自动化专业毕业设计外文翻译
自动化专业毕业论文外文文献翻译

目录Part 1 PID type fuzzy controller and parameters adaptive method (1)Part 2 Application of self adaptation fuzzy-PID control for main steam temperature control system in power station (7)Part 3 Neuro-fuzzy generalized predictive control of boiler steam temperature ..................................................................... (13)Part 4 为Part3译文:锅炉蒸汽温度模糊神经网络的广义预测控制21Part 1 PID type fuzzy controller and Parametersadaptive methodWu zhi QIAO, Masaharu MizumotoAbstract: The authors of this paper try to analyze the dynamic behavior of the product-sum crisp type fuzzy controller, revealing that this type of fuzzy controller behaves approximately like a PD controller that may yield steady-state error for the control system. By relating to the conventional PID control theory, we propose a new fuzzy controller structure, namely PID type fuzzy controller which retains the characteristics similar to the conventional PID controller. In order to improve further the performance of the fuzzy controller, we work out a method to tune the parameters of the PID type fuzzy controller on line, producing a parameter adaptive fuzzy controller. Simulation experiments are made to demonstrate the fine performance of these novel fuzzy controller structures.Keywords: Fuzzy controller; PID control; Adaptive control1. IntroductionAmong various inference methods used in the fuzzy controller found in literatures , the most widely used ones in practice are the Mamdani method proposed by Mamdani and his associates who adopted the Min-max compositional rule of inference based on an interpretation of a control rule as a conjunction of the antecedent and consequent, and the product-sum method proposed by Mizumoto who suggested to introduce the product and arithmetic mean aggregation operators to replace the logical AND (minimum) and OR (maximum) calculations in the Min-max compositional rule of inference.In the algorithm of a fuzzy controller, the fuzzy function calculation is also a complicated and time consuming task. Tagagi and Sugeno proposed a crisp type model in which the consequent parts of the fuzzy control rules are crisp functional representation or crisp real numbers in the simplified case instead of fuzzy sets . With this model of crisp real number output, the fuzzy set of the inference consequence willbe a discrete fuzzy set with a finite number of points, this can greatly simplify the fuzzy function algorithm.Both the Min-max method and the product-sum method are often applied with the crisp output model in a mixed manner. Especially the mixed product-sum crisp model has a fine performance and the simplest algorithm that is very easy to be implemented in hardware system and converted into a fuzzy neural network model. In this paper, we will take account of the product-sum crisp type fuzzy controller.2. PID type fuzzy controller structureAs illustrated in previous sections, the PD function approximately behaves like a parameter time-varying PD controller. Since the mathematical models of most industrial process systems are of type, obviously there would exist an steady-state error if they are controlled by this kind of fuzzy controller. This characteristic has been stated in the brief review of the PID controller in the previous section.If we want to eliminate the steady-state error of the control system, we can imagine to substitute the input (the change rate of error or the derivative of error) of the fuzzy controller with the integration of error. This will result the fuzzy controller behaving like a parameter time-varying PI controller, thus the steady-state error is expelled by the integration action. However, a PI type fuzzy controller will have a slow rise time if the P parameters are chosen small, and have a large overshoot if the P or I parameters are chosen large. So there may be the time when one wants to introduce not only the integration control but the derivative control to the fuzzy control system, because the derivative control can reduce the overshoot of the system's response so as to improve the control performance. Of course this can be realized by designing a fuzzy controller with three inputs, error, the change rate of error and the integration of error. However, these methods will be hard to implement in practice because of the difficulty in constructing fuzzy control rules. Usually fuzzy control rules are constructed by summarizing the manual control experience of an operator who has been controlling the industrial process skillfully and successfully. The operator intuitively regulates the executor to control the process by watching theerror and the change rate of the error between the system's output and the set-point value. It is not the practice for the operator to observe the integration of error. Moreover, adding one input variable will greatly increase the number of control rules, the constructing of fuzzy control rules are even more difficult task and it needs more computation efforts. Hence we may want to design a fuzzy controller that possesses the fine characteristics of the PID controller by using only the error and the change rate of error as its inputs.One way is to have an integrator serially connected to the output of the fuzzy controller as shown in Fig. 1. In Fig. 1,1K and 2K are scaling factors for e and ~ respectively, and fl is the integral constant. In the proceeding text, for convenience, we did not consider the scaling factors. Here in Fig. 2, when we look at the neighborhood of NODE point in the e - ~ plane, it follows from (1) that the control input to the plant can be approximated by(1)Hence the fuzzy controller becomes a parameter time-varying PI controller, itsequivalent proportional control and integral control components are BK2D and ilK1 P respectively. We call this fuzzy controller as the PI type fuzzy controller (PI fc). We can hope that in a PI type fuzzy control system, the steady-state error becomes zero.To verify the property of the PI type fuzzy controller, we carry out some simulation experiments. Before presenting the simulation, we give a description of the simulation model. In the fuzzy control system shown in Fig. 3, the plant model is a second-order and type system with the following transfer function:)1)(1()(21++=s T s T K s G (2) Where K = 16, 1T = 1, and 2T = 0.5. In our simulation experiments, we use thediscrete simulation method, the results would be slightly different from that of a continuous system, the sampling time of the system is set to be 0.1 s. For the fuzzy controller, the fuzzy subsets of e and d are defined as shown in Fig. 4. Their coresThe fuzzy control rules are represented as Table 1. Fig. 5 demonstrates the simulation result of step response of the fuzzy control system with a Pl fc. We can see that the steady-state error of the control system becomes zero, but when the integration factor fl is small, the system's response is slow, and when it is too large, there is a high overshoot and serious oscillation. Therefore, we may want to introduce the derivative control law into the fuzzy controller to overcome the overshoot and instability. We propose a controller structure that simply connects the PD type and the PI type fuzzy controller together in parallel. We have the equivalent structure of that by connecting a PI device with the basic fuzzy controller serially as shown in Fig.6. Where ~ is the weight on PD type fuzzy controller and fi is that on PI type fuzzy controller, the larger a/fi means more emphasis on the derivative control and less emphasis on the integration control, and vice versa. It follows from (7) that the output of the fuzzy controller is(3)3. The parameter adaptive methodThus the fuzzy controller behaves like a time-varying PID controller, its equivalent proportional control, integral control and derivative control components are respectively. We call this new controller structure a PID type fuzzy controller (PID fc). Figs. 7 and 8 are the simulation results of the system's step response of such control system. The influence of ~ and fl to the system performance is illustrated. When ~ > 0 and/3 = 0, meaning that the fuzzy controller behaves like PD fc, there exist a steady-state error. When ~ = 0 and fl > 0, meaning that the fuzzy controller behaves like a PI fc, the steady-state error of the system is eliminated but there is a large overshoot and serious oscillation.When ~ > 0 and 13 > 0 the fuzzy controller becomes a PID fc, the overshoot is substantially reduced. It is possible to get a comparatively good performance by carefully choosing the value of αandβ.4. ConclusionsWe have studied the input-output behavior of the product-sum crisp type fuzzy controller, revealing that this type of fuzzy controller behaves approximately like a parameter time-varying PD controller. Therefore, the analysis and designing of a fuzzy control system can take advantage of the conventional PID control theory. According to the coventional PID control theory, we have been able to propose some improvement methods for the crisp type fuzzy controller.It has been illustrated that the PD type fuzzy controller yields a steady-state error for the type system, the PI type fuzzy controller can eliminate the steady-state error. We proposed a controller structure, that combines the features of both PD type and PI type fuzzy controller, obtaining a PID type fuzzy controller which allows the control system to have a fast rise and a small overshoot as well as a short settling time.To improve further the performance of the proposed PID type fuzzy controller, the authors designed a parameter adaptive fuzzy controller. The PID type fuzzy controller can be decomposed into the equivalent proportional control, integral control and the derivative control components. The proposed parameter adaptive fuzzy controller decreases the equivalent integral control component of the fuzzy controller gradually with the system response process time, so as to increase the damping of the system when the system is about to settle down, meanwhile keeps the proportional control component unchanged so as to guarantee quick reaction against the system's error. With the parameter adaptive fuzzy controller, the oscillation of the system is strongly restrained and the settling time is shortened considerably.We have presented the simulation results to demonstrate the fine performance of the proposed PID type fuzzy controller and the parameter adaptive fuzzy controller structure.Part 2 Application of self adaptation fuzzy-PID control for main steam temperature control system inpower stationZHI-BIN LIAbstract: In light of the large delay, strong inertia, and uncertainty characteristics of main steam temperature process, a self adaptation fuzzy-PID serial control system is presented, which not only contains the anti-disturbance performance of serial control, but also combines the good dynamic performance of fuzzy control. The simulation results show that this control system has more quickly response, better precision and stronger anti-disturbance ability.Keywords:Main steam temperature;Self adaptation;Fuzzy control;Serial control1. IntroductionThe boiler superheaters of modem thermal power station run under the condition of high temperature and high pressure, and the superheater’s temperature is highest in the steam channels.so it has important effect to the running of the whole thermal power station.If the temperature is too high, it will be probably burnt out. If the temperature is too low ,the efficiency will be reduced So the main steam temperature mast be strictly controlled near the given value.Fig l shows the boiler main steam temperature system structure.Fig.1 boiler main steam temperature systemIt can be concluded from Fig l that a good main steam temperature controlsystem not only has adequately quickly response to flue disturbance and load fluctuation, but also has strong control ability to desuperheating water disturbance. The general control scheme is serial PID control or double loop control system with derivative. But when the work condition and external disturbance change large, the performance will become instable. This paper presents a self adaptation fuzzy-PID serial control system. which not only contains the anti-disturbance performance of serial control, but also combines the good dynamic character and quickly response of fuzzy control .1. Design of Control SystemThe general regulation adopts serial PID control system with load feed forward .which assures that the main steam temperature is near the given value 540℃in most condition .If