生产线平衡-电子产品装配线案例
《案例-生产线平衡改善案例OK》
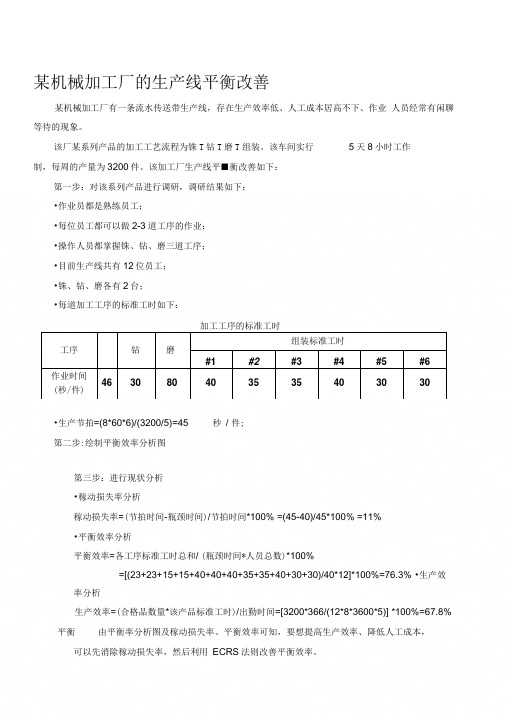
某机械加工厂的生产线平衡改善某机械加工厂有一条流水传送带生产线,存在生产效率低、人工成本居高不下、作业人员经常有闲聊等待的现象。
该厂某系列产品的加工工艺流程为铢T钻T磨T组装。
该车间实行5天8小时工作制,每周的产量为3200件。
该加工厂生产线平■衡改善如下:第一步:对该系列产品进行调研,调研结果如下:•作业员都是熟练员工;•每位员工都可以做2-3道工序的作业;•操作人员都掌握铢、钻、磨三道工序;•目前生产线共有12位员工;•铢、钻、磨各有2台;•每道加工工序的标准工时如下:加工工序的标准工时组装标准工时工序钻磨#1#2#3#4#5#6作业时间463080403535403030 (秒/件)•生产节拍=(8*60*6)/(3200/5)=45 秒/ 件;第二步:绘制平衡效率分析图第三步:进行现状分析•稼动损失率分析稼动损失率=(节拍时间-瓶颈时间)/节拍时间*100% =(45-40)/45*100% =11%•平衡效率分析平衡效率=各工序标准工时总和/ (瓶颈时间*人员总数)*100%=[(23+23+15+15+40+40+40+35+35+40+30+30)/40*12]*100%=76.3% •生产效率分析生产效率=(合格品数量*该产品标准工时)/出勤时间=[3200*366/(12*8*3600*5)] *100%=67.8% 平衡由平衡率分析图及稼动损失率、平衡效率可知,要想提高生产效率、降低人工成本,可以先消除稼动损失率,然后利用ECRS法则改善平衡效率。
第四步:消除稼动损失率消除稼动损失率的核心手段是提高生产量,使生产节拍时间与瓶颈时间相同或接近,即每周产量由3200件提高至3600件。
提高后的生产节拍=实际出勤时间/实际生产数量=8*60*60/(3600/5)=40秒/件这样可以直接减少人员等待时间,大大提高生产效率,改善后的生产效率为:生产效率=(3600*366) / (12*8*3600*5 ) *100%=76.3%第五步:通过ECRQt则进行改善由丁铁、钻的标准时间为23+23+15+15=76秒V 2个生产节拍,因为作业员熟知操作铁、钻、磨工序,所以可以减少一台钻,由4人变为2人操作。
电风扇装配流水线设计与平衡新

目录一、摘要二、企业生产线生产情况 (3)(一)物料清单 (3)(二)流程程序图 (4)三、生产线平衡分析 (6)(一)备选方案一 (7)1.平衡率分析 (8)(二)备选方案二 (9)2.平衡率分析 (9)四、系统建模与仿真 (10)(一)模型一 (10)(二)模型二 (10)五、对比分析 (11)(一) 生产平衡率对比 (11)(二)员工人数对比 (11)六、小结 (12)摘要以某企业生产线的生产情况为研究对象,通过收集生产线的相关数据,做出物料清单表,并绘制出流程程序图。
从而进行生产线平衡分析。
从生产线平衡的基本概念出发,针对该企业生产电风扇的实际情况,分析生产线的平衡设计方法与步骤。
生产线平衡是制造企业底层生产流程设计规划和重组优化的重要方法之一,是在给定的约束条件下,将一系列的作业要素分配给合适数量的工位,满足作业要素之间的优先关系,以提高生产线的生产效率。
分别计算两个方案的平衡率,在对该企业生产线进行仿真实体抽象的基础上,利用Flexsim系统仿真软件建立生产线仿真模型;针对系统仿真软件分别建立的两个模型得出的结果进行分析比较。
通过对该生产线进行设计与仿真,达到了提高生产线产能、平衡各工序负荷的效果,实际数据和仿真数据吻合,验证了仿真技术的有效性和生产线平衡优化方法的可靠性。
关键词:物料清单;流程;生产线平衡;系统建模二、企业生产线生产情况某企业生产电风扇,在一个传送带上进行组装,每天生产量为120台,销售预测量为180台,每天的生产时间为480分钟。
表1列出了电风扇的装配步骤及其定额时间,请根据节拍和作业次序的限制,求生产效率最高的生产线平衡方式。
