第2章塑性和变形抗力
机械工程材料习题答案

第六章 钢的热处理
2、何谓本质细晶粒钢?本质细晶粒钢的奥氏体晶粒是否一定比本质粗晶粒钢的细?
答: wC0.45%碳钢属于低碳钢,室温平衡组织为F+P,其中F和P相对含量分别为:
wF%0.77 0. 77 0.4542%
硬因度此和,伸该长碳率钢等的性硬能度指为标:符合加w合P法%则。 00..747558%
伸长率为:
H 4 5H PV P % H FV F % 1 8 0 5 8 % 8 4 2 % 1 0 4 .4 3 .3 6 1 0 7 .7 6
增加,材料硬度增加、塑性下降,强度在~ wC0.90% 时最高,之后下降。
因此,Rm( σb): wC0.20%< wC1.20%< wC0.77% HBW: wC0.20%< wC0.77%< wC1.20% A: wC1.20%< wC0.77%< wC0.20%
4、计算碳含量为wC0.20%的碳钢的在室温时珠光体和铁素体的相对含量。
B 将( α+β )II 视为一种组织构成项:
WαI=
W(α+β)II=
61.9-30 61.9-19 30-19 61.9-19
=74.36% =25.64%
WαI= W(α+β)II=
61.9-30 61.9-19 30-19 61.9-19
=74.36% =25.64%
则在( α+β )II中含有多少α和多少β相?
2、试述固溶强化、加工硬化和弥散强化的强化原理,并说明三者的区别。
答: 固溶强化:溶质原子溶入后,要引起溶剂金属的晶格产生畸变,进而位错运动时受到阻力增大。 弥散强化:金属化合物本身有很高的硬度,因此合金中以固溶体为基体再有适量的金属间化合物均 匀细小弥散分布时,会提高合金的强度、硬度及耐磨性。这种用金属间化合物来强化合金的方式为 弥散强化。 加工强化:通过产生塑性变形来增大位错密度,从而增大位错运动阻力,引起塑性变形抗力的增加, 提高合金的强度和硬度。 区别:固溶强化和弥散强化都是利用合金的组成相来强化合金,固溶强化是通过产生晶格畸变,使 位错运动阻力增大来强化合金;弥散强化是利用金属化合物本身的高强度和硬度来强化合金;而加 工强化是通过力的作用产生塑性变形,增大位错密度以增大位错运动阻力来强化合金;三者相比, 通过固溶强化得到的强度、硬度最低,但塑性、韧性最好,加工强化得到的强度、硬度最高,但塑 韧性最差,弥散强化介于两者之间。
工程材料力学性能第二章

❖ 7〕 缺点 外表切应力大,心部小,变形不均匀。
二、扭转实验 扭转试样:圆柱形式〔d0=10mm,L0=50m或100mm〕 试验方法:对试样施加扭矩T,相对扭转角以Φ表示
弹性范围内外表的切应力和切应变
扭转试验可测定以下主要性能指标: (1) 切变模量G
在弹性范围内,Kt的数值决定于缺口的几何形状和 尺寸 与材料性质无关.
❖ 2.厚板: ❖ εz=0, σz≠0 ❖ 根部:两向拉伸力状态, ❖ 内侧:三向拉伸的立体应力平面应变状态, ❖ σz =ν〔σy+σx〕 ❖ σy>σz >σx
3.缺口效应: 1〕根部应力集中 2〕改变缺口的应力状态,由单向应力状态改变为两
思考题: ❖ 1 缺口效应及其产生原因; ❖ 2 缺口强化; ❖ 3 缺口敏感度。
❖
第六节 硬度
前言 •古时,利用固体互相刻划来区分材料的软硬 •硬度仍用来表示材料的软硬程度。 •硬度值大小取决于材料的性质、成分和显微组织,测
量方法和条件不符合统一标准就不能反映真实硬度。 •目前还没有统一而确切的关于硬度的物理定义。 •硬度测定简便,造成的外表损伤小,根本上属于“无
可利用扭转试验研究或检验工件热处理的外表质量和各 种外表强化工艺的效果。
❖ 4)扭转时试样中的最大正应力与最大切应力在数值 上大体相等,而生产上所使用的大局部金属材料的 正断抗力 大于切断抗力 ,扭转试验是测定这些材 料切断抗力最可靠的方法。
❖ 5〕根据扭转试样的宏观断口特征,区分金属材料 最终断裂方式是正断还是切断。
油孔,台阶,螺纹,爆缝等对材料的性能影响有以下 四个方面: ❖ 1 缺口产生应力集中 ❖ 2 引起三向应力状态,使材料脆化 ❖ 3 由应力集中产生应变集中 ❖ 4 使缺口附近的应变速率增高
第二章 弹性变形与塑性变形

0
a b f = m− n r r
4
弹性变形概述
胡克定律与弹性常数
任意一点的状态 正应力σx,σy,σz 正应变εx,εy,εz 切应力τxy,τyz,τzx 切应变γxy,γyz,γzx G ≈ 2(1 +ν )E
弹性模量与切变模量
单向拉伸
1 εx = σx E
εy = εz = − σx
19
屈服强度
提高途径
点阵阻力 晶格畸变——包括固溶 位错宽度——越小越好 位错交互作用阻力 位错密度越高越好! Gb τ =α = αGb ρ l 细晶强化!