parameter of PID control changeless and the work condition and external disturbance change large, the performance will become in stable .The fuzzy control is fit for controlling non-linear and uncertain process. The general fuzzy controller takes error E and error change ratio EC as input variables .actually it is a non-linear PD controller, so it has the good dynamic performance .But the steady error is still in existence. In linear system theory, integral can eliminate the steady error. So if fuzzy control is combined with PI control, not only contains the anti-disturbance performance of serial control, but also has the good dynamic performance and quickly response.In order to improve fuzzy control self adaptation ability, Prof .Long Sheng-Zhao and Wang Pei-zhuang take the located in bringing forward a new idea which can modify the control regulation online .This regulation is:]1,0[,)1(∈-+=αααEC E UThis control regulation depends on only one parameter α.Once αis fixed .the weight of E and EC will be fixed and the self adaptation ability will be very small .It was improved by Prof. Li Dong-hui and the new regulation is as follow;]1,0[,,,3,)1(2,)1(1,)1(0,)1({321033221100∈±=-+±=-+±=-+=-+=ααααααααααααE EC E E EC E E EC E E EC E UBecause it is very difficult to find a self of optimum parameter, a new method is presented by Prof .Zhou Xian-Lan, the regulation is as follow:)0(),ex p(12>--=k ke αBut this algorithm still can not eliminate the steady error .This paper combines this algorithm with PI control ,the performance is improved .2. Simulation of Control System3.1 Dynamic character of controlled objectPapers should be limited to 6 pages Papers longer than 6 pages will be subject to extra fees based on their length .Fig .2 main steam temperature control system structureFig 2 shows the main steam temperature control system structure ,)(),(21s W s W δδare main controller and auxiliary controller,)(),(21s W s W o o are characters of the leading and inertia sections,)(),(21s W s W H H are measure unit.3.2 Simulation of the general serial PID control systemThe simulation of the general serial PID control system is operated by MATLAB, the simulation modal is as Fig.3.Setp1 and Setp2 are the given value disturbance and superheating water disturb & rice .PID Controller1 and PID Controller2 are main controller and auxiliary controller .The parameter value which comes from references is as follow :667.37,074.0,33.31)(25)(111111122===++===D I p D I p p k k k s k sk k s W k s W δδFig.3. the general PID control system simulation modal3.3 Simulation of self adaptation fuzzy-PID control system SpacingThe simulation modal is as Fig 4.Auxiliary controller is:25)(22==p k s W δ.Main controller is Fuzzy-PI structure, and the PI controller is:074.0,33.31)(11111==+=I p I p k k s k k s W δFuzzy controller is realized by S-function, and the code is as fig.5.Fig.4. the fuzzy PID control system simulation modalFig 5 the S-function code of fuzzy control3.4 Comparison of the simulationGiven the same given value disturbance and the superheating water disturbance,we compare the response of fuzzy-PID control system with PID serial control system. The simulation results are as fig.6-7.From Fig6-7,we can conclude that the self adaptation fuzzy-PID control system has the more quickly response, smaller excess and stronger anti-disturbance.4. Conclusion(1)Because it combines the advantage of PID controller and fuzzy controller, theself adaptation fuzzy-PID control system has better performance than the general PID serial control system.(2)The parameter can self adjust according to the error E value. so this kind of controller can harmonize quickly response with system stability.Part 3 Neuro-fuzzy generalized predictive controlof boiler steam temperatureXiangjie LIU, Jizhen LIU, Ping GUANAbstract: Power plants are nonlinear and uncertain complex systems. Reliable control of superheated steam temperature is necessary to ensure high efficiency and high load-following capability in the operation of modern power plant. A nonlinear generalized predictive controller based on neuro-fuzzy network (NFGPC) is proposed in this paper. The proposed nonlinear controller is applied to control the superheated steam temperature of a 200MW power plant. From the experiments on the plant and the simulation of the plant, much better performance than the traditional controller is obtained.Keywords: Neuro-fuzzy networks; Generalized predictive control; Superheated steam temperature1. IntroductionContinuous process in power plant and power station are complex systems characterized by nonlinearity, uncertainty and load disturbance. The superheater is an important part of the steam generation process in the boiler-turbine system, where steam is superheated before entering the turbine that drives the generator. Controlling superheated steam temperature is not only technically challenging, but also economically important.From Fig.1,the steam generated from the boiler drum passes through the low-temperature superheater before it enters the radiant-type platen superheater. Water is sprayed onto the steam to control the superheated steam temperature in both the low and high temperature superheaters. Proper control of the superheated steam temperature is extremely important to ensure the overall efficiency and safety of the power plant. It is undesirable that the steam temperature is too high, as it can damage the superheater and the high pressure turbine, or too low, as it will lower the efficiency of the power plant. It is also important to reduce the temperaturefluctuations inside the superheater, as it helps to minimize mechanical stress that causes micro-cracks in the unit, in order to prolong the life of the unit and to reduce maintenance costs. As the GPC is derived by minimizing these fluctuations, it is amongst the controllers that are most suitable for achieving this goal.The multivariable multi-step adaptive regulator has been applied to control the superheated steam temperature in a 150 t/h boiler, and generalized predictive control was proposed to control the steam temperature. A nonlinear long-range predictive controller based on neural networks is developed into control the main steam temperature and pressure, and the reheated steam temperature at several operating levels. The control of the main steam pressure and temperature based on a nonlinear model that consists of nonlinear static constants and linear dynamics is presented in that.Fig.1 The boiler and superheater steam generation process Fuzzy logic is capable of incorporating human experiences via the fuzzy rules. Nevertheless, the design of fuzzy logic controllers is somehow time consuming, as the fuzzy rules are often obtained by trials and errors. In contrast, neural networks not only have the ability to approximate non-linear functions with arbitrary accuracy, they can also be trained from experimental data. The neuro-fuzzy networks developed recently have the advantages of model transparency of fuzzy logic and learning capability of neural networks. The NFN is have been used to develop self-tuning control, and is therefore a useful tool for developing nonlinear predictive control. Since NFN is can be considered as a network that consists of several local re-gions, each of which contains a local linear model, nonlinear predictive control based onNFN can be devised with the network incorporating all the local generalized predictive controllers (GPC) designed using the respective local linear models. Following this approach, the nonlinear generalized predictive controllers based on the NFN, or simply, the neuro-fuzzy generalized predictive controllers (NFG-PCs)are derived here. The proposed controller is then applied to control the superheated steam temperature of the 200MW power unit. Experimental data obtained from the plant are used to train the NFN model, and from which local GPC that form part of the NFGPC is then designed. The proposed controller is tested first on the simulation of the process, before applying it to control the power plant.2. Neuro-fuzzy network modellingConsider the following general single-input single-output nonlinear dynamic system:),1(),...,(),(),...,1([)(''+-----=uy n d t u d t u n t y t y f t y ∆+--/)()](),...,1('t e n t e t e e (1)where f[.]is a smooth nonlinear function such that a Taylor series expansion exists, e(t)is a zero mean white noise and Δis the differencing operator,''',,e u y n n n and d are respectively the known orders and time delay of the system. Let the local linear model of the nonlinear system (1) at the operating point )(t o be given by the following Controlled Auto-Regressive Integrated Moving Average (CARIMA) model:)()()()()()(111t e z C t u z B z t y z A d ----+∆= (2) Where )()(),()(1111----∆=z andC z B z A z A are polynomials in 1-z , the backward shift operator. Note that the coefficients of these polynomials are a function of the operating point )(t o .The nonlinear system (1) is partitioned into several operating regions, such that each region can be approximated by a local linear model. Since NFN is a class of associative memory networks with knowledge stored locally, they can be applied to model this class of nonlinear systems. A schematic diagram of the NFN is shown in Fig.2.B-spline functions are used as the membership functions in theNFN for the following reasons. First, B-spline functions can be readily specified by the order of the basis function and the number of inner knots. Second, they are defined on a bounded support, and the output of the basis function is always positive, i.e.,],[,0)(j k j j k x x λλμ-∉=and ],[,0)(j k j j k x x λλμ-∈>.Third, the basis functions form a partition of unity, i.e.,.][,1)(min,∑∈≡j mam j k x x x x μ(3)And fourth, the output of the basis functions can be obtained by a recurrence equation.Fig. 2 neuro-fuzzy network The membership functions of the fuzzy variables derived from the fuzzy rules can be obtained by the tensor product of the univariate basis functions. As an example, consider the NFN shown in Fig.2, which consists of the following fuzzy rules: IF operating condition i (1x is positive small, ... , and n x is negative large),THEN the output is given by the local CARIMA model i:...)()(ˆ...)1(ˆ)(ˆ01+-∆+-++-=d t u b n t y a t y a t yi i a i in i i i a )(...)()(c i in i b i in n t e c t e n d t u b c b -+++--∆+ (4)or )()()()()(ˆ)(111t e z C t u z B z t yz A i i i i d i i ----+∆= (5) Where )()(),(111---z andC z B z A i i i are polynomials in the backward shift operator 1-z , and d is the dead time of the plant,)(t u i is the control, and )(t e i is a zero mean independent random variable with a variance of 2δ. The multivariate basis function )(k i x a is obtained by the tensor products of the univariate basis functions,p i x A a nk k i k i ,...,2,1,)(1==∏=μ (6)where n is the dimension of the input vector x , and p , the total number of weights in the NFN, is given by,∏=+=nk i i k R p 1)( (7)Where i k and i R are the order of the basis function and the number of inner knots respectively. The properties of the univariate B-spline basis functions described previously also apply to the multivariate basis function, which is defined on the hyper-rectangles. The output of the NFN is,∑∑∑=====p i i i p i ip i i i a y aa yy 111ˆˆˆ (8) 3. Neuro-fuzzy modelling and predictive control of superheatedsteam temperatureLet θbe the superheated steam temperature, and θμ, the flow of spray water to the high temperature superheater. The response of θcan be approximated by a second order model:The linear models, however, only a local model for the selected operating point. Since load is the unique antecedent variable, it is used to select the division between the local regions in the NFN. Based on this approach, the load is divided into five regions as shown in Fig.3,using also the experience of the operators, who regard a load of 200MW as high,180MW as medium high,160MW as medium,140MW as medium low and 120MW as low. For a sampling interval of 30s , the estimated linear local models )(1-z A used in the NFN are shown in Table 1.Fig. 3 Membership function for local modelsTable 1 Local CARIMA models in neuro-fuzzy modelCascade control scheme is widely used to control the superheated steam temperature. Feed forward control, with the steam flow and the gas temperature as inputs, can be applied to provide a faster response to large variations in these two variables. In practice, the feed forward paths are activated only when there are significant changes in these variables. The control scheme also prevents the faster dynamics of the