[1](一)物料清单物料清单是根据生产要求外购的原材料、标准件和成套部件等产生的,主要包括外购件明细表、外协件明细表、自制件明细表和材料明细汇总表。
企业电风扇外框、开关、扇叶及马达如下图1,2,3。
图1电风扇外框图2 电风扇开关图3 电风扇扇叶及马达电风扇物料清单如下表1。
生产线平衡率实例

Nt
=
11.35 mins/台 4.2 mins/台
=
2.702,
or 3
(5)根据排程排产
2
1
1
A
B
G
1.4
H
C
D
E
F
3.25
1.2
.5
1
任务 A C D B E F G H
工位 1
工位2
后续任务 6 4 3 2 2 1 1 0
时间 (Mins) 2
3.25 1.2 1 0.5 1 1 1.4
工位 3
流水线平衡
1.4 H
F 1
任务
A C D B E F G H
工位2
后续任务
6 4 3 2 2 1 1 0
时间 (Mins) 2
3.25 1.2 1 0.5 1 1 1.4
工位 3
C (4.2-3.25)=0.95
Idle=0.2
流水线平衡
2
1
1
A
B
G
C
D
E
3.25
1.2
.5
工位 1
A (4.2-2=2.2) B (2.2-1=1.2) G (1.2-1= 0.2)
Idle=0.2
Idle =0.95
2
1
1
A
B
G
C
D
E
3.25
1.2
.5
工位 1
A (4.2-2=2.2) B (2.2-1=1.2) G (1.2-1=0.2)
流水线平衡
1.4 H
F 1
任务 A C D B E F G H
工位2
后续任务 6 4 3 2 2 1 1 0
生产线平衡案例分析过程

生产线平衡案例分析过程1. 引言生产线平衡是一种优化生产过程的方法,旨在确保生产线上的工作站之间的工作负载均衡,以提高生产效率和产品质量。
本文将以一个实际案例为例,分析生产线平衡的过程。
2. 案例背景假设某公司生产手机,并且生产线上有三个关键工作站:组装、测试和包装。
每个工作站的工人数量不同,导致工作负载不均衡,组装工作站负责最多的工作量,而测试和包装工作站的工作负载较少。
3. 数据收集为了分析生产线平衡的问题,首先需要收集一些关键数据。
包括每个工作站的工作时间、工人数量以及每个工作站的工作量。
工作站工作时间(分钟)工人数量工作量(数量)组装工作站30 3 200测试工作站25 2 150包装工作站20 2 100通过收集这些数据,可以计算出每个工作站的单位时间工作量,即每分钟能完成的工作量。
根据上表数据,可以得出以下结果:•组装工作站的单位时间工作量为6.67件/分钟(200件/30分钟)•测试工作站的单位时间工作量为6件/分钟(150件/25分钟)•包装工作站的单位时间工作量为5件/分钟(100件/20分钟)4. 分析和优化通过计算每个工作站的单位时间工作量,可以判断哪个工作站是生产线上的瓶颈工作站。
在这个案例中,组装工作站的工作量最大,成为瓶颈,会导致生产线的工作负载不平衡。
为了平衡工作负载,可以采取以下优化措施:•调整工人数量:增加组装工作站的工人数量,以减轻其工作负荷。
•优化工作时间:分析工作时间,寻找减少生产时间的方法,例如改进工艺或引入自动化设备。
•转移工作量:将部分组装工作转移到其他工作站,以平衡各工作站的负载。
5. 优化结果评估经过优化措施的实施后,重新计算每个工作站的单位时间工作量,以评估结果。
工作站工作时间(分钟)工人数量工作量(数量)单位时间工作量(件/分钟)组装工作站30 4 200 5测试工作站25 2 150 6包装工作站20 2 100 5通过调整组装工作站的工人数量,将其增加到4人,重新计算单位时间工作量之后,可以看到组装和包装工作站的工作量现在已经达到了平衡,测试工作站的工作量仍然保持不变。
生产线平衡及线速的调整

线速调整的策略和技巧
线速调整的原则
优先调整瓶颈工序:将生产 线的瓶颈工序作为调整的重 点,以提高整体生产效率
保持节拍一致:确保生产线 上的各个环节保持同步,避 免出现生产瓶颈和浪费
逐步调整:不要一次性大幅 度调整线速,应该逐步调整,
