增韧理论
增韧理论

增韧理论塑料共混改性的一个重要内容是提高一种塑料的韧性,使其满足使用场合和环境对材料韧性的要求。
比较成熟的是橡胶(弹性体)增韧塑料技术,但近几年也发展了非弹性体增韧技术,如无机刚性粒子增韧塑料等。
(1) 弹性体增韧机理弹性体直接吸收能量,当试样受到冲击时会产生微裂纹,这时橡胶颗粒跨越裂纹两岸,裂纹要发展就必须拉伸橡胶,橡胶形变过程中要吸收大量能量,从而提高了塑料的冲击强度。
(2) 屈服理论橡胶增韧塑料高冲击强度主要来源于基体树脂发生了很大的屈服形变,基体树脂产生很大屈服形变的原因,是橡胶的热膨胀系数和泊松比均大于塑料的,在成型过程中冷却阶段的热收缩和形变过程中的横向收缩对周围基体产生静水张应力,使基体树脂的自由体积增加,降低其玻璃化转变温度,易于产生塑性形变而提高韧性。
另一方面是橡胶粒子的应力集中效应引起的(3)裂纹核心理论橡胶颗粒充作应力集中点,产生了大量小裂纹而不是少量大裂纹,扩展众多的小裂纹比扩展少数大裂纹需要较多的能量。
同时,大量小裂纹的应力场相互干扰,减弱了裂纹发展的前沿应力,从而,会减缓裂纹发展并导致裂纹的终止。
(4)多重银纹理论由于增韧塑料中橡胶粒子数目极多,大量的应力集中物引发大量银纹,由此可以耗散大量能量。
橡胶粒子还是银纹终止剂,小粒子不能终止银纹。
(5)银纹-剪切带理论这是业内普遍接受的一个重要理论。
大量实验表明,聚合物形变机理包括两个过程:一是剪切形变过程,二是银纹化过程。
剪切过程包括弥散性的剪切屈服形变和形成局部剪切带两种情况。
剪切形变只是物体形状的改变,分子间的内聚能和物体的密度基本不变。
银纹化过程则使物体的密度大大下降。
一方面,银纹体中有空洞,说明银纹化造成了材料一定的损伤,是亚微观断裂破坏的先兆;另一方面,银纹在形成、生长过程中消耗了大量能量,约束了裂纹的扩展,使材料的韧性提高,是聚合物增韧的力学机制之一。
所以,正确认识银纹化现象,是认识高分子材料变形和断裂过程的核心,是进行共混改性塑料,尤其是增韧塑料设计的关键之一。
塑料增韧机理
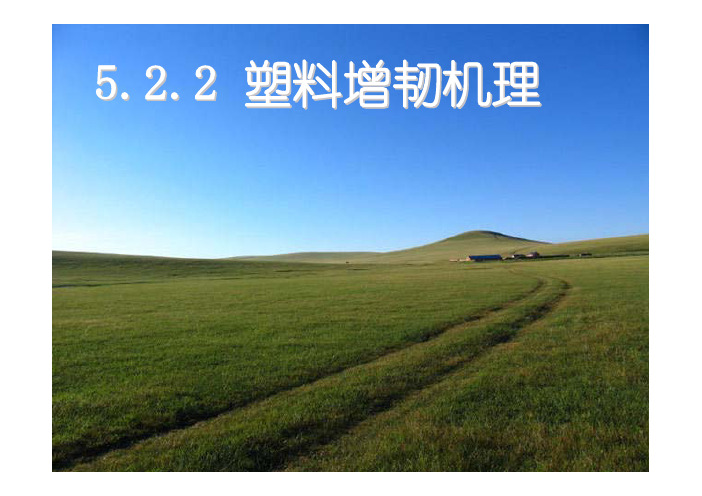
25
③弹性体增韧剂玻璃化转变温度的影响
一般而言,弹性体的Tg越低,增韧效果越好,见表。 这是由于在高速冲击载荷作用下,橡胶相的Tg会有显
著提高。 对于在室温下使用的增韧塑料,橡胶的Tg要比室温低
40~60℃才会产生显著的增韧效应。/
26
④增韧剂与基体树脂界面的影响
对于弹性体增韧塑料,界面粘接强度对增韧效果的影 响,不同的体系趋势不同。
13
不足之处
未能提供银纹终止详细机理 橡胶颗粒引发多重银纹缺乏严格数学处
理
14
5.2.3影响增韧效果的因素
可以从三个方面考虑: 基体树脂的特性, 增韧剂的特性和用量, 两相间的结合力。/
15
(1)基体树脂的特性
¾许多研究表明,提高基体树脂的韧性有利于提高增韧塑 料增韧效果。 ¾提高基体树脂韧性的主要方法有3种。
银纹支化理论 1971年 ,
Wu氏理论等。
提出了增韧塑料脆韧转变的临界 粒间距普适判据的概念,对热塑 性聚合物基体进行了科学分类。5
弹性体直接吸收能量理论 1956年
试样收到冲击→裂纹 橡胶颗粒横跨裂纹,裂纹发展必须拉伸橡