plant, i.e., the spray water valve and the water/steam mixing, from affecting the slower dynamics of the plant, i.e., the high temperature superheater. With the global nonlinear NFN model in Table 1, the proposed NFGPC scheme is shown in Fig.4.Fig. 4 NFGPC control of superheated steam temperature with feed-for-ward control.As a further illustration, the power plant is simulated using the NFN model given in Table 1,and is controlled respectively by the NFGPC, the conventional linear GPC controller, and the cascaded PI controller while the load changes from 160MW to 200MW.The conventional linear GPC controller is the local controller designed for the“medium”operating region. The results are shown in Fig.5,showing that, as expected, the best performance is obtained from the NFGPC as it is designed based on a more accurate process model. This is followed by the conventional linear GPC controller. The performance of the conventional cascade PI controller is the worst, indicating that it is unable to control satisfactory the superheated steam temperature under large load changes. This may be the reason for controlling the power plant manually when there are large load changes.Fig.5 comparison of the NFGPC, conventional linear GPC, and cascade PI controller.4. ConclusionsThe modeling and control of a 200 MW power plant using the neuro-fuzzy approach is presented in this paper. The NFN consists of five local CARIMA models.The out-put of the network is the interpolation of the local models using memberships given by the B-spline basis functions. The proposed NFGPC is similarly constructed, which is designed from the CARIMA models in the NFN. The NFGPC is most suitable for processes with smooth nonlinearity, such that its full operating range can be partitioned into several local linear operating regions. The proposed NFGPC therefore provides a useful alternative for controlling this class of nonlinear power plants, which are formerly difficult to be controlled using traditional methods.Part 4 为Part3译文:锅炉蒸汽温度模糊神经网络的广义预测控制Xiangjie LIU, Jizhen LIU, Ping GUAN摘要:发电厂是非线性和不确定性的复杂系统。
机械自动化类毕业设计外文翻译--电子设计自动化

附录B 翻译原文Electronic design automation Keyword EDA; IC;VHDL language; FPGAPROCESS DESCRIPTIONThree obstacles in particular bedevil ic designers in this dawn of the system on a chip. The first is actually a shortfall-the hardware and software components of the design lack a unifying language. Then, as the number of logic gates per chip passes the million marks, verification of a design's correctness is fast becoming more arduous than doing the design itself. And finally, not only gate counts but chip frequencies also are climbing, so that getting a design to meet its timing requirements without too many design iterations is a receding goal.As is the wont of the electronic design automation (EDA) community, these concerns are being attacked by start-up companies led by a few individuals with big ideas and a little seed money. PARLEZ-VOUS SUPERLOG?A system on a chip comprises both circuitry and the software that runs on it. Such a device may contain an embedded processor core running a software modem. Most often, after the chip'sfunctionality is spelled out, usually on paper, the hardware com- potent is handed off to the circuit designers and the software is given to the pro- grammars, to meet up again at some later date.The part of the chips functionality that will end up as logic gates and transistors is writ- ten in a hardware design language-Virology or VHDL, while the part that will end up as software is most often described in the programming language C or C++. The use of these disparate languages hampers the ability to describe, model, and debug the circuitry of the IC and the software in a coherent fashion.It is time, many in the industry believe, for a new design language that can cope with both hardware and software from the initial design specification right through to final verification. Just such a new language has been developed by Co-Design Automation Inc., San Jose, Calif.Before launching such an ambitious enterprise, cofounders Simon Davidmann, who is also chief operating officer, and Peter Flake ruled out the usefulness of extending an existing language to meet system-on-chip needs. Among the candidates for extension were C, C++, Java, and Verilog.A design language should satisfy three requirements, maintained Davidmann. It should unify the design process. It should make designing more efficient. And it should evolve out of an existing methodology. None of the existing approaches filled the bill. So Davidmann and Flake set about developing new co-design language called Superlog.A natural starting point was a blend of Virology and C since "from an algorithm point of view, a lot of Virology is built on C," explained Davidmann. Then they spiced the blend with bits and pieces of VHDL and Java. From Virology and VHDL, Superlog has acquired the ability to describe hardware aspects of the design, such as sequential, combinatorial, and multivalued logic. From C and Java it inherits dynamic processes and other software constructs. Even functions like interfaces, protocols, and state machines, which till now have often been done on paper, can be described in the new language. To support legacy code written in a hardware description or programming language, Superlog allows both Virology and C modules to be imported and used directly.It is important for the language to be in the public domain, according to Davidmann. The company has already begun to work with various standards organizations to this end.Not to be overlooked is the need for a suite of design tools based on the language. Recently Co-Design identified a number of electronic design automation companies, among them Magma Design Automation, Sente, and Viewlogic, that will develop tools based on Superlog. Co-Design will also develop products for the front end of the design process.ARACE TO THE FINISHNot everyone is convinced that a new language is needed. SystemC, a modeling platform that extends the capabilities andadvantages of C/C++ into the hardware domain has been proposed as an alternative. Such large and powerful companies as Synopsys, Coware, Lucent Technologies, and Texas Instruments have banded together under the Open SystemC Initiative to promote their version of the next-generation design platform. To get SystemC off to a running start, the group offers a modeling platform for download off their Web site free of charge. Their hope is also to make their platform the de facto standard.The rationale for developing SystemC was straightforward, according to Joachim Kunkel, general manager and vice president of the System Level Design Business Unit at Synopsys. It was to have a standard language in which semiconductor vendors, IP vendors, and system houses could exchange system-level IP and executable specifications, and the electronic design automation industry could develop interoperable tools.Supporters of SystemC believe that the would-be standard has to be based on C++ because it allows capabilities to be added to it without leaving the language standard, Kunkel told JEEE Spectrum. Most software developers use C++ and many systems developers use C++ already to describe their systems at a behavioral level. But till now it has not been possible to describe hardware using the language.The developers of SystemC have solved that problem by defining new C++ class libraries and a simulation kcrne1 that bring to C++ all of the capabilities needed to describe hardware. "These new classes implement new functionality," explained Kunkel. "Forexample, bit vectors-strings of zeros and ones-and all the operations that you would do on them." The SystemC developers also provided a class of signed and unsigned numbers, the notion of a signal, and other concepts needed to model hardware.There are still some holes, however. For example, it is still not possible to synthesize a gate-level netlist from a SystcmC description. Rut synthesis tools for SysteniC would he a natural result of broad acceptance of the language within the user community, according to Kunkel.It remains to be seen whether SystemC or Superlog wins out in the end. Least desirable would be an outcome like the impasse between Virology and VHDL, in which both prevailed, forcing electronic design automation vendors to support both platforms in a wasteful duplication of effort.THE VERIFICATION NIGHTMAREIf today's complex ICs are tough to design, they are very much tougher to verify. A variety of tools are available, each with its pros and cons. Emulation translates a design into field-programmable gate arrays (FPGAs). Presumably, if the array works as planned, the final chip will also. The emulation platform also enables designers to try 0111 the software that will run on the ASIC.The approach, though, is slow. Typical emulation systems run at a few megahertz. "At roughly one million cycles per second, designers arc not getting cnough performance out of their emulation systems toverify or understand some of the things that are going on with video generation or high bandwidth communications," said John Gallagher, director of marketing for Synplicity Inc., Sunnyvale, Calif. They must process a large number of operations to ensure their functionality is correct, he added.The reason that emulation systems are so slow, according to Gallagher, is that they route the design through many FPGAs and many boards. Simplicity solution is to use a few high-end FPGAs having over one million gates running at 100 MHz. Typically, a million FPGA gates translates into 200 000 ASIC gates. Putting nine such chips on a board in a three-by-three array allows designers to represent up to 1.8million ASlC gates. And routing delays are greatly curtailed because each chip is no more than two hops away from any other chip in the array.The company% product, called Certify, is not intended to compete with reconfigurable emulation systems, which are very effective at debugging designs during the internal design process, explained Gallagher. Rather, it is a true prototype of the system, running at speeds that may approach the real thing.Certify handles three fundamental operations, said Gallagher. The first is partitioning, or breakings up the ASIC register transfer level (RTL) code into different FPGAs. It does synthesis, turning the RTL code into ASIC gates equivalent to the final ASIC gates. Then it does timing analysis. "We haven't just linked togeth er the different tools,” he explained. 'We have taka our synthesis algorithms, between thepartitioning capabilities, and laid the timing analysis across that."In addition to emulation, two complementary approaches to design verification are simulation and model checking, a type of formal verification. Simulation applies vectors to a software model of a design and checks to sec if the output has the correct value. The approach is straightforward, but is becoming increasingly tortuous as designs become more complicated and the number of possible test vectors mushrooms. So recently, electronic design automation companies have been turning to model checking to prove that designs are correctly done.The sticking point with model checking is its great difficulty of use. "It is not for most engineers," said Simon Napper, chief operating officer OF Innol-ogic Systems Inc., San Jose, Calif. "The usage model is very difficult-it checks properties. But the designer isn't familiar with what P property is-he is used to simulation and static timing."As a remedy, InnoLogic developed a symbolic simulation tool, which blends simulation and formal verification. It is a Virology simulator except instead of sending Is and Os through the logic, the too1 propagates symbol or symbols plus binary values.The user gains improved functional coverage dong with much faster verification.To illustrate, to completely verify a fourbit adder would require 256 binary vectors-and take 256 simulation cycles. With symbols, it takes just one cycle.Just as with formal verification, there are limits to the complexity ofthe circuits that symbolic simulation can completely verily. Both have trouble with multipliers, for example. "A model checker will grind and grind and never produce a result," explained Napper. "But in our tool we take some symbol inputs and switch them to binary values, that reduces the job from a 32- to a 16-bit multiplier. And we report to the user that we were able to verify the upper the operands."InnoLogic has announced two Versifies of symbolic simulation. ESI'-XV verifies designs written in Virology. EXP-CV is meant for