PE管件注塑成型工艺优化设计
简析PE注塑管件的设计与成型工艺

简析PE注塑管件的设计与成型工艺作者:陈连成来源:《商情》2013年第24期【摘要】在我国,就最近几年的发展状况来看建筑行业在飞速发展,并成为新一代的热门行业,许多企业在陆陆续续的像一颗新星一样冉冉升起,为这个行业注入源源不断的新鲜血液,本文主要介绍了PE注塑管件在建筑行业中的应用的特点,提出了PE注塑管件系统的设计原则与其成型工艺中应考虑的问题。
【关键词】PE注塑管件设计成型工艺在我国,近几年来装修热潮不断向人们涌来,装修业也得到了很好的发展,就市场上来看,需求量不断增大的其中一个就是PE注塑管件,这个管件在现在来看缺口也是很大的,近年来不少企业纷纷投资该领域,限于各方面的因素,新投资的管件生产多集中在中小1:3径系列。
同时许多企业由于技术力量薄弱,生产的产品质量差,废品率高,严重影响企业的效益,为此本文特提出PE注塑管件的设计与成型工艺,供读者参考。
1、PE注塑管件的特点PE的中文全称就是硬质聚乙烯,这种硬质聚乙烯主要就是制成管材、管件等材料的,由于这种材料具有高抗热性、抗老化、轻度较高、不易开裂等优点,所以在人们的日常生活中也是被广泛应用的,主要是在室内外给排水、建筑给排水、燃气管、排污管等广阔的领域。
尤其是中密度聚乙烯/高密度聚乙烯(MDPE/HDPE)塑料管材上述优点更是尤为突出。
其各项技术指标均可达到国际和国家有关标准要求。
它主要有以下特点:(1)抗腐蚀性较强。
PE管主要的合成材料是惰性材料,所以这就决定了它对电流、盐分、酸和水气等电化学腐蚀具有良好的抵抗性,不易受到侵蚀,更不需要作进一步的抗酸防腐处理,这也就可以节约一些成本。
(2)使用年限长。
据国外实验室测定。
PE管的使用寿命远大于80年。
折旧成本远低于钢管。
(3)施工简便,易于运输。
小口径PE 管单管长度可进几十米甚至百米,减少了接口。
同种管径的PE管的每米重量约为钢管的l/5易于运输,施工简便,可太大降低施工费用。
(4)有较好的柔韧性。
塑料工程中的注塑成型工艺优化方法

塑料工程中的注塑成型工艺优化方法注塑成型是塑料工程中一种常用的加工方法,其优化方法对于提高产品质量、降低成本和提升生产效率至关重要。
本文将介绍塑料工程中的注塑成型工艺优化方法,帮助读者更好地理解和应用这些方法。
首先,优化注塑成型工艺的关键是选用合适的原料。
不同的塑料材料具有不同的熔化温度、流动性和收缩性等特性,因此在注塑成型之前需要根据产品要求选择合适的原料。
合适的原料能够保证产品的功能性能和外观质量,并且能够降低生产过程中的能耗和废料率。
其次,注塑成型的工艺参数调整对产品质量和生产效率都有着重要的影响。
例如,注塑温度的调整可以影响产品的缩水率和表面质量,过高或过低的温度都会导致产品瑕疵;注塑压力的调整可以控制产品的密实度和尺寸精度,过高的压力可能导致产品开裂,而过低的压力可能导致产品无法填充模腔。
因此,通过对注塑温度、注塑压力和冷却时间等参数的优化调整,可以达到最佳的成型效果。
此外,在注塑成型工艺中,模具的设计和制造也是很重要的一环。
合理的模具设计能够提高产品的质量和生产效率。
例如,增加模具的冷却系统可以加快产品的冷却速度,缩短成型周期;优化模腔和模芯的结构设计,可以减少产品的缩水率和变形。
因此,在进行注塑成型工艺优化时,需要注重模具的设计和制造,选择合适的模具材料和加工方式,以提高模具的寿命和使用效果。
此外,注塑成型过程中还应注意产品的后处理。