胶颗粒→吸收大量能量→冲击强度提高
不足: 所吸收能量不足冲击能 的1/10 气泡及小玻璃珠之类的 分散有时有增韧效应
有些增韧体系,界面粘接强度大,可有效减小分散相 粒径,在增韧剂含量相同的情况下,分散相粒子数增 多,减少了基体层厚度,有利于增韧。
例如: PVC与聚丁二烯共混,由于二者完全不相容,界面粘
接极弱,冲击强度很低;/
27
对于PVC/NBR共混体系,随着 NBR 中 AN 含 量 增 加 , NBR 与PVC 的相容性增加,
热塑性弹性体增韧聚合物理论介绍

热塑性弹性体增韧聚合物理论介绍增韧机理的研究最早开始于上世纪50年代,人们从脆性基体与橡胶分散相所组成的物理模型出发,围绕着橡胶相如何增韧机理而展开。
纵观增韧理论的发展,它主要经历了微裂纹理论、多重银纹理论、剪切屈服理论和银纹-剪切带理论等阶段。
目前被人们较普遍接受的是银纹-剪切带理论。
1、微裂纹理论最早用来解释橡胶增韧塑料的几个假设之一曾认为:橡胶通过力学阻尼来吸收冲击能量,Bucknall等最先观察到由橡胶所贡献的二级损耗峰,并发现其他许多不含橡胶的韧性聚合物在室温下也具有明显的二级损耗峰。
不过阻尼虽可以解释冲击中的某些能量吸收,但未考虑应力发白和大应变的形变。
1956年Mertz等人首次提出了聚合物增韧的理论,该理论认为作为增韧体的部分橡胶粒子会横跨在材料变形所产生的很多细微的裂缝上,阻止其继续发展,而橡胶在变形过程中消耗了能量,从而提高了材料的韧性。
该理论重视了橡胶相而忽视了母体。
如橡胶粒子吸收能量的示意图,假设橡胶粒子处于增长中的裂缝的迎面,以致在冲击中吸收的能量等于玻璃态母体断裂能和破碎橡胶粒子所做功的总和。
但是Newman和Strellla经计算表明:橡胶在拉伸过程中吸收的能量是很少的,仅占材料破坏时吸收能量的1/10,同时实验表明韧性的提高和塑料基体有关,例如,当PVC和ABS共混时,PVC分子量的提高,显著的有利于共混材料冲击强度的提高。
所以,如把增韧塑料的韧性完全归因于橡胶粒子的作用,就不完全符合事实了。
因而该理论并未揭示橡胶增韧的本质原因。
2、多重银纹理论1965年由Bucknall和Smith提出的多重银纹理论是Mertz等人微裂纹理论的发展。
该理论认为在橡胶增韧塑料体系中,橡胶相颗粒起了应力集中的作用。
当材料受到冲击时,它能引发大量的银纹,大量银纹之间的应力场将发生相互干扰,如果发生的银纹前峰处的应力集中低于临界值或银纹遇到另一橡胶颗粒时,银纹就会终止,橡胶相粒子不仅能引发银纹而且能控制银纹。
提高强度、韧性、塑性的理论

0.80 0.79
0.75
0.84 0.84
。
0.86 0.84
0.89 0.88
0.89 0.88
0.89 0.89
0.70 0℃
500℃
550℃
600℃
650℃
680℃
回火温度/℃
(a) 1#、2#钢
屈强比
屈服强度/MPa
800
Mn+Cr含量和:
1#-1.01%
2#-1.18%
700
• C下降,Mn 增加 • 0.1Mn: 10MPa, 高Mn韧性好,耐HIC差 • 0.1Cr: 10MPa,耐大气腐蚀,抗HIC
• 400-500MPa级:1.5Mn • 550-690MPa级:1.8-2.1Mn • Mn偏析!焊接性能?