晶界阻力
Hall-Petch公式 第二相强化
σ s = σ 0 + kd −1/ 2
20
屈服强度
其他影响
温度 温度升高屈服强度降低!
加载速度
7
加载速率 冷变形
弹性模量
弹性模量的各向异性
单晶体 不同晶体学方向弹性模量不同
多晶体 形变织构
宏观显示出各向同性 沿流变方向弹性模量最大
8
弹性极限
比例弹性极限
GB228-63
工程弹性极限 GB6397-86
应力σ
0
应力σ 0
应变ε
应变ε
正切值变化50%
产生0.005%或0.01%或 0.05%残余变形
9
弹性比功
弹性应变能密度
材料吸收变形功而不发生永久变形的能力
1 1 σ e2 u = σ eε = 2 2 E
应用实例
E
0
应变ε 应力σ
工艺方法
提高弹性极限
10
弹性不完善性
弹性后效
应力保持不变!
应变ε
[材料成型工艺技术基础]韩建民版第二章答案
![[材料成型工艺技术基础]韩建民版第二章答案](https://img.taocdn.com/s3/m/da2719133c1ec5da50e27077.png)
[材料成型工艺技术基础]韩建民版第二章答案1.何谓塑性变形?单晶体、多晶体塑性变形的机理各是什么?金属在外力的作用下,内部产生应力,该应力使原子偏离其原来的平衡位置,当应力超过金属材料的屈服极限,外力去除后,原子达到新的平衡状态,金属恢复不到原来的形状和尺寸,产生的永久变形。
单晶体: 晶体在切应力作用下,晶体的一部分与另一部分沿着一定的晶面彼此以刚性的整体相对滑移,滑移的距离为原子间距的整数倍。
多晶体:内部每个晶粒相互协调和配合,当外力达到一定值后晶界发生变形和破碎,其中既有晶内的滑移变形,也有晶间的滑动和转动。
2.何谓冷变形,何谓热变形,冷变形后金属的组织和性能会产生怎么样的变化,热变形后金属的组织和性能会产生怎么样的变化?金属锻造在升温变形过程中,金属原子获得能量,将低温变形中出现的应力吸收,微结构中碎晶形核等生长,将变形晶粒全部消失,这个温度就是再结晶温度,此温度以下的就是冷变形,以上的就是热变形。
冷变形后,晶粒在外力作用下倍扭曲拉长,随着变化逐渐成纤维状,有些晶粒破碎成碎晶,这种结构的晶格对进一步变形有阻碍作用,使金属的的强度和硬度升高,而塑性和韧性下降;热变形后,冷变形过程中出现的碎晶或杂志为核心形核并长大,直到全部冷变形晶粒消失为止,消除加工硬化,这个过程是再结晶不是相变,其晶粒均匀生长细化,塑性增加。
3.为什么规定锻造温度范围?碳钢合理的始锻温度和终锻温度应在铁碳合金状态图的什么位置?锻造温度范围是指始锻温度和终锻温度之间的一段温度间隔。
确定锻造温度的基本原则是,就能保证金属在锻造温度范围内具有较高的塑性和较小的变形抗力,并得到所要求的组织和性能。
锻造温度范围应尽可能宽一些,加热温度太低,表面会开裂,或者内部裂纹,加热温度过高,导致钢坯过烧,无法成型产品。
碳钢的锻造温度范围如图(铁-碳状态图)中的阴影线所示:钢的始锻温度主要受过热的限制,合金结构钢和合金工具钢的始锻温度主要受过热和过烧温度的限制。
机械制造技术基础第二章课后答案

机械制造技术基础第二章课后答案#1.金属切削过程的实质是什么答:金属切削过程就是刀具从工件上切除多余的金属,使工件得到符合技术要求的几何精度和表面质量的过程。