观察生产情况并及时调整
保持稳定:在调整线速时, 要保持生产线的稳定,避免
提高产品质量:通过优化生产线和调整线速,可以减少生产过程中的错误和缺陷,提高 产品质量。
增强企业竞争力:通过提高生产效率和降低成本,企业可以获得更高的效益和竞争力。
未来发展趋势与挑战
智能化生产线的普及与发展
线速调整技术的持续优化与提升
添加标题
添加标题
添加标题
添加标题
生产线平衡技术的不断创新与进步
面临的挑战与机遇并存,需要不断 探索与创新
持续改进与创新的重要性
总结生产线平衡及线速调整的经验和成果 分析持续改进与创新对生产效率和质量的影响 探讨未来生产线平衡及线速调整的发展趋势和方向 提出持续改进与创新的建议和措施,促进企业持续发展
THANK YOU
汇报人:
生产线平衡及线速的调整
汇报人:
单击输入目录标题 生产线平衡的概念和重要性 生产线平衡的调整方法 线速调整的策略和技巧
生产线平衡及线速调整的实践案例
总结与展望
添加章节标题
生产线平衡的概念和重要性
生产线平衡的定义
生产线平衡的概念:指在 生产线上各工序所需的时 间接近或相等,使生产线 上各工序的生产能力基本 平衡,提高生产效率。
设备布局调整注意事项:在调整设备布局时,需要考虑设备的维护和保养、员 工的操作习惯和安全等因素,确保调整后的设备布局更加合理、高效和安全。
2010年IE工业工程改善案例(精)
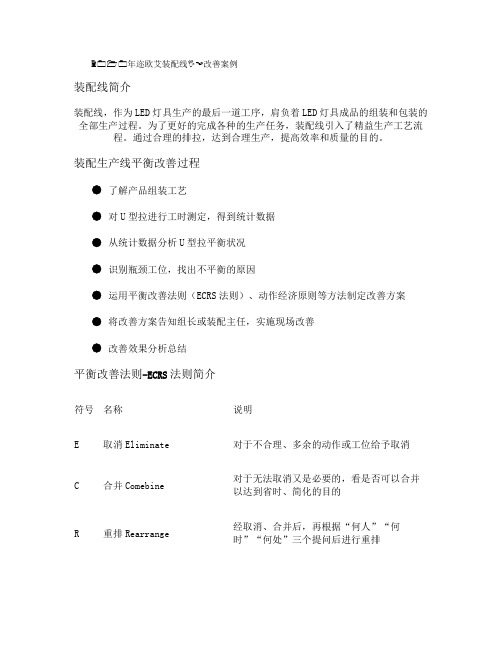
年迩欧艾装配线✋☜改善案例装配线简介装配线,作为LED灯具生产的最后一道工序,肩负着LED灯具成品的组装和包装的全部生产过程。
为了更好的完成各种的生产任务,装配线引入了精益生产工艺流程。
通过合理的排拉,达到合理生产,提高效率和质量的目的。
装配生产线平衡改善过程● 了解产品组装工艺● 对U型拉进行工时测定,得到统计数据● 从统计数据分析U型拉平衡状况● 识别瓶颈工位,找出不平衡的原因● 运用平衡改善法则(ECRS法则)、动作经济原则等方法制定改善方案● 将改善方案告知组长或装配主任,实施现场改善● 改善效果分析总结平衡改善法则-ECRS法则简介符号名称说明E取消Eliminate对于不合理、多余的动作或工位给予取消C合并Comebine 对于无法取消又是必要的,看是否可以合并以达到省时、简化的目的R重排Rearrange 经取消、合并后,再根据“何人”“何时”“何处”三个提问后进行重排S简化Simplify 经过取消、合并、重排后的必要工位,应考虑能否采用最简单的方法或设备替代,以节省人力和时间以上ECRS法则,具体可通过下列图片来说明生产中如何运用改善:装配线平衡典型案例● 数据统计时间:2010/8/2-2010/8/3● 产品编号:53072(太空车)● 组装部分:成品和包装● 改善方案提出时间:2010/8/2● 改善方案实施时间:2010/8/3 改善前各工位组装工艺工位序号组装工艺SPT(秒)人数1 9.5 12 11 13 6 14 13 15 8 16 8 17 8 18 6 19 9 110 10 111 6 112 8 1平衡率=各工序的作业时间/(瓶颈工位时间*人数=(9.5+11+6+13+8+8+8+6+9+10+6+8)/(13*12=65.71%平衡损失率=1-平衡率=34.29%改善前装配线工位平衡图改善措施从统计数据分析这条装配线,可以发现瓶颈工位是工位4。
生产线平衡分析改善案例

生产线平衡分析改善案例引言生产线平衡是指在生产过程中,通过合理分配各个工序的工作量,使得各个工序的产能能够实现平衡,从而提高生产效率、降低成本,并确保产品质量。
本文将以一个实际案例为例,介绍生产线平衡分析和改善的具体过程。
案例背景某电子产品制造公司拥有一条生产线,生产一种电子产品,该产品的组装工序分为A、B、C、D四个子工序。
在目前的生产线上,工序A的生产能力远超其他三个工序,导致A工序成为瓶颈工序,无法满足后续工序的需求,从而影响了整个生产线的效率和产量。