C-Mn-Cr-0.1Nb钢回火性能(HIC管线)
抗拉强度/MPa
TMCP工艺对性能的影响
热加工工艺对强韧化的影响
经热处理的C-Mn钢的夏比冲击试验韧性变化
板材厚度:20mm,CVR:传统热轧,N:正火,Q-T:淬火和回火
微合金元素Nb在钢板中的作用
在加速冷却钢中,微合金元素对贝氏体体积分数和α晶粒尺寸 的影响
基本组成:0.10C-0.25Si-1.50Mn。钢被再加热到1200℃并在冷却前控轧
σs σb δ
100mm厚1000MPa级直接淬火与回火板材
具有无需预热可焊接性的610MPa级板材,直接淬火与回火 (CR-DQ-T)和传统再加热—淬火和回火(RQ-T)两种工艺下的
化学成分
回火温度对直接淬火以及再加热淬火钢强度的影响
●:通过CR-DQ-T处理的含Nb钢 ○:通过RQ-T处理的无Nb 钢
聚合物强增韧化机制及测量原理简介1

聚合物强增韧化机制及测量原理简介聚合物的强韧化一直是高分子材料科学的重要研究领域,通过将有机或无机的大分子或小分子材料,采用物理或化学的方法加入高分子基体中,提高力学及其它性能。
自从上世纪50年代首次提出聚合物的增韧理论,人们利用增韧的方法研发了大量新型高聚物材料,性能较均聚物材料有很大提高。
实际上聚合物增韧的根本问题就是通过引入某种机制,使材料在形变、损伤与破坏过程中耗散更多的能量。
聚合物增韧经历了从弹性体到非弹性体增韧的过程,传统的增韧改性是以橡胶类弹性体材料作为增韧剂,以适当方式分散到塑料基体中以达到增韧目的,如高抗冲聚苯乙烯(HIPS),乙丙共聚弹性体增韧聚丙烯,粉末NBR增韧PVC等,但存在难以克服的问题,如刚度、强度、热变形温度都有较大幅度降低,于是1984年国外首次提出了以非弹性体增韧的新思想。
这种方法可以在提高基体韧性的同时提高材料的强度、刚性和耐热性,且无加工性能下降的不足,达到既增韧又增强的目的,克服了弹性体增韧出现的问题。
以增韧方法的发展为主线,介绍增韧剂从弹性体到非弹性体、从微米到纳米尺度变化,对材料的强韧结构与性能的影响,并通过对其增韧后的力学性能、微观结构形态的分析,衍生相应的的增韧机理。
脆性断面韧性断面图1- 1 典型脆-韧性材料的拉伸行为及断面形貌§1 弹性体增韧增韧机理的研究最早开始于上世纪50年代,人们从脆性基体与橡胶分散相所组成的物理模型出发,围绕着橡胶相如何增韧机理而展开。
纵观增韧理论的发展,它主要经历了微裂纹理论、多重银纹理论、剪切屈服理论和银纹-剪切带理论等阶段。
目前被人们较普遍接受的是银纹-剪切带理论。
随着增韧理念的发展,增韧理论由传统的定性分析进入了定量分析的阶段,主要是Wu 提出了橡胶粒子增韧的T判据,建立了橡胶粒子增韧的逾渗模型,对增c韧理论的定量化研究提供了一个新的思路。
粒子与纤维增韧橡胶粒子的变形与破裂银纹与剪切带空穴与脱粘图1- 2 橡胶增韧机理的示意图§1.1微裂纹理论最早用来解释橡胶增韧塑料的几个假设之一曾认为:橡胶通过力学阻尼来吸收冲击能量,Bucknall[]i等最先观察到由橡胶所贡献的二级损耗峰,并发现其他许多不含橡胶的韧性但载荷未考虑应力发白图1- 3 橡胶粒子吸收能量的示意图和大应变的形变。
增韧原理

●延性颗粒增韧
在脆性陶瓷基体中加入第二相延性颗粒能明显提 高材料的断裂韧性。其增韧机理包括由于裂纹尖 端形成的塑性变形区导致裂纹尖端屏蔽以及由 延性颗粒形成的延性裂纹桥。当基体与延性颗 粒的和E值相等时,利用延性裂纹桥可达最佳增 韧效果。但当和E值相差足够大时,裂纹发生偏 转绕过金属颗粒,增韧效果较差。