2.切削运动可分哪两类,各有什么特点答:切削运动可分为主运动和进给运动。
主运动在切削过程中速度最高,消耗的功率最大,并且在切削过程中切削运动只有一个。
进给运动的速度较低、消耗的功率较小,进给运动可以有一个或多个。
3.切削用量的主要参数有哪些答.:切削用量的参数有切削速度、进给量和背吃刀量。
4.试述车刀前角、后角、主偏角、负偏角和刃倾角的作用,并指出如何使用答:前角对切削的难易程度有很大的影响,前角大小的选择与工件材料、刀具材料、加工要求有关。
后角的作用是为了减小后刀面与工件之间的摩擦和减少后刀面的磨损。
主偏角的大小影响切削条件、刀具寿命和切削分力的大小。
!5.车外圆时,车刀装得过高或过低、偏左或偏右,刀具角度会发生哪些变化什么情况下可以利用这些变化答:当刀尖高于工作中心时,刀具工作前角将增大,工作后角将减小。
如果刀尖低于工作中心,则刀具工作前角减小,后角增大。
若刀杆右偏,则车刀的工作主偏角将增大,负偏角将减小。
若刀杆左偏,则车刀的工作主偏角将减小,负偏角将增大。
6.试标出图刀具的五个基本角度及主切削刃和副切削刃。
7.列举外圆车刀在不同参考系中的主要标准角度及其定义。
答:1)前角:在正交平面内测量的前刀面与基面之间的夹角;后角:在正交平面内测量的主后刀面与切削平面之间的夹角;主偏角:在基面内测量的主切削刃在基面上的投影与进给方向的夹角;副偏角:在基面内测量的副切削刃在基面上的投影与进给运动反方向的夹角;刃倾角:在切削平面内测量的主切削刃与基面之间的夹角;副后角:在副切削刃上选定点的副正交平面内,副后刀面与副切削平面之间的夹角。
8.偏角的大小对刀具耐用度和三个切削分力有何影响当车削细长轴时,主偏角应选得较大还是较小为什么答:当切削面积不变时,主偏角增大,切削厚度也随之增大,切屑变厚,因而主切削力随着主偏角的增大而减小,但当主偏角增大到60~70之间时,主切削力又逐渐增大主偏角;背向力随着主偏角的增大而减小,进给力随着主偏角的增大而增大。
机械制造技术基础-卢秉恒 答案 第二章

变,而切削宽度aw则随ap的增大正比增大,由于
aw的变化差不多与M和ξ无关,所以ap对Fz的影响
成正比关系。
2-8背吃刀量和进给量对切削力的影响有何不 同? (2)
而f增大一倍,Fz约增大0.8倍,因为f增大,切 削功增大,切削力也相应增大,而f增大,切削厚度 也成正比增大,ac增大,ξ减小,μ减小,又会使切 削力减小,这正反两方面的作用,使切削力的增大 与f不成正比。
磨钝标准决定刀具寿命的长短(正常磨损情况下)。
但是受切削速度,工件材料,刀具材料和刀具几何形状
影响,同一磨钝标准下,刀具寿命是不相同的。
2-16简述车刀、铣刀、钻头的特点。(1)
答:1.车刀是金属切削中使用最广泛的刀具,可完
成工作的外圆,端面,切槽或切断等不同的加工工序。
一般情况下车刀都只有一条主切削刃的单刃刀具,加工 时工作的主运动是工件的旋转运动,进给运动为车刀的 直线运动。
答:粗加工时进给量的选择应考虑机床进给机构的强 度、车刀刀杆的强度和刚度、硬质合金或陶瓷刀片的
强度和工件的装夹刚度等。上述情况可以采用增大刀
尖圆弧半径,提高切削速度的方法来保证粗糙度的前
提下选择较大的进给量。
2-20 如果选定切削用量后,发现所需的功率 超过机床功率时,应如何解决?
