lead time and a minimum order quantity.LitPN: 25000242 Rev: J Date of Issue 04/2019© 2009 Parker Hannifin CorporationVerifloOFFER OF SALE:The items described in this document are hereby offered for sale by Parker-Hannifin Corporation, its subsidiaries or its authorized distributors. This offer and its acceptance are governed by the provisions stated in the detailed “Offer of Sale” elsewhere in this document or available at /verifloWARNING USER RESPONSIBILITYFAILURE OR IMPROPER SELECTION OR IMPROPER USE OF THE PRODUCTS DESCRIBED HEREIN OR RELATED ITEMS CAN CAUSE DEATH, PERSONAL INJURY AND PROPERTY DAMAGE. THIS DOCUMENT IS FOR REFERENCE ONLY. PLEASE CONSULT FACTORY FOR LATEST PRODUCT DRAWINGS AND SPECIFICATIONSThis document and other information from Parker-Hannifin Corporation, its subsidiaries and authorized distributors provide product or system options for further investigation by users having technical expertise.The user, through its own analysis and testing, is solely responsible for making the final selection of the system and components and assuring that all performance, endurance, maintenance, safety and warning requirements of the application are met. The user must analyze all aspects of the application, follow applicable industry standards, and follow the information concerning the product in the current product catalog and in any other materials provided from Parker or its subsidiaries or authorized distributors.To the extent that Parker or its subsidiaries or authorized distributors provide component or system options based upon data or specifications provided by the user, the user is responsible for determining that such data and specifications are suitable and sufficient for all applications and reasonably foreseeable uses of the components or systems. The products described herein, including without limitation, product features, specifications, designs, availability and pricing are subject to change by Parker Hannifin Corp and it’s subsidiaries at any time without notice.Proposition 65 Warning: This product contains chemicals known to the state of California to cause cancer or birth defects or other reproductive harm.For additional information on materials of construction, functional performance andoperating conditions, please contact factory.Use mobile device to scan this QR Code.1. Design Pressure per KOSHA Guide D-5 - 2012, Para. 6.2.Vespel® is a registered trademark of DuPont Performance Elastomers L.L.C.Hastelloy C-22® is a registered trademark of Haynes International, Inc.VeriClean™ is a trademark of Parker Hannifin Corporation。
Parker Hannifin公司-MPS-6压力传感器说明书
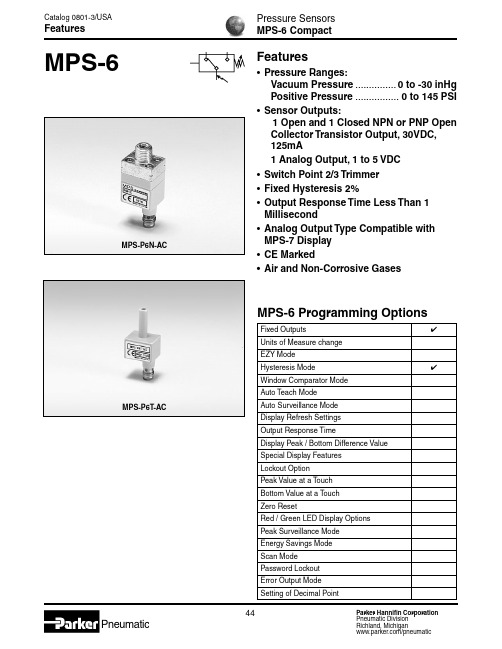