例如,对于高要求的产品,可以通过表面处理(如喷漆、打磨等)来提高产品的外观质量;对于某些产品,可以通过热处理或淬火等方法来改善产品的力学性能。
因此,了解并应用合适的后处理方法,可以满足不同产品的特定要求。
最后,注塑成型工艺优化还需要注重工艺参数的监控和调整。
通过对注塑机的监测和数据分析,可以实时了解工艺参数的变化和异常,及时调整以保证产品的质量和生产效率。
例如,通过定期维护注塑机,并进行设备清洁和润滑,可以减少设备故障和停机时间,提高生产效率。
总之,注塑成型工艺的优化是塑料工程中非常重要的一环。
注塑工艺参数优化

注塑工艺参数优化首先,注塑工艺参数优化的目标是实现产品质量要求。
为了达到产品质量要求,可以从以下几个方面进行优化。
1.注射速度的优化:注射速度会影响到产品充填和冷却过程,过快的注射速度会造成产品表面烧焦、翘曲等质量问题,而过慢的注射速度则会导致产品充填不完整。
因此,需要根据产品的尺寸、材料等特性,选择合适的注射速度。
2.射压的优化:射压是指注塑机在注射过程中对熔融塑料施加的压力。
过高的射压会导致产品变形,过低的射压会造成产品表面不光滑。
因此,需要进行射压的优化,找到合适的射压范围,以保证产品的质量。
3.模具温度的优化:模具温度直接影响到产品的冷却速度和收缩率。
过高的温度会导致产品收缩不当,过低的温度则会造成产品表面瑕疵。
因此,需要根据材料的熔点和产品的尺寸等因素,确定合适的模具温度。
其次,注塑工艺参数优化还需要考虑生产效率的提高。
通过合理调整工艺参数,可以提高注塑工艺的生产效率。
1.提高注射速度:合理提高注射速度可以缩短注射周期,提高生产效率。
但需要注意,注射速度过高会增加回缩和收缩的问题,需要进行合理控制。
2.提高射压:射压是保证产品充填完整的关键因素。
适当提高射压可以缩短充填时间,提高生产效率。
3.缩短冷却时间:通过调整模具温度和冷却介质的流动速度等方式,可以缩短产品的冷却时间,从而减少生产周期。
最后,注塑工艺参数优化需要通过实验和数据分析来进行。
可以通过仿真软件进行模拟实验,找到最佳的工艺参数组合。
同时,还需要对生产过程中的数据进行采集和分析,及时发现并纠正问题,以不断提高注塑工艺的稳定性和可控性。
总结起来,注塑工艺参数优化是一个综合性的工作,需要根据产品的质量要求和生产效率的要求,通过调整注射速度、射压、模具温度等参数来实现最佳的工艺状态。
这需要通过实验和数据分析来进行,并且需要不断改进和完善,以满足不断提升的生产需求。
塑料注射成型中的流道设计优化
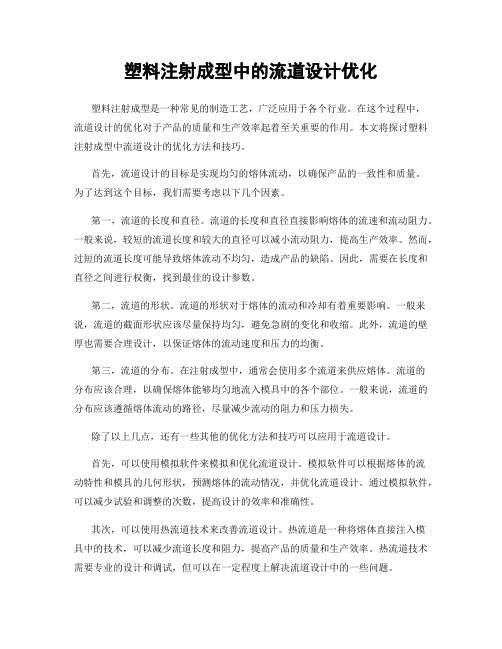
塑料注射成型中的流道设计优化塑料注射成型是一种常见的制造工艺,广泛应用于各个行业。
在这个过程中,流道设计的优化对于产品的质量和生产效率起着至关重要的作用。
本文将探讨塑料注射成型中流道设计的优化方法和技巧。
首先,流道设计的目标是实现均匀的熔体流动,以确保产品的一致性和质量。
为了达到这个目标,我们需要考虑以下几个因素。
第一,流道的长度和直径。
流道的长度和直径直接影响熔体的流速和流动阻力。
一般来说,较短的流道长度和较大的直径可以减小流动阻力,提高生产效率。
然而,过短的流道长度可能导致熔体流动不均匀,造成产品的缺陷。
因此,需要在长度和直径之间进行权衡,找到最佳的设计参数。
第二,流道的形状。
流道的形状对于熔体的流动和冷却有着重要影响。
一般来说,流道的截面形状应该尽量保持均匀,避免急剧的变化和收缩。
此外,流道的壁厚也需要合理设计,以保证熔体的流动速度和压力的均衡。
第三,流道的分布。