答:要么调换较大功率的机床、要么根据所选定的
取
(3)确定切削速度:切削速度可通过 计算,也可查表,本题
查表取
主轴转速 按机床书说明书取 ,实际切削速度为
2、半精工步 (1)确定背吃刀量 : 。
(2)确定进给量 :根据表面粗糙度和刃口圆角半径,并预估
切削速度 ,从表中查出 。按机床说明书中实有的进给量,
第二章 塑性成形力学基础

2 2 2 J 3 x y z 2 xy yz zx ( x yz y zx z xy )
称作应力张量的第一、二、三不变量
讨论: 1. 可以证明,在应力空间,主应力平面是 存在的; 2. 三个主平面是相互正交的; 3. 三个主应力均为实根,不不变量也具 有唯一性;
第二章 塑性成形力学基础
§2.1 §2.2 §2.3 §2.4 §2.5 §2.6 应力分析 应变状态分析 屈服准则 塑性应力应变关系(本构关系) 变形抗力曲线与加工硬化 影响变形抗力的因素
第一节 应力分析
§2.1.1 §2.1.2 §2.1.3 §2.1.4 应力与点的应力状态 点的应力状态分析 应力张量的分解与几何表示 应力平衡微分方程
ij xx
、
xz
……
(便于计算机应
i、j同号为正,异号为负
任意斜面的应力
变形体内任一点M某 一斜面上的应力分 布为?
设过M点三个坐标面上的应 力为已知。设斜面与三个坐 标轴的截距为dx、dy、dz,斜 面外法线n的方向余弦分别为: m、n、l ,全应力为,它在 三个坐标轴上的投影为sx、sy、 sz。在n上的分量为 ,在 作用面上的分量为 。
' x x m ,
' y y m
z' z m
讨论:
分解的依据:静水压力实验证实,静水压力不会引起变形体形 状的改变,只会引起体积改变,即对塑性条件无影响。 为引起形状改变的偏应力张量 (deviatoric stress tensor) , 为引起体积改变的球张量 (spherical stress tensor) (静水 压力)。 与应力张量类似,偏应力张量也存在相应的不变量:
第二章 材料的变形——塑性变形1
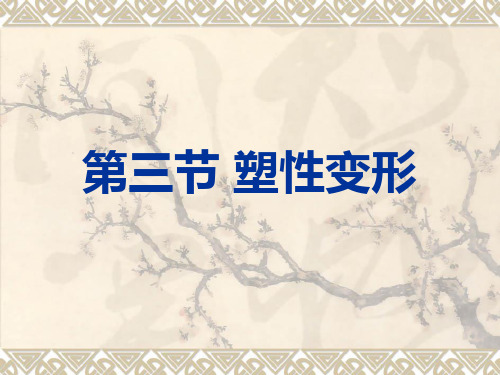
许多滑移系并非同时参与滑移。只有当外力 在某一滑移系中的分切应力达到一定临界值 时,该滑移系方可首先发生滑移,该分切应 力称为滑移的临界分切应力。 沿滑移面滑移方向的分切应力; 能够引起滑移系开动的分切应力。
切应力的作用下,晶格发生弹性外扭,进一步将使晶格发生滑 移。外力去除后,由于原子到了一新的平衡位置,晶体不能恢 复到原来的形状,而保留永久的变形。大量晶面的滑移将得到 宏观变形效果,在晶体的表面将出现滑移产生的台阶。
向(孪生方向)发生切变,形成对称的晶格排列,发生切变
部分叫做孪生带,或简称为孪晶。切变部分和未切变部分 呈镜面对称,对称面为孪生面。
孪生变形的特点
孪生需要的临界切应力很大,仅在滑移困难时才会发 生。一般孪生出现在滑移系很少的晶体结构的材料中 (如密排六方晶格金属);某些容易发生滑移的立方材 料仅在低温度滑移困难或受冲击时来不及滑移时才可 能产生孪生。 孪生是一种均匀切变,即切变区内与孪晶面平行的每 一层原子面均相对于其毗邻晶面沿孪生方向位移了一 定的距离,移动量都相同。