custom designs and memory blocks.THE TIME IS RIGHTThough the design of ICs with semiconductor geometries below 0.25 pm face challenges throughout development, some of the biggest hurdles occur during physical design, when the gates are placed on the chip and the interconnects are routed between them Problems occur here for a number of reasons. First, the capacitance, resistance, and inductance of the interconnects cannot be ignored, as they were in older, larger technologies. Crosstalk between interconnects; now closer together, must also be controlled. Several iterations through synthesis and placement may be necessary to achieve the required timing, if it can be accomplished at all.The solution proposed by Monterey Design Systems Inc., Sunnyvale, Calif., is called global design technology. This proprietary computing approach simultaneously explores, analyzes, and optimizes all aspects of the physical design. The tint productcontaining the technology is Dolphin, which was announced in April of last year. Dolphin simultaneously places and router each gate and flip-flop using the results or the analysis and maintaining all specified constraints. (Most place- and-route tools sequentially analyze the layout for each type of constraint.) It performs timing and logic optimization for every placement move.Timing closure is top priority for developers of the Blast Fusion physical design system from Magma Design Automations., Cupertino, Calif. Its methodology, called FixedTiming, brings timing within specified limits without iterating between synthesis and physical design .Basically, he approach fixes timing first, then adjusts cell sizes to achieve the timing requirements. Varying the cell sizes always he tool to supply the right drive strength or the load.EDA ON THE WEBAs established electronic design automation companies try to sort out how to utilize the internet in their product Inks, smaller, more agile companies and start-ups arc coining up with innovative products and services, mainly in the areas or design management. A pioneer in this area is Synchronicity Inc., a virtual company headquartered in Marlboro, Mass. Synchronicity is now being joined by other companies seeking to use the internet to advantage.The concern of , Milpitas, Calif a provider of Web-based engineering tools 'for; design automation, is the extraction of useful information about ICs, chip sets, and boards from suppliers'Web sites.The issue, according to Michael Bitzko, president of the company, is that designers of products based on there components need to be able to obtain information about them quickly and route it to their engineering, manufacturing, and procurement departments as quickly as possible. "In a nutshell,” said Bitzko, "people used to take weeks to get data sheets. Then along cane the Web and PDF-formatted documents. But in order to create, ray, schematic symbols and footprints fur printed circuit boards, information from PDF documents must often be reentered-a costly and time-consuming process when time to infarct is a concern.'s products are based on the electronic component interchange (ECIX) standard developed by EDA standards organization SI, Austin, Texas, and on the Extensible Markup Language (XML), that allows the creation or Web-bask documents having (more functionality than with the conventional Hypertext Markup Language (H TM1.). The company’s products include QuickData Server, a parametric search engine for electronic component information, and Quickdata Miner, which transform information contained in PDF data sheets into a usable form.The mission or Genedax Inc., Portland, Ore. is to use the Web to increase designed ability to create and manage large, complex designs, to iron design ICLISC, and to improve access to intellectual property. The company plans to announce a product in the first quarter or the year. John Ott, vice president of sales and marketing,told Sprctmni that its products will be based on the operating systems and browsers developed by Microsott Corp., Redmond, Wash. Also, the company supports a collaborative Web site, that shows what the technology can do. The site includes a search engine based on AltaVista technology that searches the Web sites of companies related to design auto illation. Ott elaborated, "We also have a free Internet locator server that lets people use Netmeeting a Microsoft product for remote sharing of computer desktops] and a Web board where you can post questions and get answers."Other aspects of electronic design on the Webs have been slower in taking off than design and information management. But Transim Corp also bared in Portland, Ore, has taken a big step toward Web-based design tools. Its product, Websim, is an interface between a Web browser and Simples, the company’s power-supply simulator. Websim allows designers, using Simplis, to simulate designs over the Internet. So rather than poring over data sheets and looking at ranges of values, designers can see actual waveforms, explained Ncls Gahbert, Transim president and chief executive officer.Transim is working with suppliers to set up component models so that designers can log on to the supplies Web rite, select parts for their power supply, enter setup or test conditions, and run the simulation on line. Users need nothing more than a Web browser. The simulation is run on Transim's "ranch" of six strivers from Sun Microsystems.The company has teamed up with National Semiconductor Corp, Santa Clara, Calif., to provide this service for National's customers. The cost is on a per-use basis and is a minimal US $10.附录C 翻译中文电子设计自动化关键字电子设计自动化;集成电路;VHDL语言;现场可编程门阵列在这个片上系统开始出现的时候,有三个问题一直困扰着集成电路设计者。
机械设计制造及其自动化毕业设计外文翻译

英文原文名Automatic production line PLC control中文译文:自动化生产线自动上料站的PLC控制自动生产线是由工件传送系统和控制系统,将一组自动机床和辅助设备按照工艺顺序联结起来,自动完成产品全部或部分制造过程的生产系统,简称自动线。
二十世纪20年代,随着汽车、滚动轴承、小电机和缝纫机和其他工业发展,机械制造业开始出现在自动生产线,第一个是组合机床自动线。
在20世纪20年代,第一次出现在汽车工业流水生产线和半自动生产线,然后发展成自动生产线。
第二次世界大战后,在机械制造工业发达国家,自动生产线的数量急剧增加。
采用自动生产线生产的产品应该足够大,产品设计和技术应该是先进的、稳定的和可靠的,基本上保持了很长一段时间维持不变。
自动线用于大,大规模生产可以提高劳动生产率,稳定和提高产品质量,改善劳动条件,降低生产区域,降低生产成本,缩短生产周期,保证生产平衡、显著的经济效益。
自动生产线的一个干预指定的程序或命令自动操作或控制的过程,我们的目标是稳定、准确、快速。
自动化技术广泛用于工业、农业、军事、科学研究、交通运输、商业、医疗、服务和家庭,等自动化生产线不仅可以使人们从繁重的体力劳动、部分脑力劳动以及恶劣、危险的工作环境,能扩大人的器官功能,极大地提高劳动生产率,提高人们认识世界的能力,可以改变世界。
下面我说下它的应用范围:机械制造业中有铸造、锻造、冲压、热处理、焊接、切削加工和机械装配等自动线,也有包括不同性质的工序,如毛坯制造、加工、装配、检验和包装等的综合自动线。
加工自动线发展最快,应用最广泛的机械制造。
主要包括:用于处理盒、外壳、各种各样的部件,如组合机床自动线;用于加工轴、盘部分,由通用、专业化、或自动机器自动专线;转子加工自动线;转子自动线加工过程简单、小零件等。
1.确保节拍时间:无论什么样的产品,都必须完成的时间生产。
2.单元过程:只有一个产品,单位部分处理、组装、加工和材料。
自动化专业毕业设计方案中英文翻译

中英文翻译Classification of control systems there are three ways: by automatic classification methods in order to participate in the control mode classification, to adjust the law category.One way to control category 1, the open-loop control system if the computer output of open loop control system to exercise control of the production process, but the control results --- the state of the production process does not affect the computer control systems, computer \ controller \ production and other sectors does not constitute a closed loop, is called open-loop control system computer. the production process of the state is no feedback to the computer, but by the operator to monitor the status of the production process, decision control program, and tell the computer to control the role of exercising control. 2, closed loop control system computer to the production of an object or process control, the state can directly influence the production process computer control system, called the closed-loop control system computer. Control of the computer monitor in the operator, the automatic acceptance of the production process state test results, calculate and determine the control scheme, the direct command and control units (devices> of action, the role of exercising control of the production process. In such systems, aircraft control components under control of control information sent to control device operation, the other running equipment condition as the output, measured by the detection part, the feedback as input to the control computer。
自动化毕业设计英文翻译
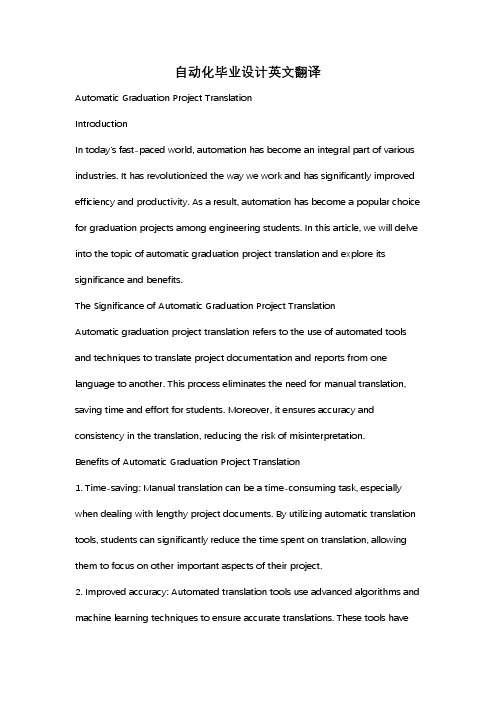
自动化毕业设计英文翻译Automatic Graduation Project TranslationIntroductionIn today's fast-paced world, automation has become an integral part of various industries. It has revolutionized the way we work and has significantly improved efficiency and productivity. As a result, automation has become a popular choice for graduation projects among engineering students. In this article, we will delve into the topic of automatic graduation project translation and explore its significance and benefits.The Significance of Automatic Graduation Project TranslationAutomatic graduation project translation refers to the use of automated tools and techniques to translate project documentation and reports from one language to another. This process eliminates the need for manual translation, saving time and effort for students. Moreover, it ensures accuracy and consistency in the translation, reducing the risk of misinterpretation.Benefits of Automatic Graduation Project Translation1. Time-saving: Manual translation can be a time-consuming task, especially when dealing with lengthy project documents. By utilizing automatic translation tools, students can significantly reduce the time spent on translation, allowing them to focus on other important aspects of their project.2. Improved accuracy: Automated translation tools use advanced algorithms and machine learning techniques to ensure accurate translations. These tools havethe ability to learn from previous translations and improve their accuracy over time. This reduces the chances of errors and ensures the quality of the translated content.3. Cost-effective: Hiring professional translators can be expensive, especially for students on a limited budget. Automatic translation tools provide a cost-effective solution, as they are often available for free or at a minimal cost. This allows students to allocate their resources efficiently and invest in other project requirements.4. Enhanced collaboration: Automatic translation tools facilitate seamless collaboration among team members who may speak different languages. By translating project documentation, everyone can understand and contribute to the project without any language barriers. This promotes effective teamwork and improves overall project outcomes.Challenges and LimitationsWhile automatic graduation project translation offers numerous benefits, it is important to acknowledge its challenges and limitations. Some of these include: 1. Language nuances: Automated translation tools may struggle to accurately capture the nuances and subtleties of a language. This can result in the loss of context and potential misinterpretation of the translated content. Therefore, it is crucial for students to review and edit the translated material to ensure its accuracy.2. Technical jargon: Engineering projects often involve complex technical jargonand terminology. Automated translation tools may not have the capability to accurately translate these specialized terms. Students must be cautious and manually review the translated content to ensure the technical accuracy of their project documentation.3. Cultural differences: Different cultures have unique ways of expressing ideas and concepts. Automated translation tools may not always be able to capture these cultural nuances, leading to misunderstandings or misinterpretations. Students should be aware of these differences and make necessary adjustments to ensure effective communication.ConclusionAutomatic graduation project translation offers students a convenient and efficient way to translate project documentation. It saves time, improves accuracy, and promotes collaboration among team members. However, it is important to recognize the limitations of automated translation tools and take necessary precautions to ensure the quality and accuracy of the translated content. By leveraging the benefits of automatic translation while being mindful of its limitations, students can enhance their graduation projects and contribute to the advancement of automation in the engineering field.。
自动化专业毕业设计外文翻译--现地控制单元在水电厂自动化中的应用
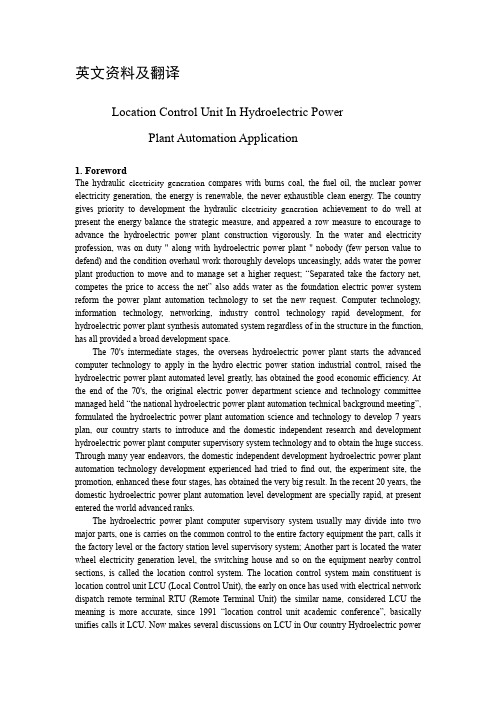
