制动盘材料
制动盘生产标准
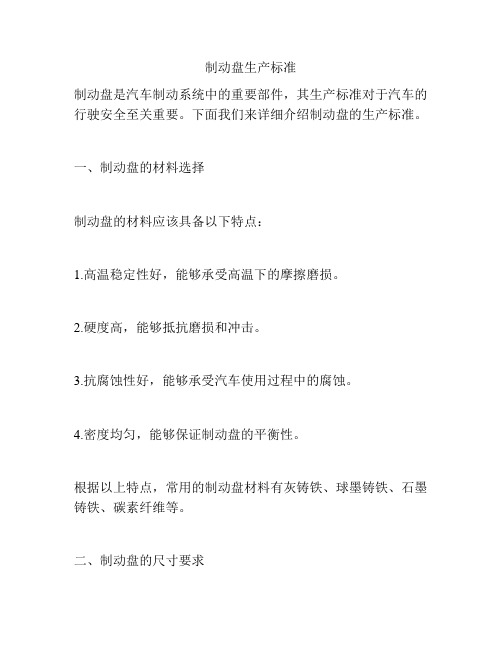
制动盘生产标准制动盘是汽车制动系统中的重要部件,其生产标准对于汽车的行驶安全至关重要。
下面我们来详细介绍制动盘的生产标准。
一、制动盘的材料选择制动盘的材料应该具备以下特点:1.高温稳定性好,能够承受高温下的摩擦磨损。
2.硬度高,能够抵抗磨损和冲击。
3.抗腐蚀性好,能够承受汽车使用过程中的腐蚀。
4.密度均匀,能够保证制动盘的平衡性。
根据以上特点,常用的制动盘材料有灰铸铁、球墨铸铁、石墨铸铁、碳素纤维等。
二、制动盘的尺寸要求制动盘的尺寸应该符合以下要求:1.直径误差不得超过0.05mm。
2.厚度误差不得超过0.02mm。
3.平面度误差不得超过0.03mm。
4.表面粗糙度应该在Ra1.0-3.2之间。
5.制动盘的圆周度误差不得超过0.05mm。
三、制动盘的检测标准为了保证制动盘的质量,应该进行以下检测:1.外观检查:检查制动盘表面是否有裂纹、气孔等缺陷。
2.尺寸检查:检查制动盘的直径、厚度、平面度等尺寸是否符合要求。
3.硬度检查:检查制动盘的硬度是否符合标准。
4.平衡性检查:检查制动盘是否平衡,以及是否存在不平衡现象。
5.性能检查:通过试车等方式检查制动盘的性能是否符合要求。
四、制动盘的包装要求为了避免制动盘在运输过程中受到损坏,应该进行合理的包装。
包装应该符合以下要求:1.包装材料应该具备一定的防震、防潮、防晒等性能。
2.包装应该紧密,避免在运输过程中出现松动现象。
3.包装应该标明制动盘的型号、数量、重量等信息,方便管理和识别。
以上就是制动盘生产标准的详细介绍。
只有严格遵守这些标准,才能保证汽车行驶中的安全。
制动盘设计应该遵循的准则

制动盘设计应该遵循的准则制动盘是汽车刹车系统中的重要组成部分,其设计的合理与否直接影响到刹车性能和安全性。
为了确保制动盘的性能和质量,设计师需要遵循一些准则和原则。
下面将介绍制动盘设计应该遵循的准则。
1. 材料选择:制动盘的材料应具有良好的热导性能和机械性能。
常用的制动盘材料有铸铁、复合材料和碳纤维等。
根据车辆类型和用途的不同,选择合适的材料可以提高制动盘的耐磨性和耐高温性能。
2. 结构设计:制动盘的结构设计应考虑到刹车时的热膨胀和热应力。
合理的结构设计可以减轻制动盘的重量,提高散热效果,并降低制动时的热应力,延长制动盘的使用寿命。
3. 制动盘的尺寸:制动盘的尺寸应根据车辆的重量和动力要求来确定。
过大或过小的尺寸都会影响刹车性能。
尺寸合理的制动盘可以提供更大的制动力矩和更好的散热效果,提高刹车的效果和稳定性。
4. 制动盘的表面处理:制动盘的表面处理对于提高刹车效果和降低刹车噪音都有重要作用。
常见的表面处理方式有镀层、磨砂和槽道等。
合适的表面处理可以提高制动盘与刹车片之间的摩擦系数,提高刹车的响应速度和稳定性。
5. 制动盘的制造工艺:制动盘的制造工艺应考虑到材料的特性和成本效益。
常见的制造工艺有铸造、锻造和机械加工等。
合理选择制造工艺可以提高制动盘的质量和性能,降低制造成本。
6. 制动盘与其他刹车系统的匹配:制动盘与刹车片、刹车液和刹车系统的匹配度直接影响到刹车性能和安全性。