滑移、孪生、蠕变、晶界滑动。
2.1 滑移
单晶体的塑性变形的主要方式是滑移和
孪生。其中滑移是最基本、最普遍的塑 性变形方式,孪生只是在滑移难以进行 的情况下出现。
单晶体的圆柱试样表面抛光后拉伸,试样表
面就会出现一系列平行的变形痕迹。 光镜观察,试样表面形成的浮凸,由一系列 滑移迹线组成,称为滑移带。
就越来越大。
此外,塑性变形也会导致晶格畸变,使外力和滑移面的相 对位向也会发生变化。使开动位错所需应力增大。
பைடு நூலகம்
2.2孪生变形
——孪晶:两个晶体或者晶体的两个部分沿
一个公共晶面构成镜面堆成的位向关系
- 1、下载文档前请自行甄别文档内容的完整性,平台不提供额外的编辑、内容补充、找答案等附加服务。
- 2、"仅部分预览"的文档,不可在线预览部分如存在完整性等问题,可反馈申请退款(可完整预览的文档不适用该条件!)。
- 3、如文档侵犯您的权益,请联系客服反馈,我们会尽快为您处理(人工客服工作时间:9:00-18:30)。
3)晶间滑移作用增强:晶界切变抗力降低;晶界滑移引起的微裂纹被消
除。 4)金属的组织、结构的变化:多相——单相;晶格的结构改变,如钛: 室温hcp(密排六方)——bcc (体心立方)
• 在加热的某些温度区间,由于相态或晶界状态的 变化而出现脆性区,使金属的塑性降低。
蓝脆区:中温(200-400℃)区,由于氧化物、氮化物以 沉淀形式在晶界、滑移面上析出; 热脆区:高温(800-950℃)区,珠光体转变为奥氏体, 使得铁素体和奥氏体共存,另外,晶界处可能析出FeSFeO低熔点的共晶体;
高温脆区:加热温度超过1250℃后,由于过热、过烧,
晶粒粗大,晶界出现氧化物和低熔物质的局部熔化
碳钢的塑性随温度的变化曲线
(四)应变速率对塑性的影响
影响是双方面的:
• 一方面,随变形速率的增大,金属的塑性降低:没有足
够的时间进行回复或再结晶,软化过程进行得不充分。 • 另一方面,随着变形速率的增加,在一定程度上使金属 的温度升高,温度效应显著,从而提高金属的塑性。但 对于有脆性转变的金属,则应变速率的增加可能引起塑 性的下降。
(三)变形温度的影响
几乎所有的金属和合金,变形抗力都随温度的升 高而降低; 但是当金属和合金随着温度的变化而发生物理-化 学变化和相变时,会出现相反的情况,如钢在加热过 程中发生的蓝脆和热脆现象。
(四)变形程度的影响
随变形程度的增加,会产生加工硬化,使继续变 形发生困难,因而变形抗力增加。 当变形程度较高时,促进了回复与再结晶过程的 发生与发展,变形抗力的增加变得比较缓慢。• • • • • •
2)外因:变形时外部条件,如变形温度和受力状况等。
塑性指标:
为衡量金属塑性的高低而确定的数量上的指标, 一般以金属材料开始发生破坏时的塑性变形量来表 示。 常用的塑性指标: 拉伸试验伸长率δ(%) δ= 100%
断面收缩率Ψ(%)
A0 Ak Ψ = A0
L0、 Lk
100%
为试样的原始标准间距和试样断裂后标距间长度; 为试样的原始横截面积和试样断裂处的最小横截面积。
碳钢塑性图
二、对塑性的影响因素
内部因素:化学成分 组织结构