在注射成型中,通常会使用多个流道来供应熔体。
流道的分布应该合理,以确保熔体能够均匀地流入模具中的各个部位。
一般来说,流道的分布应该遵循熔体流动的路径,尽量减少流动的阻力和压力损失。
除了以上几点,还有一些其他的优化方法和技巧可以应用于流道设计。
首先,可以使用模拟软件来模拟和优化流道设计。
模拟软件可以根据熔体的流动特性和模具的几何形状,预测熔体的流动情况,并优化流道设计。
通过模拟软件,可以减少试验和调整的次数,提高设计的效率和准确性。
其次,可以使用热流道技术来改善流道设计。
热流道是一种将熔体直接注入模具中的技术,可以减少流道长度和阻力,提高产品的质量和生产效率。
热流道技术需要专业的设计和调试,但可以在一定程度上解决流道设计中的一些问题。
最后,流道设计的优化还需要考虑材料的选择和加工参数的调整。
不同的塑料材料具有不同的流动特性和熔体温度范围,需要根据具体情况来选择合适的材料。
此外,加工参数的调整也可以对流道设计产生影响,例如熔体温度、注射速度和压力等。
注塑成型工艺中的模具设计与优化

注塑成型工艺中的模具设计与优化一、引言随着全球化的发展和消费需求的不断增长,注塑成型工艺在生产制造中扮演着越来越重要的角色。
在注塑成型工艺中,模具设计与优化是关键环节,决定了产品质量、生产效率和生产成本。
本文将深入探讨注塑成型工艺中的模具设计与优化。
二、模具设计的基本原理1. 注塑成型工艺的基本流程注塑成型工艺是将熔化的塑料料施加于一定压力下充填到模具腔道中,经冷却硬化得到所需产品的过程。
基本流程包括注塑机料斗→注射装置→模具→冷却→开模→脱模→修整,所以模具的设计与优化必须充分考虑每个环节。
2. 模具设计的原则(1)合理的结构设计:模具结构应合理布局,便于加工和组装,以提高生产效率。
同时,需要考虑模具在使用过程中的稳定性和耐用性。
(2)充分考虑产品特性:模具设计时要充分考虑产品的特性,例如产品形状、尺寸、材料等,以确保产品的质量和性能。
(3)考虑冷却系统:冷却系统是模具设计的关键,直接影响产品的成型质量和生产效率。
冷却系统应具备良好的冷却效果,确保产品均匀冷却,并减少生产周期。
三、模具设计的优化方法1. 充分了解材料特性模具的设计与优化首先要充分了解材料的特性,包括熔点、流动性、尺寸稳定性等,以便在设计过程中选择合适的材料,并做出相应的调整和优化。
2. 仿真技术的应用利用计算机辅助设计(CAD)和计算机辅助工程(CAE)技术,进行模具设计的仿真分析。
通过仿真,可以模拟产品的充填、冷却和开模等过程,优化模具的结构和尺寸,提高产品的质量和生产效率。
3. 模具设计的标准化模具设计的标准化是改善模具设计质量和效率的重要手段。
建立规范化的设计流程和标准,提高设计效率和一致性,并减少设计的错误和修正。
四、模具设计的实践案例以汽车零部件为例,介绍一个模具设计的实践案例,以展示模具设计与优化的重要性。
汽车零部件的模具设计需要考虑到产品的形状复杂、尺寸精度高等特点。
在该案例中,设计团队利用CAD和CAE技术对模具进行了三维建模和仿真分析。
塑料注塑成型中的模具设计与优化
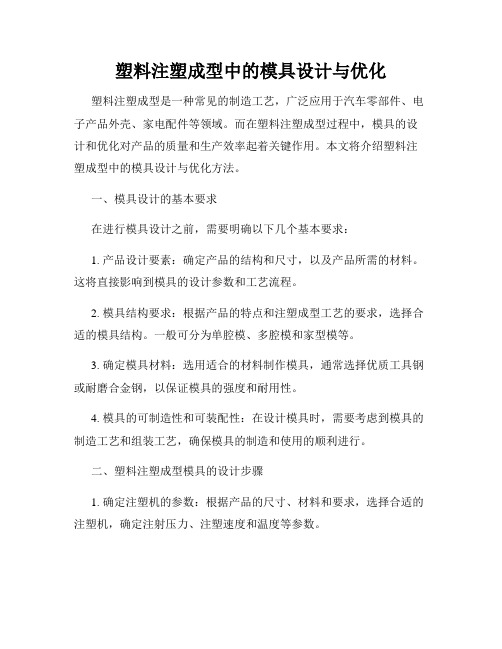
塑料注塑成型中的模具设计与优化塑料注塑成型是一种常见的制造工艺,广泛应用于汽车零部件、电子产品外壳、家电配件等领域。
而在塑料注塑成型过程中,模具的设计和优化对产品的质量和生产效率起着关键作用。
本文将介绍塑料注塑成型中的模具设计与优化方法。