MPS-6 CompactFeaturesFeatures• Pressure Ranges:Vacuum Pressure ...............0 to -30 inHg Positive Pressure ................0 to 145 PSI • Sensor Outputs:1 Open and 1 Closed NPN or PNP Open Collector Transistor Output, 30VDC, 125mA1 Analog Output, 1 to 5 VDC • Switch Point 2/3 Trimmer • Fixed Hysteresis 2%• Output Response Time Less Than 1 Millisecond• Analog Output Type Compatible with MPS-7 Display • CE Marked•Air and Non-Corrosive GasesMPS-6MPS-P6N-ACMPS-6 Programming OptionsFixed Outputs4Units of Measure change EZY Mode Hysteresis Mode4Window Comparator Mode Auto T each ModeAuto Surveillance Mode Display Refresh Settings Output Response TimeDisplay Peak / Bottom Difference Value Special Display Features Lockout Option Peak Value at a T ouch Bottom Value at a T ouch Zero ResetRed / Green LED Display Options Peak Surveillance Mode Energy Savings Mode Scan Mode Password Lockout Error Output Mode Setting of Decimal PointMPS-P6T -ACMPS-6 CompactOrdering Information, SpecificationsSpecificationsMediaAir and Non-Corrosives Gases Pressure Port (N) 1/8" NPT Male, (T) 6mm Tube Stud (Consult Factory for BSPP or BSPT Port)Proof Pressure(V) 72.5 PSI, (P) 217.5 PSI Operating Temperature 32 to 122°F (0 to 50°C)Storage Temperature14 to 140°F (-10 to 60°C)Humidity35 to 85% RHElectrical Connection(C) 4-Pin, M8 ConnectorPower Supply 10.8 to 30 VDC, Ripple Vp-p 10% max., Reverse Voltage Protection Switch Output 1 Output Signal Open and Closed, NPN or PNP , 30VDC, 125mA Linear OutputAnalog Output 1 to 5 VDC Switch Point Setting 2/3 Turn Trimmer Hysteresis Setting < 2% of F .S.Output Response Time<1ms Repeatability <0.2% F .S.Thermal Error 1% over ±25°C (77°C) Temperature Change: Range 32 to 122°F (0 to 50°C)General Protection IP40, CE Marked, EN55011 Class B, EN50082-2Current Consumption< 20mASpike Protection 400 VP , 1 µs, Surge Protection Dielectric Strength 1000VAC, 1min.Insulation Resistance > 100M ohm at 500VDCVibration Resistance 10 to 55Hz, 0.75mm Amplitude, XYZ, 2 hrs.Shock Resistance100 G, XYZMaterial Housing: Polycarbonate, Pressure Port: Zinc Die-cast MassT Port: 0.25 oz. (7g), N, R, G Port: 0.88 oz (25g)MPS-6 Ordering NumbersPressure RangePort SizeOutput CircuitElectrical ConnectorPart Number 0 to -30 inHg1/8 NPSF*PNP Sourcing 4 Pin, M8MPS-V6N-PC NPN Sinking MPS-V6N-NC 1-5VDC analog MPS-V6N-AC 6mm Tube StudPNP Sourcing 4 Pin, M8MPS-V6T -PCNPN Sinking MPS-V6T -NC 1-5VDC analog MPS-V6T -AC 0 to 145 PSI1/8 NPSF*PNP Sourcing4 Pin, M8MPS-P6N-PCNPN Sinking MPS-P6N-NC 1-5VDC analog MPS-P6N-AC 6mm Tube StudPNP Sourcing 4 Pin, M8MPS-P6T -PCNPN Sinking MPS-P6T -NC 1-5VDC analogMPS-P6T -AC* BSPP(G) and BSPT(R) are available. Replace N with G or R for port thread type Example : MPS-V6N-PC (NPT) , MPS-V6G-PC (BSPP) or MPS-V6R-PC (BSPT)Note: T o connect MPS-6 Series Analog Sensor to MPS-7 Series Remote Panel Display, use M8 to AMP Connector Cable CB-M8-4P-2E.CB-M8-4P-2EMPS-6 Compact Technical InformationDC10.8V to 30VDC10.8V to 30VAnalog PNP Open CollectorInternal CircuitCautionsThe MPS-6 Pressure Sensor is designed to monitor pressureand is not a safety measure to prevent accidents.The compatibility of the sensor is the responsibility of thedesigner of the system and specifications.Operating Environment• Parker / Convum Sensors have not been investigated forexplosion-proof construction in hazardous environments.• Do not use with flammable gases, liquids, or in hazardousenvironments.