印刷塑料表面处理分析
塑胶表面处理工艺讲解 喷漆 模内射出装饰 印刷 咬花

•.
使用Formable PET的优缺点
Benefits ◦ Excellent flex resistance ◦ Excellent chemical resistance ◦ Improved formability (form precision not yet determined)
Disadvantages ◦ Cost ◦ Compatibility with moulding resin ◦ Relaxation in mould ◦ Limited supplier choice ◦ Not yet commercial
涂料用颜料,让涂膜显现所想要的 颜色 主要分类如下:
◦ 体质颜料 ◦ 着色颜料 ◦ 特殊颜料
•.
涂料用助剂
涂料中添加例如安定剂、分散剂、防沉 剂等助剂;增加涂料的稳定性。
•.
稀释剂及用途
顾名思义就是要稀释涂料,使涂料稀 释到可以作业的浓度并可以降低涂料 的成本。
•.
稀释剂及用途
稀释剂主要用于稀释涂料中树脂,但由于树脂 的种类不同,所以稀释剂种类不同;主要成 分有机溶剂中的酮类、酯类、醚酯类。利用 有机溶剂各成分沸点的不同,干燥速度也不 同,可以制作成适合各种喷涂设备、作业方 法及涂膜不同的表现。
印刷产品表面处理检验方法与品质标准

印刷产品表面处理常见品质问题点及标准1:过油(含UV磨光):1.1:核对经过油或磨光后之产品颜色是否与OK样办一致,过油类别是否与要求一致,油层与光度是否均匀一致、不甩油或甩色,变色。
变色:油墨不耐高温、酸碱,变色不可与样办颜色明显偏差等不良。
1.2:检查产品表面有无起泡、打皱、烧焦、粘花、拖花、滴油、刮花、油痕;磨光不可有光带接头压痕,不可起灰雾状。
1.3:用光度仪测量产品表面光度能否达到其标准要求(光油≥50°,水油≥55°,UV油≥65°,磨光油≥70°,吸塑油≥75°光胶≥75°哑油:半哑UV45°- 55°,全哑UV15°- 25°);特别注意磨光后纸张收缩,不可超过3MM;1.4:过特别UV之产品则要用3M透明胶将彩纸表面粘牢,快速撕去△45°试验是否能够粘去彩纸及油墨层,不粘起则为OK。
1.5:过吸塑油之产品则要取4-5PCS产品到吸塑机上试验其吸塑效果,用手撕去吸塑罩粘合处看其产品表面彩纸层能否被撕去看到露灰层,粘烂即为OK。
1.6:过油透底,彩纸背面不能有油迹,不能出现油墨没有完全干透,过油时油墨粘在过油辊,转移到纸张其他部位。
已摆好彩纸不能出现相互粘连至脱色。
1.7: UV过厚或印刷彩纸未干透,会造成UV甩油2:过胶:2.1:过胶的类别不可错:光胶、哑胶、黑胶PE、PP薄膜电晕值达到34达因以上达因;CPP和BOPP薄膜电晕值达到38-40达因PET薄膜电晕值达到50达因;PVC薄膜电晕值达到44达因电晕:主要是针对以上材料印刷不掉色对胶膜作的一种物理处理。
不可有PP起泡、发白现象,用刀片轻轻将裱好胶的产品割开“△”撕开需粘起油墨80%在PP膜上方为合格;过胶后表面平整无起泡、砂眼、起皱、雾状、杂质、脏污及过胶不到位;磨花拖花不反光条件下不可视放行。
