丰田的模具制造概况
冲压模具技术国内外发展现状 nbsp;
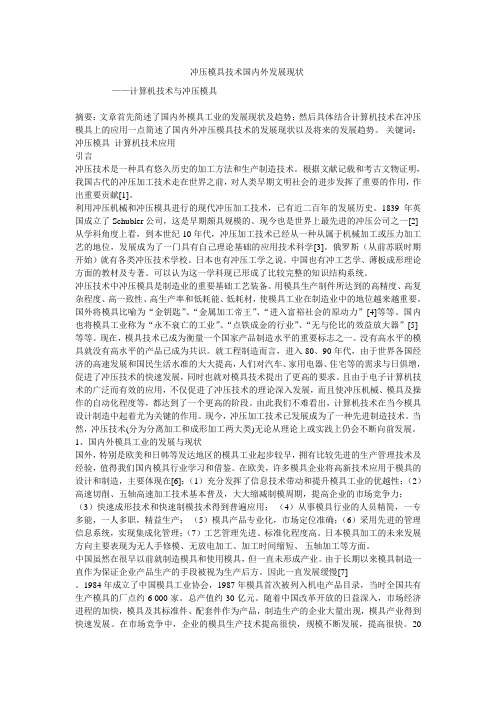
冲压模具技术国内外发展现状——计算机技术与冲压模具摘要:文章首先简述了国内外模具工业的发展现状及趋势;然后具体结合计算机技术在冲压模具上的应用一点简述了国内外冲压模具技术的发展现状以及将来的发展趋势。
关键词:冲压模具计算机技术应用引言冲压技术是一种具有悠久历史的加工方法和生产制造技术。
根据文献记载和考古文物证明,我国古代的冲压加工技术走在世界之前,对人类早期文明社会的进步发挥了重要的作用,作出重要贡献[1]。
利用冲压机械和冲压模具进行的现代冲压加工技术,已有近二百年的发展历史。
1839年英国成立了Schubler公司,这是早期颇具规模的、现今也是世界上最先进的冲压公司之一[2] 从学科角度上看,到本世纪10年代,冲压加工技术已经从一种从属于机械加工或压力加工艺的地位,发展成为了一门具有自己理论基础的应用技术科学[3]。
俄罗斯(从前苏联时期开始)就有各类冲压技术学校。
日本也有冲压工学之说。
中国也有冲工艺学、薄板成形理论方面的教材及专著。
可以认为这一学科现已形成了比较完整的知识结构系统。
冲压技术中冲压模具是制造业的重要基础工艺装备。
用模具生产制件所达到的高精度、高复杂程度、高一致性、高生产率和低耗能、低耗材,使模具工业在制造业中的地位越来越重要。
国外将模具比喻为“金钥匙”、“金属加工帝王”、“进入富裕社会的原动力”[4]等等。
国内也将模具工业称为“永不衰亡的工业”、“点铁成金的行业”、“无与伦比的效益放大器”[5] 等等。
现在,模具技术已成为衡量一个国家产品制造水平的重要标志之一。
没有高水平的模具就没有高水平的产品已成为共识。
就工程制造而言,进入80、90年代,由于世界各国经济的高速发展和国民生活水准的大大提高,人们对汽车、家用电器、住宅等的需求与日俱增,促进了冲压技术的快速发展,同时也就对模具技术提出了更高的要求。
且由于电子计算机技术的广泛而有效的应用,不仅促进了冲压技术的理论深入发展,而且使冲压机械、模具及操作的自动化程度等,都达到了一个更高的阶段。
丰田生产方式发展历史

丰田生产方式发展历史丰田汽车公司是日本最大的汽车制造商之一,也是全球最大的汽车制造商之一、丰田公司在汽车制造方面拥有丰富的经验和技术,其生产方式经历了长期的发展和演变。
从丰田公司创立之初到现在,丰田的生产方式已经成为了世界汽车制造业的标杆。
丰田公司成立于1937年,当时的丰田是一家小型的纺织机器制造商。
但是,由于日本市场逐渐增长,丰田公司开始考虑进入汽车制造行业。
在丰田公司创始人丰田喜一郎的领导下,丰田公司采用了大规模生产方式来生产汽车。
大规模生产是现代汽车制造的基础,它以高度的自动化和标准化为特征。