●纤维桥接(Fiber
Bridge)
对于特定位向和分布的纤维,裂纹很难偏转,只能沿着原 来的扩展方向继续扩展。这时紧靠裂纹尖端处的纤维并未断裂, 而是在裂纹两岸搭起小桥,使两岸连在一起。这会在裂纹表面 产生一个压应力,以抵消外加应力的作用,从而使裂纹难以进 一步扩展,起到增韧作用。随着裂纹的扩展,裂纹生长的阻力 增加,直到在裂纹尖端形成一定数量的纤维搭桥区。这时达到 一稳态韧化
●裂纹弯曲(Crackbowing)和偏转
在颗粒和短纤维(晶须)增强复合材料起到使裂纹中,裂纹扩展 时会发生偏转,从而增加复合材料(MMC、CMC)的韧性。如果在 复合材料(CMC)中预先存在有微裂纹,则这些微裂纹同样起到引 导裂纹发生偏转的作用,从而增加复合材料的韧性。
增强体的长径比越大,裂纹偏转增韧效果就越好
●裂纹偏转和裂纹桥联增韧
裂纹桥联是一种裂纹尾部效应。它发生在裂纹尖端,靠桥联 元(剂)连接裂纹的两个表面并提供一个使裂纹面相互靠近 的应力,即闭合应力,这样导致强度因子随裂纹扩展而增加。 裂纹桥联可能穿晶破坏,也有可能出现互锁现象,即裂纹绕 过桥联元沿晶发展(裂纹偏转)并形成摩擦桥。裂纹桥联增 韧值与桥联元(剂)粒径的平方根成正比。
●相变增韧
所谓“相变增韧”,实际上也是利用微裂纹增韧,即利用所谓的增 韧相产生相变,由于相变丝引起的膨胀,从而引起基体相产生微裂纹。 相变增韧的典型例子是ZrO2增韧。由于ZrO2存在两种晶型:四方相 (t)和单斜相(m),当ZrO2由四方相转变为单斜相时,具有马氏体 相变特征,伴随产生有3~5%的体积膨胀。相变温度大多处于陶瓷 材料的烧结温度范围,如基体是Al2O3,加入ZrO2 ,相变引起体积 变化,造成应力,引起基体产生微裂纹,微裂纹的出现,就增加了 Al2O3材料的韧性(相应的,材料的强度有所下降)。 氧化锆增韧陶瓷有三种:
acr增韧机理

acr增韧机理ACR增韧机理可以分为物理增韧机理和化学增韧机理两方面。
物理增韧机理主要是通过改变聚合物的结构和排列方式,增加材料的强度和韧性,而化学增韧机理则是通过引入增韧剂,改变材料的化学性质来增加材料的韧性。
在物理增韧机理方面,ACR(Acrylic rubber)增韧可以通过增加聚合物链的交联密度来提高材料的强度和韧性。
交联是指聚合物链之间形成网络结构,从而增加材料的整体强度和刚性。
在ACR中,通过引入交联剂,如双丙烯酸丁二酯(BD)或者聚合物后期交联,可以增加ACR的交联密度,提高材料的强度和韧性。
此外,物理增韧机理中还有相分离增韧机理。
当ACR中引入亲相分离增韧剂时,这些增韧剂会在材料中形成分散相或者粒子,从而改变了ACR的相结构和排列方式。
相分离的形成可以增加ACR中的界面面积,提高材料的强度和韧性。
同时,相分离的形成还可以阻碍裂纹传播,增加材料的抗裂纹扩展能力,从而提高材料的韧性。
在化学增韧机理方面,ACR的化学结构可以通过改变聚合物链上的官能团,引入增韧剂来增加材料的韧性。
例如,使用改性聚丙烯酸酯或改性丁基橡胶作为增韧剂,可以通过与ACR的聚合物链进行交联反应,形成网状结构,从而增加ACR的韧性。
此外,通过引入共聚物或者结晶增韧剂,可以改变ACR的分子结构和排列方式,提高材料的韧性。
对于ACR的增韧机理,还需要考虑材料的分子链长度和分子量分布。