因此,公司决定进行生产线平衡分析,并制定改善方案,以提高生产线的平衡度。
生产线平衡分析1. 数据收集首先,需要收集工序A、B、C、D的工作时间数据,包括每个工序的加工时间、准备时间和等待时间。
这些数据将作为分析的基础。
2. 流程图绘制根据数据收集到的各个工序的时间,并结合实际生产情况,可以绘制出生产线的流程图。
流程图可以清晰地展示每个工序的工作时间和流程顺序,有助于进一步分析。
3. 生产线平衡计算根据流程图,可以计算出每个工序的工作时间总和。
然后,根据目标产量,计算出每个工序的标准工作时间,即每个工序应该占用的时间比例。
通过比较实际工作时间和标准工作时间,可以评估生产线的平衡度。
4. 分析结果根据生产线平衡计算的结果,可以看出工序A的工作时间远超其他工序,导致生产线的不平衡。
这也解释了为什么A工序成为瓶颈工序。
改善方案1. 调整工序A的产能由于工序A是瓶颈工序,可以考虑通过增加设备或优化工艺,提高工序A的产能,以满足后续工序的需求。
这可以通过增加工序A的设备数量、提高工段效率或优化工艺流程等手段实现。
2. 优化其他工序除了调整工序A的产能外,还可以进一步优化其他工序的流程,减少每个工序的工作时间。
例如,可以通过流程改进、工艺优化、培训员工等方式,提高其他工序的效率,从而平衡整个生产线。
3. 调整生产计划根据生产线平衡分析的结果,可以对生产计划进行合理调整。
生产线平衡案例

实施平衡措施后,生产线平衡率得到显著提高, 在制品数量减少,设备故障率降低,整体生产效 率提升。
案例二:电子产品生产线平衡
生产线现状分析
针对电子产品生产线,发现其存在工序繁多、作业时间不稳定、 物料供应不及时等问题。
平衡措施实施
通过作业测定对工序进行重新组合与排序,实现作业时间的均衡化; 加强物料计划与调度管理,确保物料供应的稳定性。
稳定性。
降低生产成本和浪费
减少因生产线不平衡而产生的在制品库存和成品 库存,降低库存成本。
通过优化生产计划和调度,减少生产过程中的停 机、换模等浪费,降低生产成本。
提高设备利用率和员工工作效率,减少人力和物 力的浪费。
增强企业竞争力和可持续发展能力
• 生产线平衡有利于企业实现精益生产和敏捷制造,快速响应市场需求变 化。
优化资源配置
通过生产线平衡,合理配置人力、 物力和财力资源,使生产过程更加 顺畅,提高企业的整体运营水平。
生产线平衡的定义和意义
定义
提升生产效率
降低成本
提高产品质量
增强企业竞争力
生产线平衡是对生产线 上各个工序进行作业时 间分析和调整,使各工 序的作业时间尽可能相 等或接近,以达到提高 生产效率、降低成本的 目的。
编制方法
根据工艺流程图提供的基础数据,计算各工序的生产能力、负荷率等 指标,并按照一定的格式编制成表格。
瓶颈分析和改善
定义
瓶颈分析是指通过分析生产线上各工序的生产能力和负荷 情况,找出制约生产线整体效率的瓶颈工序,并制定相应 的改善措施。
作用
通过瓶颈分析,可以针对生产线上的瓶颈工序进行改善, 提高生产线的整体效率,降低成本,提高产品质量。
即每个产品需要在多长时间内完成生产。
- 1、下载文档前请自行甄别文档内容的完整性,平台不提供额外的编辑、内容补充、找答案等附加服务。
- 2、"仅部分预览"的文档,不可在线预览部分如存在完整性等问题,可反馈申请退款(可完整预览的文档不适用该条件!)。
- 3、如文档侵犯您的权益,请联系客服反馈,我们会尽快为您处理(人工客服工作时间:9:00-18:30)。
b d
0.5分钟 0.5分钟
e
0.2分钟 分钟
0.7分钟 分钟
例题 1: 装配线的平衡
将前一页所显示的作业, 将前一页所显示的作业,安排到工作站之中
采用1.0分钟的周期时间 采用1.0分钟的周期时间 1.0 依照后续工作数最多者, 依照后续工作数最多者,依序安排作业
结束
例题1 例题1的解答
工作站 1 剩餘時間 1.0 .9 .2 1.0 0 1.0 .5 .3 有資格 的 a c 無 b 無 d e 指派工作 閒置時間 a c b d e -
结束
作业指导书制作流程图