丰田公司在20世纪50年代初开始使用大规模生产技术,这一时期丰田的销售迅速增长。
然而,在1950年代末到1960年代初,丰田公司面临着一系列的质量问题,这也意味着大规模生产方式的局限性开始显现。
为了解决质量问题,丰田公司在20世纪50年代末到60年代初进行了一项重大,被称为“丰田生产系统”(TPS)。
这个系统是由丰田公司的工程师大野耐一提出的,他试图改变传统的大规模生产方式,以提高质量和效率。
丰田生产系统的核心原则是“精益生产”,即实现最大价值和最小浪费的生产方式。
丰田生产系统的核心是“稳态制造”,即在稳态下降低浪费和提高效率。
为了实现这一目标,丰田采用了一系列的技术和方法,如“小批量生产”、“停线”、“雪藏”和“自动化设备”。
小批量生产是指将生产任务分成较小的批次,以降低库存和浪费。
停线是指在发现问题时立即停止生产线,找出问题的根本原因,并进行纠正。
雪藏是指在生产线上停止生产,以等待下一道工序准备好。
自动化设备是指在生产线上使用自动化机器和设备,以提高效率和质量。
通过实施丰田生产系统,丰田公司获得了巨大的成功,不仅在销售和利润上增长,而且在质量和效率上也取得了显著进步。
丰田生产系统成为了世界各国汽车制造商效仿的典范,被誉为“世界级制造”。
然而,随着世界经济的变化和技术的进步,丰田公司也面临着新的挑战。
模具设计与制造毕业设计_说明
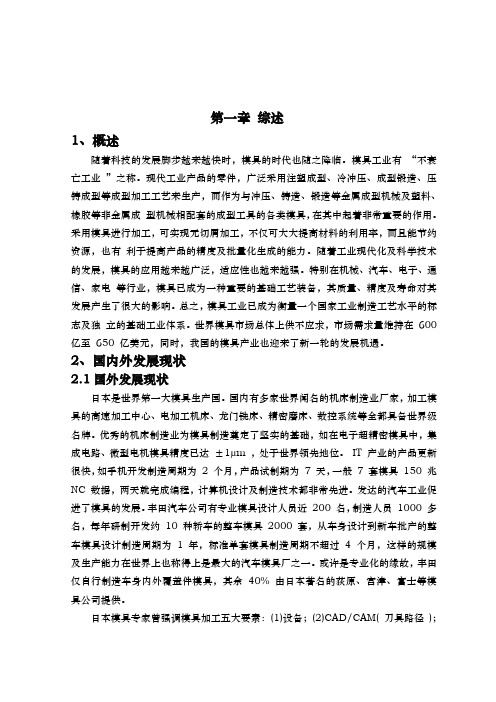
第一章综述1、概述随着科技的发展脚步越来越快时,模具的时代也随之降临。
模具工业有“不衰亡工业”之称。
现代工业产品的零件,广泛采用注塑成型、冷冲压、成型锻造、压铸成型等成型加工工艺来生产,而作为与冲压、铸造、锻造等金属成型机械及塑料、橡胶等非金属成型机械相配套的成型工具的各类模具,在其中起着非常重要的作用。
采用模具进行加工,可实现无切屑加工,不仅可大大提高材料的利用率,而且能节约资源,也有利于提高产品的精度及批量化生成的能力。
随着工业现代化及科学技术的发展,模具的应用越来越广泛,适应性也越来越强。
特别在机械、汽车、电子、通信、家电等行业,模具已成为一种重要的基础工艺装备,其质量、精度及寿命对其发展产生了很大的影响。
总之,模具工业已成为衡量一个国家工业制造工艺水平的标志及独立的基础工业体系。
世界模具市场总体上供不应求,市场需求量维持在600 亿至650 亿美元,同时,我国的模具产业也迎来了新一轮的发展机遇。
2、国内外发展现状2.1国外发展现状日本是世界第一大模具生产国。
国内有多家世界闻名的机床制造业厂家,加工模具的高速加工中心、电加工机床、龙门铣床、精密磨床、数控系统等全都具备世界级名牌。
优秀的机床制造业为模具制造奠定了坚实的基础,如在电子超精密模具中,集成电路、微型电机模具精度已达±1μm ,处于世界领先地位。