• Avoid installing the sensor in locations where excessivevoltage surges could damage or affect the performance ofthe sensor.Operations• Dedicate a power supply of 10.8 to 30VDC to the sensorand set the ripple to Vp-p10% or less. Avoid excessivevoltage. Avoid voltage surges.• A small amount of internal voltage drop is possible. Ensurethe power supply minus any internal voltage drop exceedsthe operating load.• Verify the operating media is compatible with thespecified sensor. Check the chemical make-up, operatingtemperatures, and maximum pressure ranges of thesystem before installing.• Installation of air dryer system is recommended to removemoisture.!Installation• Never insert an object into the pressure port other than anappropriate fluid connector.• Avoid short-circuiting the sensor. Connect the brown leadto V+ and blue lead to 0V.• Do not connect the output lead wires (black / white) to thepower supply.• Outputs not being used should be trimmed and insulated.Trimmer AdjustmentRotate the potentiometer trimmer to increase or decreasepressure switch point output. Excessive force or exceedingthe limits of the trimmers may cause damage.Sensor Pin Out with Analog Output Sensor Pin Out2143P in #1 Brown: 24VDC2 White: LED In 5VDC3 Blue: 0VDC4 Black: Analog 1 to 5VDCP in #1 Brown: 24VDC2 White: NPN / PNP Open Collector Output3 Blue: 0VDC4 Black: NPN / PNP Open Collector Output2143MPS-6 Compact DimensionsDimensionsN, R, G1/8" Male,M5 Female,M8, 4-PinT6Tube Stud,M8, 4-PinCables4-Pin, M82413Cable Pin Color1 Brown2 White3 Blue4 Black 4-Pin, M824134-Pin, M123421Accessories。
压力传感器ISE30-01-65(中文)

压力传感器的简要使用说明ISE30-01-65(PNP)型一、模式设置1、长按2秒以上 SET 键进入单位的设置;按左(右)键选择:MPa - Kgf/cm - bar - psi(我们选用 bar)2、按 SET 键进入颜色设置;显示 Sor(我们选用:绿色SoG)3、按一下 SET 键进入操作模式选择显示 HyS ,按左(右)键选择 HyS<P1> 或 wnd<P1,P2>单阀值模式上限和下限值模式(我们一定选用默认 HyS)4、按一下 SET 键进入输出模式选择显示 NO ,按左(右)键选择 NO 或 NC常开模式常闭模式(我们默认选用 NO)5、按一下 SET 键进响应时间设置显示2.5 , 按左(右)键选择2.5 - 20 - 160 - 640 - 1280(ms),(我们选用 1280)6、按 SET 键进入调整设置显示 mAn , 按左(右)键选择 mAn 或 AUT手动调整自动调整(我们一定选用默认 mAn)按 SET 键进入阀值设置交替显示 P1 和某一数字,按左(右)键选择调整数值;按 SET 调整数字的位, H值默认按 SET 确认。
二、值(设定值)设置方法在常态下点按 SET 键,交替显示 P1 和某一数字,按左(右)键选择调整数值;按 SET 调整数字的位。
调整好数秒后 P1和阀值互闪,按 SET 确认。
三、锁的设定;为了防止误操作引起设定值的变化要进行锁的设定。
方法:常按 SET 键4秒以上直到显示“Loc”或“Unl”上锁解锁按左(右)键选择 Loc 和 Unl。
注:1 环境温度:0-50度(C)时,为有效的检测范围。
2 设定检测数值时,有真正、负值的区别,在最左位“”或“”将闪动“”闪动是…+‟;“”闪动是…-‟。
3 需重新调整零点时,在显示当前压力的画面下,要同时按左键和右键即可调零。
Parker Hannifin MPS-2压力传感器说明书

MPS-2 VersatileFeaturesMPS-R2M5-NGRMPS-2Features• Pressure Ranges: Vacuum Pressure ..................0 to -30 inHg Compound Pressure .......-14.7 to 72.5 PSI • Sensor Outputs:2 NPN or PNP Open Collector Transistor Output , 30VDC, 125mA• Hysteresis or Window Comparator Mode • 4 Selectable Units of Measure (mmHg, -bar, -kPa, inHg) (kgf/cm 2, PSI, bar, kPa)• Output Response Time Less Than 2.0 Milliseconds • CE Marked• Air and Non-Corrosive Gases • Error MessageMPS-2 Programming OptionsOutputs Change N.O. / N.C.4Units of Measure change 4EZY Mode 4Hysteresis Mode4Window Comparator Mode4Auto Teach Mode 4Auto Surveillance Mode 4Display Refresh Settings 4Output Response Time4Display Peak / Bottom