2.2:过胶产品不到位,接纸边或搭位太大。
塑胶产品的表面处理——印刷篇

塑胶产品的表面处理——印刷篇在工程塑料的表面上印字或图案时,有以下几种方法。
丝网印刷、曲面印刷、渗透印刷、蚀刻印刷,电化铝烫印激光印字(镭雕)。
丝网印刷1).简介丝网印刷是一种古老,而又应用很广的印刷方法。
根据印刷对象材料的不同可以分为:织物印刷,塑料印刷,金属印刷,陶瓷印刷,玻璃印刷,彩票丝印,广告板丝印,不锈钢制品丝印,丝印版画以及漆器丝印等。
2). 塑料丝网印刷塑料件的丝印,是塑料制品的二次机工(或称再加工)中的一种。
塑料制品的种类繁多,但就印刷的方法而言,片材及平面体用平面丝印法;可展开成平面的弧面体用曲面丝印法;异形制品则用间接丝印法。
塑料制品固树脂、添加剂及成型方法的不同,其表面性能的差别很大,尤其是表面的平滑性、极性及静电等问题。
塑料丝网印刷的应用范围:1).ABS塑料的丝网印刷。
ABS树脂塑料,是一种工程塑料。
近年来广泛应用于电视机、计算器等产品以及国民经济许多领域。
2).电子产品塑料部件的外观面的丝网印刷。
电子产品特别是数码相机、MP4、电视机等,对于外观的要求很高的。
塑料丝印开发以后,为电子产品的装饰带来了方便。
3).塑料标牌的丝网印刷。
近年来,塑料标牌及塑料成型后进行丝印图形文字的装饰部件发展很快。
4).软质、硬质塑料件的丝网印刷。
5).仪器面板的丝网印刷。
6).彩色涤纶标牌的丝网印刷。
3.丝网印刷原理其印刷的基本原理是:丝网印版的部分网孔能够透过油墨,漏印至承印物上;印版上其余部分的网孔堵死,不能透过油墨,在承印物上形成空白。
传统的制版方法是手工的,现代普遍使用的是光化学制版法。
这种制版方法,以丝网为支撑体,将丝网绷紧在网框上,然后在网上涂布感光胶,形成感光版膜,再将阳图底版密合在版膜上晒版,经曝光、显影,印版上不需过墨的部分受光形成固化版膜,将网孔封住,印刷时不透墨;印版上要过墨的部分的网孔不封闭,印刷时油墨透过,在承印物上形成墨迹,印刷时在丝网印版的一端倒入油墨,油墨在无外力的作用下不会自行通过网孔漏在承印物上,当用刮墨板以一定的倾斜角度及压力刮动油墨时,油墨通过网版转移到网版下的承印物上,从而实现图像复制。
UV水性油墨印刷塑料底材的表面处理(上)

UV水性油墨印刷塑料底材的表面处理(上)一、光固化水性油墨的印刷和固化特点光固化水性油墨使用水作为稀释剂,采用除湿和UV 辐照固化两种技术的结合来实现印刷过程。
由于这类油墨以水作溶剂,因此,其印刷工艺是:在油墨固化前对湿墨进行除水干燥,得到可指触的干膜,然后进行UV 光辐射,实现UV 油墨的交联固化。
见光部位交联,未见光部分没有交联,冲洗掉后可制得各种图案的固化膜,这是一般的水性油墨难以实现的。
光固化水性油墨可以应用于丝网印刷油墨、凹版及柔版印刷油墨。
然而光固化水性油墨技术在国内至今基本上是空白,应该是大有发展前景的。
光固化水性油墨因其黏度较低,要求墨膜的厚度比较薄,多为微米级,若膜太厚,有可能因上层膜的光屏蔽效应,导致下层墨膜的光固化不完全。