IT 产业的产品更新很快,如手机开发制造周期为2 个月,产品试制期为7 天,一般7 套模具150 兆NC 数据,两天就完成编程,计算机设计及制造技术都非常先进。
发达的汽车工业促进了模具的发展。
丰田汽车公司有专业模具设计人员近200 名,制造人员1000 多名,每年研制开发约10 种轿车的整车模具2000 套,从车身设计到新车批产的整车模具设计制造周期为1 年,标准单套模具制造周期不超过4 个月,这样的规模及生产能力在世界上也称得上是最大的汽车模具厂之一。
或许是专业化的缘故,丰田仅自行制造车身内外覆盖件模具,其余40% 由日本著名的荻原、宫津、富士等模具公司提供。
【图】丰田全球工厂的那些事儿

【图】丰田全球工厂的那些事儿卡罗拉的销量;兰德酷路泽的越野;普锐斯的混动......想要给丰田的车型贴个标签太容易了。
不过这次我们不聊产品,应AL频道粉丝的要求,继本田之后我们再来聊聊丰田全球工厂的那些事。
汽车界的“黄金工厂”——田原工厂位置:日本本州岛爱知县投产时间:1979年生产能力:510,000辆生产车型:雷克萨斯全系面向地区:日本本土以及全球雷克萨斯出口市场1979年投产的田原工厂作为丰田在全球最大的独立工厂,也是最自动化的工厂之一,共有1500个机器人,自动化的程度高达95%,主要集中在压制和焊接的操作。
其中第四号装配线是丰田集所有的试验研究于一身,竭尽所能地提高自动化程度,是田原工厂被称为全世界最高科技的工厂的基础。
JD Powe咨询公司三度颁发白金奖项,封它为全世界最有效的工厂。
工厂中的“混合动力”——堤工厂位置:日本本州岛爱知县投产时间:1970年生产能力:500,000辆生产车型:卡罗拉、凯美瑞、皇冠、普锐斯等多款混合动力车型面向地区:日本本土以及海外市场左图:厂房顶的太阳能板右图:工业排放水出口的鱼池堤工厂目前拥有有两条生产线,第一条生产线每天生产664辆,其中混合动力约占81%;第二条生产线每天生产731辆,其中混合动力约占96%。
作为日本本土混合动力车型重要的生产基地,不仅具有高效的生产能力,而且也采用了大量的环保技术。
工厂车间顶部全部使用太阳能发电板,可以提供全厂的5%的电力供应;工厂外墙全部使用光催化涂层,净化空气,成为了真正意义上的“混合动力”环保节能型工厂。
廉颇虽老尚能饭:一汽丰田泰达工厂位置:天津市经济开发区厂区面积:217个足球场投产时间:2002年生产能力:420,000辆生产车型:威驰、花冠、皇冠、卡罗拉、锐志面向地区:中国大陆左图:泰达工厂鸟瞰图右图:泰达工厂整体布局追溯历史,天津一汽丰田前身是2000年天津汽车和丰田合资成立的天津丰田。
2002年“天一重组”成立天津一丰田,而泰达工厂是由重组之后建立的第二工厂和第三工厂改造而成。
丰田一汽在津合资兴建冲压模具公司

板后 , 用螺钉旋 人 凸模垫板 紧 固。
7极 爪 圆 弧 成 形 凸模 .