Difference Value 4Special Display Features 4Lockout Option 4Peak Value at a Touch 4Bottom Value at a Touch 4Zero Reset4Red / Green LED Display Options Peak Surveillance Mode Energy Savings Mode 4Scan Mode Password Lockout Error Output Mode Setting of Decimal PointMPS-V2N-PCOrdering Information, SpecificationsMPS-2 VersatileSpecificationsPressure RangeVacuum (V)Compound (R)Units of Measure Display Resolution bar:0.001bar:0.01kPa: 0.1kPa:1mmHg: 1kgf/cm 2: 0.01inHg:0.1PSI:0.1MediaAir and Non-Corrosive GasesPressure Port (N) 1/8" NPT, (M5) M5 Female (Consult Factory for BSPP or BSPT Port)Proof Pressure(V) 72.5 PSI, (R) 116.0 PSI Operating Temperature 32 to 122°F (0 to 50°C)Storage Temperature14 to 140°F (-10 to 60°C)Humidity35 to 85% RHElectrical Connection(C) 4-Pin, M8 Connector, (G) 2m Grommet Open LeadPower Supply10.8 to 30VDC, Ripple Vp-p 10% Max., Reverse Voltage Protection Display3-Digit, 7-Segment LEDDisplay Refresh 0.1 to 3.0 sec. (Factory set at 0.1)Output Circuit NPN (Sinking) or PNP (Sourcing) Output, Open Collector T ransistor 30VDC, 125mA Switch Output 2 Output Signals, NPN or PNP , Normally Open or Closed, LED Indicator Output Modes Hysteresis or Window ComparatorResponse Time < 2ms, with Programmable Increments 32, 128, 1024ms Repeatability ± 0.2% F .S.Thermal Error 1% over ±25°C (77°C) Temperature Change: Range 32 to 122°F (0 to 50°C)General Protection IP65 or IP40, CE Marked, EMC-EN55011 Class B, EN 50082-2Insulation Resistance > 100M ohms at 500VDC Vibration Resistance 10 to 55Hz, 1.5mm, XYZ, 2 hrs.Shock Resistance10 G, XYZMaterial Housing: Polycarbonate, Pressure Port: Zinc Die-cast Mass1.58 oz. (45g)MPS-2 Ordering NumbersPressure RangePort Size Output CircuitElectrical ConnectorPart Number 0 to -30 inHg1/8 NPT*, Male, M5 FemalePNP Sourcing 4 Pin, M8MPS-V2N-PC NPN Sinking MPS-V2N-NC -14.7 to 72.5 PSIPNP Sourcing 4 Pin, M8MPS-R2N-PC NPN SinkingMPS-R2N-NC M5 DIN Rail MountingPNP Sourcing 2M Lead WireMPS-R2M5-PGR NPN SinkingMPS-R2M5-NGR* BSPP(G) and BSPT(R) are available. Replace N with G or R for port thread type Example : MPS-V2N-PC (NPT) , MPS-V2G-PC (BSPP) or MPS-v2R-PC (BSPT)MPS-2 VersatileTechnical Information!NPN Sinking PNP SourcingInternal Circuit–INCLUDED–Cautions The MPS-2 Pressure Sensor is designed to monitor pressure and is not a safety measure to prevent accidents.The compatibility of the sensor is the responsibility of the designer of the system and specifications.Operating Environment• Parker / Convum Sensors have not been investigated for explosion-proof construction in hazardous environments.• Do not use with flammable gases, liquids, or in hazardous environments.• Avoid installing the sensor in locations where excessive voltage surges could damage or affect the performance of the sensor.Operations• Dedicate a power supply of 10.8 to 30VDC to the sensor and set the ripple to Vp-p10% or less. Avoid excessive voltage. Avoid voltage surges.• A small amount of internal voltage drop is possible. Ensure the power supply minus any internal voltage drop exceeds the operating load.