湿膜干燥方法有直接加热烘干法、高速气干法和红外辐射法,其中气干法特别适合于纸质或木质等吸收性底材。
对于吸收性承印材料,有时无需特别干燥,少量水分能直接被底材吸收。
在水性UV 固化油墨中,由于光引发剂本身用量小,且具有一定的水蒸气挥发度,故干燥温度应严格控制,干燥时间不可以太长,否则易造成光引发剂的损失。
油墨成膜过程对于固化膜的最终性能非常重要,水分散性连结料油墨的成膜过程相对于水溶性连结料油墨较难控制。
水分散性油墨的成膜过程实际上是体系中单个粒子(乳液粒或水溶胶粒)之间的聚结过程,当大部分水分蒸发掉时,这些微粒将变形、相互渗透,聚结成无数小块。
最理想的聚结发生在聚合物分子间,这样可得到非常均匀的膜。
光固化水分散性油墨的除水干燥过程因温度升高,也有利于成膜。
二、光固化水性油墨的固化过程光固化水性油墨的固化一般采用中压汞灯,固化程度与墨膜所受的辐射量有关,这一方面取决于光引发剂的有效吸光能力和光引发效率;另一方面,也与汞灯的线功率(w/cm )、辐照时间及辐照距离有关。
光固化水性油墨经紫外光固化后已经形成交联干膜,一般不需要进一步的后固化。
但由于光固化水性油墨常常含有羧基以便获得水溶性或水分散性的系统,这些羧基在光固化后仍然存在于干膜涂层中,对涂层性能会产生负面影响(如墨膜的抗水性能变差等),因此在许多应用中都加入了后固化交联剂,使墨膜在光固化期间或之后进一步固化,消耗掉亲水性的羧基。
塑料表面处理工艺

塑料表面处理工艺塑料表面处理工艺是指对塑料制品表面进行一系列加工和处理,以改善其外观和性能。
塑料表面处理工艺的主要目的是增强塑料材料的耐磨性、耐腐蚀性、耐候性和外观质量,提高塑料制品的使用寿命和附加值。
塑料表面处理工艺有多种方法,常见的包括涂层、喷涂、镀膜、热转印、印刷、丝印等。
其中涂层是最常用的一种处理方法,通过在塑料表面形成一层保护膜,可以提高塑料制品的耐磨性、耐腐蚀性和耐候性。
涂层可以根据不同的要求选择不同的涂料,如聚氨酯涂料、环氧涂料、丙烯酸涂料等。
喷涂是将涂料以喷雾的形式喷到塑料表面,形成均匀的涂层。
镀膜是将金属或其他材料的薄膜镀在塑料表面,使其具有金属的外观和性能。
热转印是将印刷图案通过加热和压力的作用转移到塑料表面,可以实现各种图案和花纹的转移。
印刷是将油墨或颜料印刷在塑料表面,可以实现各种颜色和图案的印刷。
丝印是将油墨通过丝网印刷在塑料表面,可以实现较复杂的图案和文字。
除了上述常见的表面处理工艺,还有一些特殊的工艺可以进一步改善塑料制品的性能。
例如,采用离子注入工艺可以使塑料表面形成一层硬度较高的陶瓷膜,提高塑料制品的耐磨性和耐腐蚀性。
采用纳米技术可以在塑料表面形成一层纳米级的涂层,使塑料制品具有超疏水性、超疏油性或超抗粘性。
采用激光处理工艺可以在塑料表面形成微细的纹理,改善塑料制品的摩擦性能和触感。
塑料表面处理工艺的选择应根据塑料材料的特性、使用环境和使用要求来确定。
不同的工艺有不同的优缺点,需要综合考虑。
此外,表面处理工艺的实施需要专业的设备和技术,操作人员应具备相应的经验和技能。
塑料表面处理工艺是提高塑料制品外观和性能的重要手段。
通过选择合适的处理方法,可以使塑料制品具有更好的耐磨性、耐腐蚀性、耐候性和外观质量,延长其使用寿命,提高其附加值。