因此,在制动盘设计过程中,需要考虑到与其他刹车系统的协调性,确保各个部件之间的配合良好,以获得最佳的刹车效果。
7. 制动盘的检测和测试:制动盘的设计完成后,需要进行严格的检测和测试,以确保其质量和性能符合标准和要求。
常见的检测和测试项目包括硬度测试、热膨胀测试和摩擦系数测试等。
只有通过了各项测试,才能保证制动盘的安全可靠性。
制动盘设计应该遵循的准则包括材料选择、结构设计、尺寸确定、表面处理、制造工艺选择、与其他刹车系统的匹配以及检测和测试等。
机动车制动器零部件的材料与加工工艺
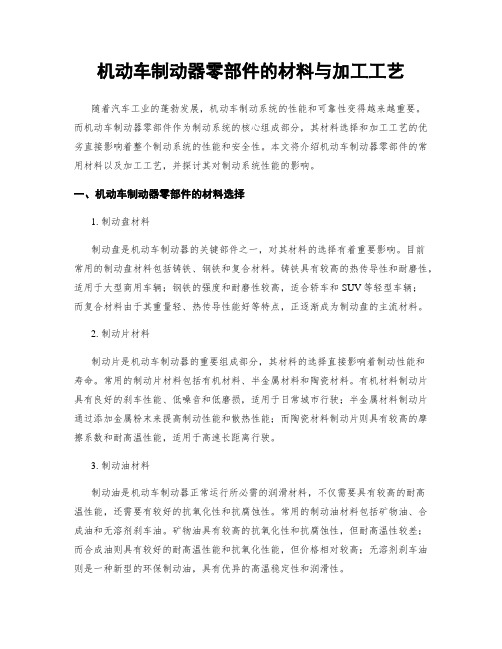
机动车制动器零部件的材料与加工工艺随着汽车工业的蓬勃发展,机动车制动系统的性能和可靠性变得越来越重要。
而机动车制动器零部件作为制动系统的核心组成部分,其材料选择和加工工艺的优劣直接影响着整个制动系统的性能和安全性。
本文将介绍机动车制动器零部件的常用材料以及加工工艺,并探讨其对制动系统性能的影响。
一、机动车制动器零部件的材料选择1. 制动盘材料制动盘是机动车制动器的关键部件之一,对其材料的选择有着重要影响。
目前常用的制动盘材料包括铸铁、钢铁和复合材料。
铸铁具有较高的热传导性和耐磨性,适用于大型商用车辆;钢铁的强度和耐磨性较高,适合轿车和SUV等轻型车辆;而复合材料由于其重量轻、热传导性能好等特点,正逐渐成为制动盘的主流材料。
2. 制动片材料制动片是机动车制动器的重要组成部分,其材料的选择直接影响着制动性能和寿命。
常用的制动片材料包括有机材料、半金属材料和陶瓷材料。
有机材料制动片具有良好的刹车性能、低噪音和低磨损,适用于日常城市行驶;半金属材料制动片通过添加金属粉末来提高制动性能和散热性能;而陶瓷材料制动片则具有较高的摩擦系数和耐高温性能,适用于高速长距离行驶。
3. 制动油材料制动油是机动车制动器正常运行所必需的润滑材料,不仅需要具有较高的耐高温性能,还需要有较好的抗氧化性和抗腐蚀性。
常用的制动油材料包括矿物油、合成油和无溶剂刹车油。
矿物油具有较高的抗氧化性和抗腐蚀性,但耐高温性较差;而合成油则具有较好的耐高温性能和抗氧化性能,但价格相对较高;无溶剂刹车油则是一种新型的环保制动油,具有优异的高温稳定性和润滑性。
二、机动车制动器零部件的加工工艺1. 制动盘的加工工艺制动盘的加工工艺通常包括铸造、热处理、机械加工和表面处理等环节。
首先,通过铸造工艺将铁水注入制动盘模具中,形成所需的制动盘形状。
然后,对铸造好的制动盘进行热处理,提高其硬度和耐磨性。
接下来,通过机械加工工艺,对制动盘进行车削、切割和打磨等工序,使其具有更加精确的尺寸和表面平整度。
制动盘材料
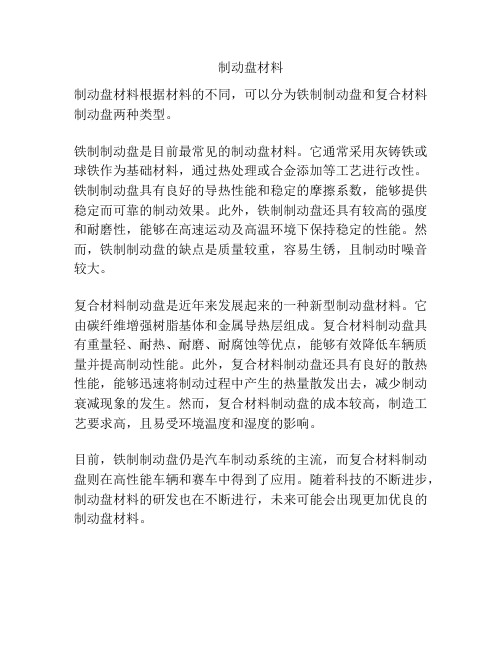
制动盘材料
制动盘材料根据材料的不同,可以分为铁制制动盘和复合材料制动盘两种类型。
铁制制动盘是目前最常见的制动盘材料。
它通常采用灰铸铁或球铁作为基础材料,通过热处理或合金添加等工艺进行改性。
铁制制动盘具有良好的导热性能和稳定的摩擦系数,能够提供稳定而可靠的制动效果。
此外,铁制制动盘还具有较高的强度和耐磨性,能够在高速运动及高温环境下保持稳定的性能。