一般来说,较长的分子链和较窄的分子量分布可以提高材料的韧性,因为分子链更容易在应力作用下进行重排,从而形成更强大的网络结构。
除了上述的物理和化学增韧机理,ACR的韧性还可以通过改变材料的配方和加工工艺来得到提高。
例如,合理的添加负载剂和填充剂可以增加ACR的强度和韧性,同时改变ACR的配方可以调节材料的硬度和弹性模量,从而适应不同应用领域的需求。
总的来说,ACR的增韧机理主要包括物理增韧和化学增韧两方面。
物理增韧可以通过增加聚合物链的交联密度和改变材料的相分离结构来提高强度和韧性,而化学增韧则是通过引入增韧剂,改变材料的化学结构来增加韧性。
增韧理论

增韧理论塑料共混改性的一个重要内容是提高一种塑料的韧性,使其满足使用场合和环境对材料韧性的要求。
比较成熟的是橡胶(弹性体)增韧塑料技术,但近几年也发展了非弹性体增韧技术,如无机刚性粒子增韧塑料等。
(1) 弹性体增韧机理(2) 屈服理论(3)裂纹核心理论(4)多重银纹理论(5)银纹-剪切带理论这是业内普遍接受的一个重要理论。
大量实验表明,聚合物形变机理包括两个过程:一是剪切形变过程,二是银纹化过程。
剪切过程包括弥散性的剪切屈服形变和形成局部剪切带两种情况。
剪切形变只是物体形状的改变,分子间的内聚能和物体的密度基本不变。
银纹化过程则使物体的密度大大下降。
一方面,银纹体中有空洞,说明银纹化造成了材料一定的损伤,是亚微观断裂破坏的先兆;另一方面,银纹在形成、生长过程中消耗了大量能量,约束了裂纹的扩展,使材料的韧性提高,是聚合物增韧的力学机制之一。
银纹的一般特征如下:1.银纹是在拉伸力场中产生的,银纹面总是与拉伸力方向垂直;在压力场中不会产生银纹;Argon的研究发现,在纯剪切力场中银纹也能扩展。
2.银纹在玻璃态、结晶态聚合物中都能产生、发展。
3.银纹能在聚合物表面、内部单独引发、生长,也可在裂纹端部形成。
4.在单一应力作用下引发的银纹,成为应力银纹。
5.银纹的外形与裂纹相似,但与裂纹的结果明显不同。
裂纹体中是空的,而银纹是由银纹质和空洞组成的。
空洞的体积分数为50%70%。
银纹质取向的高分子和/或高分子微小聚集体组成的微纤,直径和间距为几到几十纳米,其大小与聚合物的结构、环境温度、施力速度、应力大小等因素有关。
银纹主微纤与主应力方向呈某一角度取向排列,横系的存在使银纹微纤也构成连续相,与空洞连续相交织在一起成为一个复杂的网络结构。
横系结构使得银纹有一定横向承载能力,银纹微纤之间可以相互传递应力。
这种结构的形成是由于强度较高的缠结链段被同时转入两相邻银纹微纤的结果。
银纹引发的原因是聚合物中以及表面存在应力集中物,拉伸应力作用下产生应力集中效应。
- 1、下载文档前请自行甄别文档内容的完整性,平台不提供额外的编辑、内容补充、找答案等附加服务。
- 2、"仅部分预览"的文档,不可在线预览部分如存在完整性等问题,可反馈申请退款(可完整预览的文档不适用该条件!)。
- 3、如文档侵犯您的权益,请联系客服反馈,我们会尽快为您处理(人工客服工作时间:9:00-18:30)。
增韧理论:塑料共混改性的一个重要内容是提高一种塑料的韧性,使其满足使用场合和环境对材料韧性的要求。
比较成熟的是橡胶增韧技术,但近几年与发展了非弹性体增韧技术,如无机刚性粒子增韧塑料等。
⑴弹性体直接吸收能量理论:当试样受到冲击时会产生微裂纹,这时橡胶颗粒跨越裂纹两岸,裂纹要发展就必须拉伸橡胶,橡胶形变过程要吸收大量能量,从而提高了塑料的冲击强度。