英文资料及翻译Location Control Unit In Hydroelectric PowerPlant Automation Application1. ForewordThe hydraulic electricity generation compares with burns coal, the fuel oil, the nuclear power electricity generation, the energy is renewable, the never exhaustible clean energy. The country gives priority to development the hydraulic electricity generation achievement to do well at present the energy balance the strategic measure, and appeared a row measure to encourage to advance the hydroelectric power plant construction vigorously. In the water and electricity profession, was on duty " along with hydroelectric power plant " nobody (few person value to defend) and the condition overhaul work thoroughly develops unceasingly, adds water the power plant production to move and to manage set a higher request; “Separated take the factory net, competes the price to access the net” also adds water as the foundation electric power system reform the power plant automation technology to set the new request. Computer technology, information technology, networking, industry control technology rapid development, for hydroelectric power plant synthesis automated system regardless of in the structure in the function, has all provided a broad development space.The 70's intermediate stages, the overseas hydroelectric power plant starts the advanced computer technology to apply in the hydro-electric power station industrial control, raised the hydroelectric power plant automated level greatly, has obtained the good economic efficiency. At the end of the 70's, the original electric power department science and technology committee managed held “the national hydroelectric power plant automation technical background meeting”, formulated the hydroelectric power plant automation science and technology to develop 7 years plan, our country starts to introduce and the domestic independent research and development hydroelectric power plant computer supervisory system technology and to obtain the huge success. Through many year endeavors, the domestic independent development hydroelectric power plant automation technology development experienced had tried to find out, the experiment site, the promotion, enhanced these four stages, has obtained the very big result. In the recent 20 years, the domestic hydroelectric power plant automation level development are specially rapid, at present entered the world advanced ranks.The hydroelectric power plant computer supervisory system usually may divide into two major parts, one is carries on the common control to the entire factory equipment the part, calls it the factory level or the factory station level supervisory system; Another part is located the water wheel electricity generation level, the switching house and so on the equipment nearby control sections, is called the location control system. The location control system main constituent is location control unit LCU (Local Control Unit), the early on once has used with electrical network dispatch remote terminal RTU (Remote Terminal Unit) the similar name, considered LCU the meaning is more accurate, since 1991 “location control unit academic conference”, basically unifies calls it LCU. Now makes several discussions on LCU in Our country Hydroelectric powerplant automated system application and the development.2. LCU applicationIn the hydroelectric power plant computer supervisory system LCU with the power plant production process connection, is directly in the system most has the object-oriented distribution characteristic the control device. The location control unit controlled member mainly includes following several parts:(1) power plant generating set, mainly has the hydraulic turbine, the generator, the auxiliary engine, the transformer and so on;(2) switching house, mainly has the generatrix, the circuit breaker, the isolator, the earth knife switch and so on;(3) public utility, mainly has the factory to use electricity the system, the oil system, the aqueous system, the direct current system and so on;(4) strobe, mainly has the water inlet strobe, the flood discharge strobe and so on.The LCU general arrangement nearby the power plant production equipment, to is accused the object movement operating mode to carry on the real-time surveillance and the control, is the power plant computer supervisory system compares the first floor control section. The primary data carries on gathering and the pretreatment in this, each kind of control adjustment order all sends out and completes the control closed loop through it, it is in the entire supervisory system very important, to the reliable request very high control device. Uses in the hydroelectric power plant LCU may divide into unit LCU, public LCU, switching house LCU according to the monitoring object and the installment position and so on. But and disposes according to the LCU itself structure divides, then may divide into the single trigger --linear structure LCU, take programmable controller (PLC) as foundation LCU, the intelligent location controller and so on three kinds. First kind of LCU many for hydroelectric power plant automation initial period product, at present basic no longer has used in the new system. Moreover still had few small hydroelectric power plants to use based on industry PC machine (called labor controlled machine IPC) the control system, below only discussed is in the mainstream status PLC and the intelligent location controller (the recent several years still had is called PCC (Programmable Computer Controller), PAC (Programmable Automation Controller) product, should also be possible to classify).2.1 programmable controller (PLC)The PLC definition has many kinds. International electrician committee (IEC) to PLC the definition is: The programmable controller is one kind of digital operation electronic system, for designs specially in the industry environment application. It uses the programmable the memory, uses in its internally stored program, carries out the logic operation, the sequential control, fixed time, counts with the arithmetic operation and so on face user's instruction, and through digital, the simulation input and the output, controls each kind of type the machinery or the production process. The programmable controller and the related equipment, all should according to easy form a whole with the industry control system, easy to expand its function the principle design.At first, needed to produce as a result of the American automobile industry has been possible to say was primitive PLC. Although the PLC being published time does not calculate long too, but along with the microprocessor appearance, large-scale, the ultra large scale integrated circuit technique of manufacture and the data communication technology rapid development, the PLC application and the technology also obtained the rapid development, its developing processapproximately separable three stages:(1) early time PLC (at the end of 60's -70's intermediate stages): Early PLC is called the programmable logical controller generally.(2) intermediate stage PLC (in 70's intermediate stage - 80's, later period): Starts in the 70's to use the microprocessor to take PLC the central processing element (CPU). Thus, causes PLC to result in the function big enhancement. In the software aspect, in the original logic operation, fixed time, counted and so on in the function foundations to increase functions and so on arithmetic operation, data processing and data communication, from diagnosis. In the hardware aspect, has developed the simulation quantity module, the long-distance I/O module as well as each kind of special function module, enables PLC the application scope to expand rapidly to needs the automatic control very many professions.(3) near future PLC (in the 80's, later period until now) enters in for the 80's, the later period, because the microprocessor hardware technique of manufacture rapid development, simultaneously the market price large scale drop, will cause each PLC manufacturer to be possible to use a higher scale the microprocessor. In order to further enhance PLC the processing speed, the very many manufacture manufacturer also developed has developed the special-purpose logical processing chip. Afterwards PLC has also integrated Ethernet, technologies and so on Web Server, has provided the function rich necessary software, causes the user community to use handily.On the century 80's to the 90's intermediate stages, are PLC develops the quickest time, the yearly rate continuously maintenance is 30%~40%. In this time, the PLC data acquisition handling ability, the numeral operational capability, the man-machine connection and network traffic capacity all obtains the large scale enhancement, PLC enters the process control domain gradually, unified after the partial industry control device substitutes gradually in certain applications has been at the dominant position in the process control domain the DCS system. Because PLC has the versatility strongly, the reliability high, the easy to operate, the programming simple, the adaptation surface broad and so on the characteristics, caused it is specially in the sequential control obtained the extremely widespread application in the industrial automation control.Applies PLC in the hydroelectric power plant production equipment monitoring begins in on the century 80's, because PLC defers to the industry use environment the standard to carry on the design generally, the reliability high, antijamming ability strong, the programming simple practical, met inserts the performance good very quickly accepts by the power plant user and system integration business, obtained the good application. At present includes in Our country Hydroelectric power plant use widespread PLC: GE Fanuc Corporation's GE Fanuc 90 series, German Siemens Corporation's S5, S7 series, French Schneider Corporation's Modicon Premium, Atrium and Quantum, American Rockwell Corporation PLC5, Control Logix, Japanese OMRON Corporation's SU-5, SU-6, SU-8, Japanese MITSUBISHI Corporation's FX2 series and so on. Because each kind of PLC principle of design difference is big, the product function, the performance as well as may constitute the location system scale to have the very big difference. Generally speaking, according to the different power plant in the security performance (including reliability, maintainable and so on), aspect and so on application function, control scale, system structure actual demands carries on the choice, may find appropriate PLC. At present there is big part of power plants the automated system all uses the PLC constitution location control section, and matches through the reasonable disposition, they basically all can shoulder the corresponding responsibility in the system, completes the corresponding function.But PLC took but one kind of general automated installment, is by no means designs specially for the hydroelectric power plant automation, this has in the special request profession application in the water and electricity automation also to be able to have some not suitable place inevitably, presently lists following several points:(1) PLC by “scanning”the way work, cannot satisfy the event resolution and the system clock synchronization request. The hydroelectric power plant computer supervisory system all is a multi-computer system, in order to guarantee the event resolution should have certain event besides PLC itself to respond ability and the high accuracy clock, but also requests in the overall system between various part of main equipment clock synthesis precision also to have to guarantee in a millisecond level. But take PLC as the foundation location control device if does not take the special measure, is unable to guarantee the hydroelectric power plant safe operation to the event resolution and the system clock synchronization request.(2) general PLC origin mainly aims at the machine-finishing profession, later gradually will expand all the various trades and occupations. Although present PLC has strongly from diagnosis function, but regarding the input, the output unit, it only from diagnoses the module level. This produces this kind of emphasis regarding our country electric power “the safety first” the profession said that, has certain being short of, often needs to add seperately the special security measure.