9夕 形 冲切 与载体 分离 凸模 1 . 形 弹簧 l . 料螺 钉 1. . O矩 1 卸 2卸 料 定距 套 1 . 3凹模 成形 镶 套 1 . 4弹顶 杆 1. 5 凹模 镶 套 1 . 6顶 杆 1. 冲切 凹模镶 套 1 . 形 顶 块 1. 部 外形 弯 曲 凸 7夕 形 8成 9局 2 . 部外 形 圆 弧成 2局
模 I 2 . 部外 形 弯 曲 凸模 Ⅱ 2 . O局 1凹模
形镶 件 I 2 . 部外 形圆弧 成形 镶件 Ⅱ 2 . 部外 形 冲切凹模 3局 4局
镶套 I 2 . 5 局部外 形 冲切 凹模 镶 套 Ⅱ 2. 爪 冲切 凹模 镶套 6极
图… 嘲
() a () b
维普资讯
删 II 超 口梗 N ]趣 I 国 具
_
C H I A . U# N  ̄
lN UL IMO D
・ 冲
模
技
术 ・
I l 三 三 三 三 r 乌 三 曼 ~I
又是高 速冲压模具 , 凹模 为整体 结构 。 凹模 中全部冲切 与 冲裁均采用 了植入镶 拼的结构 , 以利 调整 与维修 、 更
丰田一汽在津合资兴建冲压模具公司
丰 田汽车公 司与 中 国第一 汽车集 团在天津合 资成 立了一家生产大型 汽车零件 冲压模 具 的新 公司— — 丰 田一汽 ( 天津 ) 模具有 限公 司 ( } D) 主要 生产 在汽 TT , - 家模具公 司。 D将生 产在汽车制造 中不可或缺的高 , Ⅱ 质量 型汽车零件 的 冲压模 具 ,计 划在投产初期达 到年 产 3款车 型模具 的规模 ,今后达 到年产 6款不 同车型 模具 的生产能力和 规模 。
汽车零部件四大龙头瑞鹄模具
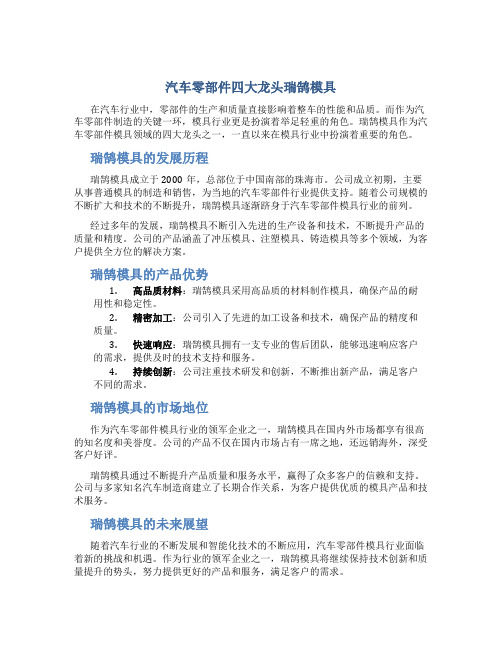
汽车零部件四大龙头瑞鹄模具在汽车行业中,零部件的生产和质量直接影响着整车的性能和品质。
而作为汽车零部件制造的关键一环,模具行业更是扮演着举足轻重的角色。
瑞鹄模具作为汽车零部件模具领域的四大龙头之一,一直以来在模具行业中扮演着重要的角色。
瑞鹄模具的发展历程瑞鹄模具成立于2000年,总部位于中国南部的珠海市。
公司成立初期,主要从事普通模具的制造和销售,为当地的汽车零部件行业提供支持。
随着公司规模的不断扩大和技术的不断提升,瑞鹄模具逐渐跻身于汽车零部件模具行业的前列。
经过多年的发展,瑞鹄模具不断引入先进的生产设备和技术,不断提升产品的质量和精度。
公司的产品涵盖了冲压模具、注塑模具、铸造模具等多个领域,为客户提供全方位的解决方案。
瑞鹄模具的产品优势1.高品质材料:瑞鹄模具采用高品质的材料制作模具,确保产品的耐用性和稳定性。
2.精密加工:公司引入了先进的加工设备和技术,确保产品的精度和质量。
3.快速响应:瑞鹄模具拥有一支专业的售后团队,能够迅速响应客户的需求,提供及时的技术支持和服务。
4.持续创新:公司注重技术研发和创新,不断推出新产品,满足客户不同的需求。
瑞鹄模具的市场地位作为汽车零部件模具行业的领军企业之一,瑞鹄模具在国内外市场都享有很高的知名度和美誉度。
公司的产品不仅在国内市场占有一席之地,还远销海外,深受客户好评。
瑞鹄模具通过不断提升产品质量和服务水平,赢得了众多客户的信赖和支持。
公司与多家知名汽车制造商建立了长期合作关系,为客户提供优质的模具产品和技术服务。
瑞鹄模具的未来展望随着汽车行业的不断发展和智能化技术的不断应用,汽车零部件模具行业面临着新的挑战和机遇。
作为行业的领军企业之一,瑞鹄模具将继续保持技术创新和质量提升的势头,努力提供更好的产品和服务,满足客户的需求。
在未来的发展中,瑞鹄模具将进一步加强与客户的合作,深入了解客户需求,为客户提供定制化的解决方案。