⑵屈服理论:橡胶增韧塑料高冲击强度主要来源于基体树脂发生了很大的屈服形变,基体树脂产生很大屈服形变的原因,是橡胶的热膨胀系数和泊松比均大于塑料的,在成型过程中冷却阶段的热收缩和形变过程中的横向收缩对周围基体产生静水张应力,使基体树脂的自由体积增加,降低其玻璃化转变温度,易于产生塑性形变而提高韧性。
另外是橡胶粒子的应力集中效应引起的。
⑶裂纹核心理论:橡胶颗粒充作应力集中点,产生了大量小裂纹而不是少量大裂纹,扩展众多的小裂纹比扩展少数大裂纹需要较多的能量。
同时,大量小裂纹的应力场相互干扰,减弱了裂纹发展的前沿应力,从而,会减缓裂纹发展并导致裂纹的终止。
⑷多重银纹理论:由于增韧塑料中橡胶粒子数目极多,大量的应力集中物引发大量银纹,由此可以耗散大量能量。
较大的橡胶粒子还是银纹终止剂,小粒子不能终止银纹。
⑸银纹-剪切带理论:是普遍接受的一个重要理论。
大量实验表明,聚合物形变机理包括两个过程:一是剪切形变过程,二是银纹化过程。
剪切过程包括弥散性的剪切屈服形变和形成局部剪切带两种情况。
剪切形变只是物体形状的改变。
分子间的内聚能和物体的密度基本不变。
银纹化过程则使物体的密度大大下降。
一方面,银纹体中有空洞。
说明银纹化造成了材料一定的损伤,是次宏观断裂破坏的先兆;另一方面,银纹在形成、生长过程中消耗了大量能量,约束了裂纹的扩展,使材料的韧性提高,是聚合物增韧的力学机制之一,所以,正确认识银纹化现象,是认识高分子材料变形和断裂过程的核心,是进行共混改性塑料,尤其是增韧塑料设计的关键之一。
银纹的一般特征如下:①银纹是在拉伸力场中产生的,银纹面总是与拉伸力方向垂直;在压力场中不会产生银纹;在纯剪切力场中银纹也能扩展。
②银纹在玻璃态、结晶态聚合物中都能产生、发展。
③银纹能在聚合物表面、内部单独引发、生长,也可在裂纹端部形成。
在裂纹端部形成的银纹,是裂纹端部塑性屈服的一种形式。
④在单一应力作用下引发的银纹,称为应力银纹。
在短时大应力作用下可以引发银纹,在长期应力作用下,即蠕变过程中也能引发银纹,在交变应力作用下也可引发银纹。
受应力和溶剂联合作用引发的银纹,称为应力-溶剂银纹。
溶剂能加速银纹的引发和生长。
⑤银纹的外形与裂纹相似,但与裂纹的结果明显不同:裂纹体中是空的,而银纹是由银纹质和空洞组成的。
空洞的体积分数50%~70%。
银纹质取向的高分子和/或高分子微小聚集体组成的微纤,直径和间距约为几到几十纳米,其大小与聚合物的结构、环境温度、施力速度、应力大小等因素有关;银纹主微纤与主应力方向呈某一角度取向排列,横系的存在使银纹微纤也构成连续相,与空洞连续相交织在一起成为一个复杂的网络结构;横系结构使得银纹有一定横向承载能力,银纹微纤之间可以相互传递应力;这种结构的形成是由于强度较高的缠结链段被同时转入两相邻银纹微纤的结果。
银纹引发的原因是聚合物中以及表面存在的应力集中物,拉伸应力作用下产生应力集中效应。
首先在局部应力集中处产生塑性剪切变形,由于聚合物应变软化的特性,局部塑性变形量迅速增大,在塑性变形区内逐渐积累足够的横向应力分量。
这是因为沿拉伸应力方向伸长时,聚合物材料必然在横向方向收缩,就产生低抗这种收缩倾向的等效于作用在横向的应力场。
当横向张力增大到某一临界值时,局部塑性变形区内聚合物中被引发微空洞;随后,微空洞间的高分子和/或高分子微小聚集体继续伸长变形,微空洞长大并彼此复合,最终形成银纹中椭圆空洞。