了解产品电子/机构 产品/雏型拆解纪录 (设计图/照片) 了解BOM结构 了解产品结构 (爆炸图) 了解生产线编制/ 能力/产品族群
结束
BOM SMT PTH
经由DCC编号 发行 Yes 各类制程 W/I齐备 No
TESTING
标准工时
了解各种作业/ 标准工时 人工编辑/软件协助 编辑
零件黏贴
Ball screw
结束
基版
传感器 送料器
取置头
焊性检验标准 (IPC STANDARDS)
•标准 标准(Preferred) 标准 (1) 零件脚位于焊垫中央。 (2) 零件端点与焊垫间皆充满足够的焊锡, 且呈平滑圆弧形。 (3) 零件脚与焊接面平贴于焊垫上。 •允收 允收(Acceptable) 允收 (1) 零件接着面在焊垫范围内,且50%以上 脚宽位于锡垫范围内。
结束
决定所需工作站的最少数目
结束
N=
(D)( ∑ t) OT
∑ t = 作業時間加總
先行图 (Precedence diagram)
先行图:用来平衡生产线的工具,以显示单元的作 用来平衡生产线的工具, 用来平衡生产线的工具
业和顺序需求
0.1分钟 分钟
第1个作业
结束
1.0分钟 分钟
简单的先行图例
a c
FINAL TEST
PACK ING
SHIP
FORM ING
SUB ASS'Y
HANDLING C BOARD (OPTIONAL) INST. W/S
POST SOLDER
SMT
FORM ING
Terms: Terms •SMT – 表面黏着技术(制程) •Forming – 零件成型 •INST. – 人工插件 (Insertion) •W/S - 波焊制程 (Wave soldering) •Post solder – 接接后作业 (Such as touch-up, rework) •B/I – 烧机测试 (Burn-in)
电子产品与制程趋势
结束
电子产品
结束
PCB 基板 (Printed Circuit Board)
结束
SMT 电子零件
结束
电子构装组织模型
结束
表面装贴 表面装贴制程 (Surface Mount 装贴制程 Technology)
电子产品生产制程 (PCBA)
•Final ass’s – 产品组装作业 •Final test – 产品测试(功能性) •Packing – 产品包装作业
结束
.2 0 .3 .5
2 3
结束
计算闲置时间百分比
每次循環的閒置時間 閒置時間百分比 = (N)(CT)
生产线平衡的规则
一些启发式 (直觉式) 规则: 依照后续作业数最多者先指派 依照最大阶位者先指派
阶位, 阶位,是各个作业时间与其所有后续作业时间的加 总
结束
例题 2
结束
0.2
0.2
0.3
a
结束
作业指导书内容
作业指导书乃依据产品设计图/零件尺寸/零件特性/组合公差 /生产线资源配置/组装方式/循环时间考虑下之产物。 作业指导书之目的在于正确无误与兼顾质量下组装产品并 需符合生产率之需求。 作业指导书内容须包含:
文件编号、产品料号、发行部门、制程别、、、 组装加工顺序 组装图 使用工具 (治夹具) 使用材料列表 工具使用参数 (例如电动起子之扭力设定) 注意事项
FCP-642
1.6M GATE
FIP-III
1M C/V
KOKI REFLOW
1M C/V UNLOADER
Screen printer
Glue dispenser
High-speed placer
Multi-purpose places
Reflow Oven
Line Layouts: •1 x High-speed + 1 x Multi-purpose •2 x High-speed + 1 x Multi-purpose •2 x High-speed + 2 x Multi-purpose
PRE B/I TEST
结束
SMT
A BOARD (TOP) INST. W/S
POST SOLDER
HANDLING
FORM ING
SMT
B BOARD (BOTTOM) INST. W/S
POST SOLDER
B/I (ESS)