然而,铁制制动盘的缺点是质量较重,容易生锈,且制动时噪音较大。
复合材料制动盘是近年来发展起来的一种新型制动盘材料。
它由碳纤维增强树脂基体和金属导热层组成。
复合材料制动盘具有重量轻、耐热、耐磨、耐腐蚀等优点,能够有效降低车辆质量并提高制动性能。
此外,复合材料制动盘还具有良好的散热性能,能够迅速将制动过程中产生的热量散发出去,减少制动衰减现象的发生。
然而,复合材料制动盘的成本较高,制造工艺要求高,且易受环境温度和湿度的影响。
目前,铁制制动盘仍是汽车制动系统的主流,而复合材料制动盘则在高性能车辆和赛车中得到了应用。
随着科技的不断进步,制动盘材料的研发也在不断进行,未来可能会出现更加优良的制动盘材料。
汽车制动盘材料的研究及发展前景(2)新

目录第一章汽车刹车盘材料................................................................... 错误!未定义书签。
1.1几种常见的汽车制动盘......................................................................................... - 1 -1.2汽车制动盘材料的种类.......................................................................................... - 2 -1.3汽车刹车盘材料的发展历程.................................................................................. - 4 -1.4汽车制动盘材料的性能要求.................................................................................. - 9 -1.5汽车制动材料需要解决的关键技术 .................................................................... - 10 - 第二章汽车制动盘材料的研究现状 ....................................................................... - 12 -2.1国内外研究现状.................................................................................................... - 13 -2.2几种目前汽车制动盘材料的分析 ....................................................................... - 15 - 第三章汽车制动盘材料发展前景............................................................................ - 25 -3.1国内外汽车制动摩擦材料发展趋势 ................................................................... - 25 -3.2 汽车制动盘的发展趋势...................................................................................... - 25 -3.3我国汽车制动盘材料的发展方向 ....................................................................... - 26 - 参考文献 ........................................................................................................................... - 27 - 致谢................................................................................................................................ - 29 -插图清单图1-1汽车制动盘 (3)图1-2汽车刹车盘几种形式 (4)图1-3石棉类制动材料 (5)图1-4金属基无石棉制动材料 (5)图1-5半金属基无石棉制动材料 (6)图1-6非金属基无石棉制动材料 (6)图1-7粉末冶金摩擦材料 (8)图1-8新型混杂纤维摩擦材料 (9)图1-9C/C复合材料 (9)图1-10新型陶瓷基摩擦材料 (11)图2-1灰铸铁材料 (18)图2-2制动盘零件与铸件图 (18)图2-3浇注系统示意图 (19)表格清单表2-1不同铝基复合材料的力学性能 (20)表2-2 3种制备工艺所得C/C-SiC复合材料的主要性能 (24)表2-3各国正在使用及研究看法的制动盘材质 (26)摘要汽车制动材料是指利用材料的摩擦性能将汽车的动能转化为热能或其他形式的能量,从而实现汽车制动的材料。
制动盘的加工工艺

制动盘的加工工艺
制动盘的加工工艺一般包括以下几个步骤:
1. 材料准备:选择合适的材料进行制动盘的加工,一般常用的材料有铸铁、钢、复合材料等。
2. 锻造或铸造:根据设计要求,对选定的材料进行锻造或铸造,得到初步的制动盘原型。
3. 粗加工:对初步成形的制动盘进行粗加工,包括车削、铣削、钻孔等操作,以达到设计要求的尺寸和形状。
4. 热处理:对粗加工后的制动盘进行热处理,常见的方法有淬火、回火等,以提高其硬度和耐磨性能。
5. 精加工:对经过热处理的制动盘进行精加工,包括车削、磨削、镗削等操作,以保证制动盘的精度和平面度。
6. 平衡调整:对精加工后的制动盘进行平衡调整,以消除制动盘在高速旋转时的不平衡现象,提高其安全性和使用寿命。
7. 表面处理:对制动盘进行表面处理,包括喷涂、镀铬等操作,以提高其表面
光洁度和防腐性能。
8. 检测与质检:对加工完成的制动盘进行检测与质检,包括尺寸检测、硬度测试、动平衡检测等,以确保制动盘的质量达到设计要求。