一、模具设计的基本要求在进行模具设计之前,需要明确以下几个基本要求:1. 产品设计要素:确定产品的结构和尺寸,以及产品所需的材料。
这将直接影响到模具的设计参数和工艺流程。
2. 模具结构要求:根据产品的特点和注塑成型工艺的要求,选择合适的模具结构。
一般可分为单腔模、多腔模和家型模等。
3. 确定模具材料:选用适合的材料制作模具,通常选择优质工具钢或耐磨合金钢,以保证模具的强度和耐用性。
4. 模具的可制造性和可装配性:在设计模具时,需要考虑到模具的制造工艺和组装工艺,确保模具的制造和使用的顺利进行。
二、塑料注塑成型模具的设计步骤1. 确定注塑机的参数:根据产品的尺寸、材料和要求,选择合适的注塑机,确定注射压力、注塑速度和温度等参数。
2. 模具整体结构设计:根据产品的结构和尺寸,设计模具的整体结构,包括模具的型腔、型芯、导向机构等,并保证模具的生产效率和质量要求。
3. 流道系统设计:流道系统是模具中传递熔融塑料的管道系统,需要根据产品的结构和注塑工艺的要求进行设计,确保熔融塑料能够顺利注入模腔中。
4. 冷却系统设计:冷却系统是模具中的关键部分,可以通过冷却系统的设计合理调节模具温度,确保产品的质量和生产效率。
一般采用水冷却方式,需要在模具设计中合理布置冷却水路。
5. 塑料料斗和顶出机构设计:根据注塑成型的要求,设计合适的塑料料斗和顶出机构,以保证熔融塑料能够顺利注塑和产品能够从模具中顺利脱模。
三、模具设计的优化方法在塑料注塑成型过程中,模具设计的优化可以提高产品的质量和生产效率,降低生产成本。
以下是一些常用的模具设计优化方法:1. 流道长度和直径优化:流道的长度和直径对产品的注塑过程有着重要影响,应根据产品的尺寸和注塑机的要求进行合理设计,以减少产品的缩水和留痕。
聚乙烯塑料管道的优化设计

计过 程 中遇到 的二个 问题 ,就是 聚 乙烯 塑料 管道 的加 固工 作 不 到位 。因为 聚乙烯 塑料具 有硬 度较低 的特 性, 因此 在遇 到 尖 锐物 的碰撞 时很 容易发 生破裂 ,这样 一来就 会 导致管 内物 体 发生 泄漏 ,产 生极 大的危 害。 聚乙烯管 道优 化设计 过程 中 遇到 的第三个 问题,就是 聚乙烯塑料管道 的材料利 用率较低 。 聚 乙烯 塑料 管道在 生产过 程 中会遇到 材料 浪费 的现象 ,这对 于 提升 产 品质量 ,提 高产 量具 有极 大的 阻碍 。因此 ,必 须要 提 高聚乙烯 塑料管道的材料利用率 。 2 解决聚 乙烯管道优化设计 工作 中遇到问题的方法
Op t i mu m De s i g n o f Po l y e t h y l e n e P l a s t i c Pi p e l i n e
Ze n g Gua n g- yu e
Ab s t r a c t: P o l y e t h y l e n e a s a n i mp o r t a n t p e t r o c h e mi c a l r a w ma t e r i a l s ,i t s a p p l i c a t i o n r a n g e i s v e r y wi d e ,l a r g e t o t h e a r c h i t e c t u r a l d e s i g n, s ma l l p l a s t i c p i p e ma n u f a c ur t i n g wi l l b e u s e d i n p o l y e t h y l e n e p l a s t i c ma t e r i a 1 . T h e u s e o f p o l y e t h y l e n e p l a s t i c p i p e n o t o n l y