塑料表面处理工艺的发展将进一步推动塑料制品的应用领域扩大,为人们的生活带来更多便利和舒适。
塑料的表面处理

塑料的表面处理在印刷效果的试验中,可以发现有些塑料的极性小,表面张力低,印刷效果和粘附牢度难以达到要求,唯有经过表面处理才能改善。
表面处理的方法很多,有机械法:喷砂及磨毛等;物理法:火焰、电晕、辐射及另加涂层等;化学法:氧化、接枝、置换及交联等。
应根据不同的塑料和工艺条件选择适当的处理方法,如聚烯烃(PE及PP)非极性塑料,采用火焰及电晕处理,能使其表面张力提高至 2.8×10-4N/cm(保证粘附牢度的低限)以上;聚酯塑料因含有苯环,其光学活性大,宜于紫外线处理;尼龙可用磷酸处理。
1.塑料印前处理的作用。
①提高丝印油墨对塑料制品的附着力。
②提高丝印效果;使丝印图案更清晰、完整、色泽更鲜艳。
③改善承印物的印刷适性,从而选择价格较合适的丝印油墨,降低印件成本。
④塑料的某些表面处理也能直接改善塑料的表面性能(如抗静电性能等)。
2.塑料印前处理的主要方法。
根据不同塑料品种,不同形状承印物的要求,可采取不同的处理方法。
为改善印刷适性,特别对许多极性小、结晶性大、表面张力低、润湿性差、表面光滑的塑料进行侦处理是十分必要的。
其方法有:退火、脱脂、除尘、溶剂、溶剂气体、化学药品、等离子、紫外线、火焰、热风处理等。
①火焰与电晕须处理。
火焰处理和电晕处理是两种较好的印前处理工艺,可以大大提高塑料片材的表面能,使表面形成很薄的氧化层。
实际上,这两种方法只能暂时提高表面能,因为增塑剂和脱膜剂从塑料中不断溶出,减弱了处理效果。
预处理不能有效地清除片树表面的外部污染物。
事实证明,电晕和火焰处理也不是有效的清!除工艺,它们的作用是提高塑料的表面能。
火焰处理和电晕处理时应当注意,不要处理过分,以免“烧伤”表面。
经测试,处理过的片材具有很高的表面能,印刷时的湿润性也很好,但油墨的粘附性能不好,这是因为燃烧形成的氧化层与原来塑料之间的吸附能力不好造成的。
油墨粘附在塑料的氧化层上,但遗憾的是,氧化层和油墨都容易脱落。
火焰和电晕处理过的塑料,还会将表面能传给表面的油污等外部污染物。
印刷后如何进行表面处理
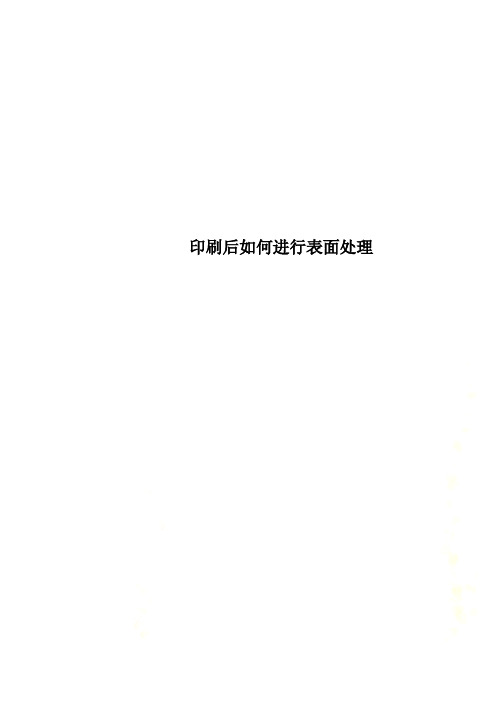
印刷后如何进行表面处理印刷后如何进行表面处理市场竞争的称王败寇,很大的因素取决于商品的包装,包装工业的迅速发展,印后表面处理在包装制作中显得尤为重要,而商品印后表面处理的好坏又决定了包装的质量。
所以,我们可以说印后表面处理是提高包装档次,加强商品市场竞争力的重要技术手段。
常用的印后表面处理技术有:1.表面涂蜡对产品的包装进行表面涂蜡,主要是为使包装能承受一定的水分和湿气,过去常用于鲜肉和农副产品的包装。
这是在帘流涂布机上完成其涂蜡过程的。
2.覆膜覆膜是在包装印刷之后,将取丙烯等塑料薄膜覆盖于印刷品表面,并采用黏合剂经加热加压后使之黏合在一起,形成纸、塑合一的印刷品。
覆膜可分为即涂覆膜与预涂覆膜。
即涂覆膜是在操作时现涂黏合剂,随后热压而得成品。