综上所述,制动盘的加工工艺是一个综合性的过程,需要通过多道工序来完成,以确保制动盘的质量和性能。
制动器的结构组成
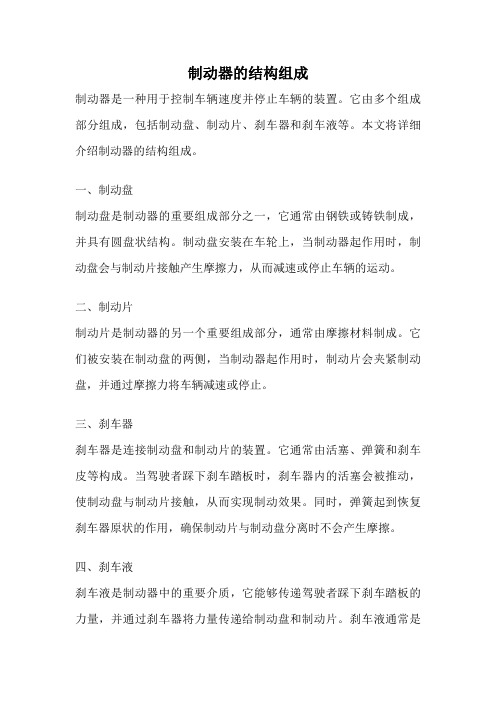
制动器的结构组成制动器是一种用于控制车辆速度并停止车辆的装置。
它由多个组成部分组成,包括制动盘、制动片、刹车器和刹车液等。
本文将详细介绍制动器的结构组成。
一、制动盘制动盘是制动器的重要组成部分之一,它通常由钢铁或铸铁制成,并具有圆盘状结构。
制动盘安装在车轮上,当制动器起作用时,制动盘会与制动片接触产生摩擦力,从而减速或停止车辆的运动。
二、制动片制动片是制动器的另一个重要组成部分,通常由摩擦材料制成。
它们被安装在制动盘的两侧,当制动器起作用时,制动片会夹紧制动盘,并通过摩擦力将车辆减速或停止。
三、刹车器刹车器是连接制动盘和制动片的装置。
它通常由活塞、弹簧和刹车皮等构成。
当驾驶者踩下刹车踏板时,刹车器内的活塞会被推动,使制动盘与制动片接触,从而实现制动效果。
同时,弹簧起到恢复刹车器原状的作用,确保制动片与制动盘分离时不会产生摩擦。
四、刹车液刹车液是制动器中的重要介质,它能够传递驾驶者踩下刹车踏板的力量,并通过刹车器将力量传递给制动盘和制动片。
刹车液通常是一种特殊的液体,具有较高的沸点和较低的凝固点,以适应不同温度下的工作环境。
以上是制动器的主要结构组成,它们共同协作,实现了车辆的制动功能。
当驾驶者踩下刹车踏板时,刹车器内的活塞被推动,使制动盘与制动片接触,产生摩擦力。
摩擦力将车辆减速或停止。
刹车液在这个过程中起到了传递力量的作用。
制动器的结构组成不仅仅是为了实现车辆的制动功能,还需要考虑安全性和稳定性。
制动器在设计和制造过程中需要考虑材料的选择、结构的合理性和制动效果的稳定性等因素,以确保驾驶者在紧急情况下能够快速减速或停止车辆。
制动器是车辆中至关重要的装置,它的结构组成包括制动盘、制动片、刹车器和刹车液等多个部分。
这些部分共同协作,实现了车辆的制动功能。
在日常驾驶中,驾驶者需要保持制动器的良好状态,并合理使用制动器,以确保行车安全。
制动盘生产工艺流程

制动盘生产工艺流程
制动盘生产工艺流程:
①原材料选择:选择合适的材料,通常为灰铸铁、球墨铸铁或合金钢等,以满足制动盘的机械性能要求。
②铸造毛坯:通过铸造工艺获得制动盘的原始形状,这一步骤可能包括砂型铸造、离心铸造或重力铸造等。
③粗车:以制动盘的大端面为基准,进行轴向定位,夹紧通风槽,粗车安装法兰面、安装孔以及初步加工刹车面,确保基本尺寸和形状。
④半精车:进一步加工最大外圆面、左端制动面、内孔、小端外圆面等,提高表面光洁度和精度。
⑤精车:完成中间大槽、右端制动面、左端制动面、小圆端面、孔部分倒角等精加工,达到最终尺寸要求。
⑥钻孔:在制动盘上钻制必要的安装孔和通风孔,保证安装和散热需求。
⑦动平衡:对制动盘进行动平衡调整,确保在高速旋转时不会产生过大的振动。
⑧清洗:去除加工过程中残留的切屑、油脂等杂质,保持制动盘的清洁。
⑨表面处理:可能包括涂层、镀层等,以增强防腐蚀性能和延长使用寿命。
⑩检验:对制动盘进行尺寸、外观、硬度等各项指标的严格检验,确保产品质量。