PE管件注塑成型工艺优化设计

A 的较好水平为 A3、因素 B 的较好水平为 B2、因素 D 的较好水平为 D1、因素 E 的较好水平为 E1、因素 F 的较好水平为 F2, 它们变化的趋如图 3所示, D E 交互作用虽然不显著, 但也有一定影响, 可用二元 表算出 D 和 E 在各种水平组合下的平均结果, 如表 4所示。由表 4可知, D1E1值最小, 故该搭配使得变 形最小, 即 A、B、C、D、E、F 的最佳组合为 A3 B2 C2 D 1 E1 F2。
本试验为多因素正交试验, 各因素、因素之间的 交互作用和误差对试验指标的影响通过其相应的离
差平方和来表示, 各离差平方和中独立数据的个数 仍用相应的自由度表示。方差分析见表 3。
表 3中 e表示误差, e 为 C、F、e之和, 表中各均 方差是为了消除数据个数对离差平方和的影响, 采 用平均离差平方和 Sj2 /f j ( j取各因素 ) 来进行比较, F 反应因素水平的改变对指标的影响与试验误差对 指标的影响之间的关系, 在一些假定条件下, 可以证 明 F j服从自由度为 ( f j, f e )的 F 分布, 对于给定的显 著水平 , 查 F 分布可得一临界值 F ( fj, fe ), 从而判 定在 水平下因素 j对指标的影响是否显著。在显 著性方差表中, 误差的平方和记为 S2e, 用 所有空列 的离差平方和之和来估计, 因 S2C、SD2 E较小, 将三者 合并为 S2e , 据此求得的 Fj如表 3所示。查 F0. 05 ( f j, fe ) 及 F0. 01 ( fj, f e ) 可知 F 值的临界值如表 3所示。 表中显著性一栏内, 对于 = 0. 05, 检验结果显著则 标以记号 * , 若对 = 0. 01, 若显著则标以 记号
- 1、下载文档前请自行甄别文档内容的完整性,平台不提供额外的编辑、内容补充、找答案等附加服务。
- 2、"仅部分预览"的文档,不可在线预览部分如存在完整性等问题,可反馈申请退款(可完整预览的文档不适用该条件!)。
- 3、如文档侵犯您的权益,请联系客服反馈,我们会尽快为您处理(人工客服工作时间:9:00-18:30)。
3. 31 3. 30 0. 34 6. 95 5. 96 1. 81
0. 62
0. 64
不圆度 /mm
6. 70 6. 78 6. 41 6. 99 7. 00 7. 83 6. 69 6. 94 6. 43 6. 84 6. 95 7. 76 7. 41 7. 84 7. 17 8. 04 8. 01 8. 68 6. 98 7. 61 7. 05 7. 55 7. 45 8. 45 5. 81 6. 33 6. 19 6. 77 6. 5 7. 59 6. 37 6. 92 6. 97 7. 49 7. 32 8. 14 6. 34 6. 93 6. 6 7. 41 6. 67 7. 51 6. 51 7. 05 6. 55 7. 45 7. 31 8. 06 6. 23 6. 37 6. 39 6. 96 6. 69 7. 33
2
3
1
2
1
2
3
3
1
2
2
3
1 6. 36
2
3
1
2
2
3
1
1
2
3
3
1
2 6. 84
2
3
1
2
3
1
2
2
3
1
1
2
3 7. 28
3
1
3
2
1
3
2