(3) general PLC all has certain surge suppression ability generally, basically may suit the majority of profession application. But says regarding the hydroelectric power plant automated system, as a result of the equipment working conditions particularity, three level of surge suppression ability which the general PLC surge suppression ability and the technology standard request also has some disparities.2.2 intelligent location controllerApplies the many another kind of location control unit in Hydroelectric power plant automated system to be supposed to be the intelligent location controller, like ABB Corporation AC450, south auspicious group's SJ-600 series, Elin Corporation's SAT1703 and so on.AC450 is being suitable which ABB Corporation produces in industry environment Advant Controller series location control unit one kind, mainly applies in other profession DCS. It has included the module which by Motorola 68040 primarily processor CPU modules and I/O, MasterBus and so on many kinds of may elect, supports centralized I/O and distributional I/O, may act according to the different application demand to use the different module to constitute the suitable location subsystem.SAT1703 is the multi-processor system which Austrian Elin Corporation produces, it is loaded with different connection processor subsystem AK1703, AME1703 and AM1703 including 3. Each sub-system by the host processor, the connection template (module), constitutions and so on connection module, can realize the data processing, the control and the correspondence function, uses SMI in the LCU interior (Serial Module Interconnector) to carry on the correspondence. SAT1703 location control unit uses OS/2 operating system, the movement control software is ToolBox.SJ-600 series is on the international telegram automation research institute the century at the end of 90's for the domestically produced intelligence distributional location control unit which moves under the bad industry environment produces, by the master control module, the intelligent I/O module, the power source module as well as connects various modules and the master controlmodule scene bus network is composed. Moved reliably in the national dozens of large and middle scale hydroelectric power plants. Below SJ-600 has the main characteristic:(1), the master control module uses conforms to IEEE1996.1's embedded module standard PC104, has the reliability high, the scene environment compatibility strong and so on the characteristics. Uses low power loss embedded CPU, may choose the CPU model from 486 to the Pentium series.(2) 32 intelligence I/O module. All modules use 32 embedded CPU, this CPU designs specially for the embedded control, on the software uses the board level real-time operating system and the unification procedure code, only is different moves the corresponding duty according to the module. Has used large-scale programmable logic chip (EPLD) and the Flash memory, simplified the system design, enhanced the reliability. The intellectualized I/O module except may complete the data acquisition and the pretreatment independently, but also has very strongly from the diagnosis function, has provided the reliable control security and the convenience breakdown localization ability.(3) has the field bus network system structure, the system uses two network architectures, first is the factory cascade control network, connects LCU and the factory level computer, constitutes the distributed computer supervisory system; Second is I/O main line network, the connection master control module and the intelligent I/O module (location or long-distance), constitutes the distributional location control subsystem. All I/O module provides two field bus network connection, these modules all may disperse the arrangement, forms the redundant reliable distributional redundant system.(4) LCU direct connection high speed network. The network has become in the computer supervisory system the important part, it involves to the power plant control strategy and the movement way. Beforehand location controller many is the use private network carries on the connection with on position machine system, but conforms to the open standard network. If AC450 uses MB300 network with on position machine system connection, but with uses TCP/IP agreement the system connection only to be able to carry on through the special-purpose module by the VIP way the data transmission which limits.(5) has provided the direct GPS synchronized clock connection, does not need to program and the establishment. GPS to when may go directly to the module level, satisfied had the special request situation to the clock, like SOE and so on.(6) provides based on IEC61131-3 standard control language, in retained trapezoidal programming language in and so on the chart, structure text, instruction list foundations, developed the use “to see namely obtained”the technical design visualization flow chart programming language. The support control flow online debugging and playbacking, suits the complex control flow extremely the production and the maintenance.(7) in view of hydroelectric power plant automation specialized application development special-purpose function module.现地控制单元在水电厂自动化中的应用1. 前言水力发电与燃煤、燃油、核能发电相比,能源是可再生的、永不枯竭的清洁能源。
毕业设计 自动化 英文翻译

DESIGN AND IMPLEME.NTATION OF A VARIABLE FREQUENCY REGULATORY SYSTEM FOR WATER SUPPL YABSTRACTThe designs of the variable frequency constant pressure water supply for a single hydraulic pump and high power multiple hydraulic motors systems are presented in this paper. This system can save energy by controlling the speed of the pipe motors which depend upon the number of consumers in use. This system was also uccessfully implemented in most of the modern buildings in. Shanghai, China. Finally, the choice criteria for variable frequency regulators for water supply system will be discussed.INTRODUCTIONIt is inevitable to install high level water storage systems or reservoirs for a multiple story building or residential areas. This kind of system results in increasing construction cost and cleaning problems. Nevertheless, hydraulic pumps are used toraise the energy level of the water. The conventional high level reservoir system is in fact a pressure regulatory system. This pressure (head) is proportional to the height of the reservoir. Resistance of pipes is varying from time to time. When number of users increases, that means number of relief valves to be open is increased. It in turn reduces the resistance of the pipes. In order to reduce the construction cost, eliminate the cleansing problem of the high level reservoirs, and make the system simple, a variable frequency constant pressure closed loop system is presented to control the speeds of the hydraulic pumps.In this paper, the designs of the variable frequency constant pressure water supply for a single hydraulic pump and high power multiple hydraulic motors systems are presented. From static characteristics of water flow system, the critical point canbe obtained to achieve the minimization of energy consumed. The implementation of this system is also discussed. The choice of variable frequency regulators for water supply system is finally presented.ADVANTAGESOFTHEPROPOSEDSYSTEMIn short, the advantages of this proposed variable frequency constant pressure system for water supply are1. In a 3 hydraulic motors system, the capacity of the variable frequency regulator is just one-third of the capacity of the overall system. The cost is much reduced.2. Since the system consists of multiple pumping motors, they can be controlled by PLC such that the system is more reliable.3. Energy saving can be achieved by controlling the speed of pump motors, pressure can be kept constant no matter what water flow is (from zero to its maximum capacity)4. Each pumping imotor can be started smoothly by using this variable frequency regulator, it reduces pulse current. This kind of water supply system could become a new trend in modern multiple-story building design.PRINCIPLE OF OPERATIONThe principle of operation was initially illustrated by a single pump system. Fig. 1 shows a block diagram of a variable frequency constant pressure system which is suitable for single pump or small scale water flow system. The model type is JS.5-P1. The pressure sensor (PS) transducers the water pressure in pipes to e1ectrical signals. This signal will go to pressure regulator (PR) through an amplifier (A)and a comparator compared with the set value of waterpressure. The difference will come to the PID control to regulate the output frequency as well as the speeds of electric motors and hydraulic pumps. The constant pressure can then be achieved. Fig. 2 shows static characteristics of this constant pressure water supply system. Curves 1 and 2 represent relationship between the pressure head (H) and flow rate (Q) for different speeds of the pump. Curves 3 and 4 represent for different values of resistance of pipe. To simply the exposition, per unit values are adopted in the Fig. 2. Hence,H*=H/H N, Q*=Q/Q Nwhere H N and Q N are the set values of head and flow rate.In this system, both flow rate and the resistance of pipes are varying because the flow rate is proportional to number of valves to be opened. Curve 3 represents the resistance of pipe when the flow rate reaches the maximum point. It intercepts with the H* - Q* at point a , which is the set point for operation. Curve 4is for resistance of pipe when the flow rate is less and only part of valves to be opened.If there is no frequency regulator, it works at point b' only. At this moment, the head pressure exceeds the set value. The flow rate Q is proportional to the speed of the pump, n. Head pressure H is thus proportional to the square of the speed, n2. The speed of the pump can be controlled by the frequency regulator. It becomes the curve 2, which intercepts curve 4at point b, it is a new set (working) point. At this time, the set speed should be n*= n/nN = K (K<l). Obviously, the point b is lower than point b'. It in turn means that H at point b is less than that at point b'.Hb < Hb'It achieves the purpose of energy saving.FURTHER MODIFICATIONThis JSS-P1 model was suitable for single pump water supply system. When the flowrate is little, the pressure can be much reduced. For example, Hp* varies from 1 to Hp-* which is less than 1 (Hp-* < 1). It is able to save much energy. From thisworking principle, it was modified to suit a large scale multiple pumping water supply system. A new model of JS5-P2 was then developed. Fig. 3shows a block diagram of a variable frequency constant pressure system consisting of 3 same capacity pumps. It was modified from the JSS-P1 model. It is designed for multi- pumps water supply system which programmable logic control (PLC) is involved such that the number of hydraulic motors in operation can be determined by the flow rate. The rest of motors are in stand-by mode and the energy saving can be realized. From Fig. 3, the system was composed of pressure sensor (PS), pressure amplifier (A), pressure regulator (AP), signal identifier (AI), programmable logic control (PLC), and frequency regulator. The main feature of this system is that one set of variable frequency regulator is in use to control one hydraulic motor. The rest is idling at starting. If the water flow is within the preset range. This motor is running according its characteristic curve. When the flow rate is increased, The second motor will be smoothly started. The preset value of pressure in pipes can be maintained. There arethree values for operating these motors, 0-33.3%, 33.3-66.6% and 66.6-100%.In brief, the first pump motor will work if the flow rate falls within 33.3% of operation. The operating region is within curves 1 and 4in the Fig. 4.When the flow rate increases, beyond 33.3%, frequency regulator keeps the output frequency at 50 Hz, PLC will control of on-off state of the motors such that the first pump motor is supplied by the mains. The speed of the first pump motor runs at rated speed. The frequency regulator also set the second pump motor in stand-by mode. The operating region of the second motor is within curves 2and 5in the Fig. 4.When the flow rate is continuously increased and beyond 66.6%, and the frequency regulator reaches its rated frequency 50 Hz, PLC will command the second motor to connect to the mains again and the third one at stand-by mode. The operating region of the third one fallswithin curves 3and 6 in the Fig. 4. If the flow rate is reduced from 66.6% to 33.3%, PIX will command to one of the pump motors cut off from the mains. When the flowrate further reduces, and less than 33.3%, there will be only one motor connected to the mains. From the working principle, the three pump motors are operated in turnto meet the requirement of energy saving.CRITERIA FOR FREQUENCY, REGULATORFor the load of the hydraulic pump, the torque is proportional to the square of the motor speed, it is also proportional to the square of the supply frequency, f2. To a electric motor, the torque is equal to C m *Φm*I2*cosα, where C m, is a constant, Φm, is the magnetic flux of