⑪标记:在制动盘上标记必要的信息,如型号、制造商、生产日期等。
⑫包装:将检验合格的制动盘进行包装,准备出厂或入库储存。
- 1、下载文档前请自行甄别文档内容的完整性,平台不提供额外的编辑、内容补充、找答案等附加服务。
- 2、"仅部分预览"的文档,不可在线预览部分如存在完整性等问题,可反馈申请退款(可完整预览的文档不适用该条件!)。
- 3、如文档侵犯您的权益,请联系客服反馈,我们会尽快为您处理(人工客服工作时间:9:00-18:30)。
+ 但在更高车速下,250Km/h易产生热裂纹,致使失效。
+ 3.1.2 蠕墨铸铁制动盘
铁液经过蠕化处理,大部分石墨呈蠕虫状的铸铁
+ 蠕化剂主要是镁或稀土。
+ 迄今为止,国内外研究结果一致认为,稀土是制取蠕墨铸
铁的主导元素。我国稀土资源富有,为发展我国蠕墨铸铁 提供了极其有利的条件和物质基础。
问题:在高摩擦速度下,随温度的上升,其摩擦系数急剧增 大,与传统制动材料的摩擦特性差别很大。磨耗量较大, 有待进一步改进。
+ 2)熔融法:在熔融的铝合金中,通过搅拌,均匀地混入
强化粒子。
3.2.2 碳/碳纤维复合材料制动盘 + 一种以碳纤维增强石墨的复合材料,其密度小,约为 1.5g/cm3,仅为铁的1/5。 + 特性: 1)导热性能很好、 2)热容量大 3)热膨胀系数小 4)因此具有质量小、抗热裂等优点。 应用:在飞机和赛车上作为制动材料已通过了实践应用的考 验。
制动衬块、含有活塞的卡钳、安装在轮毂上的转子
盘式制动器的工作原理
+ 盘式制动器的优点
1)盘式刹车散热性较鼓式刹车佳,在连续踩踏刹车时比较不 会造成刹车衰退而使刹车失灵的现象。 2)刹车盘在受热之后尺寸的改变并不使踩刹车踏板的行程增 加。 3)盘式刹车系统的反应快速,可做高频率的刹车动作,同时 便于安装ABS等控制系统。 4)盘式刹车没有鼓式刹车的自动煞紧作用,因此左右车轮的 刹车力量比较平均。 5)制动盘的排水性较佳,可以降低因为水或泥沙造成刹车不 良的情形。 6)盘式刹车的构造简单,且容易维修。
3)较高的耐磨性。以减少盘面和闸片间因强烈摩擦而产 生的磨损。
4)较好的抗热裂性能。使制动盘在激热激冷条件下不产 生裂纹。
5)密度小。以降低车辆簧下质量。 此外: 6)良好的工艺性能。 7)较低的成本。
+ 大体分为两类:铁系金属材料、复合材料。前者称为传统
制动盘材料,包括铸铁系和钢系;后者称为新型制动盘材 料。
5)热处理工艺: + 正火:900-950℃,空冷 + 正火态的蠕墨铸铁的强度、塑性、耐磨性均比铸态的高。
+ 退火工艺:为了获得体积分数85%以上的铁素体基体或者
消除薄壁处的游离渗碳体。
3.1.3 铸钢制动盘
+ 从50年代开始使用。 + 具有较高的强度(大于800MPa)、韧性和抗热裂性能. + 但由于导热性能差、热容量较大、膨胀系数大,在使用中
董立新
1. 制动盘的概述 2. 制动盘的所用材料的性能要求 3. 传统制动盘材料
4. 新型制动盘材料
1.1 定义:固定在车轮上,随车轮转动,以端平面为摩擦工 作面,通过摩擦将动能转化为热能的圆盘形运动部件。制 动盘即刹车盘。
+ 制动过程是通过制动盘和制动闸的摩擦将动能转化为热能,