1
3
2
1
3
2 6. 32
3
1
3
2
2
1
3
2
1
3
2
1
3 6. 54
3
1
3
2
3
2
1
3
2
1
3
2
1 6. 64
3
2
1
3
1
3
2
2
1
3
3
2
1 6. 45
3
2
1
3
2
1
3
3
2
1
1
3
2 6. 52
对于圆筒状注塑管件, 由于大分子链的柔顺性,
图 1 Y 型三通管件
当制品完全冷却时, 体积收缩和线性收缩变化较小,
产品的尺寸较稳定, 但随着内部残余应力的释放, 当 管件不足以抵抗变形时, 整个孔口沿径向因不均匀
的拉力作用而发生变形, 当某方向拉应力较大时, 整
个圆形便会向朝着与其垂直的方向发生椭圆形变。 不圆度的度量可以采用以下公式计算 [ 5 ] :
致, 我们采用三个孔口变形 的平均值来衡 量, 值越 小, 不圆度越好。将模拟分析的变形数据列于表 2。
1 定模座板; 2 管件; 3 浇口套; 4 定模板; 5 动模板; 6 复位杆; 7 动模固定板; 8 顶针板; 9 推杆固定板; 10 推板; 11 定模座板; 12 推杆; 13 抽芯机构 ; 14 型芯 ; 15 型芯冷却水路 ; 16 型腔冷却水路 ; 17 型芯 ; 18 抽芯机构 ; 19 浇注系统 图 2 Y型三通管件注塑模
很多, 而在一般设置工艺中可控制的主要工艺参数
有注射时间 ( A ) 、模具温度 ( B) 、熔体温度 ( C) 、保压
收稿日期: 2011-02-25
宋财福, 等: PE管件注塑成型工艺优化设计
45
压力 ( D) 、保压时间 ( E) 、冷却时间 ( F )等, 每个因素 水平的变化对制品质量都有一定的影响。此外, 保 压压力和保压时间的交互作用较明显, 亦不能忽略, 将它们记作 D E, 每个因素取 3个水平, 以三通管 件孔口的平均不圆度作为评价产品质量的指标, 其 因素水平设置见表 1。
不同密度 PE 的收缩率变化范围都很大 ( 低密 度 PE 收缩率在 1. 5% ~ 5. 0% 之间, 高密度 PE 在 2. 5% ~ 6. 0% 之间 ), 使得管件的区域收缩不均更 加突出。聚烯烃分子 取向导致的各向 收缩不均是 PE 管件收缩不均的原因, 而收缩不均、分子取向及 制品各处冷却速率不同又导致残余应力, 这是管件 孔口变形的直接原因 [ 3] 。一般而言, 产品结构决定 了 40% 的变形, 模具结 构及材料决定 了 30% 的变 形, 工艺 决定了 10% 的变形, 在制 品结构、模具结 构、材料确定的情况下, 只有利用科学合理的方法设 计制品成型工艺, 才能减少 PE管件孔口的变形 [ 4] 。 1 实例分析
不圆度 = 最大直径 - 最小直径
( 1)
1. 2 正交试验设计
正交试验是试验 设计 ( DOE ) 最常用的试 验方 法之一, 它以概率论及数理统计为理论基础, 依据多
因素、多水平试验中数据的正交性来设计试验, 充分
利用标准化的正交表来安排实验方案, 并对实验结 果进行计算分析, 利用它可以确定在影响产品质量
为了 计算方便, 式中不圆度数 据都已扩大 10 倍, 表中 、 、 分别为各因素在水平 1、2、3时所 对应的不圆度之和, T 为所有试验不圆度平均值的