同时,公司还将加大对研发和创新的投入,不断推出适应市场需求的新产品,实现可持续发展。
中国模具行业发展现状及趋势

模具行业发展前景以及趋势2014-04-08 10:18:35责任编辑:肖梓談来源:前瞻产业研究院作者:肖时祥模具是工业生产的基础工艺装备,被称为"工业之母”。
据前瞻产业研究院发布的《中国模具制造行业产销需求预测与转型升级分析报告》显示:我国现在的模具有75%的粗加工工业产品零件、50%的精加工零件由模具成型,绝大部分塑料制品也由模具成型。
作为国民经济的基础行业,模具涉及机械、汽车、轻工、电子、化工、冶金、建材等各个行业,应用范囤十分广泛。
欧洲模具设计和生产的时间分别要比我国快44%利61%左右,但我国模具设计和生产的成本只冇欧洲地区的91%.目前,国际模具行业竞争激烈,近两年来徳国模具整体价格已下降i / 4左右,且全球58%的模山徳国等西欧国家生产,中国等亚洲国家仅占极小的比例。
但目前东欧地区的模具生产岀现较大幅度增长,亚洲地区的生产规模也将增加到1/5左右。
我国的模具行业也已步入了高速发展时期,但存在的问题仍然不少。
近10年来,我国模具行业一直以每年15%的增长速度快速发展。
十五期间,我国模具行业年增长速度达到20%。
2005年模具销售额达610亿元,同比增长25%,排在世界第三位; 模具出口大幅增长,表明模具水平和竞争力提高。
据海关统计,2005年模具出口7. 4亿美元,同比增长50%以上:模具产品结构更趋高档,复杂、精密、长寿命的模具份额提髙到30%。
目前,国内约有模具生产厂商3万余家,从业人员有80多万人,全年模具产值达534 亿元人民币。
涌现出一批模具行业领头羊,如在汽车覆盖件领域的一汽模具,轮胎领域的巨轮模具,塑料模具领域的海尔,模块标准件领域的圣都等;不少地方出台了扶持肖地模具行业发展的政策,如重庆、成都、苏州、大连等地都在建立模具工业园区,改善发展环境,完善模具生产的配套体系。
中国经济的高速发展对模具行业提岀了越来越髙的要求,也为其发展提供了巨大了的动力。
中国模具行业的发展在地域分布上存在不平衡性,东南沿海地区发展快于中西部地区。
FDM(熔融沉积制造)

精品课件
精品课件
精品课件
精品课件
精品课件
精品课件
精品课件
精品课件
精品课件
精品课件
精品课件
精品课件
精品课件
精品课件
精品课件
精品课件
精品课件
精品课件
精品课件
精品课件
精品课件
精品课件
精车品灯课件-1
车灯-2
精品课件
精车品课灯件-3
精车品灯课件-4
缺点
成型件的表面有较明显的条纹 。
沿成型轴垂直方向的强度比较弱。
需要设计与制作支撑结构。
需要对整个截面进行扫描涂覆,成型时间较长。
原材料价格昂贵。
精品课件
精品课件
精品课件
三、熔融沉积工艺成形过程影响因素分析 材料性能的影响 喷头温度和成形室温度的影响 挤出速度的影响 填充速度与挤出速度交互的影响 分层厚度的影响 成形时间的影响 扫描方式的影响
该模具在模具后部设计成中空区,以减少用钢量,中空区填入化学粘结 瓷。仅花5周时间和一半的原来成本,而且制作的模具至少可生产30000套衬板。
采用FDM工艺后,福特汽车公司大大缩短了运输部件衬板的制作周期, 并显著降低了制作成本。
精品课件
(5)FDM在韩国现代公司的应用
韩国现代汽车公司采用了美国Stratasys公司的FDM快速原型系统,用于 检验设计、空气动力评估和功能测试。FDM系统在启亚的Spectra车型设计上得到 了成功的应用,现代汽车公司自动技术部的首席工程师Tae Sun Byun说:空间的 精确和稳定对设计检验来说是至关重要的,采用ABS工程塑料的FDM Maxum系统满 足了两者的要求,在1382mm的长度上,其最大误差只有0.75mm。