银纹体形成时所消耗的能量称为银纹生成能,包括消耗的 4 种形式的能量;生成银纹时的塑性功;黏弹功;形成空洞的表面功及化学键的断裂能。
银纹终止的具体原因有多种,如银纹发展遇到了剪切带,或银纹端部引发剪切带,或银纹的支化,以及其它使银纹端部应力集中因子减小的因素。
剪切带具有精细的结构,其厚度约1um,宽度5~50um;由大量不规则的线簇构成,每一条线簇的厚度约0.1um,剪切带内分子链或高分子的微小聚集体有很大程度的取向,取向方向为切应力和拉伸应力合力的方向。
剪切带的产生只是引起试样形状改变,聚合物的内聚能以及密度基本上不受影响。
剪切带与拉伸力方向间的夹角接近45°,但由于大形变时试样产生各向异性,试样的体积也可能发生微小的变化,所以与拉伸力方向间的夹角往往是45°有偏差。
剪切带的产生和剪切带的尖锐程度,除与聚合物的结构密切相关外,还与温度、形变速率有关。
如温度过低时,剪切屈服应力过高,试样不能产生剪切屈服,而是横截面处引发银纹,并迅速发展成裂纹,试样呈脆性断裂;温度过高,整个试样容易发生均匀的塑性形变,只能产生弥散型的剪切形变而不会产生剪切带。
加大形变速度的影响与降低温度是等效的。
银纹与剪切带之间的相互作用:在很多情况下,在应力作用下,聚合物会同时产生剪切带与银纹,二者相互作用,成为影响聚合物形变乃至破坏的重要因素。
聚合物形变过程中,剪切带和银纹两种机理同时存在,相互作用,使聚合物从脆性破坏转变为韧性破坏。
银纹与剪切带的相互作用可能存在三种方式:一是银纹遇上已存在的剪切带而得以与其合并终止,这是由于剪切带内大分子高度取向限制了银纹的发展;二是在应力高度集中的银纹尖端引发新的剪切带新产生的剪切带反过来又终止银纹的发展;三是剪切带使银纹的引发与增长速率下降。
该理论认为橡胶增韧的主要原因是银纹和剪切带的大量产生和银纹与剪切带相互作用的结果。
橡胶颗粒的第一个重要作用就是充当应力集中中心,诱发大量银纹和剪切带,大量银纹或剪切带的产生和发展需要消耗大量能量。
银纹和剪切带所占比例与基体性质有关,基体的韧性越大,剪切带所占的比例越高;同时,也与形变速率有关,形变速率增加时,银纹化所占的比例就会增加。
橡胶颗粒第二个重要作用就是控制银纹的发展,及时终止银纹。
在外力作用过程中,橡胶颗粒产生形变,不仅产生大量的小银纹或剪切带,吸收大量的能量,而且,又能及时将其产生的银纹终止而不至发展成破坏性的裂纹。
银纹-剪切带理论的特点是既考虑了橡胶颗粒的作用,又肯定了树脂连续相性能的影响,同时明确了银纹的双重功能,即银纹产生和发展消耗大量的能量,可提高材料的破裂能;银纹又是产生裂纹并导致材料破坏的先导。
但这一理论的缺陷是忽视了基体连续相与橡胶分散相之间的作用问题。
应该说,聚合物多相体系的界面性质对材料性能有很大的影响。
⑹空穴化理论:空穴化理论是指在低温或高速形变过程中,在三维应力作用下,发生橡胶粒子内部或橡胶粒子与基体界面层的空穴化现象。
该理论认为:橡胶改性的塑料在外力作用下,分散相橡胶颗粒由于应力集中,导致橡胶与基体的界面和自身产生空洞,橡胶颗粒一旦被空化,橡胶周围的静水张应力被释放,空洞之间薄的基体韧带的应力状态,从三维变为一维,并将平面应变转化为平面应力,而这种新的应力状态有利于剪切带的形成。
因此,空穴化本身不能构成材料的脆韧转变,它只是导致材料应力状态的转变,从而引发剪切屈服,阻止裂纹进一步扩展,消耗大量能量,使材料的韧性得以提高。