和, R 为极差, 是不同水平下实验结果离差平方和的 差值。由表 2可以很容易地看出, 第 13号试验的数 据值最小, 对于实验来说, 评价的标准是变形越小越 好, 仅从 、 、 各水平不圆度之和来看, A、B、C、 D、E、F 的水平选择分别为 A3、B2、C2、D1、E1、F2时, 实验结果最佳, 但这只是 729个全面试验中的极少 一部分, 因此所得的结果未必就是最佳的工艺组合; 此外, R 值越大, 说明对应的因素对结果的影响程度 越大, 这个因素就越重要, 反之则表明该因素对指标 的影响小, 通常是不重要因素。根据表 2的结果, 进 行主次排序, 可得各因素对变形影响的大小依次为: D、E、A、B、F、D E、C。 2 方差分析及最佳成型工艺的确定
本试验为多因素正交试验, 各因素、因素之间的 交互作用和误差对试验指标的影响通过其相应的离
差平方和来表示, 各离差平方和中独立数据的个数 仍用相应的自由度表示。方差分析见表 3。
表 3中 e表示误差, e 为 C、F、e之和, 表中各均 方差是为了消除数据个数对离差平方和的影响, 采 用平均离差平方和 Sj2 /f j ( j取各因素 ) 来进行比较, F 反应因素水平的改变对指标的影响与试验误差对 指标的影响之间的关系, 在一些假定条件下, 可以证 明 F j服从自由度为 ( f j, f e )的 F 分布, 对于给定的显 著水平 , 查 F 分布可得一临界值 F ( fj, fe ), 从而判 定在 水平下因素 j对指标的影响是否显著。在显 著性方差表中, 误差的平方和记为 S2e, 用 所有空列 的离差平方和之和来估计, 因 S2C、SD2 E较小, 将三者 合并为 S2e , 据此求得的 Fj如表 3所示。查 F0. 05 ( f j, fe ) 及 F0. 01 ( fj, f e ) 可知 F 值的临界值如表 3所示。 表中显著性一栏内, 对于 = 0. 05, 检验结果显著则 标以记号 * , 若对 = 0. 01, 若显著则标以 记号
表 1 因素水平表
水平
注射 时间 / s
模具 温度 /
1 2. 8
30
2 3. 5
40
3 4. 3
50
熔体 温度 /
200 210 220
保压
保压
压力 /M Pa 时间 / s
20
15
27
20
35
25
冷却 时间 / s
20 30 40
( 2) 正交试验方案 本实验 6个因素都是 3水平, 而且 D、E 存在交 互作用, 因此选用 L27 ( 313 ) 正交表安排试验, 表头设 计时, 将 A、B、C、D、E、F 等因素分别排 在表的第 1 列 ~ 第 6列, 同时根据 L27 ( 313 ) 的交互列表, 将 D、E 交互列 D E 分别放在第 10列、第 12列, 正交试验 方案见表 2。 图 2为所设计的模具图, 在利用 CAE 软件进行 模拟时, 可以根据模具中相应的浇注系统和冷却系 统建模。进行模拟分析时, 对于没有列入正交表的 其它因素, 如注塑压力、注射速度等每次都确保它们 固定在稳定、良好的状态。因每个孔口的变形不一
1
3
3
3
2
2
2
1
1
1
3
3
3 7. 05
1
3
3
3
3
3
3
2
2
2
1
1
1 7. 94
2
1
2
3
1
2
3
1
2
3
1
2
3 6. 98
2
1
2
3
2
3
1
2
3
1
2
3
1 7. 21
2
1
2
3
3
1
2
3
1
2
3
1
2 7. 32
2
2
3
1
1
2
3
2
3
1
3
1
2 5. 74
2
2
3
1
2
3
1
3
1
2
1
2
3 6. 15
2
2
3
1
3
1
2
1
2
3
2
3
1 6. 43
3
2
1
3
3
2
1
1
3
2
2
1
3 7. 13
3
3
2
1
1
3
2
3
2
1
2
1
3 6. 21
3