• Verify the operating media is compatible with thespecified sensor. Check the chemical make-up, operating temperatures, and maximum pressure ranges of the system before installing.• Installation of air dryer system is recommended to remove moisture.Installation• Never insert an object into the pressure port other than an appropriate fluid connector.• Avoid short-circuiting the sensor. Connect the brown lead to V+ and blue lead to 0V .• Do not connect the output lead wires (black / white) to the power supply.• Outputs not being used should be trimmed and insulated.• Install as shown using the metal mounting base.• To achieve IP65 rating, connect the o-ring and barb as shown to a normal environment with a 2mm I. D. tube.2143P in #1 Brown: 24VDC2 White: NPN / PNP Open Collector Output 23 Blue: 0VDC4 Black: NPN / PNP Open Collector Output 1Sensor Pin OutLead WiringBrown V+White NPN / PNP Output 2Blue 0VBlackNPN / PNP Output 1Error MessagesDisplay DescriptionSolutionsErr Zero Reset Error Reset Zero Below 3% of F .S. Er1System Error (Internal)Contact Factory Er2Auto Teach Mode Error Restart Function CE1Over current of Output 1Load current exceeds maximum 125mA. CE2Over current of Output 2FFF –FFApplied pressure exceeds pressure rangeApply pressures within the rating of the sensorDimensionsMPS-2 VersatileDimensionsProgramming Features MPS-2 Versatile See last page of this PDF for Symbol Explanation.AccessoriesMPS-2 VersatileMPS-ACCK4Din RailAccessoriesCablesProgramming Symbols Legend Technical DataPressure Value Display Mode. Displays Pressure for a specific time period and then updates for next time periodTime Range for Pressure Value Display Mode Value Setting for Pressure Value Display Mode Display Peak Value over selected time range Display Bottom Value over selected time range Display Difference over selected time range Display Function Mode. On/OffDisplay Function. Selects display types.Display blinks pressure when Output 1 is Passing Normal when Output 1 is Non-PassingDisplay blinks pressure when Output 2 is Passing Normal when Output 2 is Non-PassingDisplay shows pressure when Output 1 is Passing Display shows special screen when Non-Passing Display shows pressure when Output 2 is Passing Display shows special screen when Non-Passing Select Switch Output setting for MPS-31Color Setting for MPS-31MPS-4, Port Reference SelectionMPS-4, Display change of B port to A port static MPS-4, Display change of A port to B port staticMPS-4, Display change of A port tochange of B portMPS-7, Pressure Range Selection Vacuum MPS-7, Pressure Range Selection Low PressureMPS-7, Pressure Range SelectionPositive PressureMPS-7, Pressure Range Selection Compound PressureMPS-7, Energy Savings Mode, reduces current consumptionMPS-7, Peak SurveillanceDigital Input Sensors Only. Digital Input Mode for remote Zero reset of sensorsDigital InputDigital ChannelMPS-7 Scan Mode. Sensor scans and displays each channel for 3 sec.Locked. Sensor programs cannot be changed Unlocked. Sensor programs can be changedSets Sensors reference point to current atmospheric conditions。