- 1、下载文档前请自行甄别文档内容的完整性,平台不提供额外的编辑、内容补充、找答案等附加服务。
- 2、"仅部分预览"的文档,不可在线预览部分如存在完整性等问题,可反馈申请退款(可完整预览的文档不适用该条件!)。
- 3、如文档侵犯您的权益,请联系客服反馈,我们会尽快为您处理(人工客服工作时间:9:00-18:30)。
丰田的模具制造丰田汽车公司的模具设计与制造技术是世界一流水平,它的管理和技术有许多独到之处。
本文作者利用天津汽车模具有限公司与日本丰田公司技术合作的机会,于98年先后两次共一个半月的时间,在丰田公司进行培训、实际考察和较为深入的学习,掌握了大量第一手材料。
下面仅就丰田模具生产制造技术作初步的探讨。
这些内容对急待改进生产方式、推进科学管理和提高制造技术水平的国内汽车模具同行,可能会有一些借鉴和启发。
一、丰田模具设计与制造部门概况丰田汽车公司中与冲压模具设计制造有关的部门主要有两个,其中负责模具设计的是第八生产技术部,负责模具制造的是ST部(ST为冲模的英文缩写),它们都直属于总公司,生产技术1-8部属于生产准备部门,冲模部(ST部)属于工机制造部门。
1.第8生产技术部其主要职责是模具设计和冲压设备准备,加上它所属的其中与模具设计有关的技术室有三个,它们是由从事的产品件类型来划分的,如下表所示:部门职责人员一室车身周边件模具设计(车门、机盖、后行李厢盖)约70人二室主车身件模具设计(侧围、翼子板、顶盖等)约75人三室底板、梁架件模具设计(地板、发动机舱等)约30人每个室又分为冲压工艺与模具结构设计两个组。
专业化分工是丰田模具设计部门工作的特点。
a. 模具设计内容细分丰田把模具设计分成三个工序:工序设计、模面设计和结构设计,分工明确,分别由专门人员负责。
工序设计主要完成工序草图、DL图设计、作详细的模具设计任务书、模面构想等,模具设计的主要创造性劳动都在这一步靠人脑完成。
模面设计几乎是单纯的曲面造型,结构设计的重点在于模具结构的具体实现。
b. 人员专业化分工细微各个室只负责一类产品件,每个人在一定时间内负责同一个件,甚至是同一类模具。
由于丰田每年开发的新车可达十种,这就是说,可能有的人在一年内画十套非常相似的前车门外板拉延模,其专业化程度可想而知。
c. 模具的社会大分工日本的模具制造专业性分工很强,丰田虽然自己的模具制造能力很强,但它并不是什么模都干。
比如,整车所有件的冲压工艺和模具的整车协调,他自己都负责,但模具设计和制造他只干车身内外覆盖件,地板和梁架件全部到定点厂家外协。
不但丰田如此,国外的大汽车公司所属模具厂无不如此,比如日本大发公司模具厂,甚至只做侧围、翼子板、顶盖等有限的几种外覆盖件。
这可以看作是一种发展趋势,在韩国、台湾甚至是专业模具厂家也是向只做几种件的更专业方向发展。
2.模具制造部(ST部)丰田ST部负责模具制造和新车整车模具的协调,并一直到大批量生产之前的冲压生产准备。
ST部构成:科室责任人员技术室生产技术开发、生产计划、生产准备、设备计划89人NC课NC编程、检查175人实型课验具、实型制造142人机械课机械加工173人钳工课钳工、装配237人调试课试模、调试204人合计1020人主要数控加工设备:构造面加工数控铣床39台型面加工高速、五轴五面铣15台新型一体化加工设备6台其他小件加工设备31台总计92台从人员和生产能力上看,ST 部都算得上是世界上最大的汽车模具厂之一。