PRE B/I TEST POST B/I TEST
FINAL ASS'Y
电子构装生产线/ 电子构装生产线/ 作业指导书制作/ 作业指导书制作/生产线平衡
Prepared by: Dr. Tsung-Nan Tsai
电子产品与制程趋势
多重应用功能(Multi多重应用功能(Multi-purpose Applications) (Multi 携带式与缩小化(Portable 携带式与缩小化(Portable and Miniature)
平行工作站
0.8
b
0.6
e
c
d
f
1.0
g
0.4
h
0.3
结束
例题2 例题2的解答
站1
站2
站3
站4
a c
b
e f d g h
平行工作站
30/小时 30/小时 30/小时
结束
1分钟
1分钟
2分钟
1分钟
30/小时
Bottleneck
30/小时 1分钟 60/小时 1分钟 30/小时 1 分钟. 30/小时 1分钟 30/小时 1分钟 60/小时
结束
PCB PCB 组 装 爆 炸 图
产品组装爆炸图
结束
作业指导书格式
结束
结束
产 品 包 装 作 业 指 导 书
结束
BOM
生产线平衡
生产线平衡
结束
生产线平衡是指派作业到工作站的程序,并 使工作站的周期时间约略相等的方式。
生产线平衡步骤
1. 确认周期时间(Cycle time)及最少工作站数目 2. 自第一个工作站开始,利用经验法则依序自左至 右分配工作站工作。 3. 分配前须选择适当任务指派:
结束
•拒收 拒收(Rejected) 拒收 (1) 焊锡未全部充满于零件接着面与焊垫上, 且零件50%以上脚宽超出焊垫范围。
SMT 检验标准
结束
Preferred
Acceptable
SMT制程控制流程 SMT制程控制流程
结束
表面黏着制造流程
•制程变异监控 •修正措施施行
SMT制程缺点与修护成本趋势 SMT制程缺点与修护成本趋势
PLCC
Chip
元件
SOIC
DIP
Glue dot
Chip 元件 DIPs
TYPE III
Chip元件
SMT 生产作业网络
结束
SMT 生产线布置
结束
结束
High Speed Chip Shooter - Fuji
Speed: 0.09 ~ 0.45 sec/pcs
结束
MultiMulti-purple chip shooter - Fuji
Speed: 1.65 ~ 2.00 sec/pcs
SMT 生产程序
Jobname: 18193r3/18193r3Date: Fri Aug 8
Side: TOP Units: 10 Micro-meters CD PN OR X Y BX BY SD MT -----------------------------------------------------------------------------------------------------------------------------------------------------R17 2 90 -6827 5732 -6727 5732 TOP S Q4 3 90 195 12410 195 12410 TOP S U1 16 180 -8338 12641 -8338 12641 TOP S . . .
a. 所有先行任务皆以分配 b. 作业时间未超过工作站剩余时间 c. 假若找部到合适任务则移至下一个工作站
结束
4. 当每个任务分配后应确认该工作站周期时间减掉 已指派作业时间之总和,以找出剩余时间。
生产线平衡步骤
5. 产生中断时则以下列规则处理之:
a. 分配最长作业时间之任务 b. 分配后续作业最多之任务 c. 如果能处于打结状态,责任选一个任务指派
SMT生产线影像 SMT生产线影像-1 生产线影像-
结束
SMT生产线影像 SMT生产线影像-2 生产线影像-
结束
手焊与修检站
结束
人工插件生产线
结束
电子构装类型
TYPE I
锡膏 SMT Complex FPT Simple
PLCC Chip
结束