⑺Wu's逾渗增韧模型:美国杜邦公司Souheng Wu博士提出了临界粒子间距判据的概念,对热塑性聚合物基体进行了科学分类并建立了脆韧转变的逾渗模型,将增韧理论由定性分析推向定量的高度。
其特点如下:①认为共混物韧性与基体链结构间存在一定的联系,给出了基体链结构参数——链缠结密度γe和链的特征比C∞间的和定量关系式,指出聚合物的基本断裂行为是银纹与屈服存在竞争。
γe较小及C∞较大时,基体易于以银纹方式断裂,韧性较低;γe较大及C∞较小的基体以屈服方式断裂,韧性较高。
②科学地将热塑性聚合物基体划分为两大类:脆性基体和准韧性体两大类。
认为中有当体系中橡胶粒子间距小于临界值时才有增韧作用。
相反,如果橡胶颗粒间距远大于临界值时,则材料表现为脆性。
临界值是决定共混物能否出现脆韧转变的特征参数,它适用所有增韧共混体系。
其理由如下:当橡胶粒子相距很远时,一个粒子周围的应力场对其它粒子影响很小,基体的应力场是这些孤立的粒子的应力场的简单加和,基本塑性变形的能力很小时,表现为脆性。
当粒子间距很小时,基体总应力场是橡胶颗粒应力场相互作用的叠加,这样,使基体应力场的强度大为增强,产生塑性变形的幅度增加,表现为韧性。
⑻刚性粒子增韧机理:①有机刚性粒子增韧:有机刚性粒子增韧聚合物的增韧机理有两种:“冷拉”机理和“空洞化”理机。
Kurauchi等在研究PC/ABS、PC/AS共混物的力学性能时首先提出了脆性塑料粒子可以提高韧性塑料基体拉伸冲击强度的概念,并用“冷拉”机理给予了解释:拉伸前,ABS、AS都是以球形微粒状分散在PC基体中,粒径分别大约为2um和1un;拉伸后,PC/ABS、PC/AS共混物中都没产生银纹,但分散相的球形微粒都发生了伸长变形,变形幅度大于100%。
基体PC也发生了同样大小的形变。
刚性粒子变形过程中发生大变形的原因在于:在拉伸时,基体树脂发生形变,分散相粒子的极区受到拉应力,赤道区受到压应力,脆性粒子屈服并与基体产生同样大小的形变,吸收相当多的能量,使共混物的韧性提高。
界面是两相间应力传递的基础,所以界面黏结好坏直接影响刚性粒子的冷拉。
如PA6/AS共混物,不具有增韧效果,其原因在于其界面的粘接力小于屈服应力。
拉伸时,在分散相AS 粒子的两极首先发生脱黏,破坏了原有的三维应力场,无法达到使AS屈服冷拉的要求。
在PA6/AS共混物中添加增容剂SMA苯乙烯-马来酸酐共聚物,提高了界面粘接强度,消除了分散相粒子两极脱黏的现象,使共混物的韧性显著提高。
以上分析表明:冷拉增韧机理只能在拉伸时出现,因为要在分散相粒子极区形成压应力,共混物界面粘接必须很强,在极区避免界面脱黏。
“空洞化”机理:Yee等在研究PC/PE共混物增韧机理时发现,和拉伸情况不同,裂尖损伤区内分散相粒子承受三维强力,微粒PE,直径约0.3um,从界面脱黏,形成空洞化损伤,同时使基体PC易于产生剪切屈服,共混物得到增韧。
使LDPE分散相的直径减小到1um以下,在缺口产生的损伤区内也有空洞化损伤产生,共混物因此得到增韧。
②无机刚性粒子增韧机理:20世纪90年代初,发展了无机刚性粒子增韧理论。
无机粒子在基体中的分散状态有三种情况:a.无机粒子无规分散或聚集成团后单独分散:b.无机粒子如同刚性链分散在基体中;c.无机粒子均匀而单独地分散在基体中。
为达到理想的增韧效果,要尽可能地使粒子均匀分散。