3.丰田的模具设计和制造能力模具设计与制造能力每年大约可开发10个轿车整车模具模具产量(标准套)约2000套/年,内制率60%(外协40%)主要产品中模具占80%,验具占7%,其他占13%全年完成模具制造成本预算近200亿日元人均模具产量2标准套/人.年模具制造成本(不含设计) 约600万日元/套工时成本(平均) 约1万日元/小时整车模具设计制造周期12个月(由车身设计完成至新车批量生产)其中包括整车全部模具设计周期5个月制造周期5个月调试周期6个月由此可见,丰田一年的轿车生产能力大约500万辆(日本国内部分约占50%),是中国大陆轿车产量的十倍,而模具设计制造能力也超过我们全国汽车模具生产能力的数倍。
丰田的标准单套模具制造周期为三至四个月。
4.丰田一般模具制造周期丰田把模具的制造计划标准化,根据模具的复杂程度可分为短周期、标准周期和长周期三种。
现以单套模具的设计制造周期(拉延模,标准周期)为例:冲压工艺20天------------------------模具设计20天-------------模面设计8天--------NC编程15天---------实型制作7天------铸造12天------机加工9天-----钳工装配7天---单套拉延模总周期62天其中制造周期52天以上周期包括模具的设计、制造直至模具初次试模完成为止。
如果再考虑产品件各序模具的总周期,单个制件各序模具的总周期,要在拉延模的基础上再加22天(包括模具调试,但不包括整车调试),总共84天。
以上天数均为工作日(节假日除外),换算为日历日大约为20天等于一个月,也就是单套模具制造周期三至四个月。
丰田的模具制造也是按照准时化生产方式进行的,全部倒排计划,计划到每一个工作日,不提前投产,避免增加在产模具。
我们的倒排计划往往是为赶工期,人为的压缩工期。
而丰田的倒排计划,是为了在必要的时候生产出必要的产品,避免提前投产造成生产过剩的浪费。
二、丰田模具制造技术丰田的模具技术在日本的模具厂家中也是十分突出的,无论是能力、效率及技术都不愧为世界一流水平。
通过对丰田的了解我们可以看到,世界汽车模具制造技术正在向这些方向发展:计算机前的操作逐步代替现场操作,以高精度加工代替人的手工劳动,模具的设计、制造高度标准化,单件生产方式向流水线式生产方式发展等等。
丰田在以下一些地方值得我们很好的借鉴。
1. 冲压工艺设计A. 精细模面设计我们常说的模具设计实际上分为三个部分:冲压工艺设计、模面设计和结构设计。
这三种设计的内容和侧重点是完全不同的,丰田的工作流程为先有冲压工艺设计然后指导模面设计和模具结构设计,分别由不同的人来做,专业分工很明确。
传统的冲压工艺设计采用工序图或是DL图,它的模面设计是非常粗略的,以这样的图纸指导下的工艺造型,必须在后序靠人工修整、制造工艺祢补,造成模具制造的人工钳修量很大、周期延长。
丰田在设计阶段通过计算机的曲面造型,完成模面的精细设计。
比如:针对进料量不同设计各种拉延筋,同一套模不同部位的拉延筋截面不同,防回弹、过拉延处理,最小压料面设计,凸凹模不等间隙设计等等。
精细模面设计的结果,可以极大的减少型面加工,减少钳修,减少试模工时,它的作用非同小可。
对比之下,国内的模具设计还停留在结构设计阶段,模面设计没有受到很好的重视,模面实际上是靠后天完成,模具设计的落后造成了制造的落后,也就毫不奇怪了。
B.板料成型分析技术应用情况丰田公司从5-6年前,开始应用有限元法做计算机模拟板料成型分析,主要应用的解算软件为美国的DYNA3D,他们经过了近三年的努力才达到实用水平。
目前,丰田建立了一个整车身各种典型件的分析结果库。
对一个新车型的件,如果成型性没有太大的变化,只是参考原工艺不做分析,只有特殊的新造型才做板料成型分析。
丰田的新车要做样车,对造型特殊的件除了做板料成型分析外一般还要做简易模进行验证。