并通过制动盘的通风设备将热能传递到空气中。
+ 盘式制动器的不足
1)因为没有鼓式刹车的自动刹紧作用,使盘式刹车的刹车 力较鼓式刹车为低。 2)盘式刹车的刹车片与刹车盘之间的摩擦面积较鼓式刹车 的小,使刹车的力量也比较小。 3)为改善上述盘式刹车的缺点,因此需较大的踩踏力量或 是油压。因而必须使用直径较大的刹车盘,或是提高刹车 系统的油压,以提高刹车的力量。 4)手刹车装置不易安装。 5)刹车片之磨损较大,致更换频率可能较高。
4)性能
+ 具有良好的综合性能,力学性能较高。蠕墨铸铁的力学性
能介于灰铸铁和球墨铸铁之间
+ 铸造性能、减振性和导热性都优于球墨铸铁,与灰铸铁相
近
+ 高温下有较高的强度,氧化生长较小、组织致密、热导率
高以及断面敏感性小等特点
我国制作蠕墨铸铁所用的蠕化剂中均含有稀土元素, 如稀土硅铁镁合金、稀土硅铁合金、稀土硅钙合金、稀土 锌镁硅铁合金等。由此,形成了适合国情的蠕化剂系列。
制动结构示意图
高速列车制动盘
铝基复合材料制动盘
高速重载列车制动盘
1.2
制动系统的作用
+ 使行驶中的车辆按照驾驶员的要求进行强制减速甚至停车; + 使已停驶的车辆稳定驻车; + 使下坡行驶的车辆速度保持稳定。
在各类车辆制动系统中,制动器是车辆制动系中用以产 生阻止车辆运动或运动趋势力的部件。目前,各类车辆所 使用的制动器都是摩擦制动器,也就是阻止车辆运动的制 动力矩来源于固定元件和旋转工作表面之间的摩擦。
摩擦面易出现沟槽、皱折及网状裂纹;
+ 局部表面会产生融化,以“鱼鳞状”金属崁入闸片中,大
大加剧了制动盘和闸片的磨损。
+ 因此,铸钢制动盘的寿命较短,现在一些重型卡车上应用,
但在高铁上应用不理想。
+ 热处理工艺对ZDPH合金钢组织和性能的影
响
+ 铸钢-铸铁复合层制动盘
+ 兼顾了两种材料特性,高而稳定的摩擦系数和抗热裂性能。
锻钢轮装制动盘
锻钢轴装制动盘
+ 适用于CRH2型动车组
提速式客车制动盘
制动盘是制动器的关键部件,对高速列车的安全行驶 起着至关重要的作用。制动盘用于高速列车相当苛刻的摩 擦制动部件。 对于制动盘材料的要求主要有: 1)足够的强度。以承受高速旋转时的离心力以及制动时 闸片压力。
2)高而稳定的摩擦系数。以获得良好的制动效果。
3.2.1 铝合金基的复合材料 + 一种在铝合金母材中加入陶瓷粒子(SiC、Al2o3等)的复 合材料。 + 特点: 1)具有和铸铁一样的耐磨性能 2)质轻 3)导热性能好。由于铝合金导热性能好,不会发生局部过 热 4)具有较高的抗热疲劳性能
+ 制造工艺:
+ 1)粉末法:铝合金粉末与强化粒子混合后再固化;
复合材料的优势 1)轻质高强 + 质量轻、强度高、刚性大,是一种理想的结构件。 + 复合材料比常用的轨道交通车辆材料-金属材料的比强度 和比模量要高出1~5倍。 2 )可设计性强 + 纤维复合材料的最显著特点是高比强度和高比刚度,并且 它可以在一个很宽的范围内变化,因此复合材料可以通过 材料选择、结构设计、铺层设计等方法解决各种技术难题。 3)工艺性强 + 复合材料产品制造工艺多数是近终形成型,制造出的产品, 不需进行机械加工,生产效率高,制造成本低。