rotating field, I2 is the rotor current, and cosα is the power factor of rotor circuit. I2normally cannot exceed its rated value.If the voltage drop in the stator is negligible, $, will be proportional to supply voltage V. In order to maintain, the supply voltage V should be required to be proportional to the square of the frequency. Therefore, the characteristic of V versus f should be set to be a quadratic relationship.CONCLUSIONThis type of variable frequency constant pressure closed loop system for water supply was designed and implemented in Shanghai, China. The performance was proven satisfactory. A copy of a photograph of this system was shown in Fig. 5. All four advantages of this proposed system were fully realized. This system is one of the energy saving methods in tall building design.Automation System S7-300:Getting Started CPU 31xC: Commissioning1. Step: Installing the mounting rail and modulesRail installation sequenceFrom left to right: Power supply PS 307 - CPU 313C.The synopsis will provide you with an overview of the overall configuration.Install and ground the mounting rail1. Screw on the mounting rail (screw size: M6) so that at least 40 mm space remains above and below the rail. When mounting it on a grounded metallic panel or on a grounded device mounting panel made of steel sheet, make sure you have a low impedance connection between the mounting rail and the mounting surface.2. Connect the rail to the protective conductor. An M6 screw is provided on the rail for this purpose. Minimum cross-section from the cable to the protective conductor: at least 10 mm2. Installing modules on the mounting rail1. Hook the power supply module onto the rail, slide it until it reaches the grounding screw of the rail and then screw it tight.2. Hook the CPU onto the rail (1),slide it along as far as the module on the left (2), and swing it down into place (3).3. Bolt the CPU tight, applying a torque of between 0.8 and 1.1 Nm.4. Insert the micro memory card into the CPU (4); this is essential for operation. If you do not know the content of the micro memory card, erase it first on the programming device.2. Step: Wiring modulesWiring the power supply and the CPU1. Open the front panel covers of the power supply module and CPU.2. Unscrew the strain relief clamp on the power supply module.3. Remove the insulation from the power cord, attach the cable end sleeves (for stranded conductors), and connect them to the power supply.4. Screw the strain-relief assembly tight.5. Insert two short connecting cables between the power supply and the CPU and screw them tight.6. Check that the line voltage selector switch is set to the correct line voltage.The default line voltage setting for the power supply module is 230 VAC. To label a front connector, follow the steps outlined below: To change the voltage, remove the protective cap with a screwdriver, set the switch to the required line voltage and replace the protective cap. Wiring the front connectors of the DI and DO1. Open the right front panel of the CPU 313C.2. Place the front connector into wiring position. You do this by pushing a front connector into the CPU until it latches. In this position, the front connector still protrudes from the CPU. In the wiring position a wired front connector has no contact with the module.3. Remove 6 mm of the insulation from the ends of the wires that go into the front connector. Attach cable end sleeves to these ends.4. Wire the front connector (DI side) as follows:– Terminal 1: L+ of the power supply– Terminal 3: Button 1– Terminal 4: Button 2– Terminal 20: M of the power supply5. Wire the front connector (DO side) as follows:– Terminals 21 and 31: L+ of the power supply– Terminal 30: M of the power supply.6. Wire the free cable ends of the button with L+ of the power supply.7. Lead the wires downwards out of the front connector.8. Secure the front connector with the screws (this establishes contact with the module).9. Close the front panel covers of the power supply module and the front panel of the CPU.3. Step: Commissioning hardwareProcedure1. Use the PG cable to connect the programming device to the CPU. When using a cable with PROFIBUS connectors, remember to switch on the integrated terminating resistors. Close the front panel cover of the CPU, then set the mode selector switch on the CPU to STOP.2. Connect the mains cable, then switch on the power supply module PS 307.The DC24V LED on the power supply is lit. All the LEDs on the CPU light up briefly; the SF LED and the DC5V LED stay lit. The STOP LED then flashes slowly to indicate a CPU memory reset.3. Perform a CPU memory reset:– Turn the mode switch to MRES. Hold the mode selector at this position until the STOP LED lights up for the second time and then remains lit (approx. 3 seconds). Then release it.– You must press the mode switch back to MRES within 3 s. The STOP LED begins to flash rapidly and the CPU performs a reset. You can now release the mode switch.The CPU has completed the memory reset when the STOP LED remains permanently lit again.4. Start your programming device, then run SIMATIC Manager from your Windows Desktop.A window opens with SIMATIC Manager.5. Select button 1.The LED of I124.1 lights up. No DO LED lights up.6. Select button 2. The LED of I124.2 lights up. No DO LED lights up.4. Step: Programming the circuitProcedure1. Follow the instructions of the STEP 7 "New Project" wizard on the programming device and set up a new project with the following data:– CPU type: CPU 313C– Block to be created: OB 1– Project name: S7_Pro1A window, divided into two parts, opens with the title S7_Pro1 -- .2. Double-click the OB1 icon in the right-hand part of the window. The editor for editing the OB 1 block opens.3. In the "View" menu, select "LAD" to change to the ladder logic programming language. At the bottom of the left-hand window, a current path is displayed in network 1.4. Carefully click on the horizontal line representing the current path. The line is highlighted.5. On the toolbar, click twice on the --||-- icon (normally-open contact) and then once on the –( ) icon (coil). The icons are inserted into the current path.6. Click on the red question mark for the left-hand normally- open contact in the current path. The normally-open contact is highlighted and the question mark is replaced with a text input box containing the cursor.7. Enter I124.1 and press Return. The left-hand normally-open contact is now called I124.1.8. Label the right button in the same way with I124.2 and the coil with Q124.0.9. Close the editor and click Yes when you are prompted to save. The editor is closed and OB 1 is saved.5. Step: Configuring hardwareProcedure1. In SIMATIC Manager, click on SIMATIC 300 Station in the left-hand part of the window. The Hardware and CPU 313C icons appear in the right-hand part of the window.2. Double-click the Hardware icon in the right-hand part of the window.The editor for editing the hardware opens.3. If the catalog is not shown in the right section of the window, you can activate it by selecting Catalog in the View menu.4. Expand SIMATIC 300 and CPU-300 until you see CPU 313C.5. Insert the CPU 313C by dragging it to slot 2 (top or bottom left-hand window).6. Check that the order number displayed for slot 2 in the lower left-hand part of the window matches the order number of your CPU. You may need to expand the width of the order number column to see the entire number. If it does: Skip to the next step. If it does not: Expand CPU-300 in the catalog until you see CPU 313C and replace the CPU in slot 2 by dragging the CPU with the correct order number from the catalog.7. Perform steps 3 and 4 for the power supply module PS 307 too. You insert the PS 307 in slot 1.8. Go to the Station menu and select Save and compile. The hardware configuration is compiled and saved.9. Close the editor. The editor is closed.6. Step: Trial runProcedure1. Use the SIMATIC 300 station and CPU 313C to browse to the S7 program. In SIMATIC Manager click on Blocks in the right-hand part of the window. Blocks will now be highlighted.2. Select Download from the PLC menu to transfer the program and hardware configuration to the CPU. Confirm all windows with Yes. The program and configuration are downloaded from the programming device to theCPU. The program is now stored on the Micro Memory Card (in the load memory), where it is unaffected by power failures and resets.3. Set the CPU's mode switch to RUN. The STOP LED is switched off. The RUN LED starts to flash and then assumes a continuous signal.4. Press each of the buttons alternately. The LEDs of inputs I124.1 and I124.2 light up alternately. The LED of output Q124.0 is not lit.5. Press both buttons simultaneously. The LEDs of inputs I124.1 and I124.2 light up simultaneously. The LED of output Q124.0 is lit. This would switch on a connected finalcontrolling element or indicator.Further InformationDiagnostics/Correction of ErrorsWrong operation, faulty wiring or a faulty hardware configuration may cause errors which the CPU, CP or IE/PB-Link indicate with the SF group error LED after CPU memory reset. How to analyze such errors and alarms is described in the CPU31xC and CPU 31x operating instructions, Setup and Programming with STEP 7 manuals.Manuals containing further informationFor more in-depth Getting Started information, we recommend Getting Started and Exercises with STEP 7Service & Support on the InternetIn addition to our documentation, we offer a comprehensive online knowledge base on the Internet at:/automation/service&supportThere you can find:• A newsletter containing the latest information on your Siemens products.• The documents you need using our search engine in Service & Support.• the bulletin board, a worldwide knowledge exchange for users and experts.• your local contact for Automation & Drives in our contact database.• Information about on-site services, repairs, spare parts. You will find much more under "Services".第一部分供水专用变频器的设计和应用摘要:本文提出了一种用于变频恒压供水的单个液压泵和高功率多液压电机系统的设计方法。
自动化专业毕业设计翻译正文

Universal Serial Communication Interface – SPI ModeThe universal serial communication interface (USCI) supports multiple serial communication modes withone hardware module. This chapter discusses the operation of the synchronous peripheral interface (SPI)16.1 mode.Universal Serial Communication Interface (USCI) OverviewThe universal serial communication interface (USCI) modules support multiple serial communication modes. Different USCI modules support different modes. Each different USCI module is named with a different letter. For example, USCI_A is different from USCI_B, etc. If more than one identical USCI module is implemented on one device, those modules are named with incrementing numbers. For example, if one device has two USCI_A modules, they are named USCI_A0 and USCI_A1. See the device-specific data sheet to determine which USCI modules, if any, are implemented on which devices.USCI_Ax modules support:•UART mode•Pulse shaping for IrDA communications•Automatic baud-rate detection for LIN communications•SPI modeUSCI_Bx modules support:I2mode•C•SPI mode16.2 USCI Introduction – SPI ModeIn synchronous mode, the USCI connects the device to an external system via three or four pins:UCxSIMO, UCxSOMI, UCxCLK, and UCxSTE. SPI mode is selected when the UCSYNC bit is set, and SPI mode (3-pin or 4-pin) is selected with the UCMODEx bits.SPI mode features include:•7-bit or 8-bit data length•LSB-first or MSB-first data transmit and receive•3-pin and 4-pin SPI operation•Master or slave modes•Independent transmit and receive shift registers•Separate transmit and receive buffer registers•Continuous transmit and receive operation•Selectable clock polarity and phase control•Programmable clock frequency in master mode•Independent interrupt capability for receive and transmit•Slave operation in LPM4Figure16-1 shows the USCI when configured for SPI mode.16.3 USCI Operation – SPI ModeIn SPI mode, serial data is transmitted and received by multiple devices using a shared clock provided by the master. An additional pin, UCxSTE, is provided to enable a device to receive and transmit data and is controlled by the master.Three or four signals are used for SPI data exchange:•UCxSIMO slave in, master out Master mode: UCxSIMO is the data output line. Slave mode: UCxSIMO is the data input line.•UCxSOMI slave out, master in Master mode: UCxSOMI is the data input line. Slave mode: UCxSOMI is the data output line.•UCxCLK USCI SPI clock Master mode: UCxCLK is an output. Slave mode: UCxCLK is an input.