因此,丰田人认为目前板料成型分析还不是一件必需的、简单的事,无论是周期还是成本都有很大代价。
本人认为,丰田的车型开发量很大,车型之间变化不大、类似件很多,又积累了丰富的人的经验,板料成型分析确实用武之地不多,建立一个分析结果库是一个好方法(日本富士模具公司也是这么做的)。
反观国内现状,一方面模具厂专业分工很低,各种件都会遇到,难有现成经验,似乎更需要板料成型技术。
另一方面,技术水平低支持环境差(如:板料参数、摩擦系数等难掌握),模具厂应用起来,要达到实用(不讲效果、不计代价的研究不算)也是非常困难的。
即使是成立专业分析公司,考虑用户数量、周期、价格等因素,恐怕也曲高和寡。
目前,这项技术在国内的实际应用效果还难有定论。
C. 模面设计经验积累机制丰田的设计部门除手工勾画草图以外,设计已全部计算机化,一般设计人员除一台工作站外还有一台笔记本电脑。
但真正创造性的设计还是靠人脑,特别是靠人的经验积累。
丰田特别强调经验积累机制:只有集体的经验不能有只属于个人的经验,比如:资料的统一管理,草图设计的小组讨论,图纸的多部门集体审核,设计标准、规范的经常性增改等等。
经验积累机制是丰田能够不断提高模面精细设计的主要手段。
比如:模具加工完成之后,一般模具型面不用研合,刃口不必对间隙,钳工只负责安装,在初次试模时也不能随便修调模具,调试模具有模面设计人员在场,初次试模缺陷需要记录下来。
最后的休整结果,象拉延筋、拉延圆角变动、对称件的不对称现象等,还要进行现场测量。
这些资料的积累、整理、分析、存档,都是模面设计的经验积累,并随时加入到下一次的设计中去。
丰田的模具设计和调试过程,真正做到了是一个闭环制造系统,借助于这种自我完善的经验积累机制,模具的设计越来越精细,越来越准确。
D.间隙图设计在丰田,模面设计实际上是由曲面造型和NC编程两部分共同完成的,为了传达和描述模面设计思想,就产生了除DL图、模具图之外的第三种图――间隙图,也叫质量保证图。
间隙图可能是丰田的一种创造。
模具设计不是单纯为了设计出一种能够完成一定动作的机器,设计的最终目的是为了保证它所压出的产品件是合格的,间隙图就是这样一种专为保证产品质量的图。
质量保证图中,主要包括这样几项内容:模具实际符型面区域、各个符型区域的间隙值、工艺要求的模面变化情况、拉延圆角的变化、各种模面的挖空等等。
凡是无法通过曲面造型实现的模面设计,都通过间隙图的传达,依靠NC编程的设计来实现,在这里NC编程也不再是单纯的实现模具结构的加工,它实际上也参与到模面设计中来了。
因此,间隙图的应用也是精细模面设计的一种必然。
E.大规模生产对模具的影响材料利用率:对于大批量汽车生产来说,提高板料的利用率是模具设计的大事。
如果一套模具40万人民币,相当于100吨钢板的价格,以寿命50万件计算,平均每件节约0.2kg 钢板,就足可节约出这套模具费用了。
冲压工序:模具设计时考虑零件合并,左右对称件合模,前后顺序件合模等等,使单件工序大大减少,整车模具数量越来越少,对降低冲压的成本起关键作用。
例如:丰田把整车制件的模具系数,由过去的3点几降到2左右。
冲压自动化:为适应冲压线完全自动化,模具必须考虑机械手上下料,废料的自动排出,气动、自动和传感装置普遍采用等等。
快速换模:冲压线的换模时间,也成为一个模具设计必须考虑的问题。
如:拉延模完全以单动代替双动,模具自动卡紧,换模不换气顶杆等等。
2.模具结构的设计和加工不同的生产工艺流程决定了图纸的表达形式。
传统的模具总装图加零件图的形式,适应的是非框架结构的模具生产。
采用大型数控铣加工以后,模具总成图成为更好的形式。
在全面应用CAD设计之后,如果生产方式没变,那么二维设计和总图设计也不会变,只是把图板换成了屏幕和键盘。