预涂覆膜是将黏合剂预先涂布在塑料薄膜上,经烘干收卷,在覆印刷制品表面时,只需热压即成。
它们分别在即涂型覆稻草和预涂型覆稻草上完成。
3.上光上光是在包吕印刷表面涂(或喷、印)上一层无色透明涂料,以流平、干燥、压光后在印刷品表面形成薄而匀的透明光亮层。
它由上光机和压光机一道完成。
4.压光压光是对印刷品进行上光后的一道修饰工序,也有的直接对高档纸品直接进行压光。
对印刷品的压光是因为上光料经自然流平、干燥后光泽度不是太理想,对于一些精细印刷品必须进行压光处理。
其所用设备是压光机,许多压光机与上光机配套使用。
5.其他特殊处理技术近些年来出现的印刷品印后特殊处理技术很多,发展也较快。
常见的有表面涂胶(也称喷胶)、表面磨砂(也称打砂,即在印品表面均匀地磨制麻砂点)、压纹压花、压突(凹)或简称压形。
所有这些新的印后修饰技术已在日常使用的高档包装上见得较多。
尤其是精美工艺品、香烟包装上常见。
塑料表面处理工艺调研报告
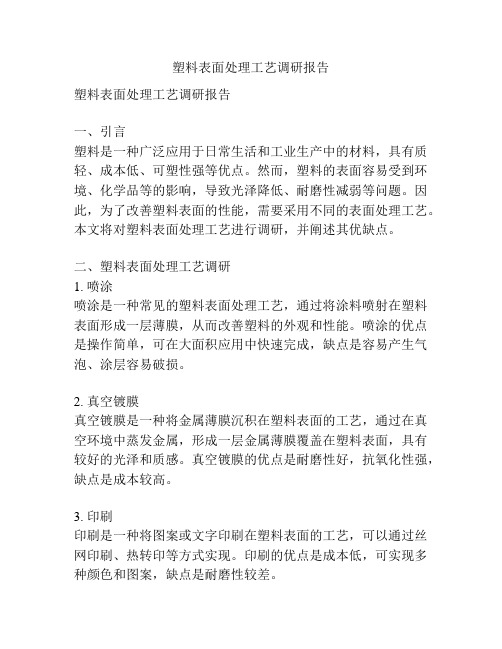
塑料表面处理工艺调研报告塑料表面处理工艺调研报告一、引言塑料是一种广泛应用于日常生活和工业生产中的材料,具有质轻、成本低、可塑性强等优点。
然而,塑料的表面容易受到环境、化学品等的影响,导致光泽降低、耐磨性减弱等问题。
因此,为了改善塑料表面的性能,需要采用不同的表面处理工艺。
本文将对塑料表面处理工艺进行调研,并阐述其优缺点。
二、塑料表面处理工艺调研1. 喷涂喷涂是一种常见的塑料表面处理工艺,通过将涂料喷射在塑料表面形成一层薄膜,从而改善塑料的外观和性能。
喷涂的优点是操作简单,可在大面积应用中快速完成,缺点是容易产生气泡、涂层容易破损。
2. 真空镀膜真空镀膜是一种将金属薄膜沉积在塑料表面的工艺,通过在真空环境中蒸发金属,形成一层金属薄膜覆盖在塑料表面,具有较好的光泽和质感。
真空镀膜的优点是耐磨性好,抗氧化性强,缺点是成本较高。
3. 印刷印刷是一种将图案或文字印刷在塑料表面的工艺,可以通过丝网印刷、热转印等方式实现。
印刷的优点是成本低,可实现多种颜色和图案,缺点是耐磨性较差。
4. 油墨喷印油墨喷印是一种采用喷墨打印设备将图案或文字喷印在塑料表面的工艺。
油墨喷印的优点是快速、高效,可实现高精度的图案印刷,缺点是需要特殊的设备和喷墨墨水,成本较高。
5. 离子注入离子注入是一种通过高能离子束轰击塑料表面,使其发生化学、物理改变的工艺。
离子注入的优点是可以增加塑料表面的硬度、耐磨性,缺点是设备复杂,操作技术要求较高。
三、结论根据对塑料表面处理工艺的调研,不同的工艺有着各自的优缺点。
喷涂工艺操作简单,但涂层容易破损;真空镀膜具有较好的光泽和质感,但成本较高;印刷成本低,但耐磨性差;油墨喷印快速高效,但需要特殊设备和喷墨墨水;离子注入可以增加塑料表面的硬度,但设备复杂。
因此,在选择表面处理工艺时,应根据具体的需求和预算,综合考虑各种因素,在几种工艺中选择最适合的一种。
综上所述,塑料表面处理工艺的选择对于改善塑料表面性能至关重要。
- 1、下载文档前请自行甄别文档内容的完整性,平台不提供额外的编辑、内容补充、找答案等附加服务。