•UCxSTE slave transmit enable. Used in 4-pin mode to allow multiple masters on a single bus.Not used in 3-pin mode. Table 16-1 describes the UCxSTE operation.16.3.1 USCI Initialization and ResetThe USCI is reset by a PUC or by the UCSWRST bit. After a PUC, the UCSWRST bit is automatically set,keeping the USCI in a reset condition. When set, the UCSWRST bit resets the UCRXIE, UCTXIE,UCRXIFG, UCOE, and UCFE bits, and sets the UCTXIFG flag. Clearing UCSWRST releases the USCI for operation.Note: Initializing or reconfiguring the USCI moduleThe recommended USCI initialization/reconfiguration process is:1. Set UCSWRST ( BIS.B #UCSWRST, & UCxCTL1 ).2. Initialize all USCI registers with UCSWRST = 1 (including UCxCTL1).3. Configure ports.4. Clear UCSWRST via software ( BIC.B #UCSWRST, & UCxCTL1 ).5. Enable interrupts (optional) via UCRXIE and/or UCTXIE.16.3.2 Character FormatThe USCI module in SPI mode supports 7-bit and 8-bit character lengths selected by the UC7BIT bit. In 7-bit data mode, UCxRXBUF is LSB justified and the MSB is always reset. The UCMSB bit controls the direction of the transfer and selects LSB or MSB first.Note: Default character formatThe default SPI character transmission is LSB first. For communication with other SPI interfaces, MSB-first mode may be required.Note: Character format for FiguresFigures throughout this chapter use MSB-first format.16.3.3 Master ModeFigure 16-2 shows the USCI as a master in both 3-pin and 4-pin configurations.The USCI initiates data transfer when data is moved to the transmit data buffer UCxTXBUF. The UCxTXBUF data is moved to the transmit (TX) shift register when the TX shift register is empty, initiating data transfer on UCxSIMO starting with either the MSB or LSB, depending on the UCMSB setting. Data on UCxSOMI is shifted into the receive shift register on the opposite clock edge. When the character is received, the receive data is moved from the receive (RX) shift register to the received data buffer UCxRXBUF and the receive interrupt flag UCRXIFG is set, indicating the RX/TX operation is complete.A set transmit interrupt flag, UCTXIFG, indicates that data has moved from UCxTXBUF to the TX shift register and UCxTXBUF is ready for new data. It does not indicate RX/TX completion.To receive data into the USCI in master mode, data must be written to UCxTXBUF, because receive and transmit operations operate concurrently.16.3.4 Slave ModeFigure 16-3 shows the USCI as a slave in both 3-pin and 4-pin configurations. UCxCLK is used as the input for the SPI clock and must be supplied by the external master. The data-transfer rate is determined by this clock and not by the internal bit clock generator. Data written to UCxTXBUF and moved to the TX shift register before the start of UCxCLK is transmitted on UCxSOMI. Data on UCxSIMO is shifted into the receive shift register on the opposite edge of UCxCLK and moved to UCxRXBUF when the set number of bits are received. When data is moved from the RX shift register to UCxRXBUF, the UCRXIFG interrupt flag is set, indicating that data has been received. The overrun error bit UCOE is set when the previously received data is not read from UCxRXBUF before new data is moved to UCxRXBUF.16.3.5 SPI EnableWhen the USCI module is enabled by clearing the UCSWRST bit, it is ready to receive and transmit. In master mode, the bit clock generator is ready, but is not clocked nor producing any clocks. In slave mode, the bit clock generator is disabled and the clock is provided by the master.A transmit or receive operation is indicated by UCBUSY = 1.A PUC or set UCSWRST bit disables the USCI immediately and any active transfer is terminated.Transmit EnableIn master mode, writing to UCxTXBUF activates the bit clock generator, and the data begins to transmit.In slave mode, transmission begins when a master provides a clock and, in 4-pin mode, when the UCxSTE is in the slave-active state.Receive EnableThe SPI receives data when a transmission is active. Receive and transmit operations operate concurrently.16.3.6 Serial Clock ControlUCxCLK is provided by the master on the SPI bus. When UCMST = 1, the bit clock is provided by the USCI bit clock generator on the UCxCLK pin. The clock used to generate the bit clock is selected with the UCSSELx bits. When UCMST = 0, the USCI clock is provided on the UCxCLK pin by the master, the bit clock generator is not used, and the UCSSELx bits are don't care. The SPI receiver and transmitter operate in parallel and use the same clock source for data transfer.The 16-bit value of UCBRx in the bit rate control registers (UCxxBR1 and UCxxBR0) is the division factor of the USCI clock source, BRCLK. The maximum bit clock that can be generated in master mode is BRCLK. Modulation is not used in SPI mode, and UCAxMCTL should be cleared when using SPI mode for USCI_A. The UCAxCLK/UCBxCLK frequency is given by:BitClock f = BRCLK f /UCBRxSerial Clock Polarity and PhaseThe polarity and phase of UCxCLK are independently configured via the UCCKPL and UCCKPH control bits of the USCI. Timing for each case is shown in Figure 16-4 .16.3.7 Using the SPI Mode With Low-Power ModesThe USCI module provides automatic clock activation for use with low-power modes. When the USCI clock source is inactive because the device is in a low-powermode, the USCI module automatically activates it when needed, regardless of the control-bit settings for the clock source. The clock remains active until the USCI module returns to its idle condition. After the USCI module returns to the idle condition, control of the clock source reverts to the settings of its control bits.In SPI slave mode, no internal clock source is required because the clock is provided by the external master. It is possible to operate the USCI in SPI slave mode while the device is in LPM4 and all clock sources are disabled. The receive or transmit interrupt can wake up the CPU from any low-power mode.16.3.8 SPI InterruptsThe USCI has only one interrupt vector that is shared for transmission and for reception. USCI_Ax and USC_Bx do not share the same interrupt vector.SPI Transmit Interrupt OperationThe UCTXIFG interrupt flag is set by the transmitter to indicate that UCxTXBUF is ready to accept another character. An interrupt request is generated if UCTXIE and GIE are also set. UCTXIFG is automatically reset if a character is written to UCxTXBUF. UCTXIFG is set after a PUC or when UCSWRST = 1. UCTXIE is reset after a PUC or when UCSWRST = 1.Note: Writing to UCxTXBUF in SPI modeData written to UCxTXBUF when UCTXIFG = 0 may result in erroneous data transmission.SPI Receive Interrupt OperationThe UCRXIFG interrupt flag is set each time a character is received and loaded into UCxRXBUF. An interrupt request is generated if UCRXIE and GIE are also set. UCRXIFG and UCRXIE are reset by a system reset PUC signal or when UCSWRST = 1. UCRXIFG is automatically reset when UCxRXBUF is read.UCxIV, Interrupt Vector GeneratorThe USCI interrupt flags are prioritized and combined to source a single interrupt vector. The interrupt vector register UCxIV is used to determine which flag requested an interrupt. The highest-priority enabled interrupt generates a number in the UCxIV register that can be evaluated or added to the program counter (PC) to automatically enter the appropriate software routine. Disabled interrupts do not affect the UCxIV value.Any access, read or write, of the UCxIV register automatically resets the highest-pending interrupt flag. If another interrupt flag is set, another interrupt is immediately generated after servicing the initial interrupt.UCxIV Software ExampleThe following software example shows the recommended use of UCxIV. The UCxIV value is added to the PC to automatically jump to the appropriate routine. The following example is given for USCI_B0.、USCI_SPI_ISRADD & UCB0IV, PC ; Add offset to jump tableRETI ; Vector 0: No interruptJMP RXIFG_ISR ; Vector 2: RXIFGTXIFG_ISR ; Vector 4: TXIFG... ; Task starts hereRETI ; ReturnRXIFG_ISR ; Vector 2... ; Task starts hereRETI ; ReturnSPI串行同步通讯接口模式这个 5 系列通用串行通信接口支持一个硬件模块下的多通道串行通信模式。
- 1、下载文档前请自行甄别文档内容的完整性,平台不提供额外的编辑、内容补充、找答案等附加服务。
- 2、"仅部分预览"的文档,不可在线预览部分如存在完整性等问题,可反馈申请退款(可完整预览的文档不适用该条件!)。
- 3、如文档侵犯您的权益,请联系客服反馈,我们会尽快为您处理(人工客服工作时间:9:00-18:30)。
编号:毕业设计英文翻译译文题目: Automation院(系):计算机系专业:自动化学生姓名:学号:指导教师:职称:2005 年6 月3日自动化汤姆里治2005 年四月 12 日目录1 介绍 . . . . . . . . . . . . . . . . . . . . . . . . . . . . . . . . . . . . . . . . . . . . . . . . . . . . . . . . . . . . . . . . . .12 需求. . . . . . . . . . . . . . . . . . . . . . . . . . . . . . . . . . . . . . . . . . . . . . . . . . . . . . . . . . . . . . . . . . .13 目前交互式证明器的自动化. . . . . . . . . . . . . . . . . . . . . . . . . . . . . . . . . . . . . . . . . . . .44 技术. . . . . . . . . . . . . . . . . . . . . . . . . . . . . . . . . . . . . . . . . . . . . . . . . . . . . . . . . . . . . . . . . . .5 4.1 证明的搜寻. . . . . . . . . . . . . . . . . . . . . . . . . . . . . . . . . . . . . . . . . . . . . . . . . . . . . . . . . . . . . .6 4.1.1逻辑系统. . . . . . . . . . . . . . . . . . . . . . . . . . . . . . . . . . . . . . . . . . . . . . . . . . . . . . . . . . . . . . .6 4.1.2引进规则. . . . . . . . . . . . . . . . . . . . . . . . . . . . . . . . . . . . . . . . . . . . . . . . . . . . . . . . . . . . . . .6 4.2 等式. . . . . . . . . . . . . . . . . . . . . . . . . . . . . . . . . . . . . . . . . . . . . . . . . . . . . . . . . . . . . . . . . . . .8 4.2.1改写. . . . . . . . . . . . . . . . . . . . . . . . . . . . . . . . . . . . . . . . . . . . . . . . . . . . . . . . . . . . . . . . . . .8 4.2.2条件的简单化. . . . . . . . . . . . . . . . . . . . . . . . . . . . . . . . . . . . . . . . . . . . . . . . . . . . . . . . . . . . . . . .9 4.2.3完成. . . . . . . . . . . . . . . . . . . . . . . . . . . . . . . . . . . . . . . . . . . . . . . . . . . . . . . . . . . . . . . . . . 10 4.2.4动态的完成. . . . . . . . . . . . . . . . . . . . . . . . . . . . . . . . . . . . . . . . . . . . . . . . . . . . . . . . . . . . . .114.2.5方程式的统一. . . . . . . . . . . . . . . . . . . . . . . . . . . . . . . . . . . . . . . . . . . . . . . . . . . . . . . . . . . . . . .125 连接与整合. . . . . . . . . . . . . . . . . . . . . . . . . . . . . . . . . . . . . . . . . . . . . . . . . . . . . . . . . . . . . .126 评估. . . . . . . . . . . . . . . . . . . . . . . . . . . . . . . . . . . . . . . . . . . . . . . . . . . . . . . . . . . . . . . . . .13 6.1 评估生产需求. . . . . . . . . . . . . . . . . . . . . . . . . . . . . . . . . . . . . . . . . . . . . . . . . . . . . . . . . . . . . .13 6.2 完整性. . . . . . . . . . . . . . . . . . . . . . . . . . . . . . . . . . . . . . . . . . . . . . . . . . . . . . . . . . . . . . . . . 14 6.3 效率. . . . . . . . . . . . . . . . . . . . . . . . . . . . . . . . . . . . . . . . . . . . . . . . . . . . . . . . . . . . . . . . . .146.4 实际应用. . . . . . . . . . . . . . . . . . . . . . . . . . . . . . . . . . . . . . . . . . . . . . . . . . . . . . . . . . . . . . 157 替代选择. . . . . . . . . . . . . . . . . . . . . . . . . . . . . . . . . . . . . . . . . . . . . . . . . . . . . . . . . . . . . . 168 结论. . . . . . . . . . . . . . . . . . . . . . . . . . . . . . . . . . . . . . . . . . . . . . . . . . . . . . . . . . . . . . . . . .191 介绍自动化可能是成功的机械化的关键。
在一些情形中,机械化不需要自动化就可以实行。
确实,在高度抽象的数学区域,大部分由使用者拼出的复杂证明组成的机械化推论远远超过了那些目前能被自动化解决的范围。
在这一背景下,如果自动化它被全部使用,将指导在容易的可以解决的被紧紧地限定的次问题上。
一个机械化的典型例子是我们的拉姆齐定理的形式化。
另一方面,在推论相对被限制的地方,自动化能富有成效地在确认类型的证明中被应用,但是绝对程度的细节将使一个非自动化的机械化不可实行。
许多人已经花费了数年来发展全自动系统。
比如Vampire [VR] 和otter [McC]全自动系统。
我们可以和这样的系统竞争的设想是愚蠢的。
它们的执行是一种方式,这种方式超过目前在交互式定理证明器被实行的系统。
这些计划正在进行是为了把这些系统和交互式定理证明器相连。
这是极其有价值的工作:如果知道一个一阶的陈述是可证明的,这时应该期待机器能提供一个证明。
在这一节中,我们简略说明一些我们已经在各种不同的情况应用研究的技术。
自然地我们不企图仅此一次去解决自动化推论的问题。
宁可我们把重心集中在问题,而这些问题典型地出现在我们已经涉及的研究。
我们首先简略说明我们需要的自动化的引擎功能。
我们然后描述我们应用的技术,而且他们是如何整合的。
我们评估根据我们的需求性质上地产生的引擎,和数量地有关于一件相当大的案例研究。
这些技术中的少数是新奇的,宁可,我们企图用一种适宜的方式来融合现行的技术。
这些步骤在HOL启发定理证明器被发展,这是我们建立的设计原型的一辆优良车辆的不同方法。
2 需求我们的自动化的需求是什么? 让我们区别一下自动化和全自动化的使用,以及交互式自动化的使用,每一种的需求都有非常地不同。
也许料想不到地,失败的自动化证明引擎是基准,是观念,这观念是当交互式发展的复杂证明使我们花费大多数时间对" 几乎" 的可证明的义务的时候。
因此我们想要证明器给我们完美的反馈作为为什么任务不能够被执行的原因。
这引证强调一种在自动化和交互式证明之间的重要的不同。
在自动校对中,可典型地知道,目标是可证明的( 或至少,非常强烈地怀疑,而且在结束相当多量的时间之前准备等候证明的搜寻)。
的确,自动证明器被判断在他们能实际上证明多少可证明的目标之上。
在交互式证明中," 我们花费我们大多数的时间在几乎可证明的义务上"。
这是交互式和证明之间的不同。
如果我们花费大部份的时间尝试去证明简单但不可证实的目标,然后校正的搜寻完全变成比较不重要。
这虽不能说是它全部失去重要::如果一个系统缺乏完整性,这时它将会无法证明一些可证明的目标。
什么类型的目标正在被放弃,这是非常必要而且主要去知道的,这是为了知道当一个证明器失败于证明一个目标时就能理解它是什么意思。
这些知识也非常有用,当混合系统为了了解作为整个系统的行为,应当首先了解部分的行为。
在一个交互式的环境中,在完全之上所有物可能被偏爱,就我们而言,自动化的最重要方面是简单化。
而这些我们不是意味着去落实简单( 要布多少根线来实现系统? 等等),而是概念上的简单化。
例如,简单化到处被用于交互式定理求证。
如果一组改写规则不能融合,这时去了解简化器的行为,必须了解适用的规则顺序。
不用说,对于理解这是一件极端复杂的事情,而且属于这些所有物的证明在推测上极端易碎。
概念上的简单化通过聚集和简易装置的终端对一个简化器进行紧密地约束。
如果一个使用者要了解系统,概念上的简单化很重要。
如果一个系统的概念简单,它将会很有希望被简单的使用。