外部因素:变形温度 应变速度 应力状态
(一)化学成分和合金成分对金属塑性的影响
• 金属的塑性随其纯度的提高而增加,如纯铝99.96%伸长率为45%, 98%伸长率为30 % • 使合金产生脆化现象,冷热变形都非常困难。如碳钢中: P(磷)——冷脆 S——热脆 N——时效脆性 H——氢脆 • 杂质的存在状态、分布情况和形状不同,对塑性的影响也不同; 不溶于金属单质或化合物 ————— 降低金属塑性 形成固溶体 塑性变化不大 溶于金属 —————
7、其它元素:主要是降低钢的塑性,提高变形抗力
合金元素对铁素体伸长率和韧性的影响
(二)组织状态对金属塑性的影响
• 晶格类型的影响 面心立方——12个滑移系,同一滑移面上3个滑移方向, 塑性最好,如铝、铜和镍等。 体心立方——12个滑移系,同一滑移面上2个滑移方向, 塑性较好,如钒、钨、钼等。 密排六方——3个滑移系,塑性最差,如镁、锌、钙等。 • 晶粒度的影响 晶粒度越小,越均匀,塑性越高。
图 13-27 九种主应力图(按塑性发挥的有利顺 九种主应力图(按塑性发挥的有利顺
图 13-27 九种主应力图(按塑性发挥的有利顺序排列) 九种主应力图(按塑性发挥的有利顺序排列) 图 13-27
•
应力状态不同对塑性的影响也不同: 主应力图中压应力个数越多,数值越大,则金属的塑性 越高;拉应力个数越多,数值越大,则金属的塑性就越低。 原因:
• 杂质的含量、杂质的性质及其在基体中的分布特性。
(二)组织结构的影响
• 结构变化: 组织状态不同,变形抗力不同; 组织结构的变化(相变),变形抗力也发生变化。 • 晶粒大小: 晶粒越细,同一体积内的晶界越多,变形抗力就高(室 温晶界强度高于晶内)。
• 单相组织和多相组织: 单相组织合金元素含量越高,晶格畸变越严重, 变形抗力越大。单相组织比多相组织的变形抗力小。 多相组织中第二相的性质、形状、大小、数量和 分布状况对变形抗力都有影响: 硬而脆的第二相在基体相晶粒内呈颗粒状弥散分布时, 合金的变形抗力就高; 第二相越细,分布越均匀,数量越多,变形抗力就越 大。
见下图
碳 含 量 对 碳 钢 力 学 性 能 的 影 响
2、磷 钢中有害杂质,在钢中有很大的溶解度,易溶 于铁素体,使钢的塑性降低,在低温时更为严重, 这种现象称为冷脆性。 此外,磷具有极大的偏析倾向,能促使奥氏体晶 粒长大。 3、硫 钢中有害物质,主要与铁形成FeS,与其它元 素形成硫化物。 硫化物及其共晶体( Fe-FeS ),通常分布于晶 界上,在钢的锻造温度范围内会发生变形开裂,即 “热脆”现象。 在钢中加入适量锰,生成MnS,硫化锰及其共 晶体的熔点高于钢的锻、轧温度,不会产生热脆性, 从而消除硫的危害。
• 相组成的影响 单相组织塑性好;多相组织塑性差。(晶界、晶内; 硬相、软相) • 铸造组织的影响 铸造组织具有粗大的柱状晶粒,具有偏析、夹杂、 气泡、疏松等缺陷,因而塑性较差。
(三)变形温度对金属塑性的影响
• 对大多数金属而言,总的趋势是随着温度升高,塑性增加。
原因:
1)发生回复与再结晶,消除了加工硬化; 2)原子动能增加,位错活动加剧,出现新的滑移系,改善晶粒之间变形 的协调性。
例子不讲!