- 2、"仅部分预览"的文档,不可在线预览部分如存在完整性等问题,可反馈申请退款(可完整预览的文档不适用该条件!)。
- 3、如文档侵犯您的权益,请联系客服反馈,我们会尽快为您处理(人工客服工作时间:9:00-18:30)。
印刷塑料表面处理分析
目前应用的塑料薄膜基本材料主要为聚丙烯(PP)、聚已烯(PE)、聚氯乙烯(PVC)、聚酯(PET)等,其表面特性因分子结构基材的极性基团,结晶程度和塑料的化学稳定性等不同而且很大的差异,这些因素对印刷油墨层的粘附牢度影响很大,例如聚乙烯材料,它的分子结构为∈CH2-CH2∈n,因不含极性基团,化学稳定性高,能耐三酸二碱,甚至氢氟酸的腐蚀,在常温下溶于一般的有机和无机溶剂,但对烃类、油类的稳定性较差,可能引起溶胀或变色,在70℃以上能少量溶于氯化烃,四氢化萘等溶剂,另外从乙烯聚合成聚乙烯,在制造聚乙烯粒料过程中,按不同要求掺入了一定数量的助剂,附加剂,下开口剂,当吸膜定型后,这些助剂就浮在膜面,形成肉眼看不见油层,能使薄膜抗老化,透明度提高,光泽度增加,柔软性增加,但这些对印刷是完全不利的,使膜面不易粘合。
其他物质因此在印刷之前,应视不同的塑料表面特性而确定是否需经过表面处理,以提高其印刷油墨粘附牢度。
对属于极性结构的PS(聚苯乙烯)、PVC,印刷前不需要做表面预处理,但对于其表面结构是非极性的PP、PE、PET等,其化学稳定性极高,不易被大多数油墨溶剂所渗透和溶解,与油墨印刷的结合牢度很低,所以在印刷之前必须经过表面处理,表面处理的目的在于使塑料表层活化生成新的化学键使表面粗化,从而提高油墨与塑料表面的结合粘附牢度。
在通常情况下,塑料表面处理的常用方法有以下几种:
1、化学法:是强氧化的一种方法,由于膜面受到侵蚀形成羰基(>C=0)键。
化学氧化处理是先将薄膜经过四氧化碳脱脂,然后浸入H2SO4 88.5%,K2Cr207 4.4%或H2CrO4 7.1%溶液中处理数分中,经水清洗和风干后,尽快地送去印刷。
2、溶剂处理:利用某些有机溶剂或氯烃等洗擦处理表面,使聚烯烃的非结晶部分产生不同程度的熔解,形成粗糙不表的表面,然后以热空气
进行干燥,通常用以下几种溶剂进行表面处理:二甲苯50%与乙醇50%相混,含有一定浓度的过氧化二苯甲酰等。
3、电晕处理:
①电晕处理原理与方法:电晕处理经常用在薄膜吹塑含温线上,因为塑料薄膜中常加入抗氧剂和爽滑剂等助剂,这些助剂有时效性,电晕处理后,即刻印刷,效果最好。
电晕处理装置中包括一个高压交流电机,输出变压器和两个电极;其中一个电级是联接在高压金属极(耐压10-40KV)和高频发生器(1-4KHZ);另一个电极是接地钢轮或刃刀,它和高压电极保持1.5---3mm距离,金属极板的宽度比被处理薄膜的宽度略窄5---10mm,以避免直接放电短路,将处理的薄膜连续的送进两个电极之间,由于高压电使空气中的氧高度电离而产生臭氧,使薄膜表面受到氧化处理,臭氧是一种强氧化剂,可以使膜面氧化,在活性点生成极生基团,从而易于接受油墨,经过处理的表面发生极化,产生静电吸附,并在膜面产生细微的糙化作用,从而改变了薄膜表面与印刷油墨的化学性结合和机械性结合。