各国正在使用及研究开发的制动盘材质:
3.1.1 铸铁制动盘
铸铁制动盘材料的化学成分及力学性能
+ 特点:
1)较好的摩擦特性,摩擦系数在0.25-0.35,且较稳定 2)耐磨性能好 3)变形小 4)铸造性能好 5)价格低
+ 但在速度130Km/h时,磨损严重,需频繁更换。
Ni-Cr-Mo低合金铸铁制动盘 ---在片状石墨铸铁中加入Ni、Cr、Mo等合金元素
100倍
蠕虫状石墨
蠕墨铸铁的显微组织
3)材料牌号:
+ 蠕墨铸铁的牌号为:RuT+数字。 + 牌号中,“RuT”是“蠕铁”二字汉语拼音的大写字头,
为蠕墨铸铁的代号;后面的数字表示最低抗拉强度。
+ 例如:牌
常用蠕墨铸铁牌号(GB/T4403-1999)
1.3
制动器的分类
1)鼓式制动器 鼓式刹车的主要优点:刹车蹄片磨损较少,成本较低, 便于维修.由于鼓式刹车的绝对制动力远远高于盘式刹车, 所以普遍用于后轮制动的卡车上.
双向增力式制动器
2)盘式制动器 + 车辆速度在不断提高,车辆的总重不断增加。采用制动热 稳定能较好的盘式制动器的日益增多。
+ 盘式制动器的主要部件包括:
1)化学成分: + C%=3.4%~3.6%;Si%=2.4%~3.0%;Mn%=0.4%~0.6%; S%<0.06%;P%<0.07%。 2)组织特征:
+ 石墨形态介于片状和球状石墨之间。
+ 石墨形态在光学显微镜下看起来像片状,但不同于灰口铸
铁的是其片较短而厚、头部较圆(形似蠕虫)。
蠕墨铸铁的显微组织
+ 现在使用的纤维从弹性模量为70 GPa和抗拉强度为3 500 MPa 的玻璃
纤维,到模量为60GPa 和抗拉强度为3 900 MPa的高模量碳纤维,其 性能范围很宽。根据已知的有关混合物的定律,通过选择基体材料, 可以改变其性能,因此每个结构件都可以根据要求找到一种最佳的铺 层结构。
4) 高安全性 + 高抗疲劳强度和低缺口敏感度 5) 低成本 ①随着原材料的发展和工艺的进步,其成本正在逐步降低; ②由于采用模块化的设计技术及整体成型技术,大大减少 了结构的复杂性、并缩短了生产实际以及总装所需要的工 作量,降低了总体成本; ③由于复合材料的耐疲劳、耐腐蚀等特性,降低了维护、 修理成本等。 ④由于减重,提高了运营能力,减少了能耗,总寿命周期 成本得到了降低。
包层制动盘的结构
+ 铸钢-铸铁复合层制动盘特点: + 1)与铸铁制动盘相比,提高使用寿命2倍; + 2)摩擦特性与铸铁的大致相同,直到高速区也有稳定的
摩擦系数。
+ 3)具有较高的抗热裂性能。
+ 复合材料是由基体材料:(聚合物材料、金属、陶瓷)和
增强体(纤维、晶须、颗粒)复合而成的具有优异综合性 能的新型材料,是本世纪中发展最迅速的新材料之一 + 复合材料已在航空、航天、交通运输、基础建设等领域中 发挥了巨大的作用,成为这些领域产品性能提高和升级换 代的关键材料。 + 特征: 1)用复合材料做成的构件,质量轻、强度高、刚性大,是 一种理想的结构件。 2)复合材料产品制造工艺多数是近终形成型,制造出的产 品,不需进行机械加工,生产效率高,制造成本低。 3)复合材料在轨道交通车辆中广泛应用,对减轻车厢质量, 降噪减振,提高安全性和舒适性,减少维修等均有重要作 用。