下面以碳钢为例,分析碳及杂质元素(P、 S、 N、 H、 o)对塑性的影响
1、碳 碳对碳钢性能的影响最大 1)碳能固溶于铁,形成铁素体和奥氏体,它们具有良好
的塑性。
2)当铁中的碳含量超过其溶碳能力时,多余的碳便以渗 碳体Fe3C形式出现,它具有很高的硬度,而塑性几乎为 零。 含碳量越高,渗碳体的数量越多,金属的塑性也越差。
A0 、Ak
塑性指标还可以用镦粗实验和扭转试验测定。 镦粗试验(试样的高度为直径的1.5倍)中,以出现
第一条裂纹时的变形程度为塑性指标:
c
、
H0 Hk = H0
100%
试样原始高度和表面出现第一条裂纹 时的高度
注样
镦粗试验
塑性图: 在不同的变形速度下,以不同温度下的各 种塑性指标( 、 、 、 、ak等)为纵坐标、 以温度为横坐标绘制成的函数曲线。
• 杂质元素之间相互作用对金属的塑性产生影响; 硫 +Fe —— FeS(熔点1190℃ ),热脆 +Mn —— MnS (熔点1600℃ ),塑性提高。 • 合金元素特性、数量、元素之间的相互作用及分布等对金属 的塑性产生影响。 碳:形成单相固溶体(fcc)——铁素体和奥氏体——有较好 的塑性; 形成脆性过剩相——渗碳体——塑性降低。 铬、钨、钼、钛、钒:形成硬而脆的碳化物——塑性下降。 钛、钒:形成高度弥散的碳化物细小颗粒——对塑性影响 不大。 注:对冷加工用钢而言,含碳量应尽量低。
第一节 金属的塑性和变形抗力
一、塑性、塑性指标和塑性图 塑性:金属在外力作用下发生永久变形而不破坏其完整性的
能力。
1、塑性反映了材料产生塑性变形的能力; 2、塑性不是固定不变的,同一种材料,在不同的变形条件 下,会表现出不同的塑性。 3、影响金属塑性的因素主要有两方面:
1)内因:金属本身的晶格类型、化学成分和金相组织等;
4、氮 在钢中主要以氮化物Fe4N形式存在。当含量较小 时,对钢的塑性影响较小;当含量增加时,钢的塑性 下降。 当含氮量较高的钢从高温快冷至低温时,α铁被 过饱和,随后以Fe4N形式析出,使钢的塑性、韧性大 大下降,这种现象称为时效脆性。 5、氢 钢中溶氢,会使钢的塑性、韧性下降,造成所谓 “氢脆” (白点) 。 6、氧 在钢中溶解度很小,主要以氧化物的形式出现, 降低钢的塑性。与其它夹杂物形成共晶体,分布于晶 界处,造成钢的热脆性。
这是由于拉应力促进晶间变形,加速晶界破坏,而压应力
阻止或减小晶间变形; 另外,三向压应力有利于抑制或消除晶体中由于塑性变形 而引起的各种微观破坏,而拉应力则相反,它使各种破坏 发展,扩大。
变形抗力: 金属在发生塑性变形时,产生抵抗变形的能力,称为 变形抗力,一般用接触面上平均单位面积变形力表示 变形抗力大小 取决于材料在一定变形条件下的真实应力,还取决于 塑性加工时的应力状态、接触摩擦状态和变形体的尺寸 因素等。 注:只有在单向应力状态下,材料的变形抗力才等于材料 在该变形条件下的真实应力。
注:塑性和变形抗力是两个不同的概念 塑性 —— 反映材料塑性变形的能力 变形抗力 —— 反映塑性变形的难易程度/强度! 塑性好不一定变形抗力低,反之亦然。
变形抗力的影响因素
(一)化学成分的影响 • 金属纯度越高,变形抗力越小。
• 合金元素的原子与基体原子间相互作用的特性、原子 体积的大小以及合金原子在基体中的分布等。(基体 点阵畸变)
拉拔和挤压时不同的应力状态和变形抗力
(五)应力状态对塑性的影响
主应力图: 自变形体中某点取一立方微单元体,用箭头表示作用 在该单元体主应力,称为主应力图,主应力图只表示出 应力的个数和方向,并不表示应力的大小。 主应力图有九种: 单向主应力图:
二向主应力图:
图 13-27 九种主应力图(按塑性发挥的有利顺序排列) 图 13-27 图 13-27 九种主应力图(按塑性发挥的有利顺序排列) 图 13-27 九种主应力图(按塑性发挥的有利顺序排列) 三向主应力图:
(五)变形速度的影响
一般情况下,随着变形速度的增加,变形抗 力提高(特别热变形)。 原因:
一方面,变形速度提高,单位时间内的发热率增加, 使变形抗力降低。
另一方面,变形速度提高也缩短了变形时间,使位错 运动的发展时间不足(滑移来不及进行) ,促使变形抗 力增加。
(六)应力状态的影响
应力状态不同,变形抗力不同。如挤压时金属处于三 向压应力状态,拉拔时金属处于一向受拉二向受压的应 力状态。挤压时的变形抗力远比拉拔时变形抗力大。