电晕处理效果,主要取决于振荡器的输出功率、电极与薄膜表面之间的距离,薄膜的材质及其薄膜通过电极的速度,调节电晕放电的强度,以形成云雾状的紫暗色火花为最佳状态。
②电晕处理对薄膜表面的作用与效果。
A、表面氧化:氧在电晕机处理高压电的作用下产生电离形成臭氧(03)。
臭氧是一种强氧化剂,它可以立即氧化聚乙烯分子,可以在聚乙烯上生产羰基,不饱和键等。
空气中的氮化也同样可以被电离成离子体与聚乙烯分子产生作用,在聚乙烯分子链上生成胺型基团,并可继续被氧化,生成一系列含氧化物。
表面氧化之结果,使聚乙烯薄膜转化极性,由低表面能转化为高表面能,使其对印刷油墨的润湿性,粘附性增加,从而提高印刷品之印迹牢度。
B、表面极化:非导性塑料薄膜在高压频电场作用下,分子内的电荷产生位移,而在表面形成感应电荷,这种感觉电荷的存在就可以在极性的油墨分子产生库仓吸收。
C、表面观察粗造:电晕处理后薄膜表面粗化,用扫描显微照相观察表明:塑料薄膜膜面摩擦系数增大,能改变原来膜面光滑的形状,有利于薄膜印刷的干燥和粘附牢度。
③、电晕表面效果鉴定方法:
A、湿性试验法:因经过氧化后表面粗化,这时若将水或油墨滴在处理过的表面上,就会很快从表面扩展开来。
B、热合粘性化:处理过的薄膜感到特别沾粘,绝热纸(如玻璃)其粘性与牢度成正比。
C、斯考茨(Scatch)粘胶袋试验法:将压敏胶带牢固地加压到薄膜印刷表面,然后快速拉开并记下油墨的转移量,一般油墨的迁移量不超过1%,被认为合格,也可以采用橡皮膏或粘胶带对印刷墨面作粘拉试验来检查处理效果。
D、折皱试验:即将印刷表面搓揉或折皱,油墨不应出现脆裂或成小碎片剥落,否则表明油墨与膜面的结合牢度是不满意的。
E、薄膜电晕处理效果的润湿力试验法。
印刷工艺规定产品质量要达到快干和墨迹厚实,层次清晰,但有时也有会产生印膜脱色和墨层在印刷之中被粘结掉的情况,可采用润湿力试验法检验薄膜电晕效果,其方法是聚乙烯或聚丙烯塑料薄膜表面用棉球棒蘸取甲酰胺和乙二醇乙醚混合液,在要试验的薄膜上涂布一粗道,此液膜保持两秒钟以上时,再用以下表面张力高的混合液试验,液膜在两秒钟内破裂成小液滴时,再用以下表面张力低的混合液试验,从而选定恰当的混合液表面张力作为润湿张力的试样。
薄膜的润湿张力大,说明与油墨的粘合性能好,凡印小面积图纹时塑料薄膜的润湿张力在360un/cm为佳,印大色块,实地薄膜的润湿张力在380un/cm前为佳。
聚烯烃润湿张力测定液配比表:
甲酰胺(%)乙二醇乙醚(%)润湿张力(un/cm)备注1981 330 在相对湿度50%-5%,温度23℃+2℃条件
26.573.5 340
3565 350
42.557.5 360
48.551.5 370
为了使油墨在聚乙烯等薄膜表面润湿,并提高其印迹牢度,必须通过电晕处理,使它从原来310un/cm的表面张力提高到380un/cm,从而使油墨保持不脱色、坚牢;也就是说,如果聚乙烯薄膜表面张力达不到油墨的表面张力数值,则印墨就会掉色,对印墨转移性能低的塑料薄膜进行电晕处理,从而使表面生成的活性游离基氧化,产生亲油层,进一步提高油墨的转移性,由于放电引起的表面极性化和粗糙化,因而可以改善印墨的转移性能。